Toshiba 48-1250 A User manual

INSTRUCTION MANUAL
TD SERIES
Low Voltage
Digital Solid State Starter
48 - 1250 A
Issued: 9/03
Manufactured in the USA
INSTALLATION - OPERATION - MAINTENANCE
DOCUMENT: NBZ0001


SAFETY
WARNING
SAFETY CODES
Toshiba motor control is designed and built in accordance with the latest applicable provisions of
NEMA and the National Electrical Code. Installations must comply with all applicable state and local
codes, adhere to all applicable National Electric Code (NFPA 70) standards and instructions provided
in this manual.
HAZARDOUS VOLTAGE will cause severe injury, death, fire, explosion and
property damage.
• Turn off and lock out Primary and Control Circuit Power before servicing.
• Keep all panels and covers securely in place.
• Never Defeat, Modify, or Bypass any Safety Interlocks.
• Qualified Operators only.
Never attempt to install, operate, maintain or dispose of this equipment until
you have first read and understood all of the relevant product warnings and
user directions that are contained in this Instruction Manual.
Use only Toshiba-authorized replacement parts.
This equipment is designed and built in accordance with applicable safety
standards in effect on the date of manufacture. Unauthorized modifications
can result in voiding the warranty, severe injury, death and property
damage. Do not make any modifications to this equipment without
the written approval of Toshiba.
For assistance, address correspondence to:
Toshiba International Corporation
Field Service Department
13131 West Little York Road
Houston, Texas 77041 USA
or call: (713) 466-0277 Fax: (713) 466-8773
(800) 231-1412
(800) 527-1204 (Canada)
Please complete the following information for your records and retain with this manual:
Model: ___________________________________
Serial Number: _____________________________
Date of Installation: _________________________
Inspected by: ______________________________
Reference Number: _________________________
© TOSHIBA INTERNATIONAL CORPORATION, 2003

SAFETY
DANGE
R
WARNING
CAUTION
IMPORTANT MESSAGES
Read this manual and follow its intructions. Signal words such as DANGER, WARNING
and CAUTION will be followed by important safety information that must be carefully reviewed.
Indicates a situation which will result in death, serious injury, and severe property damage if you
do not follow instructions.
Means that you might be seriously injured or killed if you do not follow instructions. Severe
property damage might also occur.
Means that you might be injured if you do not follow instructions. Equipment damage might
also occur.
Give you helpful information.
NOTE
READ SAFETY SIGNS
To avoid injury, you must read and follow all safety signs.
Keep the safety signs visible and in good shape. Never remove or cover any safety sign.
DANGE
R
QUALIFIED OPERATORS ONLY
Only qualified persons are to install, operate, or service this equipment according to all applicable
codes and established safety practices.
A qualified person must:
1) Carefully read the entire instruction manual.
2) Be skilled in the installation, construction or operation of the equipment and aware of
the hazards involved.
3) Be trained and authorized to safely energize, de-energize, clear, ground, lockout and
tag circuits in accordance with established safety practices.
4) Be trained and authorized to perform the service, maintenance or repair of this equip-
ment.
5) Be trained in the proper care and use of protective equipment such as rubber gloves,
hard hat, safety glasses, face shield, flash clothing, etc. in accordance with estab-
lished practices.
6) Be trained in rendering first aid.
Note: The contents of this manual will not become a part of or modify the warranty
policy, the terms of which are set forth at the end of this manual.

TD Series
Digital Solid State Soft Starter
48 - 1250A
Chapter 1: Introduction .....................................................1
1.1 General
1.2 Specifications and Performance Features
Chapter 2: Installation .......................................................4
2.1 Receiving and Unpacking
2.2 Location
2.3 Initial Unit Inspection
2.4 Warning
2.5 Mounting and Cleaning
2.6 Power Terminal Wire Range and Tightening Torque
2.7 Dimensions
Chapter 3: Motor Overload Protection ...........................7
3.1 Solid State Overload Protection
3.2 NEMA Class Trip Curves
Chapter 4: Connections ..................................................10
4.1 Power Connections
4.2 Control Connections
4.3 Interlock Connection
Chapter 5: Programming ................................................13
5.1 Introduction
5.2 Digital Interface
5.3 Display Modes
5.4 Function List
5.5 Function Descriptions
Chapter 6: Start-Up..........................................................32
6.1 Quick Start
6.2 Start-up Check List
6.3 Sequence of Operation
Chapter 7: Fault Conditions ...........................................35
7.1 Fault Codes and Numbers (In History)
Chapter 8: Troubleshooting ...........................................36
8.1 Failure Analysis
8.2 SCR Testing Procedure
8.3 Replacing SCR Devices
8.4 Replacing Printed Circuit Board Assembly
Chapter 9: Printed Circuit Board Layout .......................41
9.1 Power Board and CPU Board (PC Board Assembly)
9.2 Typical Wiriing Diagram
Chapter 10: Maintenance/Disposal/Storage .................43
Appendix 1: Ramp Profile Details
Appendix 2: Decel Mode Application Considerations
Appendix 3: Parameter Lock / User Password Instructions
Appendix 4: Soft Starter Settings
Warranty Policy
Table of Contents


TD - Series
- 1 -
TD Series Digital Solid State Soft Starter 48 - 1250A
1.1 General
The TD Series is a digitally programmable solid state reduced voltage
soft starter. Its six SCR design features a voltage/current ramp with an
anti-oscillation circuit for smooth load acceleration. The SCRs are sized
to withstand starting currents of 500% for 60 seconds (compared to
350% for 30 seconds from other manufacturers). The TD Series features
smooth, stepless ramp control which reduces motor inrush current and
excessive wear on the mechanical drive train components. In addition to
having easy to understand diagnostic LEDs, the TD Series includes a
programmable keypad for setting operating parameters for the ideal
starting cycle. Starting torque, ramp time, current limit, dual ramp, and
decel control are standard features on the TD Series. By simply adjusting
the unit’s starting torque, ramp time and current limit functions, the starting
electrical characteristics of the motor can be matched to the mechanical
characteristics of the drive train for controlled acceleration of the load.
The TD Series includes solid state electronic overload protection in
addition to numerous other protective features. It is factory wired for 120
VAC control voltage and two or three-wire start/stop control (Units can
also be ordered with 240 VAC control voltage if required). Programmable
auxiliary contacts and provisions for interlocking are also included.
Chapter 1 - Introduction
1.2 Specifications and Performance Features
Type of Load Three phase AC induction motor
AC Supply Voltage 208 - 600VAC ±10%, 50/60 Hz
HP Ratings 48 - 1250 Amps, 10 - 1125 HP
Unit Overload Capacity
(Percent of motor FLA)
125% - Continuous
500% - 60 seconds
600% - 30 seconds
Power Circuit 6 SCRs
SCR Diode Ratings
(Peak Inverse Voltage) 1600V
Phase Insensitivity Unit operates with any phase sequence
Transient Voltage Protection RC snubber dv/dt networks on each phase.
Cooling Convection up to 180A, fan assisted 62 - 120A,
Fan ventilated 220 - 1250A
Bypass Contactor
Full horsepower rated contactor included as standard in all
Type 12, 3R, 4 & 4X enclosed units 120A and above.
Ambient Condition Design
Chassis units: 0° to 50 °C (32° to 122°F)
Enclosed units: 0° to 40°C (32° to 104°F)
5 - 95% relative humidity
0 - 3300 ft. (1000m) above sea level without derating
Control 2 or 3 wire 120VAC (customer supplied)
Optional 240VAC control voltage and CPTs are available.
Type / Rating: Form C (SPDT), rated 5 Amps,
240VAC max. (1200VA)
3 Programmable Relays
Fault Indicator: AC triac solid state switch
240VAC, 50mA max.
Approvals UL Listed, Canadian UL (cUL) Listed
Auxiliary Contacts

