Smith SPS8 User manual

CUTTERS / REMOVERS / PARTS / SUPPORT
SMITH MANUFACTURING
1-800-653-9311
www.SmithMfg.com
Phone: 954-941-9744 • Fax: 954-545-0348
SPS8™
The Surface Preparator
User Guide & Parts List
SPS8 with Electric Motor

SMITH Manufacturing 1-954-941-9744 www.SmithMfg.com
21/2009
SPS8
INDEX
Page Contents
2 Index
3 Introduction
4 Safety Guidelines
5 Your SPS8™ Surface Preparator
6 Handle Adjustment Instructions
7 Cutter Selection
8 Drum Removal & Cutter Set-Up
9 Machine Start-Up
10 Substrate Removal
11 Troubleshooting
12 Maintenance Check List
13 Storage, Ordering, Warranty Claims
14-15 Cutter Set-Up Diagrams
16-17 Drum Assembly Diagram
18 Drive Shaft & Bearing Assembly
19-20 Frame Assembly
21 Engine & Pulley Assembly
22 Edger Assembly
23-24 Belt Replacement and Alignment
25-26 Optional Electric Motor & Drive Belt Assembly
27 Roto-Peen Assembly
28 Wear Parts Kits
29 Available Options
30 Maintenance Log
31 LimitedEquipmentWarrantyInfo-CerticateofWarranty
32 Warranty Activation

SMITH Manufacturing 1-800-653-9311 www.SmithMfg.com
1/2009 3
SPS8
INTRODUCTION
Congratulations on purchasing the SPS8™ Surface Preparator from SMITH Mfg. Company.
Your machine will:
•Cleansurfacesimpactedbygrease,oil,plastics,tars,resins,tileadhesives,iceandmore
•Planeormillasphaltandconcretesurfaces
•Removehighspotsincurbsandgutters
•Eliminatetrip-hazardsonconcretesidewalks
•Millareasforrumblestrips
•Cleanoutcracksandjoints
•Createanti-slippatternsinwalkwaysandbarns
•Preparesurfacesfornewcoatingapplications
•Permanentlyremoveallroadandsurfacecoatingstoinclude:
epoxy, urethane, thermoplastic, paint, glue-backed tapes and more...
•Groove-inlayasphaltforstriping
BEFORE START-UP, READ THIS...
Please read all operating instructions, including the provided engine manual and be completely
familiar with your equipment before operating. When in doubt, please contact SMITH Manufacturing
or your local dealer for operation details.
ThisOwner’sManualwillguideyouthroughtheremovalprocess,fromstarttonish,andshowyou
how to care for your machine.
UNCRATING YOUR EQUIPMENT
When you uncrate your equipment, make certain that the machine has not been
damaged and that all fasteners and guards are properly tightened.
Your machine may not have been shipped assembled with cutters and other accessories.
Assembly may be required.
Remember:Onlyauthorized,experiencedandproperly
trained personnel should operate this equipment.
Operating personnel should practice safety at all times
and wear protective gear (gloves, goggles, safety vests,
ear plugs, steel-toe shoes, etc.)

SMITH Manufacturing 1-954-941-9744 www.SmithMfg.com
41/2009
SPS8
SAFETY GUIDELINES
Incorrect use of the surface planer can result in
property damage, personal injury, or death.
Be sure to read and follow all directions and
precautions as outlined in this manual.
•Alwayswearprotectiveequipment,includingearprotectionandgoggles.
•Neverwearbaggyorloosettingclothingthatcanbecaughtoncontrolsor
moving parts.
•Thesurfacepreparatorcanemityingparticlesanddebrisduringoperation.
Neveroperatethemachinenearbystanders,animalsorchildren.
•Checkuidlevelsandgetacquaintedwiththecontrols,enginekillswitchand
other safety controls (pg. 5).
•Donotoperatethemachineinanexplosiveatmosphere,nearcombustible
materials, or when gas fumes may not be properly dispersed.
•Repairanyfuelleaksimmediatelyandremoveaccumulateddustfrequently
fromtheairltersystem.
•Neverleavethemachineunattendedwhenrunning,andyoumustholdonto
the handle with two hands when the cutter drum is engaged.
•Avoidcontactwiththemuferwhentheengineishot,asitmaycause
severe burns.
•Whenusingavacuumsystem,avoidhosecontactwiththemufer.
•Ensurethatallguardsareinplacebeforethemachineisoperated,since
rotating and moving parts will cause injury upon contact.
•Makesurethattheengineisshutdownandthesparkplugisdisconnected
before servicing.

SMITH Manufacturing 1-800-653-9311 www.SmithMfg.com
1/2009 5
SPS8
YOUR SPS8™ SURFACE PRREPARATOR
PleasetakeamomenttofamiliarizeyourselfwiththeSPS8™’s
controls, as well as some of the features of your new machine.
For Assembly diagrams and part numbers, please refer to
pages 15-24.
Read the engine manual before preparing the engine for starting.
*Note:SidePlateisnotRemovableonthe
SPS8™, except when upgraded to the
SPS10™ model.
Contact SMITH MFG for more information.
Adjustable Handlebar (optional)
Corded “Engine Kill” Buttton
Fine Adjustment Hand Wheel
Throttle
Spark Plug
Gas Tank
Oil Dipstick
Engine Mount
Belt Adjustment Screws
Handlebar
Adjustment Bolts
Cam Lever
Engine Meter
Cyclone Air Cleaner
Fuel Supply Lever
Choke
Engine Shut Off

SMITH Manufacturing 1-954-941-9744 www.SmithMfg.com
61/2009
SPS8
HANDLE ADJUSTMENT INSTRUCTIONS
The SPS machines may be ordered with optional adjustable handlebars. The handlebars are
equippedwithahigh-densityvibrationsuppressionmaterialtominimizeoperatorfatigueand
increase comfort level when operating equipment.
To adjust the handlebars to a new position for different height operators please follow these steps:
Using a box wrench or socket,
loosen the bolts on both sides
of the handlebars two to three
turns only.
Use a hammer to lightly tap the
end of the bolts to move them
in slightly. (Tapping loosens the
tapered inner plug so they may
be easily re-positioned.)
Stand behind the machine and
set the bars to a comfortable
operating height.
Re-tighten the two bolts to lock
the handlebars in the new posi-
tion.
CAUTION: Neveroperatewithhandlebarsloose.
The bolts must be fastened tightly assuring the handle
is locked into position.

