Accu1 Direct 9300 User manual

Owner’s Manual
Accu1® Model 9300
All-Fiber Insulation Blowing Machine
Manufactured By:
Accu1Direct. Inc.
138 Denslow Road
East Longmeadow, MA 01028
(T) 800-438-2776
(F) 413-224-1294
www.accu1.com

Table of Contents
1) Warranty Page 3
2) Principles of Operation Page 4
3) Maintenance Page 5
4) Warnings Page 7
5) Operating Instructions Page 8
6) Machine Settings Page 11
7) Airlock Seal Change Instructions Page 12
8) Troubleshooting Page 16
9) Exploded Views / Parts Page 17
10) Wiring Diagrams Page 25
2

Warranty
Accu1Direct / Accu1® products are warranted to be free from defects in
workmanship and materials for a period of 5 years from date of purchase.
The following restrictions apply:
1) The warranty applies to products in normal use only. The product must be
serviced and maintained as described therein.
2) If the product fails it will be repaired or replaced at the option of Accu1Direct /
Accu1®.
3) All shipment / delivery charges are the responsibility of the purchaser.
4) Warranty service claims are subject to factory inspection for product defect(s).
If during the warranty evaluation it is determined that the machine has been
used in any way other than the purpose for which it was designed, Accu1Direct /
Accu1® reserves the right to void the warranty.
5) All warranty claims must be made within the warranty period. This warranty is
non-transferable.
6) Note that the warranty does not apply if it has been determined after
inspection by Accu1Direct that the product or product part was damaged by
accident, misuse, has been tampered with or modified in any way.
7) Normal wear items (seals, filters, belts, paddles, and relays ) are specifically
excluded from warranty unless found to be defective by Accu1Direct/ Accu1®
8) Blowers, gear boxes, motors, components, and engines are covered under the
warranty of the manufacturers of those products.
9) This warranty is exclusive to Accu1® products and shall be in lieu of any other
warranty, expressed or implied , which may be available to the purchaser.
10) All returned good must be accompanied by a Return Goods Authorization
number (RGA). Contact our factory to obtain the RGA number.
3

Principles of Operation:
Accu1®9300 Insulation Blowing Machine
The Accu1®9300 insulation blowing machine moves insulation material to
specified areas by:
Conditioning insulation materials via agitator / auger shafts so that it can be
moved by pressurized air through hoses to the desired uninsulated spaces.
Insulation bales are loaded into the machine hopper. The agitator arms break up
the compressed insulation while the auger or shredder moves the material to the
air lock opening.
Agitator and Shredder
In the airlock, rotating vanes carry conditioned material to the air stream at the
bottom of the airlock. As the insulation passes by the air stream it is pushed
through the air lock exhaust tube and into the attached blowing hose. Further
conditioning of the material occurs as the insulation tumbles through the blowing
hose until it exits the hose end.
Airlock
4

Maintenance
Check for the following:
Daily:
1) Clogged filters (Figure 1, right)
Figure 1
2) Insulation build up on motors and electrical components.
Figure 2
5

Weekly:
1) Belt tension and condition (Figure 2). The belt should not be frayed or slipping
on the pulleys. Replace the belt if it is damaged. Raise the belt tensioner to
remove any slack in the belt.
Monthly:
1) Airlock seals. Check airlock seals using a pressure gauge. A minimum outlet
tube pressure of 3.0 psi must be maintained for proper operation. Replace when
pressure drops below the minimum per the instructions in this manual.
2) Chain tension. Move chain tensioner(s) to remove any slack in the chain.
Note: Do not lubricate chain (Figure 2). Lubricants may attract foreign materials
to the chain and shorten it's life.
6

Warnings
1) Do not attempt to service machine while running.
2) Guards and doors must be in place at all times during operation.
4) Do not wear loose fitting clothing or jewelry while using this machine.
5) Keep hands, and arms out of the hopper (Figure 3) and away from any
moving parts.
Figure 3
6) Do not leave the machine unattended while running.
7) Keep hands and face away from hose end while machine is operating.
8) Only trained personnel who have read this manual should be authorized to
operate this machine.
9) Do not use objects to push material in the hopper.
10) Keep cutting tools (utility knives for example) away from the hopper opening
to avoid having these items fall into the hopper and damage the machine.
7

