Technosoft iMOT Series Use and care manual

iMOT
line
Intelligent Motors
Intelligent Motors
T
echnical
Reference
Technosoft 2018 P091.042.iMOT.UM.0918

Technosoft 2018 2 iMOT Intelligent Motors Line Technical Reference
Table of contents
Table of contents ........................................................................................................... 2
Read This First ............................................................................................................... 4
About This Manual................................................................................................................. 4
Notational Conventions......................................................................................................... 5
Trademarks ............................................................................................................................ 5
Related Documentation ......................................................................................................... 5
If you Need Assistance … ..................................................................................................... 6
1Safety information.................................................................................................... 6
1.1 Warnings....................................................................................................................... 6
1.2 Cautions........................................................................................................................ 7
1.3 Quality system, conformance and certifications ....................................................... 7
2Product Overview..................................................................................................... 9
2.1 Introduction .................................................................................................................. 9
2.2 Product Features........................................................................................................ 10
2.3 Identification Labels................................................................................................... 11
3Hardware Installation............................................................................................. 12
3.1 iMOT17xB TM-CAN and TM-CAT models dimensions............................................. 12
3.2 iMOT17xB XM-CAN models dimensions................................................................... 12
3.3 iMOT172S XM-CAN model dimensions..................................................................... 13
3.4 MOT172S TM-CAN and TM-CAT models dimensions .............................................. 13
3.5 iMOT23xS XM-CAN models dimensions................................................................... 14
3.6 Mechanical Mounting................................................................................................. 15
3.7 Connectors and Pinouts ............................................................................................ 16
3.7.1...... Connectors and pinouts for iMOT17xB/iMOT172S TM-CAN models ................................... 16
3.7.2...... Connectors and pinouts for iMOT17xB/iMOT172S TM-CAT models.................................... 17
3.7.3...... Connectors and pinouts for iMOT17xB/iMOT172S XM-CAN models ................................... 18
3.7.4...... Connectors and pinouts for iMOT23xS XM-CAN models...................................................... 19
3.8 Connection diagrams................................................................................................. 20
3.8.1...... iMOT17xB/iMOT172S TM-CAN connection diagram ............................................................ 20
3.8.2...... iMOT17xB/iMOT172S TM-CAT connection diagram ............................................................ 21
3.8.3...... iMOT17xB/iMOT172S XM-CAN connection diagram............................................................ 22
3.8.4...... iMOT23xS XM-CAN connection diagram .............................................................................. 23
3.8.5...... Analog Inputs Connection Recommendations ...................................................................... 24
3.8.5.1 0-5V Input Range............................................................................................................ 24
3.8.5.2 +/- 10V to 0-5V Input Range Adapter ............................................................................. 24
3.8.5.3 Recommendation for wiring............................................................................................ 24
3.8.6...... Power Supply Connection Recommendations ...................................................................... 25
3.8.6.1 Recommendations for Supply Wiring ............................................................................. 25
3.8.6.2 Recommendations to limit over-voltage during braking ................................................. 25

Technosoft 2018 3 iMOT Intelligent Motors Line Technical Reference
3.8.7...... Serial RS-232 connection Recommendations ....................................................................... 25
3.8.8...... CAN-bus connection (for CAN motors only) Recommendations........................................... 26
3.8.9...... Removal from Autorun Mode for CAN motors ....................................................................... 26
3.9 CAN Protocol Selection for CAN motors. TMLCAN/CANopen ................................ 27
3.10 Axis ID Selection for CAN motors(SW1 settings) ................................................. 27
3.11 Recommendations for EtherCAT® Wiring ............................................................ 28
3.12 EtherCAT® LED indicators..................................................................................... 28
3.12.1.... EtherCAT® LED indicator states ........................................................................................... 29
3.13 Electrical Specifications......................................................................................... 29
3.13.1.... Operating Conditions ............................................................................................................. 29
3.13.2.... Storage Conditions ................................................................................................................ 29
3.13.3.... Environmental Characteristics ............................................................................................... 30
3.13.4.... Logic Supply Input (+VLOG) .................................................................................................... 30
3.13.5.... Motor Supply Input (+VMOT).................................................................................................... 30
3.13.6.... Digital Inputs .......................................................................................................................... 31
3.13.7.... Digital Outputs ....................................................................................................................... 31
3.13.8.... Analog 0…5V Input (ANLG) .................................................................................................. 32
3.13.9.... RS-232................................................................................................................................... 32
3.13.10.. EARTH Connection................................................................................................................ 32
3.13.11.. CAN-Bus (for CAN motors).................................................................................................... 32
3.13.12.. EtherCAT (for CAT motors) ................................................................................................... 32
3.14 Torque – Speed characteristic ............................................................................... 33
3.14.1.... iMOT17xB XM/TM-CAN/CAT ................................................................................................ 33
3.14.2.... iMOT172S XM/TM-CAN/CAT ................................................................................................ 33
3.14.3.... iMOT23xS XM-CAN............................................................................................................... 33
4Memory Map ........................................................................................................... 34

