Quantum QXS Series Operating manual

QXS-5 Hardware Installation and Maintenance Guide
6-69090-01,Rev. A

QXS-5 Hardware Installation and Maintenance Guide i
QXS-5 Hardware Installation and Maintenance Guide, 6-69090-01, Rev. A, September, 2023, Product of USA.
Quantum Corporation provides this publication “as is” without warranty of any kind, either express or implied,
including but not limited to the implied warranties of merchantability or fitness for a particular purpose. Quantum
Corporation may revise this publication from time to time without notice.
COPYRIGHT STATEMENT
© 2023 Quantum Corporation. All rights reserved. Your right to copy this manual is limited by copyright law. Making copies or
adaptations without prior written authorization of Quantum Corporation is prohibited by law and constitutes a punishable
violation of the law. ActiveScale, DXi, DXi Accent, FlexSync, FlexTier, iLayer, Lattus, Quantum, The Quantum Logo, QXS,
Scalar, StorNext, SuperLoader, Vision, and Xcellis are either registered trademarks or trademarks of Quantum Corporation and
its affiliates in the United States and/or other countries. All other trademarks are the property of their respective owners.
Quantum specifications are subject to change.

Contents ii
Contents
1 Introduction 1
Knowledge prerequisites 1
Intended audience 1
2 System overview 2
Storage enclosure components 2
Storage enclosure chassis 3
2U enclosure components 3
5U enclosure components 5
Controller module components 8
Optional components 9
3 Initial install preparations 10
Installation checklist 10
Complete installation prerequisites 11
4 Installation of 2U enclosures 13
Unpack and prepare the 2U enclosure 13
Install the 2U rackmount rail kit 14
Mount the 2U enclosure into the rack cabinet 18
Populate the 2U enclosure 20
Test enclosure electrical earth connection 21
Route 2U enclosure data cables and power cords 21
Route 2U enclosure host cables and expansion data cables 22
Route 2U enclosure power cords 25
5 Installation of 5U enclosures 27
Unpack and prepare the 5U enclosure 27
Install the 5U rackmount rail kit 28
Mount the 5U enclosure into the rack cabinet 31
Access a drawer 35
Populate the 5U enclosure 36
Test enclosure electrical earth connection 37
Route 5U enclosure data cables and power cords 37
Route 5U enclosure host cables and expansion data cables 38
Route 5U enclosure power cords 40
6 Operation of 2U enclosures 42
Apply power to the 2U enclosure 42
Remove power from the 2U enclosure 43
Interpret system LEDs 43

Interpret 2U12 and 2U24 operator's panel LEDs 44
Interpret controller module LEDs 45
Interpret SAS 12Gb/s expansion input/output module LEDs 46
7 Operation of 5U enclosures 48
Apply power to the 5U enclosure 48
Remove power from the 5U enclosure 50
Interpret system LEDs 50
Interpret 5U enclosure operator's panel LEDs 50
Interpret drawer LED panels 51
Interpret controller module LEDs 52
Interpret SAS 12Gb/s expansion input/output module LEDs 54
8 Storage enclosure management 56
Command-line interface usage 56
Install a device driver 57
Configure the management host for serial communication 57
Connect to a controller module for configuration 60
Disk Storage Management Utility usage 62
Access the web-based management interface 62
Complete the preboard and onboard process 63
Storage volume replication 63
Co-located replication configurations 64
Remote replication configurations 66
Set up storage volume replication 67
9 Hardware installation and configuration issues 68
Address initial start-up issues 68
Interpret storage and expansion enclosure fault LEDs 69
2U12 and 2U24 enclosure fault LEDs 69
5U84 enclosure fault LEDs 74
Identify 2U enclosure fault conditions 79
Identify 5U enclosure fault conditions 80
Isolate hardware and connectivity faults 81
Isolate replication faults 82
Isolate system application faults 84
Take corrective action for 2U enclosures 84
Take corrective action for 5U enclosures 86
10 In-service field maintenance for 2Uenclosures 90
Replace a 2U enclosure drive module in its carrier 91
Replace a 2U enclosure controller module 93
Replace a 2U power cooling module 95
iiiContents

Contents iv
11 In-service field maintenance for 5Uenclosures 100
Replace a 5U enclosure drive module in its carrier 101
Replace a 5U enclosure controller module 105
Replace a 5U fan cooling module 108
Replace a 5U power supply unit 110
A Technical specifications 113
B Standards and regulations 115
International standards 115
WEEE recycling 115
Index 117
D Contacting Quantum 119
Contacts 119
Comments 119

