Red Jacket 880-051-1 Installation instructions

Manual No: 051-330 ●Revision: H
Installation and Owner’s Manual
IQ Control Box
Model: 880-051-1
880-052-1
880-058-1
880-059-1

Notice
Veeder-Root makes no warranty of any kind with regard to this publication, including, but not limited to, the implied warranties of
merchantability and fitness for a particular purpose.
Veeder-Root shall not be liable for errors contained herein or for incidental or consequential damages in connection with the
furnishing, performance, or use of this publication.
Veeder-Root reserves the right to change system options or features, or the information contained in this publication.
This publication contains proprietary information which is protected by copyright. All rights reserved. No part of this publication
may be photocopied, reproduced, or translated to another language without the prior written consent of Veeder-Root.
Contact Red Jacket Technical Support for additional troubleshooting information at 800-323-1799.
DAMAGE GOODS/LOST EQUIPMENT
Thoroughly examine all components and units as soon as they are received. If any cartons are damaged or missing, write a
complete and detailed description of the damage or shortage on the face of the freight bill. The carrier's agent must verify the
inspection and sign the description. Refuse only the damaged product, not the entire shipment.
VR must be notified of any damages and/or shortages within 30 days of receipt of the shipment, as stated in our Terms and
Conditions.
VEEDER-ROOT’S PREFERRED CARRIER
1. Fax Bill of Lading to V/R Customer Service at 800-234-5350.
2. Call V/R Customer Service at 800-873-3313 with the specific part numbers and quantities that were received damaged or
lost.
3. VR will file the claim with the carrier and replace the damaged/missing product at no charge to the customer. Customer
Service will work with production facility to have the replacement product shipped as soon as possible.
CUSTOMER’S PREFERRED CARRIER
1. Customer files claim with carrier.
2. Customer may submit a replacement purchase order. Customer Service will work with production facility to have the
replacement product shipped as soon as possible.
3. If “lost” equipment is delivered at a later date and is not needed, VR will allow a Return to Stock without a restocking fee.
4. VR will NOT be responsible for any compensation when a customer chooses their own carrier.
RETURN SHIPPING
For the parts return procedure, please follow the instructions in the “General Returned Goods Policy” pages of the “Policies and
Literature” section of the Veeder-Root North American Red Jacket Mechanical Products Price Book. Veeder-Root will not accept
any return product without a Return Goods Authorization (RGA) number clearly printed on the outside of the package.
©Veeder-Root 2011. All rights reserved.

Table of Contents
iii
Introduction
Safety Precautions ............................................................................................................1
Installation and Wiring Instructions
Determine the Motor Type ................................................................................................8
Programming the Motor Type .........................................................................................11
Setup Switch Chart .........................................................................................................13
Initial Calibration .............................................................................................................14
Troubleshooting
Basic Indicator Functions ................................................................................................15
Description of Fault Conditions .......................................................................................15
Uncalibrated Controller...........................................................................................15
Overcurrent Condition ............................................................................................15
Dry Run ..................................................................................................................16
Low AC Current ......................................................................................................16
Setup/Communication Error ...................................................................................16
Low Line Voltage ....................................................................................................16
Bypass Mode..........................................................................................................16
Extended Run.........................................................................................................16
Figures
Figure 1. -051, 052 .................................................................................................2
Figure 2. -058, 059 .................................................................................................3
Figure 3. Wiring Diagram for Manifolded Systems ................................................3
Figure 4. Wiring Diagram for IQ with TLS-350 Manifolded PLLD Systems ...........4
Figure 5. Wiring Diagram for IQ Box with TLS-450 manifolded DPLLD Systems .....5
Figure 6. Isotrol to IQ Box Wiring - 120 Volt Dispenser Signals ............................6
Figure 7. Isotrol to IQ Box Wiring - 230 Volt Dispenser Signals ............................7
Figure 8. Identifying UMP Models by their End View .............................................8
Figure 9. Dip Switch SW1 and Bypass Jumper J3 ..............................................13
Tables
Table 1. Electrical Service Information (for UMPs Containing a Franklin
Motor with End View A) .............................................................................8
Table 2. Electrical Service Information (for UMPs Containing a Faradyne
Motor with End View B) .............................................................................9
Table 3. UMP Model Dimensions ..........................................................................10
Table 4. Approximate Pump Shut Off Pressures ..................................................10
Table 5. Motor Type Programming ........................................................................11
Table 6. Reset/Cal Button and LED Indicator Actions ...........................................12
Table 7. Motor Type Selections .............................................................................13
Table 8. Indicator Fault Conditions ........................................................................15

1
Introduction
RED JACKET’S IQ™ Control Box raises the standard for typical relay control boxes. Incorporating a
microprocessor on board that continuously monitors the submersible pump provides insurance against conditions
that can permanently damage the pump. In addition, the increasing number of dispensers at a station has
demanded more than one pump per tank. Red Jacket’s IQ Control Box can be connected to additional control
boxes to allow up to four pumps per tank with demand driven sequencing. This function can be set to alternate
between pumps that initiate next dispensing events to average the wear on all of the pumps in the system. The
pump control circuit features non-volatile memory retention eliminating the need to recalibrate if power is lost.
IQ Control Box version 3 software adds support for Faradyne motors. The software will also support Franklin
motors. Software version 3 requires the motor type to be programmed into the unit. The five-position unit
configuration switches, reset/calibration button, and bypass/normal jumper are used to program the Motor Type.
The microprocessor chip containing software version 3 is marked 805-001C or higher.
Retain this instruction manual with the equipment after installation for future use.
Safety Precautions
The following safety symbols are used throughout this manual to alert you to important safety hazards and
precautions.
TURN POWER OFF
Live power to a device creates a
potential shock hazard. Turn Off
power to the device and associated
accessories when servicing the unit.
ELECTRICITY
High voltage exists in, and is supplied
to, the device. A potential shock haz-
ard exists..
WARNING
Heed the adjacent instructions to
avoid equipment damage or personal
injury.
READ ALL RELATED MANUALS
Knowledge of all related procedures
before you begin work is important.
Read and understand all manuals
thoroughly. If you do not understand
a procedure, ask someone who does.
.
WARNING
FAILURE TO COMPLY WITH THE FOLLOWING WARNINGS AND SAFETY PRECAUTIONS
COULD CAUSE DAMAGE TO PROPERTY, ENVIRONMENT, RESULTING IN SERIOUS INJURY
OR DEATH.
1. All installation work must comply with the latest issue of the National Electrical Code
(NFPA 70), the Code for Motor Fuel Dispensing Facilities and Repair Garages (NFPA
30A), and any European, national, state, and local code requirements that apply.
2. To protect yourself and others from serious injury, death, or substantial property
damage, carefully read and follow all warnings and instructions in this manual.
OFF
OFF

