B-TEC d-800 Installation instructions

B -TEC GmbH • Zunftweg 6-8 • D-31303 Burgdorf / Ehlershausen • Telephone : ++49(0)5085-97100-0
Fax : ++49(0)5085-97100-30 • Email : info@btecsystems.de • www.btecsystems.de
Original Operating Manual and Test Log Book for Water-Based Paint and
Solvent Cleaning System d-800
Cleaning Device
d-800
equipment and facility engineering

B -TEC GmbH • Zunftweg 6-8 • D-31303 Burgdorf / Ehlershausen • Telephone : ++49(0)5085-97100-0
Fax : ++49(0)5085-97100-30 • Email : info@btecsystems.de • www.btecsystems.de
EU-Declaration of Conformity According to DIN EN ISO/IEC 17050-1
Manufacturer:
Herewith, we declare that the machines and marketed models described in the following conform in
conception and in design to the relevant fundamental safety and health requirements of the applicable
EU directives.
All of our manufactured or assembled parts conform to the listed regulations.
If you change the machine without our explicit agreement, this declaration will be herewith invalidated.
Product type: Spraying-gun cleaning-device
Type designation: d-800
Serial-no.: Construction year: 20_ _
The machines conform to the following regulations:
The following harmonising standards have been used:
Safety of machinery, equipment and facilities: DIN EN ISO 12100 : 2011
Machines for surface cleaning, aqueous and combustible liquids: DIN EN 12921-1:2011-02
Non-electrical equipment for use in potentially explosive atmospheres: DIN EN 13463-1
General rules and safety requirements for pneumatic-systems: DIN EN ISO 4414
Special national norms are applied:
Guidelines for facilities to clean work pieces with liquid detergents: DGUV rule 109-010
Safety- and health signs at workplace: DGUV regulation 9
Ex declaration: II 2 G c II B T6
Responsibility for technical documents: Hans-Joachim Bödrich, Michael Bellroth
Address: Refer to manufacturer´s address
Location/Date/Manufacturer`s signature
Function of the signer: Managing director
equipment and facility engineering
Machinery Directive 2006/42/EG
Explosion-Protection Directive 94/9/EG ; Registered with: PTB 0102 / R.Nr.: 05 ATEX D 116
as from 20.04.2016 directive 94/9/EG is going to be replaced and conforms the directive 2014/34/EU!
.................................................................................
Hannover, 02.01.2016
B-TEC GmbH
Zunftweg 6-8
D-31303 Burgdorf / Ehlershausen

B -TEC GmbH • Zunftweg 6-8 • D-31303 Burgdorf / Ehlershausen • Telephone : ++49(0)5085-97100-0
Fax : ++49(0)5085-97100-30 • Email : info@btecsystems.de • www.btecsystems.de
Table of Contents
1. Important Information ........................................................................................................................ 1
1.1 Explanation of the Symbols ........................................................................................................... 2
2. Intended use and range of application ................................................................................................ 3
3. Safety requirements............................................................................................................................ 5
3.1 General security ............................................................................................................................ 5
3.2 Security checks.............................................................................................................................. 6
3.3 Operational safety......................................................................................................................... 6
3.4 Hazards from pneumatic energy.................................................................................................... 8
3.5 Excitation for operating instructions.............................................................................................. 8
4. Approved Cleaning Agents .................................................................................................................. 9
5. Technical Description of the Cleaner ..................................................................................................10
5.1 Technical Information ..................................................................................................................10
5.2 Details..........................................................................................................................................11
5.3 Part Names ..................................................................................................................................13
5.4 Pneumatic Plan ............................................................................................................................14
5.5 Spare Parts Ordering Numbers .....................................................................................................15
6. Requirements for the Installation Site ................................................................................................16
7. Transport and Installation ..................................................................................................................17
7.1 Connecting Exhaust......................................................................................................................17
7.2 Connecting Compressed Air..........................................................................................................18
7.3 Grounding....................................................................................................................................18
8. Operating Instructions .......................................................................................................................19
8.1 Commissioning.............................................................................................................................19
8.2 Operational Procedure .................................................................................................................19
8.3 Adjusting Facilities........................................................................................................................21
9. Care and Maintenance .......................................................................................................................22
9.1 Maintenance of the Machine .......................................................................................................22
9.2 Disposal .......................................................................................................................................23
10. Safety Inspection Checklist...............................................................................................................24
equipment and facility engineering

