Sullair EES LS32 Series Installation and maintenance instructions

SULLAIR
HEAT RECOVERY SYSTEM
EES
Series
LS25S,
LS32
&
TS32
200-450HP/ 149-336KW
OPERATOR’S
MANUAL AND
PARTS LIST
KEEP FOR
FUTURE
REFERENCE
Part Number 02250135-752
©Sullair Corporation

AIR CARE
SEMINAR TRAINING
Sullair Air Care Seminars are 3-day courses that provide hands-on instruction in the proper operation,
maintenance and service of Sullair equipment. Individual seminars on Industrial compressors and com-
pressor electrical systems are presented at regular intervals throughout the year at a dedicated training
facility at Sullair’s corporate headquarters in Michigan City, Indiana.
Instruction includes discussion of the function and installation of Sullair service parts, troubleshooting of
the most common problems, and actual equipment operation. The seminars are recommended for main-
tenance and service personnel.
For detailed course outlines, schedule and cost information contact:
Sullair Corporate Training Department
1-888-SULLAIR or 219-879-5451 (ext. 5363)
www.sullair.com/training.shtm
or write
Sullair Corporation
3700 E. Michigan Blvd.
Michigan City, IN 46360
Attn: Service Training Department

TABLE OF CONTENTS
Section 1 PAGE
SAFETY 11.1 GENERAL
11.2 PERSONAL PROTECTIVE EQUIPMENT
11.3 PRESSURE RELEASE
21.4 FIRE AND EXPLOSION
21.5 MOVING PARTS
21.6 HOT SURFACES, SHARP EDGES AND SHARP CORNERS
21.7 TOXIC AND IRRITATING SUBSTANCES
31.8 ELECTRICAL SHOCK
31.9 LIFTING
41.10 ENTRAPMENT
Section 2
DESCRIPTION 52.1 INTRODUCTION
62.2 APPLICATION CONSIDERATIONS
72.3 DESCRIPTION OF COMPONENTS
Section 3
SPECIFICATIONS 93.1 SPECIFICATIONS
Section 4
INSTALLATION 11 4.1 LOCATION AND ASSEMBLY OF COMPRESSOR
11 4.2 THERMOSTAT PLACEMENT
11 4.3 ELECTRICAL PREPARATION
11 4.4 DUCTWORK
12 Table 1- Duct Size Conversion
14 Table 2- Ductwork Static Pressure Loss Worksheet
15 Table 3- Loss Coefficient Calculations
Section 5
OPERATION 17 5.1 INLET DAMPER LINKAGE ADJUSTMENT
17 5.2 DISCHARGE DAMPER LINKAGE ADJUSTMENT
18 5.3 SETTING OF CONTROLS
19 5.4 TROUBLESHOOTING
20 5.5 TROUBLESHOOTING GUIDE
OPERATOR IS REQUIRED TO READ
ENTIRE INSTRUCTION MANUAL

TABLE OF CONTENTS
Section 6
ILLUSTRATIONS
AND PARTS LIST 23 6.1 PROCEDURE FOR ORDERING PARTS
23 6.2 RECOMMENDED SPARE PARTS LIST
24 6.3 ASSEMBLY- EES 200-250HP/ 149-186KW
28 6.4 HORIZONTAL REMOTE COOLER PACK ASSEMBLY-
250HP/ 186KW
30 6.5 HORIZONTAL COOLER ASSEMBLY-
350HP/ 261KW (INTEGRAL)
34 6.6 HORIZONTAL COOLER PACK ASSEMBLY-
350HP/ 261KW (REMOTE)
36 6.7 HORIZONTAL REMOTE COOLER PACK ASSEMBLY
WITH DRAIN OPTION- 350HP/ 261KW
38 6.8 HORIZONTAL COOLER ASSEMBLY -
450HP/ 336KW (INTEGRAL)
40 6.9 HORIZONTAL REMOTE COOLER PACK ASSEMBY
WITH DRAIN OPTION- 400-450HP/ 298-336KW
42 6.10 HORIZONTAL REMOTE COOLER PACK ASSEMBLY-
450HP/ 336KW
44 6.11 EES ENCLOSURE- “DOGHOUSE” ASSEMBLY (INTEGRAL)
46 6.12 EES ENCLOSURE- 200-250HP/ 149-186KW (INTEGRAL)
50 6.13 EES ENCLOSURE- 300-350HP/ 224-261KW (INTEGRAL)
54 6.14 DECAL GROUP
56 6.15 DECAL LOCATIONS
58 6.16 WIRING DIAGRAM- EES SUPERVISOR CONTROL
59 6.17 WIRING DIAGRAM- EES REMOTE
60 6.18 WIRING DIAGRAM- INTEGRAL HEAT RECOVERY
WITH SUPERVISOR

