Smith-Cooper SONIC TORQUE SPNII Series User manual

IM-SPNII
12/22/2010 / REV.
Page 1 of 8
Installation, Operation, and Maintenance Manual
SONIC TORQUE SPNII SERIES
Pneumatic Actuators
MODEL: SPN 032, 050, 063, 075, 085, 100, 115, 125, 145, 160, 180, 200, 240, 265
300, 350, & 400.
WARNING AND SAFETY INSTRUCTIONS:
1. Read this Installation, Operation & Maintenance manual before using the actuator.
2. Sharpe Valves cannot anticipate all of the situations a user may encounter while installing and using the
SPNII Actuator. The user must know and follow all applicable industry specifications on the safe
installation and use of these actuators. Only qualified personnel or technicians who are trained for
maintenance work and have read the instructions are to assemble and disassemble the actuator.
Misapplication of the product may result in injuries or property damage.
3. Before operating an actuator which is connected to a valve in the pipeline, make sure you know the
valve function.
4. Make sure the actuator is not connected to the air supply or electrical system before attempting to do
any maintenance.
5. Before removing the actuator from the valve, always make sure the line has been depressurized and
drained. Cycle the valve a few times to relieve any pressure that could be trapped in the body cavity.
6. Use only Sonic Torque components and spare parts supplied in the repair kits.
7. Do not use air pressure to remove actuator pistons when covers have been removed.
8. Do not leave any grip key or shaft connection attached to the actuator, or try to manually operate the
actuator while it is still connected to the air supply.
9. The user must follow and observe any national or local safety law imposed for
for his system.
STORAGE
The Sonic Torque SPNII Actuator has been packaged to provide protection
during shipment and storage. It is however, possible that the actuator can be
damaged during transport. Inspect actuator for shipping damage prior to storage.
Keep the actuator in their original boxes and store indoor in a clean dry
environment until ready for use. Keep plastic plugs in the air ports to prevent
liquids or other materials from entering the actuator during storage. It is
recommended to stroke them periodically to prevent setting of seals.
LUBRICATION:
The actuators are pre lubricated from the factory and under normal operating conditions
do not require re-lubrication. In the event of actuator maintenance it is recommended
to use the following lubricants:
For NBR O-rings use EP1. The lubricant is suitable for use from -20ºC to +80ºC

IM-SPNII
12/22/2010 / REV.
Page 2 of 8
(-4ºF to +176ºF) with AIT/Flashpoint> (T-class +50K)
For Viton O-rings use Molykote 111 or OKS 1110. The lubricant is suitable for use from -40ºC
to +140ºC (-40ºF to +284ºF).
For EPDM O-rings use only Silicone grease
SUPPLY PRESSURE
Double-acting and Spring Return:
Max. 8 Bar (116 PSI), Minimum 3.0 Bar (40 PSI)
When sizing an actuator to available air supply, make sure you have adequate power in the actuator
to allow the valve to complete its operation and leave enough power for safety margin.
AIR SUPPLY
Use clean dry air. Do not use water as supply media.
Do not operate the actuator by using flammable, oxidizing and corrosive, explosive or unstable gasses.
Oxygen or hydrogen must not be used.
The operating medium is to be filtered to 30 micron particle size or less. Always consult with
a representative of SPNII for suitability and recommended practice. Piping connected to the
actuator or accessories should be fitted according to recommended instrumentation piping
practice. Prior to connection make sure all lines have no loops and are free of water, oil or
other contaminants that may be trapped in the pipes. Pipes must be flushed with air to clean
the passages. Where sealants are being used for threaded connections, care must be taken
to avoid excess material been forced into the actuator ports.
OPERATING TEMPERATURE
The standard temperature limits for the SPNII actuators are:
Maximum +80°C (+176°F), Minimum -20°C
temperatures below or above these figures special preparation and materials are required
such as grease, O-rings, pinion bearing and pads. The SPNII maximum working temperature
is 130°C (266°F) when used with Viton O-rings and HT grease. The minimum working
temperature is -40°C (-40°F) when used with EPDM O-rings and LT grease. For temperatures
below -40°C (-40°F) please consult with representative. When used in sub-zero temperatures
it is essential to use an air dryer for the supply to avoid any moisture. Always consult with
representative of SPNII for suitability and recommended practice.