SMITH Manufacturing 1-954-941-9744 www.SmithMfg.com
1/2009 7
SPS8
CUTTER SELECTION
CARBIDE or STEEL?
Whenconguringyourcutterdrumforremoval,oneofthemost
important questions to ask is: “Which cutter type do I use, carbide or steel?”
Tungstencarbidewillproduceasmoothersurfacenishifsetupproperlyand
Carbide also lasts longer. Professionals use carbide cutters to save time and money.
Therearevetypesofcuttersthatyoucanuseonthismachine
(RefertoourCutterDatasheetforspecicsizesandorderinginformation):
1Beam steel cutters for
gentle scarifying.
HS1000™
2Star steel cutters for light
to medium scarifying.
HS1008™
3 3MBrandRoto-peenshotapsasan
alternative to steel shot blasting
25022
4Tungsten carbide spiked cutters to remove
coatings, as well as clean, plane, mill, scarify,
CF2616™ CF2618™ roughen, smooth, groove, grind, eradicate or
remove on concrete or asphalt.
CF2516™ CF2515™
5Special carbide scrapers designed for
asphalt- removing preform tapes,
thermoplastics,orthicklmcoatings.
CM2535™ CM2150™
NOTE: Only SMITH Brand Ultra-Premium Tungsten carbide is the
most cost-effective cutting tool and lasts up to 25x longer than
conventional cutters while removing 5x faster on asphalt or concrete.

SPS8
SMITH Manufacturing 1-800-653-9311 www.SmithMfg.com
81/2009
Warning: When tilting the machine, always tilt forward.
Tiltingthemachinebackwardsatanytimewilloodthesparkplug
with oil and may cause damage to your engine! (Read pg. 8)
RIGHT WRONG
DRUM REMOVAL
With a socket wrench,
remove the two,
Left-Handed hex nuts
(located behind the
belt guard).
Tilt the machine forward
only to prevent the engine
cylinders from being
oodedwithoil.
Slide out the drive shaft
and take the drum to a work-
bench for cutter loading.
CUTTER SET-UP
Remove one retaining plate (ILL# 2, pg. 15, or ILL# 3, pg. 16) and load the cutters and spacers on
each shaft using the cutter charts (pg. 13-14) as a guide.
Make certain that the drum is balanced. An unbalanced drum is unsafe and may cause excessive
vibration, damage bearings, break shafts and reduce cutter life.
After loading the cutters, re-fasten the retaining ring and load the drum onto the machine. Lube the
driveshaftandpositionthecutterdrumrmlyonthedriverstudswhileslidingthedrumshaftcarefully
back into position. Fasten the two Left-Handed nuts securely.
TIP:Loadcutterswithoutspacersforasmoothnish.
Offset or align carbide-spiked cutters for grooving, surface leveling,
or removing. And ALWAYS load the special milling cutters in the
samedirection,withthecarbideedgecuttingrst,andspacedwith
at least one spacer (see page 13 for details). There should be
1/8” - 1/4” play on each section of cutter shaft.
Left-HandedHexNuts
(P/N:65039)
Driver Studs
Drum Axle Shaft
(P/N:65037)
(P/N:65050)
(P/N:65050
side view)
Position Driver Studs
in these holes

SMITH Manufacturing 1-954-941-9744 www.SmithMfg.com
1/2009 9
MACHINE START-UP
Do not start machine while drum is in contact with
the ground. Doing so can cause the operator to lose control of
the machine, resulting in property damage and/or personal injury.
NOTE: Do not attempt to raise or lower the cam lever by force. If it does not move
effortlessly, raise or lower the hand wheel until the cam lever can be adjusted.
Open the fuel cock on the gas tank and then place the throttle lever at the “Fast Idle” position.
Starttheengine,openchokeslightlytopreventooding.Movethrottlecontroltoopenorrun
position when engine is warmed up. Increase throttle to maximum operating position (approx.
2800RPM) and close choke. Before substrate removal, test run the drum with cutters not
touching the surface. If there is excessive vibration, you need to re-balance the cutter set-up,
check bearing condition, and/or make sure that the drive shaft is secured.
Corded “Engine Kill” Button:
In the event of a malfunction or an accident (such as
the machine operator falling or losing footing), the
SPS8 is equipped with a corded “Engine Kill” Button.
Attach the end of the cord to the operator’s belt or wrist,
and snap the clip into place on the stop switch by raising
the top of the Engine Kill Button and inserting the clip
into the gap. If the operator becomes distanced too far
from the machine, the cord will detach from the stop
switch, and the machine will stop running.
*NOTE: the Engine will not start without the Corded Engine Kill’s clip securely in place.
CAUTION: The machine will still move with the engine off.
IF THE ENGINE DOES NOT START...
1) Check Engine for proper gas and oil levels (refer to Engine manual)
2) Check spark plug. Make sure the socket areas are clean and clear of debris, and that the
proper gap is set. (Replace if needed).
3) Check Brown Electrical clip hanging on the front of the engine and ensure that the electrical
wires are making contact within the clip.
4) Turn the On/Off switch, on the front of the Engine, to “On”.
5) Check Corded Safety Stop Connections:
a) Make sure the Corded Safety Stop “C” Connector is dipped properly.
b) Try switching the connection to the opposite post (From letter “C” to letter “M”,
for example).
6) Engine may have tilted backwards. If so, allow oil to drain after removing spark plug.
*Engine repair and engine warranty issues are handled directly by
your local Honda engine service center.
Corded Safety Stop
(stops engine only)
SPS8