TD - Series
- 2 -
TD Series Digital Solid State Soft Starter 48 - 1250A
1.2 Specifications and Performance Features Cont’d
Note 1: Enabled via programming
Two Stage Electronic
Overload Curves
Starting: Programmable for Class 5 through 30
Run: Programmable for Class 5 through 30 when "At-Speed"
is detected.
Overload Reset (Note 1) Manual (default) or automatic
Retentive Thermal Memory
Overload circuit retains thermal condition of the motor
regardless of control power status. Unit uses real time clock
to adjust for off time.
Dynamic Reset Capacity
Overload will not reset until thermal capacity available in the
motor is enough for a successful restart. Starter learns and
retains this information by monitoring previous successful
starts.
Phase Current Imbalance
Protection (Note1)
Imbalance Trip Level: 5 - 30% current
between any two phases
Imbalance Trip Delay: 1 -20 seconds
OverCurrent
(Electronic Shear Pin)
Protection (Note 1)
Trip Level: 50 - 300% of motor FLA
Trip Delay: 1 - 20 seconds
Load Loss Trip Protection
(Note 1)
Under Current Trip Level: 10 -90 % of motor FLA
Under Current Trip Delay: 1 - 60 seconds
Coast Down (Back Spin)
Lockout Timer (Note 1) Coast Down Time Range: 1 - 60 minutes
Starts-per-hour Lockout Timer
(Note 1)
Range: 1 - 10 successful starts per hour
Time between starts: 1 - 60 minutes between start attempts
Type / Rating Form C (SPST), Rated 5 amps
240 VAC max, (1200 VA)
Run Indication Start/Stop or Start/End of Decel
At Speed Indication At Speed/Stop or At Speed/End of Decel
Acceleration Adjustments
Programmable Ramp Types: Voltage or Current Ramp
(VR or CR)
Starting Torque: 0 - 100% of line voltage (VR)
or 0 - 600% of motor FLA (CR)
Ramp Time: 1 to 120 seconds
Current Limit: 200 - 600% (VR or CR)
Dual Ramp Settings
4 Options: VR1+VR2; VR1+CR2; CR1+CR2; CR1+VR2
Dual Ramp Control: Ramp #1 = Default,
Ramp = #2 selectable via dry contact input
Deceleration Adjustments
Begin Decel Level: 0 - 100% of line voltage
Stop Level: 0 to 1% less than Begin Decel Level
Decel Time: 1 - 60 seconds
Programmable to decel or coast to stop upon overload trip
Jog Settings
Jog function selected via
dry contact closure input)
Voltage Jog: 5 - 100%
Time of Voltage Jog: 1 - 20 seconds
Current Jog: 100 - 500%
Kick Start Settings
(Note 1)
Kick Voltage: 10 - 100%
Kick Time: 0.1 - 2 seconds
Fault Indications
Shorted SCR, Phase Loss, Shunt Trip, Phase Imbalance
Trip, Overload, Overtemp, Overcurrent, Short Circuit, Load
Loss, or Any Trip
Lockout Indicator Coast Down Time, Starts Per Hour,
Time Between Starts, and Any Lockout
Programmable Outputs
Advanced Motor Protection

TD - Series
- 3 -
TD Series Digital Solid State Soft Starter 48 - 1250A
1.2 Specifications and Performance Features Cont’d
Phase Currents 0 - 9999 Amps, Phase A, B, or C
Remaining Thermal Capacity 0 - 100% of available motor thermal capacity
Elapsed Time 0 - 1,000,000.0 hours, non resetable
Run Cycle Counter 0 - 10,000,000 run commands non resetable
Lockout Time Values Remaining time of any enabled lockout timer
Fault Codes Abbreviated fault codes, indicating trip and operating mode
Fault History Last 3 faults with Time and Date Stamps
Protocol Modbus RTU
Signal RS-485
Network Up to 247 devices per mode
Functionality Full operation, status view, and programming
via communications port
LED Readout 4 digit alpha numeric, high brightness, 7 segment display
Keypad 8 functions keys with tactile feedback
Status Indicators 8 LEDs
Remote Mount Capability Up to 10 feet (3 meters) from chassis
Operating Memory DRAM loaded from EPROM and EEPROM at initialization
Factory Default Storage Flash EPROM, field replaceable
Customer Settings and Status Non-volatile EEPROM, no battery backup necessary
Real Time Clock Lithium ion battery for clock memory only,
10+ years life span
Operator Interface
Clock and Memory
Metering Functions
Serial Communications

TD - Series
- 4 -
TD Series Digital Solid State Soft Starter 48 - 1250A
2.1 Receiving and Unpacking
Upon receipt of the product you should immediately do the following:
•Carefully unpack the unit from the shipping carton and inspect it for
shipping damage (if damaged, notify the freight carrier and file a
claim within 15 days of receipt).
•Verify that the model number on the unit matches your purchase
order.
•Confirm that the ratings sticker on the unit matches or is greater
than the motor’s HP and current rating.
2.2 Location
Proper location of the TD Series is necessary to achieve specified
performance and normal operation lifetime. The TD Series should
always be installed in an area where the following conditions exist:
•Ambient operating temperature:
Chassis unit: 0 to 50°C (32 to 122°F)
Enclosed unit: 0 to 40°C (32 to 104°F)
•Protected from rain and moisture
•Humidity: 5 to 95% non-condensing
•Free from metallic particles, conductive dust and corrosive gas
•Free from excessive vibration (below 0.5G)
•Open panel units must be mounted in the appropriate type of
enclosure. Enclosure size and type must be suitable to dissipate
heat generated by the soft starter. Contact factory for assistance in
sizing enclosures.
2.3 Initial Unit Inspection
• Make a complete visual check of the unit for damage which may
have occurred during shipping and handling. Do not attempt to continue
installation or start up the unit if it is damaged.
• Check for loose mechanical assemblies or broken wires which may
have occurred during transportation or handling. Loose electrical
connections will increase resistance and cause the unit to function
improperly.
• Prior to beginning the installation, verify that the motor and TD unit
are rated for the proper amperage and voltage.
2.4 Warning!
Do not service equipment with voltage applied! The unit can be
the source of fatal electrical shocks! To avoid shock hazard,
disconnect main power and control power before working on
the unit. Warning labels must be attached to terminals, enclosure
and control panel to meet local codes.
Chapter 2 - Installation
WARNING

