RHINO RMCS -2303 User manual

DC Servo Drive
for Rhino Encoder DC Servo Motor
(Model No : RMCS –2303)
Operating Manual v1.0

Page | 2
Contents
Introduction –Salient Features................................................................................................................3
Technical specifications and Pin description ............................................................................................ 4
Description of the three modes of Operation and Slave ID settings..........................................................5
How to use the drive: ..............................................................................................................................7
Steps to configure the Drive using Modbus Poll Software : ......................................................................7
STEP 1: Hardware Connection.............................................................................................................. 8
STEP 2: Connect Modbus UART ASCII Drive with Modbus Poll Software............................................. 10
Step 3: Set slave ID in Modbus Poll Software to send and receive Data .............................................. 12
Step 4: Go to Function ....................................................................................................................... 15
STEP 5: Set the Lines per rotation as per the encoder and motor specifications ................................ 17
STEP 6: Program the drive to run in any one of the three modes:...................................................... 19
Mode 0 –Analog Control Mode...................................................................................................... 19
Mode 1 –Digital Speed Control Mode ........................................................................................... 21
Mode 2 –Position Control Mode ................................................................................................... 24
STEP 7: Save and Reset settings in Drive ............................................................................................ 28
Appendix 1 ............................................................................................................................................ 29
Brief Description of all configuration registers. .................................................................................. 30
Troubleshooting: ................................................................................................................................... 36

Page | 3
Introduction –Salient Features
Rhino Motion Controls RMCS-2303 with UART ASCII is a high performance dc servo drive (10–30 V DC) designed
for optimized operation of Rhino DC Servo motors with encoder feedback. This is an amazing cost effective solution
to provide closed loop servo control for various applications. The salient features of this drive:
This drive provides a closed loop speed control for the dc servo system.
The motor programmed speeds are maintained irrespective of the voltages supplied.
Also by using this drive, the rated torque of the motor is available at all speeds and the torque does not
decrease with change in speeds.
It is possible to run the motor in three different modes, analog speed control mode, digital speed control
mode and position control mode.
It has short-circuit protection for the motor outputs, over-voltage and under-voltage protection and will
survive accidental motor disconnects while powered-up.
This drive is configured using MODBUS ASCII protocol via UART.
There is a function in the drive for setting the Modbus Slave Address from 1 to 7 using physical jumpers
(Hardware Setting) or using MODBUS Tool Device (Software Setting).
There are three user modes in the drive :
oMode0 - Analog Control Mode
oMode1 - Digital Speed Control Mode
oMode2 - Position Control Mode

Page | 4
Technical specifications and Pin description
Supply Voltage and Current
Specification
Min
Max
Units
Comments
Supply Voltage
10
30
Volts DC
Between +Ve and GND
Phase Current
0.5
3
Amps
Peak 5 Amps per phase
Pin description of the drive is as per below image:
(Pins 1-7 are used for drive
Configuration and UART control)
Pin No.
Description
8
GND
9
+5VDC
10
ENC_B/Hall W
11
ENC_A/Hall U
12
Hall U
13
W
14
Motor- / V
15
Motor+ / U
16
VDD
17
GND
Pin No.
Description
1
GND
2
RXD
3
TXD
4
ENA
5
ADC
6
DIR
7
BRK
Pin No.
Description
JP1
Jumper 1
JP2
Jumper 2
JP3
Jumper 3
(Pins 8 - 17 are connected to
motor and power supply as
described)
(Jp1 to JP3 are used for
Hardware setting of slave ID)

