Aerotech ANT95R Series User manual

Revision: 1.07.00
ANT95R
HardwareManual

Global Technical Support
Go to www.aerotech.com/global-technical-support for information and support about your Aerotech products. To get
help immediately,contact aservice officeor your salesrepresentative(Support@aerotech.com). Include your customer
order number in your email.
Software Support: Aerotech offersa rangeof software packagesreadily availablefor download. Freesoftwareis
availablefor instant download. Chargeablesoftwarerequiresacurrent softwarekey. Link: SoftwareDownloads
Software Activation: Thefollowinglink providesinformation and resourcesto activate your Aerotech software.
Link: SoftwareActivation
Manuals, Help Files, and Cable Drawings: Browse adirectory of manuals,help files,and cabledrawingsfor Aerotech
softwareand hardwareproducts. Link: BrowseManuals,Help Files,and CableDrawings
Frequently Asked Questions: The Frequently Asked Questions(FAQs)section providesanswersto most common
questionsabout Aerotech products. Link: Product FAQs
Product Training: View traininginformation and schedulea training class. Link: TrainingSessions
Request Product Repair or Return: Weoffer completeserviceand repair servicesfor all of our products. Learn more
about our pricing and warranties,plusaccessthe formsrequired for many Global Technical Support port requests.
Link: Repair & Return
Remote and Field Service Technical Support: Schedulearemotesession now or afield service
appointment. Link: RemoteTechnical Support
Thismanual containsproprietary information and may not bereproduced,disclosed,or used in whole or in part without
the expresswritten permission of Aerotech,Inc. Product namesmentioned herein are used for identification purposes
only and may betrademarksof their respectivecompanies.
Copyright © 2010-2021,Aerotech,Inc.,All rightsreserved.

ANT95RHardware Manual Table of Contents
Table of Contents
ANT95R Hardware Manual 1
Tableof Contents 3
List of Figures 4
List of Tables 5
Safety Proceduresand Warnings 6
EU Declaration of Incorporation 7
Chapter 1: Overview 9
1.1. Environmental Specifications 10
1.2. Accuracy and Temperature Effects 10
1.3. BasicSpecifications 11
Chapter 2: Mechanical Specifications and Installation 13
2.1. Unpackingand Handlingthe Stage 13
2.2. Dimensions 14
2.3. SecuringtheStageto theMounting Surface 16
2.4. Attachingthe Payload to theStage 18
Chapter 3: Electrical Specifications and Installation 21
3.1. Motor and Feedback Connectors 22
3.2. Motor and Feedback Wiring 24
3.3. Motor and Feedback Specifications 25
3.4. Limits,Marker,and Machine Direction 27
3.5. Motor and Feedback Phasing 28
Chapter 4: Maintenance 31
4.1. Service and Inspection Schedule 31
4.2. Cleaningand Lubrication 32
4.3. Troubleshooting 33
Appendix A: Warranty and Field Service 35
Appendix B: Revision History 37
Index 39
www.aerotech.com 3

Table of Contents ANT95RHardware Manual
List of Figures
Figure2-1: ANT95RDimensions 14
Figure2-2: ANT95RMounting Plate(-MP)Dimensions 15
Figure2-3: MountingHolePattern 17
Figure2-4: Load Orientations 19
Figure2-5: Cantilevered Load Capabilities 19
Figure3-1: Motor and Feedback Wiring 24
Figure3-2: MachineDirection 27
Figure 3-3: Hall Phasing 28
Figure3-4: AnalogEncoder PhasingReferenceDiagram 29
Figure3-5: Encoder Phasing ReferenceDiagram (Standard) 29
4 www.aerotech.com

ANT95RHardware Manual Table of Contents
List of Tables
Table 1-1: ANT95RModel NumberingSystem 9
Table 1-2: Environmental Specifications 10
Table1-3: ANT95RSeriesSpecifications 11
Table2-1: Stageto MountingSurfaceHardware 16
Table3-1: Motor and Feedback Pinouts 23
Table3-2: Feedback Specifications 25
Table3-3: Motor Specifications 26
Table3-4: Encoder Resolution 26
www.aerotech.com 5

