Tokyo Keiso UL400 User manual

TOKYO KEISO CO., LTD.
UL400
CLAMP-ON TYPE ULTRASONIC
FLOWMETER
Thank you for purchasing our ultrasonic flow meter.
The Instruction Manual describes the standard specifications, installation
procedure, operating methods, and handling precautions of the UL400
Clamp-on Type Ultrasonic Flow Meter. Be sure to read it prior to using it.
INSTRUCTION MANUAL
B-06-E01
Sep. 2017
STORAGE
If the instrument not used just after receipt of it, be sure to store it at the
place as outlined below:
・ Free from rain or water splash
・ Stable temperature and humidity (0 to 50°C, 90%RH or less)
・ Free from vibration
・ Free from the corrosive gases

1
WARNING
This product is delivered after manufacturing and
adjustment. Inspections have been conducted
based on the optimum quality control method for
industrial instruments. If any attempt is made to
modify or change this instrument, it may fail to
perform as intended or incompatibility or accidents
may result. Do not modify or change this instrument
in any way. If it is necessary to modify or change it,
contact Tokyo Keiso Co., Ltd.
■ NOTATION RULES
Safety symbols
The manual uses the following symbols to describe what is strictly prohibited or cared about for your safety, and what
should be observed in handling the product. Be sure to read the notices marked with those symbols.
■ OPERATIONAL NOTES
If this indication is disregarded and this instrument is operated
incorrectly, serious injury or fatal accident may result.
W
ARNING
If this indication is disregarded and this instrument is operated
incorrectly, injury or property damage may result.
C
AUTION
Indicating procedures or information required to operate this product.
N
OTES
WARNING
When removing this product from your process for
maintenance or inspection, make sure there is no
object to be measured remaining in the instrument.
If the object is corrosive or toxic, the operator may be
adversely affected.
WARNING
Although this product is delivered after manufacturing,
adjustment and inspections have been conducted based
on the optimum quality control method for industrial
instruments, an unexpected defect may occur. If this
product is used for process control that may result in a
critical safety problem, take all necessary actions to
maintain safety.
CAUTION
Use this product only as an industrial instrument.
CAUTION
The material of this product is described in the Approval
drawing. Although we make every effort to select the
optimal material for the customer's specifications, it may
not be perfect due to the presence of foreign matter.
Thus you are responsible for checking anti-corrosive and
compatibility.
WARNING
Be sure to operate the instrument within the ranges of
the specifications for fluid pressure and temperature
listed in the Approval drawing. If the instrument is
operated out of these ranges, it may become
defective or be damaged.
WARNING
This UL400 converter belongs to “permanent connected”
indstrument. The power line shoud be connected to a
“Switch” (or “Circuit Breaker”) to be able to turn off the
UL400 in any situation. Please confirm the following
items when installing the switch:
1. Please consider the safety issue in factory to decide
the location of the swtich.
2. The switch should be easy for operation.
3. An indication is necessary for notifying which switch
connected to UL400 conveter.
4. Confirm that the power is turn off before opening the
UL400 cover.

2
1. OUTLINE
The UL400 is a clamp-on type ultrasonic flow meter capable of measuring a flow rate in the metal or plastic piping with
a nominal diameter of 25~400 mm (UL430) or 25~1000 mm (UL450). An ultrasonic sensor is installed on the existing
piping from the exterior by the clamp-on system, and the flow rate can be easily measured without contacting the
measuring fluid because of no moving part or pressure loss. Pay special attention in installing the ultrasonic sensor
because the measuring accuracy and stability very depend on the installation of the sensor.
2. CONTENTS OF PRODUCT
The UL400 is delivered, including the following. If you find any thing missing, contact our dealer.
No. Contents Quantity
1 Converter (UFC430/450) 1
2 Sensor (UFS430 / UFS450) 2
3 Signal cable in 10m (standard) with connector 2
4 Band to install sensor 1
5 Installation rail 2
6 Grease for sensor 1
7 Instruction manual 1
8 DATA Card 1
9 Support for 2” Pipe installation (* NOTE1) 2
10 Spare Fuse (* NOTE2) 2
<Note>
* Note 1: Only supplied for 2” Pipe installation required.
* Note 2: Subsidiary within the converter.
3. GENEAL PRECAUTIONS NOTES
3.1 Power supply
Pay attention to the following for the power supply to connect.
1) Voltage
Use the power source in the range of 100 to 240V for AC type converter (working voltage range: AC85~264V).
Use the power source 24DC for DC type converter (working voltage range: DC20~30V).
2) Frequency
Make it 50/60Hz for AC power source.
3) Common use with other power supply
Be sure to use the power supply for instrumentation, and avoid the common use with the power source for
power.
4) Noise
When sources of a noise such as an inverter are located near, be sure remove a noise at the generation source
N
OTES

