Sharp Carousel R-995J User manual

R-995J
TABLE OF CONTENTS
Page
CAUTION, MICROWAVE RADIATION .............................................................................................................. 1
WARNING ........................................................................................................................................................... 1
PRODUCT SPECIFICATIONS .......................................................................................................................... 2
GENERAL INFORMATION ................................................................................................................................. 2
APPEARANCE VIEW ........................................................................................................................................ 3
OPERATION SEQUENCE ................................................................................................................................. 4
FUNCTION OF IMPORTANT COMPONENTS ................................................................................................. 8
SERVICING ..................................................................................................................................................... 11
TEST PROCEDURE ......................................................................................................................................... 14
TOUCH CONTROL PANEL .............................................................................................................................. 22
COMPONENT REPLACEMENT AND ADJUSTMENT PROCEDURE ............................................................ 28
MICROWAVE MEASUREMENT ..................................................................................................................... 34
WIRING DIAGRAM .......................................................................................................................................... 35
PICTORIAL DIAGRAM .................................................................................................................................... 37
CONTROL PANEL CIRCUIT ............................................................................................................................ 38
PRINTED WIRING BOARD .............................................................................................................................. 39
PARTS LIST .................................................................................................................................................... 40
S9409R995JPJ/
CONVECTION
MICROWAVE OVEN
MODEL R-995J
In interests of user-safety the oven should be restored to its original
condition and only parts identical to those specified should be
used.
SERVICE MANUAL
SHARP CORPORATION

R-995J

R-995J
1
SERVICE MANUAL
CONVECTION
MICROWAVE OVEN
R-995J
GENERAL IMPORTANT INFORMATION
This Manual has been prepared to provide Sharp Corp. Service
engineers with Operation and Service Information.
It is recommended that service engineers carefully study the
entire text of this manual, so they will be qualified to render
satisfactory customer service.
CAUTION
MICROWAVE RADIATION
DO NOT BECOME EXPOSED TO RADIATION FROM THE
MICROWAVE GENERATOR OR OTHER PARTS
CONDUCTING MICROWAVE ENERGY.
Service engineers should not be exposed to the microwave
energy which may radiate from the magnetron or other
microwave generating devices if it is improperly used or
connected. All input and output microwave connections,
waveguides, flanges and gaskets must be secured. Never
operate the device without a microwave energy absorbing
load attached. Never look into an open waveguide or an-
tenna while the device is energized.
WARNING
Never operate the oven until the following points are ensured.
(A) The door is tightly closed.
(B) The door brackets and hinges are not defective.
(C) The door packing is not damaged.
(D) The door is not deformed or warped.
(E) There is not any other visible damage with the oven.
Servicing and repair work must be carried out only by trained
service engineers.
All the parts marked "*" on parts list are used at voltages more
than 250V.
Removal of the outer wrap gives access to potentials above
250V.
All the parts marked "∆" on parts list may cause undue micro-
wave exposure, by themselves, or when they are damaged,
loosened or removed.
SHARP CORPORATION
OSAKA, JAPAN
PRODUCT SPECIFICATIONS
APPEARANCE VIEW
OPERATING SEQUENCE
FUNCTION OF IMPORTANT
COMPONENTS
SERVICING AND
TROUBLESHOOTING CHART
TEST PROCEDURE
TOUCH CONTROL PANEL
ASSEMBLY
COMPONENT REPLACEMENT
AND ADJUSTMENT PROCEDURE
MICROWAVE MEASUREMENT
WIRING DIAGRAM
PARTS LIST

R-995J
2
PRODUCT SPECIFICATIONS
ITEM DESCRIPTION
Power Requirements 230 - 240 Volts
50 Hertz
Single phase, 3 wire earthed
Power Consumption 1600 W (Microwave)
1600 W (Convection)
Power Output 900 watts (IEC Test Procedure)
Operating frequency of 2450MHz
Convection heater 1500 W
Case Dimensions Width 627mm
Height 381mm
Depth 528mm
Cooking Cavity Dimensions Width 410mm
Height 246mm
Depth 410mm
Control Complement Touch Control System
Clock ( 1:00 - 12:59)
Timer (0 - 99 min. 99 sec.)
Microwave Power for Variable Cooking
Repetition Rate;
HIGH ............................................ Full power throughout the cooking time
MED HIGH ......................................................approx. 70% of Full Power
MED .................................................................approx. 50% of Full Power
MED LOW (DEFROST) ...................................approx. 30% of Full Power
LOW .................................................................approx. 10% of Full Power
Convection Temperature for Variable Cooking
CONVECTION ................................................. 40 to 250˚C Temp. control
LOW MIX(BAKE) ............................ 180˚C with 10% of microwave power
HIGH MIX(ROAST) ......................... 200˚C with 30% of microwave power
GRILL .............................................................................. 250˚C (Preheat))
HELP pad
INTELLIGENT SENSOR pad
REHEAT SENSOR pad
DEFROST SENSOR pad
WEIGHT ADJUST pad
SENSOR INSTANT ACTION pads
MORE, LESS pads
CONVECTION COOKING FUNCTION pads
POWER LEVEL pad
MEMORY pad
NUMBER and TEMPERATURE pads
STOP/CLEAR pad, CLOCK pad
INSTANT COOK/START pad
Set Weight Approx. 31 kg
GENERAL INFORMATION
WARNING
THIS APPLIANCE MUST BE EARTHED
IMPORTANT
THE WIRES IN THIS MAINS LEAD ARE COLOURED IN ACCORDANCE WITH THE FOLLOWING CODE:
GREEN-AND-YELLOW : EARTH
BLUE : NEUTRAL
BROWN : LIVE

R-995J
3
APPEARANCE VIEW
1. Oven lamp
2. Door hinges
3. Door safety latches
4. See through door
5. Door seals and sealing surfaces
6. Touch control panel
7. Digital readout
8. Waveguide cover
9. Turntable motor shaft
10. Convection air openings
11. Menu label for Intelligent sensor
12. Rating label
13. Access cover for oven lamp replacement
14. Ventilation openings
15. Power supply cord
16. Oven cavity
17. Outer cabinet
18. Low rack
19. High rack
20. Defrost rack TOUCH CONTROL PANEL
98 1 11
7
2
3
6
10
3
4
5
16
12
14 13
17
15
18
19
;;;;;;;;
;;;;;;;;
;;;;;;;;
;;;;;
;;;;;
;;;;;
20
NOTE:
The directed features are disabled after one minute when the oven is not in use. These features are automatically
enabled when the door is opened and closed or the STOP/ CLEAR pad is pressed.
MIX CONV
DEFROST
SENSOR
COOK KG HELP
Indicator
INTELLIGENT SENSOR PAD
Press to select 24 popular
Convection, Mix, Grill and
Micro cooking menus with
weight sensor or humidity
sensor.
REHEAT SENSOR PAD
Press to select 5 popular
Reheat menus with
humidity sensor.
DEFROST SENSOR PAD
Press to defrost meat, poultry
or seafood automatically with
weight sensor.
SENSOR INSTANT ACTION
PADS
Press to cook 1 of the 8
popular menus. (See Note)
MORE, LESS PADS
Press to increase/decrease the
time in one minute increments
during cooking or to alter the
doneness for the Sensor Ins-
tant Action, Reheat Sensor,
Intelligent Sensor or Defrost
Sensor modes.
CONVECTION COOKING
FUNCTION PADS
Press to cook for each function.
INSTANT COOK/START PAD
Press once to cook for 1 minute
at HIGH or increase by 1 minute
multiples each time this pad is
pressed during Microwave, Con-
vection, Grill or Mix cooking.
(See Note)
HELP PAD
Press to select auto start, in-
formation guide on/off, child
lock, demonstration mode or
info on pads.
Press to get cooking informat-
ion.
WEIGHT ADJUST PAD
Press to zero the weight of
your own dishes before
cooking with weight sensor.
POWER LEVEL PAD
Press to select microwave
power setting.
If not pressed, HIGH is auto-
matically selected.
MEMORY PAD
Press to enter the frequently
used cooking programme.
Press to recall the memorized
programme.
NUMBER AND
TEMPERATURE PADS
Press to enter cooking times,
clock time, convection tem-
perature or to select the
Intelligent Sensor menus.
STOP/CLEAR PAD
Press to clear during program-
ming.
Press once to stop operatiion of
oven during cooking; press twice
to cancel cooking programme.
CLOCK PAD
Press to set clock time.

R-995J
4
OFF CONDITION
Closing the door activates all door interlock switches
(Right latch switch, Left latch switch and stop switch.)
IMPORTANT
When the oven door is closed, the monitor switch contacts
COM-NC must be open.
When the microwave oven is plugged in a wall outlet, rated
voltage is supplied to the point A9 + common terminal of
relay RY1 in the control unit.
Figure O-1 on page 35
1. The display shows "SHARP", "MICRO-", "WAVE" and
"OVEN".
2. To set any programmes or set the clock, you must first
touch the STOP/CLEAR key.
3. " : " appears in the display and the time counts up
every minute.
NOTE: When the oven door is opened, the oven lamp
comes on at this time.
MICROWAVE COOKING CONDITION
HIGH COOKING
Select microwave cooking and power level by pressing the
POWER LEVEL pad and enter desired cooking time by
pressing NUMBER pads. When the START pad is touched,
the following operations occur:
Function sequence Figure O-2 on page 35
CONNECTED COMPONENTS RELAY
Oven lamp, Turntable motor (Power transformer) RY1
Power transformer RY2
Fan motor RY6
1. Rated voltage is supplied to the primary winding of the
power transformer. The voltage is converted to about
3.3 volts A.C. output on the filament winding and high
voltage of approximately 2000 volts A.C. on the
secondary winding.
2. The filament winding voltage (3.3 volts) heats the
magnetron filament and the high voltage (2000 volts) is
sent to the voltage doubling circuit, where it is doubled
to negative voltage of approximately 4000 volts D.C..
3. The 2450 MHz microwave energy produced in the
magnetron generates a wave length of 12.24 cm. This
energy is channelled through the waveguide (transport
channel) into the oven cavity, where the food is placed
to be cooked.
4. When the cooking time is up, a signal tone is heard and
the relays (RY1+RY2+RY6) go back to their home
position. The circuits to the oven lamp, power
transformer, fan motor and turntable motor are cut off.
5. When the door is opened during a cook cycle, the
switches come to the following condition.
Condition
During Oven Door
Switch Contact Cooking Open(No cooking)
Right Latch Switch COM-NO Closed Open
Monitor Switch COM-NC Open Closed
Left Latch Switch COM-NO Closed Open
Stop Switch COM-NO Closed Open
OPERATION SEQUENCE
The circuits to the power transformer and turntable
motor are cut off when the right latch switch and left
latch switch are made open. The fan motor is cut off
when the stop switch is made open.
The oven lamp remains on even if the oven door is
opened after the cooking cycle has been interrupted,
because the relay (RY1) stays closed. Shown in the
display is the remaining time.
6. MONITOR SWITCH CIRCUIT
The monitor switch is mechanically controlled by
oven door, and monitors the operation of the right latch
switch and left latch switch.
6-1. When the oven door is opened during or after the
cycle of a cooking program, the contacts (COM-NC)
of the monitor switch must be closed and the contacts
(COM-NO) of the right latch switch, left latch switch
and stop switch must be opened at the same time.
6-2. When the oven door is closed, the contacts (COM-
NC) of the monitor switch must be opened and the
contacts (COM-NO) of the right latch switch, left latch
switch and stop switch must be closed at the same
time.
6-3. When the oven door is opened and the contacts of the
right latch switch and the left latch switch remain
closed, the fuse M8A will blow, because the monitor
switch and relay (RY1) are closed and a short circuit
is caused.
MEDIUM HIGH, MEDIUM, MEDIUM LOW, LOW
COOKING
When the microwave oven is preset for variable cooking
power, rated voltage is supplied to the power transformer
intermittently within a 32-second time base through the
relay contact which is coupled with the current-limiting
relay RY2. The following levels of microwave power are
given.
SETTING
NOTE: The ON/OFF time ratio does not exactly correspond
to the percentage of microwave power, because
approx. 3 seconds are needed for heating up the
magnetron filament.
CONVECTION COOKING CONDITION
PREHEATING CONDITION
Press the PREHEAT pad and then select preheating
temperature by pressing the temperature pad. When the
START pad is touched, the following operations occur:
1. The coil of shut-off relays RY1+RY5+RY6 are
energized, the oven lamp, cooling fan motor, turntable
motor and convection motor are turned on.
HIGH
32 sec. ON
MEDIUM HIGH Approx. 70%
24 sec. ON 8 sec. OFF
14 sec. OFF
20 sec. OFF
26 sec. OFF
MEDIUM Approx. 50%
18 sec. ON
MEDIUM LOW Approx. 30%
12 sec. ON
LOW Approx. 10%
6 sec. ON

