White HB 300 Series Operating instructions

White Drive Products, Inc. • P.O. Box 2700 • Hopkinsville, KY 42241 • Phone: 270.885.1110 • Fax: 270.886.8462
Remove all shaft related components from shaft (27) (i.e. keys, wire rings, nuts). To aid in reassembly of the motor, make a “V”
shaped set of lines from the endcover to the housing using either paint or a marker. With shaft facing down, secure motor in vise
by clamping on to housing (16). Loosen and remove four bolts (26) holding motor assembly together. Remove endcover (24)
from motor making sure not to drop endcover piston (22). Using needle nose pliers or two small screwdrivers, lift endcover piston
(22) out of endcover (24). Remove white Teflon seal (11) and O-ring seal (10) from endcover piston (22) and discard. Remove the
piston spring (23) from endcover (24) and lay aside.
Lift commutator container and commutator (21) from motor and lay aside. Place commutator on a flat, clean surface with the
seal (9) facing up. Place the tip of a small screwdriver on the seal (9) and gently tap until opposite side of seal lifts from groove.
Remove seal (9) and discard.
Remove manifold (20), rotor assembly (19) and wear plate (17) from motor. Remove all seals (8) from components and discard.
(Caution - Do not allow rolls to drop from rotor assembly when removing rotor assembly for motor.) Remove drive link (18) from
motor and lay aside. Remove the thrust bearing (14) and thrust washer (13) from the housing (16) and lay aside. From front of
housing, gently tap shaft (27) upwards and remove through rear of housing.
Remove housing (16) from vise and lay on flat surface with dust seal (1) facing up. Using a small thin screwdriver, carefully pry
the dust seal (1) from the seal carrier (12) and discard. Using an arbor press and a sleeve, press the seal carrier (12) down into
the housing (16) approximately 6,4 [.250] until the wire ring (2) in the front of the housing (24) can be removed.
Using a small thin screwdriver, pry the wire ring (2) from the groove in the front housing (16). Also pry the backup shim (3) and the
high pressure seal (4) from the groove. Remove the seal carrier (12) from the housing bore and carefully pry the shaft seal (7),
Teflon backup seal (6) and backup shim (5) from the seal carrier (12) and discard the items (5,6 & 7). Remove two thrust washers
(13) and thrust bearing (14) from housing and lay aside.
At this point, all parts should be cleaned in an oil-based solvent and dried using compressed air (For safety, observe all OSHA
safety guidelines). All new seals should be lightly coated in clean oil prior to installation.
Using Figure 1 for correct orientation, install backup shim (5), Teflon backup seal (6) and shaft seal (7) into the seal carrier (12).
Place side of seal carrier (12) with seal down on a flat surface and press down to seat seals in seal carrier (12). Install the dust
seal (1) in the opposite side of the seal carrier (12) using Figure 1 for correct seal lip orientation. Make certain that shaft seal and
dust seal are coated with oil to provide start-up lubrication.
With the flange side of the housing face up, place one thrust washer (13), then thrust bearing (14) and second thrust washer (13)
against roller bearing in housing. Install the seal carrier assembly (5-7, 12) into the housing (16) making sure that the large O.D.
side faces down. Install the high pressure seal (4) into the housing groove. To install the metal backup shim (3), slightly squeeze
the shim between the thumb and forefinger to bow the shim. While maintaining the bow, start the shim into the groove and use a
small screwdriver to push the shim into the groove. Install the wire ring (2) into the groove making sure that the ends are butted.
Place the housing in an arbor press with the mounting flange side facing down. Press down on the rear housing bearing until it
is 4,2 - 5,2 [.164 - .205] below the surface of the housing. This distance allows for the placement of the thrust washer and thrust
bearing to be installed later.
With output end of shaft facing up, insert shaft into housing and press seal carrier down until it is seated against the wire ring in
the front groove. Remove shaft from housing. There should be 2,0 - 2,5 [.080 - .100] clearance between the rear-most thrust
washer (13) and the front shaft bearing (15) (See Figure 2). If the front shaft bearing is against the thrust washer, it must be
pushed back into the housing to provide the necessary clearance.
Mount the housing in a vise with the mounting flange side facing down. If a 1-1/4” or 32mm shaft is being installed, liberally coat
the output end of the shaft with STP®. (Make sure area around key slot is thoroughly coated before installing shaft into housing).
With the output end of the shaft facing down, insert into the housing. Place the remaining thrust washer (13) against the shaft end
followed by the remaining thrust bearing (14).
