RTA HI-MOD ET A Assembly Instructions

R.T.A. s.r.l. – HEAEME06 – 03/22
MOTION CONTROL SYSTEMS
HARDWARE INSTRUCTION MANUAL
STEPPING MOTOR DRIVES
HI-MOD ET A – HI-MOD ETS A
HI-MOD ET E – HI-MOD ETS E
R.T.A. s.r.l.
Via E. Mattei
– Frazione DIVISA
27020 MARCIGNAGO (PV)
Tel. +39.0382.929.855 - Fax +39.0382.929.150
R.T.A.
DEUTSCHLAND GmbH
Bublitzer Straße, 34
40599 DÜSSELDORF (Germany)
Tel. +49.211.749.668.60-Fax +49.211.749.668.66
Internet: http://www.rta-deutschland.de
e-mail: info@rta-deutschland.de
R.T.A. IBERICA
MOTION CONTROL SYSTEMS S.L.
C/Generalitat 22, 1° 3°
08850 GAVA – BARCELONA (Spain)
Tel. +34.936.388.805-Fax +34.936.334.595
Internet: http://www.rta-iberica.es
e-mail: [email protected]

R.T.A. s.r.l. – HEAEME06 – 03/22 2/19
INDEX
1.
NOTICES AND MANUAL STRUCTURE ........................................................................... 3
2.
LIMITATIONS, HAZARDS AND CAUTIONS........................................................ 4
3.
GENERAL CHARACTERISTICS AND IDENTIFICATION ................................................ 5
3.1.
H
I
-M
OD
ET
AND
H
I
-M
OD
ETS
IDENTIFICATION
...............................................................5
4.
MODELS WITH CONNECTORS: DIMENSIONS AND CONNECTIONS........................... 6
4.1.
M
ECHANICAL DIMENSIONS
.............................................................................................6
4.2.
E
LECTRICAL CONNECTIONS
...........................................................................................6
4.3.
CN1
CONNECTOR
........................................................................................................7
4.4.
CN2
CN3
E
THER
CAT
CONNECTORS
............................................................................8
4.5.
E
XTERNAL CONNECTIONS
.............................................................................................9
5.
DRIVE CHARACTERISTICS ........................................................................................... 10
5.1.
N
OMINAL VALUES OF ELECTRICAL AND ENVIRONMENTAL CHARACTERISTICS
.....................10
5.2.
O
PERATION MODE AND ALLOWED DUTY CYCLE
..............................................................10
6.
ELECTRICAL DIMENSIONING OF EXTERNAL COMPONENTS .................................. 10
6.1.
P
OWER SUPPLY
.........................................................................................................10
6.2.
F
USES
......................................................................................................................11
6.3.
E
ARTH CONNECTIONS
.................................................................................................11
6.4.
L
ENGTH AND SECTION OF POWER SUPPLY CABLES
........................................................11
6.5.
E
THER
CAT
CONNECTIONS
.........................................................................................11
7.
APPLICATION NOTES ....................................................................................... 11
7.1.
E
LECTROMAGNETIC INTERFERENCES AND IMMUNITY
(
DIRECTIVE
2014/30/CE)................11
8.
STO FUNCTION (FOR HI-MOD ETS).............................................................................. 13
WARNING
: It is user RESPONSIBILITY to check that this manual refers
to product model and version that will be used.
Symbol meaning
The section marked with this symbol contains warnings regarding safety problems. If the directions
indicated in these sections are not fulfilled, it could arise hazardous situations .
The section marked with this symbol contains information regarding operations which are strictly
forbidden.

R.T.A. s.r.l. – HEAEME06 – 03/22 3/19
1. NOTICES AND MANUAL STRUCTURE
1.1 - This manual covers the following items:
•HI-MOD ET and HI-MOD ETS series stepping motor drives in all their standard versions
•Standard characteristics of special versions of HI-MOD ET and HI-MOD ETS series stepping motor
drives
•For models and versions identification see also chapter 3.
This manual covers hardware characteristics of models described in Chap. 3.1 and contains informations
for mounting and electrical connections of these drives. Software characteristics are described in
programmer’s manual.
1.2 - Products described in this manual (see identification code in chapter 3) complies with Low Voltage
(2014/35/CE) and Electromagnetic Compatibility (2014/30/CE).
Product standards:
1) UL508C – Power Conversion Equipment
2) CSA C22.2 No.274 – Adjustable Speed Driver
1.3 - Remember that, as stated in all directives, compliance exists only when a product is used in accordance
with its destination and following manufacturer prescriptions. Thereby, all relevant indications about use,
cautions, installation and limitations here described must be followed by user in order to stay within
compliance limits; from this point of view the entire content of this manual has to be carefully read and
considered in order to obtain the information necessary for a correct use.
1.4 - Conformity declaration regarding above mentioned products is kept by R.T.A. (as manufacturer residing
in EEC country) together with technical construction file at authority disposal.
1.5 - This manual is conceived in a way to offer to the personnel involved in project and safety verification of a
machine all information concerning characteristics, working conditions, application limits and cautions
about stepping motor drives. The knowledge of this information is essential for a correct project of
machines, apparatus and systems in which the drives are used; it is strongly recommended not to start
any operation with the drives before you have completely read and understood the content of this
manual; if you find some part of this manual not completely understandable or lacking regarding your
particular application, do not hesitate to contact directly R.T.A. that can provide, if necessary, further
information in order to make the user able to design his machine and the related safety systems in the
best way. Take into account that an incorrect use or installation, a wrong dimensioning of external safety
elements related with the drive could bring to economical damages and also to hazards for human life.
1.6 - Consider the fact that these are products with a very wide range of possible applications in many
different working and environmental conditions. For this reason this manual can only fix limits and
general rules but cannot take in consideration every single possible application condition. If you have
problems to understand some part of this manual or to meet its indications with your specific application,
do not hesitate to contact R.T.A. for further information. Take into account that R.T.A. has twenty years of
experience in any kind of applications, which cannot be condensed in a manual but can always be at
customer disposal.
1.7 - The terms "user and customer" often used in this manual always indicate a skilled person.
1.8 - This manual is considered valid at the moment of the selling of the product. It cannot be considered
inadequate as a consequence of product or manual changes or improvements after the selling. R.T.A.
reserves the right of products and manual revisions without notice neither obligation of previous products
and manuals revision.

