AheadX SAGI User manual

Tips
Welcome to read AheadX online document. This manual will assist you with the
installation and post-installation checking of SAGI.
Blue text, suggestions and content you may need to know
Orange text, please pay close attention
Red text, must be strictly enforced
Version
Version: V1.0
Update note: Create a document
Time: 2019.03.20
Copyright Notice
The intellectual property rights of this product and the manual are solely owned by
AheadX Technology. Without written permission, any unauthorized copying,
reproduction or sale by any organization or individual is prohibited. Please state the
source is AheadX if you quote or publish any content. The manual should not be
quoted, abridged or modified without any permission
The dimension and weight listed in this manual are approximate values based on
the design and repeated measurements.
All documents have been carefully verified to make sure the accuracy. Related
information is subject to the latest version released by the company.
The company reserves the right to change product specifications without prior
notice. Please pay attention to AheadX's official website
Registered for AheadX Technology (Beijing) Co., Ltd.

Disclaimer
Please read the entire document carefully before using this product. By using this
product, you hereby signify that you have read this disclaimer carefully and agree to
abide by the terms and contents herein. This product is not suitable for children
under the age of 18.
AheadX SAGI is a high quality UAV navigation flight controller. The company shall not
be liable for personal injury, property loss, etc. (including direct or indirect damage)
due to the following reasons:
1. The operator causes damage in the case of alcohol, drug abuse, drug anesthesia,
dizziness, fatigue, nausea and other poor physical or mental condition. Any
compensation for mental injury caused by the accident.
2. The product is not assembled or manipulated in accordance with the correct
guidance of the manual
3. Personal injury or property loss caused by operator’s errors or subjective
judgment
4. Knowing that the relevant equipment is in an abnormal state (such as water
damage, oil damage, soil & sand damage and entry of other unidentified substances
and incomplete assembly, main components with obvious failures, spare parts with
obvious defect or missing), but still use the equipment and cause damages.
5. Any damage caused by flying the drone in magnetic interference zone, radio
interference zone, no-fly zone, or the pilot flies the drone with following conditions
such as in a shadow, poor light, blurred vision and vision obscured
6. Collision, overturns and force majeure as fire, storms, tornadoes, heavy rains,
floods, tsunamis, earthquakes etc.
7. Direct or indirect liability for any illegal use, or other unauthorized purposes.
8. Third-party liability arising from the use of our software and hardware products ..
9. Any loss caused by obtaining or using our software or hardware and related
manuals through unauthorized ways
10. Other losses that are not within the AheadX’s sphere of accountability
Introduction

The SAGI GNC (Micro Guidance Navigation Control System) is a new generation of
navigation flight control system designed for industrial-grade drones with high
integration, high reliability and high cost performance. According to the national
military standard related detection method, it has passed strict environmental
adaptability and screening tests. It supports VTOL quad plane, fixed wing, helicopter,
multi-rotor and other types of aircraft.
The core sensor adopts the heterogeneousdual redundancy IMU. Main IMU uses
industrial grade component which can work at -45℃~85℃. Sagi can seemlessly
switch to backup IMU when main IMU is not working. It supports automatic switch
between dual redundancy magnetic compass and dual redundancy GNSS module.
To improve its reliability, SAGI comes with all metal cover and J30J connector. SAGI
adopts a decoupled extended Kalman filter, improved L1 guidance rate, and ADRC
controller as core algorithm, which has extremely high precision.
Features and applications
Integrated industrial grade inertial measurement unit, triaxial magnetometer,
barometric altimeter, airspeedometer, GNSS module.
Dual combined navigation systems. Decoupled 17-order extended Kalman filter
to complete the information fusion. Automatically switch between the GNSS/INS
and AHRS/DR navigation modes according to satellite signals
With adaptive controller based on ADRC to improve the control accuracy and
robustness. It can adapt to different altitude and airspeed automatically
Using the adaptive guidance rate, the aircraft mathematical model is dynamically
identified, and the route loop and altitude loop control are highly accurate, and
no adjustment parameters are needed.
SAGI supports automatic take-off, automatic return, automatic landing, route
mode, intelligent protection and other functions.
With built-in global geomagnetic model, and compass calibration has been tested
in polar area. SAGI can complete one-key compass calibration, take off
immediately after satellite positioning.
Powerful remote assistance service. Whenever and wherever you need technical
support, you can request AheadX's official remote technical support via the
Internet.
10 routes (The 10th route is the landing route for fixed wing or VOTL), max 200
waypoint of each route. SAGI is able to switch the route automatically
With fixed-point, equal time, equal distance shooting function. Records the POS
data of the shooting point.

