AirCom TC8 Installation and operating instructions

Installation, Operation, and Maintenance
Information:
Temperature Sensor Assemblies with Connection
Head Enclosures
Model Series Thermocouples, RTDs, and Thermowells:
TC8, TC9, TC10, TC11, TC14, TC15, TC16, TC17, RT6, RT7, RT9, RT11, RT14, RT15, RT16, RT17, SM2,
SM4, HT2, HT3, WPT, MG1, MG2, MG3, S22, S24, S26, S32, S34, SL22, SL24, SL26, SL32, SL34,
TW52, TW72, SW22, SW24, SW26, SW32, SW34, WF22, WF24, WF26, WF32, WF34, B24, BL24, F22,
F24, F26, F32, F34, FS22, and VST

Aircom Instrumentation Ltd. – Main Office & Factory
Address:9328 - 37th Avenue
Edmonton, Alberta, Canada
T6E 5K3
Phone: 780-434-6916
Fax: 780-434-6911
Email: sales@aircominstrumentation.com
Website: www.aircominstrumentation.com
This document and the information in it are provided in confidence, for the sole purpose of installation, operation, and
maintenance instruction, and may not be duplicated, distributed, or disclosed to any third party or used for any other
purpose without the express written permission of Aircom Instrumentation Ltd.
Aircom Instrumentation Ltd. technologies are subject to patents and patent applications in various jurisdictions.
Copywrite © by Aircom Instrumentation Ltd. 2021

File: Aircom-CSA-Temperature-Sensor-Assembly-Installation-
Operation-Maintenance-r1
i
Aircom Instrumentation Ltd.
9328 - 37 Avenue NW, Edmonton,
Alberta, Canada, T6E 5K3
ph. (780) 434-6916
Sales@AircomInstrumentation.com
www.AircomInstrumentation.com
Contents
Table of Contents
1 Intended Use and Scope ....................................................................................................................... 1
2 Important Notices and Warnings.......................................................................................................... 1
2.1 Selection........................................................................................................................................ 1
2.2 Notices .......................................................................................................................................... 1
2.3 Safety Warnings ............................................................................................................................ 1
2.4 Definitions, Terms, Abbreviation, and Units................................................................................. 2
3 Assemblies Information and Specifications .......................................................................................... 4
3.1 Sizes and Models........................................................................................................................... 5
3.2 Equipment Ratings ........................................................................................................................ 7
3.3 CSA Canada and US Certifications............................................................................................... 11
4 Personnel Qualifications .....................................................................................................................11
5 Shipping, Handling, Storage, and Disposal.......................................................................................... 11
6 Installation .......................................................................................................................................... 12
6.1 Preparations................................................................................................................................12
6.2 Installation .................................................................................................................................. 13
6.2.1 Installation of Threaded Process Connections....................................................................14
6.2.2 Installation of Flanged Process Connections ......................................................................16
6.2.3 Installation of Welded Process Connections ...................................................................... 17
6.2.4 Installation of Temperature Sensor Assembly Without a Thermowell .............................. 18
6.2.5 Surface Mounts...................................................................................................................19
6.2.6 Installation of Wiring (Cable, Conduit, and Connections)................................................... 26
6.3 Pre-Commissioning .....................................................................................................................28
6.4 Commissioning............................................................................................................................ 28
6.5 Normal Operation ....................................................................................................................... 28
6.6 Start-Up, and Shut Down ............................................................................................................ 29
6.7 Emergency Shut Down................................................................................................................ 29
6.8 Inspection, Maintenance, Cleaning, Replacement, and Re-Use.................................................29
6.8.1 Accessories and Spare Parts................................................................................................ 30
6.9 Contact Information and Technical Assistance........................................................................... 30
6.10 Troubleshooting..........................................................................................................................31
6.10.1 General................................................................................................................................31

File: Aircom-CSA-Temperature-Sensor-Assembly-Installation-
Operation-Maintenance-r1
ii
Aircom Instrumentation Ltd.
9328 - 37 Avenue NW, Edmonton,
Alberta, Canada, T6E 5K3
ph. (780) 434-6916
Sales@AircomInstrumentation.com
www.AircomInstrumentation.com
Contents
6.11 Returns........................................................................................................................................35
7 Appendices............................................................................................................................................. I
7.1 Appendix I: Catalogue Information............................................................................................... II
7.2 Appendix II: Datasheets ............................................................................................................... III
7.3 Appendix III: Drawings .................................................................................................................IV
7.4 Appendix IV: Transmitter Documents...........................................................................................V
7.5 Appendix V: Certificates...............................................................................................................VI
7.6 Appendix VI: Manufacturer’s Record Book.................................................................................VII
7.7 Appendix VII: Quick Reference Information and Weblinks .......................................................VIII
7.7.1 RTD Technical Information.................................................................................................VIII
7.7.2 Thermocouple Technical Information................................................................................VIII
7.8 Area Classification Reference Information ..................................................................................IX
List of Figures
Figure 1: Components of a temperature sensor assembly with a thermowell. ........................................... 6
Figure 2: Temperature sensor assembly with a welded fixed fitting probe (Style F)................................... 7
Figure 3: Acceptable thermowell orientations per ASME PTC 19.3 TW. .................................................... 13
Figure 4: Threaded temperature sensor assembly.....................................................................................15
Figure 5: Flanged temperature sensor assembly........................................................................................ 16
Figure 6: Welded temperature sensor assembly........................................................................................17
Figure 7: Temperature sensor assemblies without thermowells. ..............................................................18
Figure 8: Typical surface mount styles........................................................................................................ 19
Figure 9: Heat trace assembly..................................................................................................................... 20
Figure 10: Pipe shoe riser assembly............................................................................................................21
Figure 11: Surface pad assembly. ...............................................................................................................22
Figure 12: Weld pad assembly. ...................................................................................................................23
Figure 13: Magnet assembly.......................................................................................................................24
Figure 14: Washer assembly. ......................................................................................................................25
Figure 15: RTD wiring diagrams. .................................................................................................................27
Figure 16: Thermocouple wiring diagrams. ................................................................................................ 28

