SUNTEC MN Series User guide

1
Installation and operating
Instruction Combined Gas Valve
M*N
Combined gas valve
with 2 safety valves
for light commercial
pressure jet burners.
Applicaon
The use of the SUNTEC M*N combined gas valve is recommended for all gaseous fuel
appliances where safety shuto is required. It is suitable for use with 1st, 2nd and 3rd
family gases, according to EN 437, for inlet pressure up to 360mbar (for M2 range) and to
160mbar (for M3 range).
M2 and M3 combined gas valve are available with 2 opons : fast opening (M*N**F) or
slow opening (M*N**S).
IIM_N - Ed. 1 - May 2022
SUNTEC INDUSTRIES FRANCE - 1, rue Lavoisier - CS 60102 - F-21603 LONGVIC Cedex
Approvals
SUNTEC M*N combined gas valve meets all the specicaons of EN 13611 and EN 161
standards. It complies with requirements of gas regulaon (EU) 2016/426 on appliances
burning gaseous fuels (CE cercate : 1312CU6361).

2IIM_N - Ed. 1 - May 2022
Technical specicaons
Safety Valves (V1 and V2) • M2N : Class A+A, according to EN 161
• M3N : Class B+B, according to EN 161
Seat size • M2N : Ø 17mm
• M3N : Ø 23mm
• M*N**F : < 0.5s
• M*N**S : < 10s
• M*N**F : < 0.2s
• M*N**S : < 0.2s
Supply voltage 230Vac +10% -15%, 50/60Hz (other voltage on request)
34 VA, steady operaon
IP54 (with suitable connector) according to EN 60529
DIN 43650 form A plug connector (not supplied)
Safety valves type of supply Independant
Air and gas of 1st, 2nd and 3rd families, according to EN 437
-
sure
• M2N : 360 mbar
• M3N : 160 mbar
Pipe sizes Inlet / outlet connecon with straight ange : DN15 (Rp1/2’’) or DN20
(Rp3/4’’).
Internal thread according to EN 10226-1.
Torsion / Bending stress M*N gas valve fulll group 2 requirements, according to EN 13611
Housing Aluminium
-20°C to +60°C
• M*N**F : 2.3kg
• M*N**S : 2.5kg
Safety shut-o valves have been cered for 200 000 ON/OFF opera-
ons according to EN 161 standard.
Pressure taps G1/8 connecons supplied in 3 locaons on the combined gas valve
(see secon ‘‘Pressure tap / pressure plugs idencaon’’, page 8),
and on inlet/outlet anges.
Seals and gaskets All NBR compounds, B2H2 and B2H3 according to EN549.
Inlet strainer Fine square mesh : 0.6 mm, AISI 304 steel Ø 0.14mm wire
Factory mounted on inlet ange.
When suitable conguraon (see page 8), can be side-mounted («P3»
tap).
General
Safety valves

3
IIM_N - Ed. 1 - May 2022
Flow curves
Operang principle
P : Inlet pressure
P1 : Strainer pressure
P2 / P3 : Intermediate pressure
P : Outlet pressure
F : Strainer
V1 : Safety shut-o valve 1
V2 : Safety shut-o valve 2
• with ow limiter (for M*N**F)
• with hydraulic damper (for M*N**S)
Dimensional drawings
Maximum ow can be reduced
when other anges are connected with.
P burner = 3 mbar
Flange = Rp3/4’’
110
165
188
95
44
133 (M*N**F - Fast opening)
182 (M*N**S - Slow opening)
40

