Atex CONEX User manual

User manual
CONEX CONTROL UNIT
2023

1. INTRODUCTION - GENERAL..........................................................................................................3
2. BASIC TECHNICAL DATA................................................................................................................3
2.1. GENERAL.......................................................................................................................................3
2.2. POWER SUPPLY..........................................................................................................................3
2.3. DETECTION LINE CABLES.........................................................................................................4
2.4. ACTIVATION LINE CABLES........................................................................................................4
2.5. OUTPUT RELAY AND INPUT SIGNAL CABLES.......................................................................5
2.6. GROUNDING OF CONTROL UNIT.............................................................................................5
2.7. INPUT SIGNALS...........................................................................................................................5
2.8. SUMMARY TABLE OF TECHNICAL DATA................................................................................6
2.9. SYNCHRONOUS WIRING DIAGRAMS OF AN ELECTRICAL SWITCHBOARD (ONLY
ORIENTATIVE)...........................................................................................................................................6
3. Output Relays ....................................................................................................................................7
3.1. “ALARM” SIGNAL......................................................................................................................................7
3.2. “FAULT” SIGNAL...........................................................................................................................7
3.3. “SERVICE” SIGNAL......................................................................................................................8
3.4. “OFF” SIGNAL...............................................................................................................................8
3.5. “RUN” SIGNAL...............................................................................................................................8
3.6. “PREALARM” SIGNAL..................................................................................................................8
3.7. SIGNALS „BATTERY AND POWER“....................................................................................................9
4. INSTALLATION AND DISASSEMBLY.............................................................................................9
5. MAINTENANCE................................................................................................................................10
6. SERVICE..........................................................................................................................................10
7. OPERATION.....................................................................................................................................10
7.1. OPERATIONAL MODE...............................................................................................................11
7.2. SERVICE MODE.........................................................................................................................11
7.3. SAFE START MODE...................................................................................................................12
7.4. ALARM AND PREALARM SIGNALIZATION.............................................................................13
7.5. FAULT SIGNALIZATION.............................................................................................................14
7.6. THE “ZONE CARD” SCREEN....................................................................................................15
7.7. OTHER TYPES OF FAULTS......................................................................................................16
7.8. SERVICE INTERVAL..................................................................................................................18
7.9. CONTROL ELEMENTS ON THE DISPLAY (BUTTONS).........................................................19
7.10. FUNCTIONS COUPLED WITH THE UNIVERSAL DISPLAY BUTTONS...........................19
7.11. THE INTERNAL CONTROL UNIT MENU.............................................................................20
7.12. SWITCHING OFF THE CONTROL UNIT WHILE RUNNING ON THE INTERNAL
ACCUMULATOR.......................................................................................................................................21
8. FORBIDDEN ACTIVITIES...............................................................................................................21

This documentation functions as a Customer Manual that concerns the CONEX Control Unit. Itcontains
basic technical data, operation description for a customer, installation, maintenance and service
instructions. It also contains prohibited functions and activities that may never be performed by
operators. The documentation is handed over to a customer together with the control unit, and serves
as instruction documentation while the system is handed over to the customer.
The documentation can also be handed over to a customer before delivery of the control unit, the
customer can get familiar with its functions, space requirements, installation manner, input and output
signals from the control unit to a superior control system, signalization, etc. in advance.
The CONEX Control Unit is an electronic system delivered by the RSBP spol. s r.o. company (further
only RSBP), and it is an integral part of technological systems, offered by this company as well that
function as a protection against explosion or fire (HRD systems, paint booth fire protection systems
and so on).
The CONEX Control Unit is made as a compact (two-zone) version, or in four, six, and eight-zone
versions. A zone is always one technological unit or section that the control unit is able to monitor and
protect against explosion or fire.
All produced control unit versions have a common basis that is derived from the two-zone version.
Multiple zone control units differ from the two-zone one in details only (more protected zones, more
output relays, bigger battery, more control elements for zones, larger sizes), and are practically only its
multiplications. All differences of individual versions are specified in this documentation with their
appropriate explanations.
The control unit can be supplied by AC power from 100 to 240V with the frequency of 50 to 60Hz (the
internal power supply will thus automatically cover power systems used in Europe and on the American
continent). The power supply cable must be protected at the source by one-pole circuit breaker In = 10A
with B or C characteristic. A three-lead cable with a minimum diameter 3 x 1.5mm2is suggested for the
control unit electrical supply. The condition is that one of the three leads was will have green-yellow color
(“PE” potential –protective lead), and the second of the three leads will have light blue color (“N” potential
–middle lead). The third lead may not have colors of the remaining two, and can be black, brown or gray
(“L” potential – phase lead). The supply cable does not have to be shielded. Any commonly used cable
types can be used (for example CYKY 3Cx1.5, CMSM 3Cx1.5, Ölflex 3G1.5 or their equivalents).

It is recommended to install a protective ferrite (type FEC 9.0) on the power supply cable to protect
against electromagnetic interference (EMC). This ferrite is installed as close as possible to the inlet of
the power cable to the control panel.
A third grade overvoltage protection (class D) in combination with a HF filter against electromagnetic
noise effects (EMC) is installed in the control unit. A customer should have the power supply equipped
by first (class B) and second grade (class C) overvoltage protection.
The power supply at the customer must meet the emergency power supply conditions (back-up by UPS,
two independent supplies, etc.) or in case of power failure the power must be resupplied within 4 hours.
At the same time the control unit power supply must be designed so it cannot be switched off by this
control unit directly or indirectly (through contacts of its output relays).
Possible failure of the power supply is handled by an internal back -up accumulator (two batteries) with
the minimum back-up time of 4 hours of operation. The most unfavorable case has been considered;
the back-up time can be longer in individual cases, depending on the configuration of connected
appliances. In case of power failure that is longer than 4 hours the back-up accumulator can be run
down, in this case the control unit will switch itself off, and proper function of the control unit and the
system is not guaranteed.
2.3. DETECTION LINE CABLES
The cables from the control unit to detectors are affected by undesirable effects of electro-magnetic
disturbances (EMC) the most.
Therefore, for the connection of active detectors requiring power (Detex, Lumex, etc.), they are
designed exclusively by HELUKABEL, specifically the types PAAR-TRONIC-CY 2x2x0.75mm2for
detection lines with the length up to 150m (the detection line length is the distance between a control
unit and the last detector on the detection line).
For the connection of non-demand passive detectors (manual call points, temperature detectors, etc.) ,
only HELUKABEL cables are designed exclusively for PA-TRONIC-CY 1x2x0.75 mm2 cables for
detecting lines up to 150 m (length of the detection line is the distance between the switchboard and the
last detector in the detection line). It is a special high-resistance cable against electromagnetic
interference (EMC). It is shielded with twisted pairs of veins.
It is recommended to install a protective ferrite (type FEC 9.0) on each cable for the detection line facing
the control panel to protect against electromagnetic interference (EMC). This ferrite is installed as close
as possible to the cable entry to the control unit.
2.4. ACTIVATION LINE CABLES
Cables from the control unit to the actuators (HRD bottles, electromagnetic valves, etc.) on the activation
line may be adversely affected by the electromagnetic interference (EMC) side effects.That's why
HELUKABEL PAAR-TRONIC-CY cables are designed for their connection. The cross section is given
by the length of the activation line (the length of the activation line is the distance between the control
panel and the last action element in the activation line). It is a special high-

