ALPHA DYNAMIC PUMPS Ruby 080 FDA User manual

ΙΙ 2G Εx h IIB T4 Gb
II 2D Εx h IIIB Τ135˚C Db
Baseefa15ATEX13DR/RN3
Installation, Operation and Maintenance
Air Operated Diaphragm Pumps
Industrial Park of Kifisia - HELLAS
www.alphadynamic.eu
RUBY 080 FDA

2
INDEX
1.0 Introduction ......................................................................................................................................................................................5
1.0.1 Pump Identification...........................................................................................................................................................................5
1.0.2 Markings and general information ...................................................................................................................................................6
1.0.3 Composition Codes..........................................................................................................................................................................6
1.1 Warranty...........................................................................................................................................................................................7
1.2 Transport , unipacking , storage.......................................................................................................................................................7
1.3 Principle of function..........................................................................................................................................................................7
1.4 Pump operation................................................................................................................................................................................8
1.5 Improper use ....................................................................................................................................................................................8
2.0 Safety Rules.....................................................................................................................................................................................8
2.1 Equipotential bonding / earthing.....................................................................................................................................................10
3.0 Installation ......................................................................................................................................................................................11
3.1 Connection of air supply line ..........................................................................................................................................................12
3.2 Connection of cuction and pressure lines ......................................................................................................................................12
3.3 Pump in suction operation .............................................................................................................................................................12
3.4 Pump in submerged operation .......................................................................................................................................................12
3.5 Connecting to the product circuit....................................................................................................................................................12
3.6 Noise emissions (2003/10/EC)).....................................................................................................................................................13
3.7 Temperature range of the diaphragm material ...............................................................................................................................13
3.8 Temperature range of the Housing material...................................................................................................................................13
4.0 Diaphragm and manifold assembly ...............................................................................................................................................14
4.1 Pump Disassembly ........................................................................................................................................................................14
4.2 Air control valve disassembly - assembly ....................................................................................................................................15
4.3 Air chamber and shaft bearing assembly-disassembly ..............................................................................................................15
5.0 Troubleshooting..............................................................................................................................................................................16
6.0 Technical data ................................................................................................................................................................................17
6.1.1 Dimensions drawing ......................................................................................................................................................................17
6.2 Performance...................................................................................................................................................................................18
6.3 Exploded View and Spare Parts List..............................................................................................................................................21
6.3.1 Spare Part list.................................................................................................................................................................................21
6.3.2 Spare Part list.................................................................................................................................................................................23

3

4

5
1.0 Introduction
Ruby pumps have been manufactured to the 2006/42/CE, 2014/34//EC directives. The relevant area criteria are indicated in the EN-60079-
10 , EN-12100:2010 , EN-809:1998+A1:2009 , EN-80079-36 , EN 80079-37 harmonized European standards. Therefore, if used according
to the instructions contained in this manual, the Ruby pumps will not represent any risk to the operator. This manual must be preserved in
good condition and/or accompany the machine as reference for maintenance purposes. The manufacturer rejects any liability for any
alteration ,modification, incorrect application or operation not complying with the content of this manual and that may cause damage to the
health and safety of persons, animals or objects stationing near the pumps
The following instructions solely refer to Ruby Air Operated Diaphragm Pumps. Since the pumps are used in combination with other
assemblies, such as solenoid valves, sensors or pulsation dampers, the valid operating instructions for these components and the associated
notes on safety must also be taken into account.
These instructions contain information on safety, installation, operation, maintenance, repair and environmental waste disposal of the Ruby
Air Operated Diaphragm Pump. Thoroughly read these instructions before use and always follow the information contained therein.
Persons entrusted with the installation, operation, maintenance or repair of the pump must have read and understood these instructions,
especially the chapter on “Health and Safety”. This applies in particular for those who are only occasionally involved in work on the pump,
like cleaning or service personnel.
Each pump is subjected to stringent inspections and function tests before leaving the factory.
You should always bear in mind that a correct function, a long lifetime and optimal operational reliability of the pump mainly depend on
■ correct installation
■ correct commissioning
■ and correctly performed maintenance and repair work.
Enquiries concerning service, spare parts or repairs should be addressed to the manufacturer
Always provide the following information:
■ Series
■ Pump size
■ Serial number of pump
This information is stamped on the identification plate on top of the pump.
Danger!
When returning pumps or pump parts to your supplier for repair or general overhaul, the delivery must be accompanied
bycertificates stating that pumps or pump parts are free of product and other aggressive or hazardous substances.
1.0.1 Pump Identification
Each pump has an identification plate carrying its specification details and materials.
Always refer to this data when contacting the manufacturer, dealer or customer service centers.
WARNING: removing or altering this identification plate and or the data it contains is forbidden.
Identification code on the plate against the “TYPE” heading specifies the composition and the materials used to build the pump. This data
will help ascertain whether the pump is suitable for the product to be pumped.

6
II 2G Ex h IIB T4 Gb
II 2D Ex h IIIB T135°C Db
II 3GEx h IIB T4 Gc
II 3D Ex h IIIB T135°C Dc
For ZONE 1 For ZONE 2
Ruby Pumps composition codes
1.0.3 Composition Codes
1.0.2 Markings and general information
In compliance with the 2014/34/EC standards, the Ruby pumps carry the following identification marks:
•EC Directive 2014/34/EC Equipment and protective systems intended for use in potentially explosive atmospheres (ATEX)
•EN ISO 80079-36 :2106 Non-electrical equipment for use in potentially explosive atmospheres - Basic method and requirements
• EN ISO 80079-37:Non electrical equipment for explosive atmospheres – No electrical type of protection by constructional safety '' c '' ,
control of ignition source “b” , liquid immersion “k”
•Machinery Safety Directive: 2006/42/EC
•IEC 60079-0 Explosive atmospheres - Equipment eneral requirements
Model Pump Body Center Se con Diaphragms Ball Seats Valve Ball O-ring Othe r Opons
Ruby 015 S:AISI 316 ELECTROPOLISHED W : PP FDA E : EPDM Conducve V : PV DF T : PTFE T : PTFE C: Triclamp
Ruby 025 A : Aluminum T : PTFE+back up (EPDM Conduc ve ) S : AISI 316 S : AISI 316
Ruby 040 Z : PTFE A+back up (EPDM Conduc ve )
Ruby 050
Ruby 080