SPS8
SMITH Manufacturing 1-800-653-9311 www.SmithMfg.com
10 1/2009
SUBSTRATE REMOVAL
Adjust the height of the cutter drum with the Hand Wheel and Cam Lever. (Turn the hand wheel to
raise the cutter drum off of the substrate. Lower or raise the cam lever to engage or disengage the
drum after setting the proper cutter depth.)
Set the deoth of cut to allow the cutters to go through only the materials to be removed. Make certain
that the drum is positioned to where only the cutters strike the surface, and that the drum assembly
never comes into contact with the substrate. The cutter tips alone should strike the surface (1/8”
to 1/4” maximum depth per removal pass on new cutters).
The drum will not withstand substrate contact. Contacting the removal surface too deeply will
cause premature wear to cutters, shafts, drum and other components!
Too much downward pressure only has negative results. Try to remove materials in several passes
rather than one, deep pass. Several tests will show the best, most appropriate cutter impact. Use a
forward,backwardand/orcircularpatterntoachieveyourdesirednish.
NOTE: Only use a forward motion when using the CM2150™ or CM2535™ carbide milling cutters.
TIP: Positioning the machine over the surface in many direrctions,
as well as dialing the hand wheel up or down can help create
desirable surface patterns. After several hours of practice, the
operator will become comfortable and should be able to remove
materials faster with enhanced results.
Whenthejobiscompleted,ortheoperatorwantstoceasework,stoptheenginebyrstliftingthe
drum above the substrate using the hand-wheel and/or the cam lever. Stop the machine only at the
engine. Then close the fuel cock to shut off the fuel supply.
The drum assembly must be removed daily and inspected for drum wear, hole elongation and pos-
sible weld separation. Replace the cutter shafts and drum bushings every 40 hours, or prior to any
drum wear (65050 Drum only). If the drum’s center holes are elongated, replace only with a SMITH
cutter drum.
Refer to pg. 10 for troubleshooting problems.

SMITH Manufacturing 1-954-941-9744 www.SmithMfg.com
1/2009 11
TROUBLESHOOTING
If engine does not start, read pg. 8
Problem Possible Reason(s)/Solution(s)
Cutters wearing unevenly/prematurely 1Drum is too low, 2Incorrect set-up,
3Material build-up,
4Cutters too tightly loaded, and/or
5Wrong cutters for the job.
Cutter shaft breakage prematurely 1Drum too low, 2End plates or bushings worn,
3Shafts worn, 4Wrong cutter set-up and/or
5Over 40 hours service-life.
Drum wearing prematurely or cracking 1Drum hitting ground, and/or
2Shafts and bushings not replaced within 40 hours.
Excess vibration 1Bearing worn or 2grease not getting into bearing.
- Line up grease hole
-Cleangreasetting
- Check Seals
- or Replace Bearing
Hex bushing worn, drive shaft worn, improper cutter
set-up, drum contacting ground, or wheels worn out.
Machine jumps erratically 1Drum hitting ground, 2RPM is too low,
and/or 3Surface is severely uneven.
“V” belt wear prematurely 1Pulley is misaligned, 2Wrong belt,
and/or 3Drum is contacting surface.
Cam lever will not raise/lower Raise or lower Hand-Wheel.
Hand-Wheel won’t turn Clean and grease threads, linkage may be bent, or
hand-wheel out of position.
Uneven Cutting Cutting too deeply, or rear wheel fork is bent.
AdjustableHandlebarisLoose InserttheatheadofascrewdriverbetweentheBolt
(Refer to pg. 5 diagrram) and Washer then tighten bolt with a 9/16” wrench
washer. Always keep tight!
For any other problems or questions, please contact your local representative
or SMITH Mfg today at 800-653-9311 or (954) 941-9744.
*Engine repair and engine warranty issues are handled
directly by your local engine service center.
SPS8

SPS8
SMITH Manufacturing 1-800-653-9311 www.SmithMfg.com
12 1/2009
MAINTENANCE CHECK LIST
Note: Make sure the ignition is in the OFF position, and
the spark plug is disconnected before servicing.
•Maintainproperengineoilandcrankcaselevels.
Change every 25-50 hours.
•Cleansparkplugsregularly,andsetthepropergap.
•Washtheaircleanerelementinanonoil-basedsolvent,thensqueezeoutresidue.
Allowltertodrybeforereinstallingincleaner.
•Keepacoatingofgreaseonthedriveshaftandthreadsforeasyinstallationorremoval,
and for longer hex bushing life.
•Greasethetwodriveshaftbearingsevery4hours.
Grease should be added slowly while the shaft is hand rotated, until a slight bead
of grease forms at the seals. Use a lithium-based, high temperature grease
(LubriLabS-350)intoeachcleanedgreasetting.DONOTOVERFILL.
Note: After machine serial number 11511 DO NOT GREASE BEARINGS.
Lifetimelubricationinstalled.Nogreasettingrequired.
•Greasethetiltlever,lowerlinkage.
(Cleandirtoffofttingsbeforegreasing.)
•Checkallfastenersandre-tighten,sincethemachinewillvibratethefastenerslooseifthey
are not secured.
•Checkthetwo“V”beltsforwear,andadjust(tighten),orreplaceasrequired.Toreplacebelts,
check for tightness:
1) Loosen the four engine bolts (ILL# 5, pg. 20) and slide the engine back.
2) Loosen the two side cap screws (ILL# 56, pg. 18), letting Engine mount slide down.
3) Adjust or replace belts as needed, making sure they are aligned properly.
4) Slide engine forward and re-tighten bolts.
5) Place one foot on the Main Frame while lifting up on the engine mount to re-tighten
Cap Screws, making sure the belts are stretched and tight.
•Checkthatthepulleysarealignedproperlytoensurethe“V”beltisrunningtrue.
•Checkwheelforwearandthattheyarerotatingproperly,replaceifworn.Cleanwheelsof
material build-up.
•Theinsidehousingmustbeclean,andremoveanybuild-upfrominsidethecagesocutters
and drum rotate freely.
•Inspectandchangedrumbushingsandshaftsevery40hours,orwhenworn(65050Drumonly).

