Astronics Max-Viz 1500 Quick setup guide

Astronics Max-Viz Max-Viz 1500 3091-00019 Rev M
Information Manual
Max-Viz 1500 Enhanced Vision System

Astronics Max-Viz Max-Viz 1500 3091-00019 Rev M
See What You’ll Be Missing
This document is private and confidential and is supplied on
the express condition that it is not copied or communicated to
another person without the written permission of:
Astronics Max-Viz
11241 SE Highway 212
Clackamas, Oregon 97015 USA
This product is protected by patents and patents pending.

Astronics Max-Viz Max-Viz 1500 3091-00019 Rev M
Revision History
Revision
Date
Change Description
-
2/16/07
Initial Release
A
2/26/07
Fixed header and footer to standardize with
other documents,
added text concerning two video outputs to
section 3.1.4,
and added Cable Assy –Sensor I/F to
Appendix A
B
9/25/07
Updated Max Power specification, changed the
name of Power Supply/Processor to Power
Supply, updated Interface connections to
remove Digital Video between Sensor and
Power Supply, removed Video # 2 output from
Power Supply, updated connector backshell
part numbers, updated description of video
outputs in section 3.1.4 to reflect a single
video output, updated power-up sequence in
section 4. Operation. Updated Interface
Drawing 952500015 and Cable Assy- EVS
1500 Sensor Interconnect 955000016, in
Appendix A.
C
2/21/08
Update the weight of the Power Supply LRU to
< 2.65 lbs.
D
4/16/08
Updated the Export Control section 2.4 from
ITAR controlled to Commerce Controlled and
changed the NUC period from 5 to 4 minutes
E
8/14/08
Updated the Interface Drawing and Sensor
Interconnect Drawing in Appendix A
F
5/1/09
Removed mention of black hot polarity from
page 11, clarified heater control in 6.4 Halo
Images, all mentions of NUC interval are now
4 minutes and fixed several typos.
G
12/08/2010
Updated the Max-Viz logo on page 1,
Updated the address on this manual,
Updated Warranty Form and Customer Service
form to latest revisions.

Astronics Max-Viz Max-Viz 1500 3091-00019 Rev M
H
06/06/2011
Updated to Add Patent language on page 2,
Updated logo in the header,
Added email address to Section 7,
Updated Warranty Form and Customer Service
Form to latest revisions.
J
09/28/2015
Changed Germanium Lens to Germanium
Window and added warning about the use of
Corrosion X to sections 6.2 and 6.3.
K
03/31/16
Updated company mailing address. Changed
Product name to Max-Viz 1500. Updated font
style and spacing for Table of Contents
L
8/29/16
Changed the recommended coax cable to PIC
V76261.
M
11/10/16
Changed the part number of the Camera Back
shell and added Max-Viz part numbers for the
back shells.

Astronics Max-Viz Max-Viz 1500 3091-00019 Rev M
Table of Contents
1. Introduction ..............................................................................................................................6
2. System Description ...................................................................................................................6
2.1. Equipment Identification.......................................................................................................6
2.2. Electrical Characteristics .......................................................................................................6
2.3. Physical Characteristics ........................................................................................................7
2.4. Export Control .....................................................................................................................7
3. Installation Planning ................................................................................................................7
3.1. Interface Connections ..........................................................................................................8
3.2. Recommended Installation Procedure..................................................................................11
3.3. Installation Assistance ........................................................................................................11
4. Operation.................................................................................................................................11
5. Maintenance .......................................................................................................................12
6. Warnings, Cautions, and Guidance ....................................................................................13
6.1. Electromagnetic Interference ..............................................................................................13
6.2. Germanium Window Breakage ............................................................................................13
6.3. Germanium Window Cleaning .............................................................................................13
6.4. Halo Images ...................................................................................................................... 13
6.5. Ice Effects and Body Heaters ..............................................................................................14
6.6. Image Quality and Interpretation ........................................................................................14
6.7. Nitrogen Added to Sensor...................................................................................................14
6.8. Non-Uniformity Correction (NUC) ........................................................................................ 15
6.9. Video Signal Interruption/ Improper Display Settings ...........................................................15
7. Max-Viz, Inc. Contact Information..................................................................................... 15
Appendix A ...............................................................................................................................16
Warranty Registration Form ....................................................................................................23
Customer Service Request Form / Return Material Authorization ..........................................24

