Verlinde Stagemaker Controllers R PRM SR Series User manual

STAGEMAKER
CONTROLLERS
INSTALLATION
MAINTENANCE
STAGEMAKER CONTROLLER
SERIES R-FL.. PRMSR
VERLINDE se réserve le droit de modifier sans préavis les caractéristiques de son matériel 06/2004 VESEGBSM CONTROL R/PR
VERLINDE reserves the right to alter or amend the above information without notice

STAGEMAKER CONTROLLER
2004.07GB 1
Series R..PRMRR
Series SC – R and FL
SERIES R - FL..PRMSR
Herewith we,
VERLINDE S.A., 2 bd de l'Industrie, BP 59,
F-28501 VERNOUILLET Cedex, Frankrijk
Declare that the product
This equipment is to be used in corporation with other machines. It cannot be put into operation until the
systems of which it is a part, has been declared as conforming to the provisions of the directive:
Machines 89/392 EEG, 91/368 EEG, 93/44 EEG, 93/68 EEG
Electric machines 73/23 EEG,
Electromagnetic compatibility 89/336 EEG, 91/263 EEG, 92/31EEG, 93/68 EEG
As well as harmonised norms, in particular EN292, chapter 1 and 2 (safety of machines),
Applied technical standards and specifications, in particular:
IEC 34-1 "Rotating electrical machines”
IEC 34-5 ""Rotating electrical machines”
IEC 947-5-1 "Lowvoltage switchgear and control gear”
IEC 364 "Electrical installations of buildings”
EN 60204 “Safety of Machines”
The party carrying out the integration will state these passages in declaration of conformity of the machines, the
party will add the regulations and standards to the final installation “machine” and has to comply with, the party
carrying out the integration will draw up the corresponding technical file.
VERLINDE S.A.,
VERNOUILLET, 1-11 -2001
STAGEMAKER CONTROLLER
Manufacturing date : ………
Ser i al No. : ………

STAGEMAKER CONTROLLER
CONTENT
chapter description page
1 Introduction 3
2 What to do - What not to do 5
3 Guarantee 6
4 Identification 7
5 Functional description 8
6 Trouble shooting 11
7 Specifications 11
Attachments general layout drawings
• R4PRM SR
• R8PRM SR
• R12PRM SR
Electrical diagrams
• R4PRM SR
• R8PRM SR
• R12PRM SR
• FL8PRMLV SR
• FL12PRMLV SR
2004.07GB 2

STAGEMAKER CONTROLLER
1 INTRODUCTION:
The STAGEMAKER®controllers with radio remote series R..PRM SR and FL..PRMLV SR has been
developed specifically for the control of VERLINDE STAGEMAKER®chain hoists (motors) series SM5
and SM10 version A for direct control. The controller series R..PRM SR and FL..PRMLV SR are available
with 4, 8 OR 12 channels and built into a compact suitcase, 19” rack casing.
These controllers allows you to control the chain hoists individually or simultaneously with one single button.
Pre-selection facilities for all units, on the controller series R..PRM SR and FL..PRMLV SR front as well on
the remote box that incorporate red and green LED indicators, which indicate the selected hoisting direction.
For larger applications, controllers series R..PRM SR and FL..PRMLV SR could be wireless interconnected
to serve a system up to 16 motors from one single remote box.
STAGEMAKER®controllers series R..PRM SR and FL..PRMLV SR fully meet the latest European electrical
standards (IEC-EMC) and have been approved by the official APAVE institute. They offer a maximum
flexibility, durability and safety.
Version A controller series R..PRM SR for direct controlled hoist:
• Combination of power switching through a unique solid state PC board
• Main contactor
• Mushroom emergency button with mechanical interlock
• Individual up/down selectors per motor
• Short circuit protection in main circuit by means of automatic fuses
• Phase reverse facility on incoming CE plug
• Automatic thermal control on each channel
• Phase reverse facility for each channel
• LED indicators for incoming phases
• Mutly connectors each to serve 4 hoists
• Single cable connections between controller series R..PRM SR and hoists
• Channel selection mode
• Frequency selection mode
Version B controller series FL..PRM LV SR for contactor controlled hoist:
• All features as mentiond above
• In dividual CEE connectors for power (red)and control (yellow)
• Twin cable connections between controller series FL..PRMLV SR and hoists
2004.07GB 3

