Amana RSKP0014 User manual

ATTENTION INSTALLING PERSONNEL
As a professional installer you have an obligation to know
the product better than the customer. This includes all safety
precautions and related items.
Prior to actual installation, thoroughly familiarize yourself with this
Instruction Manual. Pay special attention to all safety warnings.
Often during installation or repair it is possible to place yourself
in a position which is more hazardous than when the unit is in
operation.
Remember, it is your responsibility to install the product safely
and to know it well enough to be able to instruct a customer in its
safe use.
Safety is a matter of common sense...a matter of thinking before
acting. Most dealers have a list of specic good safety practices...
follow them.
The precautions listed in this Installation Manual are intended as
supplemental to existing practices. However, if there is a direct
conict between existing practices and the content of this manual,
the precautions listed here take precedence.
RECOGNIZE THIS SYMBOL AS A SAFETY PRECAUTION
Only personnel that have been trained to install, adjust, service
manual should service the equipment. The manufacturer will not
be responsible for any injury or property damage arising from
improper service or service procedures. If you service this unit,
you assume responsibility for any injury or property damage
which may result. In addition, in jurisdictions that require one or
only licensed personnel should service the equipment.
Improper installation, adjustment, servicing or repair of the
without proper training may result in product damage, property
damage, personal injury or death.
WARNING
Cancer and Reproduc�ve Harm -
www.P65Warnings.ca.gov
PROP 65 WARNING
FOR CALIFORNIA CONSUMERS
0140M00517-A
WARNING
DESCRIPTION
Control board installation procedures are described in detail in
these instructions. Read and follow these instructions carefully
before replacing the control board. Failure to do so may result in
control board damage.
Damage to the control board can occur from failure to disconnect
power supply or failure to set the master switch (located on the
control board) to OFF before removing the low voltage terminal
strip cover from an installed control board. Damage to this board
by not following these instructions is considered misuse and not
covered under either the standard unit warranty or any extended
service contract.
All warranty replaced boards must be returned to the parts source
from which they were purchased to insure proper warranty credit.
ELECTROSTATIC DISCHARGE (ESD)
PRECAUTIONS
Before removing the new control board from the static wrap, it
is very important to discharge any static electricity. Discharging
the static electricity can be accomplished by two methods: the
servicer can wear a ground strap or by touching the metal chassis
before replacing the board.
EXISTING BOARD REMOVAL PROCEDURE
1. Disconnect power to the unit by unplugging the power cord
at the wall outlet or subbase, or disconnect power at the fuse
box or circuit breaker.
19001 Kermier Rd., Waller, TX 77484
www.amana-ptac.com
IO-905B
01/2020
is a registered trademark of Maytag Corporation or its related companies and is used
under license to Goodman Company, L.P., Houston, TX, USA. All rights reserved.
© 2015 - 2016, 2020 Goodman Company, L.P.

2
2. If the cabinet front is screwed to the chassis, remove the 1/4”
screw (or screws) located behind the inlet grille. Pull the inlet
grille forward from the top of the grille to access screw(s).
FRONT MOUNTING
HOLE
3. Remove cabinet front from chassis by tilting the bottom of the
front forward, lifting slightly up and forward.
4. If a remote thermostat or any low voltage accessory is being
used, remove the low voltage pin connector from the low
voltage terminal strip. If a previous version board is being
replaced, remove wires from the low voltage terminal strip.
123
ON
PULL TO REMOVE
THERMOSTAT KNOB
Lift Off
PULL TO REMOVE
MODE SWITCH KNOB
ESCUTCHEON
SCREW (2)
SCREW
Figure 2
5. Remove knobs and escutcheon.
6. Remove the two mounting screws, one on each side of
control board cover. Some models may have a screw on
the lower right side of the control panel that will need to be
removed. Tilt control panel out and remove cover.
7. Remove the wires from the board in the unit, including
Thermistor Sensors if they plug into the board.
8. Remove the four screws holding the board and remove the
old board.
NEW CONTROL BOARD INSTALLATION
PROCEDURES
9. If existing unit has a remote mounted “o board” transformer
for board power, proceed to Step 13.
10.Lift the control panel up so the control panel is free of its
hinges. Orient the control panel so there is easy access for
mounting components to the inside of the control panel.
11. Using the two #8 screws that are provided, screw the
transformer that was provided with the kit to the control panel
in the transformer mounting holes provided in the panel. See
Figure 3.
12.The external transformer will come with the Black wires
connected to the LOAD terminal of the transformer (LOAD
terminals are the low voltage terminals) and the Gray wire
connected to the COM terminal on the transformer. The
additional Gray wire will need to be connected to the 230 or
265 volt tap on the transformer. Place the control panel back
on its hinges.
Refer to the serial plate for voltage information.
13.Install the new board and reinstall the screws removed in
step # 8.
Refer to appropriate wiring diagram
beginning on page 11 for proper wiring.
If unit has a 2 speed relay, Remove
the relay and all wires associated with it from the unit.
14.Using the insulated terminals connect the two (2) Black wires
from the Load terminals on the transformer to the “24VAC
Transformer” terminals on the control board. See Figure 4.
15.Connect the Gray wire from the COM terminal on the
transformer to line 2 on the control board. Connect the
additional Gray wire from the 230 or 265 volt tap on the
transformer to line 1 on the control board.
TRANSFORMER
Figure 3

3
GY22
BK37
BK37
LIN E 1 HEATER 1 HEATER 2
LINE 2
COMPRESSOR
24VAC~ TRANSFORMER
12VA CLASS 2 ONLY
GY21
TRANSFORMER
LINE
LOAD
COM
265
230
Figure 4
16. Thermistor Temperature Sensors Installation
A. It is recommended that the Indoor Discharge
Thermistor (with the YELLOW wires) be installed
but it is optional. If you choose not to install this
sensor, the green status light will remain illuminated
continuously. For status light functionality,
the YELLOW thermistor MUST be installed.
Instructions are as follows:
A1. Carefully cut and remove the gasket on the left
and right sides of discharge screen. Remove
the two (2) 5/16” screws holding the indoor
exhaust screen above the indoor coil. Remove
the indoor exhaust screen.
Remove the two (2) 1/4” screws connecting the
heater panel to the evaporator coil.
Remove the two (2) screws mounting the air
bae to the top of the heater panel and remove
and discard the air bae.
A2. Install the new air bae. Route the yellow
thermistor probe from right to left through the
wiring tube enclosure. Mount the black tip of
the yellow thermistor probe in the plastic clip
provided. Hold the plastic clamp in place and
secure the clamp to the left end of heater panel
using one of the original screws. Replace the
screw on the right end of the air bae being
careful not to damage the wiring insulation on
the probe.
YELLOW
THERMISTOR
PLASTIC CLAMP
CLAMP END OF
THERMISTOR
SECURELY
WIRE ENCLOSURE
ROUTE THERMISTOR
THROUGH TUBE ON
BLOWER EXTENSION
Figure 5
A3. Replace the heater panel, routing the yellow wire
around the right end of the heater panel and into the
control panel pulling snug to prevent the wire from
being entangled in the blower wheel or being visible
from above. Replace the two screws mounting the
heater panel to the evaporator coil.
A4. Replace the exhaust grille and two mounting screws.
A5. Connect the yellow wire using the plug-on connector
to the new board on the IDT (yellow) terminals.
B. If the existing Indoor Ambient Thermistor (with the
BLACK wires) was connected to the board by a plug-
on connector, reconnect it to the new board on the IAT
(black) terminals. If the existing Indoor Coil Thermistor
was soldered to the previous board, install the new black
thermistor per Figure 6 and connect as above.
Clip is designed to be pushed
into the coil between
the aluminum fins
and attach over
two (2) screws.
Figure 6
C. If the existing Indoor Coil Thermistor (with the RED wires)
was connected to the board by a plug-on connector,
reconnect it to the new board on the ICT (red) terminals.
If the previous board used indoor coil bi-metals, remove
and discard the bi-metal devices. The access door will
need to be removed on the indoor coil to gain access to
the bi-metal. See Figure 6. The Indoor Coil Thermistor
will need to clip on the vertical section of the 90-degree
bend of the inlet line to the indoor coil. See Figure 7.
Connect the Indoor Coil Thermistor to the board as
noted above.
D. If the existing Outdoor Coil Thermistor (with the BLUE
wires) was connected to the board by a plug-on
connector, reconnect it to the new board on the OCT
(blue) terminals. If the previous board used indoor coil
bi-metals, remove and discard the bi-metal devices. The
Indoor Coil Thermistor will need to clip on the crossover
tube shown in Figure 8. There will be two clips supplied
in the kit for the Blue Thermistor. One clip as supplied
on the sensor will t 5/16” tubing used on the bent coil,
and an additional clip (loose in the bag) will t 3/8” tubing
used on the at slab coil. If you have a slab coil, you
will need to remove the 5/16” clip from the sensor and
replace it with the 3/8” tube clip. Connect the Outdoor
Coil Thermistor to the board as noted above. Outdoor
Coil Thermistors are only used on Heat Pump models;
DO NOT INSTALL THIS SENSOR IF THE UNIT IS NOT
A HEAT PUMP.