File: Aircom-CSA-Temperature-Sensor-Assembly-Installation-
Operation-Maintenance-r1
iii
Aircom Instrumentation Ltd.
9328 - 37 Avenue NW, Edmonton,
Alberta, Canada, T6E 5K3
ph. (780) 434-6916
Sales@AircomInstrumentation.com
www.AircomInstrumentation.com
Contents
List of Tables
Table 1: Definitions and terms...................................................................................................................... 2
Table 2: Abbreviations. ................................................................................................................................. 3
Table 3: Units used in document. ................................................................................................................. 4
Table 4: Typical component sizes. ................................................................................................................ 5
Table 5: Temperature sensor assemblies supply, I/O connections, and operating environmental
conditions...................................................................................................................................................... 8
Table 6: Temperature code ratings based on ambient and process conditions limits................................. 8
Table 7: CSA maximum ambient working pressure. ..................................................................................... 8
Table 8: Typical component material options. ............................................................................................. 9
Table 9: CSA certifications. .........................................................................................................................11
Table 10: Temperature sensor troubleshooting potential causes and solutions. ...................................... 32
Table 11: CSA temperature classification (T-Code) maximum surface temperatures. ...............................IX
Table 12: Aircom CSA division and zone equivalents. .................................................................................IX
Revision Table
Revision
Date (YYYY-MM-DD)
By
1
2021-06-02
BSG

File: Aircom-CSA-Temperature-Sensor-Assembly-Installation-
Operation-Maintenance-r1
1
Aircom Instrumentation Ltd.
9328 - 37 Avenue NW, Edmonton,
Alberta, Canada, T6E 5K3
ph. (780) 434-6916
Sales@AircomInstrumentation.com
www.AircomInstrumentation.com
Temperature Sensor Assembly IOM
1Intended Use and Scope
The temperature sensor assembly devices in this document are used for the collection of industrial
temperature measurements. The signals may or may not be converted during transmission from the
sensor element to the acquisition system. Aircom is not liable for damages caused by improper use or
misapplication of these devices.
This document and any supplemental documents provided by Aircom are intended to help the end-user
with their temperature sensor assemblies. This document does not cover all aspects of the use of
temperature sensor assemblies, it gives a general overview of common practices. Included in this
document is information on safety warnings, important notices, installation, pre-commissioning,
commissioning, operation, and maintenance, as well as links to other relevant information. This
document covers both Resistance Temperature Detector (RTD) and thermocouple assemblies with and
without thermowells.
2Important Notices and Warnings
Ensure all installation, operation, and maintenance information, safety warnings and notices are
reviewed before using these temperature sensor assemblies.
2.1 Selection
Before using these temperature sensor assemblies, it is important to ensure that the correct assembly
was selected for the specific application, that the assembly was correctly installed, and is correctly
operated and maintained. The following information will help as guidelines to ensuring expected
temperature sensor assembly performance.
2.2 Notices
The following information provided in this document is based on common practice in industry for
specific conditions. This information does not cover all scenarios and applications and Aircom does not
guarantee this information will lead to the desired results and assumes no liability for the resulting
outcomes. Aircom’s personnel are available to help with temperature sensor assembly selection for
various applications, however, the end-user is ultimately responsible for ensuring the suitability of the
products being used and how they are used in their specific applications. Aircom is not responsible for
any damages caused due to non-conformance with the information provided in this document, or the
improper use of the devices in this document.
2.3 Safety Warnings
The devices in this document may be connected to sources that are pressurized, electrified, and may
contain hazardous mediums, products, fluids, atmospheres, or materials that may be at harmful levels.
Ensure that all personnel involved in the installation, operation, and maintenance of these devices take
care when around these devices, while handling them, and use appropriate protection for the task being
performed. Follow all safety instructions, be aware of the dangers, and heed all warnings in this

File: Aircom-CSA-Temperature-Sensor-Assembly-Installation-
Operation-Maintenance-r1
2
Aircom Instrumentation Ltd.
9328 - 37 Avenue NW, Edmonton,
Alberta, Canada, T6E 5K3
ph. (780) 434-6916
Sales@AircomInstrumentation.com
www.AircomInstrumentation.com
Temperature Sensor Assembly IOM
document and according to the local jurisdiction and site requirements. Do not install damaged devices,
and ensure all damaged devices are properly tagged/labeled as defective and are taken out of service.
2.4 Definitions, Terms, Abbreviation, and Units
The following are the definitions, terms, and abbreviation used specifically in this document and are
based on general industry terminology.
Table 1: Definitions and terms.
Definition/Term
Description
DANGER:
Means if the danger is not avoided, it will cause death or serious injury.
WARNING:
Means if the warning is not heeded, it can cause death or serious injury.
CAUTION:
Means if the precaution is not taken, it may cause minor or moderate injury.
NOTICE:
Important information that can affect the functionality of the system.
Types of Hazards:
-
Electric Hazard
- Explosive Hazard
- Fire Hazard
Conduit Connection:
This is the field wiring entry point on the head. Theses are typically threaded
connections on the connection head enclosure that connect to the
conduits/conduit fittings, or field wiring/cable.
Connection Head
Enclosure,
Connection Head, or
Head:
This is the enclosure where the lead wires and sensor wires are
connected/terminated (e.g., to a terminal block, wire splices, DIN rail
connectors, or transmitter, etc.).
Head Connection:
This is the sensor entry point on the head. These are typically a threaded
connection on the connection head enclosure that connects to the connection
extension fittings between the connection head and the process instrument
connection (e.g., thermowell, fixed fitting probe, etc.).
Connection
Extension:
This is where the sensor passes from the head to the process connection.
These are the threaded fittings that connect the connection head enclosure to
the process instrument connection (e.g., nipple-union-nipple, nipple, etc.).
Process Instrument
Connection:
This is where the sensor enters the process directly, or the process
connection. This is typically a threaded connection connecting the connection
extension to the process connection.
Process Connection:
This is where the sensor or thermowell is connected directly to the process
and is in contact with the medium. This connection varies and typically is
threaded, flanged, or welded (in some cases it may be clamped, or use other
special connection methods).
Nozzle:
General term for different types of process connections that the thermowell
or fixed fitting probe will be connected to (e.g., flange, coupling, threadolet,
sockolet, etc.).
Medium:
Any substance used in the process (e.g., fluids (liquids/gases), bulk solids,
etc.).
Aircom:
Aircom Instrumentation Ltd.
T-Code:
Temperature Code.
DIN Rail Connector:
Rail mounted wire connection tension clamp

