ATS BBR3 User manual

MAN - BBR3 - REV: Original
BBR3
Bending Beam Rheometer 3
INSTRUCTION MANUAL
This manual contains important operating and safety information. Carefully read and
understand the contents of this manual prior to the operation of this equipment.
www.atspa.com

MAN - BBR3 - REV: Original
REVISED JULY 2018.
Information in this document is subject to change without notice and does not represent a commitment on the part of
Applied Test Systems (ATS).
© Copyright Applied Test Systems 2018.
For assistance with set-up or operation, contact the ATS service department. Please have this manual and product
serial number available when you call.
Telephone: +1-724-283-1212.

MAN - BBR3 - REV: Original i
Manual Contents
A. Introduction................................................................................................................................ 1
A.1 Unpacking.................................................................................................................................................. 1
A.2 Standard Users and Passwords ................................................................................................................ 1
A.3 Warranty Information ................................................................................................................................. 1
A.4 After Sale Support ..................................................................................................................................... 1
B. Safety .......................................................................................................................................... 3
B.1 For Owners, Operators, and Maintenance ................................................................................................ 3
B.2 Cautions & Warnings ................................................................................................................................. 3
C. System Overview ....................................................................................................................... 6
C.1 Equipment Parts........................................................................................................................................ 6
Front of Unit ......................................................................................................................................... 6
Back of Unit.......................................................................................................................................... 7
Load Frame.......................................................................................................................................... 8
Tank Interior ........................................................................................................................................ 9
Gage Kit ............................................................................................................................................. 10
C.2 General Product Description ....................................................................................................................11
Major Components..............................................................................................................................11
Accessory Items..................................................................................................................................11
Product Specications ....................................................................................................................... 12
Environmental Conditions .................................................................................................................. 13
Load Frame........................................................................................................................................ 13
Specimen Support ............................................................................................................................. 14
Air Bearing ......................................................................................................................................... 15
Linear Variable Dierential Transformer (LVDT) ................................................................................ 15
Load Cell............................................................................................................................................ 15
Resistance Temperature Detector (RTD)........................................................................................... 15
Computer Control System Software .................................................................................................. 15
Mechanical Refrigeration Unit (Chiller) .............................................................................................. 16
Accessories........................................................................................................................................ 16
Specimen Molds .......................................................................................................................... 16
Condence Beam ........................................................................................................................ 16
Non-Compliant Beams................................................................................................................. 17

ii MAN - BBR3 - REV: Original
Step Disk ..................................................................................................................................... 17
Load Cell Calibration Weights...................................................................................................... 17
Controls.............................................................................................................................................. 18
Internal Controls .......................................................................................................................... 18
Data Instruments ......................................................................................................................... 19
Basic Unit Controls ...................................................................................................................... 20
D. Installation................................................................................................................................ 21
D.1 Recommended Tools............................................................................................................................... 21
Installation.......................................................................................................................................... 21
Operation ........................................................................................................................................... 21
D.2 Unpacking the BBR3 ............................................................................................................................... 21
D.3 Assembling the Load Nose...................................................................................................................... 22
D.4 Connecting Equipment ............................................................................................................................ 25
E. Operation .................................................................................................................................. 28
E.1 Filling the Bath......................................................................................................................................... 28
E.2 Power Up the BBR3 ................................................................................................................................ 28
E.3 Overview of Touchscreen and Menus ..................................................................................................... 29
E.4 Editing Users and Permissions................................................................................................................ 29
E.5 Standardization Process.......................................................................................................................... 32
E.6 Verication Process ................................................................................................................................. 36
E.7 Test Setup................................................................................................................................................ 40
Test Name.......................................................................................................................................... 41
Test Date ........................................................................................................................................... 41
Saving Test Parameters..................................................................................................................... 41
Copying a Test ................................................................................................................................... 41
Creating a New Test........................................................................................................................... 42
Deleting a Test ................................................................................................................................... 42
Adding Report Images ....................................................................................................................... 42
Adding a Test Company..................................................................................................................... 43
Standard or Data Report.................................................................................................................... 43
Deection Plot and Load Plot............................................................................................................. 43
Bath Values........................................................................................................................................ 44
Specimen Values ............................................................................................................................... 44
Test Times.......................................................................................................................................... 44
E.8 Run Test .................................................................................................................................................. 44

MAN - BBR3 - REV: Original iii
Load Setup......................................................................................................................................... 45
Start Test............................................................................................................................................ 46
Run Crack Sealant Test ..................................................................................................................... 47
View Test............................................................................................................................................ 48
E.9 Diagnostics .............................................................................................................................................. 49
Analog Inputs AI1, AI2, and AI3 ........................................................................................................ 49
Analog Outputs AO1 and AO2 ........................................................................................................... 49
Digital Inputs 1, 2, 3, and 4 ............................................................................................................... 50
Digital Outputs 1 and 2 ..................................................................................................................... 50
Digital Outputs 3 and 4 ..................................................................................................................... 50
Cool PID Values................................................................................................................................. 50
F. Troubleshooting........................................................................................................................ 52
F.1 Preface..................................................................................................................................................... 52
F.2 Load Shaft Stuck or Stalled During Verication or Standardization ......................................................... 52
G. Maintenance ............................................................................................................................ 55
G.1 Cleaning the BBR3.................................................................................................................................. 55
G.2 Changing the BBR3 Fluid Bath ............................................................................................................... 55
APPENDIX A: Warranty ............................................................................................................... 56
APPENDIX B: Wiring Diagram..................................................................................................... 57
APPENDIX C: Declaration of Conformity ................................................................................... 59
APPENDIX D: Image Glossary..................................................................................................... 60