Electrical Safety ANT95RHardware Manual
Safety Proceduresand Warnings
Thismanual tellsyou how to carefully and correctly useand operatetheANT95R.
lRead all partsof thismanual beforeyou install or operatethe ANT95Ror beforeyou do
maintenanceto your system.
lTo prevent injury to you and damageto the equipment,obey theprecautionsin thismanual.
lAerotech continually improvesitsproduct offerings; listed optionsmay besuperseded at any
time. All drawingsand illustrationsarefor referenceonly and were completeand accurateasof
thismanual’srelease. Refer to www.aerotech.com for the most up-to-dateinformation.
If you do not understand the information in thismanual,contact AerotechGlobal Technical Support.
DANGER: Thisproduct containspotentially lethal voltages. To reducethe possibility of
electrical shock,bodily injury,or death thefollowing precautionsmust befollowed.
1. Accessto theANT95Rand component partsmust berestricted while connected to a
power source.
2. Do not connect or disconnect any electrical componentsor connecting cableswhile
connected to apower source.
3. Movingpartscan causecrushingor shearing injuries. Accessto all stage and motor
partsmust berestricted while connected to apower source.
4. Disconnect electrical power before servicing equipment.
5. All componentsmust beproperly grounded in accordancewith local electrical safety
requirements.
6. Operator safeguardingrequirementsmust beaddressed during final integration of
the product.
WARNING: To prevent damageto the equipment and to decreasethe risk of electricshock
and injury,obey the precautionsthat follow.
1. Cablescan pose atripping hazard. Securely mount and position all system cablesto
avoid potential hazards.
2. Do not expose thisproduct to environmentsor conditionsoutsideof the listed spe-
cifications. Exceeding environmental or operating specificationscan cause damage
to the equipment.
3. TheANT95R stageactuator unit must bemounted securely. Improper mounting
can result in injury and damageto theequipment.
4. Use carewhen movingtheANT95Rstage actuator unit. Liftingor transportingthe
ANT95R stage actuator unit improperly can result in injury or damageto the
ANT95R.
5. If theproduct isused in amanner not specified by the manufacturer,the protection
provided by theproduct can be impaired and result in damage,shock,injury,or
death.
6. Operatorsmust betrained beforeoperating thisequipment.
7. All service and maintenancemust be performed by qualified personnel.
6www.aerotech.com

ANT95RHardware Manual Declaration of Conformity
EU Declaration of Incorporation
Manufacturer:
Aerotech,Inc.
101 Zeta Drive
Pittsburgh,PA15238-2811
USA
herewith declares that the product:
ANT95RStage
is intended to be incorporated into machinery to constitute machinery covered by the
Directive 2006/42/EC as amended;
and that the following harmonized European standards have been applied:
EN ISO 12100:2010
Safety of machinery - Basic concepts, general principles for design
EN 60204-1:2010
Safety of machinery - Electrical equipment of machines - Part
1: General requirements
and further more declares that
it is not allowed to put the equipment into service until the machinery into
which it is to be incorporated or of which it is to be a component has
been found and declared to be in conformity with the provisions of the
Directive 2006/42/EC and with national implementing legislation, for
example, as a whole, including the equipment referred to in this
Declaration.
Thisistocertifythat theaforementioned product isin accordancewith theapplicable requirementsof the
followingDirective(s):
EU 2015/863 Directive,Restricted Substances(RoHS 3)
Authorized Representative: Simon Smith,European Director
Address: Aerotech Ltd
TheOld Brick Kiln,Ramsdell,Tadley
HampshireRG26 5PR
UK
Name / Alex Weibel
Position Engineer VerifyingCompliance
Location Pittsburgh,PA
Date 4/12/2021
www.aerotech.com 7

Declaration of Conformity ANT95RHardware Manual
8www.aerotech.com
Thispageintentionallyleft blank.