4
Figure 7
INDOOR COIL THERMISTOR - RED
All Units
Connect to ICT on Control Board
Cross over tube
for 9,12 and 15k
or center tube for
7,000 BTU
Figure 8
17.The control board cover is now ready to be installed. The
ribbon for the touch pad will need to be connected to the
control board. Take caution not to bend or fold the
ribbon.
(See Figure 10 for ribbon connection).
Ensure that no wires are pinched or caught between the
cover and the panel and then reinstall the screws removed
in Step 5.
If a remote thermostat or any low voltage accessory is
being used connect the low voltage pin connector to low
voltage terminal strip.
If replacing a previous version board you will need to use
the 10 pin connector supplied with the board for low voltage
accessories. Wires supplied with this kit have terminal
ends on the wires. Insert the terminal end into the correctly
labeled slot, push in and it will lock in place. After loading
pin connector use the wire nuts supplied with the kit to wire
nut the new wires onto the existing wires supplied for low
voltage accessories. See Figure 9 on page 5.
18.Set the master switch to ON. Restore electrical power and
verify unit functionality.
19.Replace the front in reverse order as removed in Steps 2
and 3.

5
This service control until it has been configured
to control a heat pump or cooler. As long as the display shows
, the unit .
will not operate
will not operateEo
Follow the directions on Pages 6 and 7 to set feature codes C3
and “dd”.
For C3, select option H if the unit is a heat pump or
option C if the unit is a cooler with or without electric heat.
For HE* and 32* models, configuration code “dd” must be set to
correct cooling capacity: 7,000, 9,000, 12,000 15,000
or 17,000 btu’s.
Failure to set “C3” and “dd” configuration codes
correctly will cause the unit to not operate properly.
*CRITICAL STEP*
ORANGE
BLACK
RED
GREEN
WHITE
YELLOW
BLUE
GREEN w/YELLOW STRIPE
Remote Thermostat
*Only load wires needed for accessories attached to unit.
Figure 9

6
OD
FAN
LOW
OD
FAN
HIGH
LINE 1
ON
24VAC-TRANSFORMER
IN1 GL GH
B
RIBBON CONNECTOR
Left is ON
Position
R E V.
VALVE
BLUE GREENRED YELLOW
ORANGE
YELLOW
BLUE
RED
BLACK
ID
FAN
LOW
ID
FAN
HIGH
Heat Pump
models
ON LY.
Must not
be used on
PTC models.
Figure 10
INITIAL BOARD PROGRAMMING
Press and continue to hold down the plus (+) and minus
(-) keys at the same time. While holding the keys down,
push the OFF button two (2) times, within a two (2)
second time frame. The display will show two (2) dash
lines and a ashing dot ( - - . ).
Release the plus (+) and minus (-) keys and press the
HEAT button three (3) times. The display will alternate
between C3 and O.
Press the plus (+) or minus (-) key until the display reads H
(for models PTH*) or C(for models PTC*). Please check
the serial plate of the PTAC to make sure you select the
correct code. Once Hor Cis selected, press the OFF key
to exit the programming.
CONFIGURATION SETTINGS
The control can be congured to operate a wide range
of options. The options listed below with the * are the
factory default settings. If these are acceptable, then the
unit does not require any additional conguration and
is fully operable. To congure the unit, rst select the
conguration feature code setting and then an option code
to change from the factory default setting.
1. Press and continue to hold the up and down arrow keys
and quickly press the OFF key twice within a two (2)
second time frame. The display will show two (2) dash
lines and a ashing dot ( - - . ).
Release the plus (+) and minus (-) keys and press the
HEAT button one (1) time to get to the rst setting, .
To select a conguration feature code, press the HEAT
key until the desired conguration comes up. To scroll to a
previously viewed conguration codes press the COOL key.
Once you have scrolled to the correct feature, then to select
the option code for your desired conguration, press either
the up or down key to scroll through the options of the
selected feature code.
1. Press the OFF key. Conguration feature mode will also
exit if no keys are pressed for a period of two (2) minutes.

7
CONFIGURATION SETTINGS CHART
Configuration
Code
Configuration Feature Option Code Option
0 * Chassis Membrane *
L5 Wired Thermostat
rE Wireless Stat & 7-Button
L0 Locked Membrane
Au
do not use
On
do not use
bP Button present
bA* Revert to Cyclic
AAlways run fan (even if Off)
C
do not use
bC Revert to Continuous
CPTC (Standard Cooler)
H* PTH (Standard Heat Pump)
0Service No Operation "Eo"
dC DRY (Dehumidification Cooler)
dH
do not use
uC
do not use
uH
do not use
AC PMC (Cooler w/ Make-up Air)
AH PMH (Heat Pump w/ Make-up Air)
EC HEC (High Efficiency Cooler)
EH HEH (High Efficiency Heat Pump)
3C 32C (R-32 Cooler)
3H 32H (R-32 Heat Pump)
C4 Room I.D. Digit 1 & 2 00* - 99 00* - 99
C5 Room I.D. Digit 3 & 4 00* - 99 00* - 99
0* Off*
1On
18 18 Hour Automatic Entry
C8 Temp. Limiting Cool 60* - 80 60* - 80
C9 Temp. Limiting Heat 68 - 90, 80* 68 - 90, 80*
8* B*
0 O
c3 Un-rent Cooling Temp. 45 - 95, 79* 45 - 95, 79*
c4 Un-rent Heating Temp. 45 - 95, 63* 45 - 95, 63*
0* Not Twinned*
5Twinned
F* Fahrenheit Scale*
CCelsius Scale
L* On, Low Fan*
HOn, High Fan
0Off
d6 Sensorless Un-Occ. Time 1 - 32, 18* 1 - 32, 18*
d7 1st Un-Occ. Set Back Temp. 1 - 16, 2* 1 - 16, 2*
d8 1st Un-Occ. Set Back Time .1, .5*, 1 - 24 .1 ,.5 ,1 - 24, .5*
d9 2nd Un-Occ. Set Back Temp. 1 - 16, 3* 1 - 16, 3*
dA 2nd Un-Occ. Set Back Time .5, 1* - 24 (d8) - 24, 1*
db 3rd Un-Occ. Set Back Temp. 1 - 16, 6* 1 - 16, 6*
dC 3rd Un-Occ. Set Back Time
1 - 24, 3*
(dA) - 24, 3*
dd Cooling Capacity 5 - 24 5,000 - 24,000 BTU
dF Platform Group Code 00* - 99 00* - 99
dH Electric Heater Size
00*, 15, 20, 25, 35, 50
00*, 15, 20, 25, 35, & 50
dJ Operating Voltage 2, 3*, 4, 5 2, 3*, 4, 5
r4 Room Prefix 00* - 99 00* - 99
r5 Room Suffix 00* - 99 00* - 99
0* Dis-enabled*
78 - 99 78 - 99
C6
Wired Occupancy
C1
Interface
C2
ID Fan Operation
C3
Model Prefix
Cd
English / Metric Temp
CE
Freeze Protection
C0
T-stat B/ O Term.
CA
Wireless Twin Unit
u3
Heat Protection
*Indicates factory default
See manufacturer for additional conguration options.

8
Configuration
Code
Configuration Feature Option Code Option
0Off
1* On only when ID fan runs
2On when ID fan runs & room occupied
3Runs continuously
4On when room is occupied
EEconomizer
EP Economizer with compressor assist
0Off
1* May be on anytime
2Allowed on except in Off mode
3Allowed on when indoor fan runs
4Allowed on if room is occupied
5Allowed on if room is not occupied
6Allowed on when indoor humidity is high
0* Door Switch
1Motion Sensor
2Front Desk
3Wired Un-rented Set Back
4Emergency Hydronic
5Load Shedding
6Alarm Sensor
0* Door Switch
1Motion Sensor
2Front Desk
3Wired Un-rented Set Back
4Emergency Hydronic
5Load Shedding
6Alarm Sensor
0Not used
15-80, 25* % RH above which kit may run
0 Not used
15-60, 25* % RH above which kit may run
0No affect on indoor fan
1* Indoor fan forced to run with Kit
uL Config. Security Code 00* - 99 00* - 99
ub
Indoor Humidity Activation
un
Vent Dehumid Outdoor
Humidity Level
uu
Vent Dehumidification Kit
Fan Force
u9
Input Pins UN2 & COM
u8
Input Pins UN1 & COM
Smart Vent Operation
P0
Vent Dehumid Make-up Air
Kit Operation
P2
CONFIGURATION SETTINGS CHART (CONT.)

