Vertical Express ICON 32 User manual

Controller

Every attempt has been made to ensure that this documentation is as accurate and up-to-date as
possible. However, Vertical Express assumes no liability for consequences, directly or indirectly,
resulting from any error or omission. The material contained herein is subject to revision. Please report
any problems with this manual to Vertical Express, P.O. Box 2019, Memphis, Tennessee 38101.
Vertical Express • P.O. Box 2019 • Memphis, Tennessee 38101
©2020 Vertical Express. All rights reserved.
Published April 2020
First Edition
Printed in the United States of America
Manual Number: 88500 v.1.0

INSTALLATION SECTION

INSTALLATION SECTION

Installation Section Contents
Vertical Express Product Manual 1-1 88500 v.1.0
Contents
Preliminary Installation . . . . . . . . . . . . . . . . . . . . . . . . . . . . . . . . . . . . . . . . . . . . . . . . . . . . . 1-3
Prepare for Temporary Operation . . . . . . . . . . . . . . . . . . . . . . . . . . . . . . . . . . . . . . . 1-3
Configure the UPS . . . . . . . . . . . . . . . . . . . . . . . . . . . . . . . . . . . . . . . . . . . . . . . . . . 1-5
Temporary Operation . . . . . . . . . . . . . . . . . . . . . . . . . . . . . . . . . . . . . . . . . . . . . . . . . . . . . . 1-6
Runbug Set Up . . . . . . . . . . . . . . . . . . . . . . . . . . . . . . . . . . . . . . . . . . . . . . . . . . . . 1-6
Electronic Starter Setup . . . . . . . . . . . . . . . . . . . . . . . . . . . . . . . . . . . . . . . . . . . . . 1-10
Mechanical Starter Set Up with ESP200 Overloads . . . . . . . . . . . . . . . . . . . . . . . . . 1-11
Pump Motor Rotation . . . . . . . . . . . . . . . . . . . . . . . . . . . . . . . . . . . . . . . . . . . . . . . 1-13
I-2/I-3 Valve . . . . . . . . . . . . . . . . . . . . . . . . . . . . . . . . . . . . . . . . . . . . . . . . . . . . . . . . . . . . 1-14
Relief Pressure Verification . . . . . . . . . . . . . . . . . . . . . . . . . . . . . . . . . . . . . . . . . . . 1-15
Low Pressure Adjustment . . . . . . . . . . . . . . . . . . . . . . . . . . . . . . . . . . . . . . . . . . . 1-15
Selector Tape . . . . . . . . . . . . . . . . . . . . . . . . . . . . . . . . . . . . . . . . . . . . . . . . . . . . . . . . . . 1-17
Mount the Tape . . . . . . . . . . . . . . . . . . . . . . . . . . . . . . . . . . . . . . . . . . . . . . . . . . . 1-17
Hoistway Wiring . . . . . . . . . . . . . . . . . . . . . . . . . . . . . . . . . . . . . . . . . . . . . . . . . . . . . . . . . 1-20
Wireway and Conduit Layout . . . . . . . . . . . . . . . . . . . . . . . . . . . . . . . . . . . . . . . . . 1-21
Typical Hoistway Conduit/Duct Layout . . . . . . . . . . . . . . . . . . . . . . . . . . . . . . . . . . 1-22
Typical Front Conduit/Duct Layout . . . . . . . . . . . . . . . . . . . . . . . . . . . . . . . . . . . . . 1-23
Typical Rear Conduit/Duct Layout . . . . . . . . . . . . . . . . . . . . . . . . . . . . . . . . . . . . . . 1-24
Interlock Wiring . . . . . . . . . . . . . . . . . . . . . . . . . . . . . . . . . . . . . . . . . . . . . . . . . . . 1-25
Traveling Cable Installation . . . . . . . . . . . . . . . . . . . . . . . . . . . . . . . . . . . . . . . . . . 1-27
Hoistway Entrance Frames and Doors . . . . . . . . . . . . . . . . . . . . . . . . . . . . . . . . . . . . . . . . . 1-28
Cab . . . . . . . . . . . . . . . . . . . . . . . . . . . . . . . . . . . . . . . . . . . . . . . . . . . . . . . . . . . . . . . . . . 1-28
Door Operator . . . . . . . . . . . . . . . . . . . . . . . . . . . . . . . . . . . . . . . . . . . . . . . . . . . . . . . . . . 1-28
Selector Box Mounting and Alignment . . . . . . . . . . . . . . . . . . . . . . . . . . . . . . . . . . . . . . . . . 1-28
Formed Rail Selector Box . . . . . . . . . . . . . . . . . . . . . . . . . . . . . . . . . . . . . . . . . . . . 1-29
T-Rail Selector Box . . . . . . . . . . . . . . . . . . . . . . . . . . . . . . . . . . . . . . . . . . . . . . . . 1-30
Twin Post Selector Box . . . . . . . . . . . . . . . . . . . . . . . . . . . . . . . . . . . . . . . . . . . . . . 1-31
Tape Selector Bolt Kit for Crosshead Mount (200BWY001) . . . . . . . . . . . . . . . . . . . 1-32
Car Top Wiring . . . . . . . . . . . . . . . . . . . . . . . . . . . . . . . . . . . . . . . . . . . . . . . . . . . . . . . . . . 1-33
Swing Return Wiring . . . . . . . . . . . . . . . . . . . . . . . . . . . . . . . . . . . . . . . . . . . . . . . 1-34
Machine Room Wiring . . . . . . . . . . . . . . . . . . . . . . . . . . . . . . . . . . . . . . . . . . . . . . . . . . . . 1-34