2
Installation and Wiring Instructions
This equipment must be installed in a non-hazardous location.
1. Locate an area that allows all of the wiring to enter through the bottom knockouts of the control box. Consider
the ability to view the indicator on the side of the base and access to the reset button when choosing a
location.
2. Remove the cover of the enclosure and mount the base.
3. While viewing the wiring diagram (Figure 1) or inside the enclosure lid, connect the input power L1 and L2
wires to the terminal block labeled TB1. This control box is designed to operate from 200 to 250Vac. Since
the submersible turbine pump is powered by the M1 and M2 terminals (and M3 terminals -058, -059 models)
on the circuit board, refer to the installation and instruction manual that was supplied with the pump for correct
supply voltage. Typical pump ratings are 208 to 240Vac.
4. Locate the grounding lug on the enclosure base and make an electrical ground connection to this point.
5. Motor leads M1 and M2 should be terminated to the M1 and M2 terminals on TB1. The M3 lead for models -
058 and -059 should terminate to the splice provided lead from the capacitor in the lid (Figure 2).
6. The D1 and D2 terminals are reserved for the dispenser signal. These terminals are not polarity sensitive and
can accept 120V or 240V signals. For pump manifolded installations it is important to wire the dispenser
signal to all of the controllers.
7. Jumper J3 should be in the Normal position. Use the Bypass position only to program the Motor Type, or if
temporarily controlling the pump directly from dispenser. Pump protection operation is not available in this
position.
8. Installations that will operate pumps in a manifolded configuration require a two conductor, twisted pair with
shield (min. 22 AWG) connected to the COM+, COM-, and SHIELD terminals of TB1. Daisy chain the
communication cable to all of the controllers as shown in Figure 3. Belden 9462, or equivalent cable is
acceptable. The RS-485 link between pump controllers is not intended to be connected to other Red Jacket
electronic equipment such as Prolink, CPT, VSFC or other ATG devices. However, it may be necessary to
break communications in PLLD or DPLLD applications as shown in Figure 4 and Figure 5. This cable must be
installed in conduit.
Note: Approved component only. Total systems installed shall comply with all codes.
Figure 1. -051, 052
COM+
(MANIFOLDED UNITS
INSTALL IN CONDUIT
RS-485 CONNECTIONS
C23
TB1
ONLY)
D2
FROM
120V OR 240V
COM- SHLD D1 M2
FROM SUPPLY
PANEL
L1M1 L2
CONNECT TO
ELECTRICAL
GND
Z2
Z3
DISPENSER
TO PUMP
2 HP MAX
MAKE GROUND
CONNECTION IN
ACCORDANCE
WITH LOCAL CODES
WIRING MUST BE
RATED 90˚C MIN.
GROUND

IQ Control Box Installation and Owner’s Manual Safety Precautions
3
Figure 2. -058, 059
Figure 3. Wiring Diagram for Manifolded Systems
COM+
(MANIFOLDED UNITS
INSTALL IN CONDUIT
RS-485 CONNECTIONS
C23
TB1
ONLY)
D2
FROM
120V OR 240V
COM- SHLD D1 M2
FROM SUPPLY
PANEL
L1M1 L2
CONNECT TO
ELECTRICAL
GND
Z2
Z3
DISPENSER
TO PUMP
2 HP MAX
MAKE GROUND
CONNECTION IN
ACCORDANCE
WITH LOCAL CODES
WIRING MUST BE
RATED 90˚C MIN.
GROUND
FROM DISPENSERS
L
FROM PANELTO PUMP FROM PANEL
N
TO PUMP
TO 3RD
OR
4TH BOX
COM+
TB1
C23
D2COM- SHLD D1 M2 L1M1 L2 GND
Z3
Z2
COM-COM+ SHLD D2
TB1
C23
M1D1 M2 L1 L2 GND
Z3
Z2

IQ Control Box Installation and Owner’s Manual Safety Precautions
4
Figure 4. Wiring Diagram for IQ with TLS-350 Manifolded PLLD Systems
COM+ COM- SHLD
C23
TB1
D1D2 M2 M1 L1 L2 GND
Z2
Z3
#1
TO PUMP
SHLDCOM+ COM-
TB1
C23
D2 D1 M2 M1 L2L1 GND
Z3
Z2
NC NO C
1
NC NO C NC NO C NC NO C
122 33 44
4-RELAY OUTPUT MODULE
POWER AREA OF CONSOLE
P1 PR L1 PO
12
PRP1 POL1
3
PRP1 POL1
TLS 350 CONSOLE
PRESSURE LINE LEAK CONTROLLER MODULE
IQ2
IQ1
230VAC
N
L1
N
DISPENSER HOOK
PUMP OUTPUT IQ1
NTO PUMP
#2
230VAC
PUMP OUTPUT IQ2
NO C
VR RELAY
COM +
IQ2
COM +
IQ1
SHIELD
RS-485
COMMUNICATION
CABLE
COM -
330-2.eps