R-995J
5
2. The coil of relay (RY4) is energized by the CPU unit.
The damper is moved to the closed position, opening
the damper switch contacts. The opening of the damper
switch contacts sends a signal to the LSI on the CPU
unit de-energizing the relay (RY4) and opening the
circuit to the damper motor.
3. The coil of heater relay (RY3) is energized by the CPU
unit and the main supply voltage is added to the
convection heater.
4. When the oven temperature reaches the selected
preheat temperature, the following operations occur:
4-1. The heater relay (RY3) is de-energized by the CPU
unit temperature circuit and thermistor, opening the
circuit to the convection heater.
4-2. The oven will continue to function for 30 minutes,
turning the convection heater on and off, as needed
to maintain the selected preheat temperature. The
oven will shut-down completely after 30 minutes.
CONVECTION COOKING CONDITION
When the preheat temperature is reached, a beep signal
will sound indicating that the holding temperature has
been reached in the oven cavity. Open the door and place
the food to be cooked in the oven. Program desired
convection temperature and cooking time by touching the
CONVECTION pad, Temperature pad and number pads.
When the START pad is touched, the following operations
occur:
1. The numbers of the digital read-out start the count
down to zero.
2. The oven lamp, turntable motor, cooling fan motor and
convection motor are energized.
3. Heater relay (RY3) is energized (if the cavity temperature
is lower than the selected temperature) and the main
supply voltage is applied to the convection heater to
return to the selected cooking temperature.
4. Upon completion of the cooking time, the audible
signal will sound, and oven lamp, turntable motor,
cooling fan motor and convection motor are de-
energized. At the end of the convection cycle, if the
cavity air temperature is above 118˚C, the circuit to
(RY6) will be maintained (by the thermistor circuit) to
continue operation of the cooling fan motor until the
temperature drops below 118˚C, at which time the
relay will be de-energized, turning off the fan motor.
Relay (RY5) will however, open as soon as the
convection cycle has ended, turning off the convection
fan motor. This will now cool and allow the damper door
to open.
5. At the end of the convection cook cycle, shut-off relay
(RY4) is energized turning on the damper motor. The
damper is returned to the open position, closing the
damper switch contacts which send a signal to the
control unit, de-energizing shut-off relay (RY4).
MIX COOKING CONDITION
Program desired cooking time and Mix Cooking mode by
touching the LOW MIX or HIGH MIX pad and number
pads. When the START pad is touched, the following
operations occur:
1. The numbers of the digital read-out start the count
down to zero.
2. The shut-off relay (RY1+RY5+RY6) energized, turning
on the oven lamp, turntable motor, cooling fan motor
and convection motor.
3. The shut-off relay (RY4) is energized.
The damper door is closed from the open position.
4. The heater relay (RY3) is energized, adding the mains
supply voltage to the convection heater.
5. Now, the oven is in the convection cooking condition.
6. When the oven temperature reaches the selected
temperature, the following operations occur:
6-1. The power supply voltage is added to the convection
heater and power transformer alternately.
6-2. The convection heater operates through the heater
relay (RY3) contacts and the power transformer
operates through the cook relay (RY2) contacts.
6-3. These are operated by the CPU unit to supply
alternately within a 48 second time base, convection
heat and microwave energy.
The relationship between the convection and microwave
power operations are as follows.
Note: The ON and OFF time ratio does not correspond
with the percentage of microwave power, because
approx. 2 seconds are needed for heating of the
magnetron filament.
Note: During alternate Microwave/Convection operation,
the convection heater is energized only if the
cavity temperature drops below the set
temperature.
AUTOMATIC OPERATIONS
This microwave oven has 4 automatic operations as
follows.
SENSOR INSTANT ACTION
REHEAT SENSOR
INTELLIGENT SENSOR
DEFROST SENSOR
These operations work by using absolute humidity sensor
or weight sensor.
ABSOLUTE HUMIDITY SENSOR (AH SENSOR)
COOKING CONDITION
Incase where the AH sensor is used, the foods are cooked
in microwave cooking mode without figuring time, power
level or quantity. When the oven senses enough steam
from the food, it relays the information to its microproces-
sor which will calculate the remaining cooking time and
power level needed for best results.
When the food is cooked, water vapour is developed. The
16 SEC. 32 SEC.
48 SEC.
LOW MIX
HIGH MIX
MICROWAVE POWER
= APPROX. 30%
CONVECTION
TEMPERATURE
= 200˚C
MICROWAVE POWER
= APPROX. 10%
CONVECTION
TEMPERATURE
= 180˚C
40 SEC.8 SEC.
ON
ON
OFF
OFF
OFF
ON
(MICRO.)
(CONVEC.)
(MICRO.)
(CONVEC.)

R-995J
6
sensor "senses" the vapour and its resistance increases
gradually. When the resistance reaches the value set
according to the menu, supplementary cooking is started.
The time of supplementary cooking is determined by
experiment with each food category and inputted into the
LSI.
An example of how sensor works:
1. Potatoes at room temperature. Vapour is emitted very
slowly.
2. Heat potatoes. Moisture and humidity is emitted rapidly.
You can smell the aroma as it cooks. ;
3. Sensor detects moisture and humidity and calculates
cooking time and variable power.
AH SENSOR COOKING SEQUENCE
1. In case the AH sensor cooking condition is started, the
coil of shut-off relays (RY1+RY6) are energized, the
oven lamp and cooling fan motor are turned on, but the
power transformer is not turned on.
NOTE: The oven should not be operated on AH SENSOR
COOKING immediately after plugging in the unit.
Wait five minutes before cooking on AH SENSOR
COOKING CONDITION.
2. After about 16 seconds, the cook relay (RY2) is
energized. The power transformer is turned on,
microwave energy is produced and first stage is started.
The 16 seconds is the cooling time required to remove
any vapour from the oven cavity and sensor. Figure O-
2
NOTE: During this first stage, do not open the door or
touch STOP/CLEAR pad.
3. When the sensor detects the vapour emitted from the
food, the display switches over to the remaining cooking
time and the timer counts down to zero. At this time, the
door may be opened to stir food, turn it or season, etc.
NOTE: In case where a small quantity of food is cooked,
the oven will stop without displaying the remaining
cooking time.
4. When the timer reaches zero, an audible signal sounds.
The shut-off relay (RY1+RY6) and cook relay (RY2)
are de-energized and the power transformer, oven
lamp, etc. are turned off.
5Opening the door or touching the STOP/CLEAR pad,
the time of day will reappear on the display and the
oven will revert to an OFF condition.
WEIGHT SENSOR COOKING CONDITION
In case where the weight sensor is used, the foods are
cooked without figuring cooking mode, time, power level-
ler weight. When the oven sense the weight of food, it
relays the information to its microprocessor which will set
the cooking mode and will calculate the cooking time and
power level needed for best results.
ACTIVATED SENSOR FOR SENSOR COOKING
The weight sensor and AH. sensor should be worked as
following table.
Sensor Weight AH.
Cooking Menu Sensor Sensor
Roast beef, Roast beef dinner
Roast lamb, Roast lamb dinner
Roast chicken
Roast chicken dinner
Fresh vegetable, Jacket Potato
Beverage, Soup
Dinner plate, Casserole
Canned food
Pie
Pizza
Seasoned roast, Grilled fish
Roast turkey, Roast pork
Grilled steak/Chops, Biscuits
Grilled Kebabs, Roast vegetable
Frozen vegetables, Casseroles
Fish fillets, Corned meat
Rice/Pasta, Desserts
Soup, Preserves
Cake - -
Fresh vegetables Hard
White Rice
Fresh Pasta, Dry Pasta
Instant Noodles
Frozen Pasta
Porridge
Stewed Fruit
All menus
The menu "Cake" of Intelligent sensor does not use
neither the weight sensor nor the AH sensor.
FIRE SENSING FEATURE (MICROWAVE MODE)
This model incorporates a sensing feature which will stop
the oven's operation if there is a fire in the oven cavity
during microwave cooking.
This accomplished by the LSI repeatedly measures the
voltage across the temperature measurement circuit (ther-
mistor) during it's 32-seconds time base comparing the
obtained voltage measurements. If the most recent volt-
age measured is 300mV grater than the previous voltage
measured, the LSI judges it as a fire in the oven cavity and
switches off the relays to the power transformer, fan motor
and convection motor. The LSI also stops counting down
and closes the damper door so that no fresh air will enter
the oven cavity. Please refer to the following section for a
more detailed description.
MICROWAVE
MICROWAVE
AH SENSOR
SENSOR
INSTANT
ACTION
SENSOR
REHEAT
INTELLI-
GENT SEN-
SOR
DEFROST
SENSOR

R-995J
7
Operation
Please refer to the timing diagrams below.
Following operation will start 4 minutes after the oven is
started.
1. The thermistor operates within a 32-seconds time base
and it is energized for three (3) seconds and off for 29
seconds. Two (2) seconds after the thermistor is
energized, the voltage across the temperature
measurement circuit is sampled by the LSI and twenty
one (21) seconds after the thermistor is cut off the LSI
turns on the cooling fan for six (6) seconds.
2. The above procedure is repeated. If the difference
between the first voltage measured (in step 1) and the
voltage measured when the procedure is repeated
(step 2) is greater than 300mV the LSI makes the
judgment that there is a fire in the oven cavity and will
switch off the relays to the power transformer, fan
motor and convection motor. The LSI also stops
counting down and closes the damper door so that no
fresh air will enter the oven cavity.
3. Once the fire sensor feature has shut the unit down, the
programmed cooking cycle may be resumed by
pressing the "START" pad or the unit may be reset by
pressing the "CLEAR" pad.
IMPORTANT:
During sensor cooking operation, the fire sensing
operation sequence will not begin until the AH sensor
has detected vapours and initiated a sensor cooking
cycle. This is because the operation of the convection
fan would interfere with the AH sensor's vapour detec-
tion.
CONVECTION
MOTOR
THERMISTOR
Sensing
Voltage
ON
OFF
ON
OFF
ON
OFF
023243032 (sec.) 64 (sec.)
3 sec.
Sensing the voltage across temperature measurement circuit.
6 sec.