Cleaning Device d-800 Page 1
equipment and facility engineering
1. Important Information
We thank you for your trust you gave to us by buying the spraying-gun cleaning-device "d-800". On
the identification plate at your cleaner you can find the exact type designation and serial-number of
your cleaner to ensure an uncomplicated service and shipment of spare parts.
The B-TEC cleaners have been designed and manufactured to the highest quality standards for high
operational safety. Due to certain operation processes, there are places and parts that can´t be
protected without impairing operability and functionality. Therefore we ask you to read this
document carefully before using the cleaner in order to achieve maximum operational safety and
lifetime. The instructions are an integral part of the product and must be stored with the gun cleaner.
Read this document carefully before putting the gun cleaner into operation and keep
it for future reference!
On the last page of this instruction book, there is a form for documenting safety inspections, which
have to be conducted at regular intervals. The form has only to be filled out by qualified Person
(persons with sufficient knowledge and experience or manufacture´s mechanics) or experts (e.g.
engineers or Technical Control Board experts).
Safety inspections must be conducted before commissioning and at least once a
year!
The B-TEC devices and machines are only allowed to be used according to the intended purpose
explicitly described below. A usage not according to the intended purpose as well as unauthorized
modifications exclude the liability of the manufacturer for any damages resulting from this.
The B-TEC devices and machines are only to be used according to the intended
purpose explicitly described below!
These machines are to be used for cleaning varnish and spray paint guns as well as paint soiled parts
and hand tools using solvents (A I, A II, A III) or non-combustible, aqueous cleaners for water-based
paints. The Acetone content of the solvent used must be less than 65 %.
These gun cleaners must not be subjected continuous operation, such as, for instance, the serial
production. Improper use of the washers can endanger the health of the operator and of others and
cause damage to the cleaner itself or to other materials and assets.
Improper use of the cleaners can endanger the health of the operator!

Cleaning Device d-800 Page 2
equipment and facility engineering
1.1 Explanation of the Symbols
To recognize important information in this operating manual, the symbols “Caution!” and “Notice!”
are been used. Please note that text passages with these symbols on need particular attention.
Caution!
You will find this symbol whenever attention is drawn to situations in which danger to
life can arise due to or during incorrect or improper operation. Pay special attention to
these symbols and act carefully.
Notice!
You will find this symbol in the operating manual whenever your attention shall be
drawn to correct work procedures, economic ways of operation or when the machines
can be damaged by incorrect operation.

Cleaning Device d-800 Page 3
equipment and facility engineering
2. Intended use and range of application
The spray-gun cleaner d-800 may only be used for its intended purpose.
This unit is not intended for purposes beyond the following terms and
the manufacturer/supplier is not liable for any damages resulting from
it.
Intended use:
The intended use of this device is to clean spray-guns or ink-soiled pieces/tools (e.g. stirring rods,
mixing bowls etc.).
This device is suitable for:
Solvents (former danger classes A I, A II, A III according to VbF) and
Nonflammable, water-based cleaners for water-soluble lacquers according to chapter 4.
Not allowed are solvents that contain more than 65% of acetone.
This device may only be used for commercial use.
This device is classified as machine category 2, group II, machine type explosion group II B and can be
used in zone 1.
See also device type sign: II 2 G c II B T6
An extended or other use of the device must be coordinated with the manufacturer in advance and
approved by the manufacturer. The device must not be used in continuous operation (for example,
serial production)!
In case of improper use of the cleaning device there is a risk to the health of the user or a third party
as well as a deterioration of the device or other property and assets.
Requirements for the user personnel
The equipment may only be used by qualified personnel who, by virtue of their training, knowledge
or experience, ensure proper handling and are aware of the dangers (for example, by reading the
operating instructions).
Liability
The cleaning device is built according to the state of the art, tested and operationally safe. Liability
for the functioning of the device is in any case attributable to the operator as far as the device is
improperly maintained or repaired by persons who are not authorized by the manufacturer and / or
supplier, or if a handling which does not correspond to the intended use is carried out. The user is
obliged to operate the device only in perfect condition. The manufacturer is liable for errors or
omissions - to the exclusion of further claims - only within the scope of the statutory warranty
obligations. We reserve the right to make technical changes at any time with regard to the
continuous development and improvement of our products. Such changes, mistakes and misprints
do not constitute a claim for damages. Only original spare parts and accessories are to be used. The
manufacturer and / or supplier are not responsible for damage caused by ignoring the instructions in

Cleaning Device d-800 Page 4
equipment and facility engineering
this operating manual. Warranty and liability conditions of the sales and
delivery conditions of the manufacturer and / or supplier are not extended by the above notes.
Operating instructions
The operator of the cleaning device shall draw up an operating instructions in accordance with the
German Occupational Safety and Health (BetrSichV). The operating instructions must be adapted to
the cleaning medium used.
A usage not according to the intended purpose as well as unauthorized modifications
exclude the liability of the manufacturer for any damages resulting from this and
infringes European safety standards.
Read and follow this Instruction manual and the safety instructions carefully before
commissioning!

