Reer SV MR0 U User manual

8541100 - 14/10/2022 - Rev.3
1
Installation Instructions
Safety Speed Monitor
SV MR0 U
(Original instructions)

SAFETY SPEED MONITOR SV MR0 U
2 8541100 - 14/10/2022 - Rev.3
Contents
Preliminary note..............................................................................................................................................4
Symbols used ...................................................................................................4
Safety instructions ...............................................................................................5
General requirements on the safety-related functions ........................................5
Operation ............................................................................................................6
General function description .............................................................................6
Switching function: UNDerspeed .......................................................................6
Hysteresis.........................................................................................................7
Initialisation......................................................................................................7
Installation.........................................................................................................................................................8
Mechanical installation of the device ....................................................................8
Electrical Connections ..........................................................................................9
Terminals .........................................................................................................9
Set up of the device ...........................................................................................11
Automatic/Manual mode selections.................................................................14
Enable input: ..................................................................................................17
Technical data SV MR0 U .......................................................................................................................... 18
Definition of the LED’s ....................................................................................19
Faults (blinkings) ............................................................................................19
Additional notes ................................................................................................20
Pulse inputs, pulse pick-ups............................................................................20
Switching outputs: ..........................................................................................20
Restart command:...........................................................................................20
Fault output:...................................................................................................20
UNDerspeed output: .......................................................................................20
Feedback circuit:.............................................................................................20
Checklist after installation..................................................................................20
Warranty............................................................................................................21
EC Declaration of Conformity................................................................................................................. 22
UKCA Declaration of Conformity........................................................................................................... 23

SAFETY SPEED MONITOR SV MR0 U
8541100 - 14/10/2022 - Rev.3 3

SAFETY SPEED MONITOR SV MR0 U
4 8541100 - 14/10/2022 - Rev.3
PRELIMINARY NOTE
The instructions are part of the unit. They are intended for authorised persons
according to the EMC and Low Voltage Directive and safety regulations.
The instructions contain information about the correct handling of the product. Read
the instructions before use to familiarise yourself with operating conditions,
installation and operation. Adhere to the safety instructions.
SYMBOLS USED
Instructions
>
Reaction, result
Cross-reference
This safety alert symbol indicates a potential personal safety hazard.
Failure to comply with instructions bearing this symbol could pose a
very serious risk to personnel.
➔
Information
Supplementary note.

SAFETY SPEED MONITOR SV MR0 U
8541100 - 14/10/2022 - Rev.3 5
Safety instructions
Follow the operating instructions.
•Improper use may result in malfunctions of the unit. This can lead to personal
injury and/or damage to property during operation of the machine. For this
reason note all remarks on installation and handling given in these instructions.
Also adhere to the safety instructions for the operation of the whole installation.
•In case of non-observance of notes or standards, specially when tampering with
and/or modifying the unit, any liability and warranty is excluded.
•The unit must be installed, connected and put into operation by a qualified
electrician trained in safety technology.
•The applicable technical standards for the corresponding application must be
complied with.
•For installation the requirements according to EN 60204 must be observed.
•Connect and lay all cables according to EN ISO 13849-2 D.5.2 (Safety of machinery
- Safety-related parts of control systems).
•In case of malfunction of the unit please contact the manufacturer. Tampering
with the unit is not allowed.
•Disconnect the unit externally before handling it. Also disconnect any
independently supplied relay load circuits.
•After setup the system has to be subjected to a complete function check.
•Use the unit only in specified environmental conditions (→Techical data).
In case of special operating conditions please contact the manufacturer.
•Use only as described below.
GENERAL REQUIREMENTS ON THE SAFETY-RELATED FUNCTIONS
The device complies with the functional and organisational requirements of
EN ISO 13849-1 Performance-Level "e" and of EN 62061 SIL "3".
To maintain Safety Integrity Level (SIL) "3" requirements the two input
sensors shall be independent.
•Common cause failures between measuring sensors must be excluded
by observing an appropriate cable installation (i.e. separate cable paths).
To maintain the category 4 requirements during longer periods of
standstill, a forced dynamisation (t<24h) has to be carried out.