Operating Instructions
1) Starting the Accu1® 9300:
- Plug the (2) 9300 power inlets (Figure 3, black cords)into (2) dedicated
15 amp, 120 volt, grounded circuits using 10/3 AWG cords.
Figure 3
(Note: When using generators, make sure they are commercial grade and
and have a minimum wattage of 7500 watts).
- Attach hardwired remote to 9300 remote inlet (Figure 4, orange cord)
machine using remote cord. Make sure the remote switch is in the "Off"
position.
Figure 4
8

- Emergency Stop should be in the "Off" (out) position (Figure 5, red
switch).
Figure 5
- Open Slide Gate to the appropriate position and secure with pin (Figure
6).
- Depress Start Switch (Figure 5, green) and release. The control circuit
and remote are now actuated .
- Set remote switch to "On" for air & material and "Blower Only" for just
air.
2) Hoses:
- Attach 3" x 50' hose to the Airlock Exhaust Pipe (Figure 6, left) using a
hose clamp. Attach additional hose as required using the appropriate
connectors / reducers using hose clamps.
Figure 6
9

2) Stopping:
- Close the slide gate.
- Set the remote switch to "Blower Only" or "Air" depending on the
remote until the hose is clear.
- Turn remote to the "Off" position.
- Push Stop Switch (red). Note: This switch must be pulled out for the
controls to function.
3) Override Switch (use only when control circuit has failed):
- Flip up protective cover (Figure 5).
- Actuate toggle switch. Red Indicator Light, blower, and agitator motor
should come on. Remote will not affect the function of the override
switch.
- To Stop: flip toggle or protective cover down.
10

Machine Settings
Open Blow:
Slide gate fully open.
Air Speed: 8 - 10
Hose: 3"x 50' blowing hose all the way to the attic.
Wall Spray (all fibers):
Set slide gate open to 7"(10th hole).
Air Speed: 6
Hose: 3''x 50' to 3'x50' to 2.5"x50' to spray nozzle.
Dense Packing:
Set slide gate open to 3" (4th hole).
Air Speed: 6 (3.0 psi minimum)
Hose: 3"x 50' to 2.5"x50' to 2"x50' to reducer to wall tube.
Note: All the above are suggested settings and may vary depending on operating
conditions. For attics and dense packing, reduce feed slide gate opening if
clogging occurs. Increase opening to maximize production if material is moving
freely. For wall spray, reduce gate opening if material is too dry; increase gate
opening if too wet.
11

Airlock Seal Change Instructions
Regular maintenance on your Accu1® blowing and spraying machine will extend
the life of the equipment and provide better production. Replace all your seals as
soon as a decrease in production occurs (typically when the outlet pressure
drops below 3.0 psi). Airlock seal life may vary dramatically because of such
factors as the type and quality of the material used (the more abrasive the
material; the shorter the life) and damaging objects like knives, hammers, and
nails.
Tools required: pipe wrench, flat screw driver, 1/2" and 7/16" sockets, Allen
Wrench set, exterior/ clear/silicone window caulk, WD40 or similar penetrant.
To Replace Seals:
1) Flip the machine upside down.
2) Loosen chain tensioner.
Belt tentioner, airlock sprocket, chain tensioner, and large pulley
Figure 7
3) Remove chain.
4) Remove sprocket from airlock.
12