Any installation method. SAGI comes with installing angle correction and lever
arm compensation. It can be mounted at any angle and position
Simulation training function. SAGI can work with AheadX's semi-physical
simulator for pilot’s daily simulation training.
Built-in black box data logging function, it is able to cyclically record
approximately 60 minutes flight data . Supports external data recorders,
recording up to 2000 hours flight data.
Online upgrade. User can quickly get the latest firmware and ground station
software on the Internet
Technical Parameters

Item Maximum Standrad Minimum Unit Remarks
Weight 103 g
Volume 68 * 43 *
33 mm
Supply voltage 25(53 HV
version)12 9 V
Power
consumption 1.2 W
Working
temperature 85 25 -40 ℃
Attitude
accuracy 0.5 ° dynamic, after GNSS
positioned
Angular
velocity
measurement
range
300 -300 °/s
Acceleration
measurement
range
18 -18 g
Positioning
accuracy 1 m CEP
Speed
measurement
accuracy
0.1 m/s
Height
measurement
range
10000 -400 m
Airspeed
measurement
range
140 0 m/s
Ground speed
measurement
range
500 0 m/s
Servo control
channel 10 CH

SBUS input
channel 1 CH Backup radio control
data
SBUS output
channel 1 CH
Servo update
frequency 200 50 Hz
telemetry
communication
interface
1 CH
RS232 level, need to
turn off built-in data
link
Voltage
monitoring
channel
2 CH
Voltage
monitoring
range
58 0 V
Engine speed
monitoring
channel
2 CH
Engine speed
monitoring
range
65535 0 RPM
CAN interface 1 bus
Used for smart
battery, optical
camera and other
equipment
Extended serial
port 1 CH
forwarding data to
user's
equipment,connecting
external black box
and other equipment
Flight control installation and
connection

Thanks for purchasing our Leo GNC. This chapter will guide you how to install and
tune the flight controller. You can make the cables& wires and check it according to
the instruction. Please read this chapter carefully and make the installation strictly
abide to the guidance.
Self-prepared equipment
User needs to prepare the following equipment to work with:
Drone : Quad wing ——Hybrid fixed wing with four rotor configuration.
Fixed wings—— Various fixed wings
Multi-rotor—— multi-rotor drone.
Data link: with RS232 interface.
Auxiliary control joystick: AheadX A4RC01 auxiliary joystick is recommended;
Support SBUS output; Radio controller with more than 10 channels (eg FUTABA
T8FG/T14SG).
computer:Recommend Intel Core i3 processors, 2GB memory, 200M hard disk
space or better configuration to install our ground station software
Cable
SAGI adopts 30J-37TJL rectangular connector with 37 durable cables.
User can make cables according to the interface or buy AheadX’s finished cables.
Interface definition
Interface definition

Serial
number Pin Description:
1 P+: power supply "+"
Flight control power supply, DC9~25V
(standard version) 9~53V (HV version))
2PGND: power supply
"-"
3 GND: Ground
For communicating with external black box4
T2: Serial port 2
transmission, RS232
level
5 GND:Ground
6 P1+: positive output DC 5V/0.8A for powering low-power airborne
equipment,
It is strictly forbidden to supply power to ESC
and servo with 5V output.
7P1\_GND+: positive
output
8R1: Serial port 1 , 232
level
Connect to data link, it is recommended to
use the AheadX DL900 products9 T1: Serial port 1 , 232
level
10 GND:Ground
11 CAN\_H: CAN bus H
pin
CAN interface, used for connecting with other
AheadX's products, such as smart batteries,
external magnetic compass, height-finding
radar, etc.
12 CAN\_H: CAN bus L
pin
13 P2+: data link
positive input The voltage is the same as the flight control
power supply P+, the maximum current is 1A.
14 P2\_GND:data link
negative output
15 SBusIn: SBus signal
input DC 5V/0.8A for powering low-power airborne
equipment,
It is forbidden to supply power to ESC and
servo with the 5V output.
16
5V: 5V output,
powering the
receiver
17 GND: Ground
18 PWM1:PWMchannel1 Used to control the servo or ESC

