Rottler SG10A User manual

8029 S 200th St. Kent, WA 98032 USA | www.rottlermfg.com | Ph: 253-872-7050 | Fax: 253-395-0230
OPERATION AND MAINTENANCE MANUAL
17.03.2017


ORDERING PROCEDURE
Contact your regional Rottler sales rep for assistance in ordering optional equipment, replacement parts,
or tooling.
If you are unable to contact your regional Rottler sales rep, call the factory at 253-872-7050 and ask to
speak to the parts sales specialist.
Have the following information handy to expedite the ordering process:
1. Your name, business name, and contact number
2. Customer number
3. If you don’t have a customer number, your billing address
4. Shipping address if different from billing address
5. Machine model and serial number
6. Part number and description of what you want to order
7. Preferred method of shipment
8. You may also contact us via e-mail with the above information. Send e-mail requests to:
In some cases you may be requested to send a photo of the part you are ordering if it is a replacement
part, or doesn’t appear in the database.
If you are unsure which part you need to order, contact our service department and ask to speak to one of
our service consultants. They will assist you in determining which part you require.
THERE IS A MINIMUM ORDER OF $25.00
MANUAL SECTIONS
INTRODUCTION
INSTALLATION
SAFETY
CONTROL DEFINITIONS
OPERATING INSTRUCTIONS
MAINTENANCE
TROUBLESHOOTING
MACHINE PARTS
OPTIONS
MSDS


Section 1 Introduction SG10A Manual
www.rottlermfg.com
1-1
INTRODUCTION
READ THE SAFETY CHAPTER BEFORE INSTALLING MACHINE. THOROUGHLY UNDERSTAND
ALL SAFETY ISSUES BEFORE OPERATING MACHINE.
ATTENTION OWNER/BUSINESS MANAGER
To validate the warranty on your new Rottler machine, please be sure to sign
and complete the “Installation Report” located in the Installation Chapter of this
manual.
We suggest that the new user of the SG10A read the CONTROL DEFINITIONS to get an idea how the
machine operates.
The Operating Instructions chapter should be read in order to familiarize the user with the actual button
pushing sequences required to carry out a job. These chapters in the manual should be considered an
introduction. As the operators of the SG10A series machines gain experience with using the different
functions of the machine, complicated setups and programs will make more sense.
The rest of the manual contains information and part number reference on xtures, cutting tools, and
machine maintenance. The operator should read and become familiar with these areas as well.
Disclaimer
The SG10A Manual (henceforth to be referred to as the “Manual”) is proprietary to Rottler Manufacturing
LLC. (“Rottler Manufacturing”) and no ownership rights are hereby transferred. No part of the Manual
shall be used, reproduced, translated, converted, adapted, stored in a retrieval system, communicated or
transmitted by any means, for any commercial purpose, including without limitation, sale, resale, license,
rental or lease, without the prior express written consent of Rottler Manufacturing.
Rottler Manufacturing does not make any representations, warranties or guarantees, express or implied,
as to the accuracy or completeness of the Manual. Users must be aware that updates and amendments
will be made from time to time to the Manual. It is the user’s responsibility to determine whether there
have been any such updates or amendments. Neither Rottler Manufacturing nor any of its directors,