MAN - BBR3 - REV: Original | A. Introduction 1
A. Introduction
A.1 Unpacking
Retain all cartons and packing materials until the unit is operated and found to be in good condition. If damage has
occurred during shipping, notify Applied Test Systems (ATS) and the carrier immediately. If it is necessary to le a
damage claim, retain the packing materials for inspection by the carrier.
A.2 Standard Users and Passwords
Every BBR3 is programmed with three standard user settings. Each setting has a corresponding password and set of
user restrictions. Please refer to the table below to login and operate your new equipment.
User Name Password Permissions
Administrator admin Basic
Standardization Diagnostics
User Edit
Operator oper Basic
Standardization
Default Basic
A.3 Warranty Information
All new ATS systems are shipped with a warranty. Units have a warranty against defective parts and workmanship for
one full year from the date of shipment. Please see APPENDIX A of this manual for complete details on the warranty.
A.4 After Sale Support
If there are any questions concerning the operation of the unit or software, contact the ATS Service Department at
+1-724-283-1212.
Before calling, please obtain the software revision number and the serial number from the unit’s data tag. A sample
data tag is illustrated below, and can be completed with the unit’s information for easy reference. Please be prepared
to give a complete description of the problem to the ATS Service Department.

MAN - BBR3 - REV: Original | A. Introduction2
Figure A.1 - ATS Sample Data Tag

MAN - BBR3 - REV: Original | B. Safety 3
B. Safety
B.1 For Owners, Operators, and Maintenance
All ATS equipment is designed to be operated with the highest level of safety. This manual uses note, caution, and
warning symbols throughout to draw your attention to important operational and safety information.
Read and understand all instructions and safety precautions listed in this manual before installing or operating your
unit. If you have any questions regarding operation of the unit or instructions in this manual, contact the ATS Service
Department at +1-724-283- 1212.
Read and follow these important instructions. Failure to observe these instructions can result in permanent damage
to the unit, signicant property damage, personal injury or death.
B.2 Cautions & Warnings
Read and understand all instructions and safety precautions listed in this manual before installing or
operating your unit. If you have any questions regarding operation of the unit or instructions in this
manual, contact our Service Department.
Thoroughly understand the safety features and operation of the equipment. This manual will provide
operators with safety concerns and general procedures. Be familiar with correct operating principals
and use good judgment. Also refer to the appropriate manuals for system component safety
instruction manuals.
Use caution when working with liquids at low temperatures. Protect skin by wearing protective
clothing, and follow safety, operation, and maintenance procedures described in the appropriate
instruction manuals.
Obey all national and local electric code requirements.
Handle the BBR3 carefully. Avoid dropping and jarring the BBR3. Damage to machine may result.
Dangerous high voltages present. Do not attempt to open the enclosure or gain access to areas
where you are not instructed to do so. Refer servicing to qualied service personnel only.
Injury to the operator could occur if operational procedures are not followed. Follow all steps or
procedures as instructed and refer to accompanying documents.
Flammable vapors may be emitted from bath. Operate uid bath in a well ventilated area . Do not
smoke or use an open ame near the bath. Refer to uid manufacturer’s documentation for more
detailed information specic to safety precautions for the bath uid being used.

4MAN - BBR3 - REV: Original | B. Safety
Do not submerge hand and arm in extremely cold test bath. Do not attempt to pull the drain plug
when the uid bath level is high and temperature is extremely cold. Extremely cold uid may cause
frost bite.
Use caution when handling air hoses during operation or when performing maintenance as contents
will be under pressure.
Handle load cell with care. The load cell will be damaged if the load frame is put on it’s side with the
load nose attached, or if the load nose is over tightened.
Handle the refrigeration hose with care. The refrigeration hose may be damaged if it is twisted or
pulled, especially when the unit is cold. Do not move the refrigeration unit unless it has been turned
o for at least 8 hours and has reached room temperature.
Prevent damage to the cooling unit. Never operate the cooling unit if the ambient temperature is
higher than 25 degrees C.
The cooling unit should be placed in a well- ventilated area, on a stand at least six inches above the
oor and not on the same surface as the BBR3.
Carefully place the calibration weights on the load cell’s weight pan. If the Linear Variable Dierential
Transducer (LVDT) shaft is bumped, it may become inaccurate or even permanently damaged.
Avoid damage to the Condence Beam. Do not leave a load on the condence beam for an extended
period of time. This may cause the beam to bend and could result in inaccurate readings for future
tests.
Before energizing the electrical power to the bending beam rheometer, turn o all power switches and
place all controls in an OFF or neutral position. Check that your power source is of the appropriate
voltage and is surge- protected. Use appropriate power adapters based upon your region.
FLAMMABLE CHEMICALS may be located within enclosure. Exposure may result in severe injury.
Refer to maintenance manual before servicing.