R.T.A. s.r.l. – HEAEME06 – 03/22 4/19
2. LIMITATIONS, HAZARDS AND CAUTIONS
2.1 - It is not allowed the use in any condition not complying with one or more specific limitations stated in this
manual for electrical, mechanical and environmental quantity or characteristics.
2.2 - HI-MOD ET and HI-MOD ETS series drives must be mounted as in Fig. 1. Do not take out or insert
connectors when the drive is switched on.
2.3 - HI-MOD ET and HI-MOD ETS series drives contain capacitors able to store a certain amount of electrical
energy. As a consequence, in some cases, according with application conditions and supply
dimensioning, a dangerous voltage could remain on the drive, after switching off, for a time greater than
5 seconds. So it is recommended to wait an adequate time before working on the drive.
2.4 - The heatsink can reach high temperatures during normal working conditions. Do not touch this
component for some minutes, after switching off, in order to avoid scald hazard.
2.5 - The drives are suitable to be installed in environment with pollution degree 3, see Chap. 7.1. The
installation in environments in which flammable and/or explosive, and/or chemically aggressive and/or
electrically conductive gas, vapor or dust could be present is strictly forbidden. Avoid also to install near
easily flammable or sensitive to heat materials and components; we recommend to verify that all the
components located in the enclosure are realized using self-extinguishing materials.
2.6 - All products considered in this manual are sub-assemblies without a direct function, foreseen to be
integrated in a more complex machine. Only a professional assembler, expert in the field of motor drives
and in their related problems, can install and put in service this component. It is exclusive responsibility of
the designer of the complete machine or installation in which this component is used to take care of the
safety and reliability of his project. It is forbidden to use this material in application covered from one or
more EEC directives (for instance 2014/30/CE, 2006/42/CE, etc.) before the conformity to those
directives has been declared. Regarding 2014/30/CE directive, see chapter 7.
2.7 - Use for safety related functions is forbidden (EN 60204-1). Moreover, when the application arrangement
is in such way that a drive fault or failure could generate a dangerous condition, external independent
safety protection system must be provided in the machine.
2.8 - In some case of drive failure, dangerous high voltage could appear at logic low voltage input and output
terminals, even if this event is extremely rare. For this reason, from the point of view of evaluation of the
machine safety during a single fault condition, the external control system, connected to these inputs,
has to be considered potentially subjected to high voltage, unless an external separation is provided.
2.9 - EtherCAT commands used to interrupt power to the drive outputs and internal electronic functional
protections switch off the drive output power by means of semiconductor devices; they cannot be used to
interrupt power in some emergency stop function or in any function involving personnel safety.
2.10 - Some versions of Hi-MOD ET have threaded holes that allow the connection of an external source of
inert gas so that the pressure inside the drive become positive with respect to the environment. The
threaded holes must always be connected to specific fittings or plugs, even when not used.
Any different use of that holes is forbidden. RTA does not take any kind of responsibility for property
losses, equipment damages and personnel injuries resulting from use or installation of the product
without the appropriate plugs.
2.11 - In the case of an Ethercat connector is not in use, it is strongly recommended to protect the drive plug by
means of a suitable M12 dust cover.

R.T.A. s.r.l. – HEAEME06 – 03/22 5/19
3. GENERAL CHARACTERISTICS AND IDENTIFICATION
3.1. Hi-Mod ET and Hi-Mod ETS identification
The models identification of HI-MOD ETS series drives is as follows:
HI MOD ET
A5DxHn.m
HI MOD ET
A5FxHn.m
HI MOD ETS
A4FxHn.m
HI MOD ETS
E4FxHn.m
x
= Stepping motor model
11 stack 86mm motor (6 Amps)
22 stack 86mm motor (6 Amps)
n
= Release software (alphanumeric character)
m
= special version with some variations regards to standard models (is not present in standard
models and it is alphanumeric character if present).
Each sample is also identified with a serial number.