R-995J
8
The rated peak reverse voltage of D1 of the asymmetric
rectifier is 6 KV The rated peak reverse voltage of D2 of the
asymmetric rectifier is 1.7 KV. D1 and D2 of the asymmet-
ric rectifier or high voltage rectifier are shorted when the
each peak reverse voltage goes beyond the each rated
peak reverse voltage. (The process of blowing the fuse
M8A.) .
1. The high voltage rectifier is shorted by any causes
when microwave cooking.
2. The peak reverse voltage of D2 of the rectifier goes
beyond the rated peak reverse voltage 1.7 KV in the
voltagedoubler circuit.
3. D2 of the rectifier is shorted.
4. The large electric currents flow through the high
voltagewinding of the power transformer.
5. The large electric currents beyond 8A flow through the
primary winding of the power transformer.
6. The fuse M8A blows by the large electric currents.
7. The power supply to the power transformer is cut off.
FUSE M8A 250V
1. If the wire harness or electrical components are short-
circuited, this fuse blows to prevent an electric shock or
fire hazard.
2. The fuse also blows when right latch switch and left
latch switch remain closed with the oven door open and
when the monitor switch closes.
3. The fuse M8A also blows when asymmetric rectifier,
H.V. rectifier, H.V. wire harness, H.V. capacitor,
magnetron or secondary winding of power transformer
is shorted.
THERMISTOR
The thermistor is a negative temperature coefficient type.
The temperature in the oven cavity is detected through the
resistance of the thermistor, and then the control unit
causes the heating element relay to operate, thus the
current to the heating element is turned ON/OFF.
TURNTABLE MOTOR
The turntable motor drives the turntable supporting plate
to rotate the turntable.
CONVECTION MOTOR
The convection motor drives the convection fan and
provides the heated air.
FAN MOTOR
The fan motor drives a blade which draws external cool air.
This cool air is directed through the air vanes surrounding
the magnetron and cools the magnetron. This air is chan-
nelled through the oven cavity to remove steam and
vapours given off from the heating foods. It is then ex-
hausted through the exhausting air vents at the oven
cavity.
RIGHT LATCH SWITCH AND LEFT LATCH SWITCH
1. When the oven door is closed, the contacts COM-NO
must be closed.
2. When the oven door is opened, the contacts COM-NO
must be opened.
STOP SWITCH
1. This switch must make a contact when the door is
closed, and open it when the door is opened.
MONITOR SWITCH
The monitor switch is activated (the contacts opened) by
the switch lever L on the latch hook (left) while the door is
closed. The switch is intended to render the oven inopera-
tive by means of blowing the fuse M8A when the contacts
of the right latch switch and the left latch switch fail to open
when the door is opened.
Function
1. When the door is opened, the monitor switch contacts
close (to the ON condition) due to their being normally
closed. At this time the right latch switch ;and the left
latch switch are in the OFF condition (contacts open)
due to their being normally open contact switches.
2. As the door goes to a closed position, the monitor
switch contacts are opened and right latch switch, left
latch switch and stop switch contacts close. (On opening
the door, each of these switches operate inversely.)
3. If the door is opened and the contacts COM-NO of the
right latch switch and left latch switch fail to open, the
fuse M8A blows simultaneously with closing of the
monitor switch contacts.
CAUTION: BEFORE REPLACING A BLOWN FUSE M8A
TEST RIGHT LATCH SWITCH, THE LEFT
LATCH SWITCH, MONITOR SWITCH AND
MONITOR RESISTOR FOR PROPER OP-
ERATION. (REFER TO CHAPTER "TEST
PROCEDURE").
Figure D-1. Switches
MONITOR RESISTOR
The monitor resistor prevents the fuse M8A 250V bursting
when the fuse M8A 250V blows due to the operation of the
monitor switch.
ASYMMETRIC RECTIFIER
The asymmetric rectifier is a solid state device that
prevents current flow ins both directions. And it prevents
the temperature rise of the power transformer by blowing
the fuse M8A when the high voltage rectifier is shorted.
FUNCTION OF IMPORTANT COMPONENTS
D2 D1
ASYMMETRIC
RECTIFIER HIGH VOLTAGE
RECTIFIER
MONITOR
SWITCH
LEFT
LATCH
SWITCH
LATCH HOOK
(LEFT)
LATCH HOOK
(RIGHT)
RIGHT
LATCH
SWITCH
LATCH
HEADS
STOP
SWITCH

R-995J
9
selected temperature, the convection heater is de-ener-
gized. When the temperature inside the oven cavity drops
below the selected temperature, the convection heater is
energized again. In this way, the inside of the oven cavity
is maintained at approximately the selected temperature.
When the convection time reaches 0, the convection
heater is deenergzed and the convection fan stops oper-
ating and the oven shuts off.
Upon completion of the cooking time, the audible signal
will sound, and oven lamp, turntable motor, cooling fan
motor and convection motor are de-energized. At the end
of the convection cycle, if the cavity air temperature is
above 118˚C, the circuit to RY6 will be maintained (by the
thermistor circuit) to continue operation of the cooling fan
motor until the temperature drops below 118˚C, at which
time the relay will be de-energized, turning off the fan
motor. Relay RY5 will however, open as soon as the
convection cycle has ended, turning off the convection fan
motor. This will now cool and allow the damper door to
open.
DAMPER OPEN-CLOSE MECHANISM
Usually, the damper is in the open position except during
convection cooking.
Damper position is set automatically by damper motor,
damper switch, motor cam and damper shaft.
These components are operated by a signal that judges if
microwave cooking or convection cooking operation is
selected by the CPU unit.
Microwave Cooking:
Damper is in the open position, because a portion of
cooling air is channelled through the cavity to remove
steam and vapours given off from the heating foods.
It is then exhausted at the top of the oven cavity into a
condensation compartment.
Convection Cooking:
Damper is in the closed position, so that no hot air will be
allowed to leak out the oven cavity.
Damper Operation
1. When power supply cord is plugged in:
1-1. When power supply cord is plugged in, a signal is
sensed in the control unit, and operates shut-off relay
(RY4).
1-2. Contacts of shut-off relay (RY4) close, the damper
motor is energized, opening the damper door.
1-3. When the damper is moved to the open position by
the damper cam, damper switch is closed (ON
position).
1-4. The signal of damper switch is re-sensed in the
control unit and shut-off relay (RY4) is turned off.
1-5. The 240 volts A.C. to the damper motor is stopped
and the motor turns off.
2. When oven is microwave cooking:
Damper is in the open position
3. When oven is convection cooking:
3-1 Damper motor is energized by touching the convection,
temperature and START pads.
3-2. When damper is in the closed position (damper
switch is OFF), its signal is sensed by the control unit,
and shut-off relay (RY4) is de-energized.
3-3. The damper is held in the closed position during the
convection cooking operation
CONVECTION HEATER
The convection heater is located at the rear of the oven
cavity. It is intended to heat air driven by the convection
fan. The heated air is kept in the oven and force-circulated
and reheated by the convection heater.
THERMAL CUT-OUT 150˚C (OVEN)
The thermal cut-out protects the convection motor against
overheating. If its temperature rises above 150˚C because
the convection fan motor is interrupted, the ventilation
openings are obstructed or the other abnormal matter
occurs, the thermal cut-out opens and switch off the oven.
When the thermal cut-out cools itself down to 130˚C, the
contacts of the thermal cut-out will close again.
THERMAL CUT-OUT 95˚C (FAN MOTOR)
The thermal cut-out protect the fan motor against over-
heating. If its temperature goes up higher than 95˚C
because the fan motor is locked or the ventilation operat-
ing are blocked, the contacts of the thermal cut-out will
open and switch off the oven. When the thermal cut-out
cools itself down to 75˚C, the contacts of the thermal cut-
out will close again.
TEMPERATURE FUSE 150˚C (MG)
This fuse protects the magnetron against overheating. If
the temperature goes up higher than 150˚C because the
fan motor is interrupted, the air inlet duct is blocked or the
ventilation operating are obstructed, the fuse blows and
cuts off the power supplying to the power transformer. The
defective fuse must be replaced with new rated one.
THERMAL CUT-OUT 145˚C (MG)
This thermal cut-out protects the magnetron against over-
heating. If the temperature goes up higher than 145˚C
because the fan motor is interrupted, the air inlet duct is
blocked or the ventilation operating are obstructed, the
fuse blows and cuts off the power supplying to the power
transformer. The defective thermal cut-out must be re-
placed with new rated one.
CONVECTION COOKING SYSTEM
This oven is designed with a hot air heating system where
food is not directly heated by the convection heater, but is
heated by forced circulation of the hot air produced by the
convection heater.
The air heated by the convection heater is circulated
through the convection passage provided on the outer
casing of the oven cavity by means of the convection fan
which is driven by the convection motor. It then enters the
inside of the oven through the vent holes provided on the
left side of the oven. Next, the hot air heats the food on the
turntable and leaves the oven cavity through the vent in the
oven cavity left side wall.
Without leaving the oven, this hot air is reheated by the
convection heater, passes through the convection pas-
sage and enters the inside of the oven cavity again, in a
continuing cycle.
In this way, the hot air circulates inside the oven cavity to
raise its temperature and, at the same time, comes into
contact with the food being cooked.
When the temperature inside the oven cavity reaches the

R-995J
10
3-4. At the end of the convection cooking, shut-off relay
(RY4) is energized, and the damper is returned to the
open position.
NOTE: If the damper door is not in the proper position,
closed during convection or open during
microwave, the control unit will stop oven operation
after 1 minute.
Cooking Mode Operation of Damper
Microwave cooking OPEN
Convection cooking CLOSE
AH Sensor cooking OPEN
.Mix cooking CLOSE
Grill cooking CLOSE
Figure D-2. Damper Mechanism
WEIGHT SENSOR ASSEMBLY
1. When the food is placed on the turntable, the gap
between the electrodes increases in direct proportional
to the weight of food. The electrodes have the function
of a capacitor.
2. The frequency of the oscillator changes according to
the capacitance of the weight sensor.
3. The micro-computer measures the weight of food by
detecting the change in the oscillating frequency.
NOISE FILTER
The noise filter prevents the radio frequency interference
that might flow back in the power circuit.
DAMPER DUCT
DAMPER
DAMPER CAM
DAMPER MOTOR
DAMPER SWITCH
DAMPER SHAFT
FOOD
TURNTABLE
WEIGHT
SENSOR OSILATOR MICRO-
COMPUTER
(LSI)

R-995J
11
SERVICING
WARNING TO SERVICE PERSONNEL
Microwave ovens contain circuitry capable of producing very high voltage and current, contact with any part of the
high voltage circuit will result in electrocution. High voltage capacitor, Power transformer, Magnetron, High voltage
rectifier assembly, High voltage harness.
REMEMBER TO CHECK 4R
1) Reconnect all leads removed from components
during testing.
2) Replace the outer case (cabinet).
3) Reconnect the supply.
4) Run the oven. Check all functions.
Microwave ovens should not be run empty. To test for
the presence of microwave energy within a cavity,
place a cup of cold water on the oven turntable, close
the door and set the microwave timer for two (2)
minutes. Set the power level to HIGH and push the
START button. When the two minutes has elapsed
(timer at zero) carefully check that the water is now hot.
If the water remains cold carry out 3D checks and re-
examine the connections to the component being
tested.
IMPORTANT: If the oven becomes inoperative because
of a blown fuse M8A in the right latch
switch - left latch switch - monitor switch -
monitor resisitor circuit check the right
latch switch, left latch switch, monitor switch
and monitor resistor before replacing the
fuse M8A
REMEMBER TO CHECK 3D
1) Disconnect the supply.
2) Door opened, and wedged open.
3) Discharge high voltage capacitor.
WARNING: AGAINST THE CHARGE OF THE
HIGH-VOLTAGE CAPACITOR
The high-voltage capacitor remains charged about
60 seconds after the oven has been switched off.
Wait for 60 seconds and then short-circuit the
connection of the high-voltage capacitor (that is, of
the connecting lead of the high-voltage rectifier)
against the chassis with the use of an insulated
screwdriver.
Sharp recommend that wherever possible fault-finding
is carried out with the supply disconnected. It may, in
some cases, be necessary to connect the supply after
the outer case has been removed, in this event carry
out 3D checks and then disconnect the leads to the
primary of the power transformer. Ensure that these
leads remain isolated from other components and the
oven chassis. (Use insulation tape if necessary.) When
the testing is completed carry out 3D checks and
reconnect the leads to the primary of the power trans-
former.
When all service work is completed, and the oven is fully assembled, the microwave power output should be
checked and microwave leakage test carried out
When troubleshooting the microwave oven,it is helpful to
follow the Sequence of Operation in performing the checks.
Many of the possible causes of trouble will require that
aspecific test be performed. These tests are given a
procedure letter which will be found in the "Test
Procedure"section.
TROUBLESHOOTING GUIDE