ANT95RHardware Manual Overview
Chapter 1: Overview
IMPORTANT: Aerotech continually improvesitsproduct offerings,and listed optionsmay
besuperseded at any time. Refer to themost recent edition of theAerotech Motion
Control Product Guidefor the most current product information at www.aerotech.com.
Table 1-1: ANT95R Model Numbering System
ANT95R Single-axis Rotary Direct-drive Nanopositioning Stage
Travel (Required)
-360 Continuoustravel
-020 Limited travel,±10 degrees
-180 Limited travel,±90 degrees
Mounting Plate (Optional)
-MP Mounting plate
Performance Grade (Required)
-PL1 Baseperformance
-PL2 High-accuracy performance
www.aerotech.com Chapter 1 9

Overview ANT95RHardware Manual
1.1. Environmental Specifications
WARNING: Do not exposethisproduct to environmentsor conditionsoutside of the
listed specifications. Exceedingenvironmental or operating specificationscan cause
damageto the equipment.
Table 1-2: Environmental Specifications
Ambient
Temperature
Operating: 10° to 35° C(50° to 95° F)
Theoptimal operating temperatureis20° C±2° C(68° F±4° F). If at any timethe
operatingtemperaturedeviatesfrom 20° Cdegradation in performancecould
occur.
Storage: 0° to 40° C(32° to 104° F)in original shippingpackaging
Humidity Operating: 20%to 60%RH
Storage: 10%to 70%RH,non-condensing in original packaging. The stageshould be
packaged with desiccant if it isto bestored for an extended time.
Altitude Operating: 0 m to 2,000 m (0 ft to 6,562 ft) above sealevel
Contact Aerotech if your specificapplication involvesuseabove2,000 m or below
sealevel.
Vibration Use thesystem in alow vibration environment. Excessivefloor or acoustical
vibration can affect system performance. Contact Aero for information regarding
your specificapplication.
Protection
Rating TheANT95Rstagesarenot suited for dusty or wet environments. Thisequatesto an
ingressprotection rating of IP00.
Use Indoor useonly
1.2. Accuracy and Temperature Effects
Aerotech productsare designed for and built in a20°C(68°F)environment. Extremetemperature
changescould causeadecrease in performanceor permanent damageto theANT95R. At aminimum,
the environmental temperaturemust becontrolled to within 0.25ºCper 24 hoursto ensurethe ANT95R
specificationsarerepeatableover an extended period of time. Theseverity of temperatureeffectson all
specificationsdependson many different environmental conditions,including how the ANT95Ris
mounted. Contact thefactory for moredetails.
Theaccuracy specification of ANT95Rseriesstagesismeasured 25 mm above thetablewith thestagein
an unloaded condition. The stageisassumed to be fully supported by amounting surface meetingor
exceeding thespecification in Section 2.3.
10 Chapter 1 www.aerotech.com

ANT95RHardware Manual Overview
1.3. BasicSpecifications
Resolution isdependent on encoder resolution and controller interpolation.
Table 1-3: ANT95R Series Specifications -020 -180 -360
Rotation Angle 20° 180° ±360° Continuous
Accuracy(1) -PL1 10 arc sec 10 arc sec 10 arc sec
-PL2 3 arc sec 3 arc sec 3 arc sec
Resolution (Minimum Incremental
Motion) 0.01 arc sec 0.01 arc sec 0.01 arc sec
Bidirectional Repeatability(1) 1.5 arc sec 1.5 arc sec 1.5 arc sec
Unidirectional Repeatability 0.5 arc sec 0.5 arc sec 0.5 arc sec
Tilt Error
Motion Synch Not applicable Not applicable 10 arc sec
Asynch Not applicable Not applicable 3 arc sec
Axial Error
Motion(1) Synch Not applicable Not applicable 2 μm
Asynch Not applicable Not applicable 0.5 μm
Radial Error
Motion(1) Synch Not applicable Not applicable 3 μm
Asynch Not applicable Not applicable 1 μm
Maximum Speed 20 rpm 20 rpm 200 rpm
Maximum Acceleration 400 rad/s2400 rad/s2400 rad/s2
In-Position Stability(2) 0.005 arc sec 0.005 arc sec 0.005 arc sec
Aperture 11 mm (0.433 in) 11 mm (0.433 in) 11 mm (0.433 in)
Maximum Torque (Continuous) 0.2 N·m 0.2 N·m 0.2 N·m
Load
Capacity(3)
Axial 2.0 kg (4.4 lb) 2.0 kg (4.4 lb) 2.0 kg (4.4 lb)
Radial 1.5 kg (3.3 lb) 1.5 kg (3.3 lb) 1.5 kg (3.3 lb)
Moment 2 N·m 2 N·m 2 N·m
Rotor Inertia (Unloaded) 0.00065 kg·m20.00066 kg·m20.00069 kg·m2
Stage Mass 1.2 kg (2.6 lb) 1.2 kg (2.6 lb) 1.2 kg (2.6 lb)
Material Aluminum Body/Black Hardcoat Finish
Mean Time Between Failure 30,000 Hours
1. Certified with each stage.
2. In-Position Jitter listing is 3 sigma value.
3. Axis orientation for on-axis loading is listed (refer to Section 2.4. for offset loading behavior).
• Specifications are for single-axis systems measured 25 mm above the tabletop; performance of multi-axis system is
payload and workpoint dependent. Consult the Aerotech factory for multi-axis or non-standard applications.
• All error motion specifications are measured at 60 rpm.
• For high speed operation, customer payload must be balanced to G1.0 per ISO 1940.
www.aerotech.com Chapter 1 11