7
1.1 Warranty
The correct function of each Ruby pump is tested in the factory.
However, should any defect appear, please contact the Manufacturer’s After-Sales Service, your dealer or the nearest Customer Service
Centre where you will receive assistance as quickly as possible. In any case, please provide:
Α- Your complete address
B- Pump identification
C- Explosion risk protection class
D- Anomaly description
All Ruby pumps are covered by the following warranty:
1. Five years for any faulty mechanical parts. The warranty period starts from the date of supply.
2. Any fault or anomaly must be reported to the the Manufacturer within eight days.
3. Warranty repair will be carried out exclusively at the Manufacturer's premises. Transportation charges will be at the client's expense.
4. Warranty shall not be extended in case of repair or replacement.
5. Faulty parts must be forwarded to the Manufacturer who reserves the right to test them in this own factory to identify the fault or any
external reason that may have caused it. Should the parts be found not faulty, the Manufacturer reserves the right to invoice the total
cost of the parts that had been replaced under this warranty.
Costs and transportation risks of faulty, repaired or replaced parts including custom charges will be borne entirely by the client.
Repair or replacement of faulty parts cover any obligation under this warranty.
The warranty DOES NOT cover any indirect damage and in particular any normal consumable material such as diaphragms, ball seats,
balls and others.
The warranty does not cover parts damaged as a consequence of incorrect installation, carelessness, neglect, incorrect maintenance, or
damages due to transportation or to any other reason or event that is not directly linked to functional or manufacturing defects.
The warranty excludes all cases of improper use of the pump or incorrect applications or non-observance of the information
contained in this manual.
Any controversy falls within the jurisdiction of the Court of Athens.
1.2 Transport, unipacking, storage
In order to avoid any problems you should check the delivered goods against the delivery note for completeness and correctness.
Be careful when unpacking the pump and proceed as follows:
■ Check the packaging material for transport damage.
■ Take the pump carefully out of the packaging material.
■ Check the pump for visual damage.
■ Remove the plugs from all pump ports.
■ Check seals and fluid lines for damage.
The following points must be strictly observed when preparing the pump for storage:
■ Store the pump in a dry place.
■ Thoroughly clean used pumps before storage.
■ Do not subject stored pumps to extreme temperature fluctuations.
1.3 Principle of function
1 Discharge manifo d
2 Top va ve ba (c osed during suction)
3 Diaphragm
4 Pump chamber
5 Bottom va ve ba (opened. Medium f ows into chamber)
6 Top va ve ba (open. Product is pressed out)
7 Center B ock (the drive air disp aces the medium via the diaphragm
and at the same time pu s back the second diaphragm)
8 Bottom va ve ba (c osed during de ivery)
9 Suction manifo d
10 Air contro unit
11 Air va ve drive
fig.2 Design of pump

8
1.4 Pump operation
Ruby Air Operated Diaphragm Pumps are oscillating positive displacement pumps with two pump chambers arranged opposite each other.
Both of these are separated by a diaphragm each into an air and a fluid section.
Both diaphragms are linked by a piston rod, so that with every stroke product is displaced to the outside from the one pump chamber and
product is drawn into the opposite pump chamber.
1.5 Improper use
Particularly, it is FORBIDDEN to use Ruby pumps for :
- production of vacuum;
- operation as an on -off valve, as a non-return valve or as a metering valve
- operation with liquid that is chemically incompatible, with the materials of construction;
- operation with suspended products whose specific weight is higher than the liquid's (for example with water and sand) .
- With with air pressures, temperatures or product characteristics that do not comply with the pump's technical data .
WARNING: since an endless variety of products and chemical compositions exist, the user is presumed to have the best
knowledge of their reaction and compatibility with the pump's construction materials. Therefore, before using the pump. all
necessary checks and tests must be performed with great care to avoid even the slightest risk, an event that the manufacturer
cannot foresee and for which he cannot be held responsible.
WARNING: the user must consider the ratio between the pump’s maximum surface temperature indicated on the marking
and the minimum ignition temperature of the layers and clouds of powder as shown in the ΕΝ1227-1.
WARNING: Use of the pump that does not comply with the instructions indicated in the use and maintenance manual will
cancel the safety and explosion protection requirements. The risks associated with use of the pumps under the exact conditions
set forth in the use and maintenance manual have been analysed, whilst the analysis of the risks associated with the interface
with other system components must be carried out by the installer
The user is responsible for classifying the area of use whilst identification of the equipment category is the responsibility of the
manufacturer
2.0 Safety Rules
Dangerous or hazardous practices or practice not complying with the safety rules and with the recommendations contained herein, may
cause serious injuries, material damage and even explosions and /or death for which the manufacturer cannot be held responsible.
WARNING: these instructions are essential for the pumps' compliance to the requirements of the 2006/42/EC directive and
must therefore be available, known, understood and applied.
WARNING: the personnel in charge of installing, inspecting and servicing the pumps must have suitable technical knowledge
and training in matters concerning potentially explosive atmospheres and the related risks
WARNING: use of the pumps in a manner that does not comply with the instructions indicated in the use and maintenance
manυaI will cancel all the requirements for safety and protection against of explosions.
WARNING: before intervening on the pump and/or servicing or repairing it, please- note that you must:
A - Discharge any product that was being pumped
B - Wash it internally using a suitable non-flammable fluid, then drain.
C - Cut-off the air supply using the relevant valve and make sure that no residual pressure remains inside it.
D - Close all on-off valves {delivery and intake sides) relative to the product.
Ε - Disconnect the network air supply;
F - Wear suitable individual protection before any maintenance or repair (goggles / face protection,
gloves, closed shoes, aprons and others).
WARNING: before using the pump, make sure that the fluid to be pumped is compatible with the explosion protection class
and with construction materials of the pump.
DANGER OF CORROSION, PRODUCT SPILLS AND/ OR EXPLOSIONS CAUSED BY CHEMICAL REACTIONS