resistance cable against electromagnetic interference (EMC). It is shielded with twisted twisted pairs of
veins.
•For the activation line length to 50m is used HELUKABEL PAAR-TRONIC-CY 1x2x0,75 mm2
•For the activation line length to 150m is used HELUKABEL PAAR-TRONIC-CY 1x2x0,75 mm2
It is recommended to install a protective ferrite (type FEC 9.0) on each cable for the activation line
facing the control panel to protect against electromagnetic interference (EMC). This ferrite is installed
as close as possible to the cable entry to the control unit.
2.5. OUTPUT RELAY AND INPUT SIGNAL CABLES
The cable for the output relay and input signals (the output relay and input signals are described
below) is a standard multiple lead copper cable or cables (shielding is not necessary, but cannot hurt),
profile depends on the length and power system, number of leads depend on the number of signals.
Possible questions can be discussed with RSBP.
The HELUKABEL PAAR-TRONIC-CY 1x2x1.5 mm2 cable is used for the connection of external
signaling (optical, acoustic or combined optical-acoustic signaling) for lines up to 150 m (line length is
the distance between the panel and the last element in this line).
The HELUKABEL PAAR-TRONIC-CY 1x2x0.75 mm2 cable is used to connect the input signals (input
signals are described below) for lines up to 150 m (line length is the distance between the panel and the
last element in this line).
It is recommended to install a protective ferrite (type FEC 9.0) on each of the above cable facing the
control panel to protect against electromagnetic interference (EMC). This ferrite is installed as close as
possible to the cable entry to the control unit.
2.6. GROUNDING OF CONTROL UNIT
The control unit is grounded with a yellow-green grounding conductor "PE" in the power supply cable
harness. The control unit is also equipped with a grounding terminal "PE", which is used for mounting
on the grounding system of an object or technology at the location of the switchboard. All metal parts
of the control panel (mounting plate, front panel, steel panel, cabinet door) are connected to the earthing
terminal "PE". The yellow-green single-core CYA 6mm2 wire or equivalent is used to support the
switchboard.
2.7. INPUT SIGNALS
The control unit is equipped by clamps, to which input signals can be brought (when the clamps are
clamped together for example by a relay contact, the signal is active). In practice these signals can be
used to signal low amount of extinguishing agent, decrease in extinguishing agent pressure, remote
setting of the appropriate zone or other defined zones to the service mode, possibly for other functions.
We recommend consulting of these input signals with RSBP.

Ferrite
Ferrite
Ferrite
Ferrite
Ferrite
Ferrite
PAAR
PAAR
PAAR
PAAR
PAAR
CYA 6
2.8. SUMMARY TABLE OF TECHNICAL DATA
Source voltage 100 to 240Vac
Frequency of source voltage 50 to 60Hz
Power supply circuit breaker In = 10A (B or C characteristic)
Supply cable 3C x 1.5mm2(maximum 3C x 1.5mm2)
Power consumption 100mA to 2,5A (according to load, mode, etc.)
Protection IP65
Reaction time (response time) - maximum 3ms
Reaction time (response time) - SW adjustable 1 to 240s
Working temperature of surroundings -10 to 50°C (limited by accumulator)
Relay outputs (one contact NO/NC per relay) 250Vac or 30Vdc/10A
Number of relays –two-zone version 6 units
Number of relays –four-zone version 12 units
Number of relays –six-zone version 18 units
Number of relays –eight-zone version 24 units
Bus CAN (250 kbps)
Recording of events to internal memory (1024 events)
Signalization Color LED diodes on front panel
Visualization LCD display (160 x 128 pixels)
Control Buttons and controllers on the front panel
Parameter settings Through specialized software
Dimensions - two-zone version (H x W x D) 316 x 355 x 167mm
Dimensions - multiple-zone version (H x W x D) 600 x 700 x 240mm
Detection
line
Activation
line Input
signal
External
signaling
Output
relay Main
power supply
110-230 V ac
Grounding

The control unit is equipped by programmable output relays for communication with a customer superior
control system. Given signals can be used for optical or acoustic signalization of control unit function
states to a control center, for a fire department, switching off or blocking of a follow-up technology, etc.
Relay functions are not firmly set; they are assigned by programming using specialized software. The
relays are potential-less, with NC/NO switching contacts. Thus they allow passing on signals on the
levels Log 0 or Log 1, which is often advantageous for safety circuits. Protection of the contact
common pole is by a cylinder fuse 3.15A (normal characteristic). Relay contact loading is 30Vdc/10A.
The control unit in the two-zone version contains 6 output relays, four-zone version 12 output relays, the
CONEX control unit in six-zone version contains 18 output relays, and the control unit in eight-zone
version contains 24 output relays.
Each relay can be programmed using specialized software to simple functions like ALARM, FAULT,
SERVICE, OFF, RUN, PREALARM, BATTERY and POWER. Additionally, it is possible to create
combinations of these functions, time relationships, etc. –of course this will require a consultation or
technical help from RSBP.
Remark: In most applications only summary signals “ALARM” and “FAULT” are used, in some also the
signal “ALARM” and “FAULT”, in some addtional signal “SERVICE”, Sometimes division of these signals
according to individual zones is required.
3.1. “ALARM” SIGNAL
The “ALARM” signal is activated at the moment when the control unit reacts to fire or explosion, and
sends an impulse to its action element to suppress or eliminate it (the relay delay is about 10ms
against the signal on the activation line, which is practically negligible for real applications).
The “ALARM” signal can be set dependently and summarily for more zones at the same time or
independently and separately for each zone.
3.2. “FAULT” SIGNAL
The “FAULT” signal is activated at the moment of any defined defect or combination of these defects.
These defects include for example detection circuit defects (short circuit, circuit interruption, parameters
out of set range), activation circuit defects (short circuit, circuit interruption, parameters outof set range),
etc.
The “FAULT” signal can be set dependently and summarily for more zones at the same time or
independently and separately for each zone.
Remark: The exact specification of a fault or combination of faults can be found only on the control
unit display.

