Shihlin electric SDA Series User manual

Inverter
Servo motor
and drive
Temperature
Controller
Shihlin Electric
Factory Automation Products
Human Machine Interface
Area Distributor
Head Office:
16F, No. 88, Sec. 6, ChungShan N. Rd.., Taipei, Taiwan, 111
TEL:+886-2-2834-2662 FAX:+886-2-2836-6187
HsinFun Factory (Taiwan):
No.234, Chung Lun, Hsin Fun, HsinChu, Taiwan, 304
TEL:+886-3-599-5111 FAX:+886-3-5907173
SuZhou Factory(China):
No.22, HuoJu Rd., SuZhou Tech. District, JiangSu, China. 215009
TEL:+86-512-6843-2662 FAX: +86-512-6843-2669
Shihlin Electric & Engineering Corporation
Copyright reserved
www.seec.com.tw
ISO 14001
BSMI
REGISTERED
認可登錄
CERT . NO. 4A4E003
ISO 9001
BSMI
REGISTERED
認可登錄
CERT . NO. 4A4Y003
SDA Series User Manual
AC Servo System
SDA Series User Manual

I
Contents
1. Product Inspection and Model Descriptions··············································································1
1.1 Summary·····················································································································1
1.2 Product Inspection·······································································································1
1.3 Servo Actuator Appearance and Panel Descriptions····················································7
1.4 An Overview of the Servo Actuator Operation Modes ················································8
1.5 Circuit Breaker and Fuse Specifications and Recommendations·······································9
2. Installation ····························································································································· 10
2.1. Notices and Storage Methods··················································································· 10
2.2. Installation Environment Conditions········································································ 10
2.3. Installation Direction and Spacing ··········································································· 11
3.Signals and Wiring ················································································································· 13
3.1.Main Circuit Power Source and Peripheral Device Connections······························ 13
3.1.1.Peripheral Device Connection Wiring (Under 1KW)····································· 13
3.1.2.Peripheral Device Connection Wiring (Above 1.5KW) ································· 14
3.1.3.Descriptions of Actuator Connectors and Terminals ······································ 15
3.1.4.Power Source Wiring····················································································· 17
3.1.5.Connector Specifications of the Leadout Wire of Motor U, V &W ··············· 18
3.1.6.Connector Specifications of the Lead-out Wire of the Encoder ····················· 20
3.1.7.Wiring Materials···························································································· 22
3.2.Servo System Functional Block Diagram································································· 24
3.3.CN1 I/O Signal Wiring and Descriptions ································································· 26
3.3.1.CN1 Terminal Layout ···················································································· 26
3.3.2.CN1 Terminal Signal Descriptions ································································ 28
3.3.3.Interface Wiring Diagram ·············································································· 43
3.3.4.DI and DO Signals Assigned by the Users····················································· 47
3.4.CN2 Encoder Signal Wiring and Descriptions ························································· 49
3.5.CN3 Communication Port Signal Wiring and Descriptions······································ 51
3.6.CN4 USB Communication Port ··············································································· 52
3.7.Standard Wiring Method ·························································································· 53
3.7.1.Built-in single-axis Position Control (PR) ····················································· 53
3.7.2.Position control (Pt Mode) Wiring································································· 54
3.7.3.Speed Control (S Mode) Wiring ···································································· 55
3.7.4.Torque Control (T Mode) Wiring··································································· 56

II
4.Panel Display and Operation·································································································· 57
4.1.Panel Components···································································································· 57
4.2.Flow Process Display······························································································· 58
4.3.Status Display ·········································································································· 59
4.4.Abnormal Alarm Mode ···························································································· 62
4.5.The Diagnostic Mode······························································································· 63
4.5.1.External I/O Signal Indication ······································································· 64
4.5.2.Forced Output of Output Signals (DO Forced Output) ·································· 64
4.5.3.JOG Operation······························································································· 65
4.5.4.Position Operation Test·················································································· 68
4.5.5.Analog Input Auto-offset ··············································································· 69
4.5.6.Inertia Approximation Analysis Operation····················································· 69
4.6.The Parameter Mode ································································································ 72
5.Operation ······························································································································· 74
5.1.Checklist before Operation······················································································· 74
5.2.No-load Test············································································································· 75
5.2.1.No-load Test ·································································································· 75
5.2.2.No-load Positioning Test················································································ 78
5.3.Tunning Process ······································································································· 80
5.3.1.Tunning Methods and Types·········································································· 80
5.3.2.Auto-Tunning Mode ······················································································ 82
5.3.3.Manual-Tunning Mode ·················································································· 88
5.4.Parameter Setup and Operation of the Position Mode ·············································· 90
5.5.Parameter Setup and Operation of the Speed Mode ················································· 93
5.6.Parameter Setup and Operation of the Torque Mode················································ 95
6.Control Function ···················································································································· 98
6.1.Control Mode Option ······························································································· 98
6.2.Torque control mode ································································································ 99
6.2.1.Analog Torque Command Proportioner······················································· 100
6.2.2.Analog Torque Command Offset Adjustment ·············································· 100
6.2.3.Smoothing the Torque Commands······························································· 101
6.2.4.Torque Restriction of the Torque Mode ······················································· 102
6.2.5.Speed Restriction of the Torque Mode························································· 103
6.3.Speed control mode································································································105

