Toolots AD-005 User manual

Operating Manual
Freezing Compressed Air Dryer
Http://www.dryer.com.tw/
E-mail:dryer@dryer.com.tw

1. Features
1. Introduction
2. Features of Product
2. Names of Exterior Parts And Functions
1. Names of Exterior Parts
2. Operating Panel
3. Points of Installation for Attention
1. Space for Installation
2. Places Avoided for Installation
4. Method of Installation (Piping)
1. Diameters of Inlet And Outlet Pipes of Dryer
2. Piping Method
5. Method of Installation (Power Distribution)
1. Electric Features of Dryer
2. Distribution Lines
6. Method of Operation
1. Inspection Items Before Operation
2. Operation
3. Temperature Range of Dew Point
4. Stop
7. Daily Maintenance
8. Protection Device And Troubleshooting
1. Protection Device
2. Troubleshooting
9. Appendix 1: Drawing of Purification Equipment Application
1. Drawing of Electric Wires
-1-

This manual mainly provides the instructions of operating this equipment
and general maintenance tasks for the users. The purpose of this manual is
to extend the operation life of this equipment and prevent failures so as to
ensure the drying quality of the compressed air dryer.
This manual provides information related to drying equipment for reference.
Ensure to read it carefully before installing or using this air dryer and comply
with instructions of installation, operation and maintenance to prevent danger
or damage to the equipment.
Ensure to comply with instructions on installation, operation and
maintenance to prevent danger or damage to the equipment.
Features of Product
Features
-2-
1. Keep the compressed air pressure under the allowable pressure of the dryer.
2. Ensure no pressure inside the system before disassembling or installing the
pipes for maintenance.
3. The requirements for the operating power have to meet.
4. Cut off the power prior to replacing electric parts to prevent electrifying.
The major function of the freezing compressed air dryer is to remove moisture
content in compressed air by reducing the temperature of compressed air to 2
so that vapor in compressed air will be precipitated to water, which will be drained
out of the compressed air system by the automatic water drainer. Water content of
compressed air after drying is extremely little under normal circumstances.
Generally speaking, water removal rate can be up to 93%.
Ensure to follow the following regulations to avoid danger:
Notice
Introduction

Outlet Pressure
(AD-015 above models):
Outlet air pressure after
being processed by the
dryer is displayed.
Dew Point Temperature:
The cooling temperature
of compressed air is d
isplayed.
Power Switch:
Operation or stop of this
dryer is controlled by
this switch.
Overload Trip:
When the dryer fails or
operates abnormally,
the red indicator will
be on.
Compressed air
after drying flows
out from here.
Air Outlet: Air Inlet:
Wet compressed air
enters from here.
Control Panel:
This panel is
used for control,
operation and
status display.
Automatic Wat
Drainer (rear):
er
Precipitated moisture
of the dryer is removed
from here.
Power Distribution
Control Cabinet:
It is the place where
electric elements and
power are installed and
controlled.
Power Cable Hole:
There is one round
hole at the bottom of
the power distribution
control cabinet for the
power cable to go through.
Operating Panel
Names of Exterior Parts And Functions
-3-
Names of Exterior Parts

Points of Installation for Attention
Space for cleaning and
maintaining radiator
50 cm above.
Space for operation and
electric inspection
80 cm above.
Space for Installation
Places Avoided for Installation
Do not install on uneven grounds
or places where shake violently.
Do not install at places exposed
to the rain.
Do not install at places with direct
sunlight or close to heat sources.
Do not install at places that exceed
rated ambient temperature.
Do not install at places with bad
ventilation.
Do not install at places that are
dusty or with corrosive air.
Space for cleaning and
maintaining water drainer
50 cm above.
Space for maintaining
and replacing parts
80 cm above.
-4-