9
For installation and use in a potentially explosive environment, comply with these general precautions
- ascertain that the pump is full and if possible, that the level is above it by 0.5 m;
- ascertain that the fluid treated does not contain or cannot contain large solids or solids of a dangerous shape
- ensure that the intake or delivery ports are not obstructed nor limited to avoid cavitation or pneumatic motor strain.
- also ascertain that the connection piping is strong enough and cannot be deformed by the pump weight or by the intake. Also check
hat the pump is not burdened by the weight of the piping
- If the pump is to stay in disuse for a long period of time, clean it carefully by running a non-flammable liquid detergent through it that
is compatible with the pump's construction materials
- if the pump was turned off for a long period of time, circulate clean water it in for some minutes to avoid incrustations.
- before starting, after long periods of disuse, clean the Internal and external surfaces with a damp cloth;
- check the grounding;
- always protect the pump against possible collisions caused by moving objects or by various blunt materials that may damage it or react
with its materials;
- protect the pump's surrounding ambient from splashes caused by accidental pump failure;
- if the diaphragms are completely torn, the fluid may enter the air circuit, damaging it, and be discharged from the exhaust port. It is
therefore necessary for the exhaust port to be conveyed by pipes to a safe area.
WARNING: the air supply pressure must never be over 7 bar or below 2 bar
WARNING: when using the pump with aggressive or toxic liquids or with liquids that may represent a health hazard you
must install suitable protection on the pump to contain, collect and signal any spills: DANGER OF POLLUTION, CONTAMINATION,
INJURIES AND/OR DEATH.
WARNING: the pump must not be used with fluids that arc not compatible with its construction materials or in a place
containing incompatible fluids.
WARNING: installing the pumps without on off valves on the intake and delivery sides to intercept the product in case of
spillage is forbidden: danger of uncontrolled product spillage
WARNING: installing the pumps without on-off. three way or check valves on the air supply piping to prevent the pumped
liquid from entering the pneumatic circuit if the diaphragms are broken is forbidden: danger of fluid entering the compressed air
circuit and being discharged into the environment
WARNING: Should the user think that the temperature limits set forth in this manual may be exceeded during service, a
protective device must be installed on the system to prevent the maximum allowed process temperature from being reached.
If exceeded, respect of the maximum temperature marked cannot be guaranteed
WARNING: The pumps must always be grounded irrespective of any organ to which they are connected. Lack of grounding
or incorrect grounding will cancel the requirements for safety and protection against the risk of explosion
WARNING: the use of pumps made with non-conductive material, which become charged with static, and without suitable
grounding for flammable liquids is forbidden: RIS OF EXPLOSIONS DUE TO STATIC CHARGE
WARNING: Aggressive, toxic or dangerous liquids may cause serious injuries or damage to health, therefore it is forbidden
to return a pump containing such products to the manufacturer or to a service center. You must empty the internal circuits from
the product first and wash and treat it.
WARNING: Pumps containing aluminium parts or components coming into contact with the product cannot be used to ρump
Ill-trichloroethane, methylene chloride or solvents based on other halogenated hydrocarbons:
DANGER OF AN EXPLOSION CAUSED BY A CHEMICAL REACTION
WARNING: Conductive Polypropylene, conductive PVDF pumps are not to be installed in applications where the pumps
may be subjected to oil, greases and hydraulic liquids

10
WARNING: The components of the pneumatic exchanger, including the shaft are made from materials that are not specifically
resistant to chemical products, if the diaphragm should break, replace these elements completely if they have come into contact
with the product
WARNING:The air-driven motor of the Ruby pumps is self-lubricating and will not require any greasing. Therefore a void
using Iubricated and non- dried air.
WARNING: ascertain that during service no anomalous noise appears. In that case, stop the pump immediately
WARNING: ascertain that the fluid at the delivery side does not contain gas. Otherwise stop the pump immediately
WARNING: Periodic controls must be made to ensure that there is no powder and/or deposits on the external and internal
surfaces of the pump and, if necessary, they must be cleaned with a damp cloth
WARNING: removal of the silencer and the air supply fitting must be done when free from powder. Before restarting the
pump, ensure that no powder has entered the pneumatic distributor.
To replace worn parts, use only original spare parts.
Failure to comply with the above may give rise to risks for the operator, the technicians, the persons, the pump and/or the
environment that cannot be ascribed to the manufacturer.
WARNING: diaphragm pumps with negative suction are affected by the following factors:
-viscosity and specific weight of the fluid;
-suction diameter and length.
Position the pump as close as possible to the point of collection {within 2.5 m.) and in any case never more than 5 m. The diameter
of the intake pipe must never be smaller than the connection of the pump, but must be increased as the distance increases. Fluid
to be pumped with negative suction must never exceed a viscosity of 5.000 cps at 20° C and a specific weight of 1.4 g/I. These
elements can cause derating and reduce the duration of the diaphragm: DANGER OF PREMATURE BREA AGE.
2.1 Equipotential bonding / earthing
In principle, pumps and accessories must be earthed or provided with equipotential bonding if there
is the possibility of product specific electro-static charging and when used in potentially explosive
areas. Pumps and pulsation dampers with ATEX II 2 Ex h IIB T4 b -- II 2D Ex h IIB T135 b
approval are therefore fitted with an earthing screw.
Please Pay attention
For Zone 1
• Aluminum in combination with stainless steel (greater or equal 16,5% Cr) is only be used if
the steel cannot corrode and no iron oxide and/or rusty particles can be deposited on the
surface. (appropriate reference to the properties of the stainless steel shall be given in the
technical documentation and instruction for use.
• For Pumps with diaphragm type TFM:
1. Not run empty with flammable fluid/gas.
2. Flush before
For Zone 2
1. Not run empty with flammable fluid / gas.
2. Flush before
WARNING: the use of pumps made with non-conductive material, which become charged with static, and without suitable
grounding for flammable liquids is forbidden:
RIS OF EXPLOSIONS DUE TO STATIC CHARGE

11
3.0 Installation
To be observed before installation
1. The installation must only be carried out by persons who have the necessary skills for this work
2. Before installation align the pump correctly and fasten it without any tension. Pipelines must be assembled in a way that the basic
weight of the lines is not reasting on the pump
3. In order to avoid damage to the pump new installations should generally be checked for any debris (welding beads, pieces of wire, etc.)
in tankand pipeline system.
4. Consider the arrangement of the pump with respect to suction and discharge heads.
5. The pump system must be designed according to the requirements of the application. Valves or spools must be installed as close as
possible to pressure port. This also applies for T-fittings with valve for bypass control or pressure relief valves, pressure gauges, flow
control valves and shut-off valves.
6. Thoroughly examine the alignment of the pump with the pipelines, in order to avoid strain and premature wear.
7. Check all pipelines for leaks. This applies in particular for the suction line, in order to avoid the intake of air.
8. If the fluid to be pumped contains solid particles bigger than specified , a filter must be installed. The filter must be of such a size, that
the change in resistance at the pump inlet port is only minor. This filter must be permanently monitored and, if necessary, cleaned.
9. Fluids which change their viscosity must be permanently agitated, or the tank must be fitted with a temperature sensor. With increasing
viscosity start the agitator and/or the heating. This is of special importance for intermittent operation!
Note: It is recommended to install flexible, shape and pressure resistant hoses or compensators at the suction and pressure
ports of the pump (Fig. 3). This will prevent the transfer of pulsation shocks into the pump.