R.T.A. s.r.l. – HEAEME06 – 03/22 6/19
4. MODELS WITH CONNECTORS: DIMENSIONS AND CONNECTIONS
4.1. Mechanical dimensions
2 Fori
1/8 NPT
Figure 1 – Dimensions in mm.
4.2. Electrical connections
Electrical connections include:
•Cannon connector 15 terminals for power supply and logic signals (CN1 Figure 2b).
•Two connectors for IN and OUT EtherCAT (CN2, CN3 Figure 3) to allow a daisy-chain connection.
X
M Length
1
66 mm
2
96.5 mm
3
127 mm
STANDARD MOUNTING POSITION

R.T.A. s.r.l. – HEAEME06 – 03/22 7/19
4.3. CN1 connector
1 O0 OUTPUT.
Auxiliary output.
2 I1 INPUT.
Auxiliary input. This input is optically insulated towards internal power circuits. This input is ON
(logic level 1) when at its terminals there is a voltage between 8 and 24 Volt. This input is OFF
(logic level 0) when there is a voltage < 1.5 Volt.
3 I0 INPUT.
Auxiliary input/proximity input (setting through software); when input is ON, PX is the reference for
a zero search procedure This input is optically insulated towards internal power circuits. This input
is ON (logic level 1) when at its terminals there is a voltage between 8 and 24 Volt. This input is
OFF (logic level 0) when there is a voltage < 1.5 Volt.
4 COMMON OF INPUTS and O0 OUTPUT.
Internally connected to terminal 13.
5 +24 VDC.
Control logic supply positive pole (20-24 Vdc).
6,14,15 COMMON OF POWER SUPPLY VOLTAGE.
- HVDC: Power supply negative pole ( - V
DC nom
), and -24 VDC (logic supply negative pole). Supply
negative poles must be connected to earth (PE) of power supply side.
7, 8 +HVDC.
Power supply positive pole (+ V
DC nom
). Use both 7 and 8 terminals.
9 O1 OUTPUT (for HI-MOD ETS).
EDM OUTPUT (Error Detection Monitor) / Driver FAULT OUTPUT (setting through software,
see software manual).
If it is set as EDM (Error Detection Monitor), this output is ON if both STO1 and STO2 inputs are
OFF. In this case the drive is in Safe Torque Off operation mode and the current flowing in each
motor winding is inhibited. The output is OFF if one or both STO1 or STO2 inputs are ON.
If it is set as Driver FAULT OUTPUT, output is ON when drive is active; output is OFF when drive
is blocked by a protection.
O1 OUTPUT (for HI-MOD ET).
If it is set as Driver FAULT OUTPUT, output is ON when drive is active; output is OFF when drive
is blocked by a protection.
10 COMMON OF O1 OUTPUT.
11 STO1 INPUT (for HI-MOD ETS).
With this signal ON drive is active (with flowing current in each motor winding) on condition that
STO2 input is ON. When STO1 is OFF the drive is inhibited, thus motor current (and so holding
torque) is turned to zero.
I2 INPUT (for HI-MOD ET).
Auxiliary input. It is optically insulated from internal power circuits.
This input is ON (logic level 1) when at its terminals there is a voltage between 8 and 24 Volt. This
input is OFF (logic level 0) when there is a voltage < 1.5 Volt.
Maximum signal frequency of I2 input can not be > 50 Hz.
12 STO2 INPUT (for HI-MOD ETS).
With this signal ON drive is active (with flowing current in each motor winding) on condition that
STO1 input is ON.
When STO2 is OFF the drive is inhibited, thus motor current (and so holding torque) is turned to
zero.
I3 INPUT (for HI-MOD ET).
Auxiliary input. It is optically insulated from internal power circuits.
This input is ON (logic level 1) when at its terminals there is a voltage between 8 and 24 Volt. This
input is OFF (logic level 0) when there is a voltage < 1.5 Volt.
Maximum signal frequency of I3 input can not be > 50 Hz.
13 COMMON OF STO INPUTS (for HI-MOD ETS).
COMMON OF INPUTS AND OUTPUT O0 (for HI-MOD ET).
Internally connected to terminal 4.

R.T.A. s.r.l. – HEAEME06 – 03/22 8/19
I0 and I1 inputs structure scheme CN1 Connector
DRIVE
GND
R2
R1
Common
of inputs
8 < Vin < 24 Volt
R1 = 2.2 KOHM
R2 = 680 OHM
(a)
(b)
I
nputs structure scheme
STO1, STO2
(HI-MOD ETS)
Inputs structure scheme I2, I3
(HI-MOD ET)
O0 and O1 outputs structure scheme
DRIVE
R2
R1 (1W)
In+
Vin = 24 Volt
R1 = 3.3 KOHM
R2 = 390 OHM
18 Volt < Vin < 27 Volt
H
0 Volt < Vin < 3 Volt
L
DRIVE
Out
9
NOTE:
Insert a protection diode in parallel
with the load in case of inductive load
Vmax = 45 Volt
Vsat 0.8 Volt (@ 10 mA)≤
Out
10
Imax = 5 mA for output O0
Imax = 50 mA for output O1
(c)
(d)
Figure 2– Inputs and outputs scheme.
4.4. CN2 CN3 EtherCAT connectors
Two standard Ethernet M12 modular connectors (IN, OUT) are provided for the EtherCAT communication. The
same pin disposition (same signal) is assigned for both connectors. Figure 3 shows connector M12 connectors
used for connection between the drive and the control system.
1 Trasmit Data+: trasmit data positive pole;
2 Receive Data+: receive data positive pole;
3 Trasmit Data-: trasmit data negative pole;
4 Receive Data-: receive data positive pole.
Connect IN to the higher-level device and OUT to the next slave.
Use twisted-pair cables that satisfy at least “Category 5e” to connect the cable.
When you make cables using exclusive tools, use STP (Shielded twisted pair cable) and M12 modular plug
with shield.
CN3 IN
(Female)
1
2
4
3
12
43
CN2 OUT
(Female)
Figur
e
3
–
CN2 and CN3 connectors (front side)