Airlock, blower support bar, and blower connector hose
Figure 8
5) Remove the (2) bolts that hold airlock to front of the machine.
6) Remove the (8) screws holding the airlock to the bottom of the
hopper.
7) Remove blower connector hose (black) from airlock inlet located on
the square tube behind the airlock sprocket.
8) Remove blower support bar and blower and set both aside.
9) Use a flat screwdriver to pry the airlock off the 9300 cabinet. There
will be silicone caulk bead between the airlock and the hopper.
10) Lift up on the back of airlock and remove the airlock from unit setting
it on a flat surface.
Airlock shell, front (with 3" tube)plate and back plate, rotor, and seals
Figure 9
11)Remove the rubber seals from the airlock rotor.
13

Airlock front plate, bearing retainers, bearings, and filter
Figure 10
12) Remove the (2) bearing retainers from airlock.
13) Loosen the set screws on the bearings and remove the bearings from
airlock rotor shaft.
14) Remove front plate from airlock.
15) Remove rotor and inspect for bent or damaged blades.
16) Remove felt washers from the rotor shaft.
17) Clean rotor and scrape silicone from airlock plate.
18) Slide new felt washers onto rotor applying silicone in between last
felt washer and rotor blade.
Rotor, felt and foam washers
Figure 11
19) Put the rotor back into airlock in reverse order.
20) Apply silicone to airlock front plate put plate back onto airlock.
21) Replace bearings and retainers on airlock. Note: It's usually a good
idea to install new bearings when doing a rotor seal change.
22) Align rotor evenly between the front and back airlock plates.
23) Tighten bearing set screws. Use Loctite if available.
14

24) Reinstall seals so the thicker side (or side without seams) of the seals
touch the airlock shell.
25) Apply a thread penetrant like WD40 to the outside of the seals.
26) Using a pipe wrench on the sprocket, turn the rotor and seals.
27) Use a flat screwdriver to cup seals on edges.
Airlock housing and shredder
Figure 12
28)Scrape old silicone off airlock and housing. Reinstall airlock the same
way as it was removed.
29) Put bolts back and tighten.
30) Replace blower support bar and blower and tighten.
31) Replace the sprocket and chain and line up chain tighten sprocket
and chain and tensioner.
32) Flip machine back over making sure everything is tight and secure.
33) Be sure to replace agitator paddles if worn will reduce production.
15

Troubleshooting
Problem
Cause
Solution
Machine will not run
1) Power cord(s) not
plugged in.
2) Faulty power cord.
3) Circuit breakers not
reset.
4) Start Switch (green)
not depressed.
5) Faulty remote or
remote cord.
1) Plug in cords.
2) Replace or repair
power cord.
3) Reset circuit breakers.
4) Depress Start (green)
switch.
5) Replace remote or
remote cord.
Machine runs without
moving material
1) Material slide gate
closed.
2) Blowing hose clogged.
3) Blockage between
blower and airlock
(Machine run without a
filter).
1) Open gate to proper
setting.
2a) Remove hose clog.
2b) Reduce material
feed.
3a) Remove blockage
between airlock and
blower .
3b) Make sure filter is in
place.
Low Air Flow
1) Clogged Filter.
2) Hose too long.
3) Blower Control dial set
too low.
4) Air leak into hopper
(blowback).
5) Hose between blower
and airlock damaged.
1) Replace filter.
2) Shorten hose length.
3) Increase Blower
Control setting.
4) Replace airlock seals.
5) Replace hose between
blower and airlock.
Remote will not operate
1) Start Switch not
depressed.
2) Remote cord not
plugged in.
3) Faulty remote or
remote cord.
4) Transformer failure.
1) Depress Start Switch
(green).
2) Plug in remote cord.
3) Replace remote cord.
4) Replace transformer.
Blower runs, but augers
do not
1) Drive Motor thermal
breaker tripped.
2) Obstruction in hopper
or airlock.
3) Drive belt slipping.
4) Faulty auger relay.
1a) Use 10/3 AWG power
cords.
1b)Reset breaker when
motor is cool.
2 & 3a) Remove
obstruction in hopper or
airlock.
3b) Replace drive belt.
4) Replace relay.
Augers turn, blowers
don't run
1) Faulty speed control.
2) Faulty blower relay.
1) Replace speed control.
2) Replace relay.
16