TD - Series
- 5 -
TD Series Digital Solid State Soft Starter 48 - 1250A
2.5 Mounting and Cleaning
Whendrillingorpunchingholesintheenclosure,covertheelectricalassembly
to prevent metal filings from becoming lodged in areas which can cause
clearancereductionoractuallyshortoutelectronics.Afterworkiscomplete,
thoroughlycleanthe area and reinspect the unitforforeignmaterial.Make
surethere issufficientclearance (sixinches)all aroundtheunit forcooling,
wiringandmaintenancepurposes.Tomaximizeeffectiveairflowandcooling,
theunitmustbeinstalledwithitsheatsinkribsorientedverticallyandrunning
paralleltothemountingsurface.
Remove all sources of power before cleaning the unit.
Indirtyorcontaminatedatmospherestheunitshouldbecleanedonaregular
basisto ensurepropercooling.Do notuseanychemicals tocleanthe unit.
Toremovesurfacedustuse80to100psi,clean,drycompressedaironly.A
threeinch, high quality,dry paintbrushishelpfulto loosenupthedustprior
to using compressed air on the unit.
2.6 Power Terminal Wire Range and Tightening Torque
Note: All wiring must be sized according to NEC standards.
WARNING
Model Number Wire range Torque lbs/in
TD005 #18 - #4 20
TD006 #14 - #2 50
TD007
TD008
TD009
TD010
TD011
TD012
TD013
TD014
TD015
TD016
TD017
#6 - 250 kcmil 325
375(3) #2 - 600 kcmil
375(2) #2 - 600 kcmil
375(2) #2 - 600 kcmil
(4) #2 - 600 kcmil 375

TD - Series
- 6 -
TD Series Digital Solid State Soft Starter 48 - 1250A
2.7 Dimensions
TD CHASSIS (PANEL MOUNT) DIMENSIONS
Overall Dimensions Mounting Dimensions
Model Number (inches) (inches)
AB CDEF
TD005A - TD007A 16.5 10 10 15.9 9 0.28
TD008A 20 20.1 12 18.5 17.5 0.44
TD009A - TD010A 27 20.1 11.2 25.5 17.5 0.44
TD011A - TD013A 29.5 20.1 11.5 25.5 17.5 0.44
TD014A - TD015A 45 33 12.8 43.3 31.3 0.44
TD016A - TD017A 33 33 15.2 31.2 31.2 0.44

TD - Series
- 7 -
TD Series Digital Solid State Soft Starter 48 - 1250A
Chapter 3 - Motor Overload Protection
3.1 Solid State Overload Protection
The TD Series Starter provides true U.L. listed I2T Thermal Overload Protection
as a built-in function of the main digital processor. For maximum protection it
simulates the tripping action of a bimetallic overload relay, with the accuracy and
repeatability of a digital control system, yet is adjustable over a wide range and
can be easily programmed for different trip curves.
3.1.1 Thermal Memory
The TD Series microprocessor uses a sophisticated “Thermal Register” to keep
track of motor heating and cooling over time regardless of the starter’s power
status. The TD Series does not “forget” that the motor has been running even if
power to the starter is turned off and back on. Continuous overload protection is
provided based on the true thermal condition of the motor.
3.1.2 Thermal Capacity
The Thermal Register is displayed as a percentage. This percentage is the motor’s
remaining thermal capacity. The percentage value begins at 100, showing that
the motor is cool. As the motor heats up or moves toward an overload condition,
the percentage begins to drop. The Thermal Capacity is derived from the
programmed motor nameplate Full Load Amps (FLA) in Function F001, the Service
Factor rating in Function F002, and the Overload Trip Class in Functions F003
and F004. Setting these functions to the proper values will provide maximum
protection yet eliminates nuisance tripping.
3.1.2.a Motor Full Load (FLA) Setting
Use Function F001 to enter motor FLA as indicated on the motor nameplate. (Do
not calculate for service factor, this is programmed separately in F002).
Note: If F001 is left at the factory default, the unit will not operate. If the
user attempts to start the TD without entering the motor nameplate
FLA into this Function, the TD will Fault, and the display will read
“nFLA” (for no Full Load Amps).
3.1.3 Disabling the Overload Protection
The Overload Protection feature can be disabled if absolutely necessary. When
using external devices such as Motor Protection Relays or when the TD Series
is wired downstream from an existing starter, this feature can be disabled to
prevent conflicts with external overload protection devices. When the TD Series
is controlling multiple motors, Overload Protection must be disabled. Individual
thermal overload relays must be installed on the motor leads going to each
motor. To disable the Overload Protection function, use F005. (See Section 5.)
Do NOT disable Overload Protection unless another Thermal Overload
Protection device exists in the circuit for all three phases. Running a
motor without Overload Protection presents serious risk of motor damage
or fire.
3.1.3.a Manual Reset
The factory default setting is Manual Reset. This means that when the Overload
Trip is activated, the starter cannot be restarted without pressing the Reset key.
The Overload Trip will not reset until the motor cools down. The Manual Reset
function is also “trip free”. Holding in the Reset key will not prevent the Overload
Trip from activating and protecting the motor.
Note: When the Overload Trip activates, the Overload LED will glow
solid. When the motor cools down, the LED will begin to flash,
indicating that the Overload Trip can be reset.
WARNING

