Amana RSKP0006 User manual

Description
Controlboardinstallationproceduresaredescribedindetail
in these instructions. Read and follow these instructions
carefullybeforereplacingthecontrolboard.Failuretodoso
mayresultincontrolboarddamage.
ImportantNote:
Damage to the control board can occur from failure to
disconnectpowersupplyorfailuretosetthemasterswitch
(locatedonthecontrolboard)toOFFbeforeremovingthe
low voltage terminal strip cover from an installed control
board.Damagetothisboardbynotfollowingtheseinstruc-
tionsisconsideredmisuseandnotcoveredundereitherthe
standardunitwarranty or anyextendedservicecontract.
ImportantNote:
Allwarrantyreplacedboardsmustbereturnedtotheparts
source from which they were purchased to insure proper
warrantycredit.
PTAC CONTROL BOARD KIT
RSKP0006
I
NSTALLATION
I
NSTRUCTIONS
IO-660A
November2006
ATTENTION INSTALLING PERSONNEL
As a professional installer you have an obligation to know the product better than the customer. This
includes all safety precautions and related items.
Prior to actual installation, thoroughly familiarize yourself with this Instruction Manual. Pay special attention
to all safety warnings. Often during installation or repair it is possible to place yourself in a position which is
morehazardous than when the unit is in operation.
Remember, it is your responsibility to install the product safely and to know it well enough to be able to
instruct a customer in its safe use.
Safety is a matter of common sense...a matter of thinking before acting. Most dealers have a list of specific
goodsafety practices...followthem.
The precautions listed in this Installation Manual are intended as supplemental to existing practices.
However, if there is a direct conflict between existing practices and the content of this manual, the
precautionslistedheretakeprecedence.
RECOGNIZE THIS SYMBOL AS A SAFETY PRECAUTION.
Figure 1
ElectrostaticDischarge(ESD)Precautions
Beforeremovingthenewcontrolboardfromthestaticwrap,
it is very important to discharge any static electricity. This
can be accomplished in two methods. Servicer can wear a
groundstraporbytouchingthemetalchassisbeforereplac-
ingthe board.
Existing Control Board Removal Procedures
1. Disconnect power to the unit by unplugging the power
cordatthewalloutletorsubbase,ordisconnectpowerat
the fuse box or circuit breaker.
2. Ifthecabinetfrontisscrewedtothechassis,removethe
1/4”screw(orscrews)locatedbehindtheinletgrille. Pull
theinlet grilleforwardfromthetopofthegrille toaccess
screw(s).
FRONT MOUNTING
HOLE
Printed in USA

2
3. Removecabinetfrontfromchassisbytiltingthebottomof
thefrontforward,liftingslightlyupandforward.
4. If a remote thermostat or any low voltage accessory is
beingused,removethelowvoltagepinconnectorfromthe
low voltage terminal strip. If a previous version board is
beingreplacedremovewiresfromthelowvoltageterminal
strip.
123
ON
PULL TO REMOVE
THERMOSTAT KNOB
Lift Off
PULL TO REMOVE
MODE SWITCH KNOB ESCUTCHEON
SCREW (2)
SCREW
Figure 2
5. Removeknobsandescutcheon.
6. Remove the two mounting screws, one on each side of
controlboardcover.Somemodelsmayhaveascrewon
thelowerrightsideofthecontrolpanelthatwillneedtobe
removed.Tiltcontrolpaneloutandremovecover.
7. Remove the wires from the board in the unit, including
Thermistor Sensors if they plug into the board.
8. Removethefourscrewsholdingtheboardandremovethe
oldboard.
New Control Board Installation Procedures
9. If existing unit has a remote mounted “off board” trans-
formerforboardpower,proceedtoStep13.
10. Lift the control panel up so the control panel is free of its
hinges. Orient the control panel so there is easy access
for mounting components to the inside of the control
panel.
11. Using the two #8 screws that are provided, screw the
transformer that was provided with the kit to the control
panel in the transformer mounting holes provided in the
panel.SeeFigure 3.
12. The external transformer will come with the Black 37
wiresconnectedtotheLOADterminalofthetransformer
(LOADterminalsarethelow voltage terminals) and the
Grey 22 wire connected to the COM terminal on the
transformer.TheGrey21wirewillneedtobeconnected
to the 230 or 265 volt tap on the transformer. Place the
control panel back on its hinges.
NOTE:Refertotheserialplateforvoltageinformation.
13. Installthenewboardandreinstallthescrewsremovedin
step # 8.
14.Usingthe insulated terminalsconnectthetwo (2)Black
37wiresfromtheLoadterminalsonthetransformertothe
“24VACTransformer”terminalsonthecontrolboard.See
Figure4.
15.Connect Grey 22 wire from the COM terminal on the
transformertoline2onthecontrolboard. ConnectGrey
21wirefromthetransformertoline1onthecontrolboard.
TRANSFORMER
Figure 3
GY22
BK37
BK37
LINE 1 HEATER 1 HEATER 2 LINE 2 COMPRESSOR
24VAC~TRANSFORMER
12VA CLASS 2 ONLY
GY21
TRANSFORMER
LINE
LOAD
COM
265
230
Figure 4