3
side using a noise filter.
5) Instantaneous power failure
Since it is an electric device, be careful not to cause instantaneous power failure.
3.2 Measurable fluid
Although any liquids can be measured, there is the following restriction.
1) Flow velocity
The minimum full scale which can be set up is 0.3 m/s in flow velocity conversion, but it cannot be correctly
measured in the line in very slow velocity. Calculate the flow velocity in a full scale by the following formula,
and confirm that the flow velocity is 0.3m/s or more.
Measurement accuracy is deteriorated at flow velocity of 1 m/s or less.
V
: Flow velocity (m/s)
Q
: Flow rate (m3 /h)
D
: Inside dia. of pipe (mm)
2) Reynolds number
When the Reynolds number "Re" calculated by the above formula is 10000 or less, the measurement becomes
less accurate. Especially in case of the fluid of the high viscosity and the piping in small diameter,
keep it in mind that Reynolds number becomes smaller.
ρ:
Density (g/cm3 )
Q
: Flow rate (m3 /h)
μ
: Viscosity (mPa・s)
D
: Inside dia. of pipe (mm)
3) Acoustic velocity
The acoustic velocity of the fluid which can be setup is 1000 to 2500m/s.
4) Solids and bubbles
The UL400 has higher bubble resistance and slurry resistance than the conventional clamp-on type ultrasonic
flow meters, but is not suitable for large quantity of them.
5) Kinematic viscosity (mm2/s)
Kinematic viscosity can be setup is 0.3~40 mm2/s.
6) Fluid temperature
N
OTES

4
Max 90℃(the temperature of the surface on the pipe).
3.3 Notes on measuring piping
1) Measurable piping
Pipes which can be measured are as follows:
・ Nominal diameter:25 ~ 400mm (UL430),25~1000mm(UL450)
・ Material: Metals
Plastic (PP, PVC, PVDF etc.)
2) Installation position of ultrasonic sensor
・ Avoid a welding line portion to install the ultrasonic sensor.
・ For piping of an old iron, the ultrasonic wave may not be transmitted correctly due to the rust or corrosion
etc., and the measurement may not be correctly made. In this case, the position to install the sensor is
to be changed, and the proper place is to be selected.
・ If there are the rust and thick coating at a place where the sensor is to be installed on the surface of
piping, remove them.
N
OTES

5
4. SELECTION OF INSTALLATION PLACE
4.1 Converter
Regarding the installation place, the following conditions should be taken into consideration:
1) A place where the ambient temperature is -25°C to +50°C, and the humidity is less than 90%RH (without dew).
In order that it can be used for the long time in the stabilized condition, it is recommended that it is to be installed
in the place at normal temperature and humidity as much as possible.
However, if it is less than -10°C inside the converter, the indicator does not operate correctly.
2) A place with little vibration.
3) A place with little dust and corrosive gas.
When unavoidably installing the converter in a place with much corrosive gas, perform the air purge.
4) A place where the sunshine does not hit directly.
5) A place where there is no possibility of this products inking into water.
The waterproof is IP65 (Jet-proof).
6) A place without a possibility of bringing about the inductive interference.
Avoid installing it near to the power apparatus etc.
7) A place where the maintenance and inspection can be easily performed.
4.2 Ultrasonic sensor
To install the ultrasonic sensor, take the following conditions into account:
1) For outdoor installation, take suitable shading and waterproofing measures.
In case of installation in the field, consider the suitable shading and waterproofing measures to avoid the direct
sunshine and rainwater.
2) The piping should be always filled with water.
If the piping is not filled with water, a measurement error may result. Avoid a line where the fluid flows out of
the piping at the time of stopping the flow, and select a place where the piping is always filled with water.
3) The flat piping wall of at least 350mm or more is required.
In order to install a sensor rail, the flat tube wall of at least 350mm or more s required.
(For more than 200mm in nominal diameter, 650mm is required.) Select an appropriate place.
4) Avoid the place where the extremely big vibration, for instance, behind the pump and so on is expected.
The adhesion of the ultrasonic sensor to the tube wall is worsened by the vibration, which may result in poor
N
OTES
N
OTES

