Areva MiCOM C232 User manual

MiCOM C232
Compact Bay Unit for
Control and Monitoring
with Protection Functions
Version -302-401/402/403/404-603
Technical Manual
C232/EN M/A23
Volume 1.1
www . ElectricalPartManuals . com

Compact Bay Unit for Control and Monitoring
with integrated Protection Functions
C232
Version -302-401/402/403/404-603
www . ElectricalPartManuals . com

!Warning
When electrical equipment is in operation, dangerous voltage will be present in certain parts of the
equipment. Failure to observe warning notices, incorrect use, or improper use may endanger
personnel and equipment and cause personal injury or physical damage.
Before working in the terminal strip area, the device must be isolated. Where stranded conductors
are used, wire end ferrules must be employed.
Proper and safe operation of this device depends on appropriate shipping and handling, proper
storage, installation and commissioning, and on careful operation, maintenance and servicing.
For this reason only qualified personnel may work on or operate this device.
Qualified Personnel
are individuals who
are familiar with the installation, commissioning, and operation of the device and of the system to which it is being
connected;
are able to perform switching operations in accordance with safety engineering standards and are authorized to
energize and de-energize equipment and to isolate, ground, and label it;
are trained in the care and use of safety apparatus in accordance with safety engineering standards;
are trained in emergency procedures (first aid).
Note
The operating manual for this device gives instructions for its installation, commissioning, and operation. However, the
manual cannot cover all conceivable circumstances or include detailed information on all topics. In the event of
questions or specific problems, do not take any action without proper authorization. Contact the appropriate AREVA
technical sales office and request the necessary information.
Any agreements, commitments, and legal relationships and any obligations on the part of AREVA, including settlement
of warranties, result solely from the applicable purchase contract, which is not affected by the contents of the operating
manual.
www . ElectricalPartManuals . com

www . ElectricalPartManuals . com

www . ElectricalPartManuals . com

www . ElectricalPartManuals . com

Modifications After Going to Press
www . ElectricalPartManuals . com

Contents
C232-302-401/402/403/404-603 / C232/EN M/A23 7
1 Application and Scope 1-1
2 Technical Data 2-1
2.1 Conformity 2-1
2.2 General Data 2-1
2.3 Tests 2-2
2.3.1 Type Test 2-2
2.3.2 Routine Test 2-4
2.4 Environmental Conditions 2-4
2.5 Inputs and Outputs 2-4
2.6 Interfaces 2-5
2.7 Information Output 2-7
2.8 Settings 2-7
2.9 Deviations 2-7
2.9.1 Deviations of the Operate Values 2-7
2.9.2 Deviations of the Timer Stages 2-8
2.9.3 Deviations of Measured Data Acquisition 2-8
2.10 Recording Functions 2-9
2.11 Power Supply 2-10
2.12 Dimensioning of Current Transformers 2-11
3 Operation 3-1
3.1 Modular Structure 3-1
3.2 Operator-Machine Communication 3-3
3.3 Configuration of the Bay Panel
and the Measured Value Panels;
Selection of the Control Point
(Function Group LOC) 3-4
3.4 Serial Interfaces 3-11
3.4.1 PC Interface (Function Group PC) 3-11
3.4.2 “Logical” Communication
Interface 1
(Function Group COMM1) 3-13
3.4.3 “Logical” Communication
Interface 2
(Function Group COMM2) 3-13
3.5 Configuration and Operating Mode
of the Binary Inputs
(Function Group INP) 3-22
3.6 Measured Data Input (Function Group MEASI) 3-23
3.6.1 Direct Current Input 3-24
3.7 Configuration, Operating Mode
and Blocking of the Output Relays
(Function Group OUTP) 3-28
3.8 Configuration and Operating Mode
of the LED Indicators
(Function Group LED) 3-31
3.9 Main Functions of the C232 (Function Group MAIN) 3-33
3.9.1 Acquisition of Binary Signals for
Control
3-33
3.9.2 Bay Type Selection 3-37
3.9.3 Conditioning the Measured
Variables
3-38
3.9.4 Operating Data Measurement 3-40
3.9.5 Configuring and Enabling the
Device Functions
3-51
3.9.6 Activation of Dynamic Parameters 3-55
3.9.7 Inrush Stabilization (Harmonic
Restraint)
3-56
3.9.8 Function Blocks 3-58
3.9.9 Multiple Blocking 3-59
www . ElectricalPartManuals . com