SAFETY SPEED MONITOR SV MR0 U
6 8541100 - 14/10/2022 - Rev.3
Operation
GENERAL FUNCTION DESCRIPTION
The speed monitor is a two-channel pulse evaluation system for safe underspeed
detection.
To do so, it receives the pulse sequences from the pulse pick-ups connected to the
inputs. The module calculate the resulting frequency.
By continuously comparing the input frequency (actual value) and the switch point
(preset value) the evaluation system promptly detects underspeed of the set switch
point, and the output relays switch according to the preset switching function.
The preset value is achieved by setting the 3 switches located in front of the module.
The value can be set in “rpm” or “Hz” unit.
The device complies with the functional and organisational requirements of
EN ISO 13849-1 Performance-Level "e" and of EN 62061 SIL "3".
SWITCHING FUNCTION: UNDERSPEED
The output relays energise when the event occurs (10 seconds timer activated).
The relays remain ON again until the frequency value is greather that the selected
values. The NO contacts of the internal relays are connected in "series" and
connected to the terminals. If both relays are energised, the current paths are closed
so that (e.g.) a power contactor can be controlled.
If the frequency value decreases below the Fuh value the current paths open.

SAFETY SPEED MONITOR SV MR0 U
8541100 - 14/10/2022 - Rev.3 7
HYSTERESIS
The hysteresis determines the distance between the switch point (open the current
paths) and the switch-on point (close the current paths).
The hysteresis value is fixed at 5 %.
If the input frequency falls below the set switch point by 5 %, the relays are de-
energised and the current paths are open.
Example with switch point Fu = 1000 (rpm):
•the current paths are closed when the input frequency is over Fu;
•the current paths will be open when the measured value is lower than Fuh (in this
case 950 rpm).
INITIALISATION
Directly after power on, the SV MR0 U carries out an initialisation comprising a
complete self-test.
After approx. 3 s the SV MR0 U is ready for operation.

SAFETY SPEED MONITOR SV MR0 U
8 8541100 - 14/10/2022 - Rev.3
INSTALLATION
Mechanical installation of the device
Mount the device on a DIN rail in a housing protected against dust and humidity
(min. IP 54).
Leave enough space between the unit and the top and bottom of the
housing to enable air circulation and to avoid excessive heating.
Take into account the internal heating of all units when mounting several
units side by side. The environmental conditions must be observed for
every unit and, in order to avoid overheating, maintain between them one
minimal distance of 2cm.
Fasten the units to the rail.
Lock it first on the upper side of
the rail.
Pull down the locking latch on the
back of the unit.
Press the unit gently and release
the latch until you feel it snap
into place.
To remove a unit, use a
screwdriver to pull down the
locking latch on the back of the
unit; then lift the unit upwards
and pull.

SAFETY SPEED MONITOR SV MR0 U
8541100 - 14/10/2022 - Rev.3 9
Electrical Connections
Voltage supply
sensors:
+24VDC: max. 70mA, protected (by a resettable fuse at T=20 °C), short-circuit
proof, not monitored. Ground: directly connected to the device ground.
Sensors:
PNP sensors, bounce-free.
Feedback circuit:
Yes - Max. 100 mA, short-circuit proof.
Enable input:
Yes - Via the enable input is possible to switch off the limit value monitoring.
Diagnostic output:
Positive switching transistor output. Max. 100mA, short-circuit proof.
Fault output:
Positive switching transistor output. Max. 100 mA, short-circuit proof.
Enable path:
2 x NO - Potential free - Max. 6A (protected with external 3.6 A).
Supply voltage
Connect the supply voltage of the device to terminals L+ and L-.
The nominal voltage is 24VDC. This voltage may vary between 19.2 V and
28.8 V incl. 5% residual ripple.
PELV power supplies are to be used (EN 60204-1).
TERMINALS
➔
The electrical input signals meet the requirements of EN61131.
➔
Terminal tightening torque: 5÷7lb-in (0,6÷0,7 Nm).

