Unibor BD35 Assembly instructions

Magnetic Base Drilling Machine
BD35
Operators Instruction Manual
And Spare Parts Listings
Index
Chapter 1. Technical Overview.
Chapter 2. Warnings and Safety Instructions.
Chapter 3. Operating Instructions.
Chapter 4. Maintenance Instructions.
Chapter 5. Exploded views and Spares lists.
Drill break down and Parts list
Electric motor break down

Introduction
Congratulations on the purchase of your new, lightweight multi-purpose
magnetic base drill. This is a high quality product with unique features that
make it the perfect solution for your entire hole drilling requirements.
!Easy to use and rugged design makes the BD35 a cost effective
solution to drilling clean, accurately positioned holes in your work
piece.
!Powered by a BLACK AND DECKER BD1321 MOTOR
2

Chapter 1. Technical Overview.
Machine BD35
Clamping force (Kg) 400
Speed (RPM) 450
Size (LxWxH) (mm) 300x100x390
Cutter Capacity (mm) 12 - 32
Twist Drill Capacity (mm) 13
Power Consumption (Watts) 700
Weight (Kg) 10
3

Chapter 2. Warnings and Safety Instructions.
Read these instructions carefully before operating, maintaining or servicing this tool.
Please keep these instructions in a safe accessible place.
Read to fully understand and
observe the following safety
precautions and warnings.
Careless or improper use of this
equipment may result in serious or
fatal injury.
Always wear eye, head and ear
protection equipment, when
using this tool
Operator Safety
!Always read the instructions carefully so as
to avoid any injury or damage when
unfamiliar with this equipment.
!Always wear a safety face shield or goggles.
!Wear ear defenders when using this
equipment.
!Always wear heavy clothing, boots and
gloves. Do not wear loose clothing, short
pants, sandals etc. and ensure that long hair is
tied up above shoulder length.
!Do not operate this equipment when tired, ill
or under the influence of alcohol, drugs or
medication.
!Never allow an inexperienced person operate
this equipment.
!Never operate the equipment in damp, or
water logged area.
!Keep all carrying handles and levers free
from oil.
!Keep hands away from the cutter when it is
rotating. Ensure that it has stopped rotating
and is disconnected from the power source
before touching the cutter.
Tool Safety
!Inspect the entire piece of equipment
before use.
!Replace damaged components, lubricate
where necessary and ensure that all
fasteners are secure.
!Always use a safety chain to secure the
equipment when it is being used above the
ground.
!Use only accessories that have been
recommended by the manufacturer. Failure
to do so could result in damage to the tool
and may invalidate the warranty.
WARNING!
Never modify the tooling any way. Do not use
your equipment for any job other than for
which it is intended.
Maintenance safety
!Maintain according to the manufacturers
recommended procedures.
!Disconnect the equipment from the power
source before attempting any maintenance.
!Use only genuine replacement components
WARNING!
Indicates instant possibility of
severe personal injury or loss of
life, if instructions are not
followed.
CAUTION!
Indications a possibility of
personal injury or equipment
damage, if instructions are not
followed.
4

!Do not attempt to gain access into the
electrical panel. There is risk of electrical
shock.
!Never use a larger diameter cutter than
specified for use with this equipment.
!Do not attempt to connect the equipment to a
power source other than that specified by the
manufacturer.
!Ensure that the cutter being used is sharp and
free from damage.
as recommended by the manufacturer.
Transport and Storage
!Before moving the tool, ensure that the
cutter has stopped rotating.
!Carry the tool with the cutter pointing away
from the body to avoid laceration.
!After use, clean the equipment and it’s
accessories and store in a dry place.
!Store the equipment along with the
maintenance tools in its correct carrying
case when not in use.
5

