RPM MHPWS-QNN Series User manual

M-MHPWS-QNN-CAN-EN
V1.02, 2020.05.21
Electro-Hydraulic Actuators
MHPWS-QNN Series
Maintenance Manual

M-MHPWS-QNN-CAN-EN
2
Important Notice!
This manual consists of content to guide the installation and operation of the MHPWS-QNN.
Safety notices in the manual are specific precautions to reduce the risk of personal injury and
equipment damage.
Users should read and understand these instructions. Failure to observe these safety notices may
result in personal injury, equipment damage, and voiding warranty.
The safety notices are designated as follows.
: Signifies potential dangers that, if not followed, can result in serious injury or even
death.
: Outlines precautions for the user to avoid injury or equipment damage.
: Important information in understanding the installation and operation of the MHPWS-
QNN actuator.
WARNING
NOTE
CAUTION

M-MHPWS-QNN-CAN-EN
3
Table of Contents
1. Maintenance . . . . . . . . . . . . . . . . . . . . . . . . . . . . . . . . . . . . . . . . . . . . . 4
1.1 Periodic Maintenance Procedures
1.2 Troubleshooting
2. Disassembly and Assembly . . . . . . . . . . . . . . . . . . . . . . . . . . . . . . . . . . 9
2.1 Product Disassembly
2.2 Product Assembly
3. Product Disposal and Recycling . . . . . . . . . . . . . . . . . . . . . . . . . . . . . . . 13
4. Drawing . . . . . . . . . . . . . . . . . . . . . . . . . . . . . . . . . . . . . . . . . . . . . . . . . . 14
4.1 Exploded-view Drawing
4.2 Parts List

M-MHPWS-QNN-CAN-EN
4
1. Maintenance
1.1 Periodic Maintenance Procedures
Every individual part is thoroughly inspected and tested before being assembled after which
an extensive performance and functions test is executed to guarantee maximum quality and
reliability. However, our products are still subject to wearing after significant usage or
exposure to harsh environmental conditions, which may reduce the MHPWS-QNN’s
performance or cause malfunction. Following the Periodic Maintenance Procedures below
can improve the product life span and prevent possible damages to the product.
The following maintenance procedures are based on extensive technical
data and experience. However, it is still possible that issues not mentioned
in this document may arise. Contact the manufacturer if this manual is
insufficient to resolve certain issues.
1) Maintain connection to a reliable source of power to the actuator at ALL times. Perform
monthly test runs on the product if it is not being operated for a long period.
2) If the product does not perform properly after the initial installation, refer to the User
Manual for more information on Power and Signal cable connections.
3) The MHPWS-QNN’s hydraulic system is a closed-loop system meaning that its
hydraulic fluid does not usually require replacement within the product’s life span unless
there has been leakage of the fluid. However, if the operation of the valve is frequent
(more than 10 times daily) or if the valve is constantly exposed to high heat or dry
conditions, we recommend replacing the hydraulic fluid once every 2 years.
4) Regularly inspect and tighten all parts that are prone to loosening (ex. Nut/bolt
connections).
5) If the product is exposed to a large variety of temperatures (ex. drastic difference in
day/night temperatures), regularly examine the MHPWS-QNN for evidence of
condensation or flooding.
6) Refer to the following table for more information on monthly and biyearly (every 6
months) inspection.
Monthly
Inspection
Check the display and LED indicators to ensure that power is
connected.
Examine the MHPWS-QNN for any leakage of hydraulic fluid.
Tes t t o e n sur e t he act uat o r i s o pe r ati ona l.
Tes t t o e n sur e t he man u al han d p ump is ope rat ion a l.
Biyearly
Inspection
(every 6 months)
Ensure proper connection between the valve and the actuator.
Ensure that all connections (especially between the valve and the
actuator) that are prone to loosening are tightened.
Check the amount of fluid in the hydraulic reservoir.
Ensure proper functioning from the F/O state to the F/C state and
backwards.
7) Contact the manufacturer for further inquiries regarding maintenance of the product.
NOTE

