TCF ZAE Series User manual

1
INSTALLATION,
OPERATION AND MAINTENANCE
MANUAL
AIR-HANDLING
UNITS
ZAE SERIES

2
TABLE OF CONTENTS
0. INTRODUCTION
1. DESCRIPTION OF AIR TREATMENT UNIT 4
1.1 COMPOSITION 4
1.2 PERMITI ED USE 4
2. CONTROL, PACKING, TRANSPORTATION 4
2.1 INSPECTION OF SUPPLY AT THE FIRM 4
2.2 PACKING 4
2.3. LOADING, TRANSPORTATION, UNLOADING 4
3. ASSEMBLY ON SITE 5
3.1 . POST-TRANSPORTATION CHECK 5
3.2. PRESERVATION ON SITE 5
3.3. POSITIONING 5
3.3.1. Dim nsions of installation room 5
3.3.2. Bas 6
3.3.3. Vibration damping 6
3.4. ASSEMBLY OF SECTIONS 7
4. CONNECTION TO SYSTEMS AND START-UP 8
4.1. CONNECTION TO DUCTS 8
4.2. CONNECTION OF HEAT EXCHANGERS 8
4.2.1 . Wat r xchang r 8
4.2.2. Dir ct xpansion xchang r 9
4.2.3. St am xchang r 10
4.3. CONNECTION OF HUMIDIFIER SECTIONS 10
4.3.1. F d wat r 10
4.3.2. Hydraulic conn ctions for c ll block or spray
nozzl humidifi rs 11
4.3.3. Humidification with c ll block 11
4.3.4. Humidification with circulating pump 11
4.3.5. Ultrasonic, st am (subm rg d l ctrod s),
compr ss d air humidification 11
4.3.6. St am humidification with subm rg d l m nts 11
4.4. DRAINAGE AND SIPHONING 11
4.5. FILTRATION SECTIONS 12
4.6. FAN MOTOR UNIT 13
4.6.1. El ctric motors 13
4.6.1.1 . Conn ction for dir ct starting 13
4.6.1.2. Conn ction for star—d lta starting 13
4.6.1.3. Dual sp d thr -phas motor 14
4.6.1.4. P rmitt d start tim 14
4.6.1.5. R comm nd d conn ction and prot ction
acc ssori s 14
4.6.2. Fan 15
4.6.3. Driv 15
5. INSPECTION 16
5.1. PRELIMINARY CHECKS 16
5.2. INSPECTION PROCEDURES 16
5.2.1. Pow r board 16
5.2.2. Flowrat ch ck 16
5.2.3. Ch cking h at xchang r ffici ncy 17
5.2.4. Humidification syst m ch ck 18
5.3. CORRECTION OF FLOW RESISTANCE
VALUES IN CIRCUITS AND ADJUSTMENT
OF FAN AlR—MOVlNG PERFORMANCE 18
5.3.1. Insuffici nt l ngth of div rging duct s ction
b tw n Unit d liv ry inl t and obstruction 18
5.3.2. Elbows 19
5.3.3. Control air locks 19
. MAINTENANCE 20
6.1. FOREWORD 20
6.2. FILTRATION SECTIONS 20
6.2.1 . R conditionabl synth tic filt rs 20
6.2.2. M tal filt rs 20
6.2.3. Rotary filt rs 21
6.2.4. R conditionabl bag filt rs 21
6.2.5. Non-r conditionabl m dium/ high
ffici ncy filtration s ctions 21
6.2.5.1. Non-r conditionabl bag filt rs 21
6.2.5.2. Absolut filt rs 21
6.2.5.3. R plac m nt load loss chart 22
6.2.6. Activ carbon filt rs 22
6.3. HEAT EXCHANGERS 22
6.3.1 . Wat r xchang rs 22
6.3.2. Extraction of h at xchang r 22
6.3.3. St am xchang r 23
6.3.4. Dir ct xpansion xchang rs 23
6.4. HUMIDIFICATION SECTIONS 23
6.4.1. Humidification with spray nozzl s 23
6.4.2. Humidification with c ll block 23
6.4.3. Humidification with circulating pump 23
6.4.4. Ultrasonic, st am (subm rg d l ctrod s),
compr ss d air humidifi rs 23
6.4.5. St am humidification with subm rg d
l m nts 23
6.5. FAN SECTION 24
6.5.1. Fan 24
6.5.2. Motor 24
6.5.3. Driv 24
6.5.3.1. D t rmining b lt t nsion 24
6.5.3.2. Driving b lt r plac m nt 25
6.5.3.3. Driv with multipl rac pull ys 25
6.6. HEAT RECUPERATORS 25
6.6.1. Crossov r flow static r cup rator 25
6.6.2. Rotary r cup rator 25
6.6.3. H at pip r cup rator 26
6.7. ACCESSORIES 26
6.7.1. Control air locks 26
6.7.2. Ext rnal air intak grill s 26
6.7.3. Drip s parator 26
6.7.4. Sil nc r 26
6.8. TROUBLESHOOTING 26
6.8.1 . R duction in flowrat 26
6.8.2. Incr as in flowrat 26
6.8.3. R duc d xchang r ffici ncy 26
6.8.4. R duc d h at r cup rator ffici ncy 26
6.8.5. R duc d humidifi r ffici ncy 27
6.8.6. Abnormal nois l v l 27
6.9. MAINTENANCE AGREEMENT 27
7. SAFETY 27
7.1. SAFETY-RELATED FEATURES OF
AIR TREATIVENT UNIT 27
7.2. SAFETY NOTICES APPLIED TO THE
UNITS 27
7.3. PRACTICAL ACCIDENT—PREVENTION
TIPS 27
7.4. EC DECLARATTON OF COMPLIANCE 28
8. WARRANTY 29
9. UNIT INSPECTION SHEET 30

3
0. INTRODUCTION
This manual has b n compil d by TCF Srl to provid th
install r, Custom r and Us r with instructions int nd d
to nsur th prop r manag m nt and us of th Air
Tr atm nt Unit mod. ZAE and AZE-C, from d liv ry to
commissioning.
Th r comm ndations that follow ar int nd d to
nsur continuous op ration of th Air Tr atm nt Unit
and long machin lif .
Th proc dur s d scrib d b low should b follow d by
skill d p rsonn l with a good working knowl dg of air-
conditioning, syst ms ngin ring and air tr atm nt
units, v n though th unit can b op rat d by thos
unfamiliar with air tr atm nt thanks to th machin 's
simplicity of d sign.

