Specac APEX User manual

APEX Quick Release
Pellet Dies
User Manual
2I-26300-2


APEX Quick Release
Pellet Dies
User Manual
2I-26300-2

User Manual
4
APEX Quick Release Pellet Dies
P/N GS26300 Series
CONTENTS
1.
INTRODUCTION
................................................................................. 5
2.
UNPACKING AND CHECKLIST
.............................................................. 9
3.
SAFETY AND APEX DIE CARE
............................................................ 10
4.
PREPARATION FOR USE OF THE APEX DIE
.......................................... 12
FITTING THE TOP PRESSING ANVIL TO A PRESS LEADSCRE
.............. 12
FITTING OF THE BASE LOCATOR PLATE
............................................. 13
5.
LOADING A SAMPLE IN THE APEX DIE
................................................. 16
FILLING THE APEX DIE ITH A SAMPLE
.............................................. 18
6.
PRESSING TO MAKE THE SAMPLE PELLET
.......................................... 20
7.
REMOVING THE APEX DIE FROM THE PRESS
....................................... 26
8.
DISASSEMBLY FOR THOROUGH CLEANING AND STORAGE OF THE APEX
DIE
................................................................................................. 27
DISASSEMBLY OF THE APEX DIE
....................................................... 27
REASSEMBLY OF THE APEX DIE
........................................................ 30
9.
LEGEND
(
BUBBLE PART NUMBERS
)
FOR THE APEX DIE
........................ 32
10.
SPARE PARTS FOR THE APEX DIE
.................................................... 33
© June 2018 Specac Ltd. All rights reserved.
Brilliant Spectroscopy is a trademark of Specac Ltd.
Other product names mentioned herein may be trademarks
of their respective owners.

APEX Quick Release Pellet Dies
5
1. ntroduction
Thank you for purchasing a Specac product.
The APEX Quick Release Pellet Dies have been specifically designed
to work with the range of Atlas™ Power and Autotouch Presses up to a
maximum load rating of 40 tonnes. The APEX Quick Release Dies are
also compatible for use with Specac’s 15 and 25 tonnes Atlas™
Manual Hydraulic Presses.
The APEX Quick Release Dies have an inner die body made of 440C
hardened stainless steel that is contained within an outer sleeve jacket
mechanism made of anodised aluminum components. The 440C die
body has a Mohs hardness rating of circa 7.5 for the pressing of solid
sample types (powders) into pellets with a similar or lesser hardness
rating. The complete APEX Die assembly is offered in two versions to
prepare solid sample pellets/discs of 40mm or 32mm diameter size.
Both APEX Die sizes are provided complete with a top pressing anvil
assembly and base locater plate for quick and easy use.
The design of the APEX Die for its outer sleeve mechanism allows for
the pellet sample to be automatically presented to the user without
the need to reconstruct the Die from a pellet forming to a pellet
releasing pressing stage during the pressing process.
hen using a conventional, Standard Pellet Die, under a two-stage
pressing process the first stage is to compress a sample powder in the
Standard Die into a sample pellet and the second stage is to release
the sample pellet from the Standard Die body. Between the pressing
stages, the Standard Die must be removed from the Press to
exchange the pressing base with an extractor cap assembly and then
the Standard Die assembly of parts is inverted and placed back into
the Press. The ergonomics for a pressing procedure is greatly
simplified when using the APEX Quick Release Die and the time
required to produce a sample pellet is typically halved when compared
to use of a Standard Die.

User Manual
6
The typical procedure for the steps in use of the APEX Quick Release
Die are as follows:
Step 1 – oad Sample
The APEX Die is set to present
a cavity hollow at the top of the Die
to fill with sample inside the inner die
body. A stainless steel polished plate
is placed to cover over the top of the
die body containing the sample.
The inner die body and outer sleeve
parts are set to their load positions by
pressing the button on the inner sleeve
at the base.
Step 2 – Press Sample
The top pressing bolster anvil
fitted to the leadscrew of the
Press is brought into contact
with the APEX Die assembly and
a load to press is applied.
The sample within the internal
die body is compressed between
the stainless steel polished plate and
internal plunger of the APEX Die.
Step 3 – Sleeve Engages
The compression load is released
and as the top pressing anvil
separates away from the APEX Die,
the three spring tabs flip over to rest
on the top of the die body. The die
body is held in its compressed position
by an internal latching mechanism to
the sleeve assembly.