MAN - BBR3 - REV: Original | C. System Overview 5
C. System Overview
C.1 Equipment Parts
Front of Unit
1. Load Frame
2. Chiller
3. USB Port
4. Touch Screen Monitor
5. Power Indicator
6. Leveling Feet
7. ZERO Regulator
8. LOAD Regulator
Figure C.1 - Front of BBR3 Unit
1
2
3
4
5
6
7
8

6MAN - BBR3 - REV: Original | C. System Overview
Back of Unit
1. Air Connector
2. Connects to Chiller
3. Connects to Load Frame
4. Unit Power
5. Network/Ethernet
6. USB Connection
Figure C.2 - Back of BBR3 Unit
1
2
3
4
56

MAN - BBR3 - REV: Original | C. System Overview 7
Load Frame
1. LVDT Shaft
2. Weight Pan
3. Gaging Disk
4. Bearing Air Supply/Control
5. Lamps
6. Shroud
7. LVDT Housing
8. LVDT
9. Air Bearing
10. Load Cell
11. Load Nose
Figure C.3 - Load Frame
1
2
3
4
4
55
10
6
11
7
8
9

8MAN - BBR3 - REV: Original | C. System Overview
Tank Interior
Gauge Kit
1. 100g Weights
2. Step Disk
3. 2g Weights
4. Load Nose
5. Anvil Adapters
6. Non-Compliant Beam
7. Crack Sealant (CS) Non-Compliant Beam
8. Condence Beam
Figure C.5 - Gauge Kit
1
2
3
4
56
7
8
5
1. Spinner
2. RTD
3. Drain
Figure C.4 - Tank Interior
1
3
2

MAN - BBR3 - REV: Original | C. System Overview 9
C.2 General Product Description
The ATS Bending Beam Rheometer 3 (BBR3) is designed to provide a state-of-the-art means for testing the
exural creep stiness properties of asphalt binders in a temperature range from -40°C to ambient. This testing is in
accordance with the Strategic Highway Research Program (SHRP) Test Method B-002, AASHTO Designation T313,
AASHTO TP 87, BS EN14771, and ASTM D 6648 specications. The BBR3’s design does not allow for it to perform
any additional functions other than the intended functions specied in this manual.
The BBR3 test control function and data acquisition is operated by a Windows®-based computer inside the
machine. During testing, the software controls the BBR3 load function, displays and records the load, deection, and
temperature data received from the unit. When tests are not being performed, the software permits access to test
information including graphs, raw data tables, and test analysis.
The BBR3 is a fully integrated, modularized system consisting of the following:
Major Components
• Base unit
• Load frame assembly
• BBR3 software
• Mechanical refrigeration unit
Accessory Items
• Specimen Molds (5 molds)
• Condence Beam
• Non-Compliant Beam
• Crack Sealant (CS) Non-Compliant Beam
• Step Disk
• Load Cell Calibration Weights (4) 100-gram and (2) 2-gram
• Crack Sealant Specimen Molds
Product Specications
Load Frame Construction Integral stainless steel, frictionless construction
Loading Shaft Point In-line stainless steel with blunt point
Test Load Variable test range from 0 to 4,000 mN standard. System. Maintains
required test load within +/- 5mN throughout test cycle.
Test Cycle Times Cycle times for pre-load, recovery, and test load are completely
operator-adjustable.
Load Cell 500 g (temperature-compensated)

10 MAN - BBR3 - REV: Original | C. System Overview
Mechanical Overload Protection Standard
Test Weights Calibrated and traceable to NIST
BBR3 Weight Base = 83 lbs , Load frame = 15 lbs
Chiller Weight 50 lbs (23 Kg)
BBR3 Size/Dimensions H=23.5” x W=24” x D=26.5”
Rating IP20 Enclosure rating
Sample Supports 3mm (.118”) radius stainless steel spaced 4.00in (101.6mm) apart
LVDT Displacement Transducer 6.35mm (0.25in) calibrated range to provide 2μm resolution
throughout testing and verication range.
Data Display Large on-screen display of load, displacement, and bath temperature
provides ease of setup and operation. Real time displacement,
loading, and temperature graphs are displayed during the test cycle
and can be re-plotted and re-scaled as needed for easy viewing.
Chiller Included (non-CFC refrigerant)
Tank Liquid Volume 1.5 Gallons (5.5 Liters)
Operating Temperature Ambient to -40°F (-40°C)
Temperature Measurement Platinum RTD
Power Requirements 120 VAC, 60Hz or 230 VAC, 50/60 Hz 2 AMP power rating
Air Pressure 60 PSI inlet pressure (414 kpa) @ Class 3 Quality max particle of
5um
Environmental Conditions
The BBR3 is designed for use in an industry/laboratory setting in an indoor and dry environment. The base unit
should be placed on a clean, stable work surface with the connecting mechanical refrigeration unit nearby. The
mechanical refrigeration unit should be placed 6 inches above the oor and in an area that will not constitute a
tripping hazard.
Load Frame
The load frame is an independent three-point loading device designed to apply a load of up to 4000 mN. The load
frame may be operated in the supplied uid bath, or it may be used in ambient conditions. The load frame is designed
with space-saving design, rigid construction, and corrosion resistance.
The load frame is constructed of stainless steel plates and durable high-strength PVC uprights that are designed
to be dimensionally stable and provide accurate force control. The load frame consists of an integral free-oating
loading shaft within an air bearing to permit specimen loads in the range of 0 to 4000 mN. The air bearing also
provides reliable and rapid loading with an accuracy of ±5 mN.