SMITH Manufacturing 1-954-941-9744 www.SmithMfg.com
1/2009 13
STORAGE
Shut off fuel valve and siphon all excess fuel. Start engine and run until it stalls.
Remove spark plug and pour two ounces of motor oil into cylinder and slowly
crank the engine by hand to distribute oil to prevent rust during storage.
Replace spark plug and store machine upright in a cool, dry, and well-ventilated area.
ORDERING
To ensure product safety and reliability, and to maintain your
warranty, always use genuine replacement cutters and parts
from SMITH when making repairs to equipment.
When oredering please specify the model and serial number of the machine.
In addition, give a part number, description, and quantity as listed on your parts list.
If you have any questions about the operation of your machine or would like to order
replacement parts, contact your SMITH Manufacturing representative directly.
Contact 1-800-653-9311 (954) 941-9744) for information.
Visit our website at www.smithmfg.com.
WARRANTY CLAIMS
The manufacturer reserves the right to change or improve the machine design without
assuming any obligation to update any products previously manufactured before this
manual. It is the customer’s responibility to complete the warranty card and mail it to
the seller within 10 days from date of purchase. If a failure occurs during the warranty
period, the customer must contact the seller to determine the appropriate action.
Any and all transportation charges are to be borne by the purchaser.
SPS8

SPS8
SMITH Manufacturing 1-800-653-9311 www.SmithMfg.com
14 1/2009
SPECIAL TUNGSTEN CARBIDE MILLING SCRAPER
CM2535™ CM2150™
CUTTER SET-UP
(Note:QuntityofScrapersmayvary).
Bushed Drum
P/N:65050
Flip Charts upside-down for set-up of other three shafts.
Drum
P/N:65051
MILLING SCRAPER USE INSTRUCTIONS:
Milling scrapers (CM2150™) are not made for cutting into portland cement surfaces. They are made
forremovingmaterialsinoronsoftasphaltorremovingthicklmcoatingsontopofsmoothconcrete
surfaces only. If you need to cut concrete, please use SMITH’s Ultra-Premium tungsten carbide spike
cutters (CF2616™ and CF2618™). Make certain the special milling scrapers re loaded on the drum
intheproperdirection,wherebytheleadingcarbideedgewillcutrst.Loadingthescrapersback-
wards will damage the cutters and the drum.
USE A FORWARD DIRECTION ONLY.

SMITH Manufacturing 1-954-941-9744 www.SmithMfg.com
1/2009 15
CARBIDE FLAIL CUTTER SET-UP
Note:Thefollowingdiagramsareintendedtoguideyoutroughgeneralcutterset-ups.
QuantitiesofCuttersandSpacersmayvary,dependingonthenishyoudesire. CF2616™ CF2618™
Placingmorecuttersoneachshaftwillprovideasmoothernish.Addingspacerswill
giveamorecoarsenish.Aligningthecutterswillcreateagroovepattern.
CF2516™ CF2515™
GROOVEFINISH GENERALFINISH
Align Cutters and Spacers 90 CUTTERS (approx.)
2 Spacers per Cutter
FINEFINISH SUPER-FINEFINISH
114 CUTTERS (approx.) 160 CUTTERS (approx.)
1 Spacer per Cutter 0 Spacers
Flip charts upside-down for set-up of other side of drum.
STEEL CUTTER SET-UP
SUPER-FINEFINISH 456SteelCutters
(Note:QuantityofCuttersmayvary)
HS1008™ HS1000™
Bushed Drum Drum
P/N:65050 P/N:65051
Offset with
spacers to
prevent
grooving.
Drum
P/N:65051
Bushed Drum
P/N:65050
SPS8

SPS8
SMITH Manufacturing 1-800-653-9311 www.SmithMfg.com
16 1/2009
3/4” Shafted
DELUXE BUSHED DRUM ASSEMBLY
ILL# Part No. Oty. Description
1 65050.75 1 Drum Assembly (includes #2- #6)
2 65052.75 1 Kit (Set of 6 Shafts, 12 Bushings)
3 1065054 2 Retaining Plate
4 1010801.1 6 Lock Washer, 5/16
5 1010053 6 Flat Socket Head Cap Screw, 5/16 x 18 x 3/4
6 1010213 6 Washer, 10mm
7 S-20150.75 6 Cutter Shaft, 3/4”
8 SP2233 § Spacer, 3/4”
9 HS1001™ § Steel Beam Cutter
CF2128™ § 8 Spike Tungsten Carbide Cutter (large)*
CM2550™ § 100% Carbide Scraping Cutter (large)*
10 1065055.75 12 Drum Bushing (.75” diameter)
§ Refer to cutter set up on pages 14-15
*Forusewith5”RearWheels(P/N:52002)only.

SMITH Manufacturing 1-954-941-9744 www.SmithMfg.com
1/2009 17
DELUXE BUSHED DRUM ASSEMBLY
(P/N: 65050-D)
CF2618™
ILL# P/N Oty. Description
1 65050-D 1 Drum Assembly (includes #2 - #6)
2 65052 1 Kit (Set of 6 Shafts, 12 Bushings)
3 65054A 2 Retaining Plate (incl. #4 - #6)
4 10801 6 Lock Washer, 5/16
5 110053 6 Cap Screw, 5/16 x 18 x 3/4
6 110213 6 Washer, 5/16
7 S-20150.4 6 Cutter Shaft, 1/2”
8 12230 $ Spacer, 1/2”
9 HS1000™ $ Steel Beam Cutter
HS1008™ $ Steel Star Cutter
CF2516™ $ 6 Spike Tungsten Carbide Cutter
CF2535™ $ 5 Edge Carbide Scraping Cutter
CF2616™ $ 6 Spike Tungsten Carbide Cutter (large)*
CF2618™ $ 8 Spike Tungsten Carbide Cutter (large)*
CF2150™ $ 6 Edge Carbide Scraping Cutter (large)*
10 65055 12 Drum Bushing (.75” OD)
11 65049 1 Bushing Removal Punch
$ Refer to cutter set up on pages 14-15
*Forusewith5”RearWheels(P/N:52002)only.
SPS8

SPS8
SMITH Manufacturing 1-800-653-9311 www.SmithMfg.com
18 1/2009
SHAFT & BEARING ASSEMBLY
ILL# P/N Oty. Description
1 65037A 1 Drum/Hub Shaft Assembly (ILL #14 included)
2 65031 2 Retainer Bearing
3 10808 1 Grease Fitting, Straight
4 10961 1 Grease Fitting, Elbow
5 10022 4 Hex Bolt, 3/8-24 x 1 1/2 (on machines w/ Removable Sideplate)
6 1010021 4 Cap Screw, 3/8-24 x 1 1/4 (on machines w/out Removable Sideplate)
1010022 4 Cap Screw, 3/8-24 x 1 1/2
7 10811 8 Lock Washer
8 65030 2 Bearing & Snap Ring (*optional non greasing Bearing - 65030-SM)
9 65033 1 Hex Bushing
10 65038 1 Shaft Driver
11 10113 3 Spacer (9/16 x 3/8 x 7/32)
12 10859 3 Cap Screw, 3/8-24 x 1”
13 10873 1 Retainig Ring, 1-1/4
14 65039 2 JamNut,LH
15 65038.A 1 Shaft Driver Assembly (incl. ILL #10, 11 & 12)
16 65031.A 1 Bearing Retainer Assembly, Pulley Side (incl. ILL #2, 4 & 8)
17 65033.A 1 Hex Bearing Assembly (ILL #8 & 9)
18 1065033A 1 Hex Bearing Assembly, outside (incl. ILL #2, 3, 8 & 9)
19 1065033/31A 1 Set of 2 (#17 + #18) Hex Drive Bearings (*optional non greasing Assemblies)
(replaces ILL. # 8 - 9)
Hex Bearing Assembly
*
19*

