AirSource CustomAir Guide

INSTALLATION, OPERATION &
MAINTENANCE INSTRUCTIONS
INSTALLATION, OPERATION &
MAINTENANCE INSTRUCTIONS
Custo
Air Handling Units
Email:
TempAir
AirSource
Heatpumps
INSTALLATION, OPERATION &
MAINTENANCE INSTRUCTIONS
Custo
mAir
Air Handling Units
Tel: 0161
-
425
-
8553
Fax: 0161-637-0232
Email:
info@air-source.net
TempAir
AirSource
Heatpumps

1
Installation, Operation & Maintenance M
anual
fgfgffhfgfggbffgf
V11:0
2122121
21
CONTENTS
34
General
General
Unloading & Handling
General Installation
Fans
Speed Controlled Fans
Storage
4
4
5
Packaged Controls
Dampers
6
6
10
10
10
11
Locating Equipment
10
EC Fans
Thermal Wheels
Recuperators
Dampers
13
12
13
13
15
15
Maintenance of Units Containing Refrigerants
Routine Maintenance Schedule
Refrigeration Maintenance
15
WARRANTY
DELIVERY
& INSTALLATION
General
COMMISSIONING
& TESTING
MAINTENANCE
HEALTH
& SAFETY
General
Cautionary Notes
Water treatment
3
3
3
Heating & Cooling Coils
12
Invalidation of Warranty
3
8
Electrical Connections
8
Ductwork Connections
Procedure
2
2
Safety symbols
3
7
Assembly of Multiple Sect
ions
8
Motor Wiring Diagrams
9
Pipework Connections
9
Water Coils, Steam Coils & DX Coils
10
Condensate Drains
Air Filters
14
Seasonal Shutdown
16
17
Fault Finding
DECOMMISSION
& DISPOSAL
Electric Air Heater Batteries
12
OPERATION
Fans
11
Inverters
11
End of Lif
e Disassembly
Disassembly Guide
17
18

In
stallation, Operation & Maintenance Manual
2
WARRANTY
Invalidation
The warranty may be refused for the following reasons:
of Warranty
Failure to install, set up, put to work or maintain any part of the
equipment as specified in AirSource Ventilation Ltd Installation,
Operation and Maintenance Instructions.
Misapplication of product or components.
On receipt, failure to identify any damage to equipment on the delivery
note & notify AirSource Ventilation Ltd in writing within three (3) days.
Modifications to designed arrangement or performances without the
prior written approval of AirSource Ventilation Ltd.
Damage caused to equipment on site through lack of adequate
protection from the elements or misuse by other trades.
Failure to observe all normally accepted engineering practices during
installation, commissioning and subsequent operation of equipment.
Procedure
In the event of component failure during the warranty period please notify our
service department, the following details will be required to process any warranty
claim:
The unit serial number.
Full commissioning documentation.
Full description of the fault. Further details/checks may be required to
be carried out prior to our engineer’s attendance at site.
A purchase order number in the event that the fault is not covered under
the terms of the warranty.
An engineer will be scheduled to attend at the earliest availability to carry out an
inspection/repair of the fault reported. Our response will depend on the availability of
an engineer and the parts required to carry out the repair. Work outside of normal
hours will not be covered under the terms of the warranty.
Any specific access equipment required for safe working is to be provided and
erected for our use and any obstructions to the equipment are to be removed to
enable a clear working area around the unit/faulty component. Sufficient space
should be available for the removal of components if required – see installation
requirements within this manual.
General
To be read in conjunction with AirSource Ltd standard Terms & Conditions of Sale.
The equipment is covered against defective parts and workmanship under the terms
of the AirSource Ventilation Ltd warranty for the period of 12 months from the date
of delivery, and is restricted to installations within the UK only.
Any replacement parts supplied under the warranty shall be warranted for the
unexpired period of the warranty or 3 months from delivery whichever period is the
longer.

3
Installation, Operation & Maintenance M
fgfgffhfgfggbffgf
V11:0
2122121
21
HEALTH &
SAFETY
Water
T
reatment
Check for any treatment that is required to the water supply for prevention of
corrosion and
scaling of eq
be taken can be obtained from the relevant Water Supply Authority, particulars of
which can be found in the Waters Engineers Handbook yearly edition.
Cautionary Notes
No part of the unit shall be dismantled until a careful study has been made of this
manual.
This manual deals in detail with erection, commissioning, and servicing, and shall be
strictly adhered to. Wherever any maintenance
interior shall be left clean and all access panels and guards shall be correctly
fastened.
General
This section deals with the hazards that could be encountered when any work is
carried out on the equipment for which this manual is written. Therefore the
following points should be observed to avoid any injuries or health hazards.
The installation of the unit shall be checked to ensure that:
A suitable electrical supply is connected.
Prior to entry to any section please ensure that the electrical supply
isolated either at the control panel or at the incoming mains. Please note
that if the control panel isolator is switched off the incoming side of the
electric supply will remain live. DO NOT enter the unit while the fans are
running. After isolating t
to stop prior to removing fan covers.
It is suitable for the atmosphere or the environment in which it is to be
used. Coastal applications should be notified to the manufacturer prior
to order.
It is suitabl
e for the working media, temperature and pressure for which
it is to be used.
Electrical equipment is earthed to comply with I.E.E. regulations and
local by-laws.
The procedure for removing and replacing filter media are fully carried
out as set out in th
Important information
This symbol
is provided to highlight important additional information.
Caution
This symbol identifies potential situations which could lead to the damage of
equipment.
Danger
This symbol indicates situations which present hazardous conditions, which without
applyi
ng strict health and safety procedures can result in serious personal injury or
even death.
Installation, Operation & Maintenance M
anual
SAFETY
Check for any treatment that is required to the water supply for prevention of
scaling of eq
uipment. Information regarding the necessary action to
be taken can be obtained from the relevant Water Supply Authority, particulars of
which can be found in the Waters Engineers Handbook yearly edition.
No part of the unit shall be dismantled until a careful study has been made of this
This manual deals in detail with erection, commissioning, and servicing, and shall be
strictly adhered to. Wherever any maintenance
or work is done within the unit, the
interior shall be left clean and all access panels and guards shall be correctly
This section deals with the hazards that could be encountered when any work is
carried out on the equipment for which this manual is written. Therefore the
following points should be observed to avoid any injuries or health hazards.
The installation of the unit shall be checked to ensure that:
A suitable electrical supply is connected.
Prior to entry to any section please ensure that the electrical supply
isolated either at the control panel or at the incoming mains. Please note
that if the control panel isolator is switched off the incoming side of the
electric supply will remain live. DO NOT enter the unit while the fans are
running. After isolating t
he electrical supply wait 2 minutes for the fans
to stop prior to removing fan covers.
It is suitable for the atmosphere or the environment in which it is to be
used. Coastal applications should be notified to the manufacturer prior
e for the working media, temperature and pressure for which
Electrical equipment is earthed to comply with I.E.E. regulations and
The procedure for removing and replacing filter media are fully carried
out as set out in th
is manual.
Important information
is provided to highlight important additional information.
This symbol identifies potential situations which could lead to the damage of
This symbol indicates situations which present hazardous conditions, which without
ng strict health and safety procedures can result in serious personal injury or
Check for any treatment that is required to the water supply for prevention of
uipment. Information regarding the necessary action to
be taken can be obtained from the relevant Water Supply Authority, particulars of
No part of the unit shall be dismantled until a careful study has been made of this
This manual deals in detail with erection, commissioning, and servicing, and shall be
or work is done within the unit, the
interior shall be left clean and all access panels and guards shall be correctly
This section deals with the hazards that could be encountered when any work is
carried out on the equipment for which this manual is written. Therefore the
following points should be observed to avoid any injuries or health hazards.
Prior to entry to any section please ensure that the electrical supply
is
isolated either at the control panel or at the incoming mains. Please note
that if the control panel isolator is switched off the incoming side of the
electric supply will remain live. DO NOT enter the unit while the fans are
he electrical supply wait 2 minutes for the fans
It is suitable for the atmosphere or the environment in which it is to be
used. Coastal applications should be notified to the manufacturer prior
e for the working media, temperature and pressure for which
Electrical equipment is earthed to comply with I.E.E. regulations and
The procedure for removing and replacing filter media are fully carried
This symbol identifies potential situations which could lead to the damage of
This symbol indicates situations which present hazardous conditions, which without
ng strict health and safety procedures can result in serious personal injury or

DELIVERY
Unloading & Handling
Lifting P
oints
Fork lift
If off-loading with a
Manitou or Fork lift, use
fork extensions as required
to extend past the full
width of the unit.
4 Point Crane Lift
Longer straps will reduce the sideways force
applied to the roof and help prevent damage
the unit. Use of spreader beams is recommended
to prevent damage to the sides of the AHU.
6 Point Crane Lift
Use of spreader beams is recommended to
prevent damage to the sides of
the
straps/chains should be vertical during lift).
IMPORTANT: Ensure the forks extend beyond the casing of the unit.
General
Upon receipt of equipment a visual inspec
noted on the delivery form. Particulars of any damage or short delivery should be
endorsed by the driver delivering the equipment. No responsibility can be held for
damage sustained during the unloading from the delivery
thereafter.
All claims for damage or short delivery should be advised to AirSource Ltd in
writing within three (3) days of receipt.
In
stallation, Operation & Maintenance Manual
oints
Longer straps will reduce the sideways force
applied to the roof and help prevent damage
to
the unit. Use of spreader beams is recommended
to prevent damage to the sides of the AHU.
Use of spreader beams is recommended to
the
AHU (all
straps/chains should be vertical during lift).
IMPORTANT: Ensure the forks extend beyond the casing of the unit.
Upon receipt of equipment a visual inspec
tion should be made and any damage
noted on the delivery form. Particulars of any damage or short delivery should be
endorsed by the driver delivering the equipment. No responsibility can be held for
damage sustained during the unloading from the delivery
vehicle or on the site
All claims for damage or short delivery should be advised to AirSource Ltd in
writing within three (3) days of receipt.
stallation, Operation & Maintenance Manual
4
IMPORTANT: Ensure the forks extend beyond the casing of the unit.
tion should be made and any damage
noted on the delivery form. Particulars of any damage or short delivery should be
endorsed by the driver delivering the equipment. No responsibility can be held for
vehicle or on the site
All claims for damage or short delivery should be advised to AirSource Ltd in

