VAC V200P Manual

V200 POSITIONER
www.vacaccessories.com
92026r15 1


V200 POSITIONER
www.vacaccessories.com
92026r15 3
1 INTRODUCTION.................................................................................. 4
1.1 Principle of Operation.............................................................. 4
1.2 ProductIdentication............................................................... 4
1.3 Air quality recommendations................................................... 5
1.4 Safety Instructions................................................................... 5
2 INSTALLATION.................................................................................... 6
2.1 Connections ............................................................................ 6
2.2 General mounting instructions ................................................ 7
2.2.1 Rotary actuators...................................................................... 7
2.2.2 Linear actuators ...................................................................... 7
2.3 Installation instructions for rotary actuators............................. 8
2.3.1 Double acting .......................................................................... 8
2.3.2 Single acting............................................................................ 8
2.4 Installation instructions for linear actuators ............................. 9
2.4.1 Double acting .......................................................................... 9
2.4.2 Single acting............................................................................ 9
2.5 Cam......................................................................................... 10
2.5.1 Adjustments ............................................................................ 10
2.5.2 Camspecications .................................................................. 10
2.6 Spindle(Drive) ......................................................................... 11
2.6.1 Spindle removal ...................................................................... 11
2.6.2 Spindle mounting .................................................................... 11
2.7 Installing IP converter.............................................................. 12
2.7.1 Internal IP converter................................................................ 12
2.8 4-20 mA connection ................................................................ 13
2.8.1 Connecting the control signal.................................................. 13
2.8.2 Checking the control signal ..................................................... 13
2.8.3 Bench test with calibrator ........................................................ 13
2.8.4 Checking the IP internal circuit................................................ 13
2.9 Calibration ............................................................................... 14
2.10 Front cover and Indicator ........................................................ 15
2.10.1 Removing the front cover ........................................................ 15
2.10.2 Removingatindicatorcover.................................................. 15
2.10.3 Removing Dome indicator cover ............................................. 15
2.10.4 Changing the sealings in the front cover................................. 15
2.10.5 Installingatindicatorcover.................................................... 16
2.10.6 Installing Dome indicator cover ............................................... 16
2.10.7 Removing the indicator ........................................................... 16
2.11 MainsupplylterforIPconverter............................................ 17
2.12 Pilot valve remove and install.................................................. 18
---- Intentionally blank ................................................................... 19
3 SPARE PARTS ................................................................................... 20
3.1 Exploded drawing.................................................................... 20
3.2 Spare parts list ........................................................................ 21
4 SPECIFICATIONS............................................................................... 22
4.1 SpecicationsV200................................................................. 22
5 DIMENSION ........................................................................................ 23
5.1 V200P/Estd ........................................................................... 23
CONTENTS

www.vac.se
92026r15
V200 POSITIONER
4
1.1 Principle of Operation
TheV200incorporatestheforcebalance
principal of operation. The desired value, in
theformofpressure,aectsthemembrane(1)
with the force that is created and transferred to
the balance arm(2). The opposing force, which
represents the actual control value, is provided
by the feedback spring(5) and creating force in
the opposite direction on the balance arm(2).
The feedback spring, resting on the feedback
arm(3), is positioned by the shape and re-
sponse of the cam. The cam(4) is connected
to the cylinder’s (actuator) piston rod via the
drive.
The pilot valve(6) is connected to the balance
arm and follows the balance arm’s movement.
The system is stable when the gold plated
spool(7) is in the neutral position and the forces
thataectthebalancearmisinequilibrium.
As soon as a signal change occurs or a change
inthepositionofthevalve/actuatorpackage
occurs, the “force balance” is also changed
and the spool responds. Air immediately begins
toowintothepartoftheactuator(C+orC-)
which allows the feedback mechanism to return
the spool to the neutral position.
The system is self-stabilizing and searches for a
steady state position.
1.2 Product identication
TheV200identicationtags,Serialnumber
tag(1), product model tag(2) and feedback op-
tion tags(3), are placed as shown.
The product model tag contains information on
control signal, maximum working pressure and
temperature ranges. Other information can be
shown depending on the model.
1 INTRODUCTION
4
5
2
1
6
73