Technosoft 2018 4 iMOT Intelligent Motors Line Technical Reference
Read This First
Whilst Technosoft believes that the information and guidance given in this manual is correct, all parties must
rely upon their own skill and judgment when making use of it. Technosoft does not assume any liability to anyone for
any loss or damage caused by any error or omission in the work, whether such error or omission is the result of
negligence or any other cause. Any and all such liability is disclaimed.
All rights reserved. No part or parts of this document may be reproduced or transmitted in any form or by any
means, electrical or mechanical including photocopying, recording or by any information-retrieval system without
permission in writing from Technosoft S.A.
The information in this document is subject to change without notice.
About This Manual
This book is a technical reference manual for:
Product Name Part Number Description
iMOT171B TM-CAN P042.111.E320 Brushless Nema 17, size 1, CAN version, IP66 connectors
iMOT171B TM-CAT P042.111.E322 Brushless Nema 17, size 1, EtherCAT version, IP66 connectors
iMOT171B XM-CAN P042.111.E120 Brushless Nema 17, size 1, CAN version, Molex connectors
iMOT172B TM-CAN P042.121.E320 Brushless Nema 17, size 2, CAN version, IP66 connectors
iMOT172B TM-CAT P042.121.E322 Brushless Nema 17, size 2, EtherCAT version, IP66 connectors
iMOT172B XM-CAN P042.121.E120 Brushless Nema 17, size 2, CAN version, Molex connectors
iMOT173B TM-CAN P042.131.E320 Brushless Nema 17, size 3, CAN version, IP66 connectors
iMOT173B TM-CAT P042.131.E322 Brushless Nema 17, size 3, EtherCAT version, IP66 connectors
iMOT173B XM-CAN P042.131.E120 Brushless Nema 17, size 3, CAN version, Molex connectors
iMOT172S TM-CAN P036.121.E320 Stepper Nema 17, size 2, CAN version, IP66 connectors
iMOT172S TM-CAT P036.121.E323 Stepper Nema 17, size 2, EtherCAT version, IP66 connectors
iMOT172S XM-CAN P036.121.E120 Stepper Nema 17, size 2, CAN version, Molex connectors
iMOT232S XM-CAN P036.222.E120 Stepper Nema 23, size 2, CAN version, Molex connectors
iMOT233S XM-CAN P036.232.E120 Stepper Nema 23, size 3, CAN version, Molex connectors
In order to operate any of the iMOT Intelligent Motors you need to pass through 3 steps:
Step 1 Hardware installation
Step 2 Drive setup using Technosoft EasySetUp / EasyMotion Studio software for drive commissioning
Step 3 Motion programming using one of the options:
The drive’s built-in motion controller executing a Technosoft Motion Language (TML) program
developed using Technosoft EasyMotion Studio software and stored in the local non-volatile memory
A TML_LIB motion library for PCs (Windows or Linux)
A TML_LIB motion library for PLCs1
A CANopen master2or an EtherCAT master – depending on the version of the iMOT
A distributed control approach which combines the above options, like for example a host handling the
upper level of the machine application and calling motion functions pre-programmed on the drive in TML
for lower level of the machine application
This manual covers Step 1 in detail. It describes the various models of the iMOT Intelligent Motors line hardware
including the technical data, the connectors and the wiring diagrams needed for installation.
For Step 2 and 3, please consult the related documentation.
1Available for Siemens SIMATIC S7-300, OMRON CJ1, and X20CS1070 from B&R
2Available only for CAN versions, configured for CANOpen operation

Technosoft 2018 5 iMOT Intelligent Motors Line Technical Reference
Notational Conventions
This document uses the following conventions:
•iMOT – all products described in this manual
•IU units –Internal units of the drive
•SI units –International standard units (meter for length, seconds for time etc.)
•TML – Technosoft Motion Language
•CANopen – Standard communication protocol that uses 11bit message identifiers over CAN-bus
and enables connection with different brand products
•TMLCAN – Technosoft’s own communication protocol for exchanging TML commands only
between Technosoft drives/motors via CAN-bus, using 29bit message identifiers
•CoE – CANopen over EtherCAT, CANopen application protocol via EtherCAT® layer
Trademarks
EtherCAT® is registered trademark and patented technology, licensed by Beckhoff Automation GmbH,
Germany. In this document it will be further referenced as EtherCAT.
Related Documentation
iMOT Intelligent Motors line Datasheets
– describes the hardware connections of the iMOT Intelligent Motors line including the technical data and
connectors.
Help of the EasySetUp software –describes how to use EasySetUp to quickly setup any Technosoft drive
for your application using only 2 dialogues. The output of EasySetUp is a set of setup data that can be
downloaded into the drive EEPROM or saved on a PC file. At power-on, the drive is initialized with the
setup data read from its EEPROM. With EasySetUp it is also possible to retrieve the complete setup
information from a drive previously programmed. EasySetUp can be downloaded free of charge from
Technosoft web page
iPOS CANopen Programming (part no. P091.063.CANopen.iPOS.UM.xxxx) – explains how to program the
iPOS family of intelligent drives using CANopen protocol and describes the associated object dictionary
for CiA 301 v.4.2 application layer and communication profile, CiA WD 305 v.2.2.13 layer settings
services and protocols and CiA DSP 402 v3.0 device profile for drives and motion control now included
in IEC 61800-7-1 Annex A, IEC 61800-7-201 and IEC 61800-7-301 standards. Since the iMOT Intelligent
Motors are based on the iPOS family of drives, this manual also applies to them.
CoE Programming (part no. P091.064.EtherCAT.iPOS.UM.xxxx) – explains how to program the Technosoft
intelligent drives using CAN application protocol over EtherCAT® and describes the associated object
dictionary. Since the iMOT Intelligent Motors are based on the iPOS family of drives, this manual also
applies to them.
Motion Programming using EasyMotion Studio (part no. P091.034.ESM.UM.xxxx) –describes how to use
the EasyMotion Studio to create motion programs using in Technosoft Motion Language (TML).
EasyMotion Studio platform includes EasySetUp for the drive/motor setup, and a Motion Wizard for the
motion programming. The Motion Wizard provides a simple, graphical way of creating motion programs
and automatically generates all the TML instructions. With EasyMotion Studio you can fully benefit from
a key advantage of Technosoft drives – their capability to execute complex motions without requiring an
external motion controller, thanks to their built-in motion controller. A demo version of EasyMotion
Studio (with EasySetUp part fully functional) can be downloaded free of charge from the
Technosoft web page
TML_LIB v2.0 (part no. P091.040.v20.UM.xxxx) – explains how to program in C, C++,C#, Visual Basic or
Delphi Pascal a motion application for the Technosoft intelligent drives or motors using TML_LIB v2.0
motion control library for PCs. The TML_lib includes ready-to-run examples that can be executed on
Windows or Linux (x86 and x64).
TML_LIB_LabVIEW v2.0 (part no. P091.040.LABVIEW.v20.UM.xxxx) – explains how to program in
LabVIEW a motion application for the Technosoft intelligent drives or motors using TML_LIB_Labview
v2.0 motion control library for PCs. The TML_Lib_LabVIEW includes over 40 ready-to-run examples.
TML_LIB_S7 (part no. P091.040.S7.UM.xxxx) – explains how to program in a PLC Siemens series S7-300
or S7-400 a motion application for the Technosoft intelligent drives or motors using TML_LIB_S7 motion
control library. The TML_LIB_S7 library is IEC61131-3 compatible.
TML_LIB_CJ1 (part no. P091.040.CJ1.UM.xxxx) – explains how to program in a PLC Omron series CJ1 a
motion application for the Technosoft intelligent drives or motors using TML_LIB_CJ1 motion control
library for PLCs. The TML_LIB_CJ1 library is IEC61131-3 compatible.
TML_LIB_X20 (part no. P091.040.X20.UM.xxxx) – explains how to program in a PLC B&R series X20 a
motion application for the Technosoft intelligent drives or motors using TML_LIB_X20 motion control
library for PLCs. The TML_LIB_X20 library is IEC61131-3 compatible.
TechnoCAN (part no. P091.063.TechnoCAN.UM.xxxx) – presents TechnoCAN protocol – an extension of
the CANopen communication profile used for TML commands

