STERIFLOW I&M MK901 Series Installation and operating instructions

1
I
& M
MK901
Series
3170
Wasson
Road • Cincinnati, OH
45209
513
.
533
.
5600
•
800.543.7311
•
513.871.0105
(f
)
steriflow@richardsind.com • www.steriflowvalve.com
Installation
&
Maintenance
Instructions for Steriflow
MK901 Series 3- Piece Cavity Filled Ball Valves
Warning: Steriflow ball valves must only be used installed and repaired in accordance with these Installation & Maintenance
Instructions.
Observe all applicable public and company codes and regulations. In the event of leakage or other malfunction, call
a qualified service person;
continued operation may cause system failure or a general hazard.
Please read these instructionscarefully!
Your Steriflow Valve product will provide you with long,
trouble-free service if it is correctly installed and
maintained. Spending a few minutes now reading
these instructions can save hours of trouble and
downtime later. Whenmaking repairs, use only
genuine Steriflow Valve parts, available for immediate
shipment from the factory
.
Scope
This manual is intended as a guide to assist
customers in the storage, installation, and
maintenance of Steriflow MK901 Series ball valves.
Subsequent additions or special instructions will be
provided for special valves, critical service or
customer requirements.
Applicability
Thismanual is applicable to the MK901Steriflow three
piece ball valves
Caution
To help prevent injury to personnel or damage to
equipment, please read this section completely before
performing any operations.
1. Valve pressure ratings are based on many
variables, including valve series and size, as well
as body, seat and bolt material. Verify that
application does not exceed the pressure or
temperature rating on the nameplate.
2. Always depressurize the line with the valve in
the open position before disassembly. Cycle
valve in depressurized line before removing
valve.
3. Wear protective equipment and take
appr
opriate
precautions to safeguard against injury caused
by
the discharge of trapped fluids.
Use only Steriflow recommended spare parts for
maintenance.
To ensure safety and maintain warranty, never modify
valve in any way without prior approval from
Steriflow.
Storage
No internal lubricant is used on these valves. An FDA
H-1 food grade incidental contact lubricant may be
used on the threads of the body-end cap bolts. All
valves are adequately packed in a strong cardboard
case in such a way as to avoid any possible damage
during transport and storage.
Caution: If ball valves are not destined for
immediate use, the following precautions should
be taken:
1. If possible, leave the ball valves in their
packing
cases during the period of storage.
2. Ballvalvesmust remaininopen position during thistime.
4” Size
½” - 3” Sizes

2
3. In order to prevent damage, protective
plastic
covers on valve ends should not be removed
until immediately prior to installation.
4. It is advisable to store the valves in waterproof
con
ditions. Ball valves should be protected to
safeguard against humidity, moisture, dust, dirt
sand, mud, salt spray and seawater.
5. All valves equipped with actuators shall be
stor
ed
in dry conditions.
6. Valves to be stored for a long period of time
should be checked by the quality control
personnel every six months; every three months
when valves are automated.
Maintenance During Storage Period
•
Internal surface should be inspected to check
for dust or other foreign
objects.
•
Rust or dust must be removed by cleaning
with proper solvent.
•
After cleaning, ball valves must be lubricated
with an adequate lubricant.
•
Ball valves should be operated for at least two
complete cycles before installing or returning
to storage.
Installation
The ball valves may be installed in any position
using standard pipe fitting
practices.
Caution: Before installation of the valve:
1. Pipe must be free of tension both during
and
after installation.
2. Pipe must be flushed to clean dirt,
welding
residues, etc. which would damage ball or seats.
3. The valve should be kept in
OPEN
POSITION
during installation and protective
plastic
covers
must be removed only at the moment of
installation.
4. If the valve was specified to be tested per ASME
16.34, there may be some trapped water
be
-
tween the ball and the body cavity. This can
be
removed by partially opening the valve, ther
eby
exposing the cavity to the through port of the
ball.
Installation of Tri-clamp Ends
5. Be sure only specified gasket and clamp, suitable
for the application rating, are used.
6. Be sure gasket is properly seated before
tightening clamp.
Installation
of
Weld-End
Ball
V
alv
es
7.
It is recommended that tube weld end valves
be welded in line using orbital welding. This
can be done without disassembling the valve.
8.
Other welding methods may not be feasible
due to the thin wall of the tubing. If other
methods are used, the valve and connecting
pipe should be aligned, and then the center
section of the valve dropped out during
welding to prevent heat damage of seats and
seals.
Manual Operation
1. Open and close the valve by turning the handle one-quarter
turn (90°).
2. Valve is in open position when handle is in line with
the
pipe.
3.
Valve is in closed position when the handle is
per
-
perpendicular to the
pipe.
Maintenance
Before starting maintenance, please read
information contained in the Caution Section of
the manual.
1. Open and close the ball valve at least once to
release the pressure completely from valve
body
.
2. Ball valves, if correctly used, normally do not
need any internal lubrication and maintenance.
However, when necessary, ball or seats can
be
replaced by qualified personnel following the
instructions of this manual.
3. For further information, please refer to the
cross section view and parts list.
Valve Disassembly
A.To inspect and / or Replace Body Seals,
Seats, Packing & Ball
Reference cross section view for parts identification
1. Valve must be in the open position.
2. Removeone body bolt (9) opposite hinge point
and
loosen all others. This will allow center
section to swing out.
3. Close the ball and remove seats (4), ball (3),
and
body seals (5). Be careful not to damage
the ball.
4. Removethe handle nut (14), handle (15), lock
washer (20), stem nut (13), gland bushing (19),
and stem packing (8).
5. Push the stem (6) into the body (1). Remove
thrust washer (7) from stem.