4
DESCRIPTION OF AIR TREATMENT UNIT
1.1. COMPOSITION
In its most compl t v rsion, th unit, in its monoblock
or brok n down configuration, compris s:
-On or mor air lock intak s ction
-Filtration s ction
-R cov ry s ction
-H at xchang r s ction (h ating, cooling, post-
h ating)
-Humidifi r s ction
-V ntilation s ction (d liv ry, intak —outl t)
-Sil ncing s ction.
1.2. PERMITTED USE
TCF Air Tr atm nt Units ar d sign d xclusiv ly for
CIVIL AND INDUSTRIAL AIR TREATMENT
In th cas of CORROSIVE and/or EXPLOSIVE air flows
a numb r of sp cial t chnical modifications must b
mad at th d sign stag which, tog th r, adapt th
machin for th tr atm nt of sp cial typ s of flow.
Th Air Tr atm nt Unit must at all tim s b us d
strictly in accordanc with th d sign conditions
stablish d at th tim of contract in agr m nt with
th custom r. ANY OTHER USE SHALL CONSTITUTE
IMPROPER USE AND IS THEREFORE DANGEROUS.
THE MANUFACTURER MAY NOT BE HELD LIABLE
FOR DAMAGE CAUSED BY NON—STANDARD USE OR
ANY USE NOT ENVISAGED IN THE CONTRACT
2. CONTROL, PACKING, TRANSPORTATION
2.1. INSPECTION OF SUPPLY AT THE FIRM
Prior to shipping, ach TCF Air Tr atm nt Unit is
subj ct d to all th functional t sts list d on th attach d
UNIT INSPECTION SHEET (Form E.1.).
Th ch cks p rform d r gard:
- g n ral machin dim nsions
- corr ct ass mbly of th various parts and s ctions
- complianc with th various saf ty rul s in forc
- int grity of all th syst m‘s compon nt parts
- application of th id ntification, op ration and saf ty
notic s.
On compl tion of th Insp ction, th Chi f Insp ctor
appli s th EC mark d monstrating product complianc
with pr vailing Europ an Union machin dir ctiv s.
2.2. PACKING
Th Air Tr atm nt Units ar usually suppli d as fully-
ass mbl d monoblocks. Only if th custom r xpr ssly
r qu sts it can th units b brok n down into s v ral
s ctions to facilitat transportation and carriag through
narrow ap rtur s, stairs or corridors. Transportation of
th machin s, both monoblock and brok n down, can b :
- normal
- sp cial.
In th form r cas , TCF Srl do s not pack th machin . In
th cas of sp cial transportation, th packing r qu st d
is agr d at th tim of contract and is ntir ly for th
custom r's account.
Fragil compon nts suppli d s parat from th Unit,
such as humidifi rs, xchang rs, r cup rators, filt rs,
control boards, tc. ar always d liv r d pack d.
2.3. LOADING, TRANSPORTATION, UNLOADING
TCF Srl disclaims all liability for damag sustain d by th
Air Tr atm nt Units during loading, unloading and
transportation. W th r for r comm nd that sp cial
pr cautions b tak n, including:
- Th load must b firmly s cur d to nsur its int grity
during transportation
- Handling must b p rform d without x rting forc on
proj cting acc ssori s (hydraulic attachm nts, handl s,
hing s, air locks, prot ction roof)
- Do not ov rturn th s ctions as you may oth rwis
br ak int rnal supports, compon nts and damp rs
- Do not subj ct th Unit to viol nt impacts as you may
damag its int grity
- If a forklift truck is us d during th loading, unloading
and handling op rations, th forks of th truck must b
at l ast th sam l ngth as th unit to nsur stability
(fig. 1)
- if th Air Tr atm nt Unit is fitt d with a continuous
st l bas , handling may b accomplish d with a cran ,
using cabl s firmly s cur d to rods (suffici nt for th
str ss involv d) passing through th hol s provid d in
th bas .

5
If a cran is us d, proc d as shown in th illustration,
using spac rs to prot ct th structur (fig. 2).
- During transportation, prot ct th unit from
atmosph ric ag nts. Sp cial car must b tak n if th
unit is suppli d disass mbl d or d sign d for int rnal
us .
3. ASSEMBLY ON SITE
3.1. POST-TRANSPORTATION CHECK
Wh n th Air Tr atm nt Unit arriv s on sit , w
r comm nd you to mak a car ful insp ction of th
structur and th compon nt parts of th unit.
Should you com across damag sustain d during
transportation, you must r port it on th fr ight bill. Th
carri r must imm diat ly til a r port of th accid nt to
obtain comp nsation from th insuranc company
3.2. PRESERVATION ON SITE
In ord r to k p th Air Tr atm nt Unit in good and
ffici nt condition on sit , th following st ps must b
tak n first:
- Prior to installation, position th Unit and th
acc ssori s in a plac affording th b st possibl
prot ction against accid ntal knocks, dust and
atmosph ric ag nts
- Car fully cov r th inl ts and outl ts to pr v nt for ign
matt r from nt ring th unit and damaging th int rnal
compon nts
- Extract th pr -filt rs from th Unit and put th m in a
prot ct d plac to pr s rv th ir filtration ffici ncy
This is why th sup rior ffici ncy filt rs ar d liv r d
pack d; th y must b k pt in th ir packag s until th
unit is put into s rvic
- Ch ck that th hydraulic conn ctions ar prot ct d by
th r l vant caps as th y w r on d liv ry to th TCF
plant. lf th y ar not, plug th m in ord r to prot ct th
xchang rs.
3.3. POSITIONING
3.3.1. Dim nsions of installation room
Th Air Tr atm nt Unit installation room must b of
suffici nt siz to p rmit asy insp ction, maint nanc
and compon nt r plac m nt.
Accordingly, th following dim nsions ar
r comm nd d [fig. 3):

6
- h at xchang r xtraction sid
Minimum distanc Lb = (B+O.2) m
wh r B = machin width (m)
- insp ction sid Minimum distanc Li = 1.2 m
lf you do not hav th minimum spac r quir m nts as
sp cifi d abov , th Unit doors can, on r qu st, b
fitt d using PVC clamps inst ad of hing s. In this cas
th minimum distanc will b Li = 0.7 m
3.3.2. Bas
Th p rman nt installation of th Air Tr atm nt Unit
may b mad :
- dir ctly on th floor (Hg. 4a)
- on a concr t b d (fig. 4b)
- on a st l s ction b d (fig. 4c)
- on a susp nd d bas (fig. 4d)
Both th floor and th b ds must b capabl of
withstanding th machin w ight to within th
r quir d saf ty margins.
Th Air Tr atm nt Unit must b position d on a
horizontal surfac so as to pr v nt:
- damag to th fan motor units caus d by un v n
w ights on th vibration damp rs
- malfunctioning of th cond nsat drains
- difficulty in op ning and closing th insp ction doors.
Th horizontal alignm nt of th support surfac must
b ch ck d with a SPIRIT LEVEL; adjustm nts may b
mad using STEEL SHIMS.
3.3.3. Vibration damping
In ord r to nsur ff ctiv prot ction against
vibrations, th Air Tr atm nt Unit must b install d as
follows:
- suitabl DAMPERS in mat rial d sign d to withstand
th w ight involv d must b plac d b tw n th
machin and th support surfac
- th Unit must not b fast n d dir ctly with scr ws but
by m ans of brack ts (fig. 5).
Ev n in th cas of susp nd d installation of th Unit, th
supports must not b scr w d dir ctly into th c iling;
vibration damping mat rial must always b plac d
b tw n th supports and th c iling (fig. 6).
It, for r asons conn ct d with incr as d prot ction,
spring-op rat d or rigid rubb r vibration damp rs ar
r quir d b tw n th machin bas and th support
surfac , th hydraulic conn ctions must b fitt d with
appropriat JOINTS.

7
3.4 ASSEMBLY OF SECTIONS
If th Air Tr atm nt Unit is brok n down into two or
mor s ctions. proc d as follows:
- Ch ck th modul ass mbly ord r on th TCF
working drawing.
- R mov th mat rial r quir d for ass mbly, suppli d
on d liv ry, from th contain r locat d insid on of
th insp ction doors.
- Cl an th st l s ctions at th point of conn ction of
th modul s and tit th SELF—ADHESIVE SEALING
STRIP provid d (fig. 7).
Th sam strip must also b fitt d to th duct
conn ction flang s.
- S t th individual s ctions s t by sid , using a SPIRIT
LEVEL to ch ck that th ass mbl d parts ar p rf ctly
align d and l v l. (fig. 8)
- Fast n th s ctions tog th r with scr ws in th hol s
provid d.
Th hol s ar locat d on th insid of th corn rs and,
in th cas of dim nsions gr at r than 1.3 m, also in a
midway position.
Th scr w-fast ning ar as can usually b acc ss d
from th insp ction doors. Oth rwis , you must
r mov th pan ls n xt to th ar a involv d.
Should th Unit b install d outdoors, in addition to th
st ps list d abov , th points of conn ction of th
individual modul s must also b s al d with
wat rproofing silicon (fig. 9).
Sp cial car must b tak n with th roofing to afford
prot ction against th l m nts: th two dg s will b
joint d by m ans of a bayon t syst m, assist d by
silicon tr atm nt or a sp cific s al (fig. 10).