Chapter 3. Operating Instructions.
Ensure that the unit is disconnected from the power before working on the
machine.
!Insert Pilot Pin.
The pilot pin is used to align the cutter and eject
the slug on completion of the cut.
Slide the pilot through the hole in the centre of the
cutter shank.
!Fit the Cutter.
Two grub screws are used to secure the cutter to
the arbor. The cutter shank has two flats that must
be aligned with the grub screws in the arbor.
Insert the cutter shank into the arbor. The screws
must be tightened evenly so that the cutter is
prevented from moving. The screws are tightened
using the 4mm Allen key supplied.
(A cutter with a shank diameter of 19.05mm/¾”
and cutting diameter of no larger than 32mm/1¼”
must be used).
!Mark the centre of the required hole.
!Position the Machine.
Ensure that the workpiece is clean and flat. Position the machine by aligning the pilot
with the holes centre mark.
!Fit the safety chain.
!Connect the machine to the power source.
Switch on the power by depressing the RED power
switch on the side panel.
6

!Energise the magnet.
Switch on the magnetic base by depressing the
YELLOW magnet switch.
CHECK that the pilot is still aligned with the hole
centre mark, as energising the magnetic base can
cause the machine to move.
!Apply Coolant
A 500ml bottle of cutting oil is supplied with the machine. Using cutting oil can
increase the tool life and ensures that the slug is ejected cleanly.
Apply a generous amount of cutting oil to the surface to be cut.
If cutting surface is vertical or steeply inclined, then cutting paste, gel or foam should
be used.
!Start Cutting
ALWAYS ENSURE THAT
CUTTING GUARDS ARE IN
PLACE.
Start the drill by depressing the
GREEN drill switch. Lower the
cutter to the surface by turning
the handle; and with light
pressure cut an initial groove. Increase pressure until
motor is loaded then maintain steady pressure until cut is
complete.
!Finish Cutting
When the cut is complete the slug will be ejected from the cutter. Raise the cutter
again; stop the motor and switch of the magnet.
NOTE: –
!Applying too much pressure will not speed the cut, it will reduce the life of the tool
and may cause damage to the motor.
!If swarf becomes blue in colour then more cutting oil is required.
!If the power is interrupted during the cut, the magnet must be reset before the motor
will restart.
7

Chapter 4. Maintenance Instructions
!Occasionally apply a few drops of oil to the rack toothing.
!The bearings of the feed shaft are self-lubricating and must not be greased
!Grease the sliding surface of the carriage with MOLYCOTE grease.
!When not in use or being transported the unit should be kept in the case supplied.
!After use ensure unit is clean of swarf and dirt.
!Parts that are worn or damaged should be replaced immediatley with original
MAGTRON replacements.
!Ensure all cutting edges are sharp when in operation. Using blunt cutting tools may
lead to an overload of the motor.
!After repeated use, the cradle may become loose.
This is remedied by adjusting the tension screws
on the side of the body. Put 2.5mm Allen Key into
head of cradle retaining nuts, using 8mm Spanner
undo the locking nuts anti-clockwise holding the
Allen key without moving grub screws.
Using the Allen Key gently tighten screws in series
until the cradle moves freely in the slide but does
not allow the motor to wobble.
When adjustment is complete re-tighten locking
nuts clockwise.
8

Chapter 5. Exploded Views
9

Chapter 5. Component listing.
Item No. Stock Code Description Quantity
1 M0001RED Body 1
2 M0031 Magnet Base 1
3 M0166 Slide 1
4 M0101 Brass Rail 2
5 M0441 GFS 1
6 M0811A Oilfeed Top Plate 1
7 M0515RED Integral Front Steady 1
8 M0831 Rack 1
9 M0081 Pinion Bush 2
10 M0041 Pinion 1
11 M0072 Pinion End Cap 1
12 M0061 Handle 3
13 M0841 Handle Knob 3
14 PANELP NEW PANEL – NO FACIA 1
15 M0221B Warning Plate 1
16 M0444 Conduit (Black) 1
17 10231 M16 Strain Relief Cable Gland 1
18 M0451 Cable Gland 2
19 CABL02 USA Cable – 16 Gauge 1
20 BD1321-1 Black and Decker 1320-98 110V Drill 1
21 M0502 Long Reach Arbor Complete 1
22 20356 Arbor Spring 1
23 10205 Arbor Ejection Plug 1
24 CCP-19 19mm Internal Circlip 1
25 VIS08 Drill Guard (not shown) 1
26 10091 M10 Guard Locking Nut (not shown) 1
27 MO241B BD35 Switch Plate 1
28 STRAP01 Polyester Webbing Safety Strap (not
shown)
1
29 OIL05 Oil Cup Assembly (not shown) 1
30 OIL09 Coolcut 500ml Oil Bottle (not shown) 1
31 KEY01 Allen Key 2.5mm (not shown) 1
32 KEY03 Allen Key 4mm (not shown) 1
33 KEY04 Allen Key 5mm (not shown) 1
34 BOX05 Box (Sleeve) 1
35 CASE01 Carrying case – Plastic (not shown) 1
36 SC520BUT M5 x 20mm Button Head Screw 2
10