IQ Control Box Installation and Owner’s Manual Safety Precautions
5
Figure 5. Wiring Diagram for IQ Box with TLS-450 manifolded DPLLD Systems
COM+ COM- SHLD
C23
TB1
D1D2 M2 M1 L1 L2 GND
Z2
Z3
#1
TO PUMP
SHLDCOM+ COM-
TB1
C23
D2 D1 M2 M1 L2L1 GND
Z3
Z2
IQ2
IQ1
230VAC
N
L1
N
DISPENSER HOOK 330-1.eps
PUMP OUTPUT IQ1
NTO PUMP
#2
230VAC
PUMP OUTPUT IQ2
NO C
VR RELAY
COM +
COM +
RS-485
COMMUNICATION
CABLE
COM -
I/O Module

IQ Control Box Installation and Owner’s Manual Safety Precautions
6
ELECTRICAL
INTERLOCK
CONTINUOUS
DUTY
CAPACITOR
INTERNAL
OVERLOAD
PROTECTOR
JUNCTION
BOX IN
MANIFOLD
COM+
C23
TB1
D2COM- SHLD D1 M2 L1M1 L2 GND
Z2
Z3
IQ CONTROL BOX (P/N 880-051-1)
ISOTROL CONTROL BOX (P/N 880-049-1)
MOTOR
STP
NEUTRAL
(FROM SUPPLY PANEL)
208/230 VOLT
FROM SUPPLY
PANEL
CHANNEL 1
CHANNEL 2
CHANNEL 3
CHANNEL 4
CHANNEL 5
CHANNEL 6
CHANNEL 7
CHANNEL 8
120 VOLT
DISPENSER
SIGNALS
UNSWITCHED
NEUTRAL TO TB2
TB1
208/230 VOLT
UNSWITCHED NEUTRAL
NOT
USED
NOT
USED
NOT
USED
NOT
USED
ISOTROL CONTROL BOX WIRING PRECAUTIONS
This device is intended to provide electrical isolation between the dispenser pump enable (Hook) signal
and the submersible turbine pump (STP) control relay. Other energized sources of power can still exist within the dispenser
even with this device.
The neutral connection to the N terminal of TB1 and N terminal of TB2 must be from the service panel and
be a permanently connected, unswitched connection.
The N connection on TB1 and the eight N connections on TB2 may be spliced to a common neutral wire from the service
panel described above.
Make only one "wire" connection on each N terminal on TB2.
The phase of L1 (TB1) must match the phase of the power supplying the ATG device in order to prevent
cross phasing which may damage the input on some ATG equipment.
GENERAL WIRING PRECAUTIONS
Wiring must be rated 90˚C minimum.
Make ground connection in accordance with local codes.
12345678
DISPENSER INPUTS
PHASE ON L1 MUST BE SAME AS DEVICE
CONNECTED TO ATG TERMINAL
HOT
NEUTRAL
TB2
ATG NL1L2M2M1S
Danger!!
Danger!!
Caution
The following terms are used in this document to bring attention to
the presence of hazards of various risk levels, or to important information
concerning use of the product.
Indicates the presence of a hazard that will cause severe personal injury,
death, or substantial property damage if ignored.
Indicates the presence of a hazard that will or can cause minor personal
injury or property damage if ignored.
Indicates special instructions on installation, operation, or maintenance that
are important but not related to personal injury hazards.
Danger!!
Caution
yyNoticepp
yyNoticepp
RS-485 CONNECTIONS
INSTALL IN CONDUIT
(MANIFOLDED UNITS
ONLY)
CONNECT TO
ELECTRICAL
GROUND
CONNECT TO
ELECTRICAL GROUND
FROM
SUPPLY
PANEL
120 VOLT ISOLATED OUTPUT TO IQ CONTROL BOX
Figure 6. Isotrol to IQ Box Wiring - 120 Volt Dispenser Signals

IQ Control Box Installation and Owner’s Manual Safety Precautions
7
ELECTRICAL
INTERLOCK
CONTINUOUS
DUTY
CAPACITOR
INTERNAL
OVERLOAD
PROTECTOR
JUNCTION
BOX IN
MANIFOLD
COM+
C23
TB1
D2COM- SHLD D1 M2 L1M1 L2 GND
Z2
Z3
IQ CONTROL BOX (P/N 880-052-1)
ISOTROL CONTROL BOX (P/N 880-050-1)
MOTOR
STP
NEUTRAL
(FROM SUPPLY PANEL)
FROM
SUPPLY
PANEL
NEUTRAL
CHANNEL 1
CHANNEL 2
CHANNEL 3
CHANNEL 4
CHANNEL 5
CHANNEL 6
CHANNEL 7
CHANNEL 8
230 VOLT
DISPENSER
SIGNALS
UNSWITCHED
NEUTRAL TO TB2
TB1
230 VOLT
UNSWITCHED NEUTRAL
NOT
USED
NOT
USED
NOT
USED
NOT
USED
ISOTROL CONTROL BOX WIRING PRECAUTIONS
This device is intended to provide electrical isolation between the dispenser pump enable (Hook) signal
and the submersible turbine pump (STP) control relay. Other energized sources of power can still exist within the dispenser
even with this device.
The neutral connection to the N terminal of TB1 and N terminal of TB2 must be from the service panel and
be a permanently connected, unswitched connection.
The N connection on TB1 and the eight N connections on TB2 may be spliced to a common neutral wire from the service
panel described above.
Make only one "wire" connection on each N terminal on TB2.
The phase of L1 (TB1) must match the phase of the power supplying the ATG device in order to prevent
cross phasing which may damage the input on some ATG equipment.
GENERAL WIRING PRECAUTIONS
Wiring must be rated 90˚C minimum.
Make ground connection in accordance with local codes.
12345678
DISPENSER INPUTS
PHASE ON L1 MUST BE SAME AS DEVICE
CONNECTED TO ATG TERMINAL
HOT
NEUTRAL
TB2
ATG NL1L2M2M1S
Danger!!
Danger!!
Caution
The following terms are used in this document to bring attention to
the presence of hazards of various risk levels, or to important information
concerning use of the product.
Indicates the presence of a hazard that will cause severe personal injury,
death, or substantial property damage if ignored.
Indicates the presence of a hazard that will or can cause minor personal
injury or property damage if ignored.
Indicates special instructions on installation, operation, or maintenance that
are important but not related to personal injury hazards.
Danger!!
Caution
yyNoticepp
yyNoticepp
RS-485 CONNECTIONS
INSTALL IN CONDUIT
(MANIFOLDED UNITS
ONLY)
CONNECT TO
ELECTRICAL
GROUND
CONNECT TO
ELECTRICAL GROUND
230 VOLT
FROM
SUPPLY
PANEL
230 VOLT ISOLATED OUTPUT TO IQ CONTROL BOX
Figure 7. Isotrol to IQ Box Wiring - 230 Volt Dispenser Signals