Section 1
SAFETY
1
1.1 GENERAL
Sullair Corporation and its subsidiaries design and
manufacture all of their products so they can be
operated safely. However, the responsibility for
safeoperation rests with those who use and main-
tain these products. The following safety precau-
tions are offered as a guide which, if conscientious-
ly followed, will minimize the possibility of accidents
throughout the useful life of this equipment.
The compressor should be operated only by those
who have been trained and delegated to do so, and
who have read and understood this Operator’s
Manual. Failure to follow the instructions, proce-
dures and safety precautions in this manual may
result in accidents and injuries.
NEVER start the compressor unless it is safe to do
so. DO NOT attempt to operate the compressor
with a known unsafe condition. Tag the compressor
and render it inoperative by disconnecting and lock-
ing out all power at source or otherwise disabling its
prime mover so others who may not know of the
unsafe condition cannot attempt to operate it until
the condition is corrected.
Install, use and operate the compressor only in full
compliance with all pertinent OSHA regulations
and/or any applicable Federal, State, and Local
codes, standards and regulations.
DO NOT modify the compressor and/or controls in
any way except with written factory approval.
While not specifically applicable to all types of com-
pressors with all types of prime movers, most of the
precautionary statements contained herein are
applicable to most compressors and the concepts
behind these statements are generally applicable to
all compressors.
1.2 PERSONAL PROTECTIVE EQUIPMENT
Prior to installing or operating the compressor, own-
ers, employers and users should become familiar
with, and comply with, all applicable OSHA regula-
tions and/or any applicable Federal, State and
Local codes, standards, and regulations relative to
personal protective equipment, such as eye and
face protective equipment, respiratory protective
equipment, equipment intended to protect the
extremities, protective clothing, protective shields
and barriers and electrical protective equipment, as
well as noise exposure administrative and/or engi-
neering controls and/or personal hearing protective
equipment.
1.3 PRESSURE RELEASE
A. Install an appropriate flow-limiting valve between
the service air outlet and the shut-off (throttle)
valve, either at the compressor or at any other point
along the air line, when an air hose exceeding
13mm inside diameter is to be connected to the
shut-off (throttle) valve, to reduce pressure in case
of hose failure, per OSHA Standard 29 CFR
1926.302(b)(7) and/or any applicable Federal,
State and Local codes, standards and regulations.
B. When the hose is to be used to supply a mani-
fold, install an additional appropriate flow-limiting
valve between the manifold and each air hose
exceeding13mm inside diameter that is to be con-
nected to the manifold to reduce pressure in case
of hose failure.
C. Provide an appropriate flow-limiting valve at the
beginning of each additional 23m of hose in runs of
air hose exceeding13mm inside diameter to reduce
pressure in case of hose failure.
D. Flow-limiting valves are listed by pipe size and
flow-rated. Select appropriate valves accordingly, in
accordance with their manufacturer’s recommen-
dations.
E. DO NOT use air tools that are rated below the
maximum rating of the compressor. Select air tools,
air hoses, pipes, valves, filters and other fittings
accordingly. DO NOT exceed manufacturer’s rated
safe operating pressures for these items.
F. Secure all hose connections by wire, chain or
other suitable retaining device to prevent tools or
hose ends from being accidentally disconnected
and expelled.
G. Open fluid filler cap only when compressor is not
running and is not pressurized. Shut down the
compressor and bleed the sump (receiver) to zero
internal pressure before removing the cap.
H. Vent all internal pressure prior to opening any
line, fitting, hose, valve, drain plug, connection or
other component, such as filters and line oilers, and
before attempting to refill optional air line anti-icer
systems with antifreeze compound.
I. Keep personnel out of line with and away from the
discharge opening of hoses or tools or other points
of compressed air discharge.
J. Use air at pressures less than 2.1 bar for clean-
ing purposes, and then only with effective chip
guarding and personal protective equipment per
OSHA Standard 29 CFR 1910.242 (b) and/or any
applicable Federal, State, and Local codes, stan-
dards and regulations.
K. DO NOT engage in horseplay with air hoses as