Astronics Max-Viz Max-Viz 1500 3091-00019 Rev M
1. INTRODUCTION
This document provides guidance on the installation, operation, and maintenance of the
Max-Viz 1500 Enhanced Vision System (EVS) product.
2. SYSTEM DESCRIPTION
The Max-Viz 1500 is comprised of two Line Replaceable Units (LRUs) designed to
provide the flight crew with enhanced visual awareness of terrain and potential
obstacles in the aircraft’s forward field of view.
Sensor LRU
Power Supply LRU
The Sensor LRU includes a long-wave infrared (IR) camera assembly that processes a
digital video signal with advanced and patented Automatic Gain Control (AGC)
algorithms, and sends it to the Power Supply as an RS-170 signal via coax cable. The
normal horizontal field of view is 53 degrees. When the ZOOM_IN discrete input signal
is activated, the field of view is switched to 30 degrees.
The Power Supply LRU provides the Sensor with power and all electrical interfaces. The
Power Supply receives and buffers the RS-170 video signal and sends it to a video
display. An interface control drawing showing the top-level system is available in
Appendix A.
The video image presented on a display represents a thermal scene of the area in front
of the aircraft and provides the flight crew with enhanced vision capability in low
visibility conditions.
2.1. Equipment Identification
The Max-Viz 1500 system components are identified below.
Name
Part Number
Description
Sensor
756500041
Max-Viz 1500 Sensor Assembly
Power Supply
756500042
Max-Viz 1500 Power Control Assembly
2.2. Electrical Characteristics
The Max-Viz 1500 does not require any supplemental heating or cooling from the
aircraft and the electrical characteristics are listed below.
Characteristic
Specification
Voltage
28 VDC from aircraft power
Max Current at 28 VDC
5.0 A (140 Watts, heaters activated)

Astronics Max-Viz Max-Viz 1500 3091-00019 Rev M
2.3. Physical Characteristics
The physical characteristics of the two Max-Viz 1500 LRUs are listed below.
Characteristic
Specification
Sensor
Sensor Unit Diameter:
Depth:
Overall length:
Weight:
2.770 inch Diameter (70,3 mm)
6.179 in. (156,9 mm)
6.828 in. (173,4 mm)
< 2.5 lbs (1,13 kg)
Power Supply
Height:
Width (Enclosure):
Width (Overall):
Depth (Enclosure):
Weight:
2.250 in. (57,1 mm)
3.750 in. (95,2 mm)
5.330 in. (135,4 mm)
5.00 in. (127,0 mm)
< 2.65 lbs (1,20 kg)
2.4. Export Control
Export of the Max-Viz 1500 Sensor is governed by the Commerce Department, Bureau
of Industry and Security. The Sensor has Export Control Classification Number (ECCN)
of 6A003.b.4.b.
Max-Viz 1500 commodities, technology, or software shall be exported from the United
States in accordance with the Export Administration Regulations. Diversion contrary to
U.S. law is prohibited.
3. INSTALLATION PLANNING
All installations in certified aircraft should be performed per FAA-approved installation
instructions, such as an STC or service bulletin. This information is provided to assist in
the design of a certified installation. It is also provided to assist in non-certified aircraft
installations.
The Max-Viz 1500 is limited to a max altitude of 55,000 feet and a operating
temperature of -55C to +70C.
The +28 Vdc supply to the Power Supply should be routed through a suitably labeled
circuit breaker. Particular attention must be taken in routing the RS-170 video coax
cable through the aircraft structure to avoid potential RFI from noise items and to
minimize the cable bend radii.

