Apex Instruments XC-3D55 User manual

919-557-7300 or 800-882-3214
Fax 919-557-7110
DIMENSIONS ARE IN INCHES
TOLERANCES:
FRACTIONAL
ANGULAR: MACH
1 BEND
1
TWO PLACE DECIMAL
.010
THREE PLACE DECIMAL
.005
INTERPRET GEOMETRIC
TOLERANCING PER:
MATERIAL
FINISH
CREATED
CHECKED
ENG APPR.
MFG APPR.
Q.A.
COMMENTS:
DATE
NAME
TITLE:
SIZE
DWG. NO.
REV
WEIGHT:
SCALE:
UNLESS OTHERWISE SPECIFIED:
SHEET 1 OF 1
DRAWING NOT TO SCALE
SBB 9.26.17
A
XC-3D55
OPERATOR MANUAL
XC-3D55
3D Flow Measurement Console
Operators Manual
Note: Some pictures
May not reflect actual
finished product

Copyright © 2017 Apex Instruments, Inc. All Rights Reserved
This manual may not be, in part or in whole, reproduced, transmitted, transcribed, stored in a retrieval
system, or translated into any other language or computer language, in any form or by any means,
whether it be electronic, magnetic, manual, mechanical, optical or otherwise, without the prior written
consent of Apex Instruments, Inc. 204 Technology Park Lane, Fuquay-Varina, NC 27526.
Warranty
This equipment is sold subject to the mutual agreement that it is warranted by Apex Instruments, Inc.
free from defects of material and of construction, and that Apex Instruments, Inc. liability shall be
limited to replacing or repairing at our facility (without charge, except for transportation), or at
customer plant at our option, any material or construction in which defects become apparent within
one year from the date of shipment, except in cases where quotations or acknowledgments provide
for a shorter period. Components manufactured by others bear the warranty of their manufacturer.
This warranty does not cover defects caused by wear, accident, misuse, neglect or repairs other than
those performed by Apex Instruments, Inc. at our service center. We assume no liability for direct or
indirect damages of any kind and the purchaser by the acceptance of the equipment will assume all
liability for any damage which may result from its use or misuse.
We reserve the right to employ any suitable material in the manufacture of our apparatus, and to
make any alterations in the dimensions, shape or weight of any parts, in so far as such alterations do
not adversely affect our warranty.
Important Notice
This instrument provides measurement readings to its user, and serves as a tool by which valuable
data can be gathered. The information provided by the instrument may assist the user in eliminating
potential hazards caused by the utilized process; however, it is essential that all personnel involved in
the use of the instrument or its interface, with the process being measured, be properly trained in the
process itself, as well as all instrumentation related to it.
The safety of personnel is ultimately the responsibility of those who control process conditions. While
this instrument may be able to provide early warning of imminent danger, it has no control over
process conditions, and it can be misused. In particular, any alarm or control systems installed must
be tested and understood, both as to how they operate and as to how they can be defeated. Any
safeguards required such as locks, labels, or redundancy, must be provided by the user or specifically
requested of Apex Instruments, Inc. at the time the order is placed.
Therefore, the purchaser must be aware of the hazardous process conditions. The purchaser is
responsible for the training of personnel, for providing hazard warning methods and instrumentation
per the appropriate standards, and for ensuring that hazard warning devices and instrumentation are
maintained and operated properly.
Apex Instruments, Inc. cannot accept responsibility for conditions beyond its knowledge and control.
No statement expressed or implied by this document or any information disseminated by the
manufacturer or its agents, is to be construed as a warranty of adequate safety control under the
user‘s process conditions.
XC-51 SAMPLING CONSOLE
Revision:01 Page 1 of 23 9/26/2017

Revision:01 Page 2 of 23 9/26/2017
Pages
Page 1.........Warranty and Important Notice
Page 2.........Table of Contents and Figures
Page 3.........Introducton
Page 4.........Recommended XC-3D55 System Accessories
Page 5.........Recommended Calibration and Leak Check Accessories
Page 6.........Components
Page 7.........Electrical System Components
Page 8.........Electrical System Schematic
Page 9.........Plumbing Schematic
Page 10.......Pitot Heads
Page 11-12..System Assembly
Page 13.......Recalibration and Calibration
Page 14.......System Leak Check
Page 15-16..System Calibration Checks
Page 17.......Back Purging System
Page 18-21..Red Lion Cub 5 Programming Guide
Page 22.......Methods Comments
Figures
Page 4 Figure 1 .......Complete XC-3D55 System
Page 5 Figure 2.......Calibration and Leak Check Accessories
Page 6 Figure 3.......Console Components
Page 7 Figure 4.......Electrical System Components
Page 8 Figure 5.......Electrical System Schematic
Page 9 Figure 6.......Plumbing Schematic
Page 10 Figure 7.......Prism-Shaped 3D Pitot Head
Page 10 Figure 8.......Type-S Pitot Head
Page 13 Figure 9.......Reference Inclinometer Calibration
Page 23 Figure 10.....Method 1 Traverse Point Determination Marks
Page 23 Figure 11.....Probe Yaw Orientation Positive/Negative