37 SC525GRUB M5 x 25mm Grub Screw 5
38 NUT-M5 M5 Nut 5
39 SC310CSK-X M3 x 10mm Countersink Screw 2
40 NUT-M3 M3 Nuts 2
41 SELPIN410 !4 x 10mm Selop Pin 2
42 SC410CSK-X M4 x 10mm Countersink Brass (not
shown)
1
43 NUT-M4 M4 Nut Brass (not shown) 1
44 SC510BUT M5 x 10mm Button Head Screw 8
45 SC625CAP M6 x 25mm Cap Head Screw 4
46 SC88GRUB M8 x 8mm Grub Screw 2
11

Panel Spares Lists - Panel P
Item No. Stock Code Description Quantity
1 MM1-1 MM1 MAGNET BUTTON - YELLOW 1
2 MM1-2 MM1 MOTOR BUTTON - GREEN 1
3 MM1-10 MM POWER BUTTON - RED 1
4 MM1-3 MM1 L.E.D. GROMMET 3
5 MM1-4 MM1 LED BOARD – C/W LEDs 1
6 MM1-5 MM1 REPLACEMENT PCB 1
7 MM1-6 MM1 3 PIN PLUG 1
8 MM1-7 MM1 4 PIN PLUG 1
9 MM1-11 MM1 HEAT CONDUCTOR 2
10 MM1-12 MM1 SELF ADHESIVE STANDOFF 2
11 MM1-13 NEW PANEL INSULATING BUSH 1
12

