Prodigit 3341G Series User manual

3341G Series
Plug-In Electronic
Load module
Operation manual
S/N:9003341G02 REV:A

Material Contents Declaration
(材料含量宣称)
(Part Name)
零件名称
Hazardous Substance (有毒有害物质或元素)
铅(Pb)
汞(Hg)
镉(Cd)
六价铬
(Cr6+)
多溴联
苯(PBB)
多溴二苯醚
(PBDE)
PCBA
(印刷电路装配件)
x
○
x
○
○
○
Electrical part not on
PCBA’s
未在PCBA上的电子零件
x
○
x
○
○
○
Metal parts
金属零件
○
○
○
x
○
○
Plastic parts
塑料零件
○
○
○
○
x
x
Wiring
电线
x
○
○
○
○
○
Package
封装
x
○
○
○
○
○
对销售之日的所售产品,本表显示, PRODIGIT 供应链的电子信息产品可能包含这些物质。注意:在所售产品中可能
会也可能不会含有所有所列的部件。This table shows where these substances may be found in the supply chain
of Prodigit electronic information products, as of the date of sale of the enclosed product. Note that some of the
component types listed above may or may not be a part of the enclosed product. ○:表示该有毒有害物质在该部
件所有均质材料中的含量均在SJ/T 11363-2006 标准规定的限量要求以下。○:Indicates that the concentration of
the hazardous substance in all homogeneous materials in the parts is below the relevant threshold of the SJ/T
113632006 standard. ×:表示该有毒有害物质至少在该部件的某一均质材料中的含量超出SJ/T 11363-2006 标准
规定的限量要求。×:Indicates that the concentration of the hazardous substance of at least one of all
homogeneous materials in the parts is above the relevant threshold of the SJ/T 11363-2006 standard.
Note(注释):
1.Prodigit has not fully transitioned to lead-free solder assembly at this moment;However, most of the
components used are RoHS compliant.
(此刻,Prodigit 并非完全过渡到无铅焊料组装;但是大部份的元器件一至于RoHS的规定。)
2. The product is labeled with an environment-friendly usage period in years.
The marked period is assumed under the operating environment specified in the product specifications.
(产品标注了环境友好的使用期限制(年)。所标注的环境使用期限假定是在此产品定义的使用环境之下。)
Example of a marking for a 10 year period:
(例如此标制环境使用期限为10年)

SAFETY SUMMARY
The following general safety precautions must be observed during all phases of operation, service,
and repair of this instrument. Failure to comply with these precautions or with specific warnings
elsewhere in this manual violates safety standards of design, manufacture, and intended use of the
instrument. PRODIGIT assumes no liability for the customer's failure to comply with these
requirements.
GENERAL
This product is a Safety Class 1 instrument (provided with a protective earth terminal). The protective
features of this product may be impaired if it is used in a manner not specified in the operation
instructions.
ENVIRONMENTAL CONDITIONS
This instrument is intended for indoor use in an installation category I, pollution degree 2 environments.
It is designed to operate at a maximum relative humidity of 80% and at altitudes of up to 2000 meters.
Refer to the specifications tables for the ac mains voltage requirements and ambient operating
temperature range.
BEFORE APPLYING POWER
Verify that the product is set to match the available line voltage and the correct fuse is installed.
GROUND THE INSTRUMENT
This product is a Safety Class 1 instrument (provided with a protective earth terminal). To minimize
shock hazard, the instrument chassis and cabinet must be connected to an electrical ground. The
instrument must be connected to the ac power supply mains through a three conductor
power cable, with the third wire firmly connected to an electrical ground (safety ground) at the power
outlet. Any interruption of the protective (grounding) conductor or disconnection of the protective earth
terminal will cause a potential shock hazard that could result in personal injury.
FUSES
Only fuses with the required rated current, voltage, and specified type (normal blow, time delay, etc.)
should be used. Do not use repaired
Fuses or short circuited fuse holder. To do so could cause a shock or fire hazard.
DO NOT OPERATE IN AN EXPLOSIVE ATMOSPHERE.
Do not operate the instrument in the presence of flammable gases or fumes.
KEEP AWAY FROM LIVE CIRCUITS.
Operating personnel must not remove instrument covers. Component replacement and internal
adjustments must be made by qualified service personnel. Do not replace components with power
cable connected. Under certain conditions, dangerous voltages may exist even with the power cable
removed. To avoid injuries, always disconnect power, discharge circuits and remove external voltage
sources before touching components.
DO NOT SERVICE OR ADJUST ALONE.
Do not attempt internal service or adjustment unless another person, capable of rendering first aid and
resuscitation, is present.
DO NOT EXCEED INPUT RATINGS.
This instrument may be equipped with a line filter to reduce electromagnetic interference and must be
connected to a properly grounded receptacle to minimize electric shock hazard. Operation at line
voltages or frequencies in excess of those stated on the data plate may cause leakage currents in
excess of 5.0 mA peak.
DO NOT SUBSTITUTE PARTS OR MODIFY INSTRUMENT.
Because of the danger of introducing additional hazards, do not install substitute parts or perform any
unauthorized modification to the instrument. Return the instrument to a PRODIGIT ELECTRONICS
Sales and Service Office for service and repair to ensure that safety features
are maintained.
Instruments which appear damaged or defective should be made inoperative and secured against
unintended operation until they can be repaired by qualified service personnel.