Method of Installation (Piping)
-5-
Diameters of Inlet And Outlet Pipes of Dryer
MODE AD-005 AD-010 AD-015 AD-020 AD-030 AD-040 AD-050
AD-060
PT
INCH 1/2" 3/4" 1" 1-1/2" 2"
MODE AD-075SAD-100S AD-150S AD-200S AD-250S AD-300SAD-400S
PT
INCH 2" 2-1/2" 3" 3" 4"FL
Piping Method
1. Please refer to the attached drawing 1 for installation procedures
when there is purifying equipment like gas tank and filter, etc.
2. Diameter of the air inlet and outlet of the dryer is the same. Pay
attention to wrong installation that may reduce the drying efficiency
of the dryer.
3. If the compressor shakes violently while running, install an extra
high-pressure vibration-proof hose unto the connection pipe
between the compressor and the dryer to protect the dryer.
4. Install valve gates and bypass pipes at the inlet and outlet of the dryer
for service and maintenance needs.
5. Diameters of the pipes should not be too small. Avoid long pipes with
many curves to reduce the loss from pressure drop.
6. Keep dust or unnecessary objects away from the air pipes while
installing.

Method of Installation (Power Distribution)
-6-
Electric Features of Dryer
Model
AD-005AD-005 AD-010AD-010 AD-015 AD-020 AD-030 AD-040 AD-050
Power
Supply
Distribution Lines
1. Select materials like lead wires with proper diameters and capacity
in accordance with the above table.
2. Power cable should go through the round hole at the bottom of the
electric control cabinet. Use proper tools to connect it to the terminal
of the lead wire and fasten it tightly at one side of the terminal.
3. Check power supply and voltage to be connected to make sure it is
within the range of 5% of rated voltage (see the nameplate).
4. Do not share the same protection switch with other equipment.
5. Install an extra proper protection switch from electric leakage in
accordance with the aforementioned electric properties.
6. Ensure to connect to the grounding wire properly.
Running
Ampere
Diameter of
Power Cable
Capacity
2.3 A4.5 A 2.8 A5.5A 3.2 A 3.6 A 5.5 A 7.0 A 8.5 A
1 220V/ / Hz
60
50
1 110V/60Hz
1.25mm
2
above 2.0mm
2
above
2P/10 A 2P/15 A
AD-060
11.0 A
3.5mm
2
above
2P/20 A
AD-075SAD-100SAD-150SAD-200S AD-300SAD-400SAD-250S
7.8A 11A 15A 20A 29A 34A23A
3 220V/ / Hz
60
50
5.5mm
2
above 14mm
2
above
3P/20 A
3.5mm
2
above
3P/30 A 3P/75 A
Model
Power
Supply
Running
Ampere
Diameter of
Power Cable
Capacity

Method of Operation
-7-
Inspection Items Before Operation
1. Inspect the voltage of power supply.
2. Inspect the environment temperature (not over 40 ).
3. Check if the condenser and the fin of the pre-cooler are clean.
Operation
1. When the power switch is on
"I", the dryer starts to run.
2. Observe if the reading on the dew
point thermometer decreases
gradually after the dryer starts to run.
If it does, it means the freezing system
is normal.
3. Check if operation of the cooling fan motor is normal.
4. After the dryer runs for 3 minutes, open the valve gates of air inlet and
outlet and check if the bypass pipes are tightened.
5. Check if the valve gate of the automatic water drainer is open.
6. Check if air pressure is within the rated range and any leakage of the
air pipes.
The valve gate of the air inlet can't be opened until the dryer runs for
some time because it takes time for the dryer to establish sufficient
cooling temperature and the compressed air going through the dryer
at this moment can't have excellent drying effect.