hapter 5. Electric Motor Break Down
13

14

15

16
Table of contents
Other Unibor Drill manuals

Unibor
Unibor Airbor 2 User manual
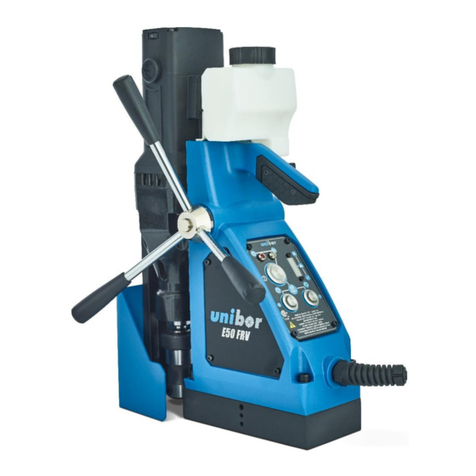
Unibor
Unibor E50 FRV User manual
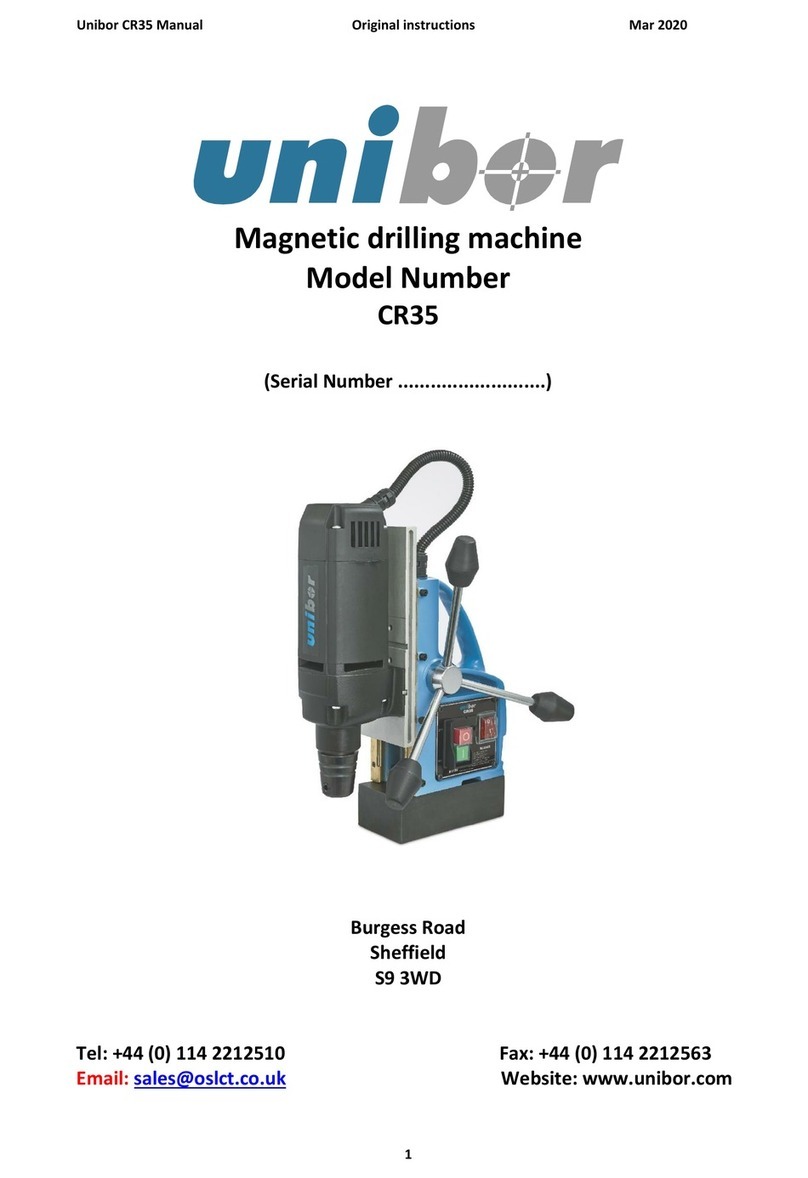
Unibor
Unibor CR35 User manual
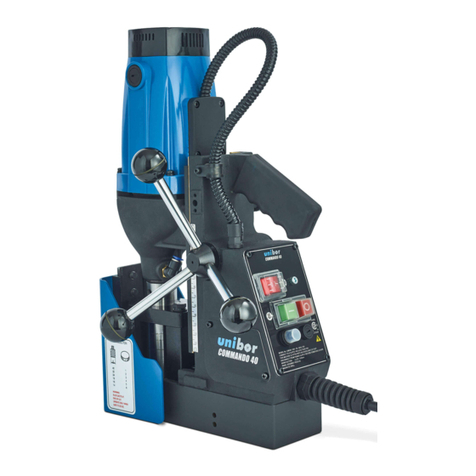
Unibor
Unibor COMMANDO 40 User manual
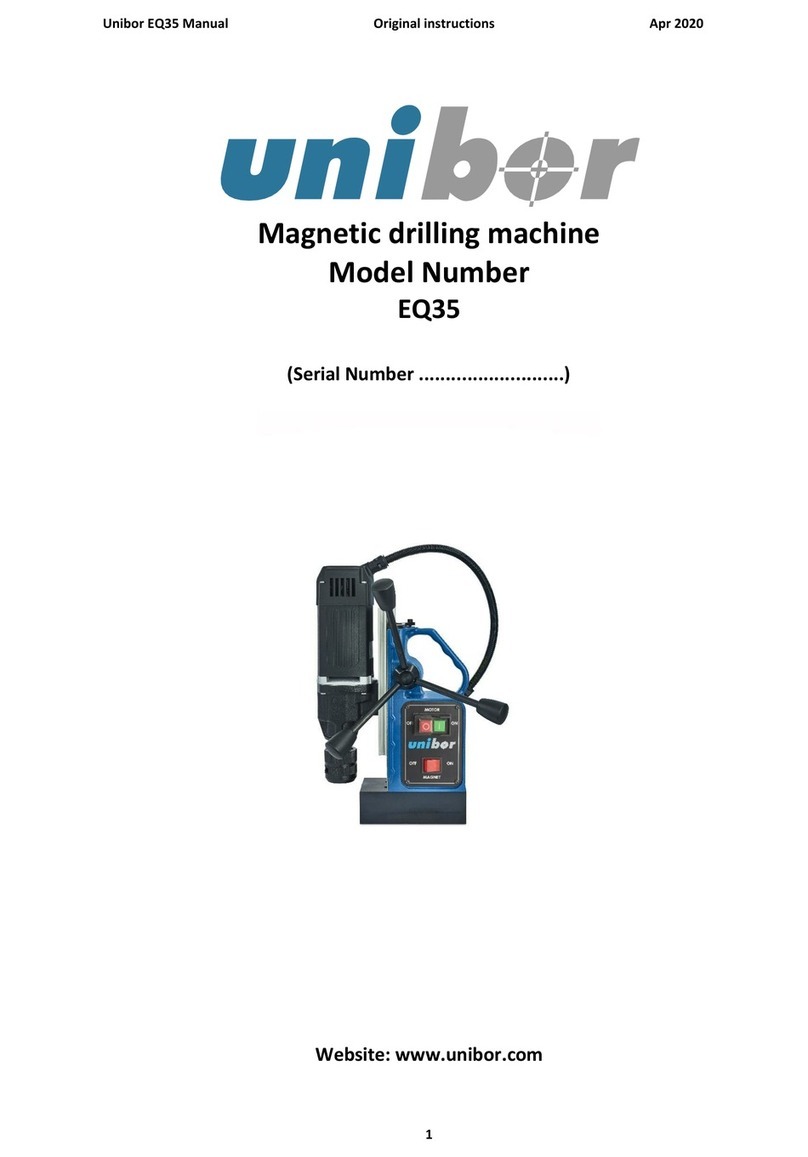
Unibor
