Apex Digital EK57 Installation and operating instructions

www.apexanalog.com © Apex Microtechnology Inc.
All rights reserved
Jan 2016
EK57U-Addendum Rev B
EK57 - Addendum
EK57
INTRODUCTION
This addendum describes how the evaluation kit for MP108 and MP111 amplifier devices (aka EK57) can
also be used to evaluate MP118. The bread boarding areas of EK57 are used for placement of additional com-
ponents to facilitate evaluation of MP118’s extra features.
WHAT IS MP118?
MP118 is a derivative of MP108. Compared to MP108 it features the following extra functionality /
improvements:
• The typical quiescent current has been reduced to 26mA (MP108: 50mA)
• MP118 contains a temperature sensor that provides a voltage proportional to the case temperature at
the TEMP pin (7)
• MP118 contains a latching protection circuit that disables the amplifier if an over-temperature or over-
current is detected. This circuit can be reset through an extra RESET pin (10)
• MP118 has an extra SHUT-DOWN pin (9) to facilitate external disabling of the module
Overall dimensions and location / size of mounting holes as well as the location of connectors and pin-out
(except the 3 previously described pins TEMP, RESET, and SD) of MP118 are the same as those of MP108.
ASSEMBLY INSTRUCTIONS
The remainder of this Addendum builds on the assembly instructions in the datasheet of EK57.
• At the end of step 2 DO NOT REMOVE the carrier strips! Since the cage jacks for pins 7, 9, and 10 are
unsoldered, they would be pulled out of the PCB by removing the carrier strip. However, we need to con-
nect to these pins!
• Strip ~0.6”(15mm) of the insulation off of very thin wired-wrap, kynar, 30AWG works best) and carefully
wrap the stripped portion of the wire around a 1/16” (1.5mm) drill bit (if not available: use one of the
cage jacks cut from the original MS11 strips);
• Carefully remove the drill bit (or cage jack), place the wrapped wire around the cage jack for pin 7 and sol-
der it. Cut the wire to leave a length of ~5” (12.5cm). Repeat for pins 9 and 10.
• Now remove the unsoldered cage jacks with the carrier strip segments. Note that the cage jacks of pins 7,
9, and 10 remain in the PCB.
• Continue with assembly step 3 of EK57’s datasheet and then perform the following (DO NOT EXECUTE
steps 4 to 17 of EK57’s datasheet yet).
Figure 1: 1.5mm drill bit used as wrap tool Figure 2: Wires connecting to pins 7, 9, and 10
after soldering

EK57
2EK57U-Addendum Rev B
Assembly Instructions (Continued)
• Not included in the kit, but ‘necessary’ to evaluate the extra functionality of MP118 are Two normally-off
pushbutton switches, like (but not necessarily the same as) Digi-Key Part# P8011S-ND.
• The listed component is an example only. Other components with similar functionality can just as well be
used.
• These switches come with 4 pins, which are internally connected as two pairs. Solder the two switches on
the bread boarding area and connect one of the pin pairs of each switch to ground and the other pin pairs
to the wires coming off pins 9 and 10 respectively (see previous steps).
ADDITIONAL COMPONENTS IN CIRCUIT DIAGRAM
Figure 3 below shows how the additional components are connected to MP118.
Figure 3: EK57’s Circuit Diagram with Pushbutton Switches for MP118

EK57
EK57U-Addendum Rev B 3
After assembly of the switches the PCB could look like this:
Figure 4: EK57 PCB Component Side
• All circuit connections have been made on the PCB’s component side. This is not a necessity.
• Compensation capacitor Cc is socketed to allow easy value changes.
• +Vb has been bridged to the +Vs. Not shown in this Picture is the same has been done to -Vb and -Vs. This
means +/-Vb = +/-Vs, and it's not necessary anymore to jumper these supply rails externally via the
(screw) terminal strip. THESE JUMPERS NEED TO BE RMOVED IN CASE ONE WANTS TO USE VBOOST
OPTION! (refer to MP118 datasheet).
• The switches have been labeled to prevent mistakes.