5
Installation, Operation & Maintenance M
anual
fgfgffhfgfggbffgf
V11:0
2122121
21
All units must be installed in accordance with good engineering standards, upright and
level on a prepared base. Fixing down of air handling units is at the discretion of the
installer and dependant of the site conditions.
Flexible connections are NOT recommended for connecting ductwork to the unit, as the
fan outlet is fitted with a flexible connector and is isolated from the unit via anti-vibration
mounts.
Provision must be made for a cleanable drain trap which should terminate at an open
drain or tundish which will ensure any blockage can be seen and remedied.
Units that are delivered in sections should be carefully checked with the general
arrangement drawings to ensure erection in the correct sequence and handing. The
sections would be bolted together using the fixing strips, screws and sealing strip
provided.
Electrical
Installation Site wiring must not penetrate or restrict opening or removal of access panels
Before mounting unit in position it is advisable that consideration is given to the access
requirements of the unit, particularly with reference to the following : That provision is
made in the plant room or wherever the unit is to be installed for access to remove the
following components :
Fans
Electric Heater Batteries
Filters (bags or panels)
Coils and Pipe work
Access space is also essential for service and maintenance purposes
and for the removal of the motor(s).
Storag
e
MAINTENANCE OF EQUIPMENT HELD IN STORAGE FOR A PERIOD OF UP TO 2 YEARS
Interior If ducting is not connected it is essential that all inlets and
discharge openings are completely sealed
Exterior The exterior shall be kept free from falling building materials,
dampness or extreme cold or heat. The unit exterior surfaces
should be inspected on a monthly basis and any sign of
corrosion or scratches are to be treated immediately.
Static Machines fitted with ball bearings may be damaged if left
Indentation stationary for too long
periods. The balls and races may suffer damage by fretting
corrosion (false brinelling, stationary vibration or static vibration
marking).
Belts & Pulleys Wedge belts should be removed from the pulleys and hung up and
not exposed to excessive heat or cold and kept free from
dampness. Belt life is reduced over a long period of non-use due to
the curing and static condition of rubber. Pulleys already taper-
locked to shafts can be lightly covered with rustproof compound.
This must be thoroughly cleaned off prior to start up.
Filters All filters, whether in the form of bags or panels, must be suitably
wrapped and sealed to prevent damp and ingress of dust or
foreign bodies, and held in a dry store.
Fan Shaft During the interval between delivery and commissioning the drive
Bearings belts should be slackened and the fan and motor shafts rotated
one quarter of a revolution at intervals of once a week. Bearings
fitted with shields should not be stored for periods exceeding two
(2) years since the grease ages. Bearings stored for longer periods
than that specified may be found to have a higher initial starting
torque and the service life of the grease will then be shortened.
It is therefore advisable to repack the grease after twelve months
of non use. Fan shafts and impellers should be protected with
rustproof compound to prevent any corrosion taking place.
Electric Motors Clean out all the dust accumulated inside and outside the motor
and make sure that all the component parts of the motor are in
good condition. Cover all the ventilating holes on the motor frame
to prevent dust from entering the motor. Apply a coating of anti-
corrosion grease or other anti-corrosion agent on all the parts that
may be subject to rusting. Care must be taken to see that the
storeroom is always dry and well ventilated while the room
temperature is regularly maintained above 0°C. During storage,
periodic inspections should be made to check for moisture, rust or
hardening of grease.
The above are intended to preserve the life of all static and
moving parts of the equipment during the period of storage. It
is advisable that regular attention of the equipment is
maintained.

INSTALLATION
Locating Equipment
It is important to ensure that adequate access is provided around the perimeter of the
AHU for
maintenance purposes as follows:
Access Side of Unit
Sufficient roo
m at the access side of the unit is required for removal of the largest
componen
t within the AHU
Back of Unit
Double width units require access to the front and back, therefore access requirements
apply as above. Where access to components is not require
recommend a minimum of 500mm is provided.
Air Intake/Discharge
Allow sufficient room for cowls to fit (dimensions as detailed on the general
arrangement drawing). We also recommend an additional distance equal to the unit
wi
dth before any obstacle to prevent recirculation of the exhaust air into the fresh air
inlet.
General
All units must be installed in accor
and
level on a prepared base. Fixing down of air handling units is at the discretion of
the installer and dependant of the site conditions. Flexible connections are NOT
recommended for connecting ductwork to t
flexible connector and is isolated from the unit via anti
must be made for a cleanable drain trap which should terminate at an open drain or
tundish which will ensure any blockage can
delivered in sections should be carefully checked with the general arrangement
drawings to ensure erection in the correct sequence and handing. The sections would
be bolted together as detailed on page 8. Site wiring mu
opening or removal of access panels.
In
stallation, Operation & Maintenance Manual
It is important to ensure that adequate access is provided around the perimeter of the
maintenance purposes as follows:
m at the access side of the unit is required for removal of the largest
t within the AHU
.
Double width units require access to the front and back, therefore access requirements
apply as above. Where access to components is not require
d at the back of the unit we
recommend a minimum of 500mm is provided.
Allow sufficient room for cowls to fit (dimensions as detailed on the general
arrangement drawing). We also recommend an additional distance equal to the unit
dth before any obstacle to prevent recirculation of the exhaust air into the fresh air
All units must be installed in accor
dance with good eng
ineering standards, upright
level on a prepared base. Fixing down of air handling units is at the discretion of
the installer and dependant of the site conditions. Flexible connections are NOT
recommended for connecting ductwork to t
he unit, as the fan outlet is fitted with a
flexible connector and is isolated from the unit via anti
-
vibration mounts. Provision
must be made for a cleanable drain trap which should terminate at an open drain or
tundish which will ensure any blockage can
be seen and remedied. Units that are
delivered in sections should be carefully checked with the general arrangement
drawings to ensure erection in the correct sequence and handing. The sections would
be bolted together as detailed on page 8. Site wiring mu
st not penetrate or restrict
opening or removal of access panels.
Minimum 500mm
for access
Air intake/d
ischarge
g
ap equal to unit width
stallation, Operation & Maintenance Manual
6
It is important to ensure that adequate access is provided around the perimeter of the
m at the access side of the unit is required for removal of the largest
Double width units require access to the front and back, therefore access requirements
d at the back of the unit we
Allow sufficient room for cowls to fit (dimensions as detailed on the general
arrangement drawing). We also recommend an additional distance equal to the unit
dth before any obstacle to prevent recirculation of the exhaust air into the fresh air
ineering standards, upright
level on a prepared base. Fixing down of air handling units is at the discretion of
the installer and dependant of the site conditions. Flexible connections are NOT
he unit, as the fan outlet is fitted with a
vibration mounts. Provision
must be made for a cleanable drain trap which should terminate at an open drain or
be seen and remedied. Units that are
delivered in sections should be carefully checked with the general arrangement
drawings to ensure erection in the correct sequence and handing. The sections would
st not penetrate or restrict
ischarge
ap equal to unit width

7
Installation, Operation & Maintenance M
fgfgffhfgfggbffgf
V11:0
2122121
21
Ass
embly of Multiple S
ections
Pull the two unit sections together along the baseframe at the bottom of the
unit using sash clamps or ratchet s
aid alignment (One section should slot into the other). CAUTION: Before drawing
together, ensure nothing will get trapped in the space between each section.
Once the unit has been pulled
togeth
er, install assembly bolts
through the corner fixing plates
on the inside of the unit. For each
corner, tighten the bolts, ensuring
good compression of the foam
sealant/silicone seal on all mating
faces of the frame.
Apply silicone seal to
outside edge to prevent
ingress of water/dirt into the
gap, as highlighted.
2)
3)
4)
Installation, Operation & Maintenance M
anual
Apply a seal to the face
of one section. O
include supplied foam or a
large bead of silicone around
the entire inner perimeter of
the aluminium frame, as
highlighted.
Pull the two unit sections together along the baseframe at the bottom of the
unit using sash clamps or ratchet s
traps/chains, using the internal corner plates to
aid alignment (One section should slot into the other). CAUTION: Before drawing
together, ensure nothing will get trapped in the space between each section.
Once the unit has been pulled
er, install assembly bolts
through the corner fixing plates
on the inside of the unit. For each
corner, tighten the bolts, ensuring
good compression of the foam
sealant/silicone seal on all mating
Apply silicone seal to
outside edge to prevent
ingress of water/dirt into the
If the AHU
roof, seal the gap between the
sections with silicone before
the joining roof cap is fitted.
1)
5)
Apply a seal to the face
of one section. O
ptions
include supplied foam or a
large bead of silicone around
the entire inner perimeter of
the aluminium frame, as
Pull the two unit sections together along the baseframe at the bottom of the
traps/chains, using the internal corner plates to
aid alignment (One section should slot into the other). CAUTION: Before drawing
together, ensure nothing will get trapped in the space between each section.
If the AHU
has a pitched
roof, seal the gap between the
sections with silicone before
the joining roof cap is fitted.

