Areva MiCOM C264 Quick start guide

MiCOM
C264/C264C
Bay Computer
Technical Guide
C264/EN T/A14


Technical Guide C264/EN T/A14
MiCOM C264/C264C Page 1/2
MiCOM C264/C264C
BAY COMPUTER
CONTENT
Safety & Handling C264/EN SA/A14
Introduction C264/EN IT/A13
Technical data C264/EN TD/A13
Functionnal Description C264/EN FT/A13
Hardware Description C264/EN HW/A13
Connection C264/EN CO/A14
Installation C264/EN IN/A13
Application C264/EN AP/A13
Settings C264/EN ST/A13
Logic Diagrams
C264/EN LG/A13
Communications C264/EN CT/A13
Commissioning C264/EN CM/A13
Commissioning Record Sheet C264/EN RS/A13
Maintenance C264/EN MF/A13
Lexical C264/EN LX/A13

C264/EN T/A14 Technical Guide
Page 2/2 MiCOM C264
BLANK PAGE

Safety & Handling C264/EN SA/A14
MiCOM C264/C264C
SAFETY & HANDLING


Safety & Handling C264/EN SA/A14
MiCOM C264/C264C
Page 1/12
CONTENT
1. INTRODUCTION 3
2. HEALTH AND SAFETY 4
2.1 Health and Safety 4
2.2 Installing, Commissioning and Servicing 4
3. DECOMMISSIONING AND DISPOSAL 6
4. TECHNICAL SPECIFICATIONS FOR SAFETY 7
5. HANDLING OF ELECTRONIC EQUIPMENTS 8
6. PACKING AND UNPACKING 9
7. GUARANTIES 10
8. COPYRIGHTS & TRADEMARKS 11
8.1 Copyrights 11
8.2 Trademarks 11
9. WARNINGS REGARDING USE OF T&D EAI PRODUCTS 12

C264/EN SA/A14 Safety & Handling
Page 2/12
MiCOM C264/C264C
BLANK PAGE

Safety & Handling C264/EN SA/A14
MiCOM C264/C264C
Page 3/12
1. INTRODUCTION
This document is a chapter of the MiCOM C264C/C264 documentation binder. It describes
the safety, handling, packing and unpacking procedures applicable to MiCOM C264C/C264
modular computer series and associated equipment's and software tools.

C264/EN SA/A14 Safety & Handling
Page 4/12
MiCOM C264/C264C
2. HEALTH AND SAFETY
For all the safety purposes please refer to the AREVA T&D Safety Guide: SFTY/4L M/D11
(or later issue) and to the following chapters.
WARNING: THIS SAFETY SECTION SHOULD BE READ BEFORE COMMENCING
ANY WORK ON THE EQUIPMENT.
2.1 Health and Safety
The information in the Safety Section of the product documentation is intended to ensure
that products are properly installed and handled in order to maintain them in a safe condition.
It is assumed that everyone who will be associated with the equipment will be familiar with
the contents of the Safety Section.
2.2 Installing, Commissioning and Servicing
Equipment connections
Personnel undertaking installation, commissioning or servicing work on this equipment
should be aware of the correct working procedures to ensure safety. The product
documentation should be consulted before installing, commissioning or servicing the
equipment.
Terminals exposed during installation, commissioning and maintenance may present a
hazardous voltage unless the equipment is electrically isolated.
If there is unlocked access to the rear of the equipment, care should be taken by all
personnel to avoid electrical shock or energy hazards.
Voltage and current connections should be made using insulated crimp terminations to
ensure that terminal block insulation requirements are maintained for safety. To ensure that
wires are correctly terminated the correct crimp terminal and tool for the wire size should be
used.
Before energising the equipment it must be earthed using the protective earth terminal, or
the appropriate termination of the supply plug in the case of plug connected equipment.
Omitting or disconnecting the equipment earth may cause a safety hazard.
The recommended minimum earth wire size is 2.5 mm², unless otherwise stated in the
technical data section of the product documentation.
When the protective (earth) conductor terminal (PCT) is also used to terminate cable
screens, etc., it is essential that the integrity of the protective (earth) conductor is checked
after the addition or removal of such functional earth connections.
For M4 stud PCTs the integrity of the protective (earth) connection should be ensured by use
of a locknut or similar."
Before energising the equipment, the following should be checked:
• Voltage rating and polarity
• CT circuit rating and integrity of connections
• Integrity of earth connection (where applicable)
Note: The term earth used throughout the product documentation is the
direct equivalent of the North American term ground.
Equipment operating conditions
The equipment should be operated within the specified electrical and environmental limits.
Current transformer circuits
Do not open the secondary circuit of a live CT since the high level voltage produced may be
lethal to personnel and could damage insulation.