FINISHING THE ASSEMBLY
EK57 comes with two large current sense resistors, which can be mounted on a heatsink. The values of
these are 50 mΩand 100 mΩ. Since MP118’s over-current trip point is given by
The two delivered resistors will yield trip points of 13A and 6.5A respectively. If one of these is OK, con-
tinue with steps 4 through 17 of EK57’s datasheet. If not, based on the equation above, alternative resistor
values can be chosen to set a different over-current trip point. When selecting RLIM it should be a type with
low inductance and its wattage rating should be at least
Please note that the PCB has been laid out for a Kelvin connection to the sense resistor (check the 2 sense
resistors supplied with EK57, these have 4 pins!); an alternative resistor should connect to two adjacent PCB
through holes on one side and to two other adjacent holes on the other side. Please also note that, depend-
ing on the power dissipation in the current sense resistor RLIM, it does not always need to be heatsinked! For
the functional test below, the over-current trip point is set to 1.2A by two 0.27 Ω/1W Allen-Bradley carbon-
composite resistors in series (without heatsink).
• Finish steps 7 through 17 of EK57 datasheet.
ISD
0.65
RLIM
------------
=A
1.5 ISD
2RLIM
W

EK57
4EK57U-Addendum Rev B
FUNCTIONAL TEST
1. Extra needed components:
1. 1 resistor 1 kΩ, 2 resistors 10 kΩ
2. 1 ceramic capacitor 10pF / 200V
3. 2 resistors 0.27 Ω/ 1W, low inductance (values may be different, but remainder of test is based
on this value)
4. Load resistance, 10 Ω, 15W (preferably more power dissipation)
2. For the purpose of this test, realize an inverting amplifier with a gain of -20 by:
1. Connecting a 1 kΩinput resistor between the BNC input terminal and pin 34 (inverting input) of
MP118.
2. Connecting the non-inverting input of MP118 (pin 33) to ground.
3. Connecting two 10 kΩfeedback resistors in series between the circuit’s output terminal (OUT)
and the inverting input of MP118 (pin 34).
4. Connecting a 10pF (200V) ceramic (phase compensation) capacitor between pins 5 and 6 of
MP118.
3. Use 2 resistors of 0.27 Ω/ 1W (or other values, but then the test criteria will change, too) to set an over-
current trip point of ~1.2A. Remember to connect (solder) each side of the current sense resistor (or of
the series combination) to two adjacent holes in the PCB, where RLIM should go (also see Figures 6 and 7).
4. The Circuit Diagram is shown in figure 5:
Figure 5: Complete Circuit Diagram, ready for functional testing

EK57
EK57U-Addendum Rev B 5
5. The EK57 now looks like this (Figures 6 and 7):
Figure 6: Complete EK57 PCB, ready for functional test (banana jacks for easy connection only)
Figure 7: Details of socketed RI and RF , as well as of RLIM(in background)

EK57
6EK57U-Addendum Rev B
6. Connection to test and measurement equipment;
1. Set up a dual 30V @ ≥2A lab power supply for -15V, GND, +15V (for symmetric supply voltages).
Switch the supply off and connect to +Vs (+15V), GND, -Vs (-15V) on the screw terminal strip.
Make sure there is a single ground point for all of these supplies.
2. Set a function generator to produce a 1 kHz, sinusoidal, 1Vp-p (centered around 0V) output
signal. Switch the output off and connect to the kit via a BNC cable.
3. Set up a scope to monitor the input and output signals of the amplifier circuit.
7. Initial Test
1. Leave the amplifier unloaded.
2. While looking at the scope, switch the power supplies on, then give the input signal.
3. The scope should show a 1 kHz, sinusoidal, 20Vp-p output signal, centered around 0V, 180° out of
phase with the input signal.
4. Push the SHUT-DOWN (SD) button, the output signal should instantly become 0V.
5. Push the RESET (RST) button, the output should take its previous shape (step G.c.) again.
6. Switch the input signal and the power supplies off.
8. Over-Current Test
1. Set the function generator to 500mVp-p.
2. Load the amplifier with a 10 Ω, ≥15W resistor (connect between OUT and GND on TS1).
3. Switch the power supplies on and give the input signal. Now slowly raise the amplitude of the
input signal while observing the output amplitude. When the output amplitude reaches 12V the
over-current protection should trip, rendering the output voltage at 0V. The experienced trip
point may differ due to tolerances in RLIM and the negative temperature coefficient (-2.2mV/°C)
of the factor 0.65 in the earlier given formula for ISD.