Section 1
SAFETY
2
death or serious injury may result.
1.4 FIRE AND EXPLOSION
A. Clean up spills of lubricant or other combustible
substances immediately, if such spills occur.
B. Shut off the compressor and allow it to cool.
Then keep sparks, flames and other sources of
ignition away and DO NOT permit smoking in the
vicinity when checking or adding lubricant or when
refilling air line anti-icer systems with antifreeze
compound.
C. DO NOT permit fluids, including air line anti-icer
system antifreeze compound or fluid film, to accu-
mulate on, under or around acoustical material, or
on any external surfaces of the air compressor.
Wipe down using an aqueous industrial cleaner or
steam clean as required. If necessary, remove
acoustical material, clean all surfaces and then
replace acoustical material. Any acoustical materi-
al with a protective covering that has been torn or
punctured should be replaced immediately to pre-
vent accumulation of liquids or fluid film within the
material. DO NOT use flammable solvents for
cleaning purposes.
D. Disconnect and lock out all power at source prior
to attempting any repairs or cleaning of the com-
pressor or of the inside of the enclosure, if any.
E. Keep electrical wiring, including all terminals and
pressure connectors in good condition. Replace
any wiring that has cracked, cut, abraded or other-
wise degraded insulation, or terminals that are
worn, discolored or corroded. Keep all terminals
and pressure connectors clean and tight.
F. Keep grounded and/or conductive objects such
as tools away from exposed live electrical parts
such as terminals to avoid arcing which might serve
as a source of ignition.
G. Remove any acoustical material or other materi-
al that may be damaged by heat or that may sup-
port combustion and is in close proximity, prior to
attempting weld repairs.
H. Keep suitable fully charged Class BC or ABC fire
extinguisher or extinguishers nearby when servic-
ing and operating the compressor.
I. Keep oily rags, trash, leaves, litter or other com-
bustibles out of and away from the compressor.
J. DO NOT operate the compressor without proper
flow of cooling air or water or with inadequate flow
of lubricant or with degraded lubricant.
K. DO NOT attempt to operate the compressor in
any classification of hazardous
environment unless the compressor has been spe-
cially designed and manufactured for that duty.
1.5 MOVING PARTS
A. Keep hands, arms and other parts of the body
and also clothing away from couplings, fans and
other moving parts.
B. DO NOT attempt to operate the compressor with
the fan, coupling or other guards removed.
C. Wear snug-fitting clothing and confine long hair
when working around this compressor, especially
when exposed to hot or moving parts.
D. Keep access doors, if any, closed except when
making repairs or adjustments.
E. Make sure all personnel are out of and/or clear
of the compressor prior to attempting to start or
operate it.
F. Disconnect and lock out all power at source and
verify at the compressor that all circuits are de-
energized to minimize the possibility of accidental
start-up, or operation, prior to attempting repairs or
adjustments. This is especially important when
compressors are remotely controlled.
G. Keep hands, feet, floors, controls and walking
surfaces clean and free of fluid, water or other liq-
uids to minimize the possibility of slips and falls.
1.6 HOT SURFACES, SHARP EDGES AND SHARP
CORNERS
A. Avoid bodily contact with hot fluid, hot coolant,
hot surfaces and sharp edges and corners.
B. Keep all parts of the body away from all points
of air discharge.
C. Wear personal protective equipment including
gloves and head covering when working in, on or
around the compressor.
D. Keep a first aid kit handy. Seek medical assis-
tance promptly in case of injury. DO NOT ignore
small cuts and burns as they may lead to infection.
1.7 TOXIC AND IRRITATING SUBSTANCES
A. DO NOT use air from this compressor for respi-
ration (breathing) except in full compliance with
OSHA Standards 29 CFR 1910 and/or any applica-
ble Federal, State or Local codes or regulations.
Death or serious injury can result from inhaling
compressed air without using proper safety
equipment. See OSHA standards and/or any
applicable Federal, State, and Local codes,
standards and regulations on safety equipment.

Section 1
SAFETY
3
B. DO NOT use air line anti-icer systems in air lines
supplying respirators or other breathing air utiliza-
tion equipment and DO NOT discharge air from
these systems into unventilated or other confined
areas.
C. Operate the compressor only in open or ade-
quately ventilated areas.
D. Locate the compressor or provide a remote inlet
so that it is not likely to ingest exhaust fumes or
other toxic, noxious or corrosive fumes or sub-
stances.
E. Coolants and lubricants used in this compressor
are typical of the industry. Care should be taken to
avoid accidental ingestion and/or skin contact. In
the event of ingestion, seek medical treatment
promptly. Wash with soap and water in the event of
skin contact. Consult Material Safety Data Sheet for
information pertaining to fluid of fill.
F. Wear goggles or a full face shield when adding
antifreeze compound to air line anti-icer systems.
G. If air line anti-icer system antifreeze compound
enters the eyes or if fumes irritate the eyes, they
should be washed with large quantities of clean
water for fifteen minutes. A physician, preferably an
eye specialist, should be contacted immediately.
H. DO NOT store air line anti-icer system antifreeze
compound in confined areas.
I. The antifreeze compound used in air line
antifreeze systems contains methanol and is toxic,
harmful or fatal if swallowed. Avoid contact with the
skin or eyes and avoid breathing the fumes. If swal-
lowed, induce vomiting by administering a table-
spoon of salt, in each glass of clean, warm water
until vomit is clear, then administer two teaspoons
of baking soda in a glass of clean water. Have
patient lay down and cover eyes to exclude light.
Call a physician immediately.
1.8 ELECTRICAL SHOCK
A. This compressor should be installed and main-
tained in full compliance with all applicable Federal,
State and Local codes, standards and regulations,
including those of the National Electrical Code, and
also including those relative to equipment ground-
ing conductors, and only by personnel that are
trained, qualified and delegated to do so.
B. Keep all parts of the body and any hand-held
tools or other conductive objects away from
exposed live parts of electrical system. Maintain dry
footing, stand on insulating surfaces and DO NOT
contact any other portion of the compressor when
making adjustments or repairs to exposed live parts
of the electrical system. Make all such adjustments
or repairs with one hand only, so as to minimize the
possibility of creating a current path through the
heart.
C. Attempt repairs in clean, dry and well lighted and
ventilated areas only.
D. DO NOT leave the compressor unattended with
open electrical enclosures. If necessary to do so,
then disconnect, lock out and tag all power at
source so others will not inadvertently restore
power.
E. Disconnect, lock out, and tag all power at source
prior to attempting repairs or adjustments to rotating
machinery and prior to handling any ungrounded
conductors.
1.9 LIFTING
A. If the compressor is provided with a lifting bail,
then lift by the bail provided. If no bail is provided,
then lift by sling. Compressors to be air-lifted by hel-
icopter must not be supported by the lifting bail but
by slings instead. In any event, lift and/or handle
only in full compliance with OSHA standards 29
CFR 1910 subpart N and/or any applicable Federal,
State, and Local codes, standards and regulations.
B. Inspect points of attachment for cracked welds
and for cracked, bent, corroded or otherwise
degraded members and for loose bolts or nuts prior
to
lifting.
C. Make sure entire lifting, rigging and supporting
structure has been inspected, is in good condition
and has a rated capacity of at least the weight of
the compressor. If you are unsure of the weight,
then weigh compressor before lifting.
D. Make sure lifting hook has a functional safety
latch or equivalent, and is fully engaged and latched
on the bail or slings.
E. Use guide ropes or equivalent to prevent twisting
or swinging of the compressor once it has been lift-
ed clear of the ground.
F. DO NOT attempt to lift in high winds.
G. Keep all personnel out from under and away
from the compressor whenever it is suspended.
H. Lift compressor no higher than necessary.
I. Keep lift operator in constant attendance when-
ever compressor is suspended.
J. Set compressor down only on a level surface
capable of safely supporting at least its weight and