Safety & Handling C264/EN SA/A14
MiCOM C264/C264C
Page 5/12
Insulation and dielectric strength testing
Insulation testing may leave capacitors charged up to a hazardous voltage. At the end of
each part of the test, the voltage should be gradually reduced to zero, to discharge
capacitors, before the test leads are disconnected.
Insertion of modules and boards
These must not be inserted into or withdrawn from equipment whist it is energised since this
may result in damage.
Fibre optic communication
Where fibre optic communication devices are fitted, these should not be viewed directly.
Optical power meters should be used to determine the operation or signal level of the device.

C264/EN SA/A14 Safety & Handling
Page 6/12
MiCOM C264/C264C
3. DECOMMISSIONING AND DISPOSAL
Decommissioning:
The auxiliary supply circuit in the MiCOM computers may include capacitors across the
supply or to earth. To avoid electric shock or energy hazards, after completely isolating the
supplies to the MiCOM computers (both poles of any dc supply), the capacitors should be
safely discharged via the external terminals prior to decommissioning.
Disposal:
It is recommended that incineration and disposal to watercourses be avoided. The product
should be disposed of in a safe manner. Any products containing batteries should have them
removed before disposal, in order to avoid short circuits. Particular regulations within the
country of operation may apply to the disposal of lithium batteries.

Safety & Handling C264/EN SA/A14
MiCOM C264/C264C
Page 7/12
4. TECHNICAL SPECIFICATIONS FOR SAFETY
The recommended maximum rating of the external protective fuse for this equipment is 16A,
Red Spot type of equipment, unless otherwise stated in the technical data section of the
product documentation.
1. Fuse rating is dependent of auxiliary voltage and circuit loading.
2. Differential protective switch on DC power supply is recommended
3. Differential protective switch on AC power supply is mandatory (printers, PACiS
workstation…)
Insulation class IEC 601010-1:
Class I
EN 61010-1:
Class I
1990/A2:
1993/A2:
1995 This equipment
requires a protective
(safety) earth
connection to ensure
user safety.
Insulation Category
(Overvoltage):
IEC 601010-1:
Class III
1990/A2: 1995 Distribution level, fixed
installation.
EN 61010-1:
Class III
1993/A2: Equipment in this
category is
qualification tested at
5kV peak, 1.2/50µs,
500Ω. 0.5J, between
all supply circuits and
earth and also
between independent
circuits.
Environment: IEC 601010-1:
Pollution degree 2
EN 61010-1:
Pollution degree 2
1990/A2:
1993/A2:
1995 Compliance is
demonstrated by
reference to generic
safety standards.
Product Safety: 72/23/EEC Compliance with the
European Commission
Law Voltage Directive.
EN 61010-1:
EN 60950:
1993/A2:
1992/A11:
1995
1997
Compliance is
demonstrated by
reference to generic
safety standards.