8
4. CONNECTION TO SYSTEMS AND START-UP
4.1. CONNECTION TO DUCTS
At th points of conn ction to th air ducts, th Air
Tr atm nt Units hav a smooth or a flang d surfac .
In ord r to optimis th conn ction with th ducts, you
must:
- cl an th conn ction dg s b tw n duct and unit
- fit a s al to th flang s in ord r to pr v nt air
infiltration
- tight n th conn cting scr ws firmly
- tr at th joint with silicon to nhanc th s al.
If th conn ction is mad with rubb ris d canvas
joints, mak sur th y ar not taut on compl tion of
ass mbly so as to pr v nt damag or th transmission
of vibrations.
In ord r to nsur th tightn ss of th conn ctions and
th int grity of th unit structur , th w ight of th
ducts must und r no circumstanc s b ar down on th
unit. Th ducts must b support d by BRACKETS.
4.2. CONNECTION OF HEAT EXCHANGERS
In ord r to pr v nt damag to th xchang r at th
joint b tw n th st l manifold and th copp r
circuits, you must:
- Us a pip wr nch to apply forc in th opposit
dir ction wh n making th conn ction to th mains
pip (fig. 1.1)
- Fit brack ts to support th conn cting pip s.
Th w ight of th pip s must und r no circumstanc s
b ar down on th manifold.
4.2.1. Wat r xchang
In ord r to nsur an optimum h at xchang , you must:
- WASH th h at xchang r b for conn cting it to th
wat r mains
- onc install d in a workmanlik fashion, any air pr s nt
in th hydraulic circuit must b xp ll d using th
r l vant valv .
To allow asy xtraction of th xchang r during
maint nanc :
- th conn ctions to th mains must b mad in such a way
as to allow r moval of th xchang r
- ON-OFF VALVES must b install d to xclud th h at
xchang r from th hydraulic circuit
- A VALVE must b install d on th low r manifold to allow
compl t drainag , and a VALVE must b titl d to th
upp r manifold to v nt th air from th xchang r (fig. 12)
Th normal h at xchang in a h ating or cooling wat r
xchang r occurs in REVERSE CURRENT (fig. 13).
In ord r to pr v nt th formation of ic in th h ating
units in th pr s nc of particularly low outsid
t mp ratur s, an EQUICURRENT h at xchang syst m
may b provid d (fig. 14).
This configuration must b d t rmin d at th d sign stag
and not during installation, sinc an obvious r duction in
ffici ncy will r sult if a h at xchang r siz d for r v rs
curr nt h at xchang is us d for quicurr nt op ration.

9
Th diagram (Hg. 15) shows th "standard" installation of
a wat r-typ h at xchang r.
4.2.2. Dir ct xpansion xchang r
In ord r to p rmit op ration of th whol syst m, mak
sur that th h at xchang occurs in r v rs curr nt
b for )making th conn ctions to th h at xchang r (fig.
16).
Th cooling circuit must b compl t with all th
n c ssary flow control, filtration and saf ty d vic s; th
pip must b siz d to allow prop r circulation of th
compr ssor prot ction oil.
W r comm nd you prot ct th xchang r against
vibrations to pr v nt th lik lihood of ruptur at th joint
b tw n manifolds and copp r pip s.
In ord r to nsur corr ct op ration of th th rmal
xpansion valv , th bulb of th valv must b in p rf ct
contact with th intak lin and fitt d on th outsid of
th air flow so as not to b aff ct d by it.
Sp cial car must b tak n with th SIPHONING of th s
xchang rs to nsur th maximum h at xchang and
corr ct ntrainm nt of th oil in th circuit. Th diagram
in fig. 16 shows a siphoning syst m without division of
h ad.
Fig. 17 Syst m siphoning xampl with division of
cooling h ad.
Fig. 18 shows an incorr ct siphon syst m (a) and a
corr ct on (b), in th cas of installation of th
compr ssors at a point b low th vaporator.

10
4.2.3. St am xchang r
In ord r to pr v nt dang rous WATER HAMMERING that
could ruptur th xchang r and l ad to th scap of
st am und r pr ssur , you must:
- mak sur that th Air Tr atm nt Unit is l v l on
installation
- corr ctly siz th flow control d vic s and th
cond nsat drains
- nsur th corr ct angl of inclination of th pip s
comprising th st am circuit.
B for starting up th syst m mak sur that th h at
xchang r is corr ctly conn ct d to it (fig. 19)
TCF installs st am batt ri s with angl d or v rtical pip s
(fig. 19) to nsur corr ct drainag of th cond nsat and
pr v nt it from accumulating insid th syst m. In Air
Tr atm nt Units with this typ of xchang r sp cial car
must b tak n to nsur that th bas is l v l (s s ction
3.3.2.).
Th st am syst m must b compl t with all th
n c ssary r gulating, filtration and saf ty d vic s, which
must b corr ctly siz d.
Each h at xchang r must b fitt d with a cond nsat
drain, which must b ov rsiz d to allow drainag of th
gr at r quantity of cond nsat that is form d during
syst m start-up.
Provision must also b mad for th automatic shut-off of
th st am f d in th cas of fan motor unit stop.
4.3. CONNECTION OF HUMIDIFIER SECTIONS
4.3.1 . F d wat r
TCF r comm nds f ding th humidifi r s ctions with
wat r that has a TOTAL HARDNESS of b tw n 15°F and
25°F. B low 15°F th aggr ssiv n ss of th wat r could
damag th unit compon nts, and th us ful lif of th
r sins in th soft ning syst m would b drastically
short n d.
Ov r 25°F th ffici ncy of th humidifi r syst m would
quickly diminish du to th build-up of scal .

11
4.3.2. Hydraulic conn ctions for c ll block or spray
nozzl humidifi rs
Th hydraulic conn ctions must b arrang d so as to
p rmit asy xtraction of th vaporating block or th
distribution ramp.
Th drain and ov rflow must b fitt d with a siphon a not
conn ct d dir ctly to th drainag syst m pip (s ction
4.4.). This op ration is xtr m ly important in ord r to
pr v nt tank ov rflows and r sulting flooding of th unit
and th sit of installation.
W r comm nd you install th following d vic s on th
hydraulic conn ction to th mains:
- a filt r
- a pr ssur gaug
- a flow control valv that also allows xclusion of th
humidification syst m.
4.3.3. Humidification with c ll block
Prior to start-up, ch ck that th c ll block is corr ctly
install d (s ction 6.4.2.).
At first-tim start-up, ch ck that th c ll block is v nly
w tt d; if you obs rv wat r j ts on its surfac , r stor
th r gular wat r flow by m ans of th tap.
4.3.4. Humidification with circulating pump
To avoid damaging th pump at first-tim start-up, ch ck
that:
- Th hydraulic conn ction has b n mad prop rly, in
accordanc with pr vailing r gulations
- Th tank is cl an and fr of any r sidu r sulting from
installation that could caus its blockag
- Th wat r l v l insid th tank is k pt at 20-30 mm
b low th ov rflow.
Should a situation aris in which th r is no wat r in th
tank, th pump motor would ov rh at and b irr parably
damag d. Conv rs ly, if th r is too much wat r in th
tank, an ov rflow may r sult, l ading to flooding of th
unit and th installation room.
4.3.5. Ultrasonic, st am (subm rg d l ctrod s),
compr ss d air humidification
For Air Tr atm nt Units with th abov -list d typ s of
humidification, you should consult th MANUAL suppli d
with th humidifi r.
4.3.6. St ams humidifi r with subm rg d l m nts
In ord r to mak th syst m op rational, you must:
- Conn ct up th l m nt l ctrically in accordanc with
pr vailing standards
- Conn ct th humidifi r to th mains n twork; an on-off
valv must b includ d to xclud th humidification
s ction from th lin
- Conn ct th ov rflow to th drain to pr v nt flooding in
th cas of float malfunction.
B for starting up th humidification syst m, you must:
- ch ck th prop r op ration of th microswitch which, in
ord r to prot ct th l m nt, int rrupts th flow of
curr nt wh n th wat r l v l drops b low a p rmitt d
l v l.
- ch ck th s tting of th float to pr v nt th ov rflow of
wat r from th tank.
4.4 DRAINAGE AND SIPHONING
B for positioning th Air Tr atm nt Unit mak sur you
hav suffici nt room to install th siphon and drainag
pip .
Th humidification and cooling xchang r s ctions of th
TCF Units ar fitt d with a thr ad d drain pip proj cting
lat rally about 80 mm.
To allow th r gular outflow of wat r v ry drain must b
fitt d with a corr ctly siz d SIPHON (fig. 22).