1-2©Vertical Express Printed in USA April 2020
Contents Installation Section
This page
intentionally
left blank.

INSTALLATION
Vertical Express Product Manual 1-3 88600 v.1.0
Installation Section Preliminary Installation
Preliminary Installation
Install the following items. Refer to the Vertical Express Installation Manual (located
at: http://www.verticalxpress.com/component_manuals/Installation Manual), and
the installation instructions that ship with the equipment.
• Pit template (if provided), pit channel, and buffers
• Jack, jack follower guides (as required), rail brackets and rails
• Car sling and platform
•Powerunitandcontroller
• Fluid line (jack line)
Prepare for Temporary Operation
1. Turn OFF, Lockout, and Tagout the mainline disconnect.
2. Pipe and install power from the mainline disconnect to the controller.
See Figure 2 on page 1-4.
• Conduit for the wires from the mainline disconnect must be installed on the
same side of the controller cabinet as the motor starter.
• The fourth wire ground from the disconnect is to be landed on the dedicated
ground bar of the controller, not the motor starter heatsink.
3. Verify that CON19, CON20, and CON21 are removed on the IOF Card. See
Figure 1.
Figure 1 - IOF Card Connectors
CON19 CON20 CON21

Preliminary Installation Installation Section
©Vertical Express 1-4 Printed in USA April 2020
Prepare for Temporary Operation
(continued)
Figure 2 - Power from Mainline Disconnect to the Controller
Mainline Disconnect Power
Connection to Controller
UPS Electrical Cords
Pass Through Knockout
UPS installed on the underside of the controller
(use the shipping bracket and screws to mount)
High Voltage In
(from knockouts in this
corner of the controller)
High Voltage Wire Routing
(straight down to the
electronic motor or
contactor starter)
Trades Access Terminal Strip
(through controller top panel)
Low Voltage In
(from knockouts on this
side of the controller)
NOTE: If the THY-02 Card (6300ACA2)
obstructs the low voltage wiring,
move the card to the DIN rail.
Ground Bar
Low Voltage
Wire Routing
(as needed)
HIGH VOLTAGE SIDE LOW VOLTAGE SIDE

INSTALLATION
Vertical Express Product Manual 1-5 88600 v.1.0
Installation Section Preliminary Installation
Installation
(continued) Configure the UPS
1. When on temporary operation, connect the following:
a. The AC receptacle cord from the IOF Card - CON18, pins 1, 2, and 3.
b. The AC plug from the IOF Card - CON18, pins 4, 5, and 6.
• The UPS should not be in the AC circuit during temporary operation. See
Figure 3.
• If battery lowering is not required for the job, no UPS will be provided.
• When battery lowering is not present, Manufacturing installs jumper wires
from CON18 pin 1 to pin 4, pin 2 to pin 5, and pin 3 to pin 6 on the IOF Card.
• The UPS may be mounted below the controller - Use the shipping bracket
and screws to hold the UPS in place, and wire the plug through a knock
out in the bottom of the controller.
Figure 3 - UPS Unit Connections
2. Use a temporary jumper to connect EPD1 and EPD2 (located in the Trades
Access Panel, on the top of the controller). See Figure 4.
The EPD1 and EPD2 jumper will be replaced by an auxiliary set of contacts in the dis-
connect to prevent the control system from operating on any form of alternate power
when the disconnect is in the OFF position.
Figure 4 - EPD1/EPD2 Jumpers
EPD1 & EPD2
Jumpers