C264/EN SA/A14 Safety & Handling
Page 8/12
MiCOM C264/C264C
5. HANDLING OF ELECTRONIC EQUIPMENTS
A person’s normal movements can easily generate electrostatic potentials of several
thousand volts.
Discharge of these voltages into semiconductor devices when handling circuits can cause
serious damage, which often may not be immediately apparent but the reliability of the circuit
will have been reduced.
The electronic circuits of T&D products are immune to the relevant levels of electrostatic
discharge when housed in their cases. Do not expose them to the risk of damage by
withdrawing modules unnecessarily.
Each module incorporates the highest practicable protection for its semiconductor devices.
However, if it becomes necessary to withdraw a module, the following precautions should be
taken in order to preserve the high reliability and long life for which the equipment has been
designed and manufactured.
1. Before removing a module, ensure that you are a same electrostatic potential as the
equipment by touching the case.
2. Handle the module by its front-plate, frame, or edges of the printed circuit board. Avoid
touching the electronic components, printed circuit track or connectors.
3. Do not pass the module to any person without first ensuring that you are both at the
same electrostatic potential. Shaking hands achieves equipotential.
4. Place the module on an antistatic surface, or on a conducting surface, which is at the
same potential as you.
5. Store or transport the module in a conductive bag.
More information on safe working procedures for all electronic equipment can be found in
IEC 60147-0F and BS5783.
If you are making measurements on the internal electronic circuitry of any equipment in
service, you must be earthen to the case with a conductive wrist strap.
Wrist straps should have a resistance to ground between 500k – 10M Ohms. If a wrist strap
is not available you should maintain regular contact with the case to prevent the build up of
static. Instrumentation which may be used for making measurements should be earthen to
the case whenever possible.
T&D strongly recommends that detailed investigations on the electronic circuitry, or
modification work, should be carried out in a Special Handling Area such as described in
IEC 60147-0F or BS5783.

Safety & Handling C264/EN SA/A14
MiCOM C264/C264C
Page 9/12
6. PACKING AND UNPACKING
All MiCOM C264/C264C computers are packaged separately in their own cartons and
shipped inside outer packaging. Use special care when opening the cartons and unpacking
the device, and do not use force. In addition, make sure to remove from the inside carton the
supporting documents supplied with each individual device and the type identification label.
The design revision level of each module included with the device in its as-delivered
condition can be determined from the list of components. This list should be carefully saved.
After unpacking the device, inspect it visually to make sure it is in proper mechanical
condition.
If the MiCOM Cx64/Cx64C computer needs to be shipped, both inner and outer packaging
must be used. If the original packaging is no longer available, make sure that packaging
conforms to ISO 2248 specifications for a drop height ≤0.8m.

C264/EN SA/A14 Safety & Handling
Page 10/12
MiCOM C264/C264C
7. GUARANTIES
The media on which you received T&D software are guaranted not to fail executing
programming instructions, due to defects in materials and workmanship, for a period of 90
days from date of shipment, as evidenced by receipts or other documentation. AREVA T&D
will, at its option, repair or replace software media that do net execute programming
instructions if AREVA T&D receive notice of such defects during the guarantee period. T&D
does not guaranty that the operation of the software shall be uninterrupted or error free.
A Return Material Authorisation (RMA) number must be obtained from the factory and clearly
marked on the package before any equipment acceptance for guarantee work. AREVA T&D
will pay the shipping costs of returning to the owner parts, which are covered by warranty.
AREVA T&D believe that the information in this document is accurate. The document has
been carefully reviewed for technical accuracy. In the event that technical or typographical
errors exist, T&D reserves the right to make changes to subsequent editions of this
document without prior notice to holders of this edition. The reader should consult AREVA
T&D if errors are suspected. In no event shall AREVA T&D be liable for any damages arising
out of or related to this document or the information contained in it.
Expect as specified herein, AREVA T&D makes no guarantees, express or implied and
specifically disclaims and guarantees of merchantability or fitness for a particular purpose.
Customer's rights to recover damages caused by fault or negligence on the part T&D shall
be limited to the amount therefore paid by the customer. AREVA T&D will not be liable for
damages resulting from loss of data, profits, use of products or incidental or consequential
damages even if advised of the possibility thereof. This limitation of the liability of AREVA
T&D will apply regardless of the form of action, whether in contract or tort, including
negligence. Any action against AREVA T&D must be brought within one year after the cause
of action accrues. T&D shall not be liable for any delay in performance due to causes
beyond its reasonable control. The warranty provided herein dues net cover damages,
defects, malfunctions, or service failures caused by owner's failure to follow the AREVA T&D
installation, operation, or maintenance instructions; owner's modification of the product;
owner's abuse, misuse, or negligent acts; and power failure or surges, fire, flood, accident,
actions of third parties, or other events outside reasonable control.