3
A3. Replace the heater panel, routing the yellow wire
aroundtherightend of the heaterpanelandintothe
control panel pulling snug to prevent the wire from
beingentangledintheblowerwheelorbeingvisible
from above. Replace the two screws mounting the
heaterpaneltotheevaporatorcoil.
A4. Replacetheexhaustgrilleandtwomountingscrews.
A5. Connecttheyellow wireusingtheplug-onconnector
to the new board on the IDT (yellow) terminals.
B. IftheexistingIndoorAmbientThermistor(withthe
BLACKwires)wasconnectedtotheboardbyaplug-
onconnector,reconnectittothenewboardontheIAT
(black) terminals. If the existing Indoor Coil Ther-
mistorwassolderedtothepreviousboard,installthe
new black thermistor per Figure 6 and connect as
above.
16. Thermistor Temperature Sensors Installation
A. ItisrecommendedthattheIndoorDischargeTher-
mistor(withtheYELLOWwires)beinstalledbutitis
optional. If you chose not to install this sensor, the
green status light will remain illuminated continu-
ously. For status light functionality, the YELLOW
thermistor MUST be installed. Instructions are as
follows:
A1. Carefully cut and remove the gasket on the left and
rightsidesofdischargescreen.Removethetwo(2)
5/16”screwsholdingtheindoorexhaustscreenabove
theindoorcoil. Removethe indoor exhaust screen.
Removethetwo(2)1/4”screwsconnectingtheheater
paneltotheevaporatorcoil.
Removethetwo(2)screwsmountingtheairbaffleto
thetopoftheheaterpanelandremoveanddiscardthe
airbaffle.
A2.Installthenewairbaffle. Routetheyellowthermistor
probefromrighttoleftthroughthewiringtubeenclo-
sure. Mount the black tip of the yellow thermistor
probe in the plastic clip provided. Hold the plastic
clampinplaceandsecuretheclamptotheleftendof
heater panel using one of the original screws. Re-
placethescrewontherightendoftheairbafflebeing
careful not to damage the wiring insulation on the
probe.
YELLOW
THERMISTOR
PLASTIC CLAMP
CLAMP END OF
THERMISTOR
SECURELY
WIRE ENCLOSURE
ROUTE THERMISTOR
THROUGH TUBE ON
BLOWER EXTENSION
Figure 5
Clip is designed to be pushed
into the coil between
the aluminum fins
and attach over
two (2) screws.
Figure 6

4
C. IftheexistingIndoorCoilThermistor(withtheRED
wires) was connected to the board by a plug-on
connector, reconnect it to the new board on the ICT
(red)terminals.Ifthepreviousboardusedindoorcoil
bi-metals,removeanddiscardthebi-metaldevices.
Theaccessdoorwillneedtoberemovedontheindoor
coiltogainaccesstothebi-metal.SeeFigure6.The
IndoorCoilThermistorwillneedtocliponthevertical
section of the 90-degree bend of the inlet line to the
indoor coil. See Figure 7. Connect the Indoor Coil
Thermistortotheboardasnotedabove.
D. If the existing Outdoor Coil Thermistor (with the
BLUE wires)wasconnectedto the board by aplug-
on connector, reconnect it to the new board on the
OCT (blue) terminals. If the previous board used
indoorcoilbi-metals,removeanddiscardthebi-metal
devices.TheIndoorCoilThermistorwillneedtoclipon
the crossover tube shown in Figure 8. There will be
two clips supplied in the kit for the Blue Thermistor.
Oneclipassuppliedonthesensorwillfit5/16”tubing
usedonthebentcoil,andanadditionalclip(loosein
the bag) will fit 3/8” tubing used on the flat slab coil.
Ifyouhaveaslabcoil,youwillneedtoremovethe5/16”
clipfromthesensorandreplaceitwith the 3/8” tube
clip.ConnecttheOutdoorCoilThermistortotheboard
as noted above. Outdoor Coil Thermistors are only
usedonHeatPumpmodels;DONOTINSTALLTHIS
SENSOR IF THE UNIT IS NOT A HEAT PUMP.
Figure 7
INDOOR COIL THERMISTOR - RED
All Units
Connect to ICT on Control Board
Cross over tube
for 9,12 and 15k
or center tube for
7,000 BTU
Figure 8
17. Iftheunithasacondensatepump,gotostep18.Iftheunit
hasapowerventorpowerdoor,gotostep19. Otherwise
proceedwithstep20. Refertowiringdiagramsinbackof
manual.
18. CondensatePumpUnitsOnly
(SeeWiringDiagramPage10
Reconnect the wires across the top terminals of the
controlboard. Connect as follows:
Red 33 to Line 1
Brown34toHeater 1
Brown34toHeater 2
Power cord (or black 18) to Line 2
Violet 12 and Yellow 3 to Compressor
Black 16 to Fan High
Red 17 to Fan Low
19fromreversingvalveandYellow1toRev.Valve.
Connecttheyellow5wiretothe230or265-voltterminal
asapplicableusingthepiggybackterminalontheyellow
5 wire. Go to step 21.