STAGEMAKER CONTROLLER
2 WHAT TO DO
• Mount the controller in a protective casing, (if standard casing is not supplied).
• Handle the controller by its grips at the front or at side.
• Store the controller in its normal operating position away from aggressive atmospheres
(du t,
humidity...).
s
s
• Make sure that the controller is always clean and protected from corrosion
.
• A technician should install the controller with the necessary competence.
• Make sure that connecting cables are in good condition and connectors are fitted properly.
• Make sure that connecting cables are always symmetrical fitted
• If one hoist direction doesn’t match with the Up / Down indicators on the controller, check intermediary
cabling and change two phases.
• If all hoists do not match with the indicators, change phases by means of phase reverse facility in the CE
plug or with the reverse switch.
• Use only original parts in case of replacements.
• Always be ready during the operation to press the emergency stop button. This makes all functions
inactive.
• Before operation, check that the load is correctly fastened and installed on the hook. The hook safety
catches should be closed correctly.
• Make sure that the load is correctly balanced before moving it.
• Make sure that each hoist is vertical to the load and hanging free on its load chain, before starting a
simultaneous operation.
• If used out door, use sufficient protection against bad weather conditions.
• Switch to another frequency of normal operation is disturbed frequently.
• Use the material under normal working conditions
(ambient temperature, atmosphere...).
• Moving a single load or truss system requires experienced operators.
• All the necessary precautions should be taken to ensure a correct the distribution of the load and to
avoid overloading a single hoist in set of multiple uses. The hoists should be carefully checked
individually before such an operation.
• Notify the responsible and competent person after a dangerous operation or if the hoist seems
problematic
(
Abnormal noi e, abnormal behaviour...).
Material used outdoors should be protected as well
as pos ible ag inst bad weather conditions.s a
2004.07GB 4

WHAT NOT TO DO
• Never connect a STAGEMAKER controller to a power source other than specified on the unit.
• Do not set down the controller without having an adapted support, to avoid damaging the components on
the rear
• Never modify the controller unless the constructor has studied and authorised the modification.
• Never modify the values and adjustments of the safety components, outside the limits provided for in the
manual, or without the approval of the constructor.
• Never try to repair or intervene on the controller without the authorisation of the constructor or a qualified
electrician.
• Do not let an unqualified person use the controller.
• Never connect more hoists than the available number of outlets (channels) or number of selector switches
available.
• Do not use additional splitters to connect more than one hoist per channel.
• Avoid shocks or accidental collision with other objects.
• Never open the controller as long as the system is under power.
• Never block, or lock the RUN button in order to continue a movement without manual interference.
• Do not operate the controller if your physical condition does not allow it.
• Never use the controller series if it is in bad condition.
• Never use suspected spare parts or parts whose origin is not known.
• Do not subject the controller to brutal shocks.
• Never distract the operator’s attention while he is being operating the system.
• Do not use the controller for a purpose or in an area for which it is not intended.
• Do not expose the controller to an aggressive atmosphere
(temperature, acidity...)
• Do not use the safety components as operation components
(emergency button, main fuse switch. etc..)
• Do not use the controls needlessly (avoid inching - stop-start operation of the buttons). This can cause
overheating and even damage to the hoist.
• Do not change the hoisting direction whilst the RUN button is pressed (hoist under power)
• If hoist direction doesn’t match with the indications on the controller, don’t change phases inside the
controller but exchange two phases on the hoist motor or the interconnecting cables.
• Never use hoists who are running in the opposite direction of the selected motion.
• Do not connect the controller to an unknown power supply, check if power source matches the specification
of the controller and the hoists.
(under voltage or over voltage +/- 5%, absence of phase etc...).
2004.07 RPRMSR GB 5

STAGEMAKER CONTROLLER
3 GUARANTEE
Our STAGEMAKER controller series R..PRM SR and
FL..PRMLV SR are guaranteed for one year from the
date of delivery.
If for a reason outside the control of the vendor, the
delivery is delayed, the time lag cannot exceed three
months.
If the use
inst llation)
of the controller is delayed, the
corresponding extension of the guarantee (a single
extension limited to three months) must be requested,
and written confirmation obtained.
( a
The vendor undertakes to eliminate all operating errors
originating from the concept, the execution, the
components or the materials themselves.
The guarantee does not cover normal wear, or the
failures resulting from abnormal use. It does not cover
damage due to a lack of supervision, to false
operation or to a bad utilisation of the controller,
particularly due to overload, inching, under voltage or
over voltage or connecting errors.
The guarantee does not apply when there is
disassembly, modification or replacement of parts
(mechanical or electrical)
by an unauthorised party or
without our prior agreement.
The guarantee only applies for original, factory-installed
spare parts.
For the duration of the guarantee, the vendor
undertakes to replace or repair, free of charge, the
parts, in his workshop, that are acknowledged to be
damaged following examination by a qualified and
authorised technical service.
The guarantee excludes any other services or
indemnities. The repairs covered by the guarantee are
carried out, as a rule, in the workshops of the vendor
or authorised agent. When servicing of the equipment
is done outside these workshops, the labour costs for
disassembly or assembly of these parts are borne by the
vendor when these are done exclusively by his staff or
by an authorised agent. The replaced parts become the
property of the vendor and must be returned to the
vendor at his expense.
For components of a relative particular importance that
are not manufactured by the vendor and which carry
the brand name of specialised manufacturers, the
manufacturer’s guarantee (which can vary according to
the manufacturer) is applicable.
*The guarantee does not apply for expendable parts
defined by the manufacturer:
- Fuses
- Contactor contacts
- Batteries
2004.07 RPRMSR GB 6