4. Lower the input amplitude and press the RESET (RST) button to turn the amplifier back on again.
5. Switch off the input signal and the power supplies.
9. Temperature Sensor Test
1. During the tests above, the temperature of MP118 can be monitored by measuring the voltage at
the SPARE-labeled TS1 screw terminal.
2. To connect a volt meter: the positive terminal should be connected to the “SPARE” screw
terminal (green banana jack in Figure 6), the negative terminal to “GND” (black banana jack in
Figure 6). The temperature can then be calculated as follows:
c. The over-temperature protection is set to trip around 100°C. This means a VTEMP of
approximately 1.278V. To test this, higher voltage / current power supplies and higher wattage
loads are needed, or the amplifier has to be left uncooled when loading it. However, care should
be taken not to make the event too fast, as the thermal protection has a certain delay. If the
thermal protection has tripped, the amplifier can be brought back to life by pressing the RESET
(RST) button, keeping in mind there is an 8°C hysteresis, i.e. the amplifier has to cool down at
least 8°C before it can resume functioning.
If EK57 + MP118 perform well in above tests the evaluation kit is now ready to be adapted to the cus-
tomer’s specific requirements and more application related evaluation. If the kit fails in any of the above test,
the assembly should be thoroughly checked for shorts, disconnects, wiring errors, the test & measurement
equipment should be checked for wrong settings and other errors. In case the problem stays, please contact
Apex Support via http://www.apexanalog.com/technical-product-support/#general. Please make sure to be
as detailed as possible when requesting for support.
T25
VTEMP 2.298–
0.0136
------------------------------------
–= C

EK57
EK57U-Addendum Rev B 7
NEED TECHNICAL HELP? CONTACT APEX SUPPORT!
For all Apex Microtechnology product questions and inquiries, call toll free 800-546-2739 in North America. For
inquiries via email, please contact apex.support@apexanalog.com. International customers can also request
support by contacting their local Apex Microtechnology Sales Representative. To find the one nearest to you,
go to www.apexanalog.com
IMPORTANT NOTICE
Apex Microtechnology, Inc. has made every effort to insure the accuracy of the content contained in this document. However, the information is
subject to change without notice and is provided "AS IS" without warranty of any kind (expressed or implied). Apex Microtechnology reserves the right
to make changes without further notice to any specifications or products mentioned herein to improve reliability. This document is the property of
Apex Microtechnology and by furnishing this information, Apex Microtechnology grants no license, expressed or implied under any patents, mask
work rights, copyrights, trademarks, trade secrets or other intellectual property rights. Apex Microtechnology owns the copyrights associated with the
information contained herein and gives consent for copies to be made of the information only for use within your organization with respect to Apex
Microtechnology integrated circuits or other products of Apex Microtechnology. This consent does not extend to other copying such as copying for
general distribution, advertising or promotional purposes, or for creating any work for resale.
APEX MICROTECHNOLOGY PRODUCTS ARE NOT DESIGNED, AUTHORIZED OR WARRANTED TO BE SUITABLE FOR USE IN PRODUCTS USED FOR LIFE
SUPPORT, AUTOMOTIVE SAFETY, SECURITY DEVICES, OR OTHER CRITICAL APPLICATIONS. PRODUCTS IN SUCH APPLICATIONS ARE UNDERSTOOD TO BE
FULLY AT THE CUSTOMER OR THE CUSTOMER’S RISK.
Apex Microtechnology, Apex and Apex Precision Power are trademarks of Apex Microtechnology, Inc. All other corporate names noted herein may be
trademarks of their respective holders.
