Areva MiCOM P441 Quick start guide

MiCOM
P441/P442 & P444
Numerical Distance Protection
VC2.x
Technical Guide
P44x/EN T/E44


Technical Guide P44x/EN T/E44
MiCOM P441/P442 & P444
Page 1/2
Numerical Distance Protection
MiCOM P44x
GENERAL CONTENT
Safety Section Pxxxx/EN SS/C11
Addendum P44x/EN AD/E44
Introduction P44x/EN IT/E33
Hardware Description P44x/EN HW/E33
Application Guide P44x/EN AP/E33
Technical Data P44x/EN TD/E33
Installation P44x/EN IN/E33
Commissioning & Maintenance P44x/EN CM/E33
Commissioning Test & Record Sheet P44x/EN RS/E33
Connection Diagrams P44x/EN CO/E33
Relay Menu Database P44x/EN GC/E44
Menu Content Tables P44x/EN HI/E44
Version Compatibility P44x/EN VC/E44

P44x/EN T/E44 Technical Guide
Page 2/2
MiCOM P441/P442 & P444
BLANK PAGE

Pxxxx/EN SS/C11
SAFETY SECTION


Pxxxx/EN SS/C11
Safety Section Page 1/10
STANDARD SAFETY STATEMENTS AND EXTERNAL
LABEL INFORMATION FOR AREVA T&D EQUIPMENT
1. INTRODUCTION 3
2. HEALTH AND SAFETY 3
3. SYMBOLS AND EXTERNAL LABELS ON THE EQUIPMENT 4
3.1 Symbols: 4
3.2 Labels 4
4. INSTALLING, COMMISSIONING AND SERVICING 5
5. DECOMMISSIONING AND DISPOSAL 7
6. EQUIPMENT WHICH INCLUDES ELECTROMECHANICAL
ELEMENTS 7
7. TECHNICAL SPECIFICATIONS FOR SAFETY 8
7.1 Protective fuse rating 8
7.2 Protective Class: 8
7.3 Installation Category: 8
7.4 Environment: 8
8. COMPLIANCE MARKING FOR APPLICABLE EUROPEAN
DIRECTIVES 9
9. RECOGNIZED AND LISTED MARKS FOR NORTH AMERICA 10

Pxxxx/EN SS/C11
Page 2/10 Safety Section
BLANK PAGE

Pxxxx/EN SS/C11
Safety Section Page 3/10
1. INTRODUCTION
This guide and the relevant operating or service manual documentation for the equipment
provide full information on safe handling, commissioning and testing of this equipment and
also includes descriptions of equipment label markings.
Documentation for equipment ordered from AREVA T&D is despatched separately from
manufactured goods and may not be received at the same time. Therefore this guide is
provided to ensure that printed information which may be present on the equipment is fully
understood by the recipient.
The technical data in this safety guide is typical only, see the technical data section of the
relevant product publication(s) for data specific to a particular equipment.
Before carrying out any work on the equipment the user should be familiar with the
contents of this Safety Guide.
Reference should be made to the external connection diagram before the equipment is
installed, commissioned or serviced.
Language specific, self-adhesive User Interface labels are provided in a bag for some
equipment.
2. HEALTH AND SAFETY
The information in the Safety Section of the equipment documentation is intended to ensure
that equipment is properly installed and handled in order to maintain it in a safe condition.
It is assumed that everyone who will be associated with the equipment will be familiar with
the contents of that Safety Section, or this Safety Guide.
When electrical equipment is in operation, dangerous voltages will be present in certain parts
of the equipment. Failure to observe warning notices, incorrect use, or improper use may
endanger personnel and equipment and cause personal injury or physical damage.
Before working in the terminal strip area, the equipment must be isolated.
Proper and safe operation of the equipment depends on appropriate shipping and handling,
proper storage, installation and commissioning, and on careful operation, maintenance and
servicing. For this reason only qualified personnel may work on or operate the equipment.
Qualified personnel are individuals who
• are familiar with the installation, commissioning, and operation of the equipment and
of the system to which it is being connected;
• are able to safely perform switching operations in accordance with accepted safety
engineering practices and are authorised to energize and de-energize equipment and
to isolate, ground, and label it;
• are trained in the care and use of safety apparatus in accordance with safety
engineering practices;
• are trained in emergency procedures (first aid).
The operating manual for the equipment gives instructions for its installation, commissioning,
and operation. However, the manual cannot cover all conceivable circumstances or include
detailed information on all topics. In the event of questions or specific problems, do not take
any action without proper authorization. Contact the appropriate AREVA technical sales
office and request the necessary information.

Pxxxx/EN SS/C11
Page 4/10 Safety Section
3. SYMBOLS AND EXTERNAL LABELS ON THE EQUIPMENT
For safety reasons the following symbols and external labels, which may be used on the
equipment or referred to in the equipment documentation, should be understood before the
equipment is installed or commissioned.
3.1 Symbols:
Caution: refer to equipment documentation Caution: risk of electric shock
Protective Conductor (*Earth) terminal. Functional/Protective Conductor Earth
terminal
Note – This symbol may also be used for a Protective Conductor (Earth) terminal if that
terminal is part of a terminal block or sub-assembly e.g. power supply.
*NOTE: THE TERM EARTH USED THROUGHOUT THIS GUIDE IS THE DIRECT
EQUIVALENT OF THE NORTH AMERICAN TERM GROUND.
3.2 Labels
See “Safety Guide” (SFTY/4L M) for equipment labelling information.