R-995J
12
Home fuse blows when power supply cord is
plugged into wall outlet.
Fuse M8A blows when the door is opened.
Fuse M8A blows when power cord is plugged into
wall outlet.
88:88 does not appear in display when power cord
is first plugged into wall outlet.
Display does not operate properly when STOP/
CLEAR pad is touched. (The time of day should
appear on the display with beep sound during
normal condition.)
Oven lamp does not light with door opened.
Oven lamp does not light in cook cycle. (It light
when door is opened)
Oven lamp does not light at all
Oven lamp light, but turntable motor does not
operate.
Cooling fan motor does not operate.
The oven stops after1 minute
Oven does not go into a cook cycle, when START
pad is touched.
Low or no power is produced during microwave
cooking (The food is heated incompletely or not
heated at all)
Extremely uneven heating is produced in oven
load (food).
Function of variable cooking does not operate
properly except HIGH power.
CONV indicator lights, but oven does not go into
cook cycle when START pad is touched.
CONV indicator lights, but heating element does
not heat.
Temperature in the oven cavity is lower or higher
than preset.
When preheating, the oven does not stop.
Convection cycle runs 3 minutes then the oven
shuts down.
Oven is in the sensor cooking condition but AH
sensor does not not stop cooking cycle.
Oven stops soon and display shows "ERROR"
After START pad is touched, the oven stops and
display shows "ADD", "TURN", "TABLE".
CK = Check / RE = Replace
MAGNETRON
POWER TRANSFORMER
H.V. RECTIFIER ASSEMBLY
HIGH VOLTAGE CAPACITOR
RIGHT LATCH SWITCH
LEFT LATCH SWITCH
STOP SWITCH
MONITOR SWITCH
FUSE M8A
TEMPERATURE FUSE
THERMAL CUT-OUT
OVEN LAMP OR SOCKET
FAN MOTOR
TURNTABLE MOTOR
POSSIBLE CAUSE
AND
DEFECTIVE PARTS
ABC
D
EEEEFGGREJJ
TEST PROCEDURE
PROBLEM
CONDITION
OFF
CONDITION
COOKING
CONDITION
(CONVECTION)
(MICROWAVE)
(AH. SENSOR)
(WEIGHT
SENSOR)

R-995J
13
CONVECTION MOTOR
CONVECTION HEATER
THERMISTOR
DAMPER MOTOR
DAMPER SWITCH
AH. SENSOR
WEIGHT SENSOR ASSEMBLY
IC-3 ON CONTROL UNIT
TOUCH CONTROL PANEL
KEY UNIT
RELAY (RY-1)
RELAY (RY-2)
RELAY (RY-3)
RELAY (RY-4)
RELAY (RY-5)
RELAY (RY-6)
OPENED WIRE HARNESS
SHORTED WIRE HARNESS
POWER SUPPLY CORD
NO POWER AT WALL OUTLET
MONITOR RESISTOR
OPEN WIRING AT SENSOR
OPEN WIRING TO WEIGHT SENSOR
FOIL PATERN ON P.W.B.
SWITCH LEVER
OPEN WIRING TO THERMISTOR
NOISE FILTER
JH I
J
EQRRMN OOOO OOCKCK CK CK K CK CK P CK CK L

R-995J
14
TEST PROCEDURES
PROCEDURE
LETTER COMPONENT TEST
AMAGNETRON TEST
NEVER TOUCH ANY PART IN THE CIRCUIT WITH YOUR HAND OR AN INSULATED TOOL
WHILE THE OVEN IS IN OPERATION.
CARRY OUT 3D CHECK.
Isolate the magnetron from high voltage circuit by removing all leads connected to filament terminal.
To test for an open circuit filament use an ohmmeter to make a continuity test between the magnetron
filament terminals, the meter should show a reading of less than 1 ohm.
To test for short filament to anode condition, connect ohmmeter between one of the filament terminals
and the case of the magnetron (ground). This test should be indicated an infinite resistance. If a low
or zero resistance reading is obtained then the magnetron should be replaced.
MICROWAVE OUTPUT POWER (1 Litre water load)
The following test procedure should be carried out with the microwave oven in a fully assembled
condition (outer case fitted). Microwave output power from the magnetron can be measured by IEC
test procedure, i.e. it can be measured by using water load how much it can be absorbed by the water
load. To measure the microwave output power in the microwave oven, the relation of calorie and watt
is used. When P(W) heating works for t(second), approximately P x t/4.187 calorie is generated. On
the other hand, if the temperature of the water with V(ml) rises ∆T (°C) during this microwave heating
period, the calorie of the water is V x ∆T.
The formula is as follows;
P x t / 4.187 = V x ∆T+ 0.55 x mc (T2-T0)/ 4.187 P (W) = 4.187 x V x ∆T / t + 0.55 x mc (T2-T0)/t
Our condition for water load is as follows:
Room temperature (T0) ... around 20°CPower supply Voltage .............. Rated voltage
Water load.................................. 1000 g Initial temperature (T1) ...................... 10±1°C
Heating time .............................. 47 sec. Mass of container (mc) ......................... 330 g
T2 ...................... Final Temperature ∆T = T2 - T1 P = 90 x ∆T + 0.55 x mc (T2-T0)/47
Measuring condition:
1. Container
The water container must be a cylindrical borosilicate glass vessel having a maximum material
thickness of 3 mm and an outside diameter of approximately 190 mm.
2. Temperature of the oven and vessel
The oven and the empty vessel are at ambient temperature prior to the start of the test.
3. Temperature of the water
The initial temperature of the water is (10±1)˚C.
4. Select the initial and final water temperature so that the maximum difference between the final
water temperature and the ambient temperature is 5˚C.
5. Select stirring devices and measuring instruments in order to minimize addition or removal of heat.
6. The graduation of the thermometer must be scaled by 0.1˚C at minimum and an accurate
thermometer.
7. The water load must be (1000±5) g.
8. “t” is measured while the microwave generator is operating at full power. Magnetron filament heat-
up time is not included.
NOTE: The operation time of the microwave oven is “t + 3” sec. 3 sec. is magnetron filament heat-
up time.
Measuring method:
1. Measure the initial temperature of the water before the water is added to the vessel.
(Example: The initial temperature T1 = 11˚C)
2. Add the 1 litre water to the vessel.
3. Place the load on the centre of the shelf.
4. Operate the microwave oven at HIGH for the temperature of the water rises by a value ∆T of
10 ˚C.
5. Stir the water to equalize temperature throughout the vessel.
6. Measure the final water temperature. (Example: The final temperature T2 = 21°C)
7. Calculate the microwave power output P in watts from above formula.

R-995J
15
TEST PROCEDURES
PROCEDURE
LETTER COMPONENT TEST
Initial temperature ............................................................................................. T1 = 11°C
Temperature after (47 + 3) = 50 sec. ................................................................ T2 = 21°C
Temperature difference Cold-Warm (∆T = T2 - T1) ......................................... ∆T = 10°C
Measured output power
The equation is “P = 90 x ∆T” ................................................. P = 90 x 10°C = 900 Watts
JUDGMENT: The measured output power should be at least ±15 % of the rated output power.
CAUTION: 1°C CORRESPONDS TO 90 WATTS REPEAT MEASUREMENT IF THE POWER IS
INSUFFICIENT.
Heat up for 50 sec.
BPOWER TRANSFORMER TEST
WARNING: High voltages and large currents are present at the secondary winding and
filament winding of the power transformer. It is very dangerous to work near this
part when the oven is on. NEVER make any voltage measurements of the high-
voltage circuits, including the magnetron filament.
CARRY OUT 3D CHECKS.
Disconnect the leads to the primary winding of the power transformer. Disconnect the filament and
secondary winding connections from the rest of the HV circuitry. Using an ohmmeter, set on a low
range, it is possible to check the continuity of all three windings. The following readings should be
obtained:
a. Primary winding ....................approx. 1.1Ω
b. Secondary winding ............... approx. 68.5 Ω
c. Filament winding ................... less than 1Ω
If the reading obtained are not stated as above, then the power transformer is probably faulty and
should be replaced.
CARRY OUT 4R CHECKS.
HIGH VOLTAGE RECTIFIER TEST
CARRY OUT 3D CHECKS.
Isolate the high voltage rectifier assembly from the HV circuit. The high voltage rectifier can be tested
using an ohmmeter set to its highest range. Connect the ohmmeter across the terminal B+C of the
high voltage rectifier and note the reading obtained. Reverse the meter leads and note this second
reading. The normal resistance is infinite in one direction and more than 100 kΩin the other direction.
CARRY OUT 4R CHECKS.
ASYMMETRIC RECTIFIER TEST
CARRY OUT 3D CHECKS.
Isolate the high voltage rectifier assembly from the HV circuit. The asymmetric can be tested using
an ohmmeter set to its highest range across the terminals A+B of the asymmetric rectifier and note
the reading obtained. Reverse the meter leads and note this second reading. If an open circuit is
indicated in both direction then the asymmetric rectifier is good. If an asymmetric rectifier is shorted
in either direction, then the asymmetric rectifier is probably faulty and must be replaced with high
voltage rectifier. When the asymmetric rectifier is defective, check whether magnetron, high voltage
CHIGH VOLTAGE RECTIFIER ASSEMBLY TEST
1000g
1000g
1000g
T1˚CT2˚C
AB
C
D2 D1
ASYMMETRIC
RECTIFIER
HIGH VOLTAGE RECTIFIER

R-995J
16
TEST PROCEDURES
PROCEDURE
LETTER COMPONENT TEST
rectifier, high voltage wire or filament winding of the power transformer is shorted.
CARRY OUT 4R CHECKS.
NOTE: FOR MEASUREMENT OF THE RESISTANCE OF THE RECTIFIER, THE BATTERIES OF THE
MEASURING INSTRUMENT MUST HAVE A VOLTAGE AT LEAST 6 VOLTS, BECAUSE
OTHERWISE AN INFINITE RESISTANCE MIGHT BE SHOWN IN BOTH DIRECTIONS.
CARRY OUT 3D CHECKS.
A. Isolate the high voltage capacitor from the circuit.
B. Continuity check must be carried out with measuring instrument which is set to the highest resistance
range.
C. A normal capacitor shows continuity for a short time (kick) and then a resistance of about 10MΩafter
it has been charged.
D. A short-circuited capacitor shows continuity all the time.
E. An open capacitor constantly shows a resistance about 10 MΩbecause of its internal 10MΩresistance.
F. When the internal wire is opened in the high voltage capacitor shows an infinite resistance.
G. The resistance across all the terminals and the chassis must be infinite when the capacitor is normal.
If incorrect reading are obtained, the high voltage capacitor must be replaced.
CARRY OUT 4R CHECKS.
CARRY OUT 3D CHECKS.
1. If the fuse M8A is blown, there could be shorts or grounds in electrical parts or wire harness. Check
them and replace the defective parts or repair the wire harness.
2. If the fuse M8A is blown when the door is opened, check the upper latch switch, lower latch switch,
monitor switch and monitor resistor.
If the fuse M8A is blown by incorrect door switching, replace the defective switch(s) and the fuse
M8A.
3. If the fuse M8A is blown, there could be short in the asymmetric rectifier or there is a ground in wire
harness. A short in the asymmetric rectifier may have occured due to short or ground in H.V.
rectifier, magnetron, power transformer or H.V. wire. Check them and replace the defective parts
or repair the wire harness.
CARRY OUT 4R CHECKS.
CAUTION: Only replace fuse with the correct value replacement.
DHIGH VOLTAGE CAPACITOR TEST
ESWITCH TEST
CARRY OUT 3D CHECKS.
Isolate the switch to be tested and using an ohmmeter check between the terminals as described in the
following table.
Table: Terminal Connection of Switch
Plunger Operation COM to NO COM to NC COM; Common terminal
Released Open Circuit Short Circuit NO; Normally open terminal
Depressed Short Circuit Open Circuit NC; Normally close terminal
If incorrect readings are obtained, make the necessary switch adjustment or replace the switch.
CARRY OUT 4R CHECKS.
FBLOWN FUSE M8A
GTEMPERATURE FUSE AND THERMAL CUT-OUT TEST
CARRY OUT 3D CHECKS.
Disconnect the leads from the terminals of the temp. fuse or thermal cut-out. Then using an
ohmmeter, make a continuity test across the two terminals as described in the table below.
CARRY OUT 4R CHECKS.