9
DIAGNOSTIC MAINTENANCE & STATUS REPORT
The Diagnostic Maintenance & Status Report provides detailed information on PTAC control operation and operational status including
present modes, failures, airow restriction warnings, operating temperatures, and past failures. The lower right hand dot on the center
display ashes in this mode. In some cases the green LED located in the lower left hand corner of the touchpad below the OFF key will
also be lit. This Green LED “Status Light“ only illuminates if there is an status code that has been activated and should be reviewed.
In most cases, this light indicates that the indoor room lter is dirty should be cleaned or replaced. Dirty lters cause the unit
to consume more energy than normally needed to condition a room. Once the lter has been cleaned or replaced, the LED should go
out. If the LED is still illuminated after the lter has been cleaned, activate the Diagnostic and Status mode to view any active codes.
The unit may need additional cleaning or maintenance of the evaporator or condenser coils. Please perform this step before calling a
servicer.
servicer should be called.
DIAGNOSTIC STATUS REPORT MODE.
To enter Diagnostic Status Report mode, press and hold the up and down arrows and, while holding, quickly press the COOL key
twice.
Active Failures.
• If there are no active failures or lockouts, the display will show a double dash, “- -”. If there is a code listed, see the unit “Diagnostic
Codes” chart for a list of denitions.
Operating Temperatures.
• If not in Diagnostic Status Report Mode, enter as instructed above and press the Fan Speed key.
• If already in Diagnostic Status Report mode, press the Fan Speed key. The display will show the temperature of the desired
set point, SP; the temperature at the wireless thermostat, rL; the indoor ambient temperature behind the lter, IA; the indoor coil
temperature, IC; the indoor discharge air temperature, Id; the outdoor coil temperature, OC; the outdoor ambient temperature, OA;
and the spare probe temperature, IH. If any of the probes are not populated the display will show the corresponding failure code.
Past Failure Log
• If not in Diagnostic Status Report Mode, enter as instructed above and press the Fan Speed key twice.
• If already in Diagnostic Status Report mode, press the Fan Speed key. While the display is showing operating temperatures,
the last 10 failure codes active or past can be requested by pressing the Fan Speed key again. The codes are displayed
last entry rst followed subsequently by each preceding code.
Note that modes F1 and Fd are also displayed in the normal control operation (see “Diagnostic Codes” chart).
To exit Diagnostic Status Report mode, press the OFF key.

10
STATUS DISPLAY
ERROR
LIGHT
SUGGESTED ACTION
FP
Freeze Protection Engaged. The room temperature
measured by the wireless remote thermostat or indoor
ambient thermistor active sensor falls below 40°F.
Y N
No Action required. This setting will disengage when the
room temperature rises above 43°F.
Fd Front Desk switch is closed. All outputs are switched off. YN
Open front desk switch to allow occupant unit operation.
Eo
Un-Configured Service Board -
All operation held awaiting configuration
Y Y
Enter Configuration Menu and set "C3" to "C" for coolers
with electric heat or "H" for heat pumps.
EH
Emergency Hydronic Engaged. The EHH switch is closed.
Compressor is switched off.
Y N
Open front emergency hydronic switch to allow occupant
unit operation.
LS
Load Shedding Engaged. The LS switch is closed.
Compressor and Electric heat is switched off.
Y N
Open load shedding switch to allow occupant unit operation.
On Control is configured to respond to a wired thermostat Y N
No action if a wired thermostat is being used.
Otherwise, see Configuration Settings.
oP
Open Door Lockout
(DS1 & DS2 open; wireless) Y Y
Close Room Door.
Unit will not condition space with door open.
nP
Window Switch Lockout -
(LS & INN open) Y Y
Close Room Door or Window.
Unit will not condition space with door or window open.
HP
Heat Sentinel -
(WIAT > u3) YN
No action required. This setting will disengage when the
room temperature falls.
UR
Un-Rented Status
(EHH & INN or wireless) Y N Front Desk needs to set to Rented mode (if applicable).
Indoor Ambient Thermistor reads outside the
range -20°F to 200°F & the wireless thermostat is not
communicating to the unit control or
Indoor Ambient Thermistor (IAT) without a wireless remote
thermostat reads outside the range -20°F to 200°F.
F2 Wireless Remote Thermostat failure N N
Replace Wireless Thermostat.
F3
Indoor Ambient Thermistor reads
outside the range -20°F to 200°F
Y N
Replace black Indoor Ambient Thermistor.
F4
Indoor Coil Thermistor either above
or below operating tolerances.
N Y
Replace Red Indoor Coil Thermistor.
F5 Wireless Thermostat failure. N Y
Attempt to rebind Wireless Thermostat or Replace Wireless
Thermostat.
F6
Indoor Discharge Thermistor either above
or below operating tolerances.
N Y
Replace Yellow Indoor Discharge Thermistor.
Fb Low Remote Battery Warning. N Y
Replace Batteries in Wireless Devices.
H1
High Voltage Protection engaged.
Power supply voltage is to high.
Y N
Check for incoming power at correct voltage.
br
Brown Out Protection engaged.
Power was lost or voltage is low.
N N
Check for incoming power at correct voltage.
L6 Discharge Air Too Hot. N Y
Clean Filter or Remove Air Blockage.
LC Outdoor Coil Thermistor temperature high. N Y
Clean Condenser Coils, Check Fan for fault. Code will reset
after cleaning.
C2
Indoor Air Recirculation. Large delta between thermostat
and
return.
N Y
Clean Filter or Remove Air Blockage or Close
Vent Door or Improve indoor to outdoor seal.
C5
Outdoor Coil temperature too high for outdoor ambient
temperature.
N Y
Check for Blocked Outdoor Air or Clean Coil.
C1 Indoor Coil is freezing up. N Y
Clean filter, Check for fan and blower operation,
Check for Refrigerant loss or Restricted capillary tube.
C3 Indoor Coil is freezing up. N Y
Clean filter, Check for fan and blower operation,
Check for Refrigerant loss or Restricted capillary tube.
C4 Indoor Coil froze up. N Y
Clean filter, Check for fan and blower operation,
Check for Refrigerant loss or Restricted capillary tube.
C6 Poor Unit Performance. N Y
Check for blower motor, compressor, or electric heat
operation.
C7 Indoor Freezing Lockout (ICT - IAT > 20) +10 Min N Y
Clean filter, Check for fan and blower operation,
Check for Refrigerant loss or Restricted capillary tube.
MODES
MODES
Y
Y
Replace black Indoor Ambient Thermistor or Wireless
Remote Thermostat.
F1
CODE
MODES
MODES
DIAGNOSTIC CODES

11
HIGH VOLTAGE!
DISCONNECT ALL POWER BEFORE SERVICING OR INSTALLING THIS
UNIT. MULTIPLE POWER SOURCES MAY BE PRESENT. FAILURE TO
DO SO MAY CAUSE PROPERTY DAMAGE, PERSONAL INJURY OR DEATH.
WIRING DIAGRAMS
TO
UNIT
MUST
BE
PROPERLY
POLARIZED
(FOR
5V)
AND
GROUNDED.
R
TO:
G,
W2
COOL
UNIT
G,
Y/W1
4
ON
UNITS
WITH
FRONT
DESK
CONTROL
SWITCH.
R
TO:
G,
W2
-----
2ND
STAGE
G,
Y/W1
G
CURRENT:
.1
FUNCTION
1ST
STAGE
NOTES:
1ST
STAGE
HEAT
HEAT
THERMOSTAT
USED
HEAT
POWER
CORD
TO
LINE
2.
CURRENT:
.1
OFF
NOTES:
W/ELECTRIC
HEAT
5
BK18
ON
LINE
2
WITH
FUSE
SHOWN
CONNECTED
FOR
265V.
FOR
230V
&
1
15V,
CONNECT
4
ON
UNITS
WITH
FRONT
DESK
CONTROL
SWITCH.
2ND
STAGE
ON
A
STRAIGHT
1ST
STAGE
FUNCTION
CURRENT:
.1
ANTICIPATOR
3
ON
HEAT
PUMP
MODELS
ONLY.
OFF
2ND
STAGE
G,B,Y/W1
HEAT
1
WARNING:
DISCONNECT
POWER
BEFORE
SERVICING.
WIRING
-----
HEAT
PUMP
W/AUXILIARY
REMOTE
THERMOSTAT
OPERATION
TO
UNIT
MUST
BE
PROPERLY
POLARIZED
(FOR
265)
AND
GROUNDED.
6
FOR
REMOTE
OPERATION,
SEE
CONFIGURATION
CHART.
ANTICIPATOR
FUNCTION
1
ARNING:
DISCONNECT
POWER
BEFORE
SERVICING.
WIRING
*
ELECTRIC
HEAT
2
RIBBED
WIRE
MUST
BE
CONNECTED
AS
SHOWN
COOLING
UNIT
G,
Y/W1
ELECTRIC
HEAT
G
3
ON
HEAT
PUMP
MODELS
ONLY.
FAN
ANTICIPATOR
G,B,Y/W1
CURRENT:
.1
COOLING
UNIT
FUNCTION
-----
*
FOR
A
HEAT
PUMP
OFF
2
RIBBED
WIRE
MUST
BE
CONNECTED
AS
SHOWN
-----
ANTICIPATOR
R
TO:
HEAT
PUMP
W/AUXILIARY
REMOTE
THERMOSTAT
OPERATION
FAN
W/ELECTRIC
HEAT
R
TO:
2ND
STAGE
1ST
STAGE
G,
Y/W1
HEAT
OFF
23
265
COM
TRANSFORMER
LOAD
R
BK18
YL10
ELECTRIC
GY22
C
H
HEATER
1
2
F
19
WIRE
RD13
S
C
G
N
RIBBED
CAP
OD
FAN/COMP
5
20
FUSE
BK37 BK37
GY21
RD33
7 IF SUPPLY VOLTAGE IS 208V/230V USE THE 230V TAP ON TRAN SFORMER.
IF SUPPLY VOLTA GE IS 265V USE THE 265V TAP ON TR ANSFORMER.
115V TRANSFORMER NOT SHOWN.
7
HEATER 2
E2 E6 E7
LI NE 2 COMPRESSOR
E E2
ON / OF F
MASTER SWI T CH
SW2
P2
P5
X3
X2
M2
P
P
P8P9
IDT
YELLOWGREEN
OCT
BLUE
ICT
RED
2VAC~TRANSFORMER
2VA CLASS 2 ONLY
ORANGE
VT12
BR34 BR34
(FACTORYORFIELD)
(FACTORY)
HIGHVOLTAGE
LOWVOLTAGE
LOWVOLTAGE
HIGHVOLTAGE
(FACTORYORFIELD)
(FACTORY)
WIRELEGEND
WIRELEGEND
HIGHVOLTAGE
HIGHVOLTAGE
(FACTORYORFIELD)
(FACTORYORFIELD)
GN
1
GN
1
CHASSIS
CHASSIS
CONDUCTORSONLY
USECOPPER
PANEL
PANEL
CONTROL
CONTROL
CONNEC
CONNECT
COOL
COOL
COMP
SOLENOID
VALVE3
REV
COOL
COOL
CONNEC
CONNECT
FOR CONTINUOUS FAN OPERATION SEE CONFIGURATION CHART.
8
IN1 COM I N2
AUXILIARY
CR GL W2 Y/W1 B GH
REM OTE THERMOSTAT
IAT
BL AC K
IN1 C OM IN2
AUXILIARY
CR GL W2 Y/W1 B GH
REM OTE THERMOSTAT
IAT
BL AC K
BR14
RD17
BK16
WH15
MOTOR
FAN