Table of contents
Other Apex Digital Motherboard manuals

Apex Digital
Apex Digital EK11 User manual
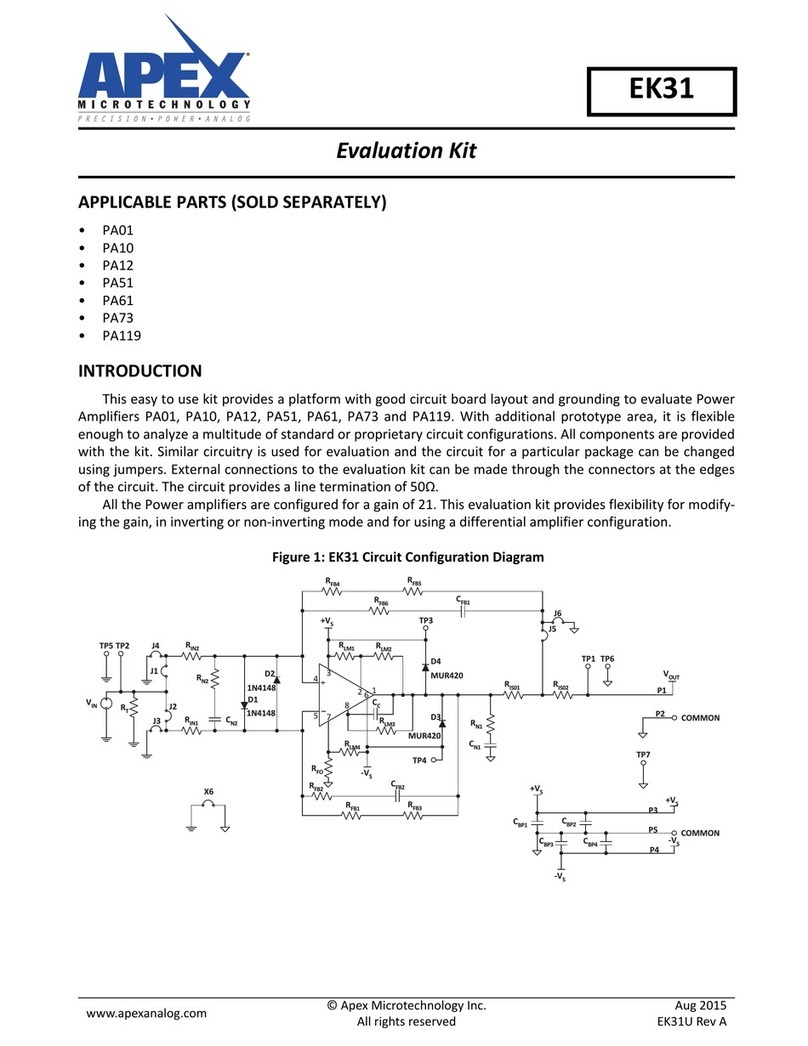
Apex Digital
Apex Digital EK31 User manual