PRINCIPLE OF OPERATION
The SPNII actuator is a two piston Rack & Pinion pneumatic actuator. Air pressure applied to
the piston surface area generates thrust which transforms linear motion to rotary motion of
the pinion.
Fig. 1
AIR CONNECTIONS
The actuator air connections are marked A and B. Both are NPT ports. Check the catalog/website
for thread sizes. Port B connects to a chain of holes to two pistons. The air passes into the body

IM-SPNII
12/22/2010 / REV.
Page 3 of 8
wall and come out in two places in the cylinder near the cover. Each piston receives the air flow
from two directions which ensures a quick response.
Looking from the top of the actuator.
A port is on the left ; B port is on the right
Fig. 2 Fig. 3
Double Acting (DA)
Fig. 2: Pressure entering port A to open.Center chamber pushes the pistons outward and
rotates the pinion CCW (counter clockwise).
Fig. 3: Pressure entering port B to close. The outer chamber pushes the pistons inward and
Rotates the pinion CW (clockwise).
Fig. 4 Fig. 5
Spring Return (SR)
Fig. 4: Pressure entering port A to open. Pressure at center chamber pushes the pistons outward and
rotates the pinion CCW (counter clockwise).
Fig. 5: Air released from center chamber exiting at port A. Spring pushes the pistons inward,
Pinion rotates CW (clockwise).
NAMUR Solenoid Mounting
Air supply connection is done by mounting a solenoid (Fig. 6) directly onto a mounting pad conforming to
the Namur standards. (only Solenoids made to the NAMUR standard can be mounted in this way.) The
SPNII actuator can also be piped with solid or flexible tubing from remote solenoid valves.
Fig. 6 Fig. 7
ISO 5211 or DIN 3337 FRONT VIEW
The actuator bottom flange is in accordance with ISO 5211 (or DIN 3337)
International standard and incorporates a star shaped female drive (Fig. 8) for flexibility to fit various
valve output shafts. The valve can be attached by bracket or mounted directly onto the actuator, using
one of the various ISO hole patterns. Please refer to the SPNII catalog for dimensions or visit our
website at “www.sharpevalves.com”.

IM-SPNII
12/22/2010 / REV.
Page 4 of 8
Fig. 8
Bottom View
Travel Adjustment
The actuator comes factory adjusted to produce 90°rotation with options available for 120° and 180°.
The rotation is restricted by adjustment of stop bolts (2) which provide fine tuning or a limiting stroke.
Fig. 9
The standard stop bolts allow adjustment of +/-5º in the travel limits.
Disassembly
General
Before performing any disassembly operations make sure you read all the warnings and safety
instructions in this leaflet.
Do not attempt to disassemble the actuator while it is still connected to the valve or to any ancillary.
Verify that the actuator is not pressurized. Check if the air ports are vented and spring return actuators
are in the fail close position.
Work in a clean area, free of dust, debris, greased, corrosives, and moisture. For security and comfort
do the repairs on a table with a vise and available air supply.
1. Disassembly of Covers
1.1 For spring return actuators; Springs in the actuator are pre-loaded. Loosen the cover screw
gradually in sequence by turning opposing screws two rotations at a time to release springs.
1.2 Remove the covers making sure not to damage the O-ring seals (14).
1.3 Remove the springs (17) from the cylinder and lay them together with their covers for the assembly
stage.
1.4 Follow the same routine on the other end.
2. Loosen the Stop Bolt
2.1 Loosen the Stop Nut (04) first then loosen the Stop Bolt (02). Remove the Washer (03) and
O-Rings (11). Check and replace damage o-rings.
3. Pistons Disassembly
3.1 Place the coupler to the vise then place the actuator on top of the coupler. With the bottom hole
of the actuator engaged with the coupler. The ports facing towards you, hold the actuator
body on both ends and turn clockwise until the pistons protrude further out from the cylinder
to be removed.
Note: If the piston is fail counter clockwise, Body must be rotated in opposite direction.
3.2 Remove the pistons by hand or with pliers. Caution not to damage the pistons surfaces.
3.3 Remove the piston O-rings (16) and piston bearings (15) if replacing all soft components.

IM-SPNII
12/22/2010 / REV.