Astronics Max-Viz Max-Viz 1500 3091-00019 Rev M
3.1. Interface Connections
3.1.1. Interconnect Pin-outs between Sensor LRU and Power Supply LRU
The cable harness between the Sensor and the Power Supply can be fabricated from
standard 22 AWG aircraft wire (e.g., M27500 twisted shielded pair). A typical
installation length is 14 to 24 inches depending on the actual locations of the two LRUs.
Notes:
Maximum recommended LRU separation is 100 feet.
If the harness between the Sensor and Power Supply is longer than 12 feet, a
larger AWG size is recommended (video coax excluded).
Pin numbers are the same at each connector between the Sensor and Power
Supply.
An overall metal cable shield tied to both ends into the connector backshells is
recommended.
TP = Twisted Pair.
If additional bulkhead connectors are connected in-line, each contact must be
rated for 5 Amps or more.
Under no circumstance may signals from multiple pins be spliced and carried in a
single wire.
Sensor
Connector
Pin No.
Description
Recommended Wire
Power Supply
Connector Pin No.
1
+ 28 VDC Heater
22 AWG Shielded TP1
1
2
28 VDC RTN Heater
22 AWG Shielded TP1
2
3
+ 28 VDC Heater
22 AWG Shielded TP2
3
4
28 VDC RTN Heater
22 AWG Shielded TP2
4
5
28 VDC RTN Switched
22 AWG Shielded TP3
5
6
28 VDC RTN Switched
22 AWG Shielded TP3
6
7
+ 15 VDC
22 AWG Shielded TP4
7
8
15 VDC RTN
22 AWG Shielded TP4
8
9
+ 15 VDC
22 AWG Shielded TP5
9
10
15 VDC RTN
22 AWG Shielded TP5
10
11
RTD +
22 AWG Shielded TP6
11
12
RTD --
22 AWG Shielded TP6
12
13
RS 232 +
22 AWG Shielded TP7
13
14
RS 232 RTN
22 AWG Shielded TP7
14
15
RS 232 --
22 AWG Shielded TP8
15
16
RS 232 RTN
22 AWG Shielded TP8
16
17
17
18
Chassis/Shields
22 AWG
18
19
19

Astronics Max-Viz Max-Viz 1500 3091-00019 Rev M
Sensor
Connector
Pin No.
Description
Recommended Wire
Power Supply
Connector Pin No.
20
20
21
RS 170 Video
RG-179 (Pic Wire &
Cable P/N V76261)
21
22
RS 170 Video RTN
Coax shield/Braid
22
3.1.2. Interconnect Pin-outs From Power Supply and Aircraft
The cable harness from the Power Supply to the aircraft can be fabricated from
standard 22 AWG aircraft wire (e.g., M27500 twisted shielded pair). If the harness to
the Power Supply is longer than 12 feet, a larger AWG size is recommended (video coax
excluded).
Pin Number
Description
Recommended Wire
1
+ 28 VDC
22 AWG Shielded TP1
2
28 VDC RTN
22 AWG Shielded TP1
3
+ 28 VDC
22 AWG Shielded TP2
4
28 VDC RTN
22 AWG Shielded TP2
5
Chassis/Shield
22 AWG
6
7
8
9
ZOOM_IN
22 AWG
10
NUC_IN
22 AWG
11
12
RS 170 Video
RG 179 (Pic Wire & Cable P/N V76261)
13
RS 170 Video RTN
Coax shield/braid
Notes:
1. A discrete input (ZOOM_IN) is provided to control the field of view (FOV)
switching function as follows:
a. Left open or grounded to 0 volts (< 2 volts), the wide angle, 53°, FOV is
selected.
b. Held at 28 volts (> 7 volts), the narrow angle, 30°, FOV is selected.
2. The 28 V discrete input is provided to control the Non-Uniform Correction (NUC)
function as follows:
a. Left open or grounded to 0 volts (< 2 volts), NUC automatically occurs at
programmed intervals.
b. On transition from 0 to 28 volts (> 7 volts), one NUC cycle occurs and
then further NUC cycles are inhibited until the input goes back to 0 (< 2
volts).
c. On transition from 28 to 0 volts (< 2 volts), one NUC cycle occurs and
then further NUC cycles automatically occur at programmed intervals.