Introduction
During the late 1990’s, the US EPA developed three new methods to account for these different
variables in flow measurement. These new methods allow the tester to account for velocity drop-off
near the stack or duct wall and the yaw and pitch angles of flow. The primary users of the new
methods will be owners and operators of utility units subject to the Acid Rain Program under Title IV
of the Clean Air Act. Flow rates must be used to determine the units’ SO2 and NOX mass emissions
and heat inputs. The XC-3D55 was designed to be utilized with Methods 2, 2F, 2G and 2H.
US EPA Method 2G allows Type S probes and 3–D probes (DAT and spherical) to be rotated into the
flow to measure total velocity pressure and yaw angle. The yaw angle is used to calculate ‘‘near-
axial’’ velocity from total velocity.
Method 2F allows 3–D probes to be used to measure total velocity, yaw angles, and pitch angle
pressure. Pitch angle pressure is used with a calibration curve to determine pitch angle. Yaw and
pitch angles are used to calculate axial velocity from total velocity.
Method 2H provides a procedure for accounting for wall effects by using either a default wall effects
adjustment factor or one derived from near wall measurements. The wall effects adjustment factor is
used with the Method 2-, 2G- or 2F-calculated velocity to derive a wall effects adjusted velocity.
Volumetric flow rate is calculated by multiplying the average flue gas velocity by the stack or duct
cross-sectional area. Yaw and pitch characterize the extent ot which flue gas is not flowing straight
out of a stack or duct. From the standpoint of a tester facing a vertical stack, a yaw angle is
represented by flow movement to the left or right of the stack centerline. The pitch angle is
represented by flow movement toward or way from the tester.
Some amount of yaw and pitch angle and wall effects are almost always present in utility stacks or
ducts. Flow disturbances produce flue gas flow that swirls and /or bounces off stack or duct walls.
Determining axial velocity without accounting for the drop-off near the stack or duct wall can result in
overstating the actual axial velocity. Thus, when enough yaw, pitch or wall effects are present,
Method 2 can overstate the measured flue gas velocities and thus, volumetric flow, because it only
allows the total velocity to be measured and does not account for yaw angles, pitch angles, or wall
effects. If the test method overstates flow rate, a flow rate monitor calibrated using the test method
may also overstate flow rate and result in overstated sulfur dioxide emissions and heat input.
Revision:01 Page 3 of 23 9/26/2017

Unpacking and Equipment Check
The system is carefully packaged to reduce the likleyhood of damage in transit. Unpack the contents
carefully, saving all the packing material until the parts have been examined for shipping damage.
Check each item against the packing list shown below. If any item is missing, notify your supplier or
Apex instruments immediately.
Recommended XC-3D55 System Accessories
Quantity Part Number Description
1 XC-3D55 3-D Flow Measurement Console
1 Pitot Type 2D, 3D or Type S
1 U-PTX-#-# 3-D Pitot Sheath Extension, 2 in. Dia. Sheath, 1/4 in. TFE Lines
1 PF-346XT32S Universal Probe Extension, Flange Fits, 3, 4 & 6 in. Ports
1 32M/32B-B 2 in. Bored Brass Bushing, 2 in. MNPT with 2.035 in. Bore
1 UINC-3D-# 3-D Umbilical Cord, Specify Length in ft., Inclinometer Pod
1 32/16PTXC 2 Piece probe collar, 2” x 1” Stainless Steel
1 32PTX-# Probe Extension, 2” Diameter, Stainless Steel, Specify Length in ft.
Figure 1 Complete XC-3D55 System
XC-3D55
UINC-3D-
3DPT4
32/16PTXC
32M/32B-B
32PTX-
32PTX- T4Q4
PF-346XT32S
U-PTX- -
32M/32B-B
TYPE-S
Pitot Head
Revision:01 Page 4 of 23 9/26/2017

Recommended Calibration and Leak Check Accessories
Part # Description
DHM-M100 Meriam Digital Hand-Held Manometer, 0-28 inch H2O Selectable Range, English/Metric
A-396A Dwyer Calibration Pump, Generate Pressure and Vacuum, NIST 0” to 5” H2O
M5C-22 Thermocouple Simulator Source
12-1057 Digital Display Reference Inclinometer
Speed Square
Probe Leak Check Plugs
QC-F4-SS Female Quick Connect with Cap
QC-F4-SS Male Quick Connect
TPU-4/2 1/8ID X 1/4OD Tubing, Polyurethane
CLP-2P Probe clamp, 2 halves
Figure 2 Calibration and Leak Check Accessories
Revision:01 Page 5 of 23 9/26/2017