Safety & Handling C264/EN SA/A14
MiCOM C264/C264C
Page 11/12
8. COPYRIGHTS & TRADEMARKS
8.1 Copyrights
Under the copyright laws, this publication may not be reproduced or transmitted in any form,
electronic or mechanical, including photocopying, recording, storing in an information
retrieval system, or translating, in whole or in part, without the prior written consent of T&D.
8.2 Trademarks
PACiS, PACiS SCE, PACiS ES, PACiS SMT, PACiS PS, PACiS SCE, AREVA T&D,
pacis.biz and pacis.com- are trademarks of AREVA T&D. Product and company names
mentioned herein are trademarks or trade names of their respective companies.

C264/EN SA/A14 Safety & Handling
Page 12/12
MiCOM C264/C264C
9. WARNINGS REGARDING USE OF T&D EAI PRODUCTS
AREVA T&D products are not designed with components and testing for a level of reliability
suitable for use in or in connection with surgical implants or as critical components in any life
support systems whose failure to perform can reasonably be expected to cause significant
injuries to a human.
In any application, including the above, reliability of operation of the software products can
be impaired by adverse factors, including, but not limited to, fluctuations in electrical power
supply, computer hardware malfunctions, computer operating system, software fitness,
fitness of compilers and development software used to develop an application, installation
errors, software and hardware compatibility problems, malfunctions or failures of electronic
monitoring or control devices, transient failures of electronic systems (hardware and/or
software), unanticipated uses or misuses, or errors from the user or applications designer
(adverse factors such as these are collectively termed "System failures").
Any application where a system failure would create a risk of harm to property or persons
(including the risk of bodily injuries and death) should not be reliant solely upon one form of
electronic system due to the risk of system failure to avoid damage, injury or death, the user
or application designer must take reasonably steps to protect against system failure,
including, but not limited to, back-up or shut-down mechanisms, not because end-user
system is customised and differs from AREVA T&D testing platforms but also a user or
application designer may use T&D products in combination with other products. These
actions cannot be evaluated or contemplated by AREVA T&D; Thus, the user or application
designer is ultimately responsible for verifying and validating the suitability of AREVA T&D
products whenever they are incorporated in a system or application, even without limitation
of the appropriate design, process and safety levels of such system or application.