Astronics Max-Viz Max-Viz 1500 3091-00019 Rev M
3.1.3. Interface Connectors
The connectors required to fabricate a harness between the Sensor and the Power
Supply (each end terminated) are the same at each end and are:
Connectors, qty 2, P/N D38999/26WC35SN (Max-Viz p/n 501500001) with
Back shells, qty 2, P/N M85049/1913W04 (Max-Viz p/n 501000017) or Glenair
380HS001M1310H3 (Max-Viz p/n 501000034) or equivalent.
The connector required to fabricate a harness from a terminated end at the Power
Supply to the aircraft is:
Connector, qty 1, P/N N D38999/26WB35SN (Max-Viz p/n 501500042) with
Back shells, qty 1, P/N M85049/1911W03 (Max-Viz p/n 501000016) or Glenair
380HS001M1104A3 (Max-Viz p/n 501000035) or equivalent.
If either of the harnesses will run through a bulkhead, ensure that the connectors have
the appropriate number of pins (i.e. 22 or 13) and no wires are spliced together.
3.1.4. Interconnection Losses
The maximum video coaxial cable loss from the Power Supply to the display should not
exceed 1dB. (Note: this is a generic figure to cover all AES types and equipment
configurations. If this cannot easily be achieved in any particular installation, then Max-
Viz, Inc. should be contacted to determine whether a more relaxed insertion loss can be
considered without decreasing system performance or raising certification issues).
There should be no cable loss limitations for RG-179 if less than 100 feet.
If multiple displays are to be connected, the video signal from the Max-Viz 1500 should
go directly to a multiple output amplified video buffer with as short of a run as feasible
prior to going to the displays in order to avoid signal termination losses
It is highly recommended to avoid routing the video coax in close proximity to electrical
noise sources such as motors, generators, transmitters, etc. Do not lace the video coax
cable together (in parallel) with high current conductors, particularly AC power type
wires such as 115 Vac 400 Hz or 60Hz.
3.1.5. Electrical Bonding Recommendation
If the Sensor or Power Supply units are not bonded electrically via their mounting holes
directly to a metal aircraft structure, then electrically bond them to the metal aircraft
structure with a heavy bonding wire (or grounding braid) from an unused mounting
hole.

Astronics Max-Viz Max-Viz 1500 3091-00019 Rev M
3.2. Recommended Installation Procedure
Do not connect the 28 Vdc power connector to the Power Supply.
Switch “ON” the circuit breaker and the “ON/OFF” switch to the Max-Viz 1500 system.
Verify and measure the +28 VDC between pins 1 and 2 and pins 3 and 4 of the Power
Supply connector. Ensure voltage within +/- 2 VDC from normal. Switch “OFF” the
circuit breaker and the “ON/OFF” switch to the Max-Viz 1500 system.
Connect the RS 170 coax video cable to the display. Connect the Power Supply
connector. Switch the input power circuit breaker and “ON/OFF” switch to “ON”.
Observe the “OK” message on the display.
After the “OK” message on the display is extinguished, observe that the infrared video
image appears on the display with no distracting RFI noise pick-up.
At four-minute intervals the system will perform a self calibration (non-uniformity
correction - NUC) and the video will momentarily go blank. This is normal. If an
appropriate switch is installed, the NUC function can be manually controlled.
3.3. Installation Assistance
If you require installation assistance, and it is a certified installation, contact the type
design holder. If it is a new or non-certified installation, contact Max-Viz, Inc.
4. OPERATION
Operationally, the Max-Viz 1500 is used as a supplemental display to enhance the view
of the outside world. It uses an infrared (IR) sensor to provide an additional visual
perspective. The Max-Viz 1500 is particularly effective at night, in smoke, haze, and in
smog. It is also effective in some conditions of rain, snow, and fog.
EVS improves the pilot’s ability to see:
ground vehicles and other ground-based equipment/obstacles
aircraft on taxi-ways and runways
other traffic during takeoff, approach, and landing
the runway and terrain features during climb, descent, and low altitude
maneuvering
The EVS system is also valuable as an aid in ground navigation, and can be used, at the
pilot’s option, throughout the full mission profile. EVS use is straightforward and does
not increase the pilot’s workload. The system is normally turned on by use of the
“ON/OFF” switch located in the cockpit or by the “ON/OFF” switch on the display.