19 PWM2:PWM
channel2
20 PWM3:PWM
channel3
21 PWM4:PWM
channel4
22 PWM5:PWM
channel5
23 PWM6:PWM
channel6
24 PWM7:PWM
channel7
25 PWM8:PWM
channel8
26 PWM9:PWM
channel9
27 PWM10:PWM
channel10
28 GND: Ground Ground
29 SBusOut:SBus
control output Used to control the servo or ESC
30 AD1: Voltage
monitoring channel 1
Voltage must be less than 58V
31 AD2: Voltage
monitoring channel 2
32
GND: Ground, for
voltage monitoring
only
33 Reserved: Alternate
RPM monitoring, compatible with 3.3V/5V
34 RPM1:RPM
monitoring 1
35 R5: Serial port 5 , 232
level
Reserved serial port for connecting RTK and
task load commands for transparent
transmission

36
T5: Serial port 5
transmission, RS232
level
37 GND: Serial port
Ground
Precautions
Please pay attention whether the power GND and signal GND are connected or not when using
ESC.
You may meet following problem if the power GND and signal GND are connected:
high current may be led back to flight controller via the signal GND cable if power
GND cable with any cold soldering or virtual open circuit, which may cause the flight
controller to be burnt.
Therefore, user can make following modification to ensure flight controller will not
be burnt even with colder soldering or virtual open circuit.

For example, when connecting nacelleto COM5, user can make self-recovering fuses
connected in series with its GND cable. This will ensure flight controller will not be
affected by external equipment failure.
Please ensure that the voltage or power input and output between all pins meet the above
requirements, otherwise the flight control or other avionics equipment will be burnt.
Please ensure GND cables are connected without any differential pressure(all avionics, including
flight controller), otherwise the flight control or other equipment will be burnt.
If using an RTK GNSS device (eg DG1, etc.), please use the dedicated GND as listed in the table
to avoid possible interference.
The voltage of P1+ and P2+ must be same if supply power at same time.
Equipment connection rules

Flight control power supply
Illustration: power supply exceeds 25V
Cable【1】【2】: "+" and GND of the flight control power input
Cable【6】【7】: Flight control 5V output, for low power equipment (power does not
exceed 2W).
Cable【13】【14】: power input of built-in data link, the voltage must be consistent
with the flight control supply voltage.
Please ensure there is no potential difference between any equipment which connected with flight
controller. Otherwise it may cause flight controller to be burnt.
Data link
SAGI: data communication RS232 level.
Cable【8】【9】【10】 are serial port data receiving, serial port data transmission
and GND. The LINK interface is used for data communication and firmware upgrade.
Please use reliable data transmission device since it will directly affect the
performance of the drone.
Please connect LINK port to your PC with the cable to upgrade firmware if you don't
know the bandwidth and SER of your data transmission device. You may fail to
upgrade firmware when your device cannot transmit data during upgrade.

PWM servo connection
Quad Plan PWM servo connection
SAGI-QP supports 4 channels of PWM multi-rotor ESC input, 6 channels of servo/ESC
input.
PWM output signal does not correspond to RC travel. PWM signal here is completely controlled by
the flight controller. You can ignore the radio control output sequence
There are strict requirements for the ESC connection of the multi-rotor part. User
must remember that right front for PWM1, connect them in counterclockwise order,
which means followed by PWM2~PWM4. Usually, it only needs to connect the signal
cable and the GND cable. Does not need 5V power supply (except for the special
model ESC, it is forbidden to take power from the flight control).
Please connect the cable【18】【19】【20】【21】four PWM outputs in turn, and
well connect GND. (example: cable [2])
Firmware 2.0 or above supports X4 and X4R configuration. Please choose the correct
configuration according to your requirement.
Please calibrate the throttle range with the radio control before using ESC. Calibrate the range with
default setting. The standard range is 1100μs~1940μs. Fail to calibrate the throttle range will result
in a power system control failure, and the resulting defect or accident is artificial.
PWM 5~PWM 10 can be connected to the servo and fixed-wing ESC (or throttle
servo) according to custom and certain rules
Please keep in mind all ESC connection sequence for following parameter adjustment.