III
6.3.1.Speed Command Options ············································································ 106
6.3.2.Analog Torque Command Proportioner······················································· 107
6.3.3.Smoothing the Torque Commands······························································· 108
6.3.4.Torque Restriction of the Speed Mode··························································111
6.3.5.Speed Loop Gain ························································································· 113
6.3.6.Resonance Suppression Filter ······································································ 115
6.3.7.Gain Switch Function ·················································································· 118
6.4.Position control mode·····························································································124
6.4.1.External Pulse Command (Pt Command) ···················································· 125
6.4.2.Internal Position Command (Pr Command)················································· 126
6.4.3.Smoothing the Position Commands ····························································· 128
6.4.4.Electronic Gear Ratio ·················································································· 130
6.4.5.Torque Restriction of the Position Loop ······················································ 133
6.4.6.Position Loop Gain······················································································ 133
6.5.Combined Control Mode························································································134
6.5.1.Position / Speed Combined Mode································································ 136
6.5.2.Speed / Torque Combine Mode···································································· 137
6.5.3.The Torque / Position Combined Mode ······················································· 137
6.6.Othe Functions ·······································································································139
6.6.1.Regenerative Resistor Selection··································································· 139
6.6.2.Analog Monitoring Function ······································································· 141
7.Parameter Setup ···················································································································145
7.1.Parameter Setup ·····································································································145
7.2.Parameter List ········································································································147
7.3.Parameter Group Descriptions ···············································································163
8.Communication Function····································································································· 198
8.1.Communication Hardware Interface and Wiring ····················································198
8.2.Communication Setup Parameter ···········································································201
8.3.MODBUS Communication Protocol······································································202
8.4.Communication Parameter Writing and Reading ···················································214
9.Basic Check and Maintenance ·····························································································222
9.1.Basic Check ···········································································································222
9.2.Maintenance···········································································································222
9.3.Component Service Life·························································································222

IV
10.Abnormal Alarm Troubleshooting························································································ 224
10.1.The Abnormal Alarm List and the Resolution ························································224
10.2.Abnormal Causes and Handling·············································································225
11.Product Specifications·········································································································· 233
11.1.Servo Actuator Specifications ················································································233
11.2.Actuator Appearance and Dimensions····································································235
11.3.Low Inertia Servo Motor Standard Specifications SMA-LR30A Series····238
11.4.Medium Inertia Servo Motor Standard Specifications SMA-MR20 Series239
11.5.Low Inertia Servo Motor Appearance and Dimension············································240
11.6.Permissive Load of Low Inertia Servo Motor Outputted Axle ·······························241
11.7.Medium Inertia Servo Motor Appearance and Dimension ·····································242
11.8.Permissive Load of Medium Inertia Servo Motor Outputted Axle ·························244
11.9.Axial Precision·······································································································245
11.10.Electromagnetic Compatibility Filter (EMC Filter)················································246
12.Features ·····························································································································247
12.1.Low Inertia Torque Features···················································································247
12.2.Medium Inertia Torque Features ············································································248
12.3.Overload Protection Features ·················································································249
13.Production Application Examples ························································································252
13.1.Internal positioning Mode Example ·······································································252
13.2.Return to Origin ·····································································································256
14.Appendix A Accessories······································································································· 266

1
1. Product Inspection and Model Descriptions
1.1 Summary
The control models for Shihlin Multipurpose AC Servo can be classified into the single
model or the combined model. There are for modes for the single model: the position mode
(terminal input), the position mode (internal register), the speed mode, and the torque
mode. The combined model has five modes: the position mode (terminal input) / the speed
mode, the positioning mode (terminal input) / the torque mode, the position mode (internal
register) / the speed mode, the position mode (internal register) / the torque mode, and the
speed mode / the torque mode.
Therefore the models are suitable for the general mechanery industry that requires a
high precision and a smooth speed control, or places that requires machine tools and
tension control.
Shihlin servo not only has RS-232 and RS-485 serial communication function but also
is equipped with USB communication functions that are the most convenieint ond on the
communication market. A computer with Shihlin communication software is available for
installation and quick parameter setups, test operation, conditioning monitoring, and gain
control adjustment.
Shihlin servo is also equipped with automatic tuning functions; the gain servo (Gain)
can perform automatic adjustment functions in coordination with machanary. For the
encorder, the encoder of Shihlin servo has a 2500 pulse/rev resolution (or 10,000 pulse/rev
after four-fold encoding) and offers a high precision control.
1.2 Product Inspection
Please review he following item to avoid product transport or human caused negligence.
Do the motors and controllers have any loosening or untightened screws?
Check product serial number on the name tag of the motor and the actuator to
determine whether they are the intened product of the purchase. The serial
number are listed in the serial number reference table provided in the following
chapter.
Check if there is any scratch or damage on the appearance of the motor and the
actuator.

2
Turn the motor axis by hand. A smooth turning indicates a normal motor axis.If the
motor has an attached electromagnetic brake, then the motor axis will not be
turned smoothly by hand.
Please contact the agent for solutions if any of the above issue happens.
A complete original set of servo components from the manufacturer should include:
(1) A servo actuator and a servo motor.
(2) A UVW motor power line with one side the three UVW line connected to the UVW
master block of the actuator while the other side connected to the UVW master
block on the motor. The green ground wire should be locked to the ground of the
actuator(An item for purchase).
(3) A communication control wire for the encoder; one side attached to CN2 of the
controller while the other side attached to the encoder master block of the
motor(An item for purchase).
(4) The RS232 wire of communication; one side attached to CN3 of the actuator while
the other side attached to the COM PORT of the computer(An item for purchase).
(5) The USB wire of communication; one side attached to CN4 of the actuator while
the other side attached to the USB PORT of the computer(An item for purchase).
(6) 50 PIN connector for CN1(An item for purchase).
(7) 5 PIN quick connection terminal; for 1 KW servos (R, S, T, L1, and L2).
(8) 3 PIN quick connection terminal; for 1KW servos (P, D, and C).
(9) 5 PIN quick connection terminal; for 1.5 KW servos (P, N, R, S, and T).
(10) 5 PIN quick connection terminal; for servos 1.5KW or above (P, N, R, S, and T).
(11) 3 PIN quick connection terminal (U, V, W).
(12) Installation manual.
(13) Shihlin User Manual (an electronic verision can be downlowed online).(An item for
purchase).