Page | 5
Description of the three modes of Operation and Slave ID settings
Before we describe the configuration settings and connection diagram of the drive with the motor, we would like to
describe the three modes in which the motor can run and slave ID addressing which are unique features of the drive.
Different Modes of Operation: The drive can be configured in the following three modes by the user -
1. Mode 0 Analog speed control mode :
a. In this mode the speed of the Rhino DC Servo motor can be controlled by an externally connected
Potentiometer.
b. So in this mode the user can increase or decrease the speed manually based on requirement.
c. The drive will provide full torque at all speeds within the range.
d. However the potentiometer has to be connected via a voltage divider to provide a maximum of 3.3
volts so as to not damage the drive.
e. Also the Enable, Brake and direction pins have to be connected as per configuration requirements.
2. Mode 1 Digital Speed control mode with direction control :
a. In this mode the speed and direction of the Rhino DC servo motor is settable / controllable via a
Computer / Arduino Controller board / any other Modbus ASCII compatible device.
b. As in the analog mode here there is no compromise in the torque output of the motor irrespective of
the operational speed and voltage supply and control at higher speeds.
c. This mode is used when multiple motors are to be used to run at exactly the same RPM and same
torque even though the voltage supply might be different.
d. Also in this mode the direction of the motor can be controlled digitally via modbus ASCII commands
to run the dc servo motor in both directions
e. In applications like conveyor belts where speed control is critical and industrial robotic applications
like solar cleaning robots where straight line motion is critical for correction operation of the
equipment, the digital speed control mode can provide optimal results.
3. Mode 2 Position Control Mode :
a. In this mode position of Rhino DC Servo Motor is controllable. This means the user can program
the number of rotations.
b. Also the direction of rotation is to be configured using the Modbus commands
c. The user needs to know the no of lines in the encoder used in the servo motor to use this mode
correctly. The no of lines of encoder also needs to be set in the drive as one of the parameters.
d. The position control mode is suitable in applications where the distance travelled by a robot is to be
fixed or the no of rotations is to be fixed.
Slave ID Addressing: The second unique feature in this drive is that a single controller can be used to control seven
drives at the same time using the physical jumpers. Using the Modbus Poll software, the slave ID can be set from 1 to
247. However, in this driver, we can set slave ID from 1 to 7 using physical jumpers also. As shown in the image
below there are three jumpers marked by a red circle shown in the image below.

Page | 6
The three jumpers JP1, JP2 and JP3 can be set in the configuration as per the below table to provide a physical
slave address to the drive. In the below table a value of ‘0’ corresponds to a state where the jumper is not connected
and a value of ‘1’ corresponds to a state where the jumper is connected. If none of the jumpers are connected the
drive has been programmed to use the Slave ID 7 in default mode.
Slave ID
JP1
JP2
JP3
Image of
connection on the
Drive
1
0
0
1
2
0
1
0
3
0
1
1
4
1
0
0
5
1
0
1
6
1
1
0
7
1
1
1

Page | 7
How to use the drive:
The drive needs to be configured to run in any one of the three modes described in the above section to make a
closed loop control system. The drive can be configured using a PC with Modbus Poll software / Modbus controller /
Arduino Board. We shall be discussing the configuration through Modbus Poll software in this document.
To describe the configuration of the drive for a closed loop system we shall be using the following:
1. PC with Modbus Poll software. ( The modbus poll software can be downloaded from the link -
https://www.modbustools.com/download.html )
2. RMCS-2303 UART ASCII Encoder DC Motor Driver
https://robokits.co.in/motor-drives-drivers/encoder-dc-servo/rhino-industrial-encoder-dc-motor-driver-50w-
with-uart-ascii-compatible-10-to-30-v-10a
3. Encoder DC Servo Motor ( any of the below motors would work with the drive)
https://robokits.co.in/rhino-planetary-encoder-dc-servo
https://robokits.co.in/rhino-ig32-precision-dc-servo
https://robokits.co.in/motors/encoder-dc-servo/high-torque-dc-encoder-motor
https://robokits.co.in/motors/encoder-dc-servo/high-torque-high-precision-motor
4. Industrial Power Supply (below is a recommended supply. It can vary as per your requirements)
https://robokits.co.in/power-supply/industrial-power-supply/24v-10a-industrial-power-supply
5. RKI-1154 CP2102 USB UART Module
https://robokits.co.in/control-boards/interface-boards/cp2102-usb-uart-module
6. External 10K Potentiometer (for analog Speed Control modeonly).
7. Voltage divider from 5V to 3.3V or Voltage converter from 5V to 3.3V (for analog speed control mode only).
Steps to configure the Drive using Modbus Poll Software :
1. Hardware Connection
2. Connect Modbus UART ASCII drive with Modbus Poll Software
3. Set Slave ID in Read/Write Function according to the physical jumper or software settings
4. Go to Function-Write Single register
5. Set the Lines per rotation as per the encoder and motor specifications
6. Set one of the three user Mode as per requirement
7. Save and Reset the settings in drive

