Teagle Tomahawk 7100 User manual

30417
10100
11/19
30970
10345
31725
11338
10056
3694
TMKBXOP1119A

EC Declaration of Conformity
conforming to EEC Directive 2006/42/EC
Teagle Machinery Ltd.
Black ater
Truro
Corn all
TR4 8HQ
United Kingdom
declares in sole responsibility that the
Tomaha k
7100, 7150, 8100, 8150, 8500, 8555, 9500, 1010
to hich this certificate applies
conforms to the essential Health and Safety requirements of
EEC Directive 2006/42/EC & 2004/108/EC.
To effect correct application of the essential
Health and Safety requirements stated in
the EEC Directives, the follo ing harmonised standards ere consulted:
BS EN ISO 12100-1
BS EN ISO 12100-2
BS EN ISO 13857:2008
BS EN 703:2004
Signed:
Duncan Wilson (Engineering Director)
Dated: 31st May, 2018
Person authorised to compile Technical File
Duncan Wilson,
Teagle Machinery
Black ater, Truro
Corn all, TR4 8HQ
United Kingdom
Machine Serial No. . . . . . . . . .

SAFETY FIRST!
1. READ THE OPERATOR’S MANUAL THOROUGHLY
before attempting to operate or carry out any
maintenance on the machine. If you do not understand
any part of this manual, ask your dealer for assistance.
2. DANGER. Always carry out sa e maintenance.
Never clean, adjust or maintain the machine until
the engine has been stopped, the machine come to
rest, the PTO disengaged and the key removed.
3. DANGER. Never work under a machine raised
on the 3-point linkage unless it is securely
supported.
4. WARNING. Never operate the machine with any
parts or guards missing. Check that all guards
including the PTO shaft guards are in good condition
and in place before operating the machine.
5. WARNING. Operate sa ely. Before starting ork,
check that there are no persons or animals in the
immediate vicinity of the machine or tractor. Al ays
maintain full control of the tractor and machine. Ensure
that you kno ho to stop the tractor and machine
quickly in case of emergency.
6. WARNING. Secure the PTO guard by means o
check chains to suitable points on the tractor and
machine to prevent the outer plastic shield from
rotating.
7. DANGER. Never stand between the machine
and the tractor wheels.
8. WARNING. Do not wear loose or ragged
clothing.
9. CAUTION. Beware o dust. Under dusty
conditions, keep the cab indo s and doors
closed. The use of a dust mask conforming to EN149 is
strongly recommended.
10. CAUTION. Beware o high noise levels.
Some tractor/implement combinations give noise
levels in excess of 90dB at the operator's ear.
Under such circumstances, ear defenders should be
orn. Keep cab indo s and doors closed to reduce
noise level.
Throughout this handbook, the term `tractor' is used to
refer to the po er source used to drive the machine. It
does not necessarily refer to a conventional agricultural
tractor.
HEALTH AND SAFETY AT WORK
Our equipment is designed so as to conform ith current
Health & Safety Regulations and therefore poses no
significant hazard to health hen properly used.
Nevertheless, in the interests of all concerned, it is
essential that equipment of our manufacture is used in
accordance ith the instructions that are supplied or are
available from our Technical Staff.
Legislation requires that all operators are instructed in the
safe operation, cleaning and maintenance of equipment
and machines. This handbook forms part of that instruction
and it must be read and understood before fitting the
machine onto the tractor or attempting to use it.
Your supplier is responsible for carrying out any necessary
pre-delivery inspection, fitting the machine onto the tractor
and test running. The supplier must also give instruction in
the safe use, maintenance and adjustment of the machine.
In the interests of safety, please ensure that the
instructions referred to above are brought to the attention of
all your employees ho are to use the equipment. We
recommend that the use of this equipment is restricted to
capable trained operatives. Persons under the age of
sixteen should not operate the machine and should be kept
a ay from here it is being used.
WARRANTY
The standard arranty is against faulty materials and
orkmanship. Components supplied as part of the original
machine, but manufactured by another company, e.g. PTO
shafts, heels etc., are subject to the original manufacturer's
conditions and arranty.
Where repairs are carried out under arranty:-
a) Claims for the fitting of non original parts ill not be
considered unless prior agreement has been obtained.
b) The repairer must be advised that the ork is to be the
subject of a arranty claim beforehand.
c) Any claim must be submitted ithin four eeks of the repair.
d) The damaged parts must be retained for inspection and
returned carriage paid if required.
The right to ithdra arranty is reserved if:-
a) Non-original parts are fitted.
b) The machine has been abused, badly maintained or used
for purposes other than that for hich it as designed.
Sa ety Alert Symbol. This symbol is used in this manual and on the machine to highlight here instructions
about the safe use of the machine or arnings about safety hazards on the machine are being given.
Signal Words The follo ing signal ords alerts vie ers to the existence and relative seriousness of a hazard.
DANGER indicates an imminently hazardous situation that, if not avoided, will result in death or injury.
WARNING indicates an imminently hazardous situation that, if not avoided, could result in death or injury.
CAUTION indicates an imminently hazardous situation that, if not avoided, may result in minor/moderate injury
NOTE indicates a potentially hazardous situation that, if not avoided, may result in property damage.
IMPORTANT indicates a statement used to notify people of installation, operation or maintenance information that
is important, but not hazard –related

INDEX
INSTRUCTIONS Page
Lubrication schedule 7100 & 7150 2
Lubrication schedule 8100, 8150 & 8500 3
Lubrication schedule 8555 4
Lubrication schedule 9500 5
Lubrication schedule 1010 6
1.1 Specifications 7100 & 7150 7
1.2 Specifications 8100 & 8150 8
1.3 Specifications 8500 & 8555 9
1.4 Specifications 9500 & 1010 10
2.1 Explanation of pictograms 11
2.2 Safety decals maintenance 12
2.3 Location of safety decals 13
3Safety 14
4Identification 14
5Use of the Tomaha k 14
6Use on the public high ay 15
7Preparation of the machine 15
8Preparation of the tractor 15
9Fitting the machine onto the tractor 16
10 Operating instructions - loading 17
11 Operating instructions - discharge 19
12 Machine protective devices 21
13 Maintenance 21
13.1 Safety 21
13.2 Blades 21
13.3 Bed chain 22
13.4 Bale restraint beam adjustment and removal 22
13.5 Dual chop sieve removal 23
13.6 Crossbeater shear bolts 23
13.7 Gearbox 23
13.8 Drive chains 23
13.9 S ivel chute 23
13.10 Hydraulics 23
13.11 Electric controls for solenoid valve 24
13.12 Slip clutch 24
13.13 PTO shaft 24
13.14 Wheel changing 25
13.15 Wheel nuts 25
13.16 Tyre pressures 25
13.17 Hub caps 26
13.18 Wheel bearings 26
13.19 Lubrication of heel bearings 26
13.20 Handbrake (1010 models) 27
13.21 Service brake maintenance 27
13.22 Service brake adjustment 28
13.23 Pneumatic brakes 29
13.24 Lubrication 29
13.25 Maintenance schedule 30
14 Special tools for repairs 30
15 Optional extras 30
16 Machine storage 31
17 Disposal 31
Fault inding chart - Part 1 32
Fault inding chart - Part 2 33
Fault inding chart - Part 3 34