Contents v
Figures
Figure 1 2U12 and 2U24 front panel area 4
Figure 2 2U12 and 2U24 rear panel area 5
Figure 3 5U84 front panel area 6
Figure 4 5U84 rear panel area 7
Figure 5 Profile and top views of fully populated 5U84 drawers 8
Figure 6 Controller module ports, sample SAS 4-port 9
Figure 7 2U12 and 2U24 storage enclosure packaging, shown without plastic for clarity 14
Figure 8 2U enclosure outer rail components 15
Figure 9 Attachment of front mount bracket to front rack cabinet posts 16
Figure 10 Adjustment of rail length to fit rack cabinet 17
Figure 11 Attachment of rear mount bracket to rear rack cabinet posts 17
Figure 12 Alignment between 2U chassis and rails (removed rear components for clarity) 19
Figure 13 Installation of 2U rear screw to secure chassis to rail 20
Figure 14 Installation of 2U operator's panel screw and cover 20
Figure 15 Sample data and management cabling among 2U controllers and host system
switches 23
Figure 16 Sample reverse cabling method among 2U controller modules (CMs) and expansion
modules 24
Figure 17 Sample invalid loop (in red) among 2U controller modules (CMs) and expansion
modules 24
Figure 18 2U power cord routing to independent power distribution units 25
Figure 19 2U power cord surrounded by secure tie 26
Figure 20 Default belt straps already around the 5U storage enclosure 27
Figure 21 5U left and right rail components 29
Figure 22 Insertion of 5U front mount bracket screw 30
Figure 23 Insertion of 5U rear mount bracket screws 31
Figure 24 Alignment between 5U chassis and rails, minus rear components for clarity 33
Figure 25 Secure chassis operator's panel to rack posts 34
Figure 26 5U rear chassis connection to outer rails, detail, minus rear components for clarity 34
Figure 27 Safety lock to release left drawer slide rail (lower drawer used for relational clarity) 35
Figure 28 Carrier latch features 36
Figure 29 Release latch open and unlocked 37
Figure 30 Release latch properly locked 37
Figure 31 Sample data and management cabling among 5U controllers and host system
switches 39
Figure 32 Sample reverse cabling method among 5U controller modules (CMs) and expansion
modules 40
Figure 33 Sample invalid loop (in red) among 5U controller modules (CMs) and expansion
modules 40

Figure 34 5U power cord routing to independent power distribution units 41
Figure 35 Route power cords to redundant PDUs 43
Figure 36 2U12 and 2U24 operator's panel LEDs 44
Figure 37 Controller module LEDs applicable to all variations 45
Figure 38 Port LEDs for SAS, fibre channel, iSCSI, and 10GBase-T iSCSI controller modules 46
Figure 39 SAS 12Gb/s expansion input/output module LEDs 47
Figure 40 Route 5U power cords to redundant PDUs 49
Figure 41 Route 5U power cords to redundant PDUs 49
Figure 42 5U84 operator's panel LEDs 51
Figure 43 5U84 drawer LED panel 52
Figure 44 Controller module LEDs applicable to all variations 53
Figure 45 Port LEDs for SAS, fibre channel, iSCSI, and 10GBase-T iSCSI controller modules 54
Figure 46 SAS 12Gb/s expansion input/output module LEDs 55
Figure 47 USB ports on sample SAS 4-port controller module 57
Figure 48 Sample of three switches for co-located controller enclosures, multiple host servers 65
Figure 49 Sample of single switch for co-located controller enclosures, single host server 66
Figure 50 Sample of two remote sites, each with a controller enclosure, switch, and its own host
server 67
Figure 51 2U12 and 2U24 operator's panel fault LEDs 69
Figure 52 2U12 and 2U24 fault LEDs on carrier bezel 70
Figure 53 Controller module fault LEDs 71
Figure 54 SAS 12Gb/s expansion module fault LEDs 72
Figure 55 Power cooling module fault LEDs 73
Figure 56 Power cooling module fault LEDs 74
Figure 57 5U84 operator's panel fault LEDs 75
Figure 58 5U84 drawer fault LEDs on drawer LED panel 76
Figure 59 Drive fault LED on carrier bezel 76
Figure 60 Controller module fault LEDs 77
Figure 61 SAS 12GB expansion module fault LEDs 78
Figure 62 Fan cooling module fault LEDs 78
Figure 63 Power supply unit fault LEDs 79
Figure 64 2U12 and 2U24 fault LEDs on carrier bezel 91
Figure 65 Removal of 2U12 and 2U24 drive in carrier 92
Figure 66 Replacement with open 2U12 and 2U24 carrier handle 93
Figure 67 Controller module LEDs to examine for fault conditions (SAS 4-port version) 94
Figure 68 Controller module removal, upper (SAS 4-port version) 94
Figure 69 Replacement controller module (SAS 4-port version) 95
Figure 70 Power cooling module fault LEDs 96
Figure 71 Power cooling module removal 98
Figure 72 Replacement power cooling module 98
viContents