V200 POSITIONER
www.vacaccessories.com
92026r15 5
CAUTION: Beware of moving parts
when positioner is operated!
CAUTION: Beware of parts with
live voltage!
A voltage, which is normally not
dangerous, is supplied to the
positioner.
Avoid touching live parts and bare
wires as well as short circuiting live
parts and the housing.
CAUTION: Do not dismantle a
pressurized positioner!
Dismantling a pressurized positioner
will result in uncontrolled pressure
release. Always isolate the relevant
part of the pipeline. Release the pres-
sure from the positioner and the pip-
ing. Failure to do this may result in
damage or personal injury.
CAUTION: Do not exceed the
positioner performance limitations!
Exceeding the limitations marked on
the positioner may cause damage to
the positioner, actuator and valve.
Damage or personal injury may result.
1.3 Air quality recommendations
Poor air quality is one of the main causes of
premature functional problems with pneumatic
and electro pneumatic equipment. The pilot
valve and IP-converter are precision instru-
ments, and are therefore the most sensitive
parts of the positioner.
a) Water in the supply air is a natural occur-
rence. This happens when air is compressed.
The compression heats the air and the natural
degree of water in the air can remain as mois-
ture. When the air cools in pipes etc.
the moisture condenses and becomes liquid
water. Large quantities can build and some-
timesoodsmallwaterseparators.Thisex-
cess water will eventually reach the control
valve and positioner. This can cause corrosion
damage to the IP converter, causing the
unit to malfunction.
We strongly recommend the use of water
separators with adequate capacity. Coales-
ingltersfromareputablemanufacturerisan
inexpensive way to help prevent unit malfunc-
tions or failures, and add life to the product.
Theseltersremoveparticlesandmoisture
from air lines.
b) Oil in the supply air usually is from the main
compressor. Oil can clog the small nozzles
anddisturbtheapperintheIP-converter.It
can also cause the gold plated spool to “drag”
within the pilot valve. The result is poor control
or in the worst case, failure.
c) Particles in the air usually occur because
of corrosion. Dirt and particles can block the
small nozzles of the IP-converter.
They can also cause the pilot valve to mal-
function. The unit may completely fail.
ToensurenormaloperationalsafetywithVAC
positioner products, we recommend that a wa-
terseparatoranda<80micrometerlterare
mounted as close to the product as possible.
If large amounts of oil are present an oil sepa-
rator should be installed as well.
To further increase operational safety, we rec-
ommend that the working air is clean, dry and
free of moisture, water, oil, particles and other
contaminants, in accordance with the standard
ANSI/ISA–7.0.01–1996
1.4 Safety Instructions

www.vac.se
92026r15
V200 POSITIONER
6
Connection Back III.eps
2. INSTALLATION
2.1 Connections
S–Supplyair
V200P:max.145PSI/1MPa
V200E:23-145PSI/0,15-1MPa
I–Input,pressuresignal
V200P:3-15PSI/20-100kPa
V200E:Plugged
IE–Input,currentsignal
V200E:4-20mA(Rimax250ohm)
V200P:Plugged
C+ -Actuatorconnection+stroke
C- - Actuator connection - stroke
OUT - All air from the actuator, IP and posi-
tioner is vented through this port.
Standardequippedwithabugscreen/silencer
Airconnectionsformale1/4”NPTorG1/4”.
Gaugeconnectionsformale1/8”NPTorG1/8”.
Cableentryformale1/2”NPTorM20cablet-
tings.
G threads are indicated by an engraved G
on the air connection side of the positioner.
GaugeportsI,C+,C-andSarefactoryplugged.
Remove plugs and replace with gauges.
The IP connection must be plugged in
V200E.
The IE entrys should be plugged in
V200P