12
3.1 Connection of air supply line
We recommend to supply the air through a hose to the pump. Using moisturized compressed air requires the installation of a service unit
with water separator. This control equipment can additionally be used to regulate the flow capacity of the pump. The diaphragm must not
be subjected to shockloads. For this reason we recommend the installation of a spool, diaphragm or needle valve as shut-off element.
WARNING: pneumatic supply to the Ruby pumps must he made using FILTERED. DRIED. NON LUBRICATED OIL FREE AIR
at a pressure of not less than 2 bars and not more than 7 bars.
WARNING: do not remove RESET for any reason and/or do not connect the air supply to the RESET channel
Warning! Do not use a ball valve as shut-off element
Note: Especially for plastic pumps or pumps with PTFE diaphragms it is highly recommended to install a slow start valve in the
supply line to the pump. This valve protects both the diaphragm and housing parts against suddenly occurring pressure shocks.
3.2 Connection of cuction and pressure lines
Suction and pressure lines must be installed in a way that no additionally loads are applied to the pump ports.
The tightening torque of the mounting screws and the pressure strength of the sockets and flanges must be observed with the installation
of the suction and pressure lines. After assembly check the system for leaks
3.3 Pump in suction operation
Ruby Air Operated Diaphragm Pumps are dry self-priming. Depending on the pump design a suction head of max. 9 m Wc can be reached,
when the suction line is filled.
3.4 Pump in submerged operation
The Ruby Air Operated Diaphragm Pumps are suitable for submerged operation. However, it must be assured that the surrounding fluid
will not attack the pump.
When installing the pump make sure that the air discharge muffler has been removed and the exhaust air is discharged from the fluid
through a hose.
3.5 Connecting to the product circuit
After positioning the pump you can now connect it to the product circuit as follows:
WARNING: only fittings with cylindrical gas threads in materials compatible with both the fluid to be pumped and the pump’s
construction materials must be used.
For example:
Pump made from PP - PP fitting
Stainless steel pump = stainless steel fitting.
1. On the suction and discharge manifold install a manual valve of the same diameter as the pump inlet (never smaller) to intercept the
fluid correctly in case of spills and / or when servicing the pump.
2. Install the sleeves to secure the flexible hoses on both valves.
WARNING: the pump must be connected with FLEXIBLE HOSES REINFORCED WITH A RIGID SPIRAL of a diameter never
smaller than the pump's connection. The filters or other equip-ment installed at the intake side must be suitably dimensioned in
οrder to avoid pressure drops. For negative installations and/or viscous fluids, use hoses with an OVERSIZE DIAMETER, especially
on the intake side. Connections using rigid pipes may cause strong vibrations and break the manifolds

13
3. Connect the product intake and delivery hoses to their respective fittings whilst taking into consideration the signs on the pump:
ΊΝ" = INTAKE (down) and
OUT" = DELIVERY (up)
or according to that indicated by the arrows.
4. Secure the hoses using the relevant clamps.
WARNING: Provide appropriate support for the piping. THE PIPING MUST BE STRONG ENOUGH TO AVOID DEFORMATION
DURING THE SUCTION PHASE AND MUST NEVER WEIGH DOWN ON THE PUMP IN ANY WAY OR VICE VERSA .
5 . If used for drum suction (not below head), the submersed end of the intake hose must be provided with a diagonally cut fixing to prevent
it from adhering to the drum bottom.
WARNING: Ascertain that the fluid treated does not contain or cannot contain large solids or solids of a dangerous shape
and that the intake or delivery ports are not obstructed nor limited to avoid either cavitation or pneumatic motor strain.
Connection off the product circuit finishes here.
3.6 Noise emissions (2003/10/EC)
In a room with several pumps you may experience an extreme development of noise . Depending on the sound pressure level the following
measures must therefore be applied:
Below 70 dB (A) : No special measures required
Above 70 dB (A) : Persons who are permanently in the room must wear ear defenders.
Above 85 dB (A : Room with dangerous noise level.! Each door must have a clearly noticeable waning sign
to warn persons from entering the room without ear defenders.
3.7 Temperature range of the diaphragm material
TFM Compound Diaphragm: -10oC - 130oC
NBR Conductive Diaphragm: -10oC - 100oC
TFM Full capacity Compound Diaphragm: -10oC - 130oC
EPDM Conductive Diaphragm: -10oC - 100oC
VITON Conductive diaphragm : -40oC - 170oC
3.8 Temperature range of the Housing material
Stainless steel: -25oC - 130oC
Aluminium: -10oC - 130oC
Polypropylene: 0oC - 60oC
PVDF + CF: -10oC - 120oC

14
4.0 Diaphragm and manifold assembly
Step 1
Insert shaft into bearings in which you have
put already P MOLYKOTE 21
Step 2
Insert into the shaft the piston inner and the
diaphragm and mount.
Step 3
Repeat same process also for the other
diaphragm after having installed the pump
housing first
Step 4
Install also second pump housing and
mount on
Step 5
Install ball valves, ball seats, o-rings
Step 6
Mount the manifolds
4.1 Pump Disassembly
Step 1
Remove the discharge manifold by untying
the screws in X formulation
Step 2
Remove the balls and the seats. Reverse
the pump and remove the suction manifold
with the same way
Step 3
Untie one of the two housings, by untying
the screws gradually and cyclically.
Step 4
Detach the diaphragm from the central
block by hand and untie it with a left rotation.
Step 5
Untie the opposite housing and pull the
diaphragm along with the shaft outwards.
Remove the diaphragm from the shaft

15
4.2 Air control valve disassembly - assembly
Step 1
We remove the safeties(step 1)
Step 2
From the one side we push the air valve
shaft
Step 3a
From the opposite side we remove both cap
and air valve shaft
Step 3b
From the opposite side we remove both cap
and air valve shaft
Step 4
We push outwards the air valve so that it
exits the central block
4.3 Air chamber and shaft bearing assembly-disassembly
Step 1
Install bearings inside the central block
reception
Step 2
Install and screw the air exhaust cover onto
the central block
Step 3
Install flanges into the air chambers
Step 4
Mount central block with air chambers
Step 5
Mount screws

16
5.0 Troubleshooting
The following instructions are intended exclusively for authorised skIilled maintenance engineers. In event of abnormal behaviour and in
order to fix faults, please refer to the following troubleshooting instructions.
WARNING: For more serious problems, we strongly recocomend that you contact the ALPHADYNAMIC PUMPS Co:
our engineers will provide you assistance as quickly as possible.