Place a body seal (8) into the groove in the rear face of the housing. Insert the drive link (18) into the shaft with the tapered end
facing up. Place the wear plate (17) over the drive link (18) and onto the housing making sure to use the alignment marks as a
guide to assure correct orientation of the wear plate (and the remaining components).
Place a body seal (8) into the groove in the face of the rotor assembly (19). With the seal side of the rotor assembly (19) facing
the wear plate, line up the splines of the drive link (18) and the rotor assembly (19) and lower the rotor assembly onto the housing
(16).
SERVICE INSTRUCTIONS FOR THE HB [300] SERIES MOTORS
PI333900 Rev. 2.06
For Use With Seal Kits: 300333900 & 300333900B
A)
B)
C)
D)
E)
F)
G)
H)
I)
J)
K)
L)
dimensions: mm [in]

White Drive Products, Inc. • P.O. Box 2700 • Hopkinsville, KY 42241 • Phone: 270.885.1110 • Fax: 270.886.8462
Place a body seal (8) into the groove in each face of the manifold (20). Lift the drive link (18) approximately 2,5 [.100] and place
the tip of a small screwdriver under the disk-shaped portion of the drive link to hold it up. Making sure that the notch in the
manifold is aligned with the notch in the rotor and that the side with the largest holes faces down. Lower the manifold (20) onto
the motor and engage the disk shaped portion of the drive link (18) into the groove in the manifold (20) (See Figure 3). Remove
the screwdriver and lower the manifold (20). If the disk is engaged in the groove, the end of the drive link will protrude above
the surface of the manifold. If it doesn’t, remove manifold and repeat this step. Using bolts or line up pins align the components
assembled thus far. Make sure that components are matching the “V” shape that you drew earlier and that the bolt holes are all
aligned. Once everything is aligned make sure that the drive link is still engaged in the manifold. (The motor will not operate if the