STAGEMAKER CONTROLLER
4 IDENTIFICATION:
Type codes
Type No. of Subscription Housing Hoist
channels connection
R4PRM SR 4 Direct control + remote 19" 3U rack in flight case multi-plug rear side
R8PRM SR 8 Direct control + remote 19" 3U rack in flight case multi-plug rear side
R12PRM SR 12 Direct control + remote 19" 6U rack in flight case multi-plug rear side
FL8PRM LV SR 8 Lowvoltage control + remote 19" 12U in flight case CEE plugs rear side
FL8PRM LV SR 12 Lowvoltage control + remote 19" 12U in flight case CEE plugs rear side
Location of controls and connections
Subscription On rack On remote
Main switch yes -
Power indicators yes -
Emergence stop with mechanical interlock yes yes
Up / Down selector switches yes yes
Channel selection switch yes yes
Reset - yes
Green RUN button yes yes
Main & secondary fuses yes -
Thermal protection per hoist yes -
Frequency mode selector switch yes yes
Main power entry 16 amp CE-5p & 0.5 m cable rear; R4.. -
Main power entry 32 amp CE-5p & 0.5 m cable rear; R8..R12..
-
Multi connectors for hoists output 16 pin –16Amp Rear R models -
CEE connector for hoists output power 4pin –16Amp red male Rear FL models -
CEE connector for hoists output control 4pin –16Amp yellow female Rear FL models -
Local remote switch yes -
Default indicator with reset yes -
Phase reverse switch Yes -
2004.07 RPRMSR GB 7

STAGEMAKER CONTROLLER
5 FUNCTIONAL DESCRIPTION
Cable connections:
• Connect an external power source with the main CE power plug. Be sure that the nature of this
source corresponds to the supplied equipment, such as mentioned aside of the plug.
• Connect the chain hoists through fan-out or multi cables with the controller series R..PRM SR’s
outlets. Controller series FL..PRM SR do have separate single cables for power and control.
Warning: Use only cables and connectors who are in good condition, inferior connections might
cause severe d mage of the equipment and electric motors.a
Connecting more than one SM10 or two SM5 hoists per channel might cause severe
damage of the equipment.
Operation:
• Release the emergency switch by turning anti-
clockwise.
• Set the local / remote switch in the required
position. Local in case of control by means of the
up/down selector switches on the controller and
remote if the radio remote handheld is being used.
UP/DOWN SELECTION
PHASE REVERSE
SELECTOR
RUN BUTTON
DEFAULT SWITC
H
• If handheld is used:
- set the channel selector in the same mode as
indicated on the display of handheld.
- set the group mode selector in the correct mode.
(see group mode selection table)
- See “REMOTE OPERATING INSTRUCTIONS” for
details.
• Use the selector switches to set the hoists in the
upper or lower mode.
• Push the RUN button to activate the pre-selected
hoists.
• Check if the hoist direction matches the selected
mode. If not reverse, phases by means of the phase
reverse switch.
CHANNEL SELECTION
and GROUP MODE
E
-
STOP
MANUAL / REMOT
E
SELECTION
2004.07 RPRMSR GB 8

STAGEMAKER CONTROLLER
Group mode selection:
Since the radio remote handheld has 16 channels
as a standard, it is possible to use different
configurations of controllers. For that purpose the
controllers have a mode selector. The setting of this
selector should be in accordance to under
mentioned table.
GROUP MODE SELECTION
Group mode selection table
Number of Number of channels
Mode selection Mode selection Mode selection Mode selection
controllers on each controller no. controller 1 no. controller 2
no. controller 3 no. controller 4
1 4 1, 2, 3 or 4 - - -
1 8 5 or 6 - - -
1 12 7 - - -
1 16* 8 - - -
2 4 and 4 1 2 - -
2 4 and 4 3 4 - -
2 4 and 8 3 5 - -
2 4 and 12 4 7 - -
2 8 and 8 5 6 - -
3 4, 4 and 4 1 2 3 -
4 4, 4, 4 and 4 1 2 3 4
*not yet available
Notes:
- Phase sequence could also be reversed by means of changing two phase-pins fitted on a
satellite inside the 32Amp CE connector. Push and turn the satellite with screwdriver
180 degrees.
- There are three pre-selection modes; upper, lower or zero modes. Only pre-selected
hoists in upper or lower mode will come in to the corresponding operation.
- If circumstances require doing so, push the RED button in order to stop all hoists
immediately. Release this button by turning it anti clockwise.
- Don’t change the hoist direction whilst motors are under power. Release first the RUN
button, make your changes and push the RUN button again.
- If a hoist output has been thermal overloaded, or there are interfering signals, the controller will
stop all motions and go to the standby mode. A red warning indicator in the front will light.
Pushing the red indicator light makes reset.
2004.07 RPRMSR GB 9