3
A Reference for Product Serial Number
Coding Rules for Shihlin Servo Motor Serial Number
(一) Coding Method
S M A ─□ ○○○ R△△ A □ □
└─┬─┘ │ │ └─┬─┘ └─┬─┘ │ │ └── Axis Mode
│ │ │ │ │ │ └──── Brake and Oil Seal
│ │ │ │ │ └────── Encoder Resolution
│ │ │ │ └───────── Rated Rotation Speed
│ │ │ └───────────── Motor Capacity
│ │ └──────────────── Inertia Class
│ └────────────────── Product Code
└───────────────────── Servo Motor Code
(二) Descriptions on Coded Items
(1) Servo Motor Code: SM denotes servo motor.
(2) Product Code: A.
(3) Inertia Class: The codes are assigned according motor inertia and frame size:
Code Class
LLow Inertia
MMedium Inertia
(4) Motor Capacity: Motor Output Power.Three digits are used to represent the
the motor’s output power multiplied by 1/10: For products with power above
10,000W, a letter K is assigned to be the third digit, representing 1,000W.
For example: 020 denotes 200W;
150 denotes 1,500W;
350 denotes 3500W,
and so forth.

4
(5) Rated Rotation Speed: The rated output speed of the motor. Three-digit Coding:
The first digit is represented by R, the second digit is
represented by 20 (for 2,000rpm) or 30 (for 3,000rpm).
For example, R20 denotes for a 2000rpm of amotor’s rated rotation speed.
(6) Encoder Resolution: It is represented by a capital letter A. The encoder
resolution of Shihlin Motor Encoder is an incremental type of 2,500ppr.
(7) Brake and Oil Seal: Whether a motor has an included brake and oil seal is
denoted by the following codings:
Coded
Item A(B) (C) (D)
Brake No Yes No Yes
Oil Seal No No Yes Yes
(8) Shaft Mode: It describes the style of the motor shaft; K denotes the inclusion
of a slot whereas no mark denotes the absence of a slot.
(三)Coding Example:
Example 1: The serial number for a 200W motor with low inertia, rated
rotation speed 3000rpm, no brake, no oil seal, and no slot for the axis would be:
SMA-L020R30AA
Example 2: The serial number for a 1500W motor with medium inertia,
2000rpm, brake included, no oil seal, and has an axis with slot would be:
SMA-M150R20ABK

5
The Coding Rules for Servo Actuator Serial Number
(一) Coding Method
S D A ─ ○ ○ ○ △ △
└─┬─┘ │└──┬──┘ └─┬─┘
│ │ │ └──── Type of the Electric Power
│ │ └─────────── Motor Capacity
│ └────────────────── Product Code
└─────────────────────── Actuator Code
(二) Descriptions on Coded Items
(1) Actuator Code: SD represents the servo actuator.
(2) Product Code: A.
(3) Motor Capacity: Motor Output Power.Three digits are used to represent the
the motor’s output power multiplied by 1/10: For products
with power above 10,000W, a letter K is assigned to be the
third digit, representing 1,000W.
For example: 020 denotes 200W;
150 denotes 1,500W;
350 denotes 3500W,
and so forth.
(4) Power Specifications: Input power specifications
A2:3-phase,220V
(三) Examples:
Example 1: The code given to a 200W motor for actuator that needs a
three-phase 200V electric power would be:
SDA-020A2

6
The Reference Table for Servo Actuator and Motor Models
Servo Actuator Corresponding Servo Motor
100W
SDA-010A2 SMA-L010R30AB
200W SDA-020A2 SMA-L020R30AB
400W SDA-040A2 SMA-L040R30AB
500W SDA-050A2 SMA-M050R20AD
750W
SDA-075A2 SMA-L075R30AB
1000W SDA-100A2 SMA-M100R20AD
1500W SDA-150A2 SMA-M150R20AD
2000W SDA-200A2 SMA-M200R20AD
3500W SDA-350A2 SMA-M350R20AD

7
1.3 Servo Actuator Appearance and Panel Descriptions
電源指示燈:
若指示燈亮,表示此時伺
服驅動器尚有高電壓
內外部回生電阻:
(A)
使用外部回生電阻時,P、
C端接電阻,P、D端開路
(B)
使用內部回生電阻時,P、
C端開路,P、D端需短路
控制板迴路電源:
L1、L2供給單相
200~230Vac,50/60Hz電源
主迴路電源:
R、S、T連結在商用電源
AC200~230V,50/60Hz電
源
伺服馬達輸出:
與馬達電源接頭U、V、W
連接,不可與主迴路電源
連接,連接錯誤時會造成
伺服驅動器損毀
散熱座:
固定伺服器及散熱之用途
顯示部:
由5位數七段顯示LED顯示
異警、伺服狀態、參數等等
操作部:
操作狀態有功能、參
數等等的設定
MODE:模式之選擇
:顯示板之值加一
:顯示板之值減一
SET:確認設定鍵
USB連接器:
連接個人電腦與控制器
RS-232/RS-485連接器:
連接個人電腦與控制器
編碼器連接器:
連接伺服馬達Encoder之連
接器
控制連接器:
可與外部控制I/O連接或
是可程式控制器連接
接地端
Ground
Display Section:
5-digit, 7-way LED displaying
alarms, server status,
parameters, etc.
Operation Section:
Operation status includes setups
for function, parameter, etc.
MODE: Mode options
▲: Add one unit to the value displayed
on the display panel
▼: Subtract one unit from the value
displayed on the display panel
Set: The confirm button
USB connector:
Connect to PC and controller.
RS-232 / RS-485 Connector:
Connect to PC and controllers
Encoder connector:
It is to connect to the encoder
of server motor.
Connector Control:
Can be connected to
the external control I/O
connector or to the
program controller.
Power Indicator Light:
If the light is on, it indicates
that the server actuator still
has a high voltage.
Internal/External Regenerative
Resistor:
a) When using the external regenerative
resistor, connect P and C terminals to
the resistor, and make P and D the
open circuits.
b) When using the internal regenerative
resistor, make P and C terminals the
open circuits, and make P and D
terminals the short circuits.
Control Panel Circuit Power:
L1 and L2 for single-phase
200 – 230 Vac, 50/60 Hz
Power Source
Server Motor Output:
Connect to U, V, and W ports of
the motor power. Cannot be
connected to the main circuit
power. Wrong connection can
cause servere actuator damages.
Main Circuit Power:
Connect R, S, and T to
commercial electrical
power of AC200 – 230V
and 50/60Hz.
Cooling Pad:
Fix the server and cool
down the temperature.