Contents vii
Figure 73 Drive fault LED on carrier bezel 101
Figure 74 Operator's panel 102
Figure 75 Drawer panel 102
Figure 76 Drawer release and access 102
Figure 77 Carrier latch features 103
Figure 78 Removal of drive in its carrier 103
Figure 79 Replacement of drive in its carrier 104
Figure 80 Release latch open and unlocked 104
Figure 81 Release latch properly locked 104
Figure 82 Safety lock to release left drawer slide rail of lower drawer 105
Figure 83 Controller module LEDs to examine for fault conditions 106
Figure 84 Controller module removal, left (SAS 4-port version) 107
Figure 85 Replacement controller module (SAS 4-port version) 107
Figure 86 Fan cooling module fault LEDs 108
Figure 87 Fan cooling module removal 109
Figure 88 Replacement fan cooling module 109
Figure 89 Power supply unit fault LEDs 110
Figure 90 Power supply unit removal 111
Figure 91 Replacement power supply unit 112

Tables
Table 1 Storage enclosure variations 2
Table 2 Installation checklist tasks 10
Table 3 Fault LED prioritization 44
Table 4 Fault LED prioritization 50
Table 5 Methods of access to controller module 56
Table 6 Interface options 56
Table 7 Supported terminal emulator applications 58
Table 8 Terminal emulator serial port hex codes 58
Table 9 Sample Linux Minicom serial port parameter settings 59
Table 10 Terminal emulator port connection settings 59
Table 11 Factory default network port IP addresses 60
Table 12 Supported browsers 62
Table 13 2U enclosure non-fault conditions 80
Table 14 5U enclosure non-fault conditions 81
Table 15 2U enclosure corrective action for fault conditions 85
Table 16 5U enclosure corrective action for fault conditions 86
Table 17 2U enclosure time limits for FRU replacement 90
Table 18 5U enclosure time limits for FRU replacement 100
Table 19 Storage enclosure dimensions 113
Table 20 Storage enclosure FRU weights 113
Table 21 Environmental specifications 113
Table 22 Power specifications 114
Table 23 Standard and approvals 115
viiiContents

Chapter 1 Introduction 1
1 Introduction
Quantum QXS storage enclosures combine strong performance with high reliability, flexibility, and
manageability. Powerful and compact, the LX2 series expandable storage solution supports business with
high-capacity and high-availability options.
The system is designed for high availability (HA), with no single point of failure for data or power. Controller
modules (CMs) are Storage Bridge Bay (SBB) v2.1 compatible for interconnects, power budgets and rails,
form factors, and footprints.
All Quantum storage enclosures contain one or more CMs, which each contain a Hewitt Lake processor, 16GB
of cache, and a custom RAID acceleration ASIC.
WARNING! Heed all warnings and cautions on labeling and throughout this guide to reduce risk of
personal injury or damage to equipment. You must adhere to all safety requirements in this document. Some
relate to the entire system, some to the rack, some to the storage enclosure, and others to the FRUs within it.
Knowledge prerequisites
Make sure you have the appropriate knowledge base prior to product installation or service.
lServer system administration
lStorage system configuration
lStorage area network (SAN) management
lEthernet protocol
lRAID technology
lRedfish Management protocol
Intended audience
This guide is for software integration providers, storage installation professionals, and system administration
personnel.