Temporary Operation Installation Section
©Vertical Express 1-6 Printed in USA April 2020
Temporary Operation
Only connect the approved thyssenkrupp pendant station (runbug, part number
9817323) for temporary operation. The pendant station connects directly to the
IOF Card (bottom left corner) at the connector “RUNBUG.”
Runbug Set Up • For Electronic Starters - Confirm that there are Manufacturing installed temporary
run jumpers between MUTS/USS1 and 134/MCC1. See Figure 5.
• For Across The Line Starters - See Figure 6 on page 1-7.
Figure 5 - Temporary Operation Pendant Station (RUNBUG) Connection for Electronic Motor Starting
AC2
RUN/STOP
ON/OFF
KEYSWITCH
ENABLE
REMOTE
INSPECTION
(RUNBUG)
IOF
FROM XFMR1 OR UPS
FROM XFMR1 OR UPS
MOTOR
PROTECTION
ADD WHEN
ON RUNBUG
MACHINE-ROOM
EPD's
HOISTWAY
EPD's
CAR
EPD's
NO JUMPER
ON RUNBUG
BYPASSED
BYPASSED
BYPASSED
MCC2 MC2
AC2
TR6
MCE
DSS1
DSS1
9:6
AC2
TR5
TR1
TR2
SCG2
9:2
121
9A:1
USS1
134134
USS1
TSRCPU
DOWN SLOW
MCD
DSS2
UP SLOWUP SLOW
MCC1
MCC2MCC2
MCC2
9:1
TR4
MCC1MCC1
MCF
RUN INPUT
FAULT
EMS?
FAULT
POWER
UP TO SPEED
SOFT START
-
9-10
-11
-
4-12
-
2
-
1
-3
-
5-6
-
7-8
USS2
TR3
RT
G24
131
9:5
AC2 EPEN
115
AC1SC
9:3
107
115
F-AC1SC
AC2
18:5
RUN/STOP
SAFSP
107
SAFCPU
102
AC2
9:4
X1
18:4
121
MUTS
131131
131
9A:2
MCE
INPUT x1
CPU
MCD
INPUT x1
CPU
MCF
INPUT x1
CPU
MUTS
INPUT x1
CPU
Note: COLOR CODING shown is for
9817323 run button units; other brands
must be wired according to CON TR
pin assignments.
(WHT)
(BLU)
(ORG)
(BLK)
(RED/BLK)
(WHT/BLK)
ADD WHEN
ON RUNBUG
DOWN UP

INSTALLATION
Vertical Express Product Manual 1-7 88600 v.1.0
Installation Section Temporary Operation
Runbug Set Up
(continued) • For Across The Line Starters - Confirm that there are Manufacturing installed
temporary run jumpers between 134, MCC1 and USS1. See Figure 6.
• The EPEN relay is energized by input EPD2 from the Trades Access Panel.
• On runbug, the CPU Card operation/faults is irrelevant to Up and Down oper-
ation because the operation is dependent on 120VAC discrete feed to relays
and solenoids from the pendant station.
Figure 6 - Temporary Operation Pendant Station (RUNBUG) Connection for Across the Line Motor Starting
AC2
AC2
RUN/STOP
ON/OFF
KEYSWITCH
ENABLE
FROM XFMR1 OR UPS
FROM XFMR1 OR UPS
TSRCPU
TR4
MC1AUX
13 14
MC2AUX
21 22
131
UP SLOW
EPEN
AC2
SAFSP SAFCPU RUN/STOP
AC2
18:2
121
121
9A:1
MCE
INPUT x1
CPU
TR3
131
9:5
RT
AC1SC
9:3
AC2
9:4
MC2
MC1
TR1
SCG2
MCE
MCF
MCC2
DSS1
G24
MCC1
MCD
MCC2
DOWN SLOW
X1
18:3
TR5
MC2AUX
13 14
9:2
TR6
9:1
9:6
TR2
DSS1
USS2
MUTS
USS1
AC2
USS1
DSS2
131
9A:2
102
MC1AUX
21 22
F-AC1SC
MCC1
107
115
115
107
MCC2
134
MCD
INPUT x1
CPU
MCF
INPUT x1
CPU
MUTS
INPUT x1
CPU
(on Across the Line with
2 Contactors only).
(WHT/BLK)
(RED/BLK)
(WHT)
(BLU)
(ORG)
(BLK)
NO JUMPER
ON RUNBUG
DOWN UP
REMOTE
INSPECTION
(RUNBUG)
Note: COLOR CODING shown is for
9817323 run button units; other brands
must be wired according to CON TR
pin assignments.
ADD WHEN
ON RUNBUG
ADD WHEN
ON RUNBUG
IOF
MOTOR
PROTECTION
MACHINE-ROOM
EPD's
HOISTWAY
EPD's
CAR
EPD's
BYPASSED
BYPASSED
BYPASSED

Temporary Operation Installation Section
©Vertical Express 1-8 Printed in USA April 2020
Runbug Set Up
(continued) 1. Remove the plug at CON16 on the IOF Card. See Figure 7.
Figure 7 - IOF Card (6300AHV001)
Initial power application occurs in the next step. If incorrect, the electronic starter
may be damaged.
2. View the nameplate sticker on the electronic starter to determine its voltage rating,
and view the power unit data tag for the motor voltage rating.
a. Compare these ratings to the known building voltage provided at the disconnect.
Before continuing, correct as required.
Most electronic starters are rated at 200-460VAC (and for special applications up to
575VAC), and should not be damaged by incorrect voltage from the disconnect that is
within this range. However, Electronic Starter #787AF14 is rated for 200-230VAC, and
application of 3 phase voltage above that rating could damage it.
b. Turn ON the mainline disconnect.
3. Use a volt meter on the AC mode, and confirm that the secondary output from XFMR1
is between 108VAC and 132VAC.
If the voltage is not correct, do not continue until this issue is resolved.
4. Turn OFF the mainline disconnect.
5. Install the plug at CON16 on the IOF Card.
6. Remove CON9A, located at the bottom left corner of the IOF Card. Be sure to save
CON9A as it will be reinstalled after temporary operation.
CON16