M-MHPWS-QNN-CAN-EN
5
1.2 Troubleshooting
If there are issues that arise during the monthly / biyearly inspections or during operation,
refer to the following list of issues and solutions.
1) Power not delivered
Issue 1-1 : The display on the front of the MHPWS-QNN is off.
à Solution 1 : Refer to the circuit diagram of the terminals to ensure proper connection. If all
connections are correct, test the main power supply using a multimeter for proper supply of
power.
à Solution 2 : Check the fuse located in the power board within the CT cover. (Fuse-250V 1A)
Issue 1-2 : The circuit breaker of the external power source breaks the circuit.
à Solution 1 : Refer to the circuit diagram of the terminals in the Interface Manuel to ensure proper
connection.
à Solution 2 : Disconnect the main power cable from the MHPWS-QNN. Inspect for electrical shorts
between the circuit breaker and the MHPWS-QNN. Inspect the MHPWS-QNN’s power
circuitry for electrical shorts in the following order: Terminals 1 and 2, Terminals 2 and 3,
Terminals 3 and 1.
2) Motor malfunction
Issue 2-1 : Motor does not function.
à Solution 1 : Ensure that the Select Switch is setup correctly according to the desired input signal.
Check that the R/S LED indicator beside the display is flashing after a signal is inputted.
Issue 2-2 : Alarm sounds and the ‘3. MOTOR ERR’ message displays on the screen.
à Solution 1 : Press the STOP button locally to disarm the alarm, or cut power from the main power
supply and repower after 5 seconds to initiate power reset. Consult the manufacturer if the
issue persists.
à Solution 2 : Open the Upper Cover to reveal the motor driver, and ensure that power is supplied
properly and the status LED indicator is not indicating an abnormality. Refer to Figure 1.1
for details.
Status LED
Status of the Motor Driver
Green LED is ON
Power is ON
Green LED is OFF
Power is OFF
Red LED is flashing
Motor is not connected
Red LED is ON
Motor Driver Malfunction
Red LED is OFF
Motor Driver is normal
Figure 1.1 [ 600W Motor Driver ]

M-MHPWS-QNN-CAN-EN
6
Issue 2-3 : Motor does not function, Display shows the following message after 15
seconds (time varies on the model): ‘6. VALVE JAMMED’
à Solution 1 : Open the Upper Cover to reveal the motor driver, and ensure that power is supplied
properly and the status LED indicator is working properly. Also, check the fuse of the Motor.
3) Hydraulic pressure not generated
Issue 3-1 : Motor functions normally, but the valve does not move.
à Solution 1 : Inspect the MHPWS-QNN for any leakage of hydraulic fluid.
à Solution 2 : Open the filler cap on top of the pump cover on the right of the MHPWS-QNN to ensure
sufficient amount of hydraulic fuel.
à Solution 3 : Ensure that the needle valve on top of the manual hand pump is closed.
4) Full OPEN / Full CLOSE failure
Issue 4-1 : The F/C or F/O LED indicators do not light up.
à Solution 1 : Ensure that the connection between the valve flange and the actuator is tight. If not,
tighten the bolts. At higher torque values, the immense force is enough to budge or slightly
move the actuator. In this case, install a solid pin between the actuator and the flange for
further stabilization.
à Solution 2 : Check if the Limit Clear switch on the position meter is OFF. Refer to the User Manual for
details.
à Solution 3 : Readjust the position meter’s F/C and F/O settings. Refer to the User Manual for details.
5) Manual hand pump malfunction
Issue 5-1 : No hydraulic pressure is generated from the hand pump.
à Solution 1 : Ensure the needle valve on the hand pump is open as much as possible.
à Solution 2 : Some air could be trapped inside the hand pump. Continue pumping until the air is
compressed and the hand pump is able to generate hydraulic pressure.
Issue 5-2 : Unable to pump, hydraulic pressure is too high.
à Solution 1 : This may be due operating the hydraulic actuator while the needle valve on the top of the
hand pump unit is open. Ensure to close the needle valve after use.
à Solution 2 : Alternate the Direction Control valve (located on the side of the hand pump) 2~3 times in
the OPEN and CLOSE direction to equalize the pressure.
Do not exert excessive force while turning the Needle Valve and the Direction Control
Valve. The Control Valve should only turn 90° between the OPEN and CLOSE
direction.
CAUTION