Page 5 of 8
Fig 10 Fig 11
4. Pinion Shaft Disassembly
4.1 Remove the snap-ring (18) using the snap-ring pliers.
4.2 Apply downward force to top of pinion until it is partially out of the bottom of the body. Then pull
the pinion completely. When the pinion does not come out freely, hit the top with a rubber
mallet or gently tap with a rubber/wooden mallet or hammer.
4.3 Remove top and bottom pinion bearings (06 & 07), and o-rings (20 & 21). If replacing all soft
components. When all components are disassembled, those are not being replaced should be
inspected for wear before being greased and reassembled.
Fig 12
5. Pinion Shaft Assembly
Prior to assembly, ensure all components are perfectly clean and free from damage. Please see
Lubrication above.
5.1 Install top and bottom pinion bearings (6 & 7) and top and bottom pinion o-rings (20 & 21).
5.2 Apply grease to the surface of the drive shaft.
5.3 Insert he pinion shaft partially from the bottom of the body. The shaft protruding at the cylinder.
5.4 Install the stroke adjustment stop thru the cylinder to the pinion shaft in the correct
position shown in figure # 13.
Fig 13
5.5 Insert the snap ring (18) to the pinion shaft.
6. Piston Assembly
6.1 Install piston o-rings (16), the piston bearing (15).
6.2 Apply grease to the contact surfaces and rack of the pistons.
6.3 Insert the two pistons in the cylinders, keeping the orientation of the racks so the teeth is engaged

IM-SPNII
12/22/2010 / REV.
Page 6 of 8
with the pinion teeth.
6.4 Hold both ends of the body with both hands, apply pressure to the pistons until pistons are flush
pistons are pulled inside. Make sure the pistons have reached the
back 90°CW to the open position so the pistons are now almost flush with the
tons in to the close position and once again apply grease in the cylinders behind
ith a new set.
7.3 Insert the screws. Tighten the screws in sequence and only two turns at a time.
Fig 14
to the body.
6.5 Place the actuator on top of the couple in the vise
6.6 Rotate the body CCW until both
same position in the cylinder.
6.7 Insert the stop bolt back until the end rest to the face of the adjustment stop.
6.8 Rotate the body
actuator body.
6.9 Screw the other stop bolt back until they it touch the stop.
6.10 Rotate the body back and forth to get the pistons running smoothly in the cylinder.
6.11 Bring the pis
the pistons.
7. End Cap Assembly.
7.1 Apply grease to all the spring sets.
7.2 Push the cover O-ring (14) in the groove of the covers. If needed, replace them w
For spring return, place the body in vertical position, place the spring set inside.
8. ADJUSTMENT INSTRUCTIONS
PORT A PORT B
"CLOSED" POSITION
ADJUSTING SCREW
"OPEN" POSITION
ADJUSTING SCREW
Fig 15
8.1 On double acting actuators, air supplied to Port B will cause the actuator shaft (and position indicator) to
rotate Clockwise, towards the “valve closed” position. Spring return actuators (fail closed) will rotate in this
direction by spring force alone.
ght
unterclockwise.
urning the adjusting screw counterclockwise will cause the shaft to rotate clockwise.
8.2 To adjust the “Valve Closed” position (as observed on the position indicator), loosen the jam nut on the ri
hand adjusting screw (above Port B) and turn the screw clockwise to rotate the shaft co
T
Note: For double acting actuators, it will be necessary to apply air to Port B after adjusting the screw
counterclockwise to rotate the position indicator and check the adjustment. Repeat as needed.

IM-SPNII
12/22/2010 / REV.
Page 7 of 8
8.3 On double acting actuators, air supplied to Port A will cause the actuator shaft (and position indicator) to
rotate Counterclockwise, towards the “valve open” position.
8.4 To adjust the “Valve Open” position (as observed on the position indicator), loosen the jam nut on the left
hand adjusting screw (above Port A) and turn the screw clockwise to rotate the shaft clockwise. Turning the
adjusting screw counterclockwise to rotate the shaft to counterclockwise.
Caution
Do not attempt any adjustments while the actuator air supply is on,
and the actuator is under pressure.
Actuator Testing
After the proper adjustment has been accomplished, it is required to follow these testing
procedures to ensure the actuator is assembled correctly and to minimize the risk of personal
injury.