Section 1 Introduction SG10A Manual
www.rottlermfg.com
1-2
ofcers, employees or agents shall not be liable in any manner whatsoever to any person for any loss,
damage, injury, liability, cost or expense of any nature, including without limitation incidental, special,
direct or consequential damages arising out of or in connection with the use of the Manual.
Description
The model SG10A machine is an automatic precision, Seat nish machine design to maintain accuracy
on every nish seat. It can be equipped with tooling and accessories to handle most American, Import,
and Diesel passenger car and truck cylinder heads. Convenient controls, easy cylinder Head Clamping,
air oated spindle base (Work Head) centering on the pilot shank and clamping, means considerable
savings in oor to oor time, and operator involvement. Making this machine highly suited to the jobber
shop where accuracy and dependability is required.
Disclaimer
The SG10A Manual (henceforth to be referred to as the “Manual”) is proprietary to Rottler Manufacturing
LLC. (“Rottler Manufacturing”) and no ownership rights are hereby transferred. No part of the Manual
shall be used, reproduced, translated, converted, adapted, stored in a retrieval system, communicated or
transmitted by any means, for any commercial purpose, including without limitation, sale, resale, license,
rental or lease, without the prior express written consent of Rottler Manufacturing.
Rottler Manufacturing does not make any representations, warranties or guarantees, express or implied,
as to the accuracy or completeness of the Manual. Users must be aware that updates and amendments
will be made from time to time to the Manual. It is the user’s responsibility to determine whether there
have been any such updates or amendments. Neither Rottler Manufacturing nor any of its directors,
ofcers, employees or agents shall not be liable in any manner whatsoever to any person for any loss,
damage, injury, liability, cost or expense of any nature, including without limitation incidental, special,
direct or consequential damages arising out of or in connection with the use of the Manual.
Rottler Manufacturing and its employees or representatives are not responsible for any information
regarding nal specications of any workpiece that is created as a nal product when using Rottler
equipment. It is the responsibility of the end user of Rottler equipment to determine the nal dimensions
and nishes of the workpiece that they are working on. Any information regarding nal dimensions and
nishes that appears in any Rottler literature or that is expressed by anyone representing Rottler is to
be regarded as general information to help with the demonstration of or for operator training of Rottler
equipment.
Limited Warranty
Rottler Manufacturing Company Model SG10A parts and equipment is warranted as to materials and
workmanship. This limited warranty remains in effect for one year from the date of delivery, provided the
machine is owned and operated by the original purchaser and is operated and maintained as per the
instructions in the manual.
Tools proven to be defective within the warranty period will be repaired or replaced at the factory’s option.
The products are warranted upon delivery to conform to their published specications and to be free from
defects in material and workmanship under normal use for a period of one year from shipment. Should a
product not be as warranted, Rottler sole obligation shall be, at its option, to repair, correct or replace the
product or to refund the amounts paid for the Product upon its return to a location designated by Rottler.
No warranty shall extend to rapid wear Products (including tooling) or to Products which have been
subject to misuse (including any use contrary to Rottler instructions), neglect, accident (including during

Section 1 Introduction SG10A Manual
www.rottlermfg.com
1-3
shipment), improper handling or installation, or subject to any modication, repair or service not certied
by Rottler. Rottler shall not be liable for any consequential, direct or indirect damages or for any other
injury or loss. Buyer waives any right, beyond the foregoing warranty, to make a claim against Rottler.
No warranty is provided for any Products not paid in full.
Merchandise cannot be returned to Rottler without prior approval. Customer must contact the Order
Department or representative to get approval and to be issued a Return Goods Authorization number
(RGR#). Merchandise authorized for return must be returned prepaid. If merchandise is returned with
shipping charges collect, the actual amount of these charges may be deducted from any credit which may
be due the customer. The RGR # assigned by the Order Department should be written on the shipping
label and must appear on a copy of the invoice(s) covering the original shipment. This invoice copy
must be included in the box with the parts. Shipment must contain ONLY those items on the RGR as
approved for return. Merchandise must be received within 10 days of the date of RGR or the RGR will be
canceled. All returned merchandise may be subject to a 20% restocking fee on under $1,000.00 amount
or 10% on any items over $1,000.00. Parts or tooling over 30 days old are considered as customer
property and can only be returned with prior written approval from Rottler Corporation Management and/
or Shipping Department.
The issuance of a RGR DOES NOT guarantee credit - it is only authorization for the return of the
goods. Credit for return merchandise is at the sole discretion of Rottler. Credit will be issued only after
inspection of returned goods.
Tools proven to be defective within the warranty period will be repaired or replaced at the factory’s option.
We accept no responsibility for defects caused by external damage, wear, abuse, or misuse, nor do
we accept any obligation to provide compensation for direct or indirect costs in connection with cases
covered by the warranty.