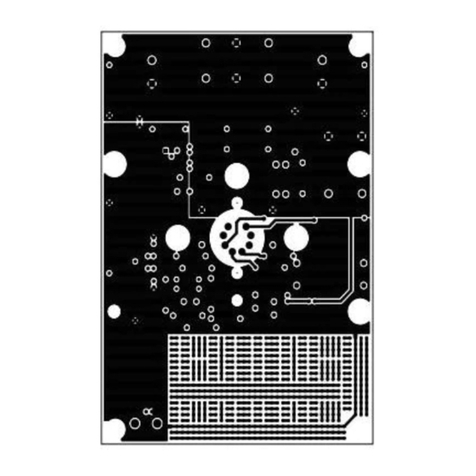
Apex Digital
Apex Digital EK30 User manual
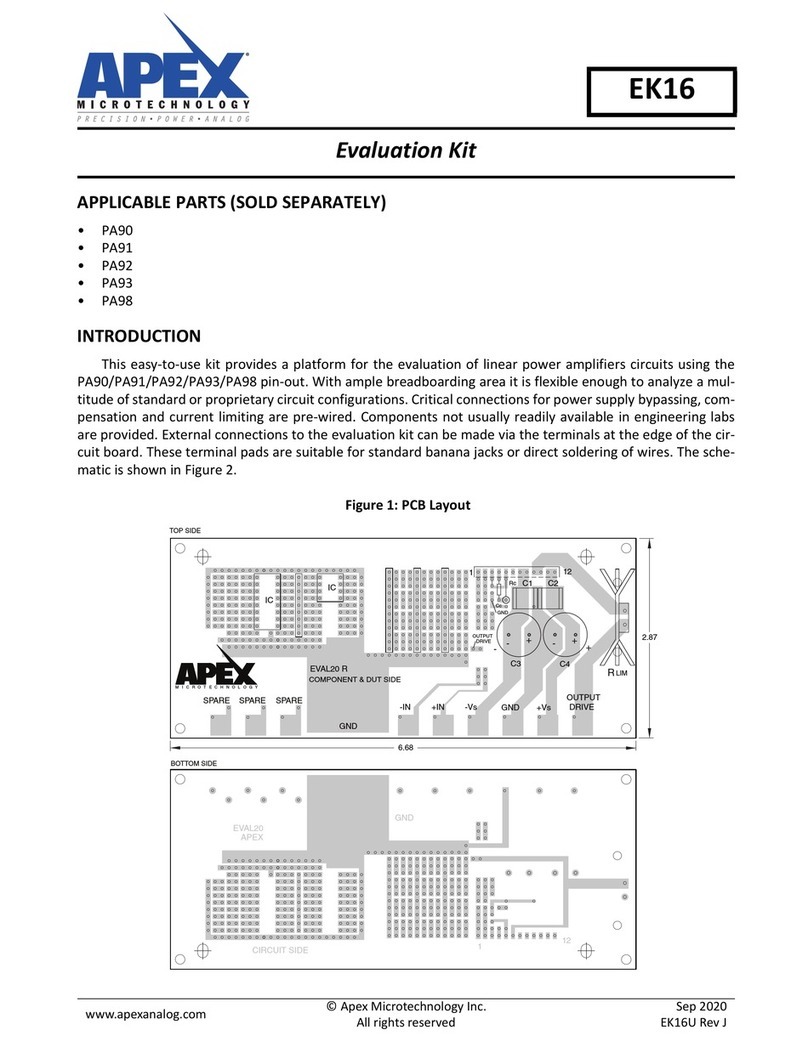
Apex Digital
Apex Digital EK19 User manual