Section 1
SAFETY
4
its loading unit.
K. When moving the compressor by forklift truck,
utilize fork pockets if provided. Otherwise, utilize
pallet if provided. If neither fork pockets or pallet
are provided, then make sure compressor is secure
and well balanced on forks before attempting to
raise or transport it any significant distance.
L. Make sure forklift truck forks are fully engaged
and tipped back prior to lifting or transporting the
compressor.
M. Forklift no higher than necessary to clear obsta-
cles at floor level and transport and corner at mini-
mum practical speeds.
N. Make sure pallet-mounted compressors are
firmly bolted or otherwise secured to the pallet prior
to attempting to forklift or transport them. NEVER
attempt to forklift a compressor that is not secured
to its pallet, as uneven floors or sudden stops may
cause the compressor to tumble off, possibly caus-
ing serious injury or property damage in the
process.
1.10 ENTRAPMENT
A. If the compressor enclosure, if any, is large
enough to hold a man and if it is necessary to enter
it to perform service adjustments, inform other per-
sonnel before doing so, or else secure and tag the
access door in the open position to avoid the pos-
sibility of others closing and possibly latching the
door with personnel inside.
B. Make sure all personnel are out of compressor
before closing and latching enclosure doors.

Section 2
DESCRIPTION
5
2.1 INTRODUCTION
The Sullair Integral Heat Recovery System is a
means of recovering energy which is expended
while producing compressed air. This energy can
be converted into a usable source of heat. The heat
is stored in the compressor cooling air as it passes
over the compressor motor, fluid cooler and after-
cooler. The compressor cooling air can then be
used as preheated make-up air or heating air for
plants, warehouses, etc. Heat may also be rejected
from the system when it is not required.
Any make-up air introduced into a heating or ven-
tilation system by this system must be of breath-
ing air quality as defined by applicable codes,
laws or regulations.
Because the heat recovery system is built into the
compressor package it requires a minimal amount
of installation labor. The system has been
designed so that use of auxiliary blowers is not
needed as long as good duct design is practiced
(See Section 4.4).
Figure 2-1 Sullair Heat Recovery System- Typical Overview

Section 2
DESCRIPTION
6
Should any questions arise which cannot be
answered in the following text, call your nearest
Sullair office or the Sullair Corporation Service
Department.
2.2 APPLICATION CONSIDERATIONS
A. GENERAL
The Sullair EES is designed primarily to recover the
heat of compression in the form of heated make-up
air. Maximum energy utilization, minimum cost of
installation, and therefore maximum return on
investment will be realized by using the EES in this
fashion. For every cubic foot of outside air brought
into a building by this EES, another cubic foot of air
that would have infiltrated into the building at out-
side temperature will be eliminated. The fuel sav-
ings result from the plant’s primary heating system
not having to heat that cubic foot of air at outside
temperature up to the temperature of the heated
space.
It is possible for the EES system to operate effi-
ciently as a heating system; that is, where air is
drawn and heated to some higher temperature (say
90ºF [32ºC]), then the hot air distributed through-out
the heated space. However, this usually requires
greater capital investment in the form of a larger
ductwork system to distribute the heated air.
As a preheated make-up air system, air is brought
in from the outside at some low temperature (say
40ºF [14ºC]), heated approximately to the heated
space temperature (say 65ºF [18ºC]), and then
released to the heated space at one point. Since
the air is close to heated space temperature, there
is little advantage in distributing this air throughout
the plant.
In either case, the same amount of heat is recov-
ered, but in the make-up air system, significant
reductions in the installed cost are possible. This is
the key to the popularity of the Sullair EES Integral
Heat Recovery System.
B. PROCESS HEATING
It is also possible to utilize the waste-heat of com-
pression for some process heating applications,
such as drying parts, etc. This type of application
will usually net a greater return on investment
because the heat can be used year round. If this is
the case, you may want to contact your local Sullair
distributor for application assistance.
C. MULTIPLE COMPRESSOR INSTALLATIONS
For multiple machine installations, it is usually less
expensive to manifold all or most of the ductwork,
rather than run separate ducts for each machine.
Care should be taken in the design of such a sys-
tem, because unlike duct elbows and straight duct,
divided flow duct fittings (tees, crosses, laterals,
and wyes) have different performance characteris-
tics depending on whether they are diverging flow
or converging flow. Generally speaking, ductwork
on the inlet side of the compressor may be treated
as a supply system, and ductwork on the discharge
side of the compressor may be considered as an
exhaust system. (Refer to Section 4.4 for more
information). It is good design practice to size all
ducts such that when all compressors are running
there will be constant velocity in all ducts.
D. COMPRESSORS IN UNHEATED SPACES
It is quite feasible to locate the Sullair compressor
with Integral EES in unheated spaces with mini-
mum modifications, because heated air is automat-
ically bypassed to maintain a thermostatically con-
trolled temperature in the compressor enclosure,
thereby allowing aftercooled compressors to run
reliably in even sub-zero temperatures. However,
provisions must be made to prevent freezing when
the compressor is not running. A heated trap should
be used, and the condensate drain should be heat
traced and insulated. The section of pipe conveying
compressed air from the compressor to the heated
space should be insulated. Some compressor fluids
may not be suitable because of excessively high
viscosity on a completely cold start-up. More infor-
mation on compressor lubricants can be found in
the Compressor Manual, or by contacting your local
Sullair Distributor.
E. COMPRESSORS IN ENCLOSED SPACES
When one or more compressors are located in an
enclosed space, no special room ventilation is
required, other than the usual ductwork. However, if
other heat-affected equipment is also located in the
enclosed space (transformers, instrumentation,
etc.), it may be necessary to provide auxiliary ven-
tilation to prevent excessive heat buildup.
F. BOOSTER FANS
The internal circulating fan on the EES has addi-
tional static capability to allow for a generous
amount of external ductwork, and it is almost
always possible to design the system ductwork in
such a way that a booster fan will not be required.
However, a booster fan will be the only practical
solution in some applications. If this is the case, the
following guidelines should be observed:
• If ductwork static is greater than 0.5 in. W.G.
(see Section 3).
• Manufacturer’s fan ratings are based on an
idealized test procedure, and some de-rat-

