Sentinel projetor Operating instructions

MAN-027-May 2007
Operating and Maintenance Manual

i
DANGER - IMPORTANT WARNINGS
The system must be operated only by trained and qualified radiographers who have read and understand this
Operating Manual or by trained assistants working under their direct supervision.
WARNING
The use of this radiographic exposure device by unqualified personnel or when safety procedures are not
fully met could result in life-threatening dangers.
Gamma radiography systems emit high levels of highly penetrating radiation during use.
An unshielded radiation source at close range can cause injury, sickness or death to anyone who is exposed to it
even for a short period of time. A radiation source (or an unshielded source assembly) must NOT be touched by the
hands under any circumstances.
Since gamma radiation cannot be detected by the human senses, strict operating and emergency procedures must
be followed. The proper use of calibrated and operable survey meters must be employed to avoid potentially
dangerous levels of radiation exposure.
Proper dosimetry including film badges or thermoluminescent dosimeters, direct reading pocket dosimeters and
audible alarm ratemeters must be worn during all radiographic operations.
During use of this radiography system, never assume the position of the radiation source. Always conduct a
thorough confirmatory survey using a calibrated and operable survey meter to verify the location of the radiation
source. Be reminded that a multitude of overexposure incidents which include injuries are directly attributed to a
failure of the radiographer to perform or supervise an adequate confirmatory survey.
It is imperative that the users of this transport container perform adequate radiation surveys of the transport container
and exposure devices. Surveys must be performed using a calibrated survey instrument before, during and after
source exchanges and before transport to determine if the source assembly is properly shielded within the transport
container. Again, the failure to perform an adequate radiation survey can cause unnecessary exposure to personnel
resulting in a reportable incident.
It is very important and required by national and international regulations to prevent access by unauthorized persons
to radiographic equipment and to the area where radiography is performed.
Take advantage of the three basic radiation protection methods to minimize radiation exposure:
TIME
Spend less time near the radiation source.
DISTANCE
Increase your distance in a direction away from the radiation source.
SHIELDING
When possible, always apply the use of effective shielding between you and the radiation source.
Do not perform any unauthorized modifications to the radiographic exposure device or components of the
radiography system.
It is important that trained and qualified radiographers perform or supervise a daily safety inspection of the
radiography system for obvious defects prior to operation of the system.
Do not use any components that are not approved for use with the radiography system or after-market components
that may compromise the safety features designed into the system.

ii
CONTENTS
_______________________________________________________________________
1 TECHNICAL SPECIFICATIONS 1.1 – 1.7
_______________________________________________________________________
2 OPERATING INSTRUCTIONS 2.1 – 2.11
_______________________________________________________________________
3 DAILY INSPECTION INSTRUCTIONS 3.1 – 3.9
_______________________________________________________________________
4 MAINTENANCE INSTRUCTIONS 4.1 – 4.24
_______________________________________________________________________
5 SAMPLE TRANSPORTATION INSTRUCTIONS 5.1 – 5.11
_______________________________________________________________________
6 DEFINITIONS AND TERMS 6.1 – 6.3
_______________________________________________________________________
7 EMERGENCIES AND PERSONNEL SAFETY 7.1 – 7.2
_______________________________________________________________________
8 INSTRUCTIONS FOR DISPOSAL 8.1
_______________________________________________________________________

iii
880 Delta 150 Ci (5.55 TBq)
Maximum package weight 880 Sigma 130 Ci (4.81 TBq)
Maximum package weight
With jacket 52 lb (24 kg) With jacket 52 lb (24 kg)
Without jacket 46 lb (21 kg) Without jacket 46 lb (21 kg)
880 Elite 50 Ci (1.85 TBq)
Maximum package weight 880 Omega* 15 Ci (0.55 TBq)
Maximum package weight
With jacket 42 lb (19 kg) With jacket 33 lb (15 kg)
Without jacket 33 lb (17 kg) Without jacket 28 lb (13 kg)
*(880 Omega is a Type A transport container)
FRONT VIEW
Outlet Port
Guide Tube Connector
REAR VIEW
Locking Mechanism
Remote Control Connector
7.5 in
191 mm
9 in
229 mm
13.3 in
338 mm

TECHNICAL SPECIFICATIONS
1.1
Exposure Device Description
The Model 880Delta, Model 880 Sigma, Model 880 Elite and Model 880 Omega are physically small,
lightweight, portable industrial radiographic exposure devices. The ‘S’ tube design exposure device
consists of a cast depleted Uranium (DU) shield contained and secured within a 300 series stainless steel
tube with stainless steel discs welded at each end to form a cylinder shaped housing. Both discs are
recessed into the stainless steel tube to provide protection for the locking mechanism at the rear side and
the outlet port at the front side.
The welded tubular hosing is oriented horizontally to provide easy access to the locking mechanism and
source assembly connector and to provide easy access to the outlet port for connection of the projection
sheaths. The internal void space of the welded housing is filled with polyurethane foam to prevent the
ingress of water or foreign material but is open to atmospheric pressure. The stainless steel housing
containing the DU shield, locking mechanism, outlet port, protective covers and required labels comprise
the radioactive material transport package.
A plastic jacket surrounds the welded housing and serves as a protective barrier for the labels and
provides the means for carrying and placement during use as a radiographic exposure device. The
Model 880 Delta is identified by a yellow colored jacket. The Model 880 Sigma is identified by a black
colored jacket. The Model 880 Elite is identified by a blue colored jacket and the Model 880 Omega is
identified by a safety orange colored jacket. The plastic jacket incorporates a carrying handle and a base
that is used during radiographic operations but is not required for transportation purposes. The plastic
jacket may be removed for certain applications such as when the exposure device is securely mounted to
a pipe-crawler locomotive or a pipe-liner sled.
The Model 880 Delta, Sigma, Elite and Omega exposure devices are designed, tested, and manufactured
to meet the requirements of ANSI N432-1980, ISO 3999-1:2000(E), IAEA TS-R-1 (1996 Revised),
USNRC 10CFR34, 10CFR71 and 49CFR173 requirements. Additionally, these exposure devices are
designed, manufactured and serviced under an ISO 9001 QA Program and a USNRC 10CFR71, Subpart
H QA Program. The QA program also includes the reporting requirements of USNRC 10CFR21 for
suppliers of source and byproduct materials.
Titanium ‘S’ TubeSource Assembl
y
Plun
g
er Lock
Locking Mechanism
Remote
Control
Connector
Welded Shield Container
Protective
Plastic Jacket with
Carrying Handle
De
p
leted Uranium Shield
Outlet Port
Guide Tube
Connector