drive link is not engaged in the manifold).
Install the commutator seal (9) into the commutator (21) with the metal side facing up. Use finger pressure to press the seal down
flush with the surface of the commutator. Place the commutator container (21) onto the manifold (20) and then place the commu-
tator onto the protruding end of the drive link (18) making sure that the seal side faces up.
Install the remaining body seal (8) in the groove in the face of the endcover (24). Install the piston spring (23) into the endcover
(24), then the white Teflon seal (11), followed by the O-ring seal (10). Lining up the alignment pin, press the piston (22) into the
endcover (24). While holding the endcover piston (22) into the endcover (24), lower the endcover assembly onto the motor.
Install the four assembly bolts (26) and pre-torque to 13,6 Nm [10 ft. lb.] Final torque all bolts to 67,8 Nm [50 ft. lb.].
M)
N)
O)
P)
1. * Dust Seal
2. * Wire Ring
3. * Metal Backup Shim
4. * High Pressure Seal
5. * Metal Backup Shim
6. * Teflon Backup Seal
7. * Shaft Seal
8. * Body Seal (5)
9. * Commutator Seal
10. * O-Ring Seal
11. * Teflon Backup Seal
12. Seal Carrier
13. Thrust Washer (3)
14. Thrust Bearing (2)
15. Roller Bearing (2)
16. Housing
17. Wear Plate
18. Drive Link
19. Rotor Assembly
20. Manifold
21. Commutator Assembly
22. Piston
23. Piston Spring
24. Endcover
25. I.D. Tag Assembly
26. Assembly Bolts (4)
27. Shaft
28. Shaft Key
29. Shaft Nut
30. Bearing Spacer
* Contained in Seal Kits:
300333900 & 300333900B
FIGURE 1 FIGURE 2 FIGURE 3
dust seal metal backup shim
seal carrier backup seal
shaft seal
2,0 - 2,5
[.080 - .100] groove
drive link
23
8
8
9
10
24
26
13
27
13
6
12
3
1
17
18
19
25
20
21
22
11
8
14
15
28
14
7
5
4
2
29
16
30
manifold
Table of contents
Other White Engine manuals
Popular Engine manuals by other brands

BMW
BMW B130 Workshop manual
