Accu-Flo Meter Service Ltd. RED SEAL MEASUREMENT neptune Manual

Operating and Maintenance
For Petroleum Meters
M233
Rev. B
P. D. Oscillating Piston Flowmeters:
11⁄4″Type A & 40 Petroleum
11⁄2″Type 40 Petroleum

TABLE OF CONTENTS
Installation and Operation ........................................................................................1
Preset Models .......................................................................................................... 2
Printer Register Models ...........................................................................................3
11⁄4Preset Models with Auto Stop Valve ...................................................................4
11⁄2Preset Models with Double Trip Valve ......................................................... 5 & 6
Double Trip Valve Maintenance ................................................................................ 7
Calibration ................................................................................................................8
Register Maintenance .............................................................................................. 9
Gear Train Maintenance .........................................................................................10
Measuring Chamber Maintenance .........................................................................11
General Maintenance .............................................................................................12
Troubleshooting ......................................................................................................13

INSTALLATION AND OPERATION
Before Installing
Plan the installation in such a way as to allow a strainer to be coupled directly to the inlet of the
flowmeter. Where this is not possible, any piping between these units should be thoroughly cleaned
out.
Be careful to allow room for easy removal of the strainer screen.
An air release or other effective means must be provided in the metering system to prevent air
from entering the flowmeter. If an air release is used, the unit should be installed in a position as
close as possible to the inlet of the flowmeter. This will ensure the removal of the greatest possible
amount of air from the liquid before metering.
The vent line from the air release should be 3⁄4″pipe or 1⁄2″inside diameter tubing. Care should
be taken to prevent any possible obstruction to the free flow of air in this line. This line should vent
into the supply tank or into a container (5 gallons or larger) to collect possible liquid spewed with the
air.
Use pipe tape or cement on male threads only.
The piping on the outlet side of the flowmeter should be so arranged as to eliminate the possi-
bility of draining the measuring chamber.
A bypass connection should not be installed around the flowmeter. Experience has shown that
the valve in this line will eventually leak, work open or be accidentally left open.
WARNING
When Installing
The connecting piping should be firmly secured to prevent strain on the flowmeter casing.
Care should be taken that there is provision for expansion due to change in temperature.
All piping on the inlet side of the flowmeter should be very thoroughly cleaned out. Whenever
possible, place a spool in the place of the flowmeter and flush out all lines thoroughly before the
flowmeter is installed. The majority of service calls on new installations would be eliminated
if these directions were followed.
Inlet and/or outlet are marked on flowmeter; do not install backwards.
After Installing
Pass sufficient liquid to clear the lines of air. Check the rate of flow. It should not exceed the
rated capacity of the flowmeter. The bypass of the pump should be regulated to deliver the maximum
practical rate of flow for the least amount of pressure. Pressure on the flowmeter should not exceed
125 psi. Do not try to increase the flow through undersized pipes and fittings by means of excessive
pressures which will cause leaking gaskets and collapsed air release floats.
Temperature of the liquid should not exceed 140°F.
All flowmeters are tested and calibrated by Actaris and adjustment should not be necessary. If
registration appears to be in error, the flowmeter registration should be checked using a calibrated
volumetric prover. The prover must be of sufficient capacity to permit a full flow delivery for at
least one minute. Do not base calibration upon assumed volume of ordinary containers or “dip
stick” measurement.
If the registration is not in agreement refer to the section on “Calibration.”
Cleaning The Strainer
While the installation is still new, the strainer, if used, should be cleaned very frequently. After
the system has been thoroughly flushed of foreign material, only periodic maintenance of the unit is
recommended.
INSTALLATION AND
OPERATION
Before Installing
When Installing
After Installing
Cleaning The Strainer
Page 1

To Operate The
Flowmeter
PRESET MODELS
To Stop In Emergency
To Adjust Tripping
Point
To Operate The Flowmeter
1. Reset register to zero by turning operating knob to the rear stop. On Printer models, first
insert ticket.
2. On Preset models, set the Preset wheels to the desired quantity.
3. Start pump — open Auto Stop valve (if used).
4. Open hose nozzle and make delivery.
5. After completion of delivery on Printer models, stamp final reading on ticket by turning oper-
ating knob to the front stop and remove ticket.
PRESET MODELS
To set the Preset mechanism press the setting buttons inward until the desired quantity is noted
on the Preset wheels.
To Stop In Emergency
Pushing the red emergency stop button will trip the valve. After it has been used either the
delivery may be completed automatically as originally set by reopening the valve or the mechanism
may be set for a new figure. The accuracy of delivery in either case is not affected.
To Adjust Tripping Point
Registers are shipped from the factory with the Preset mechanism adjusted to trip correctly at
the normal rates of flow. If, due to a change in the speed of closing of the valve or for other reasons,
the Preset does not trip at the correct point, the trip point may be adjusted as follows:
If the valve is closing “off the mark,” either late (over-delivery) or early (under-delivery), adjust
the two connecting link nuts to bring the trip point to the zero mark. For right-hand assembly turn the
nuts to lengthen the connecting link when the trip point is early, or turn to shorten if the trip point is
late. For left-hand assemblies turn in the opposite direction. Continue this procedure until the final
trip is on or close to the zero mark. On double trip valves, the intermediate flow rate will be satisfac-
tory when the final trip is adjusted, as described.
Further adjustment of the trip point is possible, but is not recommended for normal applications.
The following procedure should be used only when very exact settings of the final trip are necessary.
Adjust the connecting link nut as described above, and proceed as follows:
Remove the trip adjusting screw located in the lower right corner of the register front housing.
Insert a narrow blade (3⁄16″) screwdriver until it engages the slotted head of the adjusting screw. One
turn of this screw will change the tripping point about one-quarter of one-tenth gallon.
If the Preset trips before reaching the zero mark (early), turn the adjusting screw clockwise.
If the Preset trips after reaching the zero mark (late), turn
counterclockwise.
Do not turn the adjusting screw more than 11⁄2turns in
either direction from the initial position or pass a point where
a resistance to further turning of the screw is felt.
If the trip point is not on zero after 11⁄2turns, return the
adjusting screw to its original position and turn the connect-
ing link nut a half turn in the appropriate direction. Then re-
peat the trip screw adjustment procedure.
Gear shifter supplied as standard on 833 and 834 mod-
els. Optional on 831 and 832 models.
Page 2
DUST BAR
CLAMP
SCREW
OPERATING KNOB
PRESET BUTTONS
TRIP ADJUSTING
SCREW COVER
EMERGENCY
STOP BUTTON
FIGURE 1
PRESET 800 SERIES
PRINTER REGISTER