It is strictly forbidden to supply power to the servo ESC with the 5V output; Forbidden to connect
5V output to flight controller if the fixed-wing ESC has a 5V output; Forbidden to supply power to
the servo with 5V output. These may cause accident or damage due to insufficient power supply
Connection example (for reference only):
PWM-5 number [22]: left aileron;
PWM-6 number [23]: right aileron;
PWM-7 number [24]: elevator;
PWM-8 number [25]: rudder;
PWM-9 number [26]: throttle;
PWM-10number [27]: Camera shutter
Fixed wing PWM servo connection
SAGI-FW provides 10 channels for PWM servo / ESC .
PWM output signal does not correspond to RC travel. PWM signal here is completely controlled by
the flight controller. User can ignore the radio control output sequence.
Please calibrate the throttle range with the radio control before using ESC. Calibrate the range with
default setting. The standard range is 1100μs~1940μs. Fail to calibrate the throttle range will result
in a power system control failure, and the resulting defect or accident is artificial.
PWM 1~PWM 10 can be connected to the servo and fixed-wing ESC (or throttle servo)
according to custom and certain rules.

Signal connection example
Please keep in mind all ESC connection sequence for parameter adjustment
It is strictly forbidden to supply power to the servo ESC with the 5V output; Forbidden to connect
5V output to flight controller if the fixed-wing ESC has a 5V output; Forbidden to supply power to
the servo with 5V output. These may cause accident or damage due to insufficient power supply.
Connection example (for reference only):
PWM-1 number【18】: left aileron;
PWM-2 number【19】: right aileron;
PWM-3 number 【20】: elevator;
PWM-4 number【21】: rudder;
PWM-5 number 【22】: throttle;
PWM-6 number 【23】: Camera shutter
Multi-rotor ESC connection
SAGI-MR supports a variety of multi-rotor configurations and provides 8-channel
PWM multi-rotor ESC input. The connection sequence as follows:


PWM output signal does not correspond to RC travel. PWM signal here is completely controlled by
the flight controller. You can ignore the radio control output sequence.
Please calibrate the throttle range with the radio control before using ESC. Calibrate the range with
default setting. The standard rangeis 1100μs~1940μs. Fail to calibrate the throttle range will result
in a power system control failure, and the resulting defect or accident is artificial.
SBUS connection
SAGI has specially designed a 16-CH SBUS signal, which is independent of 10
channels of PWM output, it can connect SBUS servos and extend the servo control
PWM output signal does not correspond to RC travel. PWM signal here is completely controlled by
the flight controller. You can ignore the radio control output sequence.
Please set the servo channel of SBUS servo first. For details, please refer to the
relevant manual of SBUS servo
Please correctly record the corresponding settings between servo numbers and
control surfaces. Then connect all the SBUS servo signal cables to the flight
controller's SBusOut in parallel (cable number 【29】), and the servo ground cables
connect in parallel to the ground cable (example: cable No. 【2】). After well
connected, user should wait for the program settings.
It is strictly forbidden to supply power to servo ESC with flight controller's 5V output.
Voltage monitoring
SAGI comes with 2 channels for voltage monitoring. The detection range of each
channel is 0~58V. Cable number to be connected should be [30][31][32]. Flight
controller will be burnt if the monitored voltage exceeds the range. This is an artifical
damage.
Common rules: AD1 for power system voltage, AD 2 for servo voltage. Flight controller will judge
the low voltage and execute different command.Please don’t reverse the connection.