STAGEMAKER CONTROLLER
REMOTE OPERATING INSTRUCTION
R
▲
S C D
▼
R = reset
▲= motion Up
S = select
C = confirm
D = deselect
▼= motion Down
Starting procedure:
The controller has to be in the standby mode with selector switch set to “auto”
Pull out the red emergency stop button on the remote
Push simultaneous on Sand C
Communication is valid if the channel indicator shows the same channel number as selected on the
controller. For valid confirmation there is a short “bib” sound.
If there is no communication the “bib” sound remains.
Frequency selection:
Under certain circumstances radio interferences might disturb normal operation as a consequence of
which the radio remote will be switched off. It therefore has been equipped with 8 different
frequencies. Select an other frequency if communication is disturbed regular in the following manner:
Push the three vertical buttons ▲C▼at the
same time to open the frequency selection menu.
The value in the display starts to blink on off.
Press ▲to increase the number or ▼to
decrease the number while it is blinking.
Press Cto confirm the new selection. The display
remains at the new setting.
CHANNEL SELECTION MOD
E
Set the channel indicator on the controller in the
same mode by pressing on the button next to it.
Note: The remote box has 4-penlight batteries type AA 1.2 volt.
A bib signal alarms in case of low batteries.
In case of replacement, open the grip with a screwdriver.
2004.07 RPRMSR GB 10

STAGEMAKER CONTROLLER
Hoist selection - add:
Select hoist by pressing on Sonce (both LED’s up/down lit) and press ▲or ▼once for
selection of motion. The corresponding LED remains lit. Press Cfor confirmation, the corresponding
LED will light.
Repeat this for all hoists that are to be added; Use Sand Dto scroll through the available
channels and press Cfor confirmation.
Hoist selection - remove:
Select hoist by pressing on Donce (both LED’s up/down lit) and press ▲or ▼once for
selection of motion. The corresponding LED remains lit. Press Dfor confirmation, the corresponding
LED will light.
Repeat this for all hoists that are to be added; Use Dand Sto scroll through the available
channels and press Cfor confirmation.
Output selection - normal or inverted:
Select hoist by pressing on S once for hoist No.1, twice for No. 2 etc; press Cand Dat the
same time once, the pre-selected hoist motion LED starts flashing. Press ▲the LED will indicate
“n” (normal) or ▼the LED will indicate “i” (inverted). Press Conce for confirmation, the
corresponding LED remains flashing as long as the output is inverted.
Repeat this for all hoists that are to be selected.
Note:
change of output selection should be done after hoist selection.
RUN mode:
Once hoists have been selected and confirmed, hold pressure on the left or right RUN button to
activate the hoist(s). The corresponding LED will light. Release the RUN button to stop the
motion. If this button is released for more than 20 seconds, the function is discharged and C has
to be pressed once again to re-confirm the latest selection before the Run button will be active
again.
Change of Up/Down motion:
To change the motion, once hoists and output have been selected, press the ▲for up or ▼for
the lowering motion. The motion of all selected hoists will be altered consequently without
confirmation, provided that the RUN mode is active. If the RUN mode is de-activated meanwhile,
press Cfor re-confirmation of the new selection.
Press the RUN button to continue the operation.
Reset:
Press reset to clear all settings.
Emergency stop:
In case of emergency, press down the red E-stop button, all motions will stop immediately and all
settings will be cleared.
2004.07 RPRMSR GB 11

STAGEMAKER CONTROLLER
R model CONTROLLERS
1
1. Motor cables 10 or 20 M:
code No. 5229263 or 5229264
2. Splitter (fan-out) CE M : code No.
52292667
3. Multy cables 10 or 20 M:
code No. 5229261 or 5229262
HARTING
HARTING
2
HARTING
3
3X400V+N+T 16A
I/O START
MOTOR 1-4 MOTOR 1- 8
FUSEFUSE FUSE
L1 L2 L3
START
GENERAL
Telemecanique
OF F
STOP START
1.6
1.4
1.2 1
Test
Telemecanique
OFF
STOP START
1.6
1.4
1.2 1
Test
VERLINDE
type R8P
MOTOR 1-4
CONTROL MOTOR 5-8
0
MOTO R 5
00
MOTO R 6 MO TOR 7
0
MOTO R 1 MOTOR 3MOTO R 2
00
0
MOTOR 8
MOTOR 4
0
Power inp
Power input ut
R8PRM SR rear side
2004.07 RPRMSR GB 12