6
accuracy.
5) Secure the required upstream and downstream straight lengths.
In order to obtain the flow with the axial symmetry, the below-mentioned straight pipe lengths are required.
Otherwise, the accuracy will be out of the accuracy range.
※If the required straight lengths cannot be secured, measurement may go out of our accuracy range.
If a whirlpool or revolving stream is observed, make the straight pipe lengths longer or install a rectifier.
Table of required straight run – up stream and down stream D:Pipe Nominal Diameter
Division Upstream Straight Pipe Length Downstream Straight Pipe Length
90°Bend
L≧10D
10D 以上
L
≧
5
D
Tee
10D 以上
L≧50D
10D
以上
L
≧
10
D
Expanding
Pipe
0
.
5
D
以上
L
≧
30
D
1.5D 以上
D
L≧5D
Contracting
Pipe
L
≧
10
D
L≧5D
Valves
L
≧
30
D
When controlling the flow rate
with the upstream valve
L
≧
10
D
When controlling the flow rate
with the downstream valve
≥10D
≥10D
≥10D
≥1.5D
≥.5D

7
Pump
Source:Japanese Industrial Standards Committee JEMIS-032
6) In performing the measurement of flow rate of a liquid mixture process, install a sensor downstream
more than 30D away from the point of being mixed.
The measurement made near to the mixing point may cause the fluctuation of output.
7) Other notes
The other notes are shown in Fig. 4.1 to Fig. 4.5. Refer to these figures carefully. Pay attention to them.
Prevent the air bu
bbles from
collecting at the top of pipe by
either installing it upward or
raising the flow velocity.
Fig 4.1
Install it at the lower position of p
ipe
in discharge and delivery lines.
Fig 4.2
Air bubbles are easy
to collect
Fig 4.3
Fig 4.5
Fig 4.4
気体 液体
25
25
1007550
75 50100
150
150
気体
液体
水平配管では超音波の伝搬面を水平にして
、
気泡の影響を避ける 。
Gas
Gas
Liquid
Liquid
Desirable
installing
position
Water cannot
be easily filled
in the pipe.
Avoid the influence by cavitation by installing a
flow adjustment valve downstream.
Avoid the influence by the air bubbles, making
the ultrasonic transmitting face to be parallel.
L ≧
50 D
P
Check Valve
Gate
Valve

8
5. INSTALLATION
5.1 Installation of converter
There are two types of installation available, one is wall mounts type, the other is 2B installation. In either case,
mount it by making the cable entry part downward. If mounted sideward or upward, it may result in causing the
malfunction.
a) Wall mounts type b) 2B mounts type
5.2 Wiring of converter
5.2.1 Notes in wiring
1) The signal cable and output signal cable between the ultrasonic sensor and converter should be separated from
the power supply line or power line etc. Lay the cables not to approach the power apparatus. It is recommended
that the electric wire tube is used for the separation of each cable.
2) When connecting the exclusive cable, insert the wire into the waterproof connector in the back in the receptacle
side, and turn it clockwise securely until it clicks.
3) When connecting cable core to the terminal, insert it to the back of the terminal, but do not fasten the terminal
screw too much. Otherwise, the screw may happen to break.
2B pipe
N
OTES