4IIM_N - Ed. 1 - May 2022
Working principle
Safety valve
M*N combined gas valve comprises two automac shut-o valves, electrically operated.
Each operator consists of a plunger connected to a rubber seal. A closing spring presses the seal
against the seat, and thus ensures the ghtness of the valve. At rest, both safety valves are closed;
thus gas cannot ow beyond chamber
①
.
When energized independently or simultaneously, the coils generate a magnec eld which moves
up the plunger, and releases the gas ow from chamber
①
to chamber
②
for valve V1 (from
②
to
③
for V2).
A power-on indicator on the plasc cover lights up as valve V1 is energized.
When de-energized, each safety valve closes within 0.2 second.
A seng screw, located on the valve V2, limits the opening stroke of plunger. It can be used to
nely adjust the maximum gas ow.
A hydraulic damper slows down the opening stroke of the safety valve V2 and thus apply
a progressive gas flow in the combustion chamber during the starting phase. The presence
of a bypass allows to keep a fast opening of the safety valve V2, adjustable (Qstart) up to 80% of
the maximum ow.
①
②③
V1 V2
Qstart

5
IIM_N - Ed. 1 - May 2022
Installaon
Please read carefully these instrucons before installing, commissioning or using the product !
Hazardous situaon or damaging the product may result from their non-observance.
Herein specied rangs and product markings must be checked to ensure compability with the
appliance.
The installaon must only be carried out by a qualied technician.
A complete check of the installaon must be carried out prior any start o.
• Turn o gas supply before installaon.
• Disconnect power supply to the product before servicing to prevent any
electrical shock and damage to the product
• The gas valve must be installed so that the gas ows in the same direcon
of the arrows. Reverse mounng may render valve inoperave.
• A complete check of the installaon must be carried out prior any start o.
Any mounng posion is allowed, as long as the safety valve axis do not point downwards as
shown below.
- Apply thread sealant, sealing yarn or PTFE tape to the pipe threads. Type and amount should meet
the vendor specicaons.
- Screw the anges onto the pipes.
- Check that the anges are aligned and that spacing is sucient to insert the valve between the anges
without damaging the O-ring seals.
- Remove inlet / outlet protecve sckers and insert the 2 O-rings into their grooves. If necessary,
small amount of grease can be used to hold them on.
- Fasten the valve to the anges using the M5x20 screws supplied with the anges. Make sure that
the O-rings remain in place during this operaon.
- Perform the electrical connecon according to ‘‘Electrical connecon’’ secon page 6.
Cauon
90° 90° 90° 90°
90° 90°
To prevent dirt from entering the gas valve during installaon, inlet/outlet protecve sckers should
only be removed at the last moment.

6IIM_N - Ed. 1 - May 2022
Leak proof test
Check for gas leaks of all pipe connecons with a gas leak detecon spray. To ensure an eecve leak
test of all connecons, the gas valve must be energized (through the complete appliance) to raise
pressure all over the valve.
In case of leak detecon, gas supply must be shut o upstream and connecon ghtness redone.
• All wiring must be executed in accordance with local codes and regulaons.
• Lead wire should be selected to withstand maximum ambient and coil
temperature.
Cauon
Gas valve electrical connecon must be done with DIN 43650 form A connector (not supplied).
Gas valve wiring is shown below. Please refer to the appliance manufacturer instrucons for proper
wiring:
When the gas valve is powered, a green lamp lights up on the plasc cover. Please note that it is
supplied in parallel of valve V1, therefore it will not light up when only valve V2 is powered.
For pressure switch electrical connecon, please refer to pressure switch instrucons.
Gas valve adjustments
When fully screwed, the valve seal may be
pressed against the seat. Do not apply excessive
torque to avoid damaging the seal.
Cauon
Flow can be adjusted by the screw located on the top of the safety
valve V2 with the help of a 3 mm hex key ①. Unscrew to increase
the ow, screw gently to decrease.