STAGEMAKER CONTROLLER
FL model CONTROLLERS
Power input
1
2
Controller FL8PRMLV SR
Rear side with CE connecotors
Optional Harting 6 pin available for
combined power and control.
(FL8PRMLVH SR)
CEE
16-6h
3P+PE IP44
CEE
16-6h
3P+PE IP44
CEE
16-6h
3P+PE IP44
CEE
16-6h
3P+PE IP44
MOTOR 3MOTOR 2
MOTOR 1 MOTOR 4
CEE
16-6h
3P+PE IP44
CEE
16-6h
3P+PE IP44
CEE
16-6h
3P+PE IP44
CEE
16-6h
3P+PE IP44
MOTOR 1 MOTOR 2 MOTOR 3 MOTOR 4
CEE
16-6h
3P+PE IP44
CEE
16-6h
3P+PE IP44
CEE
16-6h
3P+PE IP44
CEE
16-6h
3P+PE IP44
MOTOR 7MOTOR 6
MOTOR 5 MOTOR 8
CEE
16-6h
3P+PE IP44
CEE
16-6h
3P+PE IP44
CEE
16-6h
3P+PE IP44
CEE
16-6h
3P+PE IP44
MOTOR 5 MOTOR 6 MOTOR 7 MOTOR 8
1. Motor cables 10 or 20 M:
code No. 52292663 or 52292664
2. Control cables 10 or 20 M:
code No. 5229853 or 5229854
2004.07 RPRMSR GB 13

STAGEMAKER CONTROLLER
8 CABLE SELECTION TABLE
The table hereunder gives an indication of the maximum length of cables between controller and hoist
(motor). They are calculated in accordance to NE 60 204 and worse case consideration
c1.5mm² or 1.5²mm² + 2.5mm² sections
400V/50Hz 230V/50Hz
L max (m) In Max
(A)
L max (m) In Max
(A)
SM1 230 115 1.4 75 35 2.5
SM5 100 50 3.2 40 20 4.5
SM10 65 1.75 25 7
d2.5mm² sections
400V/50Hz 230V/50Hz
L max (m) In Max
(A)
L max (m) In Max
(A)
SM1 255 125 1.4 80 40 2.5
SM5 110 55 3.2 45 20 4.5
SM10 75 35 1.75 25 7
Limitations
Cable with different section, i.e. 1.5mm² and 2.5mm², can be connected together. But maximum
length of cable depends of the smallest section. That is why if a cable assembling contains both
1.5mm² and 2.5mm² cable section you should refer to chart c. If the cable assembling contains only
2.5mm² section you should refer to chart d.
Those charts have been calculated according to EN-60-204 with a maximum voltage drop of 5%.
9 OPTIONAL EXTRA’S
2004.07 RPRMSR GB 14

STAGEMAKER CONTROLLER
Accessories for R..PRM SR controllers
Code Function
drawing
elec. dwg
Length
(m)
Section
(mm²)
Plugs Symbol
52292663 Motor extension cable
SMCA-04P-04P-100
10 4G2.5 CEE 3P+T
Male – Female
52292664 Motor extension cable
SMCA-04P-04P-200
20
52292667 Splitter (fan-out)
SMCA-16P-04P-005-
2
0.5 4x1.5 16P+T – CEE
3P+T
male – female
52292669 Control-box (pickle) with
E-Stop
SMBA-04P-04P-005
Z3015101
0.5 4x1.5 CEE 3P+T – CEE
3P+T
Male – female
52292661 Extension 4 motors
SMCA-16P-16P-100
10 16x1.5 16P+T – 16P+T
male – female
52292662 Extension 4 motors
SMCA-16P-16P-200
20
HARTING
Accessories for FL..PRMLV SR controllers
52293740
Control box B (pickle)
with E-stop
SMBA-04P-HOI-005
Z3015103
0.5 4x15 CEE 3P+T
Femelle
52292663
Motor extension cable
SMCA-04P-04P-100
10 4G2.5 CEE 3P+T
Male – Female
52292664
Motor extension cable
SMCA-04P-04P-200
20
52292853
Control extension cable
SMCA-04P-04P-A1
10 2.5 CEE 3P+T
Male – Female
52292864
Motor extension cable
SMCA-04P-04P-A1
20 2,5
HARTING
HARTING
2004.07 RPRMSR GB 15