SMITH Manufacturing 1-954-941-9744 www.SmithMfg.com
1/2009 19
FRAME ASSEMBLY
SPS8

SPS8
SMITH Manufacturing 1-800-653-9311 www.SmithMfg.com
20 1/2009
ILL# P/N Oty. Description
1 65012 1 Adj. Handlebar Extension (opt.)
2 65013 2 ScrewAssem.(incl.inP/N:65012)
3 14023 1 Ball Knob
4 10608 2 Hand Grip
5 1050010 1 Corded Engine Kill Button
6 68055 1 Engine Meter (opt.)
7 10127 1 Drive Screw
8 10808 2 Grease Fitting, Straight
9 65009 1 Handle Bar Assembly w/ Cam Lever
9A 1065009.50A 1 Handle Bar Assembly (incl. ILL# 1, 9B,9C)
9B 1065009.50 1 Handle Bar less Cam Lever Assembly
9C 1010608 1 Foam Grips (set of 2)
9D 65009.25 1 Cam Lever
9E 65009.25A 1 Cam Lever Assembly (incl. ILL# 3, 8, 9D)
10 10816 4 Cap Screw, 3/8-16 x 1
11 80007 1 Decal
12 14023 1 Ball Knob
13 65019 1 Hand-Wheel w/ Acme Rod
14 10346 1 Socket Head, Cap Screw, 1/2-13 x 4-1/2
15 150550 1 Sleeve, brass
16 85005 1 Bearing
17 110073 2 Flat Washer, 5/8
18 79035 3 Rubber Bushing
19 110359 1 Cap Screw, 5/8-11 x 3-1/4
20 65007 1 Upper Linkage
21 110096 1 Locking Collar, 5/8
22 65006 1 Lower Linkage
23 10339 1 Cap Screw, 1/2-20, x 4
24 10205 1 LockNut,1/2-20
25 65004 1 Fork
26 65005 2 Spacer, Wheel
27 52001 2 Wheel, 4” (opt. 5” wheel available)
28 110360 2 Cotter Pin, 3/16 x 1-1/2
29 65015 1 Cap Screw, 1/2-13 x 8
30 10312 1 Flat Washer, 1/2
31 10407 1 LockNut,1/2-13
32 65003 1 Belt Cover
32A 65022.1 1 Hole Plug, Small
32B 65022 1 Hole Plug, Large
33 10422 2 AcornNut,1/2-13