APEX Quick Release Pellet Dies
7
Step 4 – Press Again
Re-application of a low tonnage
load (up to 4 tonnes), in bringing
the top pressing anvil into contact
with the three spring tab surfaces,
will allow the internal plunger
to start pushing the sample
pellet towards the top of the
APEX Die.
Step 5 – Sample Released
hen the second pressing stage
has completed and the top
pressing anvil is withdrawn away
from the APEX Die, the stainless
steel polished plate and pellet
sample is accessible from the top
of the APEX Die.
Step 6 – Clean and Reset
After removing the sample pellet,
clean the APEX Die components
and reset it to accept a new sample
by pressing the button on the inner
sleeve at the base (As Step 1.)

User Manual
8
A powder sample or sample cup with powder that is placed into the
stainless steel die body of the APEX Die is compressed between the
polished surfaces of an internal plunger and a top stainless steel
polished plate. The top pressing anvil is permanently affixed into the
leadscrew assembly of any Specac Press for use of the APEX Die.
There are two top pressing anvils that are common for use with both
the 40mm and 32mm pellet APEX Dies. One top pressing anvil (P/N
GS26310) is specifically for fitting to the leadscrew assembly of
Specac Autotouch 40T Presses. The other top pressing anvil (P/N
GS26311) is for use with ANY other Specac Press (Manual, Power or
Autotouch variants.)
hen using the APEX Die, it is very important to position the Die
centrally within the pressing sample compartment area of the Press.
To help for a quick and consistent positioning of the APEX Die
centrally in use, a base locator plate is provided with the APEX Die.
This circular locator plate has two dowel pins projecting from its upper
surface and is fitted over the main pressing piston part of a Specac
Press. The APEX Die is simply placed onto the base locator plate and
will be positioned centrally and correctly when the outer sleeve of the
APEX Die engages to touch both dowel pins.
The overall height of both the 32mm and 40mm APEX Dies is 118mm
when the reset button is pressed (Step 1). The maximum amount of a
solid or ground, powdered sample that can be placed into the APEX
die body at the load stage (Step 1), is limited to a depth of 20mm. A
maximum compacted pellet thickness is 7.5mm. hen the APEX Die
is compressed under an applied, steady load (Step 2), the overall
height can be between 92mm to 98mm dependent upon a 1.5 to
7.5mm sample pellet thickness produced within.
The overall outer sleeve diameter of both 32mm and 40mm APEX Dies
is 90mm.
The dimensions and 2.7Kg weight of the APEX Quick Release Dies
are well suited for the preparation of solid pellets/discs for study by X-
Ray Fluorescence (XRF) spectroscopy. Their ease and quickness of
use can assist in the production of a high number of pellet samples per
hour, depending on specific pressing tonnage load cycle regimes.

APEX Quick Release Pellet Dies
9
2. Unpacking and Checklist
Remove the APEX Quick Release Die from its protective packaging.
Please check that the following have been supplied:
A 40mm or 32mm APEX Die complete with associated parts.
To include:
• APEX Die complete assembly.
(As GS26301, GS26302,
GS26303 or GS26304)
• Top stainless steel
polished plate.
(GS26315 or GS26316)
• Top pressing anvil.
(GS26310 or GS26311)
• Base locator plate
(GS26330)
• 3mm A/F Allen key tool.
• 2mm A/F Allen key tool.

User Manual
10
3. Safety and APEX Die Care
Safety
The APEX Quick Release Dies are inherently safe from correct use. It
may be that the sample type to press within the Die could pose the
most risk, so any health and safety instructions pertaining to the
sample type itself in its handling should be observed. However, when
the APEX Die is being used in a Press, any safety precautions
involved with operation of the Press itself must also be observed.
An APEX Quick Release Die must always be placed as centrally as
possible within the pressing area of a Press to provide a correct and
consistent evenness in loading when being compressed. The base
locator plate provided helps for a quick, easy and consistent way of
correctly positioning the APEX Die into a Press.
Warning!
Never exceed the stated maximum safe load of 40 tonnes
when pressing using an APEX Quick Release ie.
Die Care
The APEX Quick Release Die body, plunger, top pressing anvil and
top polished plate parts are made from corrosion resistant stainless
steel (440C), but because of the nature of certain materials that may
be used with the APEX Dies, it is necessary to take certain
precautions. Any sample to press that is harder than stainless steel in
having a Mohs value of higher than 7.5, risks damage to the parts.
Similarly, pressing of very fine particulate samples (smaller than the
minimum tolerance clearance values for the Dies), risks damage to
certain components.