Technosoft 2018 6 iMOT Intelligent Motors Line Technical Reference
If you Need Assistance …
If you want to … Contact Technosoft at …
Visit Technosoft online
World Wide Web: http://www.technosoftmotion.com/
Receive general information
or assistance (see Note)
Ask questions about product
operation or report suspected
problems (see Note)
Make suggestions about,
or report errors in documentation.
World Wide Web: http://www.technosoftmotion.com/
Email: contact@technosoftmotion.com
Fax: (41) 32 732 55 04
Email: hotline@technosoftmotion.com
Email: support@technosoftmotion.com
Mail: Technosoft SA
Avenue des Alpes 20
CH-2000 Neuchatel, NE
Switzerland
1 Safety information
Read carefully the information presented in this chapter before carrying out the intelligent motor installation
and setup! It is imperative to implement the safety instructions listed hereunder.
This information is intended to protect you, the intelligent motor and the accompanying equipment during the product
operation. Incorrect handling of the intelligent motor can lead to personal injury or material damage.
The following safety symbols are used in this manual:
WARNING!
SIGNALS A DANGER TO THE OPERATOR WHICH MIGHT CAUSE BODILY
INJURY. MAY INCLUDE INSTRUCTIONS TO PREVENT THIS SITUATION.
CAUTION!
SIGNALS A DANGER FOR THE INTELLIGENT MOTOR WHICH MIGHT DAMAGE
THE PRODUCT OR OTHER EQUIPMENT. MAY INCLUDE INSTRUCTIONS TO
AVOID THIS SITUATION.
CAUTION! INDICATES AREAS SENSITIVE TO ELECTROSTATIC DISCHARGES (ESD) WHICH
REQUIRE HANDLING IN AN ESD PROTECTED ENVIRONMENT.
1.1 Warnings
WARNING! THE VOLTAGE USED IN THE INTELLIGENT MOTOR MIGHT CAUSE ELECTRICAL
SHOCKS. DO NOT TOUCH LIVE PARTS WHILE THE POWER SUPPLIES ARE ON.
WARNING!
TO AVOID ELECTRIC ARCING AND HAZARDS, NE
VER CONNECT /
DISCONNECT WIRES FROM THE INTELLIGENT MOTOR WHILE THE POWER
SUPPLIES ARE ON.
WARNING! THE INTELLIGENT MOTOR MAY HAVE HOT SURFACES DURING OPERATION.