2Chapter 2 System overview
2 System overview
The Quantum QXS storage series enclosures consist of a sheet metal chassis that contains an integrated
midplane and module runner system. You can mount the storage enclosure into a standard 19-inch rack
cabinet, occupying either two (2U) or five (5U) EIA rack space units. All plug-in modules are hot-swappable,
but you must adhere to all safety precautions and time limitations.
Type Typical set of plug-in modules Maximum expansions
2U12 storage enclosure 2U chassis and rackmount railkit Up to 9
12 3.5-inch large form factor (LFF) drive modules in carriers (DDICs)
Two controller modules (CMs)
Two power cooling modules (PCMs)
2U24 storage enclosure 2U chassis and rackmount railkit Up to 9
24 2.5-inch small form factor (SFF) DDICs
Two controller modules (CMs)
Two power cooling modules (PCMs)
5U84 storage enclosure 5U chassis and rackmount railkit:
Contains two drawers, each with 42 drive modules
Up to 3
84 3.5-inch or 2.5-inch drive modules with adapters in carriers
Two controller modules (CMs)
Five fan cooling modules (FCMs)
Two power supply units (PSUs)
Four sideplane printed circuit boards (PCBs), two per drawer
Authorized service personnel only
Table 1 Storage enclosure variations
You can use the 2U or 5U chassis as a controller storage enclosure when configured with controller modules,
or as an expansion enclosure when configured with input/output modules.
CAUTION Make sure you are not connected to power at any time during installation procedures.
CAUTION Only operate the storage enclosure in a dust-free environment to meet temperature control
and airflow requirements.
For optimum function, use the high availability (HA) model that requires dual paths for data and power to
increase fault tolerance and minimize single points of failure. This manual assumes HA model system
integration using a minimum of one fully populated storage enclosure.
Storage enclosure components
All Quantum QXS storage enclosures have 2 main access points:
1. Front panel area — Contains the operator's (ops) panel and access to drive modules in their carriers
(DDICs)

Chapter 2 System overview 3
a. 2U enclosures — Direct access to DDICs
b. 5U enclosures — Access to DDICs by opening the related drawer
2. Rear panel area — Contains controller modules and methods for cooling and powering the storage
enclosure
Storage enclosure chassis
Chassis sheet metal is bonded and riveted together and free from non-conductive coatings. Each chassis is
designed specifically for mounting in a rack cabinet.
2U enclosure components
The front panel area hosts an operator's panel and the drive modules.
l2U12— Contains 3.5-inch large form factor (LFF) drives installed in keyed carriers, inserted into horizontal
slots, and logically numbered in rows from 0 to 11 from left to right, from top to bottom
l2U24— Contains 2.5-inch small form factor (SFF) drives installed in keyed carriers, inserted into vertical
slots, and logically numbered from 0 to 23 from left to right

4Chapter 2 System overview
1234 5
678910
1234 5
678910
Item Description Function
1 Input button Selects and sets UID when combined with system Locate command
2 Drive 0 Responds to commands for drive logically numbered "0"
3 Release latch, drive module Allows drive module insertion onto and removal from the midplane and
slot
4 Anti-tamper lock, drive module Prevents drive module removal when locked
5 Drive 3 Responds to commands for drive logically numbered "3"
6 Operator's (ops) panel on left rack ear
flange
Connects to midplane, provides users with storage enclosure information
and status
7 Drive 8 Responds to commands for drive logically numbered "8"
8 Status LEDs, drive module Provides users with drive module status
9 Drive 11 Responds to commands for drive logically numbered "11"
10 Right rack ear cover Acts as cosmetic cover over rack flange
Figure 1 2U12 and 2U24 front panel area

Chapter 2 System overview 5
The rear panel area hosts modules designed for power, thermal cooling, and host connectivity.
12Gb/s
12Gb/s
123
46
5
Item Description Function
1 Power cooling module (PCM) Provides redundant regulation of power, temperature, and airflow
2 PCM release latch Latches or unlatches PCM from midplane
3 Controller module (CM) Provides data redundancy, acts as the nerve center of the storage enclosure
4 Inverted CM
5 Inverted PCM status LEDs Provides users with PCM status
6 Inverted PCM power switch Switches power on or off
Figure 2 2U12 and 2U24 rear panel area
5U enclosure components
The 5U84 chassis retains two sliding drawers, so has drawer panels that augment the operator's (ops) panel
on the left rack ear flange. Each drawer has its own set of dedicated connectors behind the midplane that allow
continuous operation, even if the drawer is extended to the fully open service position or closed with the
drawer latch engaged.
The front panel area is the primary physical user interface. Closely watch the ops and drawer panels for status.

