Saito FG-57T User manual

INSTRUCTION MANUAL
Twin-Cylinder Gasoline Four-Stroke Engine
FG-57T

WARNING: Read the ENTIRE instruction manual to become familiar
with the features of the product before operating. Failure to operate the
product correctly can result in damage to the product, personal property and
cause serious injury.
This is a sophisticated hobby product. It must be operated with caution
and common sense and requires some basic mechanical ability. Failure to
operate this Product in a safe and responsible manner could result in injury
or damage to the product or other property. This product is not intended for
use by children without direct adult supervision. Do not attempt disassembly,
use with incompatible components or augment product in any way without
the approval of Horizon Hobby, Inc. This manual contains instructions for
safety, operation and maintenance. It is essential to read and follow all the
instructions and warnings in the manual, prior to assembly, setup or use, in
order to operate correctly and avoid damage or serious injury.
NOTICE
All instructions, warranties and other collateral documents are subject to
change at the sole discretion of Horizon Hobby, Inc. For up-to-date product
literature, visit www.horizonhobby.com and click on the support tab for this
product.
Meaning of Special Language:
The following terms are used throughout the product literature to indicate
various levels of potential harm when operating this product:
NOTICE: Procedures, which if not properly followed, create a possibility of
physical property damage AND little or no possibility of injury.
CAUTION: Procedures, which if not properly followed, create the
probability of physical property damage AND a possibility of serious injury.
WARNING: Procedures, which if not properly followed, create the
probability of property damage, collateral damage, serious injury or death
OR create a high probability of superficial injury.

Introduction
Congratulations on purchasing a
Saito™4-cycle gasoline engine. When
cared for properly, these high-quality,
finely crafted engines offer many years
of modeling enjoyment.
This instruction manual has been
developed to ensure optimum
performance from the Saito gasoline
engine you have purchased. Saito
gasoline engines are adapted from
similarly sized glow fuel engines and
are designed with an emphasis towards
high performance, durability and
weight savings. Where appropriate
the engines have been modified
to adapt to gasoline fuel usage by
equipping it with a four-stroke gasoline
engine carburetor and an ignition
system matched to your engine. The
instructions must be read through
completely and understood thoroughly
prior to mounting and running the
engine.
Features of a gasoline fueled four-
stroke engine:
- Fuel efficient
- Fuel cost is low compared to glow
fuels
- Your airplane will be cleaner at end
of a flying session
- No separate igniter system is
required
Safety Warnings
WARNING: Model engines
produce a substantial amount of power
which can create unsafe situations
if not used correctly. Always use
common sense and observe all safety
precautions when operating, handling
or performing any procedure involving
your engine. Failure to follow safety
precautions could result in serious
injury and property damage.
•Always ensure spectators, especially
children, are at least 30 feet away
when running the engine
•Always ensure that the propeller
is securely attached to the engine
shaft and all retaining fasteners are
tightened properly before EACH
flight. Use of blue threadlock to
tighten nuts is advisable.
•Always keep small parts out of the
reach of children as they can be
choking hazards
•Always secure the airplane before
powering the engine.
•Always keep your face and body
away from the path of the propeller
blades when starting or running your
engine.
•Always stand behind the propeller
when making carburetor adjustments.
•Always wear safety glasses or
goggles when starting and running
your engine.
•Always keep your fuel in a safe place
well away from sparks, heat or
SAFETY INSTRUCTIONS 1

anything that can ignite.
•Always ensure the aircraft is secure
and will not move once the engine is
started.
•Always rebind your transmitter
to your receiver(s) after setup and
before first flight.
•Always ensure the throttle failsafe is
set to low throttle in your transmitter.
•Always perform a range check prior
to flight.
•Always cut off the fuel supply (pinch
or disconnect the fuel line to the
carburetor) or use the throttle linkage
to shut off the air in order to stop the
engine.
•Never use hands, fingers, or any other
body part to stop the propeller.
•Never throw any object into a
propeller to stop it.
•Never run the engine in the vicinity
of loose small objects, such as gravel
or sand, to avoid the propeller uncon-
trollably throwing such materials.
•Never wear loose clothing or a loose
neckstrap when operating your model
engine as these items could become
entangled in the propeller.
•Never have loose objects such as
screwdrivers, pencils etc. in your
pockets when operating your model
engine. These could fall into the
propeller.
•Never allow fuel to come into contact
with eyes or mouth. Gasoline and
other fuels used in model engines are
poisonous.
•Always ensure gasoline and fuel are
stored in a clearly marked container
well away from the reach of children.
Precautionary Guidelines
•Always mount the engine securely on
a bench mount or high-quality engine
mount.
•Always use the correct size and pitch
of propeller for your engine. Refer to
Propeller Chart in this manual.
•Always confirm proper balance of
your propeller prior to installation
of the engine. Failure to do so could
cause damage to the engine and/or
the airframe.
•Always utilize an electric starter to
start your engine.
•Always discard any propeller that
is nicked, scratched, cracked or
damaged in any way.
•Always run your model engine in a
well-ventilated area. Model engines
produce possibly harmful carbon
monoxide fumes.
•Always store your fuel safely in a
sealed, water-resistant container.
•Always store fuel in a cool,
dry location. Do not allow fuel
containers to come in direct contact
with concrete, as the fuel may absorb
moisture.
•Always responsibly discard fuel if
there is condensation and/or water
inside the fuel container.
•Never return unused fuel from the
fuel tank back into the fuel container.
•Never attempt to repair or modify a
propeller beyond its intended use.
•Never handle model engines,
mufflers and/or tuned pipes until they
have had time to cool. They become
extremely hot when in use.
2 SAFETY INSTRUCTIONS