3
B. Inspection and Replacement
With the valve completely disassembled, clean
and
examine all components.
1. Ball - The surface of the ball should be free from
any defect. If any are found, the ball should be
replaced. Using a defective ball will be extremely
detrimental to valve performance.
2. Seats - Replacement of seats is recommended.
3. Stem and Body Seals – Stem and body seals
should be discarded and replaced.
4. Remaining components of the valve - After
cleaning, carefully examine for wear, corrosion
and mechanical damage. Replace all defective
parts.
5. Clean inside of body and stem housing. Light
grease, compatible with line fluid, can be used
on ball, seals and stem surface.
Note: A spare parts list is available for this valve.
Please refer to explosion view below for
identification. Please specify specific valve number
to ensure proper parts are ordered.SteriflowValve
does not take responsibility for incorrectly ordered
spare parts.
Reassembly
A. Stem
1. Replace thrust washer (7) on stem, and then insert
the stem (6) from inside the body (1).
2. Install stem packing (8), gland bushing (19), stem
nut (13), and tighten until snug, then one-half turn.
Do not over-tighten! To avoid rotation of stem,
insert the handle through the body and ball.
3. Install lock-washer (20), handle (15) and handle nut
(14), and then tighten.
B. Ball, Seats and Seals
1. Place the stem in closed position and insert the ball,
aligning groove in ball with bottom of stem.
2. Position the ball in the open position then insert the
seats and body seals.
3. Insert the centerpiece between the end caps,
reinstall removed bolts and tighten all bolts and nuts
by hand.
4. Tighten nuts to recommended torque values using
an alternating/opposing pattern with no more than
1/4 turn on each nut before alternating.
Testing
1. After completing the reassembly, check that valve
operates smoothly by opening and closing valve
several times
2. If entire valve was removed from line and if facilities
are available, test the ball valve to
appropri
ate
specifications.
Troubleshooting
A. Stem Leakage - You can eliminate leakage in the
stem area
by
increasing the torque on the stem nut
(13) in one-quarter turn increments. If leakage
persists, replace stem packing (8).
B. Body Seal Leakage - Check the torque of the body
bolts (9) according to Torque Table. Replace body
seals (5) if leakage persists.
C. In Line or Seat Leakage - Check to be sure valve is
in fully closed position. If leakage persists, the valve
must be disassembled and damaged parts
replaced.
Torque Table
Body Bolt & Stem Nut
Valve
Size
Bolt Size
Body Bolt
Torque
(in-lb)
Max Stem
Nut Torque
(in-lb
½”
5/16-18 UNC-2B
70 - 110
90
¾”
5/16-18 UNC-2B
80 - 120
90
1”
5/16-18 UNC-2B
85 - 130
110
1-½”
7/16-14 UNC-2B
120 - 180
170
2”
7/16-14 UNC-2B
200 - 300
180
2-½”
M12 x 1.75
435 - 660
260
3”
M14 x 2
480 - 725
380
4”
M16 x 2
560 - 840
450