V200 POSITIONER
www.vacaccessories.com
92026r15 7
Hole pattern II.eps
depth
depth
TheV200hastheISOF05holepattern(1)
and 2¼” x 2¼” hole pattern(2).
2.2.1 Rotary actuator
TheVACV200hasaverystableandproperly
sized drive shaft bearing. However, the posi-
tioner drive(A) should be aligned properly to
the rotary actuator spindle(B).
A relatively small error combined with a rigid
coupling can create very powerful radial
forces, which can overload and cause
premature wear.
2.2.2 Linear actuator
When mounting to linear actuators, the
positioner should be attached in such a
way that its drive is in the center (mid stroke)
of the actuator’s stroke. Proper installation
and alignment will minimize linearity error.
2.2 General mounting instructions.

www.vac.se
92026r15
V200 POSITIONER
8
R
S
P
L
I
T
R
A
N
G
E
9
0
°
D
0
%
9
0
°
L
I
N
1
0
0
%
1
0
0
%
1
8
0
°
L
I
N
5
0
%
0
%
R
S
P
L
I
T
R
A
N
G
E
9
0
°
D
0
%
9
0
°
L
I
N
1
0
0
%
1
0
0
%
1
8
0
°
L
I
N
5
0
%
0
%
R
S
P
L
I
T
R
A
N
G
E
9
0
°
D
0
%
9
0
°
L
I
N
1
0
0
%
1
0
0
%
1
8
0
°
L
I
N
5
0
%
0
%
S
P
L
I
T
R
A
N
G
E
9
0
°
D
R
0
%
5
0
%
1
8
0
°
L
I
N
1
0
0
%
1
0
0
%
9
0
°
L
I
N
0
%
B
S
P
L
I
T
R
A
N
G
E
9
0
°
D
R
0
%
5
0
%
1
8
0
°
L
I
N
1
0
0
%
1
0
0
%
9
0
°
L
I
N
0
%
B
S
P
L
I
T
R
A
N
G
E
9
0
°
D
R
0
%
5
0
%
1
8
0
°
L
I
N
1
0
0
%
1
0
0
%
9
0
°
L
I
N
0
%
B
2.3 Installation instructions for rotary actuators
2.3.2 Single acting
2.3.1 Double acting
Signal closes
Signal opens
Direct (CCW)
Reverse (CW)
Spring closes Direct (CCW)
Spring opens Reverse (CW)
Signal closes Signal opens
Spring opens Direct (CCW) Spring closes Reverse (CW)
Signal opens Signal closes

V200 POSITIONER
www.vacaccessories.com
92026r15 9
2.4 Installation instructions for linear actuators
2.4.1 Double acting
2.4.2 Single acting
Direct (CCW)
Signal closes Signal opens
Reverse (CW)
Spring opens Spring closes
Direct (CCW)
Spring opens Spring closes
Reverse (CW)
Signal opens Signal closes
Signal closes Signal opens
Signal opens Signal closes