12
WIRING DIAGRAMS
BK37
BK37
GY22
GY21
LINE
265
230
RD33
VT12
5
BK18
1
HEATER
ELECTRIC
2
GN
WIRE
RIBBED
HC
YL10
RD13
S
C
R
8
HEATER 2
E2 E6
LI N E 2 COMP RE SSOR
E E2
ON / OFF
MA ST E R SW I T CH
SW2
X3
2VAC~TRANSFORMER
2VA CLASS 2 ONLY
P
PP8P9
IDT
YELLOWG
REEN
OCT
BLUE
IC
T
RED ORANGE
BR34
BR34
COM
(PV)
BU2
(PV)
BU15
(PV)
RD14
B
3
6
9
8
5
2
A
7
4
1
(PV)
BK17
6
(PV)
BU4
(PV)
WH7
(PV)
BK11
(PV)
BU9
(PV)
BU10
(PV)
BK12
(PV)
WH8
1
2
3
SWITCH
ON/OFF
MOOR
T
LINE
COM
208
240
FAN
MUFFIN
20
P
CAP
FAN/COM
OD
BR14
19
F
P2
P5
E7
X2
POWER
T
VEN
VENT
POWER
3
SOLENOID
VALVE
REV
RD17
BK16
B
TE
LOCK
RMINAL
COMP
1ST
STAGE
ANTICIPATOR
CURRENT:
.1
2ND
STAGE
ANTICIPATOR
CURRENT:
.1
1ST
S
TAGE
ANTICIPATOR
REMOTE
THERMOSTAT
OPERATION
R
TO:
-----
G,Y/W1
G,B,Y/W1
G,W2
FUNCTION
OFF
1STSTAGE
HEAT
2NDSTAGE
HEAT
R
TO:
G,Y/W1
FUNCTION
OFF-----
HEAT
G**
FAN
G**
FAN
*
*
FOR
A
HEAT
PUMP
THERMOSTATUSED
ONASTRAIGHT
COOLUNIT
**GL-lowspeed
GH-highspeed
W/ELECTRIC
HEAT
COOLING
UNIT
ELECTRIC
HEAT
HEAT
PUMP
W/AUXILIAR
Y
CONNECT
COOL
COOL
CONNECTCONNECT
IN1 COM I N2
AUXILIARY
C R GL W2 Y/W1 B GH
REM OTE THERMOSTAT
IAT
BL AC K
IN1 COM I N2
AUXILIARY
C R GL W2 Y/W1 B GH
REM OTE THERMOSTAT
IAT
BL AC K
MOTOR
FAN
WH15
M2
(FACTORYORFIELD)
(FACTORY)
HIGHVOLTAGE
LOWVOLTAGE
LOWVOLTAGE
HIGHVOLTAGE
(FACTORYORFIELD)
(FACTORY)
WIRELEGEND
WIRELEGEND
HIGHVOLTAGE
HIGHVOLTAGE
(FACTORYORFIELD)
(FACTORYORFIELD)
GN
1
GN
1
CHASSIS
CHASS
IS
CONDUCTORSONLY
USECOPPER
PANEL
PANEL
CONTROL
CONTROL
2
RIBBED
WIRE
MUST
BE
CONNECTED
AS
SHOWN.
NOTES
1
WARNING:
DISCONNECT
POWER
BEFORE
SERVICING.
WIRING
TO
UNIT
MUST
BE
PROPERLY
POLARIZED
(FOR
265V)
AND
GROUNDED.
3
ON
HEAT
PUMP
MODELS
ONLY.
4
ON
UNITS
WITH
FRONT
DESK
CONTROL
SWITCH.
2
RIBBED
WIRE
MUST
BE
CONNECTED
AS
SHOWN.
NOTES:
1
WARNING:
DISCONNECT
POWER
BEFORE
SERVICIN
G.
WIRING
TO
UNIT
MUST
BE
PROPERLY
POLARIZED
(FOR
265V)
AND
GROUNDED.
3
ON
HEAT
PUMP
MODELS
ONLY.
4
ON
UNITS
WITH
FRONT
DESK
CONTROL
SWITCH.
5
BK18
ON
LINE
2
WITH
FUSE
SHOWN
CONNECTED
FOR
265V.
FOR
230V
AND
115V,
CONNECT
POWER
CORD
TO
LINE
2.
7
FOR
REMOTE
OPERATION,
SEE
CONFIGARATION
CHART.
6
IF
SUPPLY
VOLTAGE
IS
208V
MOVE
240V
LEAD
TO
208V
TAP
ON
TRANSFORMER.
265V
AND
115V
TRANSFORMER
NOT
SHOWN.
9
8
IF
SUPPLY
VOLTAGE
IS
208V/230V
USE
THE
230V
TAP
ON
TRANSFORMER.
IF
SUPPLY
VOLTAGE
IS
265V
USE
THE
265V
TAP
ON
TRANSFORMER.
1
15V
TRANSFORMER
NOT
SHOWN.
FOR CONTINUOUS FAN OPERATION SEE CONFIGURATION CHART.
HIGH VOLTAGE!
DISCONNECT ALL POWER BEFORE SERVICING OR INSTALLING THIS
UNIT. MULTIPLE POWER SOURCES MAY BE PRESENT. FAILURE TO
DO SO MAY CAUSE PROPERTY DAMAGE, PERSONAL INJURY OR DEATH.