Ref. Description
1Grease nipple – rear
bed chain roller bush
2Grease nipples x 2 – at
ends of SC chute ram
3Oil chain – crossbeater
drive
4Grease nipple - shear
sprocket
Ref. Description
5Oil chain - bed chain
drive
6Grease PTO U.J.
& sliding members
7Grease nipples x 4 – SC
s ivel mechanism
Ref. Description
8Grease nipple -
crossbeater bearings –
behind crossbeater
drive sprocket on LHS
9Grease nipple - bed
chain front roller
bearing
10 Layshaft bearing
Ref. Description
11 PTO guards - monthly
12 Grease nipple –
layshaft U.J. - monthly
For more detailed information see maintenance section
1.
9.
5.
6.
11.
10.
12.
7.
2.
3.
4.
8.
9.
1.
8.
2
Notes: 1. Frequencies based on typical use - 15 hours per eek - adjust frequencies based on usage
2. Use good quality semi-solid grease for all procedures detailed above
Other
Fortnightly
Weekly
Twice Weekly
Lubrication Schedule
Tomahawk 7100 & 7150

Ref. Description
1Grease nipple – rear
bed chain roller bush
2Grease nipples x 2 – at
ends of SC chute ram
3Oil chain – crossbeater
drive
4Grease nipple - shear
sprocket
Ref. Description
5Oil chain - bed chain
drive
6Grease PTO U.J.
& sliding members
7Grease nipples x 4 – SC
s ivel mechanism
Ref. Description
8Grease nipple -
crossbeater bearings –
behind crossbeater
drive sprocket on LHS
9Grease nipple - bed
chain front roller
bearing
10 Layshaft bearing
Ref. Description
11 PTO – guards -
monthly
12 Grease nipple –
layshaft U.J. - monthly
13 Wheel bearings -
annually
14 Hitch coupling –
as required
For more detailed information see maintenance section
3
Lubrication Schedule
Tomahawk 8100, 8150 & 8500
Twice Weekly
Weekly
Fortnightly
Other
Notes: 1. Frequencies based on typical use - 15 hours per eek - adjust frequencies based on usage
2. Use good quality semi-solid grease for all procedures detailed above
1.
2.
5.
6.
7.
8.
9.
10.
11.
12.
13.
3.
4.
14.
9.
8.
13.
1.

Ref. Description
1Grease nipple – rear
bed chain roller bush
2Grease nipples x 2 – at
ends of SC chute ram
3Grease nipple - shear
sprocket
Ref. Description
4Oil chain - bed chain
drive
5Grease PTO U.J.
& sliding members
6Grease nipples x 4 – SC
s ivel mechanism
Ref. Description
7Grease nipples -
crossbeater bearings
8Grease nipple - bed
chain front roller
bearing
9Layshaft bearing
Ref. Description
10 PTO – guards -
monthly
11 Grease nipple –
layshaft U.J. - monthly
12 Wheel bearings -
annually
13 Hitch coupling –
as required
14 Fill chain oiler - as
required
16 Brake levers - as re-
quired
15 Handbrake spindle - 3
monthly
For more detailed information see maintenance section
4
Lubrication Schedule
Tomahawk 8555
Twice Weekly
Weekly
Fortnightly
Other
Notes: 1. Frequencies based on typical use - 15 hours per eek - adjust frequencies based on usage
2. Use good quality semi-solid grease for all procedures detailed above
1.
2.
4. 5.
6.
7.
8.
10.
11.
12.
14.
3.
13.
8.
7. & 9.
15.
1.
12. 16.

Ref. Description
5Grease PTO U.J.
& sliding members
6Grease nipples x 4 – SC
s ivel mechanism
Ref. Description
7Grease nipple -
crossbeater bearings –
behind crossbeater
drive sprocket on LHS
8Grease nipple - bed
chain front roller
bearing
9Layshaft bearing
Ref. Description
10 PTO – guards -
monthly
11 Grease nipple –
layshaft UJ - monthly
12 Wheel bearings -
annually
13 Hitch coupling –
as required
For more detailed information see maintenance section
5
Lubrication Schedule
Tomahawk 9500
Twice Weekly
Weekly
Fortnightly
Other
Notes: 1. Frequencies based on typical use - 15 hours per eek - adjust frequencies based on usage
2. Use good quality semi-solid grease for all procedures detailed above
Ref. Description
1Grease nipple – rear
bed chain roller bush
2Grease nipples x 2 – at
ends of SC chute ram
3Oil chain – crossbeater
drive
4Grease nipple - shear
sprocket
1.
2.
5.
6.
7.
8.
9.
10.
11.
12.
3.
4.
13.
8.
7.
12.
1.

Ref. Description
1Grease nipple – rear
bed chain roller bush
2Grease nipples x 2 – at
ends of SC chute ram
3Oil chains –
crossbeater drive
4Grease nipple - shear
sprocket
Ref. Description
5Grease nipple - bale lift
pivot pins - ( here
fitted)
6Grease PTO U.J.
& sliding members
7Grease nipples x 4 – SC
s ivel mechanism
Ref. Description
8Grease nipple - cross
beater bearings –
behind crossbeater
drive sprocket on LHS
9Grease nipple - bed
chain front roller
bearing
10 Layshaft bearing
Ref. Description
11 PTO – guards –
monthly
12 Grease nipple -
layshaft U.J. - monthly
14 Wheel bearings -
annually
15 Hitch coupling -
as required
13 Handbrake spindle -
3 monthly
1.
2.
3.
4.
7.
5.
6.
1.
8.
8.
9.
10.
11.
12.
14.
14.
15.
For more detailed information see maintenance section
6
Lubrication Schedule
Tomahawk 1010
Twice Weekly
Weekly
Fortnightly
Other
Notes: 1. Frequencies based on typical use - 15 hours per eek - adjust frequencies based on usage
2. Use good quality semi-solid grease for all procedures detailed above
13.