TECHNICAL SPECIFICATIONS
1.2
Applications
The Model 880 devices are used for industrial applications of gamma radiography, mainly with Iridium-
192, to inspect materials and structures in the density range of approximately 2.71 g/cm3through 8.53
g/cm3. The Model 880 devices also accommodate low energy isotopes to permit radiography of materials
and structures of thin sections of steel and low-density alloys. The Model 880 exposure devices are also
designed for use with low activity sources with high photon energies that are used for mass absorption
(gamma scanning) studies of high-density materials up to 18.7 g/cm3.
Standard Source Assembly
Metallic Iridium-192 discs and pellets are doubly encapsulated in welded stainless steel or titanium
capsules. The sealed sources are designed and tested to achieve an ISO/ANSI minimum classification of
97C63515 and to comply with the IAEA and USDOT requirements for ‘Special Form’ radioactive material.
The ISO/ANSI classification 97C63515 stated in this manual refers to the complete source capsule which
is attached to the source assembly. This classification also applies to the Se-75, Co-60 and Cs-137
versions of the source assemblies. The Yb-169 sealed sources are designed and tested to achieve an
ISO/ANSI minimum classification of 97C63535 and to comply with the IAEA and USDOT requirements for
‘Special Form’ radioactive material.
The sealed source is swaged to one end of a source holder consisting of a short flexible steel cable which
has a female half of a connector at the other end, used for coupling to a control cable connector. The
female connector also incorporates a stainless steel stop-ball swaged onto it (older versions of this
source wire had the stop-ball as a separate component from the female connector). The purpose of the
stop-ball is to provide mechanical positioning of the source assembly within the exposure device’s
shielding and to provide a means of securing the source assembly in the exposure device’s locking
mechanism.
Model 880 Delta authorized contents
Isotope Assembly
Model Number Gamma
Energy Range Half Life Approximate
Steel Working
Thickness
Device/Source
Maximum
Capacity
Ytterbium-169 91810 8-308 keV 32 days 2-20 mm 20 Ci 0.74 TBq
Selenium-75 A424-25W 66-401 keV 120 days 3-29 mm 150 Ci 5.55 TBq
Iridium-192 A424-9 206-612 keV 74 days 12-63 mm 150 Ci 5.55 TBq
Cobalt-60 A424-19 1.17-1.33 MeV 5.27 years 50-150 mm 65 mCi 2.40 GBq
Cesium-137 A424-30 663 keV 30 years 12-63 mm 380 mCi 14.0 GBq
Model 880 Sigma authorized contents
Isotope Assembly
Model Number Gamma
Energy Range Half Life Approximate
Steel Working
Thickness
Device/Source
Maximum
Capacity
Ytterbium-169 91810 8-308 keV 32 days 2-20 mm 20 Ci 0.74 TBq
Selenium-75 A424-25W 66-401 keV 120 days 3-29 mm 150 Ci 5.55 TBq
Iridium-192 A424-9 206-612 keV 74 days 12-63 mm 130 Ci 4.81 TBq
Cobalt-60 A424-19 1.17-1.33 MeV 5.27 years 50-150 mm 25 mCi 925 MBq
Cesium-137 A424-30 663 keV 30 years 12-63 mm 380 mCi 14.0 GBq

TECHNICAL SPECIFICATIONS
1.3
Model 880 Elite authorized contents
Isotope Assembly
Model Number Gamma
Energy Range Half Life Approximate
Steel Working
Thickness
Device/Source
Maximum
Capacity
Ytterbium-169 91810 8-308 keV 32 days 2-20 mm 20 Ci 0.74 TBq
Selenium-75 A424-25W 66-401 keV 120 days 3-29 mm 150 Ci 5.55 TBq
Iridium-192 A424-9 206-612 keV 74 days 12-63 mm 50 Ci 4.81 TBq
Cobalt-60 A424-19 1.17-1.33 MeV 5.27 years 50-150 mm 25 mCi 925 MBq
Cesium-137 A424-30 663 keV 30 years 12-63 mm 380 mCi 14.0 GBq
Model 880 Omega authorized contents
Isotope Assembly
Model Number Gamma
Energy Range Half Life Approximate
Steel Working
Thickness
Device/Source
Maximum
Capacity
Ytterbium-169 91810 8-308 keV 32 days 2-20 mm 30 Ci 1.11 TBq
Selenium-75 A424-25W 66-401 keV 120 days 3-29 mm 80 Ci 2.96 TBq
Iridium-192 A424-9 206-612 keV 74 days 12-63 mm 15 Ci 0.55 TBq
Source output
Isotope At 1 m per Ci (37 GBq) At 1 ft per Ci (37 GBq)
Ytterbium-169 0.125 R/hr 1.25 mSv/hr 1.3 R/hr 13.0 mSv/hr
Selenium-75 0.203 R/hr 2.03 mSv/hr 2.2 R/hr 22.0 mSv/hr
Iridium-192 0.48 R/hr 4.80 mSv/hr 5.2 R/hr 52.0 mSv/hr
Cobalt-60 1.30 R/hr 13.0 mSv/hr 14.0 R/hr 140 mSv/hr
Cesium-137 0.32 R/hr 3.20 mSv/hr 3.4 R/hr 34.0 mSv/hr
Selected attenuation data Approximate Half Value Thickness
Inches (mm)
Material Approximate
Material
Density
(g/cm3) Ytterbium-169 Selenium-75 Iridium-192 Cobalt-60 Cesium-137
Concrete 2.35 1.140 (29.0) 1.180 (30.0) 1.700 (43.2) 2.400 (61.0) 3.00 (76.2)
Aluminum 2.65 - 1.100 (27.0) - - -
Steel 7.80 0.170 (4.3) 0.315 (8.0) 0.512 (13.0) 0.827 (21.0) 0.900 (22.9)
Lead 11.34 0.032 (0.8) 0.039 (1.0) 0.200 (5.1) 0.500 (12.7) 0.250 (6.4)
Tungsten 17.80 - 0.032 (0.8) 0.130 (3.3) 0.310 (7.9) 0.225 (5.7)
DU 18.70 - - 0.050 (1.3) 0.270 (6.8) 0.125 (3.2)
Operating Distance
The distance between the remote control and the exposure head is determined by summing the length of
the remote control conduits plus the total length of source guide tubes used, and normally should not
exceed 47 ft (14.2 m) with standard 25 ft. controls.
Standard remote controls:
25 ft (7.6 m), 35 ft (10.7 m), 50 ft (15 m)
Standard source guide tubes (projection sheaths):
7 ft (2.1 m) set of three source guide tubes: 21 ft total (6.3 m)