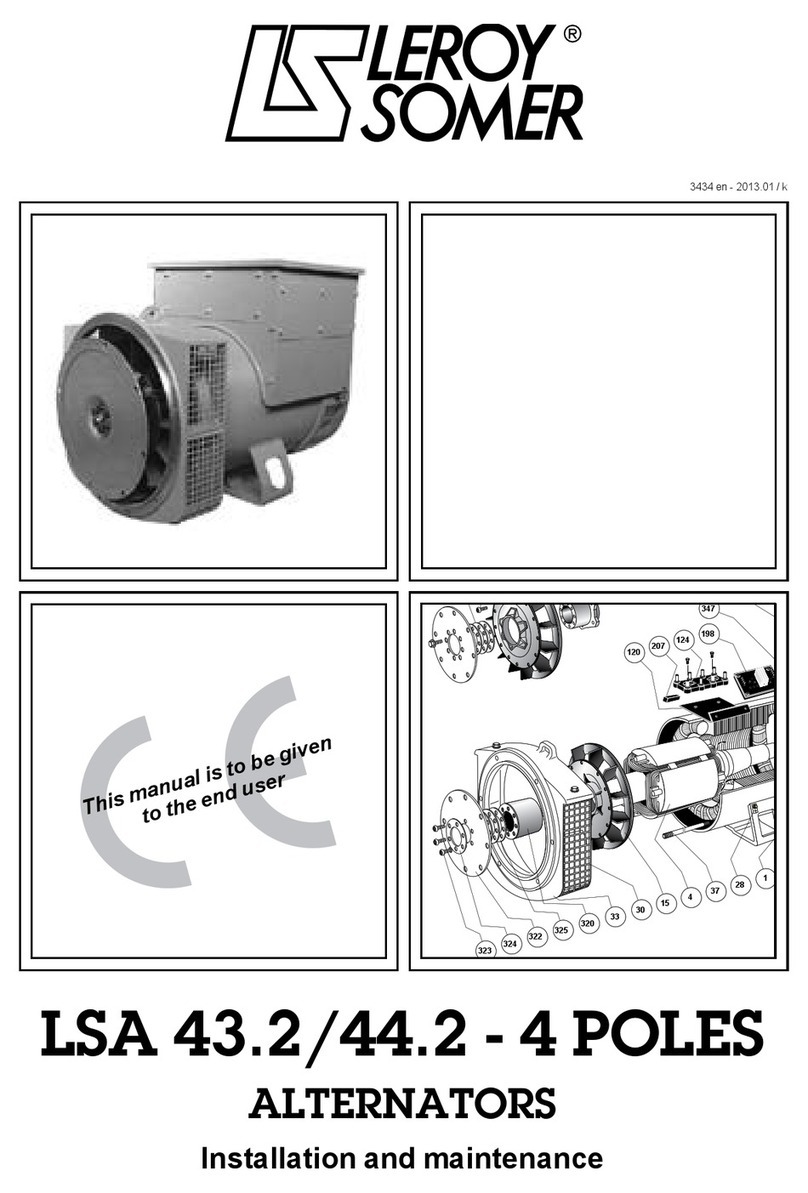
Leroy-Somer
Leroy-Somer LSA 43.2 Installation and Maintenance

Briggs & Stratton
Briggs & Stratton Vanguard 290000 Operating & maintenance instructions
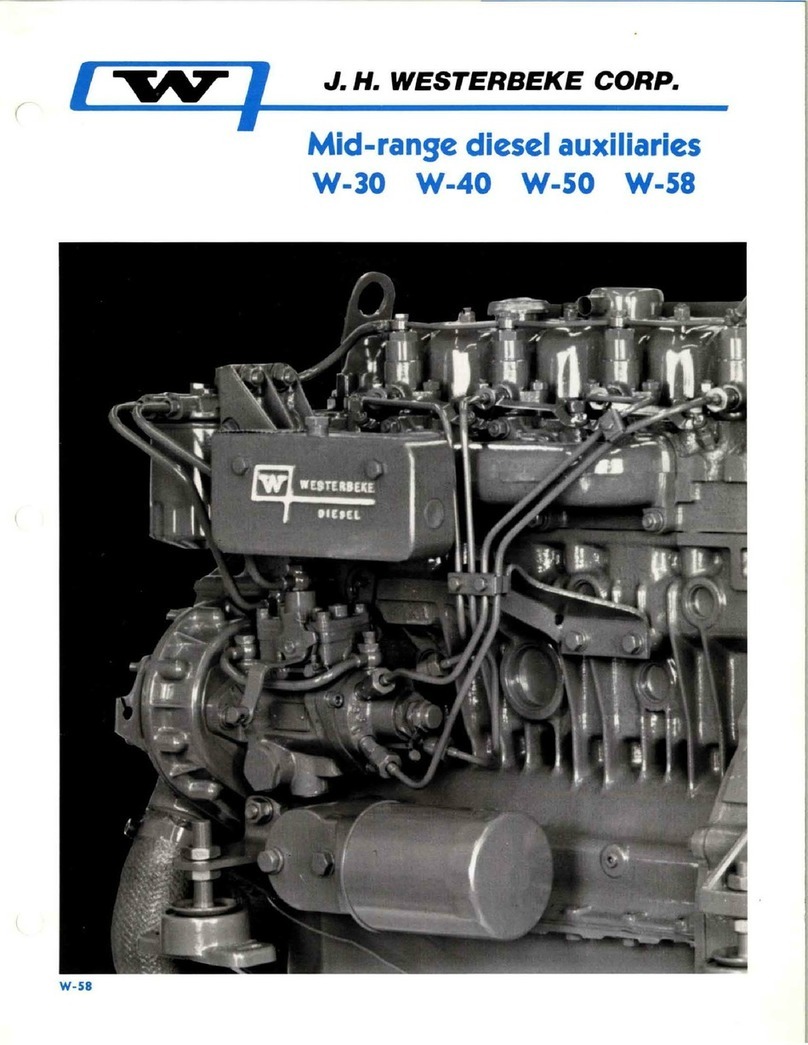
Westerbeke
Westerbeke W-3O Information sheet
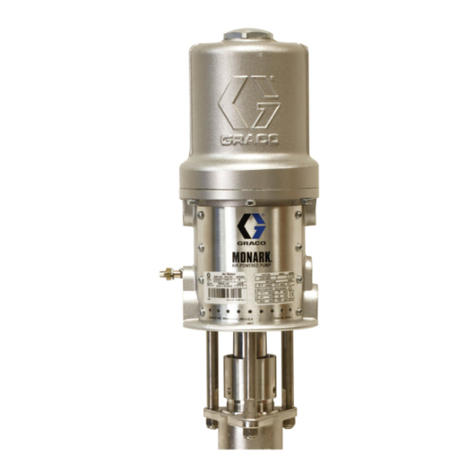
Graco
Graco Monark M Series Instructions-parts list

MTU
MTU 20V4000M73 series operating instructions
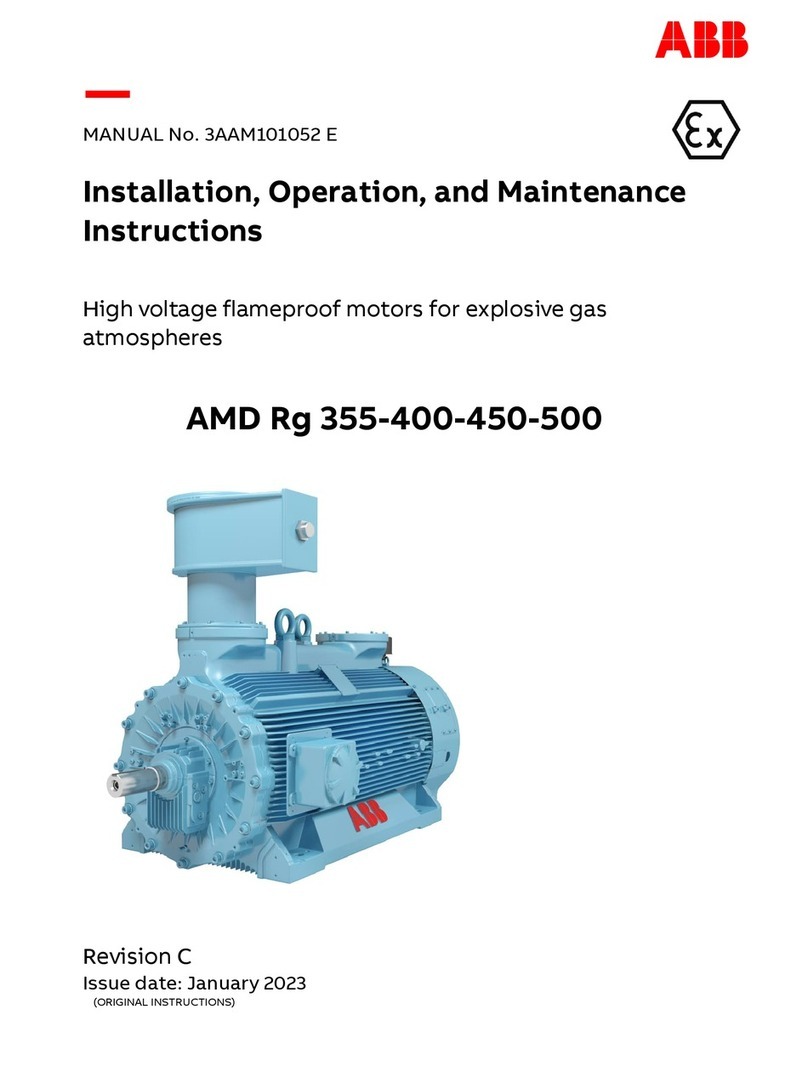
ABB
ABB AMD Rg 355 Installation, operation and maintenance instructions

Volvo Penta
Volvo Penta MD2010 Instruction book
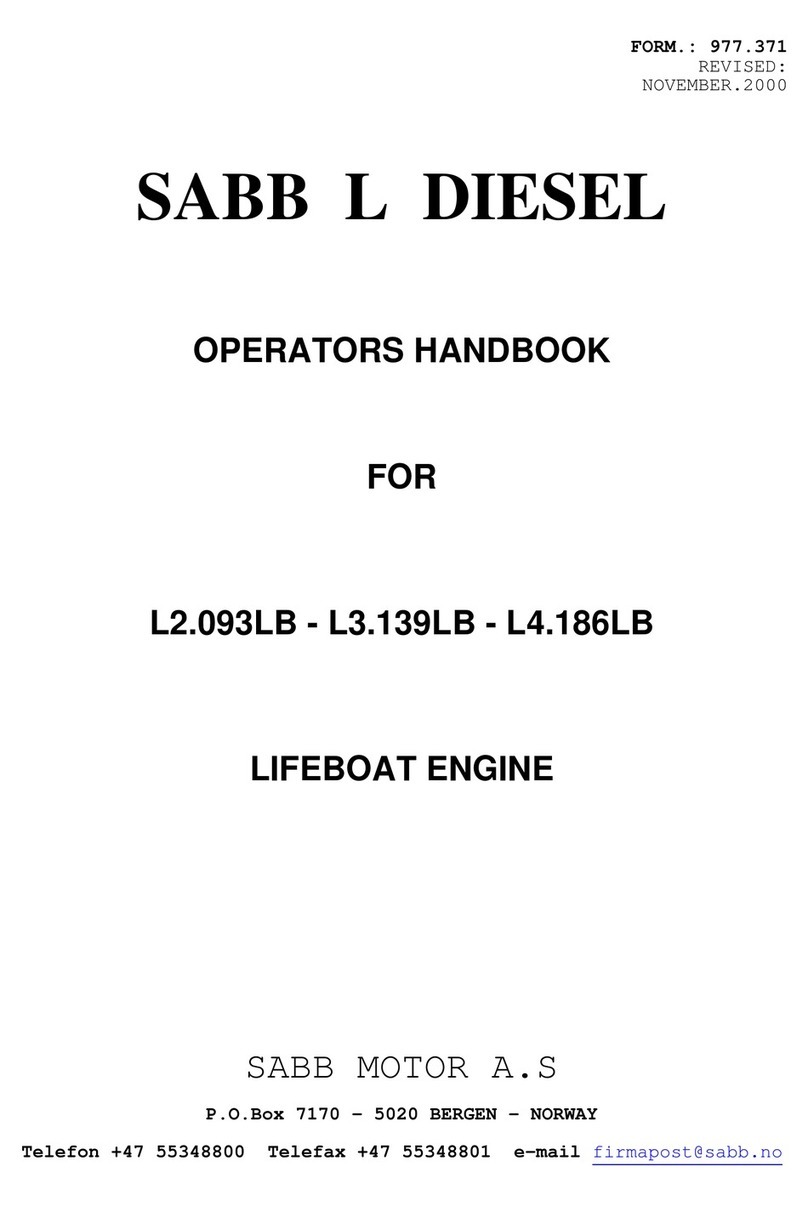
Saab
Saab L2.093LB Operator's handbook
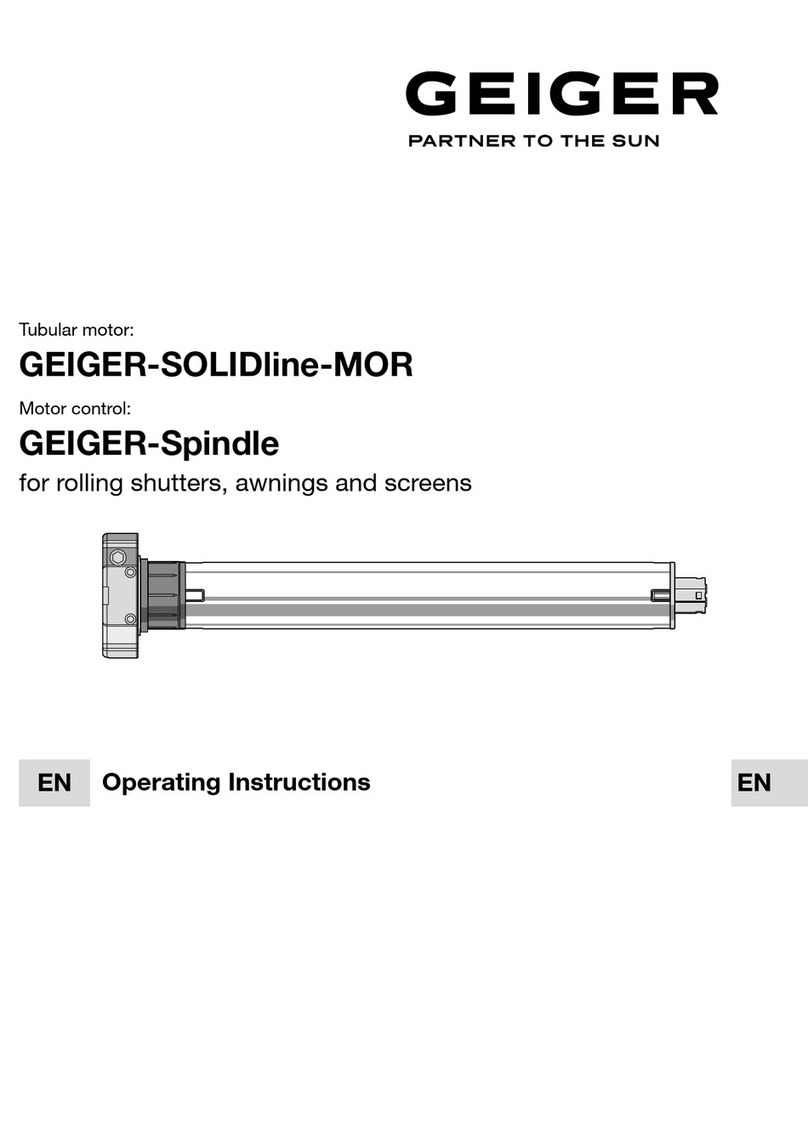
GEIGER
GEIGER SOLIDline-MOR GU4510 operating instructions
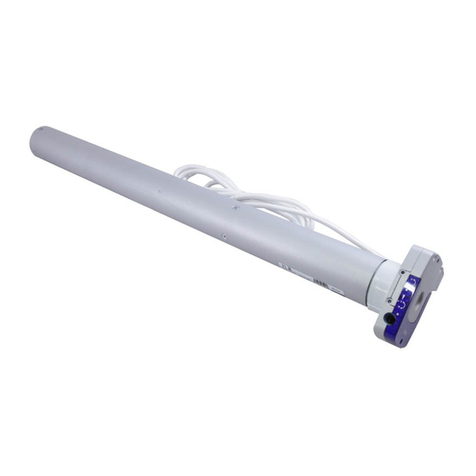
Nice
Nice NEO S Installation and use instructions and warnings
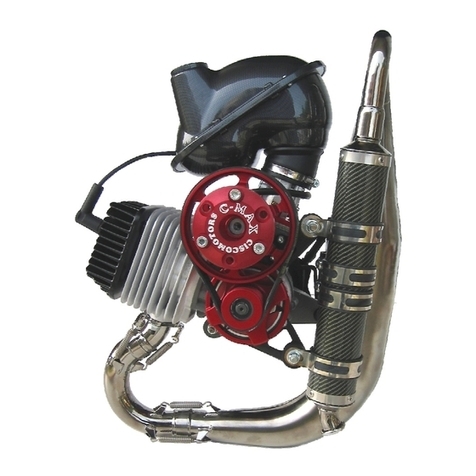
Ciscomotors
Ciscomotors C-Max Simplified maintenance manual