Technosoft 2018 7 iMOT Intelligent Motors Line Technical Reference
WARNING! DURING OPERATION THE MOTOR WILL MOVE.
KEEP AWAY FROM ALL
MOVING PARTS TO AVOID INJURY.
WARNING! IN A DOMESTIC ENVIROMENT THIS PRODUCT MAY CAUSE INTERFERENCE IN
WHICH CASE SUPPLEMENTARY MITIGATION MEASURES MAY BE REQUIRED.
1.2 Cautions
CAUTION! THE POWER SUPPLIES CONNECTED TO THE INTELLIGENT MOTOR MUST
COMPLY WITH THE PARAMETERS SPECIFIED IN THIS DOCUMENT
CAUTION! TROUBLESHOOTING AND SERVICING ARE PERMIT
TED ONLY FOR
PERSONNEL AUTHORISED BY TECHNOSOFT
CAUTION!
THE INTELLIGENT MOTOR CONTAINS ELECTROSTATICALLY SENSITIVE
COMPONENTS WHICH MAY BE DAMAGED BY INCOR
RECT HANDLING.
THEREFORE THE INTELLIGENT MOTOR SHALL BE REMOVED FR
OM ITS
ORIGINAL PACKAGE ONLY IN AN ESD PROTECTED ENVIRONMENT
To prevent electrostatic damage, avoid contact with insulating materials, such as synthetic fabrics or plastic surfaces.
In order to discharge static electricity build-up, place the intelligent motor on a grounded conductive surface and also
ground yourself.
1.3 Quality system, conformance and certifications
IQNet and Quality Austria certification about the implementation and maintenance of the
Quality Management System which fulfills the requirements of Standard ISO 9001:2015.
Quality Austria Certificate about the application and further development of an effective
Quality Management System complying with the requirements of Standard ISO 9001:2015
REACH Compliance - TECHNOSOFT hereby confirms that this product comply with the legal
obligations regarding Article 33 of the European REACH Regulation 1907/2006 (Registration,
Evaluation, Authorization and Restriction of Chemicals), which came into force on 01.06.2007.
RoHS Compliance - Technosoft SA here with declares that this product is manufactured in
compliance with the RoHS directive 2002/95/EC on the restriction of the use of certain
hazardous substances in electrical and electronic equipment (RoHS)
Technosoft SA hereby declares that this product conforms to the following European
applicable directives:
2014/30/EU Electromagnetic Compatibility (EMC) Directive
2014/35/EU Low Voltage Directive (LVD)
93/68/EEC CE Marking Directive
Conflict minerals statement - Technosoft declares that the company does not purchase
3T&G (tin, tantalum, tungsten & gold) directly from mines or smelters...
We have no indication that Technosoft products contain minerals from conflict mines or
smelters in and around the DRC.
The following technical standards have been applied in the design and qualification of the iMOT family:
EN61800-3: 2004 + Amendment 1: 2011
Adjustable Speed Electrical Power Drive Systems - EMC Requirements
BDM (Basic Drive Module) / Category C3: intended for use in Second Environment
EN61800-5-1: 2007 + Amendment 1: 2016
Adjustable Speed Electrical Power Drive Systems - Safety Requirements: Electrical, Thermal and Energy
BDM (Basic Drive Module) / DVC A, Pollution Degree 2, Over-voltage Category I
EN60529: 1992 + Amendment 2: 2013
Degree of protection provided by enclosure

Technosoft 2018 8 iMOT Intelligent Motors Line Technical Reference
IP00
EN55011: 2009 + Amendment 2: 2010
Radiated Radio Disturbance Characteristics of Industrial, Scientific and Medical Equipment
Class A / Group 1: 30MHz...1GHz, 50...60dBμV/m @10m (EN61800-3 Table 18)
EN55011: 2009 + Amendment 1: 2010
Conducted Mains Terminal Radio Disturbance Measurement
Class A / Group 1: Supply lines, 0.15MHz...30MHz, 46...66dB (EN61800-3 Table 17 <=100A)
EN61000-4-2: 2009
Electrostatic Discharge (ESD) Immunity
Level 2, Criteria A: +/-4KV Contact Discharge, Criteria A
Level 3, Criteria A: +/-8KV Air Discharge, Criteria A (EN61800-3 Table 12)
EN61000-4-3: 2006 + Amendment 2: 2011
Radiated Radiofrequency Electromagnetic Field Immunity
Level 3, Criteria A: 10V/m 80MHz...1GHz, 3V/m 1.4GHz...2GHz, 1V/m 2...2.7GHz
EN61000-4-4: 2004 + Amendment 1: 2010
Electrical Fast Transient / Burst Immunity
Level 3, Criteria A: Supplu lines, +/-2KV, Galvanic coupling
Level 3, Criteria A: Signals lines, +/-1KV, Capacitive coupling
EN61000-4-5: 2014
Surge Immunity
Level 2, Criteria B: Supply lines, +/-1KV line-to-line
EN61000-4-6: 2009
Conducted Disturbances induced by Radiofrequency Fields Immunity
Level 3, Criteria A: Signal lines, 10V, 0.15MHz...80MHz
For other certifications visit: http://technosoftmotion.com/en/quality-system

Technosoft 2018 9 iMOT Intelligent Motors Line Technical Reference
2 Product Overview
2.1 Introduction
The iMOT line of intelligent brushless and step motors combines an intelligent drive, a motor and a position sensor into
a single unit. The result is a cost effective, compact solution that translates motion commands stored by the user in its
own memory or received through a communication channel into mechanical motion.
All iMOTs perform position, speed or torque control and can be configured for either stand-alone or multi-axis operation.
Beside the motor and position sensor, thanks to the intelligent drive, the iMOTs combine motion controller PID, power
stage drive and PLC functionality in a single unit and are capable to execute complex motions without requiring
intervention of an external motion controller. Using the high-level Technosoft Motion Language (TML) the following
operations can be executed directly at drive level:
Setting various motion modes (profiles, PVT, PT, electronic gearing or camming, etc.)
Changing the motion modes and/or the motion parameters
Executing homing sequences
Controlling the program flow through:
Conditional jumps and calls of TML functions
TML interrupts generated on pre-defined or programmable conditions (protections triggered,
transitions on limit switch or capture inputs, etc.)
Waits for programmed events to occur
Handling of digital I/O and analogue input signals
Executing arithmetic and logic operations
Performing data transfers between axes
Controlling motion of an axis from another one via motion commands sent between axes
Sending commands to a group of axes (multicast). This includes the possibility to start simultaneously
motion sequences on all the axes from the group
Synchronizing all the axes from a network
By implementing motion sequences directly at the iMOT level you can really distribute the intelligence between the
master and the iMOTs in complex multi-axis applications, reducing both the development time and the overall
communication requirements. For example, instead of trying to command each movement of an axis, you can program
the iMOTs using TML to execute motion tasks and inform the master when these tasks are done. Thus, for each axis
control the master job may be reduced at: calling TML functions stored in the iMOT’s EEPROM and waiting for a
message, which confirms the TML functions execution completion.
All iMOT Intelligent Motors are equipped with a serial RS232 and a CAN 2.0B / EtherCAT interface depending on the
model. The CAN models can be set by hardware pins to operate in one of the 2 communication protocol modes:
CANopen
TMLCAN
When CANopen mode is selected, the iMOT conforms to CiA 301 v4.2 application layer communication profile, the
CiA WD 305 v2.2.13 and CiA DSP 402 v3.0 device profile for drives and motion control, now included in IEC 61800-7-
1 Annex A, IEC 61800-7-201 and IEC 61800-7-301 standards. In this mode, it may be controlled via a CANopen master.
The iMOT drive offers the possibility for a CANopen master to call motion sequences/ functions, written in TML and
stored in the drive EEPROM, using manufacturer specific objects. Also, the intelligent motors can communicate
separately between each other by using non reserved 11 bit identifiers (TechnoCAN protocol).
When TMLCAN mode is selected, the iMOT behaves as standard Technosoft intelligent drive and conforms to
Technosoft protocol for exchanging TML commands via CAN-bus. When TMLCAN protocol is used, it is not mandatory
to have a master. Any iMOT can be set to operate standalone, and may play the role of a master to coordinate both the
network communication/synchronization and the motion application via TML commands sent directly to the other
intelligent motors.
When higher level coordination is needed, apart from a CANopen master, the iMOT intelligent motors can also be
controlled via a PC or a PLC using one of the TML_LIB motion libraries.
For the commissioning of the intelligent motors, EasySetUp or EasyMotion Studio PC applications may be used.
EasySetUp is a subset of EasyMotion Studio, containing only the setup part (drive + motor). The output of EasySetUp
is a set of setup data that can be downloaded into the iMOT EEPROM or saved on a PC file. At power-on, the intelligent
motor is initialized with the setup data read from its EEPROM. With EasySetUp it is also possible to retrieve the complete
setup information from an iMOT previously programmed. EasySetUp shall be used for drive setup + motor in all cases
where the motion commands are sent exclusively from a master. Hence neither the iMOT TML programming capability
nor the camming mode are used. EasySetUp can be downloaded free of charge from Technosoft web page.