TD - Series
- 8 -
TD Series Digital Solid State Soft Starter 48 - 1250A
3.1.3.b Automatic Reset
If Automatic Reset is necessary, change from Manual Reset toAutomatic Reset
by using Function F005. (See Section 5 for details). In this mode, a 3-wire control
circuit will be capable of restart when the TD Series has reset itself after the cool
down period.
Two-wire control systems may restart without warning when Auto Reset
is selected. Extreme caution should be exercised. To prevent automatic
restarting with two-wire control systems, use external interlocking to
provide sufficient warning and safety to operators. A Warning Label (such
as the one provided in the packet with this manual) must be placed to be
visible on the starter enclosure and/or the equipment as required by local
code.
3.2 NEMA Class Trip Curves
The TD Series Soft Starter provides six NEMA Class trip curve options: 5, 10,
15, 20, 25, and 30. Program the appropriate curve according to the characteristics
of your motor and load.
NEMA Class trip curves are based on a common tripping point of 600% of rated
current. Curves vary by the amount of time before the unit trips. As an example,
a Class 20 curve will trip in 20 seconds at 600%. The factory default setting of
Class 10 will trip in 10 seconds at 600%.
3.2.1 Dual Overload Trip Curves
The TD Series Soft Starter provides two separate Overload Trip Protection Curves,
one for starting and one for running conditions. Programming a higher NEMA
Class overload during start (ramp-up) will eliminate nuisance tripping in higher
inertia or high friction loads.
The starter’s At-Speed detection circuit determines when the motor has reached
full speed based on closed loop feedback signals. When the At-Speed condition
is reached, the overload trip curve will shift from the Start to the Run level, as
programmed in Functions F003 and F004. See Section 5 for programming details.
MOTOR CONNECTED TO THIS EQUIPMENT MAY
START AUTOMATICALLY WITHOUT WARNING
WARNING

TD - Series
- 9 -
TD Series Digital Solid State Soft Starter 48 - 1250A
Note: Factory default setting is Class 10 for both Start and Run Overload Protection
C
lass
30
C
l
ass
2
5
C
l
ass
2
0
C
l
ass
1
5
C
l
ass
1
0
C
l
ass
5
MFLA
Tim
e
in
Seco
n
ds
TD Series
Overload Trip Curves

TD - Series
- 10 -
TD Series Digital Solid State Soft Starter 48 - 1250A
4.1 Power Connections
Connect appropriate power lines to the unit input terminals marked L1, L2, L3.
Avoid routing power wires near the control board. Connect the motor leads to the
unit terminals marked T1, T2, T3. Refer to NEC standards for wire length and
sizing. Never interchange input and output connections to the unit. This could
cause excessive voltage in the control logic circuit and may damage the unit.
Never connect power factor correction capacitors on the load side of the
unit. The SCRs will be seriously damaged if capacitors are located on
the load side.
The unit cannot be tested without a motor or other test load connected to the
load side of the unit. It may be necessary to use a load bank to test the unit
without a motor. Note that line voltage will appear across the output terminals if
there is no motor or load connected to the unit. In areas where lightning is a
significant problem, stationary air gap lightning arrestors should be considered
and utilized on the input power source.
TD Series Unit
Power Connections
4.1.1 Grounding
Connect the ground cable to the ground terminal as labeled on the unit. Refer to
the National Electrical Code for the proper ground wire sizing and be sure that
the ground connector is connected to earth ground.
4.2 Control Connections
4.2.1 Control Power Connections
Separate 120VAC supply is required (order 240 VAC if required). The control
voltage should be connected to pins 1 and 6 of TB1. This control voltage must be
customer supplied, unless an optional control power transformer has been supplied
with the unit. The terminal block TB1 is located on the main power board.
However, on units rated 150 Amps and above, TB1 us brought out to a duplicate
terminal block on the back panel assembly.
TB1
Chapter 4 - Connections
120V
Control
Power
120V
Control
Power
Return
Unit comes standard with
120VAC control. Order 240VAC
control as an option if required.
WARNING

TD - Series
- 11 -
TD Series Digital Solid State Soft Starter 48 - 1250A
For standard 3-wire control connect 120VAC to pins 1 and 6 of TB1. Connect
N.C. (normally closed) stop button between pins 3 and 4 of TB1. Connect N.O.
(normally open) start button between pins 4 and 5 of terminal block TB1.
4.2.3 Two-Wire Connection
An alternate connection for unattended operation replaces start/stop push buttons
by connecting a maintained contact closure between pins 3 and 5 on TB1. When
the maintained contact is used for start/stop it is necessary to set the overload
relay to the manual reset position. This will prevent the motor from restarting if
the thermal overload trips and then cools off.
When two-wire connection method is used, the user’s control circuit
must be interlocked to prevent automatic restart when protective
devices reset. Refer to section 3.1.3.b.
4.2.4 Relay Contacts
All the relay contacts are FORM C common (N.O., N.C.), except the optical
triac output. TOSHIBA recommends fusing all contacts with external fuses. TB2
is the terminal block for all auxiliary contacts. Each contact is explained in the
following sections. See Chapter 9 for main control board layout.
4.2.5 Programmable Relays
Three programmable relays are on TB2 which is located on the main control
board. The relays are rated for 240 VAC, 5 A and 1200 VA.
Factory settings for these relays are:
AUX 1 - Run / Stop (F050 = 1)
AUX 2 - At Speed / Stop (F051 = 2)
AUX 3 - Any Trip (F052 = 14)
Two-Wire Connection
TB1
Three-Wire Connection
TB1
4.2.2 Three-Wire Connection
WARNING

TD - Series
- 12 -
TD Series Digital Solid State Soft Starter 48 - 1250A
4.2.6 Fault Signal
An optical AC switch triac driver is used for fault indication. This signal energizes
with the fault LED. The optical output is rated for 240 VAC, 50 mA (maximum).
4.2.7 Resetting Faults
To reset faults, press the RESET key on the keypad.
4.2.8 Enabling the Jog Function
Closing TB4 Pins 1 and 2 will enable the Jog feature. The Jog feature can be
used for tasks such as lining up machines for blade or bit changes or inching
belts along to check tracking. See chapter 9 for main control board layout.
4.2.9 Enabling the Dual Ramp Feature
Closing TB4 Pins 1 and 3 will enable ramp 2. The dual ramp feature is useful in
instances where a load changes such as a loaded or unloaded conveyor belt.
The characteristics for starting an unloaded conveyor can be programmed for
ramp 1. The characteristics for starting a loaded conveyor can be programmed
for ramp 2.
4.3 Interlock Connection
TB1 provides a connection point for an external user N.C. (normally closed)
interlock device between pins 2 and 3. (Examples of the use of this interlock
connection would be for conditions such as low oil, high temperature, or excess
vibration from user supplied devices).
A factory installed jumper is provided which allows the TD unit to operate if
external interlocks are not used. If this jumper is removed and an interlock is not
used, the TD unit will not function.
1 2 3
TB4
Common Dual
Ramp
1 2 3
TB4
Common Jog
123456
TB1
Interlock
12345678910
C NO NC C NO NC C NO NC
TB2
240Vac
50mA240Vac / 5A / 1200VA
AUX 3
Fn F051 Fn F052
Optical Triac
Driver
AUX 1
Fn F050
AUX 2
11 12
Programmable
Relay
Programmable Programmable
Relay Relay
Fault
Signal