7
IIM_N - Ed. 1 - May 2022
To set the fast stroke remove the cap, reverse it upside
down and use it as a tool to rotate the adjustement sleeve
③between posion F (fast to 80%) and S (slow opening
for all stroke).
Refer to the posion indicator on the top of the hydraulic
damper.
②
③
V1
V2
- +
- +
Do not make any sengs in the banned
area (in grey on the diagram below).
Cauon
Posion indicator
Adjustement sleeve
Slow
Fast
The opening me is factory preset and does not need to be modied (sealing varnish
on the needle screw).
With the factory seng, the opening me can be adjusted up to 10 seconds by adjus-
ng the adjustment sleeve.
If necessary, contact SUNTEC for specic adjustment.
Cauon
The main ow rate can be adjusted by unscrewing the two screws on the base of the hydraulic damper
with a 3.5mm at screwdriver.
Adjust the desired ow rate by rotang the body ②.
Tighten the two screws.
For slow opening models, a minimum rest me of 25 seconds must be observed between
2 safety valve V2 openings.
Cauon

8IIM_N - Ed. 1 - May 2022
M2 5 0 F 0 7 2 XXXX
Gas valve size (Body / Seat)
Pressure regulator type
N = without pressure regulator
4 = 160 mbar - B + B (for M3 range)
5 = 360 mbar - A + A (for M2 range)
Regulator pressure range
0 = No pressure regulator
2nd safety valve opening
F = Fast opening
S = Slow opening
Safety valves type of supply
0 = Independent
Coils voltage
7 = 230V AC
Revision
- -
Default conguraon for gas valve consists of 1 pressure tap (P ), and 3 plugs (P1, P2 and
P3) as shown below.
P3 pressure tap can be modied upon demand (consult SUNTEC).
Following pressure signal can be selected :
- Valve V1 upstream pressure, aer strainer,
- Pressure between Valve V1 and Valve V2,
- Valve V2 downstream pressure.
Codicaon
• To avoid any damage to the needle screw head, the use of an appropriate screwdriver is
strongly recommended.
• To ensure the pressure tap ghtness :
ghtening torque must be 1 to 1.5 N.m for the needle screw of the pressure tap
ghtening torque must be 3.5 N.m for the pressure tap.
• G1/8 Pressure taps can be removed using a 5 mm hex key.
• Perform a leak proof test aer a modicaon.
Cauon

9
IIM_N - Ed. 1 - May 2022
Only the following items can be replaced during
maintenance operaon :
- Flange,
- Electronic block (This set is composed
of 2 coils and an electronic board, do not
disassemble),
- Pressure tap,
- Inlet strainer,
- O ring,
- Hydraulic damper (only for slow opening
version M*N**S).
For any disassembly, refer to the instrucons
of the kits.
Maintenance
①
②
③
④
• The components listed must be SUNTEC parts.
• Any disassembly other than menoned above is strictly forbidden.
• After replacing any of the above items and before operating the gas valve,
check for gas leaks of all pipes connecons with a leak detecon.
• After any violent shock, such as an accidental dropping, the gas valve shall
not be used anymore ; Internal and external ghtness cannot be guaranteed.
Cauon
A
⑥
X GAR
Glasgow, Kentucky 42 141, USA
60 Aberdeen Drive
Subsidiary of SUNTEC INDUSTRIES FRANCE
SUNTEC INDUSTRIES, INCORPORATED
SUNTEC INDUSTRIES FRANCE
1 - rue Lavoisier, B.P. 102
Original size
A3
Description :
General tolerances
Scale
1:5
Date Draftsman
Weight (g) : Used on / Origin
F - 21603 LONGVIC Cedex, FRANCE
≈
[inch]
UL File UL TÜV ISO 23553-1 TÜV PED VDE
mm
ISO 2768-fK - Ra 2.5 [100]
B
Spare parts
Reference
① Inlet/outlet Flange 3/4’’ with pressure tap 995001
① Inlet/outlet Flange 1/2’’ with pressure tap 995002
② Electronic block M*N/M*C 995003
③ Pressure tap 995004
④ Strainer 995005
⑤ O ring 995006
⑥ Hydraulic damper* 995007
*Only for slow opening version (M*N**S).
Accessories list
Range Reference
ADMG 010 2.0 - 10.0 mbar 8161002010
ADMG 050 2.5 - 50.0 mbar 8161006050
ADMG 150 5.0 - 150.0 mbar 8161004150
B Electric plug / ENC00_G
*SUNTEC provides another range of pressure switches adapted for direct threading on the pipelines (the F range).