13
R
C
S
RD13
YL10
F
C
H
BR34
BR34
RD33
RIBBED
WIRE
G
N
2
19
REV
VALVE
SOLENOID
3
BR14
WH15
COMP
OD
FAN/COMP
CAP
1ST
STAGE
ANTICIPATOR
CURRENT:
.1
2ND
STAGE
ANTICIPATOR
CURRENT:
.1
ELECTRIC
HEATER
20
1
3
5
A
2
4
6
B
1
VT12
240
208
COM
LINE
OR8
(CP)
6
YL1
(CP)
YL5
(CP)
YL3
(CP)
BK16RD17
WH6
(CP)
HEAT
PUMP
W/AUXILIARY
ELECTRIC
HEAT
R
TO:
-----
G,
Y/W1
G,B,Y/W1
G,W2
FUNCTION
OFF
COOL
1STSTAGE
HEAT
2NDSTAGE
HEAT
COOLING
UNIT
W/ELECTRIC
HEAT
CONNECT
R
TO:
G,
Y/W1
FUNCTION
OFF-----
REMOTE
THERMOSTAT
OPERATION
HEAT
G
FAN
G
FAN
*
*
FOR
A
HEAT
PUMP
THERMOSTAT
USED
ON
A
STRAIGHT
COOL
UNIT
1ST
STAGE
ANTICIPATOR
CURRENT:
.1
2ND
STAGE
ANTICIPATOR
CURRENT:
.1
240
208
COM
LINE
8
GY21
GY22
BK37
HE ATER 2
E2 E6 E7
LI N E 2 COMP RESSOR
E E2
ON / OFF
MA STER SWI T CH
SW2
X3
X2
M2
2VAC~TRANSFORMER
2VA CLASS 2 ONLY
P2
P5
BK18
5
BK37
CONNECTCONNECT
COOL
2
RIBBED
WIRE
MUST
BE
CONNECTED
AS
SHOWN.
NOTES
1
WARNING:
DISCONNECT
POWER
BEFORE
SERVICING.
WIRING
TO
UNIT
MUST
BE
PROPERLY
POLARIZED
(FOR
265V)
AND
GROUNDED.
3
ON
HEAT
PUMP
MODELS
ONLY.
4
ON
UNITS
WITH
FRONT
DESK
CONTROL
SWITCH.
2
RIBBED
WIRE
MUST
BE
CONNECTED
AS
SHOWN.
NOTES
1
WARNING:
DISCONNECT
POWER
BEFORE
SERVICING.
WIRING
TO
UNIT
MUST
BE
PROPERLY
POLARIZED
(FOR
265V)
AND
GROUNDED.
3
ON
HEAT
PUMP
MODELS
ONLY.
4
ON
UNITS
WITH
FRONT
DESK
CONTROL
SWITCH.
5
BK18
ON
LINE
2
WITH
FUSE
SHOWN
CONNECTED
FOR
265V.
FOR
230V
AND
115V,
CONNECT
POWER
CORD
TO
LINE
2.
6
IF
SUPPLY
VOLTAGE
IS
208V
MOVE
240V
LEAD
TO
208V
TAP
ON
TRANSFORMER.
265V
AND
115V
TRANSFORMER
NOT
SHOWN.
7
FOR
REMOTE
OPERATION,
SEE
CONFIGURATION
CHART.
8
IF
SUPPLY
VOLTAGE
IS
208V,
MOVE
204V
LEAD
TO
208V
TAP
ON
TRANSFORMER.
265V
AND
115V
TRANSFORMER
NOT
SHOWN.
9
FOR CONTINUOUS FAN OPERATION SEE CONFIGURATION CHART.
IN1 COM IN 2
AUX IL IA RY
C R GL W2 Y /W1 B GH
REMO TE THER MOST AT
I AT
BLACK
IN1 COM IN 2
AUX IL IA RY
C R GL W2 Y /W1 B GH
REMO TE THER MOST AT
I AT
BLACK
F
AN
MOTOR
(FACTORYORFIELD)
(FACTORY)
HIGHVOLTAGE
LOWVOLTAGE
LOWVOLTAGE
HIGHVOLTAGE
(FACTORYORFIELD)
(FACTORY)
WIRELEGEND
WIRELEGEND
HIGHVOLTAGE
HIGHVOLTAGE
(FACTORYORFIELD)
(FACTORYORFIELD)
GN
1
GN
1
CHASSIS
CHASSIS
CONDUCTORSONLY
USECOPPER
PANEL
PANEL
CONTROL
CONTROL
HIGH VOLTAGE!
DISCONNECT ALL POWER BEFORE SERVICING OR INSTALLING THIS
UNIT. MULTIPLE POWER SOURCES MAY BE PRESENT. FAILURE TO
DO SO MAY CAUSE PROPERTY DAMAGE, PERSONAL INJURY OR DEATH.
WIRING DIAGRAMS

14
WIRING DIAGRAMS
* FOR A HEAT PUMP THERMOSTAT USED
ON A STRAIGHT COOL UNIT.
** GL - LOW SPEED
GH - HIGH SPEED
CM
COMP
DB
EM
FC
F
HPS
HTR
MC
RCCF
RVC
TR
TB
VSM
VSTM
R
OUTDOOR FAN MOTOR
COMPRESSOR
DAUGHTER BOARD
EVAPORATOR MOTOR
FAN CAPACITOR
FUSE
HIGH PRESSURE SWITCH
HEATER ELEMENT
MAIN CONTROL
RELAY
RUN CAPACITOR
FOR COMPRESSOR AND FAN
REVERSING VALVE
TRANSFORMER
TERMINAL BLOCK
VARIABLE SPEED MOTOR
VARIABLE SPEED
TERMINAL BOARD
R
Y L
GY
BU
BR
RD
GY
TR 1
To MC
BU
RD
PK
ALTERNATE
HYDRONIC
HEAT
HEATER 1 HEATER 2
DANGER HIGH
MC
L1
WH
ALTERNATE
OUTDOOR
MOTOR
WIRING
COM
GND
INPUT
AC
TO MOTOR
VSTM OD
R485S
VSM
CM
FAN
MOTOR
1650 1500 1350 1170
MC
OD
FAN
LOW
HIGH
L1
L2
10 10
ALTERNATE
INDOOR
MOTOR
WIRING
COM
GND
INPUT
AC
TO MOTOR
VSTM ID
R485S
VSM
EM
EVAP
MOTOR
1400 1250 1200 1000
L1
MC
LOW
HIGH
ID
FAN
L2
1111
REV
VALVE
LOW
OPTIONAL
POWER
VENT/DOOR
TR 2
L1
WHOR
1
2
3
ON/OFF
SWITCH
S
L2
DB
14
OPTIONAL
CONDENSATE
PUMP
TR3
TR1
To MC
L2
L1
BU
RD
OR
GY
WH
8
S
BU
DB
120
PK
PK
COM
NO C
BK
DANGER HIGH VOLTAGE
24VAC TRANSFORMER
12VA CLASS 2 ONLY
ON OFF
MASTER SWITCH
HEATER 1 HEATER 2
LINE 1
IN1 COM IN2
A
UXILIARY
C R GL W2 Y/W1 B GH
REMOT E THERMO STAT
IAT
BLACK
ICT
RED
OCT
BLUE
IHD
ORANGE
OAT
GREEN
IDT
YELLOW
REV.
VALVE
FAN
HIGH LOW
OD
FAN
HIGH LOW
LINE 2 COMPRESSOR
L2
L1
MC
9
BK
BK
7
OR
RD
TB
EM
FAN
MOTOR
CM
FAN
MOTOR
TR 1
265
230
S
ID
OR
13
BK
DANGER HIGH VOLTAGE
24VAC TRANSFORMER
12VA CLASS 2 ONLY
ON OFF
MASTER SWITCH
HEATER 1 HEATER 2
LINE 1
IN1 COM IN2
A
UXILIARY
C R GL W2 Y/W1 B GH
REMOT E THERMO STAT
IAT
BLACK
ICT
RED
OCT
BLUE
IHD
ORANGE
OAT
GREEN
IDT
YELLOW
REV.
VALVE
FAN
HIGH LOW
OD
FAN
HIGH LOW
LINE 2 COMPRESSOR
L2
L1
MC
9
BK
BK
7
OR
RD
TB
EM
FAN
MOTOR
CM
FAN
MOTOR
TR 1
265
230
S
ID
OR
13
13
14
10
11
7
8
9
12
15!
HIGH VOLTAGE!
DISCONNECT ALL POWER BEFORE SERVICING OR INSTALLING THIS
UNIT. MULTIPLE POWER SOURCES MAY BE PRESENT. FAILURE TO
DO SO MAY CAUSE PROPERTY DAMAGE, PERSONAL INJURY OR DEATH.
Wiring is subject to change.

15
Model Starts With
High S peed
VSTM Tap
(Black Wire)
Low Speed
VSTM Tap
(Red Wire)
PTH07*G (00 to 35) 1350 1170
PMH07*G (00 to 35) 1650 1450
PMC07*G (00 to 35) 1350 1170
PMC09*G (00 to 35) 1350 1170
PMC12*G (00 to 35) 1500 1350
PMH074/PTH073H/PTH074H (00 to 35) 1650 1500
PMH094/PTH093H/PTH094H (00 to 35) 1650 1500
PMH124/PTH123H/PTH124H (00 to 35) 1350 1170
PTH153H/PTH154H (00 to 35) 1350 1170
PMC154/PMH153G/PMH154G (00 to 35) 1350 1170
PTC072G/PTC092G (00 to 35) 1650 1500
Indoor Motor Speed Selection
1
2
3
ON/OFF
SWITCH
S
DB
R
TR1
R
TR4
DB
L1
OPTION AL
AIR
DEHUMIDIFICATION
KIT
6
14
14
>
>
>>
L2
OPTIONAL ELECTRIC HEATER
OPTIONAL
TRANSFER
FAN
R
6
8
7
2
4
3
10
TR1
To M C
DB
14
S
>
>
>
>
YL
RD
BL
OPTIONAL
LIGHTING
CONTROL
TR1
To M C
7
AB
BL
DB
14
S
>>
>
>
2
5
RD
R
Model Starts With
High Speed
VSTM Tap
(Black Wire)
Low Speed
VSTM Tap
(Red Wire)
DRY093/DRY094 1350 1170
PTC173 1650 1450
HEC073/PTH073/PTH074 1350 1170
PMH094/HEC093/PTH093/PTH094 1350 1170
HEC123/PTH123/PTH124 1500 1350
PTH153/PTH154 1650 1500
PMH153/PMH154 1650 1500
PTC073/PTC074 1350 1170
PTC093/PTC094 1350 1170
PTC123/PTC124 1350 1170
PTC153/PTC154 1650 1500
Outdoor Motor Speed Selection
DIP SWITCH
12345
ON
•••••
OFF
•••••
Daug hter Board Device Address S witch 1 Switch 2 Switch 3 Switch 4 Switch 5
Smart Vent/Door operations for Power Door/Vent, Economizer and
Economizer(+) Board
17 00001
Tra n s fe r Fa n 20 00100
Condensate Pump 21 00101
Lighting Control 24 01000
DigiAIR™ Compressor 25 01001
DigiAIR™Heater 26 01010
DigiAIR™Fan 28 01100
11
10
14
WIRING DIAGRAMS
HIGH VOLTAGE!
DISCONNECT ALL POWER BEFORE SERVICING OR INSTALLING THIS
UNIT. MULTIPLE POWER SOURCES MAY BE PRESENT. FAILURE TO
DO SO MAY CAUSE PROPERTY DAMAGE, PERSONAL INJURY OR DEATH.