SAFETY SPEED MONITOR SV MR0 U
10 8541100 - 14/10/2022 - Rev.3
Terminal connection: "UPPER SIDE"
A1
1
Operating voltage (+24VDC )
2
Sensor1 supply (+24VDC)
3
Sensor1 supply (GND)
4
Sensor1 input
A2
9
Operating voltage (GND)
10
Sensor2 supply (+24VDC)
11
Sensor2 supply (GND)
12
Sensor2 input
A3
17
current path 1A (relay contacts)
18
-
19
-
20
current path 1B (relay contacts)
Terminal connection: "LOWER SIDE"
C1
5
enable plus-switching
6
enable ground-switching
7
Automatic mode selection
8
Manual mode selection
C2
13
transistor output "Fault"
(Fault output (13))
14
transistor output "Underspeed"
15
feedback circuit output
16
feedback circuit input
C3
21
current path 2A (relay contacts)
22
-
23
-
24
current path 2B (relay contacts)
➔
The relay contacts of the module shall be supplied by the same source.

SAFETY SPEED MONITOR SV MR0 U
8541100 - 14/10/2022 - Rev.3 11
Set up of the device
After the first power on of the device it is necessary to configure the Underspeed
Frequency (Fu) using the three decade switches located in front of SV MR0 U.
The switches allow the user to enter the value of the desired preset frequency (as
described below).
Switch point selection description
The switch point is selectable by means of 3 "decade switches" (270° potentiometer,
10 positions, locking).
With P1 and P2 switches numerical values from 01 to 99 can be set (switch 1
with increments of 10, switch 2 with increments of 1).
With a third switch (P3) the multiplier is set. The numerical values are multiplied
with these factors and thus provide the actual switch point value. The
multipliers have the unit "rpm" or Hz".
The unit rpm is only applicable when 1 cam/revolution is present.
To select the desired value, at the power ON, the 3 switches must be in
the “P” position.
In order to not damage the potentiometers use a screwdriver of the
appropriate size.

SAFETY SPEED MONITOR SV MR0 U
12 8541100 - 14/10/2022 - Rev.3
SWITCH
OPERATION / RESULT
LED
Start of configuration:
Set the 3 switches to configuration position 0/P
Switch on the power supply of the device
>
The LED CONF is blinking
Adjust Potentiometer P1 from the
position 0/P to the needed Value
>
During the rotation, the led ENA lapse
by every Step (check with this
visualization the corrected value)
>
System resting in Configuration-Mode
Waiting for input P2
>
The LED CONF is still blinking
Adjust Potentiometer P2 From the
position 0/P to the needed Value
>
During the rotation, the led ENA lapse
by every Step.
>
System resting in Configuration-Mode
Waiting for Input P3
>
The led CONF is still blinking
Adjust Potentiometer P3 From the
position P to the needed Value
>
During the rotation, the led ENA lapse
by every Step
>
Led CONF becomes fixed.
Wait until led CONF is blinking twice
(memorization)
Turn OFF the power
End of configuration
All the 3 switches must be moved at least one time to select a correct value
even if the selected value is “0” (correspondent to the “0/P” position).

SAFETY SPEED MONITOR SV MR0 U
8541100 - 14/10/2022 - Rev.3 13
Examples
The switch point value can only be set when operating voltage is connected to the
device and the three switches are set as indicated (factory setting).
Figure 1 Factory setting
Set P1, P2 and P3 to obtain the switch point value. Examples:
Figure 2 - Example 1: 520Hz
Figure 3 - Example 2: 6700rpm

SAFETY SPEED MONITOR SV MR0 U
14 8541100 - 14/10/2022 - Rev.3
AUTOMATIC/MANUAL MODE SELECTIONS
The selection of the operative mode between Automatic or Manual is made by two
input terminals 4 and 5. In figures below the two possible selections are showed.
Figure 4 - Manual mode selection
Figure 5 - Automatic mode selection