-8-
Temperature Range of Dew Point
According to ISO 8573.1, dew point
temperature of a freezing dryer is based
on2-10 ,astheblue area between
two dotted lines shown in the figure on
the right.
blue area
Special Situation
When the dryer starts to run without any load
or at a lower environment temperature, the
dew point temperature of the freezing dryer
might not be within the blue area (at a lower
position). The cooling fan may stop shortly
and will begin to run after the temperature
rises within the range of the blue area, which
is normal to prevent from icing and freezing.
Stop
1. Close the valve gates of air inlet and outlet and check if
the bypass pipes are tightened.
2. When the power switch is placed
on "O", the dryer stops to run.
Shut off the valve gates of air inlet and outlet before stopping the
dryer so that compressed air may continue flowing through the dryer
and get the expected drying effect after the dryer stops.
Do not turn on and off the power switch consecutively to prevent
damage to the refrigerant compressor.
power switch overload trip
dew point temperature
dew point temperature
at a lower position
power switch

Daily Maintenance
-9-
1. Check the automatic water drainer (Fig. 1) every day for any blocking or
leakage. When obstruction is spotted, remove the water drainer right
away by disassembling parts like the internal filter net, the ballcock and
the acrylic cup, etc. Use soap water or neutral detergent to clean. Erosive
solvents like petroleum, toluene and rosin, etc. are forbidden.
2. Check if the condenser and the fin of the pre-cooler are clean to ensure
best heat release for the dryer.
3. Use an air spray gun and a brush (Fig. 2) to clean the condenser and the
fin of the pre-cooler. Pay attention not to deform the fin.
The major function of the automatic water drainer is to remove cooled
and precipitated moisture out of the air system. Blocking of the dryer
will lose such function.
To stabilize the drying effect and avoid tripping or failures, ensure to
keep the condenser and the fin of the pre-cooler clean.
Fig. 2
Fig. 1
filter net
metal cup
acrylic cup
condenser
Daily Maintenance
-9-
1. Check the automatic water drainer (Fig. 1) every day for any blocking or
leakage. When obstruction is spotted, remove the water drainer right
away by disassembling parts like the internal filter net, the ballcock and
the acrylic cup, etc. Use soap water or neutral detergent to clean. Erosive
solvents like petroleum, toluene and rosin, etc. are forbidden.
2. Check if the condenser and the fin of the pre-cooler are clean to ensure
best heat release for the dryer.
3. Use an air spray gun and a brush (Fig. 2) to clean the condenser and the
fin of the pre-cooler. Pay attention not to deform the fin.
The major function of the automatic water drainer is to remove cooled
and precipitated moisture out of the air system. Blocking of the dryer
will lose such function.
To stabilize the drying effect and avoid tripping or failures, ensure to
keep the condenser and the fin of the pre-cooler clean.
Fig. 2
Fig. 1
filter net
metal cup
acrylic cup
condenser

Protection Device And Troubleshooting
1. Protection Device for control substrate Fuse (250V/3A)
When over-high voltage is input or the part on the substrate
breaks down, this fuse will be melted to prevent elements at
rear like the compressor from being damaged.
2. Protection Device for Fan Motor Fuse (250V/3A)
When the cooling fan motor breaks down to cause excessive
current, this fuse will be melted to avoid electric hazards.
3. Protection Device for Freezing System Temperature Sensor
When the freezing system is lack of maintenance or the refrigerant
leaks, backflow temperature will become too high and cause the
compressor to overheat. Thus, the compressor can be stopped
opportunely by the temperature sensor.
4. Protection Device for Compressor Current Sensor
The current sensor can detect operation status of the compressor
when the dryer is running. In case of over-current, the compressor
will be stopped at once.
Protection Device
Troubleshooting
1. Can't start
Failure Possible Reason Resolution
Power switch trips or breaks down. Check power switch and make sure if voltage is normal.
Abnormal power supply
causes the fuse of the control
substrate to melt.
Supply power of 5% of rated voltage in accordance
with the nameplate and replace the fuse.
Control substrate breaks down. Replace a new one.
Overload trip
indicator on
Condenser is blocked. Remove dust or impurities out of the surface of the fin in
compliance with service instructions.
Cooling fan breaks down to
cause the fuse of the fan to melt.
Replace a fan motor and a fuse.
Refrigerant leaks. Vacuum after repair and re-fill refrigerant.
Rated environment temperature
exceeds.
When ambient temperature is over 40 , relocate the
equipment or add ventilation facilities.
No display
-10-