16
HIGH VOLTAGE!
DISCONNECT ALL POWER BEFORE SERVICING OR INSTALLING THIS
UNIT. MULTIPLE POWER SOURCES MAY BE PRESENT. FAILURE TO
DO SO MAY CAUSE PROPERTY DAMAGE, PERSONAL INJURY OR DEATH.
WIRING DIAGRAMS
24VAC TRANSFORMER
12VA CLASS 2 ONLY
ON OFF
MASTER SWITCH
IN1 COM IN2
AUXILIARY
CRGL W2 Y/W1 B GH
REMOTE THERMOSTAT
IAT
BLACK
ICT
RED
OCT
BLUE
IHD
ORANGE
OAT
GREEN
IDT
YELLOW
REV.
VALVE
ID
FAN
HIGH LOW
OD
FAN
HIGH LOW
LINE 2COMPRESSOR
HEATER 1 HEATER 2
LINE 1
DANGER HIGH VOLTAGE
DUAL MOTOR, 2 SPEED RELAY
RVC
COMP
S
C
R
EM
FAN
MOTOR
YL
RD
BK
BK
TR
6
RD
GY
HTR
F4
WH
GN
WHITE
WIRE
2
1
FC
BR
BR
RD
BK
WH WH
BK
CM OUTDOOR FAN MOTOR
COMP COMPRESSOR
EM EVAPORATOR MOTOR
FC FAN CAPACITOR
F FUSE
HPS HIGH PRESSURE SWITCH
HTR HEATER ELEMENT
RCCF RUN CAPACITOR
FOR COMPRESSOR, ANY FAN
RVC REVERSING VALVE
TR TRANSFORMER
HPS
REMOTE THERMOSTAT
OPERATION
COOLING UNIT
W/ ELECTRIC HEAT
FUNCTION CONNECT
R TO:
OFF -----------
FAN G **
COOLG, Y / W1
HEAT
G, W2
OR
G, B, Y / W1*
HEAT PUMP W / AUXILIARY
ELECTRIC HEAT
FUNCTION CONNECT
RTO:
OFF -----------
FAN G **
COOLG, Y / W1
1ST STAGE
HEATG, B, Y / W1
2ND STAGE
HEATG, W2
USE COPPER
CONDUCTORS ONLY
CHASSIS GN1 CONTROL PANEL
WIRE LEGEND
HIGH VOLTAGE
(FACTORY)
HIGH VOLTAGE
(FACTORY OR FIELD
LOW VOLTAGE
(FACTORY OR FIELD)
VT
* FOR A HEAT PUMP,
THERMOSTAT USED
ON A STRAIGHT
COOL UNIT
** GL - LOW SPEED
GH - HIGH SPEED
5
1
2
3
4
5
6
LOAD
COM
265
230
H
RCCF
F
C
WH
BR
WARNING: DISCONNECT POWER BEFORE SERVICING.
WIRING TO UNIT MUST BE PROPERLY POLARIZED
(FOR 265V) AND GROUNDED.
WHITE WIRE MUST BE CONNECTED AS SHOWN.
ON HEAT PUMP MODELS ONLY
BK ON LINE 2 WITH FUSE SHOWN CONNECTED FOR 265V
FOR 230 V &115 V, CONNECTED POWER CORD TO LINE 2
FOR REMOTE OPERATION, SEE CONFIGURATION CHART.
IF SUPPLY VOLTAGE IS 208V / 230V, USE THE 230V TAP
ON TRANSFORMER.
IF SUPPLY VOLTAGE IS 265V, USE THE 265V TAP
ON TRANSFORMER.
115V TRANSFORMER NOT SHOWN.
WIRE CODE
BR BROWN
BK BLACK
GN GREEN
GY GRAY
RD RED
VT VIOLET
WH WHITE
YL YELLOW
RD
3
NOTES:
7 BOARD SHOWS R AND C, PLEASE IGNORE.
7
7
UI CONNECTION
BK
RD
CM
FAN
MOTOR

17
24VAC TRANSFORMER
12VA CLASS 2 ONLY
ON OFF
MASTER SWITCH
IN1 COM IN2
AUXILIARY
CRGL W2 Y/W1 B GH
REMOTE THERMOSTAT
IAT
BLACK
ICT
RED
OCT
BLUE
IHD
ORANGE
OAT
GREEN
IDT
YELLOW
REV.
VALVE
ID
FAN
HIGH LOW
OD
FAN
HIGH LOW
LINE 2COMPRESSOR
HEATER 1 HEATER 2
LINE 1
DANGER HIGH VOLTAGE
DUAL MOTOR, NO SPEED RELAY SINGLE SPEED CONDENSER FAN
RVC
COMP
S
C
R
EM
FAN
MOTOR
BK
YL
RD
BK
BK
TR
6
RD
GY
HTR
F4
WH
GN
WHITE
WIRE
2
1
FC
BR
BR
RD
BK
WH WH
BK
CM OUTDOOR FAN MOTOR
COMP COMPRESSOR
EM EVAPORATOR MOTOR
FC FAN CAPACITOR
FFUSE
HPS HIGH PRESSURE SWITCH
HTR HEATER ELEMENT
RCCFRUN CAPACITOR
FOR COMPRESSOR, ANY FAN
RVC REVERSING VALVE
TR TRANSFORMER
HPS
USE COPPER
CONDUCTORS ONLY
WIRE LEGEND
HIGH VOLTAGE
(FACTORY)
HIGH VOLTAGE
(FACTORY OR FIELD
LOW VOLTAGE
(FACTORY OR FIELD)
VT
* FOR A HEAT PUMP,
THERMOSTAT USED
ON A STRAIGHT
COOL UNIT
** GL - LOW SPEED
GH - HIGH SPEED
5
1
2
3
4
5
6
LOAD
COM
265
230
H
RCCF
F
C
CM
FAN
MOTOR
WH
BR
WARNING: DISCONNECT POWER BEFORE SERVICING.
WIRING TO UNIT MUST BE PROPERLY POLARIZED
(FOR 265V) AND GROUNDED.
WHITE WIRE MUST BE CONNECTED AS SHOWN.
ON HEAT PUMP MODELS ONLY
BK ON LINE 2 WITH FUSE SHOWN CONNECTED FOR 265V
FOR 230 V &115 V, CONNECTED POWER CORD TO LINE 2
FOR REMOTE OPERATION, SEE CONFIGURATION CHART.
IF SUPPLY VOLTAGE IS 208V/230V, USE THE 230V TAP
ON TRANSFORMER.
IF SUPPLY VOLTAGE IS 265V, USE THE 265V TAP
ON TRANSFORMER.
115V TRANSFORMER NOT SHOWN.
WIRE CODE
BR BROWN
BK BLACK
GN GREEN
GY GRAY
RD RED
VT VIOLET
WH WHITE
YL YELLOW
RD
3
CHASSIS GN1 CONTROL PANEL
REMOTE THERMOSTAT
OPERATION
COOLING UNIT
W/ ELECTRIC HEAT
FUNCTION CONNECT
R TO:
OFF -----------
FAN G **
COOLG, Y / W1
HEAT
G, W2
OR
G, B, Y / W1*
HEAT PUMP W / AUXILIARY
ELECTRIC HEAT
FUNCTION CONNECT
RTO:
OFF -----------
FAN G **
COOLG, Y / W1
1ST STAGE
HEATG, B, Y / W1
2ND STAGE
HEATG, W2
UI CONNECTION
7
7
7BOARD SHOWS R AND C, PLEASE IGNORE.
NOTES:
HIGH VOLTAGE!
DISCONNECT ALL POWER BEFORE SERVICING OR INSTALLING THIS
UNIT. MULTIPLE POWER SOURCES MAY BE PRESENT. FAILURE TO
DO SO MAY CAUSE PROPERTY DAMAGE, PERSONAL INJURY OR DEATH.
WIRING DIAGRAMS

