Textron Lycoming IO-360 User manual

This manual has reduce to only the IO-360 AIA that is in the club
aircraft. If you want the full manual for all 360 models, try:
https://www.lycoming.com/sites/default/files/O-HO-IO-HIO-AIO%20%
26%20TIO-360%20Oper%20Manual%2060297-12.pdf

Operator’s Manual
Lycoming
O-360, HO-360,
IO-360, AIO-360,
HIO-360 & TIO-360 Series
Approved by FAA
8th Edition Part No. 60297-12
652 Oliver Street
Williamsport, PA. 17701 U.S.A. October 2005
570/323-6181

O, HO, IO, AIO, HIO, TIO-360 Series Operator’s Manual
Lycoming Part Number: 60297-12
©2005 by Lycoming. All rights reserved.
Lycoming and “Powered by Lycoming” are trademarks or registered trademarks of
Lycoming.
All brand and product names referenced in this publication are trademarks or registered
trademarks of their respective companies.
For additional information:
Mailing address:
Lycoming Engines
652 Oliver Street
Williamsport, PA 17701 U.S.A.
Phone:
Factory: 570-323-6181
Sales Department: 570-327-7268
Fax: 570-327-7101
Lycoming’s regular business hours are Monday through Friday from 8:00 AM
through 5:00 PM Eastern Time (-5 GMT)
Visit us on the World Wide Web at:
http://www.lycoming.com
Revised June 2007

LYCOMING OPERATOR’S MANUAL
ATTENTION
OWNERS, OPERATORS, AND MAINTENANCE PERSONNEL
This operators manual contains a description of the engine, its specifications, and detailed information on
how to operate and maintain it. Such maintenance procedures that may be required in conjunction with
periodic inspections are also included. This manual is intended for use by owners, pilots and maintenance
personnel responsible for care of Lycoming powered aircraft. Modifications and repair procedures are
contained in Lycoming overhaul manuals; maintenance personnel should refer to these for such procedures.
SAFETY WARNING
NEGLECTING TO FOLLOW THE OPERATING INSTRUCTIONS AND TO CARRY OUT PERIODIC
MAINTENANCE PROCEDURES CAN RESULT IN POOR ENGINE PERFORMANCE AND POWER
LOSS. ALSO, IF POWER AND SPEED LIMITATIONS SPECIFIED IN THIS MANUAL ARE EXCEEDED,
FOR ANY REASON; DAMAGE TO THE ENGINE AND PERSONAL INJURY CAN HAPPEN. CONSULT
YOUR LOCAL FAA APPROVED MAINTENANCE FACILITY.
SERVICE BULLETINS, INSTRUCTIONS, AND LETTERS
Although the information contained in this manual is up-to-date at time of publication, users are urged to
keep abreast of later information through Lycoming Service Bulletins, Instructions and Service Letters
which are available from all Lycoming distributors or from the factory by subscription. Consult the latest
revision of Service Letter No. L114 for subscription information.
SPECIAL NOTE
The illustrations, pictures and drawings shown in this publication are typical of the subject matter they
portray; in no instance are they to be interpreted as examples of any specific engine, equipment or part
thereof.
iii

LYCOMING OPERATOR’S MANUAL
TABLE OF CONTENTS
Page
SECTION 1 DESCRIPTION 1-1
SECTION 2 SPECIFICATIONS 2-1
SECTION 3 OPERATING INSTRUCTIONS 3-1
SECTION 4 PERIODIC INSPECTIONS 4-1
SECTION 5 MAINTENANCE PROCEDURES 5-1
SECTION 6 TROUBLE-SHOOTING 6-1
SECTION 7 INSTALLATION AND STORAGE 7-1
SECTION 8 TABLES 8-1

LYCOMING OPERATOR’S MANUAL
SECTION 1
DESCRIPTION
Page
General..........................................................................................................................................................1-1
Cylinders.......................................................................................................................................................1-1
Valve Operating Mechanism ......................................................................................................................1-1
Crankcase ..................................................................................................................................................... 1-1
Crankshaft....................................................................................................................................................1-1
Connecting Rods .......................................................................................................................................... 1-2
Pistons ...........................................................................................................................................................1-2
Accessory Housing.......................................................................................................................................1-2
Oil Sump.......................................................................................................................................................1-2
Cooling System.............................................................................................................................................1-2
Induction System..........................................................................................................................................1-2
Lubrication System......................................................................................................................................1-3
Priming System ............................................................................................................................................1-3
Ignition System.............................................................................................................................................1-3
Counterweight System.................................................................................................................................1-3
Model Application Table.............................................................................................................................1-3

LYCOMING OPERATOR’S MANUAL SECTION 1
O-360 AND ASSOCIATED MODELS DESCRIPTION
SECTION 1
DESCRIPTION
The O. HO, IO, AIO, HIO, LIO and TIO-360 series are four cylinder, direct drive, horizontally opposed,
air-cooled engines.
In referring to the location of the various engine components, the parts are described as installed in the
airframe. Thus, the power take-off end is the front and the accessory drive end the rear. The sump section is
the bottom and the opposite side of the engine where the shroud tubes are located the top. Reference to the
left and right side is made with the observer facing the rear of the engine. The cylinders are numbered from
front to rear, odd numbers on the right. The direction of rotation of the crankshaft, viewed from the rear, is
clockwise. Rotation for accessory drives is determined with the observer facing the drive pad.
NOTE
The letter “L” in the model prefix denotes the reverse rotation of the basic model. Example:
model IO-360-C has clockwise rotation of the crankshaft. Therefore, LIO-360-C has
counterclockwise rotation of the crankshaft. Likewise, the rotation of the accessory drives of
the LIO-360-C is opposite those of the basic model as listed in Section 2 of this manual.
The letter “D” used as the 4th or 5th character in the model suffix denotes that the particular
model employs dual magnetos housed in a single housing. Example: All information
pertinent to the O-360-A1F6 will apply to the O-360-A1F6D.
Operational aspects of engines are the same and performance curves and specifications for
the basic model will apply.
Cylinders – The cylinders are of conventional air-cooled construction with the two major parts, head and
barrel, screwed and shrunk together. The heads are made from an aluminum alloy casting with a fully
machined combustion chamber. Rocker shaft bearing supports are cast integral with the head along with
housings to form the rocker boxes. The cylinder barrels have deep integral cooling fins and the inside of the
barrels are ground and honed to a specified finish.
Valve Operating Mechanism – A conventional type camshaft is located above and parallel to the crankshaft.
The camshaft actuates hydraulic tappets, which operate the valves through push rods and valve rockers. The
valve rockers are supported on full floating steel shafts. The valve springs bear against hardened steel seats
and are retained on the valve stems by means of split keys.
Crankcase – The crankcase assembly consists of two reinforced aluminum alloy castings, fastened together
by means of studs, bolts and nuts. The mating surfaces of the two castings are joined without the use of a
gasket, and the main bearing bores are machined for use of precision type main bearing inserts.
Crankshaft – The crankshaft is made from a chrome nickel molybdenum steel forging. All bearing journal
surfaces are nitrided.
1-1