INSTALLATION
Vertical Express Product Manual 1-9 88600 v.1.0
Installation Section Temporary Operation
Runbug Set Up
(continued) 7. Install the RUNBUG plug at CON9 on the IOF Card. See Figure 8.
Figure 8 - RUNBUG Plug at CON9 on the IOF Card
8. Fill the power unit fluid reservoir with the appropriate fluid for this job.
9. Turn ON the mainline disconnect.
10. Confirm that the AC LED is illuminated. See Figure 9.
Figure 9 - Illuminated AC LED on IOF Card
RUNBUG
Plug
AC LED

Temporary Operation Installation Section
©Vertical Express 1-10 Printed in USA April 2020
Electronic Starter Setup
For Across the Line Motor Starting, see Mechanical Starter Set Up with ESP200 Overloads on page 1 - 11.
Electronic Starter Display
• The electronic starter displays MOTOR STATUS STOPPED when the system is normal.
Reset the starter if it reads otherwise and, before continuing, correct any problem indi-
cated on the display.
• The starter display reverts to MOTOR STATUS STOPPED after 5 minutes of inactivity.
1. Verify that the Starting Amps = the Motor Nameplate Amps x 3 (Mfg. default).
Optional: 2 x FLA = minimum setting, 4.5 x FLA = maximum setting.
2. From the MOTOR STATUS menu, press . The STATUS menu displays.
3. Press
twice to display the PARAMETERS menu.
4. From the PARAMETERS menu, press once. STARTING AMPS displays.
5. Set the starting amps value equal to three times the nameplate FLA.
a. Press once to access the value.
b. Press or to adjust the value of the flashing digit. Press to move to the
next digit.
c. Press to exit the starting amps parameter.
A prompt to ACCEPT or REJECT the change displays. Press to accept or to reject
and correct the parameter.
EXIT MENU
OR SAVE
SCROLL DOWN
SCROLL UP
ENTER MENU
MOTOR STATUS
STOPPED

INSTALLATION
Vertical Express Product Manual 1-11 88600 v.1.0
Installation Section Temporary Operation
Electronic Starter Setup
(continued)
6. Press
once and OVERLOAD AMPS displays.
a. If the value is correct, skip to Step 8.
b. If the value is not correct, continue to Step 7.
7. Press
once to access the value.
a. Press or to adjust the value of the flashing digit.
b. Press to move to the next digit.
8. Press
to exit to the PARAMETERS Menu.
A prompt to ACCEPT or REJECT the change appears. Pressto accept, or to
reject and correct the parameter.
Mechanical Starter Set Up with ESP200 Overloads
Overload relay current settings are preset by Manufacturing. The following initial
adjustment can also be used during temporary operation for jobs that trip overloads,
but the actual overload current will be set during final adjustment.
1. Use Table 1 below or Table 2 on page 1 - 12 to determine the overload relay cur-
rent setting based on the motor horsepower and voltage or nameplate amps.
2. Set the full load amps adjustment dial to the overload current setting from
Step 1. See Figure 10.
Figure 10 - ESP200 Overload Adjustment
Table 1 - Overload Specifications For Single Phase Motors
Full Load Amps
Adjustment Dial
Motor
HP
Motor Voltage
(50 or 60 Hz)
NEC Motor NP
Rated Amps
Wiring
Configuration
Overload
Current Setting
7.5 200V/208V 46
Special,
See Wiring Diagrams
50
230 40 43
10 200V/208V 58 62
230 50 54