Main Power Switch
(M-CBR15A-M)
Velocity Pressure Display
(M-CUB5PB00)
Probe Temperature
Thermocouple Connection
(TC-PJR)
Inclinometer Amphenol Connection
(AM-T3111)
Probe Connection Quick Connects
(QC-F4M2N-SS (5x) Non-Valved Flow)
IEC Power Input Receptacle
Pitch Pressure Display
(M-CUB5PB00)
Null Angle Magnehelic
(MAG-2301)
Yaw Angle Display
(TOT4-36X72BL)
Probe Temperature Display
(TC-CUB5TCB0)
Calibration Quick Connects
(QC-F4M2N-SS (5x) Valved)
Figure 3 Console Components
Inclinometer
Red Lion Display
Magnehelic
Transducers
Power Supply
MAG-2301 Magnehelic Gauge, +-.5 inch H2O, Zero Center
Magnehelic® Differential Pressure Gauge indicates Positive, Negative or Differential
Accurate within 2% range 0.5-0-0.5" w.c., minor divisions .02
M-CUB5PB500 Process Meter, 0-10VDC supply
TC-CUB5TCB0 Display, tc, pnl, led,120/240V
TOT4-36X72BL Totalizer, quadrature, 36x72 din with back light
M-PSRD35A Power Supply, 35W, 12V@1 Amp, 5V@4 Amp, Input: 100-240VAC
M-DP-B5/B5 Populated Printed Circuit Board with Two 5" H2O Differential
Transducers, Mounted in Plastic Enclosure. 12VDC Supply
The INC-S6-1800 incremental inclinometer contains a high resolution digital tilt
sensor that reports the angle of the probe with respect to gravity in degrees with
real-time TTL outputs. The weight is placed on one side of a wheel assembly
causing it to remain stationary with respect to gravity. Internal magnetic damping
assures fast response times while minimizing oscillations and ringing. Requires
single +5VDC supply
Components
Revision:01 Page 6 of 23 9/26/2017

The XC-3D55 3-D Flow Measurement console is factory-configured for 120VAC/60Hz and
240VAC/50Hz electrical power. The Electrical Schematic for the console is presented on page 5.
A front panel-mounted circuit breaker rocker switch activates the Main Power and power supply. The
power supply energizes the velocity pressure and pitch differential pressure transducers, the
inclinometer (yaw measurement device) and the temperature display.
A 4-pin amphenol-style circular connector is mounted on the side of the console is used to provide
power to and signal from the remote inclinometer sensor. The standard size, female, Type K Stack
Temperature thermocouple jack is also mounted on the side of the console.
Output signals are included for the Stack Thermocouple, Velocity Pressure, Yaw Angle and Pitch
Angle. All signals are direct current, voltage-based. The specific outputs are listed on the electrical
schematic and in the specifications listed in Table 2.
Process meters are utilized to convert the direct current voltage (VDC) output pulses from the various
sensors into appropriate engineering units, such as inches/millimeters of water or degrees of rotation,
etc. The process meters display the P1-P2 velocity pressure and the P3-P4 pitch angle pressure. The
standard units of measurement are English units in “ H2O and ° Fahrenheit. Metric units will be
displayed in mm H2O and ° Celsius are available. The Yaw Angle is displayed via a high resolution
indicator where 1 pulse equals 0.1°.
The process meters, transducers and counter have been setup and calibrated at Apex
Instruments utilizing appropriate standards. Read this Operators Manual before making any
adjustments to the process meters, transducers or inclinometer.
Main Power Switch
(M-CBR15A-M)
Velocity Pressure Display
(M-CUB5PB00)
Probe Temperature
Thermocouple Connection
(TC-PJR)
Inclinometer Amphenol Connection
(AM-T3111)
IEC Power Input Receptacle
Pitch Pressure Display
(M-CUB5PB00)
Yaw Angle Display
(TOT4-36X72BL)
Probe Temperature Display
(TC-CUB5TCB0)
Figure 4 Electrical System Components
Electrical System Components
Revision:01 Page 7 of 23 9/26/2017

+12VDC
+5VDC
Line
Neutral
Ground
Common
Pitch (+)
9-32VDC
Common
Pitch (-)
Pressure (+)
Pressure (-)
1
2
3
M-PSRD35A
Inclinometer
Amphenol
Probe
Temperature
Display
Velocity
Pressure
Display
Pitch
Angle
Display
Pitch
Pressure
Display
M-DP-B5/B5
Main Power
Figure 5 XC-3D55 Electrical Schematic
Electrical System Schematic
Revision:01 Page 8 of 23 9/26/2017

A1
P1
A2
A3
A4
A5
P2
P3
P4
P5
-.5 .5
0
MAGNEHELIC
P1+
P2+
P1-
P2-
+
-
TRANSDUCERS
QUICK CONNECTS
2/12/2015
Plumbing Schematic
The plumbing subsystem consists of leak-free tubing and fittings allowing for accurate pressure
measurements. Two pressure transducers measure the velocity head (P1-P2) pressure and
the pitch (P4-P5) and are connected to LED process meters scaled and calibrated to the
appropriate engineering units. A Magnehelic™ differential pressure gauge is utilized to indicate
the Yaw Null Pressure (P2-P3).
Figure 6 XC-3D55 Plumbing Schematic
Revision:01 Page 9 of 23 9/26/2017