Introduction C264/EN IT/A13
MiCOM C264/C264C
INTRODUCTION

This manual suits for next models
1
Table of contents
Popular Desktop manuals by other brands
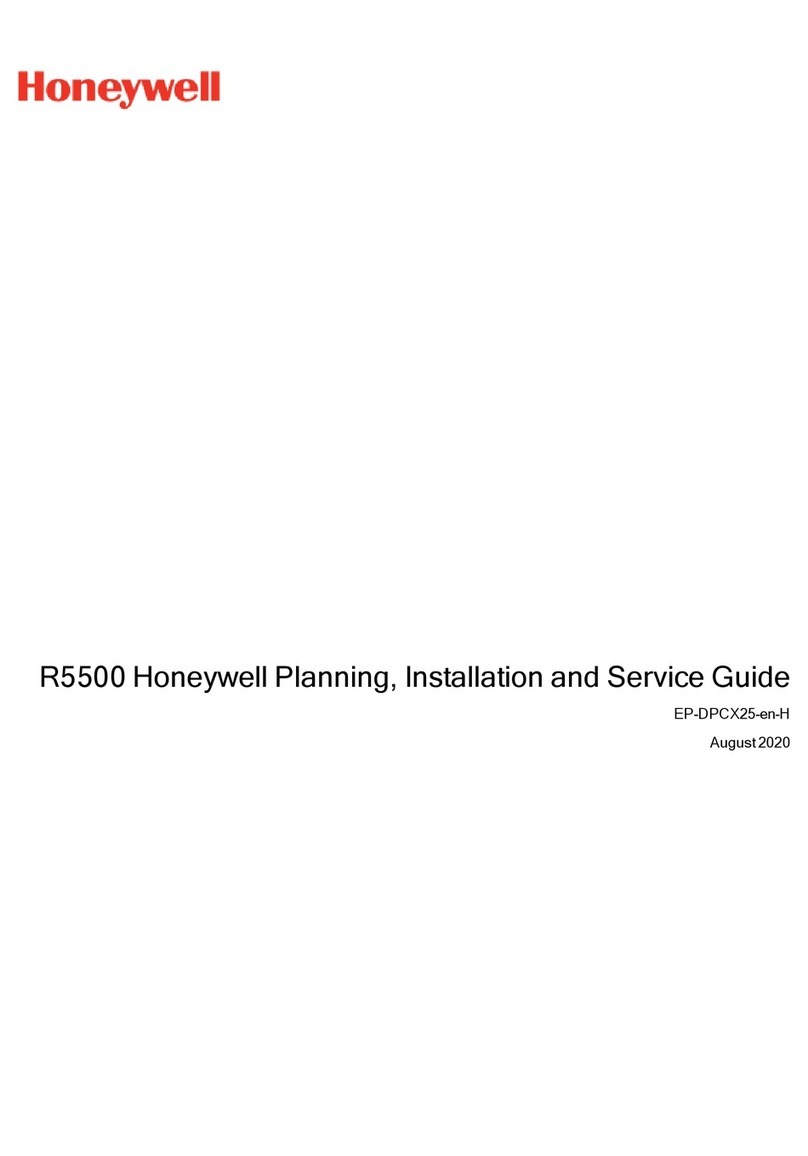