M-MHPWS-QNN-CAN-EN
7
6) Remote signal not delivered
Issue 6-1 : Unable to monitor the valves remotely.
à Solution 1 : Monitor the valves locally through the display.
à Solution 2 : Disconnect all the valve Status cables from the terminal. Test using a multimeter for a
flow of electricity between the Common and Signal Cables to ensure that the cause of the
problem is not within the MHPWS-QNN.
à Solution 3 : If the problem is not caused between the Common and Signal Cables in the MHPWS-
QNN, ensure all terminal connections are correct. Refer to the circuit diagram.
Issue 6-2 : Unable to control the valves remotely via Dry Contact signals.
à Solution 1 : Ensure that the Select Switch is set to Remote and the Display shows the corresponding
mode.
à Solution 2 : Disconnect all the Signal Cables, check each DI-COM (Loop power) one by one to
identify the cause of the issue.
à Solution 3 : Refer to the Interface Manual for the terminal configuration and details on remote control
to ensure proper connections of the Signal Cables.
Issue 6-3 : Unable to remotely operate in Speed Control Mode
à Solution 1 : Ensure that the specific model of the MHPWS-QNN supports the Speed Control Mode.
Only models K and S are equipped with this feature.
à Solution 2 : Ensure that the Select Switch is set to Remote and the operation mode is set to Speed
Control Mode by checking the Display.
à Solution 3 : Ensure that the desired Position, Speed, and Stop time are entered correctly.
Issue 6-4 : Unable to remotely operate in Step Control Mode
à Solution 1 : Ensure that the specific model of the MHPWS-QNN supports the Step Control Mode.
Only the Model I is equipped with this feature.
à Solution 2 : Ensure that the Select Switch is set to Remote and the operation mode is set to Step
Control Mode by checking the Display.
à Solution 3 : Ensure that the desired Position, Speed, and Stop time are entered correctly.
Issue 6-5 : Valve positions are not displayed accurately during remote control.
à Solution 1 : Ensure that the specific model of the MHPWS-QNN supports an output current of
4~20mA. Compatible models are G, K, M, S, I.
à Solution 2 : Ensure proper connection of the ‘+’ and ‘-‘ signal cables. Refer to the Interface Manual.
à Solution 3 : Disconnect the signal cable and test using a multimeter for DC output from the cables
between 4mA to 20mA.

M-MHPWS-QNN-CAN-EN
8
Issue 6-6 : Unable to remotely operate via 4~20mA (CPT Control)
à Solution 1 : Ensure that the specific model of the MHPWS-QNN supports Modulation Mode. Models
M and S feature modulation in the NML AI Mode and the Model I in the Step AI Mode.
(Models M and S: NML AI Mode, Model I: Step AI Mode)
à Solution 2 : Ensure that the Select Switch is set to Remote and the operation mode is set to
Modulation Mode by checking the Display.
à Solution 3 : Ensure proper connection of the ‘+’ and ‘-‘ signal cables. Refer to the Interface Manual.
à Solution 4 : Disconnect the signal cable and test using a multimeter for DC output from the cables
between 4mA to 20mA.
Issue 6-7 : Unable to remotely operate via 4~20mA (CPT Control) by 1% incremental
control.
à Solution 1 : Check the Keep Band Set in the Functions Settings. To operate with maximum accuracy
(incrementally by 1%), set the Keep Band setting to 0%.
à Solution 2 : Ensure that the remote signal cable is a shielded cable and is connected to either
terminal 31 of the MHPWS-QNN or a contact point at the remote control facility. The
shielded cable should only be connected to one end to reduce electrical interference (noise).
Issue 6-8 : During remote control via 4~20mA (CPT Control), the valve fully closes
when the position inputted was 1% or the valve fully opens when the
position inputted was 99%.
à Solution 1 : Check the Keep Band Set in the Functions Settings. To operate with maximum accuracy
(incrementally by 1%), set the Keep Band setting to 0%.
à Solution 2 : Ensure using a multimeter proper DC output signals.
(1% : 4.16mA±0.04, 99% : 19.84mA±0.04)
à Solution 3 : Remove the CT cover and ensure that the FOC Band Switch of the AIO Card is set to 1%. The
factory default setting is 1%.