-11-
Failure Possible Reason Resolution
Overload trip indicator on
Abnormal power supply Supply power of 5% of rated voltage in accordance with
the nameplate.
Rated air flow exceeds. Increase dryer equipment.
Refrigerant system is blocked. Replace the dryer and capillary. Vacuum and re-fill
refrigerant.
Compressor malfunctions. Replace a new compressor.
1. Can't start
2. Normal operation but bad dewatering effect
Failure Possible Reason Resolution
Abnormal water
draining system
Filter net is blocked. Clean or replace in accordance with service instructions.
Control valve not open. Open the control valve for water draining.
Dryer is placed unevenly. Reinstall the dryer on even grounds.
Improper operation
or pipe design
Bypass pipes not closed
completely Close tight valve gates of bypass pipes.
Wrong installation of air inlet and
outlet Reinstall the pipes of air inlet and outlet.
Rated environment temperature
exceeds.
When ambient temperature is over 40 , relocate the
equipment or add ventilation facilities.
Compressed air does not go
through the dryer.
Check the installed pipes.
Rated requirements
not met
Rated air flow exceeds. Increase dryer equipment.
3. Extreme pressure drop
Failure Possible Reason Resolution
Improper operation Valve gates of inlet and outlet
not open completely Open valve gate.
Filter in the pipe is blocked. Replace the filter element.
Rated requirements
not met
Diameter of air pipes too small Increase the diameter and re-pipe.
Bad design of air
pipes
Rated air flow exceeds. Increase dryer equipment.
Joint where air pipes connect leaks.
4. After-sale service
When the dryer malfunctions, comply with the failure, possible reason and resolution in the
above table. Do not conduct maintenance or repair if the cause of the problem is not confirmed.
Contact the manufacturer from whom the dryer was purchased and inform them the following
items:
Part To Be Purchased for Replacement
1. Model number and manufacturing number of the
product
2. Symptoms and possible reasons of failure
3. Address, phone number and contact person
1. Model number and manufacturing number of the
product
2. Name and quantity of the required part
3. Address, phone number and contact person
Notification Items for Dryer Failure
Reinstall at places where leak occurs.

Appendix 1: Drawing of Purification Equipment Application
0.01 0.003
0.01
1
By pass
Freezing dryer
Air compressor
Fast drilling, general coating,
planned packaging
Cleaning, shipping, tooling,
cutting processing
-12-
5
Air tank
Foods, medicine processing,
precision coating

Drawing of Electric Wires
Temperature sensor
AD-005~AD-020
Control board
Variable voltage
A Blue
B Brown
C Red
1234567
-13-
Switch
Starting
capacitor
Current starter
Overload
Alarm
Compressor
Fan
Optional
Variable voltage
380~460V to 220V
D
D White
E Black
A
D
A
ABCDEDE
2
4
1
3
E
B
EB
L
N
PE

L
N
PE
E
E
E
Optional
Variable voltage
380~460V to 220V
MC
B
D
A
D
AD-030~AD-060
Temperature sensor
Control board
Variable
voltage
1234567
A Blue
B Brown
-14-
EBGF
F
95 97 A1
MC
96 98 A2
E
E
B
DAC D
D
A
E
Fan
Thermal
Relay
BOverload
A
E
5
4
2
1
Voltage starter
Running
capacitor
Compressor Switch Alarm
Starting
capacitor
D
C Red
D White
E Black
F Yellow
G Orange

CD
Switch
E
BGD
AC
Variable voltage
AD-075S~AD-400S Control board
Variable voltage
12345
DA
EB
S
R
T
PE A Blue
B Brown
C Red
D White
E Black
F Yellow
G Orange
-15-
CD
EE
DD
Set 40
Temperature
Switches
Fan
Compressor Fan Thermal
Relay
Alarm
Running
E
1
3
5
4
2
6
95 97
A1
A1
MF
MC
96 98
A2
A2
F
EF
Optional
380~460V to 220V
MC MF
D
D
A
E
B
E