6Chapter 2 System overview
1234 5
678910
Item Description Function
1 Operator's (ops) panel Connects to midplane, provides users with storage enclosure information and
status
2 Drawer left sideplane
indicators
Registers activity for the related drive in its carrier (DDIC) and controller for the
drawer's left sideplane
3 Left pull handle in recessed
pocket
Provides user access to DDICs contained in drawer
4 Drawer left side anti-tamper
lock
Prevents drawer access when locked
5 Top drawer: Drawer 1 Contains DDIC slots logically numbered from 0 to 41
6 Bottom drawer: Drawer 2 Contains DDICslots logically numbered from 42 to 83
7 Drawer right side anti-tamper
lock
Prevents drawer access when locked
8 Right pull handle in recessed
pocket
Provides user access to DDICs within the drawer
9 Drawer right sideplane
indicators
Registers activity for the related DDIC and controller for the drawer's right
sideplane
10 Drawer latch Latches the drawer closed when properly engaged
Figure 3 5U84 front panel area

Chapter 2 System overview 7
The rear panel area provides you access to modules designed for power, thermal cooling, and host
connectivity.
12Gb/s
12Gb/s
1 2 3 4 5
6 7 8 9 10
Item Description Function
1 Controller module (CM) Provides data redundancy and is the nerve center of the storage enclosure
2 CM release latch Provides full contact with midplane or releases CM for inspection and service
3 CM release latch and handle
4 Fan cooling module (FCM) Provides redundant regulation of temperature and airflow
5 FCM release latch Provides full contact with midplane or releases FCM for inspection and service
6 FCM pull handle
7 Power supply unit (PSU) Provides redundant regulation of power
8 PSU release latch Provides full contact with midplane or releases PSU for inspection and service
9 PSU pull handle
10 PSU power switch Powers on or off the storage enclosure
Figure 4 5U84 rear panel area
Two sliding drawers hold DDICs and their related sideplanes.
lTwo drawers each can contain 42 DDICs. Drawer slides lock the drawer in the fully open service position,
so require release latch activation to close the drawer.
lDDICs slide into 42 slots in each drawer. The upper drawer, Drawer 1, contains slots logically numbered
from 0 to 41 in rows moving from top to bottom, then from left to right. The lower drawer, Drawer 2, contains
slots logically numbered from 42 to 83, following the same pattern.

8Chapter 2 System overview
1 2 3 4 5 6 78 9 10
11 12 13 14
Item Description Function
1 Drawer front with keyed anti-tamper lock
and 2 drawer latches
Prevents or provides access to DDICs, contains dual drawer panel
LEDs for drive activity and fault status
2 Right sideplane Registers DDIC activity and fault conditions for the primary host path
3 Drawer latch for top drawer: Drawer 1 Locks drawer open to access slots logically numbered from 0 to 41
4 Operator's (ops) panel on left rack ear
flange
Connects to midplane, provides users with storage enclosure
information and status
5 Bottom drawer: Drawer 2 Contains slots logically numbered from 42 to 83
6 Drawer slide Supports full extension to service position and access to DDICs
7 Midplane Connects modules to system controls (
Authorized service personnel
only
)
8 Controller module (CM) Provides data redundancy and acts as the nerve center of the storage
enclosure
9 Fan cooling module (FCM) Provides redundant regulation of temperature and airflow
10 Power supply unit (PSU) Provides redundant regulation of power
11 Drive module in its carrier (DDIC) Provides redundant data storage
12 Locking mechanism Secures full connection of DDIC
13 Right rack ear cover Cosmetic
14 Cable management system Protects cabling associated with the related drawer
Figure 5 Profile and top views of fully populated 5U84 drawers
Controller module components
Both controller modules (CMs) manage the flow of data to and from the storage enclosure. Each CM provides
a very specialized, solutions-specific interaction that depends on your system configuration and software
implementation, including RAIDfunctions, management functions, failover and failback procedures, and
multipath procedures.