Section 1 Introduction SG10A Manual
www.rottlermfg.com
1-4

Section 2 Installation SG10A Manual
www.rottlermfg.com
I
INSTALLATION
Contents
ROTTLER SG10A INSTALLATION REPORT..............................................................2-2
Installation Procedure.................................................................................................2-6
Unpacking and Lifting.......................................................................................................... 2-6
Removing Shipping Brackets.............................................................................................. 2-7
Preparation for Placement................................................................................................... 2-8
Machine Installation ............................................................................................................. 2-8
Positioning the Machine ...................................................................................................... 2-9
Power and Air Connections................................................................................................. 2-9
Leveling the Machine ......................................................................................................... 2-10
Air Supply.............................................................................................................................2-11
Air Adjustments...................................................................................................................2-11
Float .................................................................................................................................................2-11
Power Supply...................................................................................................................... 2-12
Grounding........................................................................................................................................2-12

Section 2 Installation SG10A Manual
www.rottlermfg.com
2-1
ATTENTION OWNER/BUSINESS MANAGER
To validate the warranty on your new Rottler machine, please
be sure to sign the installation report after the installation
technician has installed the machine and veried the machine
is operating correctly and given the operators operation and
maintenance training.
Thank you for your cooperation and the opportunity to be of
service to you.
ROTTLER MANUFACTURING

INSTALLATION REPORT
SG10A
REV 031717
OFFICE USE ONLY
Route to: Servicer Mgr Accounting Andy Accounting Warranty Exp Date ________
ROTTLER MANUFACTURING MUST HAVE THIS REPORT RETURNED
TO PROPERLY QUALIFY WARRANTY ON EQUIPMENT
Customer:____________________________ Address:_______________________________________
City:_________________________________ State:_____ Zip:_________ Phone:_______________
Country:______________________________
Machine Model:___________ Serial Number:__________ Representative:________________________
MACHINE INSTALLATION: Electrical information MUST be complete to validate this report.
Customer is responsible for providing electricity to machine in a manner that meets the local
electrical code requirements.
______Check machine level for equal support on feet.
______This machine requires between 208 and 240 Volts AC, Single Phase, 50/60 Hz, isolated power
supply. Measure the incoming voltage between L1 and L2. Current requirements for this machine
are 15 amps. Measure the incoming AC voltage at least twice during installation.
1) __________VAC 2) __________ VAC
______Measure each leg of the incoming supply to ground. When using a one leg and neutral of a 380
VAC three phase supply L1 should measure 240 VAC and Neutral should measure almost 0 VAC.
L1 to ground _________VAC L2 to ground __________VAC.
Make sure all electrical equipment has the proper overload protection. The SG10A should have a fully
isolated power supply to prevent damage and uncontrolled movement of the machine. If the SG10A is
on the same power lines that are running to other electrical equipment (grinders, welders, and other AC
motors) electrical noise can be induced into the SG10A electrical system. Electrical noise can cause the
controller to see false signals to move.
Neutral and machine ground are not the same thing. You should measure an
open circuit between Neutral and ground.
IF VOLTAGE IS OUTSIDE THE CORRECT RANGE AT ANY TIME THE
MACHINE WILL NOT OPERATE PROPERLY AND MAY BE DAMAGED.
______Relocate electrical enclosure from shipping location to operating location on lower right side of
machine.
______Air of the proper pressure and capacity connected to the machine. Air supply must be free from oil
and water. Oil or water will damage electrical and air components. Air pressure should never drop
below 90 PSI at any time. Failure to provide adequate air supply may cause improper oating and
clamping.
______BEFORE turning power on to the machine. Check all wires for security by using the correct screw
driver and turning CW until movement stops. Stranded wire can “spread” slightly from vibration
during transport.
______Install electrical component covers inside the electrical enclosure with fasteners provided.
______Remove all shipping brackets in accordance with the machine manual.
______Clean any rust inhibitor from the machine surfaces. Slide the spindle base from side to side
continually cleaning the machine base until all inhibitor is removed.