9
4) Ensure waterproofing processing of cable entries.
5.2.2 Terminals
When opening the cover of UL400 converter, there are the terminals to connect the electric wire.
・Release 4 cover screws to open the UL400 cover. There are 3 waterproof connectors for common cable,
2 waterproof connectors for sensor connection and 1 cable ground connector.
No. Name
①
Cover Screw
②
Waterproof connector for common cable
③
Waterproof connector for upstream sensor connection
④ Waterproof connector for downstream sensor connection
⑤ Cable ground
・Interior terminal layout
No Name
○
1 Power supply terminal
② Signal terminal
③ Fuse holder
・Enlarged View of Terminal Block
UL400 supply AC and DC type to choose, there are different representations according to them.
①
②
③
①
④
⑤
②
③

10
AC type DC type
Connector Sign
Polarity
Contents Connector
AC Type
power
supply
terminal
1 L1 Power supply(AC100~240V)
2 L2
3, 4 ground
DC type
power
supply
terminal
1 +24V power supply(DC20~30V)
2 0V
3, 4 ground
Signal
terminal
1 AO+ Analog output, output current DC4-20mA
3 AO-
6 DO1+ Status output DO1 (Open collector)
Status output DO2 (Open collector)
Status output common
5 DO2+
8 DCOM
7 RS485+ RS485 +
RS485 -
RS485 ground
9 RS485-
11 RS485 GND
13 DI+ Totalizing reset input (Short trigger)
15 DI--
2 PO+ Totalizing pulse output (Open collector)
4 PO-
10 S1+ Upstream sensor terminal
12 S1-
14 S2+ Downstream sensor terminal
16 S2-
5.2.3 Cable
1) Cable between ultrasonic sensor and converter
It is recommended to use the attached exclusive coaxial cable. Unless otherwise specified, the standard cable
is 10m in length.
2) Cable for power supply and output signal
Use the cables whose outside diameter is 6 to 12. (Customer's scope of supply)
(Vinyl sheathed cable, Vinyl cab tire cable etc.)
3) RS485 signal cable
Please prepare it when needed.

11
5.2.4 Wiring between ultrasonic sensor and converter
For the connection of the ultrasonic sensor to the converter, use Y-type connector at both ends of the exclusive
cable. The words "S1" and "S2" are shown at the part of signal terminal block of converter. Connect the
upstream sensor cable to the "S1" side, and the downstream sensor cable to the "S2" side. The transparent
coated wire of sensor cable is “+” and the black coated wire is “-“.
5.2.5 Wiring of power supply
1) It is to be confirmed that the voltage of converter conforms to the supply voltage to be connected.
2) Wire a power supply to L1 and 2 L2 of when using AC type.
3) Connect the positive of the power supply to +24 V and the negative to 0 V when using DC type.
4) Concerning the power supply, use the power supply for the instrumentation, and avoid sharing the power supply
with the one for the power.
5) Confirm that the supply voltage is within the specified range by the terminal of converter.
6) Wire Ground terminal to the terminal of the power supply. (Class D grounding,The allowable resistance is
100 or less)
5.2.6 Wiring of Analog Output
To use the analog output function, connect a receiver to AO + and AO – of signal terminal.
The allowable load resistance is 500 or less.
5.2.7 Wiring of Status Output (DO1 and DO2)
To use the status output function, connect a receiver to the signal terminals DO1 and DCOM, DO2 and DCOM.
The status output of this instrument is open collector type. The load voltage and current should be DC 30V and 50
mA or less, and be sure to insert a current limiting resistor. Low level is below than 2V.
AC
power supply
Ground wire
Caution
DC power supply
Ground wire

12
5.2.8 Wiring of Totalizing Pulse Output
To use the totalizing pulse output function, connect a receiver to PO+ and PO- of signal terminal. The pulse output
of this instrument is open collector type. The load voltage and current should be DC30V and 50 mA or less, and
be sure to insert a current limiting resistor. Low level is below than 2V.
5.2.9 Wiring of totalizing reset terminal
To reset a totalizing display value from the outside, connect a contact (one-shot) to DI+ and DI- of signal
terminal.
Remark) if the contact is closed, the counter function can’t work. Be sure not to reset it in close status.