SAFETY SPEED MONITOR SV MR0 U
8541100 - 14/10/2022 - Rev.3 15
Automatic mode
With Automatic Mode selected, just after the power up, a 10 seconds timer
automatically starts and during all these 10 seconds the output relays are closed.
This permits to the motor connected to the relays to reach the selected frequency.
If after these 10 seconds the frequency has been reached, the relays could remain
closed. As soon as the input frequency goes below the selected frequency
(underspeed condition) the relays are de-energised immediately.
When the input 7 is connected to 15 (pulsed output test) and the 8 input is
connected to 24VDC, the Automatic mode is selected.
If a failure is detected (short circuit to 0VDC or 24VDC or that connections have
been removed) the device will pass to the failsafe status.
The 10 seconds initial timer is a temporary suspension of the protective
function. Carefully check your risk analysis in order to assess whether
these function is compatible with your application and what additional
measures have to be taken (i.e. gard lock, protective fence, etc.)
When the relay outputs are connected directly to drive a motor, verify if the
Automatic mode could be used.
In some applications an uncontrolled restart could be dangerous. The
module must be used only as a speed monitoring device and not to directly
control the machine. Carefully check if the automatic mode could be
applied.
Manual mode
With Manual Mode selected, after the power up, the output relays are de-energised
and the module waits for a restart command. When a Restart command is received,
a 10 seconds timer starts and during all these 10 seconds the output relays are
closed. This permits to the motor connected to the relays to reach the selected
frequency.
If after these 10 seconds the frequency has been reached, the relays could remain
closed. As soon as the input frequency goes below the selected frequency
(underspeed condition) the relays are de-energised immediately and the module
waits again for a Restart command via the RESTART input (terminal 7).
This 10 seconds timer is a temporary suspension of the protective function.
Carefully check your risk analysis in order to assess whether these function
is compatible with your application and what additional measures have to
be taken (i.e. gard lock, protective fence, etc.)
>
If it is detected during the initialisation that the input 8 is connected to 15
(pulsed output test) and 7 is open then the Manual mode is selected.
>
In this case the relay path remains open until a Restart signal in Input 7
happens. The Restart signal on input 7 will respond after the falling edge (a
complete transition 0VDC >> 24VDC >> 0VDC ) of this input.

SAFETY SPEED MONITOR SV MR0 U
16 8541100 - 14/10/2022 - Rev.3
The RESTART command must be installed outside the dangerous area in a
position where the dangerous area and the entire work area concerned are
clearly visible.
It must not be possible to reach the control from inside the dangerous area.
➔
The duration of the Restart signal is also checked from a minimum of 300ms
to a maximum of 5sec. Otherwise the command is rejected.
➔
If the Restart command is activated (rising edge or falling edge or both) when
the frequency is between Fu and Fuh the command is also rejected.
When the module is waiting for the restart (clear status) a yellow led (ENA) is
blinking indicated this status.
See figure below for a diagram about the manual mode selections.
Figure 6 - Manual mode/restart diagram

SAFETY SPEED MONITOR SV MR0 U
8541100 - 14/10/2022 - Rev.3 17
ENABLE INPUT:
If several modules with different switch points are used for Underspeed monitoring
of a drive, the devices whose switch point value is not relevant can be "switched off"
by means of the enable input pairs.
The current paths are then closed. In this way the relay status can be controlled via
the enable input after power on of the device.
Activation or deactivation is done by means of an antivalent signal to both enable
inputs.
Figure 7 Enable timing
Enable inputs E1 and E2:
1: The monitoring function of the device is active/not active
2: Enable signals not simultaneous
The signal can be applied via mechanical switches.
In Figure 7 a signal curve is showed.
➔
A maximum of 0.5s of simultaneity between the two input E1 and E2 a is
allowed.