Disassembly
Do not needlessly disassemble your
Saito engine. Only qualified individ-
uals should perform engine repairs.
Damage due to improper disassembly
will not be covered under warranty.
Engine Parts
Identification
It is important to be able to identify the
parts of your Saito engine. In the
back of this manual you will find an
exploded view of Saito twin-cylinder
gasoline engines, as well as a chart
which includes part numbers and
descriptions. This will assist you in
easily and rapidly identifying the
respective parts of your Saito engine.
Ignition System.
1. Spark Plug Leads (Mesh-covered
high-tension cord) Attach the spark
plug leads to the spark plugs. These
are both identical and can be used
on either side of the engine.
2. Sensor cord (Red, Black and white
cord) This is connected to the cord
from the already attached ignition
sensor unit mounted to the output of
the crankcase. This connector has
a specific orientation, pay attention
when connecting these two cords.
3. Battery cord (Black and red
cord with a universal servo style
female connector). Attach a 6–9
volt battery of at least 1000mAh
capacity. 2S Li-Po batteries are
the recommended power source
because of their light weight and
durability. The ignition amp draw
is approximately 790mAh at full
throttle.
Carburetor
The gas twin engines are equipped
with a suitable carburetor developed in
cooperation with Walbro for exclusive
use in the Saito gasoline engine it is
mounted to. This carburetor has a
negative-pressure type fuel pump so
your tank can be mounted in most any
convenient position relatively close to
the engine. The negative pressure to
actuate the pump is drawn internally
from the intake manifold so no external
tubes or connections are required.
NOTICE
If the fuel remains in carburetor
after the days flying ends, the rubber
components of the carburetor will
tend to degrade rather quickly. When
stopping the engine after the last
flight of the day cut the fuel supply
to the carb and run the engine until
the carburetor is dry. (The parts of
the carburetor made of rubber are
considered consumables and are not
covered under the warranty of the
engine.)
NOTICE
The included gasoline carburetor is
elaborate and delicate. Do not attempt
to disassemble the carburetor yourself.
If the performance of the carburetor
indicates that service is required send it
to our qualified service technicians.
IGNITION SYSTEM 3

Support Equipment
The following items, which are not
included with your Saito engine, are
necessary in order to operate the
model engine:
1. Fuel. For maximum protection
and longevity of its engines, Saito
recommends a fuel containing a
20:1 gasoline to oil ratio. We recom-
mend a synthetic based oil such as
Evolution Oil (EVOX1001Q). High
octane fuel is not needed for this
engine.
2. Propeller and Fuel Consumption:
If you are using a high load (prop
diameter and or pitch is large), the
air-fuel mixture needs to be richer
than with a light load. The main
high-speed needle will need to be
opened even though the rpm's will
be lower than if you were using
a smaller propeller. Conversely
if you are using a low load (prop
diameter and or pitch is small), the
air-fuel mixture needs to be leaner
than with a heavily loaded engine.
The main, high-speed needle will
need to be closed, even though the
rpm's will be higher than if you
were using a larger propeller. For
the longest engine life and best fuel
consumption, the propeller you
choose should provide your best
level flight speed at less than full
throttle.
3. Fuel Filter and Fuel Pump.
Because commercial gasoline has
many impurities be sure to use a
reliable filter when refueling the
onboard tank of the aircraft.
CAUTION: If a quality filter
system is not used impurities and
dirt will be transported to the carb,
clogging internal filter screens and
passages, possibly causing an engine
failure or poor running of your engine.
This could lead to a crash resulting in
injury or property damage.
4. Fuel Tank. Choose a tank with
a capacity of 14–17 ounces (400-
500cc's). This will provide on
average a flight time of 11 to 14
minutes at full throttle. Make sure
you use a gasoline-compatible fuel
tank stopper and gasoline-
compatible fuel line both inside the
tank and for all connections outside
of the tank. (We recommend
SAIG36155 for your internal and
external fuel line) In the fuel line
between the tank and the carburetor,
make sure you use an inline fuel
filter of some type (HAN143
recommended). We also recommend
you use SAIG36154 Filter with
weight as your clunk inside the tank.
5. Spark Plug Wrench. An included
spark plug wrench is used to remove
and tighten spark plugs.
6. Manual or Electric Starter. For
manual starts, a heavy-duty leather
glove is highly recommended.
4 SUPPORT EQUIPMENT