Section 2 Installation SG10A Manual
www.rottlermfg.com
2-3
______Have the operator read through the operation manual before training begins. This will help him
be familiar with the button pushing sequences. Have the operator read through the manual again
after training and some of the sequences will make more sense.
MACHINE START-UP
When starting the machine for the rst time, it may move out of control. Make
sure all hands are clear of machine parts. Be ready to press the Emergency
Stop button if needed.
______Turn main power on from the main incoming breaker box.
MACHINE MOVEMENTS
______Make sure there is nothing obstructing the full vertical travel of the machine.
______When the machine is on the clamp mode and the air pressure is with the requirements, try to
move workhead to verify that you have a solid clamp of Work head.
______Place the level on the leveling post. The level assembly is referenced to the spindle via the level
pin. It is therefore important to check alignment of the pin in reference to the spindle. Even though
the level has been carefully calibrated at the factory, it is a good idea to recheck calibration before
putting the machine into service. In the event that the level is dropped or handled roughly then
the following recalibration methods should be implemented. If calibration is required refer to the
manual for Calibrating the Digital Level
______Start the spindle and verify operation.
INSTRUCTING THE OPERATOR:
Note: Rotter employees and representatives per company policy are not permitted to provide end
user of Rottler equipment with any OEM specications for the workpiece that is created by end
user using Rottler equipment.
______ Explain to the customer and operator that at NO time is there to be any software or hardware
other than Windows Auto Update and Rottler installed on this machine. This includes screen
savers, anti-virus software, and any hardware device that installs software on the machine.
Installation of screen savers and anti-virus software can cause dangerous control problems. Any
installation of software or hardware will void the warranty on the machine.
______Explain to the customer and operator that the machine should be hooked up to the Internet
anytime it is on. The software on the machine will automatically connect to our server to send
back useful information on machine status.
______Explain to the customer and the operator how the to log onto Skype and communicate with Rottler
when needed.
______ Computer Viruses will cause the machine control system to become unstable. This may cause
the machine to make uncontrolled moves which could create a dangerous environment for the
machine operator.
______Connect customer supplied Internet to the machine. Verify that the Internet is accessible from the
machine.

Section 2 Installation SG10A Manual
www.rottlermfg.com
2-4
______Explain to the customer the proper way for turn the machine off when it is not in use. Do not
leave the machine on overnight. It is important to close all programs followed by shutting down
Windows before turning the main power switch off. Do not turn the main power switch off before
shutting down Windows.
______Using the operating manual as a guide explain the function of all buttons.
______Cycle all machine movements and supervise the handling of same by operator.
______Demonstrate the engaging of the ne feed system.
______Point out safety features to customer and operator.
Do not push any buttons without thinking of safety rst.
Do not assume the Digital level has been calibrated rotate 180 to verify
alignment.
______The following is a checklist to go through every time the machine is started to begin machining a
seat.
• Work piece secure
• RPM set
• Tool holder adjusted to the correct setting base on the type of seat you will be machining
• Tool holder locked in place
• Floating of the Workhead and clamping
______Proceed to have operator to machine a seat under you control.
______Parts ordering, refer to the operating manual for part numbers and description.
______Review Emergency stop procedure and with operator per operating manual.
______Explain to the customer the importance of backing up the block proles to a separate device. Any
computer failure or possible operator input error can result in the loss of all block proles that
were created for the machine. Refer to Chapter 5 of the machine manual for detailed instructions
on backing up and restoring block proles.

Section 2 Installation SG10A Manual
www.rottlermfg.com
2-5
General remarks on machine performance, adjustments as received and any further organization or parts
required to complete the installation.
____________________________________________________________________________________
____________________________________________________________________________________
____________________________________________________________________________________
____________________________________________________________________________________
____________________________________________________________________________________
____________________________________________________________________________________
____________________________________________________________________________________
____________________________________________________________________________________
____________________________________________________________________________________
____________________________________________________________________________________
____________________________________________________________________________________
____________________________________________________________________________________
Instructions given to:___________________________________________________________________
Sales/Service Engineer: _______________________________________________ Date_____________
Shop Foreman/Superintendent or Owner: _________________________________ Date_____________
Once completed send this form to:
Rottler Manufacturing
attn: Service Manager
8029 S 200 St
Kent, WA 98032 USA
Alternately you may send this form via fax or e-mail:
fax: [+1] 253-395-0230
e-mail: [email protected]