IQ Control Box Installation and Owner’s Manual Determine the Motor Type
8
Determine the Motor Type
Warning! Disconnect, lock out, an tag power to the IQ Box at the panel before starting these
steps.
Determination of the Motor Type can be accomplished by measuring the resistance readings at the junction box in
the STP and comparing to Table 1 or Table 2 below. Motor Type can also be determined by observing the flow
paths in the top of the UMP (Figure 8). UMPs containing a Faradyne motor will also have an ‘FM’ designation
printed on the UMP shell.
Figure 8. Identifying UMP Models by their End View
Table 1 and Table 2 show pump electrical service requirements for UMPs with end views A and B, respectively.
Table 1. Electrical Service Information (for UMPs Containing a Franklin Motor with End View A)
Required power supply rating for 60 Hz, 1 phase pumps is 208 - 230 Vac. For 50 Hz, 1 phase pumps, required rating is 220 - 240 Vac.
UMP Model No. HP Hz PH
Voltage
Fluctuation
Range
Max.
Load
Amps
Locked
Rotor
Amps
Winding Resistance (Ohms)
Capacitor Kit (µF)Min. Max.
Black-
Orange
Red-
Orange Black-Red
AGUMP33S1,
UMP33U1
1/3 60 1 200 250 4.0 13 7.7 - 9.4 17.4 - 21.2 25 - 30.7 144-224-5 (17.5)
E85AGUMP75S1,
UMP75U1
3/4 60 1 200 250 6.5 25 2.9 - 3.6 14.9 - 18.2 17.7 - 21.9 410164-001 (17.5)
E85AGUMP150S1,
UMP150U1
1-1/2 60 1 200 250 10.5 37 2.0 - 2.5 11.6 - 14.2 13.5 - 16.8 410164-002 (25)
E85X3AGUMP150S1,
X3UMP150U1
1/1/2 60 1 200 250 10.5 37 2.0 - 2.5 11.6 - 14.2 13.5 - 16.8 410164-002 (25)
OFF
UMP End View A UMP End View B
153-2.eps

IQ Control Box Installation and Owner’s Manual Determine the Motor Type
9
E85AGUMP200S1-3,
UMP200U1-3
2 60 1 200 250 11.4 46 1.4 - 1.7 2.5 - 3.2 3.8 - 5 410164-003 (40)
AGUMP75S3-3,
UMP75U3-3
3/4 50 1 200 250 5.8 17 3.6 - 4.5 20.4 - 25 23.9 - 29.6 410164-001 (17.5)
AGUMP150S3-3,
UMP150U3-3
1-1/2 50 1 200 250 10 28 2.5 - 3.1 11.5 - 14 13.9 - 17.2 410164-002 (25)
X4AGUMP150S3,
X4UMP150U3
1-1/2 50 1 200 250 10 28 2.5 - 3.1 11.5 - 14 13.9 - 17.2 410164-002 (25)
AGUMP200S3-4,
UMP200U3-4
2 50 1 200 250 11 37 1.9 - 2.4 3.1 - 3.9 5.0 - 6.3 410164-003 (40)
Table 2. Electrical Service Information (for UMPs Containing a Faradyne Motor with End View B)
Required power supply rating for 60 Hz, 1 phase pumps is 208 - 230 Vac. For 50 Hz, 1 phase pumps, required rating is 220 - 240 Vac.
UMP Model No. HP Hz PH
Voltage
Fluctuation
Range
Max.
Load
Amps
Locked
Rotor
Amps
Winding Resistance (Ohms)
Capacitor Kit (µF)Min. Max.
Black-
Orange
Red-
Orange Black-Red
AGUMP33S1,
UMP33U1
1/3 60 1 200 250 4.0 10 8.9 -10.8 11.7 - 14.2 17.4 - 21.1 144-224-5 (17.5)
E85AGUMP75S1,
UMP75U1
3/4 60 1 200 250 6.5 19 4.6 - 5.6 7.0 - 8.5 11.6 - 14.0 410164-001 (17.5)
E85AGUMP150S1,
UMP150U1
1-1/2 60 1 200 250 10.5 33 2.6 - 3.2 6.6 - 8.0 9.2 - 11.2 410164-002 (25)
E85X3AGUMP150S1,
X3UMP150U1
1/1/2 60 1 200 250 10.5 33 2.6 - 3.2 6.6 - 8.0 9.2 - 11.2 410164-002 (25)
E85AGUMP200S1-3,
UMP200U1-3
2 60 1 200 250 11.4 44 1.7 - 2.1 3.2 - 4.0 5.0 - 6.1 410164-003 (40)
AGUMP75S3-3,
UMP75U3-3
3/4 50 1 200 250 5.8 18 4.9 - 5.9 11.0 - 12.2 15.0 - 18.2 410164-001 (17.5)
AGUMP150S3-3,
UMP150U3-3
1-1/2 50 1 200 250 10 31 2.7 - 3.3 13.2 - 16.1 16.0 - 19.4 410164-002 (25)
X4AGUMP150S3,
X4UMP150U3
1-1/2 50 1 200 250 10 31 2.7 - 3.3 13.2 - 16.1 16.0 - 19.4 410164-002 (25)
AGUMP200S3-4,
UMP200U3-4
2 50 1 200 250 11 38 2.0 - 2.4 5.8 - 7.0 7.8 - 9.5 410164-003 (40)
Table 1. Electrical Service Information (for UMPs Containing a Franklin Motor with End View A)
Required power supply rating for 60 Hz, 1 phase pumps is 208 - 230 Vac. For 50 Hz, 1 phase pumps, required rating is 220 - 240 Vac.
UMP Model No. HP Hz PH
Voltage
Fluctuation
Range
Max.
Load
Amps
Locked
Rotor
Amps
Winding Resistance (Ohms)
Capacitor Kit (µF)Min. Max.
Black-
Orange
Red-
Orange Black-Red