Pxxxx/EN SS/C11
Safety Section Page 5/10
4. INSTALLING, COMMISSIONING AND SERVICING
Equipment connections
Personnel undertaking installation, commissioning or servicing work for this
equipment should be aware of the correct working procedures to ensure safety.
The equipment documentation should be consulted before installing,
commissioning or servicing the equipment.
Terminals exposed during installation, commissioning and maintenance may
present a hazardous voltage unless the equipment is electrically isolated.
Any disassembly of the equipment may expose parts at hazardous voltage, also
electronic parts may be damaged if suitable electrostatic voltage discharge (ESD)
precautions are not taken.
If there is unlocked access to the rear of the equipment, care should be taken by
all personnel to avoid electric shock or energy hazards.
Voltage and current connections should be made using insulated crimp
terminations to ensure that terminal block insulation requirements are maintained
for safety.
To ensure that wires are correctly terminated the correct crimp terminal and tool
for the wire size should be used.
The equipment must be connected in accordance with the appropriate connection
diagram.
Protection Class I Equipment
Before energising the equipment it must be earthed using the protective conductor
terminal, if provided, or the appropriate termination of the supply plug in the case
of plug connected equipment.
The protective conductor (earth) connection must not be removed since the
protection against electric shock provided by the equipment would be lost.
The recommended minimum protective conductor (earth) wire size is 2.5 mm²
(3.3 mm² for North America) unless otherwise stated in the technical data section
of the equipment documentation, or otherwise required by local or country wiring
regulations.
The protective conductor (earth) connection must be low-inductance and as short
as possible.
All connections to the equipment must have a defined potential. Connections that
are pre-wired, but not used, should preferably be grounded when binary inputs
and output relays are isolated. When binary inputs and output relays are
connected to common potential, the pre-wired but unused connections should be
connected to the common potential of the grouped connections.
Before energising the equipment, the following should be checked:
Voltage rating/polarity (rating label/equipment documentation);
CT circuit rating (rating label) and integrity of connections;
Protective fuse rating;
Integrity of the protective conductor (earth) connection (where applicable);
Voltage and current rating of external wiring, applicable to the application.

Pxxxx/EN SS/C11
Page 6/10 Safety Section
Equipment Use
If the equipment is used in a manner not specified by the manufacturer, the
protection provided by the equipment may be impaired.
Removal of the equipment front panel/cover
Removal of the equipment front panel/cover may expose hazardous live parts
which must not be touched until the electrical power is removed.
UL and CSA Listed or Recognized Equipment
To maintain UL and CSA approvals the equipment should be installed using UL
and/or CSA Listed or Recognized parts of the following type: connection cables,
protective fuses/fuseholders or circuit breakers, insulation crimp terminals, and
replacement internal battery, as specified in the equipment documentation.
Equipment operating conditions
The equipment should be operated within the specified electrical and
environmental limits.
Current transformer circuits
Do not open the secondary circuit of a live CT since the high voltage produced
may be lethal to personnel and could damage insulation.
Generally, for safety, the secondary of the line CT must be shorted before opening
any connections to it.
For most equipment with ring-terminal connections, the threaded terminal block for
current transformer termination has automatic CT shorting on removal of the
module. Therefore external shorting of the CTs may not be required, the
equipment documentation should be checked to see if this applies.
For equipment with pin-terminal connections, the threaded terminal block for
current transformer termination does NOT have automatic CT shorting on removal
of the module.
External resistors, including voltage dependent resistors (VDRs)
Where external resistors, including voltage dependent resistors (VDRs), are fitted
to the equipment, these may present a risk of electric shock or burns, if touched.
Battery replacement
Where internal batteries are fitted they should be replaced with the recommended
type and be installed with the correct polarity to avoid possible damage to the
equipment, buildings and persons.
Insulation and dielectric strength testing
Insulation testing may leave capacitors charged up to a hazardous voltage. At the
end of each part of the test, the voltage should be gradually reduced to zero, to
discharge capacitors, before the test leads are disconnected.
Insertion of modules and pcb cards
Modules and pcb cards must not be inserted into or withdrawn from the equipment
whilst it is energised, since this may result in damage.
Insertion and withdrawal of extender cards
Extender cards are available for some equipment. If an extender card is used, this
should not be inserted or withdrawn from the equipment whilst it is energised. This
is to avoid possible shock or damage hazards. Hazardous live voltages may be
accessible on the extender card.
Insertion and withdrawal of integral heavy current test plugs
It is possible to use an integral heavy current test plug with some equipment.
CT shorting links must be in place before insertion or removal of heavy current
test plugs, to avoid potentially lethal voltages.

Pxxxx/EN SS/C11
Safety Section Page 7/10
External test blocks and test plugs
Great care should be taken when using external test blocks and test plugs such as
the MMLG, MMLB and MiCOM P990 types, hazardous voltages may be
accessible when using these. *CT shorting links must be in place before the
insertion or removal of MMLB test plugs, to avoid potentially lethal voltages.
*Note – when a MiCOM P992 Test Plug is inserted into the MiCOM P991 Test
Block, the secondaries of the line CTs are automatically shorted, making them
safe.
Fibre optic communication
Where fibre optic communication devices are fitted, these should not be viewed
directly. Optical power meters should be used to determine the operation or signal
level of the device.
Cleaning
The equipment may be cleaned using a lint free cloth dampened with clean water,
when no connections are energised. Contact fingers of test plugs are normally
protected by petroleum jelly which should not be removed.
5. DECOMMISSIONING AND DISPOSAL
Decommissioning:
The supply input (auxiliary) for the equipment may include capacitors across the
supply or to earth. To avoid electric shock or energy hazards, after completely
isolating the supplies to the equipment (both poles of any dc supply), the
capacitors should be safely discharged via the external terminals prior to
decommissioning.
Disposal:
It is recommended that incineration and disposal to water courses is avoided.
The equipment should be disposed of in a safe manner. Any equipment
containing batteries should have them removed before disposal, taking
precautions to avoid short circuits. Particular regulations within the country of
operation, may apply to the disposal of batteries.
6. EQUIPMENT WHICH INCLUDES ELECTROMECHANICAL ELEMENTS
Electrical adjustments
It is possible to change current or voltage settings on some equipment by direct
physical adjustment e.g. adjustment of a plug-bridge setting. The electrical power
should be removed before making any change, to avoid the risk of electric shock.
Exposure of live parts
Removal of the cover may expose hazardous live parts such as relay contacts,
these should not be touched before removing the electrical power.