APEX Quick Release Pellet Dies
11
For most pressing operations, the APEX Die can be cleaned quickly
and simply between samples around the top surface area of the die
body (5) and against the surfaces of the pressing parts that have
contacted with the sample. (e.g. surfaces of the top polished plate (12)
and plunger (9)).
The APEX Die parts can usually be cleaned between samples initially
using a soft cloth or tissue paper dampened with warm or cold water
and finally with a soft dry cloth or tissue paper. After washing with
water, a cloth dampened with methanol may also be used to remove
any organic sample residues that may be present and any excess
methanol is wiped away with a soft dry cloth or tissue paper. hen not
in use always ensure that the APEX Die and its component parts are
thoroughly clean and dry, and if possible store the APEX Die in a
desiccator.
Note: When cleaning the APEX ie parts, do not use a cloth that has a
hard, abrasive texture as scratches or imperfection to the
surfaces may result. Always use a soft cloth or tissue.
For a more thorough cleaning of the APEX Die if necessary, it has
been designed such that the internal die body (5), plunger (9) and
spring (8) components can be removed from the outer (6) and inner (7)
sleeve mechanism. Please see how to disassemble the APEX Die for
more thorough cleaning in Section 8, page 27 of this user instruction
manual.

User Manual
12
4.Preparations for Use of the APEX Die
Fitting the Top Pressing Anvil to a Press eadscrew
For use of the APEX Quick Release Die, there is a requirement to fit
the appropriate top pressing anvil (1) part into the leadscrew assembly
of the Press to be used.
Fig 1. Top Pressing Anvil Assembly
Fig 1. shows the top pressing anvil (1) with its securing O-ring (2).
A standard top bolster anvil as fitted to the leadscrew of the Press is
removed and is replaced by the new upper pressing anvil (1) for the
APEX Die. Both anvil types (standard bolster and APEX Die top
pressing anvil) are held into the hollow recess at the tip of the
leadscrew from a compression tight fit of the O-ring (2) on the anvils.
The standard anvil is carefully pulled out of the hollow tip of the
leadscrew and the APEX Die top pressing anvil (1) is pushed back into
place as far as it will go for the O-ring (2) to hold.
Note: For explanation, the top pressing anvil P/N GS26311 is shown
fitted into an Atlas Autotouch 8T Press at Fig 2. (For the Atlas
Autotouch 40T Press only, the top pressing anvil P/N GS26310
is used.)
1 2

APEX Quick Release Pellet Dies
13
Fig 2. Top Pressing Anvil Fitted into the eadscrew of the
Autotouch (8T) Press
Fitting of the Base ocator Plate into the Press
hen the top pressing anvil (1) has been fitted, the base locator plate
(3) is placed into the Press to cover the lower pressing piston surface
(4). Fig 3. shows both the top and underside surfaces of the base
locator plate (3).
1
4

User Manual
14
Fig 3. Base ocator Plate – Top ( eft) and Underside (Right) Views
The circular recess on the underside surface of the base locator plate
(3) allows for this part to simply fit over the main piston pressing
surface of the Press for its correct and centralised positioning. (See
Fig 4.)
Fig 4. Base ocator Plate Fitted over the Piston Pressing
Surface of the Autotouch (8T) Press
3
3
1

APEX Quick Release Pellet Dies
15
The two dowel location pins on the top surface of the base locator
plate (3) are used to centralise the APEX Die when it is placed into the
Press. The APEX Die is positioned such the outer sleeve diameter of
the APEX Die touches both dowel pins. (See Fig 5.)
Fig 5. QR Die installed between Top Pressing Anvil and Base
ocator Plate as fitted in the Autotouch (8T) Press
ith both the top pressing anvil (1) fitted and base locator plate (3)
positioned in the Press, the APEX Die can now be used.
3
1