Technosoft 2018 10 iMOT Intelligent Motors Line Technical Reference
EasyMotion Studio platform includes EasySetUp for the system setup, and a Motion Wizard for the motion
programming. The Motion Wizard provides a simple, graphical way of creating motion programs and automatically
generates all the TML instructions. Beside the setup and motion wizards, EasyMotion Studio contain also various tools
for on-line monitoring and troubleshooting of the iMOT performance. EasyMotion Studio is usually the choice when it
comes to the CAN versions of the iMOT that are going to be used in TMLCAN mode. However, it can also be used with
the CANopen protocol, if the user wants to call TML functions stored in the drive EEPROM or to use the camming mode.
With camming mode, EasyMotion Studio offers the possibility to quickly download and test a cam profile and also to
create a .sw file with the cam data. The .sw file can be afterwards stored in a master and downloaded to the drive,
wherever needed. A demo version of EasyMotion Studio (with EasySetUp part fully functional) can be
downloaded free of charge from Technosoft web page.
2.2 Product Features
•Fully digital intelligent servo or stepper motor with embedded motion controller, drive and single turn absolute
position sensor
•Very compact design
•2 control options for stepper model: closed loop stepless servo / open loop microstepping (with steploss
detection)
•Various modes of operation, including: torque, speed or position control; position or speed profiles, Cyclic
Synchronous Position (CSP) for CANopen mode, external reference mode analogue or sent via a
communication bus
•Technosoft Motion Language (TML) instruction set for the definition and execution of motion sequences
•Standalone operation with stored motion sequences
•Communication:
•RS-232 serial up to 115kbits/s
•CAN-bus 2.0B up to 1Mbit/s (for CAN drives)
•EtherCAT up to 100Mbit/s (for EtherCAT motors)
•Digital and analog I/Os:
•4 digital inputs: 5-24V, programmable polarity: sourcing/NPN or sinking/PNP (5 digital inputs for the
iMOT23xS models)
•2 digital outputs: 5-24V, with 0.5A capacity, sinking/NPN open-collector
•1 analogue input: 12 bits resolution, 0 … 5Vdc range
•Electro-Mechanical brake support: software configurable digital output to control motor brake
•Feedback device:
•Integrated absolute single-turn position sensor offering a resolution of 4096 counts/rev
•Various motion programming modes:
•Position profiles with trapezoidal or S-curve speed shape
•Position, Velocity, Time (PVT) 3rd order interpolation
•Position, Time (PT) 1st order interpolation
•Cyclic Synchronous Position (CSP) for CANopen/EtherCAT mode
•Electronic gearing and camming
•35 Homing modes
•16 h/w selectable addresses depending on model, otherwise 127/255 software selectable addresses
(CANopen / TMLCAN)
•Two CAN operation modes selectable by HW pin (only for CAN motors):
•CANopen – conforming with CiA 301 v4.2, CiA WD 305 v2.2.13 and CiA DSP 402 v3.0
•TMLCAN – intelligent drive conforming with Technosoft protocol for exchanging TML commands via
CAN-bus
•2.5K ×16 internal SRAM memory for data acquisition
•4K ×16 E2ROM to store TML motion programs, cam tables and other user data
•Motor supply: 12-48V
•Logic supply: 15-36V.
•Operating ambient temperature: 0-40°C (over 40°C with derating)
•Protections:
•Short-circuit between motor phases or between motor phases and ground
•Over and under-voltage
•Over-current and I2t
•Over-temperature
•Communication error
•Control error