Contents
(continued)
8
C232-302-401/402/403/404-603 / C232/EN M/A23
3.9.10 Blocked / Faulty
(OUT OF SERVICE)
3-60
3.9.11 Coupling between Control and
Protection for the CB Closed
Signal
3-61
3.9.12 Close Command 3-62
3.9.13 Multiple Signaling 3-63
3.9.14 Starting Signals and Tripping
Logic
3-65
3.9.15 CB Trip Signal 3-72
3.9.16 Enable for Switch Commands
Issued by the Control Functions
3-74
3.9.17 Monitoring the Switchgear Unit
Motors
3-77
3.9.18 Communication Error 3-78
3.9.19 Time Tagging and Clock
Synchronization
3-79
3.9.20 Resetting Mechanisms 3-80
3.9.21 Assignment of the “Logical”
Communication Interfaces to the
Physical Communication
Channels
3-81
3.9.22 Test Mode 3-82
3.10 Parameter Subset Selection (Function Group PSS) 3-83
3.11 Self-Monitoring (Function Group SFMON) 3-85
3.12 Operating Data Recording (Function Group OP_RC) 3-87
3.13 Monitoring Signal Recording (Function Group MT_RC) 3-88
3.14 Fault Data Acquisition (Function Group FT_DA) 3-89
3.15 Fault Recording (Function Group FT_RC) 3-93
3.16 Time-Overcurrent Protection (Function Group DTOC) 3-99
3.17 Inverse-Time Overcurrent
Protection
(Function Group IDMT) 3-108
3.18 Limit Value Monitoring (Function Group LIMIT) 3-122
3.19 Programmable Logic (Function Group LOGIC) 3-127
3.20 Control and Monitoring of
Switchgear Units
(Function Groups DEV01
to DEV10)
3-134
3.20.1 Processing of Position Signals for
Manually Operated Switchgear
3-135
3.20.2 Functional Sequence for
Controllable Switchgear Units
3-137
3.21 Interlocking Logic (Function Group ILOCK) 3-148
3.22 Single-Pole Commands (Function Group CMD_1) 3-150
3.23 Single-Pole Signals (Function Group SIG_1) 3-151
3.24 Binary Counts (Function Group COUNT) 3-153
3.25 Tap Changer (Function Group TAPCH) 3-156
www . ElectricalPartManuals . com

Contents
(continued)
C232-302-401/402/403/404-603 / C232/EN M/A23 9
4 Design 4-1
5 Installation and Connection 5-1
5.1 Unpacking and Packing 5-1
5.2 Checking the Nominal Data and the Design Type 5-1
5.3 Location Requirements 5-2
5.4 Installation 5-3
5.5 Protective and Operational Grounding 5-6
5.6 Connection 5-7
5.6.1 Connecting the Measuring and Auxiliary Circuits 5-7
5.6.2 Connecting the Serial Interfaces 5-11
6 Local Control Panel 6-1
6.1 Display and Keypad 6-2
6.2 Changing between Display Levels 6-7
6.3 Illumination of the Display 6-8
6.4 Control at the Panel Level 6-8
6.4.1 Bay Panel 6-8
6.4.2 Measured Value Panels and Signal Panel 6-15
6.5 Control at the Menu Tree Level 6-17
6.5.1 Navigation in the Menu Tree 6-17
6.5.2 Switching between Address Mode and Plain Text Mode 6-18
6.5.3 Change-Enabling Function 6-19
6.5.4 Changing Parameters 6-22
6.5.5 Setting a List Parameter 6-23
6.5.6 Memory Readout 6-25
6.5.7 Resetting 6-29
6.5.8 Password-Protected Control Actions 6-30
6.5.9 Changing the Password 6-31
7 Settings 7-1
7.1 Parameters 7-1
7.1.1 Device Identification 7-2
7.1.2 Configuration Parameters 7-4
7.1.3 Function Parameters 7-29
7.1.3.1 Global 7-29
7.1.3.2 General Functions 7-34
7.1.3.3 Parameter Subsets 7-46
7.1.3.4 Control 7-50
www . ElectricalPartManuals . com

Contents
(continued)
10
C232-302-401/402/403/404-603 / C232/EN M/A23
8 Information and Control Functions 8-1
8.1 Operation 8-1
8.1.1 Cyclic Values 8-1
8.1.1.1 Measured Operating Data 8-1
8.1.1.2 Physical State Signals 8-5
8.1.1.3 Logic State Signals 8-7
8.1.2 Control and Testing 8-18
8.1.3 Operating Data Recording 8-20
8.2 Events 8-21
8.2.1 Event Counters 8-21
8.2.2 Measured Event Data 8-22
8.2.3 Event Recording 8-22
9 Commissioning 9-1
9.1 Safety Instructions 9-1
9.2 Commissioning Tests 9-2
10 Troubleshooting 10-1
11 Maintenance 11-1
12 Storage 12-1
13 Accessories and Spare Parts 13-1
14 Order Information 14-1
AP Appendix AP-1
AP-A Glossary A-1
AP-B List of Signals B-1
AP-C List of Bay Types C-1
AP-D Terminal Connection Diagrams D-1
AP-E Address List
(The Address List is available as a PDF file.
It is not included in the printed manual.)
E-1
www . ElectricalPartManuals . com