SAFETY SYMBOLS
Direct current (DC)
Alternating current (AC)
Both direct and alternating
current
Three-phase alternating current
Off (Supply)
On (Supply)
Protective earth (ground)
terminal
Caution!Refer to this manual before using the meter.
Caution, risk of electric shock
CAT IV –Is for measurements performed at the source of the low-voltage
installation.
CAT III –Is for measurements performed in the building installation.
CAT II –Is for measurements performed on circuits directly connected to the low-
voltage installation.
.
This equipment is not for measurements performed for CAT II, III, and IV.
Fuse

3341G series module load operation manual
Table of Contents
Chapter 1 Introduction ························································································· 1
1-1. GENERAL DESCRIPTION ················································································1
1-2. FEATURES ·······························································································6
1-3. STANDARD ACCESSORIES··············································································6
1-4. OPTION ··································································································7
1-5. SPECIFICATIONS ························································································8
Chapter 2 Installation ·························································································10
2-1. INSTALLATION AND REMOVAL OF 3341G SERIES PLUG IN MODULE ····························· 11
2-2. ENVIRONMENTAL REQUIREMENTS ·································································· 12
2-3. OBSERVE THE INTERNATIONAL ELECTRICAL SYMBOL LISTED BELOW. ························· 12
2-4. CLEANING····························································································· 12
2-5. POWER UP····························································································· 12
2-6. OPERATING FLOW CHART FOR EACH LOAD MODULE OPERATION ································ 13
Chapter 3 Operation···························································································14
3-1 FRONT PANEL DESCRIPTION ········································································· 14
3-2 INSTRUCTIONS ························································································ 15
3-3 INITIAL SETTING OF 3341G SERIES LOAD MODULE ················································ 48
3-4 INPUT TERMINAL AND WIRE CONSIDERATION······················································ 50
3-5 .PROTECTION FEATURES············································································· 52
Chapter 4 Applications························································································53
4-1 .LOCAL SENSE CONNECTIONS········································································ 53
4-2 REMOTE SENSE CONNECTIONS ······································································ 54
4-3 .CONSTANT CURRENT MODE APPLICATION························································ 55
4-4 .CONSTANT VOLTAGE MODE APPLICATION························································ 57
4-5 .CONSTANT RESISTANCE MODE APPLICATION····················································· 58
4-6 .CONSTANT POWER MODE APPLICATION··························································· 59
4-7 LED MODE APPLICATIONS··········································································· 60
4-8 THE CONNECTION OF A MULTIPLE OUTPUT POWER SUPPLY······································· 63
4-9 PARALLEL OPERATION ··············································································· 64
4-10 ZERO-VOLT LOADING APPLICATION ································································ 65
4-11 3341G SERIES ELECTRONIC LOAD OCP, OPP, SHORT OPERATION FLOW······················ 66
CHART········································································································ 66
4-12 POWER SUPPLY OCP TESTING ······································································ 67
4-13 POWER SUPPLY OPP TESTING······································································· 69
4-14 LED DRIVER SHORT TESTING ····································································· 71

Figures
Fig 1-1 3341G 300V/24A/300W power contour·························································· 1
Fig 1-2 3342G 500V/12A/300W power contour·························································· 1
Fig 1-3 3343G 500V/24A/300W power contour·························································· 2
Fig 1-4 Constant Current mode·············································································· 2
Fig 1-5 Constant Resistance mode········································································· 2
Fig 1-6 Constant Voltage mode·············································································· 3
Fig 1-7 Constant Power mode ··············································································· 3
Fig 1-8 LED mode characteristics··········································································· 3
Fig 1-9 Dynamic Wave form·················································································· 4
Fig 1-10 Rise Time Transition Limitation ·································································· 5
Fig 2-1············································································································10
Binding post and withdraw handle on the front panel of 3341G series Plug-in load
module············································································································10
Fig 2-2 Plug-in installation and removal ··································································12
Fig 2-3 3341G series electronic load module load condition setting flow chart··················13
Fig 3-1 Front panel of 3341G plug-in module ···························································14
Fig 3-2 typical connection of 3341G series load module ·············································40
Fig 3-3 3341G Series Electronic Load DIM······························································42
Fig 3-4 An equivalent circuit in terms of the current monitor·········································44
Fig 3-5 (Correct) Connections to an oscilloscope ······················································45
Fig 3-6 (Wrong) Connections to an oscilloscope ·······················································45
Fig 3-7 Analog programming load current in CC mode operation ··································47
Fig 3-8 Hook Terminal Y type large size terminal connections······································50
Fig 4-1 Local voltage sense connections·································································53
Fig 4-2 Remote voltage sense connections ·····························································54
Fig 4-3 constant CURRENT mode application··························································55
Fig 4-4 Dynamic load current with independent programmed Rise/Fall slew rate ··············56
Fig 4-5 Constant Voltage mode application······························································57
Fig 4-6 Constant Resistance mode Application·························································58
Fig 4-7 CONSTANT POWER MODE APPLICATION ·················································59
Fig 4-8 LED’s equivalent circuit and characteristic curve·············································60
Fig 4-9 LED Driver ripple·····················································································60
Fig 4-10 3 LED cascading connection equivalent circuit and characteristic curve··············61
Fig 4-11 Several LED cascading and parallel connection and characteristic curve ············61
Fig 4-12 LED MODE operation mode of the application··············································62
Fig 4-13 Connection between 3341G series plug-in load and multiple output power
supply·············································································································63
Fig 4-14 3341G series plug-in module parallel operation·············································64
Fig 4-15 Zero-Volt loading connection ····································································65
Fig 4-16 3341G series electronic load OCP, OPP, SHORT operation flow chart···············66
Fig 4-17 short test connection ··············································································71
Tables
Table 1-1 3341G Series Specification······································································ 9
Table 3-2 3341G initialize····················································································48
Table 3-3 3342G initialize····················································································48
Table 3-4 3343G initialize····················································································49
Table 3-5 Stranded Copper Wire Ampere Capacity ···················································51