Honeywell
Honeywell R5500 Planning, installation and service guide
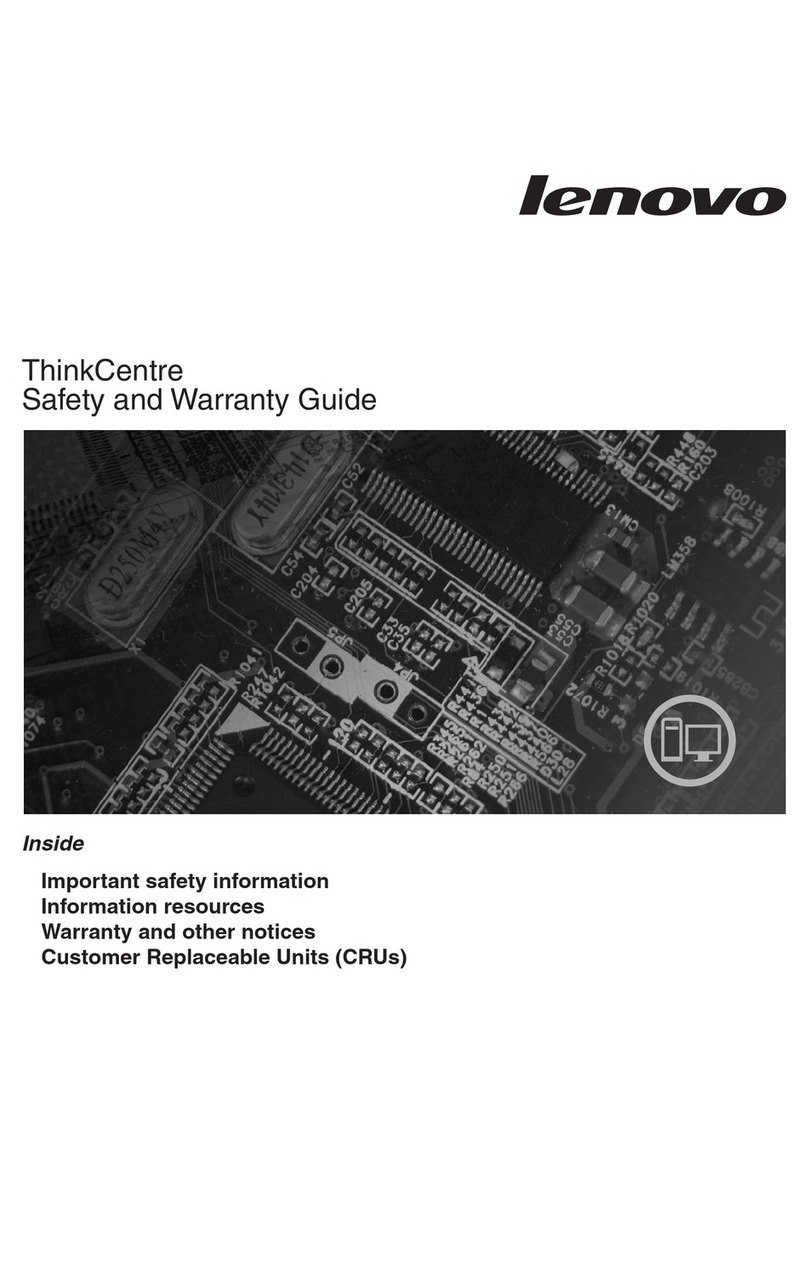
Lenovo
Lenovo ThinkCentre A57e Safety and Warranty Guide