3.3. “SERVICE” SIGNAL
The “SERVICE” signal is activated at the moment of putting a control unit zone or zones to the service
mode. The placing into the service mode can be performed by a turn switch with the key of the
appropriate zone placed on the control unit cover, control buttons and display located on the control unit
cover, or using specialized software. Operators should place zones into the service mode exclusively
by the turn switch with the key.
The “SERVICE” signal can be set dependently and summarily for more zones at the same time or
independently and separately for each zone.
3.4. “OFF” SIGNAL
The “OFF” signal includes the sum of the “ALARM”, “SERVICE”, and “FAULT” signals. Thus it is active
in cases when a zone or zones of the control unit are not able to perform their activities correctly by
having a defect, being in the service mode, or if there was an alarm already with an appropriate reaction
(suppression or prevention of explosion or fire).
The “OFF” signal can be set dependently and summarily for more zones at the same time or
independently and separately for each zone.
Remark: Negation of the "OFF“ signal tells us that a zone or zones (depending on the setting of software)
are ready for reaction (suppression or prevention of explosion or fire) –in other word on the "ON“ mode.
3.5. “RUN” SIGNAL
The “RUN” signal is activated at the moment of placing a zone or zones to the “Active” status, or it means
the state when no defect was found by the control unit at the appropriate detection line. Placement into
the “Active” or “Deactivated” status is done using specialized software. Under normal operation a zone
or zones are set to the “Active” mode. Then the above mentioned signal does not have practically any
meaning for a customer or his superior system (a customer cannot influence this setting during normal
operation).
The “RUN” signal can be set dependently and summarily for more zones at the same time or
independently and separately for each zone.
3.6. “PREALARM” SIGNAL
The “PREALARM” signal is activated at the moment of so called prealarm. This is the state when
there are detection lines set on two zones of the control unit (for safety reasons) in a specialrelationship
“2 of 2”, or when an alarm signal on a detection line lasts more than a preset time interval. In order to
achieve reaction to a fire or explosion and sending of an impulse to the activation line to suppress or
prevent these events, we need both detection lines to react in the first case or the alarm signal on a
detection line that lasted the required time interval in the second case.

If there is detection on one detection line only in the first case or of the reading of time goes on until
the end of the required time interval in the second case than this state is called prealarm –on the control
unit the signal “PREALARM” is indicated and activated. At this moment the control unit does not send
an impulse to the activation line to suppress or prevent fire or explosion. Only during concurrent detection
on the second detection line in the first case or after elapsing of the set time interval of alarm signalization
on a detection line in the second case the control unit goes to the “ALARM” mode, and sends an impulse
to the activation line to suppress or prevent fire or explosion.
3.7. SIGNALS „BATTERY AND POWER“
The "BATTERY" signal is activated at the time of battery failure. This can be due to a drop in internal
battery voltage below 18.5 V, damage to the internal wiring between internal batteries and PCB, or a
failure in the circuitry of the battery on the circuit board. The control panel is only active on the mains
power supply when this signal is activated. When activating this signal, the customer should contact
the RSBP or its authorized representative.
The "POWER" signal is activated at the time of a power failure from the power supply. This can be due
to a power supply failure, a power supply circuit breaker or a damaged circuit breaker, a damaged supply
cable, or a fault on the internal power circuits of the control panel. The control panel is only running on
the internal battery when this signal is activated. When activating this signal, the customer can try to
eliminate the causes of a power failure (power supply, circuit breaker, cable). If the signal is still active
then the customer should contact RSBP or its authorized representative.
The control unit in the compact version (two-zone) is supplied as a plastic box with IP65 protection
and transparent hinged front cover. An aluminum panel with a display and other control and signalization
elements (display buttons, turn controllers and LED diodes) is located under the front cover. There is an
independently removable cover of the terminal section at the bottom of the plastic box. Screws of the
terminal section cover are provided with a seal, and a customer cannot access this section. The plastic
box dimensions are: 316 x 355 x 167mm (H x W x D), it is installed using three attachment bolts or
screws to a wall, construction, girders, etc. A space and knock-out spaces for cables and installation of
grommets are situated under the control unit; the cables can also be brought out through knock-out
holes in the back wall of the control unit.
Control units in four, six and eight zone versions are supplied in a steel wall distribution box with IP65
protection with a transparent hinged front cover installed on the door. An aluminum panel with adisplay
and other control and signalization elements (display buttons, turn controllers and LED diodes) is located
under the front cover in a door cutout. Distribution box door bolts are provided with a seal, and a customer
cannot access this section. The distribution box dimensions are: 600 x 700 x 240mm (H x W x D), it is
installed using four attachment bolts or screws to a wall, construction, girders, etc. A space to bring out
cables and install grommets is situated under the control unit.
Control units in four, six and eight-zone versions can also be supplied in custom design, for example
installed into a distribution box with a display and other control and signalization elements (display
buttons, turn controllers and LED diodes) located in its door. In these cases technical parameters and
installation methods depend on each specific version.

The following principles are valid for installation of all control unit types:
•A control unit must be installed in the height approx. 170cm –upper edge (for easy operation)
•An access space with the minimum length of 80 cm must be left in front of the control unit.
•The access space may not be filled either permanently or temporarily
•The control unit installation space must be equipped by lighting
•Harmful effects (vibrations, smoke, dust and gases) may not occur in the control unit
installation space
•The temperature in the control unit installation space must be in the range -10°C to 50°C
•There must be a functioning electrical socket 230V/50Hz near the control unit to connect
installation tools, PC, etc.
The control unit does not pollute environment during its proper function, and does not emit harmful
substances or electromagnetic radiation higher than accepted limits. It is harmless from the ecological
point of view.
Disassembly and liquidation of control units is performed exclusively by RSBP or its authorized
representative. During this they proceed according to the laws concerning electric waste; the internal
accumulator (that is installed in the control unit) is ecologically liquidated, other parts are ecologically
liquidated as well or recycled.
The control unit maintenance that is performed by a customer lies only in visual control for cleanliness,
mechanical damage and integrity of the control unit and cables. In case of any damage or breach of
integrity of the control unit and cables RSBP or its authorized representative must be contacted.
Customers or other entities cannot perform any other maintenance than specified above.
Complete control unit service is performed by RSBP or its authorized representative in regular half
year intervals. Customers or any other entities cannot perform any control unit service.
The control unit that is connected to a complete system for suppression or prevention of fire or explosion
can work automatically and without human intervention. Operators cannot and are not authorized to
change control unit parameters set by RSBP or its authorized representative.
Operators can place appropriate zones or the whole control unit to the service mode and back to the
operational mode, monitor control unit function states, control unit fault states, display control unit
records, service intervals, actually measured values, etc. All these operational regimes and operator
procedures are specified below.