Overview ANT95RHardware Manual
12 Chapter 1 www.aerotech.com
Thispageintentionallyleft blank.

ANT95RHardware Manual Mechanical Specifications and Installation
Chapter 2: Mechanical Specifications and Installation
WARNING: The ANT95R must be installed accordingto theinstructionsin thismanual and
any accompanyingdocumentation. Failureto follow these instructionscould result in
injury or damage to the equipment.
2.1. Unpacking and Handling the Stage
WARNING: Manually liftingand movingthestagerequiresaminimum of two people on
either sideof the stage. Refer to Section 1.3. for stagemassspecifications.
lDo not attempt to lift heavy loadssinglehanded.
lFollow theliftinginstructionsand only manually lift from thespecified surfaces(if
liftinghardwarehasn't been supplied).
lDo not use any of thecablesaslifting points.
WARNING: It isthe customer'sresponsibility to safely and carefully lift thestage.
lMakesure that all movingpartsare securebeforemovingthe ANT95R. Unsecured
movingpartsmay shift and causebodily injury.
lImproper handlingcould adversely affect the performance of theANT95R. Usecare
when movingthe ANT95R.
IMPORTANT: If any damagehasoccurred during shipping,report it immediately.
Carefully remove theANT95R from itsprotectiveshipping container. Gently set theANT95Ron a
smooth,flat,and clean surface.
Beforeoperatingthe ANT95R,it isimportant to let it stabilizeat room temperaturefor at least 12 hours.
Allowing it to stabilizeto room temperaturewill ensurethat all of thealignments,preloads,and
tolerancesarethe same asthey werewhen tested at Aerotech. Usecompressed nitrogen or clean,dry,
oil-freeair to removeany dust or debristhat hascollected duringshipping.
Each ANT95Rhasalabel listing thesystem part number and serial number. These numberscontain
information necessary for maintainingor updatingsystem hardwareand software. Locate thislabel and
record the information for later reference.
www.aerotech.com Chapter 2 13

Mechanical Specifications and Installation ANT95RHardware Manual
2.2. Dimensions
Figure 2-1: ANT95R Dimensions
14 Chapter 2 www.aerotech.com

ANT95RHardware Manual Mechanical Specifications and Installation
Figure 2-2: ANT95R Mounting Plate (-MP) Dimensions
www.aerotech.com Chapter 2 15

Mechanical Specifications and Installation ANT95RHardware Manual
2.3. Securing the Stage to the Mounting Surface
WARNING: TheANT95Rmust be mounted securely. Improper mountingcan result in
injury or damage to the equipment.
Themounting surface must beflat and haveadequatestiffnessto achievethemaximum performance
from the ANT95Rstage. When it ismounted to a non-flat surface,thestagecan bedistorted whilethe
mountingscrewsare tightened. Thisdistortion will decreaseoverall accuracy. Adjustmentsto the
mountingsurfacemust bedonebeforethe stageissecured.
Inspect themountingsurface for dirt or unwanted residueand clean if necessary. Useprecision
flatstoneson the mountingsurfaceto removeany burrsor high spots. Clean themounting surface with
alint-freecloth and acetoneor isopropyl alcohol and allow thecleaningsolvent to completely dry.
Gently placethe stageon the mountingsurface.
IMPORTANT: To maintain accuracy,themounting surfacemust beflat to within 1 µm per
50 mm.
IMPORTANT: TheANT95Risprecision machined and verified for flatnessprior to product
assembly at thefactory. If machiningisrequired to achieve thedesired flatness,it should
beperformed on the mountingsurfacerather than theANT95R. Shimmingshould be
avoided if possible. If shimmingisrequired,it should beminimized to retain maximum
rigidity of thesystem.
ANT95Rseriesstageshaveafixed mountingpattern (asshown in Figure 2-3).
Tightening torquevaluesfor the mountinghardwarearedependent on the propertiesof thesurface to
which the stageisbeingmounted. Valuesprovided in Tablearetypical valuesand may not beaccurate
for your mountingsurface.
Table 2-1: Stage to Mounting Surface Hardware
Mounting Hardware Typical Screw Torque
M4 by 16 mm [#8 by 5/8 in] SHCS 2.3 N·m
16 Chapter 2 www.aerotech.com