R.T.A. s.r.l. – HEAEME06 – 03/22 9/19
4.5. External connections
+
PE_2
C1
F1
220
V
AC
V nom
AC
PE_1
HVDC-
HVDC+
CN1
CN3 INCN2 OUT
F2
EtherCAT
CONNECTION
EtherCAT
CONNECTION
EMI FILTER
Fuses
Transformer
Figura 4a
–
HI-MOD ET connections scheme
Figura 4b –
HI-MOD ETS connections scheme
Note 1: See Chap. 7 and software manual, cap 3.7 for power supply and fuses
dimensioning and features.
Note 2: See Chap. 8 for connections of STO1 and STO2 inputs and EDM output.
Note 3: See software manual, cap. 3.7 for informations about reverse energy

R.T.A. s.r.l. – HEAEME06 – 03/22 10/19
5. DRIVE CHARACTERISTICS
5.1. Nominal values of electrical and environmental characteristics
Table 1
V
DC
nom (V) 80
V
DC
nom tolerance (%) +/-20
Pnom (W) 310
I nom (A) 4.0
Iph nom (A) 4.3
Iph % (H motors) (%) 0÷120%
Operating temperature (%) from + 5°C to + 40°C
Environment installation pollution degree 3
Overvoltage category II
Insulation Class F
Definition of terms used in Table 1:
V
DC
nom:
Nominal value of DC voltage supply at the drive input.
Tolerance:
Maximum percentage variation allowed regard to VDC nom values.
I nom:
Nominal current at the drive power supply input.
Pnom:
Nominal power absorbed by the drive.
I
ph
nom
RMS value of motor nominal phase current.
I
ph
%:
Percentage values
regard to phase current nominal values, setting by means of software
commands (see software manual).
5.2. Operation mode and allowed duty cycle
Hi-Mod series drives are suitable for intermittent operation mode. Table 2 shows allowed duty cycle limits:
Table 2
Motors 1H, 2H and 3H Motors 2M and 3M
Speed (RPM) ≤300 > 300 ≤300 >300
Max duty cycle (%) 30 25 50 40
Maximum cycle (Sec) 240
6. ELECTRICAL DIMENSIONING OF EXTERNAL COMPONENTS
6.1. Power supply
Power supply shown in Figure 4 can be realized with single-phase bridge rectifier (as indicated in figure) or with
three-phase bridge rectifier. C1 filter capacitor can never have a capacitance below 4700 x n µF
(n = number of
drives connected to the same power supply). The use of three-phase solution has to be preferred when the
number of drives connected to the same power supply is more than three.
Power supply must fulfill the following requirements:
•Separation from the main: the separation from the main must be granted in order to ensure that
the over-voltage category of the DC side is II.
•Nominal power of power supply has to be the sum of every single connected drive power.
•Short-circuit current must be lower than 1000 Amp

R.T.A. s.r.l. – HEAEME06 – 03/22 11/19
6.2. Fuses
•F1 fuses (or equivalent protection systems) must be dimensioned in accordance with total
power of power supply.
•F2 fuse: a Branch circuit protection fuse 8 Amp must be for each drive. The fuse that fulfils
requirements of UL directive is the following:
Class CC - Current Limiting Time-Delay - Rated: 150 Vdc – 600 Vac 8 A
Fuse: Listed – Cartridge Fuses (JDDZ)
Manufacturer: Cooper Bussmann LLC - Model No.: LP-CC – 8 A
6.3. Earth connections
The points PE_1 (drive case) and PE_2 (power supply negative pole) must be connected to earth line of the
machine (PE). The length, section, and topology of the connections that connect PE_1 and PE_2 have to be
realized in a way to present the less possible inductance.
6.4. Length and section of power supply cables
For power supply can be used AWG16 cables for a length of 25 mt.
6.5. EtherCAT connections
For this connection can be used whatever EtherCAT bus cable in accordance with valid directive and with drive
connectors.
7.
APPLICATION NOTES
7.1 Electromagnetic interferences and immunity (directive 2014/30/CE)
HI-MOD ET and HI-MOD ETS series drives are BDM (Basic Drive Module) conceived for restricted
distribution (EN 61800-3). This means that R.T.A. has the responsibility to verify the products
compatibility in some typical way of use in order to give correct installation information. In any cases, it is
responsibility of the professional assembler, who installs this product, to verify the compatibility of the
complete machine or system.
7.2 The set consisting of drive, motor and all related cablings are source of electromagnetic interferences.
The assembler of installation must consider these problems during the project of the plant where the
drive (or drives) will be installed in order to shield and/or reduce these interferences. Tests performed by
R.T.A. show that the most effective measures able to reduce these interferences are the following:
•Use only shielded cable for power supply.
•Interpose an EMI filter (CORCOM mod. 6VDK1) on the transformer power that is used to supply the
drives in order to reduce conducted electromagnetic interferences.
•Connection made to Protective Earth terminal (PE), shown in Fig. 4, must be short and have the
lowest possible inductance.
•All connections made to Protective Earth (PE) must be realized to have the lowest possible
inductance.
7.3 Considering drive logic input signals immunity from external noise present in the environment in which
they are most often used, take in account following normal procedures, suggested from the classical
techniques about relatively fast signals treatment:
•Use shielded cables.
•Keep shielded signal cables separate from shielded power cables.
•Verify carefully logic level compatibility when interfacing drive with control system.
7.4 A correct accomplishment of these procedures constitutes an essential starting point in order to realize
an installation which complies with the requirements of 2014/30/CE directive. The effective compliance
with specific standards covering the particular application in which this drive is used will have in any