www.vac.se
92026r15
V200 POSITIONER
10
R
S
P
L
I
T
R
A
N
G
E
9
0
°
D
0
%
9
0
°
L
I
N
1
0
0
%
1
0
0
%
1
8
0
°
L
I
N
5
0
%
0
%
0
%
9
S
P
L
I
T
R
A
N
G
E
9
0
°
D
R
0
%
5
0
%
1
8
0
°
L
I
N
1
0
0
%
1
0
0
%
9
0
°
L
I
N
0
%
B
R
S
P
L
I
T
R
A
N
G
E
9
0
°
D
0
%
9
0
°
L
I
N
1
0
0
%
1
0
0
%
1
8
0
°
L
I
N
5
0
%
0
%
2.5 Cam
The V200 is standard shipped
with the C1-cam, factory set
for 90° ±1°, direct (CCW) turning.
2.5.1 Adjustments
Remove the front cover and indicator.
(see page 15)
1. Loosen the locking screw(2) and the cam
nut(1).
2.Strokethevalve/actuatortothestop/end
position at 0% input.
3. Turn the cam(3) so that the index mark(5)
for the selected curve aligns with the ball
bearing(4). A small gap between the roller and
the cam tip is desirable.
4. Tighten the cam nut by hand(1).
Check that the locking screw(2) is still loose.
(if not, loosen the locking screw slightly and
tighten the nut again).
5. Tighten the locking screw(2).
Do not tighten cam nut with screw(2) down.
2.5.2 Cam specications C1
Indexmark/Startingpointofrotation*
5. 90° Linear 0-100% CCW
6. 180° Linear 0-100% CW
6. 90° Linear 0-50% CW split range
7. 90° Linear 50-100% CW split range
8. 90° Linear 0-100% CW
9. 180° Linear 0-100% CCW
10. 90° Linear 0-50% CCW split range
11. 90° Linear 50-100% CCW split range
*Increasingsignalrotation.
MostvalvesrotateCWtoclose/CCWtoopen
When eld reversing action of positioner
tubing must be reversed as well
(see page 7 and 8)

V200 POSITIONER
www.vacaccessories.com
92026r15 11
2.6 Spindle (Drive)
VACoersavarietyofspindles/drives(1),suitable
for the most frequently used actuator types.
2.6.1 Spindle Removal
Releasethespindle/drivebypryingwith
two screwdrivers, equally under the edges(2) of
thespindle/drive,usingthehousingasfulcrum.
The spindle has a snap ring that is “released” with
the equal pressure.
2.6.2 Spindle Mounting
Press the spindle down into the spindle shaft hole.
Turntheats(3)intoplaceandpressdown.
Checktoseethatthespindle/driveissetsecurely
in place.
To install the spindle correctly will result in two
“snaps” of the spindle into the housing.
3
1
2

www.vac.se
92026r15
V200 POSITIONER
12
2.7 Installing IP converter
2.7.1 Internal IP Converter
Remove the front cover and indicator.
(see page 15)
1. Loosen the two screws that secure the
pneumatic sealing plate(1) and remove
the plate.
2. Make sure the two O-rings(2) are still in the
positioner housing.
3. Install the IP converter(3) and tighten the
screws(4).
4.Installthe1/4¨plug(5)intheportmarkedI.
1
3
45
2

V200 POSITIONER
www.vacaccessories.com
92026r15 13
2.8 4-20 mA connection
2.8.1 Connecting the control signal
Remove the front cover and indicator.
(see page 15)
Terminal block(1) is now easily acces-
sible. Connect the cables to their
respective pole.
Maximum cable size AWG 13 (2,5 mm2 )
2.8.2 Checking the control signal
The control signal can be checked
without having to break the signal loop.
This is done by connecting a low ohmic
ampere meter over the test points(2).
2.8.3 Bench test with the calibrator
When bench testing, it is possible to
connect the control signal (signal gen-
erator clips) to the two points(3), thus
eliminating the need for temporary leads.
2.8.4 Checking the IP internal circuit
With an ohm meter connected over the
two test points(3) it is possible to check
the IP’s internal circuit.
At room temperature the meter should
read ~150 - 200 Ohms. No reading indi-
cates an internal circuit break and the
IP converter needs replacement.
The IP converter is factory-
adjusted. No extra range or
zero adjustments are
necessary.
1
2
3

www.vac.se
92026r15
V200 POSITIONER
14
ZeroRange Spring III.eps
Zero Range III.eps
2.9 Calibration
The V200 is delivered factory
calibrated 0-100 % ±1%.
Calibration procedure
Zero position
Note:Alwayssetzerorst!
1. Set 0% input signal.
2.Waituntilthevalve/actuatorhasresponded.
3. Adjust the zero position by turning
the zero screw(1), with a screwdriver.
Range (Span)
4. Increase to 100% input signal.
5.Waituntilthevalve/actuatorhasresponded.
6. Adjust the range (span) by turning the
range wheel(2).
Check the zero position
Makeneadjustmentsifnecessary.*
*Whensplitranging,wherezerocanbe
a signal other than 0%, the steps
1-6 must be repeated until the desired
setting has been reached.
12