Pxxxx/EN SS/C11
Page 8/10 Safety Section
7. TECHNICAL SPECIFICATIONS FOR SAFETY
7.1 Protective fuse rating
The recommended maximum rating of the external protective fuse for equipments is 16A,
high rupture capacity (HRC) Red Spot type NIT, or TIA, or equivalent, unless otherwise
stated in the technical data section of the equipment documentation. The protective fuse
should be located as close to the unit as possible.
DANGER - CTS MUST NOT BE FUSED SINCE OPEN CIRCUITING THEM
MAY PRODUCE LETHAL HAZARDOUS VOLTAGES.
7.2 Protective Class:
IEC 61010-1: 2001
EN 61010-1: 2001
Class I (unless otherwise specified in the equipment
documentation). This equipment requires a protective
conductor (earth) connection to ensure user safety.
7.3 Installation Category:
IEC 61010-1: 2001
EN 61010-1: 2001
Installation Category III (Overvoltage Category III):
Distribution level, fixed installation.
Equipment in this category is qualification tested at
5 kV peak, 1.2/50 µs, 500 Ω, 0.5 J, between all
supply circuits and earth and also between
independent circuits
7.4 Environment:
The equipment is intended for indoor installation and use only. If it is required for use in an
outdoor environment then it must be mounted in a specific cabinet or housing which will
enable it to meet the requirements of IEC 60529 with the classification of degree of
protection IP54 (dust and splashing water protected).
Pollution Degree – Pollution
Degree 2
Altitude – operation up to 2000 m
IEC 61010-1: 2001
EN 61010-1: 2001
Compliance is demonstrated by reference to safety
standards.

Pxxxx/EN SS/C11
Safety Section Page 9/10
8. COMPLIANCE MARKING FOR APPLICABLE EUROPEAN DIRECTIVES
The following European directives may be applicable to the equipment, if so it will carry the
relevant marking(s) shown below:
Marking
Compliance with all relevant European
Community directives:
Product safety:
Low Voltage Directive - 73/23/EEC
amended by 93/68/EEC
EN 60255-5: 2001
Relevant clauses of
EN 61010-1: 2001
EN 60950-1: 2001
EN 60664-1: 2003.
Compliance demonstrated by reference to safety
standards.
Electromagnetic Compatibility Directive
(EMC) 89/336/EEC amended by
93/68/EEC.
The following Product Specific Standard
was used to establish conformity:
EN 50263 : 2000
Compliance demonstrated via the Technical
Construction File route.
Where applicable :
II (2) G
ATEX Potentially Explosive
Atmospheres directive 94/9/EC,
for equipment.
The equipment is compliant with Article 1(2) of European
directive 94/9/EC. It is approved for operation outside an
ATEX hazardous area. It is however approved for
connection to Increased Safety, “Ex e”, motors with rated
ATEX protection, Equipment Category 2, to ensure their
safe operation in gas Zones 1 and 2 hazardous areas.
CAUTION – Equipment with this marking is not itself
suitable for operation within a potentially explosive
atmosphere.
Compliance demonstrated by Notified Body certificates of
compliance.
Radio and Telecommunications
Terminal Equipment (R & TTE)
directive 95/5/EC.
Compliance demonstrated by compliance to the Low
Voltage Directive, 73/23/EEC amended by 93/68/EEC,
down to zero volts, by reference to safety standards.

Pxxxx/EN SS/C11
Page 10/10 Safety Section
9. RECOGNIZED AND LISTED MARKS FOR NORTH AMERICA
CSA - Canadian Standards Association
UL - Underwriters Laboratory of America
If applicable, the following marks will be present on the equipment:
– UL Recognized to UL (USA) requirements
– UL Recognized to UL (USA) and CSA (Canada) requirements
– UL Listed to UL (USA) requirements
– UL Listed to UL (USA) and CSA (Canada) requirements
– Certified to CSA (Canada) requirements

Update Documentation P44x/EN AD/E44
MiCOM P441, P442 & P444
UPDATE DOCUMENTATION
VERSION C2.X


Update Documentation P44x/EN AD/E44
MiCOM P441, P442 & P444
Page 1/82
P44X UPDATE DOCUMENTATION
In the firmware version C2.x of P441, P442 & P444, several changes in hardware & software
on existing features have been added. These are described with reference to the
documentation listed below:
Release Version Documentation
April 2004 P44x/EN T/E33 Technical Manual
(Firmware version B1.2)
Document Ref. Section Page No. Description
2. 4/24 Introduction to MiCOM Guide:
Ref P440/EN BR/Eb has been removed
UCA2 has been added
3.1.1 5/24 New Front Panel:
Front panel – new design
(hotkeys explanations-LCD contrast)
3.1.2 6/24 Ethernet board + InterMicom/2nd rear port added
3.2 9/24 UCA2 added in the table+DNP3Floc in%
3.6.3 14/24 Hotkeys menu navigation
3.9 23/24 Second rear communication port
3.10 24/24 InterMiCOM teleprotection
P44x/EN IT/E33
3.11 24/24 Ethernet Rear Port: UCA2 Communication
1.1.5 5/44 Inputs & Outputs Boards:
P444 – option with 46 outputs
Fast outputs in option
Hysteresis remark
1.1.7 5/44 Second rear port & InterMiCOM
1.1.8 5/44 Ethernet board
2.1
2.2
8/44
8/44
Section 2 – Hardware Module
TMS 150MHz
Coprocessor board – item corrected & section
removed
2.4.3 9/44 Duals optos
2.7 11/44 Second rear port
2.8 11/44 Ethernet board
3.3 14/44 Platform Software: DNP3-UCA2
3.3.1 14/44 Record Login: 96 alarms
3.4.1 15/44 P440 Overview : 48 samples / 24 samples
3.4.5 16/44 Disturbance Recorder: Additive commentsr
4 17/44 Distance Algorithms: Priority between the 2
algorithms
4.1 18/44 Distance & Resistance Measurement:
24 Samples & remark Rfault Dfault
4.2 21/44 Delta Algorithms: “computed in parallel”
4.2.1 22/44 Network Status monitoring: 48 samples since
C1.x
4.3 28/44 Conventional Algorithms: Comments added
P44x/EN HW/E33
4.3.1 29/44 Convergence Analysis: 15 loops