Pitot Heads
Several types of pitots may be used to meet method criteria.
The 3-D Pitot (Figure 6) probe assembly consists of a 5-hole prism-shaped head machined from
stainless steel. The extensions are high-temperature 1/8” brazed tubing to the pitot head. The 1” OD
extension section is then welded to pitot head.
The pitot has been calibrated per the US EPA Method 2F specifications and a copy of the
calibration is included. The unique serial number of the pitot is machined in the head. If an
additional copy of the calibration is needed, please contact Apex Instruments,Inc at 877-726-3919.
The Type-S Pitot (Figure 7) is designed to measure gas velocities. When the pitot is faced into the
gas stream, flow and the pressure difference between the two ports equates to the velocity pressure.
This differential velocity pressure is measured with liquid manometers or electronic pressure
transducers. The Baseline coefficient value for the Type-S pitot is 0.84.
The economically priced Type-S pitot’s compact design allows it to fit easily into sampling ports. Its
large openings resist plugging in particulate laden and saturated gas streams and maintains calibration
in harsh environments. Another advantage of the Type-S pitot is high differential pressure readings are
beneficial in low velocity gas streams and are suitable for determining cyclonic flow and measuring
yaw-angle of the velocity vector.
P5
P2
P4
P1
P3
TC
Figure 7 Prism-Shaped 3-D Pitot Head Figure 8 Type-S Pitot Head
6PT- -T032M
Revision:01 Page 10 of 23 9/26/2017

System Assembly
1) Connect the 1/4 inch compression fittings of U-PTX-# together to connect the stainless tubes of the
pitot tube head (3DPT4) to the PTFE lines. Connect the Thermocouple connectors.
2) Slide the pitot tube head through the extension (32PTX-##T4Q4) into and through the clamping
area of the extension.
3) Rotate the pitot head so Velocity Pressure P1 faces the direction of stack flow.
4) Place the collar (32/16PTXC) into the probe extension and over the pitot probe. Check P1 Position.
5) Put anti-seize on the four screws and insert into the collar.
6) Securely tighten the four screws.
7-8-9) With the assembled pitot tube head and the extension assembled, with Velocity Pressure P1
Port facing directly into the stack flow, mark the pitot head (as shown) with the edge of the fixed
clamp. This mark is established to ensure the probe does not rotate within the extension during use.
2
13
5
46
8
7
Apply Anti-Seize
to Screw Threads
9Fixed Clamp
9Fixed Clamp
Mark Mark
Apply Anti-Seize
to Screw Threads
Revision:01 Page 11 of 23 9/26/2017

10) Slide the Inclinometer Pod with umbilical (UINC-3D-##) over the open end, opposite the pitot
clamp, of the extension (32PTXT32S).
11) Secure the assembly to the extension by turning the wing nuts
12) Screw the two Bored Brass Bushings (32M/32B-B) into the ends of the Universal Probe
Extension (PF-346XT32S).
13) Mount to the stack flange using the universal 3, 4 or 6 inch pattern mounting holes.
14) Slide the probe into the Universal Probe Extension (PF-346XT32S)
15) Connect the Umbilical/Pod Assembly (UINC-3D-##) to the XC-3D55 Console by connecting the
male quick connects to the female quick connects (P1 to P1, P2 to P2, P3 to P3, P4 to P4,P5 to P5).
16) Insert the male thermocouple plug into the female receptacle. Screw the amphenol (circular
connector) from the umbilical onto the inclinometer enclosure.
17) Insert the IEC end of the power cord into the mating receptacle on the front of the meter console.
18) Plug the male end into the appropriate power supply, 120VAC standard or 240VAC.
19) Switch the main power on from the front panel of the console.
10 11
12 13 14
15 16 17-1917-19
Revision:01 Page 12 of 23 9/26/2017