Ductwork
Connection
Ensure ductwork is adequately sealed to the AHU and supported separately.
connection is to be of the size as recommended on our general arrangement drawing.
Electrical
Connection
Do not penetrate or obst
cables
penetrate the AHU casework, ensure that the casework is
prevent air leakage/water ingress. If the unit is provided with package controls then
always use the cable en
3 Phase Motor Wiring Diagrams
IT IS IMPORTANT TO
USE THE CORRECT WIRING DIAGRAM AS DETAILED BELOW
TO SUIT THE INCOMING MAINS VOLTAGE. FAILURE TO DO SO MAY RESULT IN
PERMANENT DAMAGE TO THE MOTOR/
STAR Connection (Y):
DELTA Connection (Δ
):
Inverters
When inverters are provide
inverter to the motor will be completed at the factory, refer to inverter
documentation for wiring & setup instructions.
Loose inverters may be provided for fitting and wiring by others, refer to inve
documentation for wiring & setup instructions.
In
stallation, Operation & Maintenance Manual
Ensure ductwork is adequately sealed to the AHU and supported separately.
connection is to be of the size as recommended on our general arrangement drawing.
Do not penetrate or obst
ruct the removal of any doors/access panels
penetrate the AHU casework, ensure that the casework is
adequately sealed to
prevent air leakage/water ingress. If the unit is provided with package controls then
always use the cable en
try as provided.
USE THE CORRECT WIRING DIAGRAM AS DETAILED BELOW
TO SUIT THE INCOMING MAINS VOLTAGE. FAILURE TO DO SO MAY RESULT IN
PERMANENT DAMAGE TO THE MOTOR/
CONTROL GEAR.
):
When inverters are provide
d fitted to the AHU the electrical connection from the
inverter to the motor will be completed at the factory, refer to inverter
documentation for wiring & setup instructions.
Loose inverters may be provided for fitting and wiring by others, refer to inve
documentation for wiring & setup instructions.
stallation, Operation & Maintenance Manual
8
Ensure ductwork is adequately sealed to the AHU and supported separately.
Ductwork
connection is to be of the size as recommended on our general arrangement drawing.
ruct the removal of any doors/access panels
. Where electrical
adequately sealed to
prevent air leakage/water ingress. If the unit is provided with package controls then
USE THE CORRECT WIRING DIAGRAM AS DETAILED BELOW
TO SUIT THE INCOMING MAINS VOLTAGE. FAILURE TO DO SO MAY RESULT IN
d fitted to the AHU the electrical connection from the
inverter to the motor will be completed at the factory, refer to inverter
Loose inverters may be provided for fitting and wiring by others, refer to inve
rter

9
Installation, Operation & Maintenance M
fgfgffhfgfggbffgf
V11:0
2122121
21
DX
C
oils
When brazing close to the AHU
pipework seals. Following completion of the refrigeration installation, a nitrogen
pressure test should be carried out on the system. All refrigerant coils should be
vacuum dehydrated after installatio
Steam
Ensure that installation is correct to provide adequate drainage of co
Coils prevent water
hammer, freezing and corrosion within the coil and pip
Ensure that the AHU
is level to avoid condensate being held wi
use of flexible connections or swing joints is recommended. Adequate condensate traps
should be provided on each coil section and be trapped separately. Fluid filters are also
recommended.
Water
General
Coils
Coils are normally designed as either cartridge arrangement where they are fitted inside
the casework of the air handling unit, or bolted directly between two sections of the
AHU. All LPHW and chilled water coils are fitted with an ai
header connections.
Drain Connections
All cooling coils include a condensate drain tray fitted with a drain connection to be
connected to an appropriate trapping system. Care must be taken to ensure that the
correct type of dr
ain trap is used depending on positive / negative air pressure within
the coil section (see condensate drains section).
Drain lines from the trap must be pitched downwards, a slope of 1:25 is recommended.
Ensure that the water flow & return connections ar
entering the coil on the leaving
Frost protection
Water systems should be provided with a suitable anti
freezing. Fluid filters are also
Pipework
The installer should ensure that all pipework is of the correct s
Pipework must not block or restrict access to any doors or access panels.
Care must be taken to
ensure the foll
•
Water flow & return connections are correctly connected.
•
All connecting pipe
•
Any pipe movement caused by expansion or contraction must be absorbed by
flexible joints.
•
Coils located at high points of the system should be regularly vented,
otherwise coils may become air locked causing a reduction in duty.
•
When connecting screwed fittings, it is necessary to restrain the back nut to
avoid damage to the coil.
Installation, Operation & Maintenance M
anual
When brazing close to the AHU
c
asework, take care not to cause damage to the paint or
pipework seals. Following completion of the refrigeration installation, a nitrogen
pressure test should be carried out on the system. All refrigerant coils should be
vacuum dehydrated after installatio
n.
Ensure that installation is correct to provide adequate drainage of co
ndensate to
hammer, freezing and corrosion within the coil and pip
ework system.
is level to avoid condensate being held wi
thin the coil tubes. The
use of flexible connections or swing joints is recommended. Adequate condensate traps
should be provided on each coil section and be trapped separately. Fluid filters are also
Coils are normally designed as either cartridge arrangement where they are fitted inside
the casework of the air handling unit, or bolted directly between two sections of the
AHU. All LPHW and chilled water coils are fitted with an ai
r vent and drain plug on the
All cooling coils include a condensate drain tray fitted with a drain connection to be
connected to an appropriate trapping system. Care must be taken to ensure that the
ain trap is used depending on positive / negative air pressure within
the coil section (see condensate drains section).
Drain lines from the trap must be pitched downwards, a slope of 1:25 is recommended.
Ensure that the water flow & return connections ar
e correctly connected with the water
entering the coil on the leaving
-
air side to give counterflow for improved performance.
Water systems should be provided with a suitable anti
-
freeze solution to prevent
freezing. Fluid filters are also
recommended.
The installer should ensure that all pipework is of the correct s
ize and
Pipework must not block or restrict access to any doors or access panels.
ensure the foll
owing conditions are satisfied:
Water flow & return connections are correctly connected.
All connecting pipe
work is indepe
ndently supported with adequate
Any pipe movement caused by expansion or contraction must be absorbed by
Coils located at high points of the system should be regularly vented,
otherwise coils may become air locked causing a reduction in duty.
When connecting screwed fittings, it is necessary to restrain the back nut to
avoid damage to the coil.
asework, take care not to cause damage to the paint or
pipework seals. Following completion of the refrigeration installation, a nitrogen
pressure test should be carried out on the system. All refrigerant coils should be
ndensate to
ework system.
thin the coil tubes. The
use of flexible connections or swing joints is recommended. Adequate condensate traps
should be provided on each coil section and be trapped separately. Fluid filters are also
Coils are normally designed as either cartridge arrangement where they are fitted inside
the casework of the air handling unit, or bolted directly between two sections of the
r vent and drain plug on the
All cooling coils include a condensate drain tray fitted with a drain connection to be
connected to an appropriate trapping system. Care must be taken to ensure that the
ain trap is used depending on positive / negative air pressure within
Drain lines from the trap must be pitched downwards, a slope of 1:25 is recommended.
e correctly connected with the water
air side to give counterflow for improved performance.
freeze solution to prevent
ize and
lagged.
Pipework must not block or restrict access to any doors or access panels.
ndently supported with adequate
mountings.
Any pipe movement caused by expansion or contraction must be absorbed by
Coils located at high points of the system should be regularly vented,
otherwise coils may become air locked causing a reduction in duty.
When connecting screwed fittings, it is necessary to restrain the back nut to

COMMIS
SIONING
Packaged
If the unit is complete with a factory provided control panel and the fan directions are
Controls
incorrect, it is recommend
This will then keep other equipment such as compressors in synchronisation. The unit will be
provided with a specific wiring diagram located in the control panel. A controls philosophy will
also be provided to the contractor.
Speed
Follow the instructions in the manual for the inverter. Check rotational d
Controlled change
polarity of electrical supply by reversing any two incoming supply lines to the
Fans
motor to change direction if required. Set the inverter frequency as indicated on the
A
HU general arrangement drawing.
Fans
Pre
-
Start Checks
After assembly of the
AHU
General Arrangement drawing for specific details. Isolate electric supply to f
before entering the fan section.
Check for any visible damage to the fan impeller and mounting assembly
Check that anti-
vibration mountings are level and that bolts are tight
Check motor terminal cover is secure and that bolts are tight.
Ensure al
l left over installation materials and other foreign objects have
been removed from the fan cavity.
Test Run
Test run the motor and drive to ensure that the fan is rotating in the correct direction
as identified by the arrow on the fan scroll. If the rota
and reverse any two
incoming supply lines to the motor or starter (3 phase supply).
Check that the current being drawn by the motor does not exceed
current
. Note! All access panels must be closed durin
readings will be obtained.
Condensate
Drains
All condensate drains on the AHU require a suitable
our drawing
. It is important to select the correct type and depth of trap otherwise a
build-up o
f condensate may occur
water prior to start-up
.
General
All units require airside commissioning on site.
to commission the air volume.
It is recommended to
use large radius swept
bends to avoid air
locks. Ensure all pipes,
including drain
connections from the
A.H.U. fall to drain.
In
stallation, Operation & Maintenance Manual
SIONING
& TESTING
If the unit is complete with a factory provided control panel and the fan directions are
incorrect, it is recommend
ed that the polarity of the unit be changed at the incoming mains.
This will then keep other equipment such as compressors in synchronisation. The unit will be
provided with a specific wiring diagram located in the control panel. A controls philosophy will
also be provided to the contractor.
Follow the instructions in the manual for the inverter. Check rotational d
polarity of electrical supply by reversing any two incoming supply lines to the
motor to change direction if required. Set the inverter frequency as indicated on the
HU general arrangement drawing.
AHU
, the following checks should be made. Refer to
General Arrangement drawing for specific details. Isolate electric supply to f
before entering the fan section.
Check for any visible damage to the fan impeller and mounting assembly
vibration mountings are level and that bolts are tight
Check motor terminal cover is secure and that bolts are tight.
l left over installation materials and other foreign objects have
been removed from the fan cavity.
Test run the motor and drive to ensure that the fan is rotating in the correct direction
as identified by the arrow on the fan scroll. If the rota
tion is in reverse, stop th
incoming supply lines to the motor or starter (3 phase supply).
Check that the current being drawn by the motor does not exceed
the motor full load
. Note! All access panels must be closed durin
g this test, otherwise false
readings will be obtained.
All condensate drains on the AHU require a suitable
trap. Drain locations are shown
. It is important to select the correct type and depth of trap otherwise a
f condensate may occur
. IMPORTANT: Ensure that the
trap is charged with
.
All units require airside commissioning on site.
The fans should be operated in hand
to commission the air volume.
use large radius swept
locks. Ensure all pipes,
stallation, Operation & Maintenance Manual
10
If the unit is complete with a factory provided control panel and the fan directions are
ed that the polarity of the unit be changed at the incoming mains.
This will then keep other equipment such as compressors in synchronisation. The unit will be
provided with a specific wiring diagram located in the control panel. A controls philosophy will
Follow the instructions in the manual for the inverter. Check rotational d
irection and
polarity of electrical supply by reversing any two incoming supply lines to the
motor to change direction if required. Set the inverter frequency as indicated on the
, the following checks should be made. Refer to
data chart on
General Arrangement drawing for specific details. Isolate electric supply to f
an-motor
Check for any visible damage to the fan impeller and mounting assembly
vibration mountings are level and that bolts are tight
l left over installation materials and other foreign objects have
Test run the motor and drive to ensure that the fan is rotating in the correct direction
tion is in reverse, stop th
e motor
incoming supply lines to the motor or starter (3 phase supply).
the motor full load
g this test, otherwise false
trap. Drain locations are shown
on
. It is important to select the correct type and depth of trap otherwise a
trap is charged with
The fans should be operated in hand