V200 POSITIONER
www.vacaccessories.com
92026r15 15
2.10 Front cover and indicator
2.10.1 Removing the front cover
Loosen the two screws(1) and
remove the front cover.
2.10.2 Removing at indicator cover
With the main cover removed, the indicator
cover(2) (clear cover) can be removed with
pressure from the backside.
2.10.3 Removing Dome indicator cover
Due to the combined depth of the dome indicator
andV200cover,careshouldbeexercisedwhen
removing the dome. It is recommended that
something sturdy and protective be placed un-
der the dome and equal pressure applied to the
cover. The dome should release without damage.
2.10.4 Changing the sealing in the front cover
Remove the O-ring(4) and replace if needed.
Check the O-ring(5) on the backside of the
front cover and replace if needed.
1
3
4
5
2
1

www.vac.se
92026r15
V200 POSITIONER
16
2.10.5 Installing at indicator cover
Place the indicator cover(1) facing down to-
ward the front cover. Press in the center of the
indicator cover until it snaps into place.
2.10.6 Installing Dome Indicator cover
Place the dome indicator cover(2) so that
it is aligned with its seat in the front cover
on one side. Use inside of palm and give the
indicator cover a hard distinctive punch.
Adjust the display position by turning the
indicator cover(2) to its desired position-it is a
reasonablytightfrictiont.
2.10.7 Removing the indicator
Pull the indicator(6) straight up; it is a friction
t.
Important Note!
Note the indicator’s position so it
can be installed in the same position.
Installing the indicator
Install the indicator in place over the drive
shaft and press it straight down.
Be sure to press the indicator completely
down so that it does not interfere with the indi-
cator cover (clear cover).
Turn the indicator to the proper display
1
2
6

V200 POSITIONER
www.vacaccessories.com
92026r15 17
2.11 Main supply lter for IP converter
Changing the lter
1. Turnoordisconnectthemainairsupply.
Should air supply not be disconnected or
turnedo,thepressuremaycausethe
ltercovertoejectfromtheunit.
2. Loosenthescrew(1)andremovelter
cover(2)
3. Cautiouslyremovethelter(3)witha
sharp pointed object e.g. a pocket knife.
4. Pressthenewlter(3)intothehousing.
5. Check the O-ring(4) and replace if
needed.
5. Installtheltercover(2)andtightenthe
screw(1)
If the lter(3) shows traces of
oil or water, check the water/oil
separator in the supply line.
Oil and water can cause
functional problems in
the IP converter.
1
2
34
2

www.vac.se
92026r15
V200 POSITIONER
18
Max. 20°
2.12 Pilot valve
Removal
Remove the front cover and indicator. (see
p.15)
Loosen the pilot retaining screw(1).
Lift the pilot valve(2) straight up.
Cleaning
Remove the gold plated spool(3) from the valve
housing
Clean the parts with a soft cloth and pipe
cleaner using alcohol, acetone or something
similiar.
Blow dry with clean, pressurized air.
Install the spool back in the valve housing.
Place the gold plated spool in its
“working position”.
(all four pistons inside the valve housing)
Slowly lift the pilot valve in one end.
The spool should start to glide before the
angle exceeds 20°. (see sketch)
If any of the parts show signs of wear, we
recomend replacing with a new pilot valve
assembly.
The pilot valve´s parts are matched to
attain the best possible performance.
Mixing of parts can result in high
excessive bleed and/or poor function.
Install Pilot
Checkthepilotvalve´sveO-rings(4).
Be sure that the gold plated spool´s “gap”(5)
tsoverthebalancearm(6)andplacethevalve
straight down into place. Tighten the screw(1).
3
4
5
6
2
1