5
19. PowerVent/PowerDoorUnitsOnly
(SeeWiringDiagramPage9)
Reconnect the wires across the top terminals of the
controlboard. Connect as follows:
Red 33 to Line 1
Brown34toheater1
Brown34toHeater 2
Power cord (or black 18) to Line 2
Violet12toCompressor
Blue 4 to Fan high
Blue 15 and Blue 10 to Fan Low
19fromreversingvalvetoRev.Valve
Connectthewhite7wiretothe230or265-voltterminalas
applicable using the piggyback terminal on the white 7
wire. Go to step 21.
20. Reconnect the wires across the top terminals of the
controlboard.Connectasfollows:
(SeeWiringDiagramPage8)
Red 33 to line 1
Brown34toheater1
Brown34toheater2
Power cord or black 18 to line 2
Violet 12 to compressor
Black 16 to Fan High
Red 17 to Fan Low
19fromreversingvalvetoRev.Valve.
21. If aremote wired thermostatand an additionalREK01B
escutcheonthatstates“THISUNITISCONTROLLEDBY
WALLMOUNTEDTHERMOSTAT”isused,theknoband
potentiometer will need to be removed. To remove the
knob, loosen the set screw on the side of the knob with
aflatscrewdriverandpullknobfrompotentiometershaft.
Toremovethepotentiometer,loosenthenutwitha10mm
driver and remove the nut and 2 washers. Pull the shaft
freeofthepanel.Reassemblepotentiometer,washers,
nut and knob and store for future use. These will be
requirediftheunitiseverconvertedbacktolocalcontrols
insteadofwiredthermostatoperation.
Thecontrolboardcoverisnowreadytobeinstalled.The
ribbonforthetouchpadwillneedtobeconnectedtothe
control board. Take caution not to bend or fold the
ribbon(SeeFigure9forribbonconnection).
Installorangeconnectorfromthethermostatonthetouch
pad to the IHD Terminals on control board, unless the
knobhasbeenremoved.
Ensurethatnowiresarepinchedorcaughtbetweenthe
coverandthepanelandthenreinstallthescrewsremoved
in Step 5.
22. If a remote thermostat or any low voltage accessory is
beingusedconnectthelowvoltagepinconnectortolow
voltageterminalstrip.
Ifreplacingapreviousversionboardyouwillneedtouse
the 18 pin connector supplied with the board for low
voltage accessories. Wires supplied with this kit have
terminal ends on the wires. Insert the terminal end into
thecorrectlylabeledslot,pushinanditwilllockinplace.
After loading pin connector use the wire nuts supplied
with the kit to wire nut the new wires onto the existing
wiressuppliedforlowvoltageaccessories.SeeFigure9
on page 5.
23. Set the master switch to ON. Restore electrical power
andverifyunitfunctionality.
24. This control can be configured for several operational
features.
A. If the unit was being controlled by a wired wall
thermostat, the board will have to be configured to
allowthethermostattooperatetheunit.Toconfigure
for a wired wall thermostat, press and hold the FAN
SPEEDbuttonandpresstheCOOLbuttontwice.The
lightinthebottomlefthandcornerbelowtheOFFlight
will blink twice to confirm that the configuration was
successful. Repeat step 24 if the light did not blink.
B. If the unit will be controlled by a wireless thermostat
(GoodmanDS01AusingDT01Aantennaontheunit),
the board may have to be configured to allow the
wirelessthermostattooperatetheunit.Toconfigure
forwirelessoperation,pressandholdtheFANSPEED
buttonandpresstheHEATbuttontwice. Thelightin
the bottom left hand corner below the OFF light will
blink twice to confirm that the configuration was
successful. Repeat step 24 if the light did not blink.
C. If constant fan is desired, the unit will need to be
configuredbypressingandholdingtheHEATbutton
andpressingtheOFFbuttontwice.Toreverttoauto/
cyclicfanoperation,pressandholdtheCOOLbutton
and press the OFF button twice.
D. Other configuration items exist, but can only be
accessedoverthewirelessantennatoawirelesssite
platform(GoodmanDP01A).
E. Toresetalltheconfigurationitemsbacktothefactory
defaults, turn the master switch off for 10 seconds,
and then hold the HEAT and COOL button while
turning the master switch back on.
25. ReplacethefrontinreverseorderasremovedinSteps2
and3.

6
BLACK w/WHITE STRIPE
YELLOW w/BLACK STRIPE
RED
GREEN
WHITE
YELLOW
BLUE
GREEN w/YELLOW STRIPE
Remote Thermostat
BROWN
*Only load wires needed for accessories attached to unit.
Figure 9

7
REV.
VALVE
FAN
LOW
FAN
HIGH
LINE 1
ON
24VAC-TRANSFORMER
DSI IN GL GH
B
YELLOW
Heat Pump models ONLY.
Must not be used
on PTC models.
RIBBON CONNECTOR
Left is ON
Position
YELLOW
ORANGE from Touch Pad
BLUE
RED
BLACK
Figure 10