1.1 7100 / 7150 SPECIFICATIONS
Specifications
Right Hand
Chute
Sloping Swivel
Chute
Dual Chop
Chamber idth 1.4m
Giraffe discharge height N/A 3.5m 3.5m
Giraffe rotation angle N/A 280 degrees 280 degrees
Side discharge height 1.7m N/A N/A
Overall idth (chutes closed) 2.2m 1.86m 1.86m
Maximum overall idth 2.9m 2.75m 2.75m
Overall height - maximum 2.3m 3.6m 3.6m
Overall height - minimum 2.11m 2.4m 2.4m
Overall length - tailgate up 2.71m
Overall length - tailgate do n 3.95m
Maximum round bale diameter 1.83m
Maximum rectangular bale size 1.3m x 1.2m x 2.5m
Weight 1620kg 1680kg 1820 kg
Maximum hydraulic oil pressure 220 bar (3190 psi)
Maximum hydraulic oil flo 60 litres/minute (13.2 gal/min)
Minimum hydraulic oil flo 35 litres/minute (7.7 gal/min)
Time averaged sound po er 92dBA 92dBA 92dBA
Minimum tractor size 70K (90hp)
Vertical load at hitching point - un-laden 1620kg 1680kg 1820kg
Vertical load at hitching point - laden 2420kg 2480kg 2620kg
Model 7100 7100SC 7150
Machine Fitted With Dra bar & Axle
Specifications T7100 T7100SC T7150
Overall idth 2.38m 2.2m 2.2m
Weight 1805kg 1865kg 2005kg
Maximum dra bar load 325kg 325kg 365kg
Wheel track 1.75m
Machine Fitted With Castor Wheels
Specifications T7100 T7100SC T7150
Weight 1757kg 1817kg 1957kg
Wheel size 18x7-8
Wheel track 1.09m
Wheel speed rating 25 km/h
Maximum journey distance 2 km
Load rating per heel 1650 kg
7

Speci ications Right hand chute Sloping Swivel Chute Dual Chop
Model 8100 8100SC 8150
Number of crossbeaters 1 1 1
Chamber idth 1.55 m 1.55 m 1.55 m
Side discharge height - barrier 1.55 m 2.38 m 2.38 m
Giraffe discharge height - max. N/A 3.66 m 3.66 m
Giraffe rotation angle N/A 280 degrees 280 degrees
Overall idth (all chutes closed) 2.27 m 2.02 m 2.02 m
Overall idth (side chute raised) 3.06 m N/A N/A
Overall height - maximum 2.41 m 3.22 m 3.22 m
Overall height - minimum 2.41 m 2.54 m 2.54 m
Overall length (tailgate up) 4.19 m 4.19 m 4.19 m
Overall length (tailgate do n) 5.42 m 5.42 m 5.42 m
Maximum round bale diameter 1.83 m 1.83 m 1.83 m
Maximum rectangular bale size 1.3m x 1.2m x 2.5m
Tyre size (standard tyres) 10.0/75 – 15.3 10.0/75 – 15.3 10.0/75 – 15.3
Wheel track (standard Tyres) 1.75 m 1.75 m 1.75
Weight 1880 Kg 1960 Kg 2168 Kg
Volume of clamp silage 2.5 m3 2.5 m3 N/A
Maximum hydraulic oil pressure 220 bar (3190 psi)
Maximum hydraulic oil flo 60 litres/minute (13.2 gal/min)
Minimum hydraulic oil flo 35 litres/minute (7.7 gal/min)
Maximum dra bar load 650 Kg 650 Kg 650 Kg
Minimum tractor size 45kW (60hp) 45kW (60hp) 45kW (60hp)
Sound po er level 95 dbA 95 dbA 95 dbA
1.2 8100 / 8150 SPECIFICATIONS
8

Specifications Right hand chute Sloping s ivel chute Dual Chop
Model 8500 8500 8555
Number of crossbeaters 111
Chamber idth 1.7 m 1.7 m 1.7 m
Side discharge height - barrier 1.55 m 2.38 m 2.38 m
Giraffe discharge height - maximum
N/A 3.66 m 3.66 m
Giraffe rotation angle
N/A 280 degrees 280 degrees
Overall idth (all chutes closed) 2.48 m 2.21 m 2.21 m
Overall idth (side chute raised) 3.47 m N/A N/A
Overall height - maximum 2.77 m 3.51 m 3.51 m
Overall height - minimum 2.57 m 2.83 m 2.83 m
Overall length (tailgate up) 4.19 m 4.19 m 4.19 m
Overall length (tailgate do n) 5.42 m 5.42 m 5.42 m
Max Round bale diameter 2.00 m 2.00 m 2.00 m
Maximum rectangular bale size 1.3m x 1.2m x 2.5m 1.3m x 1.2m x 2.5m 1.3m x 1.2m x 2.5m
Tyre size (standard tyres) 12.5/80 – 15.3 12.5/80 – 15.3 12.5/80 – 15.3
Wheel track (standard tyres) 1.90 m 1.90 m 1.90 m
Weight 2080 Kg 2080 Kg 2,450 Kg
Volume of clamp silage 4.5 m3
4.5 m3
N/A
Maximum hydraulic oil pressure 220 bar (3190 psi) 220 bar (3190 psi) 220 Bar (3190 psi)
Maximum hydraulic oil flo 60 l/min (13.2 gal/min) 60 l/min (13.2 gal/min) 60 l/min (13.2 gal/min)
Minimum hydraulic oil flo 35 l/min (7.7gal/min) 35 l/min (7.7 gal/min) 35 litres/min (7.7 gal/min)
Maximum dra bar load 650 Kg 650 Kg 600 Kg
Minimum tractor size 60kW (80hp) 60kW (80hp) 66kW (90hp)
Sound po er level 95 dbA 95 dbA 95 dbA
1.3 8500 / 8555 SPECIFICATIONS
9