Page | 8
STEP 1: Hardware Connection
The hardware connections need to be setup between the motor, drive and PC as per the below block diagram and
the pin out tables provided below. The potentiometer connections need to be provided only to run the driver and
motor in Mode0 analog speed control mode. For analog mode connect ENA (Pin 4) to GND (Pin 8) to enable motor.
Drive Pin outs
Pin No.
Description
8
GND
9
+5VDC
10
ENC_B/Hall W
11
ENC_A/Hall U
12
Hall U
13
W
14
Motor- / V
15
Motor+ / U
16
VDD
17
GND
Motor Pin outs
Motor
Wire Color
GND
Black
VCC(5 V DC )
Brown
ENC_B(Encoder B)
Red
ENC_A(Encoder A)
Orange
M-( Motor-)
Yellow
M+( Motor+)
Green
Power Supply Pin outs
VCC –10 to 30V
GND
Drive Pin outs
Pin No.
Description
8
GND
9
+5VDC
10
ENC_B/Hall W
11
ENC_A/Hall U
12
Hall U
13
W
14
Motor- / V
15
Motor+ / U
16
VDD
17
GND
Motor Pin outs
Motor
Wire Color
GND
Black
VCC(5 V DC )
Brown
ENC_B(Encoder B)
Red
ENC_A(Encoder A)
Orange
M-( Motor-)
Yellow
M+( Motor+)
Green
Power Supply Pin outs
VCC –10 to 30V
GND

Page | 9
Drive Pin outs
Pin No.
Description
1
GND
2
RXD
3
TXD
4
ENA
5
ADC
6
DIR
7
BRK
CP2102 Pin outs
GND
TXD
RXD
Potentiometer Pin outs
GND
GND
Output
Signal
VCC
3.3 V DC
Voltage Divider Pin outs
GND
GND
3.3V
Signal
5 V
5 V DC

Page | 10
STEP 2: Connect Modbus UART ASCII Drive with Modbus Poll
Software
a) Once the Modbus Poll software is installed and the CP2102 is connected, please run the Modbus Poll
software.
b) Proceed to the Connection Tab on the screen and click the same as per below image.
c) Then click on the connect tab which will open the connection settings as per the next image.

Page | 11
d) Please make sure the connection setup settings are as per above for all parameters including the parity and
stop bit.
e) Once the OK button is pressed in the connection setup, the screen should show connected and it should be
as per below image.
f) This concludes STEP 2 of the configuration procedure.

Page | 12
Step 3: Set slave ID in Modbus Poll Software to send and receive Data
Read/Write Definition:
a) Right Click on the Table shown on the home screen of Modbus Poll software. It should pop up a menu as
per below image. Change screenshot
b) Now select the first option Read / write Definition. It should open up a window as per below image.
c) Make all the settings as per above image except the slave ID. The slave ID needs to be set as per your
requirement or physical jumper settings. For a slave ID of 7, please ensure below settings are updated.

Page | 13
1. Slave ID: As per jumper setting as shown on page 4.
2. Function: Select Function as 03 Read Holding registers (4x).
3. Select quantity as 2.
4. Select Display as “Hex”.
d) Once all settings are done, click on apply then select ok.
e) You should receive data in the main table as per below image.
f) The procedure to set Slave ID through software setting is explained below with images. User can set 1 to
247 Slave ID through software setting. For example If user wants to set slave ID 247 then Send Hex value
F7FF (247) to address 0 as per below image.

Page | 14
g) Then with power reset also remove all the three jumpers and enter Slave ID 247 as per below image.
h) Then your drive is connected with Modbus Poll Software and Slave ID is 247.
i) This concludes STEP3 of the configuration procedure.

Page | 15
Step 4: Go to Function
This step is to understand the procedure to write the data to the drive to run it as per the requirement.
a) Go to Functions tab on the home screen and click on “06: Write Single Register” as per the below image.
b) It should open up a screen as per below image.

Page | 16
c) This pop Window enables us to write data in HEX value to the drive in different Address Registers. Eg. When we
write HEX value 0101 in the Address register 2 with a slave ID 7, this command will enable the Digital speed
control mode of the drive.
d) Once the data is input in the window, click send.
e) Response OK message will be displayed as per below.
f) Once the response OK is received, it means that the data setting is complete.
g) The complete list of registers for drive settings and their functionality and examples are provided in Appendix 1.
h) This concludes STEP4 of the configuration procedure.