13
5.2.10 Wiring of RS-485 serial output
To use the communication function, connect a communication cable to RS485+, RS485- and RS485 GND of
signal terminal.
5.2.11 Power fuse
A spare fuse is included in the product.
To change power fuse, unplug the original fuse vertically and insert the spare to the end vertically.
5.3 Installation of ultrasonic sensor
5.3.1 Installation of ultrasonic sensor
There are two ultrasonic sensors mounting methods available, “V” path (reflex mode) and “Z” path (Diagonal mode),
depending on the kind of piping and the pipe diameter.
25
25
1007550
75 50100
150
150
25
25
10075 12550
75 50100125
150
150
V method Z method
a) Mounting of the sensor rail
Using the mounting bands, mount the piping as shown in the figure below.
Note: When mounting to the horizontal piping, ensure that an ultrasonic wave transmission route is made
horizontal. If the transmission route is made vertical, the bubbles in the pipe may block transmission of the
ultrasonic wave, disabling normal operation.
Z method
*Note the direction of the sensor rail.
Notes
Mounting bands
Sensor rail
150
150
150
150

14
b) Application of grease
Apply the grease to the face where the ultrasonic sensor touches the wall tube in order to eliminate the air space
between the ultrasonic sensor and the wall tube.
c) Mounting of the ultrasonic sensor
Put the ultrasonic sensor into the rail through a square hole. When this is done, turn the sensor pressing screw
fully counterclockwise to keep the grease applied inside the rail, so that the applied grease will not be adhered to
unintended areas of the piping or the rail.
150
150
150
150
d) Setup of distance between sensors
By inputting the data required for the converter, the distance between sensors is automatically calculated and
displayed. (Confirm the Install Distance (Distance between sensors) of 『6.6.2 Setup of Basic Parameters
[1.BASIC] 』) Turn the sensor fixing screw counterclockwise to loosen it, and align the tip of the vernier with the
scale to set up the distance between the sensor.
250
25
75
0
50
75 50
5.3.2 Fixation of ultrasonic sensor
After the fixation to piping is completed, a sensor pressing screw is turned clockwise to make the sensor stick
Grease applied face
Sensor Forcing Screw
Note
vernier sensor fixing screw
sensor fixing screw scale
square hole

15
firmly to the piping.
5.3.3 Connection of Exclusive Cable
After fixing the sensor, connect S1 (upstream side) and S2 (downstream side) of a signal cable correctly.
5.3.4 Waterproof measure for sensor
The waterproof class of UL400 is IP65. Sensor may be flooded by dew condensation on insulation materials
or rainwater accumulated in a waterproof cover when outdoor installation, so please set the drainage holes.
When installing the ultrasonic sensor onto the outdoor piping:
Waterproof property of the sensor is assured only after connecting the exclusive signal cable. After
fixing the sensor, be sure to connect the cable, or take some water resisting measure.
Grease for a coupling may be washed away by rainwater, impairing long-term stability. If this is case, it
is recommended to take some water resisting measure in the field.
Note

16
6. OPERATION OF CONVERTER
6.1 Necessity of setup
If the specifications are presented at the time of ordering the UL400 ultrasonic flowmeter, it will be delivered with the
prescribed data set up in the converter with Tag No. (If you confirm the combination method of converter and
sensors and mount the sensors to the piping according to the install distance set up in the converter, it can be
operated only by making zero point adjustment described later.)
If the above setup is not made, or if the operation conditions are changed, the setup is to be performed in
accordance with the below-mentioned procedure.
6.2 Operation part
No. Name Function
① Alarm LED working correctly⇒ LED off, alarm happen⇒ LED on
② Error LED working correctly⇒ LED off, error happen⇒ LED on
③ Status LED Green: forward flow / Orange: reverse flow / Red:
setting now
④ LCD display Display of flow rate, tantalization and setup
parameter
⑤ M/ENT key Switch the measuring and setting mode.
Decision of setup
⑥ SHIFT key
Refer to 6.3 Basic Key Operation
⑦ UP key
⑧ DOWN key
Refer to 7.2.2 for more detailed functions of LED.
1
2
3
4
5
6
7
8