17
6.0 Technical data
6.1.1 Dimensi ns drawing

18
6.2 Perf rmance
Ruby 080 FDA pump
PTFE A Full capacity Diaphragm Fitted
Flow. Rate.....................................................830 L/min
Air inlet ...................................................................3/4"
Suction – Discharge port................DN 80 RI-CLAMP
Suction lift (dry).......................................................5 m
Max. Solid size ( diameter) ..................................8 mm
* he curves and performance values refer to pumps with submerged suction and a free delivery outlet with water
at 20°C, and vary according to the construction material.
0
10
20
30
40
50
60
70
80
0
500
1000
1500
2000
2500
3000
3500
4000
0 50 100 150 200 250 300 350 400 450 500 550 600 650 700 750 800 850 900
2 bar
3 bar
4 bar
5 bar
6 bar
7 bar
7 bar
6 bar
5 bar
4 bar
3 bar
2 bar
Capacity L/min
Head (m)
Air Consumption NL/min
Air Consumption NL/minAir Pressure Supply

19
EPDM Diaphragm Fitted
Flow. Rate.....................................................830 L/min
Air inlet ...................................................................3/4"
Suction – Discharge port................DN 80 RI-CLAMP
Suction lift (dry).......................................................5 m
Max. Solid size ( diameter) ..................................8 mm
* he curves and performance values refer to pumps with submerged suction and a free delivery outlet with water
at 20°C, and vary according to the construction material.
0
10
20
30
40
50
60
70
80
0
500
1000
1500
2000
2500
3000
3500
4000
0 50 100 150 200 250 300 350 400 450 500 550 600 650 700 750 800 850 900
2 bar
3 bar
4 bar
5 bar
6 bar
7 bar
7 bar
6 bar
5 bar
4 bar
3 bar
2 bar
Capacity L/min
Head (m)
Air Consumption NL/min
Air Consumption NL/minAir Pressure Supply