1 Application and Scope
C232-302-401/402/403/404-603 / C232/EN M/A23 1-1
1 Application and Scope
The C232 bay unit integrates control and protection (model 4 only) into one single
device (One-box solution).
The unit’s protection functions provide selective short-circuit protection in medium- and
high-voltage systems. The systems can be operated as impedance-grounded, resonant-
grounded, or isolated-neutral systems.
The control functions are designed for the control of up to six electrically operated
switchgear units equipped with electrical check-back signaling located in the bay of a
medium-voltage substation or a non-complex high-voltage station. External auxiliary
devices are largely obviated by the integration of binary inputs and power outputs that
are independent of auxiliary voltages, by the direct connection option for current and
voltage transformers, and by the comprehensive interlocking capability. This simplifies
the handling of switchbay protection and control technology from planning to
commissioning.
During operation, the user-friendly interface makes it easy to set the unit and allows safe
operation of the substation by preventing non-permissible switching operations.
The C232 has the following general functions:
Control functions
Control and monitoring of up to six switchgear units
Selection from over 200 pre-defined bay types
Bay interlock
Tap changer controller
Local control and display via user-selected panels on the LCD display:
Bay Panel
Measured Value Panel
Signal Panel
Protection functions
Optional Three-pole measurement (A, B, C) + voltage or current measurement
Definite-time overcurrent protection, three stages, phase-selective (model 4 only)
Inverse-time overcurrent protection, single-stage, phase-selective (model 4 only)
Limit value monitoring
Programmable Logic
0..20 mA interface (option)
The user can select all general functions individually for inclusion in the device
configuration or cancel them as desired. By means of a straightforward configuration
procedure, the user can adapt the device flexibly to the scope of protection required in
each particular application. The unit’s powerful, freely configurable logic also makes it
possible to accommodate special applications.
www . ElectricalPartManuals . com

1 Application and Scope
(continued)
1-2
C232-302-401/402/403/404-603 / C232/EN M/A23
Global functions
In addition to the features listed above, as well as comprehensive self-monitoring, the
following global functions are available in the C232:
Parameter subset selection (model 4 only)
Operating data recording (time-tagged signal logging)
Fault data acquisition (model 4 only)
Fault recording (time-tagged signal logging together with fault value recording of the
three phase currents, the residual current as well as the three phase-to-ground
voltages and the neutral-point displacement voltage)
Design
The C232 is housed in an aluminum case with threaded terminal ends in the form of
plug-in blocks and with reversible mounting brackets. The case is equally suitable for
surface mounting of flush panel mounting.
Inputs and outputs
The C232 has the following inputs and outputs:
Up to 4 current-measuring inputs (option)
Up to 14 output relays with freely configurable function assignment
Up to 20 optical coupler inputs for binary signals with freely configurable function
assignment for single signals
1 analog input, 0 to 20 mA (optional)
With the maximum number of binary inputs and outputs fitted, 6 switchgear units can be
monitored and 6 of these can be electrically controllable.
The nominal voltage range of the optical coupler inputs is 24 to 250 V DC without
internal switching. The auxiliary voltage input for the power supply is a wide-range
design. The nominal voltage ranges are 48 to 250 V DC and 100 to 230 V AC.
All output relays are suitable for both signals and commands. Nominal voltages and
currents of the measuring inputs has to be defined by using the appropriate order code.
The optional 0 to 20 mA input provides open-circuit and overload monitoring, zero
suppression defined by a setting, plus the option of linearizing the input variable via 20
adjustable interpolation points.
Interfaces
Local control and display:
Local control panel with LCD display (16 lines of 21 characters each with a resolution
of 128 x 128 pixels)
13 LED indicators, 8 of which allow freely configurable function assignment
PC interface
Communication interface(s) for connection to a substation control system or for
remote setting (optional)
Information is exchanged through the local control panel, the PC interface, or the
optional communication interfaces.
The communication interface (COMM1) is designed to conform either to international
standard IEC 60870-5-103 or to IEC 60870-5-101, MODBUS, or DNP 3.0. The C232
can be integrated into a substation control system through this communication interface.
www . ElectricalPartManuals . com

2 Technical Data
C232-302-401/402/403/404-603 / C232/EN M/A23 2-1
2 Technical Data
2.1 Conformity
Notice
Applicable to C232, version -302 – 401 / 402 / 403 / 404 - 602.
Declaration of conformity
(Per Article 10 of EC Directive 72/73/EC.)
The product designated ‘C232 Compact Bay Unit’ has been designed and manufactured
in conformance with the European standards EN 60255-6 and EN 61010-1 and with the
‘EMC Directive’ and the ‘Low Voltage Directive’ issued by the Council of the European
Community.
2.2 General Data
General device data
Design
Extruded aluminum case with cover plate for wall installation or flush panel mounting
Installation Position
Vertical ±30°
Degree of Protection
Per DIN VDE 0470 and EN 60529 or IEC 529.
Case and Terminals: IP 20
Front panel, flush-mounted: IP 51
Weight
Up to 3,5 kg
Dimensions and Connections
See dimensional drawings (Chapter 4) and terminal connection diagrams (Appendix E).
Terminals
PC Interface (X6):
DIN 41652 connector, type D-Sub, 9-pin.
Communication Interface:
Optical fibers (X7 and X8): F-SMA optical fiber connection per IEC 874-2 or
DIN 47258 (plastic fiber)
or
BFOC(ST) fiber-optic connection for glass fiber
(STis a registered trademark of AT&T Lightguide
Cable Connectors)
or
Leads (X9, X10): M2 threaded terminal ends for wire cross sections to
1.5mm
2.
Current- and Voltage Measuring Inputs:
M5 threaded terminal ends, self-centering with wire protection for conductor cross
sections 0.5 to 6 mm2.
Other Inputs and Outputs:
M3 threaded terminal ends, self-centering with wire protection for conductor cross
sections from 0.2 to 2.5 mm2.
www . ElectricalPartManuals . com