Exploded Views / Parts
17

18

19

20
Table of contents
Popular Power Tools manuals by other brands
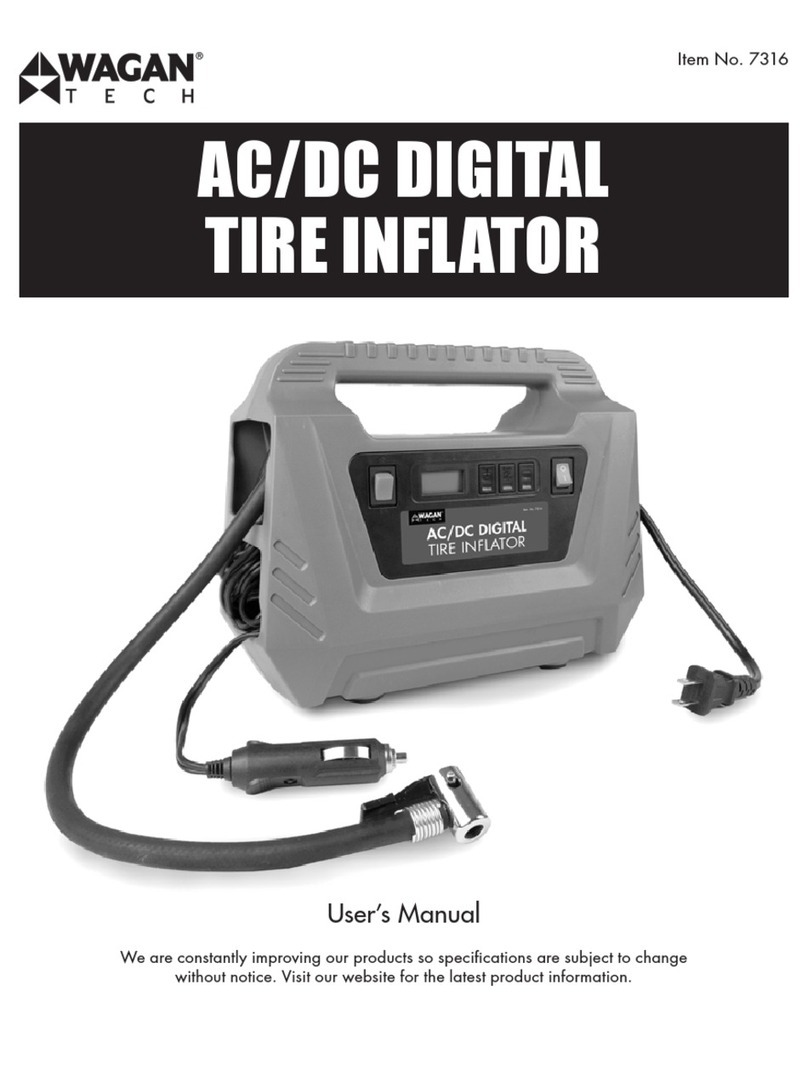
Wagan
Wagan 7316 user manual