User Manual
16
5. Loading a Sample in the APEX Die
The APEX Die can accept a powder or appropriate diameter sample
cup filled with powder once it has been initially set in its load sample
position. (See Apex Die Tips page 22.)
Fig 6. APEX Die Set for Sample oading
Fig 6. shows the APEX Die complete assembly when set in its load
position for filling with a sample. The inner die body (5) sits within the
outer sleeve assembly (6) and is free to slide past the outer sleeve (6)
during any compression event. The outer sleeve assembly (6) is in turn
free to slide past the inner sleeve (7) assembly during any
compression event cycle.
7
6
11
10
10
5 10
9

APEX Quick Release Pellet Dies
17
The die body (5) is supported by an internal spring (8) (not shown) that
is in turn connected to the plunger (9). During a compression event
from application of a load to the APEX Die, the die body (5) is forced
downwards to compress the spring (8) and the plunger (9) pressing
face travels in an upwards direction within the bore of the die body.
The sample itself is compressed between the faces of the top pressing
anvil (1) or top polished plate (12) and the plunger (9) as contained
within the bore of the die body (5).
Note: The tolerance of fit is 10 microns minimum and 30 microns
maximum between the outer circumference surface of the
plunger (9) and walls of the ie body (5) inner cylinder surface.
On the outer sleeve assembly (6) there are three hinged tab pieces
(10) that rest against the outer circumference of the die body (5). In the
load position they rest as seen in Fig 4. against the die body, but after
a sample has been compressed in the APEX Die and with release of
the applied load from the Press to the APEX Die assembly, the hinged
tab pieces (10) automatically engage to flip over to form a new
pressing surface level at the top of the APEX Die. (See Step 3, page
6). It is this automatic deployment of the tab pieces (10) to their flipped
over position that allows for an immediate second pressing stage to be
applied to the APEX Die assembly to gain quick and easy access to
the sample pellet that has been pressed.
On the inner sleeve assembly (7) there is a button (11). Depression of
this button releases any compression that has been applied to the
spring (8) which is held under compression by an internal ratchet
locking mechanism for the die body (5).
Note: Pressing of the button (11) resets the APEX ie to its start set
position but not or its sample load latched position seen as
at Fig 6. The load latched position must be set to ill the Die.
Warning!
Keep hands/fingers away from the three hinged tabs (10)
when the reset button (11) is pressed. Hold the APEX Die
towards the bottom of the outer sleeve (6) with one hand,
whilst pressing the reset button (11).

User Manual
18
Filling the APEX Die with a Sample
Having pressed the button (11) to reset the APEX Die, push down on
the die body (5) to hold for its first latching position against the outer
sleeve assembly (6) before filling with a sample. (See APEX Die Tips
page 22.) A solid powder sample can be transferred for filling the die
body (5) using a spatula or by making a paper chute or funnel.
Note: If filling the die body (5) to a depth of circa 10mm with a powder
sample to compress, a circa 8ml volume of sample is used with
the 32mm ie and circa 12.5ml of sample with the 40mm ie.
For a mass of sample, Specac suggest typically 4 to 5 grams for
the 32mm size and 6 to 8 grams for the 40mm size ie is used.
If using an aluminium or plastic support cup with a solid sample,
ensure that an empty support cup is first placed into the die body (5)
and pushed towards the surface of the plunger (9) within the die body.
Note: If using a support cup, the amount of solid sample powder that
you should place into the die body (5) should be sufficient to
cover over the support cup completely but to no more than the
20mm uncompacted sample depth limit for the die body.
hen all the sample powder to be compressed has been placed into
the die body (5), use the tip of a spatula to spread the powder such
that it has a flat, evenly distributed surface. Preparation of the
uncompacted powder surface helps to produce a more homogenously
compressed sample pellet. An uncompacted powder sample depth
limit is up to 20mm maximum within the die body (5), with use of the
top polished plate (12).
Important! Before any pressing is to take place ensure the top surface
level area of the ie Body (5) is clean and free of sample.
Any sample residues above the maximum sample depth
limit within the bore of the ie Body or that spill over
around the top edge, may impede the top polished plate
(12) for contact and fit and compromise for a correct
pressing of the sample within the ie Body (5) itself.