R-995J
17
TEST PROCEDURES
PROCEDURE
LETTER COMPONENT TEST
Table: Temperature Fuse and Thermal cut-out Test
Temperature of “ON” condition Temperature of “OFF” condition Indication ofohmmeter
Parts Name (closed circuit) (˚C) (open circuit) (˚C) (When room temperature
is approx. 20˚C)
Temp. fuse 150˚C (MG) This is not resetable type. Above 150 ˚C Closed circuit
Thermal cut-out 145˚C(MG) This is not resetable type. Above 145˚C Closed circuit.
Thermal cut-out 150˚C(OVEN)
Below 130˚C Above 150˚C Closed circuit.
Thermal cut-out 95˚C(FM) Below 75˚C Above 95˚C Closed circuit.
If incorrect readings are obtained, replace the temperature fuse or thermal cut-out.;
An open circuit temperature fuse 150˚C (MG)/ thermal cut-out 145˚C (MG) indicates that the
magnetron has overheated, this may be due to resistricted ventilation, cooling fan failure or a fault
condition within the magnetron or HV circuit.
An open circuit thermal cut-out 150˚C (OVEN) indicates that the convection motor has over heated,
this may be due to convection motor locked.
An open circuit thermal cut-out 95˚C (FM) indicates that the fan motor winding has overheated, this
may be due to blocked ventilation or locked cooling fan.
CARRY OUT 3D CHECKS.
Disconnect connector-E from the CPU unit. Measure the resistance of the thermistor with an
ohmmeter. Connect the ohmmeter leads to Pin No’s E-3 and E-4 of the thermistor harness.
Room Temp. .................. 20˚C - 30˚C
Resistance ..................... Approx. 326kΩ- 175kΩ
If the meter does not indicate above resistance, replace the thermistor.
CARRY OUT 4R CHECKS.
ITHERMISTOR TEST
CARRY OUT 3D CHECKS.
Before carring out the following tests make sure the heater is fully cool.
1. Resistance of heater
Disconnect the wire leads to the heater to be tested. Using ohmmeter with low resistance range.
Check the resistance across the terminals of the heater.
The resistance of heater is approximately 37.5 ohms.
2. Insulation resistance
Disconnect the wire leads to the heater to be tested. Check the insulation resistance between the
element and cavity using a 500V - 100Mohms insulation tester. The insulation resistance should
be more than 10Mohms in the cold start.
If the results of above test 1 and/or 2 are out of above specifications, the heater is probably faulty
and should be replaced.
CARRY OUT 4R CHECKS.
H CONVECTION HEATER TEST
JMOTOR WINDING TEST
CARRY OUT 3D CHECKS.
Disconnect the leads from the motor.
Using an ohmmeter, check the resistance between the two terminals as described in the table below.
Table: Resistance of Motor
Motors Resistance
Fan motor Approximately 295 Ω
Turntable motor Approximately 12 kΩ
Convection fan motor Approximately 210 Ω
Damper motor Approximately 11 kΩ
If incorrect readings are obtained, replace the motor. CARRY OUT 4R CHECKS.

R-995J
18
TEST PROCEDURES
PROCEDURE
LETTER COMPONENT TEST
KMONITOR RESISTOR TEST
CARRY OUT 3D CHECKS.
Disconnect the leads from the monitor resist. Using an ohmmeter and set on a low range. Check
between the terminals of the monitor resistor.
The resistance of monitor resistor is approx. 0.8 ohms.
If incorrect readings are obtained, replace the monitor resistor.
CARRY OUT 4R CHECKS.
L NOISE FILTER TEST.
CARRY OUT 3D CHECKS.
Disconnect the leads from the terminals of the noise
filter. Using an ohmmeter, check between the termi-
nals as described in the following table.
If incorrect readings are obtained, replace the noise
filter unit.
MEASURING POINT INDICATION OF OHMMETER
Between N and L Open circuit
Between terminal N and WHITE Short circuit
Between terminal L and RED Short circuit
CARRY OUT 4R CHECKS.
The touch control panel consists of circuits including semiconductors such as LSI, ICs, etc. Therefore,
unlike conventional microwave ovens, proper maintenance cannot be performed with only a
voltmeter and ohmmeter. In this service manual, the touch control panel assembly is divided into two
units, Control Unit and Key Unit and troubleshooting by unit replacement is described according to
the symptoms indicated.
1. Key Unit. Note: Check key unit ribbon connection before replacement.
The following symptoms indicate a defective key unit. Replace the key unit.
a) When touching the pads, a certain pad produces no signal at all.
b) When touching a number pad, two figures or more are displayed.
c) When touching the pads, sometimes a pad produces no signal.
2. Control Unit.
The following symptoms indicate a defective control unit. Replacethe control unit.
2-1 In connection with pads.
a) When touching the pads, a certain group of pads do not produce a signal.
b) When touching the pads, no pads produce a signal.
2-2 In connection with indicators.
a) At a certain digit, all or some segments do not light up.
b) At a certain digit, brightness is low.
c) Only one indicator does not light.
d) The corresponding segments of all digits do not light up; or they continue to light up.
e) Wrong figure appears.
f) A certain group of indicators do not light up.
g) The figure of all digits flicker.
2-3 Other possible troubles caused by defective control unit.
a) Buzzer does not sound or continues to sound.
b) Clock does not operate properly.
c) Cooking is not possible.
d) Proper temperature measurement is not obtained.
MTOUCH CONTROL PANEL ASSEMBLY TEST
FUSE
M8A
LN
LINE CROSS CAPACITOR 0.22 / AC 250V
noise suppression coil
LINE BYPASS
CAPACITOR
0.0022 /AC 250V
LINE BYPASS
CAPACITOR
0.0022 /AC 250V
NOISE FILTER
WHT RED
Other manuals for Carousel R-995J
1
Table of contents
Other Sharp Microwave Oven manuals
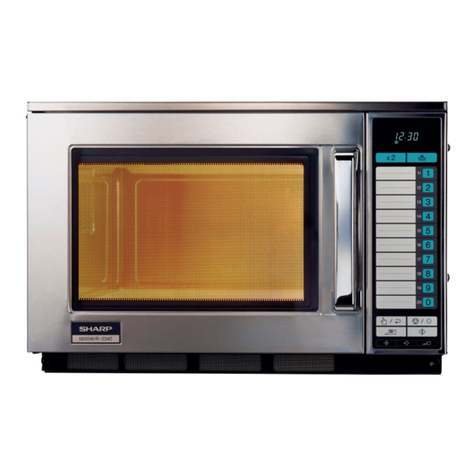
Sharp
Sharp R-23AT User manual