File: Aircom-CSA-Temperature-Sensor-Assembly-Installation-
Operation-Maintenance-r1
3
Aircom Instrumentation Ltd.
9328 - 37 Avenue NW, Edmonton,
Alberta, Canada, T6E 5K3
ph. (780) 434-6916
Sales@AircomInstrumentation.com
www.AircomInstrumentation.com
Temperature Sensor Assembly IOM
Definition/Term
Description
CSA B51:
CSA B51 Boiler, pressure vessel, and pressure piping code
ASME B1.20.1:
ASME B1.20.1 Pipe Threads, General Purpose (Inch)
ASME B16.5:
ASME B16.5 Pipe Flanges and Flanged Fittings NPS ½ Through NPS 24
Metric/Inch Standard
ASME B16.11:
ASME B16.11 Forged Fittings, Socket-Welding and Threaded
ASME PCC-1:
ASME PCC-1 Guidelines for Pressure Boundary Bolted Flange Joint Assembly
ASME PTC 19.3:
ASME PTC 19.3 Part 3 Temperature Measurement Instruments and Apparatus
Supplement to ASME Performance Test Codes
ASME PTC 19.3 TW:
ASME PTC 19.3 TW Thermowells Performance Test Codes
ASME B31.1:
ASME B31.1 Power Piping ASME Code for Pressure Piping, B31
ASME B31.3:
ASME B31.3 Process Piping ASME Code for Pressure Piping, B31
ASME VIII-1:
ASME Boiler and Pressure Vessel Code, Section VIII, Division 1, Rules for
Construction of Pressure Vessels
e.g.:
exempli gratia (“for example”)
etc.:
et cetera (“and the rest”)
Table 2: Abbreviations.
Abbreviation
Description
IOM:
Installation, Operation, and Maintenance
MRB:
Manufacturer’s Record Book (Databook)
MTR:
Material Test Report (Mill Test Report/Certificate)
ITP:
Inspection Test Plan
PWHT:
Post Weld Heat Treatment
NDE:
Non-Destructive Examination
CSA:
Canadian Standards Association
CEC:
Canadian Electrical Code
NEC:
National Electrical Code (US)
SELV:
Safety Extra-Low Voltage
RTD:
Resistance Temperature Detector
MI:
Mineral Insulated (Cable)
NI:
Non-Incendive (e.g., Field Wiring)
NPS:
Nominal Pipe Size
NPT:
National (American Standard) Pipe Taper (Thread)
NPTF:
National (American Standard) Pipe Taper Fuel (Thread)
BSP:
British Standard Pipe (Thread)
BSPP:
British Standard Parallel Pipe (Thread)
BSPT:
British Standard Pipe Taper (Thread)
UN:
Unified National (Thread)
UNF:
Unified National Fine (Thread)
PTFE:
Polytetrafluoroethylene (e.g., Teflon ™)
PVC:
Polyvinyl Chloride
AWG:
American Wire Gauge
ASME:
American Society of Mechanical Engineers

File: Aircom-CSA-Temperature-Sensor-Assembly-Installation-
Operation-Maintenance-r1
4
Aircom Instrumentation Ltd.
9328 - 37 Avenue NW, Edmonton,
Alberta, Canada, T6E 5K3
ph. (780) 434-6916
Sales@AircomInstrumentation.com
www.AircomInstrumentation.com
Temperature Sensor Assembly IOM
Abbreviation
Description
PTC:
Performance Test Code
TW:
Thermowell
DIN:
Deutsches Institut fur Normung (German Institute for Standardization)
EN:
European Standard
SI:
Le Système International d'Unités (The International System of Units)
EMI:
Electromagnetic Interference
RFI:
Radio Frequency Interference
I/O:
Input/Output
RH:
Relative Humidity
N/A:
Not Applicable
US:
United States of America (also USA)
Table 3: Units used in document.
Document Unit Type
Metric
Imperial
Pressure
kPa (kilopascal)
1 kPa = 1 x 10
3
Pa
psi (pounds-force per square inch)
[lbf/in²]
Temperature
°C (degree Celsius)
0°C = +273.15 K
°F (degree Fahrenheit)
+32°F = +491.67°R
Voltage
Vdc (volts direct current)
Current
A (ampere) / mA (milliampere)
Distance | Length m (meter) / mm (millimeter)
′ (foot) / ″(inch)
[ft] / [in]
3Assemblies Information and Specifications
Aircom’s temperature sensor assemblies are built to measure temperatures in a variety of applications
including industrial processes with CSA hazardous location approvals on various models in Canada and
the US. Aircom temperature sensor assemblies consist of a sensor element (RTD, or Thermocouple), a
connection head enclosure, a terminal block, or optional wire splice connectors, DIN rail connectors or a
transmitter, connection extension fitting(s), and a thermowell or fixed fitting probe. There are options to
have the sheath as spring-loaded or fixed. These assemblies should be shipped, handled, and stored
with care to avoid damage that could affect their functionality. Temperature sensor assembly design,
selection, and construction should take the following factors into considerations which include but are
not limited to construction, response time, tolerance (accuracy/precision), immersion length,
temperature (minimum/maximum), pressure (minimum/maximum), compatibility (physical and
chemical), applied forces (fluid flow, cycling, etc.), vibration, and thermal effects (ambient temperature,
low/high-temperatures, thermal equilibrium, thermal cycling, passive/forced heating/cooling,
intermediate temperature material property changes, etc.).