8
WIRING DIAGRAMS
TO
UNIT
MUST
BE
PROPERLY
POLARIZED
(FOR
5V)
AND
GROUNDED.
R
TO:
G,
W2
(FACTORY
OR
FIELD)
COOL
UNIT
G,
Y/W1
4
ON
UNITS
WITH
FRONT
DESK
CONTROL
SWITCH.
R
TO:
G,
W2
-----
(FACTORY)
2ND
STAGE
G,
Y/W1
G
HIGHVOLTAGE
CURRENT:
.1
FUNCTION
1STSTAGE
NOTES:
LOW
VOLTAGE
1STSTAGE
GN
1
HEAT
HEAT
LOW
VOLTAGE
THERMOSTAT
USED
HIGH
VOLTAGE
HEAT
POWER
CORD
TO
LINE
2.
(FACTORY
OR
FIELD)
CURRENT:
.1
OFF
NOTES:
W/ELECTRIC
HEAT
(FACTORY)
CONDUCTORS
ONLY
5
BK18
ON
LINE
2
WITH
FUSE
SHOWN
CONNECTED
FOR
265V.
FOR
230V
&
1
15V,
CONNECT
WIRELEGEND
4
ON
UNITS
WITH
FRONT
DESK
CONTROL
SWITCH.
2ND
STAGE
ON
A
STRAIGHT
1ST
STAGE
WIRELEGEND
FUNCTION
CURRENT:
.1
ANTICIPATOR
3
ON
HEAT
PUMP
MODELS
ONLY.
OFF
2ND
STAGE
CHASSIS
G,B,Y/W1
HEAT
1
WARNING:
DISCONNECT
POWER
BEFORE
SERVICING.
WIRING
HIGH
VOLTAGE
-----
HEAT
PUMP
W/AUXILIARY
REMOTE
THERMOSTAT
OPERATION
TO
UNIT
MUST
BE
PROPERLY
POLARIZED
(FOR
265)
AND
GROUNDED.
6
FOR
REMOTE
OPERATION,
SEE
CONFIGURATION
CHART.
ANTICIPATOR
FUNCTION
1
ARNING:
DISCONNECT
POWER
BEFORE
SERVICING.
WIRING
*
ELECTRIC
HEAT
2
RIBBED
WIRE
MUST
BE
CONNECTED
AS
SHOWN
COOLING
UNIT
G,
Y/W1
USE
COPPER
ELECTRIC
HEAT
G
3
ON
HEAT
PUMP
MODELS
ONLY.
FAN
PANEL
ANTICIPATOR
G,B,Y/W1
CURRENT:
.1
COOLING
UNIT
FUNCTION
-----
HIGHVOLTAGE
*
FOR
A
HEAT
PUMP
OFF
2
RIBBED
WIRE
MUST
BE
CONNECTED
AS
SHOWN
-----
ANTICIPATOR
GN
1
R
TO:
HEAT
PUMP
W/AUXILIARY
REMOTE
THERMOSTAT
OPERATION
FAN
PANEL
W/ELECTRIC
HEAT
CHASSIS
R
TO:
2ND
STAGE
1ST
STAGE
G,
Y/W1
(FACTORY
OR
FIELD)
(FACTORY
OR
FIELD)
HEAT
OFF
230
265
COM
TRANSFORMER
LOAD
SOLENOID
R
SWITCH
BK18
YL10
BR14
ELECTRIC
GY22
C
CAP
H
HEATER
4
1
DESK
2
F
19
WIRE
RD17
RD13
BK16
S
OD
VALVE
C
G
N
RIBBED
FAN/COMP
3
5
20
FUSE
BK37 BK37
GY21
RD33
7 IF SUPPLY VOLTAGE IS 208V/230V USE THE 230V TAP ON TRANSFORMER.
IF SUPPLY VOLTAGE IS 265V USE THE 265V TAP ON TRANSFORMER.
115V TRANSFORMER NOT SHOWN.
7
LINE1
E1
HEATER 1 HEATER 2 REV
VALVE
FAN
LOW
FAN
HIGH
K1 K2 K3
E2 E3 E4 E5 E6 E7 E8 E9 E10
LINE 2 COMPRESSOR
K4 K5 K6
E11 E12
ON / OFF
MASTER SWITCH
COM A COM B
CP4
SW2 P10 P11
DS1
P13
IAT
BLACK
P2
P5
CR11
X1
X3
X2
X4
M2
M1
P1
P4P8P9
IDT
YELLOWGREEN
OCT
BLUE
ICT
RED
24VAC~TRANSFORMER
12VA CLASS 2 ONLY
DS2 MS1MS2 EH IN LS FD1 FD2 TF- TF+ C R
AUXILIARY GL W2 Y/W1 B GH
REMOTE THERMOSTATE
ORANGE
VT12
BR34 BR34
8 FOR CONTINUOS FAN OPERATION SEE CONFIGURATION CHART.
6
WIRING
DIAGRAM
WIRING
DIAGRAM
205180
REV.0
CONTROL
CONTROL
FRONT
CONNEC
CONNECT
COOL
COOL
COMP
WH15
MOTOR
FAN
REV
COOL
COOL
CONNEC
CONNECT
HIGH VOLTAGE!
DISCONNECT ALL POWER BEFORE SERVICING OR INSTALLING THIS
UNIT. MULTIPLE POWER SOURCES MAY BE PRESENT. FAILURE TO
DO SO MAY CAUSE PROPERTY DAMAGE, PERSONAL INJURY OR DEATH.