Temporary Operation Installation Section
©Vertical Express 1-12 Printed in USA April 2020
Mechanical Starter Set Up with ESP200 Overloads
(continued)
Table 2 - Overload Specifications For ESP 200 Overload Applications
Motor
HP
Motor Voltage
(50 or 60 Hz)
NEC Motor NP
Rated Amps
Line or Phase
Wiring
Configuration
Overload
Current
Setting
Motor
HP
Motor Voltage
(50 or 60 Hz)
NEC Motor NP
Rated Amps
Line or Phase
Wiring
Configuration
Overload
Current
Setting
5
200V/208V 17.5 Line 25.0
30
200V/208V 92 Line 131.6
220V 15.9 Line 22.8 220V 84 Line 120.1
230V 15.2 Line 21.7 230V 80 Line 114.4
380V 9.2 Line 13.2 380V 48 Line 68.6
415V 8.4 Line 12.1 415V 44 Line 62.9
460V 7.6 Line 10.9 460V 40 Line 57.2
575V 6.1 Line 8.7 575V 32 Line 45.8
7.5
200V/208V 25 Line 35.8
40
200V/208V 120 Phase 99.1
220V 23 Line 32.9 220V 109 Phase 90.0
230V 22 Line 31.5 230V 104 Phase 85.9
380V 13 Line 18.6 380V 63 Line 90.1
415V 12 Line 17.2 415V 57 Line 81.5
460V 11 Line 15.7 460V 52 Line 74.4
575V 9 Line 12.9 575V 41 Line 58.6
10
200V/208V 32 Line 45.8
50
200V/208V 150 Phase 123.8
220V 29 Line 41.5 220V 136 Phase 112.3
230V 28 Line 40.0 230V 130 Phase 107.3
380V 17 Line 24.3 380V 79 Line 113.0
415V 15 Line 21.5 415V 72 Line 103.0
460V 14 Line 20.0 460V 65 Line 93.0
575V 11 Line 15.7 575V 52 Line 74.4
15
200V/208V 48 Line 68.6
60
200V/208V 177 Phase 146.0
220V 44 Line 62.9 220V 161 Phase 132.9
230V 42 Line 60.1 230V 154 Phase 127.1
380V 25 Line 35.8 380V 93 Line 133.0
415V 23 Line 32.9 415V 85 Line 121.6
460V 21 Line 30.0 460V 77 Line 110.1
575V 17 Line 24.3 575V 62 Line 88.7
20
200V/208V 62 Line 88.7
75
200V/208V 221 Phase 180.0
220V 56 Line 80.1 220V 201 Phase 166.0
230V 54 Line 77.2 230V 192 Phase 158.0
380V 33 Line 47.2 380V 116 Phase 95.8
415V 30 Line 42.9 415V 106 Phase 87.5
460V 27 Line 38.6 460V 96 Phase 79.3
575V 22 Line 31.5
25
200V/208V 78 Line 111.5
220V 71 Line 101.5
230V 68 Line 97.2
380V 41 Line 58.6
415V 37 Line 52.9
460V 34 Line 48.6

INSTALLATION
Vertical Express Product Manual 1-13 88600 v.1.0
Installation Section Temporary Operation
Pump Motor Rotation
Swapping motor leads to correct motor rotation will result in a motor wiring
fault. Motor rotation is controlled through adjustments in the starter and
also the line input to the starter.
1. Turn ON the mainline disconnect.
2. Momentarily press UP and SAFE on the temporary run box, and observe the
direction of the motor rotation (clockwise rotation is standard for Vertical Express
equipment when viewed from the shaft end).
ABC = Standard Dry (AP) units (CW rotation as viewed from the shaft end). The
motor is mounted to the left of the pump.
CBA = Standard Wet (EP) units (CCW rotation as viewed from the pump end).
– If the motor rotation is correct, continue to Step 5.
– If the rotation is incorrect, complete the appropriate procedure below.
• For Mechanical Starters - Reverse L1 and L2 on the starter.
• For Electronic Starters - Change the line rotation setting in the starter.
a. Press once. The STATUS menu displays.
b. Press twice. The PARAMETERS menu displays.
c. Press and STARTING AMPS displays.
d. Press until LINE ROTATION displays.
e. Press to access the value.
f. Press for CBA. (CBA = standard wet unit.)
g. Press to select the value displayed.
h. Press to accept the value, or to reject the change. If the wrong value is
accepted, repeat steps e. through h.
3. Verify the correct motor wiring. See Figure 11 on page 1-14.
4. Check the motor rotation direction. If the direction is incorrect or if the
motor is making loud sounds, swap two phase leads at the top of the con-
troller’s main line fuses (FL1 - FL3).
5. Confirm the motor rotation. It may take multiple attempts to get the incoming line
phase relationship correct.

I-2/I-3 Valve Installation Section
©Vertical Express 1-14 Printed in USA April 2020
Pump Motor Rotation
(continued)
Figure 11 - Electronic Starter Pump Motor Wiring Diagram
I-2/I-3 Valve
The I-2/I-3 Valve is preset by Manufacturing, assembled on the power unit, and has been
tested and adjusted. The presets are attached inside the controller, ensure movement of
the car, and reduce final adjustment time.
• The I-2/I-3 Valve requires a minimum static system pressure of 90 PSI to function
properly.
• Adjust and confirm the Relief Pressure and Low Pressure on each job—at this
time if possible.
• If the empty sling is too light to achieve 90 PSI, defer the Low Pressure adjustment
until the cab is installed and 90 PSI is achieved.
• Valves by other manufacturers: refer to the applicable valve product manual for
initial setup - Bypass/Low Pressure and Relief Pressure Adjustments.
Electronic
Motor
Starter
L1 L2 L3
T1 T2 T3
MC2
T3
T1
T2
T4
T5
T6
5
2
31
46