11
Installation, Operation & Maintenance M
anual
fgfgffhfgfggbffgf
V11:0
2122121
21
OPERATION
Dampers
Most dampers are opened and closed automatically via actuator with signal prov
ided
by the controller, however some may be manually operated via a lifting handle at the
side of the damper.
Fans Fan switches on the front of the control panel have 3 settings: Auto, Off and Test.
‘Auto’ will enable the fans when there is a demand from the controller, which may be
set via BACnet or local timeclock, dependent upon the controls configuration. This is
the normal mode of operation.
‘Off’ will disable the fans so long as other criteria is satisfied (such as a electric
heater fan run-on operation has been completed, and inverters, if applicable, are set
to automatic mode). To ensure the fans will not run during a maintenance routine,
they must be isolated using the main fan isolators mounted on the exterior of the
unit in the section where the fans are physically located. If the fans are operated via
inverters, it is recommended to switch off the main isolator to the unit before using
the fan isolators to prevent the inverters recording a fault and requiring a reset.
‘Test’ is for air balancing purposes only. Each unit may have a different
configuration. However, generally, ‘Test’ mode will fully open any fresh air and
extract dampers, fully close any recirc dampers and run the fans at a speed which
can be set by a speed potentiometer connected the control panel, an inverter control
pad, or through a software setting which can be set via touchscreen if applicable. It
is not recommended to run the unit in ‘Test’ mode, other than for air balancing
purposes, otherwise the unit will not operate correctly.
Inverters Fan inverters can be controlled via a control pad installed inside the control panel
interior, if applicable. Generally, there is a control pad for each fan. However, in some
cases, several fans may be run from one control pad.
‘Auto’ will enable the fan when a signal is received from the controller and run at
speeds determined by a combination of the settings in the inverter and a control
signal. This is the normal mode of operation.
‘Hand’ will run the fan at the speed set on the control pad, which is a frequency in
Hz, limited by the settings. This can be manually changed using the up and down
arrows on the keypad to speed up and slow down the fan accordingly. This can be
useful for air balancing purposes.
‘Off’ disables the fan.
There may be occasions when a fault is shown on the inverter control pad. If you
notice a fault on the inverter, make a note of the fault code and message.
The most common fault occurs when power to the fans is isolated before the
inverters are isolated. The fan will not run until the fault is reset on the control pad.
This can be rectified by restoring power to the fans by switching the isolator back on,
then pushing the ‘Reset’ button on the control pad when the fault is active. If the
fault does not reset, it may be necessary to turn off power to the main isolator, then
turn it back on again.
For all other inverter faults, please refer to the ABB manual.

MAINTENANCE
Fans
Due to the bearing type in EC fans, they are maintenance free. However, once the
grease consumption period has expired (approximately 30000
necessary to replace the bearings.
At least every 12 month
as follows, whilst observing all relevant safety regulations:
Fully isolate electric supply to fan
Do NOT continue until fan impeller has come to a standstill.
Do NOT use a high
agents when cleaning.
Inspect and clean the fan if necessary to prevent imbalance due to ingress of
d
irt, using a damp
Be careful to avoid using too much force and damaging the fan impeller.
Keep the ai
rways of the fan free to prevent danger due to flying objects.
Frequent inspec
tion should be made of the fan.
depend on how essential the service, the application operating environment
number of hours run, but shou
operating in dusty atmospheres or exposed to weather will need to be inspected and
cleaned every 3 months.
If a fan is stationary for long periods in a humid atmosphere, it should be switched on
for a
minimum of two hours every month to remove any moisture that may have
condensed within the motor.
Electric
These should be wired up in accordance with I.E.E. Regulations and local by
Heater is
essential that the heater contactor is interlocked
Batteries the heater
being energised when the fans are not running. Additionally, it is
recommended that a fan run on facility is included within the controls to dissipate
heat form the battery at the end of operation. All
safety cut-
out which must be wired into the controls system. Ensure the size of
cable and contactors are suitable for the load being carried. It is not recommended
for P.V.C. cable to be run into the terminal box. The cable
high temperature sleeving.
Heating
Coils should be inspected every three (3) months to check for build
& Cooling
between the fins and that coil and connections are free from leaks. Should any foreign
Coils matter be found,
cleaning should be carried out with a high
the air-
off face of the coil. Alternatively, the coil can be washed down with a mild
solution of detergent and water, after which the coil should be thoroughly rinsed
clean water. Eliminators should be cleaned down using a soft brush and hot water, any
sediment cleared out of drain tray and drain pipe, and if necessary repair any areas of
corrosion.
Coils located at the high points of the system should be regul
In
stallation, Operation & Maintenance Manual
Due to the bearing type in EC fans, they are maintenance free. However, once the
grease consumption period has expired (approximately 30000
-
40000 hours), it is
necessary to replace the bearings.
At least every 12 month
s a major inspection of the fan section should be carried out
as follows, whilst observing all relevant safety regulations:
Fully isolate electric supply to fan
-motor.
Do NOT continue until fan impeller has come to a standstill.
Do NOT use a high
-pressure
jet or any aggressive, paint solvent cleaning
agents when cleaning.
Inspect and clean the fan if necessary to prevent imbalance due to ingress of
irt, using a damp
cloth.
Be careful to avoid using too much force and damaging the fan impeller.
rways of the fan free to prevent danger due to flying objects.
tion should be made of the fan.
General inspection of the fan will
depend on how essential the service, the application operating environment
number of hours run, but shou
ld not be more than three monthly intervals. On fans
operating in dusty atmospheres or exposed to weather will need to be inspected and
cleaned every 3 months.
If a fan is stationary for long periods in a humid atmosphere, it should be switched on
minimum of two hours every month to remove any moisture that may have
condensed within the motor.
These should be wired up in accordance with I.E.E. Regulations and local by
essential that the heater contactor is interlocked
with the fa
n starter to prevent
being energised when the fans are not running. Additionally, it is
recommended that a fan run on facility is included within the controls to dissipate
heat form the battery at the end of operation. All
heater batteries incorporate a
out which must be wired into the controls system. Ensure the size of
cable and contactors are suitable for the load being carried. It is not recommended
for P.V.C. cable to be run into the terminal box. The cable
should be insulated with
high temperature sleeving.
Coils should be inspected every three (3) months to check for build
-
up of foreign matter
between the fins and that coil and connections are free from leaks. Should any foreign
cleaning should be carried out with a high
-
pressure air line directed at
off face of the coil. Alternatively, the coil can be washed down with a mild
solution of detergent and water, after which the coil should be thoroughly rinsed
clean water. Eliminators should be cleaned down using a soft brush and hot water, any
sediment cleared out of drain tray and drain pipe, and if necessary repair any areas of
Coils located at the high points of the system should be regul
arly vented.
stallation, Operation & Maintenance Manual
12
Due to the bearing type in EC fans, they are maintenance free. However, once the
40000 hours), it is
s a major inspection of the fan section should be carried out
jet or any aggressive, paint solvent cleaning
Inspect and clean the fan if necessary to prevent imbalance due to ingress of
Be careful to avoid using too much force and damaging the fan impeller.
rways of the fan free to prevent danger due to flying objects.
General inspection of the fan will
depend on how essential the service, the application operating environment
, and
ld not be more than three monthly intervals. On fans
operating in dusty atmospheres or exposed to weather will need to be inspected and
If a fan is stationary for long periods in a humid atmosphere, it should be switched on
minimum of two hours every month to remove any moisture that may have
These should be wired up in accordance with I.E.E. Regulations and local by
-
laws. It
n starter to prevent
being energised when the fans are not running. Additionally, it is
recommended that a fan run on facility is included within the controls to dissipate
heater batteries incorporate a
out which must be wired into the controls system. Ensure the size of
cable and contactors are suitable for the load being carried. It is not recommended
should be insulated with
up of foreign matter
between the fins and that coil and connections are free from leaks. Should any foreign
pressure air line directed at
off face of the coil. Alternatively, the coil can be washed down with a mild
solution of detergent and water, after which the coil should be thoroughly rinsed
with
clean water. Eliminators should be cleaned down using a soft brush and hot water, any
sediment cleared out of drain tray and drain pipe, and if necessary repair any areas of
arly vented.