12
In ord r to pr v nt ov rflowing from th cond nsat
coll ction tank and r sulting flooding of th machin and
th room in which it is install d, th siphon must b fitt d
with a DRAIN VALVE to p rmit th r moval of impuriti s
that s ttl on th bottom (fig. 23).
In ord r not to und rmin th op ration of th drainag
syst m, pr ssuris d siphons and siphons op rating und r
suction pr ssur must not b conn ct d tog th r.
THE WASTE PIPE (fig. 24) l ading to th drainag
n twork:
- Must not b conn ct d dir ctly to th siphon in ord r to
absorb air or wast backflow and to p rmit dir ct visual
control of th corr ct outflow of wast wat r
- Must hav a diam t r larg r than th drain pip and a
minimum angl of 2% to nsur prop r functioning.
4.5. FILTRATION SECTIONS
Ch ck th corr ct installation of th pr filt rs locat d in
th r l vant count r-fram s with saf ty springs or guid s.
Th l ctrical conn ction and installation instructions for
th rotary filtration s ction ar provid d in th sp cific
manual provid d. Th instructions for introduction of th
r conditionabl filtration diaphragm ar s t out in th
maint nanc chapt r (6.2.3.).
Aft r r moving th filt rs from th packing (in which th y
ar suppli d to pr v nt d t rioration during transport
and on sit ), plac th bag, absolut and activ carbon
filt rs in th r l vant s ction, taking car to nsur rigid
ass mbly and p rf ct gask t tightn ss.
This op ration must b p rform d about on hour aft r
th unit has b n start d up for th first tim , wh n dust
and installation r sidu hav b n r mov d from th
ducts. In this way th non-r conditionabl filtration
s ctions will b pr s rv d.
On r qu st, TCF suppli s diff r ntial analogu pr ssur
gaug s (fig. 25) or oil-column, gaug s (fig. 26) of th typ s
shown.
Fig. 25
Fig. 26

13
4. . FAN MOTOR UNIT
4.6.1. El ctric motors
B for start-up:
- Insp ct th motor control board and ch ck that th
motor prot ction d vic s ar siz d for th maximum
amp rag . corr sponding to th rat d valu on th plat .
If th prot ction d vic s ar siz d for an amp rag in
xc ss of th rat d valu , you must mak sur that th
working rang is suffici nt.
- Th th rmistors (op rating voltag 1 V) must not b
conn ct d to th l ctric motor pow r supply lin , as
oth rwis th y would b irr parably damag d
- Ch ck that th mains supply voltag is suit d to that of
th motors as indicat d on th r l vant plat s.
4.6.1.1. Conn ction for dir ct starting
Th simpl st l ctric motor start—up syst m is obtain d
by conn cting th motor dir ct to th pow r supply.
How v r, this m thod has limitations du to th high
start-up curr nt (pick-UD); this typ of start-up is
r comm nd d for pow r ratings of up to 5.5 KW at which
TCF installs 4 pol , 220/380 V thr —phas motors as
standard.
Th wiring diagrams ar shown in fig. 27.
4.6.1.2. Conn cting with d lta—star start r
If th motor start-up curr nt xc ds th valu p rmitt d
by th pow r supply you may d cid to opt for d lta-star
starting.
For this purpos TCF installs dual voltag 380/660 V
motors on its Air Tr atm nt Units starting from an output
of 7.5 KW, th r by allowing th motor to function
normally at 380 V (d lta conn ction) and to start-up at
660 V (star conn ction).
This arrang m nt r duc s th starting curr nt to
approximat ly 30% of th curr nt involv d in th cas of
dir ct starting.

14
4.6.1.3. Dual sp d thr -phas motors
Th diagram in fig. 29 shows th conn ction of a TWO-
SPEED MOTOR with two s parat windings to th pow r
supply. TCF installs motors of this kind on its Units:
- 220/380 V for pow r ratings up to 5.5 kW
- 380/660 V for pow r ratings ov r 7.5 kW.
This typ of l ctric motor p rmits d lta-star conn ction
with start r.
Th two-sp d motors with a singl DAHLANDER
commutabl winding (fig. 30) (sid conn ction) off r th
advantag of g n rating gr at r pow r than motors of th
sam siz but with s parat windings.
4.6.1.4. P rmitt d start tim
With r gard to th t mp ratur incr as . th start-up
tim of a motor may not xc d th valu shown in tabl
1. In th cas of r p at d starts with unchanging rat d
pow r th t mp ratur of th motor must b th sam as
it was b for th first start. Th r for , in ord r for th
valu s in th tabl to b valid. it is assum d that th motor
is cold.
4.6.1.5. R comm nd d conn ction and prot ction
acc ssori s
Tabl 2 r comm nds, d p nding on th l ctric motor
install d in th Unit:
- th cross-s ction of th conn cting cabl , in copp r or
aluminium
- th ov rload cut-out
- th fus
lsp = starting curr nt int nsity
IN = rat d curr nt int nsity

15
4.6.2. Fan
B for start-up, carry out th following ch cks:
- mak sur that th fan wh l is functioning corr ctly by
turning it manually
- ch ck that any saf ty clamps fitt d to pr v nt damag
during transportation hav b n r mov d from th
damp rs (fig. 31).
4.6.3. Driv
B for starting th Air Tr atm nt Unit, ch ck:
- th t nsion of th “V“ b lts (s ction 5.5.4.)
- that th pull ys ar align d (s ction 5.5.4.)
- that th dow ls, shown in fig. 32 in th ir possibl
installation positions, ar doing th ir job of s curing th
pull ys to th hubs.
4.6.4. Nois l v l
Th computation and control of nois missions has today
b com particularly important, both during th d sign
and installation phas s.
Th sound pr ssur valu s of our machin s ar indicat d
In our t chnical catalogu s or can b suppli d dir ctly by
our T chnical D partm nt according to th r qu st d air
moving charact ristics.
B ing th r for awar of th sound missions produc d
by th Unit, th D sign r must mak sur that, in tr at d
nvironm nts, maximum valu s laid down by curr nt
r gulations ar not xc d d.
It must how v r b str ss d that v ry nvironm nt has
its own acoustic charact ristics which can consid rably
aff ct sound pr ssur valu s of m chanical v ntilation
syst ms. THE NOISE LEVEL DATA SUPPLIED BY US
SHOULD CONSEQUENTLY BE CONSIDERED AS A
CALCULATION BASE FOR MORE lN-DEPTH
CONSIDERATIONS WHICH TAKE INTO ACCOUNT THE
SYSTEM AND BUILDING STRUCTURE AS A WHOLE.