Section 2
DESCRIPTION
7
ing might be required depending on how the
fan is applied.
• Tube-axial type fans are the most common-
ly used type of booster fans.
• The selected fan should be non-overloading;
i.e. if the fan discharge or inlet is shut off, the
fan drive motor should not overload.
2.3 DESCRIPTION OF COMPONENTS
Refer to Figure 2-1. The basic components of the
Sullair Integral Heat Recovery System are shown.
The complete package of a structural steel base
frame, inlet and discharge plenums, oil cooler
(aftercooler optional), motor and cooling fan, mois-
ture separator and heated trap, damper panels for
outdoor air, recovered heated air, bypass air, and
rejected heated air; two temperature probes; two
pneumatic cylinders; room thermostat; damper
actuator motor; solenoid valve; and a temperature
controller.
The following text explains the functional descrip-
tion of these components.
TEMPERATURE PROBE “A”- MIXED AIR
Probe A is mounted in the compressor enclosure,
where it monitors the temperature of the mixture of
bypass and outdoor air. Refer to Figures 2-2, 2-3
and 2-4.
The damper motor actuator will modulate so that
the set mixed air temperature will be maintained.
Since the mixed air temperature remains constant,
the heated exhaust air temperature will vary
depending on the demand for compressor loading.
The air temperature rise across the coolers can be
as little as 5ºF (3ºC) for a completely unloaded
compressor. This is a thermistor type of tempera-
ture probe.
TEMPERATURE PROBE “B”- OUTSIDE AIR
This probe monitors the outdoor air temperature.
When the outdoor temperature exceeds the set
value on the temperature controller, an electrical
signal is sent to the exhaust plenum damper motor
actuators, and the heated cooling air will be reject-
ed outdoors.
At the same time, the temperature controller sends
an electrical signal to the mixed air damper motor
actuator, which positions the dampers so that all
cooling air will enter the compressor cabinet from
outdoors.
ROOM THERMOSTAT
This thermostat monitors the temperature of the
heated space. If the set value on this thermostat is
exceeded, an electrical signal is sent to the exhaust
plenum damper motor actuators, and the heated
cooling air will be rejected outdoors.
DAMPER MOTOR ACTUATORS- RECOVERED
AND REJECTED AIR
The motor actuators control the movements of the
rejected and recovered air dampers. When the
compressor is not running, the motor actuators
maintain the recovered and rejected dampers in a
closed position.
When the compressor is running and the room ther-
mostat and the outside air temperature probe indi-
cate temperatures below their setpoints, the motor
actuator will fully open the recovered air damper
directing all heated cooling air to the heated space.
When the recovered air damper motor actuator
receives an electrical signal due to a rise in room
temperature, it will close the recovered air damper.
The rejected air damper actuator will simultaneous-
ly open the rejected air damper, directing all heated
cooling air outdoors.
MOTOR ACTUATOR- MIXED AIR
The motor actuator positions the outdoor and
bypass air dampers. It utilizes an electrical signal,
which is a function of the temperature sensed by
Probe “A”. The actuator maintains the outdoor air
damper in a closed position when the compressor is
not running.