Specifications Right Hand Chute
Sloping S ivel
Chute
Right Hand Chute
Sloping S ivel
Chute
Model 9500 9500SC 1010 1010SC
Number of crossbeaters 2222
Chamber idth 1.7 m 1.7 m 1.7 m 1.7 m
Side discharge height - barrier 2.00 m 2.45 m 2.00 m 2.45 m
Giraffe discharge height - maxi-
mum
N/A 3.00 m N/A 3.00 m
Giraffe rotation angle
N/A 280 degrees
N/A 280 degrees
Overall idth (all chutes closed) 2.48 m 2.20 m 2.57 m 2.39 m
Overall idth (side chute raised) 3.47 m
N/A 3.56 m N/A
Overall height - maximum 2.93 m 3.54 m 2.96 m 3.61 m
Overall height - minimum 2.93 m 2.91 m 2.96 m 2.95 m
Overall length (tailgate up) 5.17m 5.17m 6.19 m 6.19 m
Overall length (tailgate do n) 6.34m 6.34m 7.32 m 7.32 m
Max Round bale diameter 2.00 m 2.00 m 2.00 m 2.00 m
Maximum rectangular bale size 1.5m x 1.2m x 2.5m 1.5m x 1.2m x 2.5m 1.3m x 1.2m x 2.5m 1.3m x 1.2m x 2.5m
Tyre size (standard tyres) 305/55 R22.5 305/55 R22.5 385/55 R22.5 385/55 R22.5
Wheel track (standard tyres) 1.9 m 1.9 m 2.0 m 2.0 m
Weight 3080 Kg 3160 Kg 3510 Kg 3590 Kg
Volume of clamp silage 8 m3
8 m3
10.0 m310.0 m3
Maximum hydraulic oil pressure 220 bar (3190 psi) 220 bar (3190 psi) 220 Bar (3190 psi) 220 Bar (3190 psi)
Maximum hydraulic oil flo
60 litres/min (13.2
gallons/min)
60 litres/min (13.2
gallons/min)
60 litres/min (13.2
gallons/min)
60 litres/min (13.2
gallons/min)
Minimum hydraulic oil flo
45 litres/min (9.9
gallons/min)
45 litres/min (9.9
gallons/min)
45 litres/min (9.9
gallons/min)
45 litres/min (9.9
gallons/min)
Maximum dra bar load 600 Kg 600 Kg 600 Kg 600 Kg
Minimum tractor Size 65kW (87hp) 65kW (87hp) 66kW (90hp) 66kW (90hp)
Sound po er level 86 dbA 86 dbA 86 dbA 86 dbA
1.4 9500 / 1010 SPECIFICATIONS
10

11
Please read instruction book
before using the machine
Tighten heel nuts to setting in
operators handbook
Be are thro n objects
keep your distance
Allo rotor to stop before removing
blockage ith tool provided
Direction of rotation and
speed of PTO input shaft
Blockage removal tool
Tractor Control Desk Panel
Remote Tailgate Control Box Panel
High rotor speed Lo rotor speed
2.1 EXPLANATION OF PICTOGRAMS
Bed chain speed
Raise giraffe
chute deflector
Rotate giraffe
clock ise
Rotate giraffe
anti-clock ise
Lo er giraffe
chute deflector
Bed chain for ard Bed chain reverse
Po er on Po er off
Giraffe chute selector
or
long chop
RH chute selector
or
short chop
Lo er tailgate
Lo er RH chute
Raise RH chute
Raise tailgate
Bed chain reverse
Bed chain for ard
Raise tailgate
Lo er tailgate
Hold to run button
(must be depressed
to ork any other
function)
On light
Bluetooth on
Flashing = connecting

Increase bed chain
speed
Bed chain for ard Raise deflector Rotate chute
clock ise
Tailgate raise
Decrease bed chain
speed
Bed chain reverse Lo er deflector Rotate chute
anti-clock ise
Tailgate lo er
12
Do not allo anyone to ride on
the machine
Be are crushing hazard
keep clear
Hydraulic flo rate & direction
60 L/min
13.2 Gal/min
MAX
DL1109
Maximum hydraulic circuit pressure
Tractor Cable Control Panel
2.2 Sa ety Decals Maintenance
The safety signs fitted to the machine arn of hazards and form an important part of keeping the operator and by-
standers safe.
It is important that the signs are
- kept clean and visible ( ash ith arm ater and detergent).
- replaced if missing or illegible.
When replacement parts are fitted it is important that any safety decals affixed to them are replaced.
Replacement decals are listed in the spare parts lists and can be purchased as spare parts.
Jack Information Label
Bluetooth Symbol
Lubrication point

10
5.
9
2.
7.
8.
9.
10
2.3 LOCATION OF SAFETY DECALS
Key
4.
6.
3.
1.
8.
13
6 Please read the instruction book.
7 Direction of rotation and speed of PTO
input shaft.
8 Jacking point Information Label.
9 Tighten heel nuts to setting in
operators handbook.
10 Be are crushing hazard keep clear.
1 Unblocking procedure.
2 Be are thro n objects keep your
distance.
3Do not allo anyone to ride on the
machine.
4Maximum hydraulic circuit pressure
5Blockage removal tool

3. SAFETY
In addition to the standard safety guidelines listed at the
beginning of this handbook, the follo ing special safety
items apply to the Tomaha k.
3.1 WARNING. The machine shall be operated by
one person only.
3.2 CAUTION. Never put your hands inside the
delivery chutes. In the event of a blockage
clear it using the blockage removal tool provided,
located on the front of the lo er housing. First,
disengage the PTO, stop the engine, remove the
key, and ait for the rotor to come to rest.
3.3 DANGER. Never enter the bale chamber
unless the PTO has been disengaged, the
engine has been stopped ith the key removed from
the ignition, and the machine has come to rest.
3.4 WARNING. Never insert anything inside the
chute or bale chamber hile the machine is
running.
3.5 CAUTION. When entering or leaving the bale
chamber take care, the tailgate surface may be
slippery.
3.6 DANGER. Be are of overhead po er lines
hen the s ivel chute deflectors are fully
raised. Contact ith po er lines could result in the
operator receiving a severe electric shock.
3.7 DANGER. Do not climb onto the top edges of
the bale chamber hilst the machine is use.
3.8 WARNING. Do not allo anyone to ride on the
machine, tractor linkage or dra bar.
3.9 WARNING. Do not allo persons or animals to
stand in front of the outlet chutes hilst the
machine is running.
3.10 WARNING. Do not operate the tailgate if any
person or animal is standing in the loading
area behind the machine, al ays ensure good
rear ard visibility hen lo ering the tailgate.
3.11 WARNING. Never put your hand over a
hydraulic leak. Oil under pressure may enter
the blood stream.
3.12 CAUTION. The shredding of dusty or mouldy
material can create dust hich may have
adverse health effects. Operator exposure to such
conditions should be avoided here possible. When
circumstances prevent this, either use a tractor ith
a suitable forced air cab filtration system or an
adequate respirator. Respirators must comply ith
the relevant Standard and be approved by the Safety
Inspectorate. Disposable filtering face piece
respirators to EN149 or half mask respirators to
EN140 fitted ith filters to EN 143 are likely to be
adequate.
3.13 CAUTION. Before disconnecting the hydraulic
hoses al ays lo er the tailgate onto the
ground for safety reasons and to avoid residual
pressure in the hoses.
3.14 WARNING. Al ays fit the correct size tyre onto
the rims hen fitting replacements.
3.15 WARNING. Care must be taken hen handling
large bales, as they have sufficient eight and
density to cause serious injury. Large bales should
be handled ith appropriate machinery either directly
into the Tomaha k or into a position here they can
be self loaded. Do not manually load bales from the
stack above the machine, so as to prevent the risks
of falling into the machine and collapse of the stack
of bales.
3.16 CAUTION. After prolonged intensive use of the
machine, the oil may have risen in temperature
causing the unions and hoses to be hot.
4. IDENTIFICATION
4.1 Serial Number
The serial number of the machine is engraved on the front
right hand side of the chassis and on the serial number
plate attached to the inner face of the left hand discharge
rotor gearbox mounting plate.
4.2 Le t and right hand
In this handbook and parts list, the terms Left and Right
Hand apply to the machine hen standing behind the
machine looking to ards the rear of the tractor.
5. USE OF THE TOMAHAWK
The Tomaha k bale processor is designed to process
baled and bulk loose materials such as stra , hay or
silage and dispense them either for bedding or as feed for
livestock.
The materials sho n in Table 1 belo can be processed
depending on the type of crossbeater fitted to the
particular model of machine.
Table 1. Recommended material
14
Type o material Single
crossbeater
7100, 8100 &
8500
Twin
crossbeater
9500 & 1010
Baled silage Yes No
Baled hay Yes Yes
Baled stra Yes Yes
Clamp silage Yes Yes
7150 &
8150
8555
Type o
material
Blades
Up or
Down
Blades
Down
Blades
Up
Screen
Fitted
Blades
Up
Screen
Out
Baled silage No No No Yes
Baled hay Yes Yes Yes Yes
Baled stra Yes Yes Yes Yes
Clamp silage No No No Yes