SAFETY SPEED MONITOR SV MR0 U
18 8541100 - 14/10/2022 - Rev.3
TECHNICAL DATA SV MR0 U
Voltage supply
Supply voltage UV
24VDC
Voltage range
80 .. 120 %
Power consumption
< 3 W
Device response time (ms)
(fsel>100Hz)
Tr= 10,7 + 400*(fsel/fin)
fsel = selected frequency (by potentiometers)
fin = input frequency (from proximities)
(fsel<100Hz)
Tr= 14 + (4500/fin)
Inputs
Voltage
24VDC
Current
typ. 6mA / 24VDC (for HIGH level)
Max. input frequency
2,000 Hz
Min Pulse Width for frequency > 500Hz: 100µs.
Min Pulse Width for frequency < 500Hz: 150µs.
Setting range of the limit speed
0.5 … 990 Hz
Speed ranges
10 rpm to 49,500 rpm
Outputs
Output function
2 safety-related switching outputs (floating contacts)
1 fault output “FAULT” (positive switching)
1 diagnostic output “UNDERSPEED” (positive switching)
Output data
FAULT (13) and UNDERSPEED (14)
≤20mA / 24VDC, voltage drop, ≤2V short-circuit proof, not safe
Switching function
Outputs 17-20 and 21-24 open if input frequency below switch point
Transistor outputs 13 open (LOW) in case of internal/external fault
Transistor outputs 14 open (LOW) when current paths are open
Sensor outputs
Voltage
24VDC
Current
≤ 70 mA / 24VDC
Voltage drop
≤ 2 V
Diagnostic and fault outputs
Voltage
24VDC
Current
≤ 20mA / 24VDC
Voltage drop
≤ 2 V
Enabling circuits
Switching capacity
24VDC , 250VAC / 6mA - 6A, resistive Load
Protection housing and terminals
IP 20
Contact protection
3.6A externally
Max. ambient temperature
-40 .. +55 ºC
Max. storage temperature
-40 .. +70 ºC
Max. altitude (above sea level)
2000 m
Relative humidity
10% ÷ 95%
Connection type
terminals blocks
Housing
Housing
108 x 22.5 x 114.5
Standards
EN ISO 13849 / EN 61508
PL e / Cat. 4; SIL 3;
RoHS
conform
TECHNICAL DATA
CONCERNING SAFETY*
PFHd
(IEC 61508)
HFT
(IEC 61508)
MTTFd
(EN ISO 13849-1)
DCavg
(EN ISO 13849-1)
DC13 (2A)@24Vdc
7,69E-09
1 type B
528,73
99,0%
AC15 (1A) @220Vac
8,25E-09
1 type B
496,36
99,0%
AC15 (3A)@220Vac
9,15E-09
1 type B
451,54
99,0%
Device lifetime
20 years
Safe state
Output relay open
Failure response time
5,5 ms
* Considering 1000 relay operations/year

SAFETY SPEED MONITOR SV MR0 U
8541100 - 14/10/2022 - Rev.3 19
LED
COLOUR
IN2
Input IN2
yellow
IN1
Input IN1
Yellow
K2
Indicator Relay K2
Green
K1
Indicator Relay K1
Green
ENA
Indicator Enable
Yellow
CONF
Indicator Configuration
Blue
ON
Power Indicator
Green
FAULT
Fault Indicator
Red
IN2
Input Sensor IN2 lights, when a high signal at the input IN2 was detected.
IN1
Input Sensor IN1 lights, when a high signal at the input IN1 was detected.
K2
Indicator Relay K2 lights when the safety output relay K2 is switched on.
K1
Indicator Relay K1 lights, when the safety output relay K1 is switched on.
ENA
Indicator Enable lights when the Enable inputs are logical on. In configuration mode
this LED blinks rotating the potentiometers (one blink for each step). In clear status
(waiting for a restart command) this led blinks.
(Manual Mode)
CONF
ON when device in configuration mode
Blinking when switches are in P position.
ON
Indicator ON lights, when the safety module is powered.
FAULT
Indicator Fault lights when an internal fault is detected. Indicator Fault is flashing,
when an external fault (i.e. the sensor-test) is detected.
(Faults (Blinkings))
FAULTS (BLINKINGS)
Number of blinkings
Fault
1
MANUAL/AUTOMATIC configuration error
2
Switches incorrect position (frequency selectors)
3
EDM error (With IN1/IN2 flashing simultaneously: IN1 or IN2 absent.)
4
Proximity error
5
Overload outputs 2 (sensor1 supply) or 10 (sensor2 supply) or 13 (fault) or
14 (Underspeed) or 15 (FBK circuit).

SAFETY SPEED MONITOR SV MR0 U
20 8541100 - 14/10/2022 - Rev.3
Additional notes
PULSE INPUTS, PULSE PICK-UPS
➔
The input signals from proximity must be bounce-free.
SWITCHING OUTPUTS:
➔
The NO contacts of the internal relays are connected "in series" so that the
current paths are not closed before both relays have switched.
RESTART COMMAND:
➔
The duration of the Restart signal is checked from a minimum of 300ms to
a maximum of 5sec. Otherwise the command is rejected.
FAULT OUTPUT:
➔
The transistor output "Fault" (13) opens when an internal or external error
occurs. Output characteristics: max. 100mA, short-circuit proof, non-safe.
UNDERSPEED OUTPUT:
➔
The Underspeed output (14) is "HIGH" when the current paths are closed
and "LOW" when the current paths are opened.
Output characteristics: max. 100mA, short-circuit proof, non-safe.
FEEDBACK CIRCUIT:
➔
➔
When Underspeed is detected the current paths open and the external
relays are de-energised. If the feedback circuit (series on external contactor
NC contacts) does not close within 1s there will be an error message
(FAULT led lighted on and K1, K2 led blinking).
If the feedback function is not required, the terminals (15-16) can be
permanently bridged.
Checklist after installation
➔
Directly after power on, the SV MR0 U carries out an initialisation comprising
a complete self-test. Anyway to have the system perfect operation perform
the following checks at start up and at least every one year:
1. Verify that all the cables are correctly inserted and the terminal blocks well screwed.
2. Verify that all the leds (indicators) light on correctly.
3. Verify the positioning of all the sensors connected to SV MR0 U.
4. Verify the correct fixing of SV MR0 U to the Omega rail.
5. Verify that all the external indicators (lamps) work properly.
6. Verify that the potentiometers works correctly.
Table of contents
Popular Monitor manuals by other brands