M-MHPWS-QNN-CAN-EN
9
2. Disassembly and Assembly
Please be cautious of the following if disassembly of the Main Controller, Power Module Ass’y,
Motor Driver, or Position Meter is necessary for repairs or maintenance.
■ Ensure the environment is safe from any flammable gas or electricity.
■ Ensure all parts are not exposed to water or moisture.
■ Ensure that the power is off.
■ Handle all parts with care and caution
■ Ensure that all screws and holes are clean and not damaged from impact
■ Do not use excessive force to assemble the cover.
2.1 Product Disassembly
1) Main Controller
① -
Main housing
② -
Main controller
③ -
Display Cover Ass'y
④ -
Bolt & Washer
a. Disassemble the Bolt & Washer<④> on the Display Cover Ass'y <③>.
b. Ensure that all the on the cables are not damaged or disconnected while
disassembling the Display Cover Ass'y <③>.
c. Unscrew the Main controller <②> and disassemble the connector.
d. Assemble in inverse order.
CAUTION
Figure 2.1 [ Exploded view of the Main Controller ]
①
②
③
④

M-MHPWS-QNN-CAN-EN
10
2) Power Module Ass’y
① -
C.T. Cover
② -
Bolt & Washer
③ -
Power Module Ass'y
④ -
Main Housing
⑤ -
Terminal Block
a. Disassemble the Bolt & Washer<③>'from'the'C.T.'Cover
b. Remove the bolts that connect the Power Module Ass'y<④> and the C.T. Cover
<②>.
c. Be cautious of the cables connected to the Terminal Block <⑤>.
④
⑤
②
③
Figure 2.2 [ Exploded view of the Power Module Assembly ]
①

M-MHPWS-QNN-CAN-EN
11
3) Motor Driver
a. Remove the Bolt & Washer <①> on the Upper Cover <②>.
b. Unscrew the bolt on the Motor Driver<③> connected to the Upper Cover <②>.
c. Disconnect the power and signal cables connected to the Motor Driver <③>.
① -
Bolt & Washer
② -
Upper Cover
③ -
Motor Driver
④ -
Bolt for Motor Driver
⑤ -
Main housing
④
②
Figure 2.3 [ Exploded view of the Motor Driver ]
③
①

M-MHPWS-QNN-CAN-EN
12
4) Position meter
①-
Bolts for Cover
②-
Cover
③-
Bolts for PM Board
④-
PM Board
⑤-
O-ring
⑥-
Housing
a. Remove Bolts for Cover <①> and separate the Cover<②> from the Housing<⑥>.
The Bolts for Cover <①> are integrated to the Cover<②>.
b. Separate the control cables connected to PM Board<④>.
c. Remove Bolt for PM Board <③> and separate PM Board<④> from Housing<⑥>.
When disassembling, be cautious as to prevent interference between the internal
parts.
①
⑥
④
②
③
⑤
Figure 2.4 [ Position meter ]