3341G Series Operation Manual 1
Chapter 1 Introduction
1-1. General description
The 3341G series of Electronic Load modules are designed to test and evaluate a wide
range of DC Sources. They are often used in the burn-in and validation of DC power
supplies and the testing of batteries. The 3341G series of electronic load modules are
operated from within a suitable mainframe. The 3300F/3302F/3305F mainframes allow 1, 2
or 4 modules to be operated. The mainframes provide the necessary mains power
conversion along with computer and analogue interfaces. A front panel memory function
is provided. 150 memory locations are available to store the set-up of the load modules
within the mainframe. It is also possible to program and recall a test sequence consisting of
different steps against time. Please refer to the separate 3300F/3302F/3305F operating
manuals for the mainframe functions.
Each load module is capable of sinking a wide range of voltage and current values. The
load modules are limited by the maximum power they can sink. For example the 3341G
can sink up to 24A and 300Vdc at a maximum of 300W. So if the maximum voltage of
300Vdc is present at the load’s input terminals a maximum load current of 0.5A is possible.
Conversely if the 3341G is required to sink 24A the voltage must be limited to 12.5V.
The power contour of 3341G 300 watts Electronic Load is shown in Fig 1-1; it has an input
from 0-24A, and 0-300V current and voltage operating range respectively. The power
contour of 3341G (300V, 24A, 300W), 3342G (500V, 12A, 300W), 3343G (500V, 24A,
300W) Electronic Load are shown in Fig 1-1 ~1-3 respectively.
Fig 1-1 3341G 300V/24A/300W power contour
Fig 1-2 3342G 500V/12A/300W power contour
24A
1A
Current
300V
12.5V
3V
300 W
Power Curve
Voltage
500V
6V
12A
0.6A
300W
Power Curve
Current
Voltage
25V

2 PRODIGIT
Fig 1-3 3343G 500V/24A/300W power contour
The 3341G series of electronic load modules feature 5 operating modes. These are
Constant Current ( CC ) mode, Constant Resistance ( CR ) mode, Constant Voltage ( CV )
mode, Constant Power ( CP ) and( LED) mode.
1.1.1. CC Mode
With the operating mode of Constant Current, the 3341G series electronic load will sink a
current in accordance with the programmed value regardless of the input voltage (see
Fig.1-4).
I
V
CC
LOAD
CURRENT
CURRENT SETTING
INPUT VOLTAGE
Fig 1-4 Constant Current mode
1.1.2. CR Mode:
At Constant Resistance mode, the 3341G series Electronic Load will sink a current linearly
proportional to the load input voltage in accordance with the programmed resistance
setting (see Fig 1-5).
I
V
LOAD
CURRENT
INPUT VOLTAGE
RESISTANCE
SETTING
Fig 1-5 Constant Resistance mode
500V
6V
24A
0.6A
300W
Power Curve
Current
Voltage
12.5V

3341G Series Operation Manual 3
1.1.3. CV Mode:
At Constant Voltage mode, the 3341G series Electronic Load will attempt to sink enough
current until the load input voltage reaches the programmed value (see Fig 1-6).
I
V
LOAD
CURRENT
INPUT VOLTAGE
VOLTAGE
SETTING
Fig 1-6 Constant Voltage mode
1.1.4. CP Mode:
At Constant Power mode, the 3341G series Electronic Load will attempt to sink load power
(load voltage x load current) in accordance with the programmed power. (See Fig 1-7).
Fig 1-7 Constant Power mode
1.1.5. LED Mode
In the LED mode of operation, Voltage is applied to the 3341G series electronic load until
the voltage is greater than Vd load on, Vo = (Io * Rd) + Vd last provided by LED DRIVER
corresponding to a constant current Io Io and Vo Vo for their work to this point shown in
Figure 1-8.
Fig 1-8 LED mode characteristics
Io
I
V
Rd
Vd
Vo
Rd=(Vo-Vd)/Io

4 PRODIGIT
1.1.6. Dynamic Waveform Definition
Along with static operation the 3341G series load modules are built with a Dynamic mode
for operation in Constant Current (CC), Constant Resistance (CR) or Constant Power (CP).
This allows the test engineer to simulate real world pulsing loads or implement a load
profile that varies with time.
A dynamic waveform can be programmed from the front panel of the 3341G series load
module. The user would first set a High and low value of load current using the Level
button. The Dynamic Setting then allows for the rise and fall time between these 2 current
values to be adjusted. The time period that the waveform is high (Thigh) along with the
time period that the waveform is low (Tlow) can also be set.
The dynamic waveform is illustrated below in Fig 1-9.
I
V
LOAD
CURRENT
RISE
SLEW RATE
HIGH LOAD
LOAD
LOW LOAD
LEVEL
T
HIGH
T
LOW
FALL SLEW RATE
Fig 1-9 Dynamic Wave form
The dynamic waveform can also be set up via the optional computer interface. Dynamic
waveform settings made from the front panel of the load module can also be saved in the
memory of the mainframe. For the store/recall procedure and the computer command set
please refer to the relevant operating manual for the 3300F/3302F/3305F mainframes.
Further dynamic waveform definitions are:
The period of dynamic waveform is Thigh + Tlow
The dynamic frequency = 1 /( Thigh + Tlow )
The duty cycle = Thigh / ( Thigh + Tlow )
The analogue programming input also provides a convenient method of implementing a
dynamic waveform. Please see the section 3.1.29 titled ‘Analog Programming Input’ for
further information.
1.1.7. Slew Rate
Slew rate is defined as the change in current or voltage over time. A programmable slew
rate allows for a controlled transition from one load setting to another. It can be used to
minimize induced voltage drops on inductive power wiring, or to control induced transients
on a test device (such as would occur during power supply transient response testing).
In cases where the transition from one setting to another is large, the actual transition time
can be calculated by dividing the voltage or current transition by the slew rate. The actual
transition time is defined as the time required for the input to change from 10% to 90% or
from 90% to 10% of the programmed excursion.
In cases where the transition from one setting to another is small, the small signal

3341G Series Operation Manual 5
bandwidth (of the load) limits the minimum transition time for all programmable slew rates.
Because of this limitation, the actual transition time is longer than the expected time based
on the slew rate, as shown in Figure 1-10
Slew Rate
Expected time
Actual Time
10 %
0 %
100 %
90 %
Voltage (Volts)
Or
Current (Amps)
Slew Rate
Time
mS
Fig 1-10 Rise Time Transition Limitation
Therefore, both minimum transition time and slew rate must be considered when
determining the actual transition time.
Following detail description is exclude in operation manual.
The minimum transition time for a given slew rate as about a 30% or greater load change,
The slew rate increases from the minimum transition time to the Maximum transition time
at a 100% load change. The actual transition time will be either the minimum transition time,
Or the total slew time (transition divided by slew rate), whichever is longer.
Use the following formula to calculate the minimum transition time for a given slew rate
Min transition time=7.2A(24*30%) / slew rate (in amps/second).
72uS (7.2A/0.1) x 0.8(10%~90%) =57.6uS
Use the following formula to calculate the maximum transition time for a given slew rate
Max transition time=24A / slew rate (in amps/second).
240uS (24A/0.1) x 0.8(10~90%) = 192uS
EX. CCH=3A, CCL=0A Slew Rate =0.1A, the expected time is 24uS but the actual
Transition Time will be limited to 57.6uS
30uS( 3/0.1)x 0.8(10%~90%) = 24uS