PRINTER REGISTER
MODELS
To Insert and Remove
Tickets
To Adjust Ticket Guides
To Change Settings
of “Letter” Wheels
To Change Position
of the Register
(Non-Preset Models)
Page 3
PRINTER REGISTER MODELS
To Insert and Remove Tickets
To insert a ticket be sure that the operating knob is turned forward to a stop. Then depress the
dust bar and insert the ticket in the ticket slot under it, either “face down bottom end first” or “face up
top end first,” as noted on the instruction plate. Turn the operating knob backward to the stop. This
resets the visible wheels to zero, locks the ticket in place and prints the initial reading on the ticket.
Upon completion of delivery, turn the operating knob forward to the stop. This operation prints
the final reading and releases the ticket. It is now possible to remove the ticket.
To Adjust Ticket Guides
The Printer registers are shipped from the factory with the ticket guides adjusted for a standard
(41⁄8″) width ticket. If for any reason it is necessary to reposition the ticket, proceed as follows:
1. Remove top cover.
2. Insert a ticket into the printer. Loosen the
clamp screws on the rear of the ticket guides.
Move the guides to the right or left as re-
quired. Tighten clamp screws. The ticket must
slide freely between the guides. If the ticket
bends at the forward end of the guide, re-
move the guide and rebend the tail of the
guide.
3. If it is necessary to raise or lower the print-
ing, push the two stop pins to the front or
rear with the end of a screwdriver.
4. Replace the top cover and reseal.
To Change Setting of “Letter” Wheels
1. With the top plate removed, the “letter”
wheels are visible (see Figure 2).
2. By means of a screwdriver or similar tool,
turn the wheels until the desired letters appear at the top where they are in position to print.
To Change Position Of The Register
(Non-Preset Models)
Remove the register from the flowmeter. Two studs and two threaded holes will be seen on the
flowmeter cover. Turn register 180°and tighten the screws in front of the register. For convenience
the operating knob may be moved to the opposite side of the register. If the register is to be turned
90°transfer the studs to the two empty holes.
Gear shifter standard on 833 and 834 models. Optional (extra charge) on models 831 and 832.
STOP PINS
CLAMP SCREWS LETTER WHEELS
FIGURE 2
PRINT UNIT ADJUSTMENTS

11⁄4″″
″″
″PRESET MODEL
WITH AUTO-STOP
VALVE
To Rotate Register
To Adjust Linkage
Valve
Page 4
11⁄4″″
″″
″PRESET MODELS WITH AUTO STOP VALVE
To Rotate Register
When the flowmeter is assembled as a Left Hand assembly and it is desired to change it to a
Right Hand assembly, or vice versa, proceed as follows:
1. Remove cotter pins (E) from valve linkage.
2. Unscrew the outside register link lock nut (P) and remove connecting rod (G).
3. Remove register link (N), rotate 1/2 turn and reassemble onto register as described in appro-
priate valve adjustment instructions.
4. Loosen two clamp screws on lower front of register, lift register up and turn register 180°.
5. Remove four handle housing assembly hex screws (C) and remove handle housing assem-
bly from valve.
6. Remove valve handle set screw (B) and slide handle off bushing. Remove two cam retaining
screws (
not shown
). Remove shaft seal plug (D). Disassemble valve operating shaft and
valve operating cam. Reassemble valve operating shaft and install valve operating cam in
the reverse direction. Reinstall two cam retaining screws and shaft seal plug. Reinstall hous-
ing assembly with valve operating cam acting on pilot rod. Secure with four hex screws (C).
Reassemble valve handle (A) on knurled knob in position as shown for specific assembly.
After completing the above instructions, the valve linkage must be adjusted in accordance with
the procedure for the specific type valve as outlined on the following pages.
RIGHT HAND ASSEMBLY
M
P
N
O
A
G
E
D
B
C
TO OPEN
TO OPEN
A
G
E
D
B
C
M
P
N
O
FIGURE 3
VIEW LOOKING AT BACK OF REGISTER
LEFT HAND ASSEMBLY
To Adjust Linkage Valve
Note: Before any adjustment of the Auto-Stop Valve is made, be sure that the Auto-Stop set-
ting wheels indicate a quantity other than zero to ensure that the trip mechanism of the register is in
proper position.
1. Depress the emergency stop button on the register and turn the shaft (O) clockwise (
as
viewed from rear of register
).
2. Assemble register arm (N) on knurled knob in position as shown for specific assembly. (See
Fig. 3 ). Arm should move an equal distance each side of vertical center line (M) (Angle x=x).
3. Assemble one nut (P) on connecting rod (G) and the other end of the connecting rod to the
center hole in handle (A) using washers and cotter pins (E).
4. Open valve all the way. Turn shaft (O) counter clockwise to latch up mechanism. With valve
held open tighten nut (P) against register arm link. Then assemble and tighten second nut at
(P).

5. Depress the emergency stop button and allow the valve to close. At this point the leakage
between the valve and the register must be free. If it is not, the above adjustments must be
rechecked.
6. Set the register to deliver the minimum quantity and open the valve to run product through
the flowmeter.
7. After the initial trip occurs the valve should close to the intermediate flow position. This rate
will vary depending on product metered. If the valve closes too far, or all the way, adjust nuts
(P) to provide additional rod length.
8. It is sometimes necessary to change the position of the handle. This can be done by loosen-
ing handle screw (B) and repositioning the handle as follows: if the register mechanism will
not latch up, position the handle further toward the register. If the valve will not close, the
handle may be positioned away from the register. Fine adjustments may be made by chang-
ing the effective length of connecting rod (G) utilizing nuts (P). Effective length of connecting
rod (G) may also be varied by positioning the end of the rod in the upper or lower holes in the
valve handle.
9. The Auto-Stop trip adjusting screw should be near its mid-position.
To Adjust The Tripping Point
The flowmeter is shipped from the factory with Auto-Stop mechanism adjusted to trip correctly
at maximum rates of flow while the flowmeter is measuring a non-viscous liquid. Trip adjustment
after final installation may be necessary due to differing flow rate and/or viscosity.
If the Auto-Stop does not trip off at the correct mark due to a change in the speed of closing of
the valve, different rates of flow, or any other reason, the adjustment is made as follows:
Remove the screw located in the lower right corner of the front housing. Insert a medium-sized
screwdriver into this hole until it engages the slotted head of an adjusting screw. One turn of this
screw will change the tripping point about one-quarter of one graduation of the first wheel.
If the Auto-Stop trips before reaching the zero mark, turn the adjusting screw in a clockwise
direction.
If the Auto-Stop trips after the zero mark, turn the adjusting screw in a counterclockwise direction.
11⁄2″″
″″
″PRESET MODEL WITH DOUBLE TRIP VALVE
To Rotate Register
When the flowmeter is assembled as a left-hand assembly and it is desired to change it to a
right-hand assembly, or vice versa, proceed as follows:
1. Remove clevis pin (E) from valve linkage.
2. Unscrew the outside register link lock nut (P) and remove connecting rod (G) and clevis (F)
as a unit.
3. Remove register link (N), rotate 1/2 turn and reassemble onto register as described in ap-
propriate valve adjustment instructions.
4. Loosen two clamp screws on lower front of register, lift register up and turn register 180°.
5. Remove operating shaft cap screw (C) on both sides.
6. Interchange connecting rod arm (H) and valve operating handle (A). The connecting rod arm
must be assembled with notches (J and K) in specific relationship. (See item 3 of valve
adjustment instructions for details regarding position of notches.)
7. Reassemble operating shaft cap screws (C).
8. Remove valve handle stop set screw (B) and screw into hole on opposite side of valve.
To Adjust The Tripping
Point
11⁄2″″
″″
″PRESET MODEL
WITH AUTO-STOP
VALVE
To Rotate Register
Page 5