IQ Control Box Installation and Owner’s Manual Determine the Motor Type
10
Table 3 lists UMP weights and lengths and Table 4 lists pump shut off pressures.
NOTE: The weights and lengths listed below are approximate values and will vary due to manufacturing
tolerances.
The optional trapper intake screen is available as a field installed accessory. Trapper options will increase the
length of the UMP by 3.3 inches (83 mm). For installation instructions, see Red Jacket installation instructions
#051-256-1. For models with floating suction adapter, add 2-3/8 inches (59 mm) and 4 pounds (1.8 kg).
Table 3. UMP Model Dimensions
Franklin Motor
(Use these lengths for
UMPs with end view A
shown in Figure 8)
Faradyne Motor
(Use these lengths for
UMPs with end view B
shown in Figure 8) Weight
UMP Model HP in. mm in. mm lb. kg
UMP33U1, AGP33R1 1/3 15-1/2 390 15-3/8 391 24 11.0
UMP75U1, E85AGUMP75S1 3/4 17-3/4 447 17-5/8 448 28 12.7
UMP75U3-3, AGUMP75S3-3 3/4 20 507 19-7/8 505 30.5 13.9
UMP150U1, E85AGUMP150S1 1-1/2 20-1/2 519 20-5/8 524 34 15.5
X3P150U1, E85X3AGUMP150S1 1-1/2 21-1/4 540 21-1/2 546 35 15.8
UMP150U3-3, AGUMP150S3-3 1-1/2 22-1/4 565 22-1/4 565 34 15.5
X4P150U3, X4GUMP150S3 1-1/2 22-3/4 576 22-7/8 581 35 15.9
UMP200U1-3, E85AGUMP200S1-3 2 24-1/4 618 24-5/8 626 36 16.3
UMP200U3-4, AGUMP200S3-4 2 26 660 26-1/4 667 38 17.2
Table 4. Approximate Pump Shut Off Pressures
UMP Model Approximate Shut Off Pressure
AGUMP33S1, UMP33R1 25 psi (172 kPa) .74 SG @ 60°F (15°C)
E85AGUMP75S1, UMP75U1 28 psi (193 kPa) .74 SG @ 60°F (15°C)
E85AGUMP150S1, UMP150U1 30 psi (207 kPa) .74 SG @ 60°F (15°C)
E85X3AGUMP150S1, X3UMP150U1 43 psi (297 kPa) .74 SG @ 60°F (15°C)
AGUMP75S3-3, UMP75U3-3 30 psi (207 kPa) .74 SG @ 60°F (15°C)
AGUMP150S3-3, UMP150U3-3 32 psi (220 kPa) .74 SG @ 60°F (15°C)
X4AGUMP150S3, X4UMP150U3 40 psi (275 kPa) .74 SG @ 60°F (15°C)
E85AGUMP200S1-3, UMP200U1-3 43 psi (297 kPa) .74 SG @ 60°F (15°C)
AGUMP200S3-4, UMP200U3-4 43 psi (297 kPa) .74 SG @ 60°F (15°C)

IQ Control Box Installation and Owner’s Manual Programming the Motor Type
11
Programming the Motor Type
WARNING! Disconnect, lock out, and tag power to the IQ box at the panel before starting this procedure.
1. Open the IQ box cover.
2. Place the Bypass Jumper in the Bypass Position (Figure 9)
3. Set the five Motor Type Programming DIP switches (Figure 9) to the positions indicated in Table 5 for your
Motor Type.
4. Close and secure IQ Box cover.
5. Reapply power to the IQ Box. (Hook signal must be Off).
6. Locate the Code LED Indicator and the Reset/Calibration button on the side of the IQ Box. Depress the
Reset/Cal button 20 seconds as you observe the Code LED flashing sequence shown in Table 6. Note the
number of Green flashes for your Motor Type.
Table 5. Motor Type Programming
Number of
Code LED
Flashes
Switch Position
Manufacturer Motor
12345
1 OFF OFF OFF OFF OFF
FARADYNE
1/3 60 Hz
2 OFF OFF OFF OFF ON 3/4 60 Hz
3 OFF OFF OFF ON OFF 1.5 60 Hz
4 OFF OFF OFF ON ON 2.0 60 Hz
5 OFF OFF ON OFF OFF X3
6 OFF OFF ON OFF ON 3/4 50 Hz
7 OFF OFF ON ON OFF 1.5 50 Hz
8 OFF OFF ON ON ON 2.0 50 Hz
9 OFF ON OFF OFF OFF X4
OFF