6 PRODIGIT
1-2. Features
The main features of the 3341G series of load modules are highlighted below.
Bench top and rack mounting flexibility with single, dual and 4 slot mainframes
CC, CR, CV, CP, LED, Dynamic, and Short Operating Mode.
Remote control via a choice of computer interfaces.
High accuracy & resolution with 16 bit voltage and current meter.
Built in pulse generators for dynamic loading.
Independently adjustable current rise and fall times.
Short circuit test with current measurement
Dedicated over current and overpower protection test functions
Programmable voltage on/off capability.
Full protection from overpower, over-temperature, overvoltage, and reverse polarity.
Analogue programming input for tracking an external signal
Current Monitor with BNC (non-isolated) socket.
Digital Calibration
Advance Fan speed control
Ability to save load set-ups via the mainframe memory (150 store/recall locations)
Auto sequence function allowing test routines to be set from the mainframe
1-3. Standard Accessories
a 4mm Banana Plug (Red) 1 PC
b 4mm Banana Plug (Black) 1 PC
c 2mm Banana Plug (Red) 3 PCS
d 2mm Banana Plug (Black) 3 PCS
e ZE090 SNB8-6 Y type terminal 4 PCS
f 3341G series operation manual 1 PC

3341G Series Operation Manual 7
1.3.1 Accessories Installation Description
1-4. Option
a Short Relay BD 1 PC

8 PRODIGIT
1-5. Specifications
MODEL
3341G
3342G
3343G
Power
300W
300W
300W
Current
0 –6A
0 –24A
0 –3A
0 –12A
0-6A
0-24A
Voltage
0~300V
0~500V
0~500V
Min. Operating Voltage
3V @ 24A
6V @12A
6V @ 24A
Constant Current Mode
Range *1
0 –6A
0 –24A
0 –3A
0 –12A
0 –6A
0 –24A
Resolution
0.1mA
0.4mA
0.05mA
0.2mA
0.1mA
0.4mA
Accuracy
±0.1﹪OF(SETTING +RANGE)
Constant Resistance Mode
Range
CRL:0.125Ω~1.5KΩ(150V)
CRH:0.25Ω~3KΩ(300V)
CRL:0.5Ω~1.5KΩ(300V)
CRH:1Ω~3KΩ(500V)
CRL:0.25Ω~3KΩ(300V)
CRH:0.5Ω~6KΩ(500V)
Resolution
133.333uS
66.666uS
33.333uS
16.666uS
66.666uS
33.333uS
Accuracy
±0.2﹪OF (SETTING +RANGE)
Constant Voltage Mode
Range
30V/150V/300V
60V/300V/500V
60V/300V/500V
Resolution
0.0005V/0.0025V/0.005V
0.001V/0.005V/0.01V
0.001V/0.005V/0.01V
Accuracy
±0.05﹪OF (SETTING +RANGE)
Constant Power Mode
Range
0-300W
0-300W
0-300W
Resolution
0.005W
0.005W
0.005W
Accuracy
±0.5﹪OF (SETTING +RANGE)
LED Mode
Vo Voltage Range
LEDL:30V / LEDM:150V / LEDH:300V
LEDL:60V / LEDM:300V / LEDH:500V
LEDL:60V / LEDM:300V / LEDH:500V
Rd Resistance Range
LEDL : 0.125 ~ 125 Ω@ Vo-Vd = 0~3V
LEDL : 1.25 ~ 1.25KΩ@ Vo-Vd = 3~30V
LEDM: 0.625 ~ 625 Ω@ Vo-Vd = 0~15V
LEDM: 6.25 ~ 6.25KΩ@ Vo-Vd = 15~150V
LEDH: 1.25 ~ 1.25KΩ@ Vo-Vd = 0~30V
LEDH: 12.5 ~ 12.5KΩ@ Vo-Vd = 30~300V
LEDL : 0.5 ~ 100Ω@ Vo-Vd = 0~6V
LEDL : 5 ~ 1KΩ@ Vo-Vd = 6~60V
LEDM: 2.5 ~ 500Ω@ Vo-Vd = 0~30V
LEDM: 25 ~ 5KΩ@ Vo-Vd = 30~300V
LEDH: 5 ~ 1KΩ@ Vo-Vd = 0~60V
LEDH: 50 ~ 10KΩ@ Vo-Vd = 60~500V
LEDL : 0.25 ~ 125Ω@ Vo-Vd = 0~6V
LEDL : 2.5 ~ 1.25KΩ@ Vo-Vd = 6~60V
LEDM: 1.25 ~ 625Ω@ Vo-Vd = 0~30V
LEDM: 12.5 ~ 6.25KΩ@ Vo-Vd = 30~300V
LEDH: 2.5 ~ 1.25KΩ@ Vo-Vd = 0~60V
LEDH: 25 ~ 12.5KΩ@ Vo-Vd = 60~500V
Resolution
16Bits
Accuracy
Vd : ±(0.05﹪OF SETTING +0.1% OF RANGE), Rd : ±(0.05﹪OF SETTING +0.1% OF RANGE)
Dynamic Mode
Timing
THIGH &TLOW
0.050~9.999 / 99.99 / 999.9 / 9999mS
Resolution
0.001 / 0.01 / 0.1 / 1mS
Accuracy
1uS/10uS/100uS/1mS + 50ppm
Slew Rate
4.8-300mA/uS
19.2-1200mA/uS
2.4-150mA/uS
9.6-600mA/uS
4.8-300mA/uS
19.2-1200mA/uS
Resolution
1.2mA/uS
4.8mA/uS
0.6mA/uS
2.4mA/uS
1.2mA/uS
4.8mA/uS
Min. Rise Time
20uS(Typical)
20uS(Typical)
20uS(Typical)