STAGEMAKER CONTROLLER
10 CABLE CONNECTION DATA
Controllers R.. and FL.. single motor
cable with CEE plugs for power
Wires Colour Pin n°
L1 / U1 brown 1
L2 / V1 blue 2
L3 / W1 black 3
PE yellow/green PE
Controllers R.. fan-out
Wires Colour Pin n°
L1 brown 1
L2 blue 2
L3 black 2
GND yellow/green 4
L1 brown 5
L2 blue 6
L3 black 7
GND yellow/green 8
L1 brown 9
L2 blue 10
L3 black 11
GND yellow/green 12
L1 brown 13
L2 blue 14
L3 black 15
GND yellow/green 16+PE
Controllers FL.. single cable with CEE
plugs for control
Wires Colour Pin n°
Common brown 1
Motion Up blue 2
Motion Down black 3
PE yellow/green PE
Controllers R.. multi cable, extension
cable for 4 motors
Wires Wire n° Pin n°
L1 1 1
L2 2 2
L3 3 2
GND 4 4
L1 5 5
L2 6 6
L3 7 7
GND 8 8
L1 9 9
L2 10 10
L3 11 11
GND 12 12
L1 13 13
L2 14 14
L3 15 15
GND 16
16+PE
Controllers FL.. single cable with
Harting plugs for power & control
Wires Pinn°
L1 1
L2 2
L3 3
Common 4
Motion Up 5
Motion Down 6
PE yellow/green PE
Note :
These tables should be respected at any
time to avoid damage to the hoists or
ntrollers !co
2004.07 RPRMSR GB 16

STAGEMAKER CONTROLLER
11 TROUBLE SHOOTING
If your controller doesn’t work, check;
• the power source : all three lamps should blink
• the fuses : switch bar in upper mode
• thermal protection : red default lights
• if the emergency button is pressed : turn anticlockwise and pull
• pre-selection switch settings : up or down mode
• output cables : connected
• channel selector : in correct mode
• manual – remote switch : in correct position
• batteries in remote set : charged
Warning: Before going in the panel it self, or removing the top plate, first disconnect the m in
power entry plug.
a
12 SPECIFICATIONS
• Power supply : 400Vac-3f – 50 Hz
or 230Vac-3f – 50Hz
• Controls direct switching models : solid state with contactor output
• Controls remote switching models : radio
• Maximum switching capacity : 1.75 kW per channel at 400 V
0.9 kW per channel at 230 V
2004.07 RPRMSR GB 17
This manual suits for next models
5
Table of contents
Popular Remote Control manuals by other brands
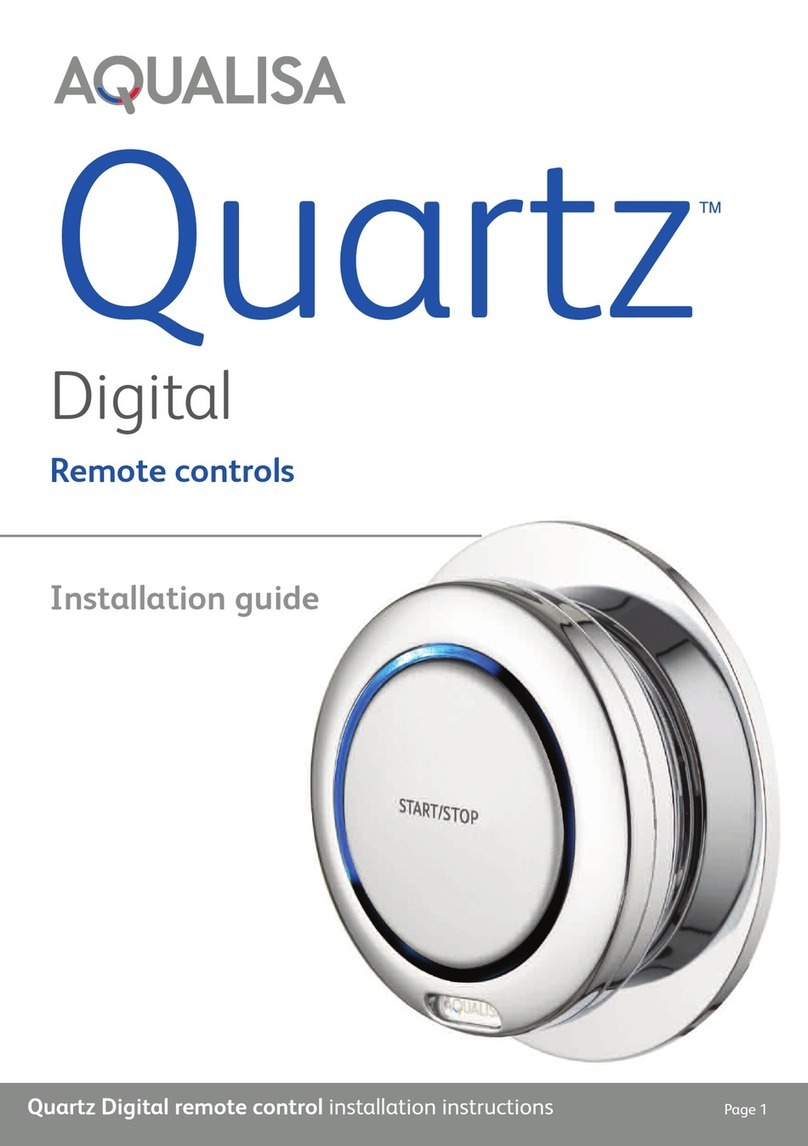
Aqualisa
Aqualisa Quartz Digital QZD.B3.DS.14 installation guide