Section 2 Installation SG10A Manual
www.rottlermfg.com
2-6
Installation Procedure
The productivity of this machine will depend a great deal on it’s proper initial installation, particularly the
means by which cylinder heads are lifted into the machine as well as the material handling to and from
other operations in your shop.
The proper loading arrangement and location for your SG10A machine is extremely important.
A slow travel (6 to 10 feet / min.) power hoist operated from either a bridge crane or a jib crane
arrangement works very well.
Unpacking and Lifting
Carefully uncrate the machine. Remove all tooling from storage compartments and unpack. Locate the
leveling bolts and leveling pads. Clean all surfaces with solvent and rags to remove protective shipping
coatings.
THIS MACHINE IS TOP-HEAVY. Use care when lifting and moving Machine. Approximate shipping
Weight of Machine is 2800 lbs. (1258 kg).

Section 2 Installation SG10A Manual
www.rottlermfg.com
2-7
Removing Shipping Brackets
Before leveling the machine, loosen and remove the all shipping brackets and bolts. (Figures 1 – 5)

Section 2 Installation SG10A Manual
www.rottlermfg.com
2-8
Preparation for Placement
Air supply is connected at the left side of the machine, at base of lower casting. Connection can either
be a quick disconnect or permanent threaded connection. Be certain to use an adequately sized airline,
permitting proper operation of oat. Air pressure should never drop below 90 PSI at any time. Failure to
provide adequate air supply may cause improper oating and clamping.
At this time, some customers will install a T tting or manifold at the regulator, allowing another air hose to
be connected, providing a connection point for air tools. The auxiliary hose, if tted, should be of sufcient
length to easily reach the entire front of the machine.
This machine comes pre-wired and ready to be connected to the power source. The power source should
meet all local and national electrical codes. This service should connect to its own circuit breaker or fuse.
The machine will require 220 VAC, 15 amp, single-phase power supply.
Machine Installation
• Lift Machine using a fork lift. Move fork lift to front of Machine and separate forks so they are visually
centered.
• Insert forks under front-center of Machine, using care not to damage Foot Pedals Valve or Air Lines.
Tilt forks slightly upward so Machine will lean toward fork lift and lift Machine.
• While Machine is on fork lift, install six (6) Leveling Screws and Jam Nuts in holes provided in bottom
of Machine Base. Two (2) Screws installed in rear-corners and two (2) Screw installed in front corners
of Machine Base will serve as Leveling Screws; while two (2) Screws installed in center of Machine
Base will serve only as Support Screws.
• Move Machine to desired location and placed leveling bolts over the center hole of the Leveling Pad.
Be certain to allow sufcient clearance to allow access for leveling and also for connecting air and
electrical lines.
• Lower machine onto leveling pads making certain that the leveling bolts align into counter bore on
leveling pads.
• Be certain nothing interferes with air or electrical tracking running from the oating head assembly to
the cabinet.
• Determine there is no possibility of air or electrical tracking dragging on wall surfaces or adjacent
machinery.
• Wipe top Rails with a clean, dry cloth to remove protective shipping oil.
Do not attempt to move the Work Head unless Air Supply is connected, and air
valve is turned on and power has been turn on (make sure the EMERGENCY STOP
Button is off). From the touch screen, oat the workhead, spray, and clean surface with (WD40) or similar
degreaser and ow the work Head side by side to remove all the shipping oil from under the work head.
(Top Upper surfaces rails should be clean and free of oil).