3341G Series Operation Manual 9
Current
Range
0 –6A
0 –24A
0 –3A
0 –12A
0 –6A
0 –24A
Resolution
0.1mA
0.4mA
0.05mA
0.2mA
0.1mA
0.4mA
Accuracy
±0.1﹪OF(SETTING +RANGE)
±0.1﹪OF(SETTING +RANGE)
±0.1﹪OF(SETTING +RANGE)
Measturement
Voltage Read Back
Range
30V/150V/300V
60V/300V/500V
60V/300V/500V
Resolution
0.5mV/2.5mV/5mV
1mV/5mV/10mV
1mV/5mV/10mV
Accuracy
±0.025﹪OF (READING + RANGE)
Current Read Back
Range
6A
24A
3A
12A
6A
24A
Resolution
0.1mA
0.4mA
0.05mA
0.2mA
0.1mA
0.4mA
Accuracy
±0.1﹪OF (READING + RANGE)
Power Read Back
Range
300W
300W
300W
Accuracy *2
±0.1﹪OF (READING + RANGE)
Gernaral
Imonitor
2.4A/V
1.2A/V
2.4A/V
Short Signal Output
12V/100 mAmax
12V/100 mAmax
12V/100 mAmax
Dimming Control
Level Range
0~12V
Resolution
0.048V
Accuracy
1% of (SETTING + RANGE)
Frequency Range
DC~1KHz
Resolution
10Hz
Duty Range
0.01~0.99(1%~99%)
Resolution
0.01
Temperature Coefficient
100ppm/℃(typical)
Power
Supply from mainframe
Operating Temperature *3
0~40℃
Dimension(HxWxD)
143x108x405mm
Weight
3.5Kg
3.5Kg
3.5Kg
Safety & EMC
CE
Note *1 : The range is automatically or forcing to range II only in CC mode
Note *2 : Power F.S. = Vrange F.S. x Irange F.S.
Note *3 : Operating temperature range is 0~40℃, All specifications apply for 25℃± 5℃, Except as noted
Table 1-1 3341G Series Specification

10 PRODIGIT
Chapter 2 Installation
This chapter details the installation and removal procedure of the 3341G series load module when
used in conjunction with the 3300F (quad module mainframe). The same procedure is used for the
3302F (single module mainframe) and the 3305F (dual module mainframe).
Please note that the 3341G series load module does not need any user adjustment after it has been
plugged in to the mainframe.
Fig 2-1
Binding post and withdraw handle on the front panel of 3341G series Plug-in load module

3341G Series Operation Manual 11
2-1. Installation and Removal of 3341G series plug in module
The 3341G series Electronic load module operates from within the 3300F/3302F/3305F
mainframe. The mainframe is required to provide power to the module’s control circuitry. It is
also needed for the computer interfaces, analogue programming input and the 150 store/recall
memory.
Unless the 3300F/3302F/3305F mainframe and 3341G series Electronic load module were
purchased separately, the 3341G series Electronic load module should be installed in the
3300F mainframe before shipment from Prodigit.
One of the benefits of the modular approach is that different models of load module can be
operated from within the same mainframe. It is easy for the user to reconfigure the mainframes
by changing or adding different load modules.
The following procedure should be followed for installing or removing the 3341G series load
module in or out from the 3300F /3302F/3305F.
2.1.1. Installation of 3341G series plug-in load:
2.1.1.1 Turn the 3300F/3302F/3305F mainframe power OFF before inserting the
3341G series load module. Failure to switch the mains power off may
Result in Damage to the plug-in module’s circuitry.
2.1.1.2 Align the upper and lower grooves of the 3300F mainframe with the
upper and Lower guides of the selected compartment.
2.1.1.3 If correctly positioned the 3341G series load module will slide in easily
Until some 30-40mm is left protruding from the mainframe. At this point a
Little more Force will be required to seat the load module’s circuit board
In the Interconnecting jack of the mainframe. It is recommended that the
binding posts on the load module’s front panel be used to push the
Module home.
2.1.1.4 Use the supplied screw to fasten the load module to the mainframe. The
Screw hole is located at the end of the pull out handle at the bottom right
hand Corner of the 3341G load module. The screw location is shown on
Fig 2-1 and Is below and to the right of the LOAD + binding post.
2.1.1.5 Only after all the load modules are installed to the 3300F/3302F/3305F
Mainframe should the mains power be switched ON.
2.1.2. Removal of 3341G series plug-in load:
2.1.2.1. Firstly ensure that the mains power to the 3300F/3302F/3305F
mainframe is
Switched off. Failure to do so may result in damage to the load module.
2.1.2.2. Take the screw out of the pull out handle in the lower right corner of the
Module.
2.1.2.3. After removal of the screw the handle can be pulled towards you to lever
The module out of the mainframe.

12 PRODIGIT
Fig 2-2 Plug-in installation and removal
2-2. Environmental requirements
Indoor use.
Measurement Category I.
Pollution Degree 2.
Relative Humidity 80% Max.
Ambient Temperature 0 to +40°C
Altitude up to 2000m.
The equipment is not for measurements performed for CAT II, III and IV.
Transient Overvoltage on the mains supply can be 2500V.
2-3. Observe the International Electrical Symbol listed below.
Warning!Risk of electric shock
Caution!Refer to this manual before using the load.
2-4. Cleaning
2-5. Power Up
The following procedure should be followed before applying mains power:
2.5.1 Check that the POWER switch is in the off (O) position
2.5.2 Check the rear panel voltage selector of the 3300F/3302F/33305F mainframe is
Correctly set.
2.5.3 Check that nothing is connected to the DC INPUT (load input terminals) on the
Front panel of the 3341G load module.
2.5.4 Connect correct AC mains lead to the 3300F/3302F/33305F mainframe
2.5.5 Turn on (I) the POWER switch.
To clean this product, use a soft or wet cloth.
Before you clean this product, power this product off and disconnect the power plug.
・Please do Not use any organic solvent capable of changing the nature of the plastic
such as benzene or acetone.
・Please pay attention that any liquid should not be penetrated into this product.