File: Aircom-CSA-Temperature-Sensor-Assembly-Installation-
Operation-Maintenance-r1
5
Aircom Instrumentation Ltd.
9328 - 37 Avenue NW, Edmonton,
Alberta, Canada, T6E 5K3
ph. (780) 434-6916
Sales@AircomInstrumentation.com
www.AircomInstrumentation.com
Temperature Sensor Assembly IOM
3.1 Sizes and Models
The typical sizes of the temperature sensor assembly components are as follows; other sizes are
available when requested.
Table 4: Typical component sizes.
Component
Size Ranges
Connection Head Enclosure Nozzles
NPT Thread: ½”, ¾”, 1”, 1-¼”, 1-½”, 2”
(Reducer bushings also available)
Terminal Blocks, Wire Splice Connectors,
and DIN Rail Connectors
Number of Terminals/Connections: up to 8
Connection Extension Fittings (Conduit,
Nipples, Unions, Bushings, etc.)
NPT Thread: ½” (typically)
Length: 0.00 mm to 6.1 m (0.0” to 241.5”)
Sensor Probe Sheaths
Outer Diameter: 1.6 mm to 12.7 mm (
1/16
” to ½”)
Length: 6.35 mm to 12.192 m (¼” to 480”)
Minimum Wall Thickness: 0.10 mm (0.004”)
Lead Wires
Diameter: 8 AWG to 30 AWG
Threaded & Flanged Thermowells
Length: 50.8 mm to 4.3 m (2.00” to 169.75”)
NPT Thread: ⅛” to 2”
Minimum Tip Thickness: 6.4 mm (¼”)
Minimum Wall Thickness: 3.0 mm (0.12”)
*Flange Class: 150# to 2,500#
NPS Flanges: ≥1” (typically 1” to 10”)
(Reducing flanges also available)
Fixed Fitting Probes
NPT Thread: ½” (typically)
Probe Outer Diameter: 1.6 mm to 12.7 mm (” to ½”)
Probe Length: 6.35 mm to 12.192 m (¼” to 480”)
**Flex-Armour Sheath (Flex-Cable)
Probes
NPT Thread: ½”, ¾”
Outer Diameter: 3.2 mm to 9.5 mm (⅛” to ⅜”)
Probe Outer Diameter: 1.6 mm to 12.7 mm (1/16” to ½”)
Probe Length: 6.35 mm to 12.192 m (¼” to 480”)
Flex-Cable Length: 25.4 mm to 6.1 m (1” to 241.5”)
Notes: These are the common sizes of components if other sizes are required contact Aircom (“Contact Information and
Technical Assistance”).
*Various styles of flanges are available (some styles include ported flanges, raised faced flanges, high-hub flanges, etc.).
**Can be provided with or without a polyurethane, Teflon, or polyvinyl chloride (PVC) coating.
Refer to the catalogue pages for the configuration and technical specifications of the temperature
sensor assemblies. The following information in this document is general to all temperature sensor
assemblies unless otherwise specified. Customizations and alternate options for most components are
available upon request including but not limited to connection head enclosures, transmitters, extension
connections, and thermowells.

File: Aircom-CSA-Temperature-Sensor-Assembly-Installation-
Operation-Maintenance-r1
6
Aircom Instrumentation Ltd.
9328 - 37 Avenue NW, Edmonton,
Alberta, Canada, T6E 5K3
ph. (780) 434-6916
Sales@AircomInstrumentation.com
www.AircomInstrumentation.com
Temperature Sensor Assembly IOM
This document covers the model series thermocouple, and RTD temperature sensor assemblies as
follows:
•The TC9, TC14, RT9, and RT14 are CSA rated as Class I, Division 1, Groups A, B, C, D; Class I, Zone
1, Groups IIC, IIB plus hydrogen, IIB; Class II, Division 1, Groups E, F, G; Zone 20; Class III; T6…T1;
(explosion proof) assemblies that include a sensor probe, thermowell or fixed fitting probe,
connection extension fittings, connection head enclosure, and a terminal block, wire splice
connectors, DIN rail connectors or transmitter.
•The TC8, TC10, TC17, RT6, RT7, and RT17 are CSA rated as Class I, Division 1, Groups B, C, D;
Class I, Zone 1, Groups IIB plus hydrogen, IIB; Class II, Division 1, Groups E, F, G; Zone 20; Class
III; T6…T1; (explosion proof) assemblies that include a sensor probe, thermowell or fixed fitting
probe, connection extension fittings, connection head enclosure, and a terminal block, wire
splice connectors, DIN rail connectors or transmitter.
•The TC16, and RT16 are CSA rated as Class I, Division 1, Groups C, D; Class I, Zone 1, Group IIB;
Class II, Division 1, Groups E, F, G; Zone 20; Class III; T6…T1; (explosion proof) assemblies that
include a sensor probe, thermowell or fixed fitting probe, connection extension fittings,
connection head enclosure, and a terminal block, wire splice connectors, DIN rail connectors or
transmitter.
•The TC11, TC15, RT11, RT15, SM2, SM4, HT2, and HT3 are CSA rated as Class I, Division 2, Groups
A, B, C, D; Class I, Zone 2, Group IIC (US only); T6…T1; (non-incendive) assemblies include a
sensor probe with a fixed fitting probe with or without flex-armour cable, and a connection
head enclosure. The assemblies also include either a terminal block, wire splice connectors, DIN
rail connectors, or may be provided with a transmitter only when installed outside of the
hazardous zone or as per the control drawing and with non-incendive field wiring. The
assemblies may also be provided with optional connection extension fittings, and/or a
thermowell.
Figure 1: Components of a temperature sensor assembly with a thermowell.

File: Aircom-CSA-Temperature-Sensor-Assembly-Installation-
Operation-Maintenance-r1
7
Aircom Instrumentation Ltd.
9328 - 37 Avenue NW, Edmonton,
Alberta, Canada, T6E 5K3
ph. (780) 434-6916
Sales@AircomInstrumentation.com
www.AircomInstrumentation.com
Temperature Sensor Assembly IOM
Figure 2: Temperature sensor assembly with a welded fixed fitting probe (Style F).
3.1.1.1 Quick Weblinks
•Overview of Products and Services
oRTD Sensor Probes and Assemblies
oThermocouple Sensor Probes and Assemblies
oThermowells and Protection Tubes
•Aircom - Home
oAbout Aircom
oInnovation at Work
oNews & Resources
oContact Information
3.2 Equipment Ratings
Temperature sensor assemblies’ ratings shall be based on local jurisdictional requirements, regulation,
bylaws, codes, and standards. The following ratings may vary depending on the installation location, and
configuration of the assembly.