34 10045 2 Lock Washer, 1/2”
35 10312 2 Flat Washer, 1/2”
36 10072 2 Nut,1/2-13
37 65016 2 Tube Spacer
38 65017 2 Cap Screw, 1/2-13 x 5
39 822.25.0 9 NYLock,1/4-20
41 10834 7 Hex Bolt, 1/4-20, 1/2
42 10835 2 Hex Bolt, 1/4-20, 3/4
43 65036 1 Brushes, Set of 4
44 52001 2 Wheel, 4”
45 10428 2 Locking Collar, 3/4
46 65014 1 Axle Shaft
47 10304 2 Cap Screw, 1/2-20 x 1
48 110045 2 Lock Washer, 1/2
49 10312 2 Flat Washer, 1/2
50 65001 1 Main Frame
52 10811 2 Lock Washer, 3/8
53 10025 2 Flat Washer, 3/8
54 65021 1 2” Cap Plug, Vacuum
55 10816 2 Cap Screw, 3/8-16 x 1
56 10802 2 Carriage Bolt, 3/8-16 x 1
57 65002 1 Engine Mount
58 110025 2 Flat Washer, 3/8
59 10004 2 LockNut3/8-24
60 80001 1 Serial Plate
61 10129 2 Drive Screw
Please note that
due to improvements
and changes in the
equipment, the
illustrations shown
may be different than
the actual machine.
FRAME ASSEMBLY
Table of contents
Other Smith Floor Machine manuals
Popular Floor Machine manuals by other brands
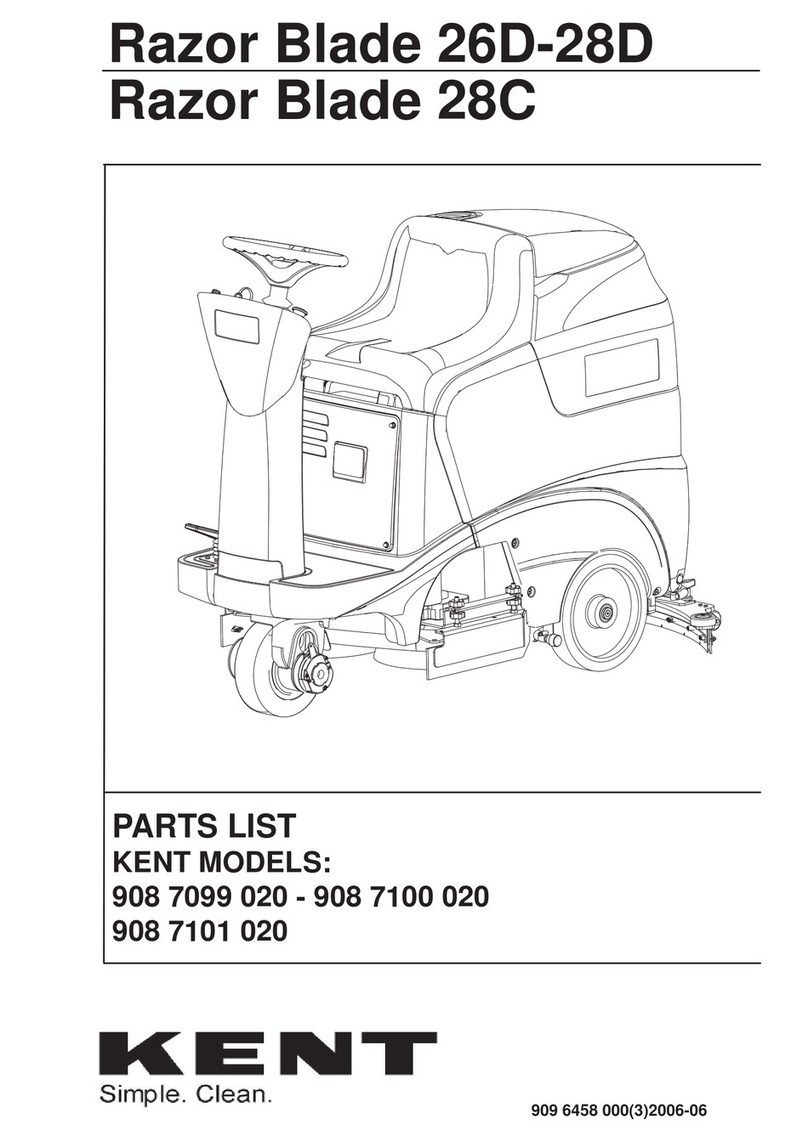
KENT
KENT Razor Blade 26D parts list
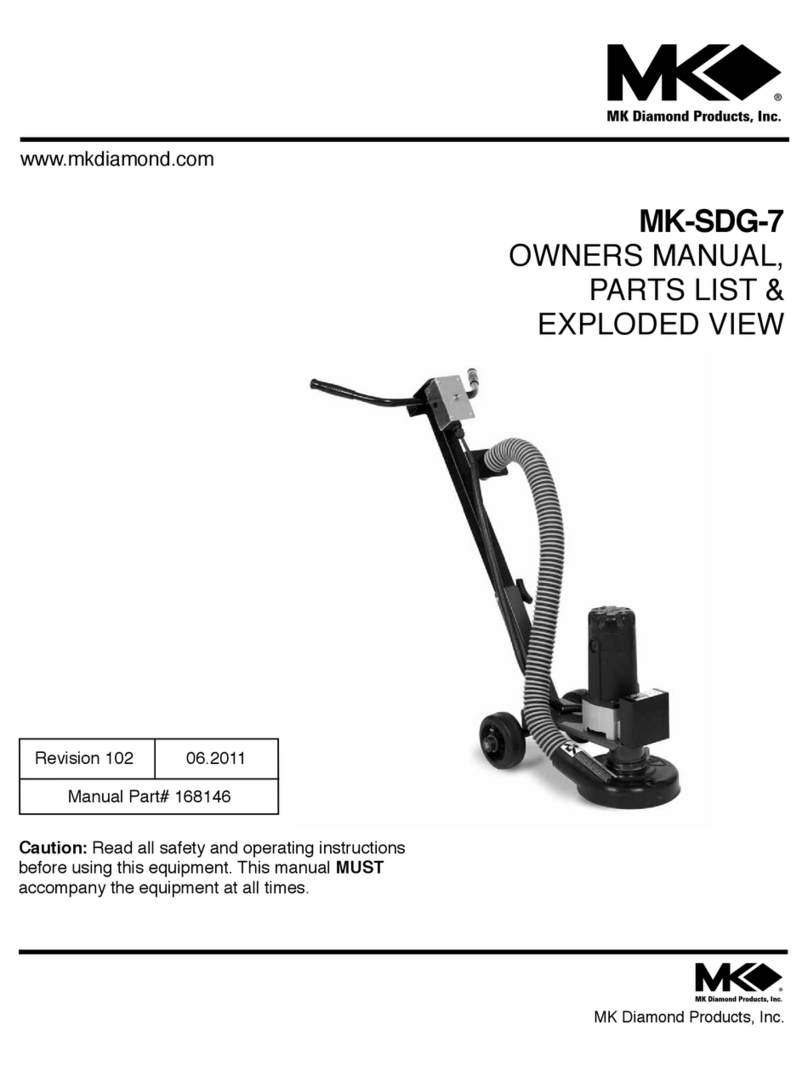
MK Diamond Products
MK Diamond Products MK-SDG-7 OWNERS MANUAL, PARTS LIST & EXPLODED VIEW
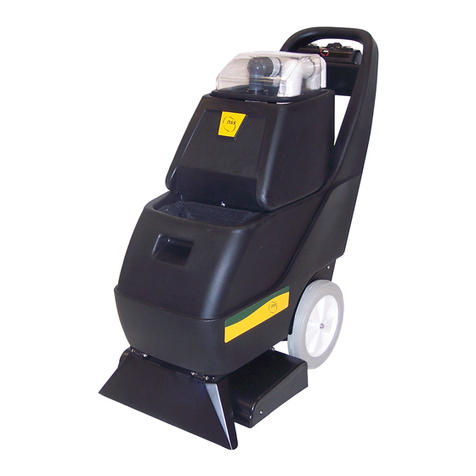
NSS
NSS STALLION 818 SC Operation manual
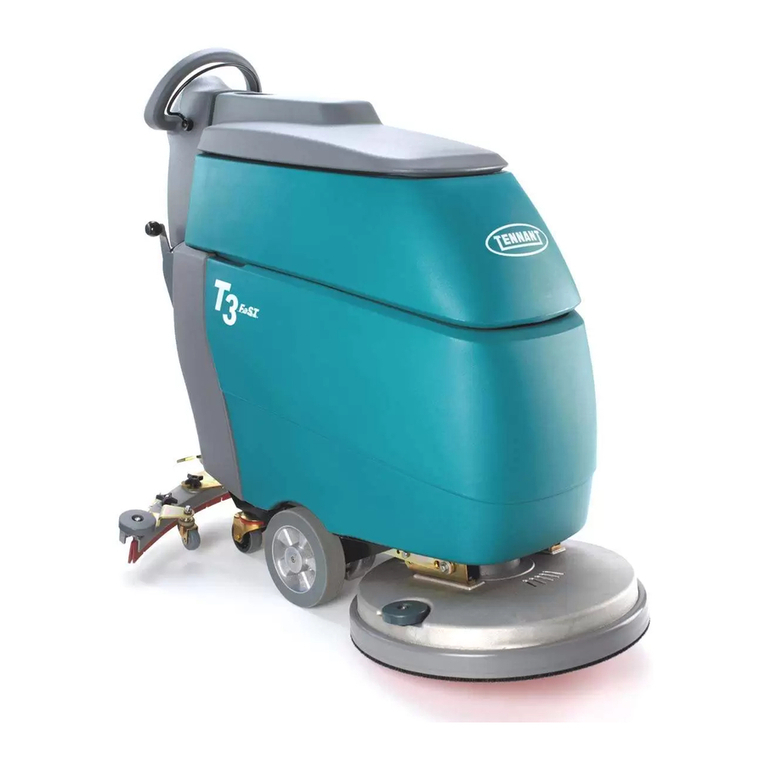
Tennant
Tennant T3 Operator's manual
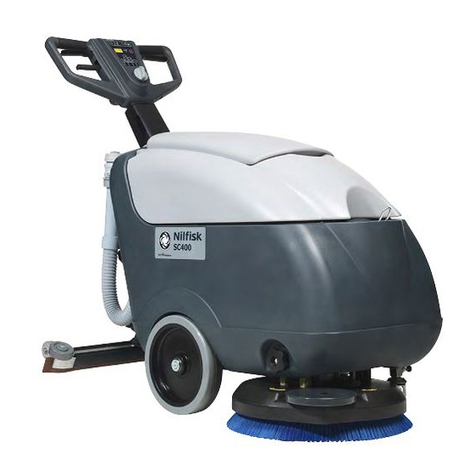
Advance acoustic
Advance acoustic SC400 Instructions for use