TD - Series
- 13 -
TD Series Digital Solid State Soft Starter 48 - 1250A
5.1 Introduction
It is best to operate the motor at its full load starting condition to achieve the
proper time, torque and ramp settings. Initial factory settings are set to
accommodate general motor applications and provide basic motor protection.
Advanced features must be enabled via programming. The only parameter that
MUST be set by the user is motor FLA (F001).
5.2 Digital Interface
The TD Soft Starter includes an intuitive, digital keypad with eight LEDs, seven
command keys, and an LED display with four alphanumeric digits.
Chapter 5 - Programming
MOTOR FLA (F001)
must be programmed
for unit to operate.
Reset Clears the trip indicator and releases the trip relay.
Fn Enters or exits the program mode.
Up Arrow
Navigates through the Status Display Mode, scrolls up through the list
of functions, increases the value of an active (flashing) digit, and scrolls
through the history of fault conditions.
Right Arrow Each keypress shifts the active (flashing) digit to the right one position,
use to change function number or value.
Down Arrow
Navigates through the Status Display Mode, scrolls down through the
list of functions, decreases the value of an active (flashing) digit, and
scrolls through the history of fault conditions.
Left Arrow Each keypress shifts the flashing digit to the left one position, use to
change function number or value.
Read Enter Selects and stores the value of a function.
Power On Control power is present.
At Speed Motor is at full speed and power.
(The SCRs have phased fully on.)
Shorted SCR Shorted SCR has been detected in the unit. Refer to section 8.2 for
instructions on checking SCRs.
Phase Loss One or more of the phase currents is low or has been lost while the
motor was starting or running.
Over Temp Motor starter has tripped due to heat sink over temperature.
Over Load Starter's motor overload has tripped. The overload must be reset
before the fault can be cleared
Display 8888 4 digit 7 segment display
Keys
Green
LEDs
Two or more power poles are shorted and current is passing to the
motor while in the off mode. For positive motor protection, an auxiliary
relay should be be programmed for "Shunt Trip" and should be
interlocked with a shunt trip breaker or in-line contactor. (In the event o
f
a shunt trip, do not re-power the unit without repairing the power poles.)
Over Current
Over Current LED illuminates for two sets of fault conditions: over
current and short circuit.
If unit experiences output current (of any phase) in excess of the value
programmed in F034 (over current trip %) for the time period specified
in F035 (over current trip delay), this LED will illuminate and either
oCA, oCC, or oCd will be displayed.
If unit experiences a short circuit fault condition, the Over Current LED
illuminates and either SCA, SCC, or SCd will be displayed. This trip is
fixed at 10 times the full load motor current and is not adjustable.
Shunt Trip
Yellow
LEDs

TD - Series
- 14 -
TD Series Digital Solid State Soft Starter 48 - 1250A
5.3 Display Modes
There are three modes of display: the Status Display mode, the Program mode,
and the Fault mode.
5.3.1 Status Display Mode
The Status Display Mode displays three phase motor current information and the
thermal capacity remaining.
Status mode:
•[0000.] The initial display on power up is four digits and the decimal. This
indicates the motor current for Phase A of the motor.
•[0000] Scroll up to display four digits only (no decimal). This indicates
the motor current for either Phase B or C. While viewing Phase A, press
the UP arrow once to view Phase B or twice to view Phase C current.
•[H000] Scroll up to display the “H”. This indicates that this value is the
remaining thermal capacity of the motor (as a percentage i.e. H070 =
70% remaining thermal capacity)
Reading Phase Current and Thermal Capacity (See Example)
[0120.] Indicates that Phase A is
drawing 120 amps.
Press the UP arrow.
[0121] Indicates that Phase B is
drawing 121 amps.
Press the UP arrow.
NOTE: Decimal points are not
present in the readouts
for Phase B and Phase C.
[0120] Indicates that Phase C is
drawing 120 amps.
Press the UP arrow.
[H051] Indicates that the motor has
51% of its thermal capacity
remaining.
5.3.2 Program Mode
Use the Program Mode to view or change Function (Fn) settings.
To enter the Program Mode, press the [Fn] key once. The first time you enter
Program Mode after power has been cycled to the starter, the initial function
[F001] should display with the selected digit flashing. If the TD Soft Starter has
been programmed and power to the unit has not been cycled, the readout will
display the last function viewed or changed.
To change to a different function, use the arrow keys.
Program Mode:
•[F001] The “F” indicates the programmable function.
•[0000] This is the present setting of the applicable function. This display
may include decimals between digits depending on the function setting’s
range and incremental step.
Display
Reading Phase Current
and
Thermal Capacity
0 120.
0 121
0 120
H05 1
Phase A
Phase B
Phase C
Remaining Thermal
Capacity
Press
This manual suits for next models
1
Table of contents
Other Toshiba Automobile Part manuals
Popular Automobile Part manuals by other brands
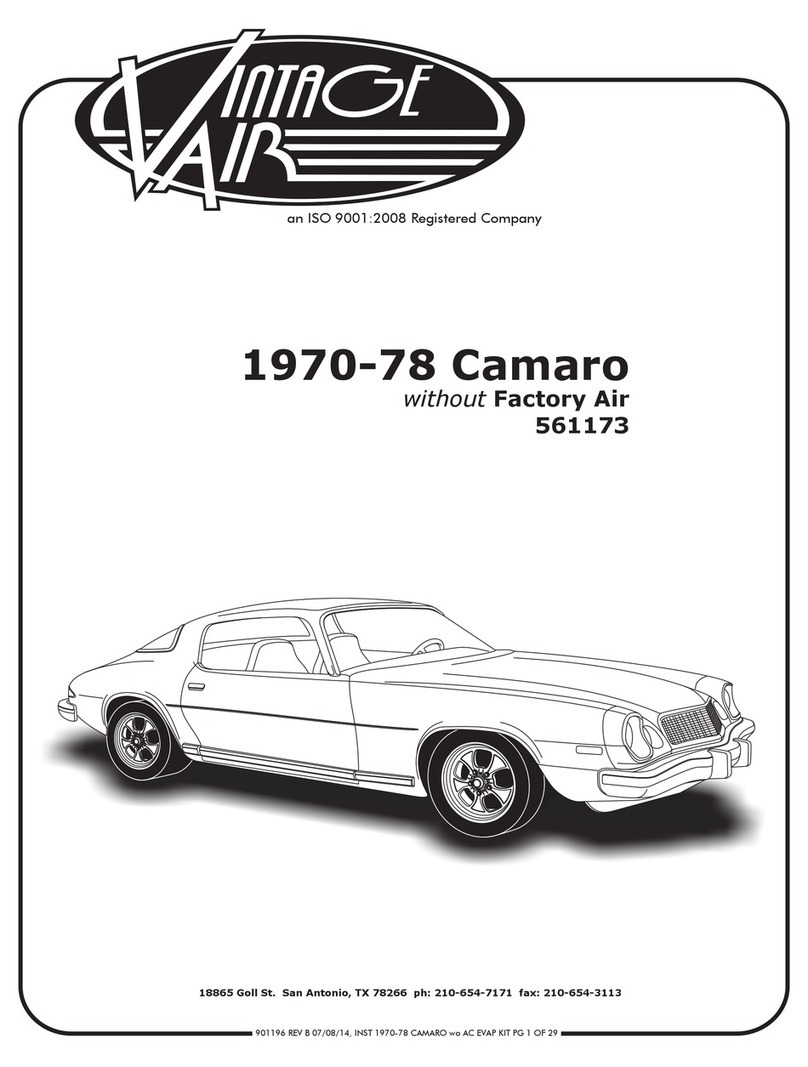
Vintage Air
Vintage Air 1970-78 Camaro instructions