SECTION 1 LYCOMING OPERATOR’S MANUAL
DESCRIPTION O-360 AND ASSOCIATED MODELS
Connecting Rods – The connecting rods are made in the form of H sections from alloy steel forgings.
They have replaceable bearing inserts in the crankshaft ends and bronze bushings in the piston ends. Two
bolts and nuts through each cap retain the bearing caps on the crankshaft ends.
Pistons – The pistons are machined from an aluminum alloy. The piston pin is of a full floating type with a
plug located in each end of the pin. Depending on the cylinder assembly, pistons may be machined for either
three or four rings and may employ either half wedge or full wedge rings. Consult the latest revision of
Service Instruction No. 1037 for proper piston and ring combinations.
Accessory Housing – The accessory housing is made from an aluminum casting and is fastened to the rear of
the crankcase and the top rear of the sump. If forms a housing for the oil pump and the various accessory
drives.
Oil Sump (Except AIO Series) – The sump incorporates an oil drain plug, oil suction screen, mounting pad
for carburetor or fuel injector, the intake riser and intake pipe connections.
Crankcase Covers (AIO Series) – Crankcase covers are employed on the top and bottom of the engine.
These covers incorporate oil suction screens, oil scavenge line connections. The top cover incorporates a
connection for a breather line and the lower cover a connection for an oil suction line.
Cooling System – These engines are designed to be cooled by air pressure. Baffles are provided to build up a
pressure and force the air through the cylinder fins. The air is then exhausted to the atmosphere through gills
or augmentor tubes usually located at the rear of the cowling.
Induction System – Lycoming O-360 and HO-360 series engines are equipped with either a float type or
pressure type carburetor. See Table 1 for model application. Particularly good distribution of the fuel-air
mixture to each cylinder is obtained through the center zone induction system, which is integral with the oil
sump and is submerged in oil, insuring a more uniform vaporization of fuel and aiding in cooling the oil in
the sump. From the riser the fuel-air mixture is distributed to each cylinder by individual intake pipes.
Lycoming IO-360, AIO-360, HIO-360 and TIO-360 series engines are equipped with a Bendix type RSA
fuel injector, with the exception of model IO-360-B1A that is equipped with a Simmonds type 530 fuel
injector. (See Table 1 of model application.) The fuel injection system schedules fuel flow in proportion to
air flow and fuel vaporization takes place at the intake ports. A turbocharger is mounted as an integral part
of the TIO-360 series engines. Automatic waste gate control of the turbocharger provides constant air
density to the fuel injector inlet from sea level to critical altitude.
A brief description of the carburetors and fuel injectors follows:
The Marvel-Schebler MA-4-5 and HA-6 carburetors are of the single barrel float type equipped with a
manual mixture control and an idle cut-off.
The Marvel-Schebler MA-4-5AA carburetor is of the single barrel float type with automatic pressure
altitude mixture control. This carburetor is equipped with idle cut-off but does not have a manual mixture
control.
The Bendix-Stromberg PSH-5BD is a pressure operated, single barrel horizontal carburetor, incorporating
an airflow operated power enrichment valve and an automatic mixture control unit. It is equipped with an
idle cut-off and a manual mixture control. The AMC unit works independently of, and in parallel with, the
manual mixture control.
1-2

LYCOMING OPERATOR’S MANUAL SECTION 1
O-360 AND ASSOCIATED MODELS DESCRIPTION
The Bendix RSA type fuel injection system is based on the principle of measuring air flow and using the
air flow signal in a stem type regulator to convert the air force into a fuel force. This fuel force (fuel
pressure differential) when applied across the fuel metering section (jetting system) makes fuel flow
proportional to airflow.
The Simmonds type 530 is a continuous flow fuel injection system. This continuous flow system has three
separate components:
1. A fuel pump assembly.
2. A throttle body assembly.
3. Four fuel flow nozzles.
This system is throttle actuated. Fuel is injected into the engine intake valve ports by the nozzles. The
system continuously delivers metered fuel to each intake valve port in response to throttle position, engine
speed and mixture control position. Complete flexibility of operation is provided by the manual mixture
control, which permits the adjustment of the amount of injected fuel to suit all operating conditions. Moving
the mixture control to Idle Cut-Off results in a complete cut-off of fuel to the engine.
Lubrication System – (All models except AIO-360 series). An impeller type pump contained within the
accessory housing actuates the full pressure wet sump lubrication system.
AIO-360 Series – The AIO-360 series is designed for aerobatic flying and is of the dry sump type. A double
scavenge pump is installed on the accessory housing.
Priming System – Provision for a primer system is provided on all engines employing a carburetor. Fuel
injected engines do not require a priming system.
Ignition System – Dual ignition is furnished by two Bendix magnetos. Consult Table 1 for model
application.
Counterweight System – Models designated by the numeral 6 in the suffix of the model number (Example:
O-360-A1G6) are equipped with crankshafts with pendulum type counterweights attached.
TABLE 1
MODEL APPLICATION
Model Left** Right** Carburetor
O-360
-A1A, -A2A, -A3A, -A4A
-A1C, -C2D
-A1D, -A2D, -A3D, -A4D, -A2E
-A1F, -A2F, -A1F6
-A1G, -A2G, -A4G, -A1G6
-A1H, -A2H, -A4J
-A1H6
-A1P, -A4P, -B2C, -C4P
-A4K, -C1F, -C4F
-A4M
S4LN-21
S4LN-200
S4LN-200
S4LN-1227
S4LN-1227
S4LN-21
4273
4373
4371
4371
S4LN-20
S4LN-204
S4LN-204
S4LN-1209
S4LN-1209
S4LN-204
4270
4370
4370
4370
MA-4-5
PSH-5BD
MA-4-5
MA-4-5
HA-6
HA-6
HA-6
MA-4-5
HA-6
MA-4-5
* - Models with counterclockwise rotation employ S4RN series.
** - See latest revision of Service Instruction No. 1443 for alternate magnetos.
1-3