TECHNICAL SPECIFICATIONS
1.4
Note:
The total length of source guide tubes utilized must be shorter in length than the remote controls to
ensure the source assembly will project into the working position.
e.g. When using 25 ft (7.6 m) remote controls, a maximum of three 7 ft (2.1 m) source guide tubes can be
used with a combined length of 21 ft (6.4 m).
Conversely, when using 35 ft (10.7 m) remote controls, a maximum of four 7 ft (2.1 m) source guide tubes
can be utilized.
When using 50 ft (15 m) remote controls, a maximum of six 7 ft (2.1 m) source guide tubes can be
utilized. This limitation is due to the weight and friction of remote control cable length.
Control Specifications
Complete Remote Control Assemblies
Product code Model number Control cable length Unit weight
TAN66425 664/25 25 ft (7.6 m) 21 lb (10 kg)
TAN66435 664/35 35 ft (10.7 m) 24 lb (11 kg)
TAN66450 664/50 50 ft (15.2 m) 27 lb (12 kg)
TAN69325 693/25 25 ft (7.6 m) 21 lb (10 kg)
TAN69335 693/35 35 ft (10.7 m) 24 lb (11 kg)
TAN69350 693/50 50 ft (15.2 m) 27 lb (27 kg)
TAN69225 692/25 25 ft (7.6 m) 21 lb (10 kg)
TAN69235 692/35 35 ft (10.7 m) 24 lb (11 kg)
TAN69250 692/50 50 ft (15.2 m) 27 lb (12 kg)
88325 883/25 25 ft (7.6 m)
88335 883/35 35 ft (10.7 m)
88350 883/50 50 ft (15.2 m)
Model 664 Control Storage Reel Unit Size _____
Length Width Height
21 in (533 mm) 12 in (305 mm) 6.6 in (168 mm)
The Model 664 reel and 693 pistol grip controls are equipped with odometers. The Model 692 pistol-grip
controls are not equipped with an odometer.
Source Guide Tube (with source stop)
Product Code Model Number Length
TAN48906 48906 7 ft (2.1 m) male 1-18 threaded fitting
48906-X 48906-X Customer specified length
48931-7 48931-7 7 ft (2.1 m) with bayonet fitting
48931-X 48931-X Customer specified length with bayonet fitting
95020 95020 7 ft (2.1m) male 1-18 threaded fitting
95020-X 95020-X Customer specified length
Source Guide Tube Extension
Product Code Model Number Length
TAN48907 48907 7 ft (2.1 m) male/female 1-18 threaded fittings
48930-7 48930-7 7 ft (2.1 m) bayonet fitting/female 1-18
48930-X 48930-X Customer specified length bayonet fitting/female 1-18
95021 95020 7 ft (2.1 m) male/female 1-18 threaded fittings
95021-X 95021-X Customer specified length
NOTE: Xindicates customer can order lengths other than the standard length.

TECHNICAL SPECIFICATIONS
1.5
Exposure Device Specifications
Manufacturer Length
Sentinel - QSA Global, Inc. 13.33 in (33.8 cm) all models
40 North Avenue, Burlington, Massachusetts, USA 01803
Primary Application Width
Industrial gamma radiography 7.5 in (19.1 cm) all models
Model Numbers Height
Model 880 Delta, Model 880 Sigma, Model 880 Elite 9 in (22.9 cm) all models
and Model 880 Omega
Weight of Exposure Device Type B(U) Certification
Delta: 52 lb (24 kg), Sigma: 52 lb (24 kg) The Models 880 Delta, 880 Sigma and
Elite: 42 lb (19 kg), Omega: 33 lb (15 kg) 880 Elite are certified by the following:
Weight of Depleted Uranium Shield USA/9296/B(U)-96
Delta: 34 lb (15.4 kg), Sigma: 34 lb (15.4 kg) CDN/E199/-96
Elite: 25 lb (11.4 kg), Omega: 17 lb (7.7 kg)
Activity of Depleted Uranium Shield Type A Approval
Delta: 5.4 mCi (200 MBq), Sigma: 5.4 mCi (200 MBq) All Models meet the Type A package
Elite: 3.8 mCi (141 MBq), Omega: 2.7 mCi (101 MBq) requirements of 49 CFR 173.415 and
IAEA TS-R-1 (1996 revised)
Special Form Certifications
Iridium-192, Cobalt-60 & Cesium-137: USA/0335/S-96
Selenium-75: USA/0502/S-96
Ytterbium-169: USA/0597/S-96