16
5. INSPECTION
5.1. PRELIMINARY CHECKS
- THE DELIVERY AND OUTLET HYDRAULIC
CONNECTIONS must b compl t d. Ch ck th pr ssur
s al of th various circuits and th fr passag th y
afford to th carrying fluid
- THE INTAKE AND DELIVERY AIR-MOVING
CONNECTIONS must b compl t d. Ch ck th tightn ss of
th lin s against air l aks in both th main s ctions and
th various branch s l ading to th utilisation points
- THE EXTERNAL AIR INTAKES AND OUTLETS must
pr s nt ntir ly fr passag s. If th Units r main on sit
for som tim prior to insp ction, mak sur that th
passag s hav not b com obstruct d by for ign matt r
and that th flow control locks ar not in th fully or
partly clos d position. TCF fits standard on outdoor
installations sp cial "RAIN-SHIELDS" compl t with l af-
coll ction n t with a m sh siz of 10 mm x 1 mm. It is
how v r advisabl to ch ck that th s air intak s ar fr
of obstructions.
Similarly you must mak sur that th r ar no air locks
in th clos d position in th AIR DISTRIBUTION CIRCUITS
and that any saf ty syst ms install d, such as lir or
smok gat s, ar not activat d and blocking th air
passag
- THE CARRIER FLUIDS such as hot or sup rh at d wat r;
st am, cool d wat r glycol mixtur s or cooling gas s must
b availabl in th actual conditions (t mp ratur and
pr ssur ) consid r d at th d sign stag
- THE POWER AND CONTROL BOARDS must b suppli d
with th normal op rating voltag
- OUTSIDE WEATHER CONDITIONS, DIFFERENT FROM
THOSE CONSIDERED ATTHE DESIGN STAGE, must b
ass ss d and mad allowanc for so as to nsur that th
insp ction is r liabl .
5.2. INSPECTION PROCEDURES
5.2.1. Pow r board
Insp ct th motor control board and ch ck that th motor
prot ction d vic s ar siz d for th maximum amp rag
corr sponding to th rat d valu .
lf th prot ction d vic s ar siz d for an amp rag in
xc ss of th rat d valu , you must mak sur that th
working rang is suffici nt.
5.2.2. Flowrat ch ck
- Using an oil or wat r column pr ssur gaug or an
analogu and/or digital gaug , ch ck th FLOW
RESISTANCE in th various filtration s ctions and
cons qu ntly th ir fouling factor. Th TREATED AIR
FLOW can b d t rmin d with a good d gr of pr cision
on th basis of th filt rs' op rating curv and th
working lif consid r d at th d sign stag .
To mak this ch ck you must first tak pr ssur r adings
at th PRESSURE POINTS in front of and b hind ach
filtration s ction (on r qu st, TCF can provid th
r l vant attachm nts during manufactur )
- Compar th flow rat valu obtain d as d scrib d
abov with th valu obtain d from th following
formula:
Q = 3600xSxV wh r :
Q = flow rat in m“/h
V = air v locity in Ws
S = passag ar a in m2
Th v locity valu "V" can b m asur d with hot-wir or
r volving-van an mom t rs.
You must d duct from th front ar a of th grill s or
inl ts th ar a lost through th pr s nc of th conv ying
fins in ord r to consid r just th NET PASSAGE SECTION.
Th ar a occupi d by th fins can b obtain d from th
t chnical sp cifications and is, on av rag , approximat ly
15% of th total ar a.
In ord r to tak VELOCITY MB\SUREMENTS with th
HOFWIRE ANEMOMETER, hol s of suffici nt diam t r to
allow th introduction of th t l scopic prob must b
mad in th ducts.
You should s l ct straight duct s ctions at l ast 2.5
quival nt diam t rs in l ngth or as far away as possibl
from obstructions or points of probabl turbul nc . In
ord r to obtain r liabl flow rat m asur m nts, a
PERFORATED GRID must b mad in th duct according
to th "point sampling" m thod shown in fig. 33.

17
Th mor turbul nt th air flow in th duct ( valuat d by
broad d viations b tw n on m asur m nt and th
n xt) th d ns r th m sh s in th sampling grid will b .
Th REFERENCE MEASUREMENT is th arithm tic m an
of th m asur m nts tak n.
Using a REVOLVING-VANE ANEMOMETER a s ri s of
VELOCITY MEASUREMENTS must b tak n on th
xt rnal air intak s (if th Unit is configur d for outsid
air only) or at th intak grill s or d liv ry inl ts.
Th r volving-van an mom t r is not r liabl for
m asur m nts r lat d to an mostatic or high-induction
diffus rs.
Th r volving-van an mom t r is r comm nd d wh n
m asur m nts ar tak n on a maximum of 2 or 3 intak
grill s so as to avoid summing tog th r m asur m nt
rrors that would l ad to an unacc ptabl calculation of
th hourly flow. It is th r for cl ar that, for
m asur m nts on 4 or mor diffusion inl ts, th
r liability of th m asur m nt is compromis d and may
only b us d as an approximat r f r nc or as a rough
ch ck on mor accurat m asur m nts mad at on or
two positions on th intak duct
- Th TCF T chnical D partm nt r comm nds you
doubl -ch ck th flow rat r sults obtain d as d scrib d
abov , using th charact ristic curv of th fan wh l
us d (graph 1 shows an xampl ):
- id ntify th curv corr sponding to th fan's rpm.
- id ntify th curv corr sponding to th absorb d pow r
at th shaft (P), pr viously calculat d using th formula:
GRAPH 1
Th CURRENT INTENSITY m asur m nt of th fan motor
units und r op rating conditions should b mad on th
r mot control pow r switch s insid th control board,
using an amp rom t r clamp.
Und r no circumstanc s must th m asur m nts b mad
dir ctly on th motor t rminals sinc this is possibl only
with th insp ction door op n, a condition that would
alt r th l ngth of th air circuit and th r for th
working point of th fans.
- D sc nd v rtically from th point of int rs ction of th
pow r and rpm curv s to obtain th FLOWRATE valu on
th x-ax s.
5.2.3. Ch cking h at xchang r ffici ncy
Ch ck th EFFICIENCY OF THE HEAT EXCHANGERS by
m asuring th t mp ratur of th air and th carri r fluid
at th inl t and outl t with t mp ratur gaug s fitt d with
t l scopic contact prob . Th s m asur m nts may b
mad only aft r you hav ch ck d:
- corr ct conn ction to th distribution circuits (s ction
4.2.
- compl t d -a ration of th circuits
- complianc of fluid t mp ratur valu s with th d sign
valu s
- prop r op ration of th l ctronic adjustm nt
- corr ct op ning and closing of th mixing valv s and th
oth r xchang r control d vic s install d (div rt r and
ch ck valv s, ON/OFF or modulating s rvomotors on air
locks, tc).
Th AIR TEMPERATURE MEASUREMENTS must b mad
with a t l scopic t mp ratur gaug through hol s mad
in th unit ducts or pan ls upstr am and down-str am of
th xchang rs to b ch ck d.
Th s nsitiv l m nt of th t mp ratur gaug must b
plac d insid th duct or th Unit so that it is dir ctly in
th path of th air flow, avoiding "d ad zon s" ( .g. by th
walls on th h at xchang r manifolds) which would
falsify th m asur m nts (fig. 34).
On compl tion of th op ration CLOSE THE HOLES mad
with plugs.