Chapter 2 System overview 9
The CM has a number of ports and any related LEDs. See "Interpret controller module LEDs" on page52.
12Gb/s
= SAS 4-port
12Gb/s
12345
Item Description Function
1 SAS 12Gb/s ports Serial Attached SCSI (SAS) 12Gb/s data exchange with host computer
2 Mfg USB port Manufacturing Universal Serial Bus (USB) port: do not use
3 CLI USB port Serial command line interface port used to manage the system
4 Ethernet port Ethernet connection to host system
5 SAS expansion port SAS expansion 12Gb/s data exchange with other expansion enclosures
Figure 6 Controller module ports, sample SAS 4-port
Optional components
Occasionally, you may configure the storage enclosure to operate without all of its components. The most
common reason is to perform in-field maintenance. Temperature and airflow requirements for 2U enclosures
mandate you immediately use blanks to replace modules you remove and adhere to all specified time
limitations for replacement.
lCarrier blank— For 2U enclosures not fully populated, occupies any empty drive slot to secure proper airflow
lController blank— For 2U enclosures configured with a single controller, occupies the empty controller slot
to secure proper airflow

10Chapter 3 Initial install preparations
3 Initial install preparations
Each storage enclosure installation requires the same amount of preparation to successfully mount it into your
industry-standard rack cabinet of up to 1.2m in depth.
WARNING! Heed all warnings and cautions on labeling and throughout this guide to reduce risk of
personal injury or damage to equipment. You must adhere to all safety requirements in this document. Some
relate to the entire system, some to the rack, some to the storage enclosure, and others to the FRUs within it.
CAUTION Use only power cords supplied in the installation kit or those that meet product specifications.
IMPORTANT Only a qualified service technician should perform the installation.
Installation checklist
Read this entire section before you begin. You must adhere to all safety requirements prior to and during
installation.
WARNING! Do not attempt to install the 5U storage enclosure into the rack cabinet with drive modules
preloaded in the slots. Serious injury and damage could result. Unload any drive modules in storage
enclosure slots to a static-protected area. Do not further lighten the storage enclosure by removing other
components.
Use this checklist, performing each task only in the sequence presented after successful completion of the
prior step.
Step Task Reference
1 Complete all installation prerequisites Identified below
2 Unpack the storage enclosure "Unpack and prepare the 2U enclosure" on page13,
"Unpack and prepare the 5U enclosure" on page27
3 Prepare the site for installation of the storage enclosure
into the rack cabinet
"Unpack and prepare the 2U enclosure" on page13,
"Unpack and prepare the 5U enclosure" on page27
4 For rackmount installation, temporarily move to a static-protected area any drive modules not installed in the
storage enclosure
5 Install the rackmount kit in the rack cabinet "Install the 2U rackmount rail kit" on page14,
"Install the 5U rackmount rail kit" on page28
6 Mount the storage enclosure into the rack cabinet "Mount the 2U enclosure into the rack cabinet" on
page18,
"Mount the 5U enclosure into the rack cabinet" on
page31
7 Install drive modules in carriers (DDICs) in the storage
enclosure
"Populate the 2U enclosure" on page20,
"Populate the 5U enclosure" on page36
8 (Optional) Install expansion enclosures Follow same process for chassis installation up to this
step
Table 2 Installation checklist tasks