Unibor EQ35 User manual
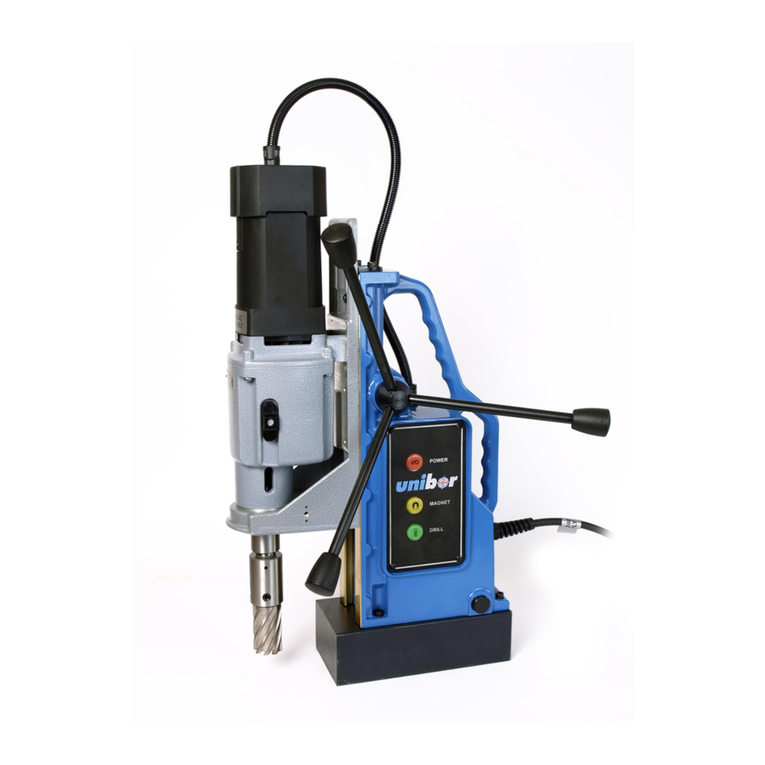
Unibor
Unibor E100 PLUS User manual
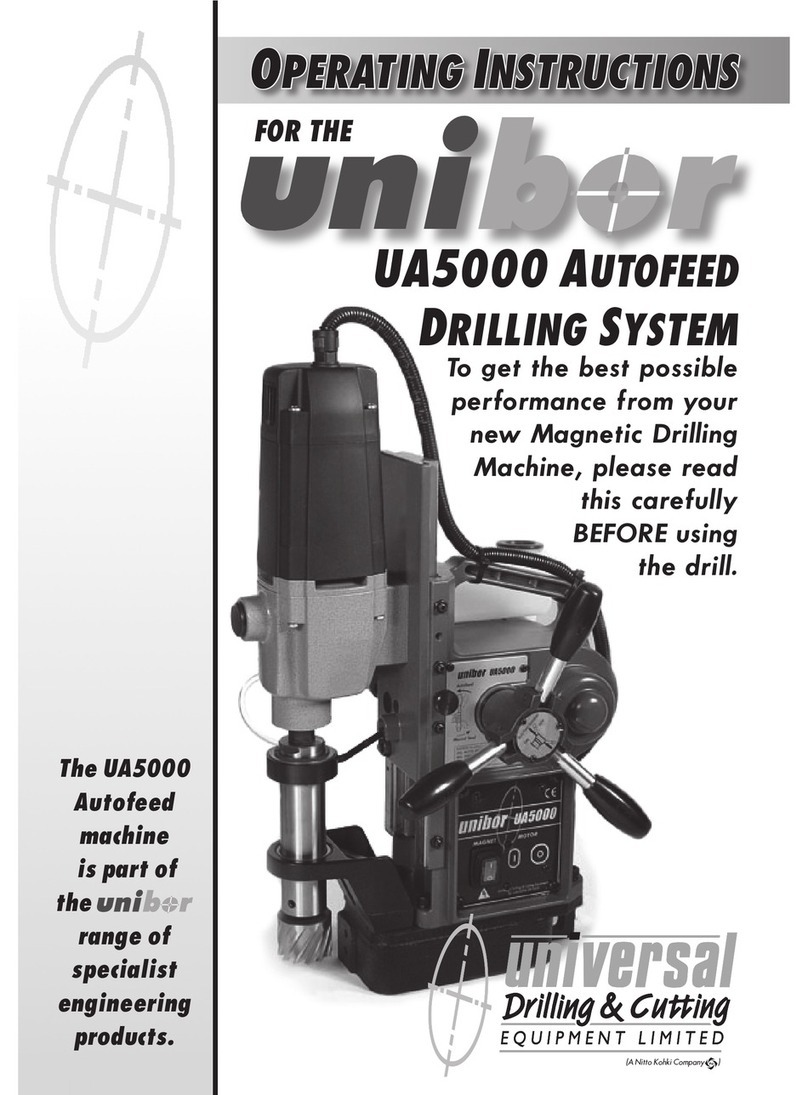
Unibor
Unibor UA5000 User manual
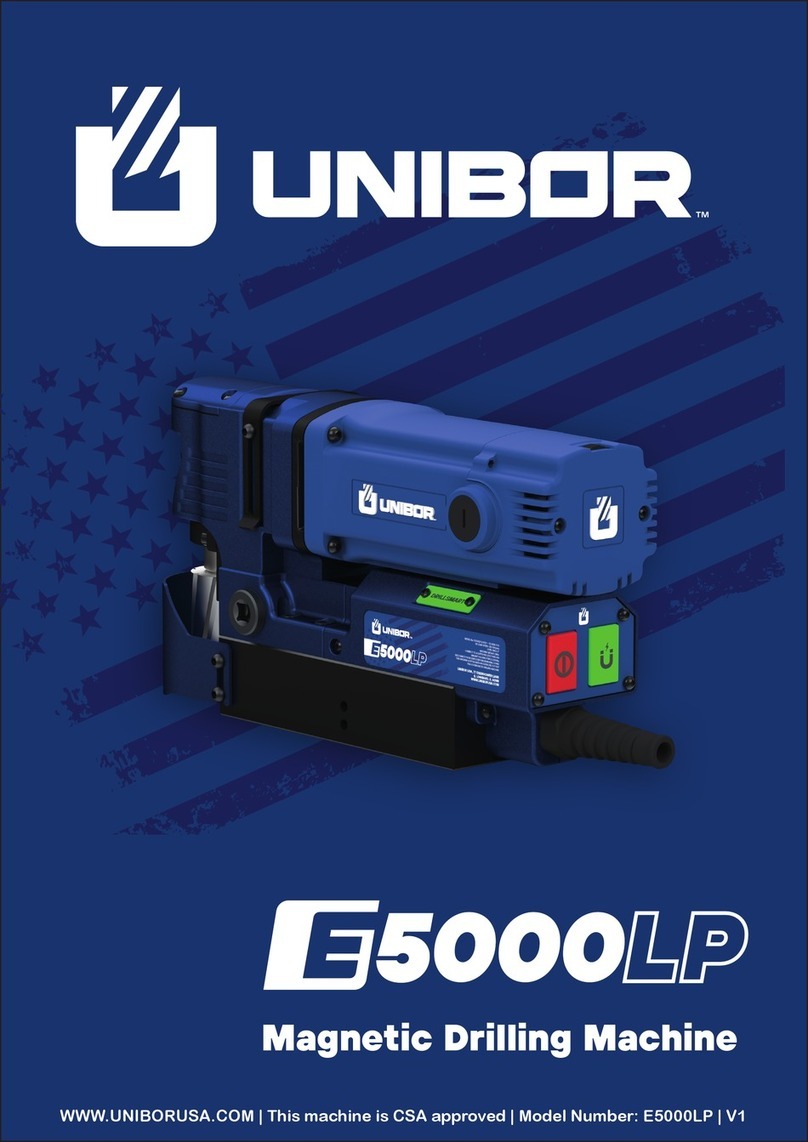