Cleaning Device d-800 Page 5
equipment and facility engineering
3. Safety requirements
3.1 General security
The device is built according to the state of the art and is safe to operate. However, this does not
mean that the consequences of all operational failures are protected by technical measures. Dangers
can arise from this cleaning device if it is used unqualified or improperly. However, additional
organizational measures have to be taken into account through certain workflows, such as the
removal of residual paint from the gun.
Read and observe the operating instructions for the cleaning unit as well as the safety
instructions before commissioning.
Keep the operating instructions in the vicinity of the device accessible.
The unit may only be operated by trained personnel. Young people under the age of 18 may
be employed only under the supervision of a specialist.
For some users hazard assessment activity restrictions may result, e.g. for persons with
chronic respiratory problems or allergic diseases as well as for becoming or nursing
mothers.
For the operation of the cleaning device, the safety and operating instructions are valid in
all cases; these must be noticed and observed!
The following occupational safety provisions, rules and information (DGUV) have to be followed
while using spray gun and part cleaning systems:
DGUV Provision 1
"Principles and prevention", general rules
DGUV Provision 9
"Safety and health protection warnings at the workplace"
DGUV Rule 109-002
"Safety rules for air pollution control systems for the workplace"
DGUV Information 211-010
"Security by operating instructions"
DGUV Information 213-060
" Avoidance of ignition from electrostatic charges"
DGUV Rule 109-010
" Guidelines for facilities for cleaning parts with solvents"
DGUV Rule 112-189
" Use of protective clothing"
DGUV Rule 112-192
"Use of eye and face protection"
DGUV Rule 112-195
"Use of protective gloves"
BetrSichV
" Ordinance on Industrial Safety"
The source documents (with exception of the " Ordinance on Industrial Safety") can be obtained
from: Carl Heymann Verlag KG, Luxemburger Str. 449, D-50939 Köln, Germany.

Cleaning Device d-800 Page 6
equipment and facility engineering
3.2 Security checks
In order to meet the requirements of the DGUV regulation 109-010, there is the necessity to check
the cleaning device for "safe working condition" before initial start-up as well as annually.
In the appendix of this operating manual, the "Safety test sheet" form is available for proof of regular
safety tests. The form in connection with the tests to be carried out may only be carried out by
qualified persons. Qualified persons are specialists who, due to their training and experience, are
technically able to assess the working condition of a work equipment. For a specific definition of a
qualified person, please refer to the definition of the operational safety ordinance BetrSichV.
3.3 Operational safety
Follow warnings and warning signs!
• Fire, open light and smoking prohibited!
• Open fires and other sources of ignition (eg grinders or welding points) are not allowed within a
radius of 5 meters around the device. This applies e.g. also for lighting and fans as well as the
associated electrical components.
• In all cases, the local safety and operating instructions are valid for the operation of the device.
Accident prevention regulations must be followed and observed.
The device may only be operated if the integrated suction device (Venturi system with
flexible exhaust hose) is connected and the evolved (solvent) fumes are safely discharged
to the outside in the free air stream in order to avoid fire, explosion and health hazards.
Should the distance to be bridged exceed the length of the supplied exhaust air hose or should local
requirements exclude the previously described exhaust air guidance, we recommend the inclusion of
a specialist company for ventilation construction to ensure the correct operation of the device.
• Compliance with workplace exposure limits (AGW) according to safety data sheets must be
documented.
• The limit values of the TA-air and their adherence must be observed.
• In the event of a fire, immediately interrupt the compressed air supply and close the cover of the
device.