Kärcher
Kärcher BD 50/70 R Bp Classic manual
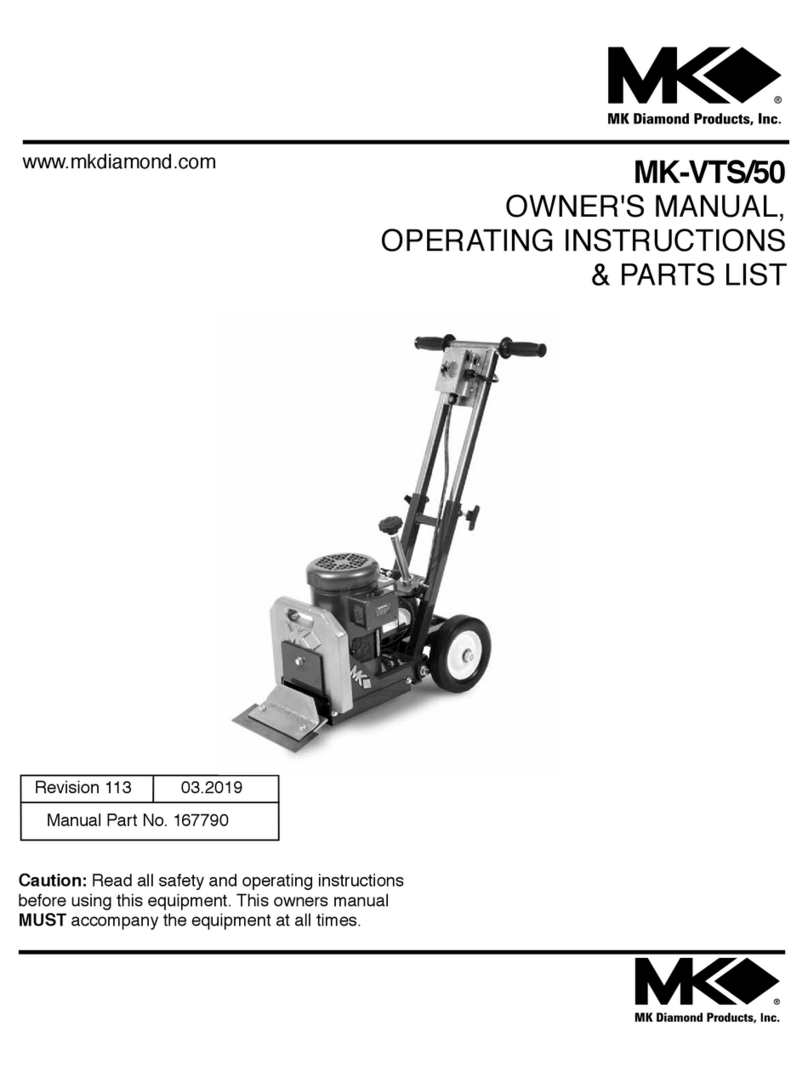
MK Diamond Products
MK Diamond Products MK-VTS/50 Owner's manual operating instruction & parts list
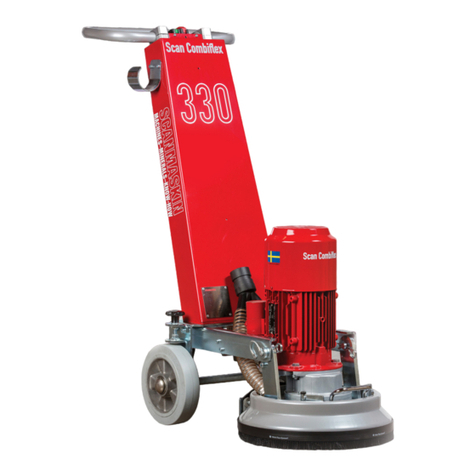
SCANMASKIN
SCANMASKIN Scan Combiflex 330 manual
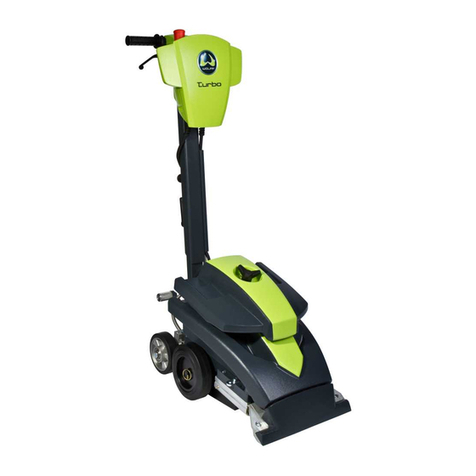
WOLFF
WOLFF TURBO-STRIPPER Translation of the original instruction