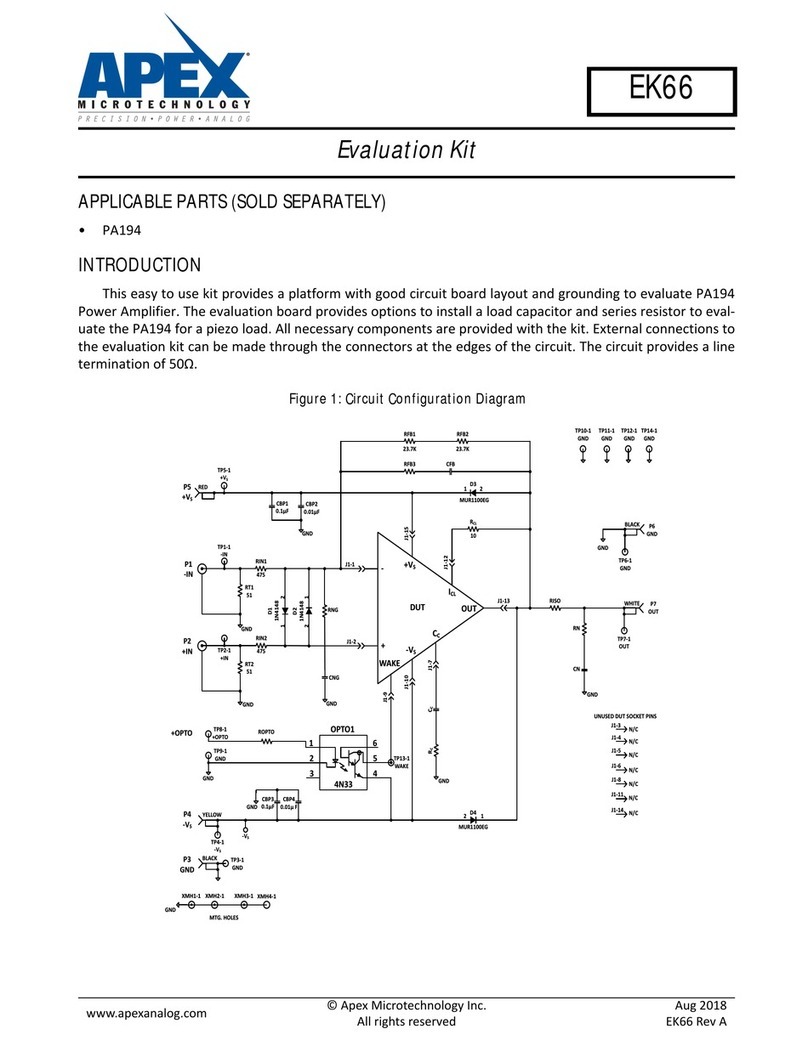
Apex Digital
Apex Digital EK66 User manual
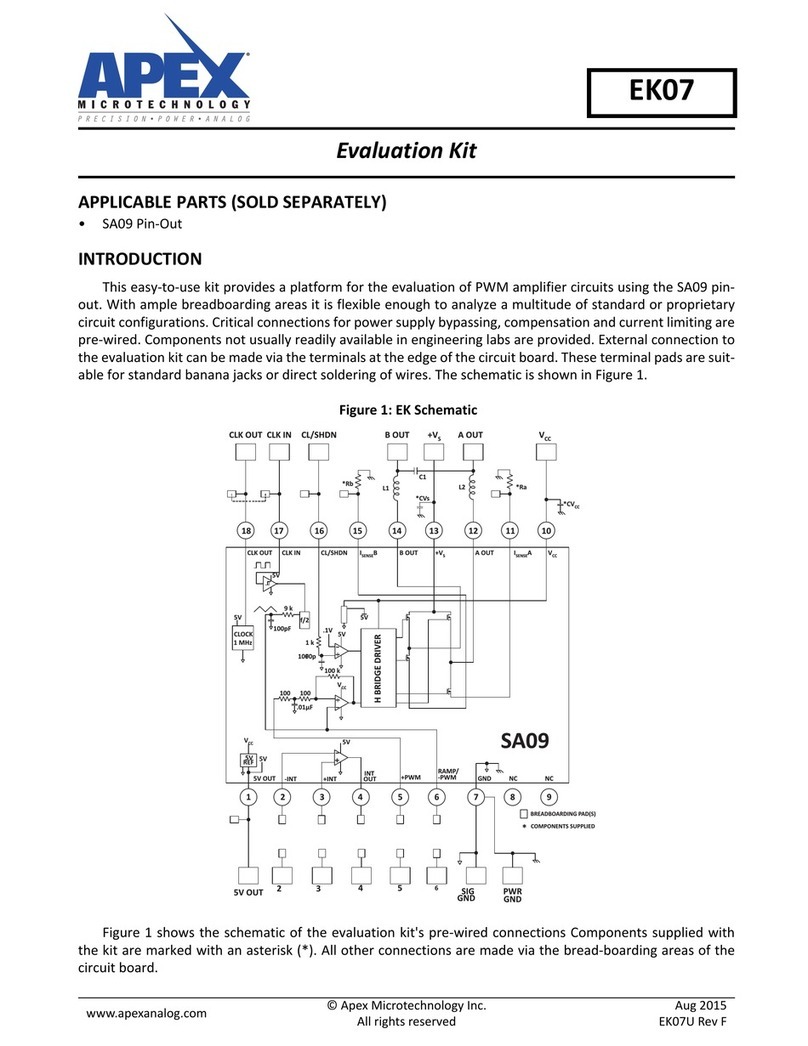
Apex Digital
Apex Digital EK07 User manual