13
Installation, Operation & Maintenance M
fgfgffhfgfggbffgf
V11:0
2122121
21
Recuperators
Recuperators have no moving parts, hence mechanical maintenance is unnecessary.
When dealing with dusty and polluted air, filters should be regularly checked and
replaced when necessary. It is possible to clean the unit with compressed air (in case of
dust deposit) or by spraying it with a detergent solution in case of any greasy de
In order to remove greasy deposits, a water
150, CHEM ZYME, PRIMASEPT, POLY
following the manufacturer’s instructions.
Strongly alkaline or any products that may be
avoided.
Thermal
Cleaning
Wheels
In most cases, the counterflow principle will allow the rotary wheel to self clean itself
of contaminants that may adhere to the rotor surface. In situations where self
cleaning is not sufficient (dependant on the d
be periodically cleaned with compressed air or high pressure water (room
temperature water only).
Belt drive
The V-
belt is designated SPZ or SPA and is commercially supplied with the
designated “endless V
-
the V-
belt is subject to natural stretching which may well exceed the size of the
tensioning device it is recommended to periodically check the tension of the belts. In
particular, in the first 440 op
no longer be guaranteed because the V
to be shortened.
Dampers
Installation
When connecting ductwork to dampers take care to ensure that damper casing is not
twisted by ductwork and that fixings do not penetrate cog housing of the damper
which will affect the dampe
supported and should not be left to hang from the damper. Sealing should be in the
form of prestik or neoprene strip. Ensure actuator rotation is correct in relation to
blade location to prevent breaking linkages
Maintenance
At six (6) month intervals disconnect actuator and check for freedom of movement.
Installation, Operation & Maintenance M
anual
Recuperators have no moving parts, hence mechanical maintenance is unnecessary.
When dealing with dusty and polluted air, filters should be regularly checked and
replaced when necessary. It is possible to clean the unit with compressed air (in case of
dust deposit) or by spraying it with a detergent solution in case of any greasy de
In order to remove greasy deposits, a water
-
detergent solution such as DECADE, ND
150, CHEM ZYME, PRIMASEPT, POLY
-DET, O
akite 86m or similar should be used,
following the manufacturer’s instructions.
Strongly alkaline or any products that may be
aggressive to aluminium should be
In most cases, the counterflow principle will allow the rotary wheel to self clean itself
of contaminants that may adhere to the rotor surface. In situations where self
cleaning is not sufficient (dependant on the d
egree of fouling), the rotary wheel can
be periodically cleaned with compressed air or high pressure water (room
temperature water only).
belt is designated SPZ or SPA and is commercially supplied with the
-
belt”. Con
nection is done by flexible links. Due to the fact that
belt is subject to natural stretching which may well exceed the size of the
tensioning device it is recommended to periodically check the tension of the belts. In
particular, in the first 440 op
erating hours. In case the drive of the rotary wheel can
no longer be guaranteed because the V
-
belt has insufficient tension, the V
When connecting ductwork to dampers take care to ensure that damper casing is not
twisted by ductwork and that fixings do not penetrate cog housing of the damper
which will affect the dampe
r mechanism. Ductwork must be independently
supported and should not be left to hang from the damper. Sealing should be in the
form of prestik or neoprene strip. Ensure actuator rotation is correct in relation to
blade location to prevent breaking linkages
.
At six (6) month intervals disconnect actuator and check for freedom of movement.
Recuperators have no moving parts, hence mechanical maintenance is unnecessary.
When dealing with dusty and polluted air, filters should be regularly checked and
replaced when necessary. It is possible to clean the unit with compressed air (in case of
dust deposit) or by spraying it with a detergent solution in case of any greasy de
posits.
detergent solution such as DECADE, ND
-
akite 86m or similar should be used,
aggressive to aluminium should be
In most cases, the counterflow principle will allow the rotary wheel to self clean itself
of contaminants that may adhere to the rotor surface. In situations where self
egree of fouling), the rotary wheel can
be periodically cleaned with compressed air or high pressure water (room
belt is designated SPZ or SPA and is commercially supplied with the
nection is done by flexible links. Due to the fact that
belt is subject to natural stretching which may well exceed the size of the
tensioning device it is recommended to periodically check the tension of the belts. In
erating hours. In case the drive of the rotary wheel can
belt has insufficient tension, the V
-belt has
When connecting ductwork to dampers take care to ensure that damper casing is not
twisted by ductwork and that fixings do not penetrate cog housing of the damper
r mechanism. Ductwork must be independently
supported and should not be left to hang from the damper. Sealing should be in the
form of prestik or neoprene strip. Ensure actuator rotation is correct in relation to
At six (6) month intervals disconnect actuator and check for freedom of movement.

Air F
ilters
COSHH Regulations
The components of filters are inherently safe, but changing air filters could expose
operators to a ‘Nuisance Dust’ hazard
changing be carried out by maintenance personnel wearing simple dust masks, eye
protection, overalls or protective clothing & gloves. Dirty filters should be sealed into
plastic bags for disposal.
Disposable Filters
These are supplied in the forms of panel & bag filters and are fitted into steel frames.
Panel filters are removed through the access door by simply sliding the filter out
along the channel runner (as shown below).
Bag Filters
Bag filters require
unlocking before removal. To remove, gently turn the screw grips
(as shown highlighted in the red box above) at the top of the bag filter anti
clockwise, then when the screw has been loosened enough, twist the locking
mechanism horizontally to allow room f
Filters should generally be replaced when the pressure drop increases to 125pa
above the initial level.
HEPA Filters
(High Efficiency Particle Arrestors)
This type of filter is generally fitted in a front with
into the
frame by retaining bars which can be removed to allow access to replace
filters.
Carbon Filters
Carbon filters normally have an active life of about twelve (12) months, or more. It is
advisable to remove a sam
the remaining working life, preferably after the first six (6) months & subseq
(6) monthly intervals.
In
stallation, Operation & Maintenance Manual
The components of filters are inherently safe, but changing air filters could expose
operators to a ‘Nuisance Dust’ hazard
. We would therefore recommend that filter
changing be carried out by maintenance personnel wearing simple dust masks, eye
protection, overalls or protective clothing & gloves. Dirty filters should be sealed into
plastic bags for disposal.
These are supplied in the forms of panel & bag filters and are fitted into steel frames.
Panel filters are removed through the access door by simply sliding the filter out
along the channel runner (as shown below).
unlocking before removal. To remove, gently turn the screw grips
(as shown highlighted in the red box above) at the top of the bag filter anti
clockwise, then when the screw has been loosened enough, twist the locking
mechanism horizontally to allow room f
or the bag filter to be removed with ease.
Filters should generally be replaced when the pressure drop increases to 125pa
(High Efficiency Particle Arrestors)
This type of filter is generally fitted in a front with
drawal frame. Filters will be held
frame by retaining bars which can be removed to allow access to replace
Carbon filters normally have an active life of about twelve (12) months, or more. It is
advisable to remove a sam
ple from the pack to return to manufacturer to determine
the remaining working life, preferably after the first six (6) months & subseq
stallation, Operation & Maintenance Manual
14
The components of filters are inherently safe, but changing air filters could expose
. We would therefore recommend that filter
changing be carried out by maintenance personnel wearing simple dust masks, eye
protection, overalls or protective clothing & gloves. Dirty filters should be sealed into
These are supplied in the forms of panel & bag filters and are fitted into steel frames.
Panel filters are removed through the access door by simply sliding the filter out
unlocking before removal. To remove, gently turn the screw grips
(as shown highlighted in the red box above) at the top of the bag filter anti
-
clockwise, then when the screw has been loosened enough, twist the locking
or the bag filter to be removed with ease.
Filters should generally be replaced when the pressure drop increases to 125pa
drawal frame. Filters will be held
frame by retaining bars which can be removed to allow access to replace
Carbon filters normally have an active life of about twelve (12) months, or more. It is
ple from the pack to return to manufacturer to determine
the remaining working life, preferably after the first six (6) months & subseq
uent six

15
Installation, Operation & Maintenance M
anual
fgfgffhfgfggbffgf
V11:0
2122121
21
ROUTINE MAINTENANCE SCHEDULE
REFRIGERATION MAINTENANCE
Monthly
3
Monthly
6
Monthly
Annually
Fan Shaft Bearings
✓
Motors
✓
Belts & Pulleys
✓
Electric Heater Battery
✓
Coils & E
liminators
✓
Dampers
✓
Panel & Bag Filters
✓
HEPA
F
ilters
✓
Carbon Filters
✓
Thermal W
heel
✓
Recuperator
✓
External Surfaces
✓
Maintenance
of Units Containing Refrigerant
It is a legal requirement that all units containing F Gas refrigerants such as R407c,
R410a are serviced on a regular basis and that leak tests are carried out. This should
generally be carried out at least every six months and a service inspection sheet
issued to the customer upon completion. Log books should be kept on site by the
end user to prove that these works have been carried out. The responsibility of
compliance is shared by the end user and the appointed maintenance engineers.
Failure to comply with the F Gas regulations will result in invalidation of the warranty
on the refrigeration system within the unit.
Safety Warning
Ensure that all power to the unit is switched off before carrying
out any servicing or maintenance task. Only trained and qualified service
personnel should repair or service air conditioning equipment containing a
refrigeration system. Follow all safety codes. Wear safety glasses and work
gloves. Extinguish any cigarettes or naked flames. If on inspection of the
refrigeration pressures a refrigerant leak is suspected, open all access panels to
ensure the gas has dissipated to atmosphere.
Access The access panel to the refrigeration service valves and switches is identified by
a red flammability label. Access to the compressor section is identified on the
unit drawing.
Electrical Check all electrical connections for signs of overheating or arcing. Check all
cables for signs of chafing or physical damage.

