AVR 30 Series Instruction manual

Instruction for use
Thank you for selecting an AVK product. With correct use, the product is guaranteed to deliver a long and
reliable service. This manual has been prepared to assist you with the installation, operation and maintenance
of the hydrant to the maximum efficiency. For ease of reference, it has been divided into sections covering all
aspects of use, in the users best interests please read it and ensure that it is fully understood.
Health and Safety
It is always recommended that wherever work is being conducted on a valve, the valve is fully depressurised
prior to carrying it out, and for convenience, draining of the line may be beneficial.
It is essential that the user of the valve is aware of the weight of the components and/or assemblies that must
be handled and manipulated during installation and maintenance. It is the users responsibility to ensure that
safe working practices are followed at all times.
Whenever AVK products are installed, operated, or maintained, it is essential that the staff that undertake
these operations be adequately trained. The hazards of pressurised liquids and gases can be severe, and it is
the responsibility of the users to ensure that trained, competent staff undertake these duties. This manual has
been designed to assist, but it can never fully replace quality training in the workplace. AVK technical staff will
always be available to answer any questions relating to specific problems that may not be covered by this
manual.
AVK products are designed and manufactured to be fit for purpose, and to a high and reliable standard. This
provides a safe product with minimum risk to health when used correctly for the purpose for which it was
designed. However, this assumes that the equipment is used and maintained in accordance with the manual,
and the user is advised to study this manual, and to make it available to all staff that may need to refer to it.
AVK cannot be held responsible for any incidents arising from incorrect installation, operation or maintenance.
The responsibility for this must rest wholly with the user.
SERIES 30 HYDRANT
INSTALLATION, OPERATION & MAINTENANCE MANUAL
AVK Australia Holdings Pty Ltd - 559A Grand Junction Road, Wingfield, SA 5013, Australia - Tel: +61 8 8368 0900 - Email: enquires@avkau.com.au - www.avkcivil.com.au Version number 2
COPYRIGHT©AVK GROUP A/S 2017 Pg1

1. Introduction
IT IS IMPORTANT TO STATE OPERATING TEMPERATURE, PRESSURE, MEDIUM AND OPERATING CONDITIONS WITH
ENQUIRIES/ORDERS, SO THE MOST SUITABLE VALVE WILL BE SUPPLIED FOR YOUR SPECIFIC PURPOSE.
AVK Valves Pty Ltd - 559A Grand Junction Road, Wingfield, SA 5013, Australia - Tel: +61 8 8368 0900 - Email: [email protected] - www.avkvalves.com.au Version number 2
COPYRIGHT©AVK GROUP A/S 2017
SERIES 30 HYDRANT
INSTALLATION, OPERATION & MAINTENANCE MANUAL
Refer to individual datasheets for specific information
QLD, NSW, VIC, TAS
Series 30/00 Spring Hydrant
Series 30/10 Spring Hydrant (Swab Type)
Both series available with blue yoke for potable water or purple yoke for recycled water
The valves are 100% factory tested hydrostatically.
AVK series 30 hydrants are designed to meet local specifications and include:
Standards Mark Compliance - According to AS3952-2020
AVK Australia Holdings Pty Ltd - 559A Grand Junction Road, Wingfield, SA 5013, Australia - Tel: +61 8 8368 0900 - Email: enquires@avkau.com.au - www.avkcivil.com.au Version number 2
COPYRIGHT©AVK GROUP A/S 2017 Pg 2
Series 30/00

SERIES 30 HYDRANT
INSTALLATION, OPERATION & MAINTENANCE MANUAL
Component list 30/00 series
Spare parts component list 30/00 series
Component Code
2. Yoke 300801512
3. Protective plug 3008017
4. Seat 3008013
5. Spring 3008016
6. Dome 300801400
AVK Australia Holdings Pty Ltd - 559A Grand Junction Road, Wingfield, SA 5013, Australia - Tel: +61 8 8368 0900 - Email: enquires@avkau.com.au - www.avkcivil.com.au Version number 2
COPYRIGHT©AVK GROUP A/S 2017 Pg 3
series 30/10 swab
has a removable guide