Astronics Max-Viz Max-Viz 1500 3091-00019 Rev M
Upon power-up the Sensor requires approximately 20 seconds to produce a useable
image. During this time period a video test pattern is displayed for approximately 5
seconds followed by the message “OK”. After approximately 20 seconds the display will
blank momentarily for a NUC cycle and a useable image then appears. The image
generated is a monochrome (i.e., black and white) image. The hotter an object is the
whiter it appears on the display. This is known as “white hot” polarity.
The display should be adjusted for optimum brightness and contrast, and readjusted
only during relatively benign phases of flight or periods of low workload. The image
then should be cross checked in a manner similar to other cockpit displays, using short
dwell times and appropriate cockpit priorities.
To optimize the IR image the EVS system periodically recalibrates itself. The
recalibration process is known as “Non-Uniformity Correction” (NUC). NUC can be
observed on the display as a momentary image interruption with “CAL” displayed. The
shutter closes for approximately one second during the NUC process, which happens
every four minutes or when manually activated, if an appropriate switch is installed in
the cockpit.
5. MAINTENANCE
Both the Sensor and Power Supply may be viewed as sealed “black boxes” where no
field maintenance, repair, or upgrade is performed. All such activities are conducted at
Max-Viz, Inc.
To ensure your system will be covered under warranty, fill out and submit the Max-Viz
Warranty Registration form located at the end of this manual, at the time of system
installation.
If you have difficulties operating the system, first contact your authorized Max-Viz
dealer for technical support. They will contact the type certificate holder, if it is a
certified installation. The type certificate holder will contact Max-Viz as necessary. If it is
not a certified installation, the dealer will contact Max-Viz.
If it is determined the Max-Viz 1500 must be returned for service or maintenance, Max-
Viz will issue a Return Material Authorization (RMA). Fill out Max-Viz Customer
Service Request Form located at the end of this manual and submit it to receive a RMA.
After receipt of the RMA, return the system to the address in Section 7.
A copy of the Customer Service Request Form (RMA) and Warranty Registration Form
are included at the end of this manual, but are also available at www.max-viz.com.

Astronics Max-Viz Max-Viz 1500 3091-00019 Rev M
6. WARNINGS, CAUTIONS, AND GUIDANCE
6.1. Electromagnetic Interference
The Max-Viz 1500 system is qualified (RTCA/DO-160) to operate in normal aircraft EMI
environments.
When installing the system, be sure that the Sensor window is
not installed in close proximity to high power EMI transmitters, such as
transponders.
High energy transmitters mounted directly in front of the germanium
lens may cause video disturbance.
Particular attention must be taken in routing the RS-170 video coax cable through the
aircraft structure to avoid potential RFI from noise items. It is highly recommended to
avoid routing the video coax in close proximity to electrical noise sources such as
motors, generators, transmitters, etc. Do not lace the video coax cable together (in
parallel) with high current conductors, particularly AC power type wires such as 115 Vac
400 Hz or 60Hz.
6.2. Germanium Window Breakage
The Sensor window is made of Germanium. If this window is ever broken, use extreme
caution when handling broken germanium shards or dust.
Always use gloves and
masks when handling broken germanium window material.
6.3. Germanium Window Cleaning
In contrast to visible light energy, infrared energy typically passes through dirt or bug-
debris build-up on the window. As such, the Sensor window requires only occasional
cleaning with mild liquid soap and water or isopropyl alcohol, and a soft cloth.
Do not use abrasive cleansers or cleaning pads on the germanium window.
Abrasive cleaning can damage the window coating. The use of products such as
Corrosion X can damage the RTV seals and coating on the germanium window.
Do not
use any cleansers with ammonia. Ammonia will remove the window coating.
6.4. Halo Images
Under certain circumstances, it is possible a “halo” will be seen around the image. The
following sequence of events will occur:
The Sensor has automatically temperature controlled heaters. When the heaters
first turn on, they will begin to heat the window from the outside-in.
As the window is heated, the infrared detector will not be able to compensate for
the signal coming from the window, as compared to the outside view, and thus a
white (hot) area will appear around the outside of the image, working its way in.