18
5.2.4. Humidification syst m ch ck
- Ch ck that th humidification syst m is functioning
corr ctly, and particularly th xact humidistat or
r gulator l ctrical conn ction to nsur that th syst m
com s into op ration if th r lativ humidity in th
nvironm nt drops in r lation to th s t-point, and vic
v rsa. As with v ry oth r control f atur , you must
th r for simulat diff r nt valu s on th r gulators or
humidistats to ch ck th activation of th pump, th
subm rg d l ctrod st am g n rator or any oth r
compon nt involv d in th tr atm nt
- Ch ck th corr ct siphoning of th drains (s ction 4.4.).
5.3. CORRECTION OF FLOW RESISTANCE VALUES IN
CIRCUITS AND ADJUSTMENT OF FAN AIR-MOVING
PERFORMANCE
MODIFICATIONS TO THE AIR-MOVING CIRCUIT may
som tim s b n c ssary during installation as a r sult, for
xampl , of dim nsional or routing r quir m nts that
cannot b anticipat d at th d sign stag .
Th s modifications fr qu ntly r sult in incr asing th
numb r and typ of factors that aff ct fan p rformanc .
H nc th n d to approximat as r alistically as possibl
th SYSTEM CHARACTERISTIC CURVE, accurat ly
r calculating th n w flow r sistanc valu s and
introducing corr ction factor.
On th basis of its thirty y ars' xp ri nc in th fi ld, TCF
T chnical D partm nt us s and r comm nds th SE
(SYSTEM EFFECTS) ADDITIONAL FLOW RESISTANCE
SYSTEM bas d on th charts d v lop d by AMCA (AIR
MOVING AND CONDITIONING ASSOCIATION).
To calculat th additional flow r sistanc a graph is us d
which pr s nts a family of straight lin s on logarithmic
v locity/flow r sistanc coordinat s. Each lin , which is
id ntifi d by a diff r nt l tt r of th alphab t, r pr s nts
an abnormal situation that d t rmin s an additional flow
r sistanc .
AMCA lists th adv rs installation situations and
indicat s th l tt r corr sponding to th straight lin in
th SE graph with which to d t rmin th additional loss
factor. Th flow loss s Pa ar calculat d on th SE graph
as follows:
- nt r th x-axis
• with th fan output v locity V if th obstruction is on th
d liv ry sid
• with th fan input v locity V if th v locity r f rs to th
intak sid
- asc nd v rtically to th straight lin r pr s nting th
abnormal installation situation
- mov horizontally to th y- axis to r ad off th Pa valu .
5.3.1. Insuffici nt l ngth of div rging duct s ction
b tw n unit d liv ry inl t and obstruction
In th v nt that a giv n acc ssory has b n install d at
such a distanc from th d liv ry inl t as not to allow th
compl t xpansion of th air flow in th duct, abnormal
conditions quantifiabl using th SE METHOD may aris .
In ord r for th air flow to xpand and occupy th ntir
duct s ction, a straight lin distanc is r quir d qual to:
L>= 2.5 quival nt diam t rs (low/m dium v locity ducts
L >= 6 quival nt diam t rs (high v locity ducts with V
>= 30 ITT/S)
Tabl 3 shows th valu of th quival nt diam t rs for
r ctangular ducts.

19
Tabl 4 shows th LETTER TO BE USED IN THE SE
GRAPH to d t rmin th additional loss Pa in th cas in
qu stion.
PLN: R pr s nts th p rc ntag of th straight lin
l ngth r quir d for compl t xpansion of th air
flow l aving th fan unit
S : Ar a of th fan d liv ry inl t actually aff ct d by
th air flow (valu sp cifi d in manufactur r's
catalogu )
Sp: Ar a of fan d liv ry inl t.
5.3.2. Elbows
Th FLOW RESISTANCE conn ct d with th pr s nc of
lbows in th ducting d p nds:
- on th ir arrang m nt
- on th PLN valu
- on th fan unit install d
Tabl 5 shows th l tt r corr sponding to th straight lin
in th SE graph to b us d to obtain th additional flow
r sistanc valu Pa, d p nding on:
- th S /Sp ratio
- th arrang m nt of th lbow (fig. 35)
- th PLN valu .
TABLE 6
5.3.3. Control air locks
Tabl 6 shows th MULTIPLIERS TO BE APPLIED TO THE
AIR LOCK FLOW RESISTANCE VALUES according to th
S /sp ratio, should th locks b install d on th d liv ry
inl t. If th air locks ar suppli d by TCE consult th "SAL"
air lock t chnical bull tin.
Abnormal situations in r lation to th r f r nc standard
may also occur on th intak and ar basically conn ct d
with;
- th possibl formation of ddi s caus d by curv s in th
inl t conduit in conflict with th fan wh l rotation
- choking on th intak lbows
- th installation of containm nt housings around th fans
- mor g n rally, th installation of acc ssori s such as
driv prot ction guards, flow rat control locks, tc.
For all th s valuations and any oth rs, all th AMCA
PUBLICATION 201 FANS AND SYSTEMS t chnical
docum ntation is availabl from th TCF T chnical
D partm nt. How v r, w would advis custom rs to
contact cur sp cialist p rsonn l for a rapid, xp rt s rvic
during insp ction. Th fan units will b adapt d to th
n w r quir m nts by adjusting th driv ratios. In this
r sp ct our Custom r S rvic is always on hand to carry
out th n c ssary jobs.

20
TABLE 7 . MAINTENANCE
6.1. FOREWORD
TCF r comm nds that its custom rs carry out pr v ntiv
maint nanc on th Air Tr atm nt Units in ord r to
nsur long-t rm ffici ncy. Th s units r quir littl
maint nanc and hav b n d sign d to mak ach
op ration as asy and saf as possibl .
6.2. FILTRATION SECTIONS
Th filtration s ctions r quir th most fr qu nt
maint nanc in ord r to:
- nsur that th air is filt r d with th r quir d ffici ncy
in th condition d nvironm nt
- to pr v nt unit compon nts from b ing damag d.
6.2.1. R conditionabl synth tic filt rs
Th s ar c lls m asuring 50 or 1 O0 mm in thickn ss,
also known as PREFILTERS, which off r th advantag of
b ing r conditionabl . Th RECONDITIONING can b
p rform d using two diff r nt m thods, d p nding on th
typ of dust tr at d:
- In th cas of DRY DUSTS, a compr ss d air j t is
dir ct d against th filt r in th opposit dir ction to
normal op ration.
- In th cas of WET DUSTS, th filtration diaphragm is
wash d (without r moving it from th fram ), if
n c ssary using dom stic d t rg nts.
To avoid damaging th filt r th t mp ratur of th wat r
must not xc d 50°C. Do not us solv nts or caustic soda.
L t th diaphragm dry by vaporation and r fit it only
wh n it is p rf ctly dry.
TCF advis s you to CHECK THE CONDITION OF THE
FILTERS ON A WEEKLY BASIS.
THE PREFILTERS MUST BE RECONDITIONED EVERY 7-
20 DAYS d p nding on th typ of nvironm nt b ing
condition d. Aft r 7-10 r conditioning op rations, th
diaphragm d t riorat s and its original charact ristics
will b impair d; it should th r for b r plac d.
6.2.2. M tal filt rs
Th s ar filt rs of consid rabl str ngth and long s rvic
lif ( sp cially if th m sh is stainl ss st l). You should
insp ct th m visually to d cid wh n th y n d r placing.
THESE FILTERS MUST BE RECONDITIONED AT LEAST
ONCE A WEEK sinc th y g n rally tr at xtr m ly
impur air (gr asy and highly lad n with particl s).
Th RECONDITIONING consists in washing th filt rs, if
n c ssary with solv nts and caustic soda mixtur s.
Th filtration diaphragm may b dri d with warm air or
compr ss d air.
Table of contents
Other TCF Air Handler manuals
Popular Air Handler manuals by other brands
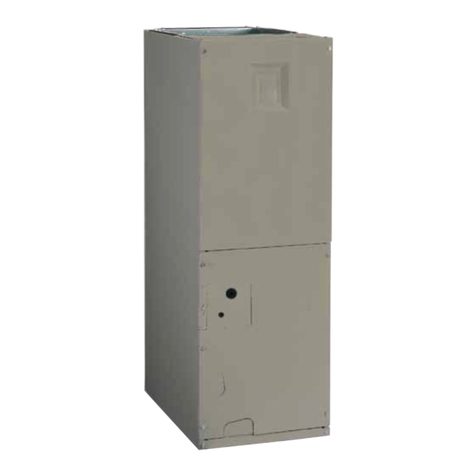
Nordyne
Nordyne B6EM Series installation instructions
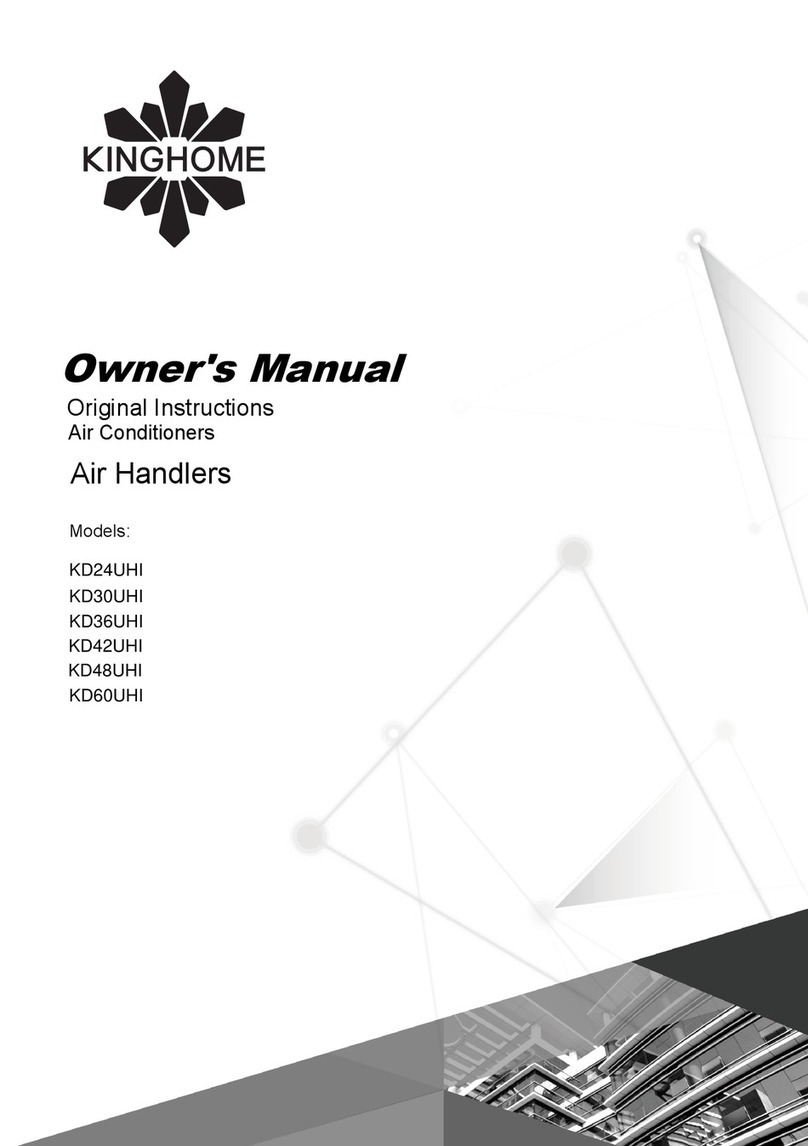
Kinghome
Kinghome KD24UHI owner's manual