MAN - BBR3 - REV: Original | C. System Overview 11
The load frame is constructed with a horizontal shelf that extends across the top of the base unit to provide supports
to suspend the lower portion of the load frame in the uid bath. The upper part of the load frame is covered by an
access panel that permits the user to easily view the top of the loading shaft. This panel also provides access to
the weight pan for easy calibration of the load cell and the Linear Variable Dierential Transformer (LVDT). Two low
voltage, sealed lamps are mounted in the base of the load frame in order to illuminate the specimen in the uid bath.
The load frame is made up of an LVDT shaft, weight pan, air bearing, load shaft, load cell, and adapter. A metal plate
cover is mounted to the front of the load frame and serves to protect the load cell from splashing uid and minimize
the eect of uid movement on the load nose.
Specimen Support
The bottom half of the load frame consists of an anvil with two metal supports designed for alignment of the
specimen. These specimen supports have a 3 mm contact radius and are xed 102 mm apart from each other. They
are designed to align samples that are approximately 127.00 mm x 12.70 mm x 6.35 mm.
Resting on each of the anvil’s specimen supports are two anvil adapters (see Figure C.7). During crack sealant
testing these anvil adapters need to be removed by lifting STRAIGHT UP on the adapter and pulling it o of the guide
pin. The load frame should be removed from the bath and allowed to warm to room temperature before removing the
anvil adapters.
The specimen supports and lower portion of the load frame are designed to be submerged in the constant-
temperature uid bath during the test. The uid in the bath provides a buoyant force that counterbalances the weight
of the specimen.
Air Bearing
The BBR3 incorporates an air bearing to provide frictionless loading performance. The air bearing control system
requires a constant 60 – 65 psi (414 – 448 kPa) minimum clean and dry air supply, @ Class 3 Quality max particle
of 5um. The air pressure to the air bearing is controlled by a set of high-precision air regulators located on the front
panel of the base unit.
Figure C.7 - Load Frame with Anvil Adapters
Figure C.6 - Load Frame without Anvil Adapters

12 MAN - BBR3 - REV: Original | C. System Overview
Linear Variable Dierential Transformer (LVDT)
The LVDT is calibrated at between 0 and 6 mm and is mounted in the upper section of the load frame assembly. A
free-oating core rod is attached directly to the load shaft. It measures the displacement of the specimen as the test
load is applied.
Load Cell
The load cell is a precision strain gauge-type, with 500 gram (4903 mN) force capacity. It is constructed of stainless
steel to prevent corrosion or damage by the uid during test procedures.
CAUTION: The load cell can be easily damaged, especially from side loading and excessive torque.
Use caution while handling the test frame when the loading shaft is attached. Remove loading shaft
before laying load frame on its side, especially before shipping.
Resistance Temperature Detector (RTD)
The RTD is a platinum measuring device that measures the cooling uid bath temperature, is attached to the chiller,
and relays the information to the computer control system software. It is mounted in the BBR3 bath directly under the
test specimen supports.
Computer Control System Software
The computer control system software provides user control of the BBR3 system in a Windows® environment with
touchscreen access. The software provides pull- down menus, button selections, and data entry text boxes for easy
updates and access to information.
The base unit contains an integrated personal computer, designed to eciently run the software. During operation,
the software collects and records the data from the various sensors on the load frame. During tests, the software
controls specimen loading and unloading. The software is organized so all the information required to conduct a
particular test is stored internally.
Mechanical Refrigeration Unit (Chiller)
The refrigeration unit (chiller) is an immersion cooler designed to act as a cooling source for sub ambient work in
liquid baths. It maintains the cooling uid at a constant temperature using the unit’s temperature controller and the
magnetic stirrer located in the bath. The single stage refrigeration system is equipped with one compressor. A hose
carries refrigerant through the cooling probe located in the bath.
Refer to the separate manufacturer’s literature for more detailed information regarding safety, operation, and
maintenance of the refrigeration unit.
WARNING: Refrigeration unit (chiller) will cause the test bath to be extremely cold. Do not submerge
hand or arm in extremely cold test bath. Do not attempt to pull the drain plug when the test bath level
is high and the temperature is extremely cold. Extremely cold uid may cause frostbite.