Astronics Max-Viz Max-Viz 1500 3091-00019 Rev M
The image will re-stabilize after a Non-Uniformity Correction cycle (NUC), described
in Section 4. Operation and Section 6.8 below.
This process will continue, with the halo encompassing more and more of the image
between NUC cycles until the window reaches a constant temperature across the
surface.
After approximately 20 minutes (depending upon the temperature of the camera
when the heater was turned on and the ambient operating temperature), there will
be a NUC cycle that creates a clean image and the halo will no longer form.
To best prevent a halo from occuring during flight, turn the system on during
preflight or run-up to stabilize the window and body heaters prior to flight and allow
thermal stabilization.
6.5. Ice Effects and Body Heaters
During in-flight use, the Sensor uses heaters to keep ice from building up over the
window. If the heaters fail and ice builds up, infrared energy will be unable to pass
through the ice, and the image will begin to fade. (In this situation, ice build up may
first occur around the outside of the image, and eventually close up as a circle of ice
closes in over the circular lens).
If the heaters fail, EVS use should be discontinued and the Sensor should be returned
to the factory for service. (If the Sensor is iced over on a cold winter morning before
start-up, it may take a few minutes before the ice melts off and an image appears).
Please use caution when handling the Sensor during cold weather operation.
Note: the Sensor could be warm to the touch (25 degrees Celsius).
6.6. Image Quality and Interpretation
Independent of the operation of the Sensor, image quality is a function of target size,
target temperature, background temperature, and atmospheric attenuation from
particles or moisture in the air.
As such, it is important to know that the quality
of the image will appear different as these variables change.
If the video
image appears clear in the cool morning and a little “washed out” on a hot/humid
summer afternoon, the difference is probably caused by changes in the infrared
environment, and not from changes in the operation of the system.
6.7. Nitrogen Added to Sensor
The Sensor is sealed at the factory and filled with nitrogen to eliminate moisture. If the
Sensor is opened, the nitrogen will be lost.
Do not open the Sensor during system
installation or maintenance, warranty is void if opened.

Astronics Max-Viz Max-Viz 1500 3091-00019 Rev M
6.8. Non-Uniformity Correction (NUC)
The Sensor hosts a 320 x 240 pixel sensor array. At four-minute intervals the system
automatically performs a Non-Uniformity Correction (NUC), where an internal shutter
assembly closes, to give the array a standard temperature target for array correction
and re-calibration.
During the NUC cycle, the video image is interrupted for
approximately one second.
6.9. Video Signal Interruption/ Improper Display Settings
If the video signal is ever completely interrupted, the display may appear as a solid field
(e.g., gray, white, or blue, etc.) and the message “no video” may appear, depending on
the display, to indicate a video failure. In this case the video coax may have an open
circuit or the Sensor may have a failure.
Please also note; if the brightness and contrast settings on the video display are not set
properly, the image will be degraded, or possibly even displayed as solid black or solid
white.
Following initial power-up of the system, always adjust brightness and
contrast settings to obtain the best image.
7. MAX-VIZ, INC. CONTACT INFORMATION
Astronics Max-Viz
11241 SE Highway 212
Clackamas, OR 97015 USA
Office:(503) 968-3036
Email: [email protected]
Website: www.max-viz.com

Astronics Max-Viz Max-Viz 1500 3091-00019 Rev M
APPENDIX A
A-1 “Interface Drawing –EVS –1500”: 952500015 Rev. 3
A-2 “Cable Assy –EVS - 1500 Sensor Interconnect”: 955000016 Rev. 1