A graphical LCD display, LED diodes, user buttons on the display and turn switches with keys are
used for communication of operators with the control unit. All these components are located on the
aluminum panel under the hinged front control unit cover. Operators can open the front cover and
operate the appropriate components as needed. LCD display and LED diodes are visible and readable
through the closed front cover.
All operator interventions to the control unit should be demonstrably recorded to the technological
system Book of Operations, including dates, names, and operator signatures.
Operators must be demonstrably instructed in the control unit operation by RSBP or its authorized
representative. Uninstructed personnel are expressly forbidden to operate the control unit.
7.1. OPERATIONAL MODE
A customer accepts the control unit from the contractor in operational mode –a zone or appropriate
zones are set to the operational mode and tested for correct operation, checked that there is no
defect, and the system controlled by the control unit is ready for suppression or prevention of fire or
explosion. No operator intervention is needed, the system works automatically.
In case of OPERATIONAL MODE the control unit display looks as follows:
Actual date, time, manufacturer’s logo and icon are indicated
symbolizing the status “Control unit is in the operational mode”.
A green LED diode marked with is on in the left upper corner.
7.2. SERVICE MODE
A customer can place any zone (also individually) to the service mode –the appropriate zone thus
indicates a possible occurrence of fire or explosion, but in no case there is reaction of the system and
suppression or prevention of the event. This can be utilized during long-term shut-down of theprotected
technology, cleaning of the protected technology, etc.
During the service mode a given zone is not protected against explosion or fire. However, other zones
that are in the operational regime are able to react properly and in the event of fire or explosion to
suppress or prevent it.
Placement of a zone to the service mode is done by switching the turn switch of the appropriate
zone over from the position ON to the position OFF. To perform this manipulation a key needs
to be inserted into the switch, which is a safety feature (unauthorized personnel cannot
perform the manipulation). Placement of the zone back tothe operational mode is done by
switching the turn switch of the appropriate zone over from the position OFF to the position
ON.

In case of SERVICE MODE the control unit display looks as follows:
Actual date, time, manufacturer’s logo and icons and are
indicated symbolizing the status “At least one control unit zone is in
the service mode”.
A green LED diode marked is on in the left upper corner.
A yellow LED diode marked is on in the left upper corner.
During operations a situation can occur, when in the zone that is in the service mode an alarm is
indicated –there is no reaction of the control unit to the alarm (for example if an infrared detector of
the switched-off zone is exposed to day or other light during cleaning).
In this case the control unit display looks as follows:
Actual date, time, and icons icons and , are indicated symbolizing
the statuses “At least one control unit zone is in the service mode”, and
“Alarm signalization” –icon at the same time. The icon “Prealarm
signalization” may or may not be indicated.
The internal control unit horn does not sound any acoustic signal. The
blinking sign “ZONE 1” indicates the place the alarm comes from.
A green LED diode marked is on in the left upper corner.
A yellow LED diode marked is on in the left upper corner.
A red LED diode marked is on in the left bottom corner.
A red LED diode marked may or may not be on in the left bottom corner.
If this state occurs, operators must, before the zone that is in the service mode, and from where the
alarm is indicated, returns back to the operational mode, reset it by the button. If the control unit
display does not change after this reset, and the alarm signalization continues, the defect is more
serious, the control unit may not be placed into the operational regime, and RSBP or authorized
representative workers must be contacted.
7.3. SAFE START MODE
The control unit will set itself to the safety start mode automatically during switching of a zone from the
operational to the service mode or vice versa, after reset, and after the main power comes back on.
During this mode it tests its internal circuits and switching-on of the activation lines is blocked. All other

control unit features are fully functional. This regime last about 4 seconds and disappears
automatically. If it does not, RSBP or its authorized representative workers need to be contacted.
In case of SAFE START MODE the control unit display looks as follows:
Actual date, time, and icon and the sign “START” are indicated
symbolizing the status “Safe start mode”.
LED diodes in the upper and lower left corners of the display can be on
according to situation.
7.4. ALARM AND PREALARM SIGNALIZA TION
If a control unit zone is in the operational mode, and if there is signalization of explosion or fire on the
detection line of this protected zone, the control unit will evaluate this state and will consequently send
an impulse to the appropriate activation line –and the event is suppressed or prevented. This state is
called ALARM.
During reaction to the ALARM state in one zone other zones (if they are in the operational mode) are
still able to suppress or prevent explosion or fire if these events are indicated on the appropriate
zones.
The term “PREALARM” is explained above.
In case of PREALARM SIGNALIZATION the control unit display looks as follows:
Actual date, time, and the icons and , are indicated symbolizing
the status “Prealarm signalization”.
The blinking sign “ZONE 1” indicates the place the prealarm comes from.
A green LED diode marked is on in the left upper corner.
A red LED diode marked is on in the left bottom corner.
If this situation occurs, the control unit waits for the given time interval, whether the signalization of alarm
on the detection line lasts, or whether the alarm signalization occurs on the paired detection line (setting
“2 of 2”) as well. If it happens the control unit will automatically switch over to the “Alarm signalization”
mode and adequately reacts to the fire and explosion. If it does not occur the control unit switches back
over to the operational mode.

In case of ALARM SIGNALIZATION the control unit display looks as follows:
Actual date, time, and the icons and are indicated symbolizing the
status “Alarm signalization”. The “Prealarm signalization” state may or
may not be indicated –icon , if this state precedes the alarm
signalization.
The blinking sign “ZONE 1” indicates the place the alarm comes from.
The internal control unit horn sounds continuous acoustic signal.
A green LED diode marked is on in the left upper corner.
A red LED diode marked is on in the left bottom corner.
A red LED diode marked may or may not be on in the left bottom corner.
If this situation occurs the control unit will send an impulse to the appropriate activation line –and the
explosion or fire is suppressed or prevented. It is likely that the given activation line will get into the
fault state afterwards (in case of HRD system there will be an interruption of electrical circuit). Thus
the zone will not be protected against explosion of fire any longer, and operators will need to contact
RSBP or its authorized representative.
The internal control unit horn sounds continuous acoustic signal during alarm signalization. Operators
can switch this signal off by the button . A repeated push of this button will renew the acoustic signal;
another push switches it off, and so on.
Switching off the internal control unit horn is indicated by the icon on the display.
7.5. FAULT SIGNALIZATION
If there is any defect on detection or activation lines the control unit will evaluate this status as non-
standard (fault).
During indication of this fault type in one zone other zones (if they are in the operational mode) are still
able to suppress or prevent explosion or fire if these events are indicated on the appropriate zones.
In case of FAULT SIGNALIZATION the control unit display looks as follows:
Actual date, time, and the icons and , are indicated symbolizing
the status “Fault signalization”. Other icons may or may not be indicated.
The blinking sign “ZONE 1” indicates the place the fault comes from.
The internal control unit horn sounds interrupted acoustic signal.
A green LED diode marked is on in the left upper corner.