9
WIRING DIAGRAMS
2
RIBBED
WIRE
MUST
BE
CONNECTED
AS
SHOWN.
NOTES:
1
WARNING:
DISCONNECT
POWER
BEFORE
SERVICING.
WIRING
TO
UNIT
MUST
BE
PROPERLY
POLARIZED
(FOR
265V)
AND
GROUNDED.
3
ON
HEAT
PUMP
MODELS
ONLY.
4
ON
UNITS
WITH
FRONT
DESK
CONTROL
SWITCH.
WIRING
DIAGRAM
1ST
STAGE
ANTICIPATOR
CURRENT:
.1
2ND
STAGE
ANTICIPATOR
CURRENT:
.1
2
RIBBED
WIRE
MUST
BE
CONNECTED
AS
SHOWN.
NOTES:
1
WARNING:
DISCONNECT
POWER
BEFORE
SERVICING.
WIRING
TO
UNIT
MUST
BE
PROPERLY
POLARIZED
(FOR
265V)
AND
GROUNDED.
WIRING
DIAGRAM
20518101
REV0
GN
1PANEL
CHASSIS
WIRE
LEGEND
HIGH
VOLTAGE
(FACTORY)
HIGH
VOLTAGE
(FACTORY
OR
FIELD)
LOW
VOLTAGE
(FACTORY
OR
FIELD)
3
ON
HEAT
PUMP
MODELS
ONLY.
4
ON
UNITS
WITH
FRONT
DESK
CONTROL
SWITCH.
1ST
STAGE
ANTICIPATOR
5
BK18
ON
LINE
2
WITH
FUSE
SHOWN
CONNECTED
FOR
265V.
FOR
230V
AND
115V,
CONNECT
POWER
CORD
TO
LINE
2.
7
FOR
REMOTE
OPERATION,
SEE
CONFIGARATION
CHART.
REMOTE
THERMOSTAT
OPERATION
USE
COPPER
CONDUCTORS
ONLY
GN
1PANEL
CHASSIS
WIRE
LEGEND
HIGH
VOLTAGE
(FACTORY)
HIGH
VOLTAGE
(FACTORYORFIELD)
LOW
VOLTAGE
(FACTORY
OR
FIELD)
3
BK37
BK37
GY22
GY21
LINE
265
230
4SWITCH
DESK
FRONT
RD33
(PV)
BU2
RD17
BK16
(PV)
BU15
(PV)
RD14
BLOCK
TERMINAL
B
3
6
9
8
5
2
A
7
4
1
(PV)
BK17
6
(PV)
BU4
(PV)
WH7
(PV)
BK11
(PV)
BU9
(PV)
BU10
(PV)
BK12
(PV)
WH8
1
2
3
SWITCH
ON/OFF
VT12
5
BK18
MOOR
T
1
LINE
COM
208
240
FAN
MUFFIN
20
HEATER
ELECTRIC
CAP
FAN/COMP
OD
WH15
BR14
19
SOLENOID
VALVE
2
GN
WIRE
RIBBED
HCF
YL10
RD13
S
C
R
R
TO:
-----
G,
Y/W1
G,B,Y/W1
G,
W2
FUNCTION
OFF
1ST
STAGE
HEAT
2ND
STAGE
HEAT
R
TO:
G,
Y/W1
FUNCTION
OFF-----
HEAT
G**
FAN
G**
FAN
*
*
FOR
A
HEAT
PUMP
THERMOSTAT
USED
ON
A
STRAIGHT
COOL
UNIT
**
GL-
low
speed
GH-
high
speed
W/ELECTRIC
HEAT
COOLING
UNITELECTRIC
HEAT
HEAT
PUMP
W/AUXILIARY
8
LINE 1
E1
HEATER1 HEATER2 REV
VALVE
FAN
LOW
FAN
HIGH
K1 K2 K3
E2 E3 E4 E5 E6 E7 E8 E9 E10
LINE 2 COMPRESSOR
K4 K5 K6
E11 E12
ON / OFF
MASTERSWITCH
COMA COMB
CP4
SW2 P10 P11
DS1
P13
IAT
BLACK
P2
P5
CR11
X1
X3
X2
X4
M2
M1
P1
P4P8P9
IDT
YELLOWGREEN
OCT
BLUE
ICT
RED
24VAC~TRANSFORMER
12VA CLASS 2 ONLY
DS2 MS1 MS2 EH IN LS FD1 FD2 TF- TF+ C R
AUXILIARY GL W2 Y/W1 B GH
REMOTE THERMOSTATE
ORANGE
BR34
BR34
7
6
IF
SUPPLY
VOLTAGE
IS
208V
MOVE
240V
LEAD
TO
208V
TAP
ON
TRANSFORMER.
265V
AND
115V
TRANSFORMER
NOT
SHOWN.
9
FOR
CONTINUOS
FAN
OPERATION
SEE
CONFIGURATION
CHART.
8
IF
SUPPLY
VOLTAGE
IS
208V/230V
USE
THE
230V
TAP
ON
TRANSFORMER.
IF
SUPPLY
VOLTAGE
IS
265V
USE
THE
265V
TAP
ON
TRANSFORMER.
115V
TRANSFORMER
NOT
SHOWN.
CONTRO
CONTROL
POWER
T
VEN
VENT
POWER
REV
CONNECT
COOL
COM
MOTOR
FAN
COMP
COOL
CONNECTCONNECT
HIGH VOLTAGE!
DISCONNECT ALL POWER BEFORE SERVICING OR INSTALLING THIS
UNIT. MULTIPLE POWER SOURCES MAY BE PRESENT. FAILURE TO
DO SO MAY CAUSE PROPERTY DAMAGE, PERSONAL INJURY OR DEATH.