2 Technical Data
(continued)
2-2
C232-302-401/402/403/404-603 / C232/EN M/A23
Creepage Distances and Clearances
Per EN 61010-1 §and IEC 664-1
Pollution degree 3, working voltage 250 V,
overvoltage category III, impulse test voltage 5 kV.
2.3 Tests
2.3.1 Type Test
Type tests
Tests per EN 60255-6 §or IEC 255-6.
EMC
Interference Suppression
Per EN 55022 §or IEC CISPR 22, Class A.
1 MHz Burst Disturbance Test
Per IEC 255 Part 22-1 §or IEC 60255-22-1, Class III.
Common-mode test voltage: 2.5 kV
Differential test voltage: 1.0 kV
Test duration: > 2 s
Source impedance: 200 Ω
Immunity to Electrostatic Discharge
Per EN 60255-22-2 §or IEC 60255-22-2, severity level 3.
Contact discharge,
single discharges: > 10
Holding time: > 5 s
Test voltage: 6 kV
Test generator: 50 to 100 MΩ, 150 pF / 330 Ω
Immunity to Radiated Electromagnetic Energy
Per EN 61000-4-3 §and ENV 50204 §, severity level 3.
Antenna distance to tested device: > 1 m on all sides
Test field strength, frequency band 80 to 1000 MHz: 10 V/m
Test using AM: 1 kHz / 80 %
Single test at 900 MHz: AM 200 Hz / 100%
Electrical Fast Transient or Burst Requirements
Per EN 61000-4-4 §or IEC 60255-22-4, severity levels 3 and 4.
Rise time of one pulse: 5 ns
Impulse duration (50% value): 50 ns
Amplitude: 2 kV / 1 kV or 4 kV / 2 kV
Burst duration: 15 ms
Burst period: 300 ms
Burst frequency: 5 kHz or 2.5 kHz
Source impedance: 50 Ω
§For this EN, ENV, or IEC standard, the DIN EN, DIN ENV or DIN IEC edition
respectively, was used in the test.
www . ElectricalPartManuals . com

2 Technical Data
(continued)
C232-302-401/402/403/404-603 / C232/EN M/A23 2-3
Surge Immunity Test
Per EN 61000-4-5 §or IEC 61000-4-5, insulation class 4.
Testing of circuits for power supply and unsymmetrical or symmetrical lines.
Open-circuit voltage, front time / time to half-value: 1.2 / 50 µs
Short-circuit current, front time / time to half-value: 8 / 20 µs
Amplitude: 4 / 2 kV
Pulse frequency: > 5 / min
Source impedance: 12 / 42 Ω
Immunity to Conducted Disturbances Induced by Radio Frequency Fields
Per EN 61000-4-6 §or IEC 61000-4-6, severity level 3.
Prüfspannung: 10 V.
Power Frequency Magnetic Field Immunity
Per EN 61000-4-8 §or IEC 61000-4-8, severity level 4.
Frequenz: 50 Hz,
Feldstärke: 30 A / m.
Alternating Component (Ripple) in DC Auxiliary Energizing Quantity
Per IEC 255-11.
12 %.
Insulation
Voltage Test
Per EN 61010-1 §and IEC 255-5.
2 kV AC, 60 s.
Direct voltage (2.8 kV DC) must be used for the voltage test of the power supply inputs.
The PC interface must not be subjected to the voltage test.
Impulse Voltage Withstand Test
Per IEC 255-5.
Front time: 1.2 µs,
Time to half-value: 50 µs
Peak value: 5 kV
Source impedance: 500 Ω
Mechanical robustness
Vibration Test
Per EN 60255-21-1 §or IEC 255-21-1, test severity class 1.
Frequency range in operation: 10 to 60 Hz, 0.035 mm, and 60 to 150 Hz, 0.5 g
Frequency range during transport: 10 to 150 Hz, 1 g
Shock Response and Withstand Test,
Bump Test
Per EN 60255-21-2 §or IEC 255-21-2, test severity class 1.
Acceleration: 5 g / 15 g
Pulse duration: 11 ms
Seismic Test
Per EN 60255-21-3,§test procedure A, class 1
Frequency range:
5 to 8 Hz, 3.5 mm / 1.5 mm, 8 to 35 Hz, 10 / 5 m/s2, 3 x 1 cycle
www . ElectricalPartManuals . com