File: Aircom-CSA-Temperature-Sensor-Assembly-Installation-
Operation-Maintenance-r1
8
Aircom Instrumentation Ltd.
9328 - 37 Avenue NW, Edmonton,
Alberta, Canada, T6E 5K3
ph. (780) 434-6916
Sales@AircomInstrumentation.com
www.AircomInstrumentation.com
Temperature Sensor Assembly IOM
Table 5: Temperature sensor assemblies supply, I/O connections, and operating environmental conditions.
Item
Description
Operation
Conditions:
Continuous operation in extended environmental conditions
Electrical Rating:
30 Vdc, 1.0 A maximum
Enclosure Rating:
for indoor use, unless marked with an enclosure rating (e.g., 4, 4X, none,
etc.)
Maximum Altitude:
2,000 meters (6,561 feet)
Maximum Relative
Humidity:
80% for temperatures up to +31°C (+87°F), decreasing linearly to 50% RH
at +40°C (+104°F)
Equipment Class:
I
Overvoltage
Category:
II
Pollution Degree:
2
Intended Supply:
Class 2, SELV (Safety Extra Low Voltage), or equivalent
Note: Temperature sensor assemblies are intended to be connected to control/monitoring systems, consult the specific
equipment documents for the I/O requirements.
Table 6: Temperature code ratings based on ambient and process conditions limits.
*Minimum Connection
Extension (Nipple) Length
Rated Ambient
Temperature Range
Rated Process
Temperature Range
**T-Code
None (Style F probe) /
zero clearance nipple
-50°C to +50°C
(-58°F to +122°F)
-50°C to +50°C
(-58°F to +122°F)
T6 (+85°C)
(+185°F)
Short (1-inch)
-50°C to +50°C
(-58°F to +122°F)
-50°C to +200°C
(-58°F to +392°F)
T4A (+120°C)
(+248°F)
Long (3-inch)
-50°C to +50°C
(-58°F to +122°F)
-50°C to +230°C
(-58°F to +446°F)
T3C (+160°C)
(+320°F)
Extra-Long (8-inch)
-50°C to +50°C
(-58°F to +122°F)
-50°C to +450°C
(-58°F to +842°F)
T2 (+300°C)
(+572°F)
Note: Surface temperatures not exceeding 100°C (T5) may not be marked on products.
Pressure components may have different temperature ratings based on the design code or standard used.
*The minimum connection extension length is the minimum length not in contact with the process at its maximum temperature.
*This also applies to the flex-armor extension, probe tubing/MI cable extension, or other styles of extensions (when adding an
additional 1.5” to the nipple length to account for not having the thermowell hex fitting length).
**The maximum surface temperature at the maximum rated ambient temperature and the maximum rated process
temperature.
Table 7: CSA maximum ambient working pressure.
Style
Maximum Working Pressure
(Process Gauge-Pressure)
**Threaded Thermowell
Up to 48,260 kPa @ 20°C (7,000 psi @ 68°F)
*Flanged Thermowell
Up to 43,090 kPa @ 38°C (6,250 psi @ 100°F)
**Style F – Welded Probe
Up to 34,400 kPa @ 20°C (5,000 psi @ 68°F)
**Style G – Flex-Assembly Probe
Up to 34,400 kPa @ 20°C (5,000 psi @ 68°F)
Notes: *Flanged Thermowell pressure ratings are based on their Class from ASME B16.5 (e.g., 150# to 2,500#).
**Pressure ratings may be limited depending on the fitting type, materials selected, and the design code or standard used.
The pressure values in this table are based on CSA and CRN rated values, for specific ratings contact Aircom (“Contact
Information and Technical Assistance”).

File: Aircom-CSA-Temperature-Sensor-Assembly-Installation-
Operation-Maintenance-r1
9
Aircom Instrumentation Ltd.
9328 - 37 Avenue NW, Edmonton,
Alberta, Canada, T6E 5K3
ph. (780) 434-6916
Sales@AircomInstrumentation.com
www.AircomInstrumentation.com
Temperature Sensor Assembly IOM
Table 8: Typical component material options.
*Component Material Options
**Materials Assembly
Temperature Ratings
Ranges
Assembly
Enclosure Ratings
Connection Head
Enclosures
Aluminum
-50°C to +125°C
(-58°F to +257°F)
Type 4
Epoxy Coated Aluminum
-50°C to +85°C
(-58°F to +185°F)
Type 4/4X
Stainless Steel
-50°C to +125°C
(-58°F to +257°F)
Type 4/4X
Cast Iron
-25°C to +120°C
(-13°F to +248°F)
Type 4
Extension Connections
Stainless Steel
-50°C to +450°C
(-58°F to +842°F)
Type 4/4X
Galvanized Steel
-45°C to +450°C
(-49°F to +842°F)
None
Lead Wires
Teflon
Up to +260°C
(Up to +500°F)
Not Applicable
****Fiberglass
Up to +450°C
(Up to +842°F)
Not Applicable
***Thermowells & Sensor
Probes
300 Series Stainless
Steel
-50°C to +450°C
(-58°F to +842°F)
Type 4
302, 303, 304, 305, 309,
& 316
-50°C to +450°C
(-58°F to +842°F)
Type 4/4X
310 Series
-48°C to +450°C
(-54°F to +842°F)
Type 4
400 Series Stainless
Steel
-50°C to +450°C
(-58°F to +842°F)
Type 4
Duplex Stainless Steel
-50°C to +316°C
(-58°F to +600°F)
Type 4
Inconel
-50°C to +450°C
(-58°F to +842°F)
None
Incoloy
-50°C to +450°C
(-58°F to +842°F)
None
Monel
-50°C to +450°C
(-58°F to +842°F)
None
Hastelloy
-50°C to +450°C
(-58°F to +842°F)
None
Hastelloy B2
-50°C to +427°C
(-58°F to +800°F)
None
Hastelloy C-22
-50°C to +427°C
(-58°F to +800°F)
None
Nickel 200
-50°C to +316°C
(-58°F to +600°F)
None