8
1.4 An Overview of the Servo Actuator Operation Modes
Shihlin Actuator provides multiple operation mode for the users to select. More detailed
descriptions are listed as follows:
Mode Code Description
Single Mode
Position Mode
(Internal
Register)
Pt
The actuator accepts position commands for controlling
the motor to reach the target position. Position
commands are inputted by the terminal block, and the
signals are in the form of pulse waves.
Position Mode
Internal
Register
Pr
The actuator accepts position commands for controlling
the motor to reach the target position. Position
commands are given by the internal register (eight sets
of registers). The user can use DI signals to select the
register code.
Speed Mode S
The actuator accepts speed commands for controlling
the motor to reach the target rotation speed. DI signals
can be used to select the speed command to be analog
voltage command or internal speed command (seven
sets of register).
Torque Mode T
The actuator accepts torque commands for controlling
the motor to reach the target torque. Torque commands
are provided by analog voltage commands.
Combined Model
Pt-S The switch for Pt to S or vice versa is carried out by DI
signals.
Pt-T The switch for Pt to S or vice versa is carried out by DI
signals.
Pr-S The switch for Pt to S or vice versa is carried out by DI
signals.
Pr-T The switch for Pt to S or vice versa is carried out by DI
signals.
S-T The switch for S to T or vice versa is carried out by DI
signals.
Mode selection can be completed by setting up the parameter PA 01. After modifying the
parameter PA01, restart the electric power to complete the modification.

9
1.5 Circuit Breaker and Fuse Specifications and Recommendations
Circuit breaker and fuse specifications for Shihlin servo actuator:
Actuator Serial No. Fuse Circuit Breaker
SDA-010A1 5A 5A
SDA-020A1 5A 5A
SDA-040A1 20A 10A
SDA-050A1 20A 10A
SDA-075A1 20A 10A
SDA-100A1 25A 15A
SDA-150A1 40A 20A
SDA-200A1 60A 30A
SDA-350A1 80A 30A

10
2. Installation
2.1.Notices and Storage Methods
Do not install the product on inflammable matters or close to inflammable matters.
Do not over tighten the wire between the actuator and the motor.
Do not place heavy objects on top of the actuator.
Be sure to tighly lock the fixing spots of the actuator when fastening the actuator.
Install the actuator at a location that can bearthe weight of the actuator.
Align the axle of the motor and the axle of the device.
No oil-like inflammable objects or conductive bjects such as metal pieces or screws are
allowed inside the actuator.
Thicken thicken the wire between U, V, W and the encoder if the wiring between the
actuator and the motor is more than 20 m.
Do not clogged the vent of the actuator, or breakdowns may happen.
Do not drop or clash the actuator.
Do not run the actuator if the actuator has been damaged.
Please refer to Section 11.1 and 11.3 for actuator and motor storage details.
2.2. Installation Environment Conditions
The ambient temperature for Shihlin actuator is between 0℃and 55℃. If the
operation environment is higher than 45℃, place the actuator in a place with good air
circulation or with air conditioning.For a long-term operation, place the product in an
environment with temperature below 45℃to ensure the reliability of the product.If the
product is installed inside an electric box, make sure that the size and the ventilation of the
electric box can prevent over-heating of the electronic components inside the electric
box.Make sure that machine vibration will not affect the electronic devices of the electric
box.In addition, meet the following criteria for using Shihlin servo:
Avoid locations with inflammable or high-heat devices.
Avoid locations with floating dust or metal particles.
Avoid locations with corrosive, inflammable gases and liquids.
Avoid locations with water drops, steam, dust, or oily dust.

11
Avoid locations with electromagnetic interference.
Select solid, vibration-free locations.
2.3. Installation Direction and Spacing
Note:
Follow the regulations for installation direction to avoid causing servo breakdowns.Provide
a good circulation cooling by keeping sufficient space between Shihlin AD servo actuator
and objects or baffle board/walls when installing Shihlin AD servo actuator to avoid
breakdowns.Do not seal the suction and the ventilation opening or place the AD servo
actuator upside down during the installation to avoid breakdowns.
Installation Diagram:
To achieve a lower wind resistance of the heat-dissipation fan for a more effective heat
removal, follow the spacing recommendation for installing one or multiple AD servo
actuator (See the fiure below).

12
50mm
(2.0in)min.
50mm
(2.0in)min.
20mm
(0.8in)
Min.
20mm
(0.8in)
Min.
FAN FAN
100mm
(4.0in)
Min.
100mm
(4.0in)
Min.
100mm
(4.0in)
Min.
100mm
(4.0in)
Min.
40mm
(1.6in)
Min.
40mm
(1.6in)
Min.
10mm
(0.4in)
Min.
10mm
(0.4in)
Min.
10mm
(0.4in)
Min.