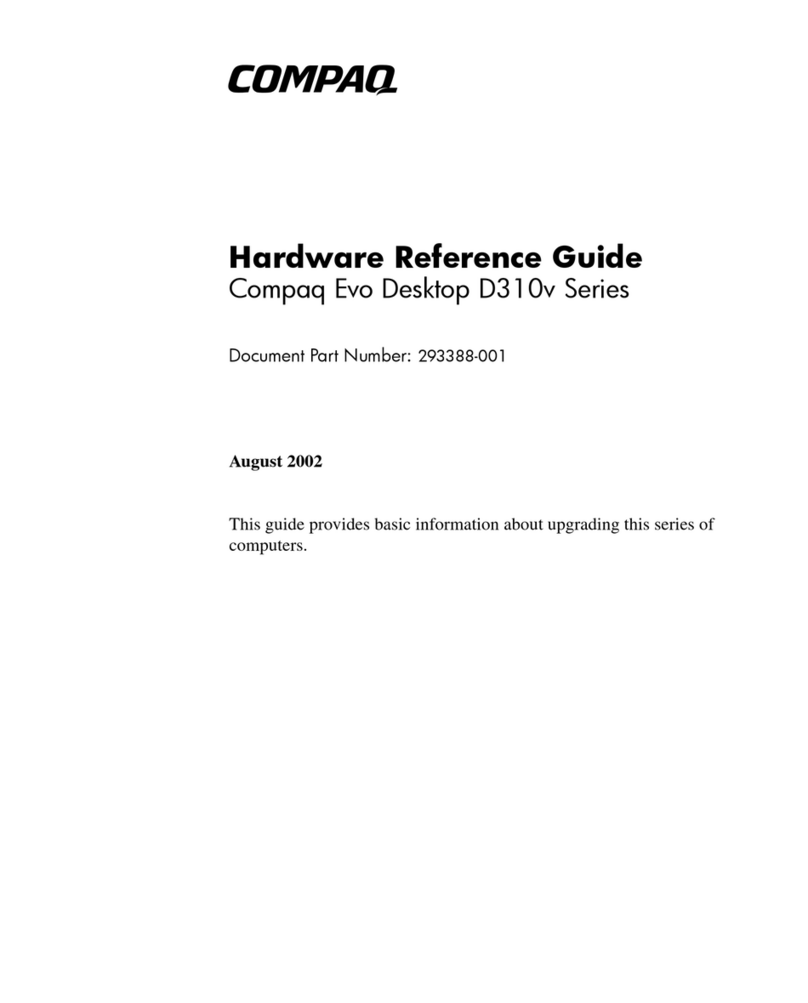
Compaq
Compaq D310v - Evo - 256 MB RAM Hardware reference guide
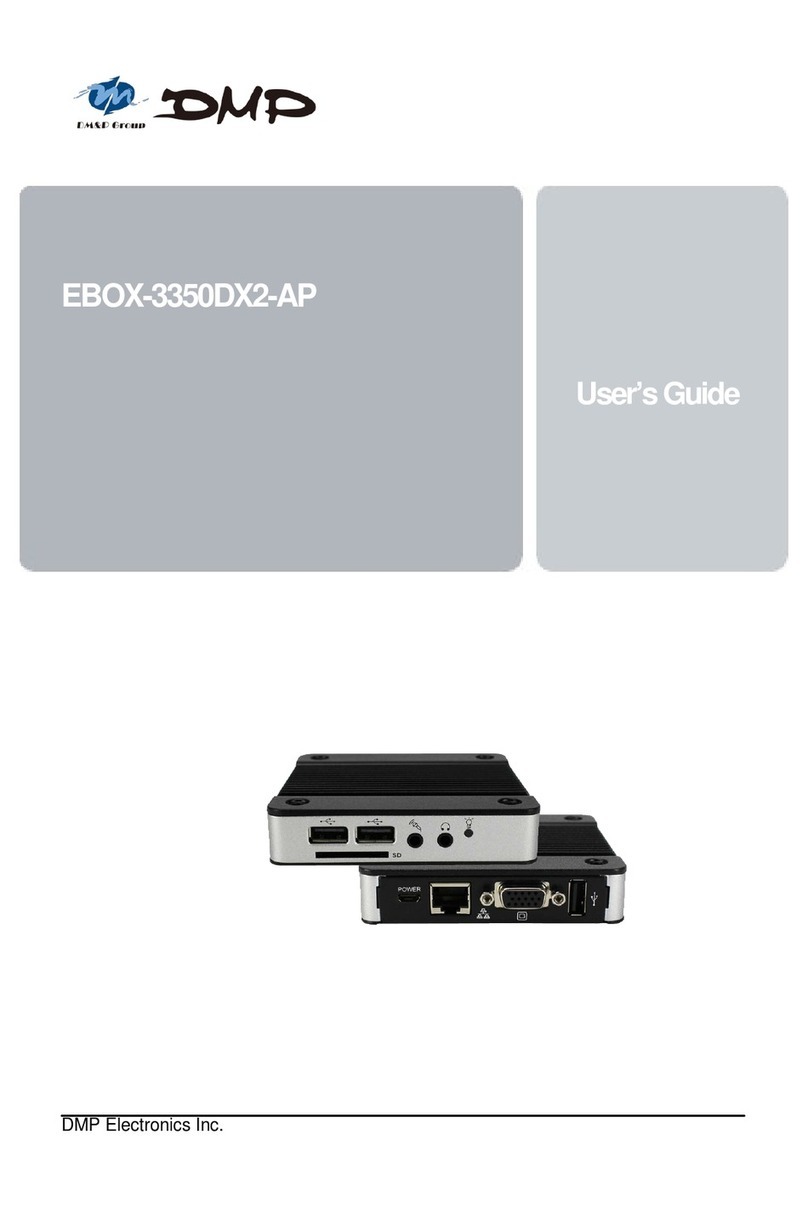
DMP Electronics
DMP Electronics EBOX-3350DX2-AP user guide