Adjustment of Auto-
Stop Valve
To Adjust Valve
Linkage
Page 6
FIGURE 4
VIEW LOOKING AT BACK OF REGISTER
After completing the above instructions, the valve linkage must be adjusted in accordance with
the following procedure:
Adjustment Of Auto-Stop Valve
Before any adjustment of the valve is made, be sure that the Preset setting wheels indi-
cate a quantity other than zero to insure that the trip mechanism of the register is in proper
position.
To Adjust Valve Linkage
1. Depress the emergency stop button on the register and turn the shaft (O) clockwise.
2. Assemble register arm (N) on knurled knob in position as shown for specific assembly. (See
Fig. 4). Arm should move an equal distance each side of vertical center line (M) (Angle x = x).
3. Assemble valve arm (H) as shown for specific assembly. On the right hand assembly there
must be one notch between the cast mark (K) on the valve arm and the cast mark (J) on the
stop plate (J above K). On the left hand assembly these cast marks must be in line.
4. Assemble one nut (P) on connecting rod (G) and assemble clevis to the other end of the
connecting rod a distance of 1″.
5. Insert end of connecting rod through register arm link and assemble clevis (F) to valve arm
(H) using upper hole. (See Figure 4). Insert clevis pin (E).
6. Open valve all the way. The opening of the valve is stopped by the set screw (B) which should
project approximately 1⁄8″below the lug holding it. Turn shaft (O) counterclockwise to latch up
mechanism. With valve held open, tighten nut (P) against register arm link. Then assemble
and tighten second nut at (P).
7. Depress the emergency stop button and allow the valve to close. At this point the linkage
between the valve and the register must be free. If it is not, the above adjustments must be
rechecked.
8. Set the register to deliver the minimum quantity and open the valve to run product through
the flowmeter.
9. After the initial trip occurs the valve should close to the intermediate flow position. This rate
should be approximately 15 to 20 gpm. If the valve closes too far, or all the way, unscrew
clevis (F) on rod (G) to hold valve open further. If the rate of flow is too fast during the
intermediate position, turn the clevis onto the rod to allow the valve to close further. It should
not be necessary to turn more than one turn in either direction.
M
O
N
P
XX
G
TO OPEN
FE
A
B
DIRECTION OF FLOW
Y
H
J
K
C
D
OUTLET
RIGHT HAND
ASSEMBLY
LEFT HAND
ASSEMBLY
M
O
N
P
XX
G
TO OPEN
F
E
A
B
DIRECTION OF FLOW
YH
J
K
C
D
OUTLET

DOUBLE TRIP
MAINTENANCE
To Disassemble and
Assemble Double Trip
Valve (Type 1A)
Page 7
10. It is sometimes necessary to change the position of set screw (B) if the clevis has been
readjusted. If the register mechanism will not latch up, unscrew the set screw to allow the
valve to open further. If the connection rod (G) is under compression, when the valve is
held all the way open, turn the set screw down to relieve the pressure on the register.
11. The Auto-Stop trip adjusting screw should be near its mid-position. If a small adjustment of
this screw will not permit the register to shut off “on the mark” it is usually possible to correct
this by a slight adjustment of the clevis (F). This will move the main valve nearer to or further
away from its seat during the intermediate flow and thereby change the amount of time
needed for the valve to fully close at the last trip (Also see To Adjust The Tripping Point.)
NOTE: If it is difficult to obtain proper rate of flow during intermediate trip position and still
have regular latch up fully. Check Auto-Stop valve to insure that it is opening all the way.
Check valve by removing set screw (B) and clevis (F) from valve arm; open valve as far as
possible. The distance between lug on arm and lug on stop plate must not be more than 1⁄4″.
DOUBLE TRIP MAINTENANCE
To Disassemble and Assemble Double Trip Valve
1. Remove valve from flowmeter.
2. Remove two screws (A) holding retaining ring (B) at inlet of valve. (Caution: End plate should
be held by hand when removing screws because of spring tension beneath the plate.) All
internal parts of the valve can now be removed with the exception of the operating shaft
mechanism. The removal of the internal parts from the valve body may be assisted by oper-
ating the valve handle as when operating the valve.
3. Disassemble piston and throttling ring assembly (items F to K). Inspect valve seats, “O” ring
gaskets, piston ring (D), and cylinder (C) for damaged surfaces. Replace all defective parts
with new parts.
4. Reassemble piston and throttling
ring assembly. Apply Loctite Black
Max 380 to bond the disc (G) to
the piston (F), and allow 24 hours
to cure before placing in service.
Apply Loctite Threadlocker 242
under heads of three piston as-
sembly screws (H).
5. Assemble pilot valve (E) on pilot
valve rod (J). Place assembly into
valve body.
6. Place one end of spring over pilot
valve boss.
7. Place other end of spring over boss in cylinder (C) and press cylinder down over piston (F).
Back of cylinders should be below flange face for proper assembly.
8. Hold cylinder in place, place “O” ring in body recess and attach retaining ring (B) with two
screws (A).
9Open valve as far as possible — make sure that valve is not being stopped by set screw (L).
FIGURE 5
VALVE ASSEMBLY