Its use for shredding other materials is not recommended
ithout first seeking further advice from Teagle Machinery
Ltd.
WARNING. The machine must never be run ith
any of the chute components removed.
Unapproved chute modifications should not be
carried out as Safety Regulations may be infringed.
6. USE ON THE PUBLIC HIGHWAY
If the machine is to be transported along the public
high ay (any road here the public have access) behind
the tractor, it may be necessary to fit lights to comply ith
local road traffic legislation, as the machine is likely to
obscure the tractor rear light units.
Suitable lighting kits are available from your local supplier
or may be obtained by contacting Teagle Machinery Ltd.
The Tomaha k (except the Tomaha k 1010), hen fitted
ith a dra bar and axle is classed as a trailed implement
and as such does not require brakes hen used in the
United Kingdom provided the maximum speed limit of 20
mph is observed. For all other countries local regulations
must be observed.
Please contact the relevant government department to
ensure local regulations are complied ith.
Failure to comply ith road traffic legislation may lead to
prosecution by local la enforcement agencies and could
also result in a road traffic accident.
In addition the overall length of the mounted Tomaha k
7100/7150 ill require marker boards to be fitted. The
requirements vary according to hether the tailgate is
raised or lo ered (see Table 2). Further information is
given in the “Road vehicles (Authorisation of Special
Types) (General) Order 2003” and “Road Vehicles
(Construction and Use) Regulations 1986”.
Table 2. Road traffic markings
IMPORTANT. Teagle Machinery Ltd are able to
supply machines that have been type approved to
Regulation (EU) No 167/2013 that are suitable for
use on the public high ay throughout the European
Economic area.
7. PREPARATION OF THE MACHINE
Remove the PTO shaft and any other loose items from
the body of the machine.
8. PREPARATION OF THE TRACTOR
WARNING. For good visibility do n both sides of
the machine hen orking and reversing, the tractor
should be fitted ith mirrors.
The minimum PTO po er required to drive a Tomaha k
varies ith model as sho n in Table 3.
Table 3. Minimum tractor horsepo er
Ho ever, the suitability of any particular tractor ill
depend upon:
a) The size and eight of the bale to be spread
b) The availability of front counter eights
c) Whether the machine is to be used to transport
bales along the road.
The machine is designed to use the standard 540 rpm
PTO shaft.
NOTE. The hydraulic valve block requires an unrestricted
return ith a maximum return line pressure of 25 bar
(360 psi) measured at the outlet port of the valve block.
This is required to ensure correct operation of the valve
and to reduce heating of the oil.
Where the machine is to be operated on a tractor ith
closed centre hydraulics and the flo can not be
controlled, the solenoid valve may be adapted ith a
closed centre plug, details of hich can be obtained from
Teagle Machinery Ltd.
8.1 Cable Valve Controls
The cable control unit mounting bracket should be fitted
inside the cab so that it is conveniently situated for the
operator. Structural members of the cab must not be
drilled or elded in order to site the bracket.
8.2 Solenoid Valve Control Desk & Junction Box
The control desk for the solenoid valve is supplied ith a
suction cup attachment. This should be fitted in the cab
in a suitable position that is convenient for the operator
on a smooth, clean dust free surface.
The electric control supply cable should be connected to
the tractor’s auxiliary 3 pin socket. Should a socket not
be available then the control desk must be ired directly
to the battery. Remove the connector plug to reveal the
bro n and blue ires, bro n is positive, blue is
negative. Wire directly to the battery ith a suitable lead
and insulated connectors. A po er lead ith a 3 pin
female connector is available (part number SC3598).
NOTE. If the supply cable is connected to the battery
ith the rong polarity the control desk and junction box
ill not po er up and the Bluetooth connection LED ill
not illuminate.
If the fuse on the po er lead to the junction box should
blo this ill be indicated by the red LED illuminating.
CAUTION. Under no circumstances remove the
fuse holder or use fuses ith a higher rating than
7.5amps. Warranty will be invalidated i this
occurs.
The control desk ill not turn on until the Bluetooth
connection ith the machine has been established, the
LED stops flashing and is illuminated.
15
Tailgate position
Length of
projection
Rear
marker
Side
marker
Raised 2.57m Yes No
Lo ered 3.87m Yes Yes
Model Mounted Trailed
7100 / 7150 70 kW (90 Hp) 60 kW (80 Hp)
1010 - 67.5 kW (90 Hp)
8100 / 8150 - 60 kW (80 Hp)
8500 / 8555 - 60 kW (80 Hp)
9500 - 65 kW (87 Hp)