2 Technical Data
(continued)
2-4
C232-302-401/402/403/404-603 / C232/EN M/A23
2.3.2 Routine Test
All tests per EN 60255-6§ or IEC 255-6
and DIN 57435 part 303.
Voltage Test
Per IEC 255-5.
2.2 kV AC or 2.8 kV DC, 1 s.
Direct voltage (2.8 kV DC) must be used for the voltage test of the power supply inputs.
The PC interface must not be subjected to the voltage test.
Additional Thermal Test
100% controlled thermal endurance test, inputs loaded
2.4 Environmental Conditions
Environment
Temperatures
Recommended temperature range: -5°C to +55°C or +23°F to +131°F.
Limit temperature range: -25°C to +70°C or -13°F to +158°F.
Ambient Humidity Range
≤75 % relative humidity (annual mean),
56 days at ≤ 95 % relative humidity and 40°C or 104°F, condensation not permissible.
Solar Radiation
Direct solar radiation on the front of the device must be avoided.
2.5 Inputs and Outputs
Measurement inputs
Current
Nominal current Inom: 1 and 5 A AC (per order).
Nominal consumption per phase: < 0.1 VA at Inom.
Load rating:
continuous 4 Inom
for 10 s: 30 Inom
for 1 s: 100 Inom
Nominal surge current: 250 Inom
Voltage
Nominal voltage Vnom: 50 to 130 V AC (adjustable)
Nominal consumption per phase: < 0.3 VA at Vnom = 130 V AC
Load rating: continuous 150 V AC
Frequency
Nominal frequency fnom: 50 Hz and 60 Hz (adjustable)
Operating range: 0.95 to 1.05 fnom
www . ElectricalPartManuals . com

2 Technical Data
(continued)
C232-302-401/402/403/404-603 / C232/EN M/A23 2-5
Binary signal inputs
Nominal auxiliary voltage VA,nom: = 24 to 250 V DC
Operating range: 0.8 to 1.1 Vin,nom with a residual ripple of up to 12 % Vin,nom
Power consumption per input:
Vin = 19 to 110 V DC: 0.5 W ± 30 %
Vin > 110 V DC: 5 mA ± 30 %
Binary count input
Maximum frequency of 10 Hz with a pulse/interpulse period of 1:1
Direct current input
Input current: 0 to 20 mA
Value range: 0.00 to 1.20 IDC,nom (IDC,nom = 20 mA)
Maximum permissible continuous current: 50 mA
Maximum permissible input current: 17 V
Input load: 250 Ω
Open-circuit monitoring: 0 to 10 mA (adjustable)
Overload monitoring: > 24.8 mA
Zero suppression: 0.000 to 0.200 IDC,nom (adjustable)
Output relays
Rated voltage: 250 V DC, 250 V AC
Continuous current: 8A
Short-duration current: 30 A for 0.5 s
Making capacity: 1000 W (VA) at L/R = 40 ms
Breaking capacity: 0.2 A at 220 V DC and L/R = 40 ms
4 A at 230 V AC and cos ϕ= 0.4
2.6 Interfaces
Local control panel
Input or output:
More than 12 keys and an LCD display with 16 lines and 21 columns (128 x 128 pixels)
State and fault signals:
13 LED indicators (5 permanently assigned, 8 freely configurable)
PC interface
Transmission rate: 300 to 115 200 baud (adjustable)
Communication interface
The communication module can have two communication channels – depending on the
version. Channel 1 is designed for wire connection or fiber optic connection, whereas
Channel 2 is intended for wire connection only.
For one channel (COMM1), interface protocols based on IEC 60870-5-103,
IEC 60870-5-101, MODBUS, or DNP 3.0 can be set. The second channel (COMM2)
can only be operated using the interface protocol based on IEC 60870-5-103.
www . ElectricalPartManuals . com

2 Technical Data
(continued)
2-6
C232-302-401/402/403/404-603 / C232/EN M/A23
Wire Leads
Per RS 485 or RS 422, 2 kV isolation
Distance to be bridged:
Point-to-point connection: max. 1200 m
Multipoint connection: max. 100 m
Order Code Transmission Rate Interface
- 456 - 925
(one channel available)
300 to 64,000 baud (adjustable) COMM1
- 456 - 921
(two channels available)
300 to 64,000 baud (adjustable)
300 to 57,600 baud (adjustable)
COMM1
COMM2
Plastic Fiber Connection
Optical wavelength: typically 660 nm
Optical output: min. -7,5 dBm
Optical sensitivity: min. -20 dBm
Optical input: max. -5 dBm
Distance to be bridged:1) max. 45 m
Order Code Transmission Rate Interface
- 456 - 926
(one channel available)
300 to 64,000 baud (adjustable) COMM1
- 456 - 922
(two channels available)
300 to 64,000 baud (adjustable)
300 to 57,600 baud (adjustable)
COMM1
COMM2
Glass Fiber Connection G 50/125
Optical wavelength: typically 820 nm
Optical output: min. -19.8 dBm
Optical sensitivity: min. -24 dBm
Optical input: max. -10 dBm
Distance to be bridged:1) max. 400 m
Order Code Transmission Rate Interface
- 456 - 927
(one channel available)
300 to 64,000 baud (adjustable) COMM1
- 456 - 924
(two channels available)
300 to 64,000 baud (adjustable)
300 to 57,600 baud (adjustable)
COMM1
COMM2
1) Distance to be bridged given identical optical outputs and inputs at both ends, a
system reserve of 3 dB, and typical fiber attenuation.
www . ElectricalPartManuals . com