Section 2
DESCRIPTION
8
Figure 2-2 High Room Temperature Figure 2-3 Low Room Temperature
Figure 2-4 No Power

Section 3
SPECIFICATIONS
9
3.1 SPECIFICATIONS
COMPRESSOR POWER RANGE: 200-450HP/ 149-335KW
FAN DIAMETER: 42” (200-250HP/ 149-186KW)
48” (300-450HP/ 224-336KW)
FAN POWER: 71/2HP (REMOTE) (200HP)/900RPM/AOPE
10HP (INTEGRAL) (250HP)/1200RPM/AOPE
15HP (300-350HP)/900RPM/AOPE
20HP (400-450HP)/1200RPM/AOPE
TEMPERATURE CONTROLLERS:
Electrical: 120VAC Input/24VAC Output 50/60HZ
Enclosure: Nema 1
Mixed Air Range: 10º to 90ºF (-12º to 32ºC)
Outdoor Air Changeover Range: 20º to 90ºF (-6º to 32ºC)
ROOM THERMOSTAT:
Electrical: 120VAC
Range: 40º to 90ºF (4º to 32ºC)
Solenoid Valve:
Electrical: 120VAC/60HZ
Enclosure: Nema 1
AIR VOLUME
(at listed Water Gauge Duct Restriction): 18,000 CFM- 200HP/149KW
30,000 CFM- 250-350HP/186-261KW
35,000 CFM- 400-450HP/298-336KW
Allowable ductwork pressure drop is 0.5 w.g. static maximum for all horsepowers listed. A booster
fan is required if pressure drop exceeds 0.5 w.g.

Section 3
SPECIFICATIONS
10
Figure 3-1 Identification- TS32A-300/350 EES (Typical)
02250133-419R00

Section 4
INSTALLATION
11
4.1 LOCATION AND ASSEMBLY OF COMPRESSOR
Upon delivery, check your compressor and integral
heat recovery system for any damage which may
have occurred during shipment. Any damage
should be noted on the delivery receipt and a dam-
age claim filed with the shipper.
After the EES is in place, seal all unused holes in
the cabinet and base frame. This is to insure that
cooling air can only enter the compressor cabinet
through the outside air damper.
4.2 THERMOSTAT PLACEMENT
Install the room thermostat (Refer to room thermo-
stat description in Section 2.3) in the space to be
heated in a location where it will sense a represen-
tative temperature and be safe from physical dam-
age or tampering.
4.3 ELECTRICAL PREPARATION
Interior electrical wiring is performed at the factory.
Required customer wiring is minimal, but should be
done by a qualified electrician in compliance with
OSHA, National Electric Code, and/or any other
applicable local electrical codes concerning isola-
tion switches, fused disconnects, etc. Refer to
Sections 6.16, 6.17or 6.18 for the internal heat
recovery system wiring diagram proportionate to
your EES package.
4.4 DUCTWORK
A. TYPE OF DUCT
Traditionally, duct systems are rectangular and con-
structed of light gauge, galvanized steel. However,
in recent years, round section galvanized steel and
round or rectangular section fiberglass products
have found increased use because of generally
lower installed costs. Galvanized steel, flat, oval
and cross section duct are also available.
The best type of duct system to use should be eval-
uated on an individual basis because each installa-
tion has its own unique requirements and prob-
lems. Because of the large air volumes, low veloci-
ties and low pressures normally encountered, gen-
erally, round section sheet metal duct will produce
the lowest installed cost.
For EES units located in a heated space, it is rec-
ommended that the duct carrying cold, outdoor air
be insulated to prevent wintertime, (exterior of the
duct) water condensation (sweating). If the exterior
of the duct is insulated, a vapor barrier should be
used. If the interior of the duct is insulated, this will
affect the air handling performance of the duct and
should be accounted for in the ductwork static pres-
sure calculations. For EES units located in an
unheated space where the recovered air is ducted
to a heated space, that portion of the duct exposed
to low ambient temperatures should be insulated to
prevent excessive heat loss. For EES units mount-
ed in a space that is also air-conditioned in sum-
mer, the summer rejected air duct should be insu-
lated to reduce the air conditioning load.
B. DUCTWORK STATIC PRESSURE CALCULA-
TION
The static pressure loss imposed by the ductwork
must be calculated. The static pressure loss must
not exceed .50 inches of water column at the rated
CFM. Static pressure loss is calculated using the
total of the inlet duct loss and discharge duct loss.
The following text, tables and formulas will show
how to calculate the ductwork static pressure loss
for your machine. A worksheet has been included
to help in the calculation.
The following three steps must be taken to ensure
the adequacy of an installation’s ductwork design.
1. A total static pressure loss must be calculated for
each branch by summing the static pressure
losses for every component of that branch
2. A total system static pressure loss is calculated
by adding the greater of the two discharge duct
static pressure losses to the inlet duct static
pressure loss.
3. If total system pressure loss exceeds .50 inches
of water, the ductwork must be redesigned or
booster fans added. To reduce the amount of
system static pressure loss, the following
changes will have the greatest effect:
a) Increase in duct size.
b) Increase in the radius of elbows and tees.
c) Addition of turning vanes to tees and elbows.
d) Avoid the use of abrupt duct size changes.
e) Redesign the entrances and exits for the system.
f) Add booster fans if necessary (see Section 3).
C. COMPONENT STATIC PRESSURE LOSS
CALCULATION
STRAIGHT DUCT STATIC PRESSURE LOSS
1. Determine the volume of air to be handled by the
ductwork (consult Section 3).
2. If your ductwork is square or rectangular, find the
equivalent round duct diameter from Table 1.
3. Using Figure 4-1, find the static pressure loss for
100 feet of straight duct.
4. Find the actual static pressure loss in the straight