ANT95RHardware Manual Mechanical Specifications and Installation
Figure 2-3: Mounting Hole Pattern
www.aerotech.com Chapter 2 17

Mechanical Specifications and Installation ANT95RHardware Manual
2.4. Attaching the Payload to the Stage
Inspect themountingsurface for dirt or unwanted residueand clean if necessary. Clean themounting
surfacewith alint-freecloth and acetoneor isopropyl alcohol and allow thecleaningsolvent to
completely dry.
Aerotech recommendsthat customersusearepresentativepayload duringstart-up to prevent
accidental damageto thestageand thepayload. Proceed with the electrical installation and test the
motion control system in accordance with the system documentation. Document all resultsfor future
reference. For information on electrical installation refer to Electrical Specificationsand Installation and
the documentation delivered with thestage.
IMPORTANT: If your ANT95R was purchased with Aerotech controls, it might have been
tuned with a representative payload based on the information provided at the time of order. If the
ANT95R is started up without a payload, the servo gains provided by Aerotech with the
shipment may not be appropriate and servo instability can occur. Refer to the controller help file
for tuning assistance.
Thepayload must beflat,rigid,and comparableto thestagein quality to maintain optimum
performance.
IMPORTANT: If possible,use3-point mountingwhen you attach thepayload to thestage.
IMPORTANT: For valid system performance, the mounting interface should be flat within 1 µm
per 50 mm.
WARNING: Refer to thedimensionsin Section 2.2. for maximum allowablethread
engagement. Ascrew extendingthrough thestagetablecan affect travel and damage the
stage.
18 Chapter 2 www.aerotech.com

ANT95RHardware Manual Mechanical Specifications and Installation
Applied loadsshould besymmetrically distributed whenever possible(i.e.,thepayload should be
centered on the stagetableand the entire stageshould becentered on the support structure).
If cantilevered loadsare applied,refer to Figure2-4 to find theloadingcondition. Refer to Figure2-5 to
find the maximum allowableload.
Figure 2-4: Load Orientations
Figure 2-5: Cantilevered Load Capabilities
www.aerotech.com Chapter 2 19

Mechanical Specifications and Installation ANT95RHardware Manual
20 Chapter 2 www.aerotech.com
Thispageintentionallyleft blank.
Table of contents
Other Aerotech Tools manuals
Popular Tools manuals by other brands
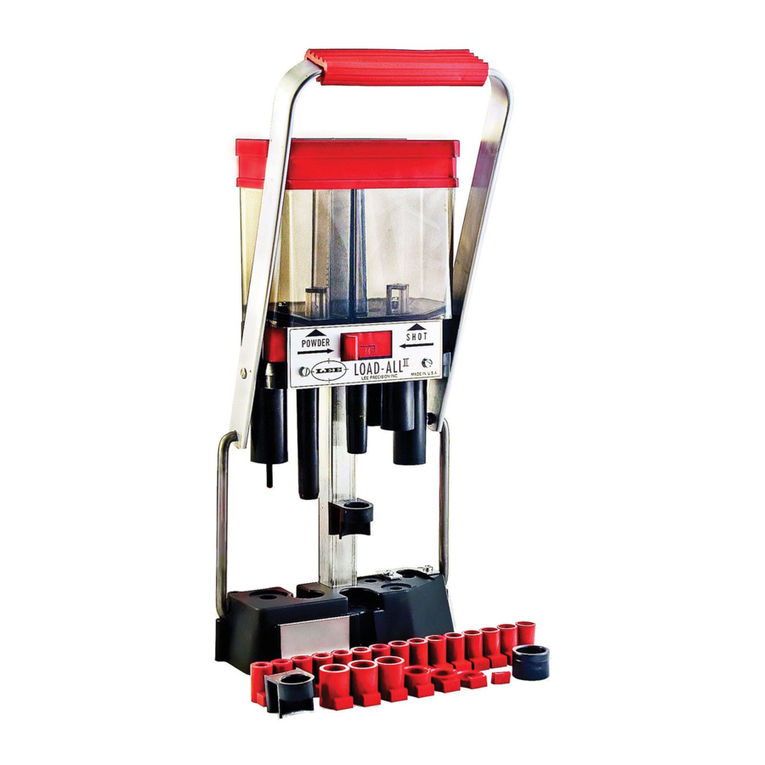
Lee Precision
Lee Precision Load-All II user manual