18
HIGH VOLTAGE!
DISCONNECT ALL POWER BEFORE SERVICING OR INSTALLING THIS
UNIT. MULTIPLE POWER SOURCES MAY BE PRESENT. FAILURE TO
DO SO MAY CAUSE PROPERTY DAMAGE, PERSONAL INJURY OR DEATH.
WIRING DIAGRAMS
24VAC TRANSFORMER
12VA CLASS 2 ONLY
ON OFF
MASTER SWITCH
IN1 COM IN2
AUXILIARY
CRGL W2 Y/W1 B GH
REMOTE THERMOSTAT
IAT
BLACK
ICT
RED
OCT
BLUE
IHD
ORANGE
OAT
GREEN
IDT
YELLOW
REV.
VALVE
ID
FAN
HIGH LOW
OD
FAN
HIGH LOW
LINE 2COMPRESSOR
HEATER 1 HEATER 2
LINE 1
DANGER HIGH VOLTAGE
DUAL MOTOR, DC OD MOTOR
RVC
COMP
S
C
R
YL
RD
BK
BK
TR
6
RD
GY
HTR
F4
WH
GN
WHITE
WIRE
2
1
RD
BK
WH WH
BK
3
HPS
* FOR A HEAT PUMP,
THERMOSTAT USED
ON A STRAIGHT
COOL UNIT
** GL - LOW SPEED
GH - HIGH SPEED
5
1
2
3
4
5
6
LOAD
COM
265
230
H
RCCF
C
WARNING: DISCONNECT POWER BEFORE SERVICING.
WIRING TO UNIT MUST BE PROPERLY POLARIZED
(FOR 265V) AND GROUNDED.
WHITE WIRE MUST BE CONNECTED AS SHOWN.
ON HEAT PUMP MODELS ONLY
BK ON LINE 2 WITH FUSE SHOWN CONNECTED FOR 265V
FOR 230 V &115 V, CONNECTED POWER CORD TO LINE 2
FOR REMOTE OPERATION, SEE CONFIGURATION CHART.
IF SUPPLY VOLTAGE IS 208V / 230V, USE THE 230V TAP
ON TRANSFORMER.
IF SUPPLY VOLTAGE IS 265V, USE THE 265V TAP
ON TRANSFORMER.
115V TRANSFORMER NOT SHOWN.
RD
COM
1650 1500 1350 1170
7 7
230 / 265
BK
GND TO MOTOR
VSTM ID
RS485
OUTDOOR MOTOR SPEED SELECTION
MODEL STARTS WITH HIGH SPEED
VSTM BLACK
LOW SPEED
VSTM RED
PTH073G (00 TO 35)1350 1170
DRY093G (00 TO 35) 1350 1170
DRY094G(00 TO 35) 1350 1170
PTC173G(00 TO 35) 1500 1350
CM OUTDOOR FAN MOTOR
COMP COMPRESSOR
EM EVAPORATOR MOTOR
FC FAN CAPACITOR
F FUSE
HPS HIGH PRESSURE SWITCH
HTR HEATER ELEMENT
RCCF RUN CAPACITOR
FOR COMPRESSOR, ANY FAN
RVC REVERSING VALVE
TR TRANSFORMER
VSM VARIABLE SPEED MOTOR
VSTM VATIABLE SPEED TERMINAL BOARD
USE COPPER
CONDUCTORS ONLY
CHASSIS GN1 CONTROL PANEL
WIRE LEGEND
HIGH VOLTAGE
(FACTORY)
HIGH VOLTAGE
(FACTORY OR FIELD
LOW VOLTAGE
(FACTORY OR FIELD)
HIGH VOLTAGE
DC HARNESS
(FACTORY)
7SEE TABLE FOR MOTOR SPEED SELECTION
GN
VT
EM
FAN
MOTOR
FC
BR
BR
VSM
CM
FAN
MOTOR
BK
RD
BK
RD
WH
REMOTE THERMOSTAT
OPERATION
COOLING UNIT
W/ ELECTRIC HEAT
FUNCTION CONNECT
R TO:
OFF -----------
FAN G **
COOLG, Y / W1
HEAT
G, W2
OR
G, B, Y/ W1*
HEAT PUMP W / AUXILIARY
ELECTRIC HEAT
FUNCTION CONNECT
RTO:
OFF -----------
FAN G **
COOLG, Y / W1
1ST STAGE
HEATG, B, Y/ W1
2ND STAGE
HEATG, W2
8BOARD SHOWS R AND C, PLEASE IGNORE.
NOTES:
8
8
UI CONNECTION
WIRE CODE
BR BROWN
BK BLACK
GN GREEN
GY GRAY
RD RED
VT VIOLET
WH WHITE
YL YELLOW

19
HIGH VOLTAGE!
DISCONNECT ALL POWER BEFORE SERVICING OR INSTALLING THIS
UNIT. MULTIPLE POWER SOURCES MAY BE PRESENT. FAILURE TO
DO SO MAY CAUSE PROPERTY DAMAGE, PERSONAL INJURY OR DEATH.
WIRING DIAGRAMS
24VAC TRANSFORMER
12VA CLASS 2 ONLY
ON OFF
MASTER SWITCH
IN1 COM IN2
AUXILIARY
CRGL W2 Y/W1 B GH
REMOTE THERMOSTAT
IAT
BLACK
ICT
RED
OCT
BLUE
IHD
ORANGE
OAT
GREEN
IDT
YELLOW
REV.
VALVE
ID
FAN
HIGH LOW
OD
FAN
HIGH LOW
LINE 2COMPRESSOR
HEATER 1 HEATER 2
LINE 1
DANGER HIGH VOLTAGE
DUAL MOTOR, DC ID MOTOR
RVC
COMP
S
C
R
BK
RD
YL
RD
BK
BK
TR
6
RD
GY
HTR
F4
WH
GN
WHITE
WIRE
2
1
RD
BK
WH WH
BK
HPS
VT
* FOR A HEAT PUMP,
THERMOSTAT USED
ON A STRAIGHT
COOL UNIT
** GL - LOW SPEED
GH - HIGH SPEED
5
1
2
3
4
5
6
LOAD
COM
265
230
H
RCCF
F
C
CM
FAN
MOTOR
WH
BR
WARNING: DISCONNECT POWER BEFORE SERVICING.
WIRING TO UNIT MUST BE PROPERLY POLARIZED
(FOR 265V) AND GROUNDED.
WHITE WIRE MUST BE CONNECTED AS SHOWN.
ON HEAT PUMP MODELS ONLY
BK ON LINE 2 WITH FUSE SHOWN CONNECTED FOR 265V
FOR 230 V &115 V, CONNECTED POWER CORD TO LINE 2
FOR REMOTE OPERATION, SEE CONFIGURATION CHART.
IF SUPPLY VOLTAGE IS 208V / 230V, USE THE 230V TAP
ON TRANSFORMER.
IF SUPPLY VOLTAGE IS 265V, USE THE 265V TAP
ON TRANSFORMER.
115V TRANSFORMER NOT SHOWN.
RD
COM
1400 1250 1200 1000
77
230 / 265
BK
GND TO MOTOR
VSTM ID
RS485
VSM
EM
EVAP
MOTOR
INDOOR MOTOR SPEED SELECTION
MODEL STARTS WITH HIGH SPEED
VSTM BLACK
LOW SPEED
VSTM RED
M/PTH074G (00 TO 35) 1250 1000
M/PTH093G (00 TO 35) 1200 1000
M/PTH093G50 1400 1250
M/PTH094G (00 TO 35) 1200 1000
M/PTH094G50 1400 1250
M/PTH123G (00 TO 35) 1250 1000
M/PTH123G50 1400 1250
M/PTH124G (00 TO 35) 1250 1000
M/PTH124G50 1400 1250
CM OUTDOOR FAN MOTOR
COMP COMPRESSOR
EM EVAPORATOR MOTOR
FC FAN CAPACITOR
F FUSE
HPS HIGH PRESSURE SWITCH
HTR HEATER ELEMENT
RCCF RUN CAPACITOR
FOR COMPRESSOR, ANY FAN
RVC REVERSING VALVE
TR TRANSFORMER
VSM VARIABLE SPEED MOTOR
VSTM VATIABLE SPEED TERMINAL BOARD
USE COPPER
CONDUCTORS ONLY
CHASSIS
WIRE LEGEND
HIGH VOLTAGE
(FACTORY)
HIGH VOLTAGE
(FACTORY OR FIELD
LOW VOLTAGE
(FACTORY OR FIELD)
HIGH VOLTAGE
DC HARNESS
(FACTORY)
7SEE TABLE FOR MOTOR SPEED SELECTION
GN
REMOTE THERMOSTAT
OPERATION
COOLING UNIT
W/ ELECTRIC HEAT
FUNCTION CONNECT
R TO:
OFF -----------
FAN G **
COOLG, Y / W1
HEAT
G, W2
OR
G, B, Y / W1*
HEAT PUMP W / AUXILIARY
ELECTRIC HEAT
FUNCTION CONNECT
RTO:
OFF -----------
FAN G **
COOLG, Y / W1
1ST STAGE
HEATG, B, Y / W1
2ND STAGE
HEATG, W2
GN1 CONTROL PANEL
UI CONNECTION
8
8
8BOARD SHOWS R AND C, PLEASE IGNORE.
NOTES:
WIRE CODE
BR BROWN
BK BLACK
GN GREEN
GY GRAY
RD RED
VT VIOLET
WH WHITE
YL YELLOW
3