P44x/EN AD/E44 Update Documentation
Page 2/82
MiCOM P441, P442 & P444
Document Ref. Section Page No. Description
4.3.5 32/44 New page make up & I>3 comment & SOTF
settings with 13 bits
4.5 33/44 Tripping Logic: Comments about General trip
equation & Timers initiated with the start
4.7 36/44 Power Swing Detection: Out Of Step (OOS)
comments
4.7.1 36/44 Pswing (PS) updated (Ph/Ph detection)
4.7.2 37/44 Power Swing during Open Pole (Ph/Ph
detection)
4.7.4 37/44 Pswing (PS) & OOS updated (Delta Current)
4.9 40&41/44 DEF: comments added
Iev corrected in Irev & settings range
1.2.1 8/220 Protection Features:
49:Thermal Overlaod – 68:Out Of Step
1.3 10/220 DDB& model n° 30 comments added
2.1 12/220 Configuration column : new features added
Distance characteristic with Tilt fig1 –Fig2
2.5.1 15/220 Z1X opto
2.7.1 18/220 New distance settings
2.7.2.1 20/220 Fig3- remark about symbols in Scheme Logic
2.7.7 27/220 Single ph loop R value – new PS detected on
PP loop
2.9.3 47-49/220 Weak Infeed improved – PAP function for RTE
2.12.2 61/220 TOR-SOTF bits ref
2.13.2 69/220 Power Swing – Delta Current
2.13.5 NEW New Section: Out Of Step Logic
2.17 82/220 IN>3 – IN>4 created
2.18.3 89/220 DEF improved
4.4.5.1 123/220 Bus/line cells for synchrocheck
4.5.1 126/220 5bits added in AR lockout
(Zsp / IN>3 / IN>4 / PAP / Thermal)
4.9 166/220 Event Recorder: AREVA name
5.1.1 176/220 Zsp Function: Diagram amended with Ta
6.1 181/220 Reference of Software version
P44x/EN AP/E33
8 189/220 Comments for ref models n° by branch
9 New Additional functions – Version C2x
New reference 030G/H/J
9.1 Hardware new features
9.2 Function Improved : Distance
9.3 New Function Description : Out Of Step & Stable
Swing
9.4 Function Improved: DEF
9.5 New Function Description: IN>3 – IN>4
9.6 New Function Description: Thermal Overload (as