20
PTFE Diaphragm Fitted
Flow. Rate.....................................................750 L/min
Air inlet ...................................................................3/4"
Suction – Discharge port................DN 80 RI-CLAMP
Suction lift (dry).......................................................5 m
Max. Solid size ( diameter) ..................................8 mm
* he curves and performance values refer to pumps with submerged suction and a free delivery outlet with water
at 20°C, and vary according to the construction material.
0
10
20
30
40
50
60
70
80
0
500
1000
1500
2000
2500
3000
3500
4000
0 50 100 150 200 250 300 350 400 450 500 550 600 650 700 750 800
Capacity L/min
Head (m)
Air Consumption NL/min
Air Consumption NL/minAir Pressure Supply
2 bar
3 bar
4 bar
5 bar
6 bar
7 bar 7 bar
6 bar
5 bar
4 bar
3 bar
2 bar
Table of contents
Other ALPHA DYNAMIC PUMPS Water Pump manuals
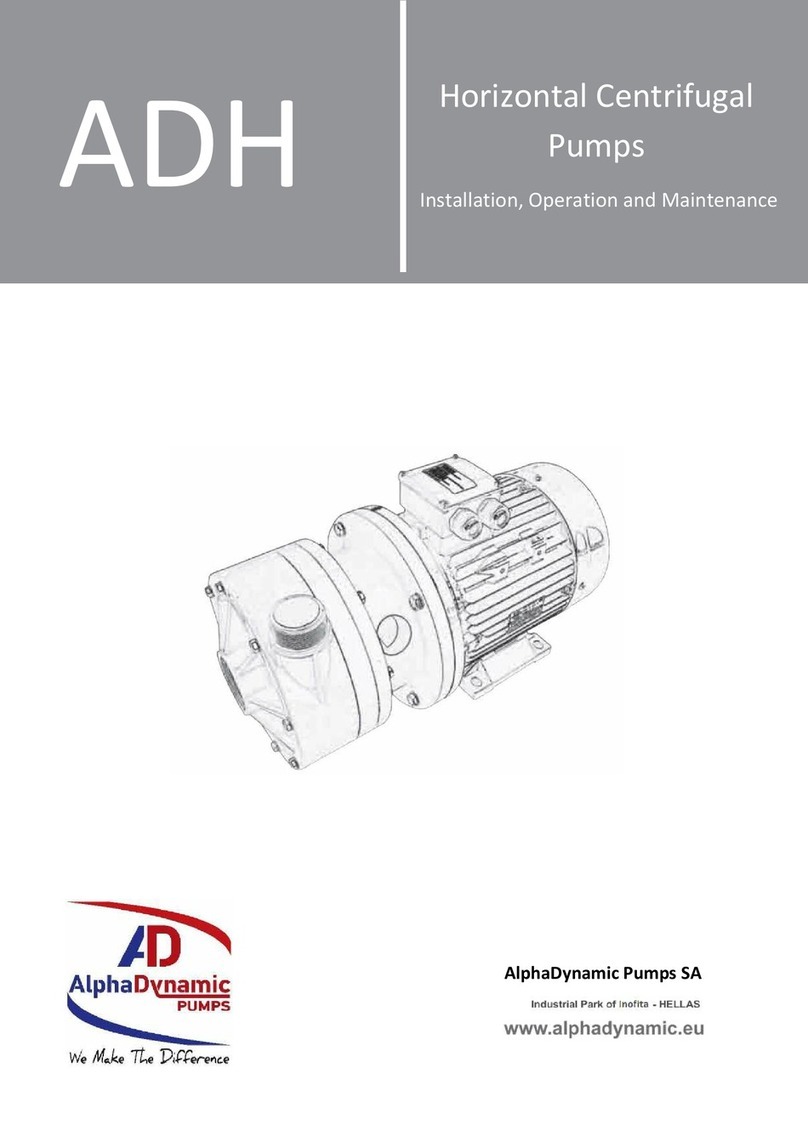
ALPHA DYNAMIC PUMPS
ALPHA DYNAMIC PUMPS ADH Series Manual
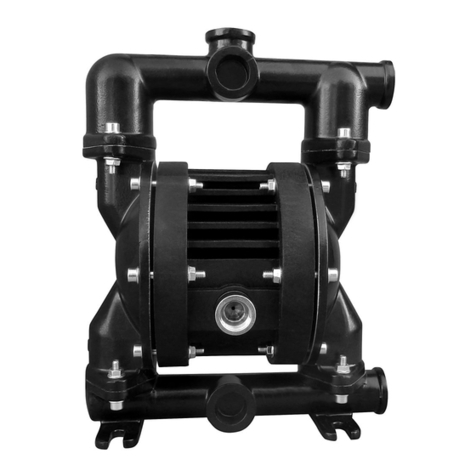
ALPHA DYNAMIC PUMPS
ALPHA DYNAMIC PUMPS Ruby 051 User manual
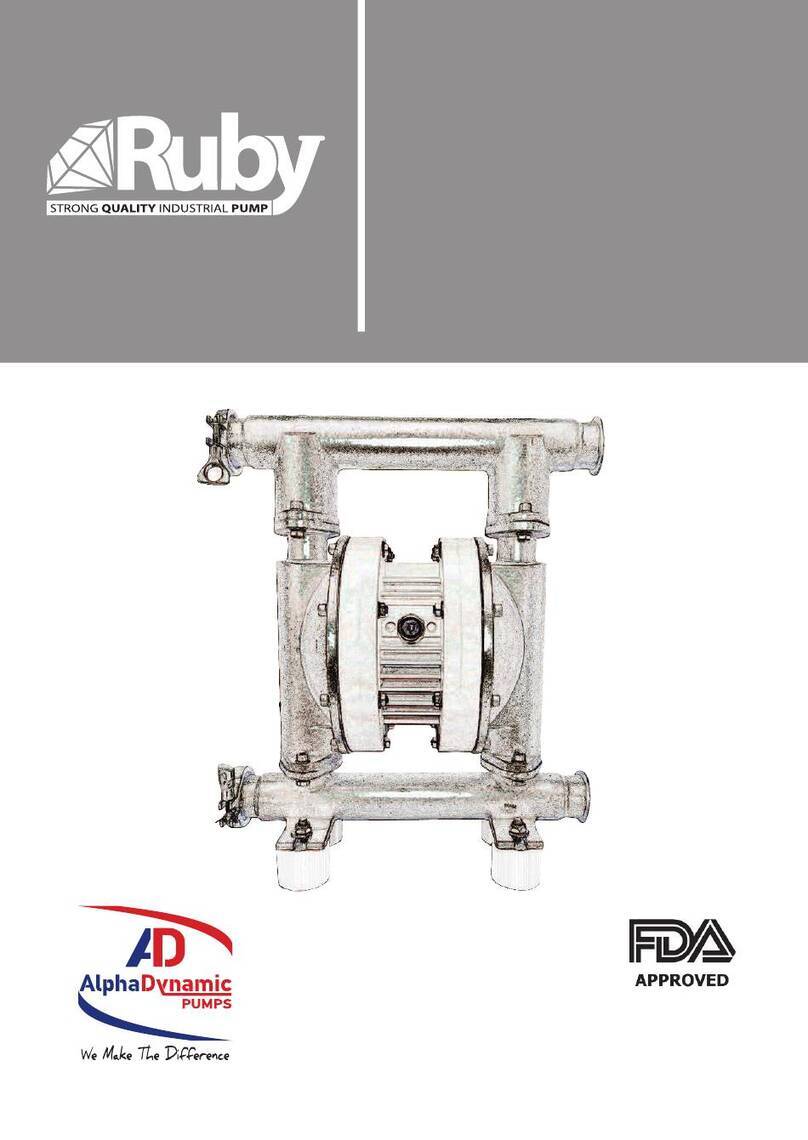
ALPHA DYNAMIC PUMPS
ALPHA DYNAMIC PUMPS Ruby 040 FDA User manual
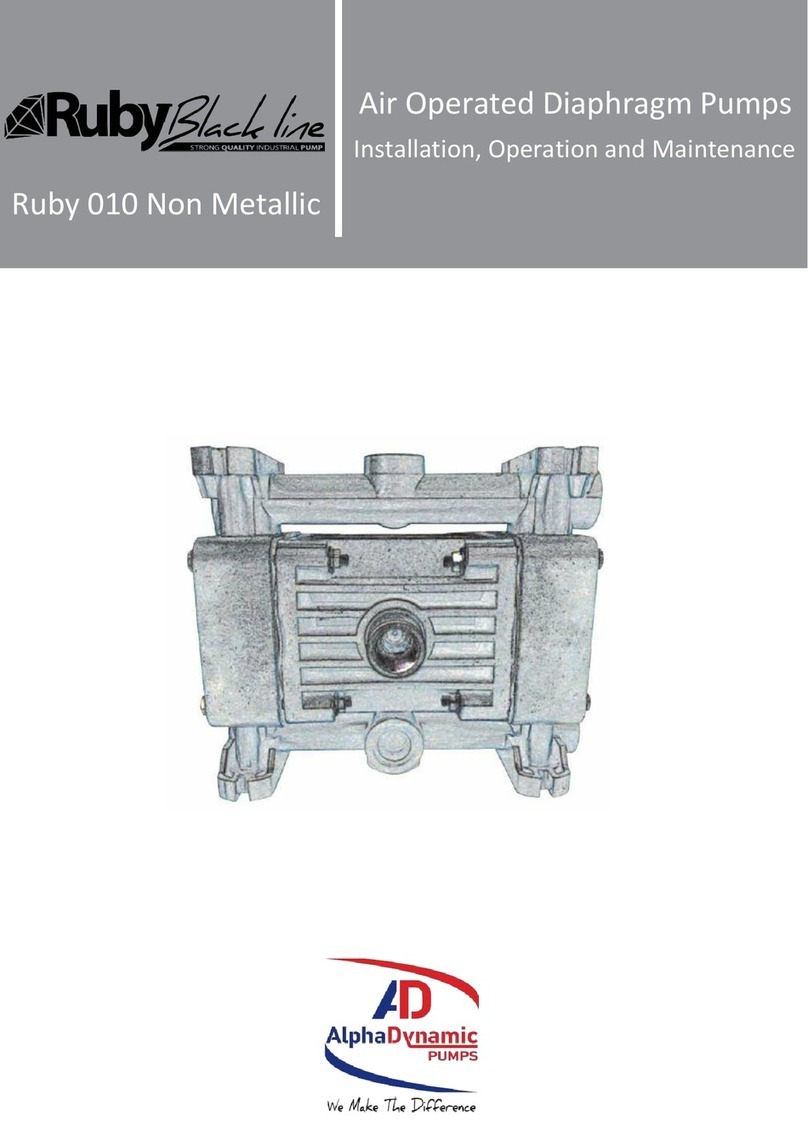
ALPHA DYNAMIC PUMPS