10
WIRING DIAGRAMS
2
RIBBED
WIRE
MUST
BE
CONNECTED
AS
SHOWN.
NOTES
1
WARNING:
DISCONNECT
POWER
BEFORE
SERVICING.
WIRING
TO
UNIT
MUST
BE
PROPERLY
POLARIZED
(FOR
265V)
AND
GROUNDED.
3
ON
HEAT
PUMP
MODELS
ONLY.
4
ON
UNITS
WITH
FRONT
DESK
CONTROL
SWITCH.GN
1CONTROL
PANEL
CHASSIS
WIRE
LEGEND
HIGH
VOLTAGE
(FACTORY)
HIGH
VOLTAGE
(FACTORY
OR
FIELD)
LOW
VOLTAGE
(FACTORY
OR
FIELD)
R
C
S
RD13
YL10
F
C
H
BR34
BR34
RD33
RIBBED
WIRE
G
N
2
2
RIBBED
WIRE
MUST
BE
CONNECTED
AS
SHOWN.
NOTES
1
WARNING:
DISCONNECT
POWER
BEFORE
SERVICING.
WIRING
TO
UNIT
MUST
BE
PROPERLY
POLARIZED
(FOR
265V)
AND
GROUNDED.
REV
VALVE
SOLENOID
19
WIRING
DIAGRAM
205184
REV
0
GN
1CONTROL
PANEL
CHASSIS
WIRE
LEGEND
HIGH
VOLTAGE
(FACTORY)
HIGH
VOLTAGE
(FACTORY
OR
FIELD)
3
BR14
WH15
LOW
VOLTAGE
(FACTORY
ORFIELD)
3
ON
HEAT
PUMP
MODELS
ONLY.
4
ON
UNITS
WITH
FRONT
DESK
CONTROL
SWITCH.
COMP
OD
FAN/COMP
CAP
1ST
STAGE
ANTICIPATOR
CURRENT:
.1
2ND
STAGE
ANTICIPATOR
CURRENT:
.1
ELECTRIC
HEATER
20
1
3
5
A
2
4
6
B
1
FAN
MOTOR
VT12
5
BK18
ON
LINE
2
WITH
FUSE
SHOWN
CONNECTED
FOR
265V.
FOR
230V
AND
115V,
CONNECT
POWER
CORD
TO
LINE
2.
6
IF
SUPPLY
VOLTAGE
IS
208V
MOVE
240V
LEAD
TO
208V
TAP
ON
TRANSFORMER.
265V
AND
115V
TRANSFORMER
NOT
SHOWN.
240
208
COM
LINE
OR8
(CP)
7
FOR
REMOTE
OPERATION,
SEE
CONFIGURATION
CHART.
6
YL1
(CP)
YL5
(CP)YL3
(CP)
BK16RD17
WH6
(CP)
HEAT
PUMP
W/AUXILIARY
ELECTRIC
HEAT
RTO:
-----
G,
Y/W1
G,B,Y/W1
G,
W2
FUNCTION
OFF
COOL
1ST
STAGE
HEAT
2ND
STAGE
HEAT
COOLING
UNIT
W/ELECTRIC
HEAT
CONNECT
R
TO:
G,
Y/W1
FUNCTION
OFF-----
REMOTE
THERMOSTAT
OPERATION
HEAT
G
FAN
G
FAN
*
*
FOR
A
HEAT
PUMP
THERMOSTAT
USED
ON
A
STRAIGHT
COOL
UNIT
USE
COPPER
CONDUCTORS
ONLY
FRONT
DESK
SWITCH
4
1ST
STAGE
ANTICIPATOR
CURRENT:
.1
2ND
STAGE
ANTICIPATOR
CURRENT:
.1
240
208
COM
LINE8
GY21
GY22
BK37
LINE 1
E1
HEATER 1 HEATER 2 REV
VALVE
FAN
LOW
FAN
HIGH
K1 K2 K3
E2 E3 E4 E5 E6 E7 E8 E9 E10
LINE 2 COMPRESSOR
K4 K5 K6
E11 E12
ON / OFF
MASTERSWITCH
COMA COMB
CP4
SW2 P10 P11
DS1
P13
IAT
BLACK
P2
P5
CR11
X1
X3
X2
X4
M2
M1
P1
P4P8P9
IDT
YELLOWGREEN
OCT
BLUE
ICT
RED
24VAC~TRANSFORMER
12VA CLASS 2 ONLY
DS2MS1MS2EH IN LS FD1FD2TF-TF+ C R
AUXILIARY GL W2 Y/W1 B GH
REMOTE THERMOSTATE
ORANGE
BK18
5
7
BK37
8
IF
SUPPLY
VOLTAGE
IS
208V,
MOVE
204V
LEAD
TO
208V
TAP
ON
TRANSFORMER.
265V
AND
115V
TRANSFORMER
NOT
SHOWN.
9
FOR
CONTINUOS
FAN
OPERATION
SEE
CONFIGURATION
CHART.
CONNECTCONNECT
COOL
HIGH VOLTAGE!
DISCONNECT ALL POWER BEFORE SERVICING OR INSTALLING THIS
UNIT. MULTIPLE POWER SOURCES MAY BE PRESENT. FAILURE TO
DO SO MAY CAUSE PROPERTY DAMAGE, PERSONAL INJURY OR DEATH.

11
THIS PAGE LEFT INTENTIONALLYBLANK

12
GoodmanCompany,L.P.
2550 North Loop West, Suite 400
Houston, TX 77092
Quality Makes the Difference!
All of our systems are designed and manufactured with the same high quality standards regardless of size or
efficiency. We have designed these units to significantly reduce the most frequent causes of product failure.
Theyaresimpletoserviceandforgivingtooperate.Weusequalitymaterialsandcomponents.Finally, every
unit is run tested before it leaves the factory. That’s why we know. . .There’s No Better Quality.
Visit our website at www.amana-ptac.com for information on:
• Products
• Warranties
• Customer Services
• Parts
• Contractor Programs and Training
• Financing Options
©2006 Goodman Company, L.P.
®
is a trademark of Maytag Corporation and is used under
license to Goodman Company, L.P. All rights reserved.
Table of contents
Other Amana Control Unit manuals
Popular Control Unit manuals by other brands