Sharp
Sharp R-820BW User manual
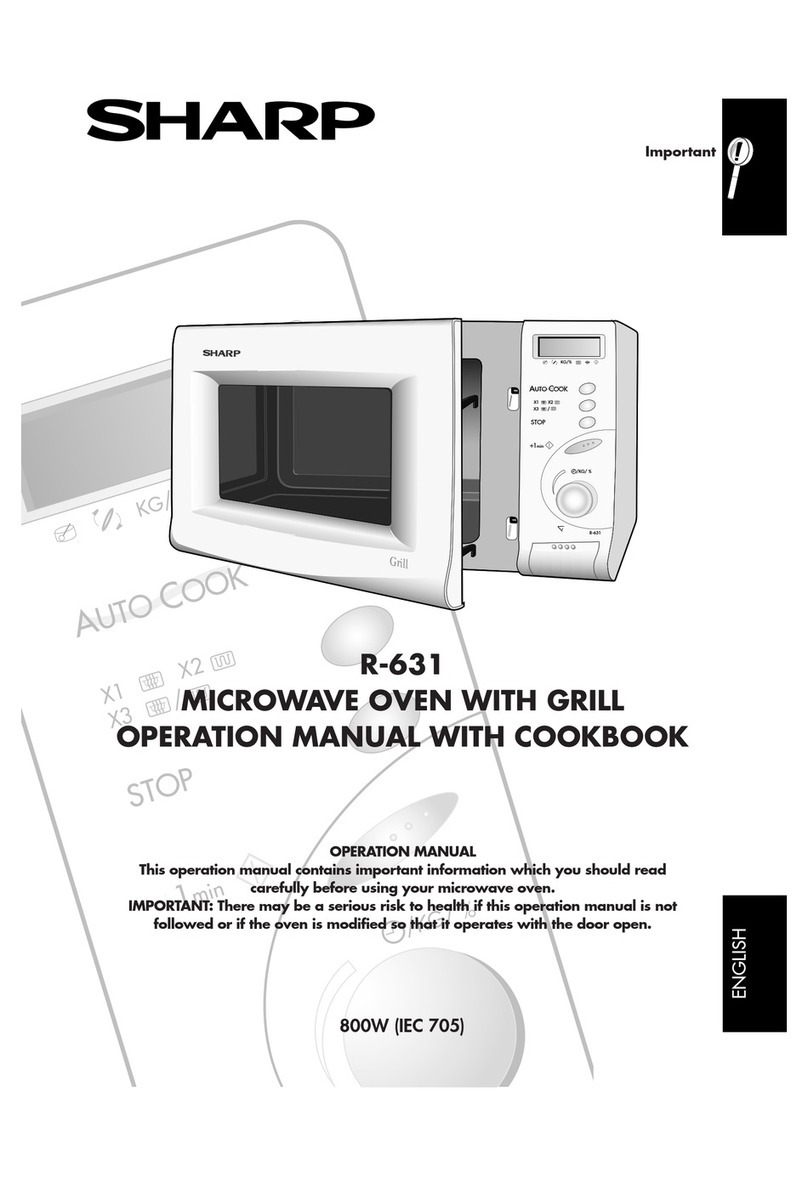
Sharp
Sharp R-631 Instruction Manual
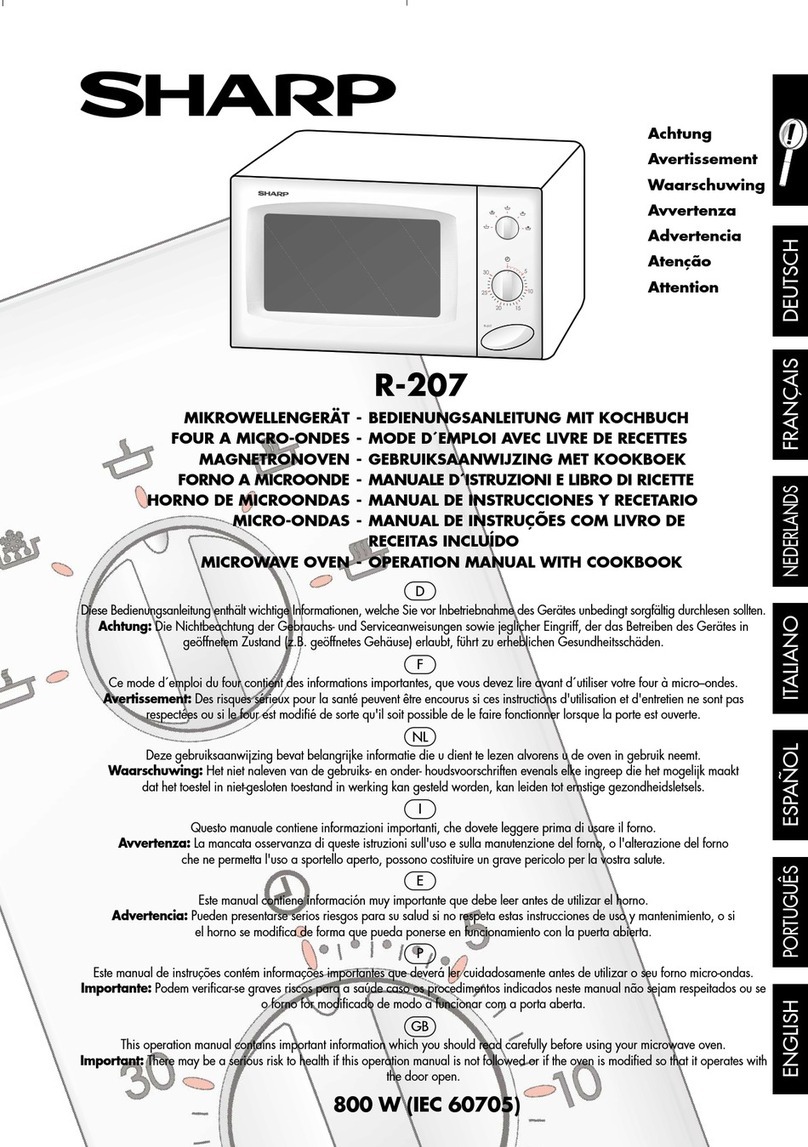
Sharp
Sharp R-207 Instruction Manual
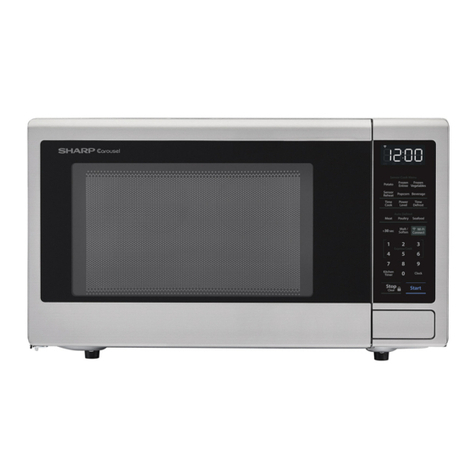
Sharp
Sharp SMC1449FS User manual
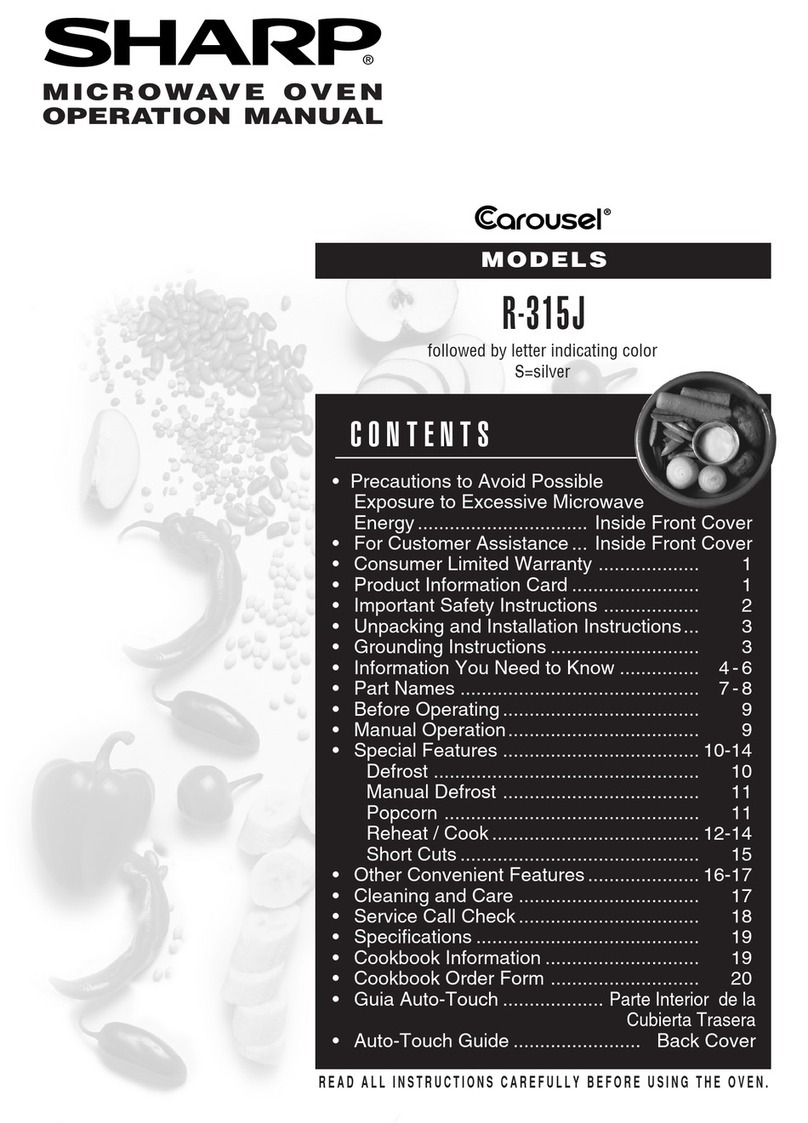
Sharp
Sharp Carousel R-315J User manual
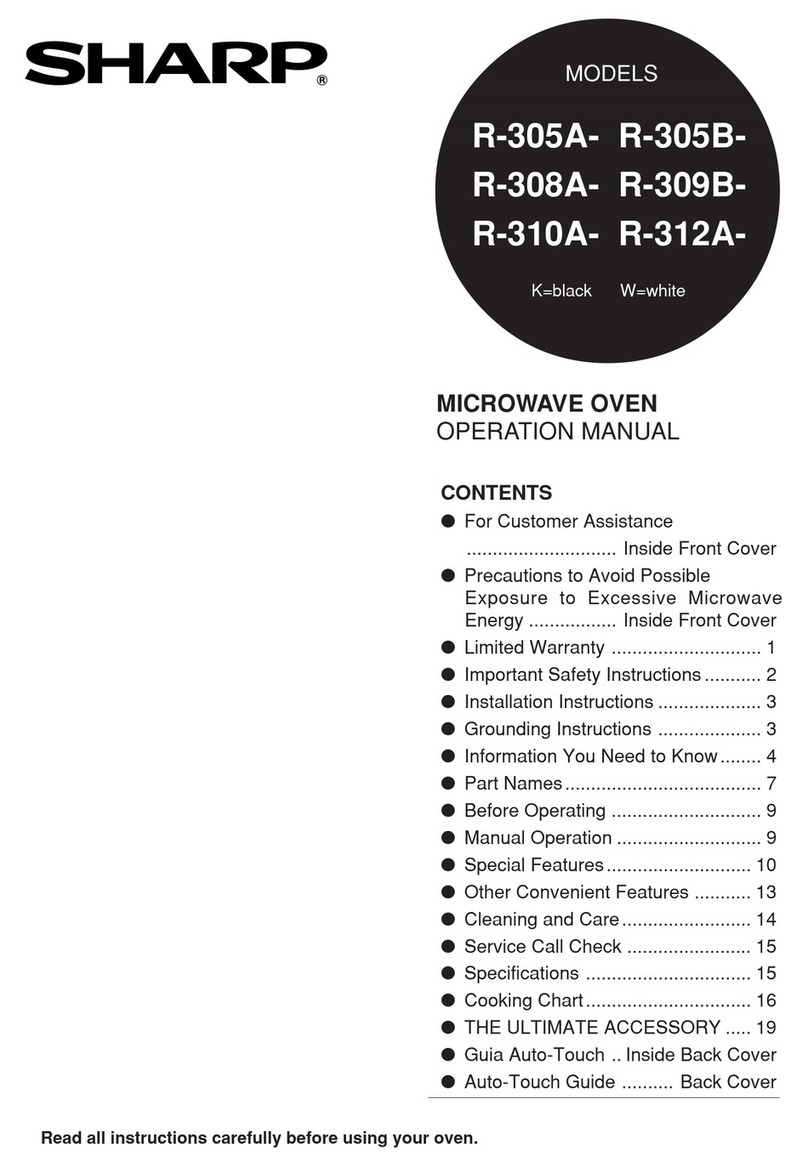
Sharp
Sharp R-305B User manual
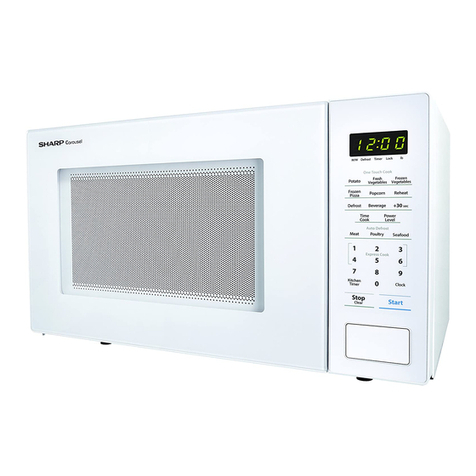
Sharp
Sharp SMC1131CW User manual
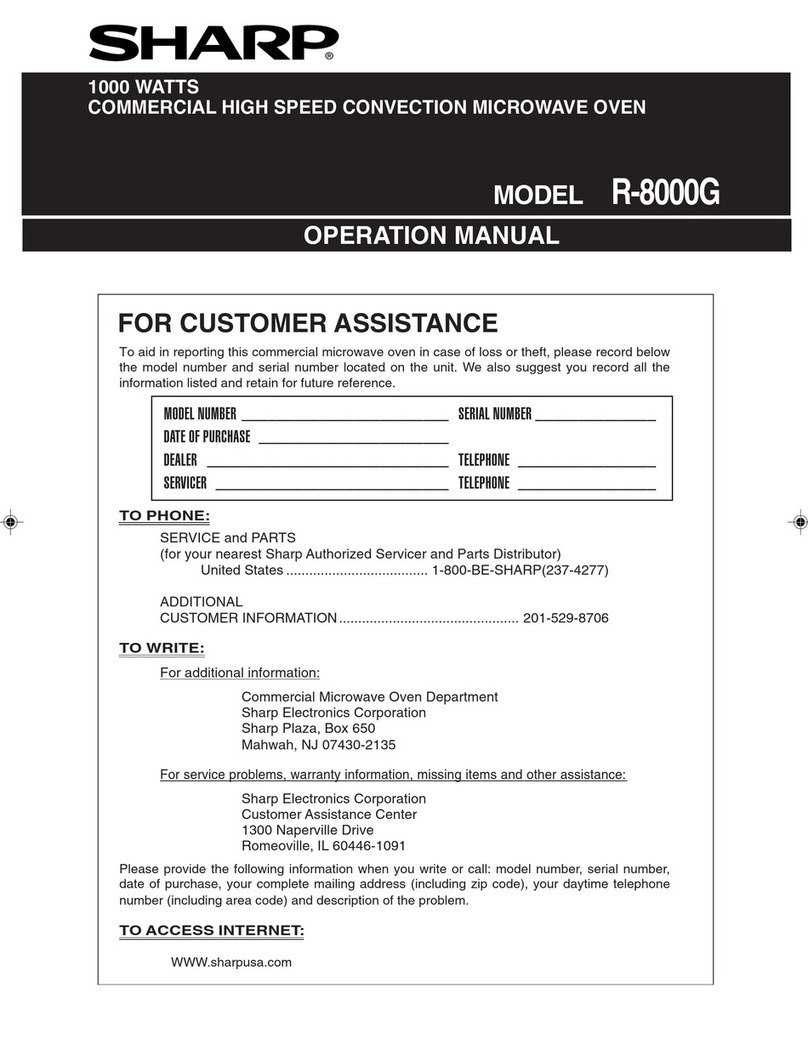
Sharp
Sharp R-8000G User manual
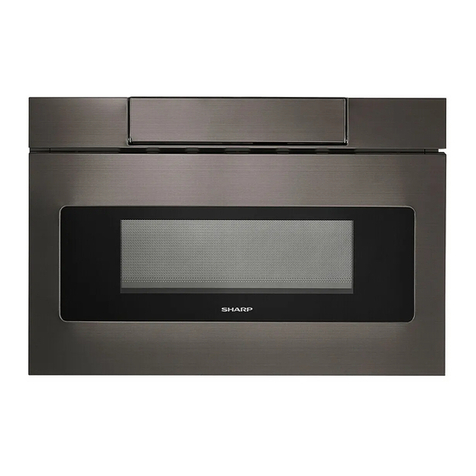