In
stallation, Operation & Maintenance Manual
16
FAULT FINDING
Fault Possible Cause Remedy / Action
Unit not operating.
No power to unit. Check mains supply and main AHU isolator.
No Supply or Extract fans
running.
Fire link open. Inspect fireman’s panel.
Defective damper end switch.
Check actuator operation
an
d
end swit
c
h
making when open.
No power to fans Check control switch, fuses, MCB’s and
control circuit wiring.
No air volume.
Fan drive or motor failure
Inspect drive belts when applicable. Check
motor winding resistance.
Low air volume, fans
Running, airflow fail on.
Filters blocked
Remove packaging or replace.
Incoming phases crossed.
Check fan rotation. If incorrect change mains
incoming phases over. Not individual fans.
Refrigeration Circuits
4 Monthly Checks At every service visit the following checks should be carried out: - Check the
suction and discharge pressures using a service gauge manifold and compare
them with the commissioning sheet. If there is any significant variation, then the
fault should be found and corrected. Refer to the troubleshooting chart. If on
inspection of the refrigeration pressures a refrigerant leak is suspected, open all
access panels to ensure the gas has dissipated to atmosphere.
Visually examine pipework and components for damage, wear and tear and oil
patches, the latter being indicative of a system leak.
Check that the high and low pressure switches are cutting out the compressors
at the correct settings.
High pressure switch cut-out 320psi
Low pressure switch cut-out 30psi
Low pressure switch cut-in 50psi
The gauges can then be removed from the system. Do not forget to replace
the security caps on the Schrader valves.
Annual Checks Check all electrical connections for tightness.
Check all refrigeration connections with a foam or detergent leak detector.

17
Installation, Operation & Maintenance M
anual
fgfgffhfgfggbffgf
V11:0
2122121
21
Fault Finding Continued:
DECOMMISSIONING & DISPOSAL
Fault
Possible Cause
Remedy / Action
No heating or cooling
Temperature controller. Contact controls specialist.
No air volume.
Inspect drive belts. Check motor winding
resistance.
Pressure switch failure. Inspect fan pressure switch and tubing,
replace as necessary.
Refrigeration fault. Contact refrigeration specialist.
Low heating output or Air
Volume
Compressor fault indication.
Contact refrigeration specialist.
Dirty filters.
Replace filters.
Defective Heat Recovery device.
Thermal Wheel:
Check wheel rotation.
Recuperator:
Check bypass damper closed on heating
demand. Replace if faulty.
Frost coil not operational (if
applicable).
Contact controls specialist.
Re-heat coil not operational.
Investigate operation of control valve.
Seasonal
Shutdown
Before an extended period of non-use, it is recommended to reduce the system to
minimum capacity using the regulation/control system, then set any dampers to run
in a recirculating arrangement (if applicable) in order to reduce risk of frost.
It is also advisable to close all control valves, then switch off any recirculating
pumps, followed by closing all fresh water and manual valves. Small empty spaces
suffer from a risk of frost, so it is a good idea to blow compressed air through them, if
available, until they are free from residue.
Allow the fan to run until all surfaces are dry. Switch off the mains switch and lock
everything up.
If the unit is not to be used for several months and the fan(s) have a belt (most non-
EC fans), then it is advisable to either slacken or remove the fan belt to avoid
tensioning damage during storage.
End of Li
fe
Disassembly
Before starting disassembly, the AHU and all built-in components must be
disconnected from the mains and all live connections removed by a qualified
electrician. Additionally, all media-bearing components must be completely emptied.
This must be conducted by a specialized company which can carry out the
professional disposal of water with antifreeze, and refrigerants.
The AHU can then be dismantled on-site into individual unit modules or into its
component parts. It is advisable for this to be carried out by a specialized company,
familiar with the environmentally friendly disposal of all component parts.

In
stallation, Operation & Maintenance Manual
18
Disassembly
Guide
Doors/Panels: All exterior panels and doors are constructed using plastisol and/or
galvanised steel as an exterior surface, containing fibre glass insulation within, along
with a polymerised acoustic barrier (if applicable) which must both be removed from
the steel casing before recycling. Removal of the rivets for each door/panel can be
performed by drilling. Once the two shells of the panel have been separated, other
plastic components can be removed, such as door handles and locks, for separate
recycling.
Fans: Once all panels and doors have been disassembled and sorted for recycling,
large components can be removed, such as fans and thermal wheels/recuperators.
To remove the fans, remove all fixings from where the fan flange meets the fan plate,
then loosen and remove the nuts at the base of the fan. Depending on the weight
and size of the fan, some specialised lifting equipment may be required to lift out the
fan from inside the unit using the lifting hooks provided at the crest of the motor.
Thermal wheels/Recuperators: To remove a thermal wheel or recuperator, remove
all fixings then slide out onto a suitable lifting platform, using loading straps attached
to fixing points if necessary to balance. Thermal wheels are predominantly made
from steel with aluminium fins, however the motor and circuit boards contain some
toxic materials and must be disposed of according to local regulations for such
electronic components. There are also some plastic components such as the brush
fibres which may require separation. Recuperators are made from steel with
aluminium fins. Removal may require first removing part of the aluminium frame.
Filters: Filters can be removed by loosening the fixings as per the normal
maintenance process then recycled. Panel filters are comprised of paper cardboard,
synthetic felt polymer and steel wire frame. Bag filters have a steel frame, with felt
polymer comprising the main body of the filter and thus must be additionally
separated into individual components for most recycling centres.
Refrigeration: Refrigeration circuits MUST be isolated and purged by F-GAS
registered professionals and/or a relevant accredited professional in the applicable
country by law. Refrigeration gases are destructive to the natural environment and
serious fines can occur due to inadequate disposal. They must be decanted into a
suitable canister and can either be recycled or taken to a lawful and registered
disposal site. See BS EN 378 for more information regarding British and European
guidelines on refrigerants.
Coils: When removing coils, care needs to be taken that the coils have been isolated
from the main circuit and purged properly by the relevant professionals (for coils
containing refrigerants). Once the inlet and outlet pipes have been disconnected and
drained, remove the fixings holding the coil into place on the access side, then slide
out gently onto specialised lifting equipment. Coil pipes are manufactured from
copper, fixed onto a steel frame containing aluminium fins, and are widely recyclable.
All pipes connecting to the coils are manufactured from copper and can either be cut
out with pipe cutting equipment or removed using a cutting torch (IMPORTANT:
Pipes must be purged thoroughly before removal).
Compressors: Compressors require special handling and disposal due to residual
refrigerant gases which may be present in the system. Contact your local
refrigeration handling facility for more information.
Dampers: Dampers blades are predominantly aluminium with some plastic
components, contained within an aluminium housing which includes some plastic
gears.

19
Installation, Operation & Maintenance M
anual
fgfgffhfgfggbffgf
V11:0
2122121
21
Frame/Other F
ittings:
The main frame body for the AHU consists of aluminium
beams which can be removed and recycled. All other sheet metal parts are made
from galvanised steel, stainless steel, or plastisol coated steel. For units with
separator panels between two sections, the separator panels generally have the
same composition as ordinary door/panels and can be recycled as such. Other
fittings which may be recycled are the stadium knobs for holding panels, which are
made from plastic. All self tapping screws and rivets are steel or stainless steel.
Sensors/Cables: All cables are copper with plastic sleeve and are widely recyclable,
some sensors
(such as gas sensors and pressure transducers) may contain circuit boards which
must be disposed of according to the WEEE (Waste Electrical and Electronic
Equipment) directive inside Europe, or relevant RoHS directives.
Control panel: Within the United Kingdom and Europe, the majority of electronic
components within the control panel will be required to be sent to an accredited
waste handling centre with facilities for electrical and electronic equipment in order
to safely recycle and manage electronic waste, under the terms of the WEEE (Waste
Electrical and Electronic Equipment) 2012/19/EU directive which prohibits municipal
disposal of some electrical and electronic components which may contain hazardous
materials, such as lead and polychlorinated biphenyls. Outside Europe, please refer
to local official guidelines on the correct process for handling electronic waste.
This manual suits for next models
1
Table of contents
Popular Air Handler manuals by other brands
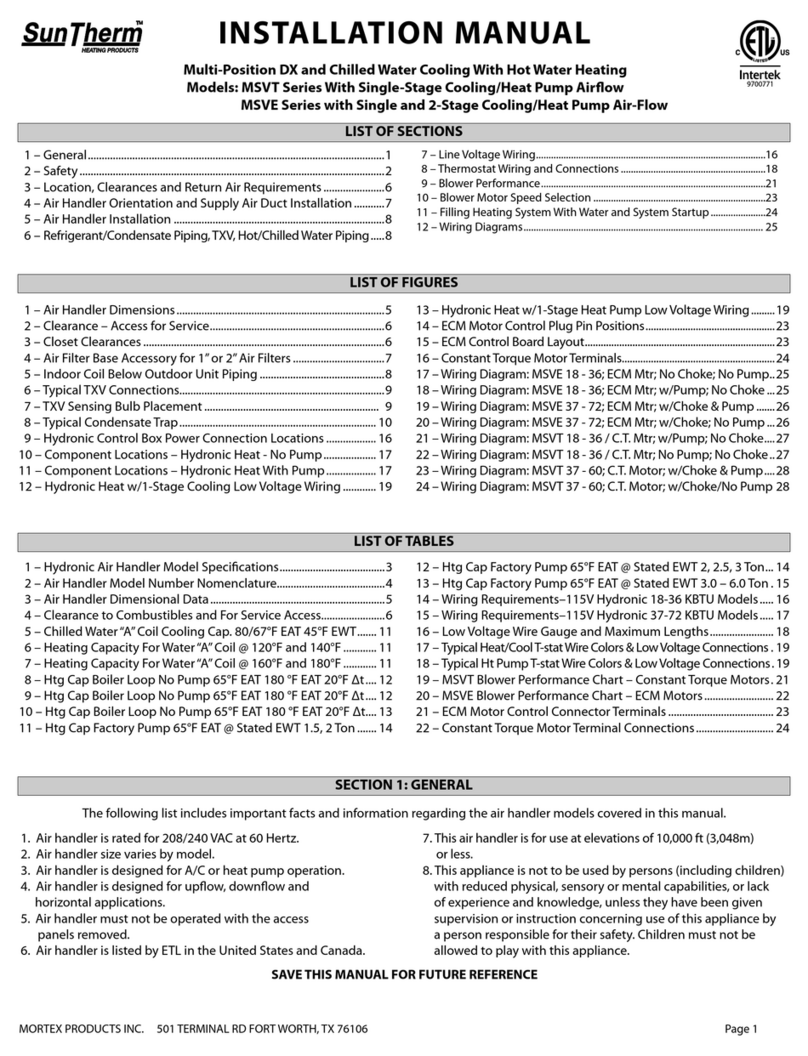
Suntherm
Suntherm MSVT Series installation manual
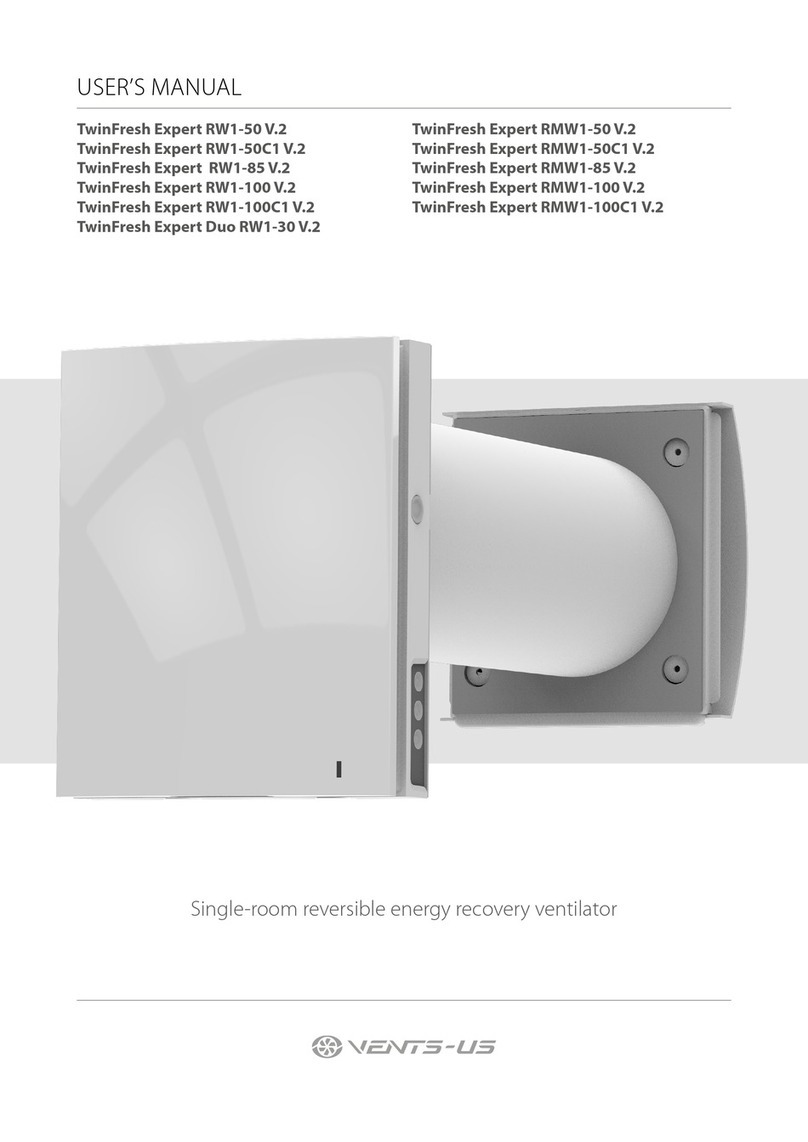
Vents-us
Vents-us TwinFresh Expert RW1-50 V.2 user manual