9. FITTING THE MACHINE ONTO THE TRACTOR
9.1 Fitting The PTO Sha t
Hitch the machine to the tractor either on the 3 point
linkage or on the dra bar.
Proceed as follo s:
9.1.1 Measure the distance bet een the annular groove
on the tractor output shaft to the annular groove on the
machine input shaft.
9.1.2 Measure approximately the distance bet een the
retaining balls of each sliding yoke at either end of the
PTO shaft ith it fully collapsed.
9.1.3 If the distance bet een the grooves is 150mm (6”)
longer or more than the distance bet een the locking
balls then the PTO shaft ill not require cutting.
If the distance is less than 150mm the PTO shaft ill need
to be shortened. Calculate the difference bet een the t o
measured values and add 150mm (6”). The ans er is the
amount to be removed from each half of the PTO shaft.
For example:
Distance measured bet een grooves 1100mm
Length of shaft bet een locking balls 1200mm
Length to reduce shaft by = (1200 - 1100 ) +150
Length to reduce shaft by = 100 +150
Length to reduce shaft by = 250 mm
9.1.4 Separate the 2 halves of the PTO shaft and remove
the amount calculated from each half guard and each half
tube. Deburr the drive tubes after cutting. Remove the
guards to facilitate cutting if required.
9.2 Trailed Machines
Hitch the machine dra bar to the tractor and turn off the
tractor engine. Fit the PTO shaft, ith the clutch end of
the PTO shaft attached to the machine.
Make sure the dra bar is securely attached to the tractor,
as hen loading bales or silage the eight of the material
on the tailgate may cause the dra bar to lift.
Check that the lo er links are at a height such that they
ill not contact the PTO shaft hen the tractor is turning.
If they are not used regularly, it is recommended that they
be removed.
Gradually turn the tractor until maximum turning lock is
achieved, and drive over undulating ground, checking that
the PTO shaft does not come to ithin 100 mm (4 inches)
of bottoming. If necessary, cut the PTO shaft to the
correct length. With the shaft in its most extended
position, there should not be less than half of the original
overlap bet een the sliding members.
It is essential to get the relationship bet een the tractor
PTO shaft and the gearbox input shaft correct to give a
satisfactory PTO shaft life. The correct geometry exists
hen the machine is horizontal, see Figure 1.
If the machine is shredding hilst turning on a regular
basis it is recommended that a PTO shaft ith a ide
angle, constant velocity joint be fitted.
9.3 Mounted Machines
Attach the Tomaha k to the 3 point tractor linkage. Make
sure the lo er link stabilisers or check chains are tight
and the lo er link arms are fixed from moving
horizontally.
When machine is fully attached lo er the lo er link arms
until the machine is resting on the ground. Turn off the
tractor engine and fit the PTO shaft, ith the clutch end of
the PTO shaft attached to the machine.
Gradually lift the machine until minimum shaft length is
achieved checking that the PTO shaft does not come to
ithin 25 mm (1”) of bottoming. If necessary, cut the PTO
shaft to the correct length. With the shaft in its most
extended position, there should not be less than half of
the original overlap bet een the sliding members.
It is essential to get the relationship bet een the tractor
PTO shaft and the gearbox input shaft correct to give a
satisfactory PTO shaft life. The correct geometry exists
hen the machine is horizontal. The height of the
gearbox input shaft should be adjusted to keep the PTO
shaft as straight as possible. For mounted machines the
length of the top link and the lift height can be adjusted,
see Figure 1.
Figure 1. Correct PTO geometry.
9.4 Trailed And Mounted Machines
Connect the hydraulic supply hose into the spool valve
connection of the tractor and the return hose to the free
flo return. It is important that the supply hose to the
valve is connected to the pressure port of the tractor, this
hose is marked ith an identifying tag.
Place the control desk in the cab and attach it to the
indo in a convenient location using the suction cup.
Once the control desk has been positioned, route the
machine cable into the cab making sure it is kept a ay
from the rear heel and any pinch points bet een the
PTO shaft and link arms. Where possible, route into the
cab through cable entry points on the tractor, allo ing the
rear indo to be kept closed during use. Plug the cable
connector into the 3 pin po er socket on the control desk
po er lead.
WARNING. Ensure the functions of the control desk
are completely understood before proceeding to use
the machine. In particular the bed chain is actuated
in the for ard direction by pushing the for ard direction
button and stopped by pressing the button again. Reverse
of the bed chain can only be actuated by holding the
reverse button.
Where the machine is supplied ith a cable controlled
valve place the cable control unit in the cab and attach it
to the socket provided.
16
Tomaha k
Gearbox
Both Angles
Similar
Tractor