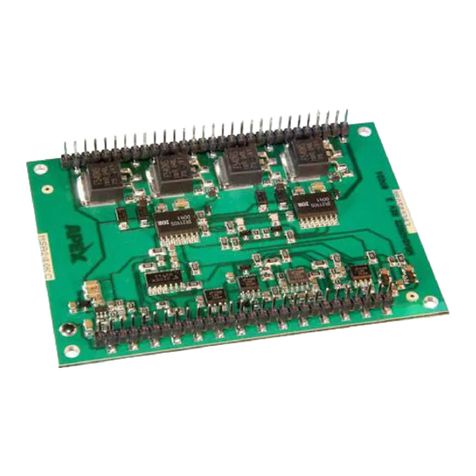
Apex Digital
Apex Digital MSA240KC User manual
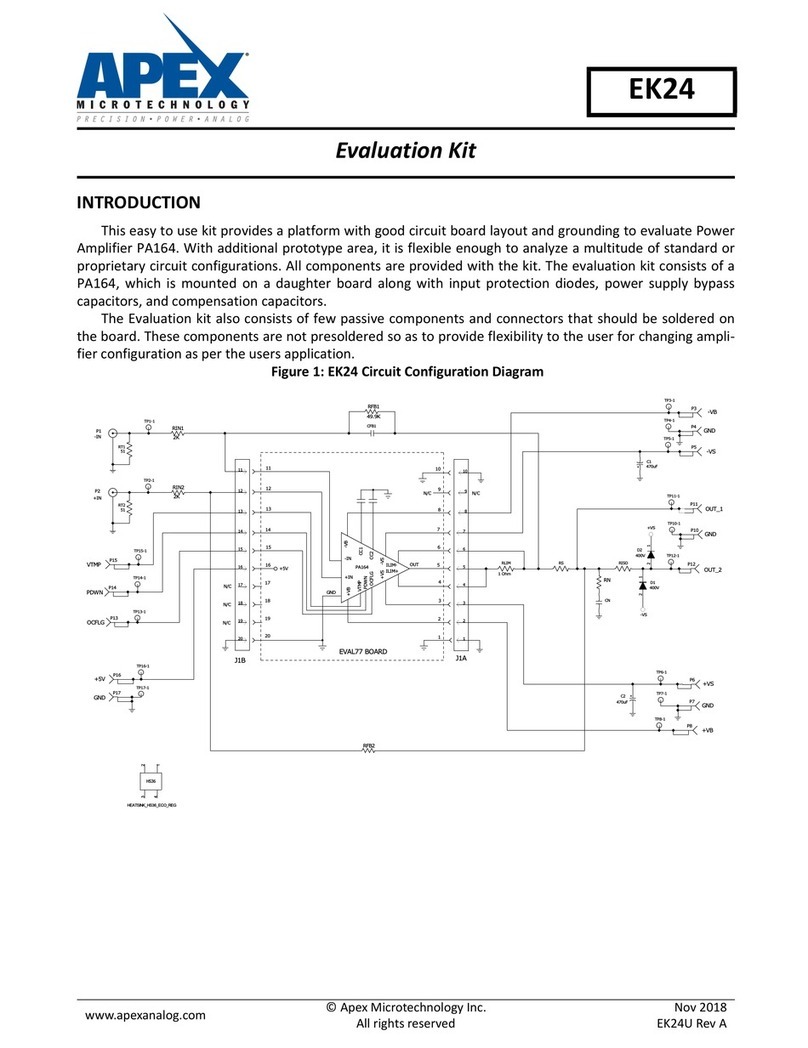
Apex Digital
Apex Digital EK24 User manual
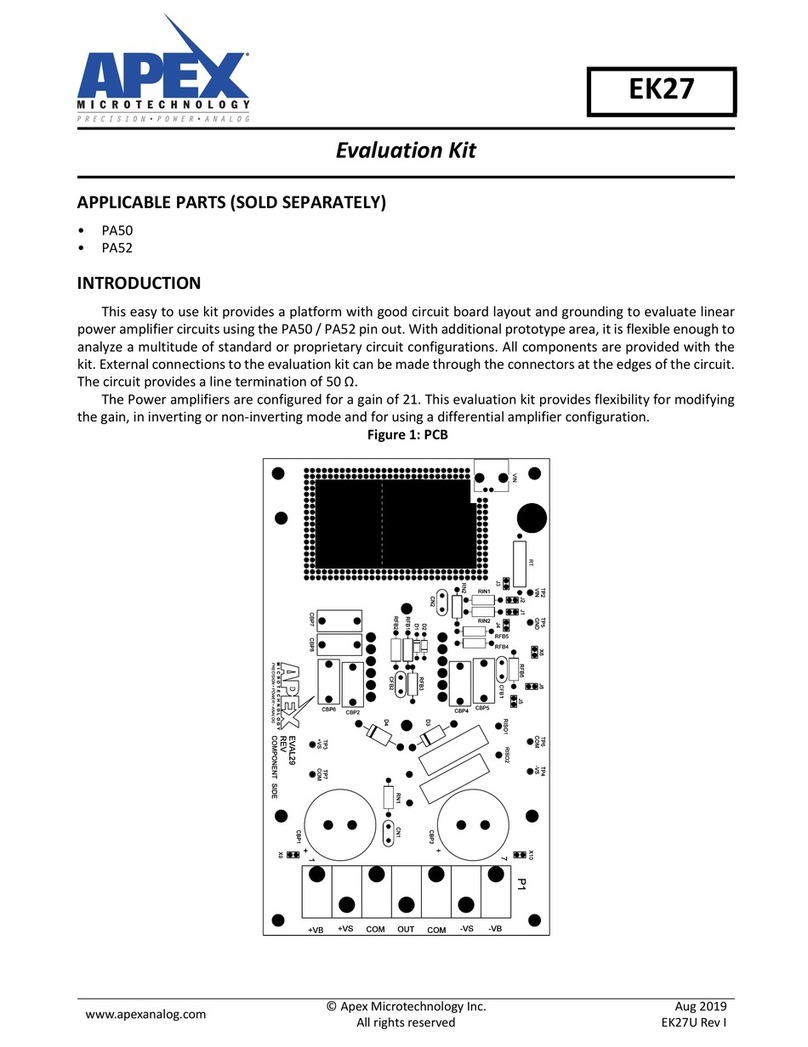