File: Aircom-CSA-Temperature-Sensor-Assembly-Installation-
Operation-Maintenance-r1
10
Aircom Instrumentation Ltd.
9328 - 37 Avenue NW, Edmonton,
Alberta, Canada, T6E 5K3
ph. (780) 434-6916
Sales@AircomInstrumentation.com
www.AircomInstrumentation.com
Temperature Sensor Assembly IOM
*Component Material Options
**Materials Assembly
Temperature Ratings
Ranges
Assembly
Enclosure Ratings
***Thermowells & Sensor
Probes
Alloy 20
-50°C to +427°C
(-58°F to +800°F)
None
Super Ferritic 446
-8°C to +371°C
(-17°F to +699°F)
None
Titanium TI2
-50°C to +316°C
(-58°F to +600°F)
None
5 Chrome, 9 Chrome
-29°C to +450°C
(-20°F to +842°F)
Type 4
Aluminum
-50°C to +50°C
(-58°F to +122°F)
Type 4
Copper
-50°C to +50°C
(-58°F to +122°F)
Type 4
Brass (80% Cu)
-50°C to +50°C
(-58°F to +122°F)
None
Carbon Steel
-45°C to +450°C
(-49°F to +842°F)
None
Note: *Additional material options are available upon request (e.g., aluminum, copper, brass, etc.), and for specific grades
contact Aircom (“Contact Information and Technical Assistance”).
**These temperature ratings may be lower than the range stated depending on the component selected, contact Aircom to
confirm the rating (“Contact Information and Technical Assistance”).
***Temperature ratings of individual components may vary (be higher or lower) depending on the materials selected, and the
design code or standard used. Sensor probe tips can be manufactured with a copper tip (tip sensitive).
****Fiberglass lead wires are rated up to +510°C.

File: Aircom-CSA-Temperature-Sensor-Assembly-Installation-
Operation-Maintenance-r1
11
Aircom Instrumentation Ltd.
9328 - 37 Avenue NW, Edmonton,
Alberta, Canada, T6E 5K3
ph. (780) 434-6916
Sales@AircomInstrumentation.com
www.AircomInstrumentation.com
Temperature Sensor Assembly IOM
3.3 CSA Canada and US Certifications
Consult Aircom to confirm the exact certification based on the configuration selected.
Table 9: CSA certifications.
Item
Description
Master Contract:
163846
Certificate:
1526478
Hazardous Location Designations:
*Class I, Division 1, Groups A, B, C, D; Class II, Division 1, Groups
E, F, G; Class III; T6…T1
Class I, Zone 1, Groups IIC, IIB plus hydrogen, IIB, Zone 20
*Class I, Division 1, Groups B, C, D; Class II, Division 1, Groups E,
F, G; Class III; T6…T1
Class I, Zone 1, Groups IIB plus hydrogen, IIB, Zone 20
*Class I, Division 1, Groups C, D; Class II, Division 1, Groups E, F,
G; Class III; T6…T1
Class I, Zone 1, Groups IIB, Zone 20
**Class I, Division 2, Groups A, B, C, D; T6…T1, (NI)
Class I, Zone 2, Group IIC, (US only)
Notes: *Canada only when SNUN, or STXUN is selected (for stainless steel unions).
**Non-Incendive when installed per control drawing and using non-incendive field wiring.
4Personnel Qualifications
The installation, pre-commissioning, commissioning, operation, and maintenance of temperature sensor
assemblies should only be done by qualified and authorized personnel. These personnel (installers,
technician, operators, users, etc.) must follow local jurisdictional and plant specific requirements,
specifications, acts, regulations, codes, standards, bylaws, approval processes, and safe practices. The
personnel must review and understand all relevant specifications, datasheets, manuals, instructions,
drawings, and other pertinent documentation before acting, including the information in this document.
These documents may include but is not limited to installation details, functional testing requirements,
repairs, replacement, operation, maintenance, and troubleshooting for pressure retaining and electrical
devices as required for the specific industry, country, and region where being used.
5Shipping, Handling, Storage, and Disposal
Aircom temperature sensor assembly consider applicable regulation as specified in any provided
procurement documents from the end-user/purchaser and is built and verified to be fully functional and
free of defects before leaving the factory. Verify that the temperature sensor assembly has not been
damaged from shipping, handling, or storage before installing. Ensure the assembly is complete and has
no missing components.

File: Aircom-CSA-Temperature-Sensor-Assembly-Installation-
Operation-Maintenance-r1
12
Aircom Instrumentation Ltd.
9328 - 37 Avenue NW, Edmonton,
Alberta, Canada, T6E 5K3
ph. (780) 434-6916
Sales@AircomInstrumentation.com
www.AircomInstrumentation.com
Temperature Sensor Assembly IOM
Ensure that any prolonged storage is done in a protected, dry, and warm indoors location. For
components that are prone to rusting (e.g., uncoated carbon steel, etc.) ensure measures are taken to
prevent excessive corrosion.
Temperature sensor assemblies are intended to be replaced at the end of their useful life. When
disposing of the device, ensure local regulations and good practices are followed.
6Installation
NOTICE:
•Thermowells conforming to ASME PTC 19.3 TW are limited to an insertion length from 63.5 mm
to 609.6 mm (2.5” to 24”). Going outside of this range does not conform to the standard and
requires a custom engineered solution.
6.1 Preparations
Review all relevant plant schematics, drawings (including control drawings), and documents to
understand how the temperature sensor assembly integrates with the facility’s systems. Review all
applicable acts, regulations, codes, standards, bylaws, and jurisdictional requirements (e.g., local
electrical codes, CEC, NEC, etc.).
Verify the temperature sensor assembly ratings are appropriate for the installation location
(minimum/maximum ambient temperature, minimum/maximum process temperature and pressure,
area classification, materials compatibility, etc.).
If equipped with, test the spring range of the spring-loaded temperature sensor assembly, typically it
has a range of 12 mm (½”).
Locate the process connection (port) where the temperature sensor assembly will be mounted.
DANGER:
•Ensure the process connection nozzle is isolated from all hazardous sources before installing the
thermowell.
•Ensure all electrical sources are isolated from all hazardous atmospheres before installing the
temperature sensor assembly.
•Hazardous areas/locations may have flammable/ignitable, or explosive materials present
(e.g., gases, vapours, dust, fibres, etc.).
WARNING:
•Do not exceed the temperature/pressure ratings of the process connection fitting (e.g.,
thermowell, fixed fitting probe, etc.).
•Do not exceed the rated temperatures of the temperature sensor assembly components.