Pneumatic Leak Test
The pneumatic test checks there is no leakage across the pistons or to environment. Use
commercial leak testing solution to check leakage to atmosphere. It is acceptable to allow a
small amount of leakage to atmosphere. A bubble which breaks every 10 seconds is considered
acceptable. The leak testing pressure will be 80 psig (5.5 barg). Use a calibrated pressure
regulator to apply pressure to the actuator. Warning: Do not exceed the maximum operating
pressure rating listed on the nameplate. Cycle the actuator at least 5 times to allow the seals
to find their position before commencing with the leak test.
Piston Leakage
Any leakage across the piston is not acceptable.
1.0 Apply the pressure to port A and leave port B open.
2.0 Apply a leak testing soap solution to port B and check for leakage.
3.0 For DA actuators repeat this applying pressure to port B and check port A for leakage.
4.0 If Leakage is observed, disassemble the actuator again and check the seal, surface finish and
cleanliness of the internal parts to find the cause of leakage. After doing the repair work, the
leakage test must be performed again.
External Leakage
For SR actuators apply the pressure to port A and leave port B open. For DA actuators apply the
pressure to port A and B. After applying pressure, wait a few seconds to let the pistons stabilize
and then check for leakage. Apply the leak testing solution to the pinion output. For DA actuators
apply the leak testing solution to the covers.

IM-SPNII
12/22/2010 / REV.
Page 8 of 8
PARTS AND IDENTIFICATION
Fig. 16
Fig. 17
This manual suits for next models
17
Table of contents
Popular Controllers manuals by other brands
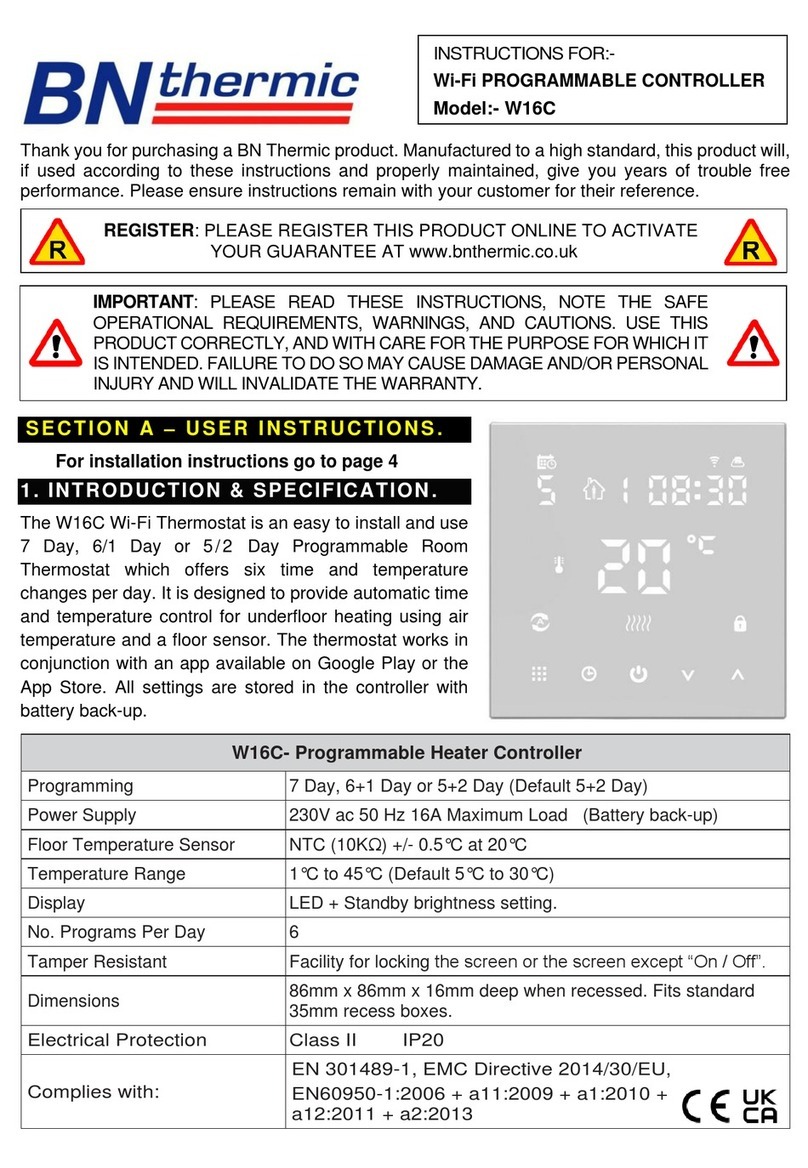