V200 POSITIONER
www.vacaccessories.com
92026r15 19
Intentionally blank

www.vac.se
92026r15
V200 POSITIONER
20
59
3. SPARE PARTS
3.1 Exploded drawing
This manual suits for next models
1
Table of contents
Other VAC Controllers manuals
Popular Controllers manuals by other brands
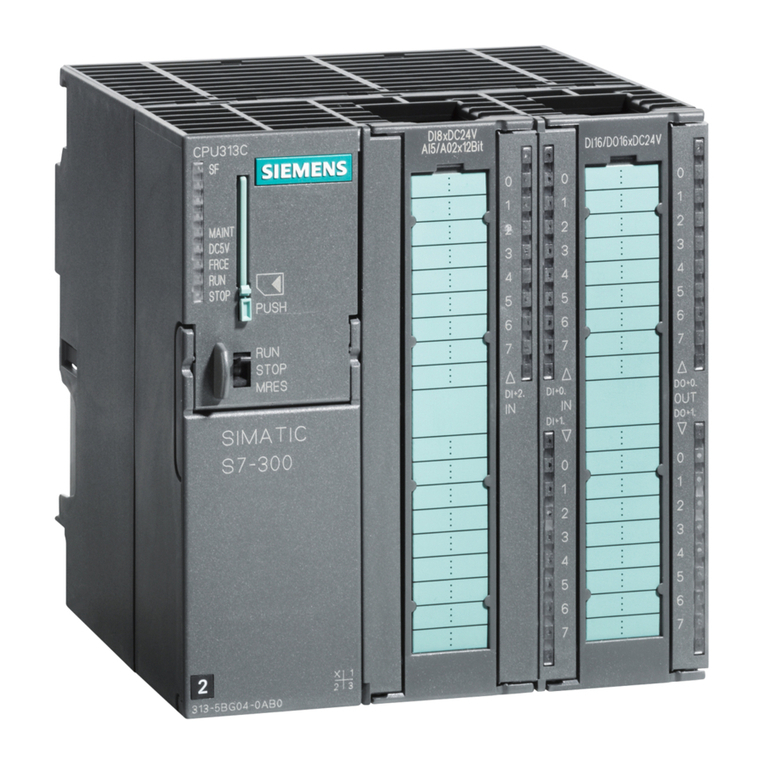
Siemens
Siemens Simatic S7-300 Hardware and installation guide
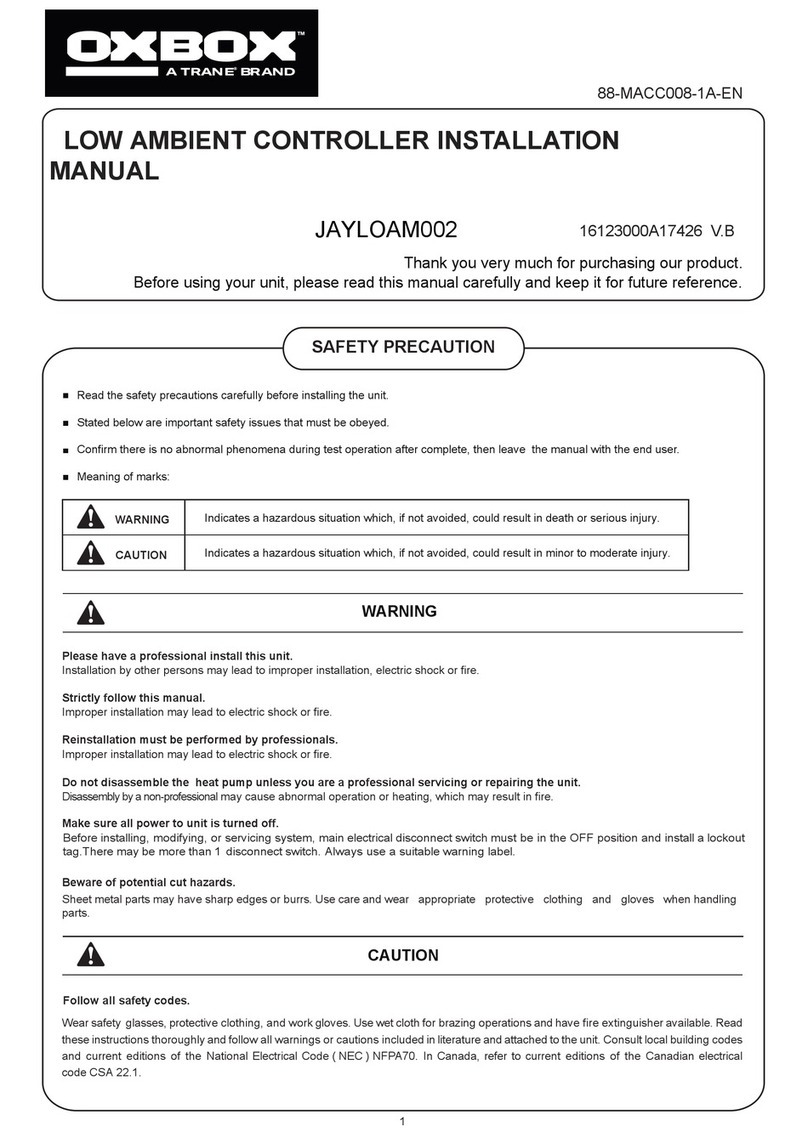
Trane
Trane Oxbox JAYLOAM002 installation manual
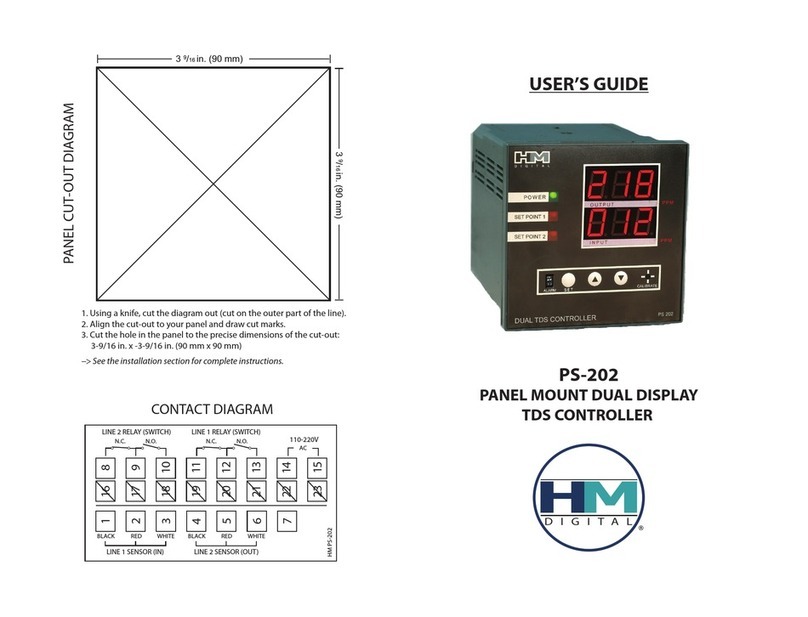
HM Digital
HM Digital PS-202 user guide
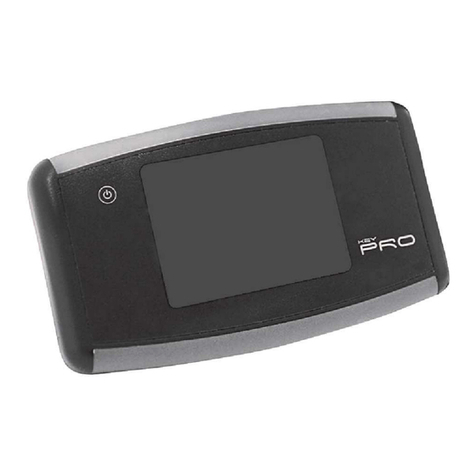