2. Installation
•When installing the valve, ensure the flange faces are clean.
•To ensure adequate sealing it is important to select the correct type of gasket for the medium concerned, a gasket with the
correct flange size must be used.
•Place valve onto the pipe flange, and insert the bolts.
•Tighten bolts loosely.
•Tighten bolts in a diagonal sequence to ensure flanges are pulled parallel.
•Finally tighten bolts to correct torque levels as recommended in WSA 109.
2.1. Bolts
2.1.1 Bolt size
The following table shows the bolt size you should use for each valve size
3. Operation
DN
mm Bolts Quantity
80 M 16 4
100 M 16 4
SERIES 30 HYDRANT
INSTALLATION, OPERATION & MAINTENANCE MANUAL
This series of Spring fire hydrants are suitable for use with clean water and neutral liquids, to a maximum temperature of
70°C. Minimum liquid temperature must be above freezing. Insulation is essential for external temperatures on 0°C and
below to a limit of -10°C. They are rated for a maximum working pressure of 16 bar.
SWABBING
it is not possible to use the 30/00 series spring type for this purpose.
Only the 30/10 Swab type is suitable for the introduction and retrieval of swabs.
4. Method of Operation
The AVK 30 series Hydrant is spring loaded and opened and closed by an approved standpipe arrangement.The standpipe
locks into position under the yoke and the tap at the top controls a rod that compresses the dome.
AVK Australia Holdings Pty Ltd - 559A Grand Junction Road, Wingfield, SA 5013, Australia - Tel: +61 8 8368 0900 - Email: enquires@avkau.com.au - www.avkcivil.com.au Version number 2
COPYRIGHT©AVK GROUP A/S 2017 Pg 4
Series 30/10 Swab Type
Typical standpipe

4. Maintenance
SERIES 30 HYDRANT
INSTALLATION, OPERATION & MAINTENANCE MANUAL
SAFETY PRECAUTIONS:
When changing the Seat seal, Maintenance Procedures MUST NOT be carried out whilst the hydrant is installed in a
live water main under pressure.
4.1. PROCEDURE for Removal of the Seat, Dome and Spring Assembly
SAFETY PRECAUTION:
This procedure
MUST
NOT
be carried out with the hydrant under pressure.
Check to ensure there is no pressure in the main prior to commencing work.
Ensure the main WILL NOT be recharged before all work on the hydrant is completed
1)
First insert a stand pipe to ensure the pipeline is not under pressure.
2)
Ensure area around the hydrant is clear of soil and debris so contaminants don't enter the pipeline when the top yoke
is removed
.
Caution at this point is required as the spring behind the dome will have tension upwards forcing the
yoke up once nuts are removed
3) Remove
nut
(
7
)
from bolt (8), removing both equally as the spring dome (6) will have tension upwards on the seat (4) and
yoke (2)
.
4)
Keep pressure down on the yoke (2) during the final removal of the bolts
as the dome is forcing upwards
5)
Remove the yoke (2) carefully, the seat (4) the dome (6) and spring (5)
will
be accessible to remove from the body (1).
SWAB 30/10 VERSION
6) The insert that supports the spring and dome can be removed at this point
AVK Australia Holdings Pty Ltd - 559A Grand Junction Road, Wingfield, SA 5013, Australia - Tel: +61 8 8368 0900 - Email: enquires@avkau.com.au - www.avkcivil.com.au Version number 2
COPYRIGHT©AVK GROUP A/S 2017 Pg 6

4.2. PROCEDURE for Replacement of Seat, Dome and Spring Assembly
3) Depress the dome manually to check for freedom of movement
4) Position the resilient seat in the yoke groove, with the dome
seat downwards.
5) Carefully place the resilient seat and yoke over the dome, ensuring alignment
of the bolt holes, checking the seat is sitting central.
6) If the hydrant is in the work shop and you have provisions of a press, compress
the the dome down without damaging the spring, enough to fit the nuts.
Otherwise insert the bolts and place the washer and nut on with two threads each
side, pushing down on the dome.
Note The nut shall be installed upside down.
This is an Australian Standard requirement
9) Check to make sure that the resilient seat is sitting centrally. If the seat is not
sitting centrally depress plunger again loosen off bolts, reposition seat and
re-tighten.
7) Tighten the nuts ensuring the yoke is compressing evenly
8)Tighten the bolts evenly to 60nm using a torque wrench maintaining an even space
between the matting flanges on both sides
10) When satisfied the seat and dome are correctly installed, depress the dome twice
and check for freedom of movement and alignment.
11) Check final bolt torques
SERIES 30 HYDRANT
INSTALLATION, OPERATION & MAINTENANCE MANUAL
12) The valve is ready to be pressure tested
Diagram (a) 30/10 series swab insert
1
a
)
Swab version 30/10 has a removable insert to support the spring
and dome. Ensure this is inserted first and centrally located in recess.
(See diagram (a) below)
1) Insert the dome pin inside the spring with the dome head going over the
spring.
2) Insert the spring and dome into the body of the hydrant with the spring going
over the spindle guide and the stem through the guide.
AVK Australia Holdings Pty Ltd - 559A Grand Junction Road, Wingfield, SA 5013, Australia - Tel: +61 8 8368 0900 - Email: enquires@avkau.com.au - www.avkcivil.com.au Version number 2
COPYRIGHT©AVK GROUP A/S 2017 Pg 7
1)
2)
4)
6)
8)
12)
Table of contents
Other AVR Control Unit manuals
Popular Control Unit manuals by other brands