P443)
P44x/EN AP/E33
NEW SECTION
9.7 New Function Description: PAP – RTE feature
This manual suits for next models
2
Table of contents
Other Areva Other manuals
Popular Other manuals by other brands
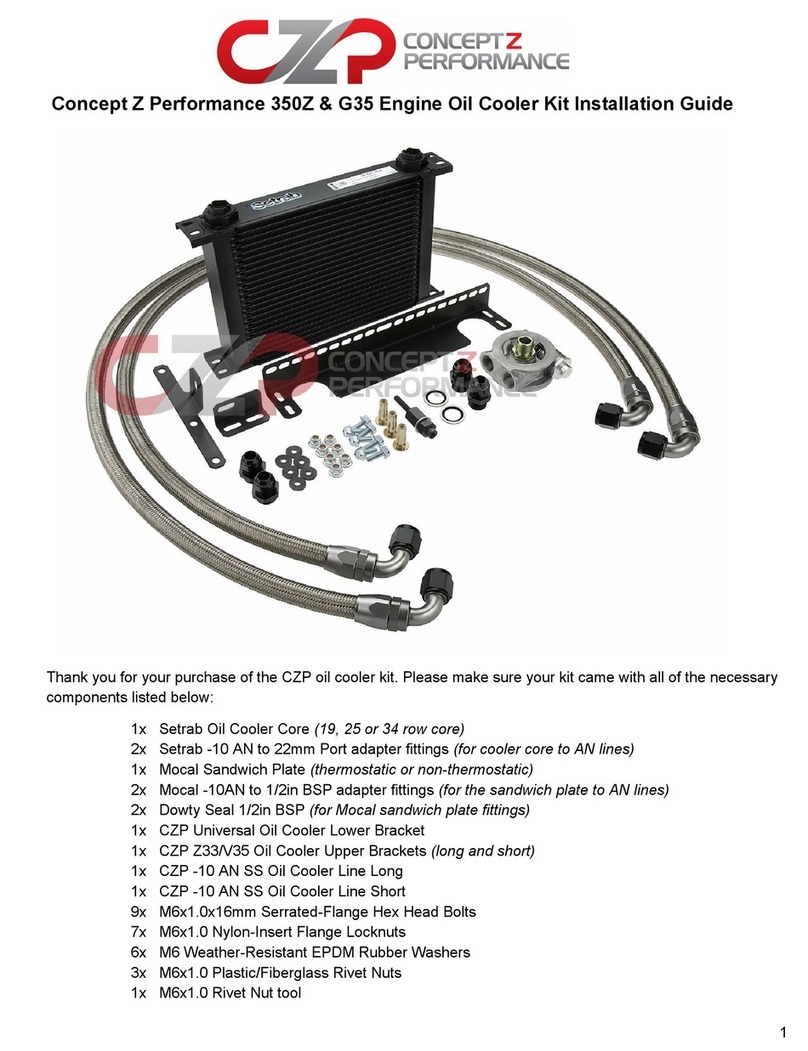
Concept Z Performance
Concept Z Performance 350Z installation guide
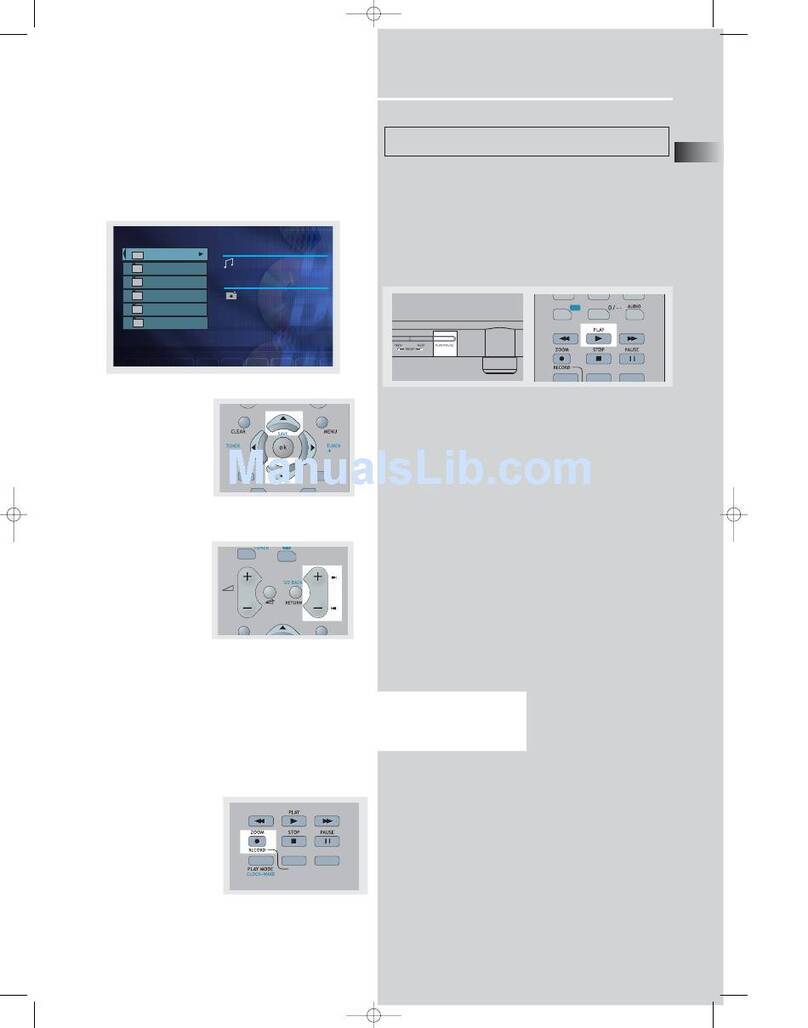
THOMSON
THOMSON DPL907VD-JPEG manual
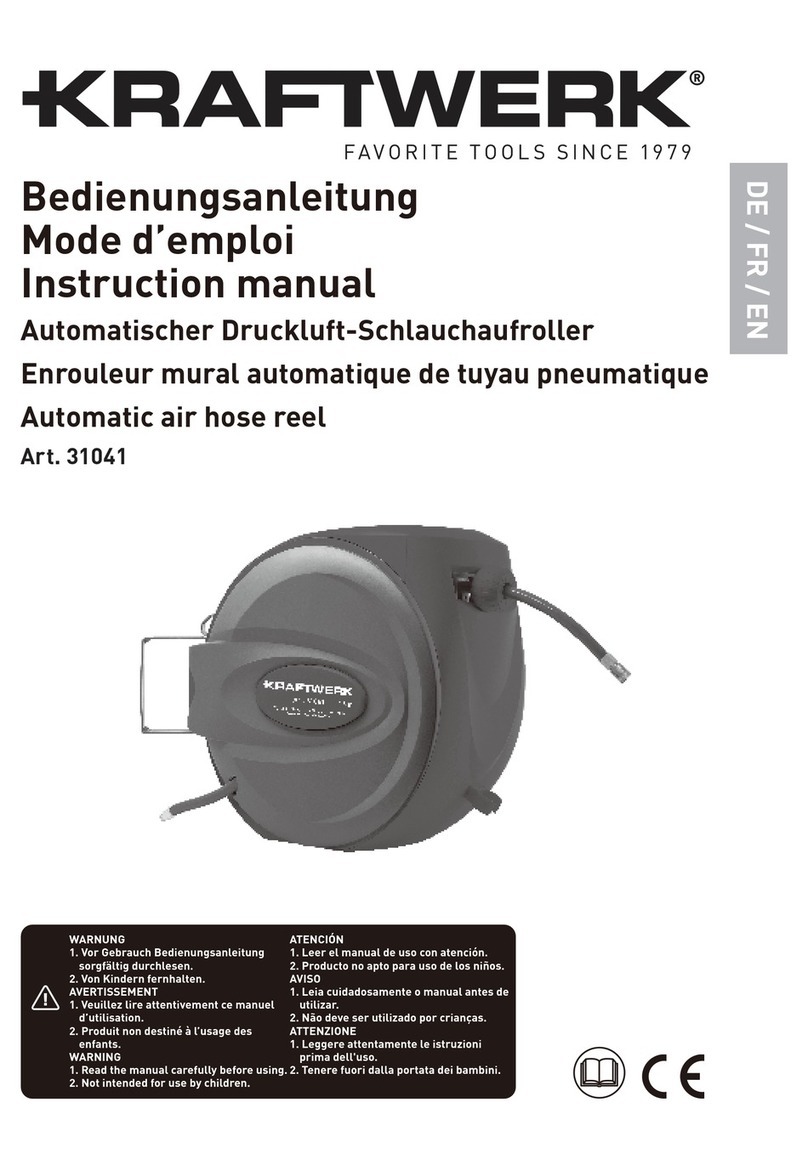
KRAFTWERK
KRAFTWERK 31041 instruction manual
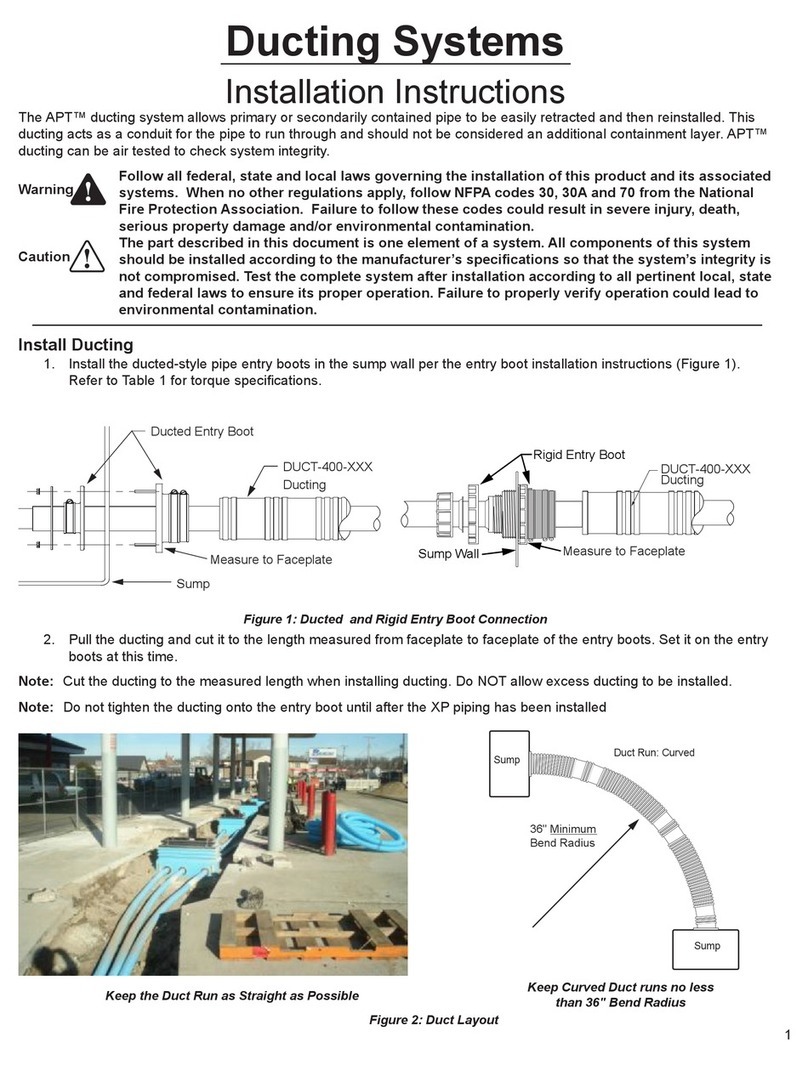
Franklin Fueling Systems
Franklin Fueling Systems APT installation instructions
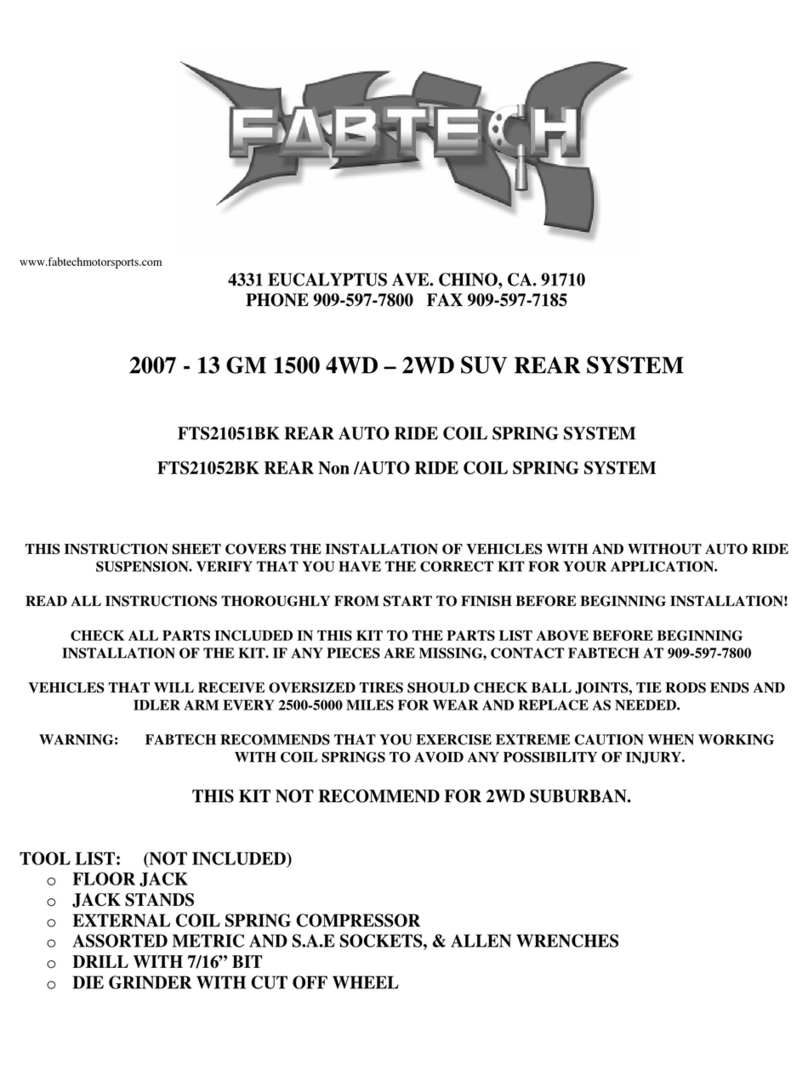
Fabtech
Fabtech FTS21052BK instruction sheet
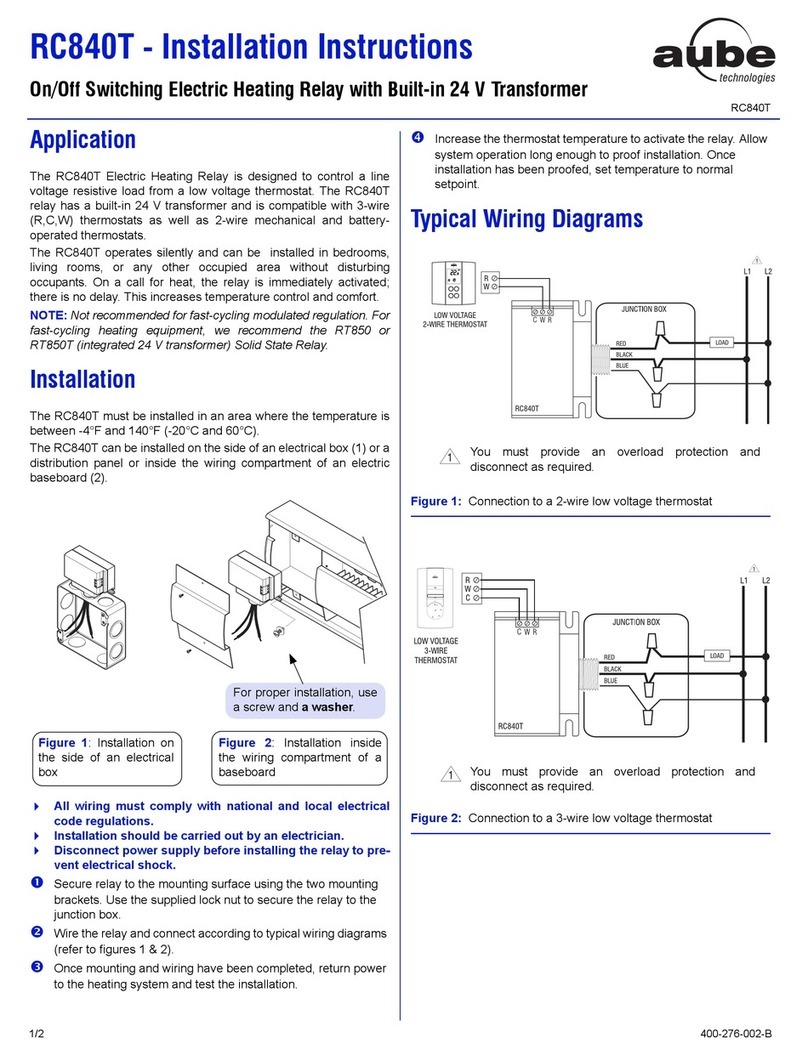
Aube Technologies
Aube Technologies RC840T Installation instructions manual
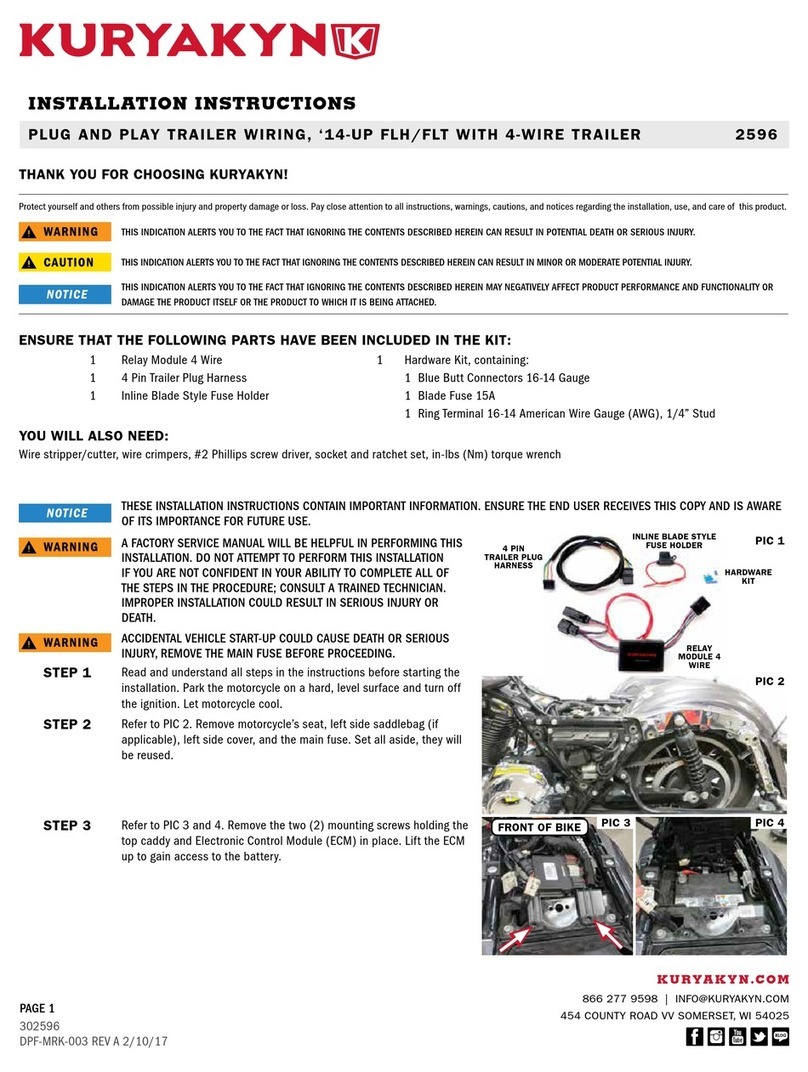
Kuryakyn
Kuryakyn 2596 Installation instructions manual