13
3. Signals and Wiring
This chapter provides definitions of the wiring and signals of Shihlin servo actuator and the
standard wiring diagrams for all the models.
3.1. Main Circuit Power Source and Peripheral Device Connections
3.1.1. Peripheral Device Connection Wiring (Under 1KW)
電源:三相200~230V
P
C
外部回生電阻接在伺服P、
C兩端,P、D兩端開路
CN4
USB通訊連接
CN3
RS-232 RS-485通訊連接
CN2
編碼器連接
CN1
I/O連接,連至上
位控制器
伺服馬達
電磁接觸器
Server motor
Power Source:
Three-phase 200 – 230V External regenerative resistors at
terminal P and C and the opening
of terminal P and D
CN4 USB
communicative
connection
RS-232 RS-485
communication connection
CN2
encoder connection
CN1
I/O connection with
the host controller
Eletromagnetic connection

14
3.1.2. Peripheral Device Connection Wiring (Above 1.5KW)
電源:三相200~230V
P
C
外部回生電阻接在伺服P、
C兩端,P、D兩端開路
CN4
USB通訊連接
CN3
RS-232 RS-485通訊連接
CN2
編碼器連接
CN1
I/O連接,連至上
位控制器
伺服馬達
電磁接觸器
Power Source:
Three-phase 200 – 230V
Server Motor
RS-232 and RS-485
communication connection
CN4 USB
communication
connection
encoder connection
Electromagentic contactor
External regenerative resistor
connected to terminal P and C and
the opening of terminal P and D
I/O connection with
the controller