LYCOMING OPERATORS MANUAL SECTION 1
O-360 AND ASSOCIATED MODELS DESCRIPTION
TABLE 1 (CONT.)
MODEL APPLICATION
Model Left** Right** Fuel Injector
IO-360 (Cont.)
-B1A
-B1D, -C1A
-B1F, -B2F, -B2F6
-B4A, -K2A
-C1C, -C1C6, -C1D6
-C1E6, -C1F, -F1A
-D1A, -E1A
-A1D
-L2A
, -M1B, -B1G6
-C1G6
S4LN-200
S4LN-200
S4LN-1227
S4LN-21
S4LN-1227
S4LN-1227
S4LN-1208
S4LN-21
4371
4371
4345
S4LN-204
S4LN-204
S4LN-1227
S4LN-20
S4LN-1209
S4LN-1209
S4LN-1209
S4LN-204
4371
4370
4345
530
RSA-5AD1
RSA-5AD1
RSA-5AD1
RSA-5AD1
RSA-5AD1
RSA-5AD1
RSA-5AD1
RSA-5AD1
RSA-5AD1
RSA-5AD1
IO-360 Dual Magneto
-A1B6D, -A3B6D, -J1AD, -J1A6D
-A1D6D, -A3D6D
D4LN-3021
D4LN-3000
RSA-5AD1
RSA-5AD1
AIO-360
-A1A, -A2A
-A1B, -A2B, -B1B
S4LN-1208
S4LN-1227
S4LN-1209
S4LN-1209
RSA-5AD1
RSA-5AD1
TIO-360
-A1A, -A1B, -A3B6 S4LN-1208 S4LN-1209 RSA-5AD1
TIO-360 Dual Magneto
-C1A6D D4LN-3021 RSA-5AD1
* - Models with counterclockwise rotation employ S4RN series.
** - See latest revision of Service Instruction No. 1443 for alternate magnetos.
- For information pertaining to engine model (L)IO-360-M1A, refer to Operation and Installation
Manual P/N 60297-36
Engine models with letter D as 4th or 5th character in suffix denotes dual magnetos in single housing.
Basic models employing 21 or 1227 (impulse coupling magnetos) use D4LN or D4RN-3021. Basic
models employing 200 and 1208 (retard breaker magnetos) use D4LN or D4RN-3000. Example Basic
model IO-360-C1C uses S4LN-1227 and S4LN-1209, therefore model IO-360-C1CD would employ
D4LN-3021.
Revised March 2009 1-5

LYCOMING OPERATORS MANUAL
SECTION 2
SPECIFICATIONS
Page
Specifications
O-360-A, -C, -F.......................................................................................................................................... 2-1
O-360-B, -D................................................................................................................................................ 2-1
O-360-J2A.................................................................................................................................................. 2-1
HO-360-A, -C............................................................................................................................................. 2-2
HO-360-B ................................................................................................................................................... 2-2
IO-360-L2A................................................................................................................................................ 2-2
IO-360-B1G6, , -M1B.............................................................................................................................. 2-3
IO-360-A, -C, -D, -J, -K ............................................................................................................................ 2-3
IO-360-B, -E, -F......................................................................................................................................... 2-4
AIO-360-A, -B ........................................................................................................................................... 2-4
HIO-360-A, -B ........................................................................................................................................... 2-4
HIO-360-C ................................................................................................................................................. 2-5
HIO-360-D ................................................................................................................................................. 2-5
HIO-360-E ................................................................................................................................................. 2-5
HIO-360-F1AD.......................................................................................................................................... 2-6
HIO-360-G1A ............................................................................................................................................ 2-6
TIO-360-A.................................................................................................................................................. 2-6
TIO-360-C.................................................................................................................................................. 2-7
Accessory Drives .......................................................................................................................................... 2-7
Detail Weights .............................................................................................................................................. 2-7
Dimensions.................................................................................................................................................... 2-9
- For information pertaining to engine model (L)IO-360-M1A, refer to Operation and Installation
Manual P/N 60297-36.
Revised March 2009

LYCOMING OPERATORS MANUAL SECTION 2
O-360 AND ASSOCIATED MODELS SPECIFICATIONS
SPECIFICATIONS (CONT.)
IO-360-B1G6, . -M1B*
FAA Type Certificate ................................................................................................................................. 1E10
Rated horsepower...........................................................................................................................................180
Rated speed, RPM........................................................................................................................................2700
Bore, inches.................................................................................................................................................5.125
Stroke, inches..............................................................................................................................................4.375
Displacement, cubic inches.........................................................................................................................361.0
Compression ratio ....................................................................................................................................... 8.5:1
Firing order ............................................................................................................................................. 1-3-2-4
Spark occurs, degrees BTC..............................................................................................................................25
Valve rocker clearance (hydraulic tappets collapsed) ......................................................................... .028-.080
Propeller drive ratio ....................................................................................................................................... 1:1
Propeller driven rotation (viewed from rear) ......................................................................................Clockwise
- For information pertaining to engine model (L)IO-360-M1A, refer to Operation and Installation Manual
P/N 60297-36.
* - This engine has an alternate rating of 160 HP at 2400 RPM.
IO-360-A, -C, -D, -J, -K Series
FAA Type Certificate ................................................................................................................................. 1E10
Rated horsepower...........................................................................................................................................200
Rated speed, RPM........................................................................................................................................2700
Bore, inches.................................................................................................................................................5.125
Stroke, inches..............................................................................................................................................4.375
Displacement, cubic inches.........................................................................................................................361.0
Compression ratio ....................................................................................................................................... 8.7:1
Firing order ............................................................................................................................................. 1-3-2-4
Spark occurs, degrees BTC..........................................................................................................................25**
Valve rocker clearance (hydraulic tappets collapsed) ......................................................................... .028-.080
Propeller drive ratio ....................................................................................................................................... 1:1
Propeller driven rotation (viewed from rear) ......................................................................................Clockwise
NOTE**
On the following model engines, the magneto spark occurs at 20° BTC. Consult nameplate
before timing magnetos.
Models Serial No.
IO-360-A Series (Except -A1B6D) L-14436-51 and up
IO-360-C, -D Series (Except -C1C, -C1F, -C1C6, -C1D6) L-14436-51 and up
IO-360-C1C, -C1F L-13150-51 and up
IO-360-C1D6 L-14446-51 and up
LIO-360-C1E6 L-1064-67 and up
AIO-360-A1A, -A1B, -B1B L-220-63 and up
HIO-360-C1A, -C1B L-14436-51 and up
IO-360-C1C6 All Engines
IO-360-C1G6 All Engines
IO-360-J1AD, -K2A All Engines
Revised March 2009 2-3