Technosoft 2018 11 iMOT Intelligent Motors Line Technical Reference
2.3 Identification Labels
Figure 2.3.1. iMOT intelligent motors identification labels
The iMOT intelligent motors can have the following part numbers and names on the identification label:
Product Name Part Number Description
iMOT171B TM-CAN P042.111.E320 Brushless Nema 17, size 1, CAN version, IP66 connectors
iMOT171B TM-CAT P042.111.E322 Brushless Nema 17, size 1, EtherCAT version, IP66 connectors
iMOT171B XM-CAN P042.111.E120 Brushless Nema 17, size 1, CAN version, Molex connectors
iMOT172B TM-CAN P042.121.E320 Brushless Nema 17, size 2, CAN version, IP66 connectors
iMOT172B TM-CAT P042.121.E322 Brushless Nema 17, size 2, EtherCAT version, IP66 connectors
iMOT172B XM-CAN P042.121.E120 Brushless Nema 17, size 2, CAN version, Molex connectors
iMOT173B TM-CAN P042.131.E320 Brushless Nema 17, size 3, CAN version, IP66 connectors
iMOT173B TM-CAT P042.131.E322 Brushless Nema 17, size 3, EtherCAT version, IP66 connectors
iMOT173B XM-CAN P042.131.E120 Brushless Nema 17, size 3, CAN version, Molex connectors
iMOT172S TM-CAN P036.121.E320 Stepper Nema 17, size 2, CAN version, IP66 connectors
iMOT172S TM-CAT P036.121.E323 Stepper Nema 17, size 2, EtherCAT version, IP66 connectors
iMOT172S XM-CAN P036.121.E120 Stepper Nema 17, size 2, CAN version, Molex connectors
iMOT232S XM-CAN P036.222.E120 Stepper Nema 23, size 2, CAN version, Molex connectors
iMOT233S XM-CAN P036.232.E120 Stepper Nema 23, size 3, CAN version, Molex connectors

Technosoft 2018 12 iMOT Intelligent Motors Line Technical Reference
3 Hardware Installation
3.1 iMOT17xB TM-CAN and TM-CAT models dimensions
19
5
-
0
0.013
21 ±0.5016.504
61
L
42
31 ±0.20
42
31 ±0.20
22
-
0
0.05
45°
4 x M3 threaded holes
depth 4mm
51
61
37
45
20
FR
FA
Model
L [mm]
iMOT171B
44±1.5
iMOT172B
62±1.5
iMOT173B
82±1.5
Axial force FA[N]
10
Radial force FR[N]
28
Figure 3.1. iMOT17xB TM-CAN and TM-CAT models dimensions
All dimensions are in mm. The drawings are not to scale. Tolerance ±0.1mm (unless otherwise noted).
TM-CAN model shown.
3.2 iMOT17xB XM-CAN models dimensions
19
5
-
0
0.013
21 ±0.5016.504
61
L
42
31 ±0.20
42
31 ±0.20
22
-
0
0.05
45°
4 x M3 threaded holes
depth 4mm
51
61
37
45
20
FR
FA
Model
L [mm]
iMOT171B
44±1.5
iMOT172B
62±1.5
iMOT173B
82±1.5
Axial force FA[N]
10
Radial force FR[N]
28
Figure 3.2. iMOT17xB XM-CAN models dimensions
All dimensions are in mm. The drawings are not to scale. Tolerance ±0.1mm (unless otherwise noted).

Technosoft 2018 13 iMOT Intelligent Motors Line Technical Reference
3.3 iMOT172S XM-CAN model dimensions
5 -0
0.012
61
24 ±0.50
22
48 ±1.5016.504
42.30
42.30
22
-
0
0.05
31 ±0.20
31 ±0.20
4 x M3 threaded holes
depth 4.5mm
51
61
37
45
20
FR
FA
Axial force FA[N]
7
Radial force FR[N]
20
Figure 3.3. iMOT172S XM-CAN model dimensions
All dimensions are in mm. The drawings are not to scale. Tolerance ±0.1mm (unless otherwise noted).
3.4 MOT172S TM-CAN and TM-CAT models dimensions
5
-0
0.012
61
24 ±0.50
22
48 ±1.5016.504
42.30
42.30
22
-
0
0.05
31 ±0.20
31 ±0.20
4 x M3 threaded holes
depth 4.5mm
51
61
37
45
20
FR
FA
Axial force FA[N]
7
Radial force FR[N]
20
Figure 3.4. iMOT172S TM-CAN and TM-CAT models dimensions
All dimensions are in mm. The drawings are not to scale. Tolerance ±0.1mm (unless otherwise noted). TM-
CAN model shown.

Technosoft 2018 14 iMOT Intelligent Motors Line Technical Reference
3.5 iMOT23xS XM-CAN models dimensions
47.20 ±0.20
56
47.20 ±0.20
56
38 ±0.05
45°
4 x 5 holes
20
22 ±1
6.34
-0
0.013
L
16.80
73.60
56.80
73.60
Model
L [mm]
iMOT232S
73.2
iMOT233S
48.2
20
FR
FA
Axial force FA[N]
15
Radial force FR[N]
75
Figure 3.5. iMOT23xS XM-CAN models dimensions
All dimensions are in mm. The drawings are not to scale. Tolerance ±0.1mm (unless otherwise noted).

Technosoft 2018 15 iMOT Intelligent Motors Line Technical Reference
3.6 Mechanical Mounting
There are no restrictions to the mounting orientation of the iMOTs although you must pay attention to the axial forces
“FA” in Figure 3.1..Figure 3.5 applied to the motor shaft during the installation procedure and on the final position. At
the bottom of the motor shaft there’s a small magnet (marked with red) that is positioned very close to the magnetic
encoder circuit surface (marked with green). The motor housing allows axial movements of the shaft big enough to hit
and destroy the magnetic encoder circuit if a hammer or sufficient force is used.
Figure 3.1. Panel cut-out
The IMOT intelligent motor was designed to be cooled by natural convection. It can be mounted horizontally or vertically.
Always bolt the motor to a metallic surface, which will act as a heat sink. Use only the front plate for mounting.
Make sure the metallic surface is free from paint, eloxation, etc. and that the surface is part of a construction connected
to earth (PE – protection earth). This will ensure proper EMC performance.