R.T.A. s.r.l. – HEAEME06 – 03/22 12/19
case to be proved in the complete installation, because the effectiveness of suggested actions depends
also on machine topology and on their correct fulfillment. Tests performed by R.T.A. simulating typical
installations and following above mentioned indications show that it is possible to stay within the limit of
EN61800-3 standard.
7.5 In some cases, due to the characteristics of particular installations, conflicts between ground
connections necessary for shielding purposes and ground connections necessary for safety reasons
could arise. Remember that, in such cases, prescriptions regarding safety take priority, but remember
also that, in the great majority of cases it is possible to find a solution meeting both prescriptions;
R.T.A. is at disposal for further information about these problems.
7.6
REVERSE ENERGY MANAGEMENT.
During deceleration of load with high inertia, some amount of energy can flow from motor to drive. In
case of excessive reverse energy, an overvoltage protection could inhibit the drive operation making
impossible the application. During the test of a new application in which there are decelerations starting
from relatively high speed, with high inertial load, always check carefully the operation conditions
during the decelerations.
If speed problems occur, it is necessary to check speed and acceleration parameters of the application
and make sure about the value of the capacity in the power supply.

R.T.A. s.r.l. – HEAEME06 – 03/22 13/19
8. STO FUNCTION (for HI-MOD ETS)
8.1-
SYSTEM CONFIGURATION DESCRIPTION
STO1
Monitor
STO2
SAFETY UNIT
Safety
output
Feedback
input
Emergency
Stop button
CN1
Figure 5
– Connection scheme.
8.2-
STO FUNCTION
Safe-torque-off function reduces injury risks and ensures the safety for those who work near moving
parts of equipment. This function employs 2-channel input signal that independently block the motor
current.
8.3-
STO FUNCTION SCHEME DESCRIPTION
STO function disables the current flowing into motor windings.
Each of two STO1 and STO2 channels act independently to shut down motor current. A failure of one
single channel does not compromise the activation of the safety function.
8.4-
STANDARD CONFORMITY
STO function meets the following safety standards:
•IEC 61800-5-2, safe torque off (STO)
•IEC 61508, SIL3
Probability of a dangerous failure per hour, with use of Error Detection Monitor (EDM) to grant
Diagnostic Coverage (DC), is described in the following table:
PHFd Test Timing Mission Timing SIL
3.54x10
-
10
1 month 10 years 3
4.11x10
-
10
10 years 10 years 3

R.T.A. s.r.l. – HEAEME06 – 03/22 14/19
8.5-
RISK ASSESSMENT
The drive meets the requirements safety standards above described.
However, before activating safety function, make sure to assess the risks associated with the overall
equipment to ensure complete safety.
8.6-
RESIDUAL RISK
Even if STO function is active, the following risks remain. Please ensure the installation safety is
maintained, even in case the below-indicated situations occur, through a correct risk assessment.
1. When STO function is activated while the motor is running, the current into the motor is shut down. The
motor continues to run due to inertia. Please make sure to ensure safety conditions of the system to
avoid any danger until the motor stops completely.
2. When the motor is used in vertical axes, it is possible that without holding torque, the axes rotate due to
gravity. In this case, it is necessary to provide external device (i.e. electromagnetic brake) to stop the
motor within requested range.
3. In case of short circuit or failure of power device transistor, the motor could make an uncontrolled
movement within a range up to 180 degrees in electrical angle (180 degrees in electrical angle=1/50 of
a turn) and then remain a stable position. It is necessary to verify that this limited movement does not
correspond to some risky conditions.
4. Be sure that SAFE TORQUE OFF function properly works before machine use, at first machine start-
up and at every drive replacement. If input / output signals are not used correctly, the STO function
doesn’t work properly and dangerous situation can occur.
5. When STO function is active, the drive power supply is not shut down. In case of maintenance or check
of the drive, please be sure to shut down power supply to avoid electric shock.
8.7-
CONNECTIONS
All input and output logic signals are optically insulated among them and from internal power circuits.
Positive and negative terminals are separately accessible. For all logic signals in the following we
indicate the corresponding numbers of connector C2. An input signal is considered ON when a voltage
is applied (Fig. 2a).
9 and 10 EDM OUTPUT (ERROR DETECTION MONITOR):
this output is ON if both STO1 and
STO2 inputs are OFF. In this case, the drive is in Safe Torque Off operation mode and the current
flowing in each motor winding is inhibited. The output is OFF if one or both STO1 or STO2 inputs are
ON.
12(+) and 13(-) STO2 INPUT:
with this signal ON drive is active (with flowing current in each motor
winding) on condition that STO1 input is ON. When STO2 is OFF the drive is inhibited, thus motor
current (and so holding torque) is turned to zero.
11(+) and 13(-) STO1 INPUT:
with this signal ON drive is active (with flowing current in each motor
winding) on condition that STO2 input is ON. When STO1 is OFF the drive is inhibited, thus motor
current (and so holding torque) is turned to zero.