Calibration / Recalibration
DIGITAL
INCLINOMETER
DIGITAL
INCLINOMETER
30.0
-30.0
Side B (R2)Side A (R1)
Angle
- Negative + Positive
O
Angle
O
Figure 9 Reference Inclinometer Calibration
Recalibration
Recalibrate the probe either within 12 months of its first field use after its most recent calibration or
after 10 field tests, whichever occurs later. In addition, whenever there is visible damage to the probe
head, the probe shall be recalibrated before it is used again.
Calibration
Calibration of inclinometers pressure measuring devices, transducers and process meters/display are
required before initial use in the field.
To calibrate the inclinometer system, secure a calibration triangular block in a fixed position. Place the
inclinometer on one side of the block (side A) to measure the angle of inclination (R1). Repeat this
measurement on the adjacent side of the block (side B) using the inclinometer to obtain a second
angle reading (R2). The difference of the sum of the two readings shall be within ±2° of the known
angle.
Calibrate each pressure measuring device (except those used exclusively for yaw nulling) using the
three-point calibration procedure described in section 10.3.3 of US EPA Method 2F. The device shall
be recalibrated according to the procedure in section 10.3.3 no later than 90 days after its first field
use following its most recent calibration. At the discretion of the tester, more frequent calibrations
(e.g., after a field test) may be performed. No adjustments, other than adjustments to the zero setting,
shall be made to the device between calibrations. A single-point calibration check shall be performed
on each pressure-measuring device after completion of each field test. At the discretion of the tester,
more frequent single-point calibration checks (e.g., after one or more field test runs) may be
performed. It is recommended that the post-test check be performed before leaving the field test site.
The check shall be performed at a pressure between 50 and 90 percent of upper scale by taking a
common pressure reading with the tested probe and a reference pressure measuring device.
At each pressure setting, the readings made must agree to within ± 2% of full scale of the device
being calibrated or 0.5mm H2O (0.02in H2O), whichever is less restrictive. Differential pressure
devices not meeting this requirement shall not be used.
180° - |R1 + R2| = +/-2°
120°
Revision:01 Page 13 of 23 9/26/2017

System Leak Check
1) Connect the pressure measuring device and the pressure generating device. Connect the quick
connect from the pressure measuring device to the A1 Audit Port on the console.
2) Plug the P1 Velocity Pressure port on the pitot probe head
3) Pressurize the probe’s A1 pressure port until at least 7.6 cm H2O (3 in. H2O) pressure, or a
pressure corresponding to approximately 75 percent of the pressure-measuring device’s
measurement scale, whichever is less restrictive, registers on the device. The pressure shall remain
stable [±2.5 mm H2O (±0.10 in. H2O)] for at least 15 seconds.
Check the P2, P3, P4, and P5 pressure ports in the same fashion.
1 2 3
P3
P2
P4 P5
NOTE: The P1, P2, P3 Ports are larger than the P4, P5 Ports
2 different plugs are required
Revision:01 Page 14 of 23 9/26/2017

Calibration Checks of Pressure Measuring Devices
Prior to initial field testing, each pressure transducer requires a 3 point calibration check with a
precision manometer or a NIST traceable pressure source within a year of its most recent certification.
1) Disconnect the P1 and P2 lines from the console.
2) Press Reset to Zero.
3) Connect the pressure measuring device with pressure generator to P1 Port.
4) Vent all ports. Let devices settle. Record values for ZERO (50% of full range). Value must be
within +/- 0.03” H2O of ZERO. If reading FAILS, consult Transducer Calibration section of this manual
to recalibrate transducer.
5-10) If reading PASSES, Conduct calibration checks at -4.5, -3, -1.5, 1.5, 3, and 4.5” H2O.
3
4
8 9
3
4
8 9
2
12
1
771010
5566
Revision:01 Page 15 of 23 9/26/2017

Calibration Checks of Temperature Measuring Device
1) Connect the NIST traceable Reference Temperature generating device to the Thermocouple Jack
on the console.
2) Starting at ZERO °F, check the temperature display on the console at 0°F, 100°F, 200°F, 300°F,
400°F and 500°F. The console display temperature reading must be +/-5°F of the reference reading.
Should any reading FAIL the acceptable limit, consult the Calibration Procedures section.
4) Record the reading at each calibration check point.
Calibration Checks of Angle Measuring Device
1) Securely attach the calibrated Reference Inclinometer to the P1 Velocity Pressure orifice flat on the
Pitot Probe Head. Insure the UINC-3D-## assembly is securely attached to the Probe Extension and
Pitot..
2) Rotate the Reference Inclinometer to a desired position and record the angle.
3) Read the Yaw Angle indicated on the console display and press reset.
2
132
13
2
132
13
Revision:01 Page 16 of 23 9/26/2017

Back-Purging System
Method 2 Section 6.1.2 “...The static and impact pressure holes of standard pitot tubes are
susceptible to plugging in particulate-laden gas streams. Therefore, whenever a standard pitot tube
is used to perform a traverse, adequate proof must be furnished that the openings of the pitot tube
have not plugged up during the traverse period.
This can be accomplished by comparing the velocity head (Δp) measurement recorded at a selected
traverse point (readable Δp value) with a second Δp measurement recorded after "back purging" with
pressurized air to clean the impact and static holes of the standard pitot tube. If the before and after
Δp measurements are within 5 percent, then the traverse data are acceptable.
Otherwise, the data should be rejected and the traverse measurements redone. Note that the
selected traverse point should be one that demonstrates a readable Δp value. If "back purging" at
regular intervals is part of a routine procedure, then comparative Δp measurements shall be
conducted as above for the last two traverse points that exhibit suitable Δp measurements.”
If water or debris blockage is suspected, using an aspirator pump (squeeze bulb), apply a small
amount of pressure at the affected Audit Port (A1, A2, A2, A4, A5) Figure 10
NOTE: Take care in pressurizing the Audit Ports so the Transducer(s) will not be damaged.
If there still appears to be a blockage, disconnect the sample lines affected from the UINC-3D-## and
apply pressure to the affected sample line (P1, P2, P3, P4, P5) using an aspirator pump or some
other pressure generating device. Figure 11
Figure 10 Using A-350 pump to pressurize P1 Line
through A1 Port on the XC-3D55 Console
Figure 11 Using A-350 pump to pressurize P1 Line
coming directly out of Probe Extension
Revision:01 Page 17 of 23 9/26/2017