Technosoft 2018 16 iMOT Intelligent Motors Line Technical Reference
3.7 Connectors and Pinouts
3.7.1 Connectors and pinouts for iMOT17xB/iMOT172S TM-CAN models

Technosoft 2018 17 iMOT Intelligent Motors Line Technical Reference
3.7.2 Connectors and pinouts for iMOT17xB/iMOT172S TM-CAT models

Technosoft 2018 18 iMOT Intelligent Motors Line Technical Reference
3.7.3 Connectors and pinouts for iMOT17xB/iMOT172S XM-CAN models

Technosoft 2018 19 iMOT Intelligent Motors Line Technical Reference
3.7.4 Connectors and pinouts for iMOT23xS XM-CAN models

Technosoft 2018 20 iMOT Intelligent Motors Line Technical Reference
3.8 Connection diagrams
3.8.1 iMOT17xB/iMOT172S TM-CAN connection diagram
Figure 3.2. iMOT17xB/iMOT172S TM-CAN connection diagram
This manual suits for next models
14
Table of contents
Popular Engine manuals by other brands
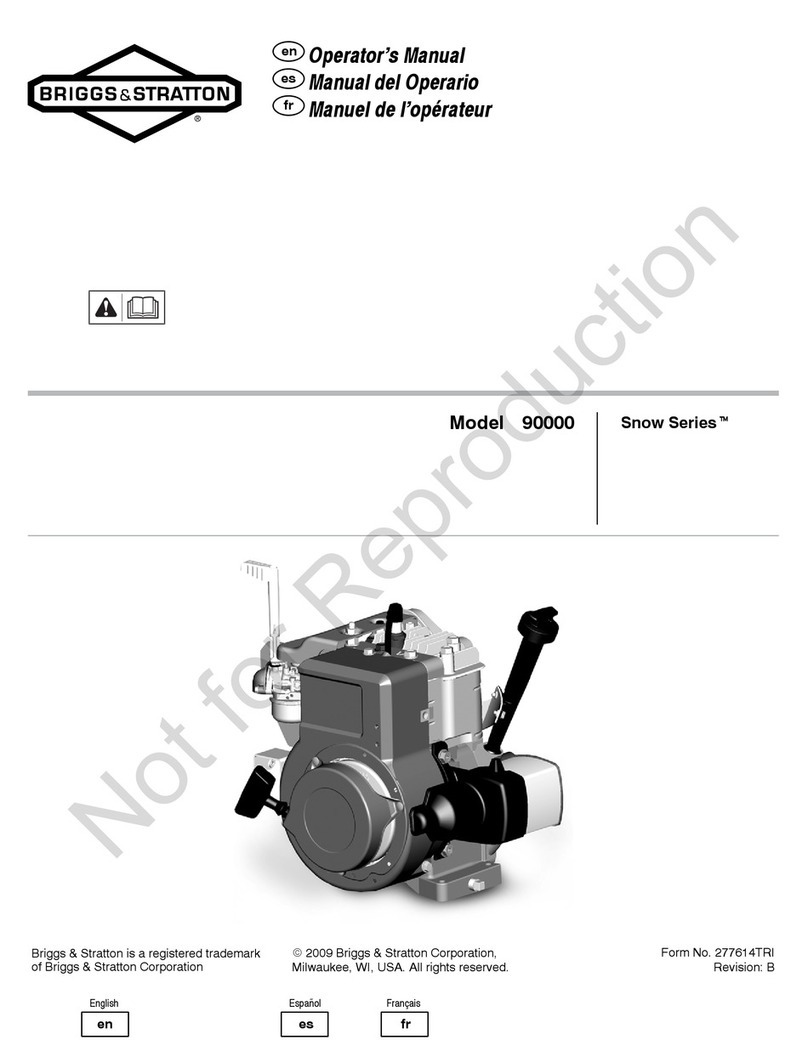
Briggs & Stratton
Briggs & Stratton Snow Series MAX Operator's manual