Page | 17
STEP 5: Set the Lines per rotation as per the encoder and motor
specifications
Lines per rotation concept is very important for Position Control mode. We have two types of quad encoders for
Rhino DC Servo Motors which are :
High Precision encoder
Quad Encoder
Both these encoders are quad encoders. Also the basemotor specs are provided on in datasheet of each motor.
High Precision Encoder
Lines per rotation = 334
For one rotation of encoder, the no of steps = 334 x 4 = 1336 ( As it is quad encoder)
So for 1336 steps, the base motor would move one rotation.
However as the motors are geared motors, the ratio of the gear box determines the rotation of the output
shaft of the motor for each rotation of the base motor.
Eg For a motor of 200 RPM with base motor of 18000 rpm, the gear ratio is 90. Hence for a full rotation of
the output shaft in this motor, the no of steps to be programmed would be 1336 x 90 = 120,240 steps.
Quad Encoder
Lines per rotation = 41
For one rotation of encoder = 41 x 4 = 164( As it is quad encoder)
So for 164 steps, the base motor would move one rotation.
For one rotation at output shaft of motor for Base Motor 18000 RPM and 200 RPM at Output shaft of Motor
One rotation of encoder x gear ratio
Gear ratio = Base Motor RPM / RPM at output shaft of motor
18000 / 200 = 90
So for one rotation of motor at output shaft of motor = 164 x 90 = 14760
The procedure to set lines per rotation in this drive is explained below:

Page | 18
a) Go to Functions tab on the home screen and click on “06: Write Single Register” as per the below image.
b) Send lines per rotation Hex value to address 10. For High Precision encoder motor lines per rotation is 334
so send Hex value 14E(334) to address 10 as per below image.
c) This concludes STEP 5 of the configuration procedure.

Page | 19
STEP 6: Program the drive to run in any one of the three modes:
oMode0 - Analog Control Mode
oMode1 - Digital Speed Control Mode
oMode2 - Position Control Mode
Mode 0 –Analog Control Mode
a) For analog control mode we need to have the proper hardware connections as per STEP 1 and set the
values in address 2 as per below table which is described from point no. b.
Slave ID
Address
Value(hex)
Description
7
2
0000
Enables mode 0 (analog mode)
7
2
0001
Enable the motor
b) To prgram the address click the functions tab and click write singe register as per below image.
c) This should open up a window as per below image. Write the HEX value 0000 to address 2 to enable mode
0 and click send.