3341G Series Operation Manual 13
2-6. Operating flow chart for each load module operation
The following flow chart shows the typical load current level and status setting procedures
of each load module within 3300F mainframe, the load channel number 1 to 4 is from left to
right compartment on 3300F mainframe respectively, please skip Channel setting if single
load mainframe 3302F is used.
The string between "____" in the flow chart is a RS-232C or GPIB programming
commends.
Please follow the flow chart sequence to have proper and effective load settings.
The load mode (CC, CR, CV, CP or LED) should be set first, where only Static mode is
available for CR and CV mode, both Static and Dynamic modes are available for CC and
CP mode, then choose high or Low load level and programming the load level for Static
mode, or programming the six parameters for Dynamic mode.
The Limit key set the GO/NG check upper and lower limit for DVM, DAM, and DWM
respectively, the system configure setting of V-sense control, Load ON voltage, and load
OFF voltage is within the Limit key setting.
Others key (Load ON/OFF, Short ON/OFF) can be controlled independently.
Fig 2-3 3341G series electronic load module load condition setting flow chart
START
CHAN 1
CHAN 2
CHAN 3
CHAN 4
SET CHAN1
SET CHAN2
SET CHAN3
SET CHAN4
CC MODE?
CR MODE?
CV MODE?
CP MODE?
SET MODE CC
SET MODE CR
SET MODE CV
SET MODE CP
STA OR DYN?
SET DYN OFF
LIMIT
SET DYN ON
CURR:HIGH NR2
CURR:LOW NR2
RISE:NR2
FALL NR2
PERD:HIGH NR2
PERD:LOW NR2
HIGH OR LOW
LEVEL?
SET LEV
HIGH
SET LEV
LOW
HIGH OR LOW
LEVEL?
SET LEV
HIGH
SET LEV
LOW
HIGH OR LOW
LEVEL?
SET LEV
HIGH
SET LEV
LOW
SET
Voltage Hi/Lo LIMIT
Current HI/Lo LIMIT
Power Hi/Lo LIMIT
Sense Auto/ON
Vd-on
Vd-off
STA OR DYN?
SET DYN OFF
SET DYN ON
CURR:HIGH NR2
CURR:LOW NR2
RISE:NR2
FALL NR2
PERD:HIGH NR2
PERD:LOW NR2
HIGH OR LOW
LEVEL?
SET LEV
HIGH
SET LEV
LOW
DYN
STA
LOW
LOW
LOW
DYN
STA
LOW
YES
NO
NO
NO
NO
NO
YES
YES
YES
YES
NO
NO
NO
NO
YES
YES
YES
YES
HIGH
HIGH
HIGH
HIGH
LED MODE?
NO
SET MODE LED
YES
SET LED No
SET Vo
SET Vd
SET Rd or Io

14 PRODIGIT
Chapter 3 Operation
This chapter describes the front panel operation of each 3341G series load module. Please note
that the memory store/recall function and the GPIB/RS-232C/USB/LAN remote programming terms
are detailed in the separate 3300F/3302F/3305F mainframe operation manual.
3-1 Front panel description
The following sketch shows the layout of the front panel of the unit. Please refer to the relevant
Section as indicated by the number assigned to a front panel function.
For example to understand more about the Imonitor function labeled 26 please refer to 3.1.26
Fig 3-1 Front panel of 3341G plug-in module
This manual suits for next models
2
Table of contents
Popular Control Unit manuals by other brands

Pepperl+Fuchs
Pepperl+Fuchs VAA-2E-G4-SN instruction manual
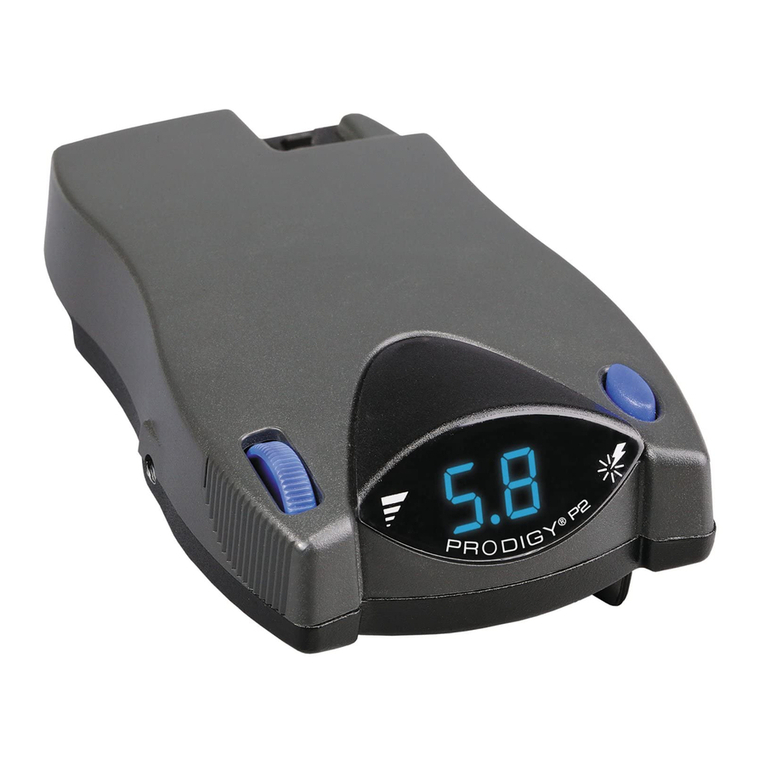
Prodigy
Prodigy P2 user manual
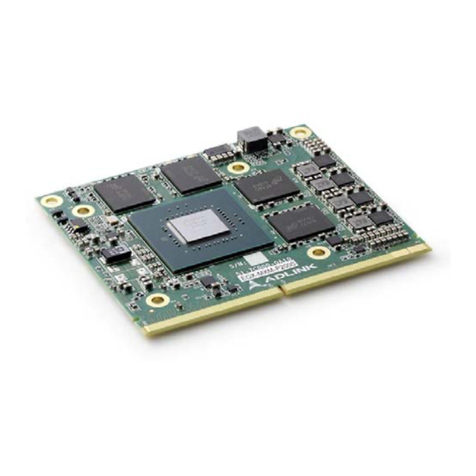
ADLINK Technology
ADLINK Technology EGX-MXM-P2000 user manual
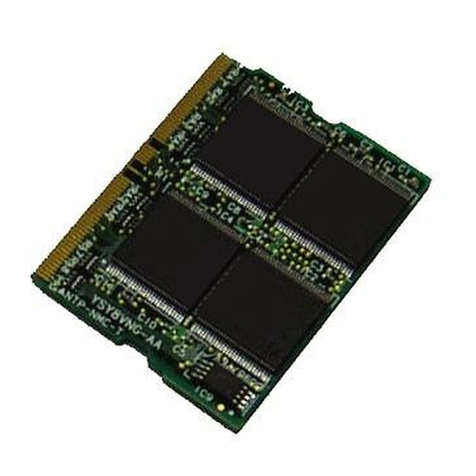
Panasonic
Panasonic CF-BAP0128U operating instructions
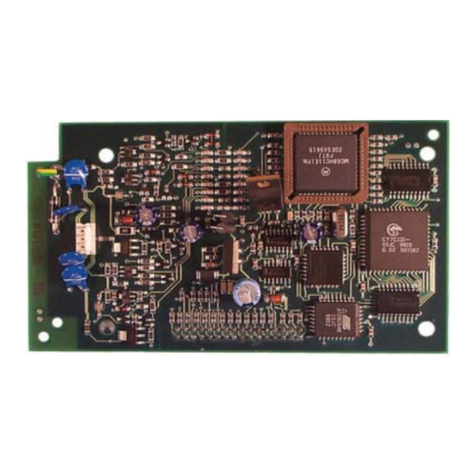
Bosch
Bosch D7039 installation guide