10 IIM_N - Ed. 1 - May 2022
Cercate of tesng
We cerfy that all delivered products have been fully tested in accordance with SUNTEC INDUSTRIES France
Quality Management System.
According to Regulaon (EU) 2016/426.
Manufacturer’s name: SUNTEC INDUSTRIES FRANCE
Manufacturer’s address : 1 rue Lavoisier, CS 60102, F-21603 LONGVIC Cedex, France
Product descripon : Mulfunconal gas control
Type : M2 and M3
SUNTEC INDUSTIES FRANCE ceres that type M*N/M*C gas valves comply with the essenal requirements of
Regulaon (EU) 2016/426 «Gas Appliances».
: 1312CU6361
M2C55S07-2, M2C52S07-2, M2N50S07-2,
M2C55F07-2, M2C52F07-2, M2N50F07-2
M2C55F07-1, M2C52F07-1, M2N50F07-1
M3C45S07-2, M3C42S07-2, M3N40S07-2,
M3N40F07-2, M3C45F07-2, M3C42F07-2
The products are in compliance with the following direcves, regulaons and standards :
Gas appliances
Electromagnec Compability
Low voltage
Safety and control devices for burners
Automac shut-o valves for gas appliances
Automac electrical controls
Mulfunconal controls for gas burning appliances
Pressure regulators for inlet pressures up to 50 kPa
Noed body : Cergaz
Address : Immeuble Le Linéa, 1, rue du Général Leclerc, CS 60254, 92800
PUTEAUX CEDEX, FRANCE
Conformity process : Modul B+D
Longvic, october 7th 2021,
G. NOBLET
Q&E Manager

11
IIM_N - Ed. 1 - May 2022
Notes
.........................................................................................................................
.........................................................................................................................
.........................................................................................................................
.........................................................................................................................
.........................................................................................................................
.........................................................................................................................
.........................................................................................................................
.........................................................................................................................
.........................................................................................................................
.........................................................................................................................
.........................................................................................................................
.........................................................................................................................
.........................................................................................................................
.........................................................................................................................
.........................................................................................................................
.........................................................................................................................
.........................................................................................................................
.........................................................................................................................