LYCOMING OPERATOR’S MANUAL SECTION 2
O-360 AND ASSOCIATED MODELS SPECIFICATIONS
TIO-360-C Series
FAA Type Certificate ..............................................................................................................................E16EA
Rated horsepower...........................................................................................................................................210
Rated speed, RPM........................................................................................................................................2575
Bore, inches.................................................................................................................................................5.125
Stroke, inches..............................................................................................................................................4.375
Displacement, cubic inches.........................................................................................................................361.0
Compression ratio ....................................................................................................................................... 7.3:1
Firing order ............................................................................................................................................. 1-3-2-4
Spark occurs, degrees BTC..............................................................................................................................20
Valve rocker clearance (hydraulic tappets collapsed) ......................................................................... .028-.080
Propeller drive ratio ....................................................................................................................................... 1:1
Propeller driven rotation (viewed from rear) ......................................................................................Clockwise
*Accessory Drive Drive Ratio **Direction of Rotation
Starter 16.556:1 Counterclockwise
Generator 1.910:1 Clockwise
Generator 2.500:1 Clockwise
Alternator*** 3.20:1 Clockwise
Tachometer 0.500:1 Clockwise
Magneto 1.000:1 Clockwise
Vacuum Pump 1.300:1 Counterclockwise
Propeller Governor (Rear Mounted) 0.866:1 Clockwise
Propeller Governor (Front Mounted) 0.895:1 Clockwise
Fuel Pump AN20010 0.866:1 Counterclockwise
Fuel Pump AN20003 1.000:1 Counterclockwise
Fuel Pump Plunger Operated Dual Drives 0.500:1
Vacuum Hydraulic Pump 1.300:1 Counterclockwise
Vacuum Prop. Governor 1.300:1 Counterclockwise
* - When applicable.
** - Viewed facing drive pad.
*** - HIO-360-D1A Alternator drive is 2.50:1.
- TIO-360-C1A6D, HIO-360-E, -F have clockwise fuel pump drive.
NOTE
Engines with letter “L” in prefix will have opposite rotation to the above.
DETAIL WEIGHTS
1. ENGINE, STANDARD, DRY WEIGHT.
Includes carburetor or fuel injector, magnetos, spark plugs, ignition harness, intercylinder baffles,
tachometer drive, starter and generator or alternator drive, starter and generator or alternator with mounting
bracket. Turbocharged models include turbocharger, mounting bracket, exhaust manifold, controls, oil lines
and baffles.
2-7

LYCOMING OPERATOR’S MANUAL SECTION 2
O-360 AND ASSOCIATED MODELS SPECIFICATIONS
DETAIL WEIGHTS (CONT.)
Model Lbs.
IO-360 Series (Cont.)
-A1A, -A2A, -C1F, -C1G6 ....................................................................................................324
-A1C, -A2A, -A1D ................................................................................................................325
-A1B, -A2B............................................................................................................................326
-C1D6.....................................................................................................................................328
-C1C6.....................................................................................................................................329
-A1B6D, -A3B6D, -J1A6D ...................................................................................................330
-A1B6, -A3B6........................................................................................................................333
-A1D6 ....................................................................................................................................335
-C1E6 .....................................................................................................................................337
AIO-360 Series
-A1A, -A2A ...........................................................................................................................331
-A1B, -A2B, -B1B .................................................................................................................332
HIO-360 Series
-G1A ......................................................................................................................................283
-B1A, -B1B ............................................................................................................................290
-A1A ......................................................................................................................................311
-A1B.......................................................................................................................................312
-D1A, -E1AD, -E1BD............................................................................................................321
-C1A.......................................................................................................................................322
-C1B.......................................................................................................................................323
-F1AD ....................................................................................................................................324
TIO-360 Series
-C1A6D..................................................................................................................................379
-A1A, -A1B............................................................................................................................386
-A3B6.....................................................................................................................................407
DIMENSIONS, INCHES
MODEL HEIGHT WIDTH LENGTH
O-360 Series
-A1A, -A1P, -A2A
-A1C
-A1D, -A2D
-A1F, -A2F
-A1F6
-A1G, -A2G
-A1H, -A2H
24.59
19.68
24.59
24.59
24.59
19.22
19.22
33.37
33.37
33.37
33.37
33.37
33.37
33.37
29.56
30.67
29.81
30.70
30.70
31.82
31.82
2-9