2 Technical Data
(continued)
C232-302-401/402/403/404-603 / C232/EN M/A23 2-7
Glass Fiber Connection G 62,5/125
Optical wavelength: typically 820 nm
Optical output: min. -16 dBm
Optical sensitivity: min. -24 dBm
Optical input: max. -10 dBm
Distance to be bridged:1) max. 1.400 m
Order Code Transmission Rate Interface
- 456 - 927
(one channel available)
300 to 64,000 baud (adjustable) COMM1
- 456 - 924
(two channels available)
300 to 64,000 baud (adjustable)
300 to 57,600 baud (adjustable)
COMM1
COMM2
1) Distance to be bridged given identical optical outputs and inputs at both ends, a
system reserve of 3 dB, and typical fiber attenuation.
2.7 Information Output
Counters, measured data, signals, and indications: see "Address List."
2.8 Settings
Typical characteristic data
Main Function
Minimum output pulse for trip command: 0.1 to 10 s (adjustable)
Output pulse for close command: 0.1 to 10 s (adjustable)
Definite-Time and Inverse-Time Overcurrent Protection
Operate time inclusive of output relay (measured variable from 0 to 2-fold operate
value): ≤40 ms, approx. 30 ms
Reset time (measured variable from 2-fold operate value to 0): ≤40 ms, approx. 30 ms
Starting resetting ratio: approx. 0.95
2.9 Deviations
2.9.1 Deviations of the Operate Values
Definitions
‘Reference Conditions’
Sinusoidal signals at nominal frequency fnom, total harmonic distortion ≤ 2 %,
ambient temperature 20°C (68°F), and nominal auxiliary voltage VA,nom.
'Deviation'
Deviation relative to the setting under reference conditions.