ALPHA DYNAMIC PUMPS Ruby Black Line 010 Non Metallic User manual
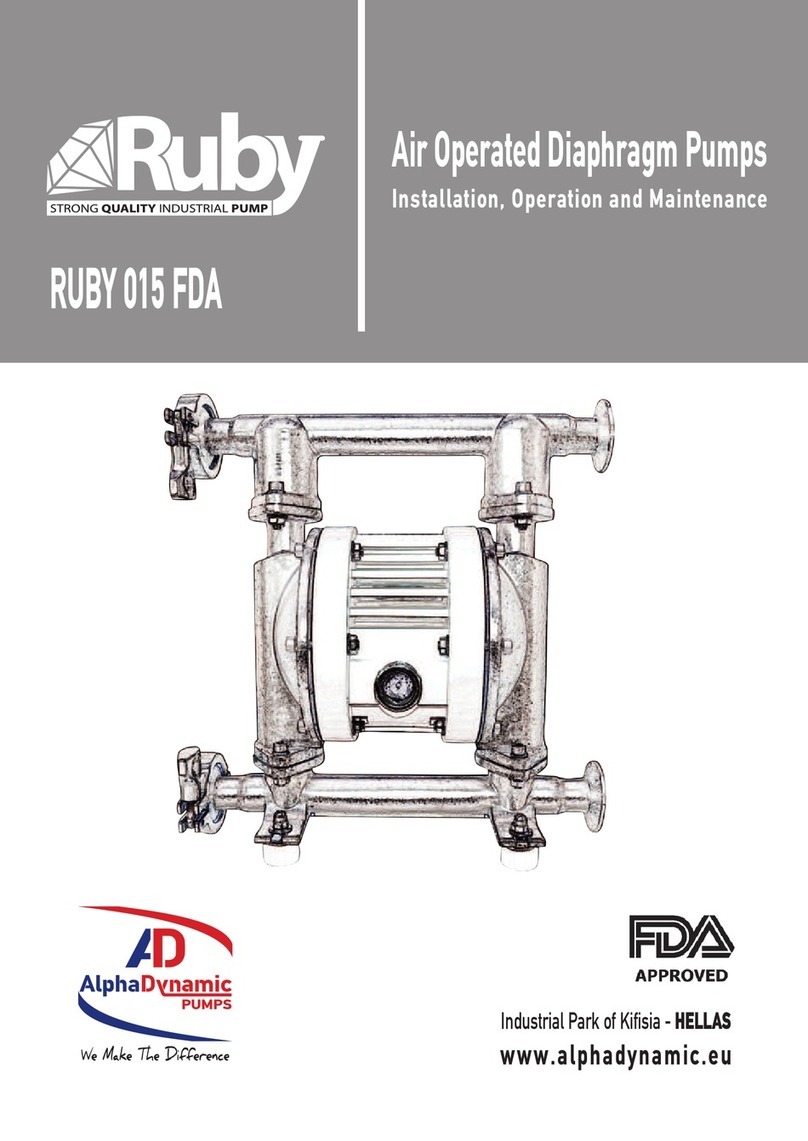
ALPHA DYNAMIC PUMPS
ALPHA DYNAMIC PUMPS Ruby 015 Installation and operating instructions
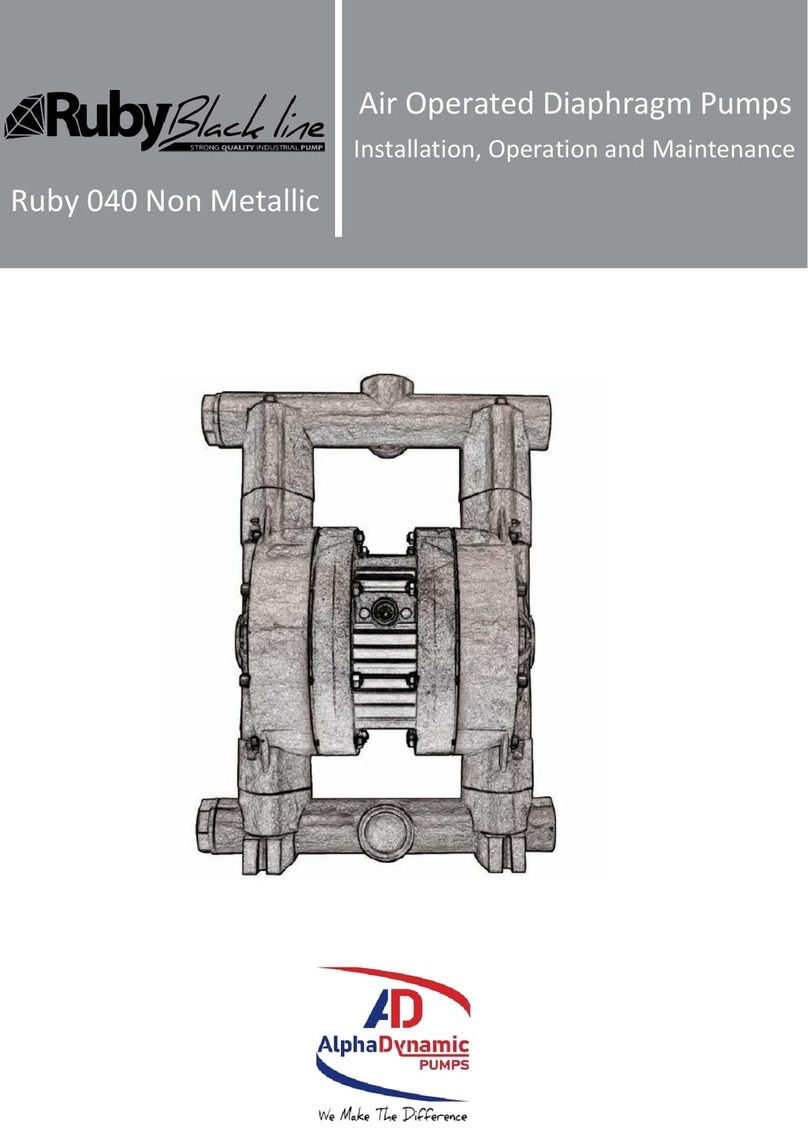
ALPHA DYNAMIC PUMPS
ALPHA DYNAMIC PUMPS Ruby Black Line 040 User manual
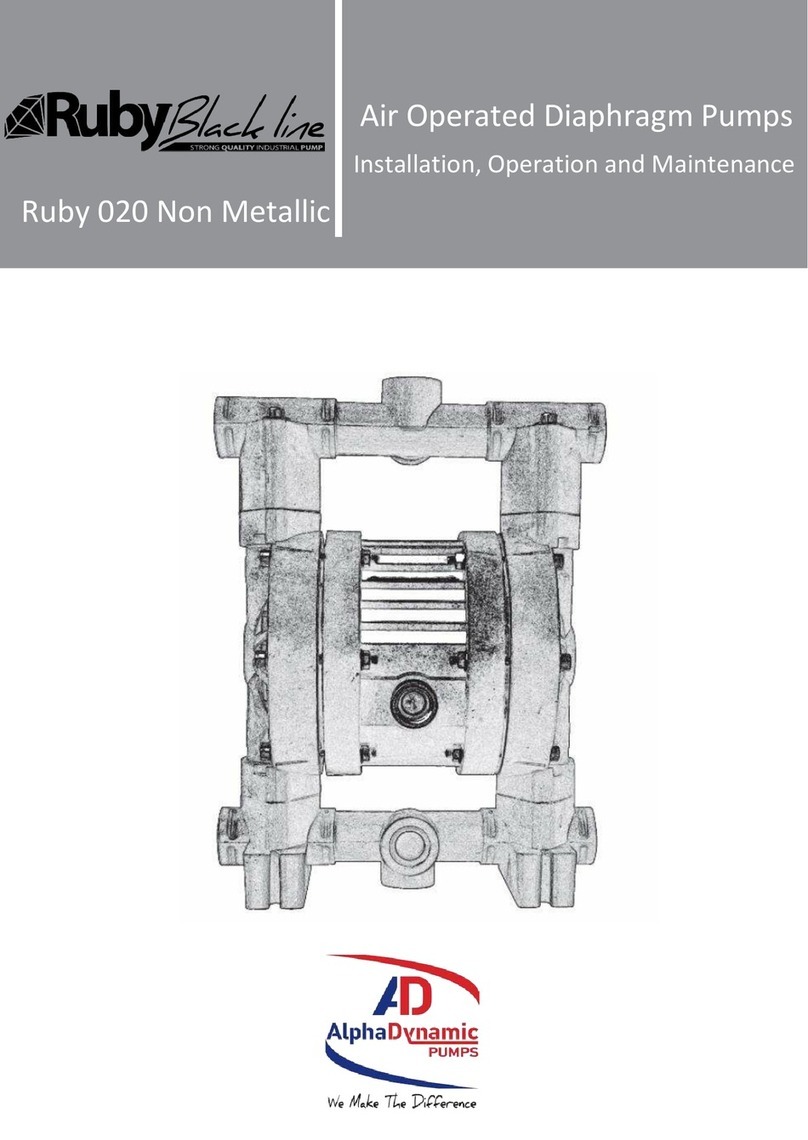
ALPHA DYNAMIC PUMPS
ALPHA DYNAMIC PUMPS Ruby Black Line 020 Non Metallic User manual
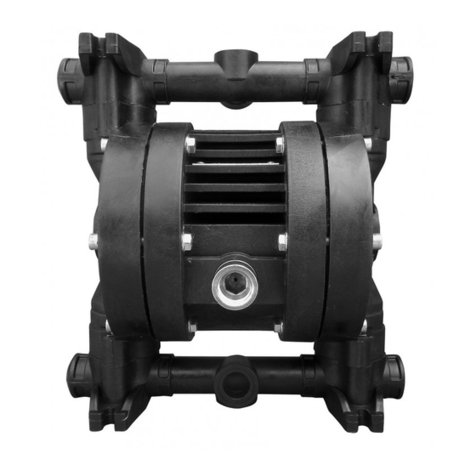
ALPHA DYNAMIC PUMPS
ALPHA DYNAMIC PUMPS MINI 005 Installation and operating instructions
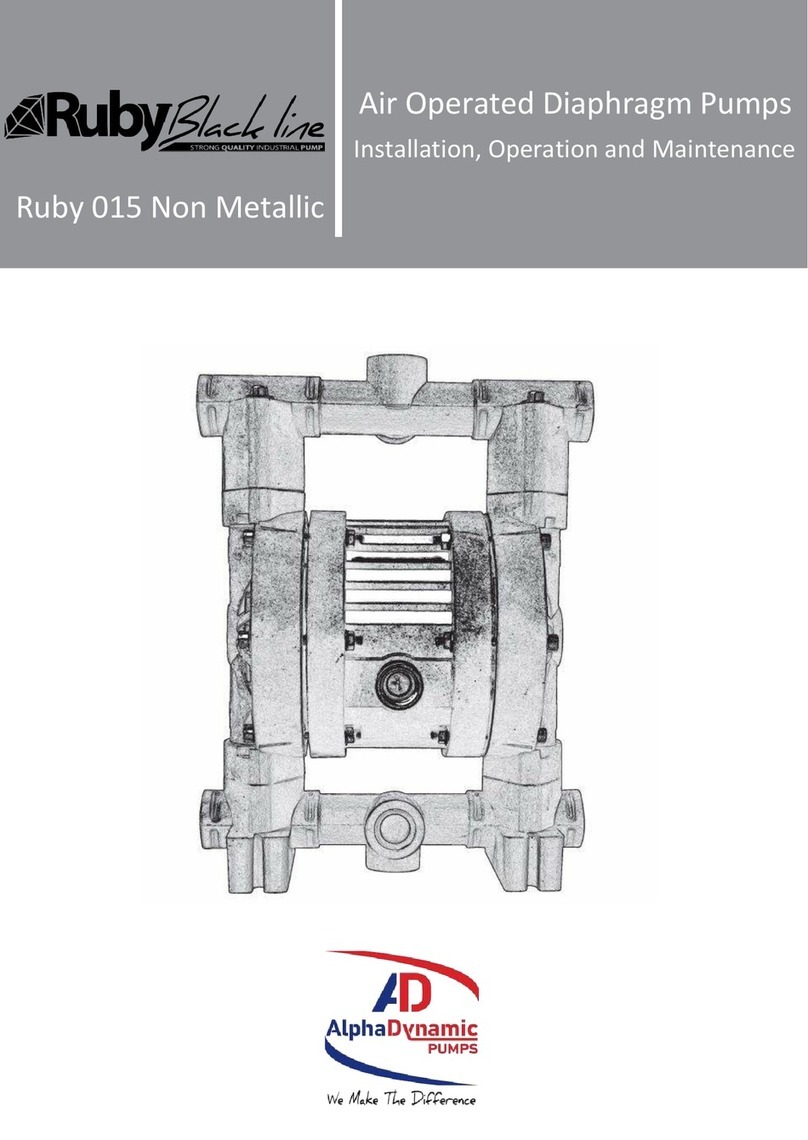
ALPHA DYNAMIC PUMPS
ALPHA DYNAMIC PUMPS Ruby Black Line 015 User manual