Briggs & Stratton
Briggs & Stratton 150000 HORIZONTAL SERIES Operator's manual
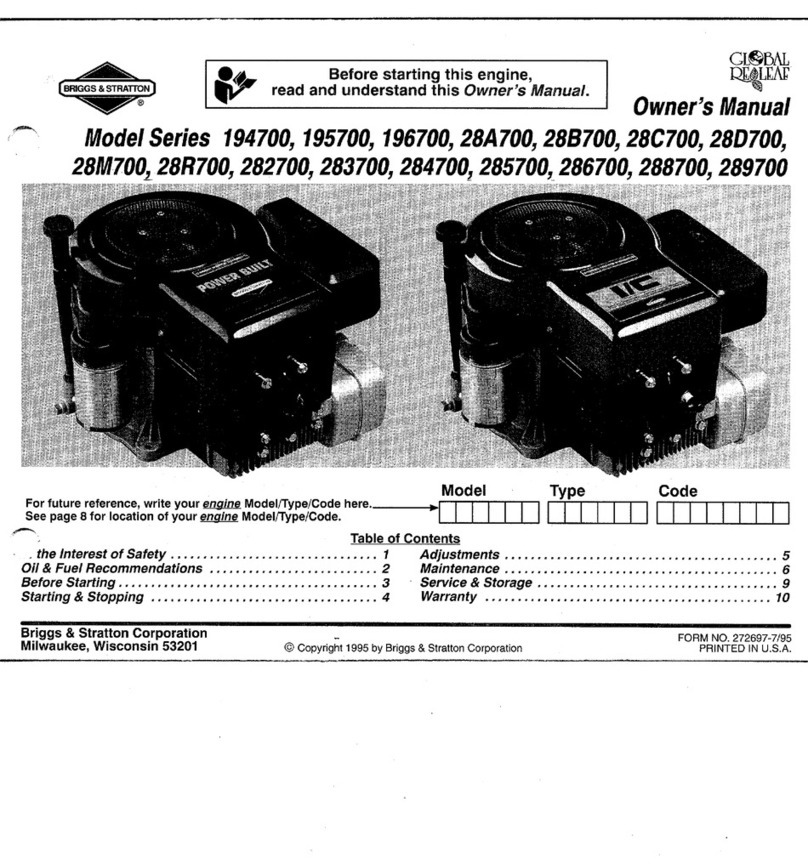
Briggs & Stratton
Briggs & Stratton 194700 Series owner's manual
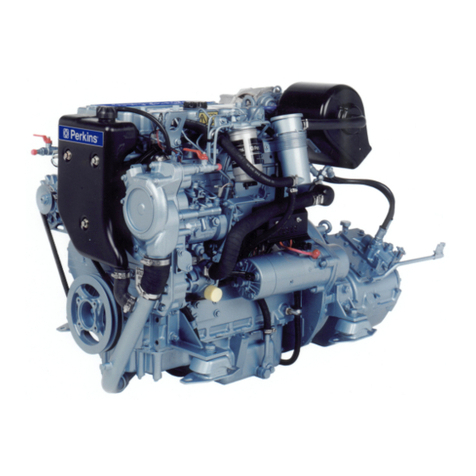
Perkins
Perkins M92 User handbook
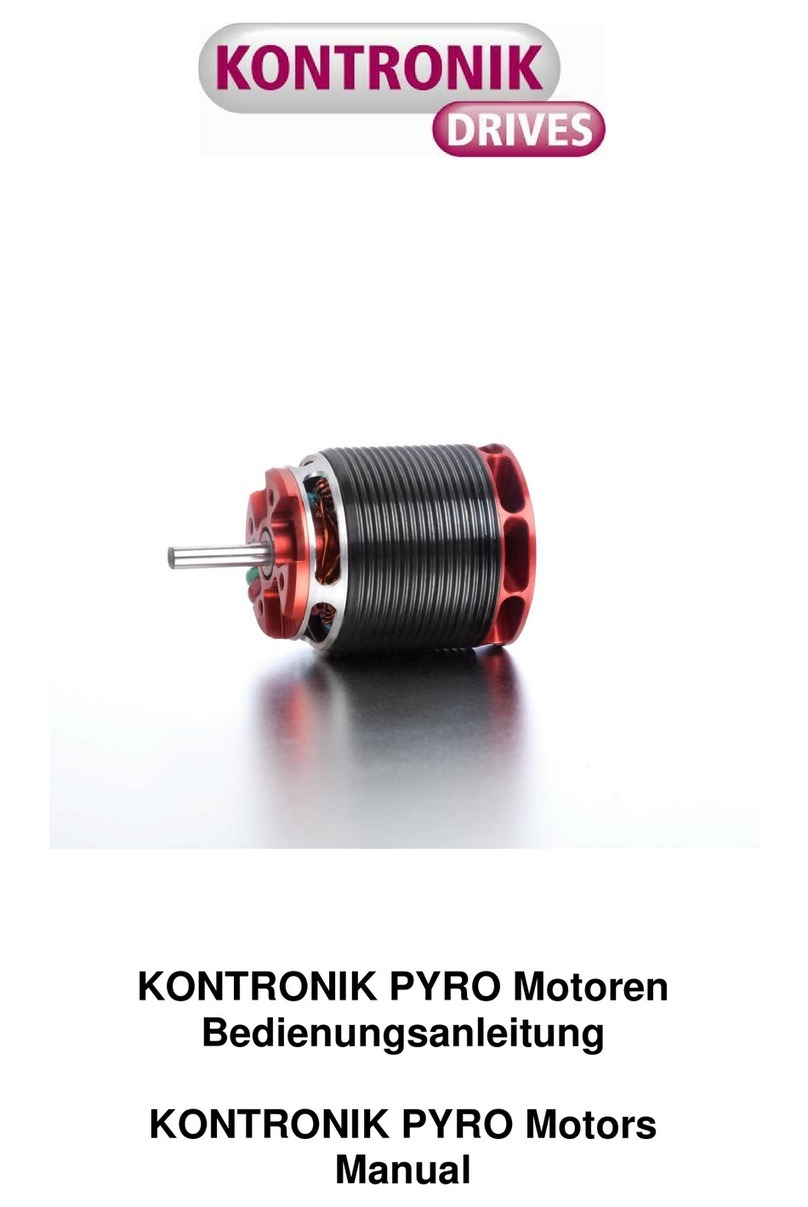
KONTRONIK
KONTRONIK PYRO manual
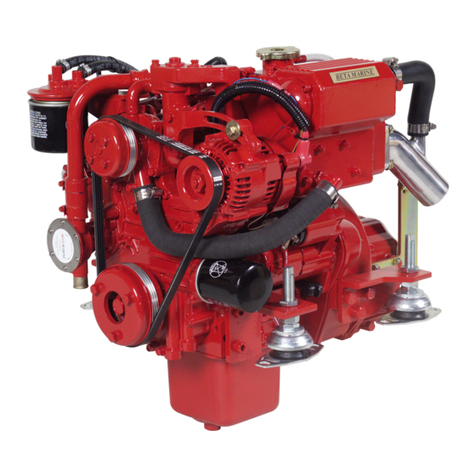
Beta Marine
Beta Marine Beta 14 installation guide