CAUTION: Never use your bare
fingers to start any model engine. This
could lead to injury.
There are a variety of electric starters
on the market. The Hangar 9®
PowerPro™H-D 12V starter (HAN162)
will work perfectly on all of the twin-
cylinder gasoline Saito engines.
Engine Mounting
When mounting the engine please
note that the carburetor of the engine
extends beyond the mounting pads
of the engine mount and this requires
the use of at least 1.0-inch (25mm)
standoffs between the firewall and the
engine mounting pads. Conversely,
you could provide a relief hole in
the firewall for the carburetor to
stick through into the interior of the
fuselage/nacelle.
The engine mounting holes are sized
for M4 screws. If you choose a
different screw, carefully enlarge the
holes in the engine mount to provide
the proper clearance.
Make sure that adequate cooling air
is circulating around the engine! The
cooling air should pass around and
through the cylinder fins and over the
exhaust pipes as insufficient cooling
will cause the engine to run poorly and
cause mechanical failures. Without
cooling air over the exhaust pipes, it is
very likely they will become loose at
the cylinder head. Always ensure that
there is at least a 3:1 (5:1 preferred)
ratio of cool air exhaust outlet area to
inlet area. If you need to add baffles
within your cowl to direct the air over
and through the cylinders, you should
do this before you have an overheating
problem that could possibly damage
your engine.
When attaching the muffler pipes,
screw the pipes into the cylinder heads
as far as possible before tightening
the locking nut to the cylinder head.
This ensures adequate strength in the
threaded joint between the cylinder and
the muffler/exhaust pipe. (The use of
a thread locking compound will help
greatly in this area.)
Included with your engine is a muffler
clamp that is designed to be mounted
to the airframe and provides the
support necessary for the exhaust
pipes. It is important to either use
the supplied exhaust pipe mounts or
devise another method for yourself to
adequately support the exhaust tubes
and prevent tube breakage in flight.
ENGINE MOUNTING 5
Breather
nipple Muffler
clamp

Preparing your engine
The first run on any engine, whether
2-cycle or 4-cycle, is critical to the
future of the engine itself. During this
time, metal mating parts (piston and
cylinder, ball bearings, etc.) settle in.
Care must be taken that the engine is
clean and free of any dust or grit that
may have accumulated while building
the model.
There are two accepted methods for
breaking in a new engine: test stand
mounted and run or aircraft mounted
and run. Either method is acceptable;
however, mounting the engine to a test
stand allows the engine to be observed
throughout its operation, as well as
elevating it above the ground and away
from harmful dust and dirt.
Note: Because your engine may have
been sitting for an extended period of
time prior to running it, a few drops of
light oil applied through the crankcase
breather nipple (19 on the exploded
view) and down the push-rod tubes
(40) will ensure proper lubrication for
the first run.
Regardless of the mounting method
chosen for break-in, the following
procedures are applicable:
1. Use a break-in fuel as described in
the“Support Equipment” (20:1 -
gasoline:oil ratio).
2. Use the proper spark plugs. Your
engine includes the NGK CM-6
spark plugs (SAIG36120).
3. Check whether you can completely
open and close the throttle barrel. If
it cannot be completely closed you
will have a hard time drawing fuel
to the carburetor for a manual start.
4. Check to make sure the ignition
system wiring is connected
correctly.
5. Use a 14 –17 oz (400-500cc) fuel
tank for your test bench. Use the
installed tank if breaking in mounted
to an airframe.
6. Use a 22 x 10 propeller for break-in.
We prefer a carbon propeller such
as a Mejzlik. Since this engine can
easily be started manually, position
the propeller with the blades at
about 1:30 and 7:30 position (when
viewed from the front) as the engine
comes up against compression. This
will be a good position to allow a
quick and strong flip of the prop
when starting.
If starting with an electric start
motor, also add a spinner nut
or cone to the propeller/engine
assembly.
CAUTION: The safest way to
start the engine is with an electric
starter.
6 PREPARING YOUR ENGINE

7. Because it is more difficult to set
the needles of a 4-stroke engine
than a 2-stroke engine by ‘ear’, we
highly recommend the use of an
optical tachometer (HAN156) when
attempting to set the needles of any
4-stroke engine.
8. Make sure you use a fuel filter
between the fuel tank and the
engine. Also make sure you use
filtered fuel in the fuel tank.
How to choke your Saito
Gasoline engine equipped
with the Saito/Walbro
Carburetor.
Provided with your engine is a choke
bar. This bar has a 90 degree bend on
one end and a 3.5mm thread on the
opposite end for engaging the internal
threads of the rotating barrel of the
carburetor.
You engage the internal threads of
the rotating barrel by inserting the
threaded end of the choke bar into
the hole in the center of the lever and
rotate clockwise to engage the internal
threads. Once engaged with the threads
you can begin the choke procedure:
1. Make sure the ignition module is
turned off.
2. Fully close the throttle barrel. (If it
is not fully closed it will be difficult
to draw fuel into the carburetor for
choking).
3. Pull the choke bar and fix it in place
with a clamping tool of some sort
against the side of your cowling so it
cannot spring back into the normal
operating position.
4. Rotate the propeller by hand in a
clockwise direction (from the front
of the airplane) until you hear a
hissing sound come from the carb-
uretor a total of 5 times. This gets
fuel into the carburetor.
5. Now quickly flip the propeller 10
times in a clockwise direction and
your choking process is complete.
This gets fuel into the cylinders of
your engine.
6. Remove the choke bar from the
carburetor, turn on the ignition and
begin flipping the propeller. Your
engine should readily start. If it
doesn’t, repeat the above procedure.
Starting The Engine
The following procedures assume the
engine is properly mounted and the
tank is full of fuel.
Starting with an electric
starter motor.
1. Turn on the transmitter, and then
turn on the receiver switches.
Position the throttle stick to the fully
closed position.
2. Turn on the ignition system.
3. Open the throttle to approximately
¼ throttle.
STARTING THE ENGINE 7