York
York YSHW Installation operation & maintenance data

Innotherm
Innotherm UCCA-48HDC installation instructions
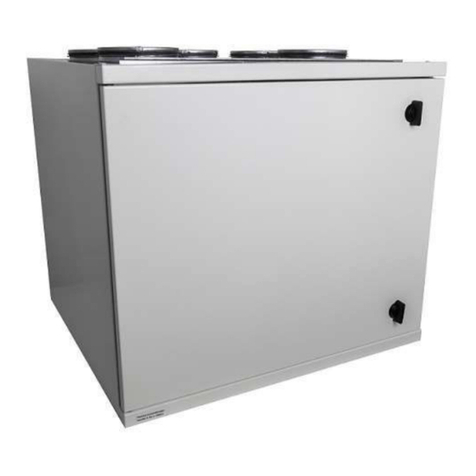
Deekax
Deekax TALTERI DIVK-C 96 C Installation and user manual
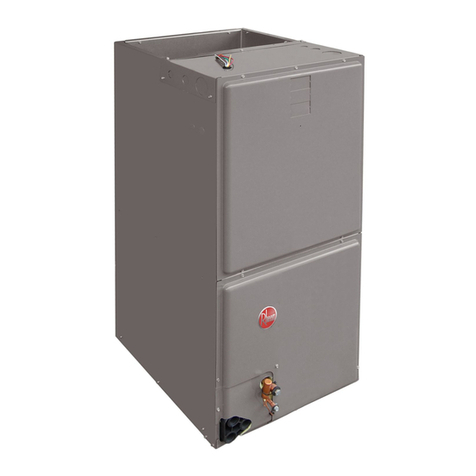
Rheem
Rheem RH1V2417STANJA installation instructions
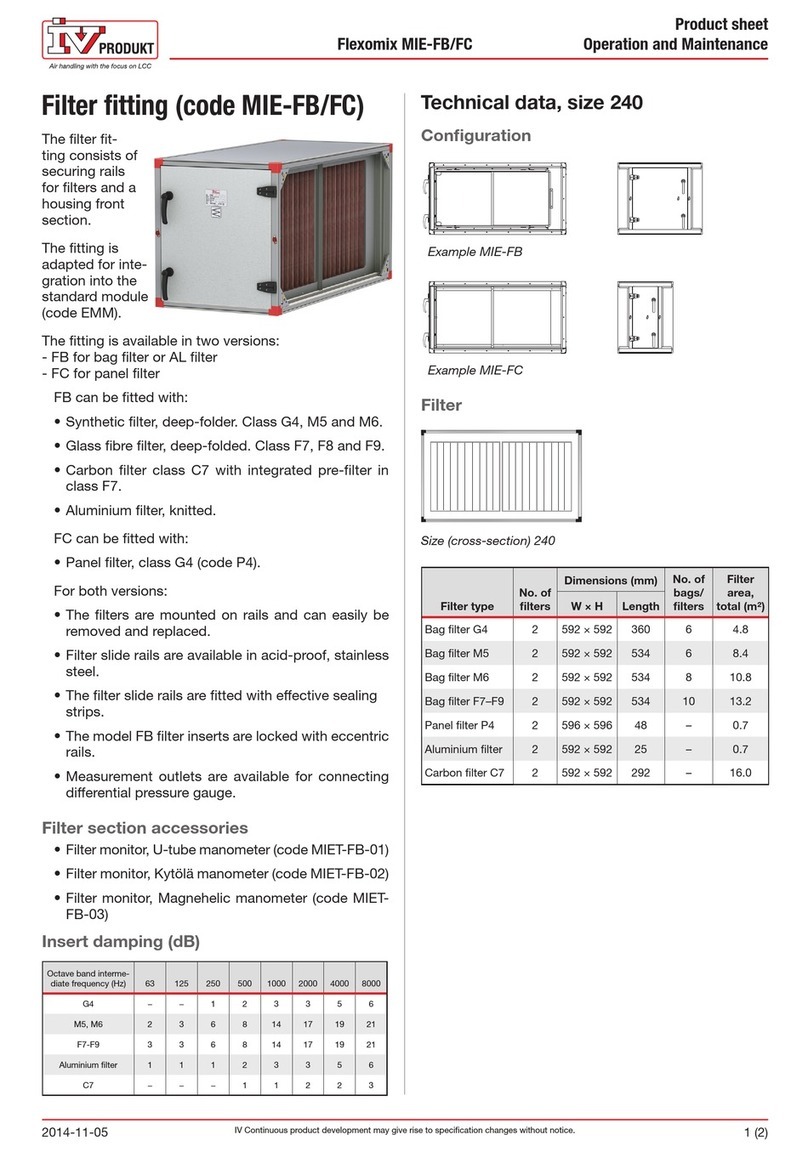
IV Produkt
IV Produkt Flexomix MIE-FB Operation and maintenance manual