Marantz
Marantz 2294 manual
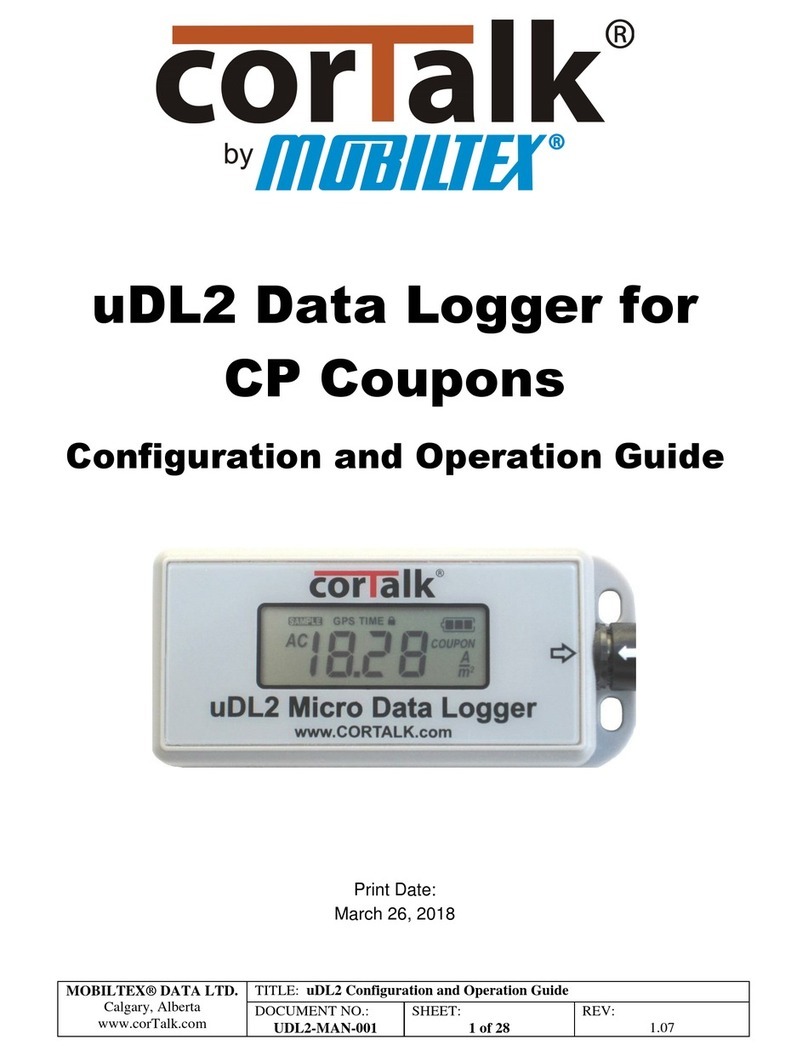
Cortalk
Cortalk uDL2 Configuration & operation guide