4. Engage the electric starter for about
5 seconds and the engine should
start.
Manually starting the engine
CAUTION: Use a starting stick
or leather workman’s gloves to protect
your hands.
1. Turn on the transmitter, and then
turn on the receiver switches.
Position the throttle stick to the fully
closed position.
2. Check that the ignition system is
turned off.
3. Insert the choke bar through the carb
and engage in the rotating barrel of
the carb.
4. Pull the choke bar out and hold in
position.
5. Next to pull fuel into the carb, grasp
and rotate the propeller through
a number of times. This choking
operation works better if the
propeller is not quickly flipped but
pulled through the operation. Once
you hear that fuel is flowing to the
carburetor, rotate through another 5
times.
6. Now quickly flip the propeller 10
times in a clockwise direction and
your choking process is complete.
This gets fuel into the cylinders of
your engine.
7. Release and remove the choke bar.
8. Turn on the ignition.
9. Quickly flip the engine through.
The engine should start easily. If
it does not start, repeat the above
choking procedure.
Break-in
Break-in is a very important start to
a long and enjoyable engine life so
please do these steps with patience and
care.
The main purpose of the break-in
period is to provide plenty of lubricant
to each and every moving part in
the engine. Rough engine operation
during break-in because of a rich fuel
mixture is ok and required to ensure
that adequate lubrication is being
provided to the newly mated parts.
1. Start the engine as described and
allow it to operate at low rpm for
3–5 seconds.
2. While running at slow rpm, open
the main (high-speed) needle ½
turn and open the throttle ½ way. If
a rich mixture is not evident at this
point, open the low-speed needle to
achieve a rich mixture. While no
particular rpm target is given, this
should all be accomplished at or
below 5000 rpm. The object is to
run this way for two full tanks. This
provides sufficient lubrication to all
the mating surfaces to allow them to
begin to work together.
3. Reset the low-speed needle to the
factory specification and run one
full tank of fuel with the rich high-
speed needle setting and ½ throttle.
4. With a fresh tank of fuel restart
the engine, this time leaning the
high-speed needle to achieve a
8 ENGINE BREAK-IN

peak setting followed by richening
to cool. Do this about 10 times
throughout the course of this tank
of fuel.
5. Leaving the high-speed needle in
a peaked condition, check your
throttle response, going from
low to high and back, gradually
lengthening the duration of high
rpm. Continue the break-in process
until you can get a stable high rpm
for at least one minute. At this point
the ground break-in is complete.
Carburetor
Adjustments
Low-speed
needle
High-speed
needle
Notice: Before adjustment make sure
the low-speed needle is set at the target
position. In particular make sure this is
done after doing the break-in process.
It is also preferable to start with the
main (high-speed) needle ½ turn open
from the target position. In principal
the carburetor should be adjusted by
first achieving peak rpm with the main
(high-speed) needle valve and then
adjusting the low-speed needle valve.
(Until the high-speed needle setting
is fixed low-speed adjustment will be
difficult and not stable.)
1. Fill the fuel tank and then start the
engine as previously described.
After the engine starts allow it to
warm up for 20 seconds and then
fully open the throttle.
2. Utilizing a tachometer, adjust the
main (high-speed) needle valve to
peak rpm carefully. Note as you
lean the motor the drop off in rpm,
richen back to the peak rpm from
that position.
CAUTION: Over-closing
(leaning) the main needle valve can
be dangerous, causing pre-ignition,
knocking and possibly loosening the
propeller. If you hear these symptoms,
immediately richen the needle valve.
3. Next close the throttle until the
engine idles reliably at about 1700
rpm. Careful coordination between
the idle (low-speed) needle and the
throttle position is needed to achieve
this.
4. After you have a reliable idle now
check for a good slow transition
from low to high. If the engine
CARBURETOR ADJUSTMENTS 9

10 NORMAL ENGINE OPERATION
bogs down during the transition,
then the idle is too rich and needs
to be adjusted leaner. If during the
transition the rpm increases quickly,
the idle is likely too lean and needs
to be adjusted richer. Continue
working in this manner until you
are satisfied with the slow transition
from low to high rpm.
5. Once you have completed the slow
transition adjustment now is the
time to check how the engine reacts
to a fast throttle transition from low
to high speed. If the quick transition
results in a gradual increase in rpm
to a peak setting, the high speed
is likely too rich and should be
adjusted leaner. If the engine quits
or hesitates during this transition the
high-speed adjustment is likely too
lean and should be made slightly
richer. Continue working in this
way until you are satisfied with the
quick low to high speed transition
of the engine.
Because the engine will unload in
the air when the propeller operates
in turbulent free conditions, it is
necessary to richen the high speed
slightly before your first flight. Final
adjustment of the carburetor needs
to be made after actually flying the
airplane in the conditions and manner
that you enjoy.
Normal Engine
Operation
1. Ensure the ignition battery is
adequately charged before flying
your aircraft. The ignition system
usage is roughly 790mAh at full
throttle so judge the required
capacity of your pack based on the
flight time expectations you have.
2. Connect a heat-proof and gasoline-
proof line to the crankcase breather
nipple. Make this line long enough
to exit the cowl so the interior of
the engine compartment will remain
mostly oil free.
3. Lubrication for the piston, conrod,
bearings and cam gears comes from
the blow-by fuel and oil between
the cylinder and the piston. The
engine is designed to provide
adequate lubrication to these
crankcase-located parts when good
reliable oil is used. We have used
Evolution®Oil (EVOX1000Q) with
good results.
4. Over-closing (over-leaning) the
main (high-speed) needle valve
will result in overheating, pre-
ignition, knocking, engine failure
and adverse effect on the conrods
and cam gears. Always set the main
needle on the ground slightly rich
to allow the peak rpm and setting to
occur once the airplane is airborne.
5. When attaching the exhaust pipe
to the cylinder or the propeller nut
to the shaft, apply a threadlocking