15
Installation Note:
cMake sure that the terminal wiring of servo motor output U, V, Q is correct, or the
motor will rotate randomly or be unrotatable.
dIf external brake resistors are used, be sure to connect the open circuit resistor and
the external brake resistor of P and D terminals to the P and C terminals. If built-in
brake resistors are used, be sure to make the P and D terminals short circuits while
the P and C open circuits.Be sure that the brake resistor is connected when wiring
the servo.
eCheck whether the power source and the wiring of R, S, T, L1 and L2 are correct.
Wrong short circuits may blow up the machine.
3.1.3. Descriptions of Actuator Connectors and Terminals
Name Terminal Code Description
Main Circuit Power
Source Input Terminal
R、S、T Connect to three-phase AC.
Power Source Input
Terminal
L1、L2 Connect to single-phase AC.
Motor Power Input
Terminal
U、V、W、PE
Terminal Code Wire Color
U Red
V White
W Black
PE Green
Brake Resistor
Terminal
P、D、C
Using
external
resistors
Connect the resistor to the P and
C terminals while making the P
and D terminals the open circuits.
Using
built-in
resistors
Make the P and D terminal short
circuits while the P and C
terminals open circuits.
Ground Terminals Connect it to the ground terminal of the power
source and of the motor (the green screws at the
exterior of the controller.
This manual suits for next models
18
Table of contents
Popular Servo Drive manuals by other brands
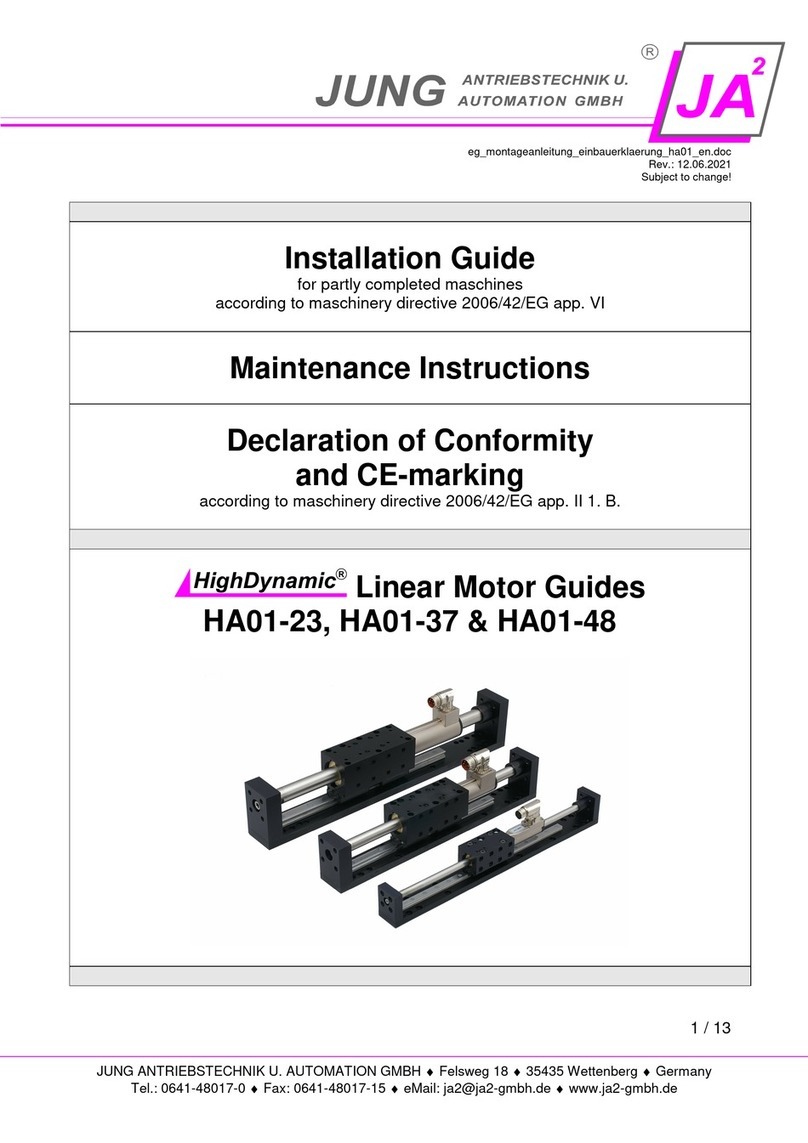
JUNG ANTRIEBSTECHNIK U. AUTOMATION GMBH
JUNG ANTRIEBSTECHNIK U. AUTOMATION GMBH HighDynamic HA01-23 installation guide
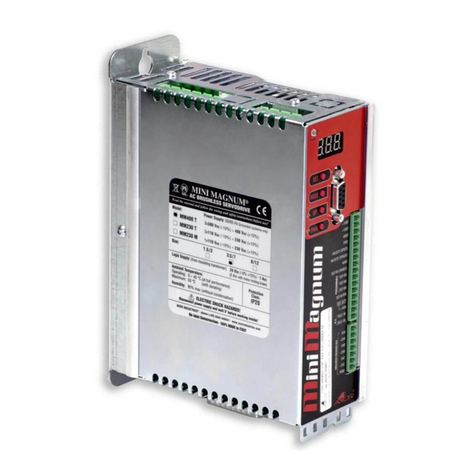
AXOR Industries
AXOR Industries MiniMagnum Series Service manual
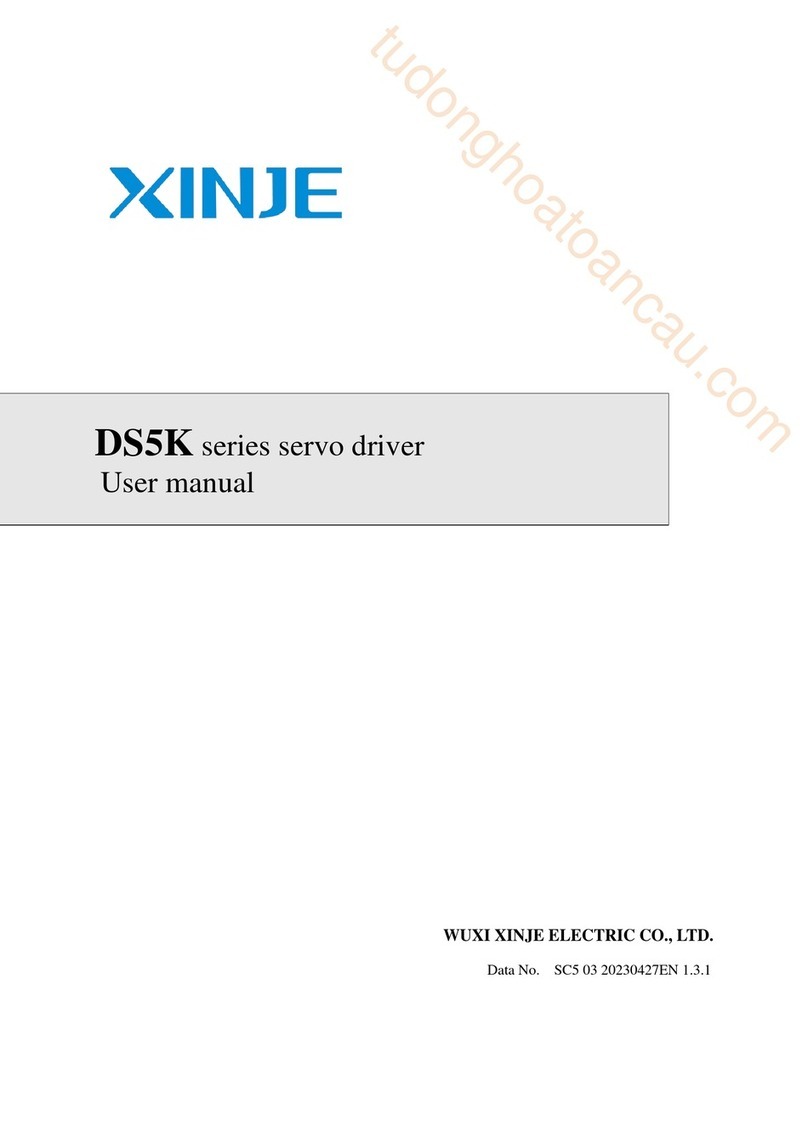
Xinje