Chamberlain
Chamberlain E940C quick start guide
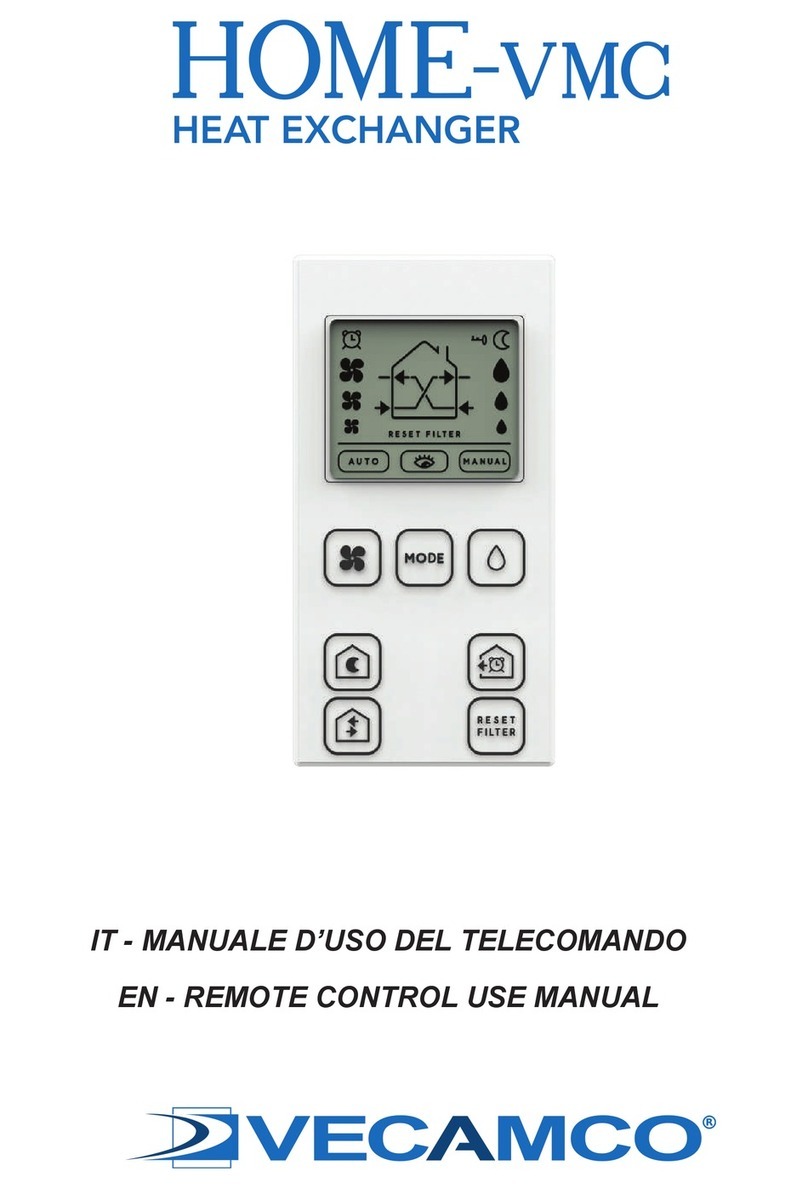
Vecamco
Vecamco HG60 S user manual