MAN - BBR3 - REV: Original | C. System Overview 13
Accessories
Specimen Molds
A specimen mold is used to create specimens. Each mold consists of ve aluminum bars of various sizes, three
mylar strips, and two holding rings. Five of these molds are supplied with the BBR3.
Condence Beam
The condence beam is a thin stainless steel beam of a known stiness. This beam is placed on the specimen
supports of the load frame during the condence check.
Non-Compliant Beams
The BBR3 comes with a Non-Compliant Beam and a Crack Sealant Non-Compliant Beam. The Non-Compliant
Beam is a length of stainless steel that has the same dimensions as a specimen. This beam is placed on the
specimen supports when verifying and calibrating the load cell and when performing the compliance test. The
Crack Sealant Non-Compliant Beam is the thicker of the two beams, and is used only for Crack Sealant tests.
Step Disk
The step disk is used during LVDT standardization and veri-
cation. It has ve positions containing high precision balls. The
calibration positions include a zero gaging and four subse-
quent steps which decrease in increments of 1, 3, 5, and 6
mm. These steps are labeled on the disk using the letters A
(1 mm), B (3mm), C (5mm), and D (6mm). This provides the
6mm test range required by both ASTM and AASHTO Speci-
cations.
Load Cell Calibration Weights
Four 100 gram and two 2 gram load cell calibration weights are supplied with the BBR3. These weights are
placed on the load frame weight pan during load cell verication. The weights are also used to calibrate the
load cell and ensure system compliance.
Figure C.8 - BBR3 Step Disk

14 MAN - BBR3 - REV: Original | C. System Overview
Controls
Internal Controls
Five Internal Controls are located inside the LEFT panel of the BBR3 base unit, when viewed from the front
(Figure C.9). These controls are factory set.
1. LINE PRESSURE REGULATOR - The line pressure regulator is positioned on the LEFT inside the panel. This
pressure is set at 60 psi.
2. BEARING PRESSURE REGULATOR - The bearing pressure regulator is located to the RIGHT of the line
pressure regulator, and the bearing pressure is set at 15 to 20 psi. Verify the settings if necessary.
3. DC POWER SUPPLY - This supplies DC Power necessary to operate the computer, touch screen display,
and other operating systems of the BBR3. A Green LED on the module indicates that the power output from
the power supply is in the desired range.
4. AMP CIRCUIT BREAKER - Provides over current protection for the electronics of the BBR3. The circuit
breaker handle should be in the UP position to allow current to ow to the BBR3.
5. LOAD CONTROL SOLENOID VALVE - Switches control of the air ow to the load frame air bearing between
the Zero and Load Control Valves on the front of the BBR3 during set-up and testing.
1
Figure C.9 - Internal Controls
2
34
5

MAN - BBR3 - REV: Original | C. System Overview 15
Data Instruments
The Data Instruments box and Signal Conditioner Modules, along with the 3 Solid State Relays, are all located
on the RIGHT side of the BBR3 base unit as viewed from the front (see Figure C.10).
1. DATA ACQUISITION BOX - Digitizes the amplied voltages from the Load Cell and Signal Conditioner
Modules and sends that information to the PC. Also receives command signals from the BBR3 Computer
and sends those signals to the Solid State Relays to operate the stirrer motor, bath heater, and load control
solenoid valve.
2. LOAD CELL SIGNAL CONDITIONER MODULE - Receives and conditions the output of the Load Cell, and
supplies an amplied voltage output to the Data Acquisition Box.
3. LVDT SIGNAL CONDITIONER MODULE - Receives and conditions the output of the LVDT
Displacement Sensor, and supplies an amplied voltage output to the Data Acquisition Box.
4 - 6. DC VOLT SOLID STATE RELAYS - Used to control the functions of the Bath Heater (4), Stirrer Motor (5),
and Load Control Solenoid Valve (6). These modules are identical and interchangeable.
Figure C.10 - Data Instruments
1
2
3
4
5
6
Table of contents
Other ATS Measuring Instrument manuals
Popular Measuring Instrument manuals by other brands

Castle group
Castle group Castle Sonus L quick start guide
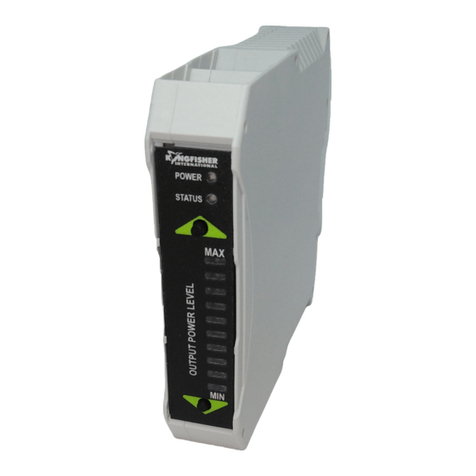
Kingfisher
Kingfisher KI5000 Series user manual