Vestil
Vestil EPC Series Use and maintenance manual

Würth
Würth STP 140 EXACT-S Translation of the original operating instructions
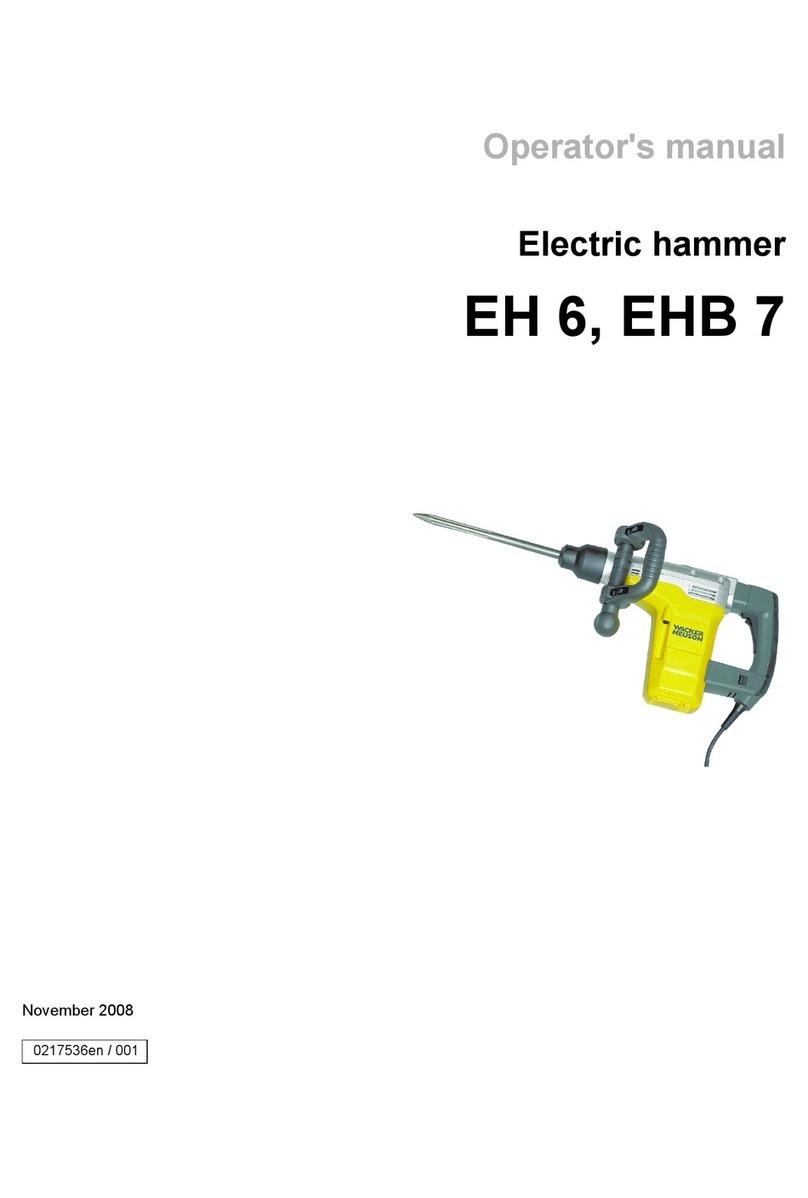
Wacker Neuson
Wacker Neuson EH 6 Operator's manual
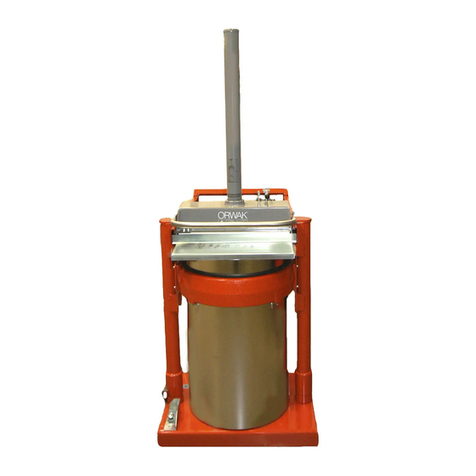
Tomra
Tomra Orwak 5030 Series operating instructions
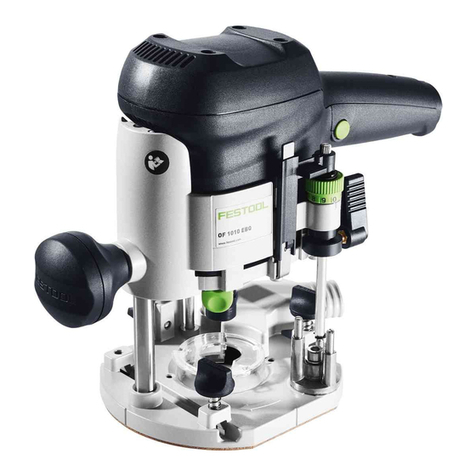
Festool
Festool OF 1010 EQ Original operating manual/spare parts list