TECHNICAL SPECIFICATIONS
1.6
Construction
A depleted Uranium (DU) shield is encased within a welded tubular stainless steel shell with stainless
steel end plates. The interior void space is filled with rigid polyurethane foam. The exposure device body
is encased in an engineered plastic jacket also consisting of the handle and a base.
Materials
Titanium ‘S’ tube, DU shield, 300 series stainless steel tubular shell and plate, aluminum, brass, tungsten
and polyurethane.
Maximum Capacities
See previous table listings in this section.
Inspection Requirements
Daily pre-operational inspection for obvious damage to the system.
Maintenance Requirements
Most national regulations require inspection and maintenance of the system at quarterly intervals. The
complete annual servicing ensures the integrity of the system. Shorter frequencies of inspection and
maintenance are required when the system is operated under severe operating environments. In some
cases, the system should be serviced immediately after certain jobs in severe environmental working
conditions.
Device Operating Temperature Range
-40°F to 300°F (-40°C to 149°C)
Source Assembly
See previous table listings in this section.
NOTICE
These industrial radiography systems are used as an exposure device, a Type A shipping container and
for the Models 880 Delta, 880 Sigma and 880 Elite as Type B(U)-96 shipping containers for QSA Global,
Inc. source assemblies. The purpose of this manual is to provide information that will assist qualified
radiographers in using the Model 880 Delta, 880 Sigma, 880 Elite and 880 Omega gamma radiography
systems. The user must be thoroughly familiar with this instruction manual before attempting operation
and use of this equipment.
In order to use this equipment or perform source changes, users within the USA must be specifically
licensed to do so. Applications for a license should be filed with the Materials Licensing Section of the
appropriate U.S. Nuclear Regulatory Commission regional office or with the appropriate Agreement State
office. All users within Canada must have a Canadian Nuclear Safety Commission license.
Prior to the initial use of the exposure device as a shipping container, the user must register with the
Office of Nuclear Material Safety and Security, U.S. Nuclear Regulatory Commission. The user should
have in his possession a copy of the Certificate of Compliance issued for the exposure device, which may
be obtained from Sentinel, QSA Global, Inc. customer service centers upon request. This also applies to
users from Agreement States and other regulatory jurisdictions.
It is the responsibility of users of this equipment outside of the United States to comply with all local,
national and international regulatory, licensing and transportation rules and regulations as they apply in
their respective countries.

TECHNICAL SPECIFICATIONS
1.7
Warranty and Limitation of Liability
QSA Global, Inc. (herein referred to as the manufacturer) warrants its product which it manufactures and
sells to be free from defects in material and workmanship for a period of one year from the date of
shipment. This warranty shall not apply to any product or parts which have been subjected to misuse,
improper installation, repair, alteration, neglect, accident, abnormal conditions of operation, or use in any
manner contrary to instructions.
The manufacturer's liability under such warranty shall be limited to replacing or repairing, at its option, any
parts found to be defective in such respects, which are returned to the manufacturer, transportation
prepaid; or at its option, to returning the purchase price thereof.
The warranty on other manufacturer's components shall be that of the original manufacturer whose
warranty shall be binding.
In no event shall the manufacturer be liable for any incidental or consequential damages, whether or not
such damages are alleged to have resulted from the use of such product in accordance with instructions
given by or referred to by the manufacturer.
QSA Global, Inc. assumes no liability or responsibility for the usage of any radioactive material or device
generating penetrating radiation used in connection with this product. The use of such material or
generators in any manner other than prescribed in the U.S. Nuclear Regulatory Commission or equivalent
Agreement State or permitted by any regulation of the U.S. Nuclear Regulatory Commission or State
Regulation may constitute a violation of such license terms.
All other warranties, except those warranties expressly stated herein, including without limitation
warranties of, merchantability and implied warranties of fitness, are expressly excluded.
The warranty on this device is specifically limited to its use only with sealed sources and connectors,
parts, and accessories manufactured by QSA Global, Inc.
QSA Global, Inc. has received equipment approvals for the Model 880 Delta, Model 880 Sigma and
Model 880 Elite systems from the Commonwealth of Massachusetts, the USNRC Transportation Branch,
the U.S. Department of Transportation, and the Canadian Nuclear Safety Commission. (The Model 880
Omega is not currently authorized for use in the USA or Canada). This requires use of Agreement State
or USNRC registered and approved remote controls, control cables, projection sheaths, sealed source
assemblies, remote control cranks used in conjunction with the Model 880 Delta, Model 880 Sigma and
Model 880 Elite. For additional information on compliance with Type B(U)-96 certifications, USNRC
10CFR34, ANSI N432-1980 or ISO 3999-1:2000(E) please contact QSA Global, Inc.
SentinelTM, QSA Global, Inc. shall not be liable for any errors or omissions contained herein and the
provision by SentinelTM, QSA Global, Inc. of the information set out in this manual does not in itself
constitute acceptance of any liability on the part of SentinelTM, QSA Global, Inc.