A yellow LED diode marked is on in the left upper corner.
Other LED diodes may or may not be on.
The internal control unit horn sounds interrupted acoustic signal during fault signalization. Operators can
switch this signal off by the button . A repeated push of this button will renew the acousticsignal; another
push switches it off, and so on.
Switching off the internal control unit horn is indicated by the icon on the display.
Operators can reset the fault by pressing the button if this type of fault is indicated. If, even after
this reset, the fault signalization lasts, the given zone is not protected against explosion of fire any longer,
and operators need to contact RSBP or its authorized representative.
Operators can get directly to the screen ZONE CARD (see below) by pressing the button , where
they can find the exact type of the fault.
7.6. THE “ZONE CARD” SCREEN
This screen indicates measured data (detection line supply voltage, detection line re sistance, and
activation line resistance) for each zone separately. Beyond this there are icons with fault types in
detection or activation lines, again for each zone individually.
This information can be important for example for a phone communication with RSBP or its authorized
representative, when a customer can localize the fault type more exactly.
The control unit ZONE CARD screen looks as follows:
0mA and 48mA –actual supply currents for detection lines 1 and 2
65535R and 4700 R –actual resistances of detection lines 1 and 2
860R and 4R –actual resistances of activation lines 1 and 2
- The appropriate control unit zone is in the operational mode
- Signalization of alarm or prealarm on the appropriate zone
- Signalization of a summary fault of the appropriate zone (for exact description see other icons)
- The fault “Supply voltage of the appropriate detection line is out of the set range”
- The fault “Ground connection of a detection line”
- The fault “Short on a detection line”
- The fault “Disconnection on a detection line”

- The fault “Ground connection or short of an activation line”
- The fault “Disconnection on an activation line”
Remark: For illustration the screen picture shows all icons, in reality all of them may not be indicated -
only the ones that describe a given situation.
7.7. OTHER TYPES OF FAULTS
The control unit can evaluate and indicate also other types of faults (not only detection and activation
line ones). Other types of faults may include electricity supply failure, battery failure, integrity failure, and
horn failure. These indications disappear automatically when the faults disappear.
After the power failure the control unit display looks as follows:
Actual date, time, and the icons , and are indicated
symbolizing the status “Power supply failure”.
The indicator shows the remaining internal accumulator capacity.
The internal control unit horn sounds interrupted acoustic signal.
A green LED diode marked is on in the left upper corner.
A yellow LED diode marked is on in the left upper corner. A
yellow LED diode marked is on in the left bottom corner.
If this situation occurs operators should be able to renew the control unit power supply. In case of power
failure that is longer than 4 hours the internal back-up accumulator can be exhausted, in this case the
control unit will switch itself off, and proper function of the control unit and the system is not guaranteed.
If operators are not able to secure the power supply within 4 hours, or if this fault is active even after the
power is back on, they have to switch the control unit off from running on the internal accumulator only,
in order not to run the accumulator down (this operation is described below), and contact RSBP or its
authorized representative. The system is not protected against explosion or fire when the control unit is
switched off.

During the internal accumulator failure the control unit display looks as follows:
Actual date, time, and the icons , a , are indicated symbolizing
the status “Internal accumulator failure”.
The internal control unit horn sounds interrupted acoustic signal.
A green LED diode marked is on in the left upper corner.
A yellow LED diode marked is on in the left upper corner.
A yellow LED diode marked is on in the left bottom corner.
If this situation occurs operators should contact RSBP or its authorized representative. The back-up
power supply is in fault, which can cause that the system is not or will be not protected against explosion
or fire.
During the integrity failure the control unit display looks as follows:
Actual date, time, and the icons and the Integrity sign are
indicated symbolizing the status “Integrity failure”.
The internal control unit horn sounds interrupted acoustic signal.
Then the address or a description of the faulty component is indicated (if
possible).
If this situation occurs operators should contact RSBP or its authorized representative. The control unit
is faulty (wrong configuration, missing component), which can cause that the system is not protected
against explosion or fire.
During the external horn circuit (signalization) defect the control unit display looks as follows:
Actual date, time, and the icons , , and the BUZZER sign are
indicated symbolizing the status “External horn circuit (signalization)
defect”.
The internal control unit horn sounds interrupted acoustic signal.
If this situation occurs operators should contact RSBP or its authorized representative. A defect of the
external horn (signalization) does not have any influence on the proper function of the system that reacts
to fire or explosion, but the external acoustic horn (and possibly the acoustic signalization) does not
work.

Remark: The external signalization (optical or acoustic) is not used in some applications.
The internal control unit horn sounds interrupted acoustic signal during signalization of these defects.
Operators can switch this signal off by the button . A repeated push of this button will renew the
acoustic signal; another push switches it off, and so on.
Switching off the internal control unit horn is indicated by the icon on the display.
Operators can get directly to the CONTROL CARD screen (see below) by pressing the button , where
they can find additional information to the given fault.
The control unit CONTROL CARD screen looks as follows:
24.0V –actual voltage transformed from the external power supply
25.3V –actual voltage supplied by the internal accumulator
124mA –the value of current consumed at a given moment from main
power supply
Other icons have the same meanings like in the ZONE CARD screen.
Remark: For illustration the screen picture shows all icons, in reality all of them may not be indicated -
only the ones that describe a given situation.
7.8. SERVICE INTERVAL
The control unit works with the real time and calendar, and the data about the last service and the future
planned one are stored in its internal memory. This information cannot be changed by operators;
however, it can be invoked and displayed any time on the screen (see below). When the date of the
planned service comes about, the screen shows notification information about this activity.
During the display of service interval the control unit screen looks as follows:
08/2009 –the date of the planned service
This is only an information screen; the control unit can work without any limitations (if it is in the
operational mode, and no other defect is reported), and theoretically even after the date of the future
planned service. However, operators should contact RSBP or its authorized representative with the
request to perform the regular service of the control unit and the system, since the control unit and the
whole system must be serviced in regular time intervals.