www . ElectricalPartManuals . com
Other manuals for MiCOM C232
1
Table of contents
Popular Control Unit manuals by other brands
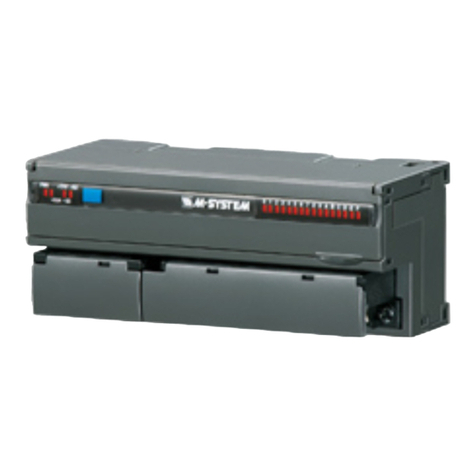
M-system
M-system R7M-YS2 instruction manual
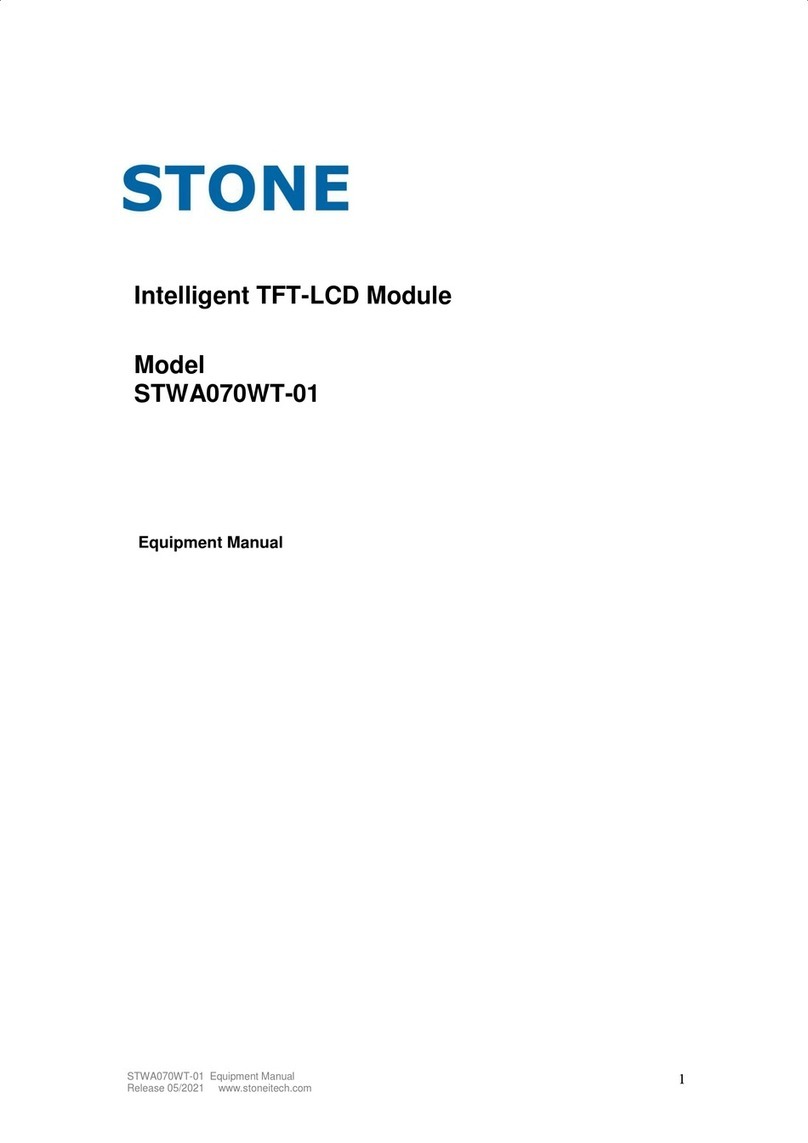
Stone
Stone STWA070WT-01 Equipment manual
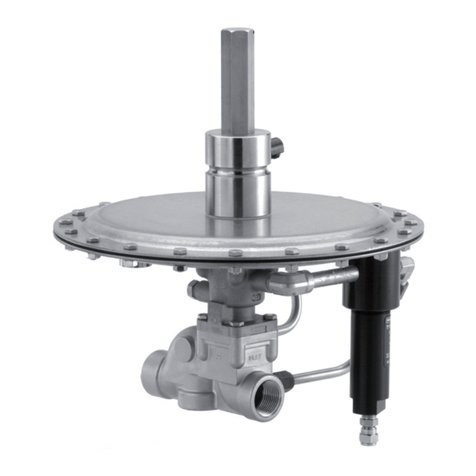
Emerson
Emerson Fisher ACE95 Series installation guide
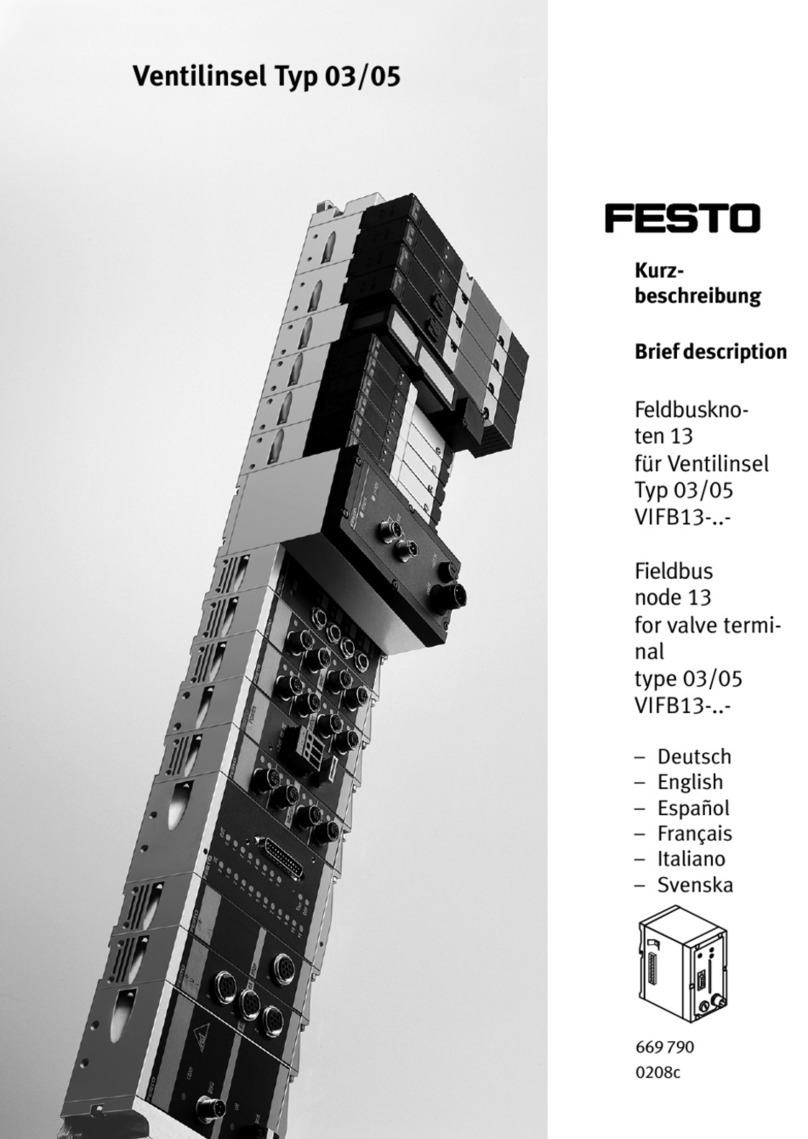
Festo
Festo VIFB13 Series manual
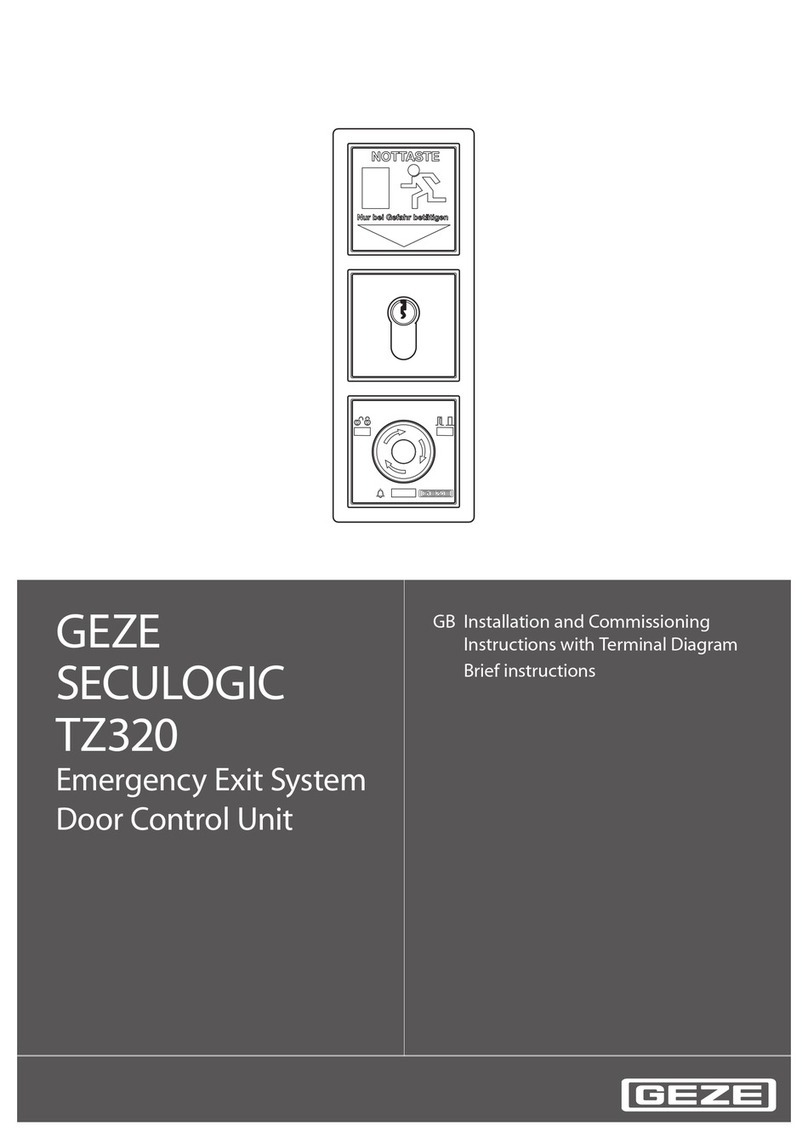
GEZE
GEZE SecuLogic TZ320 Installation and Commissioning Instructions with Terminal Diagram Brief instructions
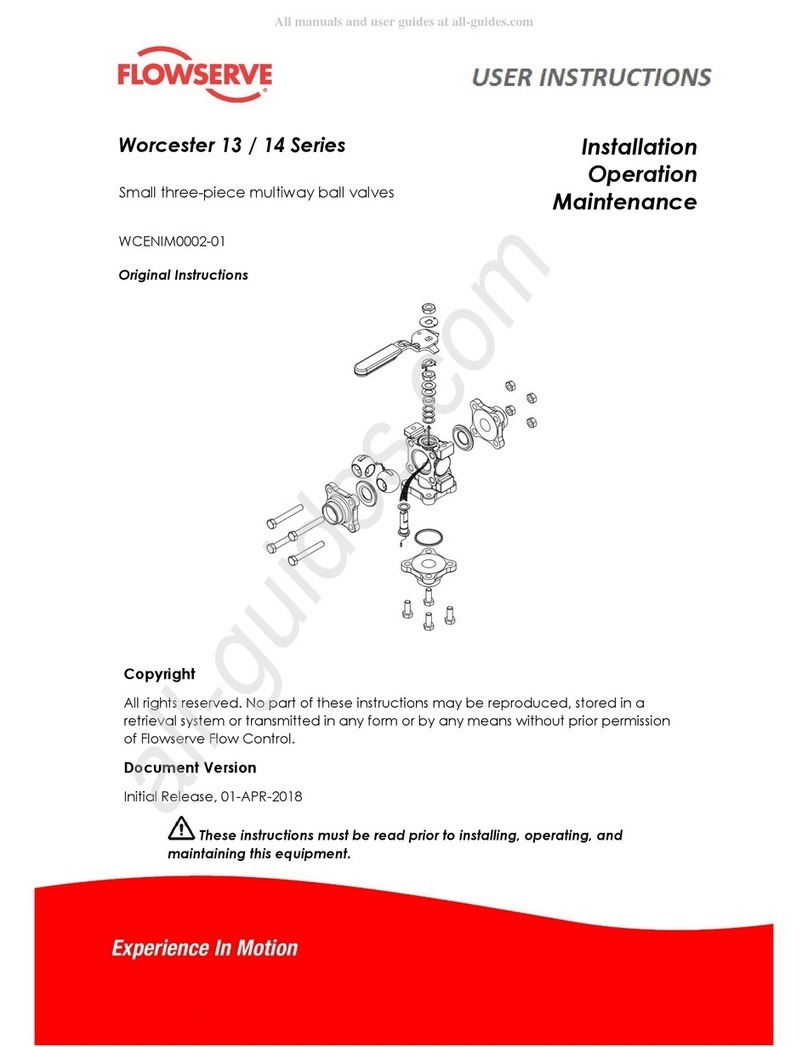
Flowserve
Flowserve Worcester 13 Series User instructions