Georg Fischer
Georg Fischer Signet 9900 instruction sheet
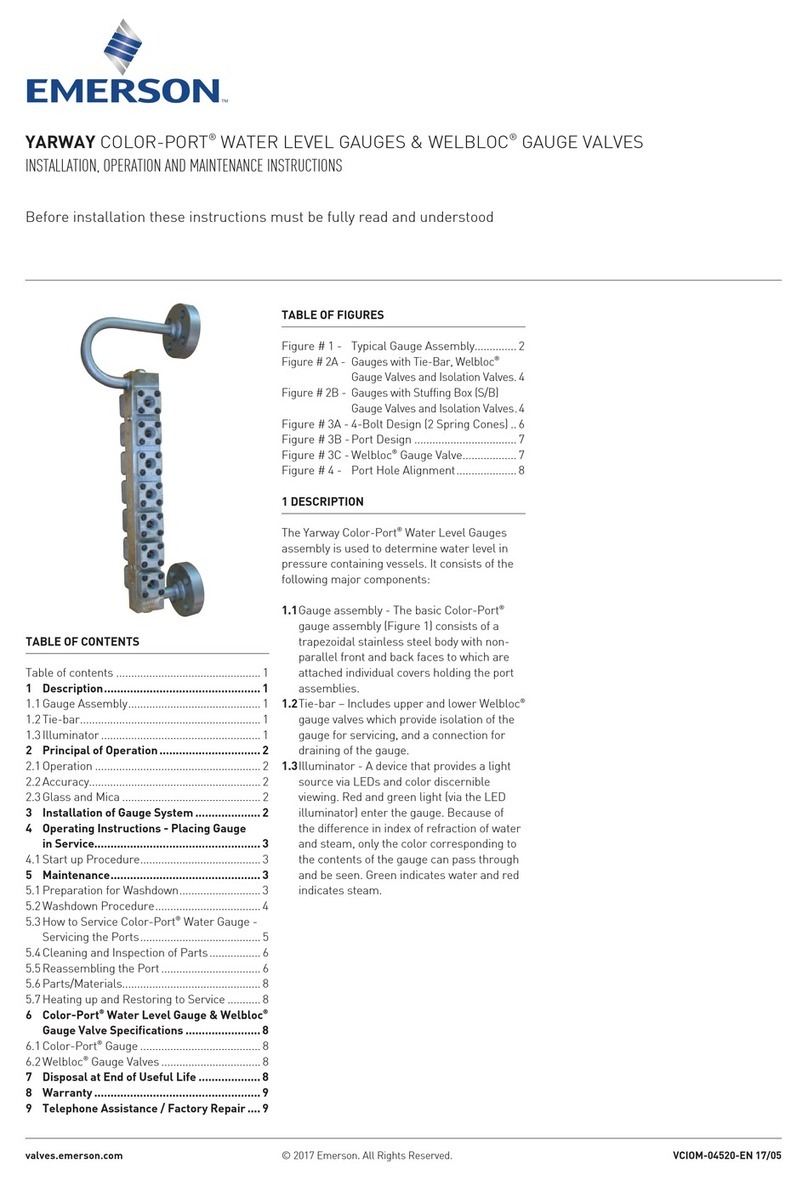
Emerson
Emerson Yarway Color-Port 4511N Installation, operation and maintenance instructions
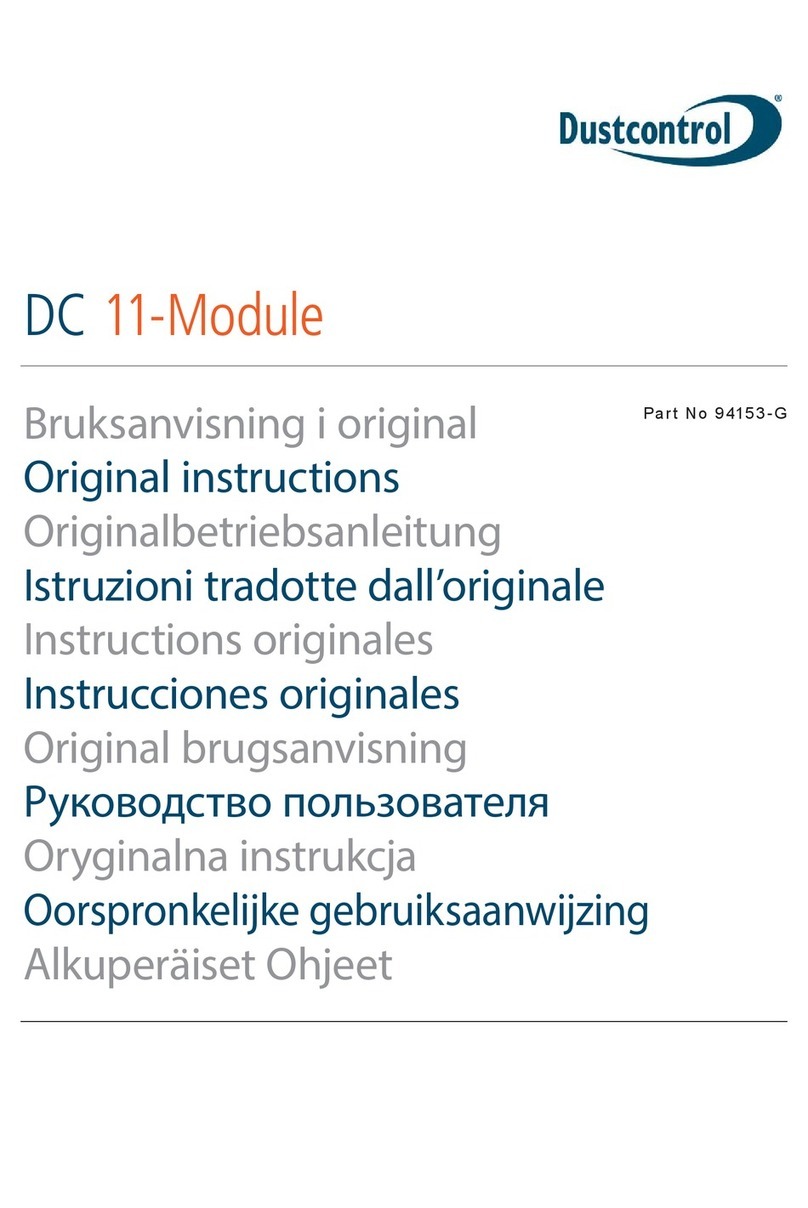
Dustcontrol
Dustcontrol 14124x Original instructions
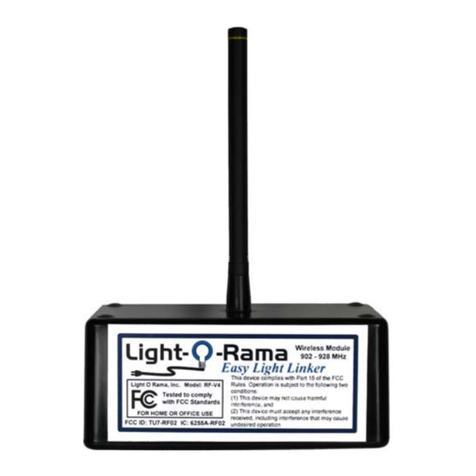
Light O Rama
Light O Rama Easy Light Linker RF-V4 user manual