7.9. CONTROL ELEMENTS ON THE DISPLAY (BUTTONS)
Control elements (user display buttons) can be found on the aluminum panel under the hinged front
cover of the control unit. These buttons are used to control the control unit functions, and aredescribed
below.
The reset button –used for resetting of faults, alarms, etc.
The internal horn button –used to switch off (or back on) the control unit acoustic signal
The return button –used to return one level back in the display menu
The confirm button –used to confirm an operation
The move button –used to move around the menu
The universal buttons –used to control an actual operation that is displayed above the button on
the display
7.10. FUNCTIONS COUPLED WITH THE UNIVERSAL DISPLAY BUTTONS
The icons of actual operations that can be controlled by the universal buttons are located at the
bottom part of the control unit display (see above). They are described below.
The appearance of the display bottom section in the operational mode
The icon to enter the “Service mode”
The control unit can be placed in the service mode by pressing this button (however, this is only allowed
to the RSBP or authorized representative employees). This operation is forbidden to operators, since
the collision with the turn switch with key position could occur (the disagreement between the mode set
by pressing of the button and the mode set by the turn switch).
Operators can place zones to the service mode exclusively by switching the turn switch of the
appropriate zone over from the position ON to the position OFF. To perform this manipulation a key
needs to be inserted into the switch, which is a safety feature (unauthorized personnel cannot perform
the manipulation). Placement of the zone back to the operational mode is done exclusively by switching
the turn switch of the appropriate zone over from the position OFF to the position ON.
The icon to enter the regime “Recording of events”
The control unit is equipped by the internal processor with memory that enables automatic archiving of
all events that were recorded and evaluated by the control unit, including date and time when they
happened (faults, power failures, service modes, alarms, etc.). The memory capacity is 1024 events.
These records are used for backward analysis of events. Operators can display them in sequence;
however, they cannot change or delete them.

In the contacts regime the bottom section of the control unit display displays the auxiliary menu of
contacts that are related to service data (contacts to RSBP or its authorized representative –email,
phone, and web pages).
The icons of the auxiliary contact menu
The data about the last service and about the future planned service is shown
The contact for RSBP or its authorized representative (to perform service) is shown
The contact for RSBP or its authorized representative (to perform service) is shown
The icon to access the regime “Internal control unit menu”
7.11. THE INTERNAL CONTROL UNIT MENU
In this menu it is possible to manage control unit functions created by operators. A direct access to the
control card screen and the zone card screen are enabled, as well as switching off the control unit, while
it is operating on the internal accumulator (batteries), and also the immediate reset of the control unit.
The control unit Internal menu screen looks as follows:
This icon allows the direct access to the Control card screen
This icon allows the direct access to the Zone card screen
This icon allows the direct access to the Zone card screen
Table of contents
Popular Control Unit manuals by other brands