Chapter 3 Initial install preparations 11
Step Task Reference
9 Test for safety electrical earth connection "Test enclosure electrical earth connection" on page37
10 Connect all host and any expansion data cables "Route 2U enclosure data cables and power cords" on
page21,
"Route 5U enclosure data cables and power cords" on
page37
11 Connect all power cords
Table 2 Installation checklist tasks (continued)
lSite preparation
1. Use the installation checklist.
2. Clear the site for installation and secure a static-protected area.
lBefore storage enclosure installation
1. Unpack the storage enclosure in a clear area, using appropriate safety precautions.
2. Temporarily set aside all drives in carriers (DDICs) into a static-protected area, regardless of how your
storage enclosure or drives ship.
3. Follow all instructions for installing the provided rackmount rails into the rack cabinet.
4. Review all related warnings before mounting the storage enclosure into the rack.
lStorage enclosure installation
1. Move the storage enclosure onto a suitable mechanical lift.
a. For the 2U storage enclosures, have two people move the enclosure to a lift.
b. For the 5U storage enclosures, have three people use the provided belt straps to move the enclosure
to a lift.
2. Use a mechanical lift for positioning the storage enclosure and mounting it into the rack cabinet. Do not
use a vacuum lift. To maintain personal and equipment safety, do not use any other method to support
the weight of the storage enclosure during installation or maintenance.