Cleaning Device d-800 Page 7
equipment and facility engineering
• If the device is not used, the device cover must always be closed for safety reasons.
Before commissioning, the earthing must be ensured via a sufficiently dimensioned earth
cable (potential equalization)! The connection must be made by a specialist.
• The user has to ensure that nobody is in the danger area of the cleaning device.
• Use only permitted solvents / cleaning media (see chapter 4). These must be free of
Halogenated hydrocarbons (CKW, CFC, TRI, PER, etc.).
• If water (e.g. with additives) is used as a cleaning medium, this must not be discharged into the
sewer system.
• Take into account that the chosen cleaning medium is suitable for use and does not attack surface.
Suitability shall be ensured by the operator in preliminary tests. The manufacturer and / or supplier
does not assume any liability for damages caused by these tests.
• The safety data sheet of the cleaning medium must be observed.
• Use personal protective and chemical resistant protective equipment, e.g. face protection,
protective gloves, protective aprons etc.
• Ensure that the clothing (especially the footwear) is adequately conductive
• Do not place the protective equipment on the device.
• If clothing has been wetted with solvent / cleaning medium, do not smoke in this area. Put off the
contaminated clothing immediately. Risk of skin irritation, allergies, etc.
• Persons wearing moistened clothing must not be exposed to sources of ignition (e.g. welding). Risk
of fire!
• Do not fill any additional cleaning media into the unit, as this may lead to a overflow of the barrel.
• Immediately collect spilled solvent (s) with suitable binders (blinding mica, kieselguhr, etc.) and
dispose it of in accordance with regulations. The water resources law must be satisfied.
• Clean your hands before eating any food or drink. Danger of poisoning!
• Avoid inhalation of fumes and contact with the solvent / cleaning medium.
• Do not add any other liquids to the cleaning medium, such as kerosene, gasoline, chlorinated
hydrocarbons, acids, alkalis.
• When changing the cleaning medium, all valid regulations (e.g. wastewater-regulations) must be
observed!

Cleaning Device d-800 Page 8
equipment and facility engineering
3.4 Hazards from pneumatic energy
Only specialists with special knowledge and experience may work on pneumatic equipment. When
working on pneumatic aggregates or elements, these must be made pressureless beforehand in
order to prevent injury!
Prevent disconnected not pressurized compressed air supply lines from restarting. If the systems
leaks, disconnect it from air supply and then tighten the screwed connections.
3.5 Excitation for operating instructions
Operating instructions are regulations that a company creates for safe operation. These are binding
instructions issued by the entrepreneur within the framework of his management right. The
employees are obligated to follow these instructions.
The general obligation of the entrepreneur to create and publish operating instructions is laid down
in the Occupational Safety and Health Ordinance (BetrSichV), the water resources law (WHG) and,
where applicable, the Ordinance on Hazardous Substances (GefStoffV). The present operating
instructions are therefore to be complemented by national regulations on accident prevention (UVV)
and environmental protection.
Give information to the employee about:
• the dangers involving the handling of contaminated parts and the solvents used, the necessary
protective measures and behavior, including instructions in case of danger and first aid.
• Type and scope of periodic inspection for safe working condition of the device
• Environmental Protection
• Safe handling of the pneumatic system
• By means of instructions and controls, the user has to ensure cleanliness and clarity at the
workplace of the device.
• The responsibility for operation must be clearly regulated by the user and must be complied by all
persons, so that no unclear competences occur under the safety aspect.
• The operator has to undertake to operate the cleaning device only in perfect condition and to
immediately notify its supervisor of any changes that affect safety and environmental protection.
• Observe all warnings and warning signs.
• The user has to ensure that no unauthorized persons are at the cleaning device.
It is prohibited to open the pump case in B-TEC cleaning devices!
The manufacturer is not liable for any damage and/or secondary/following damage caused
by opening the pump case on purpose or negligent opening.
If you got any problems with your pump device, please contact your distributor or the B-
TEC support.