APEX Quick Release Pellet Dies
19
hen the die body (5) is filled correctly with a sample, the top polished
plate (12) is correctly positioned over the top of the Die Body (5). (See
Fig 8.)
The Top Polished Plate
The top polished plate (12) is provided with an appropriate 32mm or
40mm diameter pressing surface to match the size of APEX Die being
used.
Upper Surface Underside Surface
Fig 7. Top Stainless Steel Polished Plate
Only one surface of the plate (12) is polished and this sur ace must
be in contact with the sample to be pressed. Fig 7. shows the top
polished plate (12) for its upper and underside surfaces. The
underside surface is polished and is the matching diameter of 32mm
or 40mm to fit inside the die body (5).
Fig 8. Top Polished Plate fitted over APEX Die Body
ith the top polished plate (12) fitted, the APEX Die can be installed
into a Press. (See Fig 9.)
12
12 5

User Manual
20
6. Pressing to Make the Sample Pellet
Place the prepared APEX Die with sample in its upright position
carefully into a Press fitted with a top pressing anvil (1) and lower base
locator plate (3).
Fig 9. APEX Die with Sample as Fitted into a Press
(Autotouch (8T) Press shown as example)
Table of contents
Popular Tools manuals by other brands
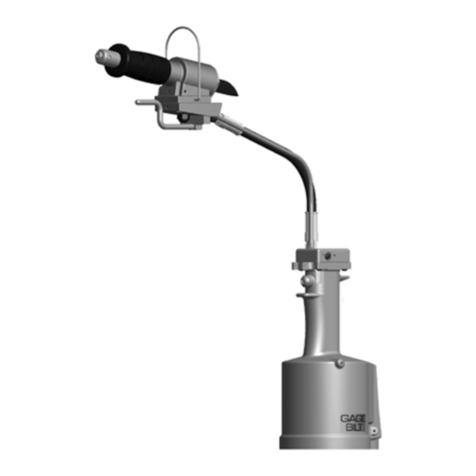
Gage Bilt
Gage Bilt GB743SRVT Installation Tool Information