WEG
WEG CFW500 Series Installation, configuration and operations guide

Bandini Industrie
Bandini Industrie GiBiDi BA100 Instructions for installations
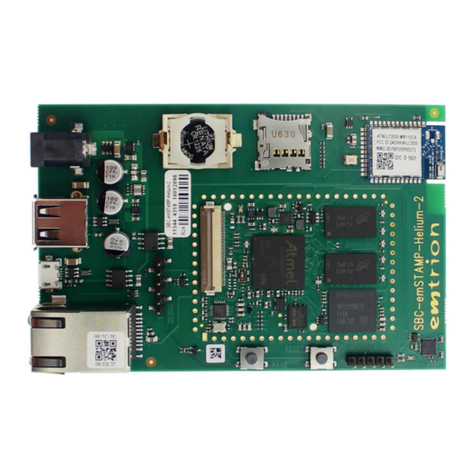
EMTRION
EMTRION emSTAMP Helium Hardware manual
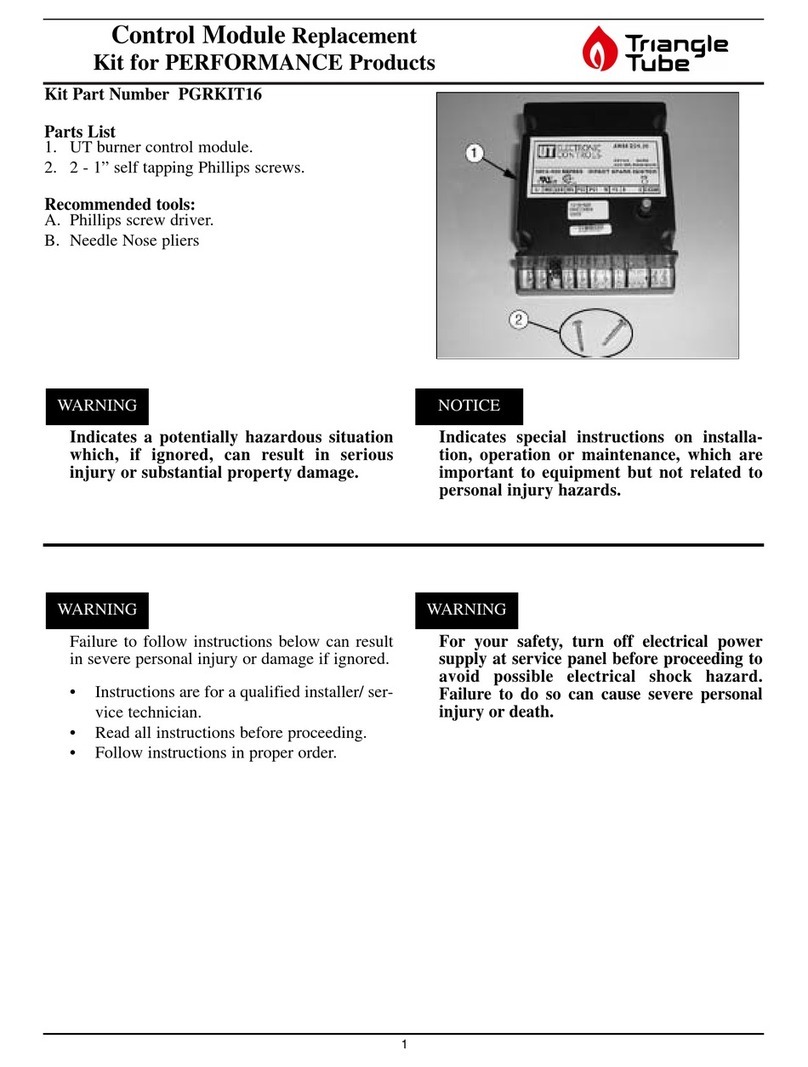
TriangleTube
TriangleTube PGRKIT16 quick guide