Moretti Design
Moretti Design KEYPRO user manual
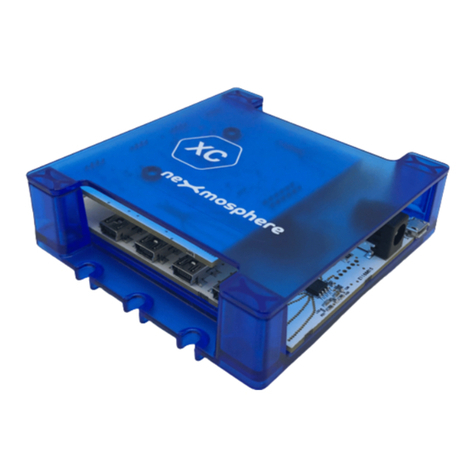
Nexmosphere
Nexmosphere XC-847 quick start guide
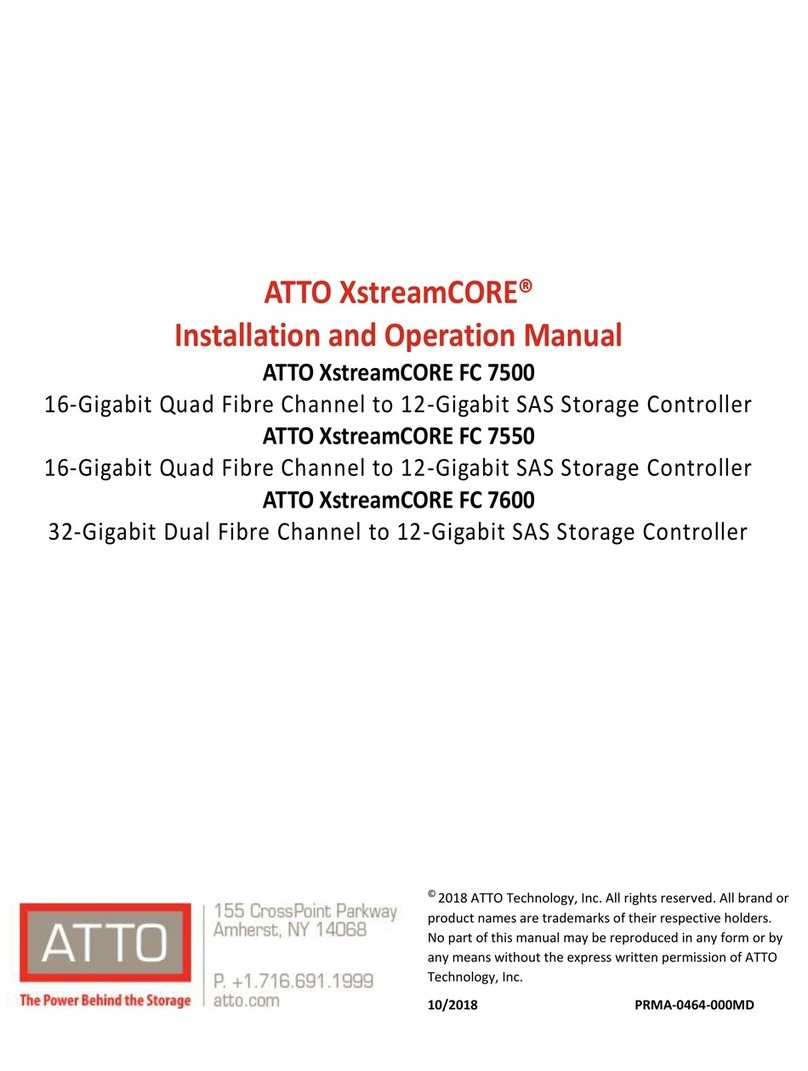
ATTO Technology
ATTO Technology ATTO XstreamCORE FC 7500 Installation and operation manual