R.T.A. s.r.l. – HEAEME06 – 03/22 15/19
STO1 and STO2 inputs structure scheme MONITOR output structure
DRIVE
R2
R1 (1W)
In+
Vin = 24 Volt
R1 = 3.3 KOHM
R2 = 390 OHM
18 Volt < Vin < 27 Volt
H
0 Volt < Vin < 3 Volt
L
DRIVE
Out
9
NOTA:
Insert a protection diode in parallel
with the load in case of inductive load
Vmax = 45 Volt
Vsat 0.8 Volt (a 10 mA)≤
Out
10
Imax = 50 mA
(
6
a)
(
6
b)
Figure 6
– STO1 and STO2 inputs and EDM output scheme.
Emergency
Stop Button
11
13
12
STO1+
STO-
STO2+
0V
Safety Unit
9
10
EDM+
EDM-
Output
Monitor
Input
Drive
Figure 7
– Wiring to SAFETY UNIT example.

R.T.A. s.r.l. – HEAEME06 – 03/22 16/19
8.8-
ENABLE / DISABLE STO: TIMING INDICATIONS
The correct and stable enabling of STO function is effective after a maximum time of 20 ms after STO1
and STO2 switching off.
Monitor Output indicates that STO function is active with a maximum delay of 20 ms from STO1 and
STO2 input signals switch off (Figure 8).
ON 24 V
max 20ms
OFF 0 V
DRIVE
STATE
MONITOR
STATE
STO1, STO2
ON
SAFE TORQUE OFF
Figure 8
– STO Timing.
8.9-
TIMING OF INPUT-OFF SHOT PULSE FOR SAFETY DEVICE SELF-DIAGNOSIS
In case of the safety device perform self-diagnosis through input-off shot pulses, the input-off shot
pulse must have a maximum duration of 1 ms.
STO function is not activated when the period of STO inputs signal STO1 / STO2 - OFF is 1 ms or less.
In order to surely grant the activation of the Safe Torque Off function, it is necessary that STO1 and
STO2 input signals are turned off for 20 ms or more.
NOTE:
When STO1 and STO2 input signals switch ON and OFF in a range of 1-20 ms, motor loss of
synchronism and/or wrong signaling can occour.
ON
max 1ms
OFF
DRIVE
STATE
MONITOR
STATE
STO1, STO2
ON
SAFE TORQUE
OFF
max 20ms
Figure 9
–STO Self-Diagnosis Timing.

R.T.A. s.r.l. – HEAEME06 – 03/22 17/19
8.10-
EDM (ERROR DETECTION MONITOR)
Error Detection Monitor output is a signal to monitor problems in safe-torque-off circuit or between
SAFETY UNIT and STO1 and STO2 inputs. The following Table 10 shows correspondences between
STO1 and STO2 inputs and Monitor Output states.
STO1 STO2 MONITOR OUT
ON ON OFF
ON OFF OFF
OFF ON OFF
OFF OFF ON
Table 10
8.11-
EDM – CONNECTION EXAMPLE
In Figure 7 is described a connection example that allows to enable Safe Torque Off function by means
of emergency stop button through SAFETY UNIT (Figure 7).
Under normal conditions, pressing emergency stop button, STO1 and STO2 become OFF and EDM
becomes ON (with maximum delay of 10 ms). When emergency stop button is released, if feedback
circuit of SAFETY UNIT is reset and two safety inputs are set ON, EDM becomes OFF. This allows to
restart the machine working.
8.12-
ERROR DETECTION METHOD
Errors between input logic states and monitor output must be detected by means of SAFETY UNIT.
For correct connections, please refer to the SAFETY UNIT manual.
EDM (Error Detection Monitor) is not a safety output. Do not use EDM for any purpose other than
failure monitoring.
8.13-
VERIFICATION TEST
Please verify that SAFE TORQUE OFF function properly works at every first machine start-up and at
every drive replacement.
Before check the correct working of SAFE TORQUE OFF function, please verify that every drive
connections properly operate.
Verification Test needs the following procedures:
1. Switch on the drive power supply.
2. Set ON both STO1 and STO2 inputs.
3. Verify that motor is in CURRENT ON state.
4. Verify corresponding EDM output state.
5. Set OFF both STO1 and STO2 inputs.
6. Verify that motor runs without holding torque and it is in CURRENT OFF state.
7. Verify corresponding EDM output state.
8. Repeat the points from 5 to 7 setting OFF STO1 and STO2 inputs separately.
8.14-
SAFETY CAUTIONS
Please thoroughly observe the following safety cautions to use safe-torque-off function.
Not correct use of safe-torque-off function can result to personal injury or death.
1. Safety system with safe-torque-off function must be designed by person with expertise of related
safety standards and through understanding the descriptions specified in this manual.
2. The security system development that involves the use of STO function must be the result of an
appropriate risk assessment.
3. When safe-torque-off function is active during the motor run, current motor is turned to zero and the
motor continues to run due to inertia. Please design safety system so that no risks occur until the
system stopped.
4. When the motor is used in vertical axes, the motor can rotate due to gravity. Please provide external
device (i.e. brake) to stop the motor within requested range.
5. In case of short circuit or failure of power device transistor, the motor could make an uncontrolled
movement within a range up to 180 degrees in electrical angle (180 degrees in electrical angle=1/50
of a turn) and then remain a stable position. It is necessary to verify that this limited movement does
not correspond to some risky conditions.