IQ Control Box Installation and Owner’s Manual Programming the Motor Type
12
7. Release the Reset/Cal button after confirming the Green LED has flashed the correct number of times for your
Motor Type as show n in Table 5.
10 ON OFF OFF OFF OFF
FRANKLIN
1/3 60 Hz
11 ON OFF OFF OFF ON 3/4 60 Hz
12 ON OFF OFF ON OFF 1.5 60 Hz
13 ON OFF OFF ON ON 2.0 60 Hz
14 ON OFF ON OFF OFF X3
15 ON OFF ON OFF ON 3/4 50 Hz
16 ON OFF ON ON OFF 1.5 50 Hz
17 ON OFF ON ON ON 2.0 50 Hz
18 ON ON OFF OFF OFF X4
SOLID ANY OTHER SETTING UNKNOWN UNKNOWN
Table 6. Reset/Cal Button and LED Indicator Actions
LED
Reset/Cal Button -
Time Depressed Action
Off Start Press And Hold The Reset Button
Green 5 seconds Clears Alarms
Red 10 seconds Queues Calibration
Off 20 seconds
Cancel calibration. If in Bypass mode,
reads and stores Motor Type.
Green 20 seconds
Flashes saved Motor Type code (see
Table 5)
Table 5. Motor Type Programming
Number of
Code LED
Flashes
Switch Position
Manufacturer Motor
12345

IQ Control Box Installation and Owner’s Manual Setup Switch Chart
13
WARNING! Disconnect, lock out, and tag power to the IQ box at the panel before starting these steps.
8. Disconnect power from the IQ Box.
9. Place the Bypass Jumper in the Normal Position.
10. The unit must be calibrated every time the Motor Type programming is performed even if the Motor Type does
not change. Set the five DIP switches to the desired pump type and mode / role select configuration (see
Figure 9). NOTE: The unit will not calibrate if a Motor Type has not been programmed.
Setup Switch Chart
Each controller must have its duty established through the dip switch bank labeled SW1 on the circuit board
(Figure 9).
Figure 9. Dip Switch SW1 and Bypass Jumper J3
Follow Table 7 below to properly set the five switches for the controller.
Manifolded PLLD mode allows interfacing with an ATG console. This mode has special
communication wiring requirements. Refer to Figure 4 for IQ with manifolded PLLD systems or
Figure 5 for IQ with manifolded DPLLD systems
Manifolded Direct mode allows for a primary pump to initiate all dispensing events and secondary
pumps to help when required. The control box set as Unit 1 (switch 4 & 5 on) is the Primary.
Table 7. Motor Type Selections
Pump Type
Switch
Mode Select
Switch
Role Select
Switch
12345
Standard ON Stand Alone ON ON Unit 1 ON ON
X-Series OFF Manifolded PLLD ON OFF Unit 2 ON OFF
Manifolded Alternating OFF ON Unit 3 OFF ON
Manifolded Direct OFF OFF Unit 4 OFF OFF
OFF
NORMAL
J3 JUMPER POSITIONS
BYPASS
1
PUMP TYPE
SW1
O
N
SELECT
MODE
SELECT
ROLE
23 54
ON
OFF

IQ Control Box Installation and Owner’s Manual Initial Calibration
14
Initial Calibration
Once all of the wiring is complete and the dip switch and jumpers are set the cover can be attached to the
enclosure. Every controller in the system must be calibrated at this time.
WARNING! Power to the controller should only be applied when all wiring is connected and the cover
is installed.
1. Energize the supply voltage to the control box. At this time the indicator on the side of the enclosure should
illuminate green acknowledging circuits are energized. A single red flash from the indicator signals that the
controller has not been calibrated.
2. Press and hold the Reset/Cal button on the side of the enclosure for 10 seconds until the indicator turns red.
3. Release the Reset/Cal button. The controller will automatically start the pump and perform a calibration
procedure. Once the procedure is complete the pump will shut off and the indicator will display solid green.
Should a dispenser handle be lifted during the calibration procedure the controller will suspend the calibration
and dispense fuel as long as the handle remains lifted. A suspended calibration procedure is indicated by
alternating red and green indication through the duration of the dispense event. Once the dispensing event is
over the controller will perform the calibration procedure. Anytime that the pump or dispensing equipment has
been replaced perform a new calibration to update the stored information in memory.
4. The saved Motor Type can be verified with the Bypass jumper in the Normal position.
5. Depress the Reset/Calibration button for 20-seconds – continue holding the button in until the Green LED
has flashed the Motor Type code.
6. If the number of green flashes matches your Motor Type code noted in Step 6 on page 11 above, The IQ Box
is now ready for operation.

15
Troubleshooting
WARNING! If at any time during a troubleshooting procedure the enclosure must be opened,
disconnect controller power prior to removal of the cover. The input terminals D1 and D2 are powered
from the dispenser which is on a different circuit and may be energized even with the control box
power disconnected. Remember to remove power to dispenser circuits that energize the D1 and D2
terminals of TB1 whenever removing power to service the unit.
Basic Indicator Functions
• Solid green – controller circuit is energized
• Flashing green – pump is running
Description of Fault Conditions
The indicator on the side of the enclosure flashes the following alarms in red:
Uncalibrated Controller
This fault indicates that the controller has not been run through an initial calibration to setup all critical points for
pump protection. The device will operate the pump if a dispenser signal is detected but cannot correctly monitor
pump until initialized. See Calibration Section. NOTE: The unit will not calibrate if the Motor Type has not been
programmed.
Overcurrent Condition
This fault indicates that the device detected a high current in the pump’s wiring which could be either a short in the
wiring between the M1 and M2 terminals to ground or a locked rotor in the pump. The following procedure will
determine if wiring must be replaced or the pump must be removed and replaced.
WARNING! Before starting this troubleshooting procedure disconnect all electrical power to the controller
including the dispenser inputs. Failure to do so may COULD CAUSE DAMAGE TO PROPERTY, ENVIRONMENT,
RESULTING IN SERIOUS INJURY OR DEATH.
Table 8. Indicator Fault Conditions
# of Flashes Condition
1 Uncalibrated Controller
2 Overcurrent Condition – Pump Shutoff
3 Dry Run Detected – Pump Shutoff
4 Low AC Current
5 Setup/Communication Error
6 Low Line Voltage < 200Vac
7 Bypass Mode
8 Extended Run Condition
OFF