Salda
Salda RIRS EKO 3.0 1200 VEL MOUNTING AND INSTALLATION INSTRUCTION
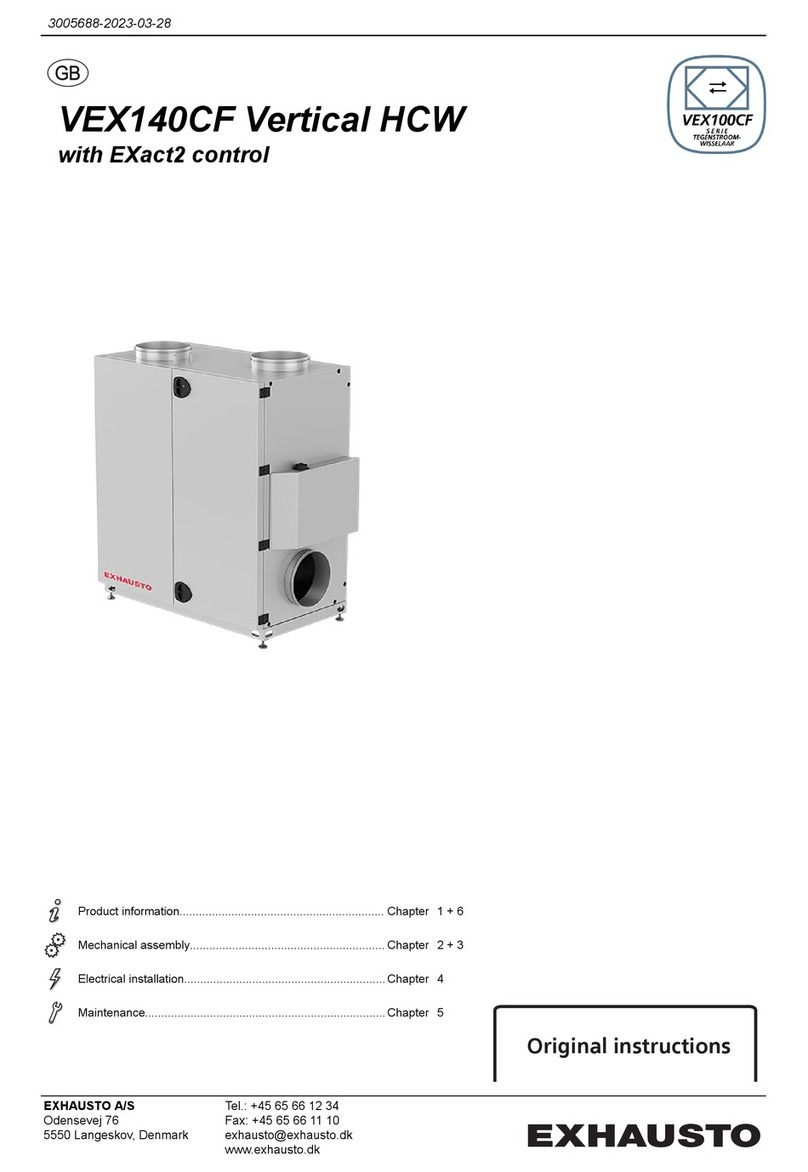
Exhausto
Exhausto VEX140CF H Original instructions
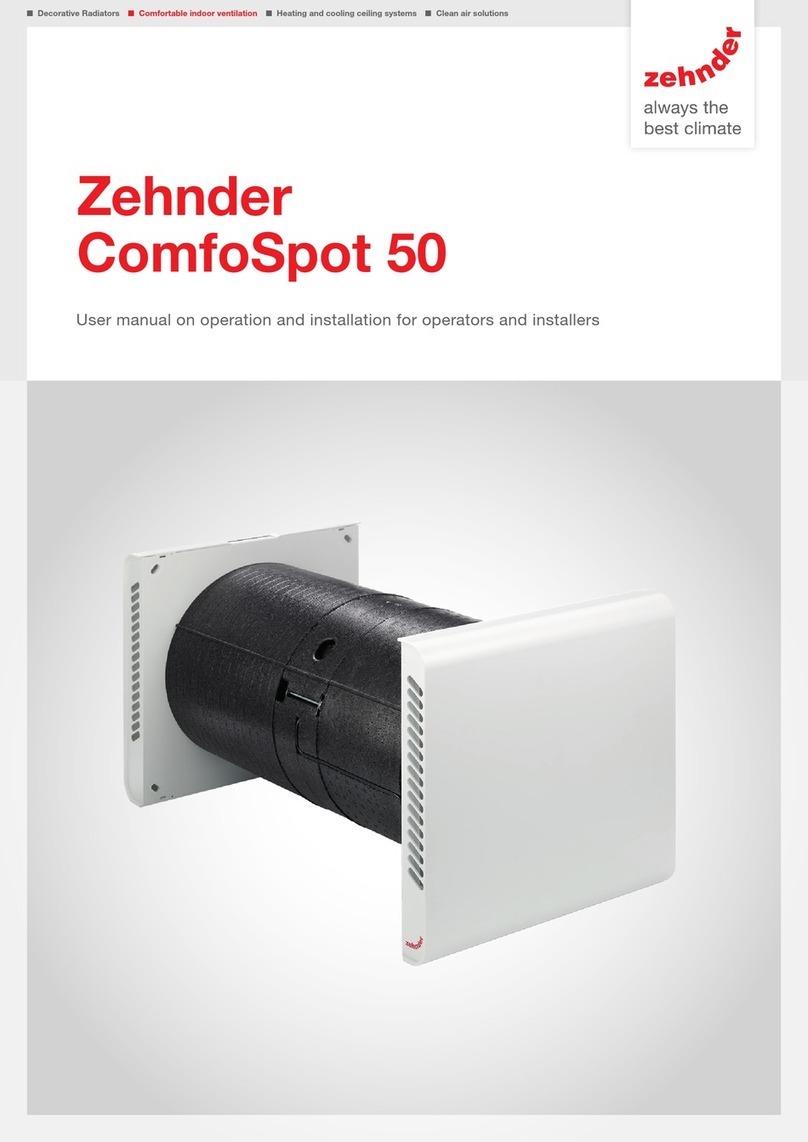
Zehnder Rittling
Zehnder Rittling ComfoSpot 50 manual
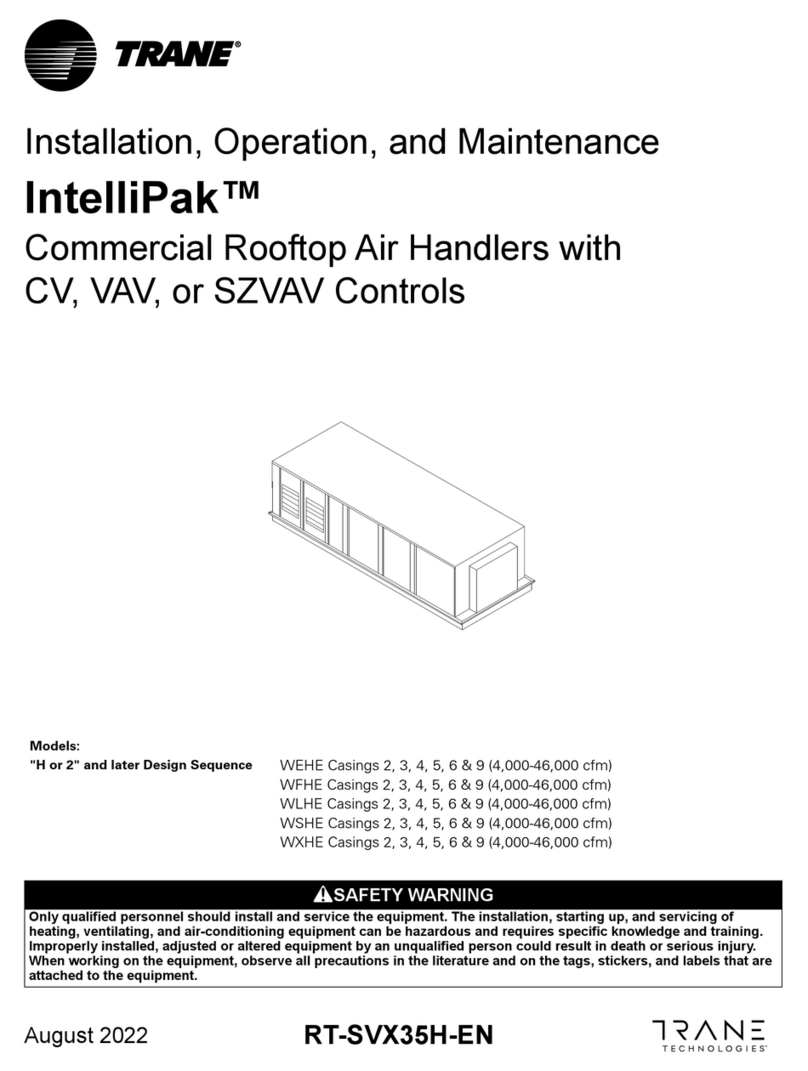
Trane
Trane IntelliPak WEHE Series Installation, operation and maintenance