NSI Solutions
NSI Solutions Rapid Z-CUT instructions
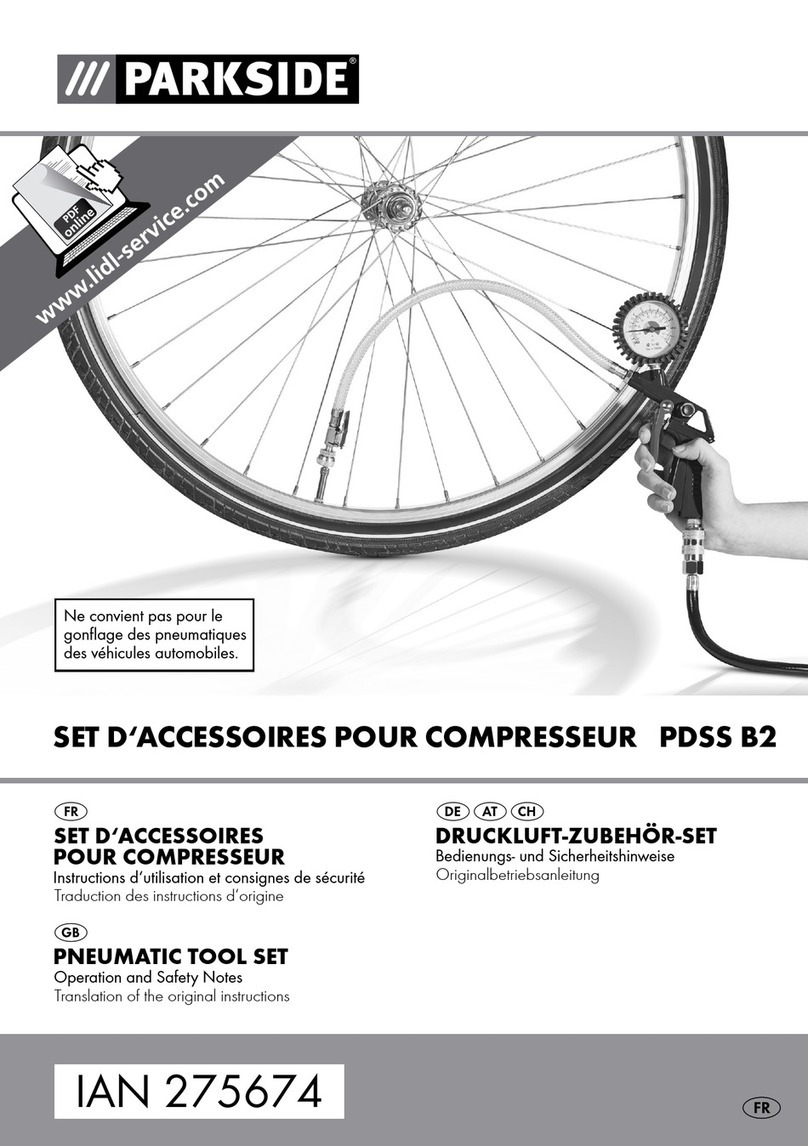
Parkside
Parkside 275674 Operation and safety notes translation of the original instructions
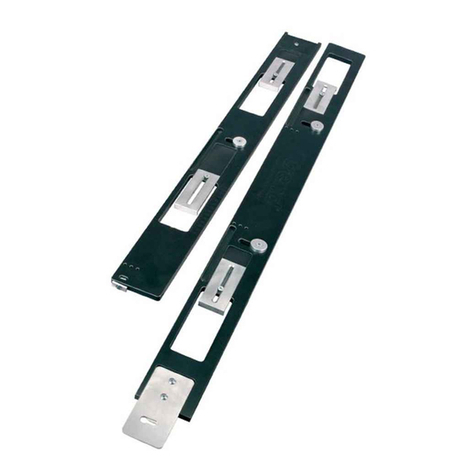