ENGINE MAINTENANCE 11
compound before attaching the
two parts together. This will help
to keep these parts tight and help
prevent any leakage from occurring.
6. The propeller nut and the exhaust
locking nuts should be tightened
when the engine is hot.
Engine Maintenance
NOTICE: DO NOT NEEDLESSLY
DISASSEMBLE YOUR SAITO
ENGINE. ONLY QUALIFIED
INDIVIDUALS SHOULD PERFORM
ENGINE REPAIRS. DAMAGE DUE
TO IMPROPER DISASSEMBLY
WILL NOT BE COVERED UNDER
WARRANTY.
If it becomes necessary to dismantle
your Saito engine, the following
procedure should be followed:
It’s important to maintain identif-
ication of the “left”and“right”
cylinder parts when dismantling and
reassembling the engine. Looking
forward from the rear of the engine
with the engine upright, the cylinder
on the right side is the right cylinder.
Therefore, the cylinder to
the left is, of course, the left cylinder.
Adjustment of the
Tappet Gap
1. Once the break-in on the ground is
completed, you should adjust the
tappet/valve gap for the first time.
After the initial adjustment, inspect
the tappets at least after every 10
hours of operation and check for
the proper gap. Your experience
may cause you to do this more
frequently.
2. Adjustment of the tappet is done
when the engine is cold.
3. Remove the spark plugs and the
rocker covers from the engine.
4. Rotate the propeller slowly in the
normal direction of rotation. Once
you see the intake valve open and
close, rotate the propeller another
180 degrees and you should be at
the compression top dead center.
5. In that position loosen the tappet
locking nut and adjust the clearance
to virtually zero. (You should not
be able to insert the included feeler
gauge between the tappet and the
valve.)
6. After the gap is checked tighten the
locking nut firmly but do not over-
tighten.
Note. In normal maintenance of
full-size four-stroke engines, a little
clearance between the tappets and the
pushrods/camshaft is allowed because
of the assumed expansion of the valve.
Saito engines are different because
of the aluminum construction. The

12 TIPS FOR EXTEDED ENGINE LIFE
cylinder in Saito engines elongates
more than the valve and the clearance
gets larger as the engine heats up.
Therefore, in cold conditions the
clearance should be virtually zero.
After several hours of running the
occasional check of the tappet clear-
ance can be performed quite easily.
Once the engine is cool set the engine
up as described above (intake closed
and at top dead center) and check to
see if you can slide the included feeler
gauge (0.10mm thick-ness) between
the tappet and valve. If you can it is at
its absolute maximum and valve tappet
adjust-ments should be made. If you
cannot slide the feeler gauge between
the two, then your adjustment is fine
and nothing further needs to be done.
Tips For Extended
Engine Life
To add longer life to your Saito™
engine the following recommendations
are made:
1. Use a fuel 20:1 gasoline to oil ratio.
2. Use recommended spark plugs.
3. Use the proper propeller size and
balance the propeller prior to use.
4. Use a tachometer for precise engine
adjustments.
5. For long-term storage, make sure
there is no fuel left in the tank,
caburetor and the engine. Store the
engine in the box or on the airplane
with the nose down in order to keep
oil in the bearings.
FG-57T Needle Valve
Target Positions
High Speed - 2 turns + 50 minutes
Low Speed - 4 turns + 10 minutes
Spark Plug Gap
Please maintain your spark plug gap
between 0.7mm (0.027") and 0.8mm
(0.031")

TROUBLESHOOTING 13
Troubleshooting
Generally speaking, there are very few things that will keep today’s modern
gas engines from starting. To that end, make sure you’re using good quality
“fresh” fuel, you have a fully charged ignition battery, and good spark plugs
installed. Should the engine fail to start after these items are verified, refer to
the troubleshooting chart below.
SYMPTOM
CAUSE
CORRECTIVE ACTION
Engine fails to Low voltage on Replace/recharge the
start ignition battery ignition battery
Bad spark plug(s) Inspect/replace bad spark plug
Insufficient priming Repeat priming procedure
“Flooded” due to Disconnect ignition battery,
excessive priming remove the spark plugs, and
rotate the propeller several
times to “clear” the cylinder
Engine fires but Over-primed Disconnect ignition battery and
does not run rotate propeller several times to
“clear” cylinder
Engine starts but Mixture too rich Close high-speed needle valve
slows down and 1/4turn and start again. Repeat
then stops
until engine is running smoothly
Engine starts, Mixture too lean Open high-speed needle valve
speeds up, and 1/4turn and start again. Repeat
then quits
until engine is running smoothly
Rough idle Plug Change plug type
In the event that none of the above procedures results in the engine running
properly, contact our service department for suggestions:
Horizon Service Center
4105 Fieldstone Road
Champaign, Illinois 61822
877-504-0233 (Mon–Fri 8:00–5:00 CST)