ViewSonic
ViewSonic VX2406-P-mhd user guide
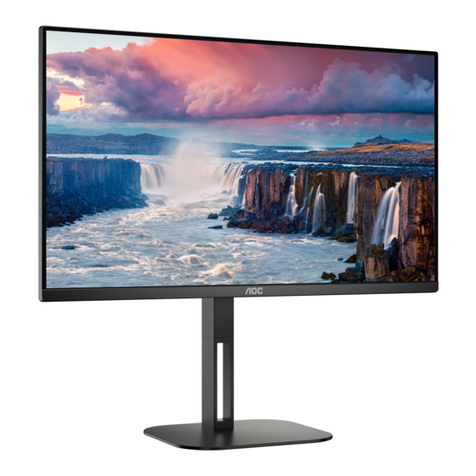
AOC
AOC 24V5C/BK user manual

Kenwood
Kenwood LZ-702W instruction manual
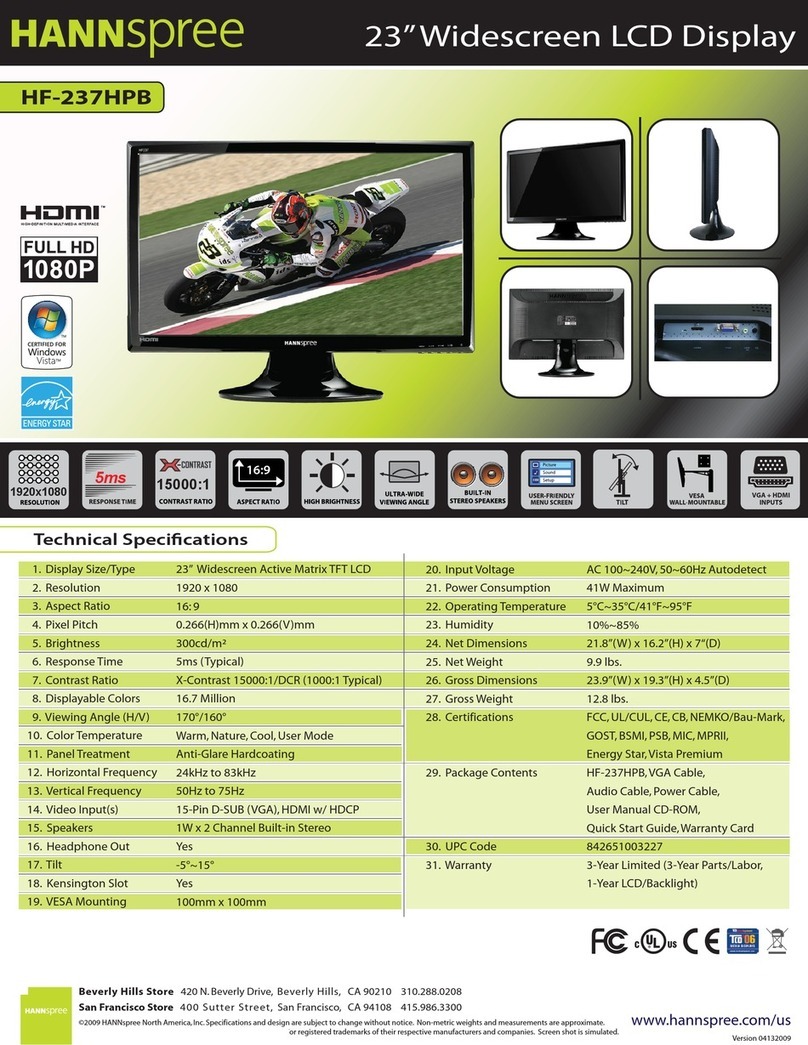
HANNspree
HANNspree HF-237HPB Technical specifications