9.5 Programming Electronic Controls To Suit Tractor
Figure 2. Control desk.
Each tractor has different flo rates from its hydraulic
system. The electronic controls are programmable via the
control desk to optimise the performance of the machine
depending on the oil flo that the tractor can deliver.
The follo ing instructions ill allo you to programme the
stop position (0) and high speed position (10) of the bed
speed dial. This process ill allo maximum bed speed
ithout compromising the other services the valve block
can provide.
To perform this operation the follo ing steps must be
follo ed exactly.
a) Turn on the tractor and engage the hydraulic
systems.
b) Set the tractor engine revs to a normal orking
RPM.
c) With the control desk off, turn the bed speed dial
do n to 0.5.
d) The follo ing buttons must then be pressed & held
do n in this order;
1Bed for ard.
2Long chop.
3On.
e) Hold the sequence of buttons for 8 seconds until
both the ‘bed for ard’ and ‘on’ LED’s illuminate.
f) Release buttons and the LED’s should flash
alternately.
g) Using the long chop button to slo do n,
and the short chop button to speed up,
slo the bed do n to the point here it just stops.
Press the ‘off’ button to save the slo speed.
You have no programed the electronic controls for the
minimum bed speed.
To programme the electronic controls for the maximum
speed repeat the same process again BUT Step c should
have the speed dial set to 10 and in Step g you should
increase the bed speed to the maximum desired.
IMPORTANT, if the tractor hydraulic oil flo is less than
the maximum required by the valve (60 litres per minute)
then setting the maximum bed speed to use the full flo
of oil ill result in the other valve functions not orking
hen the bed is operating at maximum speed. The bed
speed may then need to be reduced from maximum to
allo operation of the chute / tailgate functions.
This can be programmed hen setting the maximum
speed of the machine by slo ing do n the maximum bed
speed a small amount before s itching off.
Ho ever, if full bed speed is required, please be a are
that the other valve functions may be compromised
during full bed speed operation.
10. OPERATING INSTRUCTIONS - LOADING
10.1 General
IMPORTANT. The strings or net should be removed from