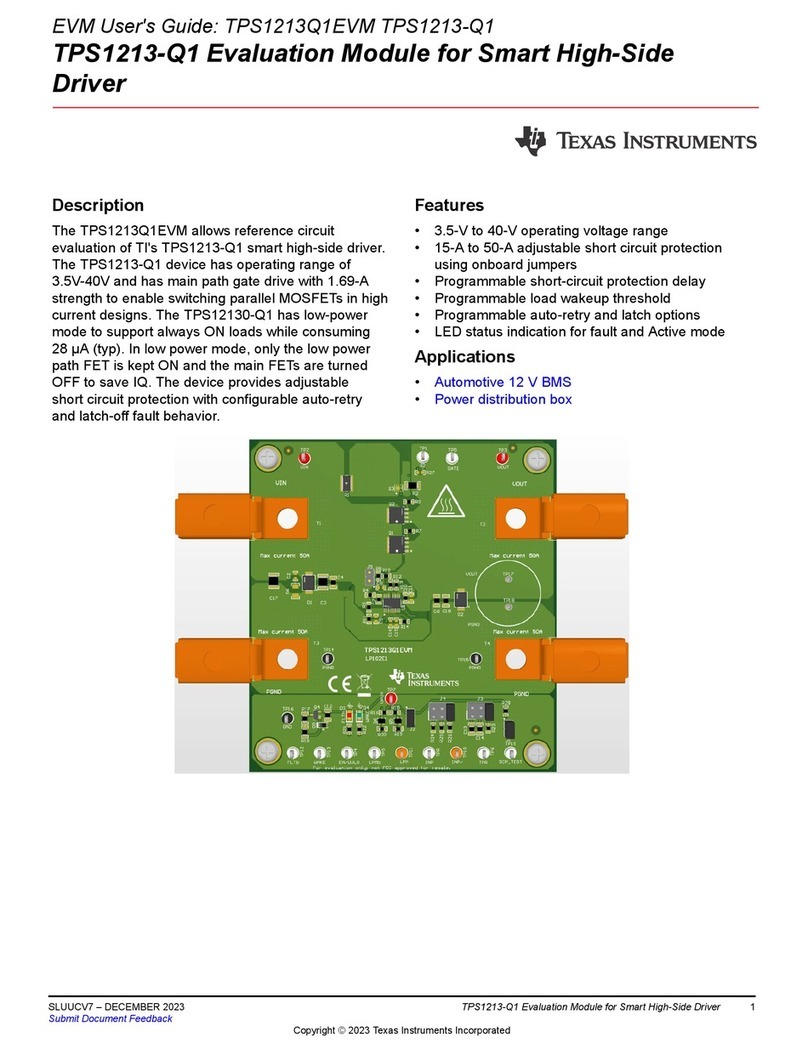
Texas Instruments
Texas Instruments TPS1213Q1EVM user guide
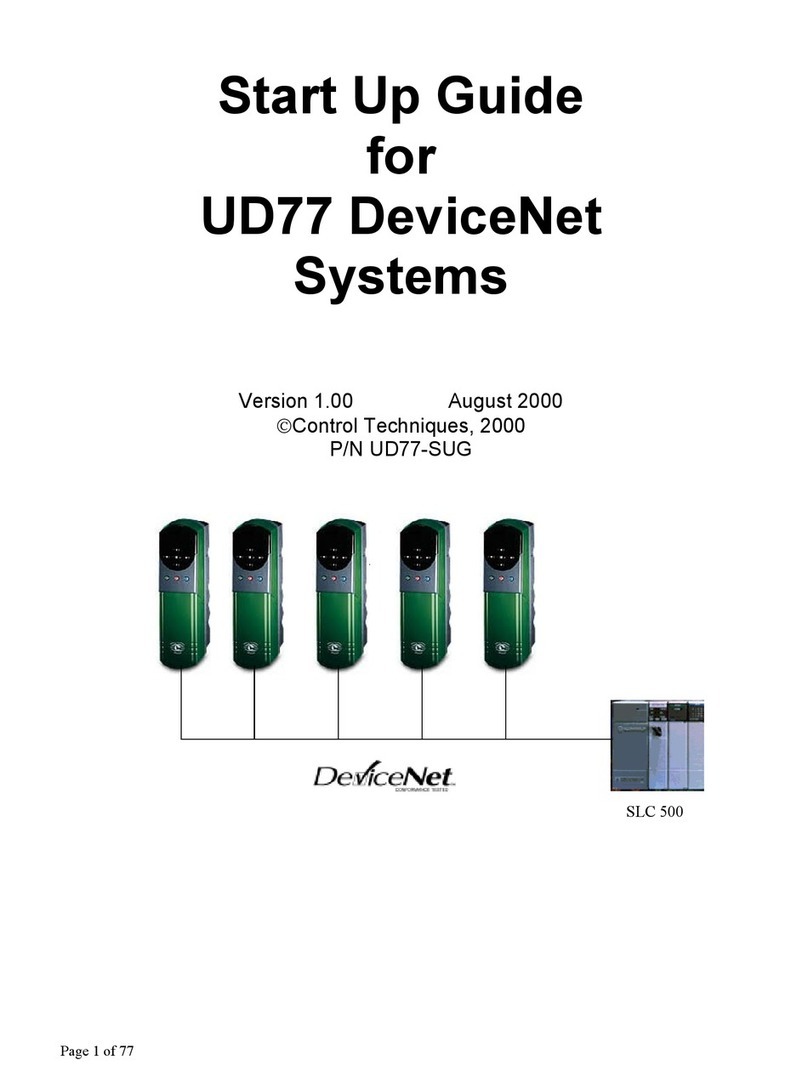
Control Techniques
Control Techniques UD77 DeviceNet Startup guide
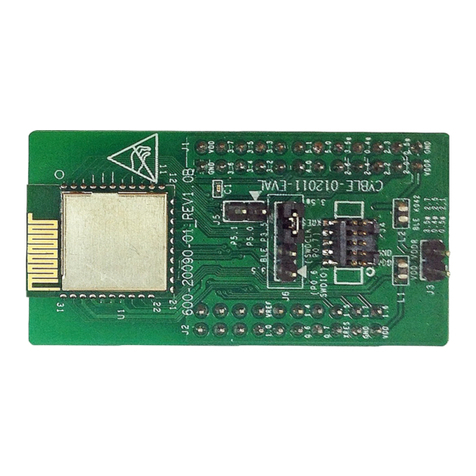
Cypress
Cypress EZ-BLE PRoC CYBLE-012011-00 manual