Salda
Salda VEKA 350 EC Technical data
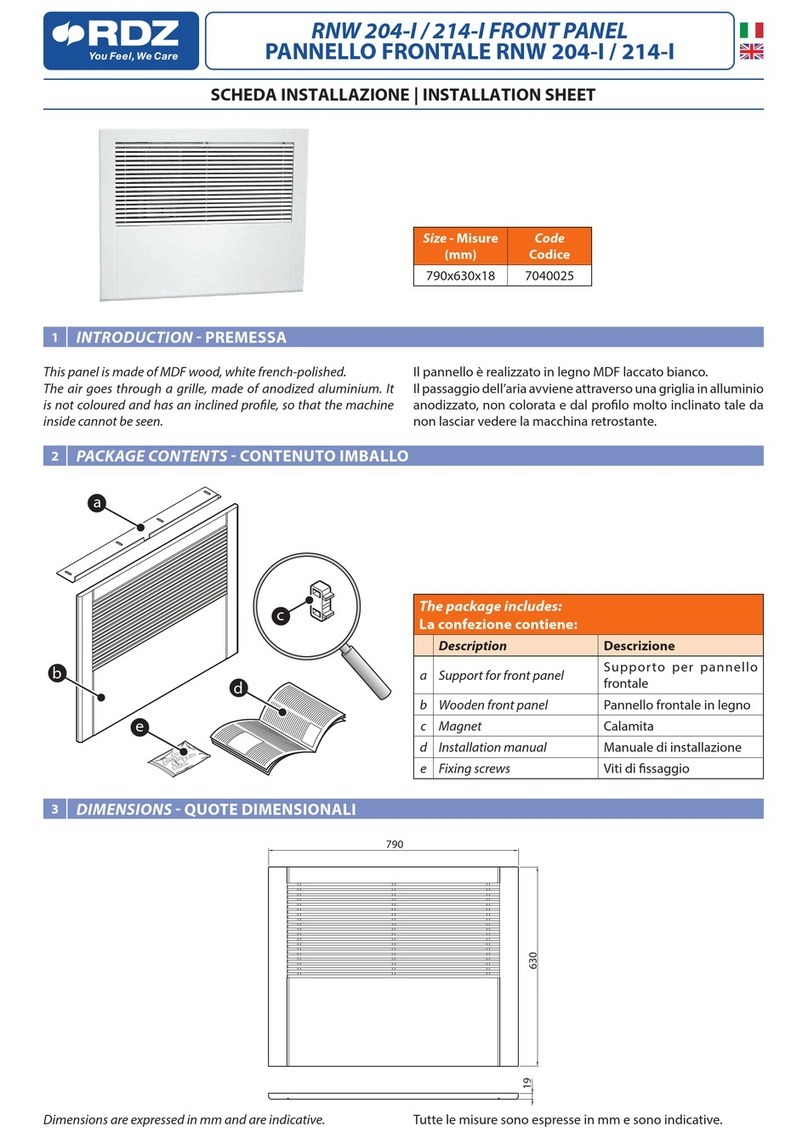
RDZ
RDZ RNW 204-I Installation sheet
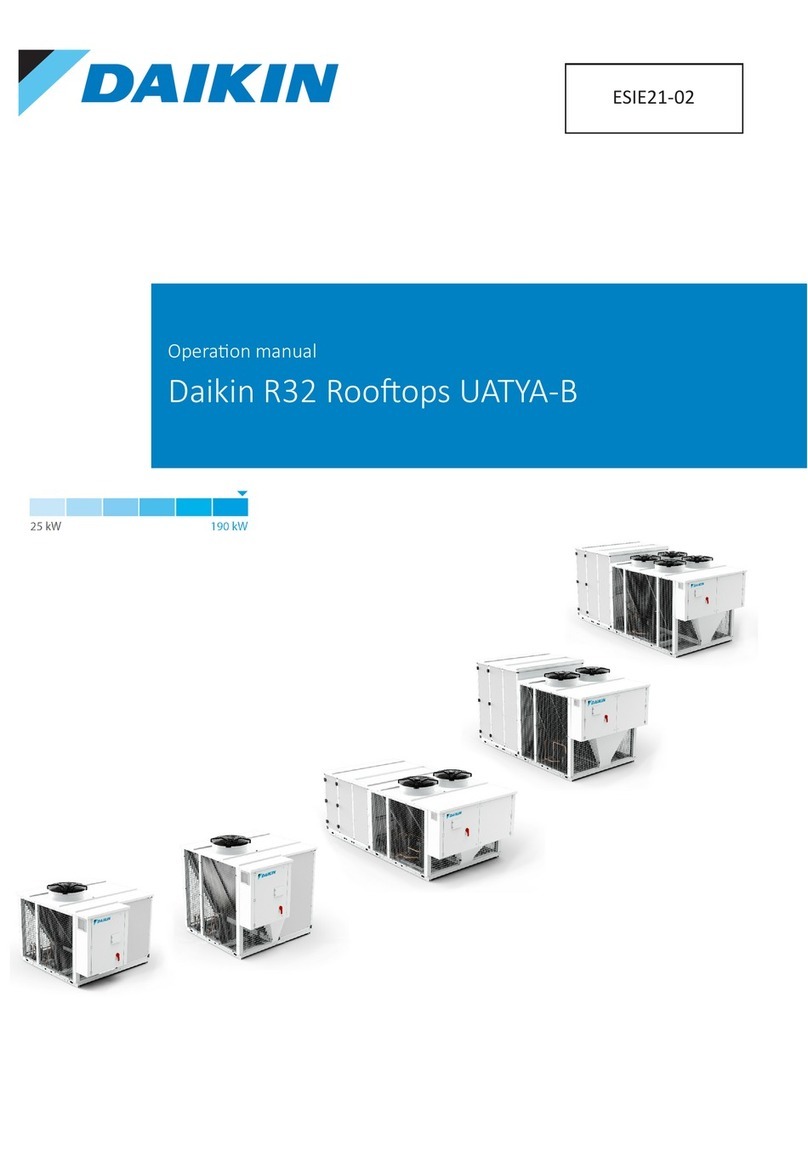
Daikin
Daikin UATYA-B Operation manual
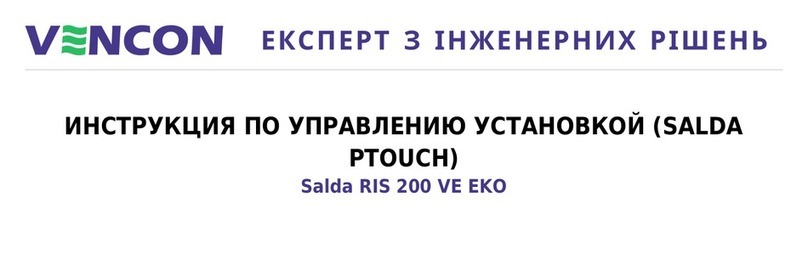
Salda
Salda SA-CONTROL RIS 200 VE EKO QUICK LAUNCH GUIDE
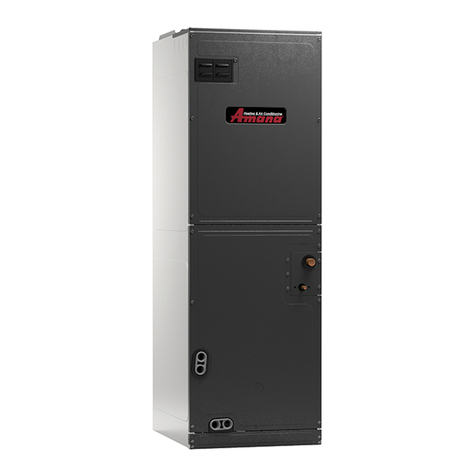
Maytag
Maytag Amana ARUF 14 Series Installation & operating instructions