Page | 20
d) After receiving response OK in the window, we need to enable motor.
e) Send Hex value 0001 to address 2 as per below image to enable the motor.
f) For analog mode connect external potentiometer to change speed of motor.
g) Connect enable (Pin 4) of drive to GND (Pin 8) to enable motor in analog mode.
h) User can change direction of motor in analog mode to connect the Direction (Pin 6) to the GND (Pin 8).
i) User can lock motor by connecting brake (Pin 7) to GND (Pin 8).
j) This concludes the settings for Mode0.
The Gain and acceleration of the motor can be set as per described in Apendix 1. If you intend to use the motor
in Mode0 as described above, please skip to Step 7 to save settings.
Other manuals for RMCS -2303
1
Table of contents
Popular Servo Drive manuals by other brands
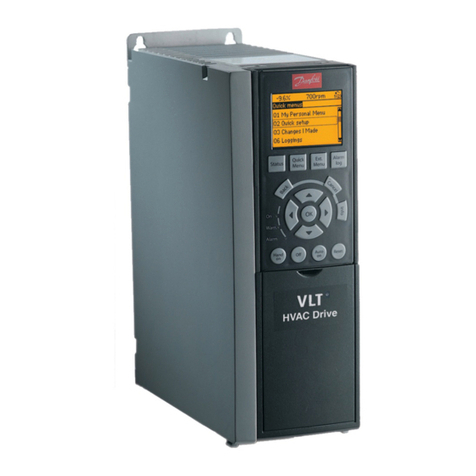
Danfoss
Danfoss VLT HVAC Drive FC 102 operating instructions
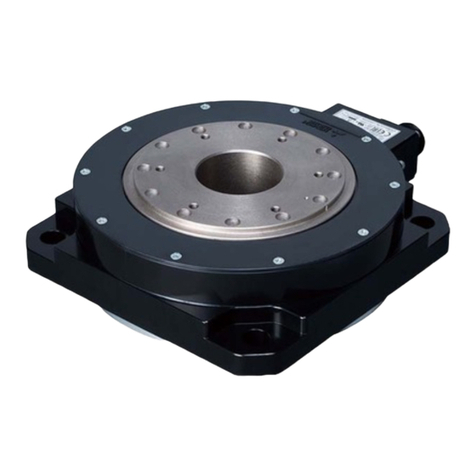
Mitsubishi Electric
Mitsubishi Electric TM-RFM instruction manual
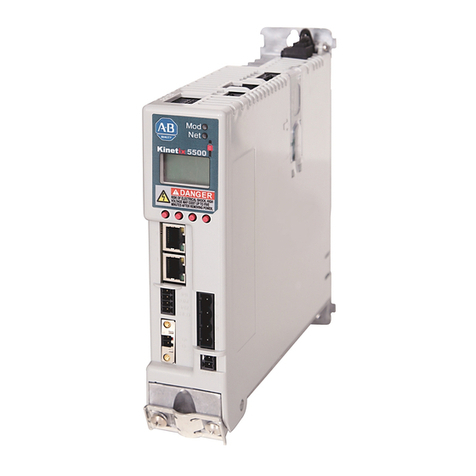
Rockwell Automation
Rockwell Automation Allen-Bradley Kinetix 5500 installation instructions
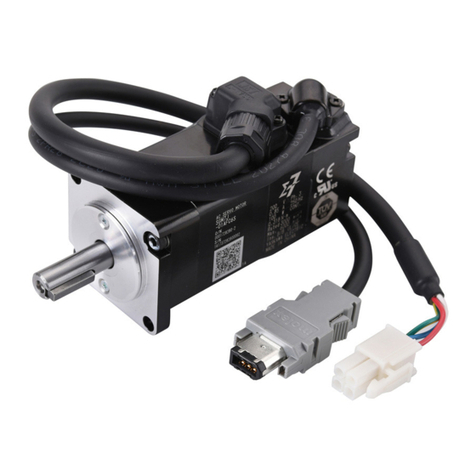
YASKAWA
YASKAWA E Series product manual
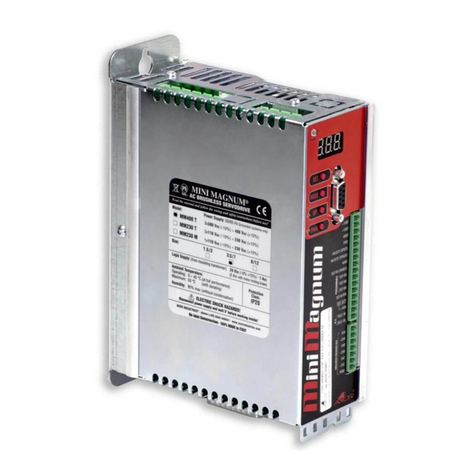
AXOR Industries
AXOR Industries MiniMagnum Series Service manual
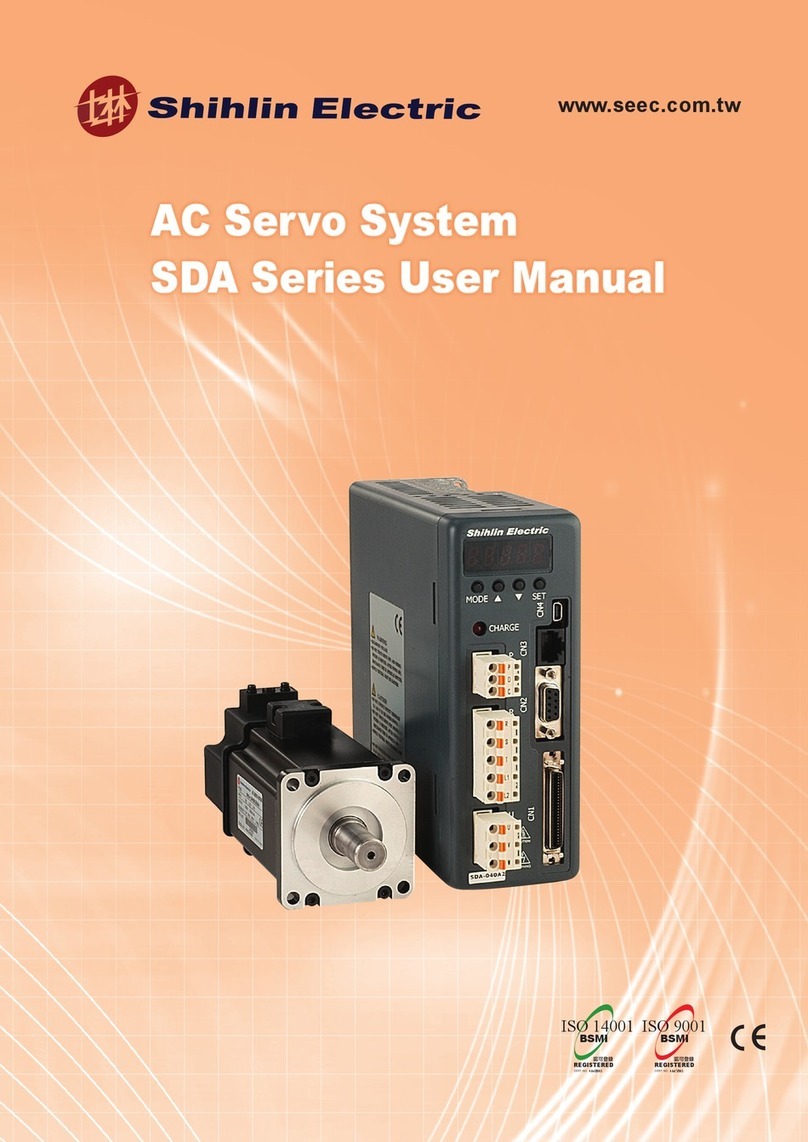
Shihlin electric
Shihlin electric SDA Series user manual