IQ Control Box Installation and Owner’s Manual Description of Fault Conditions
16
Using an ohmmeter measure the resistance between the M1 and M2 terminals to ground. Ground can be found at
the screw on the enclosure base. Both measurements should be greater than 1Meg ohm. Any measurement less
may indicate a short in wiring between the control box and the submersible pump. The location of the short can be
determined by breaking the wiring connections in the junction box at the pump’s packer/manifold and taking
ohmmeter readings on both sides of the circuit.
Refer to the manual for the extractable pump on instructions for its wiring, servicing, or replacement. Reset the
controller by pressing the reset button momentarily and verify operation once condition is resolved, all wiring
reconnected, and after power is reapplied.
Dry Run
This fault will shut off the pump since the level of the product has fallen below the suction end of the pump. The
controller will automatically reset and start the pump when the next dispenser signal is received. Add fuel to the
tank to restore operation.
Low AC Current
This fault indicates that the submersible pump will not operate. One of the following conditions are present: wire
disconnected resulting in open circuit, thermal switch in motor has opened due to overheating, or the control relay
has failed and the contacts will not close.
Setup/Communication Error
Five red flashes indicate that the controller has detected an improper dip switch setup or a missing connection on
the RS-485 communication cable when set to manifolded operation. Verify that each controller has a unique unit
number setting on the SW1 dip switch. Insure that all controllers have a communication cable connection unless
in standalone mode.
Low Line Voltage
This fault will not shut off the pump but will indicate if at any time the line falls below 200V which is the minimum
specified operating voltage.
Bypass Mode
If jumper J3 is set to bypass this mode will be displayed. Use this only to verify operation between dispenser and
pump since controller cannot provide pump protection in this mode. Return the jumper to the normal condition to
reset this alarm and have the controller monitor the pump.
Extended Run
Use this indicator to signal any pump that has run for more than 6 hours continuously. This may also indicate a
nozzle that has not been properly stowed after dispensing.
Contact Red Jacket Technical Support for additional troubleshooting information at 1-800-323-1799.