OPERATING INSTRUCTIONS
2.1
Job site safety precautions
Instruments
The radiographer and radiography assistants must at all times wear a film badge or TLD and pocket
dosimeter with a range of 0-2 mSv (0-200 mRem). Regulatory requirements in the USA also require that
an audible alarm ratemeter be worn at temporary jobsites. Specifically, those locations that are not
permanent radiographic installations equipped with functional door interlocks and audible/visual alarms.
Radiographers in the USA must also have a survey meter capable of measuring in the range
20 µSv/hr (2 mR/hr) up to 10 mSv/hr (1,000 mR/hr). Canadian regulations require that survey meters
used for industrial radiography be capable of measuring from 2 µSv/hr (0.2 mR/hr) and up to 100 mSv/hr
(10 R/hr). In any regulatory jurisdiction, always verify survey meter requirements affecting the range and
calibration requirements prior to engaging in industrial radiography operations.
An audible ‘chirper’ pocket alarm may be required in some countries.
Restricted Area
Radiography must be performed only in a restricted area that is marked with the appropriate radiation
warning signs and secured against unauthorized entrance.
Distance
Since the source emits high levels of radiation it is good practice to operate the system from as great a
distance as possible.
Shielding
Whenever possible, situate the radiographic exposure area in a room with suitably thick walls, floor,
ceiling and doors. Whenever possible, the use of a collimator (beam limiter) provides effective shielding to
reduce radiation levels outside of the central beam. It is recommended that collimators be used at
temporary job sites to minimize occupational exposure to radiation.
Surveillance
Only trained and qualified radiographers or assistants working under their direct supervision may operate
radiography systems. The radiographer must be physically present at the site and able to control and limit
access to the restricted area.
Locking
Keep the exposure device locked while assembling the system and when not being used to perform
radiography. Locked is defined as the exposure device's lock is fully engaged with the key removed.
Store the key in a secured location.

OPERATING INSTRUCTIONS
2.2
It is essential that the 5 STEPS set out below are followed in the
correct order to ensure safe operation and compliance with
regulations.
STEP 1 Exposure Device Survey
STEP 2 Connecting the Source Guide Tube(s)
STEP 3 Connecting the Remote Control Cable
STEP 4 Projecting and Retracting the Source Assembly
STEP 5 Dismantling Equipment
STEP 1
Exposure Device Survey
Check the operation of the survey meter by measuring the radiation level at the surface of the
exposure device. The radiation level measurement should not exceed 2 mSv/hr (200 mR/hr) on any
surface of the exposure device. Use this measurement for verification surveys of the source
assembly’s return to the fully shielded/secured position within the exposure device after each
radiographic exposure.
STEP 2
Source Guide Tube (projection sheath) Layout
Ensure all source guide tubes that will be utilized have received a daily inspection according to the
daily inspection section of this manual. Position and secure the source stop (exposure head) of the
terminating source guide tube at the radiographic focal position using the tripod stand and swivel
clamps or some other secure and suitable means.
Ensure that a source stop (end stop) is in place on the terminating source guide tube.
Use a collimator (beam limiter) to limit the primary beam in unwanted directions.
Determine where the exposure device will be positioned and lay out the source guide tubes as
straight as possible, with no bend radius less than 20 in (0.5 m) to avoid restricting the movement of
the source assembly.
Make sure that the source guide tubes do not contact any heated surface greater than 140°F (60°C).
Avoid any risk of crushing the source guide tube(s) by falling objects, vehicles or doorways during
set-up and during radiographic exposure.
Connecting the Source Guide Tube(s)
The source guide tubes must always be attached to the outlet port of the device before connecting
the remote controls in the set-up for a radiographic exposure.
Connect the source guide tube(s) to the exposure device outlet port as shown.

OPERATING INSTRUCTIONS
2.3
STEP 2
Connecting the Source Guide Tube(s)
Simultaneously pull and rotate the
spring-loaded outlet port cover a quarter of
a turn in a clockwise direction.
Insert the bayonet fitting of the source guide tube
Into the exposed outlet port.
Align the GREEN MARKINGS on the bayonet
fitting and outlet port.
Rotate a quarter of a turn counter-clockwise.
Rotate the spring-loaded outlet port cover
an additional 60 degrees in a clockwise direction
until it stops.
1
2
3
4

OPERATING INSTRUCTIONS
2.4
STEP 2
WARNING
Ensure that the available length of the control cable is greater than the total length of the
source guide tubes. See the technical specifications section for details.
If the remote control conduits are shorter than the total length of the source guide tubes:
1 The source assembly cannot be projected all the way to the source stop of the terminating
source guide tube and be correctly positioned for the exposure.
2 The source assembly may not reach a collimator; therefore, restricted area dose rates may be
higher than expected.
3 The control cable end may be cranked beyond the drive wheel of the remote controls if the drive
cable is not be fitted with a safety retaining spring. This scenario must be treated as an
EMERGENCY.
STEP 3
Remote Control Conduit Layout
Lay out the remote control conduits as straight as possible, with no bend radii less than about 36 in
(approximately 1 m).
Avoid any risk of crushing the remote control conduits by falling objects, moving vehicles or closing
doors, etc.
The remote control crank mechanism (operator's hand-crank) should be placed as far away from the
source focal position as possible (preferably behind shielding).
Connecting the Remote Control Cable
Connect the control cable to the source projector as shown.