SECTION 2 LYCOMING OPERATOR’S MANUAL
SPECIFICATIONS O-360 AND ASSOCIATED MODELS
DIMENSIONS, INCHES (CONT.)
MODEL HEIGHT WIDTH LENGTH
O-360 Series (Cont.)
-A1H6
-A3A, -A4A, -A4M, -A4P
-A3D, -A4D, -A2E
-A4G, -A4J, -A4K
-A1G6, -A1G6D, -C1F, -C4F
-A4N
-A1AD, -A3AD, -A5AD
-A1A5D, -A1F6D, -A1LD
-B1A, -B2A, -B2C
-B1B, -B2B
-C1A, -C2A
-C1C, -C2C, -C4P
-C1E, -C2E
-C2B, -C2D
-C1G, -D1A, -D2A
-D2B
-J2A
-F1A6
-G1A6
19.33
24.59
24.59
19.22
19.22
24.59
24.59
24.59
24.68
24.68
24.72
24.59
24.59
19.68
24.59
24.59
22.99
19.96
19.96
33.38
33.37
33.37
33.37
33.37
33.37
33.37
33.37
33.37
33.37
33.37
33.37
33.37
33.37
33.37
33.37
32.24
33.38
33.37
31.81
29.56
29.81
31.82
31.82
29.05
31.33
31.33
29.56
29.81
29.56
29.81
29.05
30.67
29.56
29.81
29.81
31.81
31.83
HO-360 Series
-A1A
-B1A, -B1B
-C1A
24.59
19.68
19.22
33.37
33.37
33.37
29.81
30.67
31.82
IO-360 Series
-A1A, -A2A, -A1D
-A1B, -A2B
-A1B6, -A3B6
-A1C, -A2C
-A1D6
-A1B6D, -A3B6D, -J1AD
-A1D6D, -A3D6D
-B1A
-B1B, -B1D, -L2A
-B1C
-B1E
-B1F, -B2F, -B2F6
-B4A
-C1A, -C1B
-C1C, -C1C6
-C1E6, -C1F
19.35
19.35
19.35
19.35
19.35
19.35
19.35
22.47
24.84
20.70
20.70
24.84
24.84
19.48
19.48
19.48
34.25
34.25
34.25
34.25
34.25
34.25
34.25
33.37
33.37
33.37
33.37
33.37
33.37
34.25
34.25
34.25
29.81
30.70
30.70
29.30
30.70
31.33
31.33
32.81
29.81
30.68
32.09
30.70
29.56
31.14
33.65
33.65
2-10

LYCOMING OPERATOR’S MANUAL
SECTION 3
OPERATING INSTRUCTIONS
Page
General..........................................................................................................................................................3-1
Prestarting Items of Maintenance..............................................................................................................3-1
Starting Procedures.....................................................................................................................................3-1
Cold Weather Starting ................................................................................................................................3-3
Ground Running and Warm-Up................................................................................................................3-3
Ground Check..............................................................................................................................................3-4
Operation in Flight ......................................................................................................................................3-5
Engine Flight Chart...................................................................................................................................3-10
Operating Conditions ................................................................................................................................ 3-11
Shut Down Procedure................................................................................................................................3-16
Performance Curves..................................................................................................................................3-17

LYCOMING OPERATOR’S MANUAL SECTION 3
O-360 AND ASSOCIATED MODELS OPERATING INSTRUCTIONS
SECTION 3
OPERATING INSTRUCTIONS
1. GENERAL. Close adherence to these instructions will greatly contribute to long life, economy and
satisfactory operation of the engine.
NOTE
YOUR ATTENTION IS DIRECTED TO THE WARRANTIES THAT APPEAR IN THE
FRONT OF THIS MANUAL REGARDING ENGINE SPEED, THE USE OF SPECIFIED
FUELS AND LUBRICANTS, REPAIR AND ALTERATIONS. PERHAPS NO OTHER ITEM
OF ENGINE OPERATION AND MAINTENANCE CONTRIBUTES QUITE SO MUCH TO
SATISFACTORY PERFORMANCE AND LONG LIFE AS THE CONSTANT USE OF
CORRECT GRADES OF FUEL AND OIL, CORRECT ENGINE TIMING, AND FLYING
THE AIRCRAFT AT ALL TIMES WITHIN THE SPEED AND POWER RANGE SPECIFIED
FOR THE ENGINE. DO NOT FORGET THAT VIOLATION OF THE OPERATION AND
MAINTENANCE SPECIFICATIONS FOR YOUR ENGINE WILL NOT ONLY VOID YOUR
WARRANTY BUT WILL SHORTEN THE LIFE OF YOUR ENGINE AFTER ITS WARRANTY
PERIOD HAS PASSED.
New engines have been carefully run-in by Lycoming and therefore, no further break-in is necessary
insofar as operation is concerned; however, new or newly overhauled engines should be operated on straight
mineral oil for a minimum of 50 hours or until oil consumption has stabilized. After this period, a change to
an approved additive oil may be made, if so desired.
NOTE
Cruising should be done at 65% to 75% power until a total of 50 hours has accumulated or
oil consumption has stabilized. This is to ensure proper seating of the rings and is applicable
to new engines, and engines in service following cylinder replacement or top overhaul of one
or more cylinders.
The minimum fuel octane rating is listed in the flight chart, Part 8 of this section. Under no circumstances
should fuel of a lower octane rating or automotive fuel (regardless of octane rating) be used.
2. PRESTARTING ITEMS OF MAINTENANCE. Before starting the aircraft engine for the first flight of the
day, there are several items of maintenance inspection that should be performed. These are described in
Section 4 under Daily Pre-Flight Inspection. They must be observed before the engine is started.
3. STARTING PROCEDURES. O-360, HO-360, IO-360, AIO-360, HIO-360, TIO-360 Series.
The following starting procedures are recommended, however, the starting characteristics of various
installations will necessitate some variation from these procedures.
a. Engines Equipped with Float Type Carburetors.
(1) Perform pre-flight inspection.
3-1

SECTION 3 LYCOMING OPERATOR’S MANUAL
OPERATING INSTRUCTIONS O-360 AND ASSOCIATED MODELS
(2) Set carburetor heat control in off position.
(3) Set propeller governor control in Full RPM position (where applicable).
(4) Turn fuel valves On.
(5) Move mixture control to Full Rich.
(6) Turn on boost pump.
(7) Open throttle approximately ¼ travel.
(8) Prime with 1 to 3 strokes of manual priming pump or activate electric primer for 1 or 2 seconds.
(9) Set magneto selector switch (consult airframe manufacturers handbook for correct position).
(10) Engage starter.
(11) When engine fires, move the magneto switch to Both.
(12) Check oil pressure gage. If minimum oil pressure is not indicated within thirty seconds, stop
engine and determine trouble.
b. Engines Equipped with Pressure Carburetors or Bendix Fuel Injectors.
(1) Perform pre-flight inspection.
(2) Set carburetor heat or alternate air control in Off position.
(3) Set propeller governor control in Full RPM position (where applicable).
(4) Turn fuel valve On.
(5) Turn boost pump On.
(6) Open throttle wide open, move mixture control to Full Rich until a slight but steady fuel flow is
noted (approximately 3 to 5 seconds) then return throttle to Closed and return mixture control to
Idle Cut-Off.
(7) Turn boost pump Off.
(8) Open throttle ¼ of travel.
(9) Set magneto selector switch (consult airframe manufacturers handbook for correct position).
(10) Engage starter.
3-2