BN Thermic
BN Thermic W16C instructions
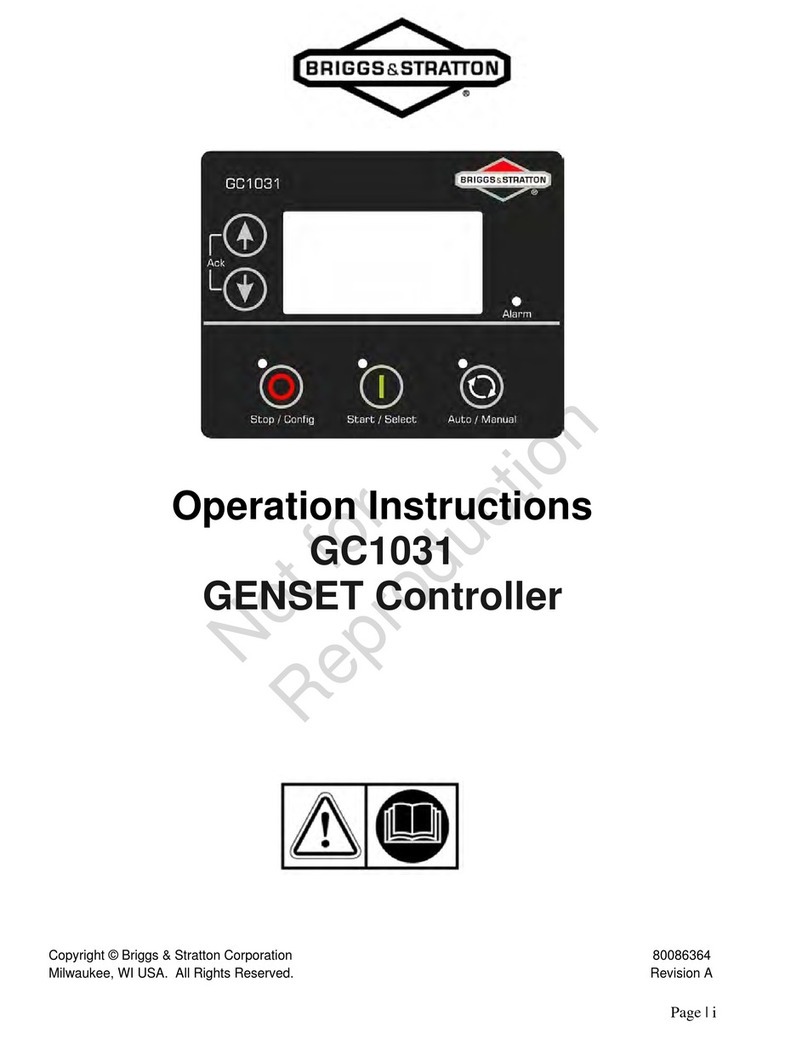
Briggs & Stratton
Briggs & Stratton GC1031 Operation instructions
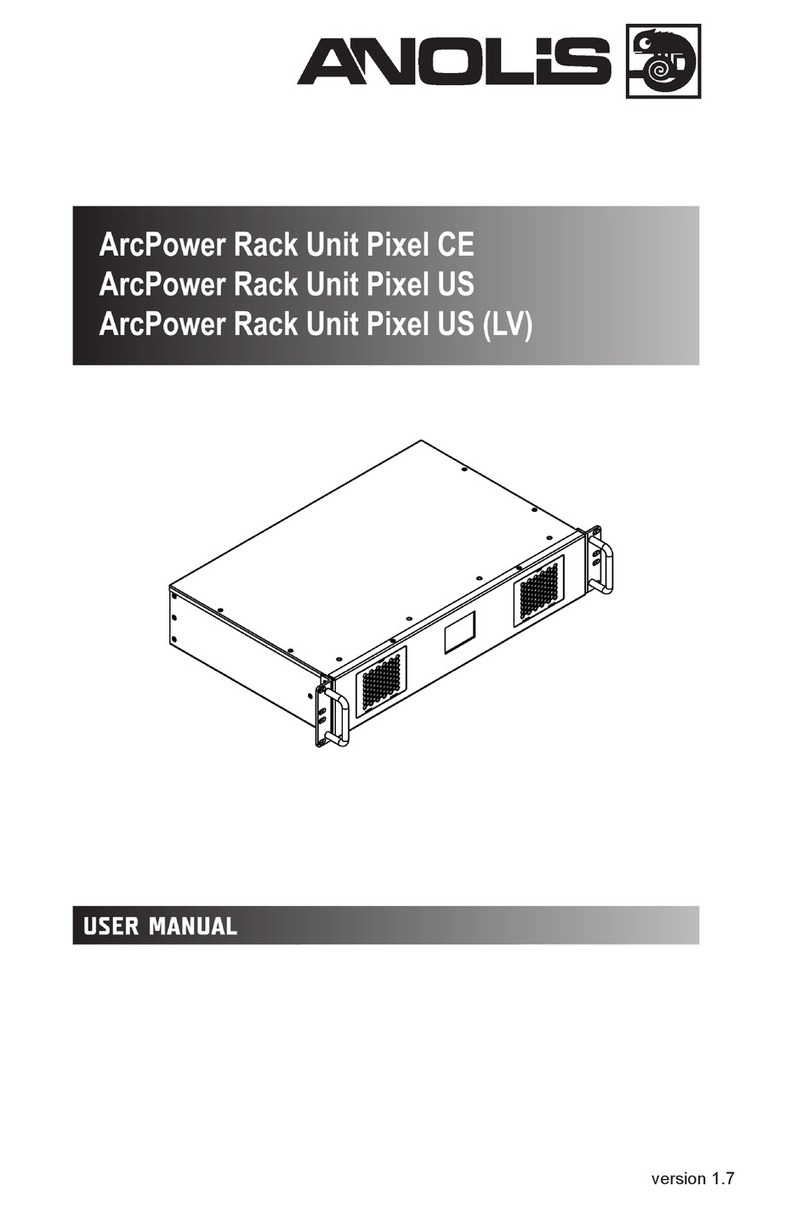
Anolis
Anolis ArcPower Rack Unit Pixel CE: ArcPower Rack Unit Pixel... user manual
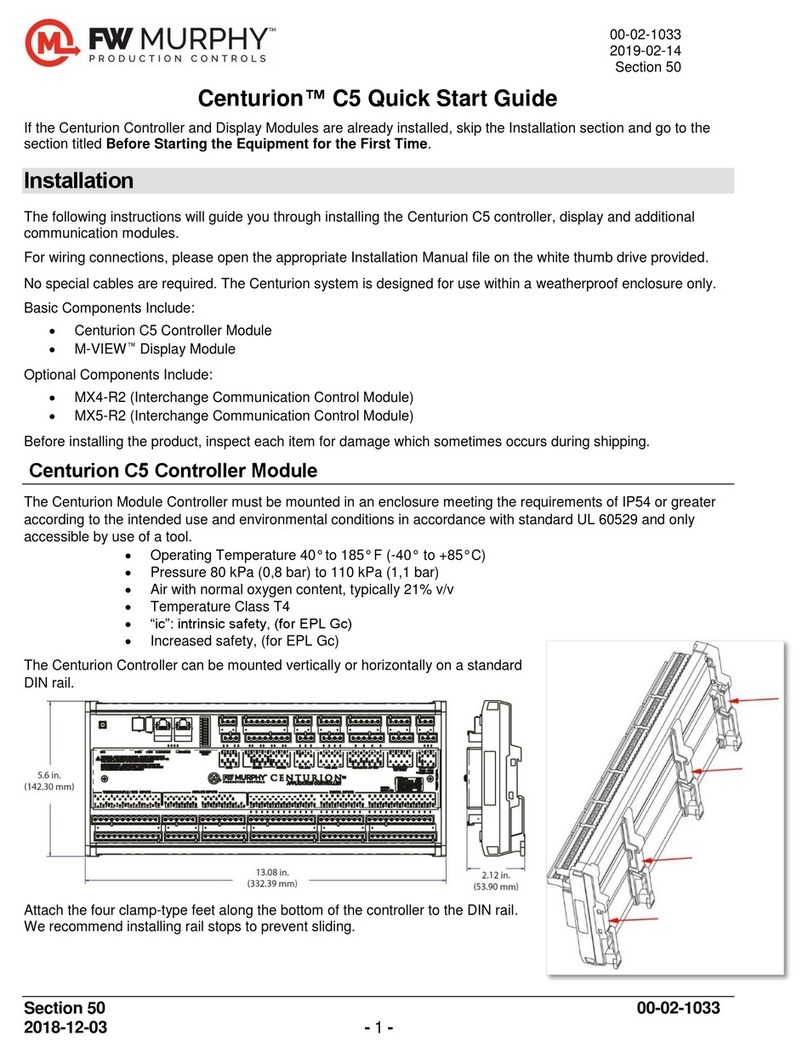
FW Murphy
FW Murphy Centurion C5 quick start guide
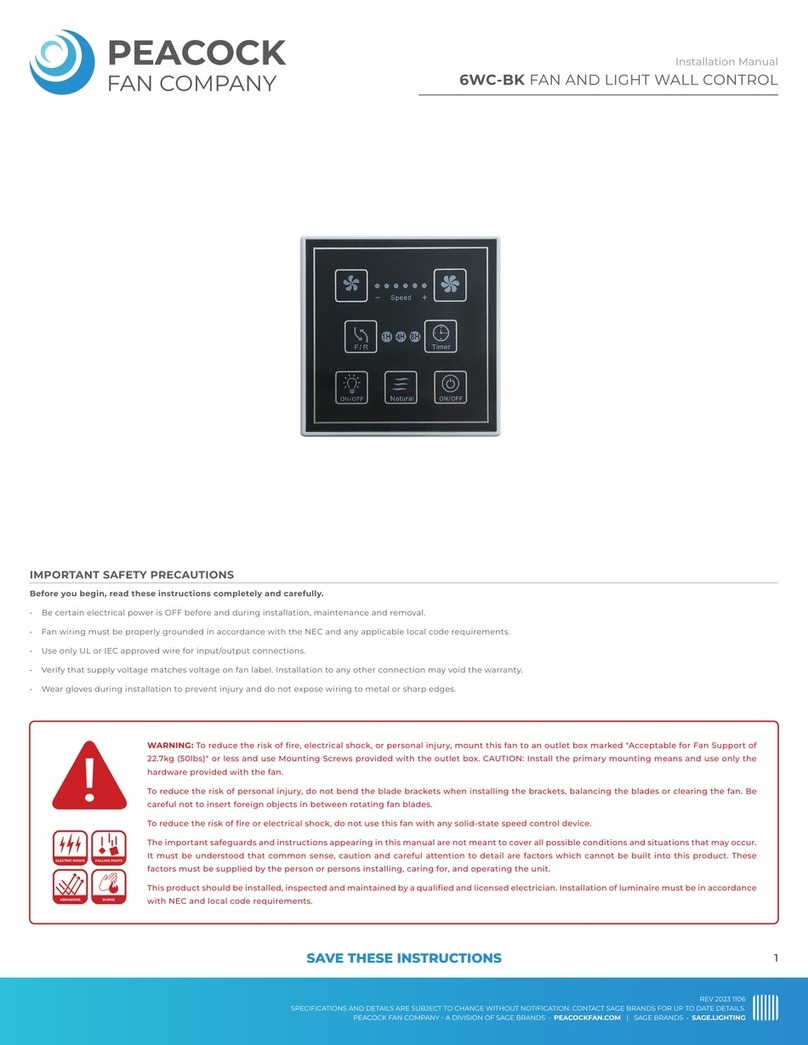
PEACOCK
PEACOCK 6WC-BK installation manual
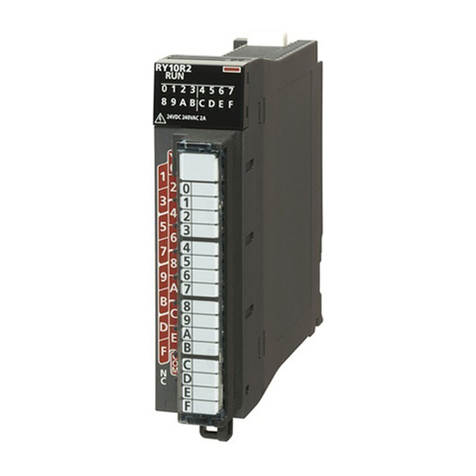
Mitsubishi Electric
Mitsubishi Electric MELSEC iQ-R Series user manual