Section 4
INSTALLATION
12
duct using the following equation:
Ft. of Straight X Static Press. = Actual Static
Duct (I) Pressure Loss
100
DUCT FITTING STATIC PRESSURE LOSS
1. The volume of air to be delivered through the fit-
ting is 30,000 CFM (250HP), and 35,000 CFM
(450HP).
2. Calculate the fitting area through which the air is
flowing. Be sure this area corresponds to the
area used in Table 3 for calculating the loss
coefficient.
For Rectangular Duct:
Area = Width (II) x Height (II)
144
For Round Duct:
Area = .00545 x Diameter2(II)
3. Calculate the air velocity through the fitting.
Velocity (III) = CFM - From Step 1
Area - From Step 2
4. Select the proper loss coefficient from Table 3.
Be sure that the loss coefficient corresponds to
the area calculated in Step #2.
5. Calculate the static pressure loss for the fitting
using the following equation:
C(III) x (Velocity [ft./min.])2= Static Pressure Loss
4005 (inches of water)
6. Repeat Steps 2 through 5 for each fitting. The
calculations for each fitting and section of
straight duct should be tabulated on the work-
sheet provided (Table 2).
7. Total the static pressure loss for each duct
branch.
(I) Because fitting static pressure losses are “zero
length” losses, calculation of amount of straight
duct should be from the intersections of the center-
lines of the straight duct sections.
(II) In feet per minute.
(III) Use C, C1, C2, or C0 as indicated in Table 3.
Table 1- Duct Size Conversion
DUCT SIZE EQUIVALENT
(INCHES) ROUND DUCT
DIAMETER
(INCHES)
18 X 36 27
18 X 42 29
18 X 48 31
18 X 54 33
18 X 60 34
18 X 66 36
18 X 72 37
24 X 24 26
24 X 30 29
24 X 36 32
24 X 42 34
24 X 48 37
24 X 54 39
24 X 60 40
30 X 30 33
30 X 36 36
30 X 42 39
30 X 48 41
30 X 54 44
30 X 60 46
36 X 36 39
36 X 42 42
36 X 48 45
36 X 54 49
36 X 60 50
42 X 42 46
42 X 48 49
42 X 54 52
48 X 48 52
48 X 54 56
54 X 54 59
54 X 60 62
60 X 60 66
60 X 72 73
72 X 72 79

Section 4
INSTALLATION
13
Figure 4-1 Static Pressure Loss
TYPE ILLUSTRATION LOSS
CONDITIONS COEFFICIENT
A1/A2C1C2
0.1 0.81 81
0.2 0.64 16
0.3 0.49 5
Abrupt 0.4 0.36 2.25
Expansion 0.5 0.25 1.00
0.6 0.16 0.45
0.7 0.08 0.18
0.8 0.04 0.06
0.9 0.01 0.01

Section 4
INSTALLATION
14
Table 2- Ductwork Static Pressure Loss Worksheet

Section 4
INSTALLATION
15
Table 3- Loss Coefficient Calculations
©Copyright 1972 by the American Society of Heating, Refrigerating and Air-Conditioning Engineers, Inc.

NOTES
16
This manual suits for next models
2
Table of contents
Popular Heater manuals by other brands

CONVECTAIR
CONVECTAIR Samba Installation and operation notice
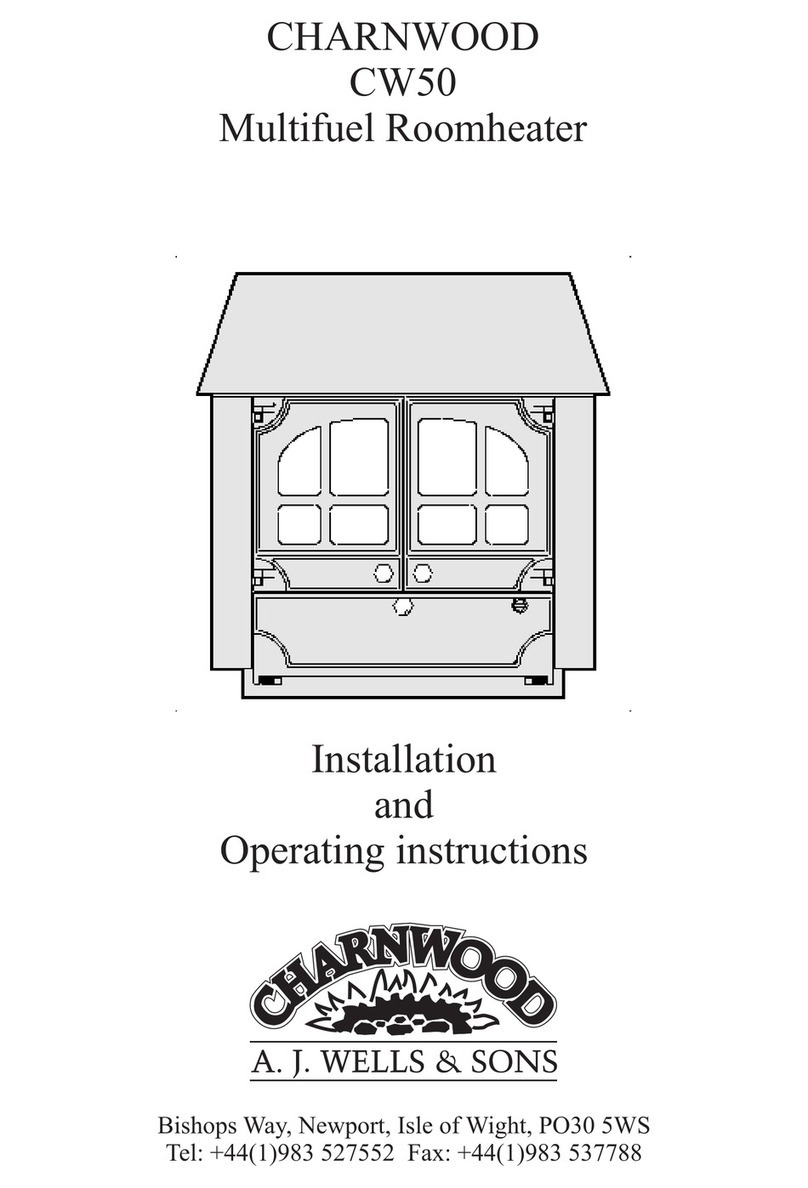
Charnwood
Charnwood CW50 Installation and operating instructions