Apex Digital
Apex Digital EK27 User manual
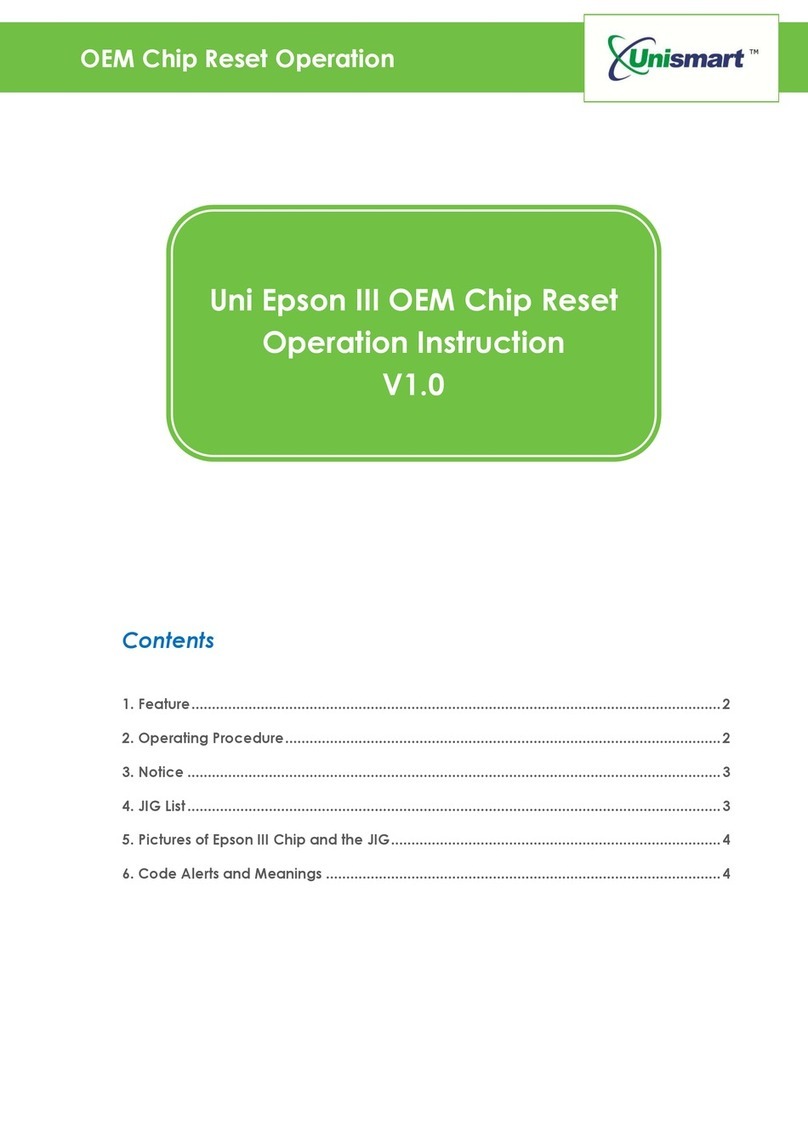
Apex Digital
Apex Digital Unismart Uni Epson III OEM Chip Reset Technical manual