Danaher Motion
Danaher Motion S200-CNS Hardware installation manual

Astor
Astor Astraada SRV-63 series Operation manual
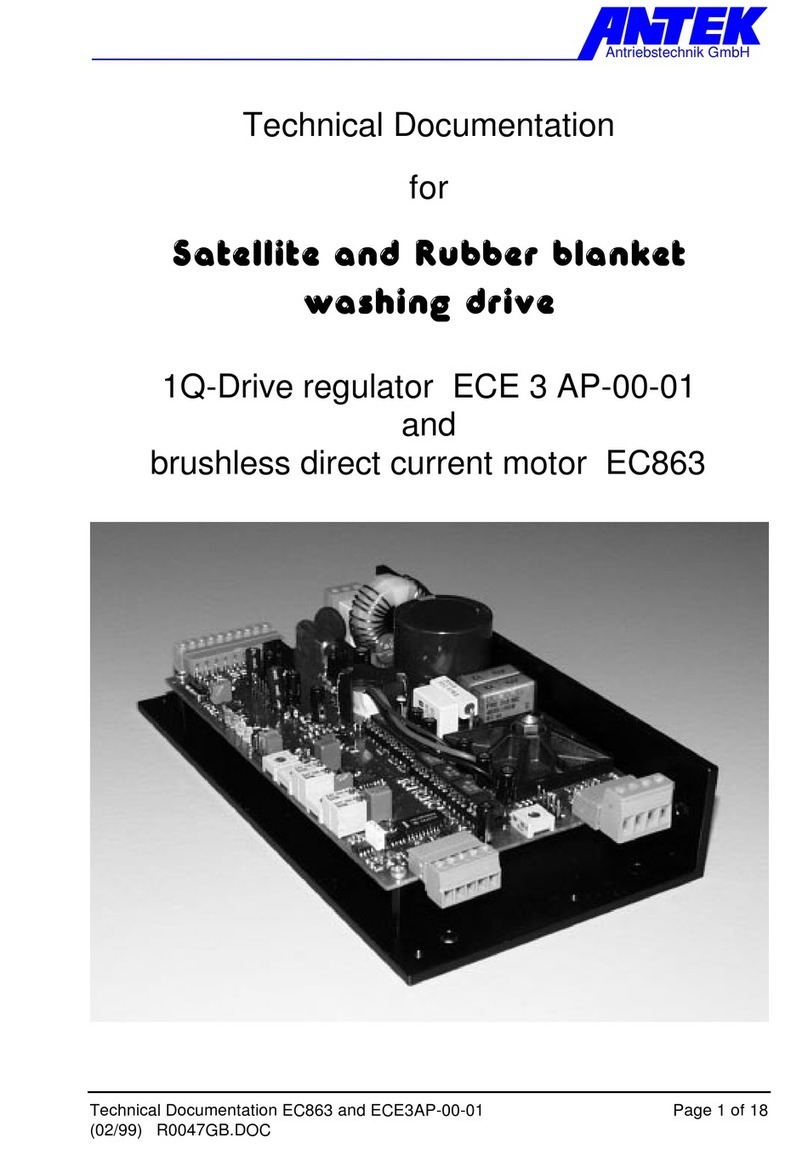
ANTEK
ANTEK ECE863 Series Technical documentation
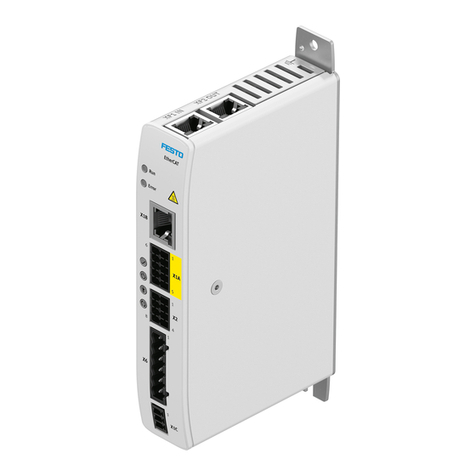
Festo
Festo CMMT-ST-C8-1C-...-S0 Series manual