To Adjust Rate of
Closing of Valve
To Inspect Operating
Shaft Seals of Preset
Valves
CALIBRATION
Page 8
To Adjust Rate of Closing Of Valve
Variations in the viscosity of the liquids being measured will cause changes in the rate of closing
of the valve from its full open position to its intermediate position. (Valve should reach its intermedi-
ate position with approximately 4 gallons remaining on Preset setting wheels.)
Setting of orifice plate is indicated on tag attached to valve.
The rate of closing can be adjusted by changing the posi-
tion of orifice plate which is readily accessible through inlet of
valve. (Valve does not have to be disassembled.)
View of valve inlet showing position of orifice plate for gaso-
line and other low viscosity liquids. Note that orifice opening is
completely covered. (Photo shows 11⁄2″valve.)
The normal position of orifice plate in valve to be used with
gasoline or other low viscosity liquids will be set with orifice open-
ing covered. If valve closes too slowly with this setting, turn plate
counterclockwise to expose either small, medium or large hole
as required.
To Inspect Operating Shaft Seals of Preset Valve
The following steps should be followed if it becomes necessary to disassemble the operating
shafts because of leakage. Shaft seal cannot be
corrected by tightening of the bearing bracket
screws. In this case new “O” rings are usually re-
quired. (See parts list for 2″Type 1A Double Trip
Preset Valve.)
1. Remove the valve handle (A), connecting
rod arm (I), two stop plates (B and H), and
two roll pins (C). Remove eight screws and
pry off two shaft bearing brackets (D). Do
not damage gaskets (G).
2. The two “O” ring seals (E) can be inspected
for damaged surfaces. Replace any defec-
tive “O” rings.
3. To remove the operating shaft (J) and two
shaft bearings (D), first remove the two
screws in the valve operating cam (K). In-
spect the shaft for score marks and replace
if necessary. New “O” ring seals are worth-
less if used with a badly scored shaft.
4. Remove retainer (F), replace “O” rings (G) and reinstall shaft bearings (D).
5. Reassemble the operating shaft and cam.
6. Replace rings, flat gaskets, two roll pins, two stop plates, connecting rod arm and valve
handle.
CALIBRATION
Preset flowmeters should first be tested and adjusted without the Preset (set the Preset setting
wheels at 9999); then with the Preset to check trip point. If the Preset mechanism does not trip
correctly, see instructions “To Adjust the Tripping Point” and/or “To Adjust Valve Linkage.” Rerun the
test.
FIGURE 7
SHAFT ASSEMBLY
FIGURE 6
VALVE ORIFICE PLATE

Erratic Registration
Consistent Over- or
Under-Registration
REGISTER MAINTENANCE
Repair of Register
To Remove Register
from Flowmeter
Page 9
Erratic Registration
Erratic registration is an indication of trouble in the system caused by air or dirt in the measuring
chamber. Do not try to correct this by recalibration of the flowmeter, but first check over the piping for
air entry, clean the strainer, and then, if the trouble has not been found, clean the flowmeter as
directed. If this does not correct the trouble, check for faulty installation.
Over-registration is an indication of air, whereas under-registration is generally caused by dirt or
pipe scale in the measuring chamber, or the liquid bypassing the flowmeter in some manner.
Consistent Over or Under-Registration
When the flowmeter registers consistently either more or
less than is delivered, the calibration may be corrected in the
following manner:
1. Remove four screws holding top cover and remove
cover.
2. Lift and turn the change gear shifter (see Figure 8) in
the direction indicated on the top of the shifter.
3. There is a series of holes, marked A to H, in the plate
into which the guide pin enters at different settings.
Altering the setting by one hole changes the calibra-
tion approximately 17 cubic inches in 50 gallons.
Example:
Suppose the flowmeter consistently gives 34
cubic inches too much when it registers 50 gallons. After removing the cover plate move the gear
shifter 2 spaces to the right
(from position E to position C)
to decrease the delivery about 34 cubic
inches in 50 gallons.
After changing the calibration always replace top cover, making sure that the sheet steel hous-
ing on the sides and back fits into the groove in the bottom edge of cover. Run a small amount of
liquid through the flowmeter before testing. To prevent tampering, always reseal after calibration.
Note: For broader change gear requirements, refer to form TSG-310.
REGISTER MAINTENANCE
Repair of Register
Register parts are such that only minor field repairs are advisable. When a register is in need of
repair or service other than that for which instruction is given here, it should be returned to an autho-
rized Actaris distributor for service.
To Remove Register From Flowmeter
Loosen the two clamp screws on lower front of the register. Lift the register off. On Preset
Models the valve linkage must first be disconnected. (Remove cotter pin and washer at valve end.)
When one register is removed and another substituted,
1. Check the number of teeth on the change gears (See
Figure 9). They must be the same as the gears on the
old register and on the same respective spindles.
The number of teeth is stamped on each gear. To re-
move these gears, close the split end of the spindle
with a pair of pliers and pull off the gear. After putting
on a gear, spread the end of the spindle slightly.
2. Make sure the position of the “Gear Shifter” is the same
on the new register as on the old one — each hole is
lettered for convenience.
GEAR
SHIFTER
FIGURE 8
GEAR SHIFTER ADJUSTMENTS
FIGURE 9
CHANGE GEAR ARRANGEMENT
CHANGE GEAR “R” CHANGE GEAR “S”
(ON “STD” SPINDLE)

To Clean Register
Masks
GEAR TRAIN
MAINTENANCE
Loose or Worn Stuffing
Box Nut
To Repair Leaking “U”
Cup Seal Stuffing Box
To Replace Gear Train
Page 10
To Clean Register Mask
Register masks being made of plastic require special treatment. Manufacturer’s instructions for
cleaning are quoted below:
If masks become soiled with grease and oil, solvents for these substances, such as kerosene or
naptha, may be used to remove dirt. However, sprays that are commonly employed in cleaning glass
windshields must not be used as cleaners, since they may contain solvents.
A water solution of nonabrasive soap is recommended for washing grease, oil, or dirt from
mask. Clean by rubbing gently with a soft cloth in a manner similar to cleaning window glass, rinsing
the plastic with clean water, and finally drying.
Scouring cleanser and similar material must not be used in cleaning mask, since they contain
abrasives that scratch the surface.
The use of solvents, such as acetone, ethyl acetate, benzene, ethylene dichloride, etc., to brighten
the surface is never recommended since these substances soften the surface of the plastic.
GEAR TRAIN MAINTENANCE
Loose or Worn Stuffing Box Nut
Remove the register. If tightening the stuffing box nut by the
fingers does not stop this leak, replace with a new “U” cup. It may
also be necessary to replace the gear train.
To Repair Leaking “U” Cup Seal Stuffing Box
1. Remove the register.
2. Remove the star connection (1), using a No. 8 Allen wrench.
3. Unscrew the stuffing box nut (2).
4. Remove shaft seal (3). Inspect upper end of spindle to be
sure it is free of nicks or burrs which might damage the
new shaft seal when it is placed on spindle. Remove the
clamp nut (6); gear train assembly can be removed from
underside of flowmeter cover.
5. Replace shaft seal with new part. Be sure expander (4)
and spring (5) are in position before inserting new seal.
6. Assemble nut and tighten down all the way.
To Replace The Gear Train
1. Remove the register (see page 5).
2. Remove the star connection (1), using a No. 8 Allen wrench.
3. Remove the flowmeter cover, with gear train assembly at-
tached. Keep dirt out of flowmeter and avoid injury to the
cover gasket.
4. Unscrew the stuffing box nut (2).
5. Remove clamp nut (6); gear train assembly can be removed from underside of flowmeter
cover.
FIGURE 10
GEAR TRAIN ASSEMBLY