OPERATING INSTRUCTIONS
2.5
STEP 3
Connecting the Remote Control Cable
Unlock the plunger lock with the key.
Turn the selector ring from LOCK to CONNECT
The protective cover will disengage from the projector.
1
2
3

OPERATING INSTRUCTIONS
2.6
STEP 3
Connecting the Remote Control Cable
Insert the protective cover into the lock housing during use of
the device.
Check the control cable and source assembly connectors
using the NO GO gauge according to the daily inspection
section.
Remove the protective rubber cap from the remote control
connector.
IMPORTANT WARNING
The control cable connector is a made from hardened
steel and should never be left unprotected or forced into
connection with the source assembly as this could
damage the connector overtime leading to possible
breakage during use.
ALWAYS use the protective end-cover when remote
controls are not connected to the exposure device and
ALWAYS manually move the sleeve of the female
connector of the source assembly to the OPEN position
when connecting and disconnecting the control cable
from the source assembly.
Slide the remote control connector assembly’s collar back
and open the jaws to expose the male portion of the control
cable connector (i.e. the ball-end on the control cable
connector).
Press back the spring-loaded locking pin of the source
assembly connector with a thumb-nail and engage the
male and female portions of the connectors.
Release the locking pin of the source assembly connector
and check that the connection is secure.
Use the NO GO gauge to check the gap between the
joined connectors during the daily inspection.
4
5
6
7

OPERATING INSTRUCTIONS
2.7
STEP 3
Connecting the Remote Control Cable
Close the jaws of the control cable connector over the joined
connectors.
Slide the remote control connector assembly collar over the
connector jaws.
NOTE: The control cable connector, when properly installed
with the selector ring in the CONNECT position, displaces anti-
rotation lugs which allows the selector ring to be rotated to the
LOCK position and when required, through to the OPERATE
position.
Push and hold the remote control connector assembly collar
flush against the exposure device’s locking mechanism and
rotate the selector ring from CONNECT to LOCK. The
selector ring can be secured in this position by engaging the
plunger lock.
Do Not Rotate past LOCK.
The remote control cable connector is now secured into the
exposure device’s locking mechanism.
Keep the exposure device in the lock position until ready to
start the exposure.
Checks Before Exposure of the Source
Verify that the source guide tubes are attached to the outlet port.
Verify that the remote control connector assembly is correctly connected to the exposure device’s
locking mechanism.
Ensure that no personnel are inside the Restricted Area or exposure room.
Ensure that the proper signs are posted and required warnings are in operation.
NOTE
If the remote control is fitted with an additional lock, release this lock and apply a forward motion to
control crank handle, as if exposing the source, until a resistance is felt. Release the control crank
handle and proceed with the next step.
CAUTION
Do not apply excessive force to the control crank handle in the expose direction as this could
cause the source assembly to move forward out of the stored position when the lock slide is
released. Do not retract the control cable and apply the control crank brake. Leave the control
crank and the control cable in a neutral tension position.
8
9

OPERATING INSTRUCTIONS
2.8
STEP 4
Projecting and Retracting the Source Assembly
Unlocking
If engaged, unlock the exposure device’s plunger lock with
the key.
Rotate the selector ring to the OPERATE position.
Ensure there is no tension/force in either direction on the
control cable.
Push the lock slide GREEN MARKING laterally from left to
right (as seen behind the projector) until the lock slide
RED MARKING fully appears on the right side of the
selector ring and you feel or hear the sleeve snap into the
slide.
When the GREEN MARKING is visible, the source
assembly is locked into the secured position within the
exposure device.
When the RED MARKING is visible, the source assembly
is free to be projected from, and retracted to, the projector.
Ensure all personnel leave the immediate area.
Got to the remote control crank.
If an odometer is fitted, adjust the reset knob to read zero.
The source assembly can now be projected.
1
2
3
4