17
6.3 Basic key operation
There are 4 setting keys including M/ENT in the converter of UL400.
Holding down M/ENT can switch the operation mode between measurement and setup.
To change parameter, go to the setting mode and use setting keys to change its setting. In a parameter menu,
when a setting value is not right, an error message is displayed. Recheck the contents of the setting and redo
the setup.
・Functions of Setting Keys
Name Operating condition
Measuring mode
S
etting mode
M/ENT
key
(MENU/ENTER key)
Holding down to enter setting
mode by inputting the right
password
Determine parameter and
numerical value
Return to measuring mode by
holding down the M/ENT key
UP key
H
olding down
to display
the
install distance of sensor.
After 10sec, return to
measuring mode
automatically.(refer to
6.6.2.12)
Change parameter menu/item
Increase the setting value
DOWN key
Holding down to enter the
check mode.
Change parameter menu/item
Decrease the setting value
SHIFT key
H
olding down
to
display
the
S/N, CPU firmware and
FPGA program version. After
10 sec, return to measuring
mode automatically.
Enter the parameter
menu/item.
Shift the numeric position of
setting value
M
ENT

18
6.4 Flowchart for data setup
There are measuring, setting and check three kinds of mode for UL400 as shown below. The movement between
each mode is performed by M/ENT, SHIFT, UP and DOWN key.
6.4.1 Measuring mode
The measured flow rate is displayed and output in the LCD screen according to setting parameters of converter.
What is displayed and output can be changed by setting.
6.4.2 Setting mode
This mode is to setup various parameters of the converter. Holding down
M/ENT key
in the measuring mode
to input the password and then press M/ENT key. If the password is correct, the mode is changed over.
Password has two kinds. The user password default is “0000” and can be changed. The maker password
does not make public and only for maintainance staffs. Inputting the user password can choose 1.Basic~
6.Advanced parameter menu. Inputting the marker password can choose 1.Basic ~ 7.Maker Param.
parameter menu. Measurement and output continues in the setting mode, but the mode『AO test』、『PulseOut
test』、『Flow test』of『7.Maker Param.』, the output changes according to the setting test. Setting mode consists
of 7 kinds of parameter menu depending on the function.
1. Basic …… Setup of basic items
Set up or change the basic items related to measurement, such as the piping dimensions, full-scale flow
rate, etc.
2. Totalization …… Totalizing setup
Set up totalizing function.
3. Display …… Display setup
Set up LCD Screen display in measuring mode.
4. Operation …… Setup of measurement parameter
Set up the items related to measurement operation.
5. Communication …… Setup of communication function
Set up the items related to communication function and others.
6. Advanced …… Setup of Advanced function
Set up user password and the default of totalizing value.
7. Maker Param. …… Maker parameters
Initialize the parameters and change measurement parameters without needed change generally.
Input password, hold on M/ENT key
Display the install
distance of sensor
Display S/N, CPU firmware
and FPGA program version
H
old down
M/ENT
key
Hold down
UP key
Hold down
M/ENT
key
Hold down SHIFT key
C
heck mode
T
urn on power
Setting mode
setting mode
Check password
false
true
M
easuring mode
Hold down DOWN
key
Hold down M/ENT key
※
Return to measuring mode automatically after showing the
S/N information 10sec.

19
Flowchart of setting mode
Select Para Menu
1. Basic
Check
password
Password Check
####
12.3%
123.4m3/h
Turn on power
Sensor Kind
1MH
z
<42.5
°
Pipe Kind
Plastic1
Pipe Diameter
####.# mm
Wall SoundSpeed
#### m/s
Fluid SoundSpeed
#### m/s
Kinem Viscosity
##.## mm2/s
Fullscale
##.### m3/h
Decimal point
##.##
Pipe Thickness
##.# mm
1. Setup of basic parameters(refer to 6.6.2)
・选择传感器的形式
・Selection of piping material
・Setup of outside diameter of piping
・Setup of wall thickness of piping
・Setup of sound speed of piping material
・Setup of sound speed of lining material
・Setup of sound speed of fluid
・Kinematic viscosity of Fluid
↵
↵
Liner Thickness
#### m/s
Liner SoundSpeed
#### m/s
・Setup of full-scale flow rate
・Set up decimal point
・Setup of thickness of lining
True
False
▲
▼
Measuring mode
Hold down
・Setup of K-factor
K Factor
#.###
Description of Graphic Symbols
↵
:M/ENT key
▲
:UP key
▼
:DOWN key
►
:SHIFT key
・For the detailed functions of the keys, refer to “6.3 Basic Key
Operation”.
・Anywhere during setup, you can return to the measuring mode
by holding down the M./ ENT key.
・Initial user Password:「0000」
↵
►
Hold down
▼
▲
Unit of Change
m3/h
・Set up flowrate unit
・Selection of sensor type
▼
▲
▼
▲
▼
▲
▼
▲
▼
▲
▼
▲
▼
▲
▼
▲
▼
▲
▼
▲
▼
▲
▼
▲
Other Tokyo Keiso Measuring Instrument manuals
Popular Measuring Instrument manuals by other brands