INSTALLATION
Vertical Express Product Manual 1-15 88600 v.1.0
Installation Section I-2/I-3 Valve
I-2/I-3 Valve
(continued) Relief Pressure Verification
This preliminary check is to ensure that the pipe couplings and valve will not be dam-
aged if the elevator system’s oil flow or platform become restricted. The final check
for the relief pressure is set with the procedure Final Relief Pressure with Full Load on
page 2-33.
1. Close the shut-off valve.
2. Install a pressure gauge on the silencer's quick connect.
Immediately stop the power unit if the pressure exceeds 625 PSI.
3. While monitoring the pressure gauge, run the power unit in the up direction from
the runbug in short bursts. Once confirmed that the pressure will not exceed 625
PSI, the pump motor can run constantly to verify the relief pressure setting.
4. Adjust the pressure relief (if necessary) to reduce pressure below 625 PSI.
a. IN (CW) = Increase Relief Pressure
b. OUT (CCW) = Decrease Relief Pressure
5. Briefly open the Manual Lowering Valve to relieve pressure from the valve, and
confirm that the valve is fully closed when finished.
Low Pressure Adjustment
When operating elevator from the controller, follow all safety precautions.
• If the low pressure adjustment is made with the CPUC online, temporarily set
the Z44 timer to 10 seconds, and run the motor less than 10 seconds at a
time from Inspection Operation.
• OUT = Counterclockwise, CCW
IN = Clockwise, CW
1. Ensure that the car is empty and the manual lowering valve is closed.
2. Turn OFF, Lockout, and Tagout the mainline disconnect.
3. Disconnect CON15 (on the IOF Card in the controller) to disable the
valve’s up slow solenoid.
4. Turn the Low Pressure adjustment screw OUT 13/4" beyond the cover
plate. See Figure 12 on page 1-16.
5. Turn the Low Pressure adjustment screw IN by hand until it touches the regu-
lator piston.

I-2/I-3 Valve Installation Section
©Vertical Express 1-16 Printed in USA April 2020
Low Pressure Adjustment
(continued)
6. Turn the power ON, and use the runbug to start the motor.
7. Turn the Low Pressure adjustment screw IN just until the car starts to move.
8. Turn the Low Pressure adjustment screw OUT until the car movement stops.
9. After the car stops, turn the Low Pressure adjustment screw OUT an additional one-
half turn.
10. Tighten the locknut.
11. Stop the motor, and turn the power OFF.
12. Reconnect CON15 to enable the valve’s up slow solenoid.
Figure 12 - I-2/I-3 Valve
Low Pressure
Adjustment
Manual Lowering Valve
Lowering & Leveling
Speed Adjustment
Down Slowdown
Adjustment
Down Stop
Adjustment
Up Leveling
Adjustment
Down Start
Adjustment
Up Start
Adjustment
Up Stop
Adjustment
Up Slowdown
Adjustment
High Pressure
Relief Adjustment
Table of contents
Popular Controllers manuals by other brands