TREND
TREND H/JIG/B manual
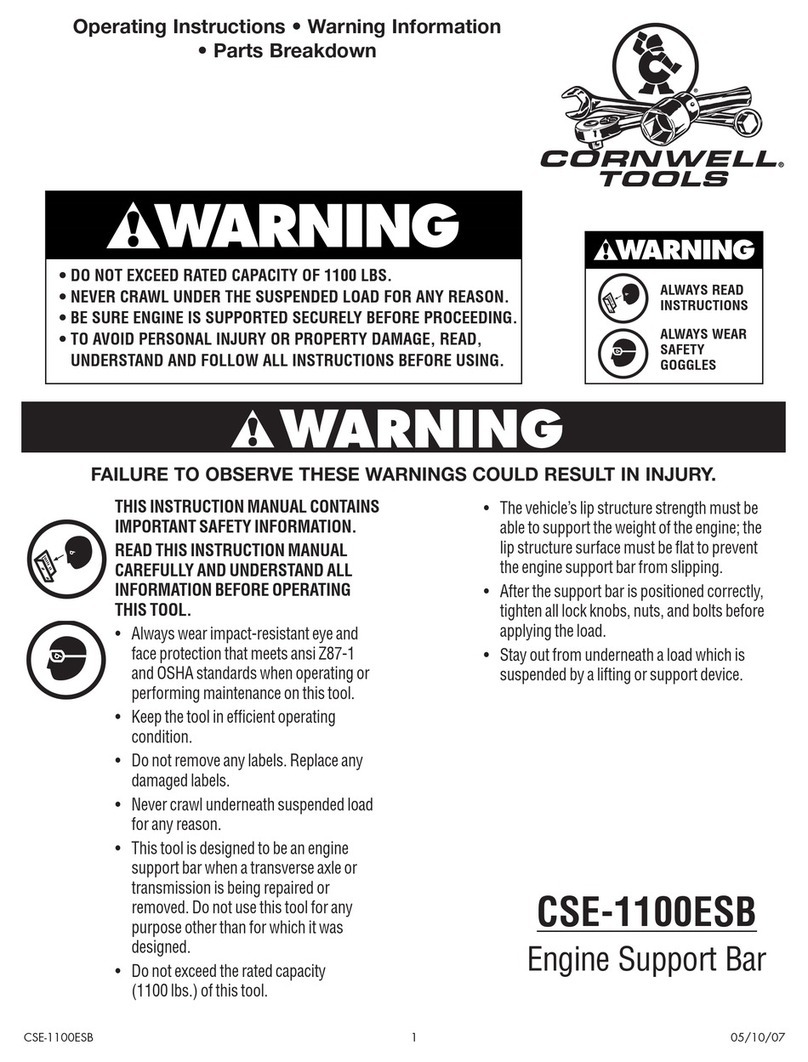
Cornwell Tools
Cornwell Tools CSE-1100ESB operating instructions
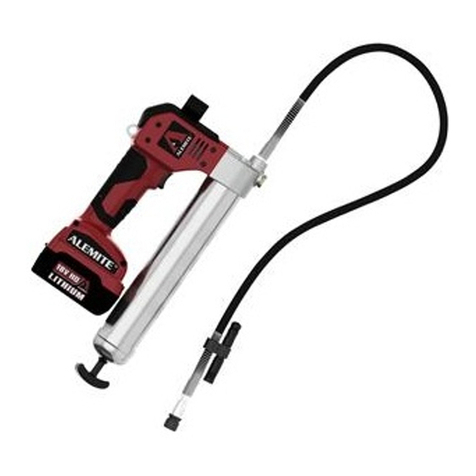
Alemite
Alemite 595 Series Service guide