Murphy
Murphy Gear Oil Pressure Sender EGPK-95083N installation instructions

Vintage Air
Vintage Air 571063 manual
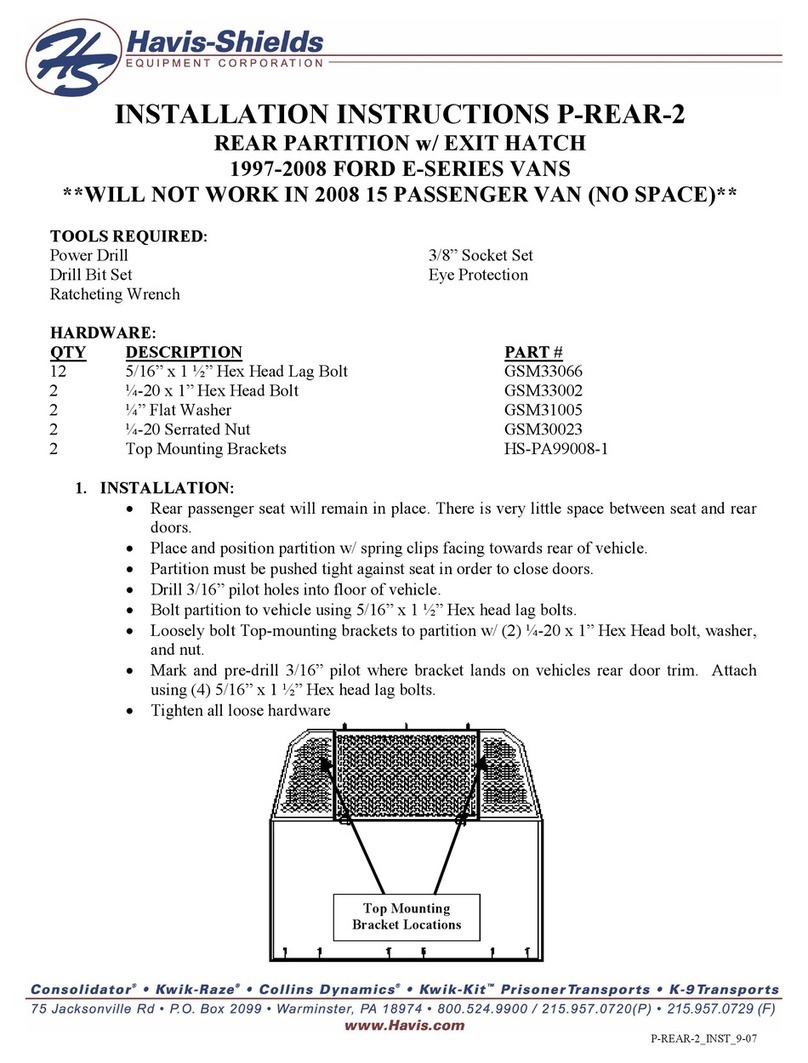
Havis-Shields
Havis-Shields Rear Partition w/ Exit Hatch P-REAR-2 installation instructions
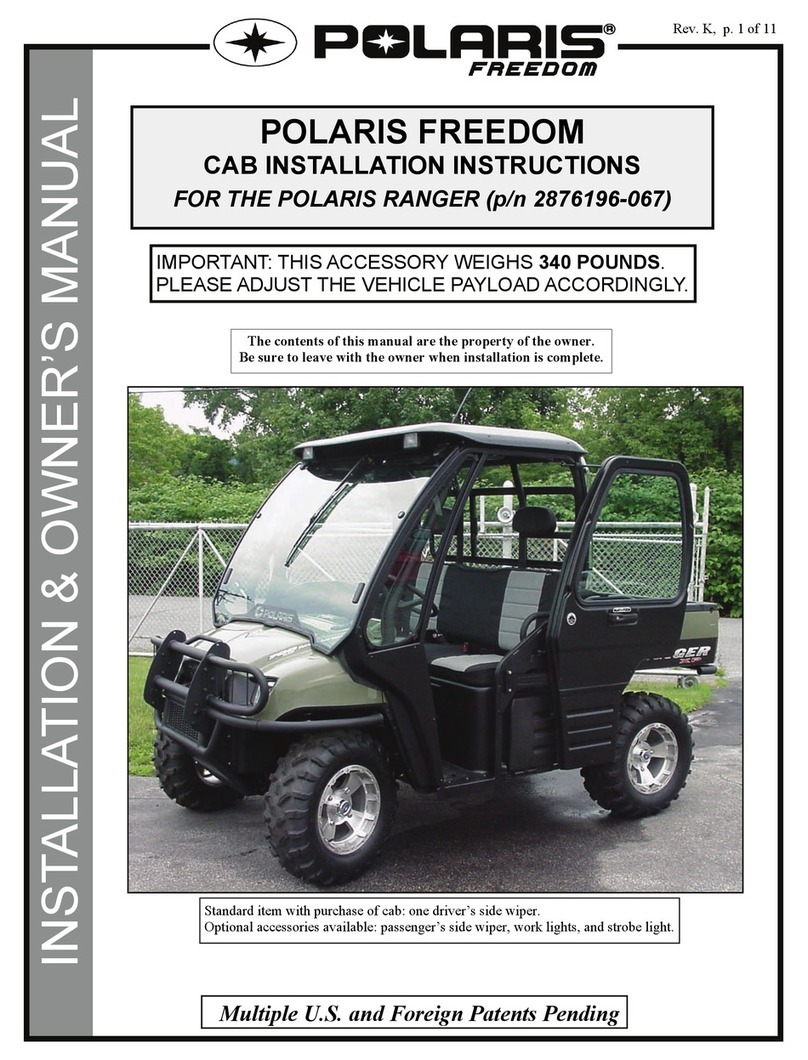
Curtis