BENDIX
BENDIX TW-12 installation instructions
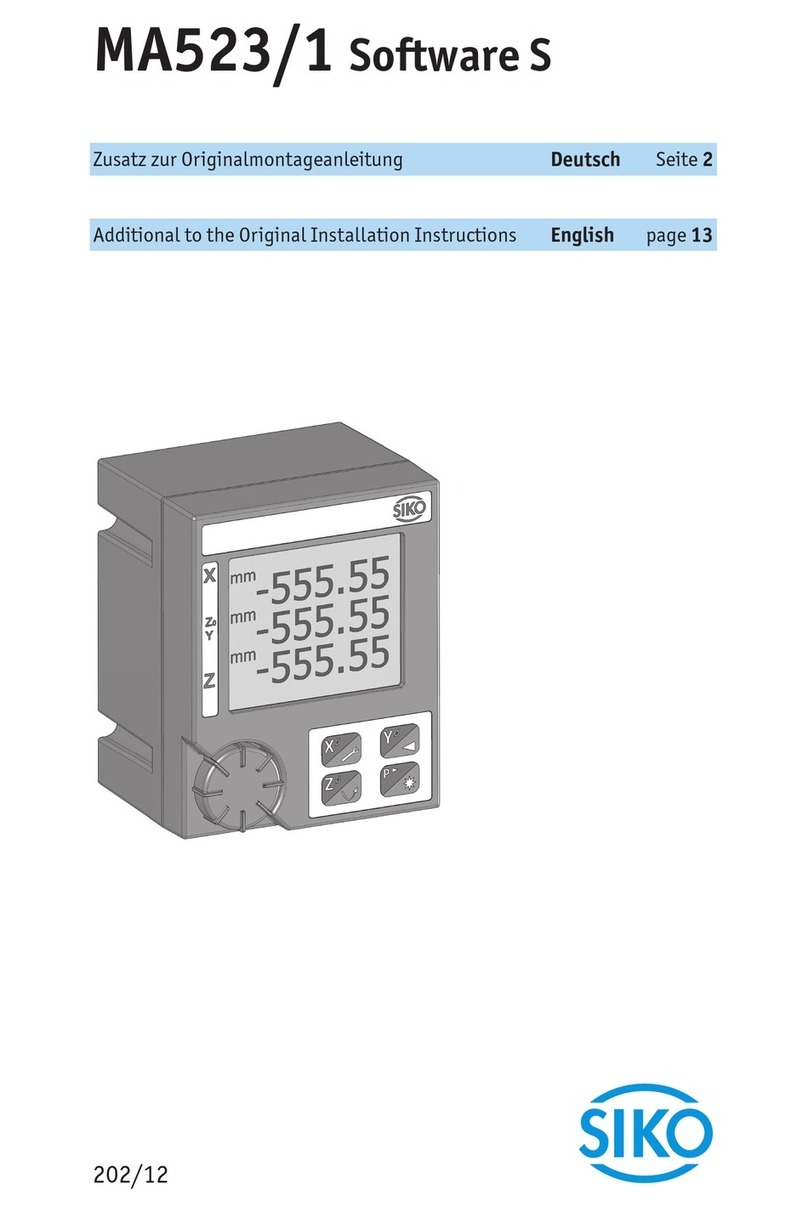
Siko
Siko MA523/1-S installation instructions
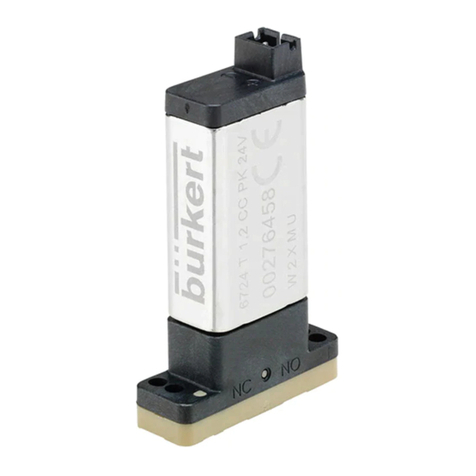
Burkert
Burkert WhisperValve 6724 operating instructions
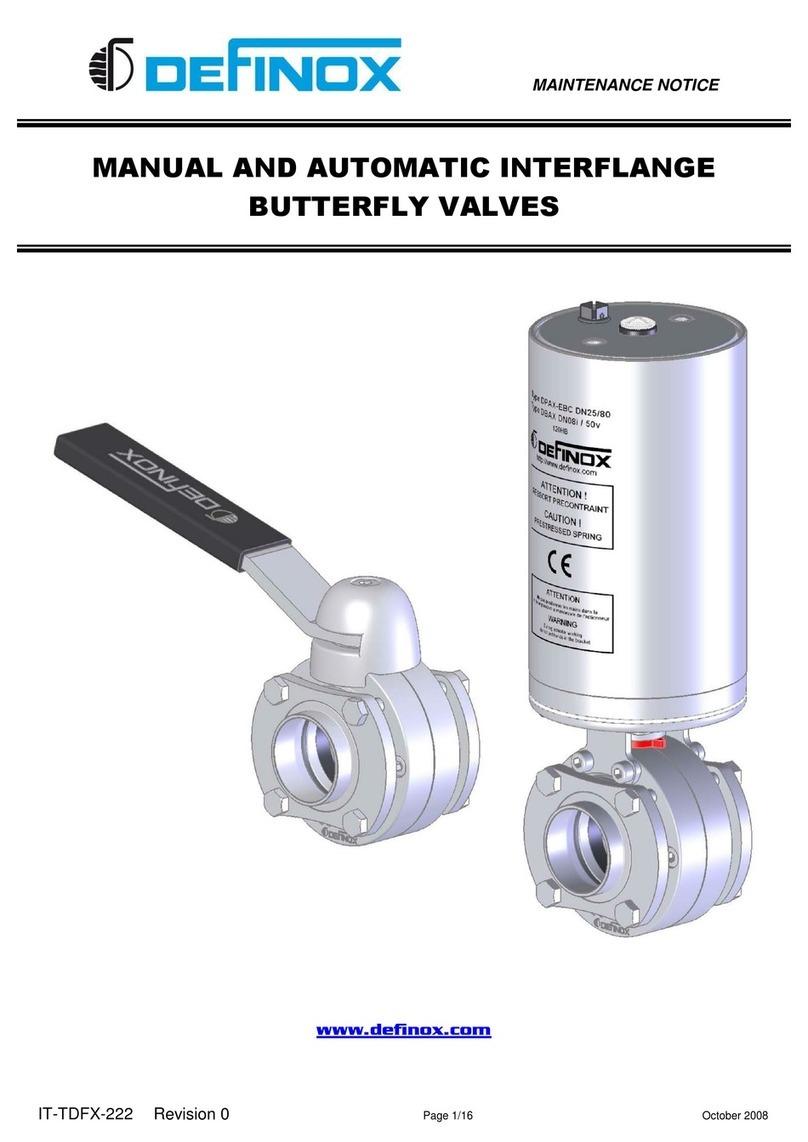
Definox
Definox DPX1EBC Maintenance notice
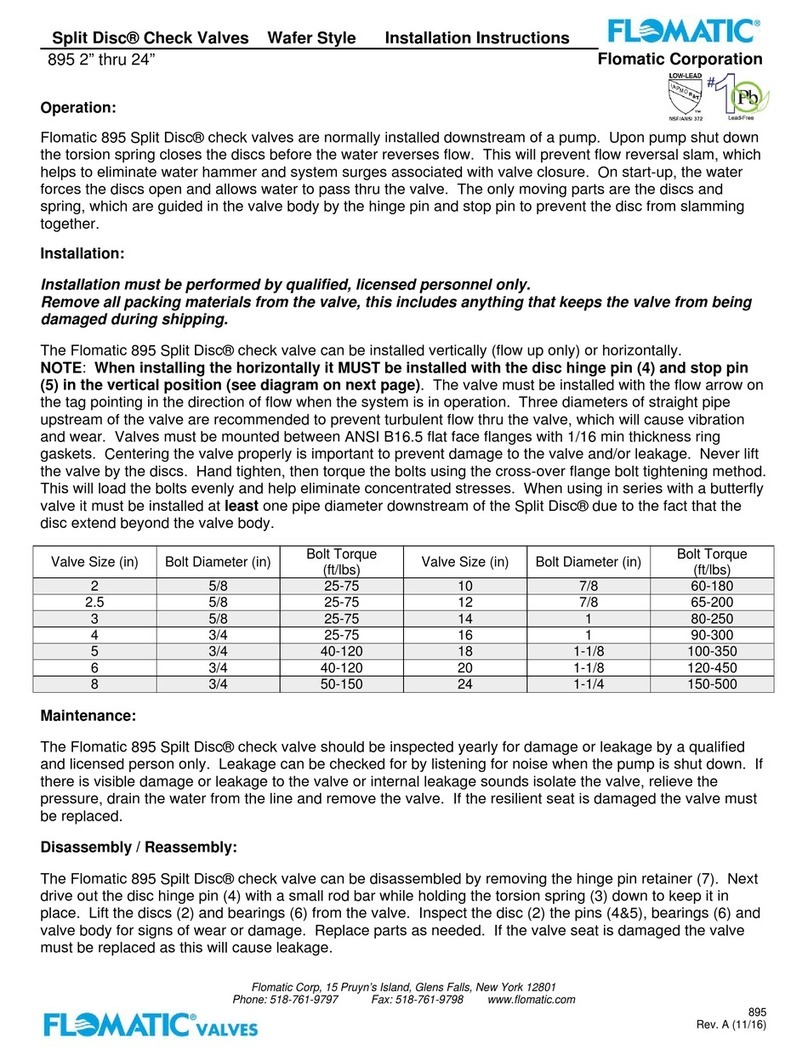
Flomatic
Flomatic Split Disc 895 installation instructions
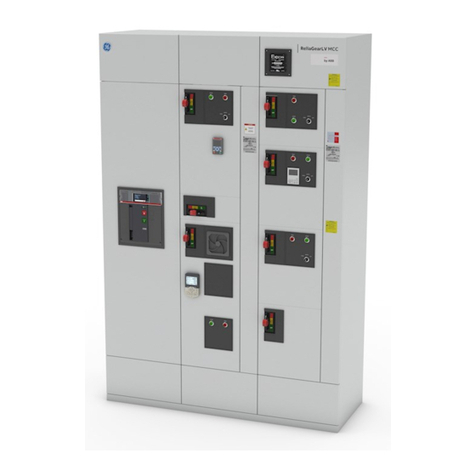
GE
GE ReliaGear LV MCC Installation, operation and maintenance manual
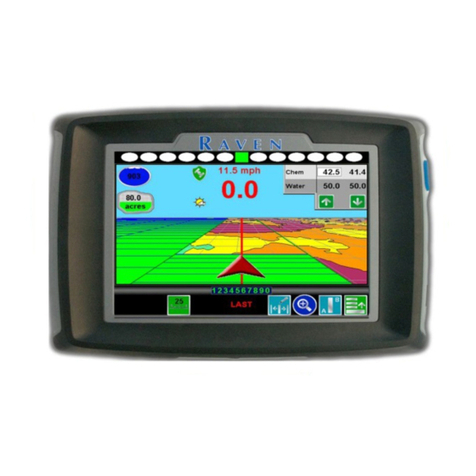
Raven
Raven Envizio Pro Series Quick reference guide
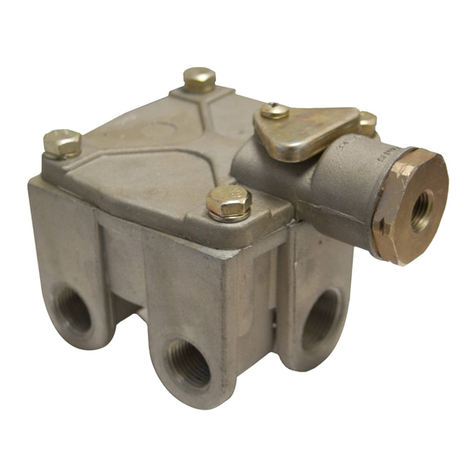
BENDIX
BENDIX R-12-R-14 RELAY VALVES manual
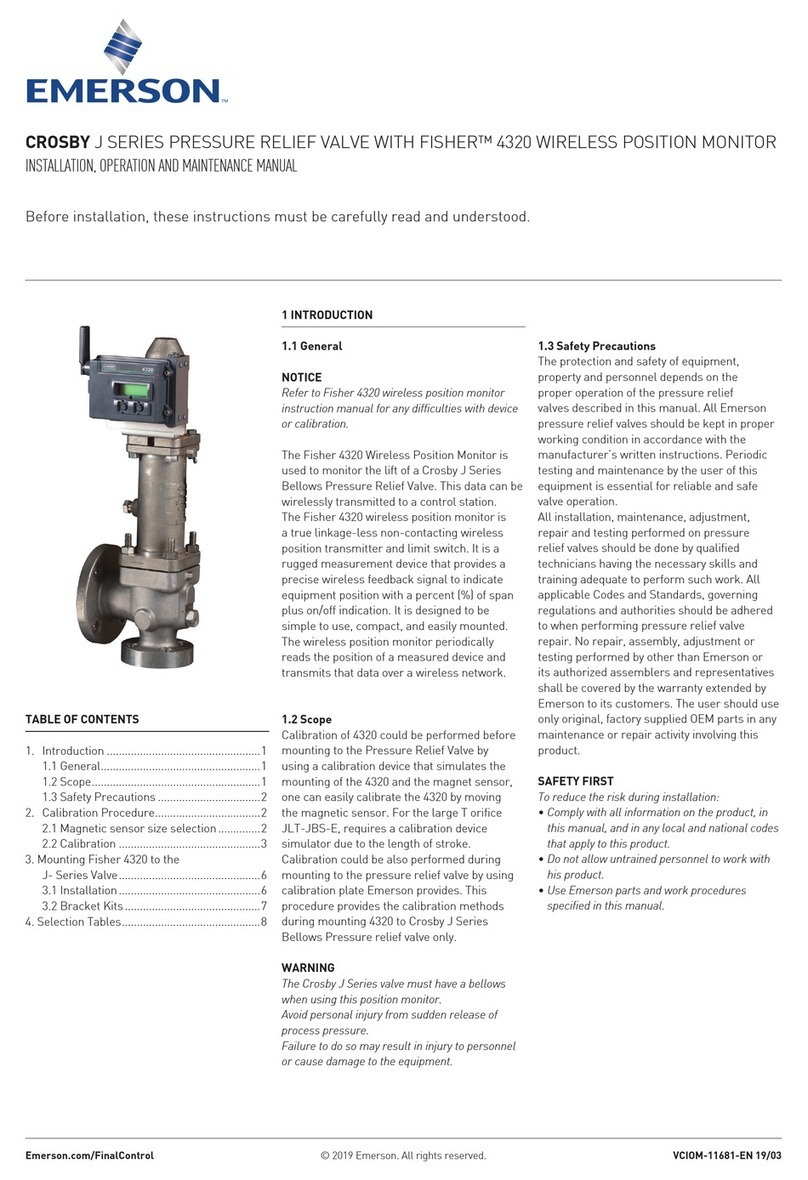
Emerson
Emerson Crosby J Series Installation, operation and maintenance manual