M-MHPWS-QNN-CAN-EN
13
2.2 Product Assembly
The product can be assembled in the exact inverse order of disassembly. Please be cautious
of the following during assembly.
■ Ensure all parts being sealed are free of any contaminants.
■ Apply small amounts of grease (not acidic) on the surface of the seal.
■ Inspect the O-Ring for damages or deformation. Place the O-Ring precisely.
■ Handle all parts with care.
■ Tighten all screws and bolts as much as possible.
3. Product Disposal and Recycling
The following are types of waste that can be produced during and after maintenance.
■ Oil / Grease
■ Plastics
■ Metals
■ Electronic waste
Oil and grease are factors that cause water pollution. We strongly
recommend the separation of any oil or grease during the disposal
process. Always dispose responsibly.
Contact the manufacturer for any electronic parts that could be recycled
or reused in which case the manufacturer will undertake a collection
process.
CAUTION

M-MHPWS-QNN-CAN-EN
14
4. Drawing
4.1 Exploded View Drawing
Figure 4.1 [ Exploded view of the MHPWS-QNN ]

M-MHPWS-QNN-CAN-EN
15
4.2 Parts List
NO
DESCRIPTION
MATERIAL
Q'TY
REMARK
01
Main Housing
AC4C-T6
1
RND14-015-A-001
01-1
Tank Pipe
STS304
1
Ø6 X 1T X 125L (M6)
01-2
Plug
STS316
3
DVSTI-M10ED (M10X1.0P)
01-3
Pressure Plug
SCM
1
PT1/8
01-4
O-Ring
NBR
1
AN-166
01-5
O-Ring
NBR
5
AN-109
01-6
Oil Seal
NBR
1
Ø14 X Ø25 X 7
02
Pump Cover
AC4C-T6
1
RND14-015-A-004
02-1
Wrench Bolt
STS304
4
M10 X 1.5P X 25L
02-2
Spring Washer
STS304
4
M10
02-3
Plug
STS316
1
DVSTI-03GED (PF3/8)
02-4
Plug
STS316
1
DVSTI-M10ED (M10X1.0P)
02-5
O-Ring
NBR
1
AN-161
03
CT Cover
AC4C-T6
1
RND14-015-A-002
03-1
Wrench Bolt
STS304
4
M10 X 1.5P X 25L
03-2
Spring Washer
STS304
4
M10
03-3
Roundhead + Home Sems Bolt
STS304
2
M6 X 1.0P X 10L
03-4
O-Ring
NBR
1
AN-161
03-5
Explosion Proof Plug
AL
1
PF1
03-6
Explosion Proof Plug
AL
2
PF3/4
04
Terminal Cover
AC4C-T6
1
RND14-015-A-003
04-1
Wrench Bolt
STS304
4
M10 X 1.5P X 25L
04-2
Spring Washer
STS304
4
M10
04-3
O-Ring
NBR
1
G-140
05
Upper Cover
AC4C-T6
1
RND15-004-A-006
05-1
Wrench Bolt
STS304
10
M6 X 1.0P X 15L
05-2
Spring Washer
STS304
10
M6
05-3
Motor Drive
*SWIS
1
SBDSMD-05A
05-4
Roundhead + Home Sems Bolt
SS400
4
M4 X 0.7P X 12L
06
Display Cover Ass’y
-
1
RND15-004-A-007
06-1
Wrench Bolt
STS304
1
M10 X 1.5P X 20L
06-2
Spring Washer
STS304
4
M10
06-3
O-Ring
NBR
1
AN-159
06-4
Main Controller
RPMTECH
1
MHP-A1S46-AA-MAIN
06-5
Roundhead + Home Sems Bolt
SS400
4
M4 X 0.7P X 8L
*SWIS: Sewoo Industrial Systems Co., LTD