For technical support, sales or
other assistance, please visit:
www.veeder.com
This manual suits for next models
3
Table of contents
Popular Control Unit manuals by other brands
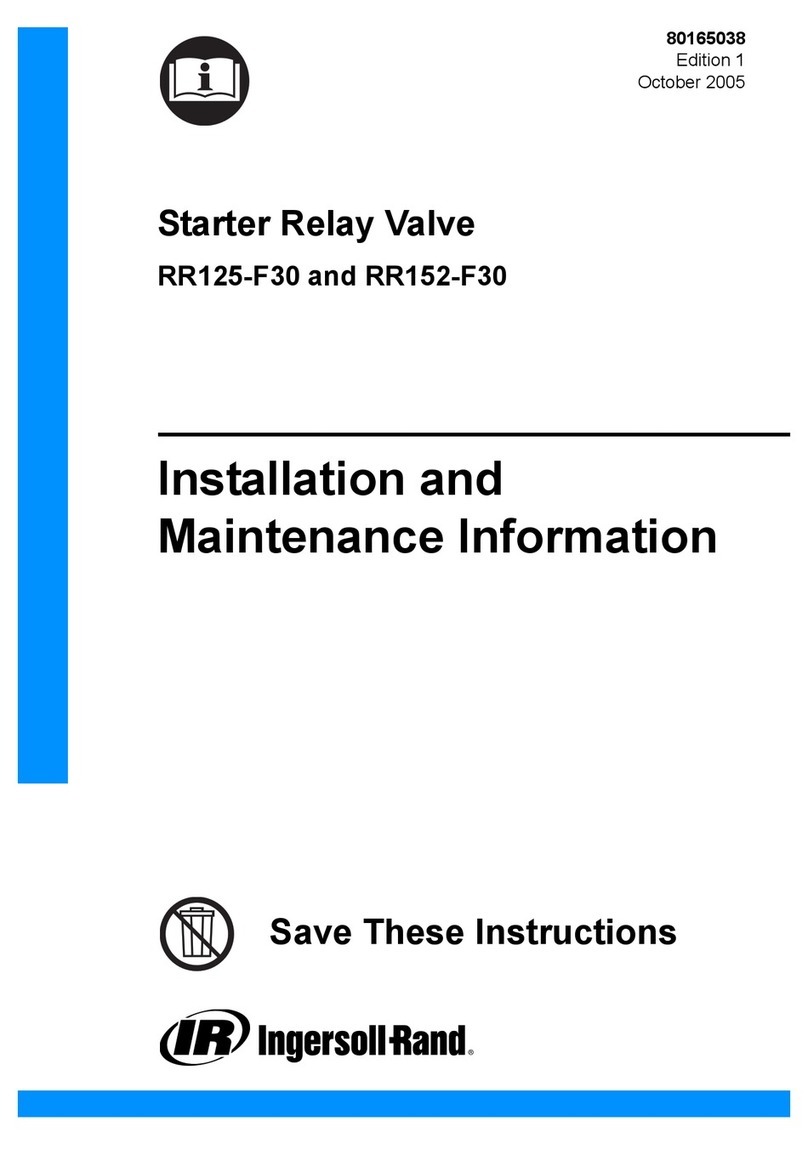
Ingersoll-Rand
Ingersoll-Rand RR125-F30 Installation and maintenance information
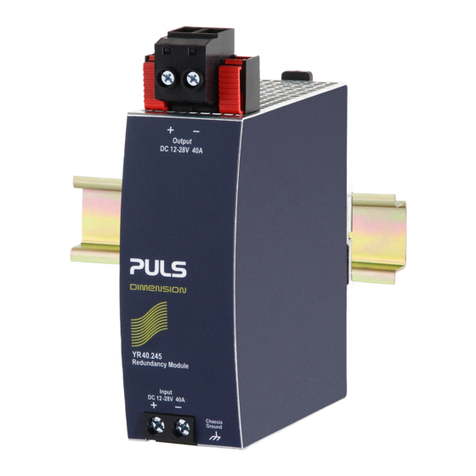
Puls
Puls DIMENSION YR40.245 manual
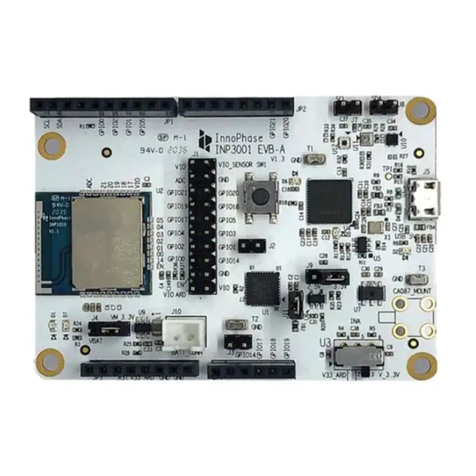
Innophase
Innophase Talaria TWO EVB-A user guide
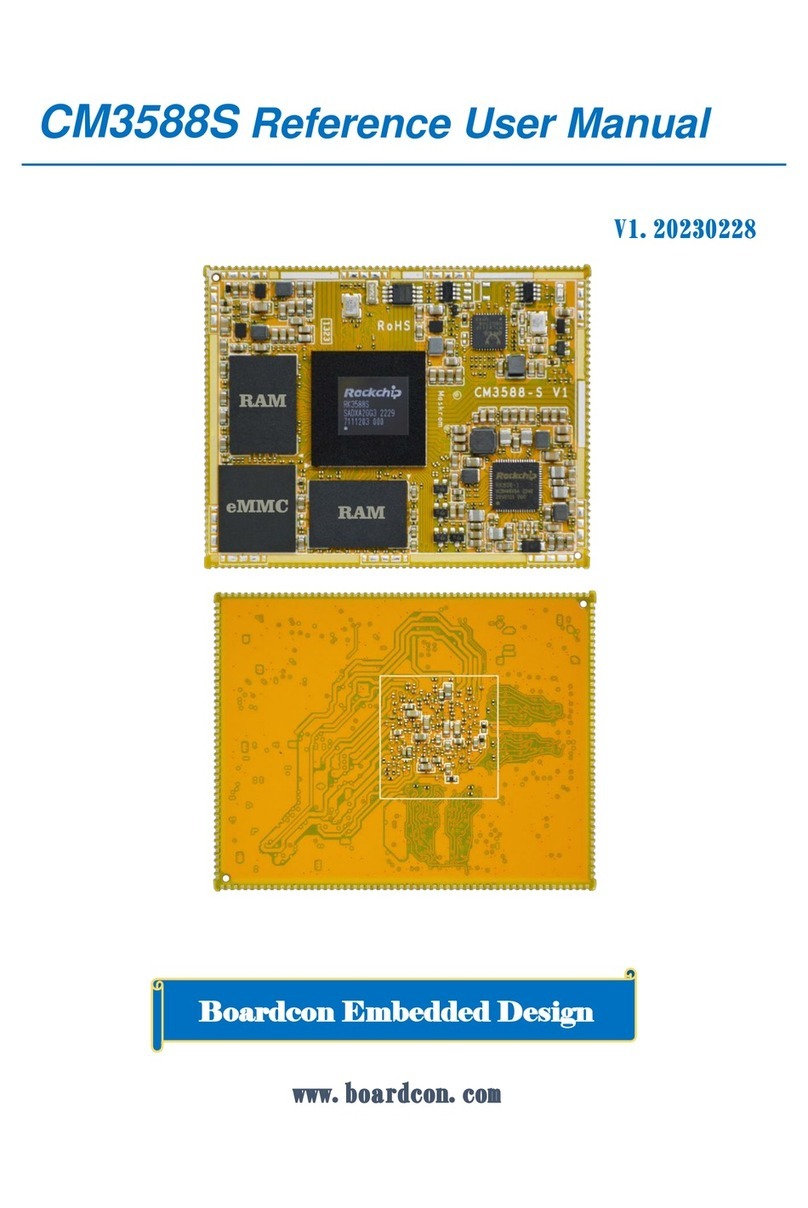
Boardcon Embedded Design
Boardcon Embedded Design CM3588S Reference User Manual
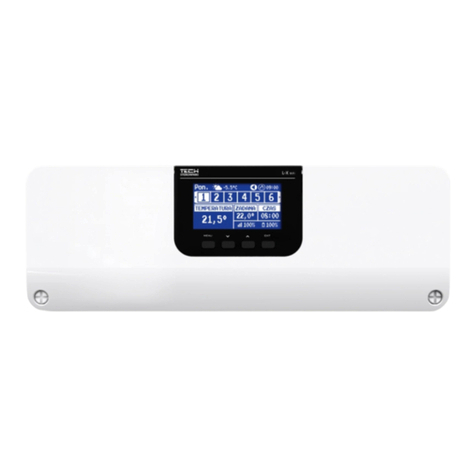
Tech Controllers
Tech Controllers EU-L-X WiFi user manual
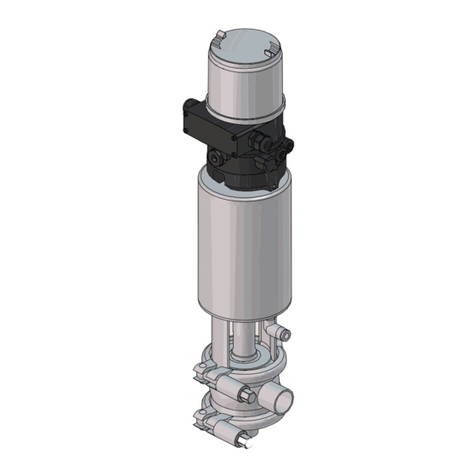
Alfa level
Alfa level CSI RV-ST instruction manual