Xinje DS5K Series user manual
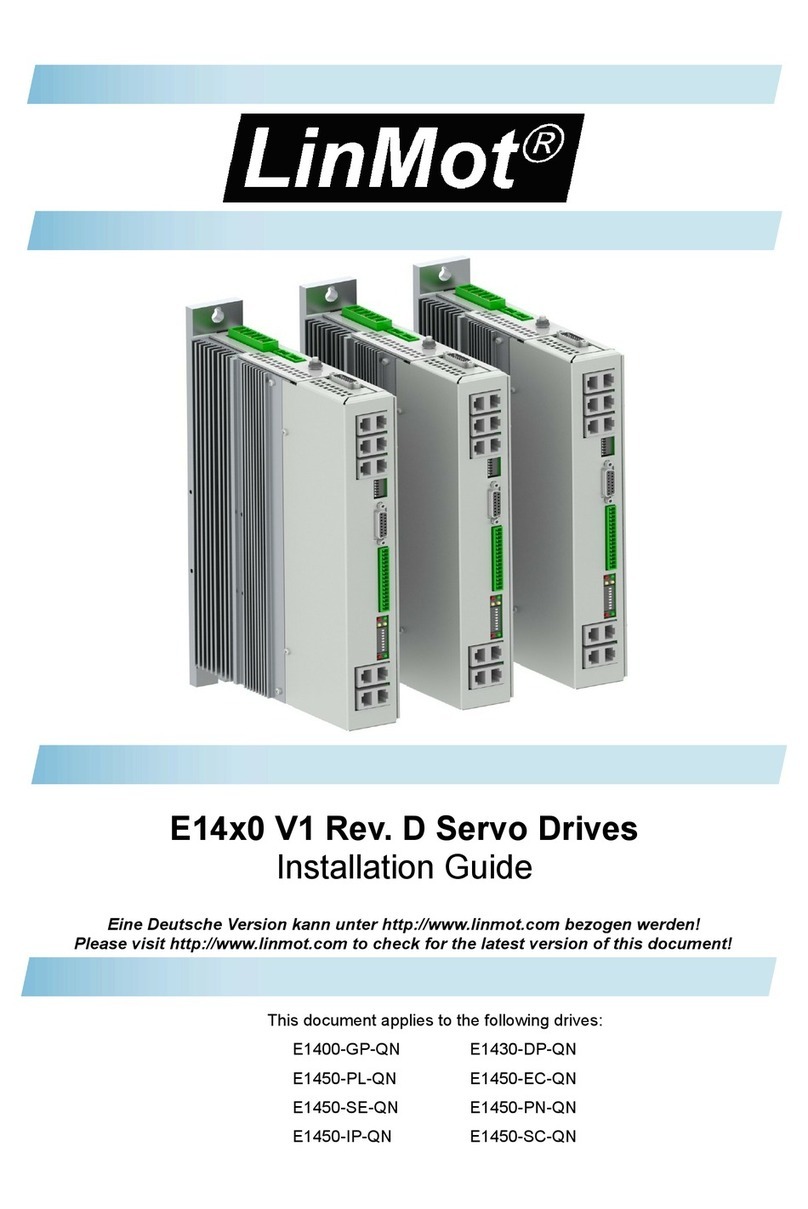
LinMot
LinMot E1400-GP-QN installation guide
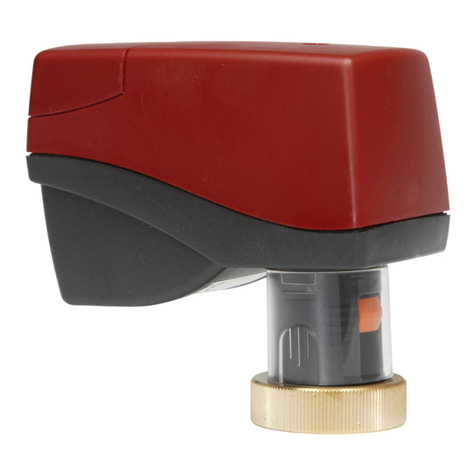
IMI TA
IMI TA MC15/24 Mounting instructions
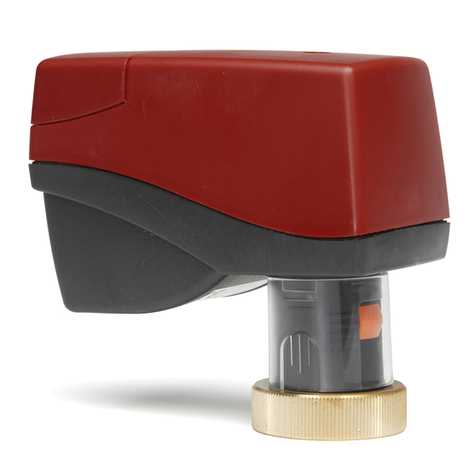
IMI
IMI MC15/24-C Mounting instructions
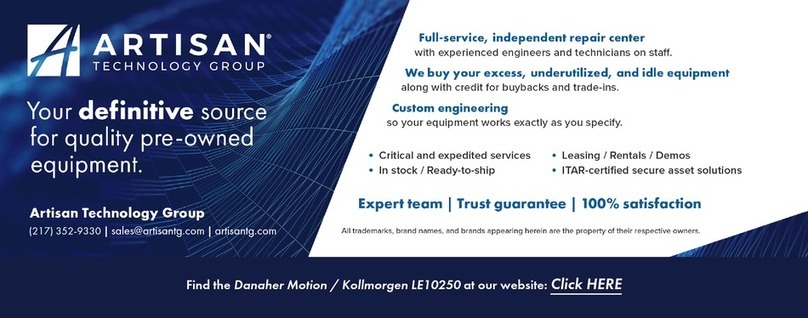
Danaher Motion
Danaher Motion SERVOSTAR CD-LITE user manual
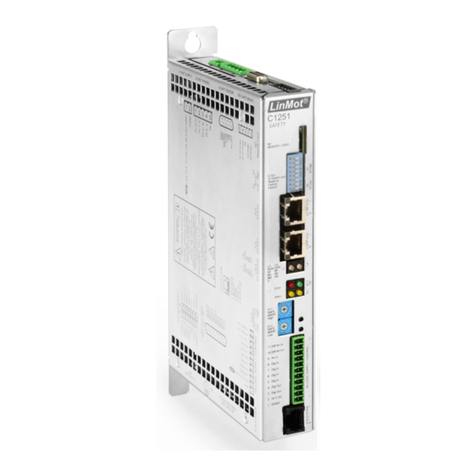
LinMot
LinMot C1251-MI-XC-2S-0E Series manual
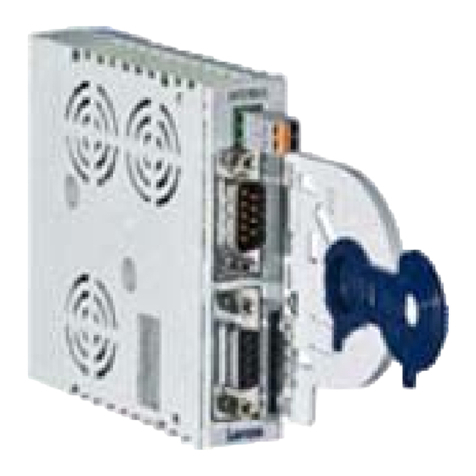
Lenze
Lenze L-force 9400 Communications manual
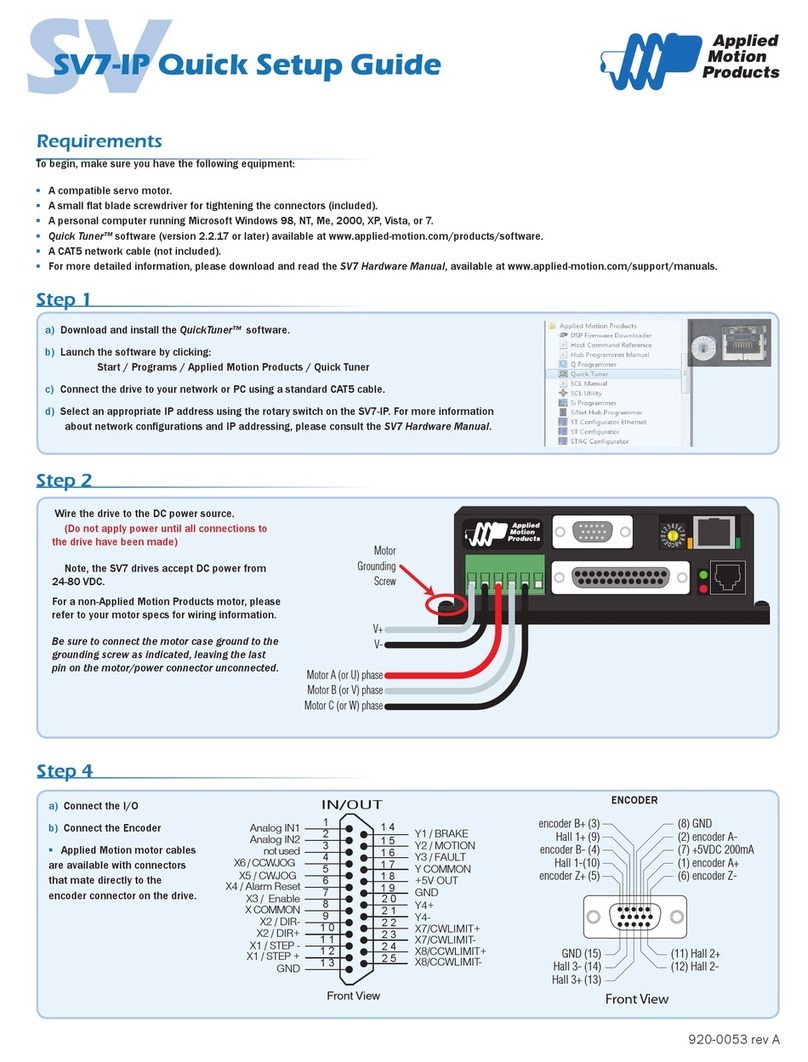
Applied Motion Products
Applied Motion Products SV7-IP Quick setup guide
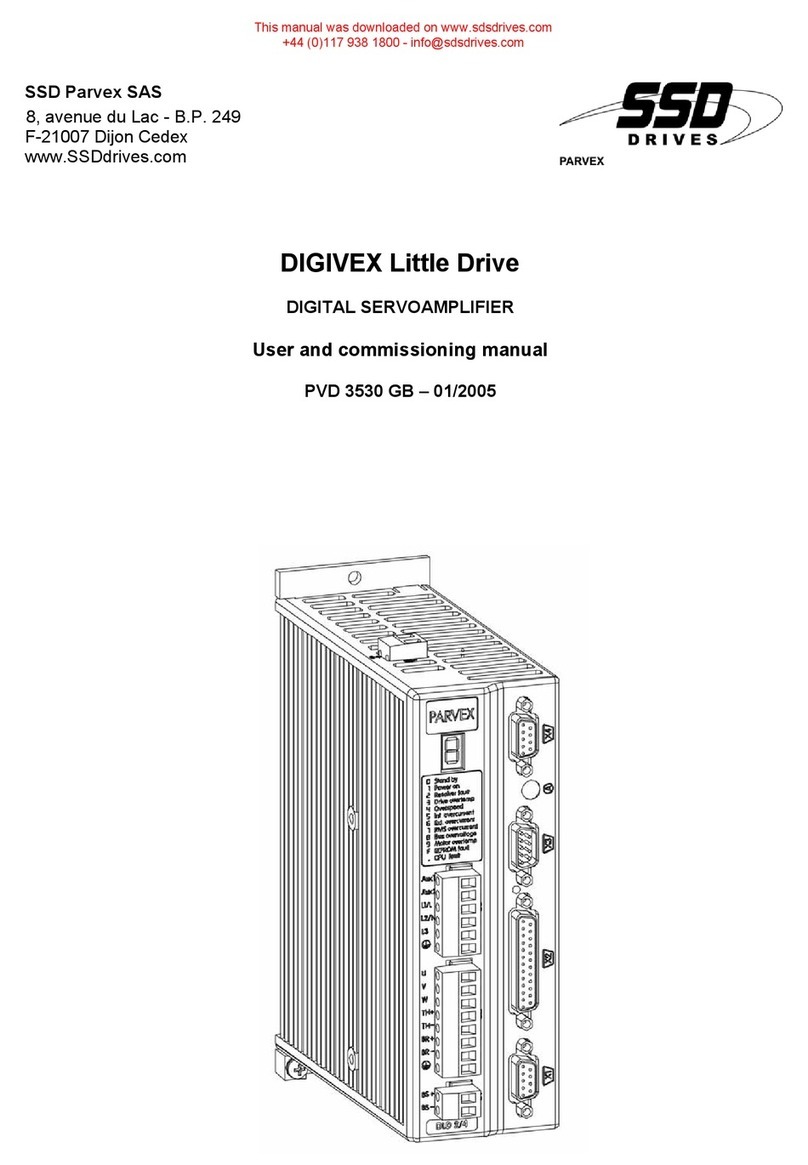
SSD Parvex
SSD Parvex DIGIVEX Little Drive Servoamplifier User and commissioning manual
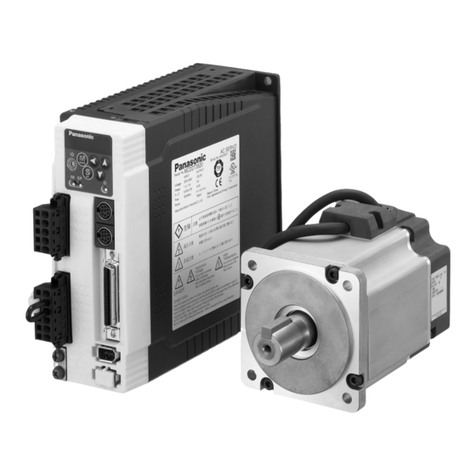
Panasonic
Panasonic MINAS A4-series Technical reference