Curtis Cab Installation & owner's manual
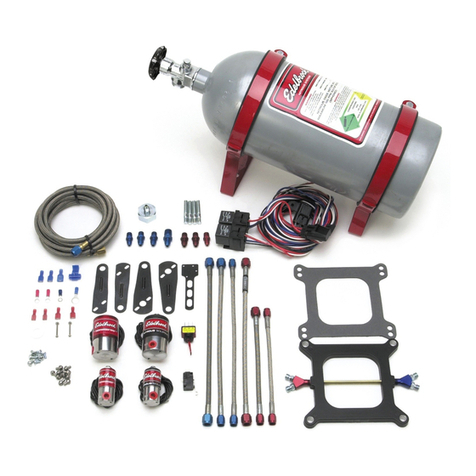
Edelbrock
Edelbrock 70003 installation manual
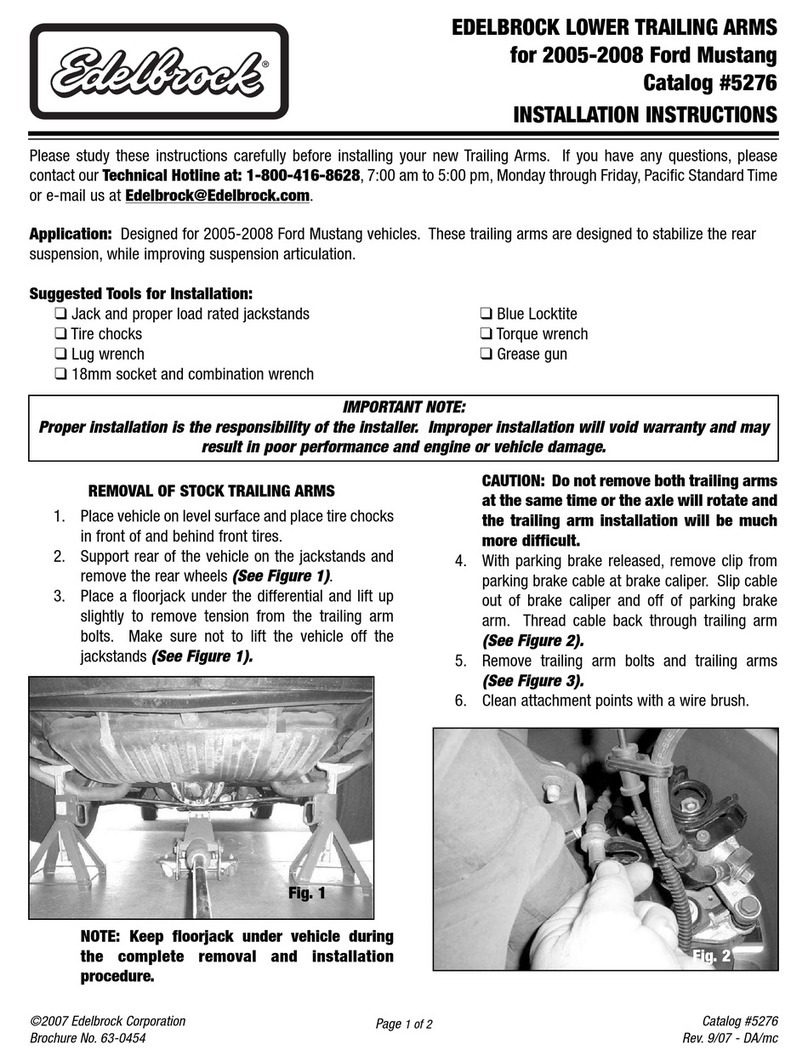
Edelbrock
Edelbrock 5276 installation instructions
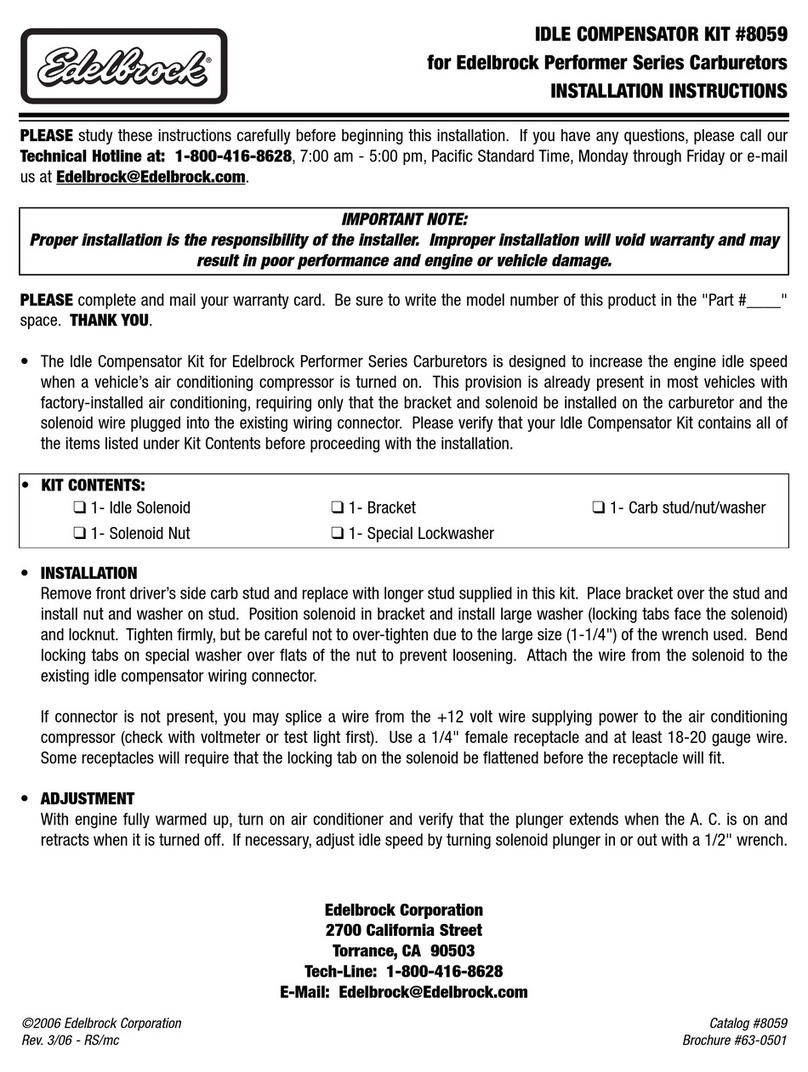
Edelbrock
Edelbrock Performer Series 8059 installation instructions