SUNTEC INDUSTRIES FRANCE
1, rue Lavoisier - CS 60102 - F-21603 LONGVIC Cedex
Tel. +33 (0) 3 80 70 60 70 - www.suntec.fr
This manual suits for next models
17
Table of contents
Other SUNTEC Control Unit manuals
Popular Control Unit manuals by other brands
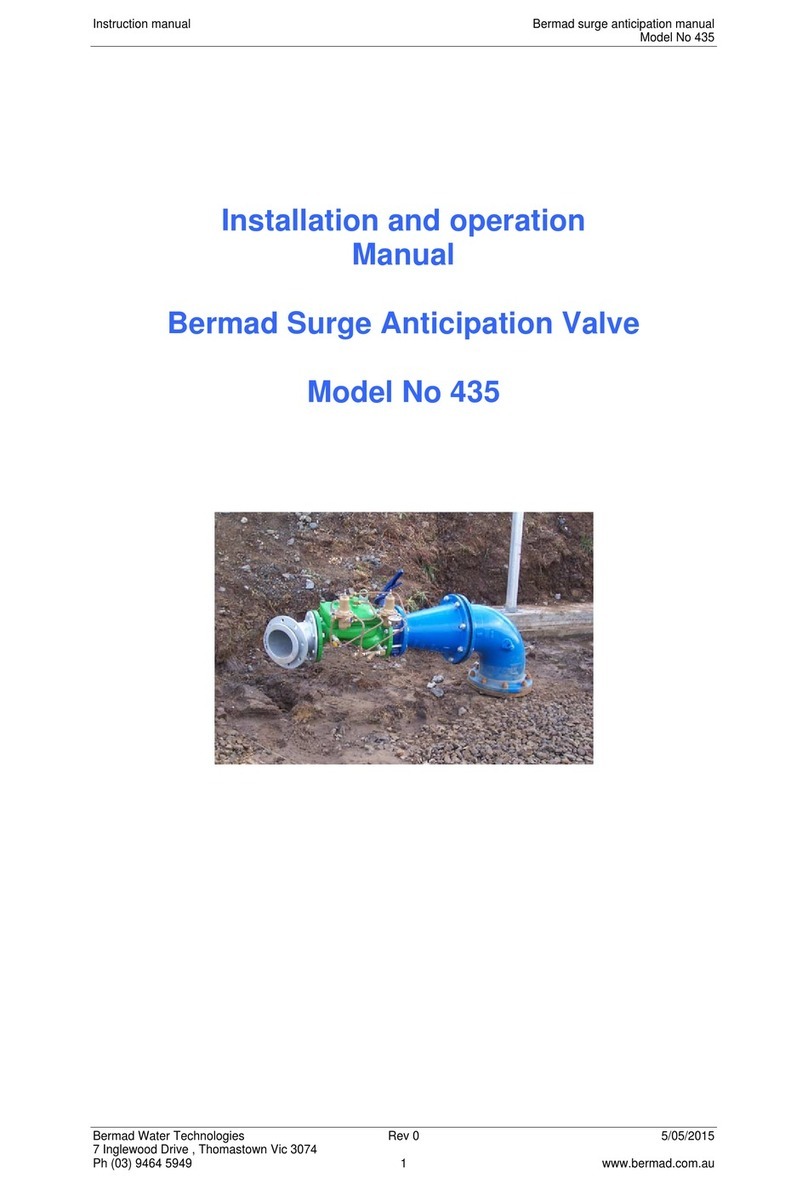
BERMAD
BERMAD 435 Installation and operation manual
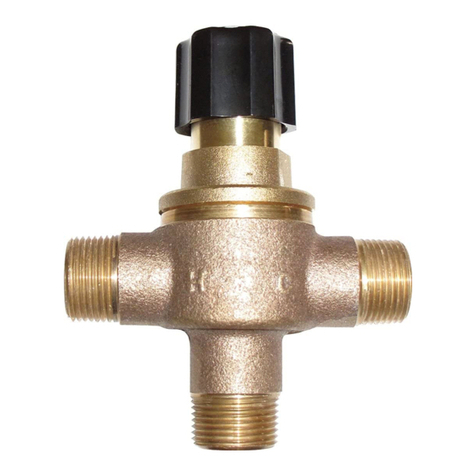
Leonard
Leonard MEGATRON 270 INSTALLATION ADJUSTMENT SERVICE