Page 11
MEASURING CHAMBER MAINTENANCE
To Remove and Disassemble Flowmeter Measuring Chamber
This operation is not difficult and may be performed by any competent mechanic. No special
tools are required. No trouble need be expected, if these few simple, but important, directions are
followed. Do not open the flowmeter until you have checked over all other possible causes of erratic
registration.
1. Prepare a clean surface on which to place the parts as they are removed. The parts are
machined to close tolerances and should be handled with care. Have a replacement gasket
ready before opening the flowmeter.
2. Loosen the two clamp screws on the lower front of the register. Lift the register off. On Preset
Models the valve linkage must first be disconnected. (Remove cotter pin and washer at valve
end.)
3. Remove the flowmeter cover taking care not to damage the gasket.
4. Lift the measuring chamber from the flowmeter casing.
5. Remove the upper cylinder head by inserting a screwdriver in one of the slots provided and
prying it off. Be careful not to scratch or nick any part of the chamber.
6. Lift out the piston by its spindle. If care
is taken to draw it straight, it should
come out easily. Do not force it.
7. Remove the control roller and the
diaphragm from the lower cylinder
head.
8. The seal pin may be removed (for
replacement only) by pulling upward,
using pliers if necessary.
Diaphragm, seal pin, and roller are
available as spare parts for rebuilding mea-
suring chamber.
To Clean The Measuring Chamber
The parts may be most easily cleaned of scale, etc., by means of a good, coarse, stiff bristle (not
wire) brush and gasoline. All foreign matter, except deeply embedded chips or heavy corrosion due to
water, may be removed in this manner. Do not use abrasives, such as emery cloth or sandpaper.
The parts of the measuring chamber which may show wear after long periods of service are the
diaphragm and the control roller. These parts will not require replacement until the accuracy begins
to fall off at low rates of flow. To change these parts, merely substitute the new for the old when the
flowmeter has been taken down for cleaning.
Experience has shown that the sliding surfaces between the chamber and piston take on a
burnished finish and wear little if any.
To Reassemble The Chamber In The Flowmeter
Before reassembling the flowmeter, rinse all parts
in gasoline. If possible, flush out the flowmeter body. As-
semble the parts carefully; they should slide together
easily without hammering or forcing. It is essential that
all contact surfaces between the cover and chamber, or
between the measuring chamber and its seat in the cas-
ing, be clean and free from nicks.
1. Assemble diaphragm and seal pin in chamber if
replacement was necessary.
MEASURING CHAMBER
MAINTENANCE
To Remove and
Disassemble Flowmeter
Measuring Chamber
To Clean the Measuring
Chamber
To Reassemble the
Chamber in the
Flowmeter
FIGURE 12
CHECKING THE PISTON MOVEMENT
FIGURE 11
MEASURING CHAMBER COMPONENTS

2. Place the control roller on its pin and see that it will rotate freely.
3. Replace the piston and oscillate it carefully by hand; it should move easily without binding. If
it sticks, do not force it, but remove and locate the cause. Do not file down the roller as this
will impair the accuracy of the flowmeter.
4. Replace the upper cylinder head and again oscillate the piston to make sure that is free.
5. When replacing the measuring chamber in the casing, be sure that the seat is clean and free
from nicks. Make sure the dowel pin enters the hole or slot provided and allows the chamber
to rest squarely on its seat.
6. Before replacing the cover, first be sure the chamber is properly seated and inspect the
gasket. Then set the arm of the gear train so that it will not come down on top of the piston
spindle.
7. Make sure the cover is down on its seat before tightening the bolts. If not, do not force it but
remove and locate the cause.
GENERAL MAINTENANCE
In the maintenance of these flowmeters, little is necessary other than to see that the proper
conditions of operation are preserved. These conditions, once the flowmeter has been properly
installed, consist merely in guarding against foreign matter such as air, sediment and water entering
the measuring chamber.
Sediment
The liquid passing through the measuring chamber must be free of grit and other forms of
sediment in order to prevent unnecessary friction and the scoring of the piston and chamber walls.
Evidence of trouble from this source will be found in under-registration of the flowmeter.
Periodic cleaning of the strainer at the inlet of the flowmeter will help to ensure against this
trouble. In the design of this unit, particular care has been taken to make this operation as simple as
possible.
Air
Being an instrument which measures by volume, a flowmeter will record the passage of air as
well as the liquid being measured. Over-registration is the result. The air release is intended to
prevent this condition by venting air before it passes through the measuring chamber.
Water
Incidental water will cause no damage to the flowmeter. Trouble from this source may be ex-
pected only when water is allowed to stand in the flowmeter for considerable periods of time.
Storage
Before a flowmeter is put in storage the measuring chamber must be flushed with a light lubri-
cating oil of the best quality to prevent damage from condensation.
Page 12
GENERAL
MAINTENANCE
Sediment
Air
Water
Storage

Page 13
TROUBLESHOOTING
TROUBLESHOOTING
Register Not Working When Liquid is Flowing
a) Bypass around flowmeter not shut off.
b) Frozen condensation inside register.
c) Register in need of repair.
d) Sheared key on “Change Gear” — caused by ice in register.
Leakage at the Stuffing Box
a) Loose stuffing box nut or worn spindle.
Chronic Leakage at the Main Case Gasket
a) Excessive line or shock pressure.
b) Broken gasket or loose bolts.
Reduction in the Rate or Complete Stoppage of Discharge
a) Pump bypass stuck open.
b) Air release valve fails to close allowing the liquid to escape through air vent.
c) An open valve in the piping allowing liquid to circulate around the pump.
d) Worn pump.
e) Blocked strainer due to sediment or frost.
f) Piston in flowmeter stuck, caused by dirt. Check strainer and clean measuring chamber.
Over-Registration — Erratic
a) Leaking valve in empty compartment causing an emulsion of air and oil.
b) Air release valve jamming allowing air to pass through the flowmeter
c) Spring in back pressure valve broken or valve stuck open.
d) Vent line from the air release valve plugged causing air to pass through the flowmeter.
e) Leaks in the suction line such as at valve stems, pump packing, or flange gaskets.
f) Air pockets in closed-end piping in the suction line.
g) Manifold or compartment valves only partly open causing excessive suction.
h) Suction piping too small causing excessive suction.
Under-Registration — Erratic
a) Dirt in the measuring chamber.
b) Badly worn control roller or diaphragm.
c) Main casing distorted or damaged.
d) Dirt under the seat of the measuring chamber at the outlet port (after cleaning).
e) Leakage around the flowmeter due to partly open valve.