Endress+Hauser
Endress+Hauser Prothermo NMT81 operating instructions
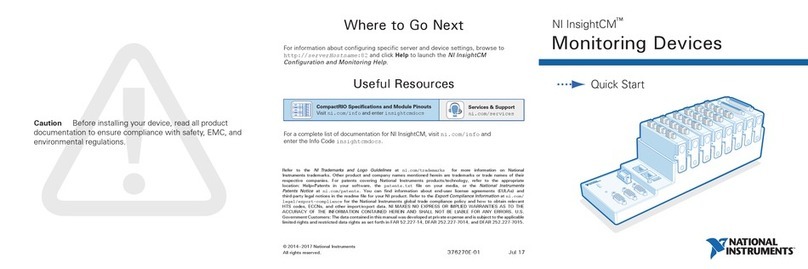
National Instruments
National Instruments InsightCM quick start
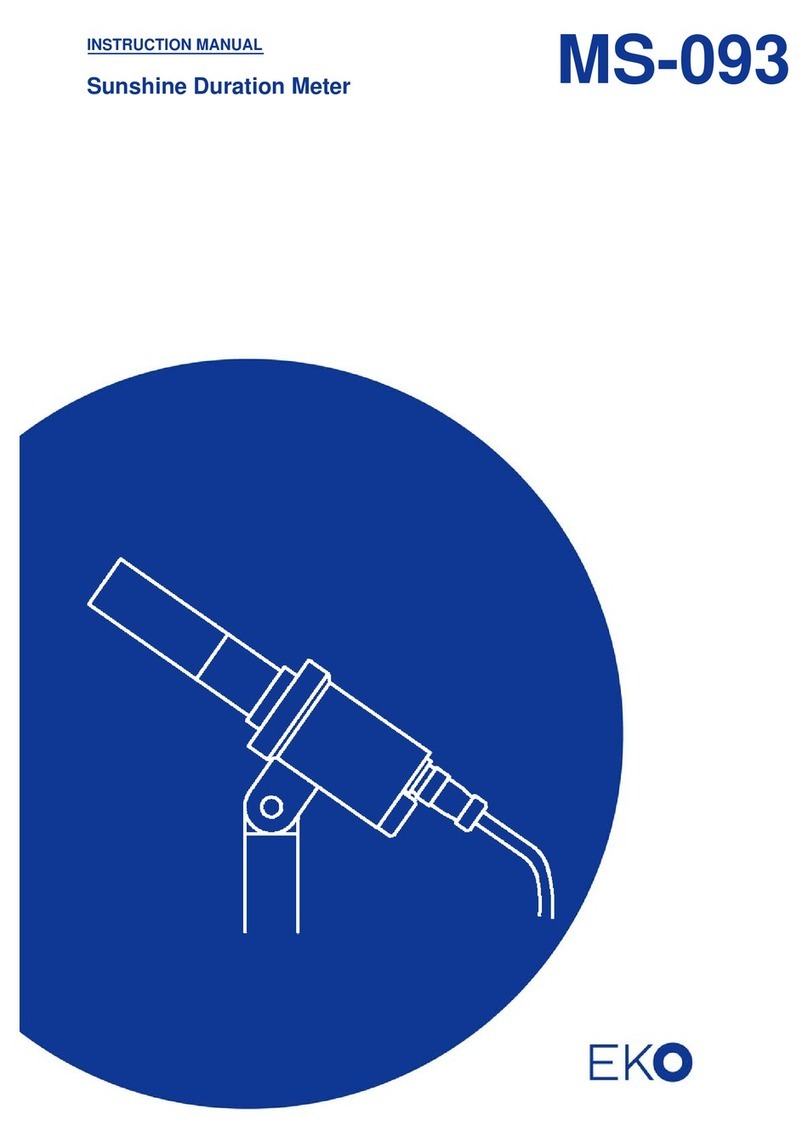
EKO
EKO MS-093 instruction manual