R.T.A. s.r.l. – HEAEME06 – 03/22 18/19
Be sure that SAFE TORQUE OFF function properly works at first machine start-up and at every drive
replacement. If input / output signals are not used correctly (for example due to miswiring), the STO function
doesn’t work properly and dangerous situation can occur.
9- UL SPECIFICATIONS AND REQUIREMENTS
When the drives are installed in machines which have to be compliant with UL standards, the following
specifications and requirements must be taken into account.
Electrical ratings
Table 3
Motor Series Hi-Mod Vdc A
(Max) Rpm
Max allowed value
Intermittent Duty
Time %
A4.x.1Hx.y, E4.x.1Hx.y, B4.x.1Hx.y
A5.x.1Hx.y, E5.x.1Hx.y, B5.x.1Hx.y
80
1.5 < 300 72" ON / 168" OFF 30
3.6 300 - 2500 60" ON / 180" OFF 25
A4.x.2Hx.y, E4.x.2Hx.y, B4.x.2Hx.y
A5.x.2Hx.y, E5.x.2Hx.y, B5.x.2Hx.y
2.2 < 300 72" ON / 168" OFF 30
2.8 300 - 2000 60" ON / 180" OFF 25
A4.x.3Hx.y, E4.x.3Hx.y, B4.x.3Hx.y
A5.x.3Hx.y, E5.x.3Hx.y, B5.x.3Hx.y
2.5 < 300 72" ON / 168" OFF 30
4.0 300 - 2000 60" ON / 180" OFF 25
A4.x.2Mx.y, E4.x.2Mx.y, B4.x.2Mx.y
A4.x.3Mx.y, E4.x.3Mx.y, B4.x.3Mx.y
A5.x.2Mx.y, E5.x.2Mx.y, B5.x.2Mx.y
A5.x.3Mx.y, E5.x.3Mx.y, B5.x.3Mx.y
2.4 <300 120" ON / 120" OFF
50
3.6 300 - 1500 96" ON / 144" OFF 40
Duty cycle
The allowed limits of duty cycle, defined in Table 3, meet the following requirements:
•They are in accordance with the tests made by UL during the approval process and therefore they can
be directly used without further investigation.
•Within these limits, the system can run indefinitely without any intervention of the thermal protection in
the full range of allowed operating temperature.
From the technical point of view, if the internal phase current setting is less than the maximum or some kind of
forced cooling is provided, it is possible to use a wider range of duty cycle. In this case it’s important to take in
account the following points:
•There is no more accordance with the tests made by UL during the approval process and therefore
the approval thermal testing have to be done again.
•In this case, the thermal tests must be done on the machine in the specific installation situation and
working conditions.
Enviromental Condition
•"Maximum Operating Ambient Temperature 40°C".
•“Suitable for Industrial Pollution Degree-3 Environment”.
•
Installation instructions
•“Suitable for use on a circuit capable of delivering not more than 1000 Amperes, 80 Vdc +15%
maximum”.
•“When protected by UL-Listed Cartdridge Fuses, Nonrenewable (JDDZ), Class CC, Current Limiting,
Time Delay, rated 150 Vdc / 600 Vac, 8 A, 20 kAdc AIC / 200 kArms AIC”.
•The final end-use connections of these Drives with the “Input Power- Supply”, with “Auxiliary Control
Supply” and with “Auxiliary Signal I/O’s Ports (Encoder & Can Bus)” are provided R/C Connectors
(ECBT2/8), suitable for Factory-Wiring only.