14 PARTS LIST
Twin Cylinder Gas Cross-Reference Chart
TWIN CYLINDER GAS CROSS REFERENCE CHART
ITEM
P
FG-57T
01 Cylinder, Left
02 Cylinder, Right
06 Piston
07 Piston Pin
08 Piston Pin Ret
09 Piston Ring
10 Con Rod
11 Linked Con Rod
12 Conrod Linkpin/Scr
13 Con Rod Screw
14 Cyl Screw Set
15 Crankcase
19 Breather Nipple
20 Frt Ball Bearing
21 Main Ball Bearing
22 Rear Ball Bearing
23 Crankshaft
24 Pinion-crankshaft
25 Pinion gear pin
26 Collar, Crankshaft
27 Tapered Collet & Drv
28 Prop Wash/Nut
29 Prop Nut Spinner
31 Crankcase Screw S
32 Eng Gasket Set
33 Cam Gear Housing (right)
33 Cam Gear Housing (left)
34 Cam Gear Left
35 Cam Gear Right
36 Cam Gear Shaft
37 Steel Wash Set
38 Tappet
39 Pushrod
40 Push Rd Cvr Rb sea
41 Rocker Arm
42 Rckr arm scrw nut
43 Rckr arm pin
46 Valve in/out
47 Vlv spg/kpr/rtr
48 Vlv Retainer
49 Rocker Arm Cover
69 Intake manifold, lft
70 Intake manifold, rt
G57T01
G57T02
G57T06
18007
300T08
18009
300T10C
*
*
300T13
G57T14
G57T15
G3619
300T20A
300T21
300T22
G57T23
*
*
*
G57T27
450R3D28
*
300T31
G57T32
G3633
G57T331
300T35
120S35
5036A
G57T37
120S38
G57T39
G57T40
120S41
120S42
120S43
120S46
120S47
120S48
150S49
G57T69
G57T70
ITEM
P
FG-57T
73 Muffler, Left
80 Muffler nut
821 Carb comp
831 Carb body assy
90 Carb scr/spring set
91 Carb gasket set
93 Intake velocity stk
96 Tool set
97 Instruction Manual
99 Muffler bracket
110 Anti-loos Prop nut
119 Rear Cvr/w eng mt
120 Spark Plug
140 Muffler Rt Angle Adapter
152 Screw Pin
123 Rub bush PRC U
124 Rub bush PRC L
153 Electronic Igntion System
164 Inlet Manifold
165 Throttle Control Assembly
135 Prop Wash w/Anti-loos nut
F-1 Fuel Filter
Filter w/weight
G57T73
22OA8O
G57T821
G57T831
G3690
G3691
57T93
G57T96
SAIMANGAST
300T99A
G57T110
G57T119
G36120
220A140
G36152
120S123
120S124
G57T153
G57T164
G57T165
G57T135
50109
G36154
Fuel Tube (Gasoline) G36155

PROPELLER SELECTION 15
Propeller Selection
Below you will find a propeller
selection chart. This chart will enable
you to select the best propeller for
initial setup of your Saito engine.
Remember, it is imperative to balance
each propeller prior to installation
onto your Saito engine.
Failure to do so may cause unwanted
vibration in your aircraft.
SaitoTwin-Cylinder Gas Propeller Chart
ENGINE SPORT SCALE
FG-57T
1,500 - 7,000 rpm 21 x 10, 22 x 8 22 x 8, 22 x 10, 23 x 8,
22 x 10
NOTE: Observe operating rpm ranges as excessive rpm can result in damage to the engine.
Damage from overrevving the engine will not be covered under warranty
OUTSIDE DIMENSIONS (mm)
FEDC2B1BAsmetI
FG-57T Twin Cylinder Gas 104 26.5 33 168.5 232 80 83
SPECIFICATIONS
psiDsmetI
(cc)
Bore
(mm)
Stroke
(mm)
Total Weight
(g)
K
(ISO)
Cylinder Thrust
FG-57T Gas 57.0 36.0 28.0 2435 M10 x 1.25 28.5 x 2AAC 6 - 8 Kg
(13.2 - 17.6 lb)
TM

16 PARTS LIST
Table of contents
Other Saito Engine manuals
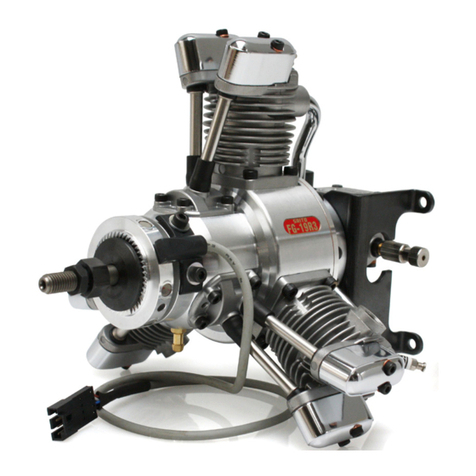
Saito
Saito FG-19R3 User manual
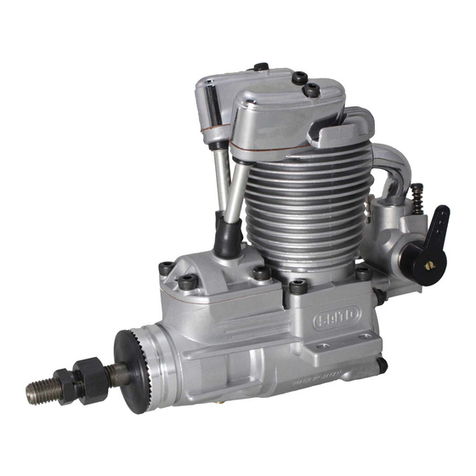
Saito
Saito FA-56B User manual