Astronics Max-Viz Max-Viz 1500 3091-00019 Rev M

Astronics Max-Viz Max-Viz 1500 3091-00019 Rev M

Astronics Max-Viz Max-Viz 1500 3091-00019 Rev M

Astronics Max-Viz Max-Viz 1500 3091-00019 Rev M
Table of contents
Popular Machine Vision System manuals by other brands
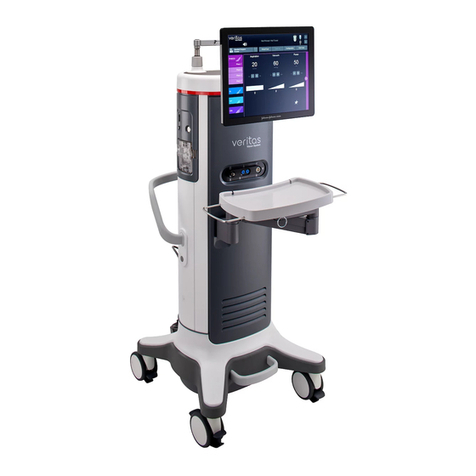
Johnson & Johnson Surgical Vision
Johnson & Johnson Surgical Vision Veritas Operator's manual
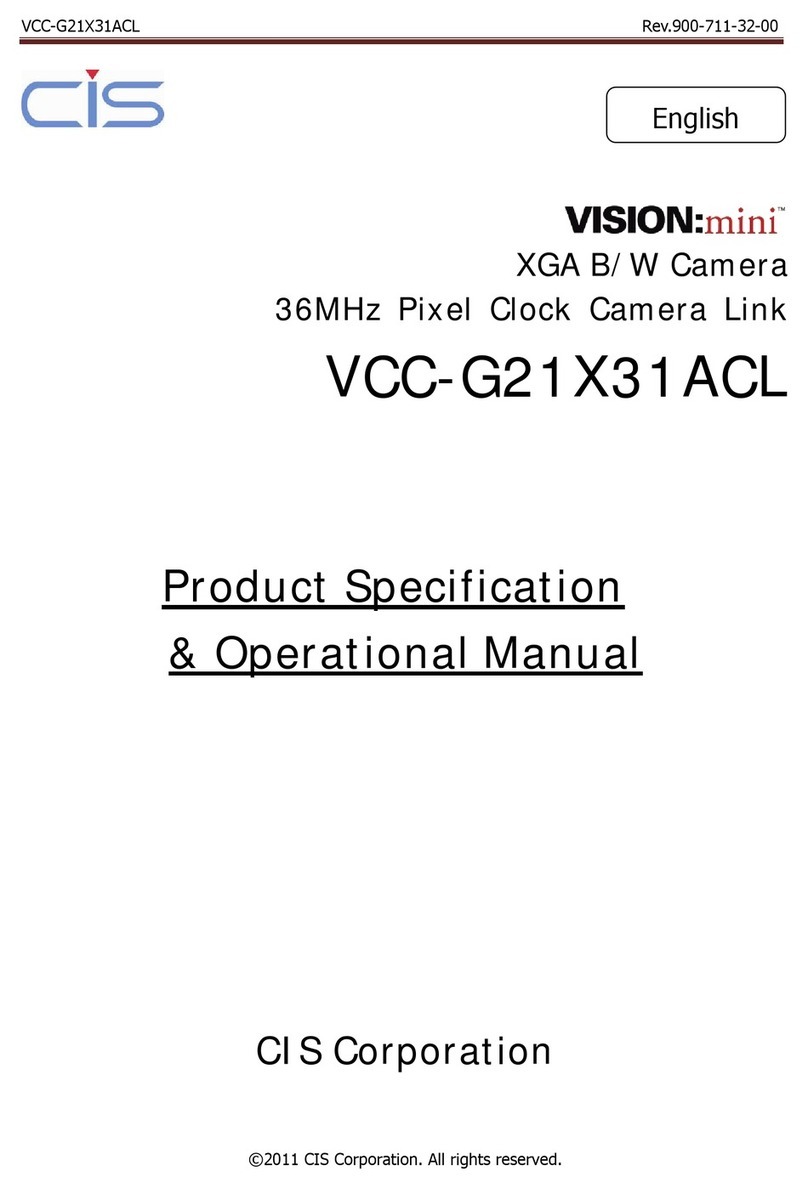