Windsor
Windsor D250(115V) 10070100 operating instructions
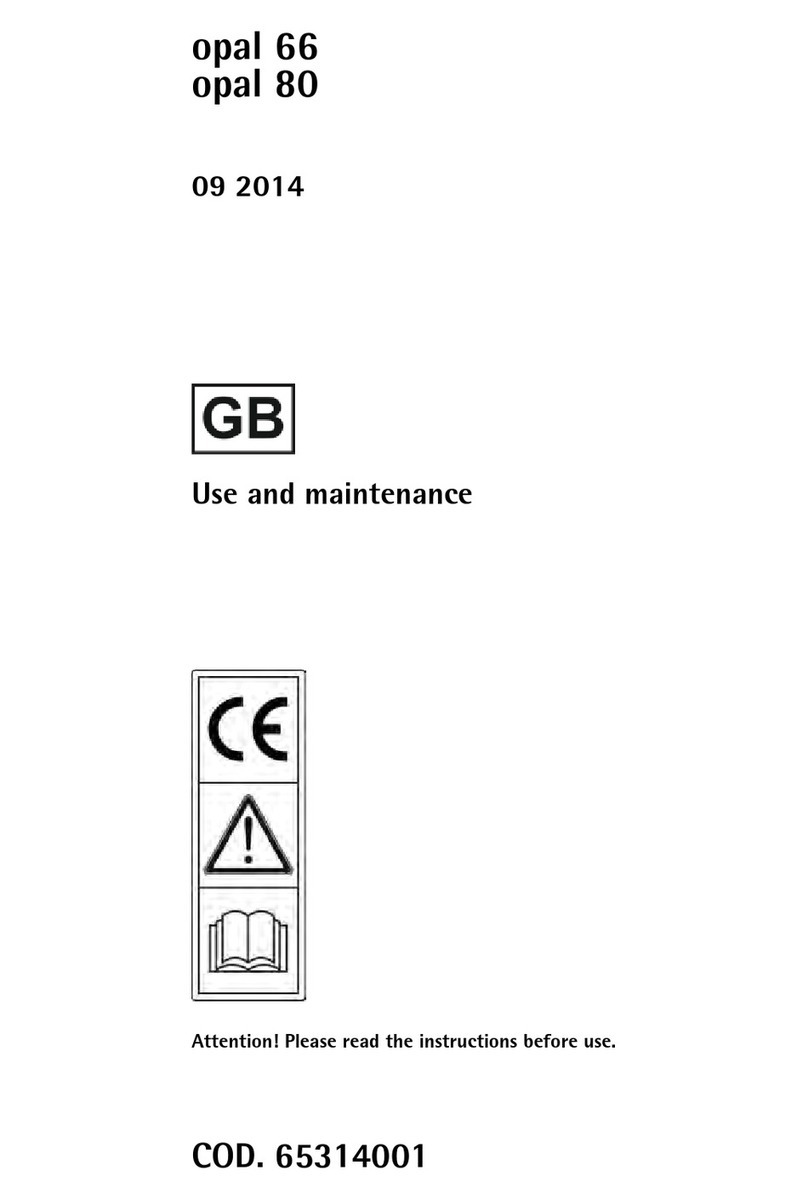
ADIATEK
ADIATEK Opal 66 Use and maintenance
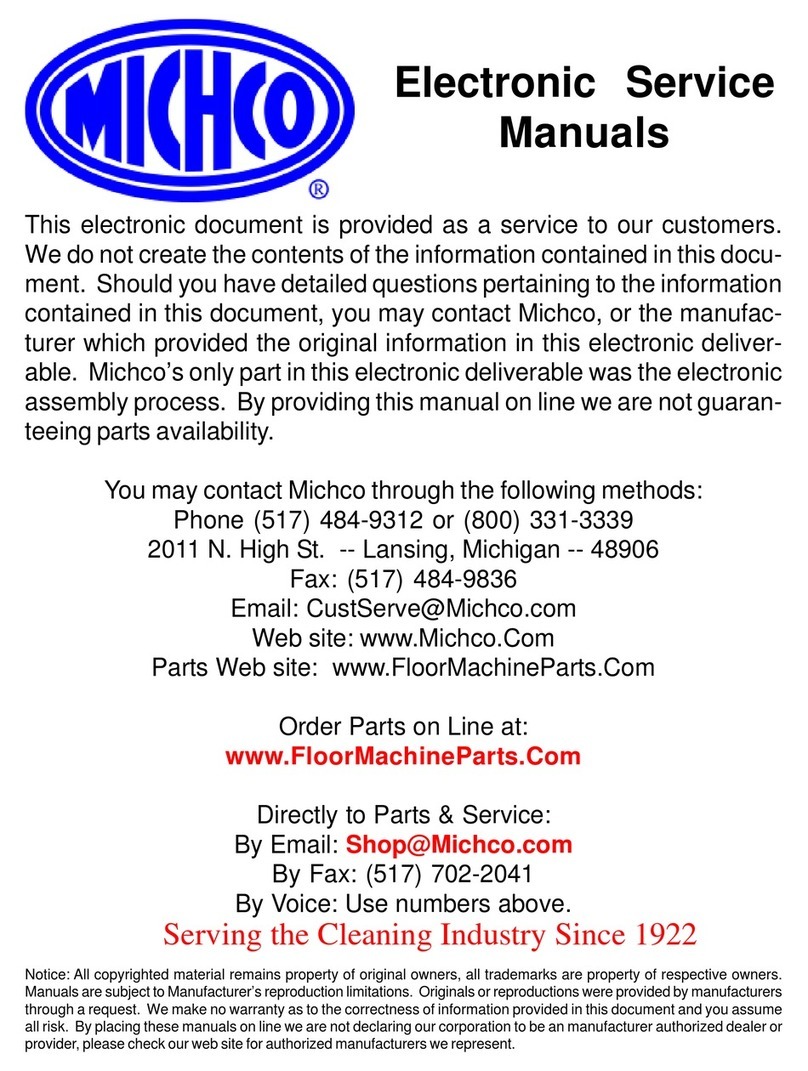
Minuteman
Minuteman C-BOX 100 instruction manual