LYCOMING OPERATOR’S MANUAL SECTION 3
O-360 AND ASSOCIATED MODELS OPERATING INSTRUCTIONS
(11) Move mixture control slowly and smoothly to Full Rich.
(12) Check oil pressure gage. If minimum oil pressure is not indicated within thirty seconds, stop
engine and determine trouble.
c. Engines Equipped with Simmonds Type 530 Fuel Injector.
(1) Perform pre-flight inspection.
(2) Set alternate air control in Off position.
(3) Set propeller governor control in Full RPM position.
(4) Turn fuel valve On.
(5) Turn boost pump On.
(6) Open throttle approximately ¼ travel, move mixture control to Full Rich until a slight but
steady fuel flow is noted (approximately 3 to 5 seconds) then return throttle to Closed and
return mixture control to Idle Cut-Off.
(7) Turn boost pump Off.
(8) Open throttle ¼ travel.
(9) Move combination magneto switch to Start, using accelerator pump as a primer while cranking
engine.
(10) When engine fires allow the switch to return to Both.
(11) Check oil pressure gage. If minimum oil pressure is not indicated within thirty seconds, stop
engine and determine trouble.
4. COLD WEATHER STARTING. During extreme cold weather, it may be necessary to preheat the engine
and oil before starting.
5. GROUND RUNNING AND WARM-UP.
The engines covered in this manual are air-pressure cooled and depend on the forward speed of the aircraft
to maintain proper cooling. Particular care is necessary, therefore, when operating these engines on the
ground. To prevent overheating, it is recommended that the following precautions be observed.
NOTE
Any ground check that requires full throttle operation must be limited to three minutes, or
less if the cylinder head temperature should exceed the maximum as stated in this manual.
3-3