GRASS VALLEY
GRASS VALLEY Kaleido-X16 Hardware description and installation manual

CAVIDYNE
CAVIDYNE CaviBlaster 2828-D Operation and maintenance manua
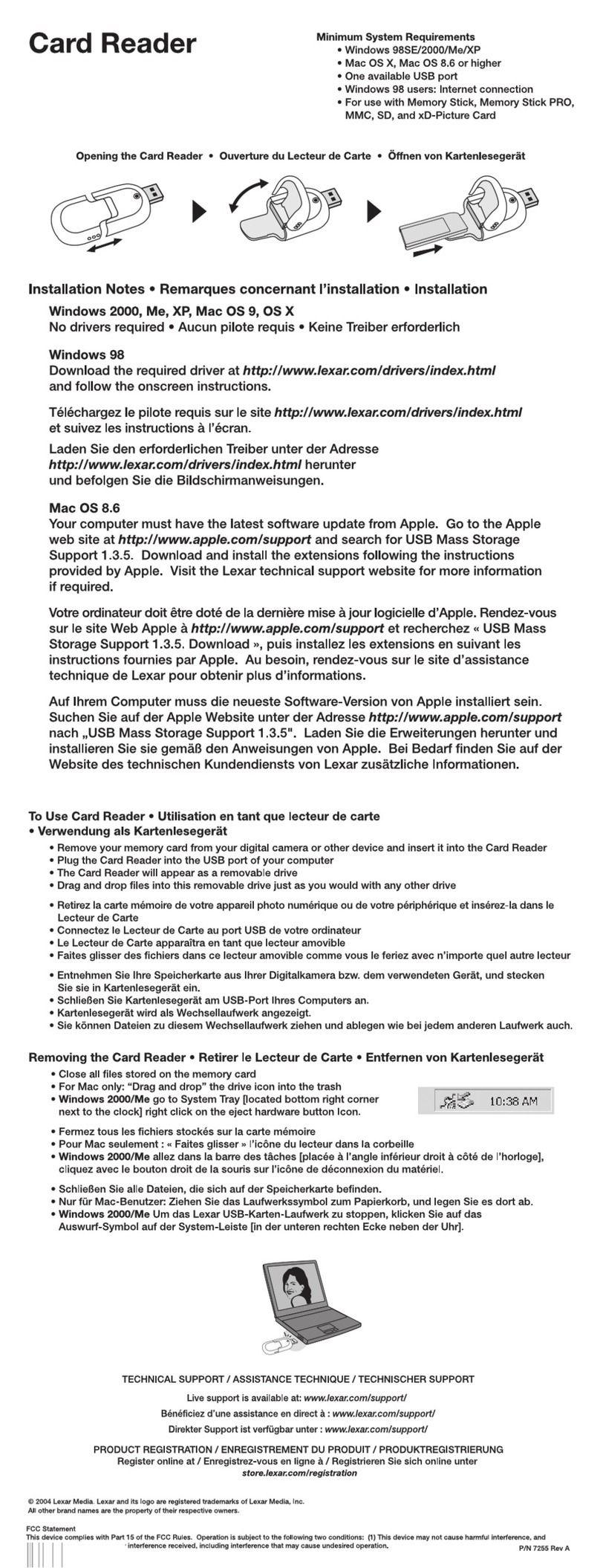
Lexar
Lexar CARD READER Installation