RedLion CUB5 Thermocouple Meter Set-Up(TC-CUB5TCB0)
Press and hold SEL for 2 seconds
Display will now alternate from Pro to NO screen Pro NO
Press RST once
Your screen should display 1- InP
Press SEL once
Display will now alternate from tyPE to tc-J
Press RST once to select Type-K ( )
Display will now alternate from tyPE to tc-
Press SEL until your screen displays End
Your screen should look like the following screen
The display will automatically revert to the standard displaying screen after displaying End
1- Inp
typE tc-j
tc-
typE
End
RedLion CUB5 Thermocouple Meter Offset Guide (TC-CUB5TCB0)
Press and hold SEL for 2 seconds
Display will alternate from Pro to NO screen
Press RST once
Your screen should switch to1- InP screen
Press SEL 5 times
Display will now alternate from OFSEt to 000
Press RST once to unlock the value and
allow user input
Press SEL to scroll through the digits and
press RST to change the values
Press RST on the left most digit to scroll
through the values or assign +/- value
Press SEL until your screen displays End
The display will automatically revert to standard displaying screen after displaying END.
1- Inp
000
End
OfsEt
-03
Sample Offset Value
Pro NO
-04
-08
-08
tc-
New Replacement
New Replacement and Offset for Calibration Purposes
Revision:01 Page 18 of 23 9/26/2017