ActronAir
ActronAir CP10 operating instructions
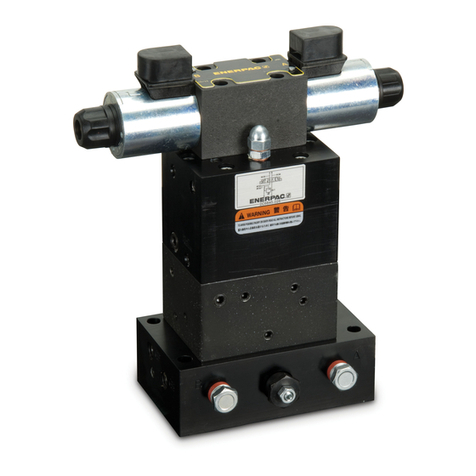
Enerpac
Enerpac VE33 Repair Parts Sheet
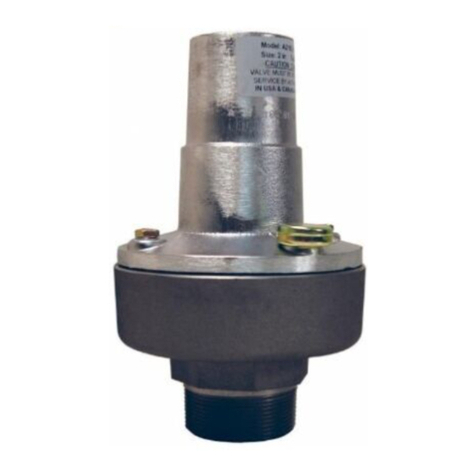
Dixon
Dixon BAYCO 2182 Series Maintenance & Operating Instructions
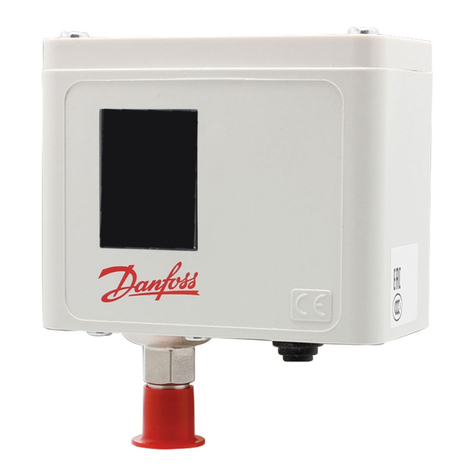
Danfoss
Danfoss KP 1 installation guide

Technibel
Technibel K 60 D 066 Z Installation instruction
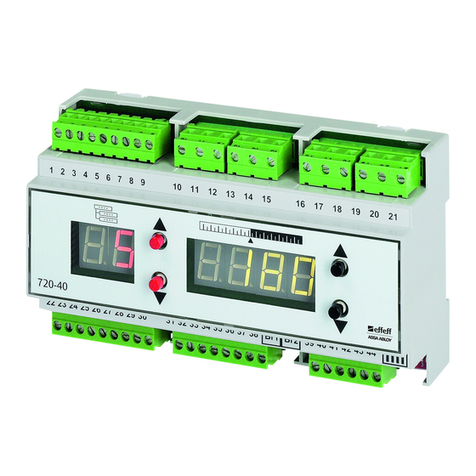
Assa Abloy
Assa Abloy effeff 720-40 Connecting diagrams
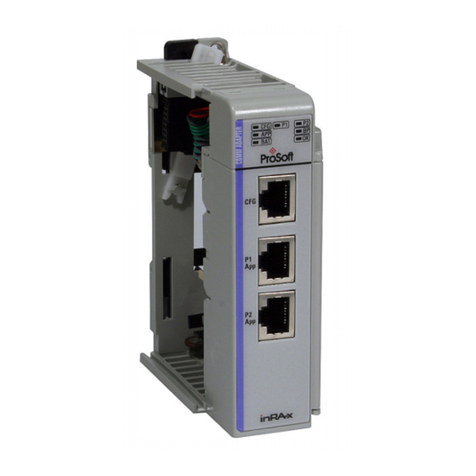
ProSoft Technology
ProSoft Technology inRax MVI69-101M user manual
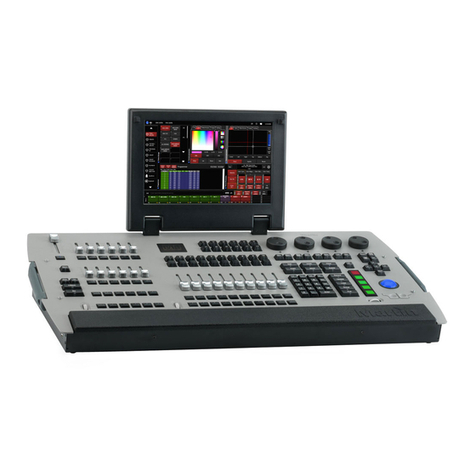
Martin Professional
Martin Professional M1 user manual