Page 14
DIMENSIONS
11⁄4″″
″″
″TYPE 40 METER
WITH 800 SERIES REGISTER
11⁄2″″
″″
″TYPE 40 METER
WITH 800 SERIES REGISTER

Page 15
11⁄2″″
″″
″TYPE 40 METER
WITH 600 SERIES REGISTER
DIMENSIONS
45⁄16 57⁄8
15⁄87⁄16
137⁄8
OUTLETINLET
60°3⁄8-16UNC-2B
(3) HOLES
INLETOUTLET
47⁄8 DIA.
3⁄4DIA.
BOTTOM VIEW OF
MAIN CASE MOUNTING HOLES
SCALE:HALF
93⁄8
411⁄16 5⁄8
CLEARANCE FOR REMOVING REGISTER
241⁄425⁄8
65⁄8 DIA.
11⁄2 DIA.
11⁄16 DIA. (2) HOLES
EACH FLANGE
17⁄8
2
4

Page 16

Page 17

U.S.A./International
1310 Emerald Road
Greenwood, SC 29646-9558
Tel.: Toll-Free (800) 833-3357
(864) 223-1212
Fax: (864) 223-0341
Specifications subject to change without prior notification.
Table of contents
Other Accu-Flo Meter Service Ltd. Measuring Instrument manuals
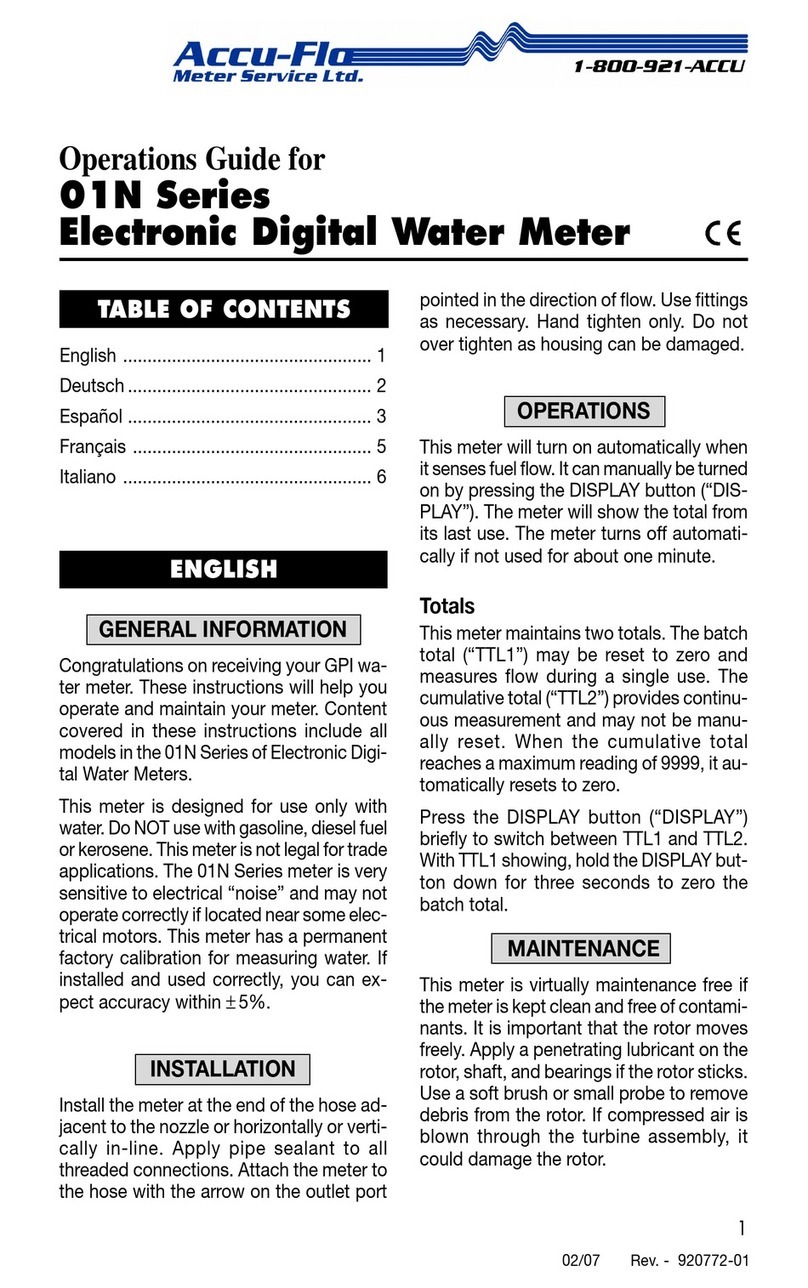
Accu-Flo Meter Service Ltd.
Accu-Flo Meter Service Ltd. 01N Series User manual
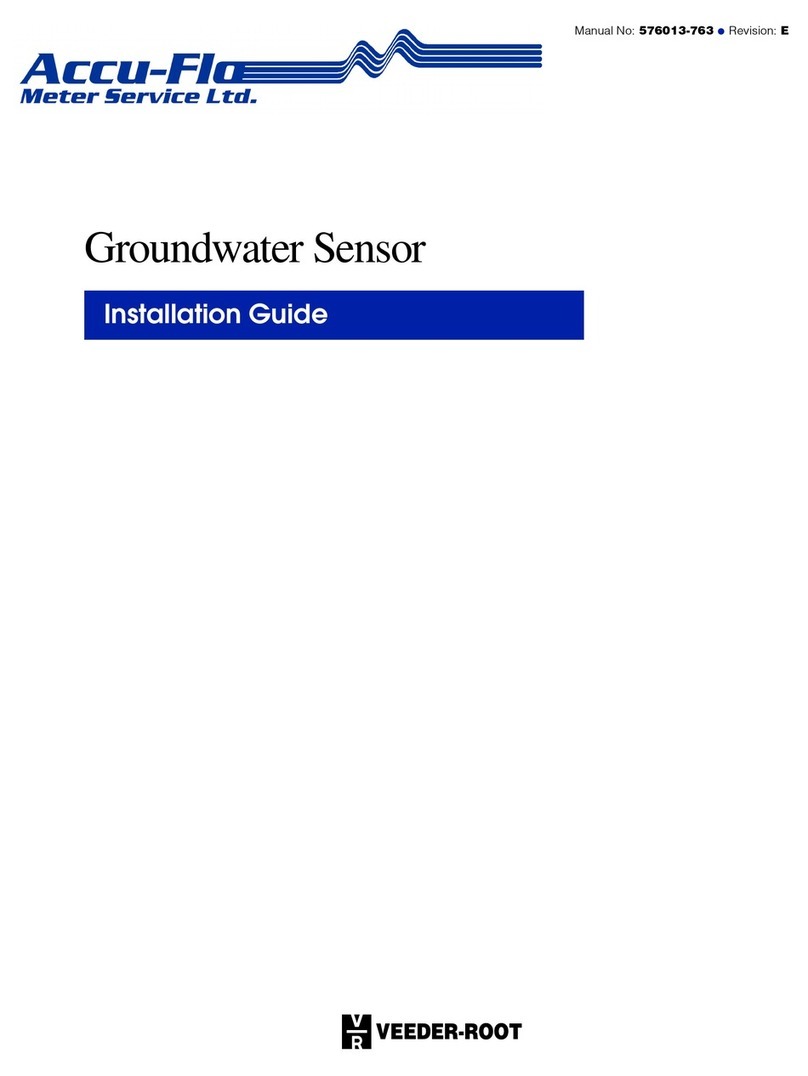
Accu-Flo Meter Service Ltd.
Accu-Flo Meter Service Ltd. Veeder-Root User manual
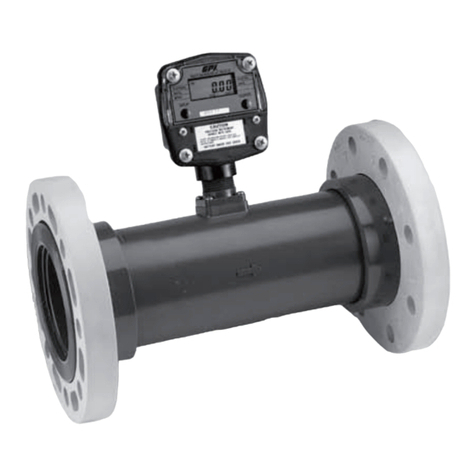
Accu-Flo Meter Service Ltd.
Accu-Flo Meter Service Ltd. TM Series User manual
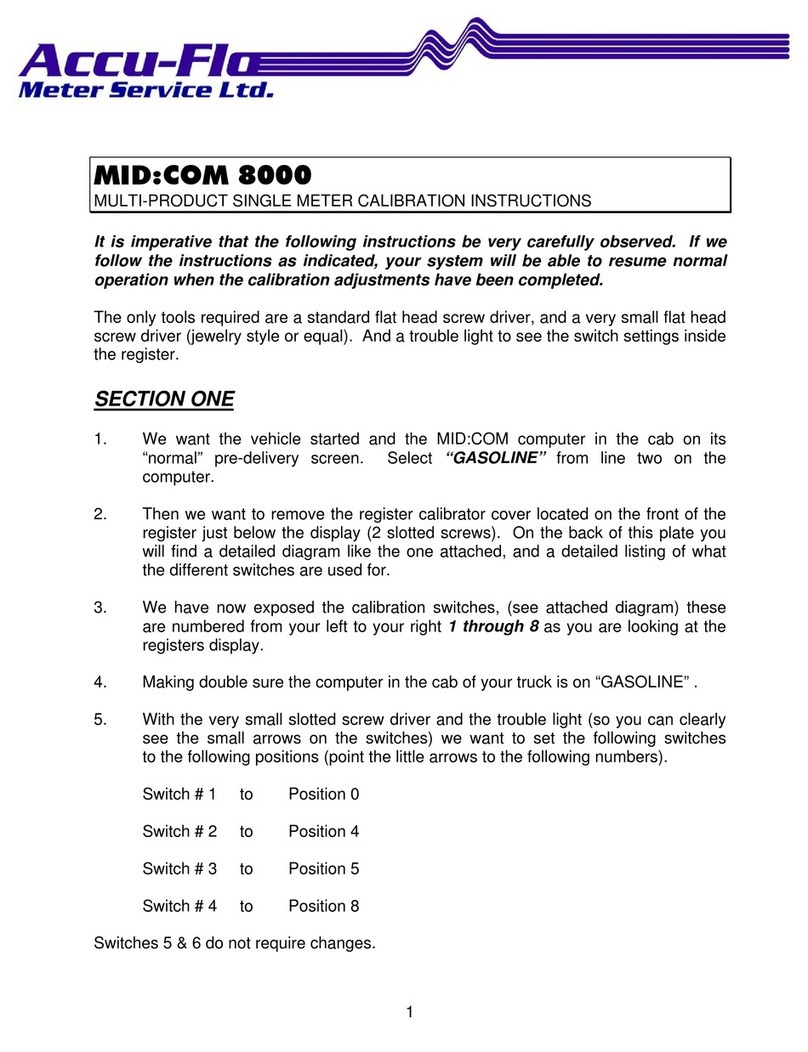
Accu-Flo Meter Service Ltd.
Accu-Flo Meter Service Ltd. MID COM 8000 Use and care manual