Brightlink
Brightlink BL-VW37-4K operating instructions
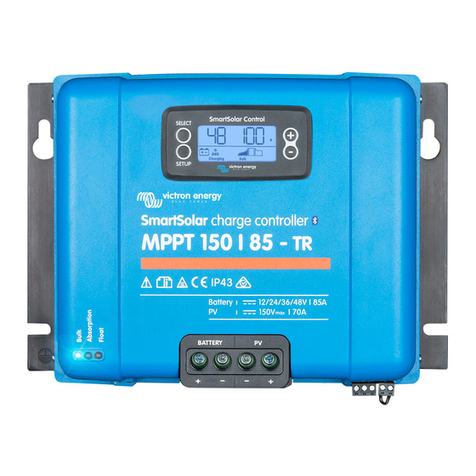
Victron energy
Victron energy BlueSolar MPPT 150/70-Tr manual
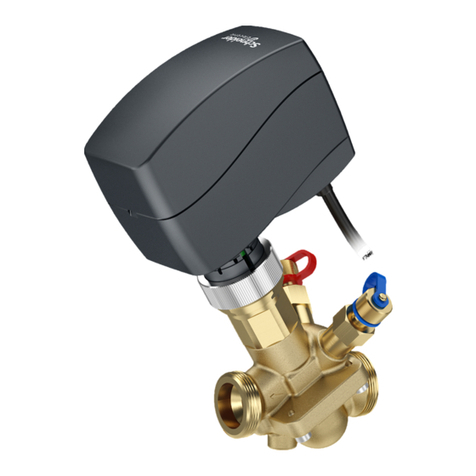
Daikin
Daikin DKN-MP130-24MP installation instructions
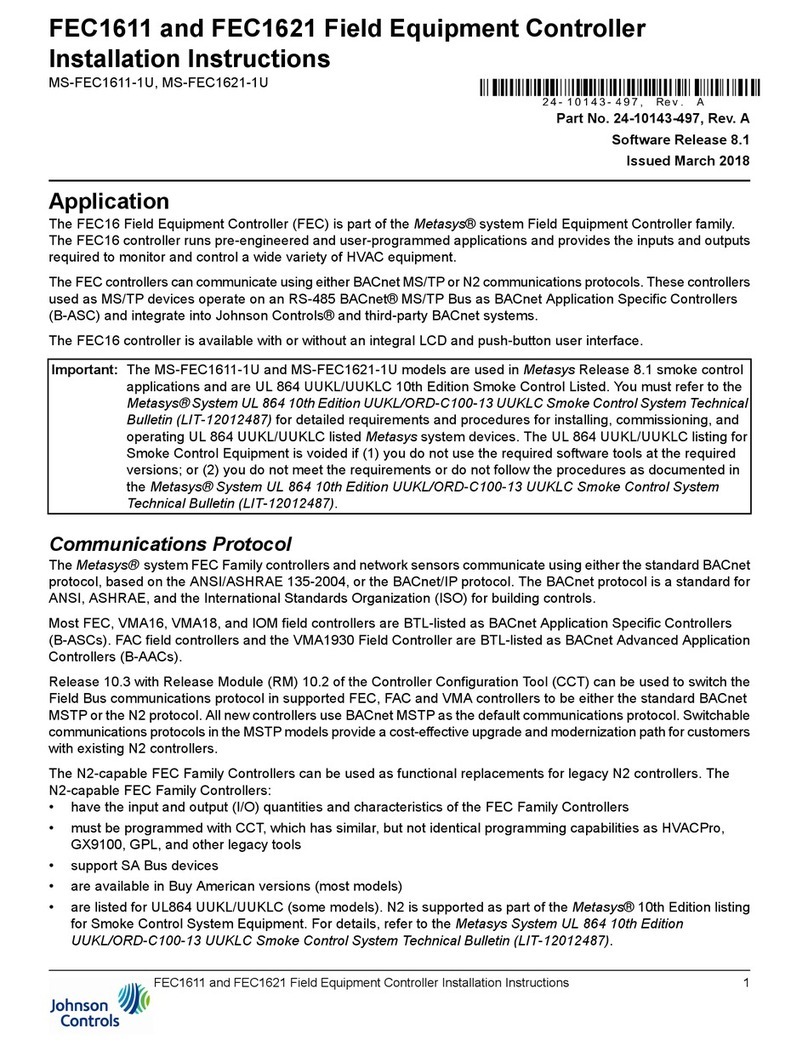
Johnson Controls
Johnson Controls MS-FEC1611-1U installation instructions