20
CUSTOMER FEEDBACK
We are very interested in all product comments.
Please ll out the feedback form on one of the following links:
Daikin Products: (hps://daikincomfort.com/contact-us)
You can also scan the QR code on the right for the product brand you purchased
to be directed to the feedback page. DAIKIN
is a registered trademark of Maytag Corporation or its related companies and is used under license
to Goodman Company, L.P., Houston, TX, USA. All rights reserved.
© 2015 - 2016, 2020 Goodman Company, L.P.
19001 Kermier Rd. •Waller, TX 77484 •www.amana-ptac.com
Table of contents
Other Amana Control Unit manuals
Popular Control Unit manuals by other brands
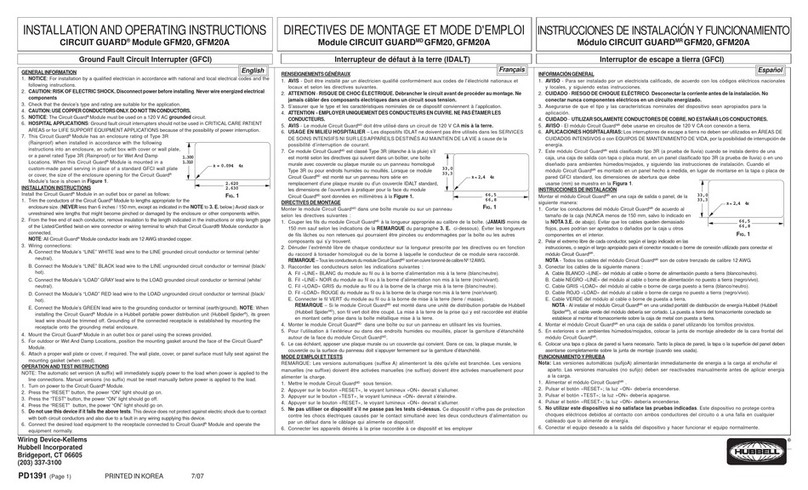
Hubbel
Hubbel CIRCUIT GUARD GFM20 Installation and operating instructions

WAGO
WAGO 750-538 manual
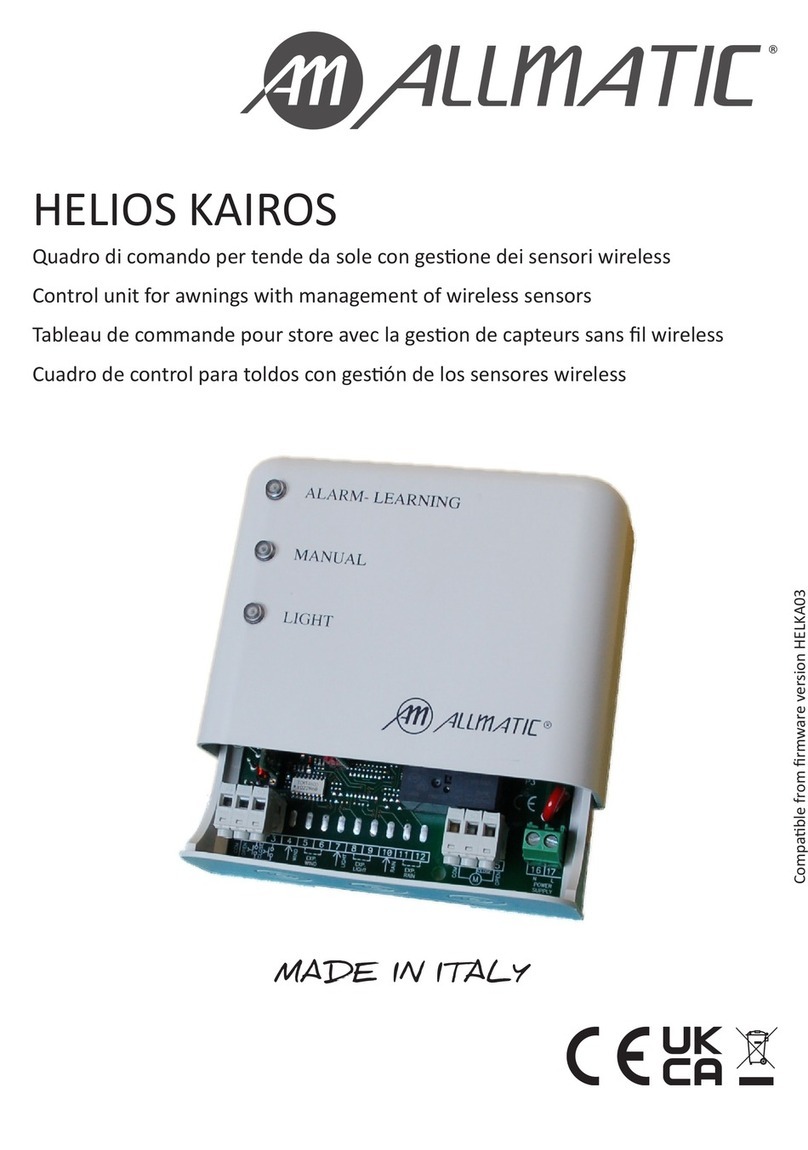
Allmatic
Allmatic HELIOS KAIROS manual
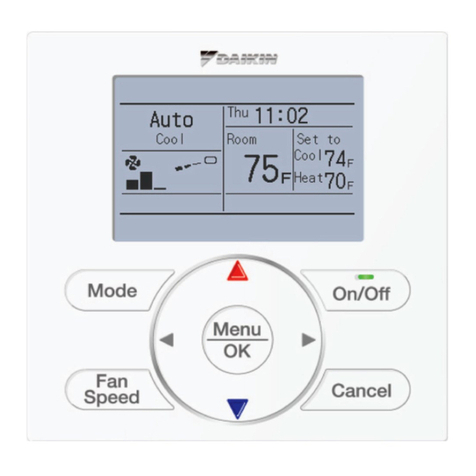
Daikin
Daikin BRC1E71 Engineeiring data
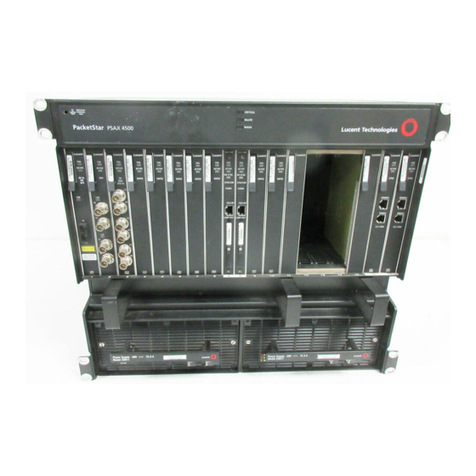
Lucent Technologies
Lucent Technologies PacketStar PSAX 1000 user guide
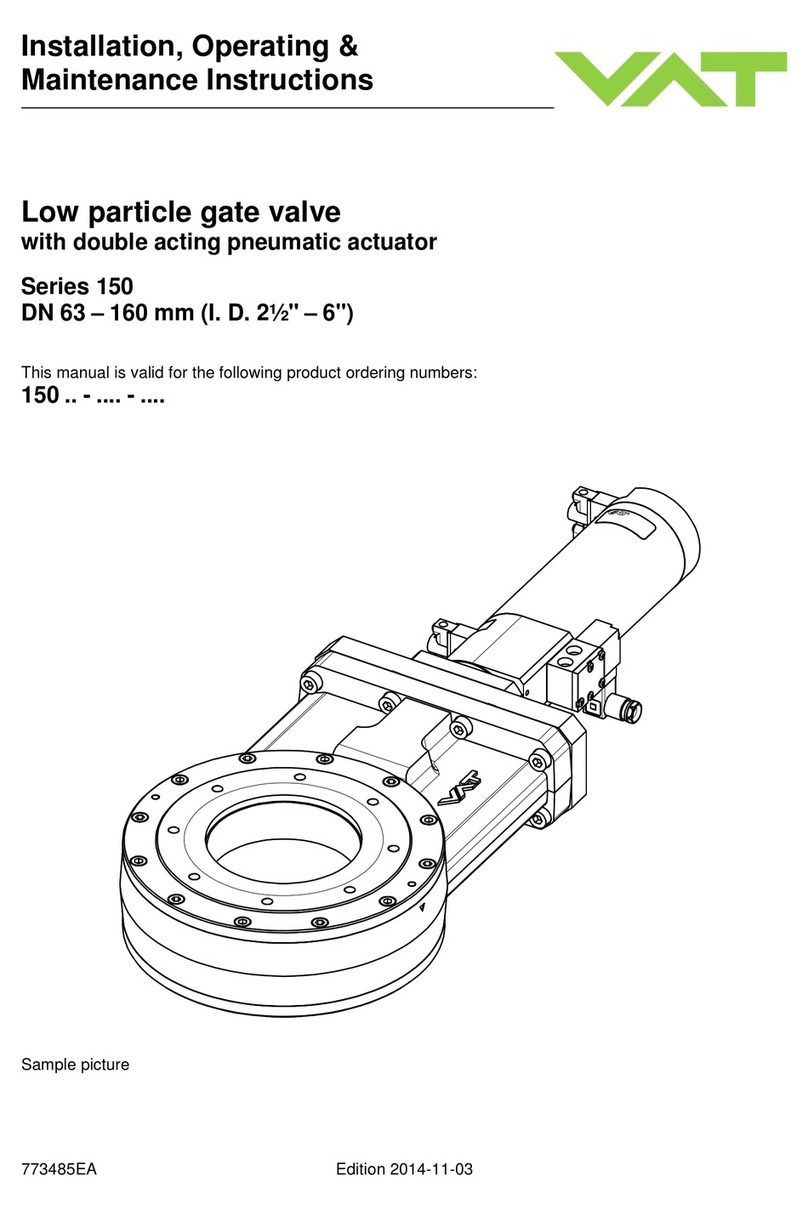
VAT
VAT 150 Series Installation, operating, & maintenance instructions