SECTION 3 LYCOMING OPERATOR’S MANUAL
OPERATING INSTRUCTIONS O-360 AND ASSOCIATED MODELS
a. Fixed Wing.
(1) Head the aircraft into the wind.
(2) Leave mixture in “Full Rich”.
(3) Operate only with the propeller in minimum blade angle setting.
(4) Warm-up to approximately 1000-1200 RPM. Avoid prolonged idling and do not exceed 2200
RPM on the ground.
(5) Engine is warm enough for take-off when the throttle can be opened without the engine faltering.
Take-off with a turbocharged engine must not be started if indicated lubricating oil pressure, due
to cold temperature is above maximum. Excessive oil pressure can cause overboost and
consequent engine damage.
b. Helicopter.
(1) Warm-up at approximately 2000 RPM with rotor engaged as directed in the airframe
manufacturer’s handbook.
6. GROUND CHECK.
a. Warm-up as directed above.
b. Check both oil pressure and oil temperature.
c. Leave mixture control in “Full Rich”.
d. Fixed Wing Aircraft (where applicable). Move the propeller control through its complete range to
check operation and return to full low pitch position. Full feathering check (twin engine) on the
ground is not recommended but the feathering action can be checked by running the engine between
1000-1500 RPM, then momentarily pulling the propeller control into the feathering position. Do not
allow the RPM to drop more than 500 RPM.
e. A proper magneto check is important. Additional factors, other than the ignition system, affect
magneto drop-off. They are load-power output, propeller pitch, and mixture strength. The important
point is that the engine runs smoothly because magneto drop-off is affected by the variables listed
above. Make the magneto check in accordance with the following procedures.
(1) Fixed Wing Aircraft.
(a) (Controllable pitch propeller). With the propeller in minimum pitch angle, set the engine to
produce 50-65% power as indicated by the manifold pressure gage unless otherwise specified
in the aircraft manufacturer’s manual. At these settings, the ignition system and spark plugs
must work harder because of the greater pressure within the cylinders. Under these conditions,
ignition problems can occur. Magneto checks at low power settings will only indicate fuel/air
distribution quality.
3-4 Revised December 2007
Table of contents
Other Textron Engine manuals
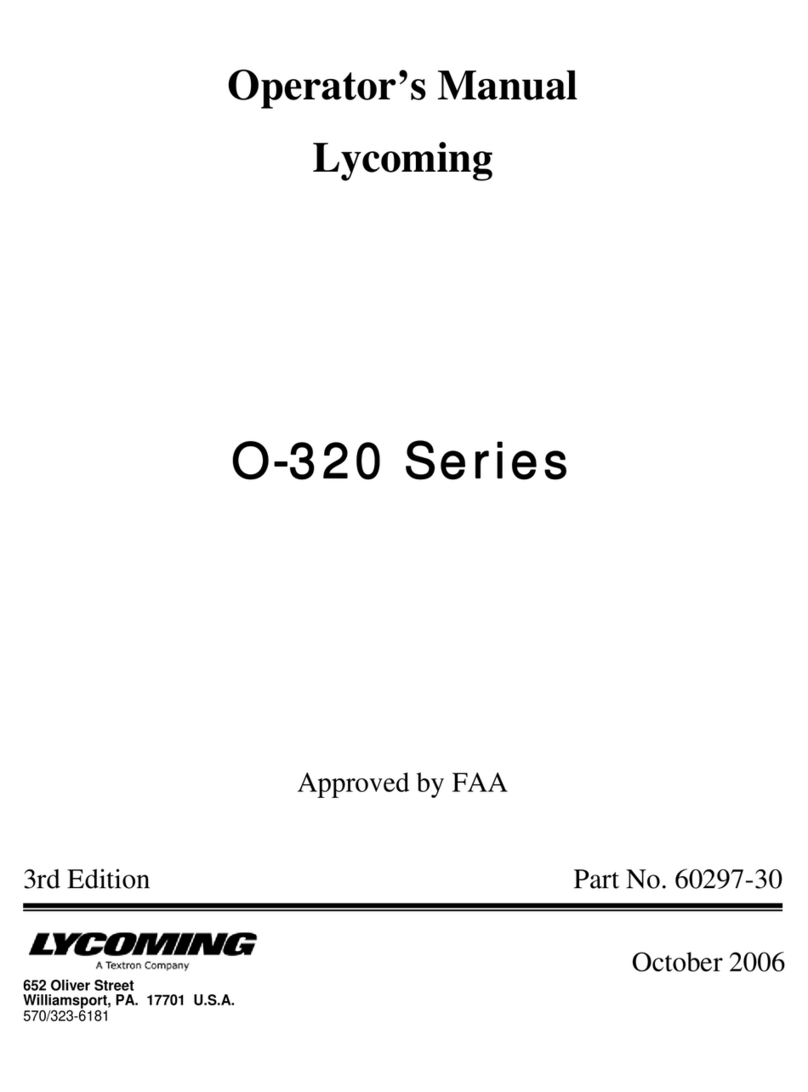
Textron
Textron LYCOMING O-320 Series User manual
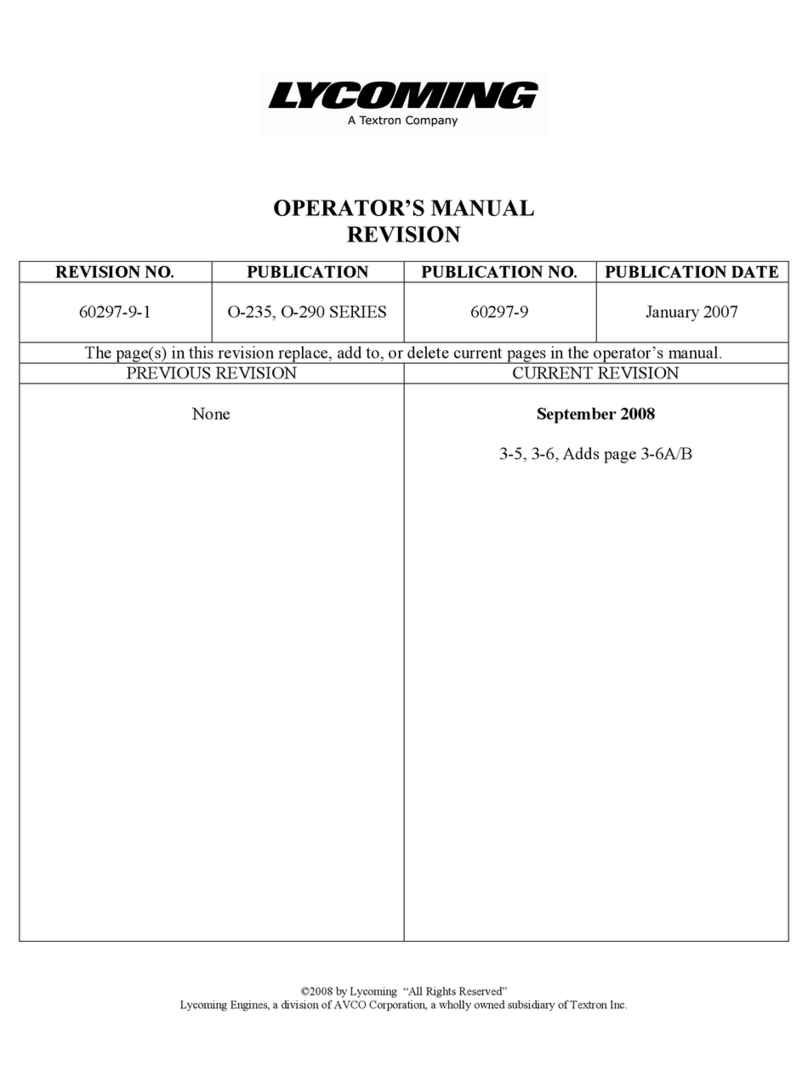
Textron
Textron Lycoming O-235-C User manual
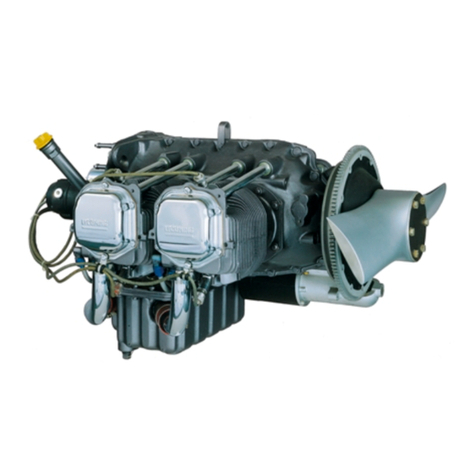
Textron
Textron Lycoming O-235 Series User manual