Teledyne Lecroy
Teledyne Lecroy WaveMaster 8000HD Getting started guide
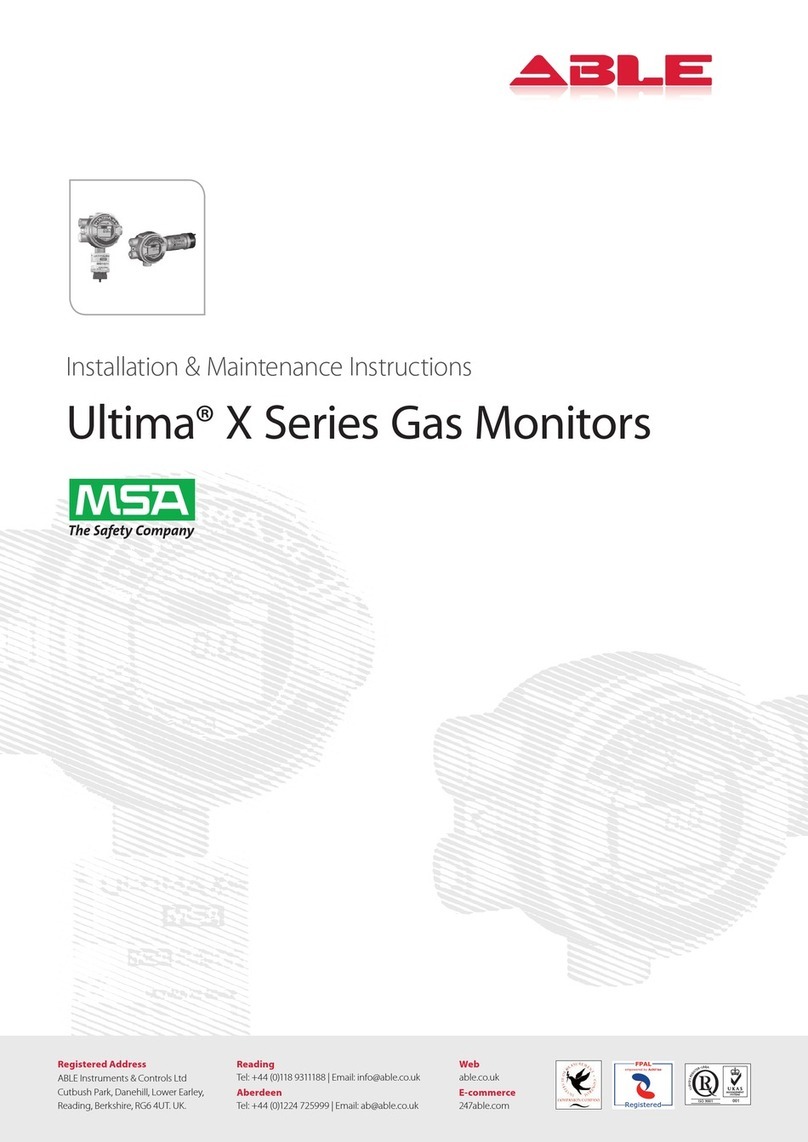
MSA
MSA Ultima X Series Installation & maintenance instructions
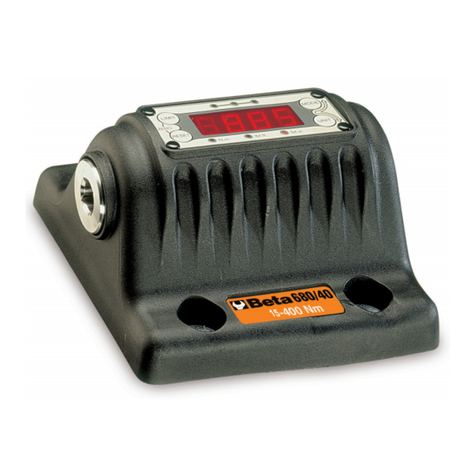
Beta
Beta 680 Instructions for use