Cross Section View
Bulletin
IM-MK901-0115
3170
Wasson Road •
Cincinnati, OH
45209
USA
Phone 513-533-
5600
• Fax
51
3-8
71
-0
105
Steriflow@richardsind.com
•
www
.Steriflow
v
alv
e.com
Item No.
Part Name
Quantity
Item No.
Part Name
Quantity
1
Body
1
12
Belleville Washer
2
2
End Cap
2
13
Nut, Stem
1
3
Ball
1
14
Nut, Handle
1
4
Seat *
2
15
Handle
1
5
Gasket, Body *
2
15A
Adapter, Handle
1 (4” Only)
6
Stem
1
15B
Bolt, Handle
1 (4” Only)
7
Thrust Washer *
1
16
Cover, Handle
1
8
Packing, Stem *
1 Set
17
Locking Device
1
9 Bolt or Stud, Body
(½”-3”) 4
(4”) 6
18 Stop Pin, Handle 1
10 Nut, Body
(½”-3”) 4
(4”) 12
19 Gland Bushing 1
11 Washer, Body Bolt
(½”-3”) 4
(4”) 12
20 Lock Washer, Stem Nut 1
½”-3” SIZES
ART1232
TRI-CLAMP ENDS
TUBE END
ART1233
4” SIZE (Tri-Clamp Ends Shown)
* Recommended Spare Parts
Popular Control Unit manuals by other brands

Viessmann
Viessmann Vitotronic 100 HC1 User's manual and operating instructions

Definox
Definox DCX3 Maintenance notice

Task Force Tips
Task Force Tips Twister Instructions for installation, safe operation and maintenance

NR Electric
NR Electric PCS-9705 Series instruction manual
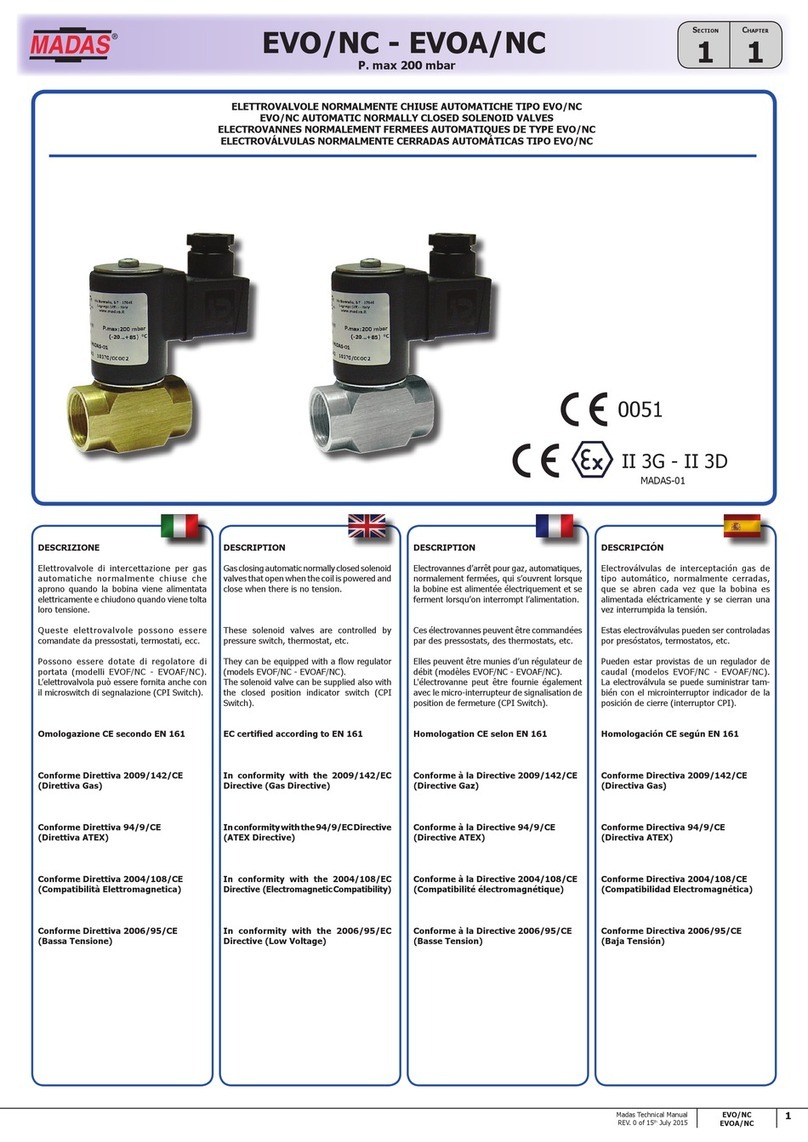
Madas
Madas EVO/NC quick start guide