Textron
Textron MPE 850 OFF-ROAD Operating instructions
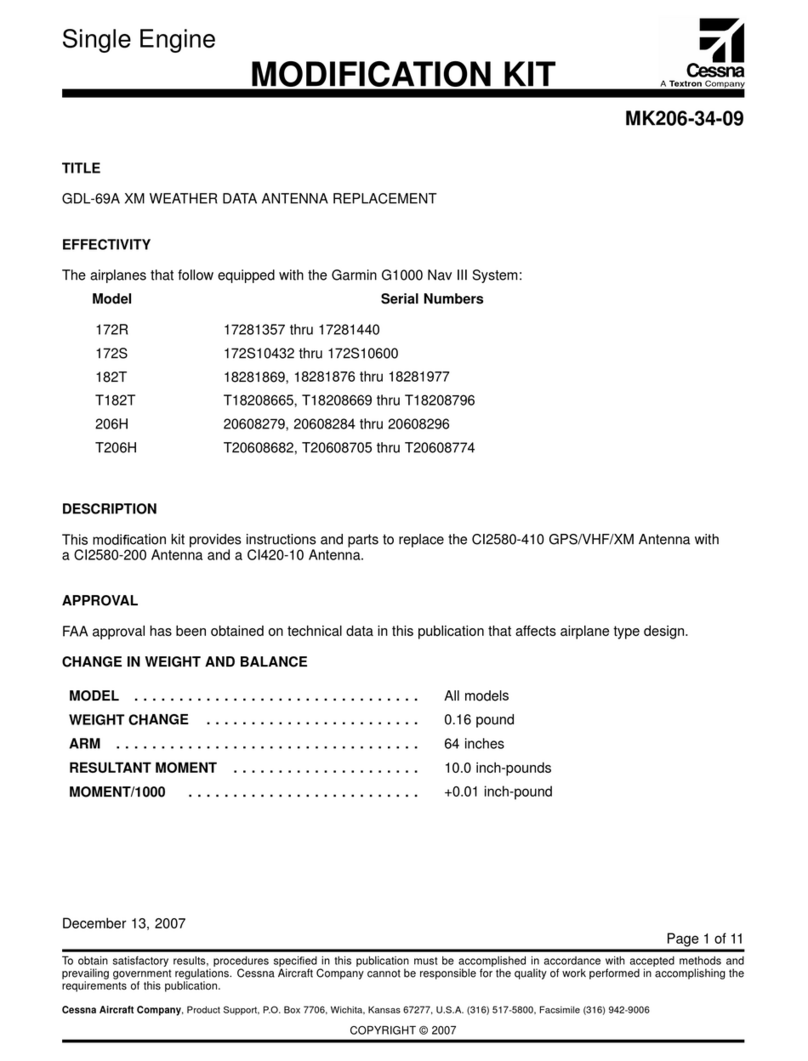
Textron
Textron Cessna MK206-34-09 User manual
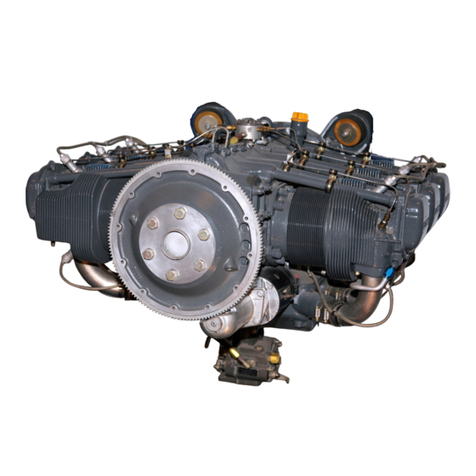
Textron
Textron Lycoming IO-540 Series User manual
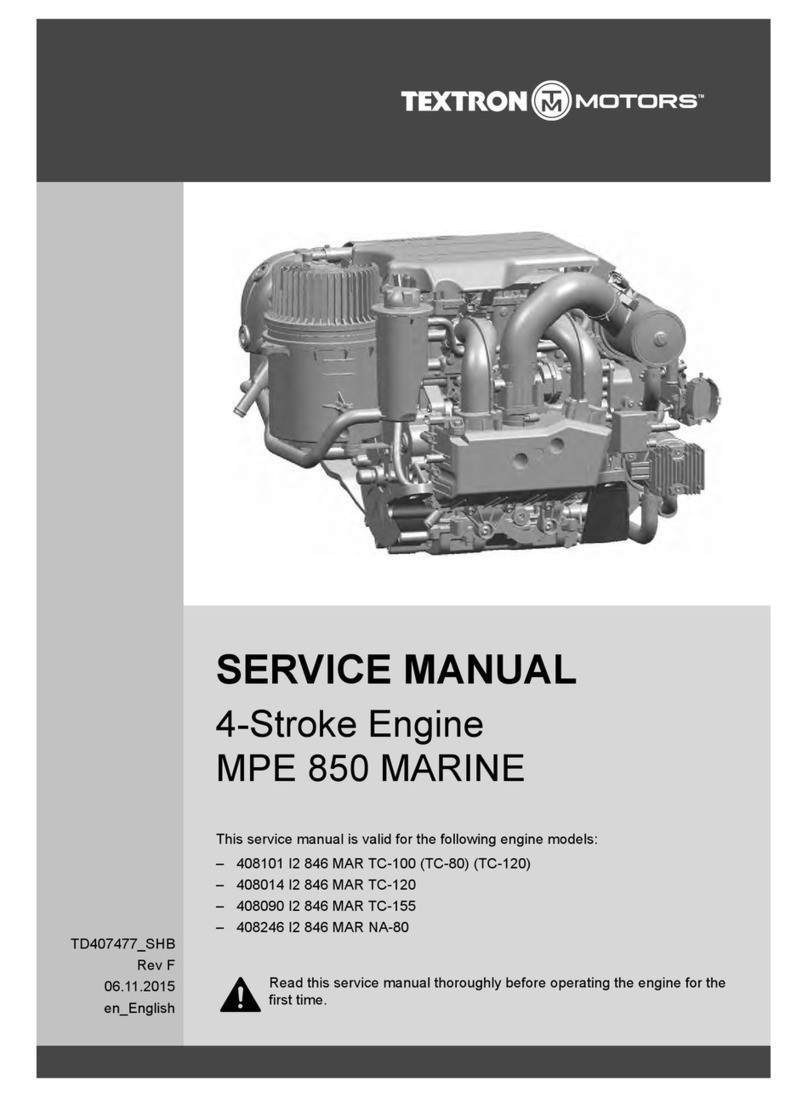
Textron
Textron MPE 850 MARINE User manual
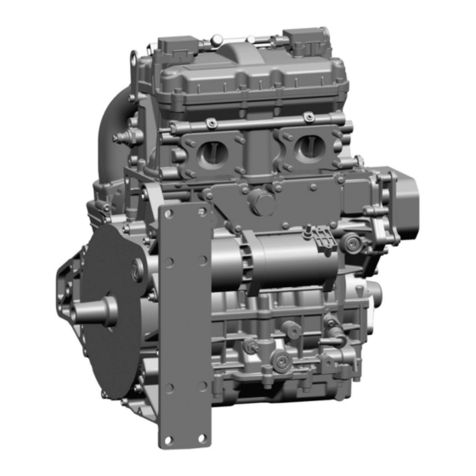
Textron
Textron MPE 850 OFF-ROAD User manual