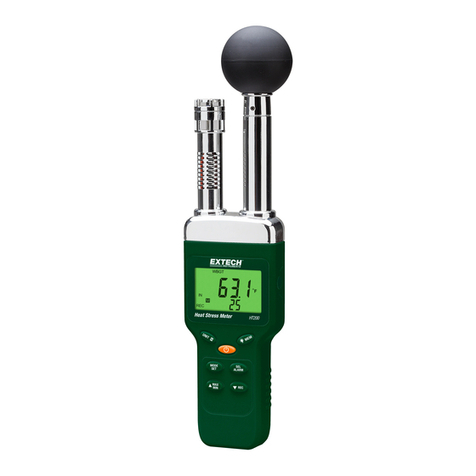
Extech Instruments
Extech Instruments HT200 user manual
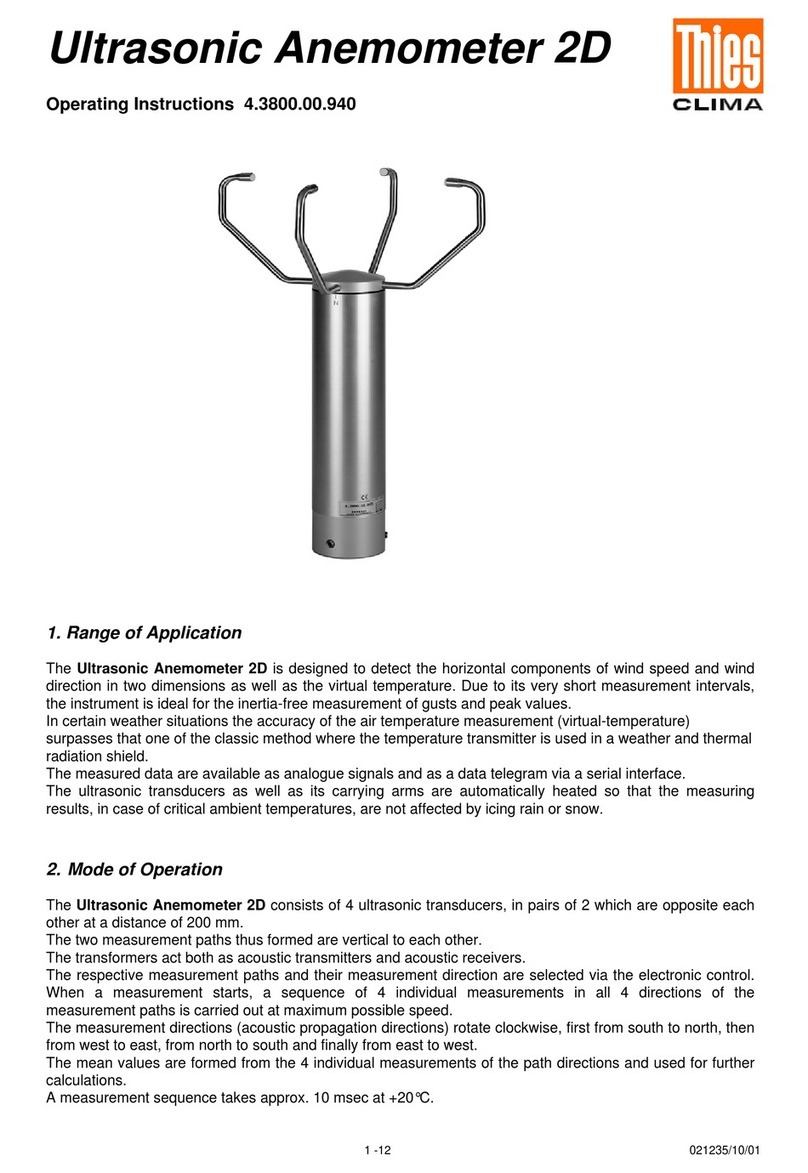
Thies CLIMA
Thies CLIMA Ultrasonic Anemometer 2D operating instructions
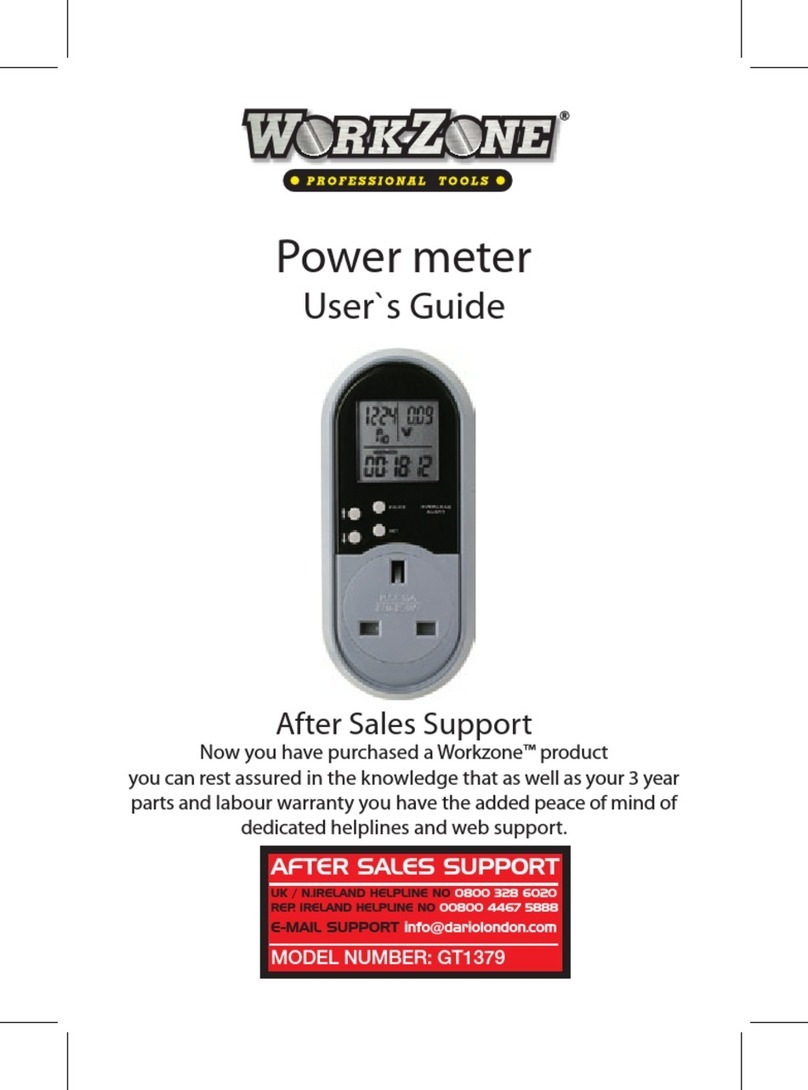
Workzone
Workzone GT1379 user guide