Popular Measuring Instrument manuals by other brands
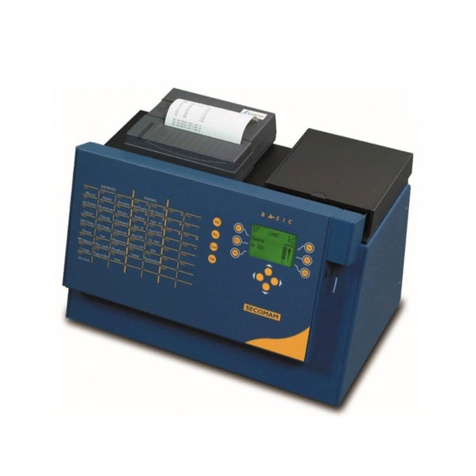
Secomam
Secomam Basic user manual
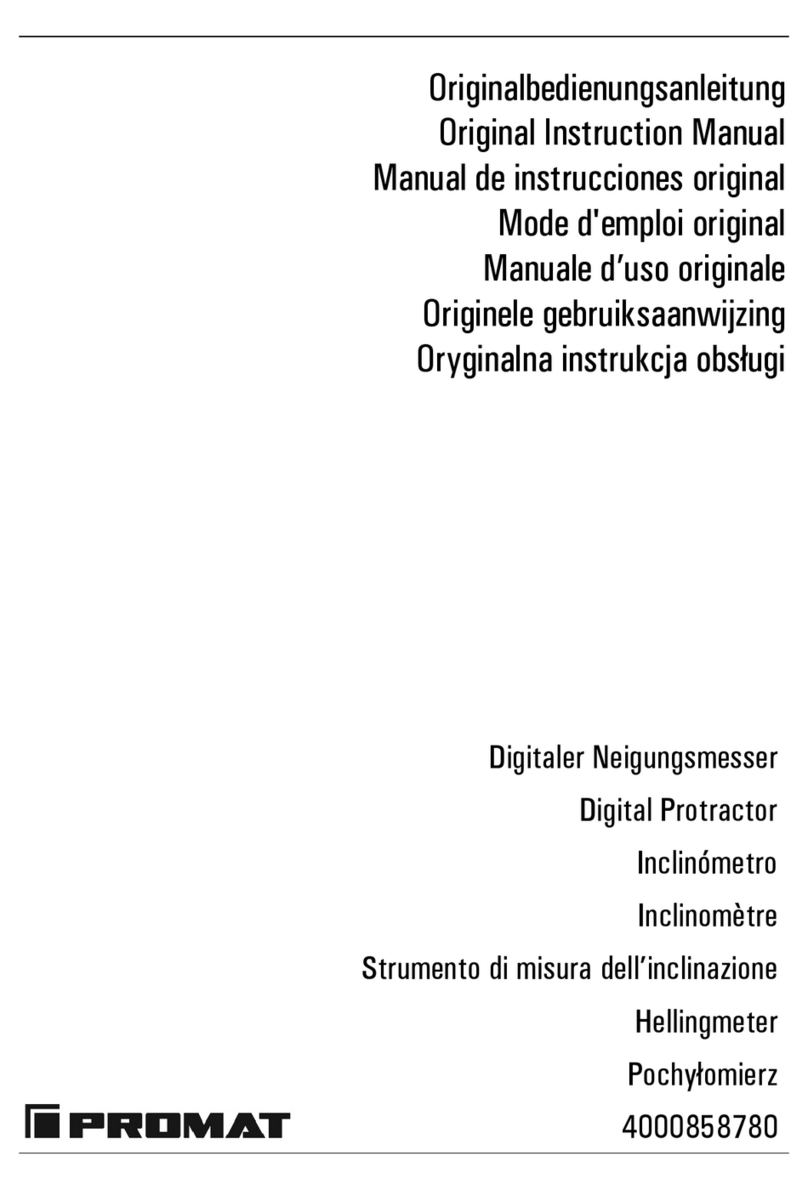
PROMAT
PROMAT 4000858780 Original instruction manual
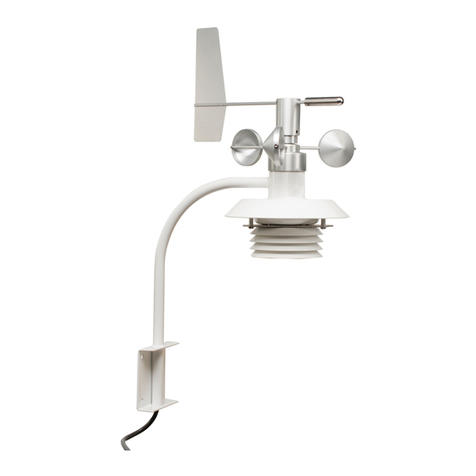
Met One Instruments
Met One Instruments MSO Quick reference guide
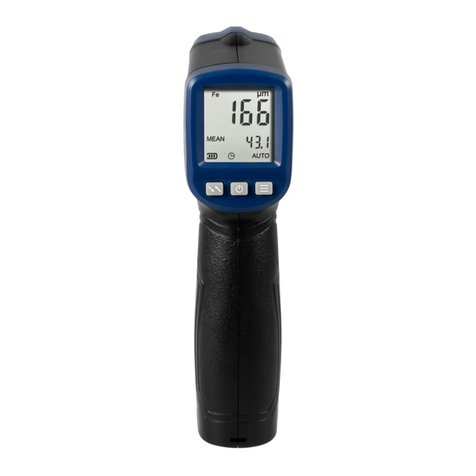
PCE Health and Fitness
PCE Health and Fitness PCE-CT 25FN user manual
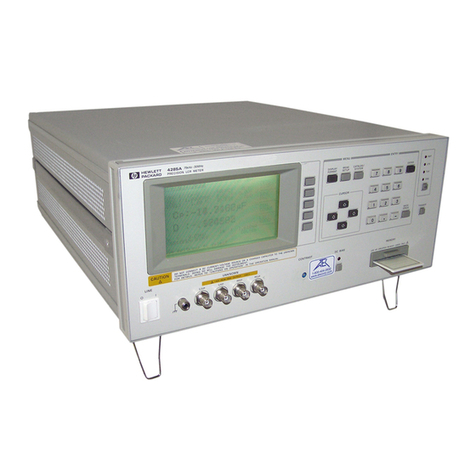
Agilent Technologies
Agilent Technologies 4285A Getting started guide
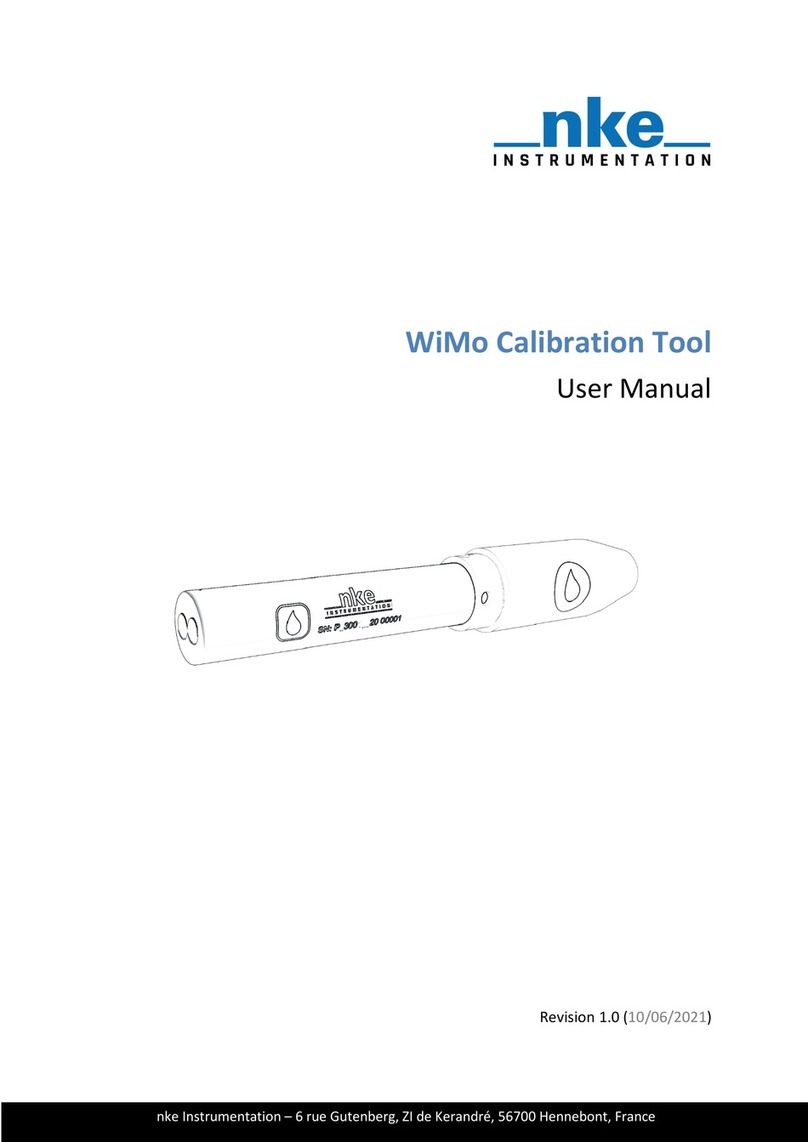
NKE
NKE WiMo user manual