File: Aircom-CSA-Temperature-Sensor-Assembly-Installation-
Operation-Maintenance-r1
13
Aircom Instrumentation Ltd.
9328 - 37 Avenue NW, Edmonton,
Alberta, Canada, T6E 5K3
ph. (780) 434-6916
Sales@AircomInstrumentation.com
www.AircomInstrumentation.com
Temperature Sensor Assembly IOM
CAUTION:
•Keep covers closed and sealed when there is a hazardous atmosphere.
•For Class I, Division 1, and Class II, Division 1 rated devices:
oOpen circuit before removing cover.
oKeep covers tight while circuits are alive.
Figure 3: Acceptable thermowell orientations per ASME PTC 19.3 TW.
Before installing the temperature sensor assembly, isolate the installation location from any hazardous
conditions including but not limited to process conditions and mediums (process fluids, dust, flyings,
bulk solids, materials, pressure, temperature, etc.), and disconnect and isolate from electrical power.
6.2 Installation
Temperature sensor assemblies are installed by mounting the thermowell to the process connection
nozzle (e.g., to piping, pressure vessels, furnaces, autoclaves, etc.), and then connecting the wiring
inside the connection head enclosure, with appropriate methods for the hazardous area location rating.
Thermowells can be mounted in various ways including threaded, flanged, socket-welded, direct
welded, and others.
Install the device before the process and equipment are filled with the process medium and put into
operation.
When thermowell materials do not match each-other, or the process connection it can cause bi-
metallic/galvanic corrosion to occur, ensure this factor is taken into consideration when selecting
materials.
Insulation may be required for various reasons including but not limited to personnel safety, system
performance/efficiency, and measurement accuracy. Insulation can affect the performance of the
sensor assembly by isolating the externally exposed components from atmospheric conditions that may
factor into the thermal equilibrium and transient thermal effects of the installation.
For Class I, Division 1 Rated Devices a seal shall be installed within 50 mm (2 in) of the connection head
enclosure.

File: Aircom-CSA-Temperature-Sensor-Assembly-Installation-
Operation-Maintenance-r1
14
Aircom Instrumentation Ltd.
9328 - 37 Avenue NW, Edmonton,
Alberta, Canada, T6E 5K3
ph. (780) 434-6916
Sales@AircomInstrumentation.com
www.AircomInstrumentation.com
Temperature Sensor Assembly IOM
6.2.1 Installation of Threaded Process Connections
WARNING:
•Do not over tighten the threads on the assembly.
•Do not use if any threads are damaged or striped.
•
Do not install without the required seal (e.g., PTFE tape, seal weld, etc.).
CAUTION:
•Using dissimilar metals for the thermowell and the process connection nozzle may lead to various
issues including but not limited to corrosion issues (e.g., galvanic corrosion, etc.), differential
thermal expansion issues, and potential damage to the weaker thread when installing/removing
the thermowell.
NOTICE:
•There are many types of threads that may be used, ensure the thermowell thread type matches
the process connection nozzle thread type (e.g., NPT/NPTF, BSP/BSPP, BSPT, UN/UNF, straight,
metric (tapered, parallel), etc.) and that the correct type is being used for the application.
oAircom standard thread is NPT (per ASME B1.20.1).
•If the materials of the thermowell threads is different from the process connection nozzle
threads, then the rating of the assembled parts will need to be verified and the weaker material
may reduce the combinations pressure rating.
•Seal welded threads do not use thread sealants (e.g., no PTFE tape, etc.)

File: Aircom-CSA-Temperature-Sensor-Assembly-Installation-
Operation-Maintenance-r1
15
Aircom Instrumentation Ltd.
9328 - 37 Avenue NW, Edmonton,
Alberta, Canada, T6E 5K3
ph. (780) 434-6916
Sales@AircomInstrumentation.com
www.AircomInstrumentation.com
Temperature Sensor Assembly IOM
Figure 4: Threaded temperature sensor assembly.
Ensure the following items are checked/verified:
•The thermowell thread size matches the process connection thread size (e.g., ½” NPT, ¾” NPT,
etc.).
•Any combination of dissimilar materials/metals meets the systems ratings.
•Install the thermowell into the process connection nozzle with the following steps:
Installation Steps:
1. If applicable, apply the specified thread sealant (e.g., PTFE tape, etc.).
2. Thread the thermowell into the process connection nozzle hand-tight first.
3. Tighten the threads to the specified torque using appropriate tools (e.g., a torque wrench, etc.).
4. If applicable, seal weld the thermowell using the specified weld procedures.
This manual suits for next models
54
Table of contents
Popular Accessories manuals by other brands