3. Maintain adequate storage enclosure clearances, both front and back.
lBefore FRU installation
1. Prior to handling the DDICs, make sure you are static-compliant.
2. Confirm you can easily reach the slots and you can visually inspect the installation of each DDIC in the
enclosure, while safely maintaining your balance.
lDDIC installation
1. Only after you securely mount the storage enclosure in the rack can you retrieve the DDICs from their
static-protected area.
2. Install all DDICs into the proper module slots.
lPrior to testing the enclosure
1. Examine cables and make sure connections are completely secure on both ends.
2. Adhere to all electrical safety guidelines.
Complete installation prerequisites
The rackmount rails are designed to bear the maximum weight of the storage enclosure when it is properly
mounted in a standard rack cabinet. You can install multiple storage enclosures in a single rack cabinet.
This manual suits for next models
1
Table of contents
Other Quantum Enclosure manuals
Popular Enclosure manuals by other brands
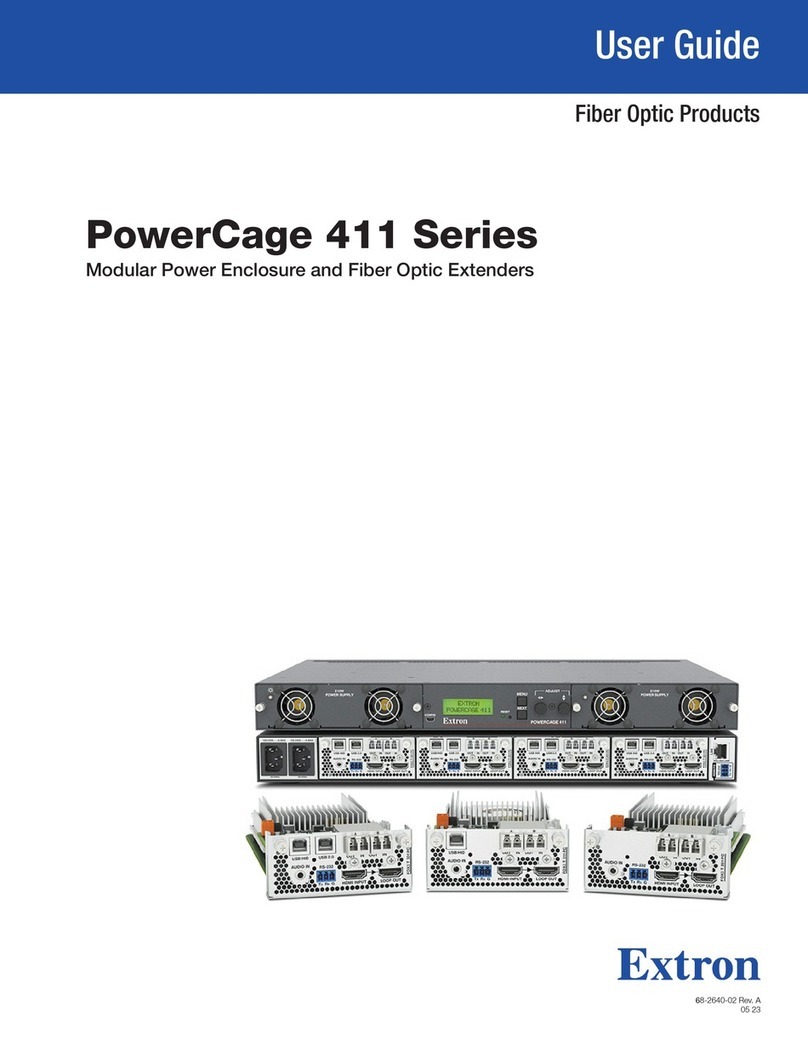
Extron electronics
Extron electronics PowerCage 411 Series user guide
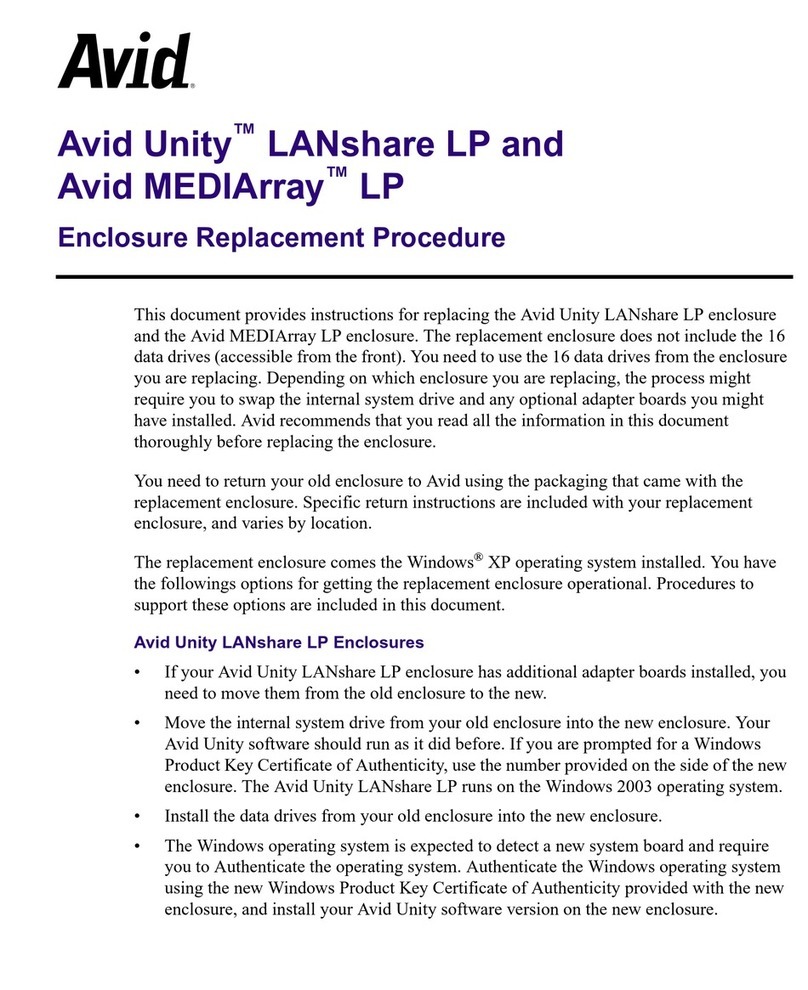
Avid Technology
Avid Technology Unity LANshare LP Replacement procedure
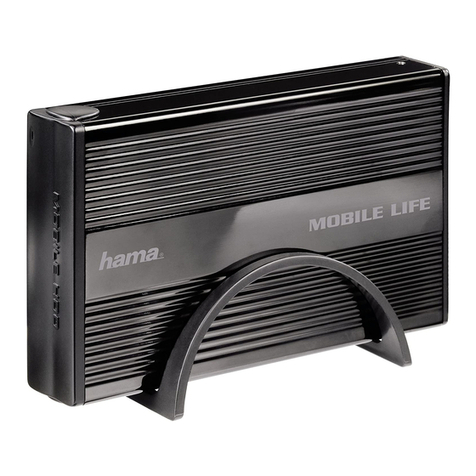
Hama
Hama 3.5" Hard Disk Enclosure operating instructions
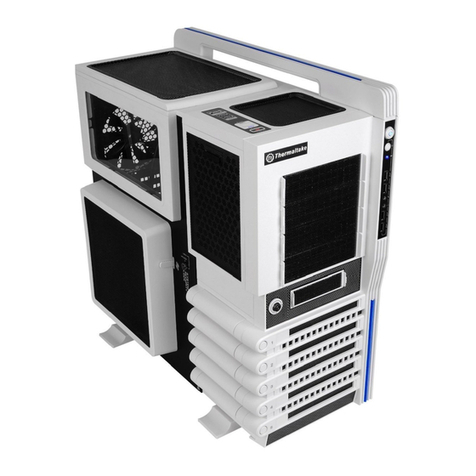
Thermaltake
Thermaltake VN10006W2N user manual
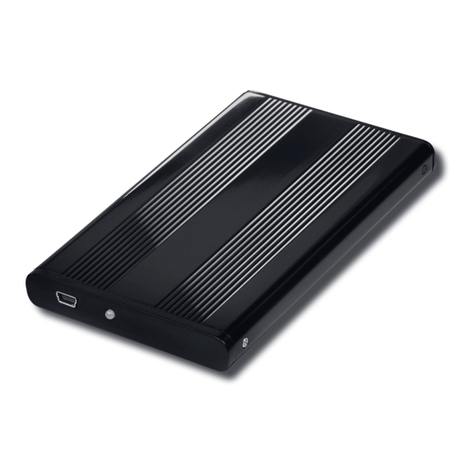
Hama
Hama 2.5" Hard disk Enclosure Operating instruction

CRU
CRU DE100 Ultra 160 install guide