Emerson
Emerson Dixell XR20T Installing and operating instructions
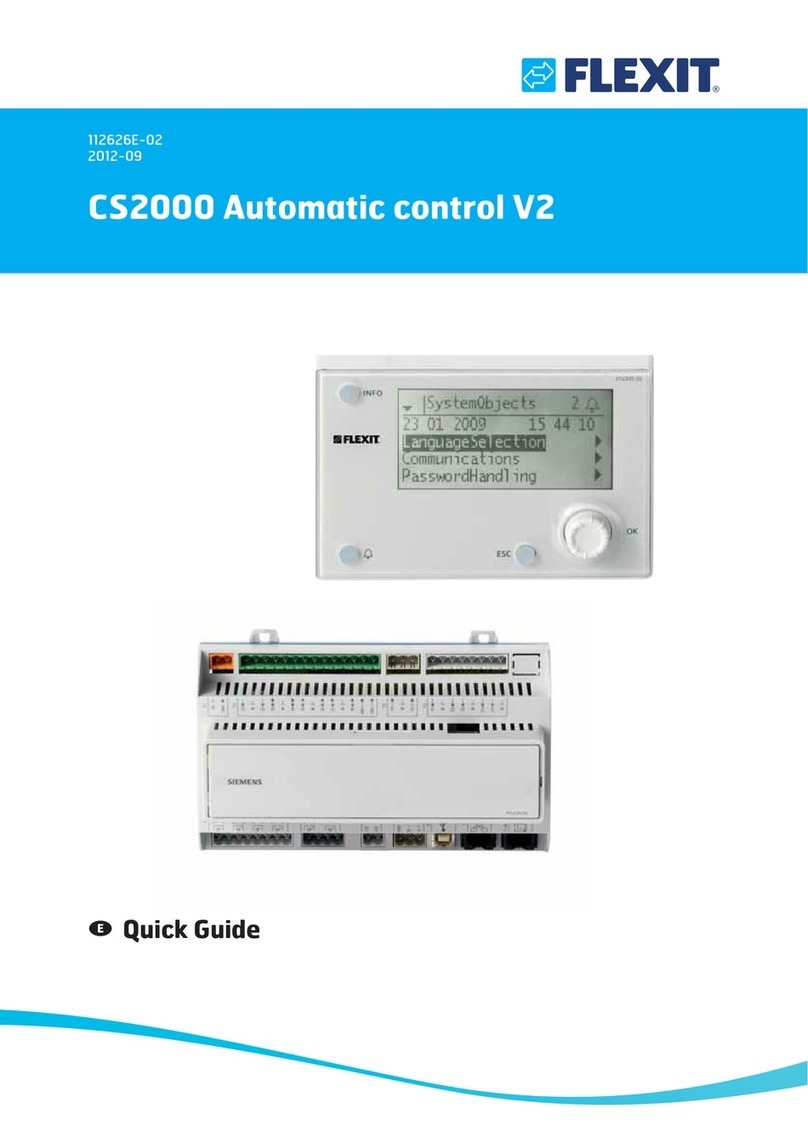
Flexit
Flexit CS2000 quick guide
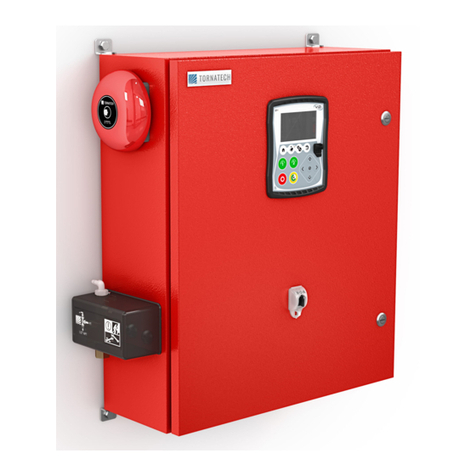
Tornatech
Tornatech GFD Installation and maintenance manual
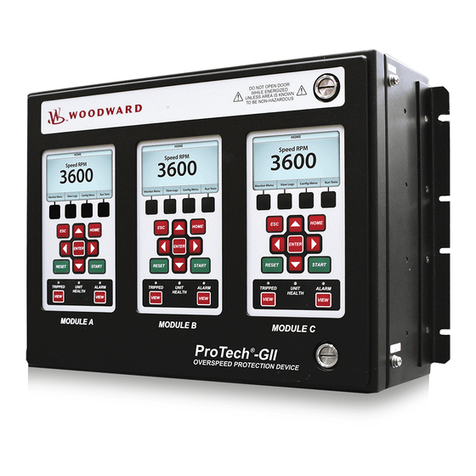
Woodward
Woodward ProTech-GII Installation and operation manual

Prolon
Prolon PL-M2000 Series installation guide
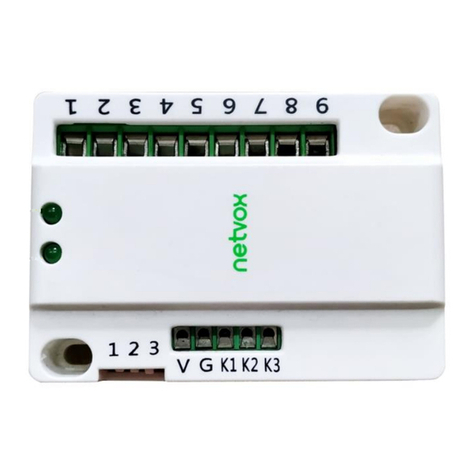
netvox
netvox R831A user manual
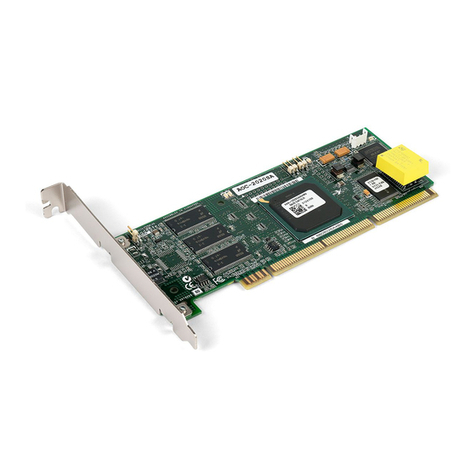
Adaptec
Adaptec 2025ZCR - SCSI RAID Storage Controller Installation and user guide
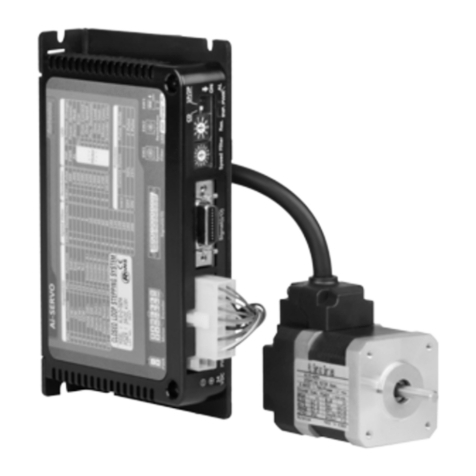
Autonics
Autonics AiS Series manual