Footnote
-16-

Footnote
-17-

Footnote
-18-

This manual suits for next models
14
Table of contents
Popular Dehumidifier manuals by other brands

Mitsubishi Electric
Mitsubishi Electric MJ-E130AL-H instruction manual
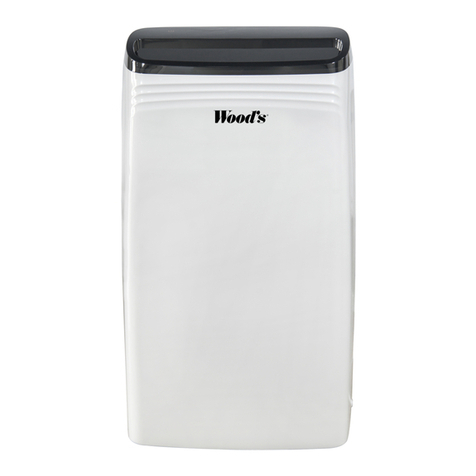
Wood’s
Wood’s MDK21 operating instructions
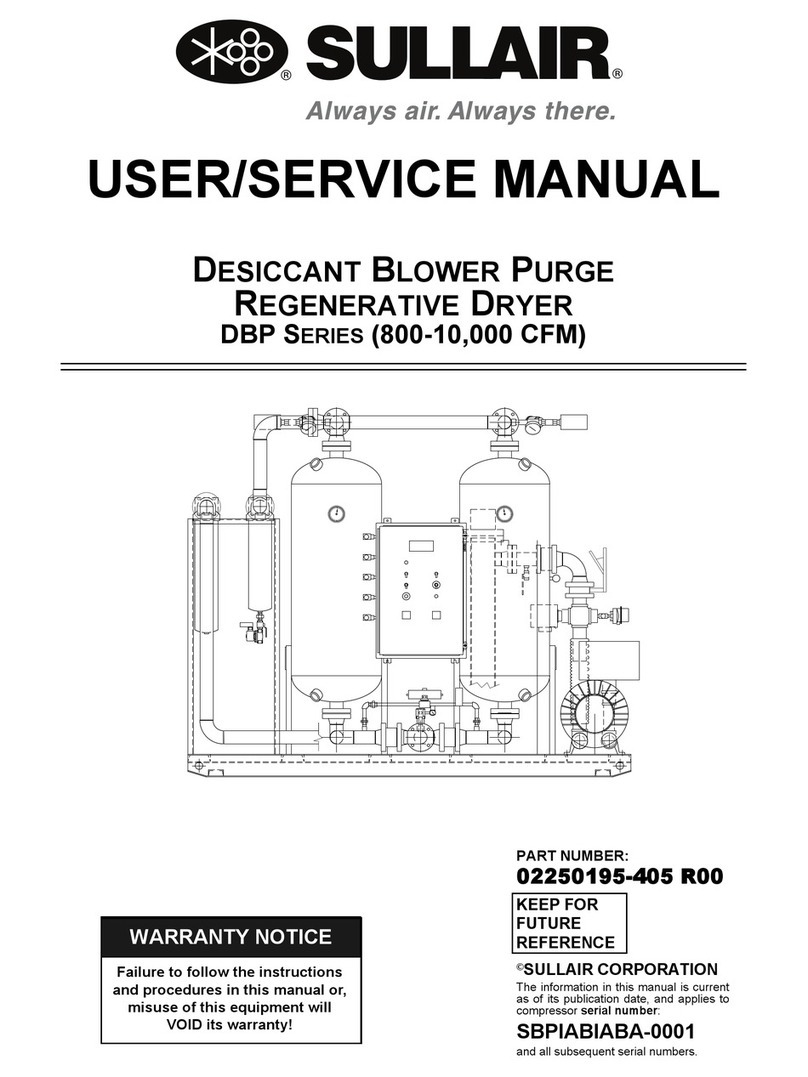
Sullair
Sullair DBP Series User & service manual