R.T.A. s.r.l. – HEAEME06 – 03/22 19/19
However the Drives shall be provided with the Wiring diagrams (Fig. 4) and the instructions to indicate the
wiring connections for the end-use equipment installation (Fig. 2b e Fig. 3).
•Over-Voltage Control - “D.C. Enclosed Motor Drive” Mod. No. “HI-MOD (A-B-E) Series” the levels of
“Overvoltage Protection” will be secured by a “Power Supply or System” of “Over-Voltage Category-II”
(LOAD LEVEL – Secondary Circuit of a “protected utility Transformer” / “protected Power Supply”)
suitable to control over-voltages at the maximum rated “Impulse withstand Voltage-peak” of 0.8 kV, for
rated “Phase-Ground (rms/dc)” of 85 V, and with a maximum “Short-circuit Current” available of 1 kA.
Grounding Identification - A wire connector intended for connection of a installed equipment grounding
conductor shall be plainly identified, with the symbol (see Fig. 4 for details).
This manual suits for next models
3
Table of contents
Other RTA DC Drive manuals
Popular DC Drive manuals by other brands
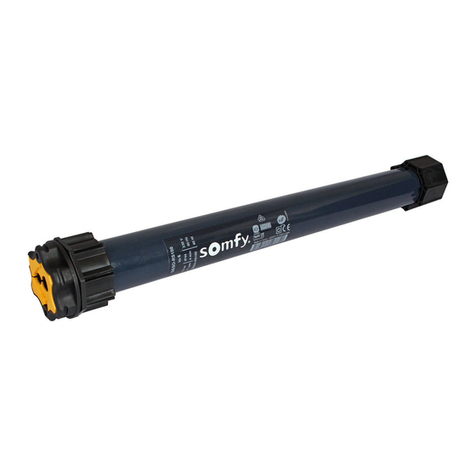
SOMFY
SOMFY S&SO-RS100 io instructions
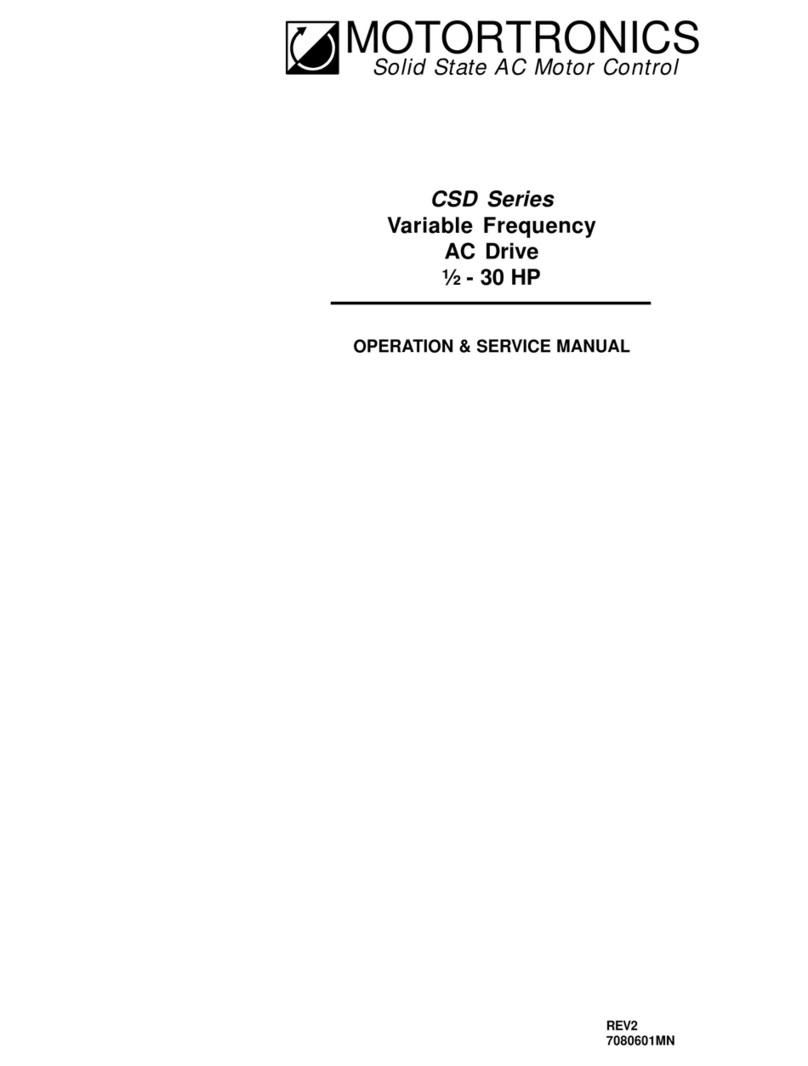
motortronics
motortronics CSD Series Operation & service manual
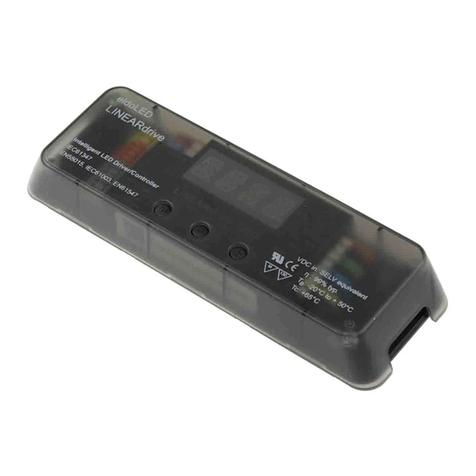
eldoLED
eldoLED LINEARdrive 720D quick start guide

Control Techniques
Control Techniques Midi-Maestro user guide

Siemens
Siemens PXC00-PE96.A installation instructions

Siemens
Siemens SINAMICS PERFECT HARMONY GH180 Reference manual