Saito
Saito FG-33R3 User manual
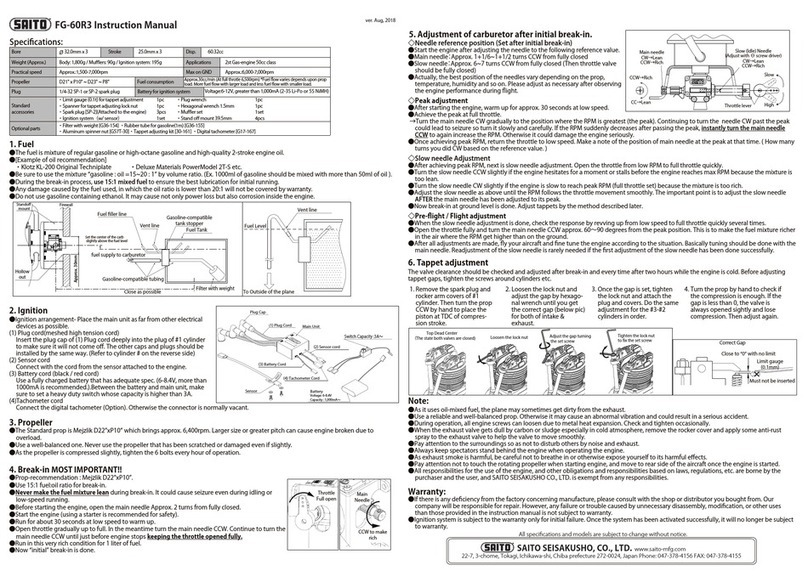
Saito
Saito FG-60R3 User manual
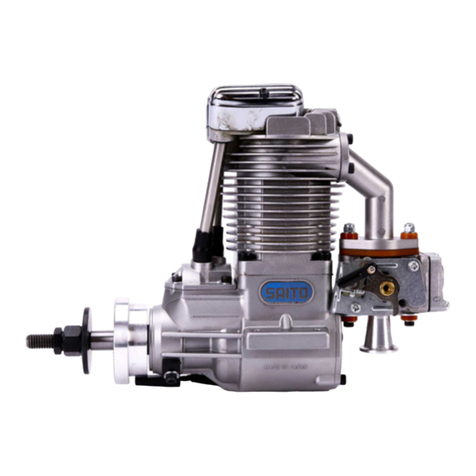
Saito
Saito FG-40 User manual
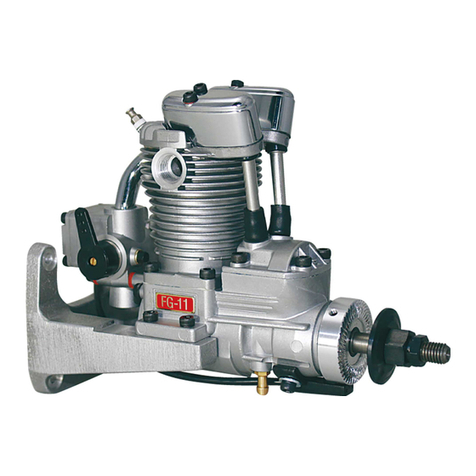
Saito
Saito FG-11 User manual

Saito
Saito FG-14C User manual
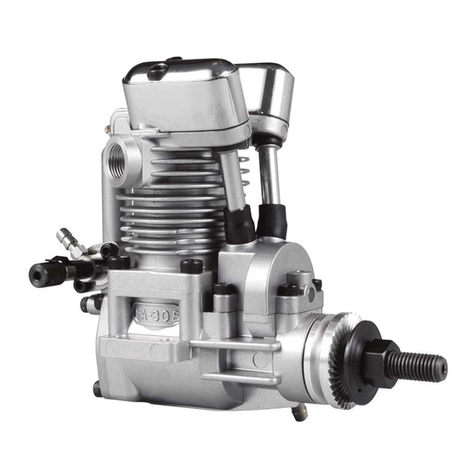
Saito
Saito FA-30S Golden Knight User manual
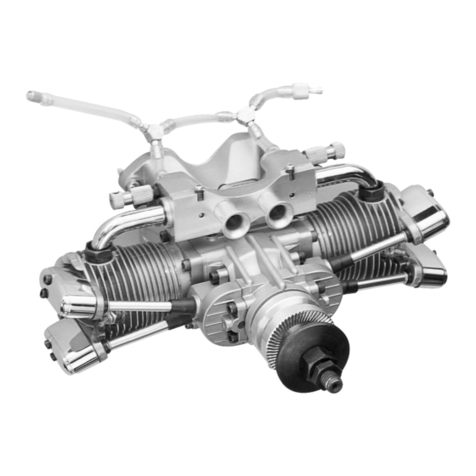
Saito
Saito FA-60T User manual
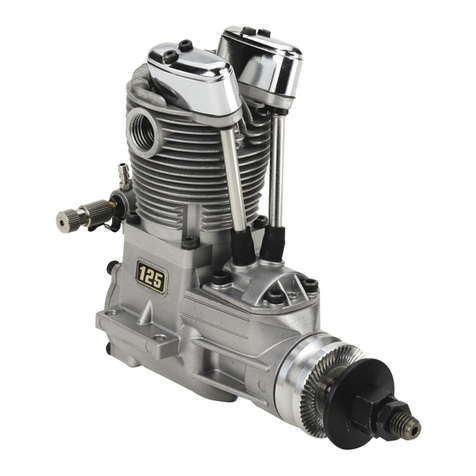
Saito
Saito FA-30S (H) User manual
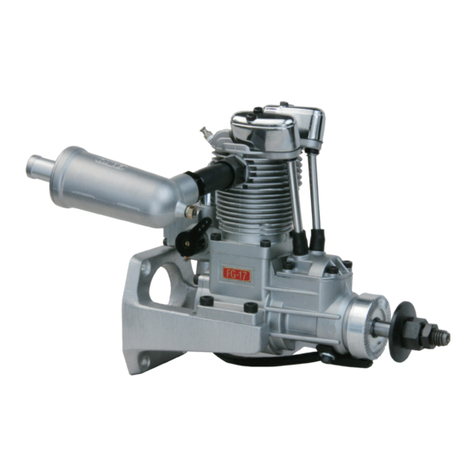
Saito
Saito FG-17 Operation manual