Healthy Climate Solutions
Healthy Climate Solutions HCWHD4-080 owner's manual
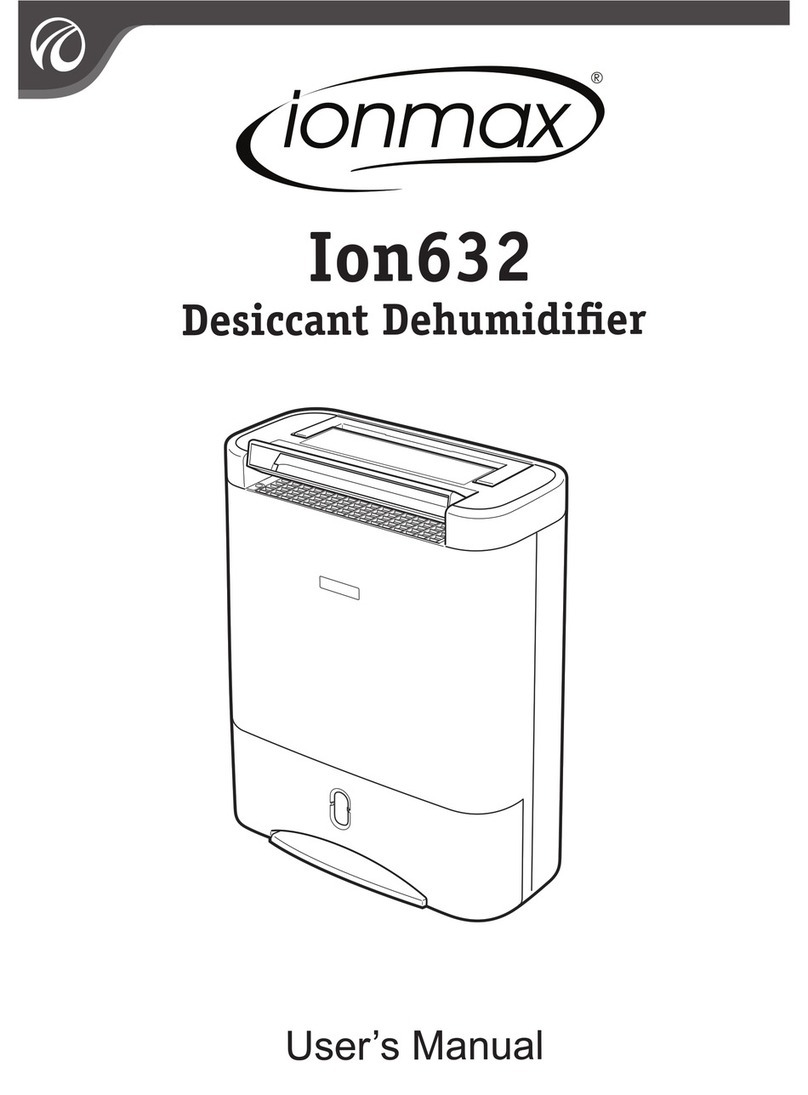
ionmax
ionmax Ion632 user manual
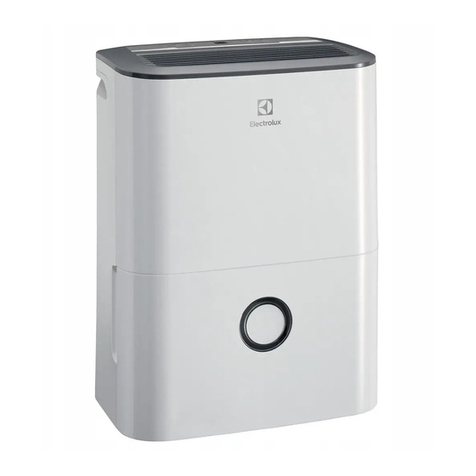
Electrolux
Electrolux EXD16DN4W user manual