Rpm monitoring
Quad plane & fixed wing: SAGI-QP and SAGI FW come with two channels to
monitor RPM signal inputs, typically used to monitor fixed-wing power system.
The ESC should have RPMoutput; Or use the engineRPMmonitoring module.
SAGI is compatible with 3.3V or 5V signal feedback.
The flight controller can be burnt if user mixed up the voltage and RPM monitoring interface. This is
artificial damage.RPM monitoring must be connected to RPM1 when using a single engine.
Multi-rotor: SAGI-MR reserves one RPM monitoring channel, RPM1. It is only used to
monitor RPM. It can not judge or execute any command.
Auxiliary joystick
User can use a radio control to assist SAGI to control the drone. There are two ways
to do that. Please choose the appropriate way according to your requirement.
1.Receiver connects to data link: supports SBUS-to-USB module to upload radio
control signal to AheadX Space. The signal will be transmitted to FC via data link.
Upstream frequency is 10Hz, and max to 20Hz in remote control mode which
basically meets the control requirement of most drones.
2. Receiver directly connects to FC: install the receiver on the drone, FC will directly
collect the data. But the transmission distance is short, the drone will lose signal no
more than 1km. We don’t recommend this way, please weigh the advantage and
disadvantage carefully.
Flight controller can directly collect the SBUS signal by connecting cable [15] [16] [17]
to the receiver.
BUS signal support: SBUS (example R6208SB) SBUS\_2 (example R7008SB) Please use low
speed mode (70Hz), and avoid using high speed mode (140Hz).
CAN bus air unit
Used to connect AheadX’s avionics, including smart batteries, external magnetic
compass, height finding radar, camera gimbal/pod, smart navigation lights etc.
AheadX‘s CAN HUB or CAN POWER HUB is a better choice if there are many CAN bus
units on the drone .
Please contact AheadX for custom service if user needs a customized CAN unit.

Alternate interface
SAGI reserves T2 channel(cable number 【4】) to connect Halley data recording
module, which can expand the flight data recording time up to 2000 hours.
Serial port R5 and T5 ,(cable number [35] [36]) for external custom avionics, which is
used for transparent transmission, dual redundancy GNSS or RTK .
Equipment installation rules
Due to the need to connect with other avionics equipment, cable welding or plug
connection will be involved. To ensure reliability, the following points should be
noted:
Extend the welding connection, use high temperature resistance, pull resistance, and
silver plating cable as much as possible. In any airborne environment, avoid the
broken core of the cable, damage the outer skin, and excessive welding resistance.
The connector plug should be connected with a self-locking structure and fastened
and dispensed at key parts to improve connection reliability.
Shock absorption requirements
Shock absorption requirements
1. For small drones, user can use rubber damper with the mounting plate to reduce
vibration. Mount the flight controller as close as possible to the center of gravity of
the drone
2. For medium and large drones, user can use gel damping device or high quality
rubber damping device. Please ensure that the entire damping device is well
connected to the fuselage
The shock absorbing mechanism should not be too soft to avoid unpredictable resonance
phenomena or the attitude measurement can not truly reflect the state of the drone.
Recommended shock absorption structure:
AheadX has designed shock absorbers for SAGI , which are standard and
professional version.
The standard (DMP307STD01) adopts a rubber shock absorbing structure that is
easy to use and suitable for most small drones with less vibration

SAGI standard shock absorber (DMP307STD01)
SAGI professional shock absorber (DMP307PRO01)
The professional (DMP307PRO01) adopts an advanced shock absorbing gel structure
with complete shock absorption performance,which is compact and easy to install.
Suitable for drones used in harsh environment.
Table of contents
Popular Controllers manuals by other brands