Omron
Omron ZW-C1*T user manual

Hytronik
Hytronik HBIR30/CA Installation and instruction manual
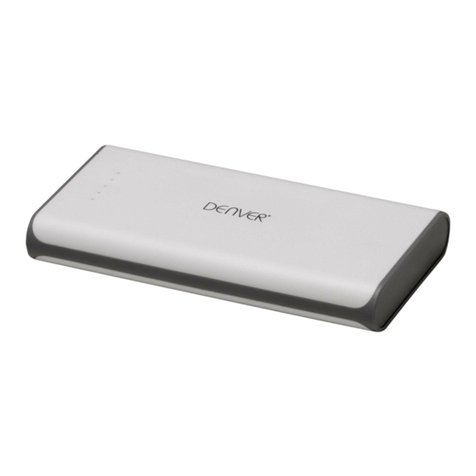
Denver Electronics
Denver Electronics PBA-16001MK2 instruction manual
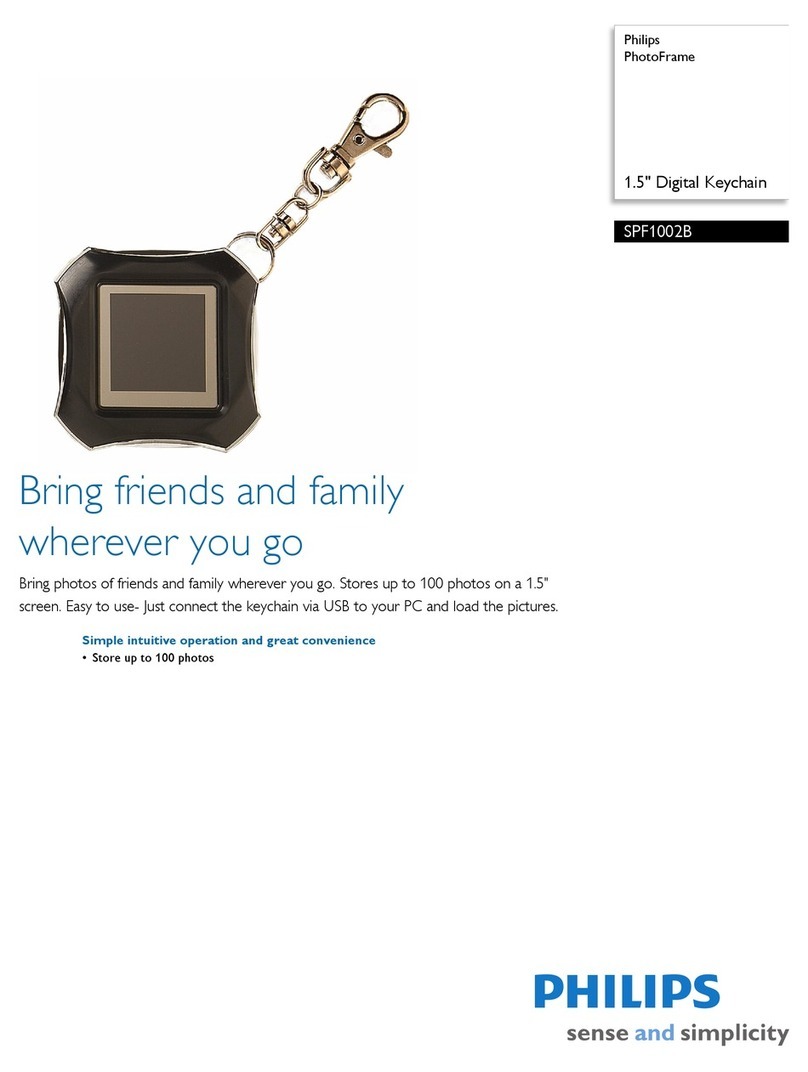
Philips
Philips SPF1002B Specifications
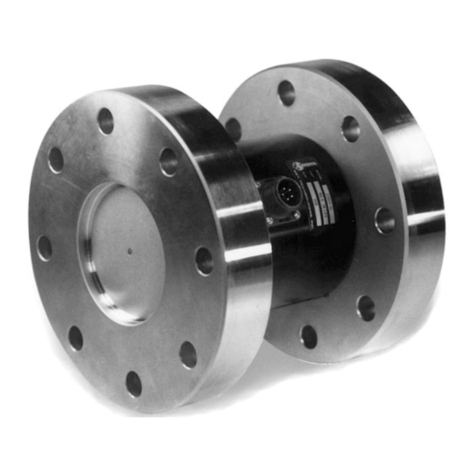
PCB Piezotronics
PCB Piezotronics 2508-02A Installation and operating manual
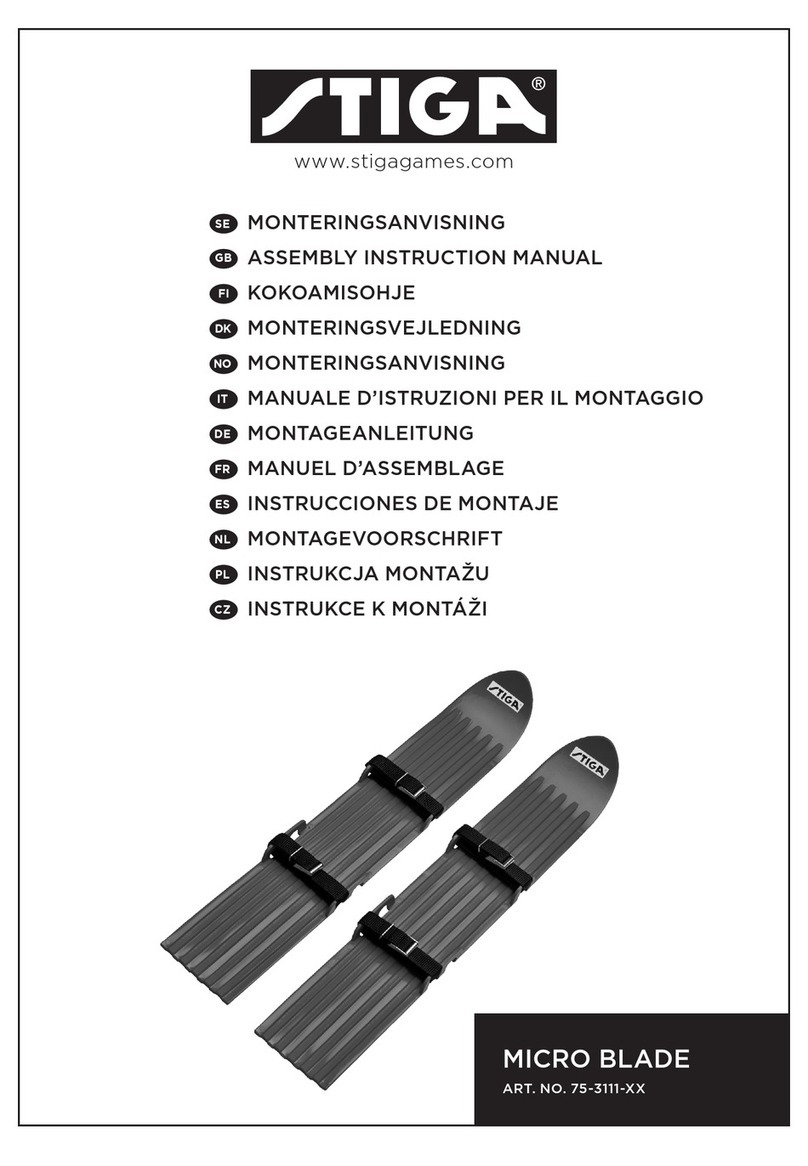
Stiga
Stiga Micro Blade Assembly & instruction manual