OPERATING INSTRUCTIONS
2.9
STEP 4
Projecting
Rapidly rotate the control crank handle in the EXPOSE direction (counter-clockwise) to move the
source assembly out of the exposure device to the radiographic focal position.
The control crank handle will stop turning when the source reaches the source stop. Do not use
excessive force.
The odometer (if fitted) will indicate the approximate total distance traveled, 7 ft (2.1 m) for each guide
tube section.
Set the brake to ON to prevent movement of the source assembly during the radiographic exposure.
Start timing the radiographic exposure from the moment the source assembly reaches the exposure
head.
Survey meter readings observed during the projection operation should increase rapidly from
background to a high level as the source emerges from the projector. Then readings should fall as
the source moves out towards the focal point, fall sharply as the source enters a collimator (if used)
and remain steady throughout the exposure.
Actual survey meter readings will depend on the source activity, distance, collimators and shielding.
The sequence of changes should be observed and the readings noted.
During retraction of the source assembly from the exposure head to the exposure device, the
sequence will reverse. The survey meter should indicate a continually increasing radiation level as
the source assembly is retracted, then drop to background when the source assembly is stored in the
exposure device.
During the radiographic exposure, use the survey meter to check the boundary dose rate, but spend
as little time as possible in and near the restricted area to minimize personal exposure.
This manual suits for next models
4
Table of contents
Other Sentinel Projector manuals
Popular Projector manuals by other brands
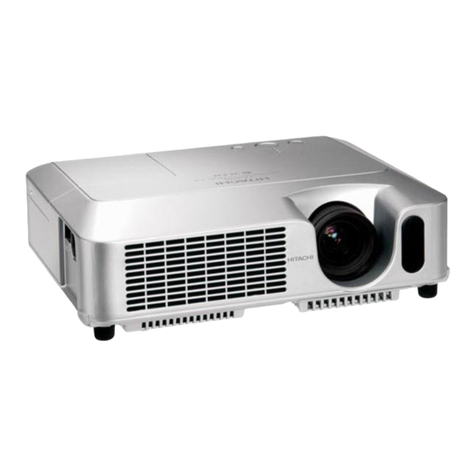
Hitachi
Hitachi X260 - CP XGA LCD Projector User's manual and operating guide
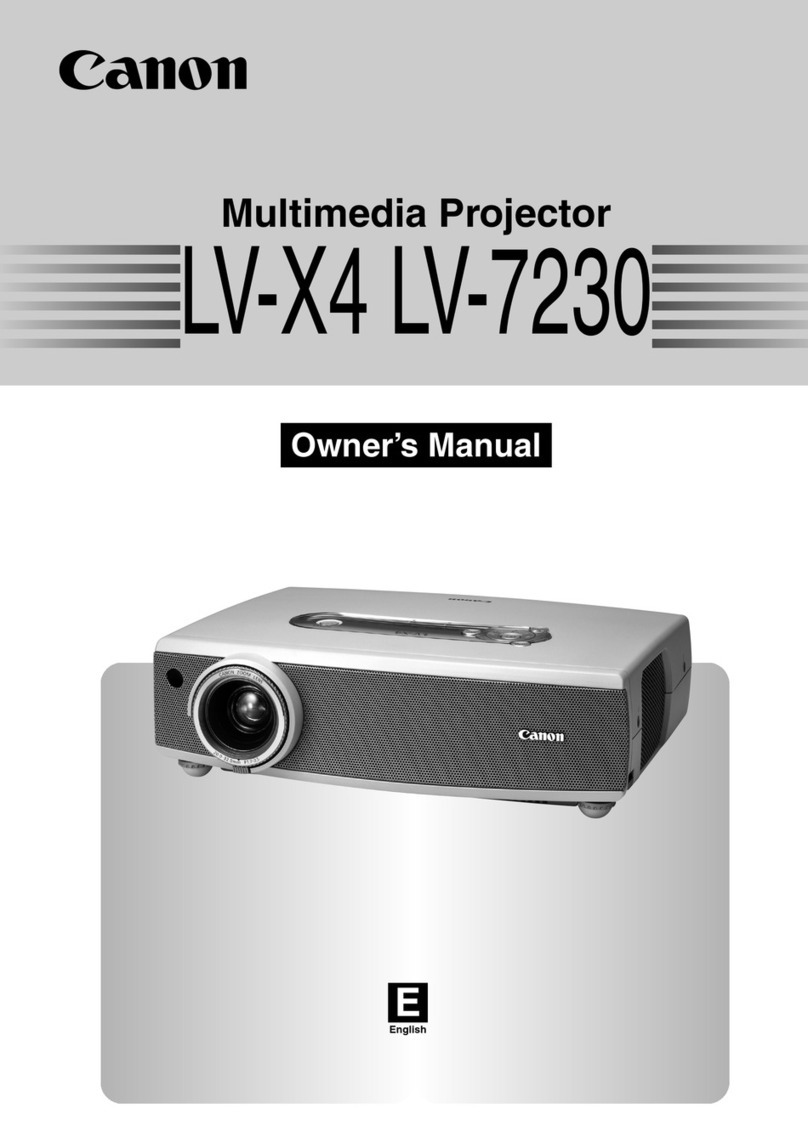
Canon
Canon LV-X4 LV-7230 owner's manual
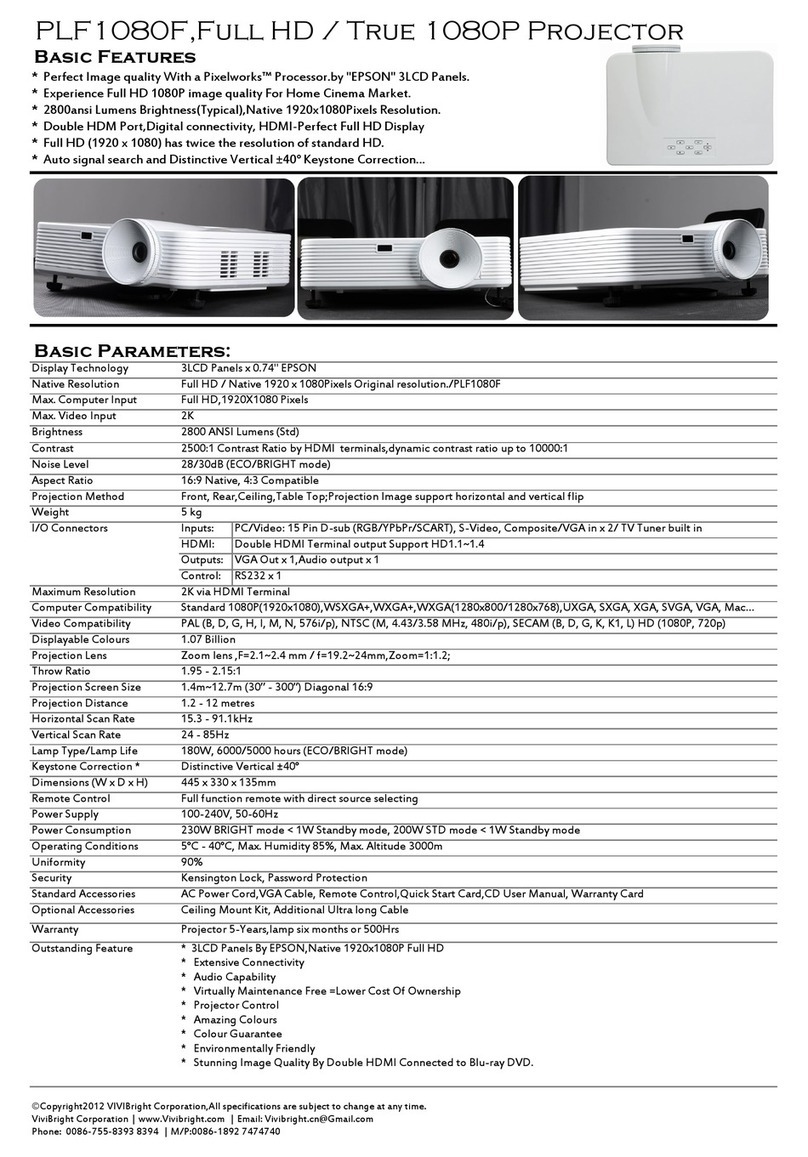
VIVIBright
VIVIBright PLF1080F Specifications
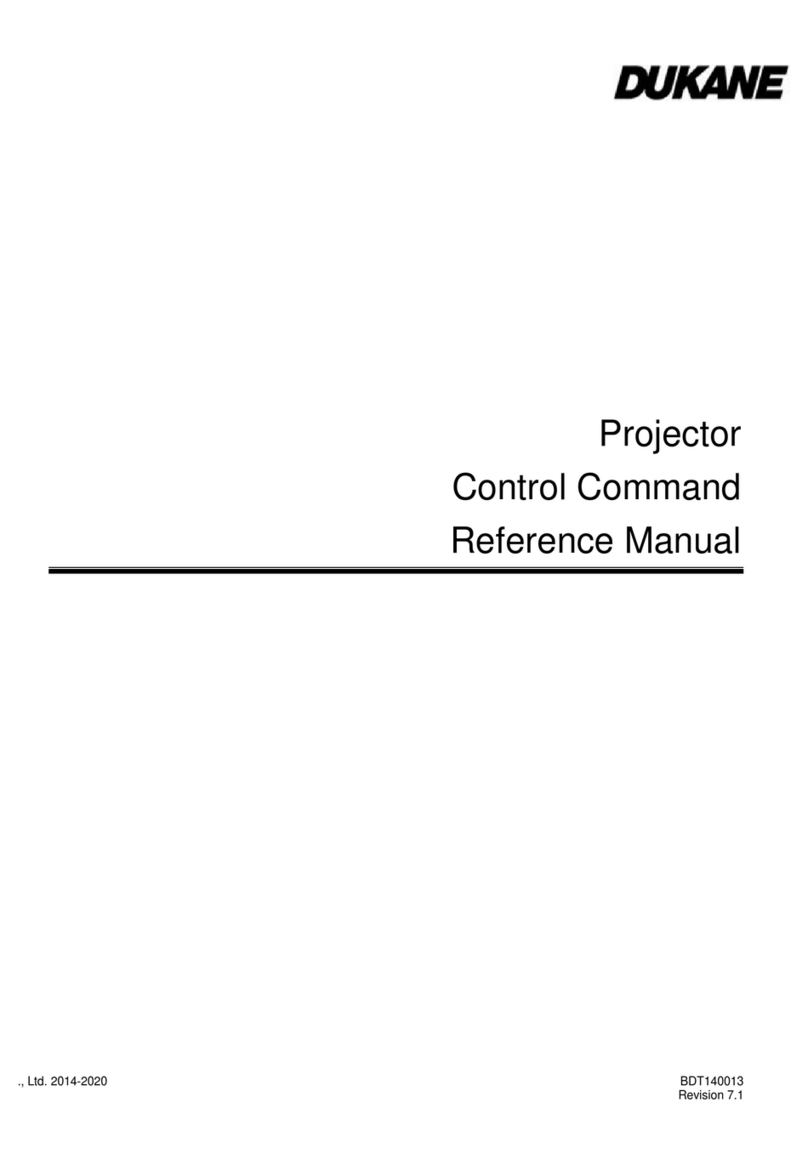
Dukane
Dukane ImagePro 6662UL Reference manual
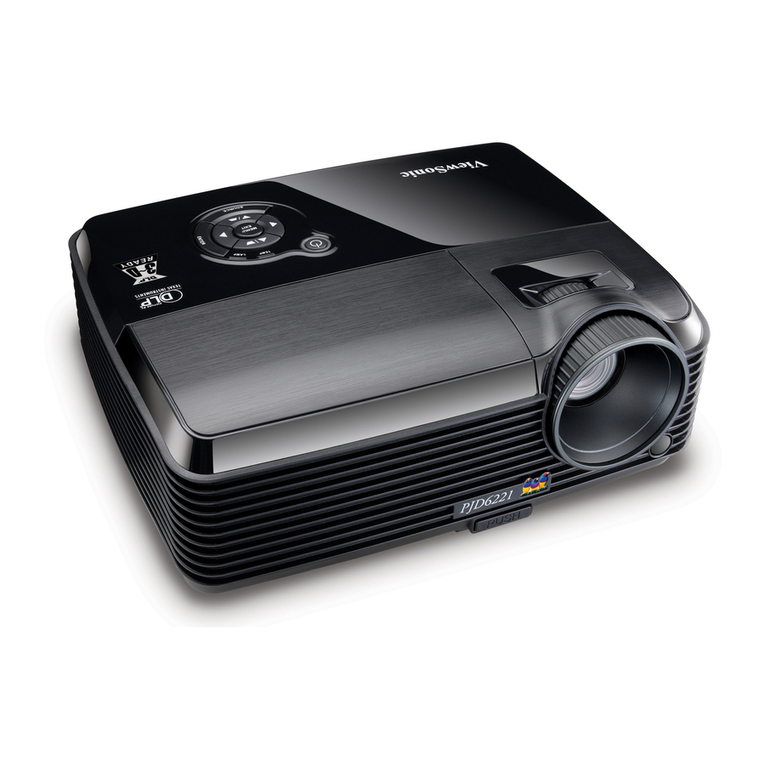
ViewSonic
ViewSonic PJD6221 - 2700 Lumens XGA DLP Projector user guide
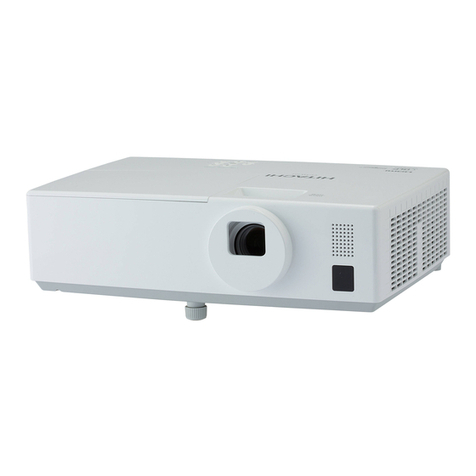
Hitachi
Hitachi CP-DX351 user manual