X-cam
X-cam GSM110 user manual

Burkert
Burkert 6026 operating instructions
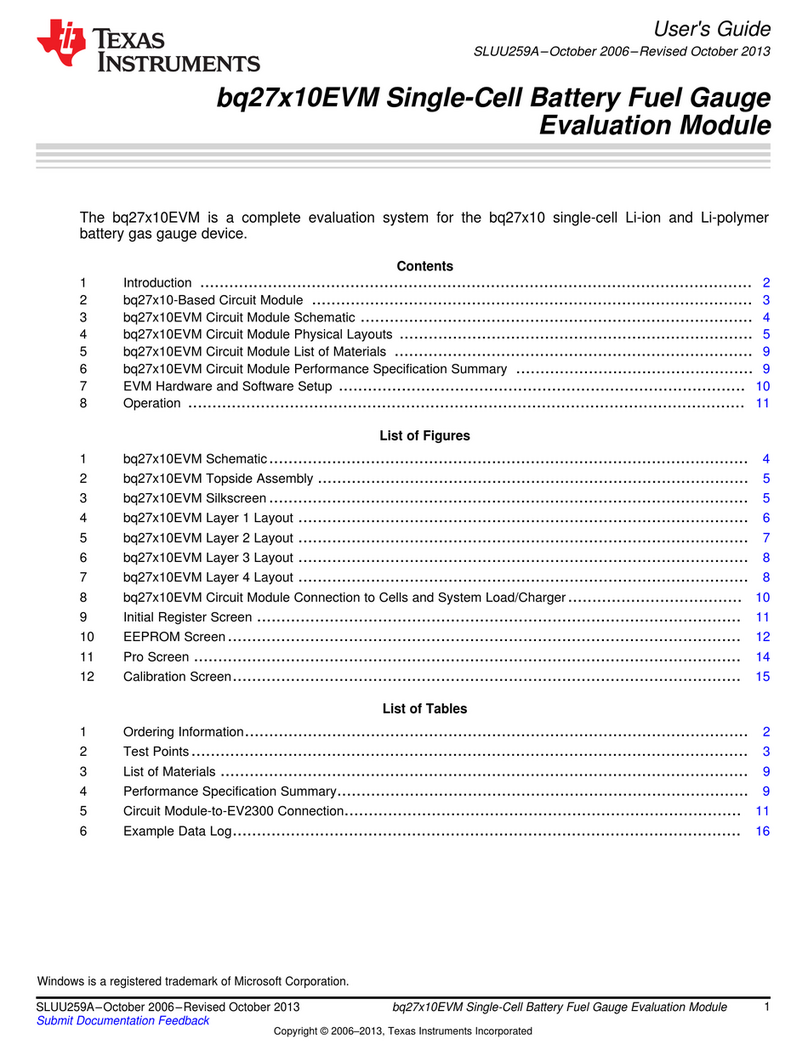
Texas Instruments
Texas Instruments bq27 10EVM Series user guide