Contrel
Contrel EMA90 user manual
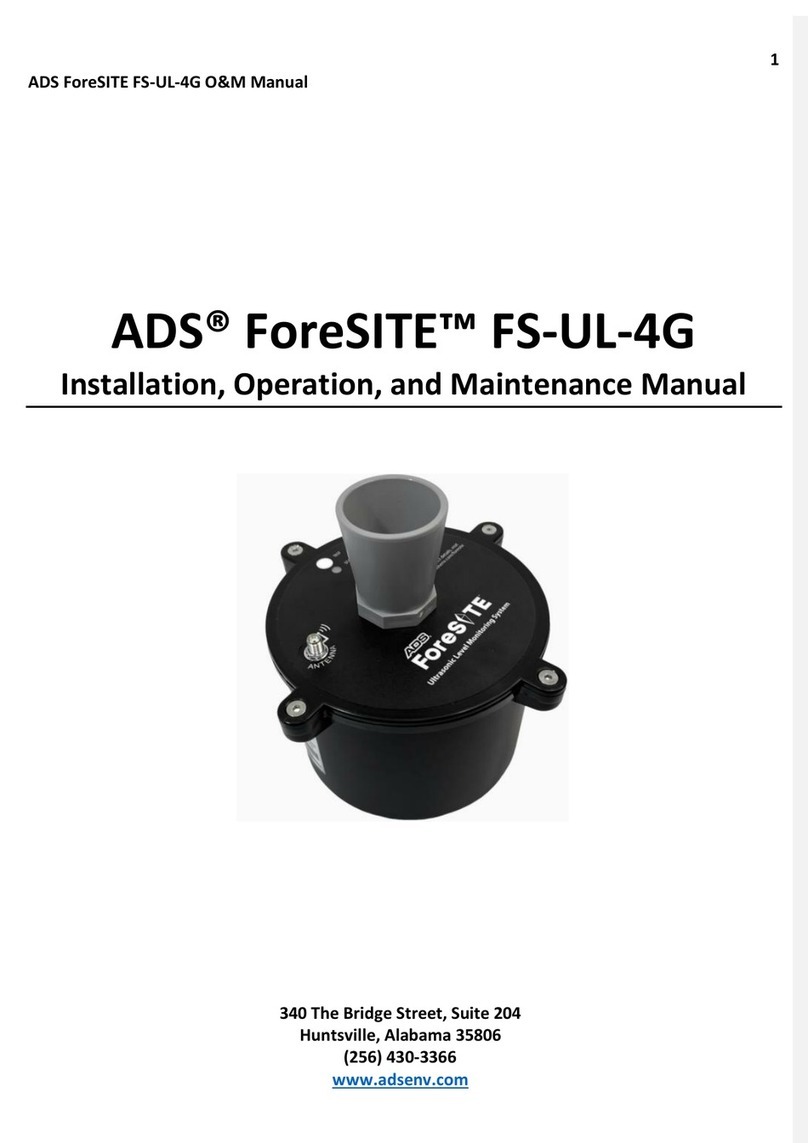
ADS
ADS ForeSITE FS-UL-4G Installation, operation and maintenance manual
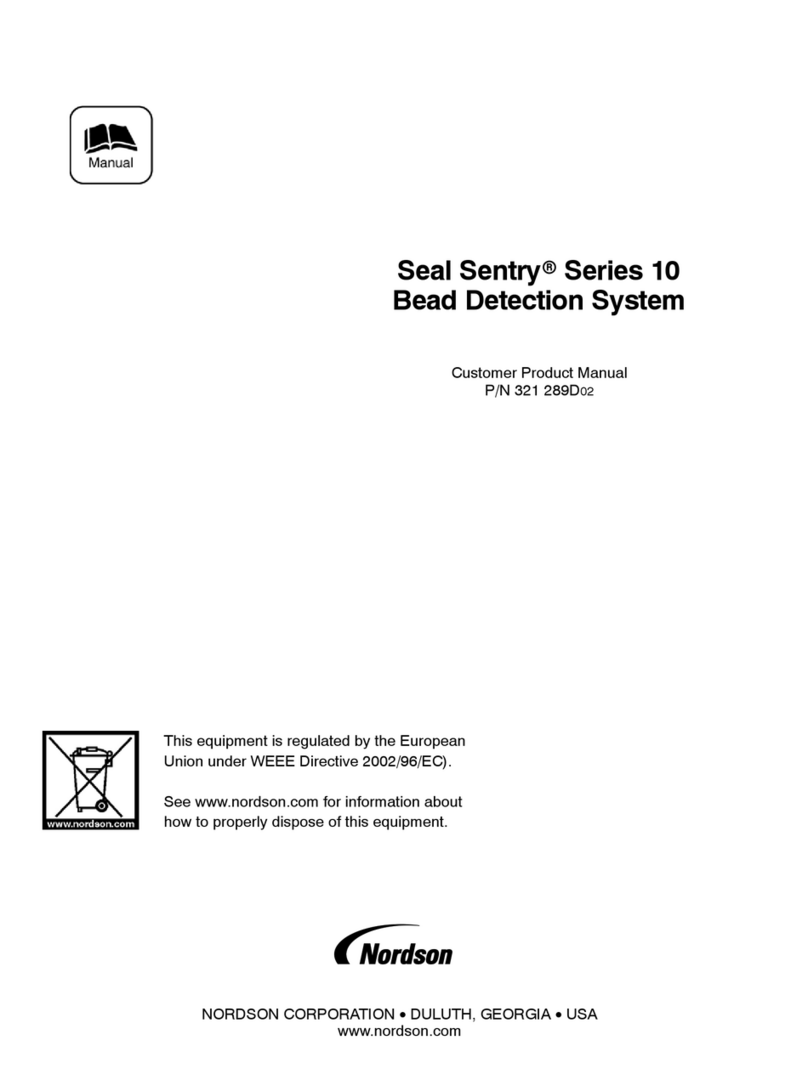
Nordson
Nordson Seal Sentry 10 Series Customer product manual

Niigata seiki
Niigata seiki CDI-50 instruction manual