M-MHPWS-QNN-CAN-EN
16
NO
DESCRIPTION
MATERIAL
Q'TY
REMARK
17
Name Plate
STS304
1
RND15-024-A-011
17-1
Button Head Wrench Bolt
STS304
4
M4 X 0.7P X 5L
18
Power Module Ass’y
RPMTECH
1
MHP-A1S46-AA-MAIN
18-1
Roundhead + Home Sems Bolt
SS400
2
M4 X 0.7P X 5L
19
Terminal Block
PBT+GF30%
1
RND15-004-A-013
19-1
Wrench Bolt
STS304
8
M4 X 0.7P X 15L
19-2
Flat Washer
STS304
8
M4
19-3
O-Ring
NBR
1
G-100
21
600W Brushless DC Motor
*SWIS
1
RND15-004-A-014
21-1
Wrench Bolt
SCM
4
M6 X 1.0P X 20L
21-2
Spring Washer
SCM
4
M6
22
Manifold B Ass’y
-
1
MFB121202
22-1
Wrench Bolt
SCM
4
M6 X 1.0P X 30L
22-2
Spring Washer
SCM
4
M6
22-3
O-Ring
NBR
1
AN-027
23
Quarter-turn Cylinder
KSB Seil
1
HQ25~HQ1600
23-1
Spring Washer
STS304
6
M10
23-2
Wrench Bolt
STS304
6
M10 X 1.5P X 130L
24
Position Meter
RPMTECH
1
DPMW ASS'Y
24-1
IP68 Connector
PMA
2
BVNV-G027
24-2
IP68 Tube
PMA
1
LLPA-17A
24-3
Wrench Bolt
SCM
4
M8 X 1.25P X 25L
24-4
Spring Washer
SCM
4
M8
25
Hand Pump
RPMTECH
1
-
25-1
O-Ring
NBR
2
AN-109
*SWIS: Sewoo Industrial Systems Co., LTD
(Table does not include cables)