the bale as it is being loaded into the machine. The
Tomaha k ill shred some string but some ill tend to
rap around the crossbeater(s). Putting t ine or net rap
through the machine is not recommended as it ill be
eventually spread on the land and pollute subsequent
crops.
DANGER. When removing string or net rap from
bales never climb into the bale chamber or onto the
tailgate behind a bale unless the PTO has been
disengaged, the engine has been stopped, the key
removed and the machine come to rest.
WARNING. Do not stand above the machine on a
stack of bales or in a barn to load the machine
manually.
Bales can be loaded into the machine in t o ays, using a
loader or by self-loading using the machine tailgate. If a
loader is used, simply load the bale into the bale chamber
such that it is fully inserted, but do not force it against the
crossbeater(s).
CAUTION. When loading the machine, it ill be
necessary to run the bed chain to help self load the
bale into the chamber. Ho ever, excessive use of the bed
chain for this purpose may cause material to enter the rotor
housing resulting in a blockage during machine start up.
The tailgate is designed to load bales into the chamber of
the machine. Where a telescopic tailgate is fitted to the
Tomaha k 1010, it is important to only self load ith it in
the retracted position.
To retract the tailgate:
1.) Lo er the tailgate.
2.) S itch off the tractor and remove the key.
3.) Remove the extension retaining bolts.
4.) Slide the rear tailgate section to ards the machine,
replace the retaining bolts in the retracted position.
17
Po er on
Short chopLong chop
Bed for ard
Other manuals for Tomahawk 7100
1
This manual suits for next models
7
Table of contents
Popular Computer Hardware manuals by other brands
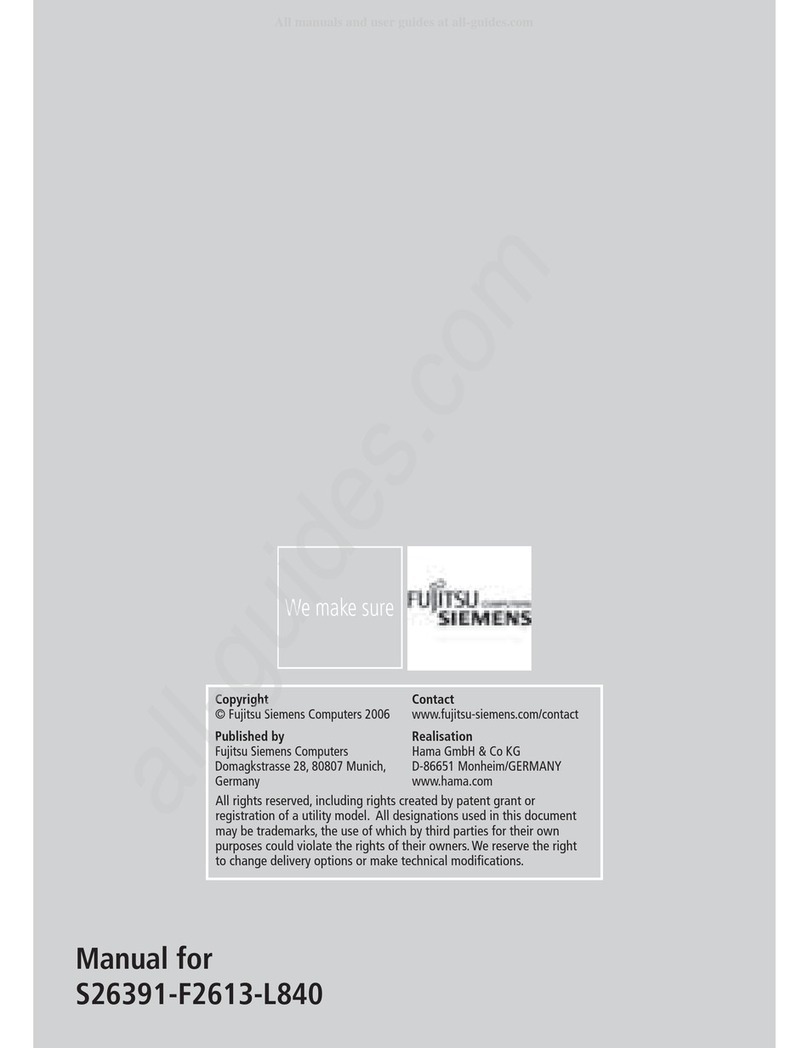
Fujitsu Siemens Computers
Fujitsu Siemens Computers POCKET LOOX N100 series operating instructions
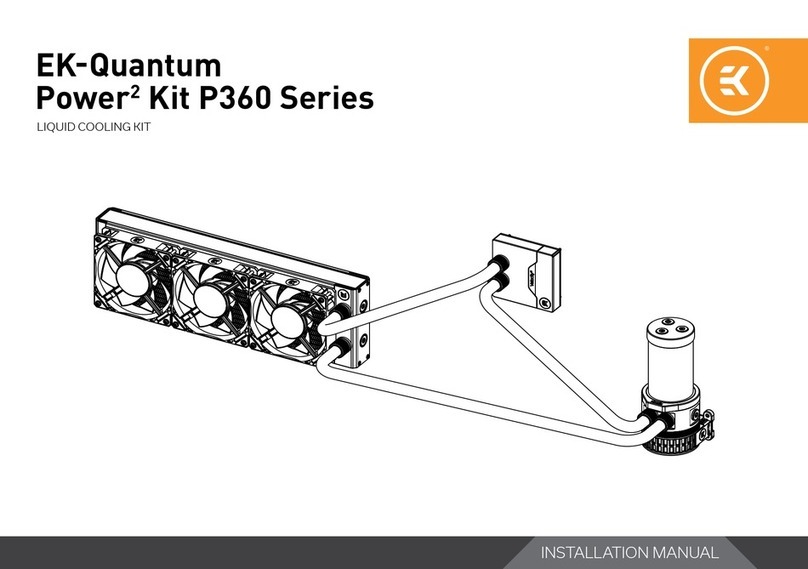
EK-Quantum
EK-Quantum Power2 Kit P360 Series installation manual
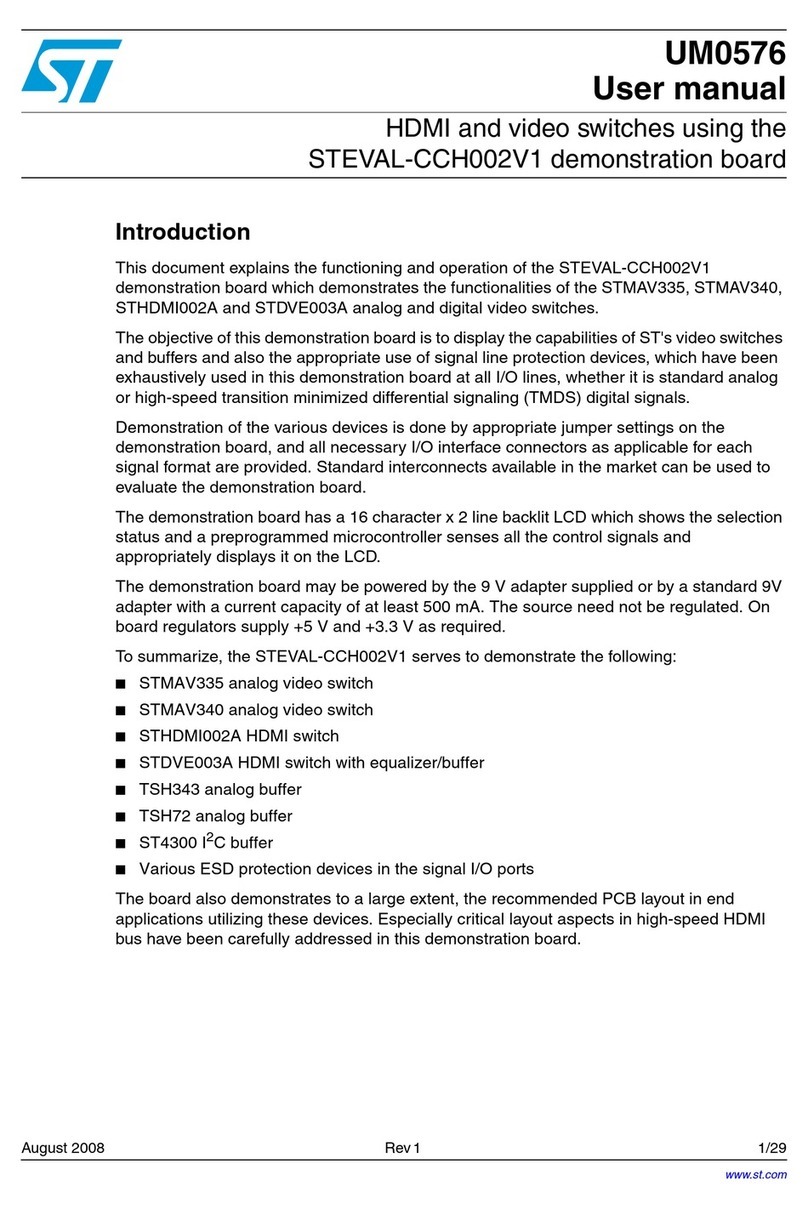
ST
ST STEVAL-CCH002V1 user manual
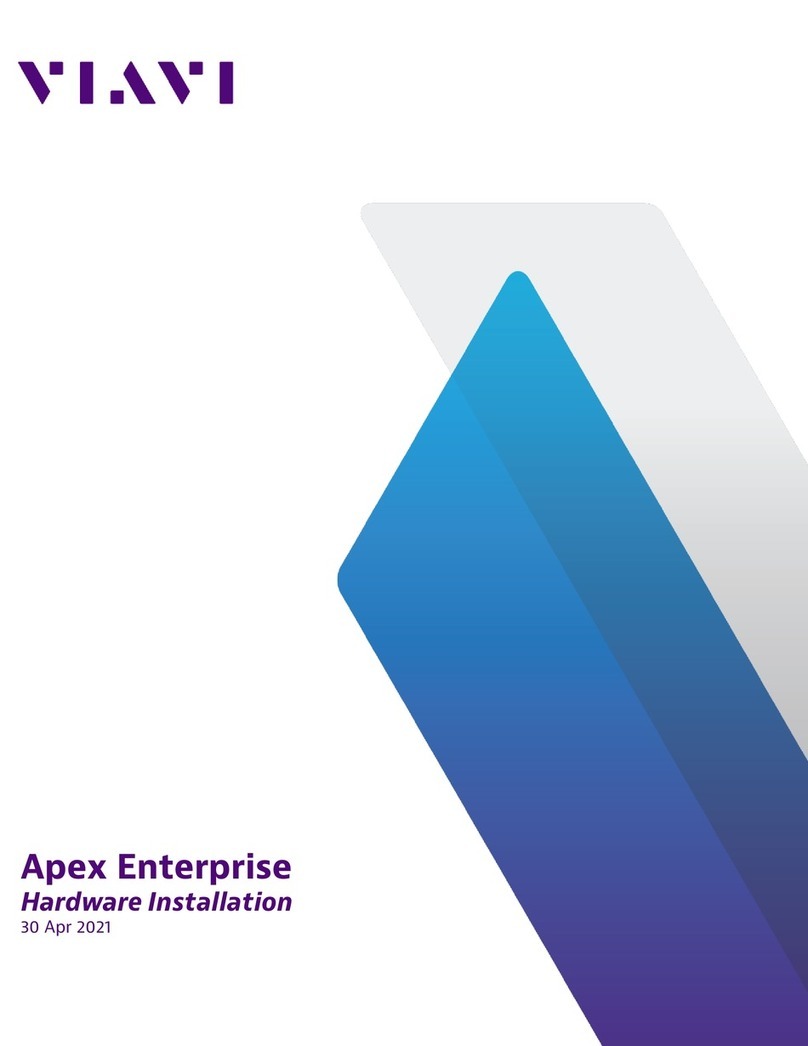
Viavi
Viavi Apex Enterprise G3-APEX-ENT-32T Hardware installation
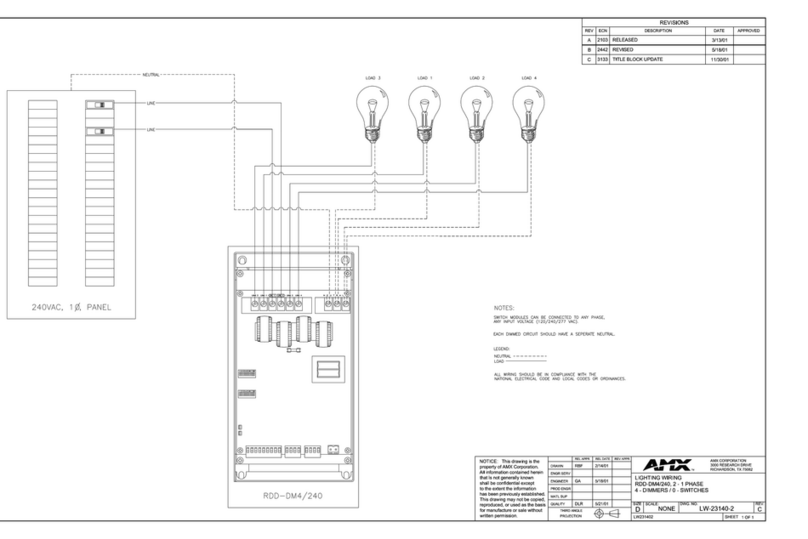
AMX
AMX RDD-DM4/240 Schematic diagram

Delta
Delta CMM-DN01 Operation manual