Section 2 Installation SG10A Manual
www.rottlermfg.com
2-9
Positioning the Machine
• Lift Machine using a fork lift. Move fork lift to front of Machine and separate forks so they are visually
centered.
• Insert forks under front-center of Machine, using care not to damage Foot Pedals Valve or Air Lines.
Tilt forks slightly upward so Machine will lean toward fork lift and lift Machine.
• While Machine is on fork lift, install ve (6) Leveling Screws and Jam Nuts in holes provided in bottom
of Machine Base. Two (2) Screws installed in rear-corners and one (2) Screw installed in front and
rear -center of Machine Base will serve as Leveling Screws; while two (2) Screws installed in front-
corners of Machine Base will serve only as Support Screws.
• Move Machine to desired location and placed leveling bolts over the center hole of the Leveling Pad.
Be certain to allow sufcient clearance to allow access for leveling and also for connecting air and
electrical lines.
• Lower machine onto leveling pads making certain that the leveling bolts align into counterbore on
leveling pads.
• Be certain nothing interferes with air or electrical lines running from the oating head assembly to the
cabinet.
• Determine there is no possibility of air or electrical lines dragging on wall surfaces or adjacent
machinery.
• Wipe top Rails with a clean, dry cloth to remove protective shipping oil.
Do not attempt to move the Work Head unless Air Supply is connected, and air
valve is turned on and power has been turn on (make sure the EMERGENCY STOP
Button is off). From the touch screen, oat the workhead, spray, and clean surface with (WD40) or similar
degreaser and ow the work Head side by side to remove all the shipping oil from under the work head.
(Top Upper surfaces rails should be clean and free of oil).
Power and Air Connections
Air supply is connected at the right, rear of the machine, at base of upper casting. Connection can either
be a quick disconnect or permanent threaded connection. Be certain to use an adequately sized air line,
permitting proper operation of oat. Air pressure should never drop below 90 PSI at any time. Failure to
provide adequate air supply may cause improper oating and clamping.
At this time, some customers will install a T tting or manifold at the regulator, allowing another air hose to
be connected, providing a connection point for air tools. The auxiliary hose, if tted, should be of sufcient
length to easily reach the entire front of the machine.
This machine comes pre-wired and ready to be connected to the power source. The power source should
meet all local and national electrical codes. This service should connect to its own circuit breaker or fuse.
In most cases the machine will require 220 VAC, 15 amp, single-phase service but you should verify
voltage requirements by inspecting the electrical tag located on the rear of the machine

Section 2 Installation SG10A Manual
www.rottlermfg.com
2-10
Leveling the Machine
Use required machinist level. (Starret 98 or better).
NOTE: Rotate Level 180º to check that Level is properly adjusted. If Level does not read same in both
directions, recalibrate level.
Use the level on the upper oat surface, level the machine as precisely as possible, front to back and side
to side.
Adjust 4 corners until level and then extend the 2 center leveling bolts to support machine. Tighten jam
nuts on leveling bolts and recheck level

Section 2 Installation SG10A Manual
www.rottlermfg.com
2-11
Air Supply
It is very important the air source for the SG10A / SG80A machine be moisture free. Water and oil in the
line will result in early cylinder and valve failure. The factory recommends installing a water trap at the
machine. Attach an air source of at least 100 PSI to the appropriate intake in the small enclosure located
on the left rear of the machine near the bottom. Bellow you will see the Air regulator panel for the different
settings on the oating planes on the machine. And cabinet cooler air regulator.
Air Adjustments
Float
The oat regulators are located on the left side of machine base. Marked “Work Head Air Float
Adjustment” If the work head is not oating properly it could be from too much or too little air from the
regulator. Starting with all regulators set at 1 bar with “workhead oat” button activated, slowly turn all
up .5 bar at a time until workhead start to oat. Pushing work head front to rear checking for stiff spots.
If workhead is dragging in the forward position, (workhead pulled closest to operator) raise the 2 front
regulators 1 mark until it oats without dragging. Same for rear. You may have to go back and forth a few
times to get this correct. If workhead is not dragging lower the PSI until it does and then raise 1 notch at
a time until it is free. Typically the front two regulators will be slightly higher than the rear two. Once the
correct oat is established lock the regulators in place by pushing in on the blue adjusting knob.
Use as little air as possible to achieve correct oatation. Using too much air will / could cause
excessive movement of workhead.
Table of contents
Popular Sander manuals by other brands
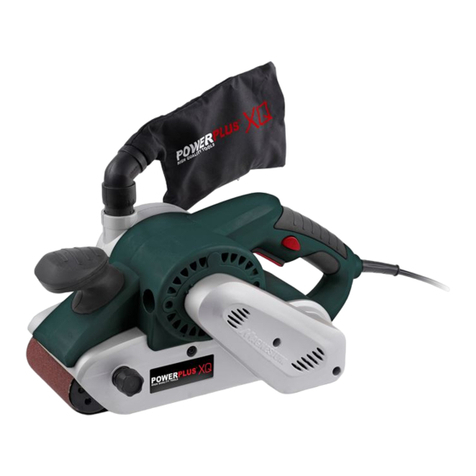
Powerplus
Powerplus XQ POWXQ5406 quick start guide
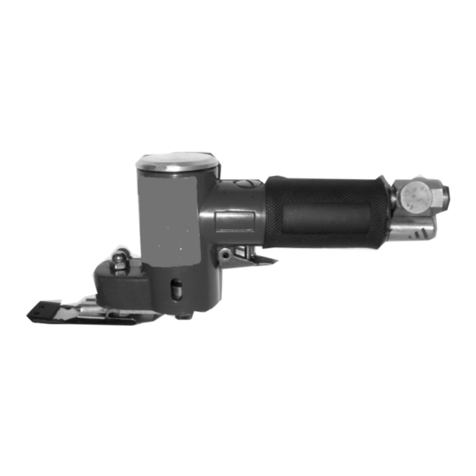
Central Pneumatic
Central Pneumatic 98189 Set up and operating instructions