Geckodrive
Geckodrive G320X manual
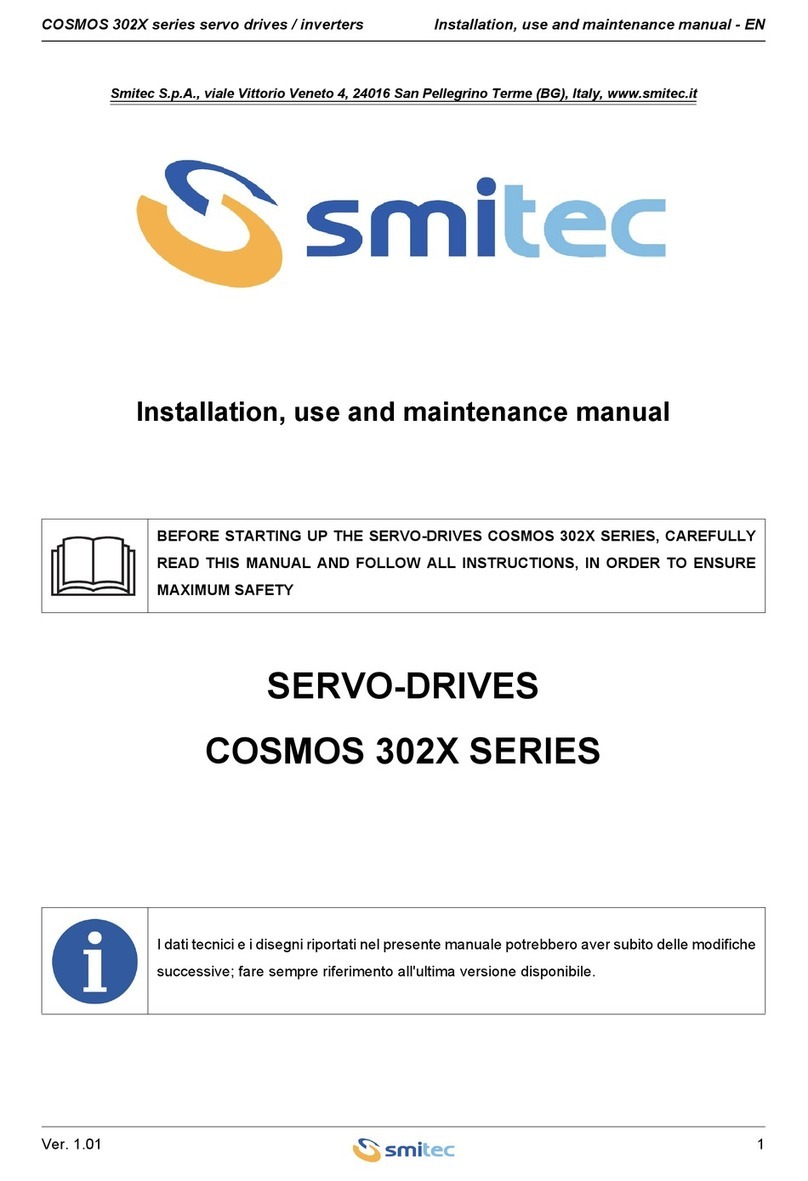
Smitec
Smitec COSMOS 302 Series Installation, use and maintenance manual