aFe Power
aFe Power 50-70046R instruction manual

Cannondale
Cannondale MC1000 Service bulletin
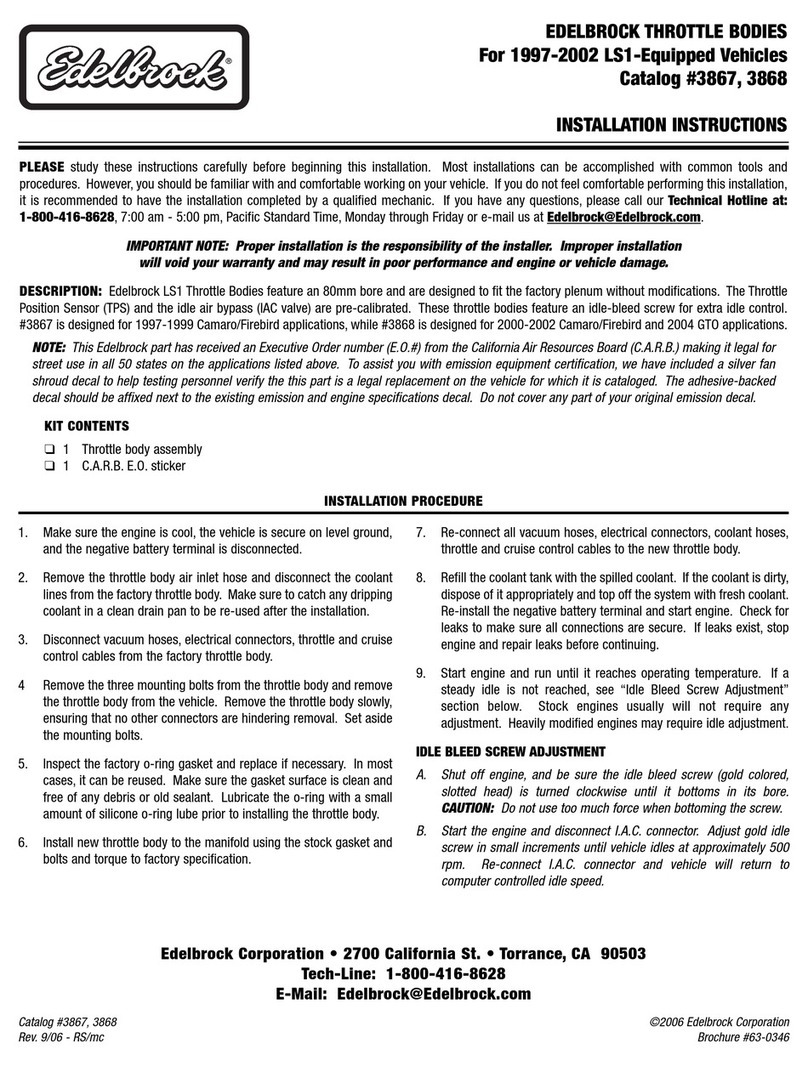
Edelbrock
Edelbrock 3867 installation instructions
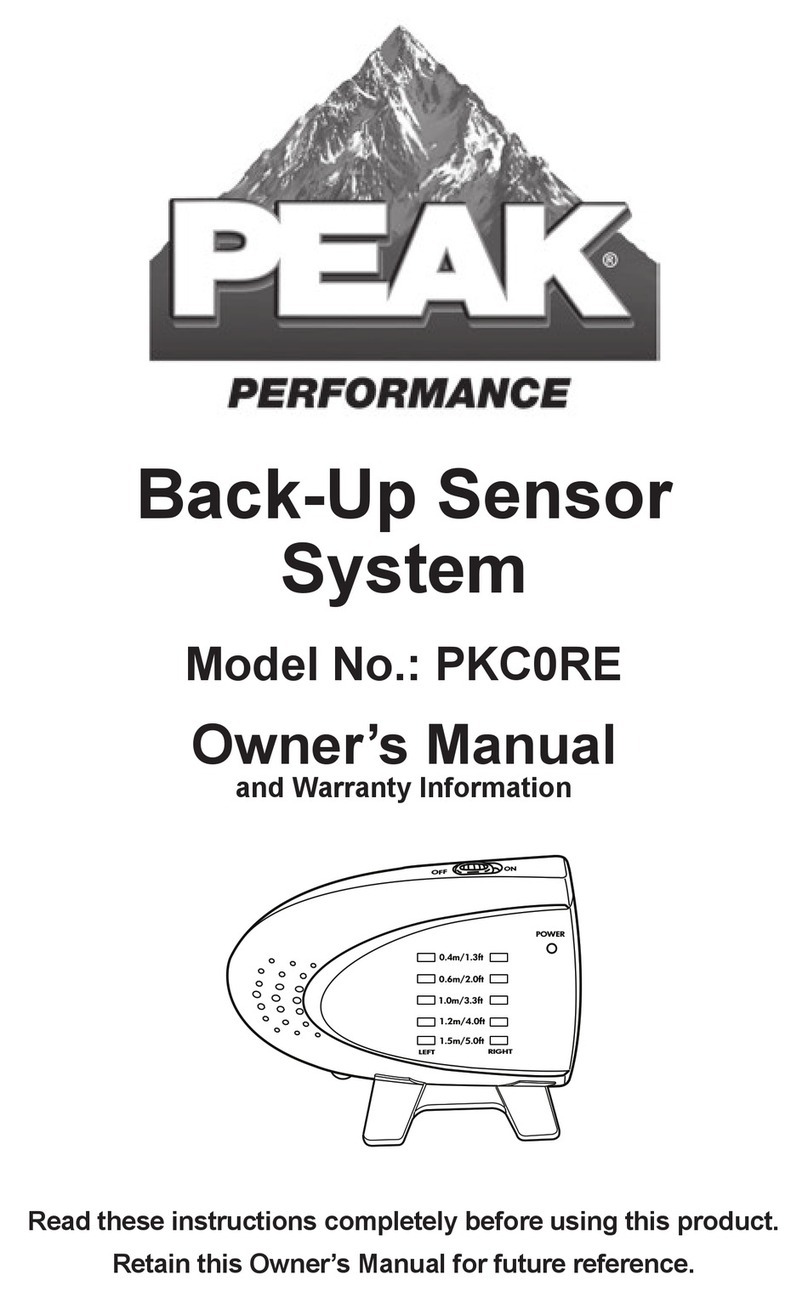
Peak Performance
Peak Performance PKC0RE owner's manual