Viessmann
Viessmann VITOTRONIC 100 Installation and service instructions

Quectel
Quectel BG95 Series Application note
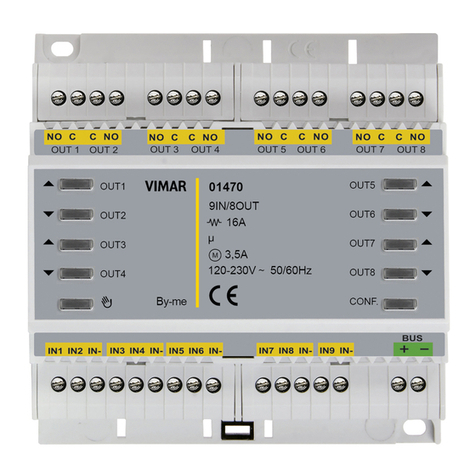
Vimar
Vimar 01470 manual
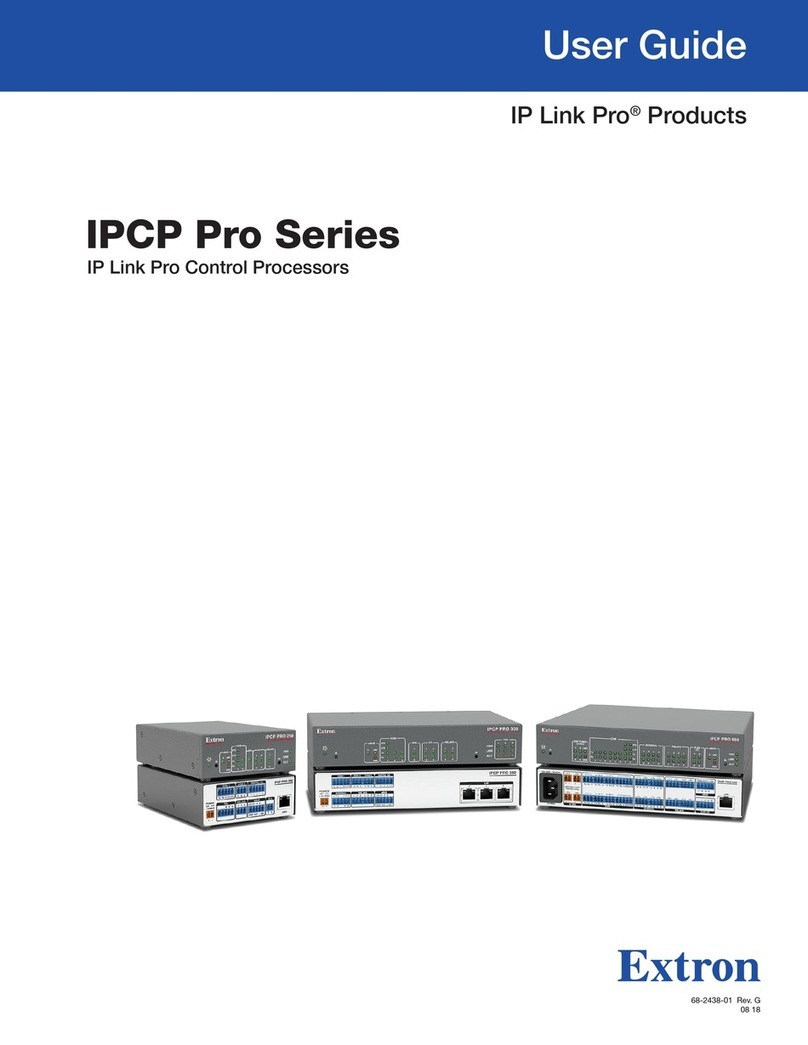
Extron electronics
Extron electronics IPCP Pro Series user guide

Fuji Electric
Fuji Electric MICREX-SX Series SPH user manual

Comunello
Comunello QUAD 24V HP Installation and user manual