Sharp
Sharp SMD2470AH User manual
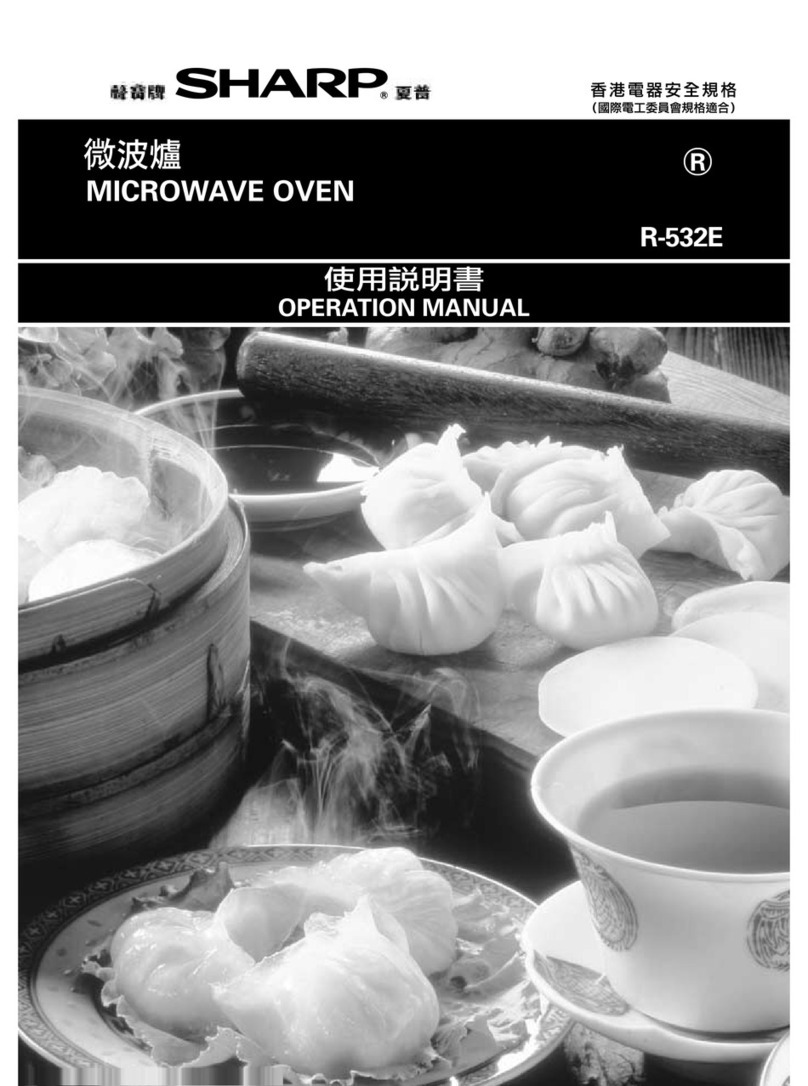
Sharp
Sharp R-532E User manual
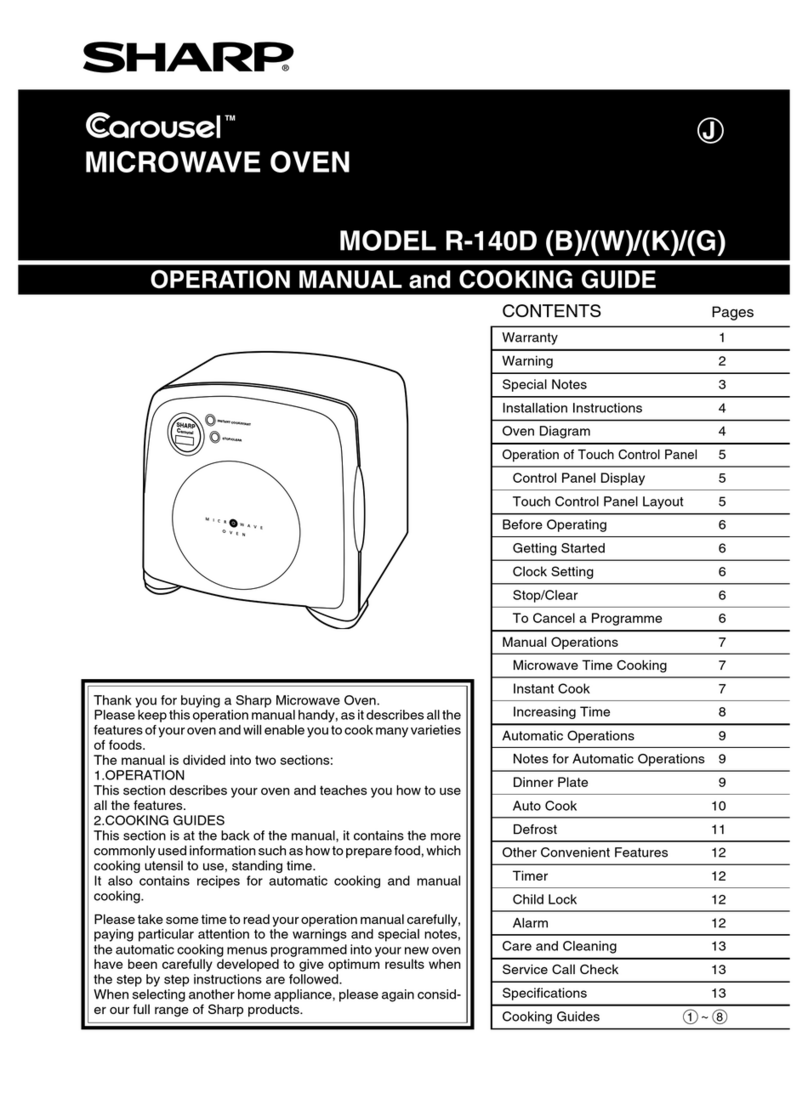
Sharp
Sharp Carousel R-140D User manual
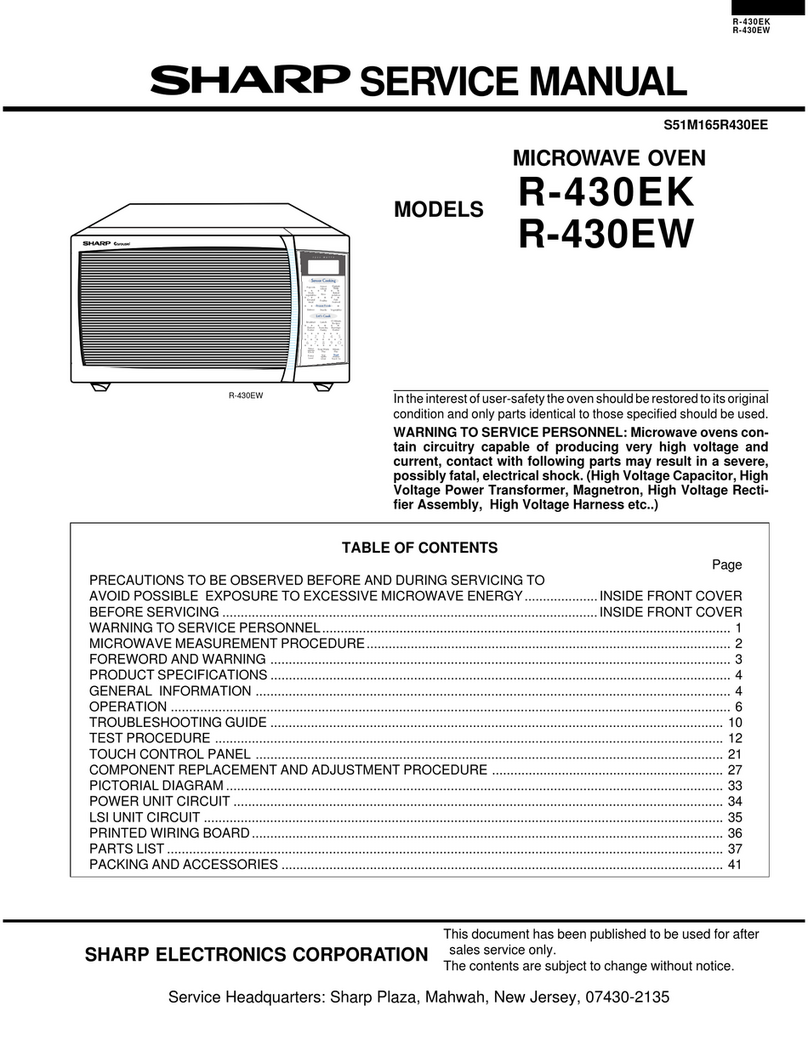
Sharp
Sharp R-430EK User manual
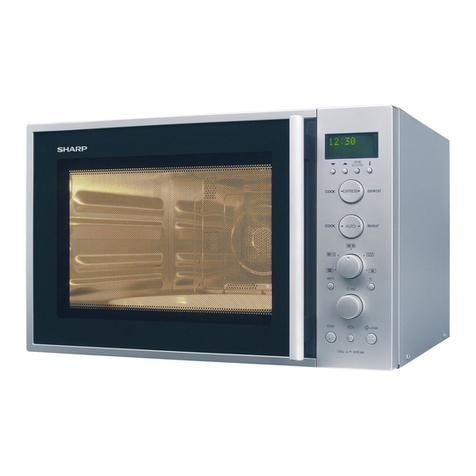
Sharp
Sharp R-939 User manual
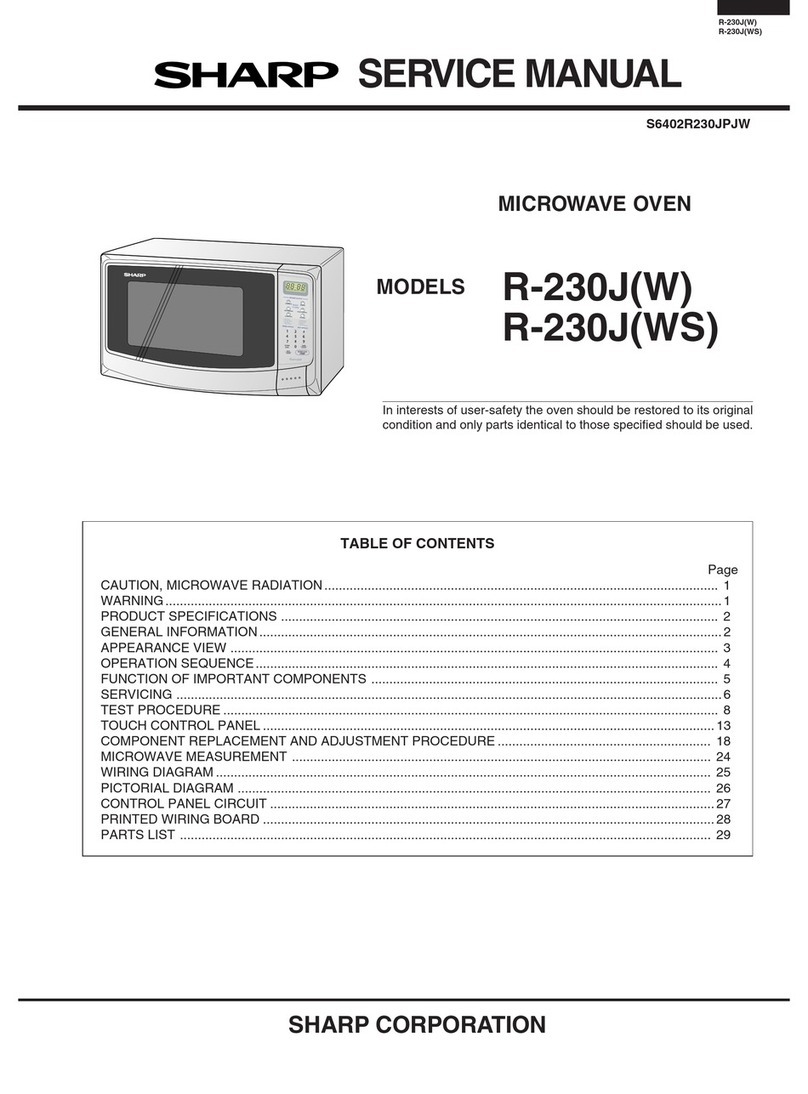
Sharp
Sharp Carousel R-230J User manual
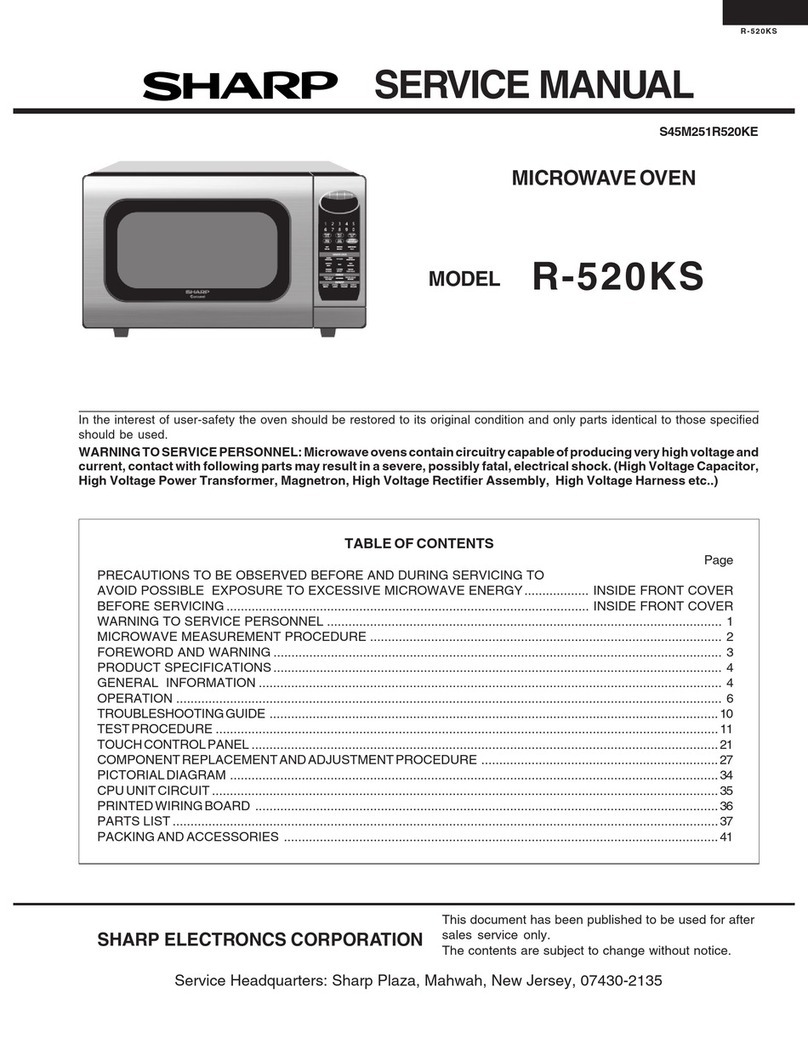
Sharp
Sharp R-520KS User manual
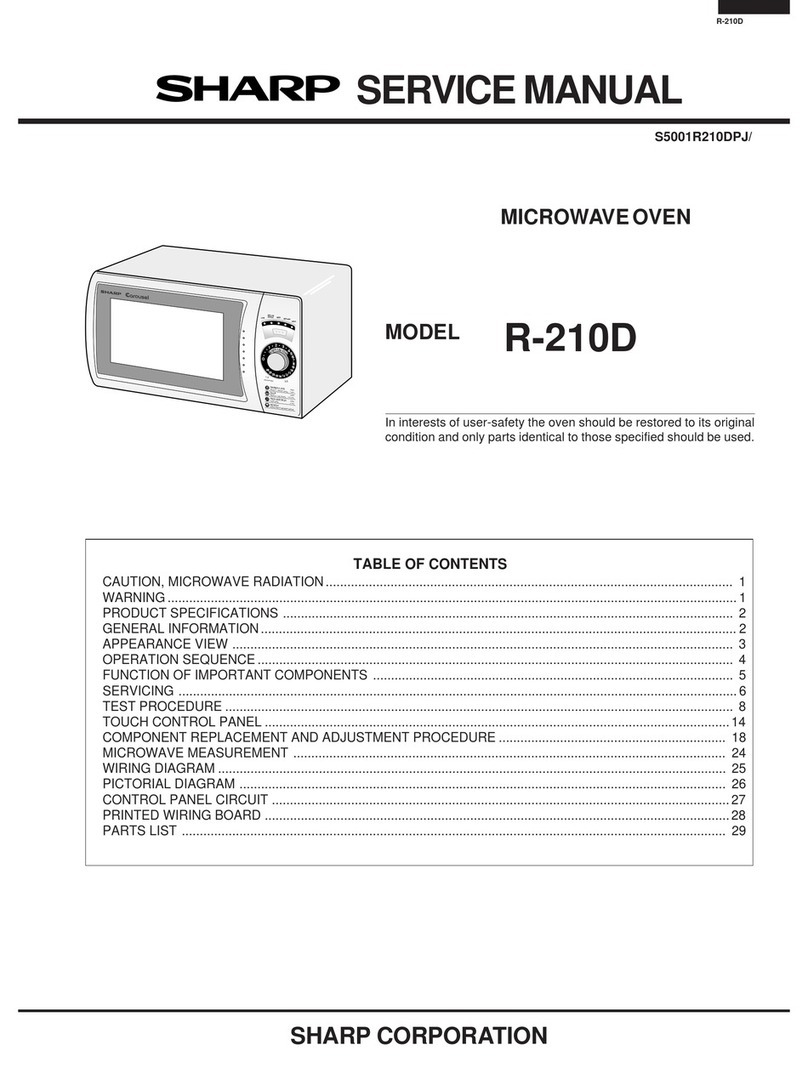
Sharp
Sharp Carousel R-210D User manual