NUTOOL
NUTOOL RED NEP1200R Original Operating Instruction
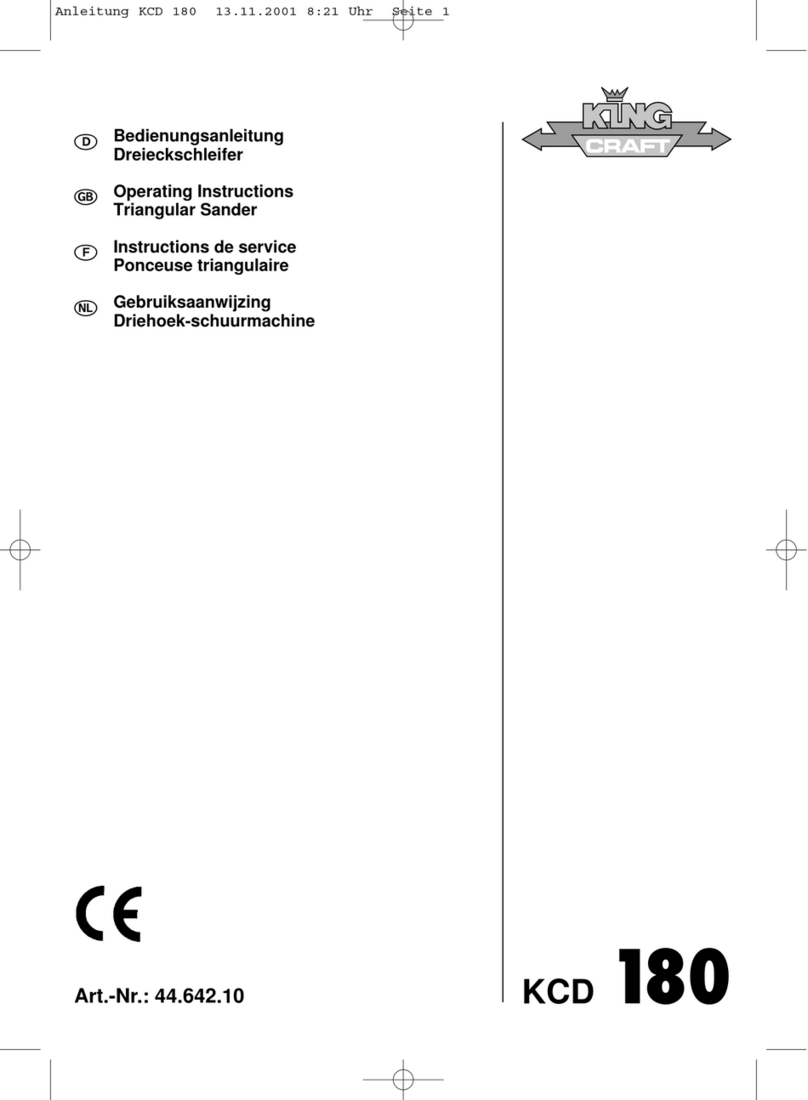
KING CRAFT
KING CRAFT KCD 180 operating instructions