System air
System air Topvex SR installation instructions
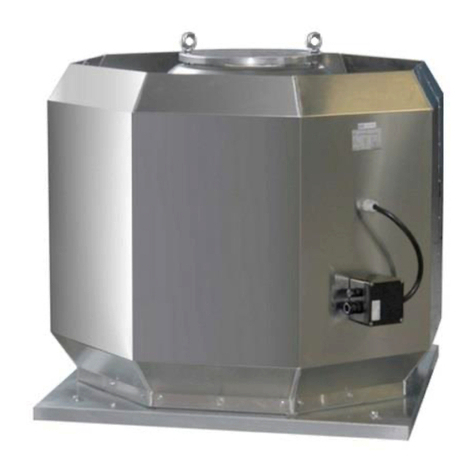
System air
System air DVV-Ex Installation and operating instructions
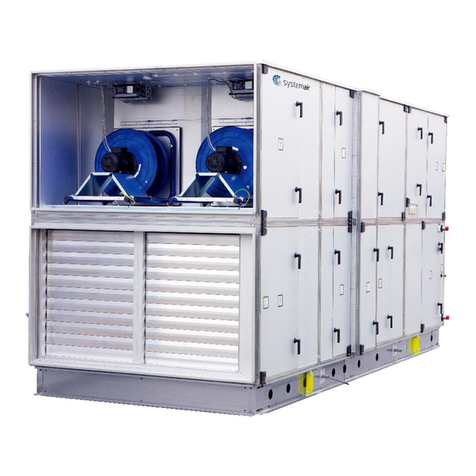
System air
System air Danvent TIME Annex for the user manual
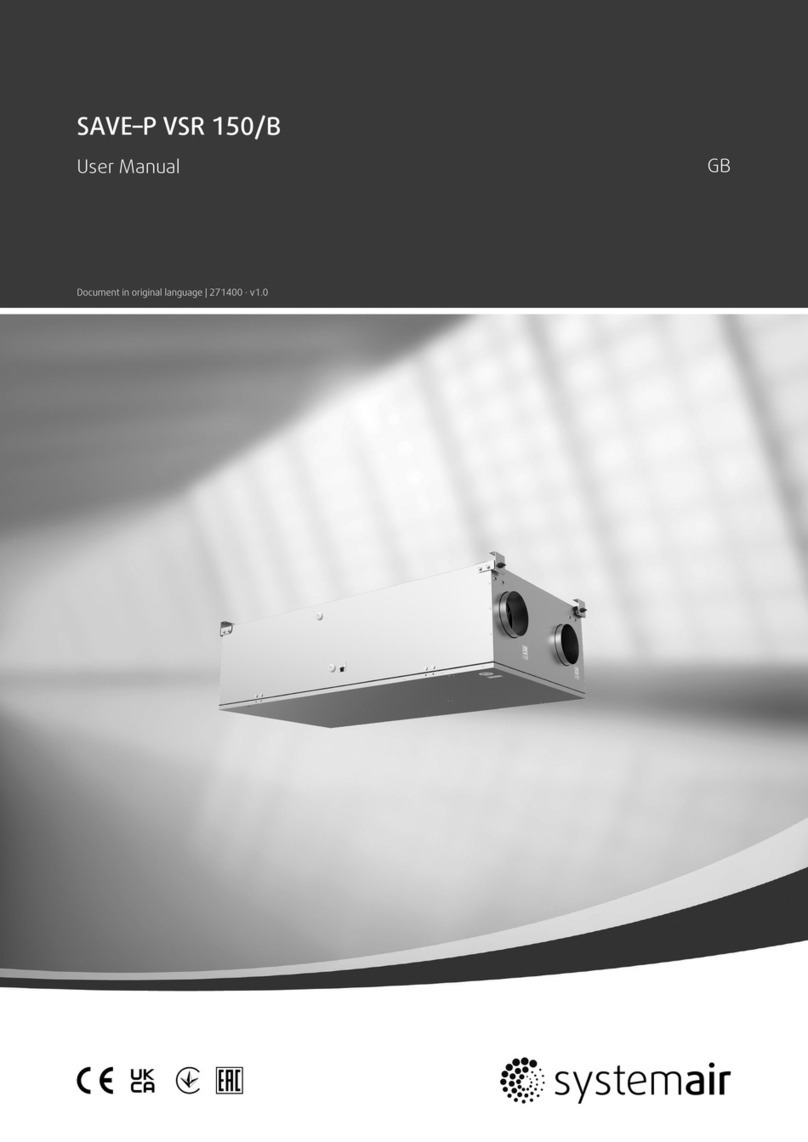
System air
System air SAVE-P VSR 150/B user manual

Comfort Star
Comfort Star CASSETTE Installation & operation manual
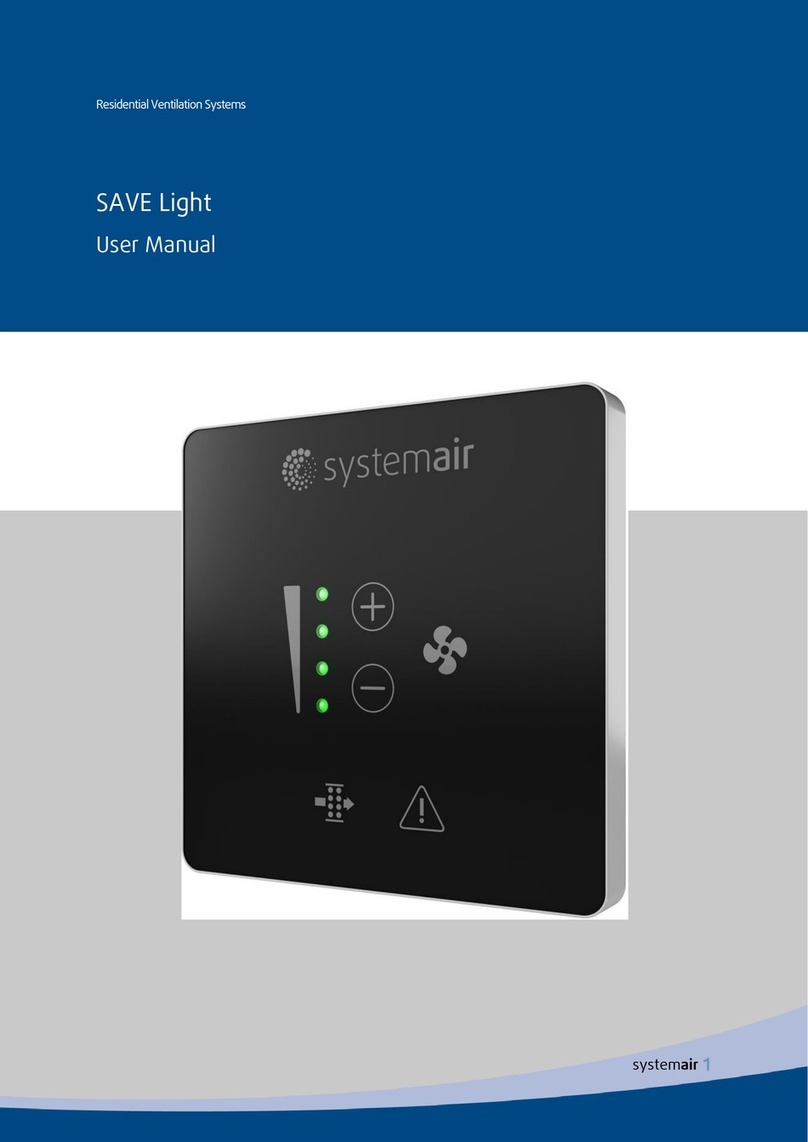
System air
System air SAVE CONNECT user manual