Sharp
Sharp R-340A User manual
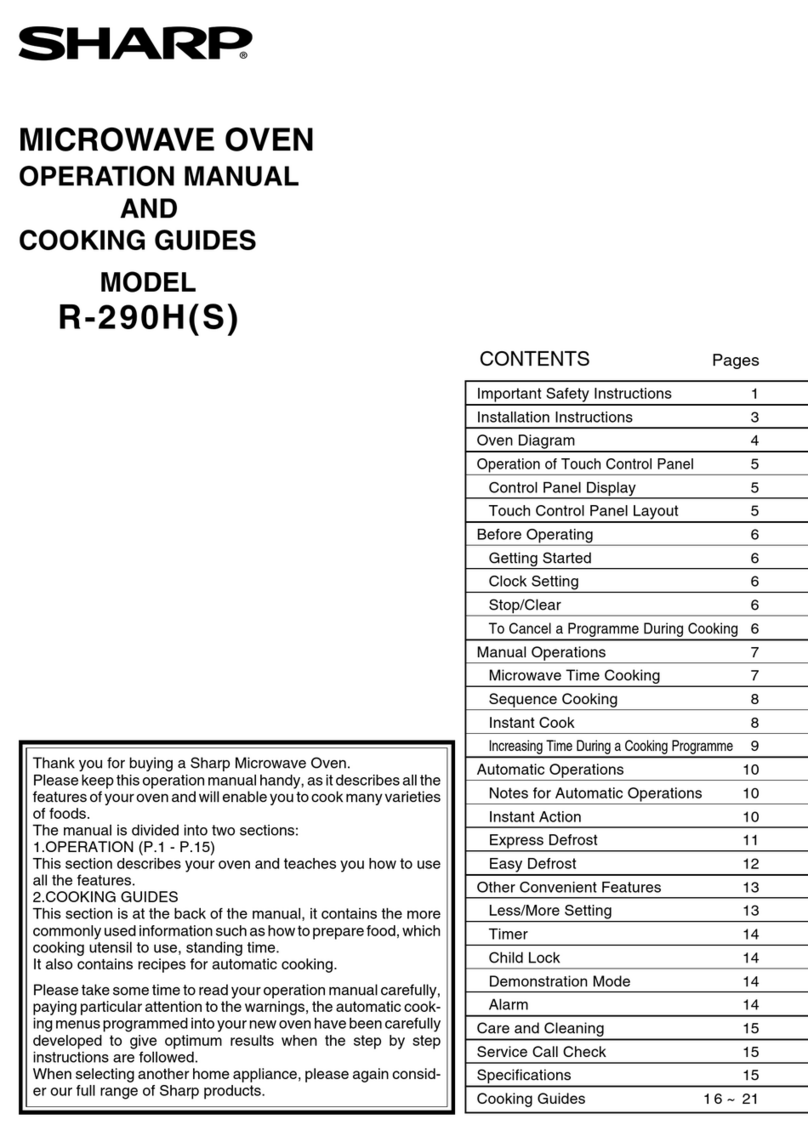
Sharp
Sharp R-290S User manual
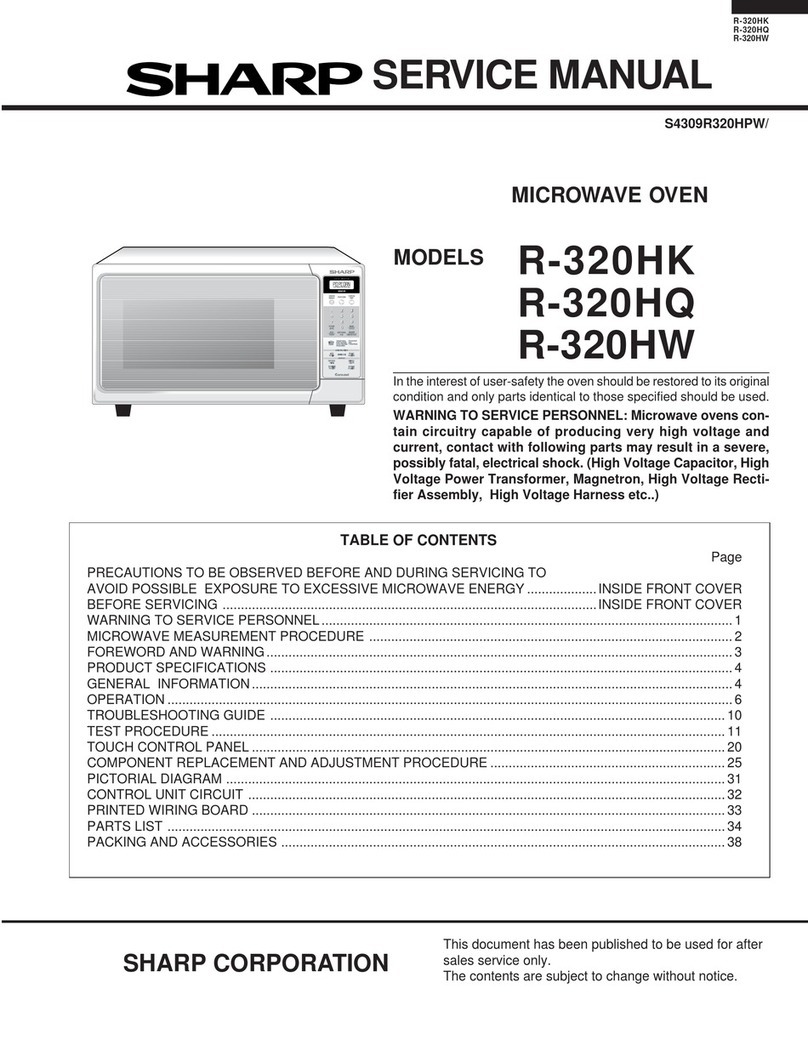
Sharp
Sharp R-320HK User manual