Textron
Textron Cessna 182S Wiring Diagram Manual

BorMann
BorMann HOME BDA1500 owner's manual
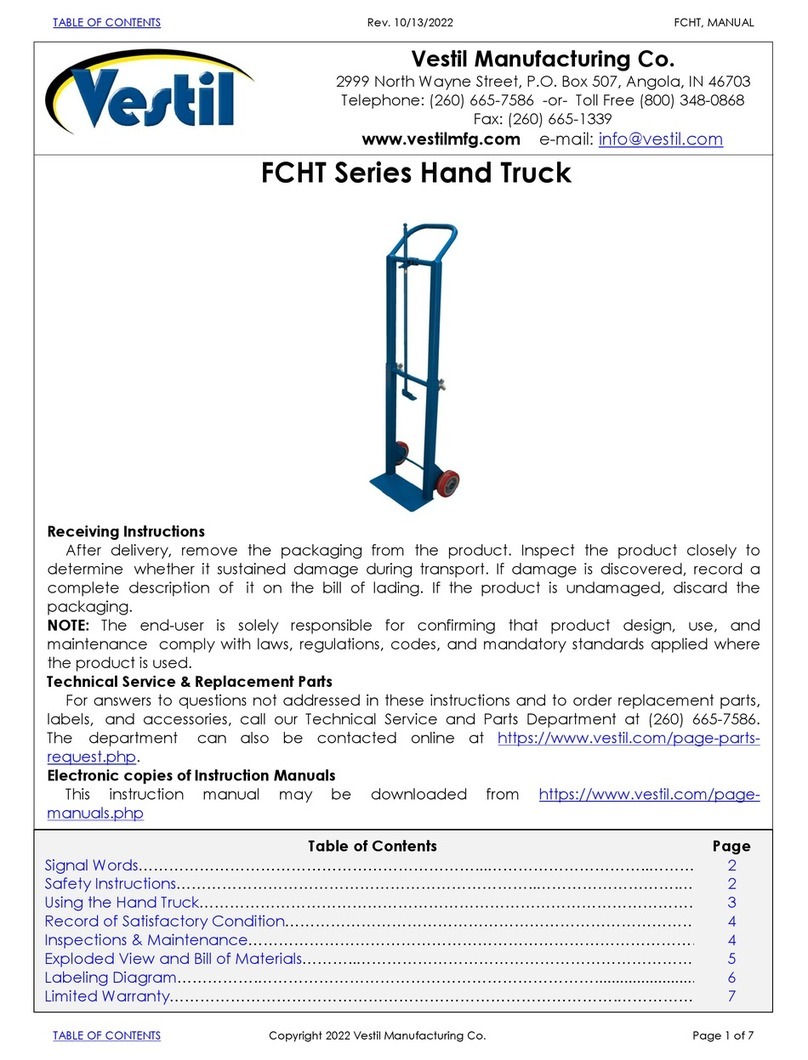
Vestil
Vestil FCHT Series Use and maintenance instructions
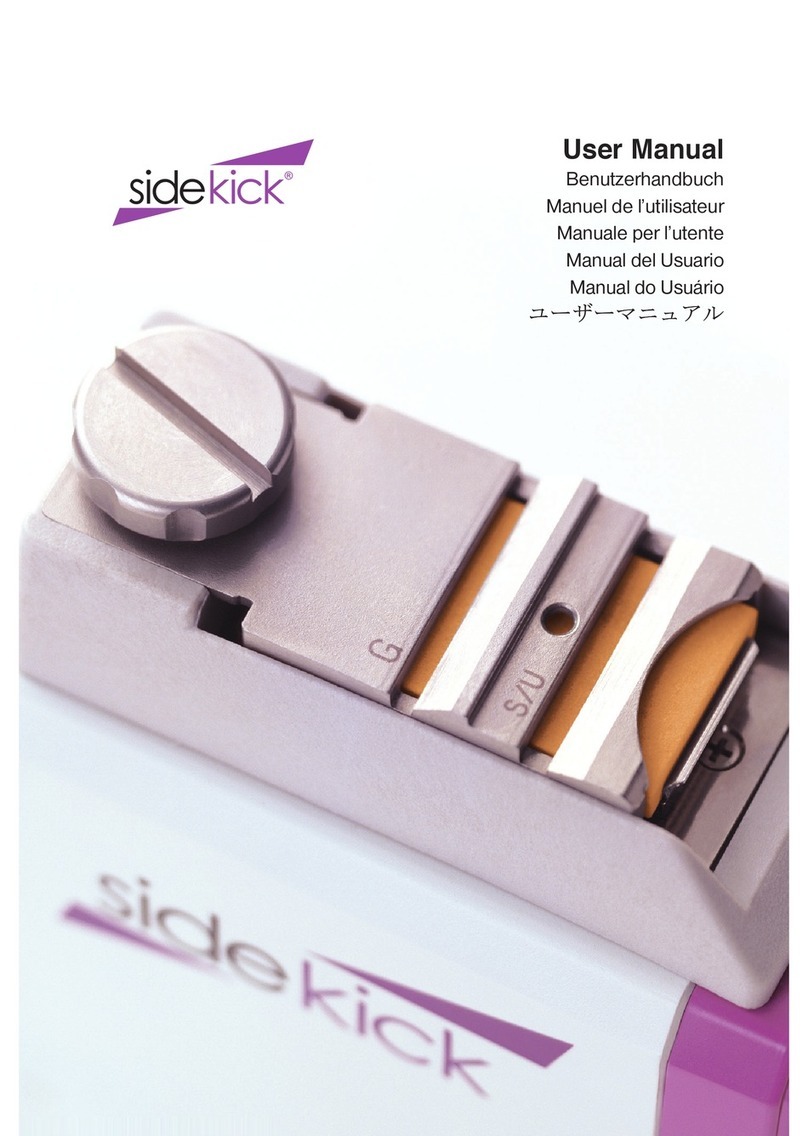
Hu-Friedy
Hu-Friedy Sidekick user manual

Parker Research Corp
Parker Research Corp B300 operating instructions