Unibor
Unibor E5000LP User manual
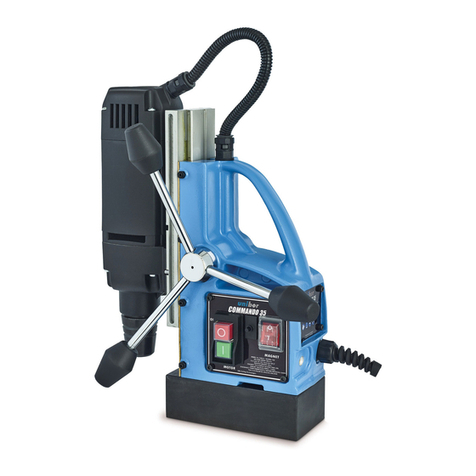
Unibor
Unibor COMMANDO 35 User manual
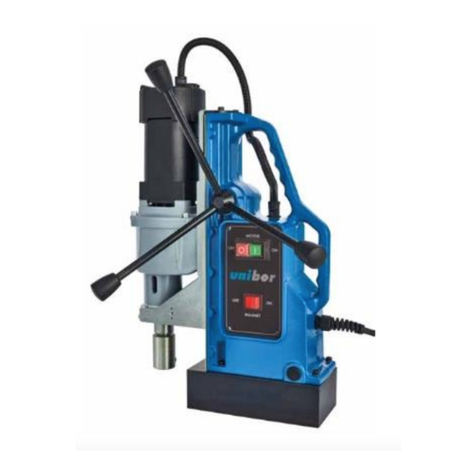
Unibor
Unibor E100 User manual