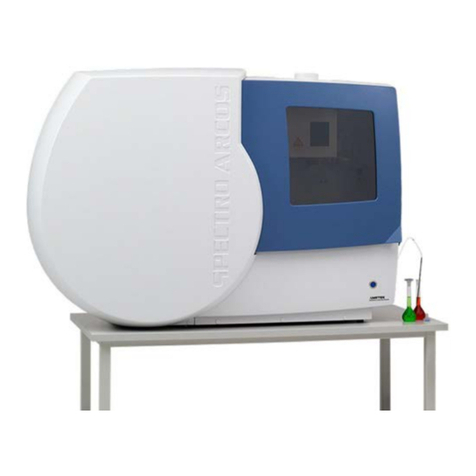
Ametek
Ametek SPECTRO ARCOS FHX22 Original operating instructions
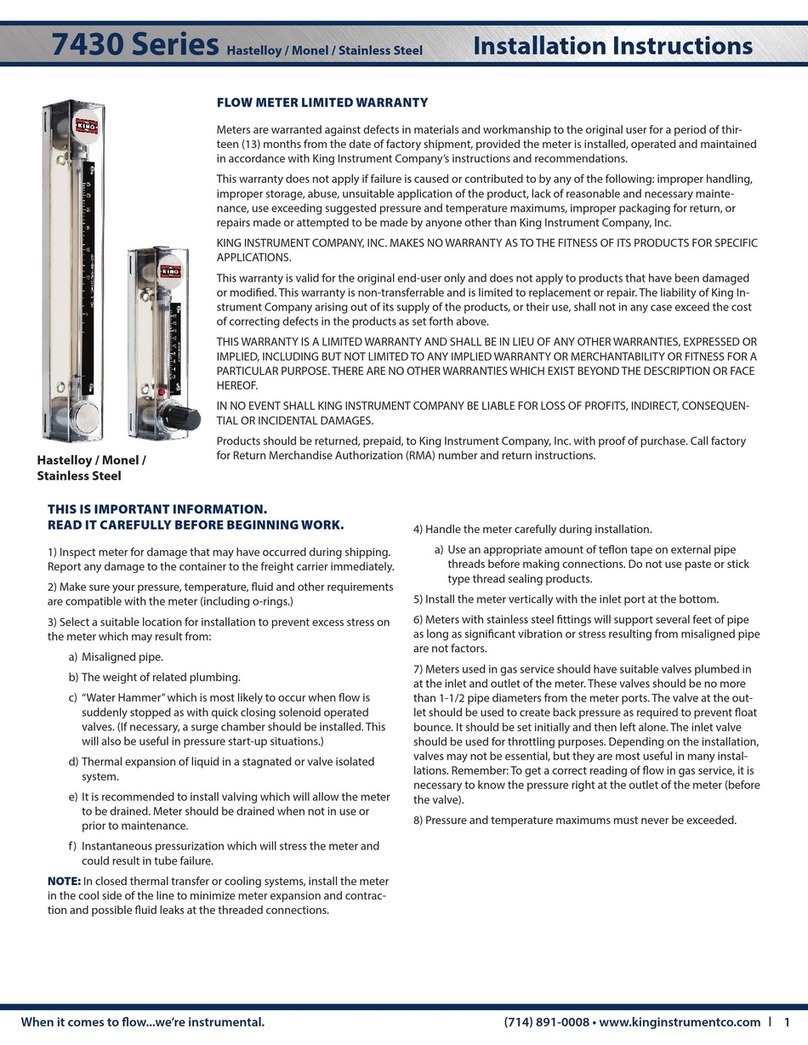
KING
KING 7430 Series installation instructions

Endress+Hauser
Endress+Hauser PROFIBUS PA Proline Promass 80 operating instructions