Carter Hoffman
Carter Hoffman FH90 Cleaning, assembly and operation instructions
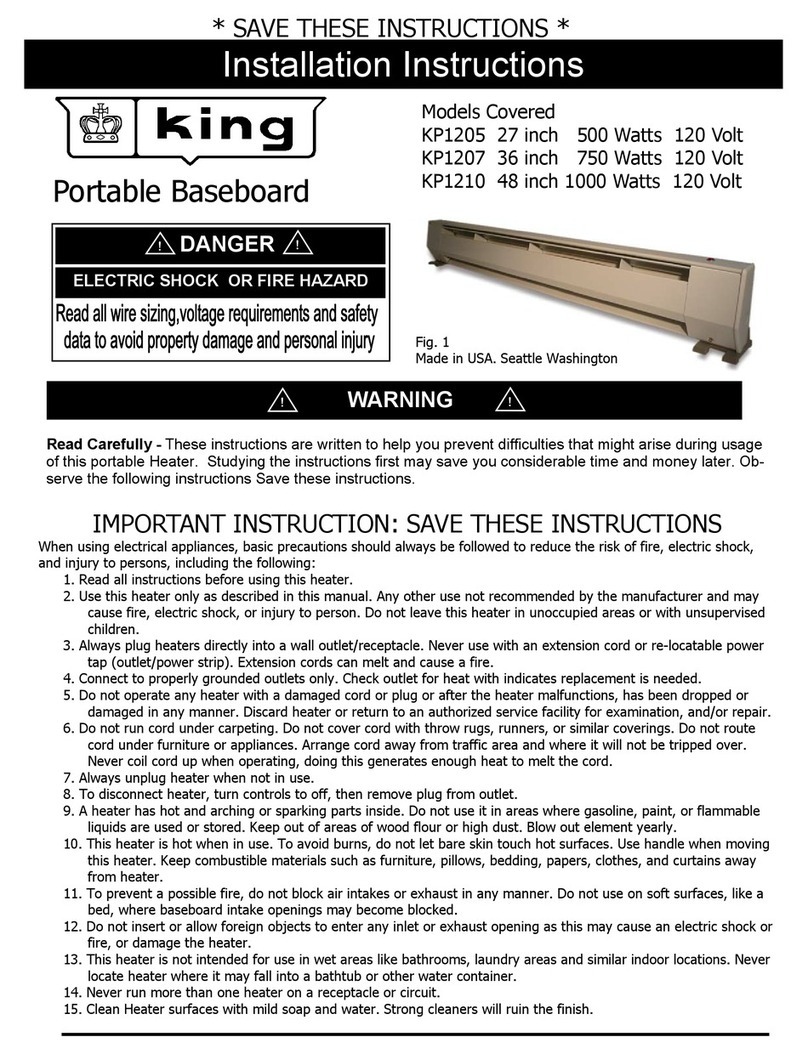
King Electrical
King Electrical KP1205 installation instructions
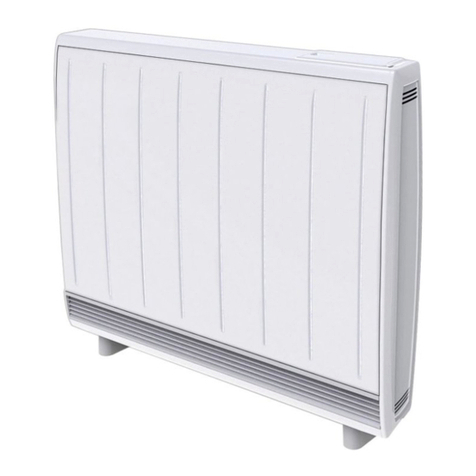
Dimplex
Dimplex QM070 QM100 QM125 QM150 operating instructions

Ferplast
Ferplast PET THERMAL MAT user manual