Dungs
Dungs DGAU. 09/2 Operating and assembly instructions
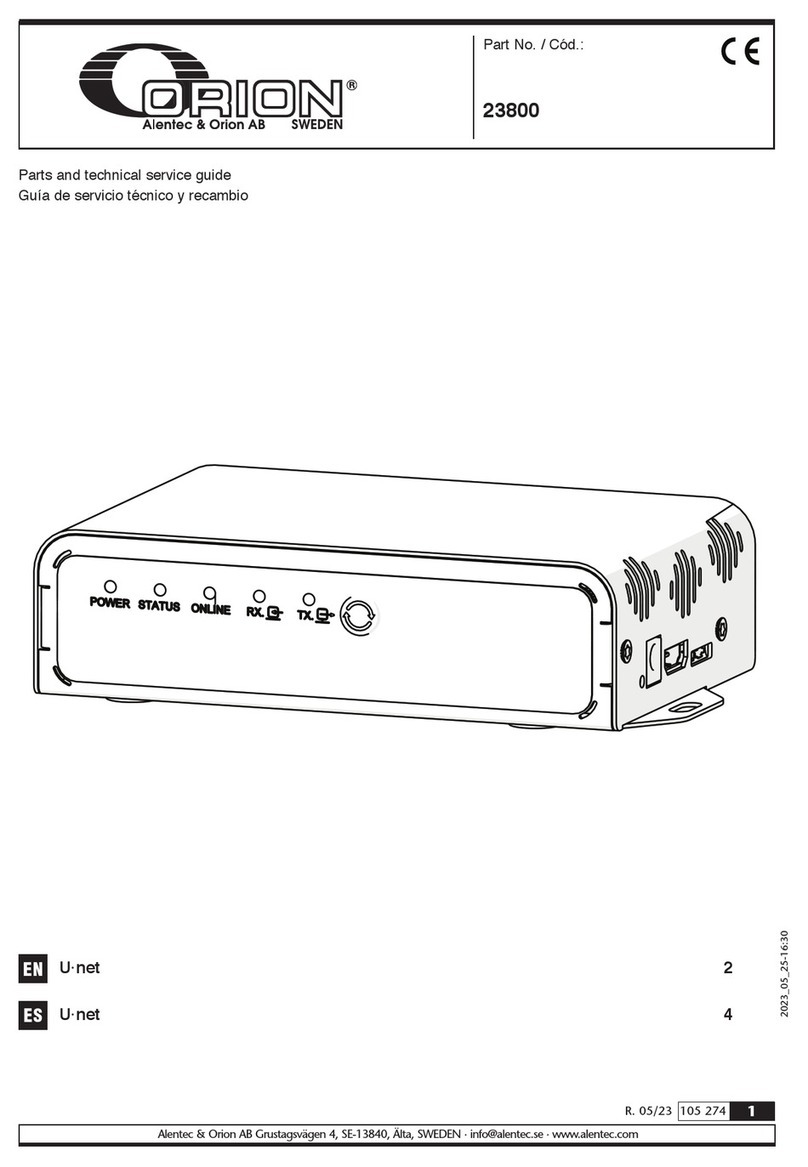
Alentec & Orion
Alentec & Orion NEX-U 23800 Parts and technical service guide