Miranda
Miranda imagestore 750 user manual
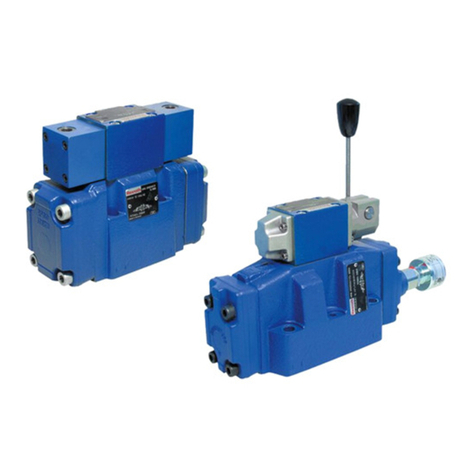
Bosch
Bosch WPH operating instructions
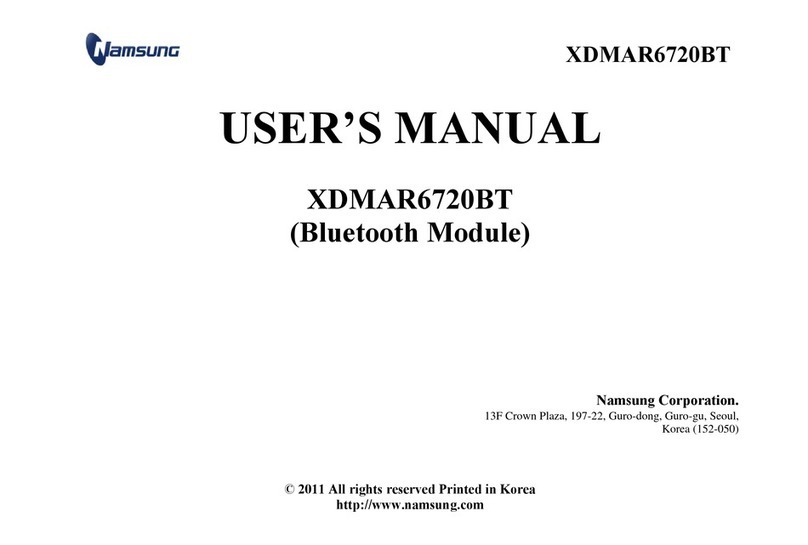
Namsung
Namsung XDMAR6720BT user manual
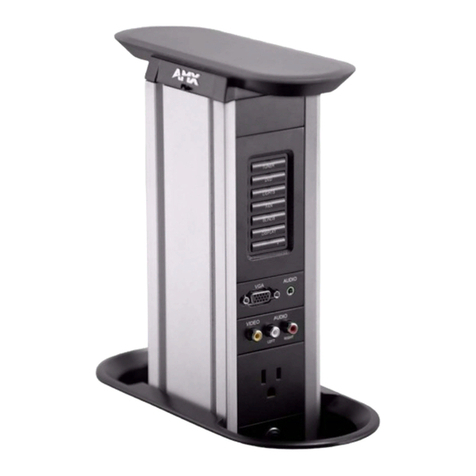
AMX
AMX HPX-1600 installation manual
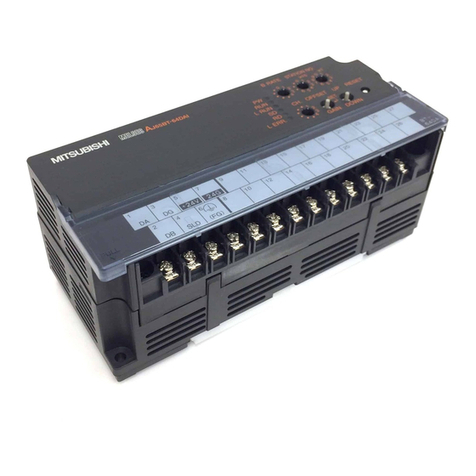
Mitsubishi
Mitsubishi AJ65BT-64DAV user manual
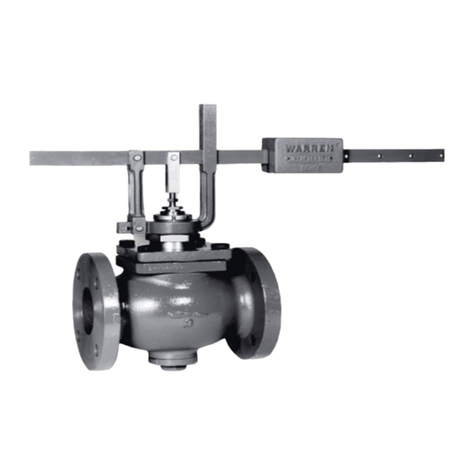
Warren Controls
Warren Controls 377 Installation, operation & maintenance instructions

Siemens
Siemens SIRIUS 8WD4428-0BF Original operating instructions