M-MHPWS-QNN-CAN-EN
17
MEMO
Other manuals for MHPWS-QNN Series
1
Table of contents
Other RPM Controllers manuals
Popular Controllers manuals by other brands
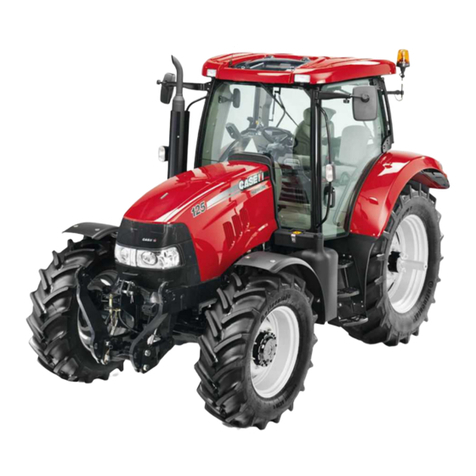
Case IH
Case IH MAXXUM 100 Service manual
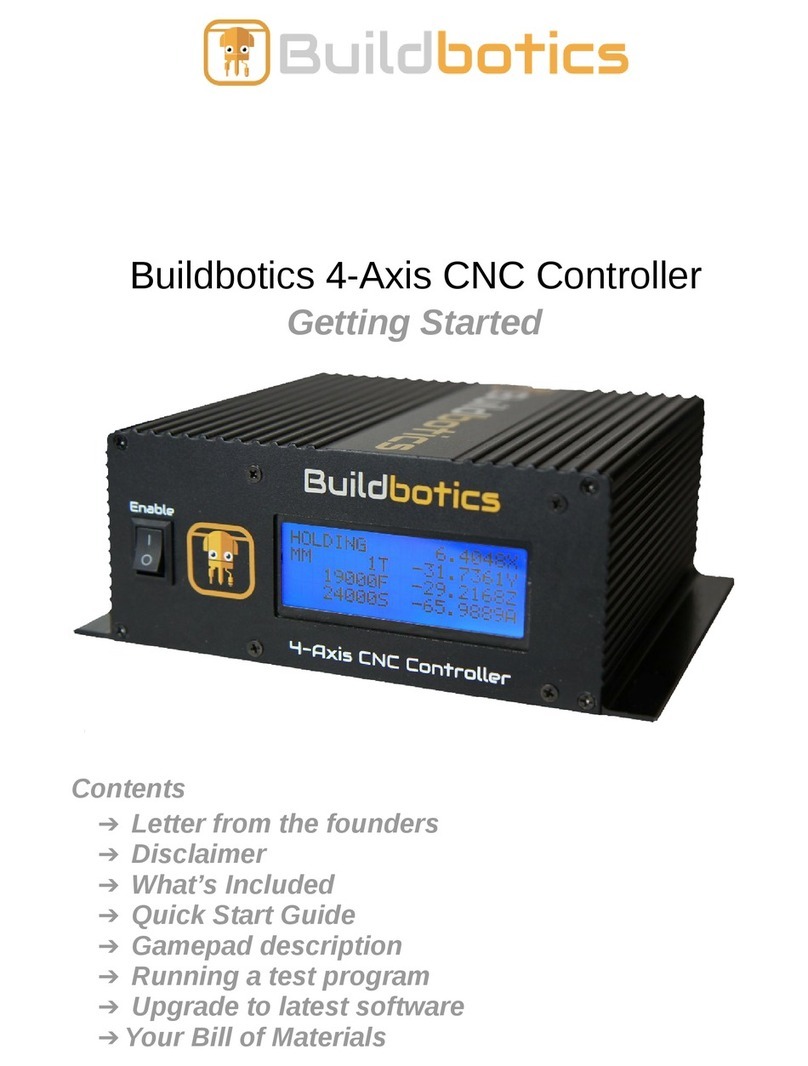
Buildbotics
Buildbotics 4-Axis CNC Controller Getting started