CIS
CIS VISION:mini VCC-G21X31ACL Product specification & operational manual
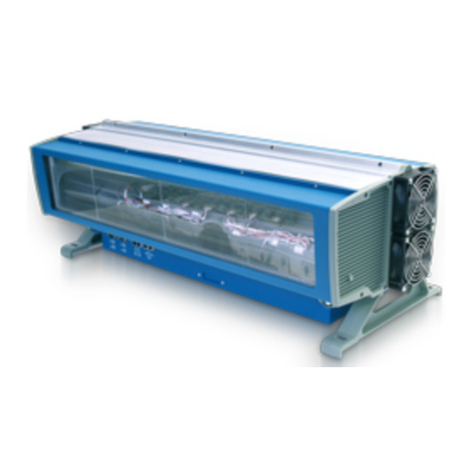
Datalogic
Datalogic Accu-Sort AccuVision AV6010 System manual
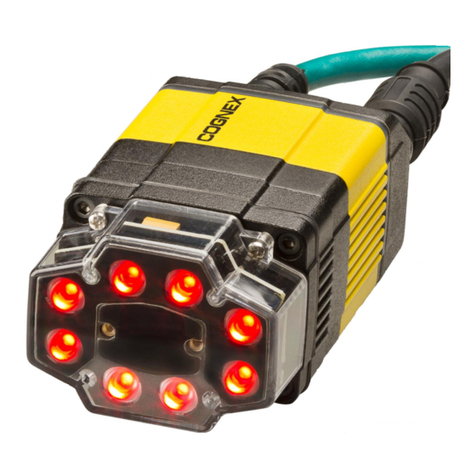
Cognex
Cognex DataMan 360 Series Quick reference guide
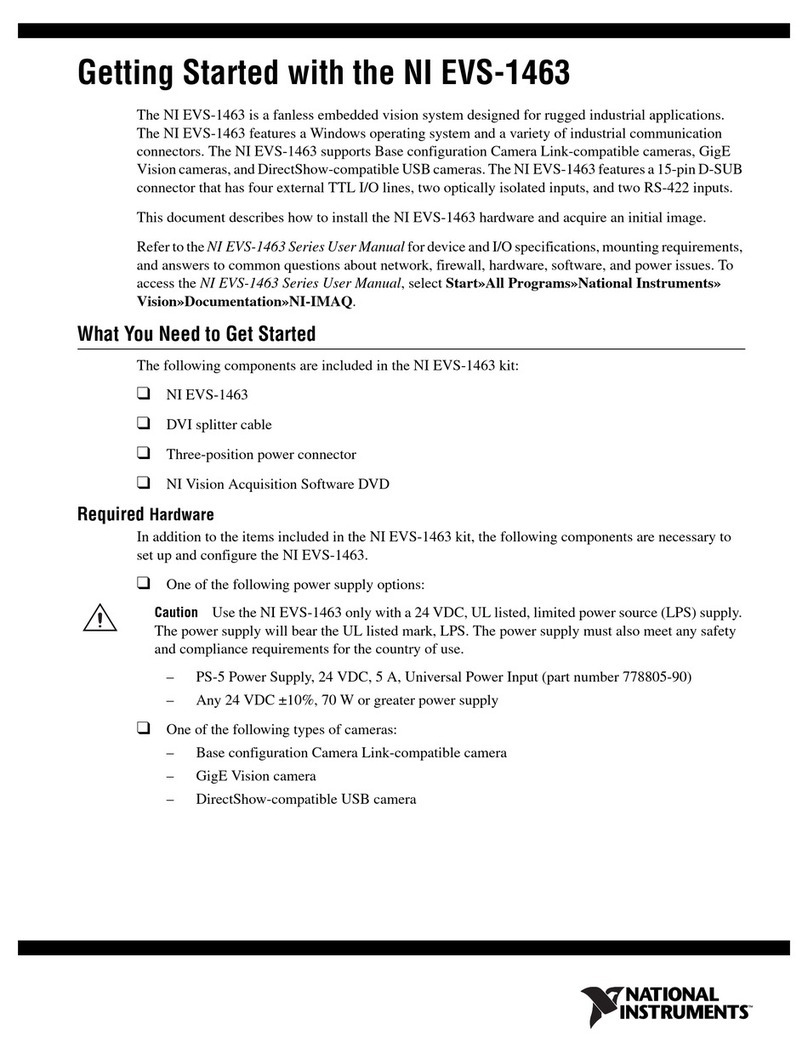
National Instruments
National Instruments NI EVS-1463 Getting started

Omron
Omron FLV-FB Series instruction sheet