Emerson
Emerson Bettis EHO Installation and operation manual
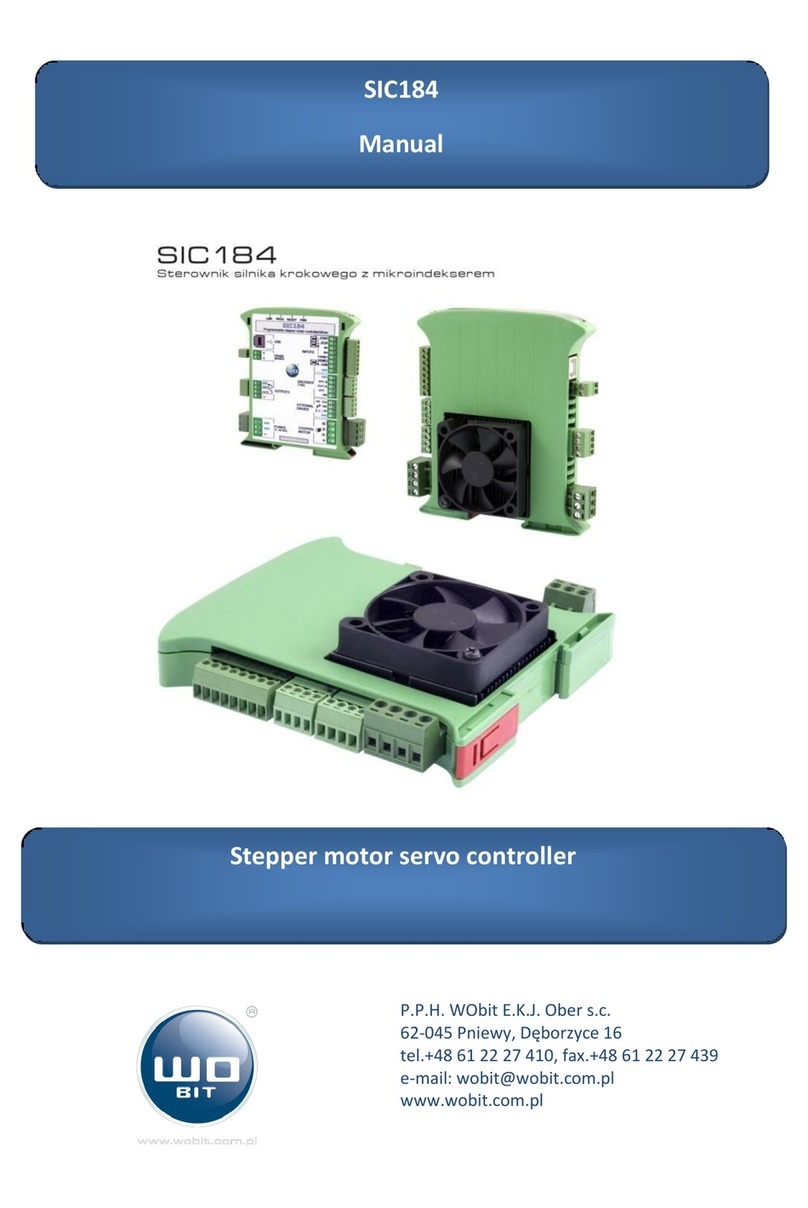
WOBIT
WOBIT SIC184 manual
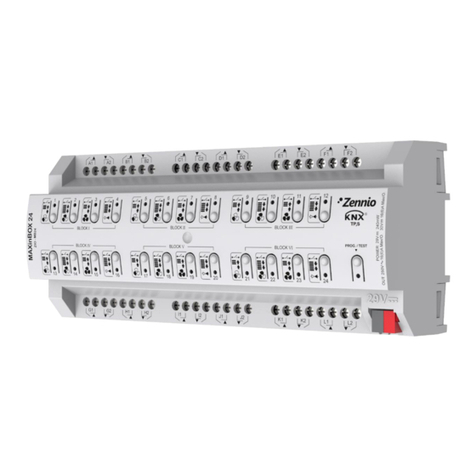
Zennio
Zennio MAXinBOX 24 Technical documentation
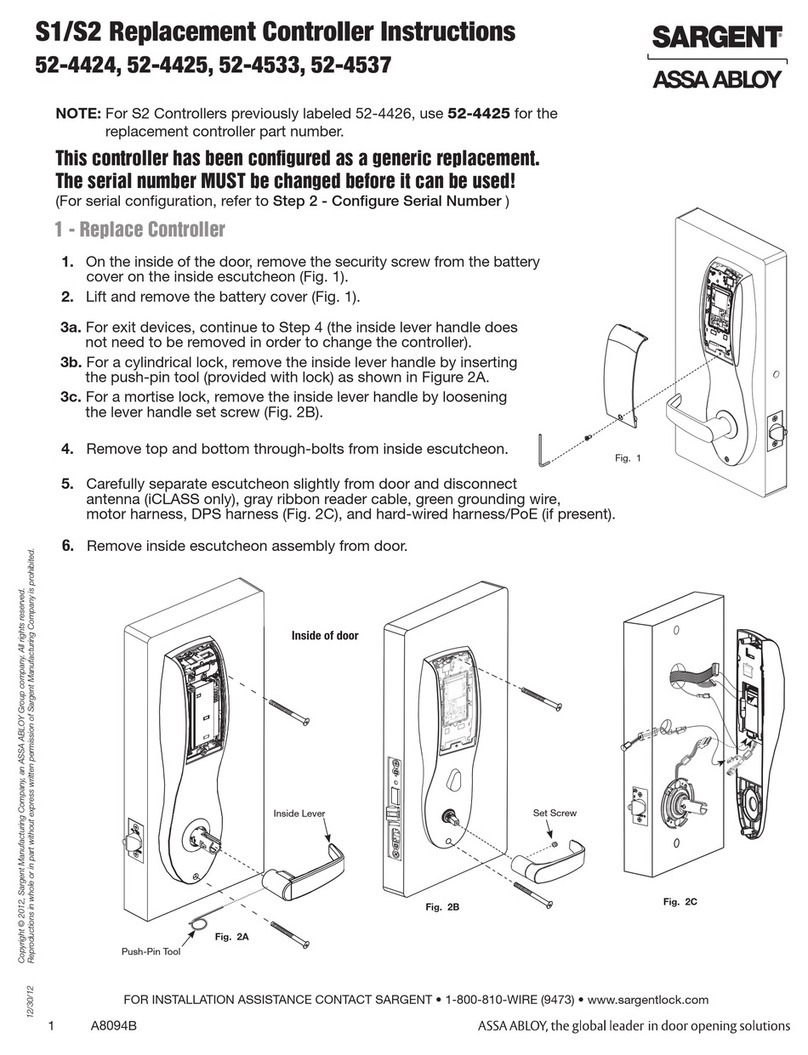
Assa Abloy
Assa Abloy Sargent 52-4424 instructions
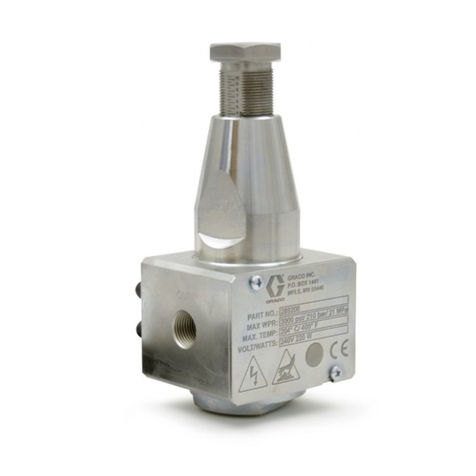
Graco
Graco 289208 Instructions-parts list
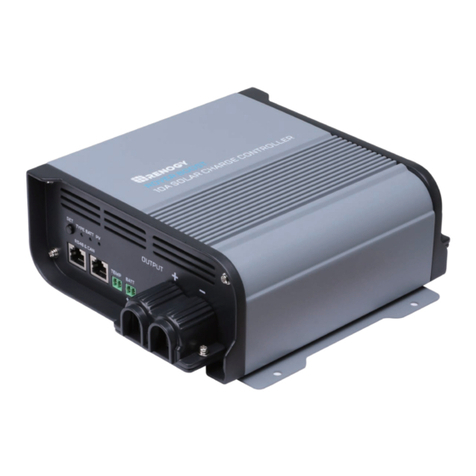
Renogy
Renogy ROVER BOOST manual
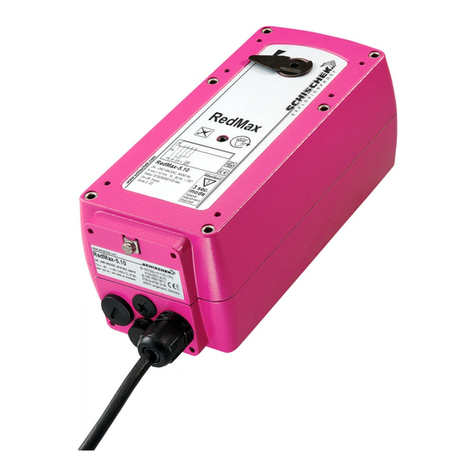
Schischek
Schischek RedMax-Y Series quick start guide