Saito
Saito FG-21 User manual
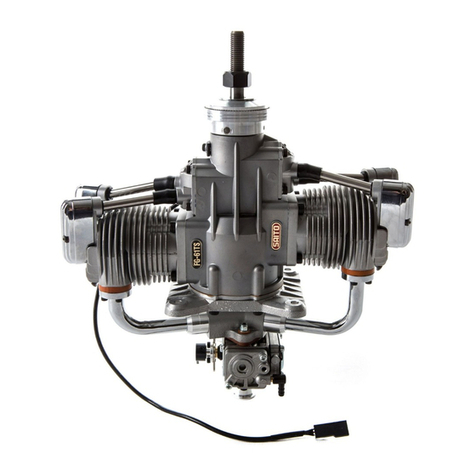
Saito
Saito FG-61TS User manual

Saito
Saito FG-60R3 User manual
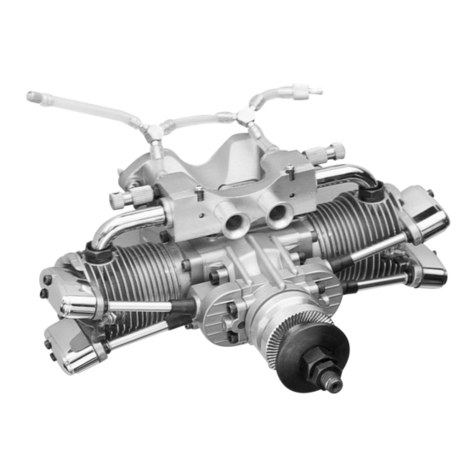
Saito
Saito FA-60T User manual
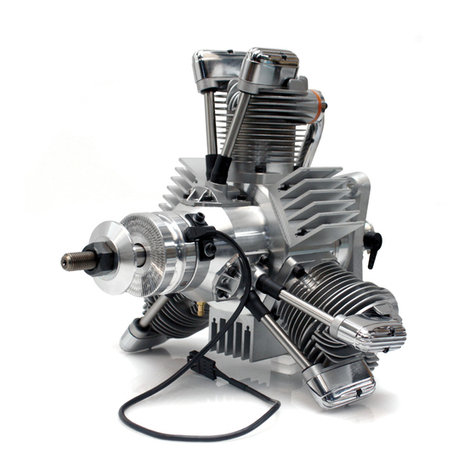
Saito
Saito FG-90R3 User manual
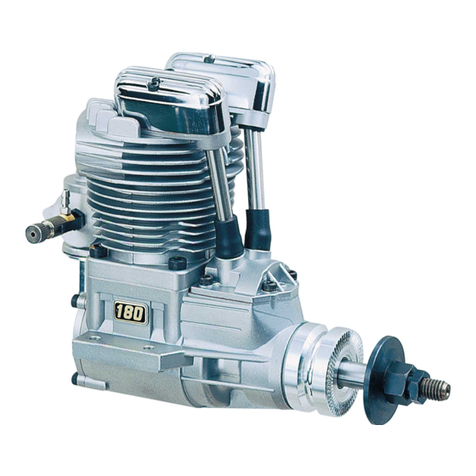
Saito
Saito FA-72B User manual

Saito
Saito FA-30S(H) User manual
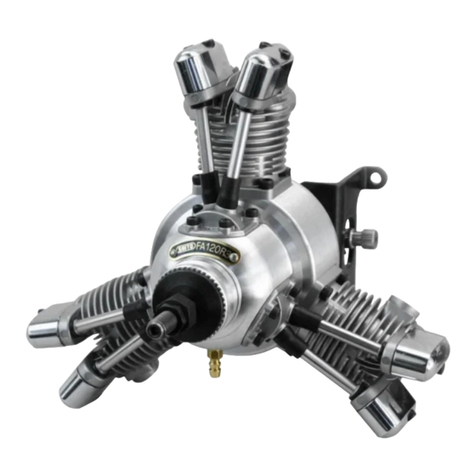
Saito
Saito FA-120R3 Firmware update
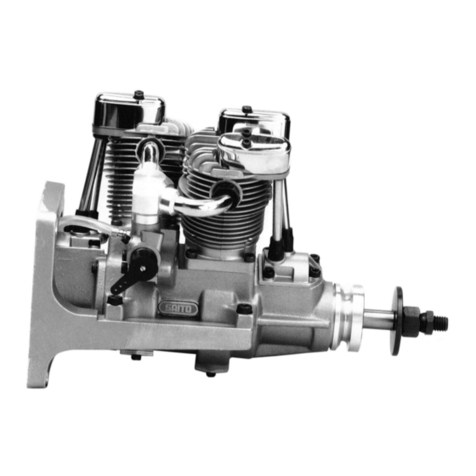
Saito
Saito FA-100Ti User manual