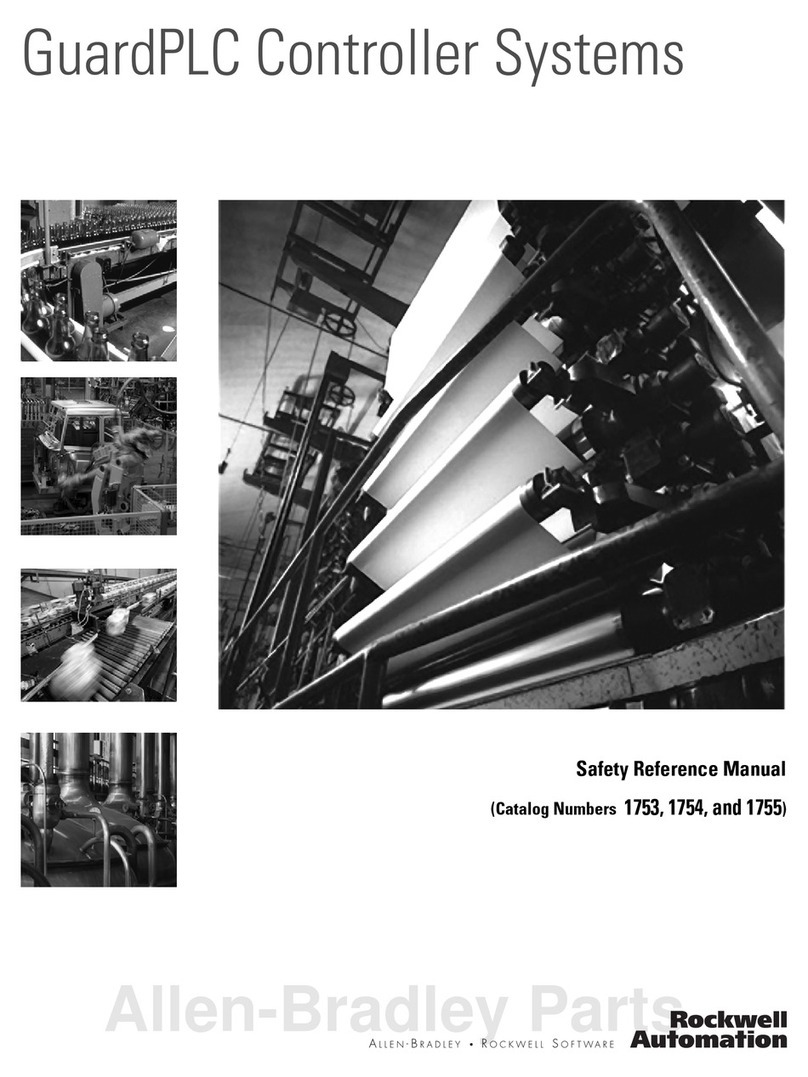
Allen-Bradley
Allen-Bradley GuardPLC 1754 Safety Reference Manual
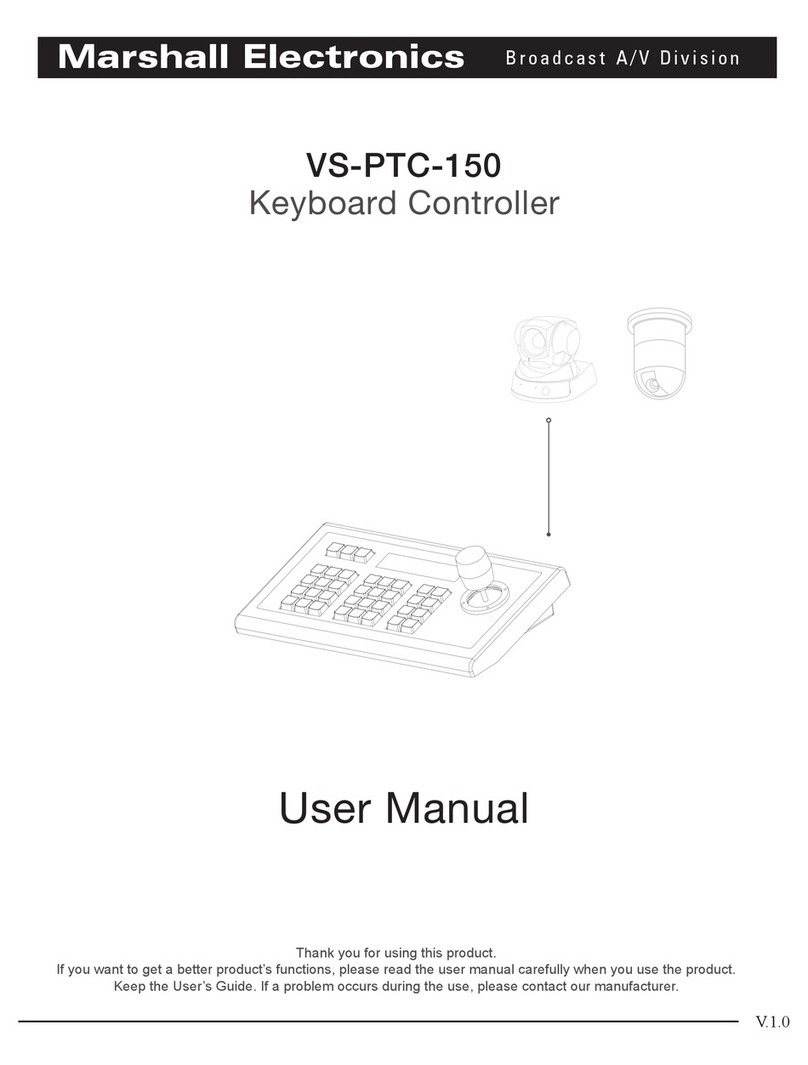
Marshall Electronics
Marshall Electronics VS-PTC-150 user manual
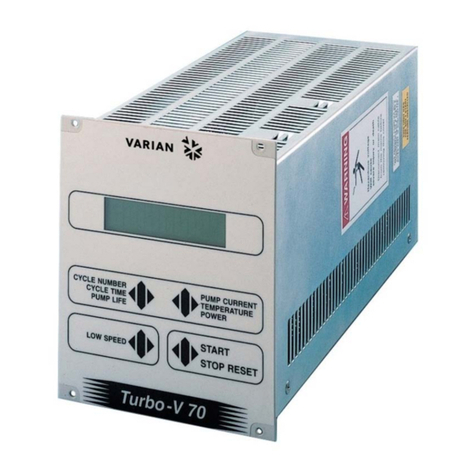
Varian
Varian Turbo-V 70 instruction manual

Brivis
Brivis ZonePlus B061006 Installer manual