Monte Carlo Fan Company
Monte Carlo Fan Company MCRC1R series Installation and operation instruction
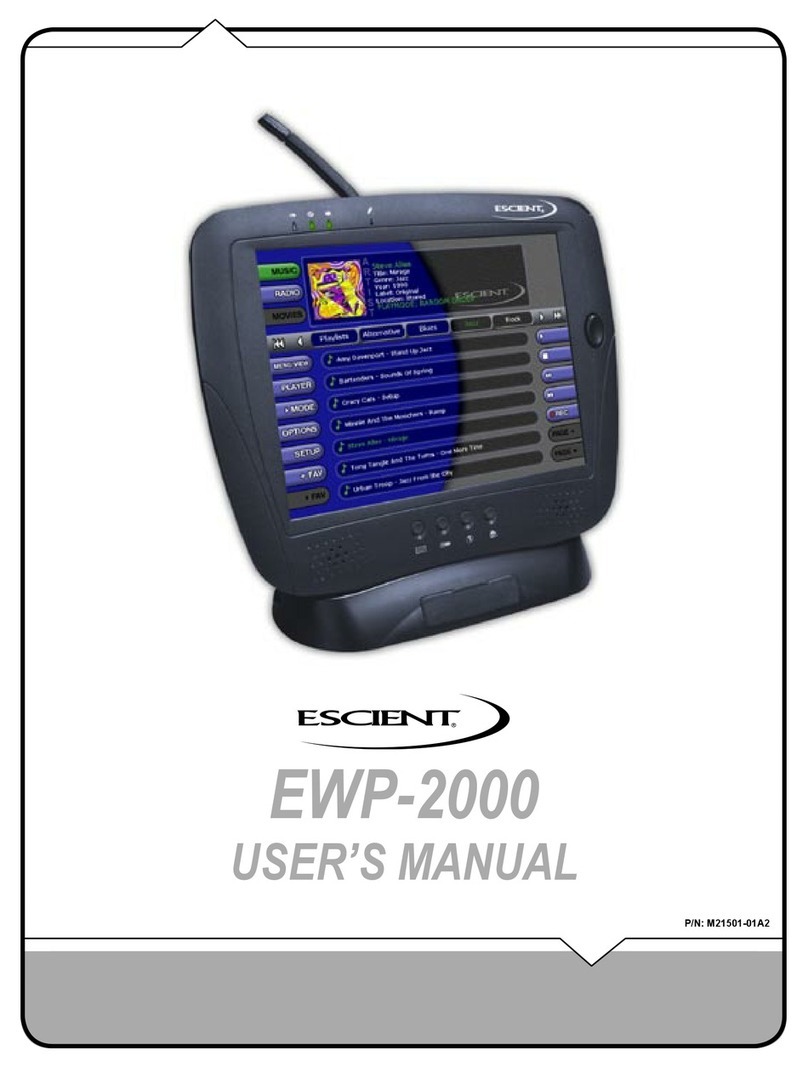
Escient
Escient EWP-2000 user manual
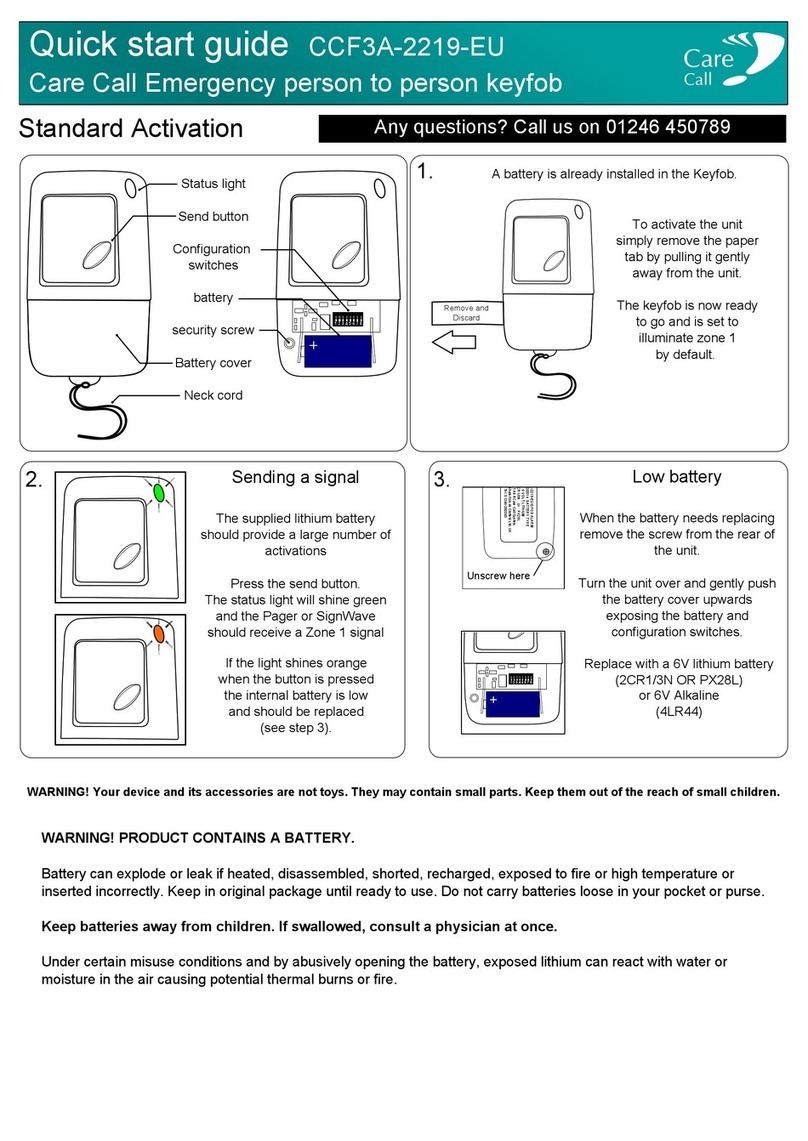
Care Call
Care Call CCF3A-2219-EU quick start guide