ICM Controls
ICM Controls ICM2811 Installation, operation & application guide
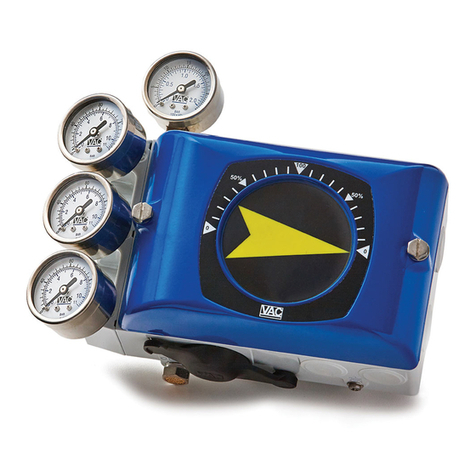
VAC
VAC V200P Installation, operation and maintenance instructions
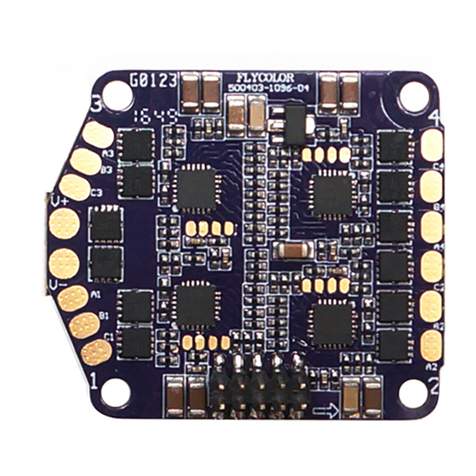
Flycolor
Flycolor Raptor390 4in1-20A user manual