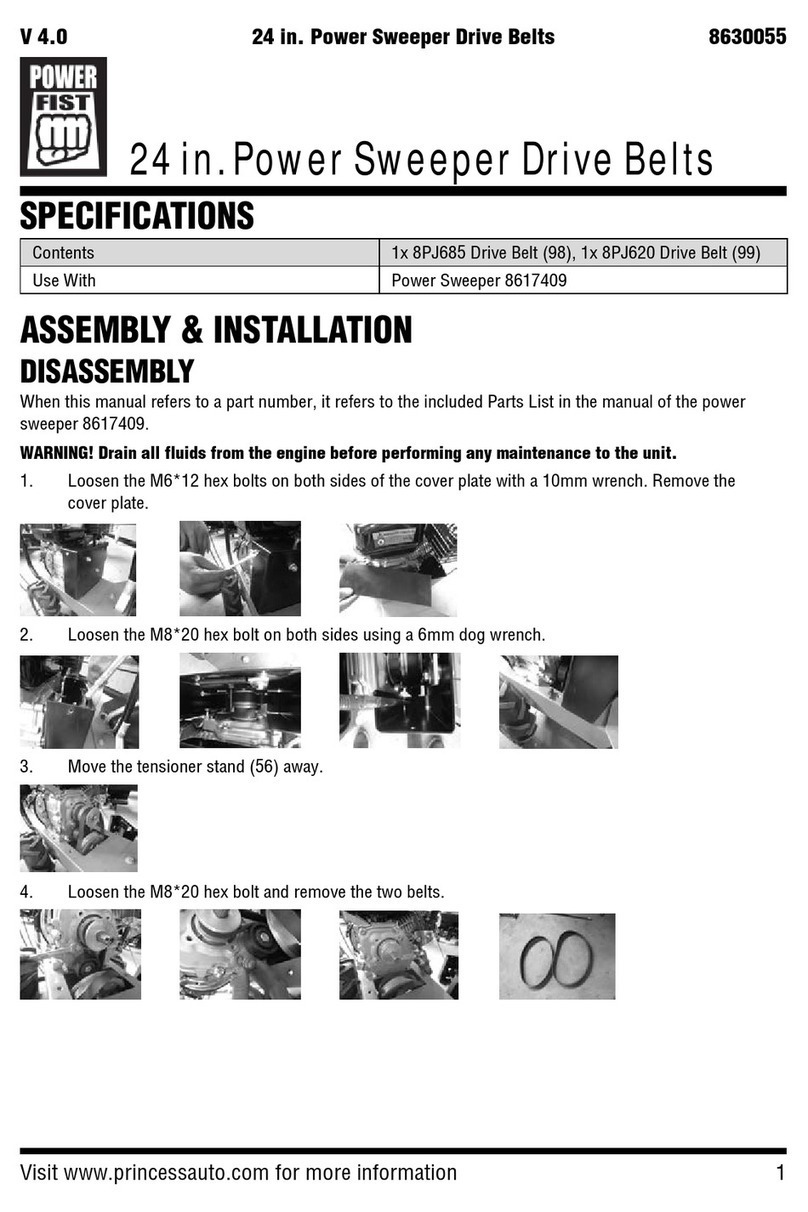
Power Fist
Power Fist 8630055 quick start guide
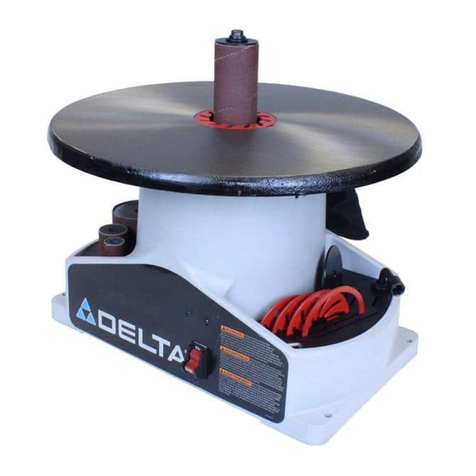
Delta
Delta B.O.S.S. SA350 instruction manual