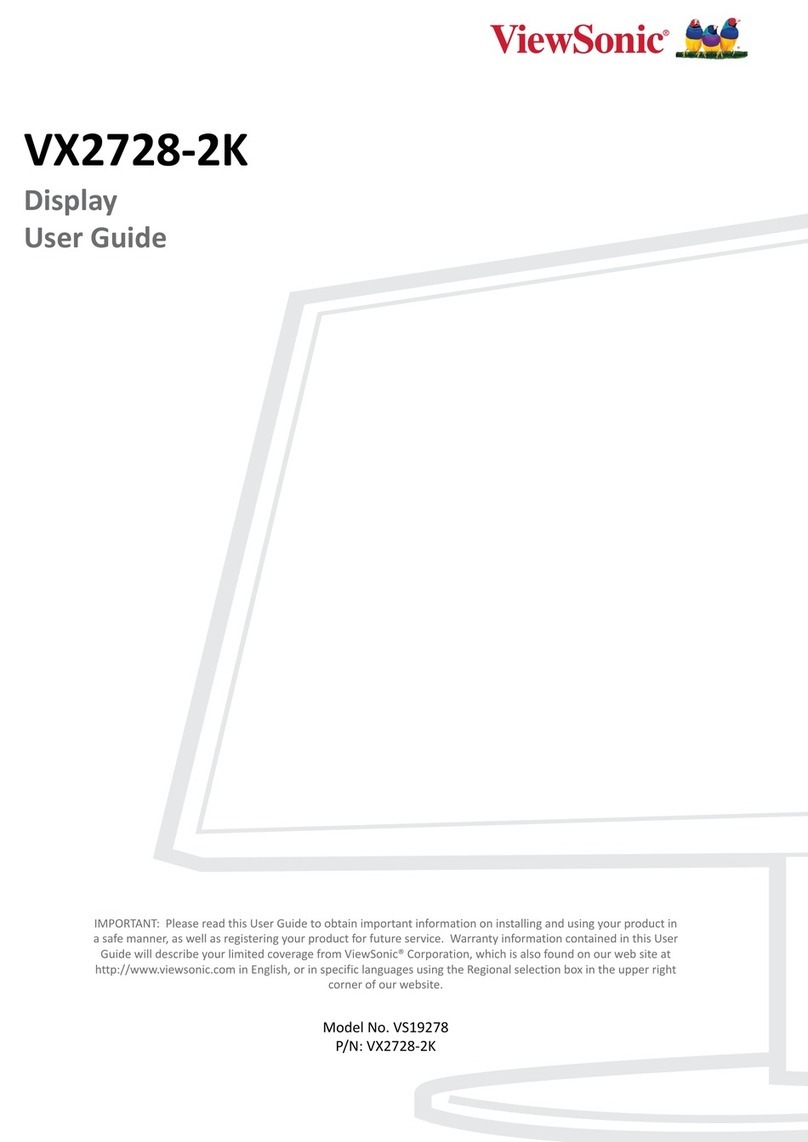
ViewSonic
ViewSonic VS19278 user guide
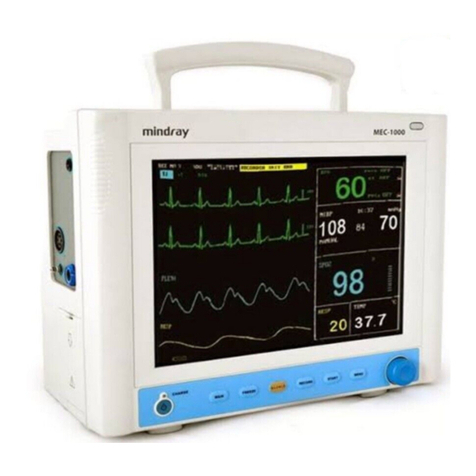
Shenzhen Mindray Bio-Medical Electronics
Shenzhen Mindray Bio-Medical Electronics MEC-1000 Service manual