FMA Direct
FMA Direct Cellpro 4s quick start guide
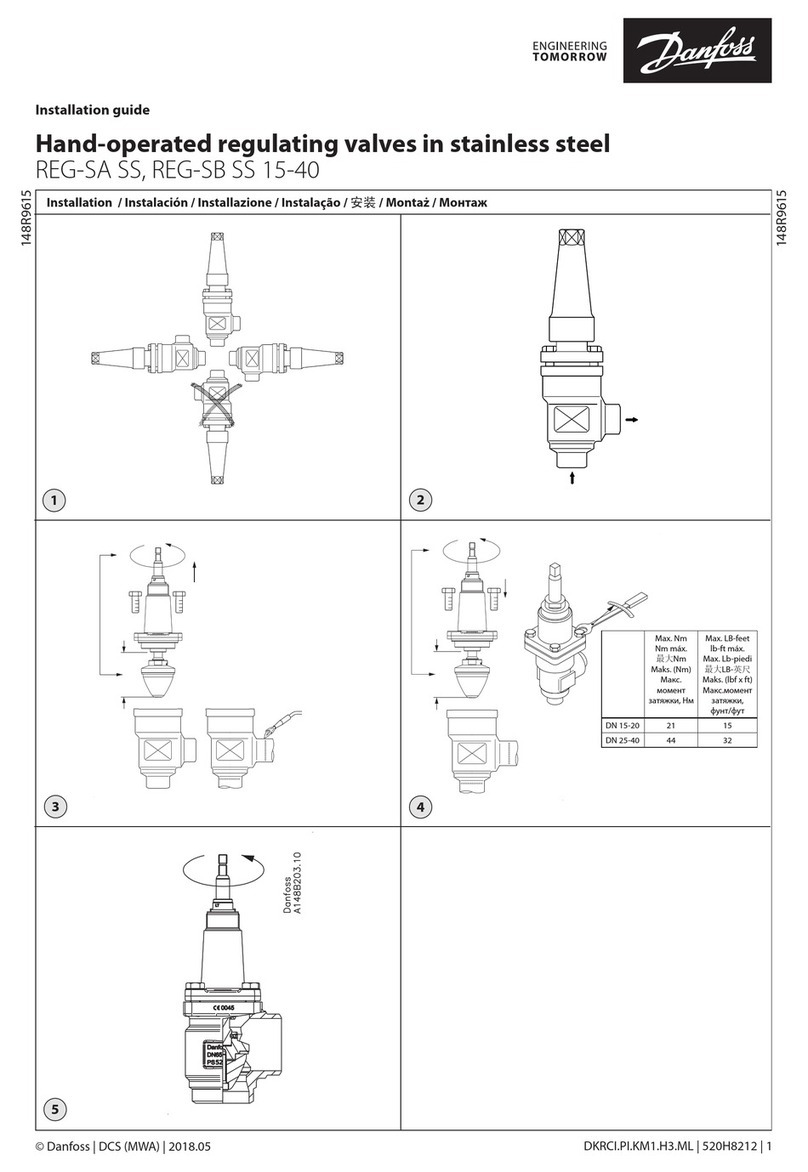
Danfoss
Danfoss REG-SA SS 15-40 installation guide
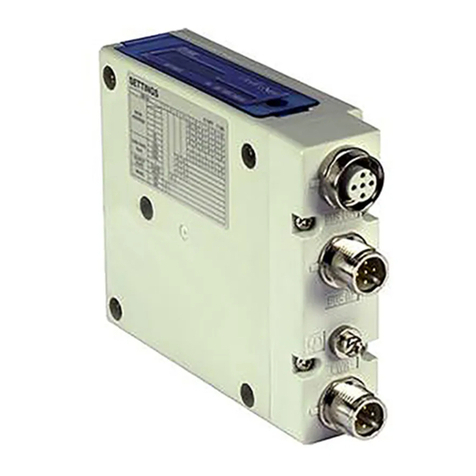
SMC Networks
SMC Networks EX260 Series Operation manual
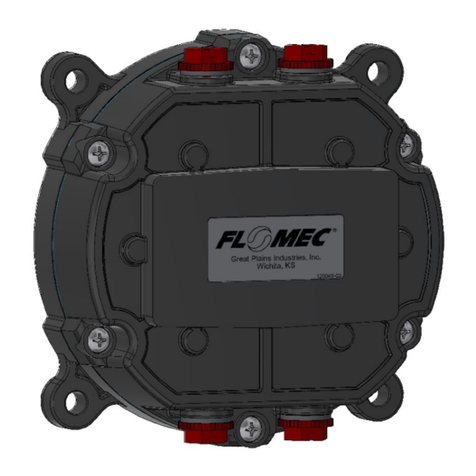
Flomec
Flomec QSI1 Products Installation Instructions