RedLion CUB5 Process Meter Set-Up(M-CUB5PB00)
Press and hold SEL for 2 seconds
Display will now alternate from Pro to NO
Press RST once
Your screen should switch to 1- InP
Press SEL six times
Display will now alternate from StyLE to KeY
Display will now alternate from Key to APLY
Press SEL once to move to InP 1
Press RST once to unlock the value
Ensure P1 port is disconnected
The display will indicate the VOLTAGE being supplied to reach this value
Press SEL once to capture the reading and move to dSP 1
Press RST once to unlock the value for change
Note: 0.000 is the default value.
If = 0.000 skip next 2 steps If = 0.000 follow next 2 steps
Press RST until each value equals 0
Hold SEL for 2 seconds to move to Inp 2
Press RST once to unlock the value
Press RST once to unlock the value for change
Press SEL 3 times to select the correct digit
Press RST until value equals 5
Hold SEL for 2 seconds
Press SEL until End
Pro NO
1- Inp
StyLE Key
Key Aply
dsp 1
0.000
InP 1
0.000
0.000
0.000
inp 2
0.000
dsp 2
0.000 0.000
5.000
5.000
0.000
End
0.000
The display will automatically revert to standard displaying screen after displaying END.
Use the digital manometer and Dwyer pump to apply 5.000” of pressure to P1
The display will indicate the VOLTAGE being supplied to reach this value
Press SEL once to capture the reading and move to dSP 2
Press SEL to select the correct digit
New Replacement
Revision:01 Page 19 of 23 9/26/2017
Table of contents
Popular Music Mixer manuals by other brands
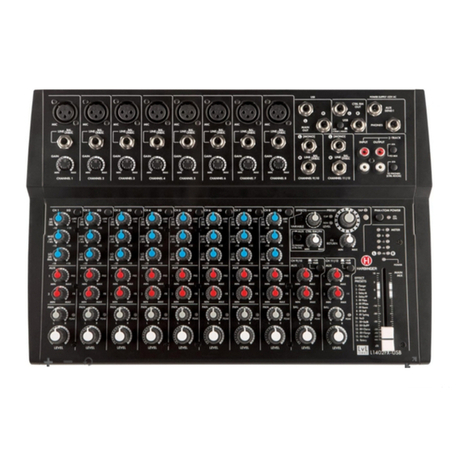
Harbinger
Harbinger L1402FX-USB user manual
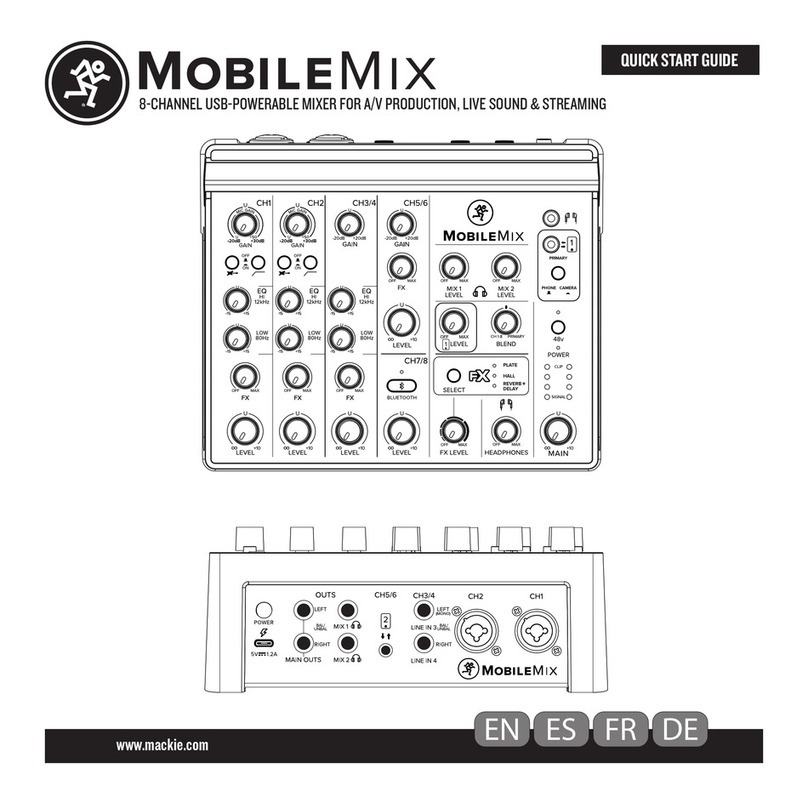
Mackie
Mackie MobileMix quick start guide
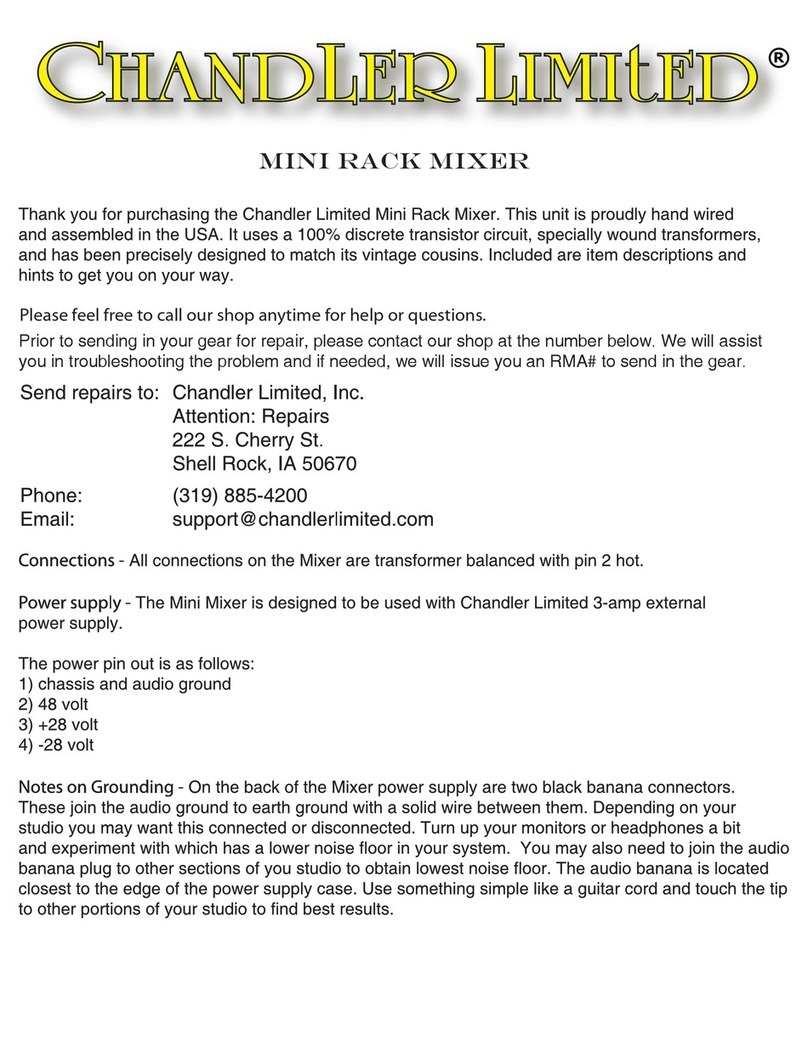
Chandler Limited
Chandler Limited Mini Rack Mixer Controls and features
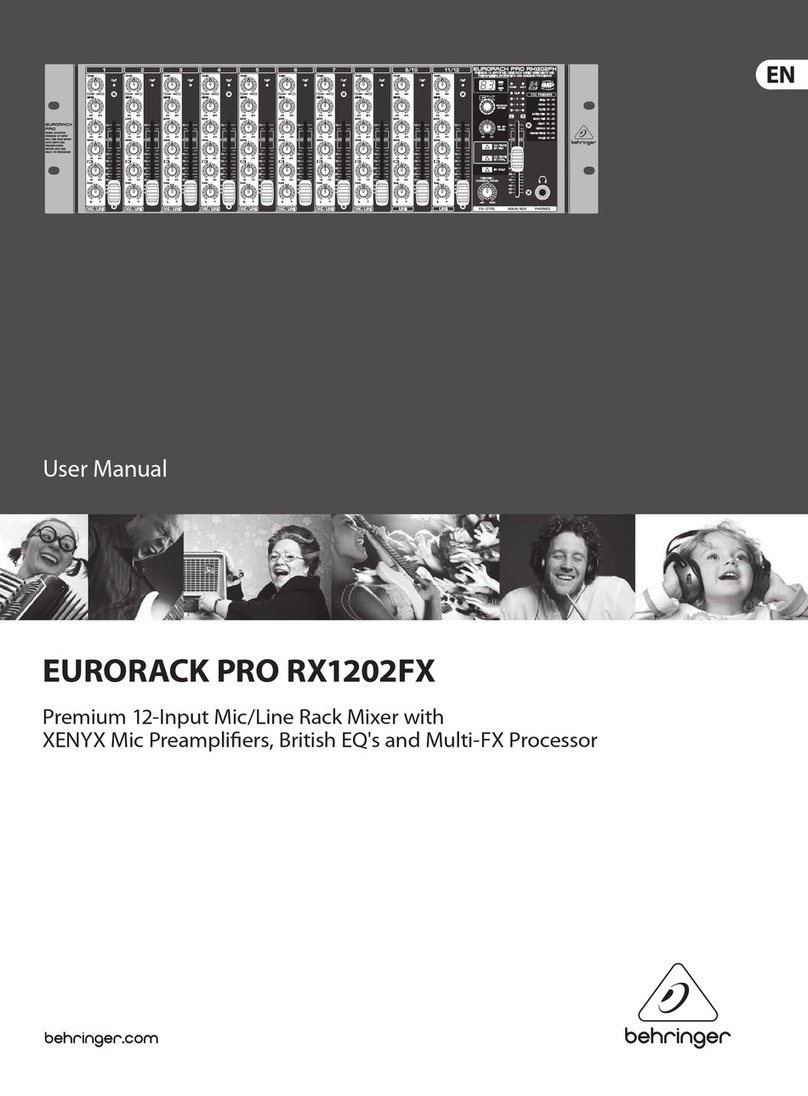
Behringer
Behringer EURORACK PRO RX1202FX user manual
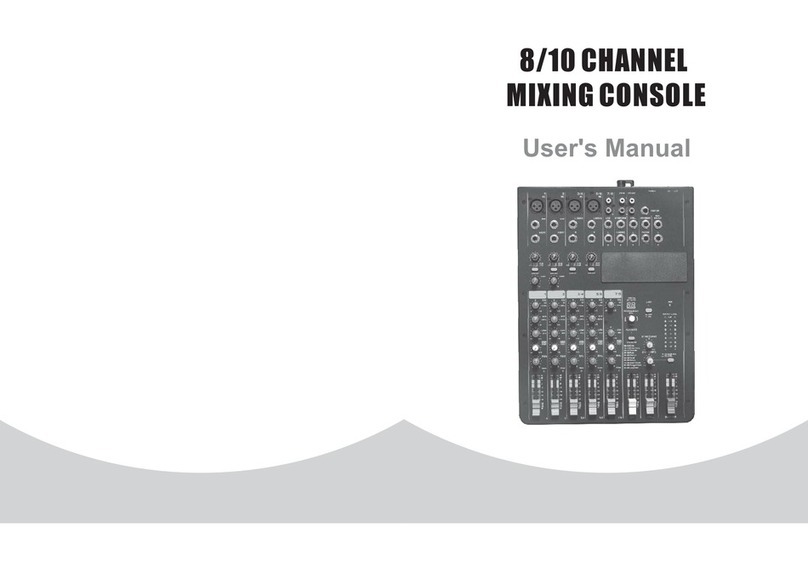
SEIKAKU
SEIKAKU 8/10 channel mixing console user manual
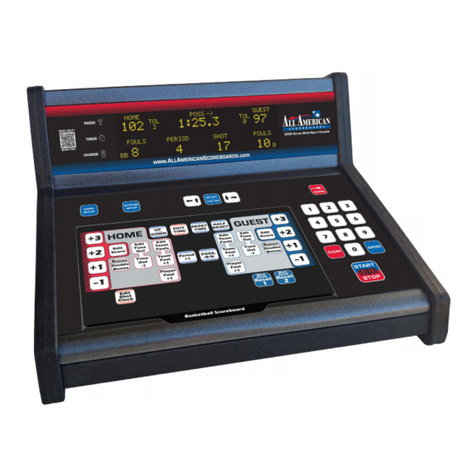
All American Scoreboards
All American Scoreboards 9000 Series manual