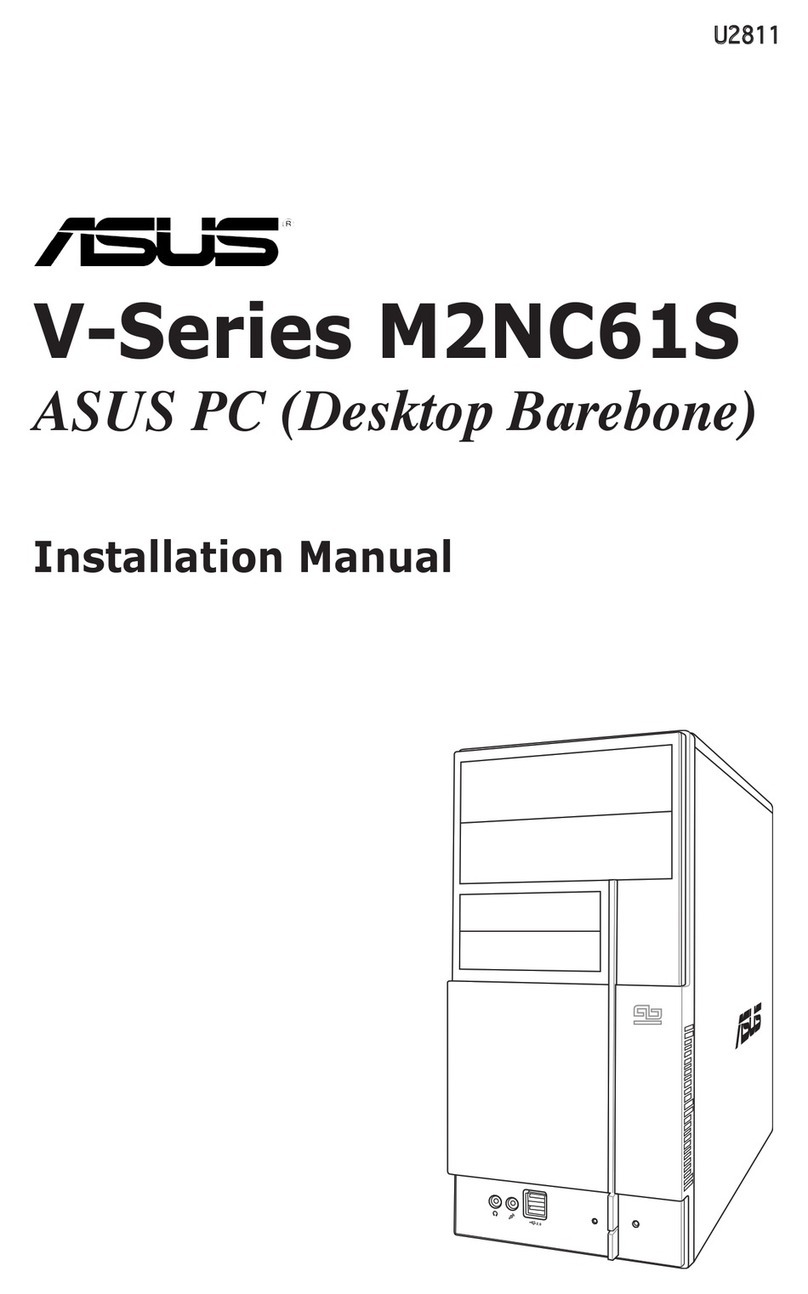
Asus
Asus V2-M2NC61S installation manual
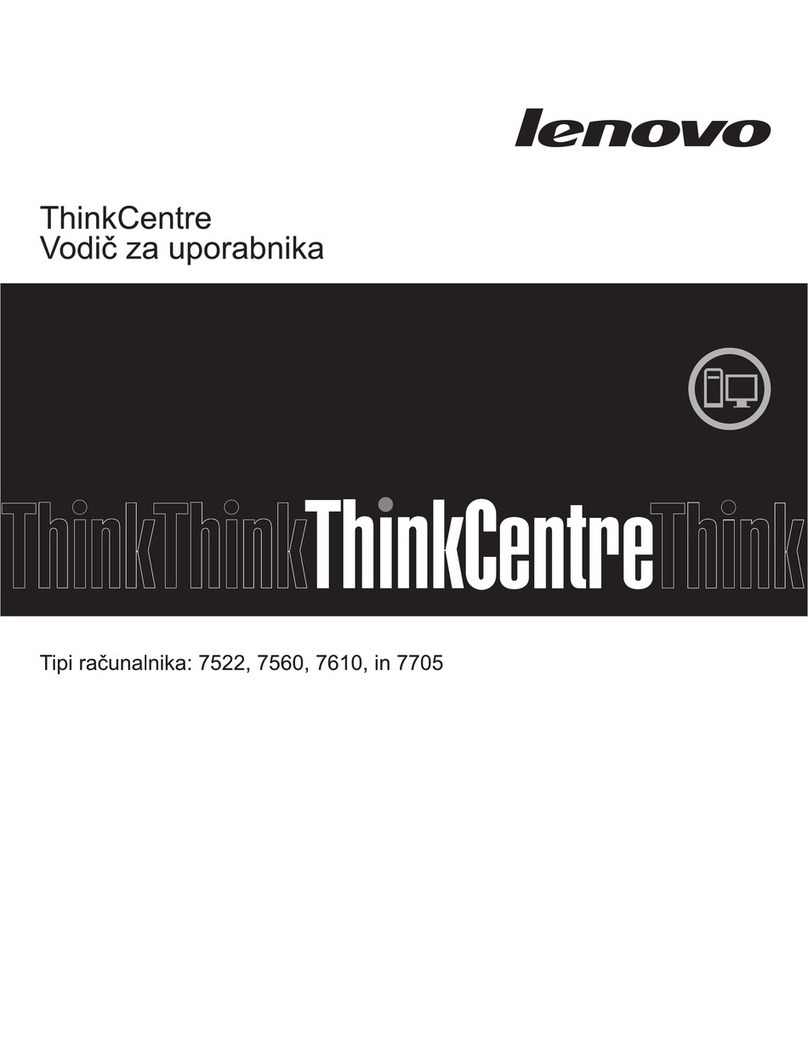
Lenovo
Lenovo ThinkCentre A58 user guide