Cleaning Device d-800 Page 9
equipment and facility engineering
4. Approved Cleaning Agents
Only use solvents / cleaning media that meet the following specifications:
Highly flammable liquids, hazard symbol „F“ / R 11 flashpoint < 21°C such as lacquer solvents,
but excluding all "extremely flammable" fluids with a flash point under 21°C.
GHS/CLP H 225 flashpoint < 23°C, boiling point > 35°C.
Flammable liquids, hazard symbol - / R 10, flashpoint 21 –55°C.
GHS/CLP H 226 flashpoint 23 –60°C.
Non-flammable, aqueous cleaning agents (neutral or slightly alkaline pH) such as distilled
water for water-soluble varnishes and paints.
The machine d-800 is classified as machine category 2, group II,
machine type explosion group II B and can be used in zone 1.
See also machine rating plate: II 2 G c II B T6
Acids are not permitted. Paint strippers or other additives (e.g. brake cleaners etc.)
may must not be used in the washing unit.
Safety data sheets relevant to the products supplied should always be available on the
premises. These will contain the information about the cleaning agents that you are
using.
Never alternate the use of solvents and cleaning fluids (for water-based paints) in the
same machine as this will damage it and void the warranty. Follow the manufacturer’s
instructions at all times. Alternating the two types of cleaning agents can cause gas
build up and explosions!
When changing from solvents to cleaning fluids for water-based paints (or vice-versa)
the paint gun washer must be completely cleaned of paint, water and fluid residues.
Recommendation to reduce solvent consumption:
If the unit shall be connected to a continuously running exhaust when using solvent,
we recommend the pneumatic exhaust damper to reduce solvent consumption.
See B-TEC, catalog no.: 10000348 / ATEX version.

Cleaning Device d-800 Page 10
equipment and facility engineering
5. Technical Description of the Cleaner
The universal washer "d-800" is produced for automatically cleaning spray paint guns. The automatic
wash cycle is activated by a timer. In addition, there is a brush and a fresh solvent jet in the wash
enclosure for cleaning objects or spray guns manually.
All models have a strong exhaust system that switches on and off automatically as soon as the hatch
is opened or closed. All models are operated exclusively by pneumatic parts.
5.1 Technical Information
Compressed-air connection
Operating pressure:
max. 6 bar
Acoustic emission
Average level of acoustic emission:
76 dB(A)
Total exhaust air flow rate:
At 0,2 m/s
432 m³/h
Max. container size per side under the cleaning device:
Container size max. 60 l
Container size max. 30 l
1 pc. circulating solvent
1 pc. clean solvent
- Technical changes and errors reserved. All pictures similar -

Cleaning Device d-800 Page 11
equipment and facility engineering
5.2 Details
Cup holder
Middle-jet
Jet gun
Injector
Brush with hose
Timer
Button
clear rinse
Dip-switch
fresh solvent jet
Dip-switch brush
Door for
automatic
cleaning room
Lid holder
Exhaust opening
Fresh solvent jet
Compressed air
hose for flushing
spray gun
Waste air hose

Cleaning Device d-800 Page 12
equipment and facility engineering
Flap
Clamp for spray
gun
Circulating solvent
(Grey and black
hoses)
Clean solvent
(transparent hose)

Cleaning Device d-800 Page 13
equipment and facility engineering
5.3 Part Names
A-1
-
Pump brush
P
-
Injector
A-2
-
Pump rinse
Q
-
Chromed hand grip
A-3
-
Pump jet automatic
R
-
Two ball snapper
B
-
Dip-switch
S
-
Discharge hose
D
-
Role valve with connections
T-1
-
Intake-strainer
E
-
Role valve
T-2
-
Strainer connecting clamp
G
-
Rinse button
U-1
-
Transparent intake hose clean solvent
H
-
Fresh solvent jet
U-2
-
Grey intake hose circulating solvent
K
-
Timer
V
-
Brush with hose
L
-
Connecting plug compressed air
W
-
Compressed air hose for flushing spray
M
-
Middle-jet
gun
N
-
Cup holder
X
-
Grounding cable
O
-
Lid holder
Y
-
Jet gun with short tube
- Spare parts ordering numbers on page 15 -
A-3
A-2
A-1
B
D
R
E
V
G
H
L
M
O
N
P
Q
S
T-2
T-1
U-1
U-2
W
X
Y
K
S

Cleaning Device d-800 Page 14
equipment and facility engineering
5.4 Pneumatic Plan
A-3
C
E
A-1
K-5
A-2
I
G
C
C
K-4
K-3
K-1
B
B
H
C
F
C
J
D
I
Air-Connection
K-2
E
Y

Cleaning Device d-800 Page 15
equipment and facility engineering
5.5 Spare Parts Ordering Numbers
A-1/3
-
Pump 1/4"
10000554
A
-
Clean rinse pump 1/8", with connctors
10000565
B
-
Dip-switch
10000589
C
-
Throttle valve
10000582
D
-
Roller valve, G1/8", for activation
10000620
E
-
Roller valve 3/2 ways M5, for timer, lifts, ud-
800 flap
10000579
F
-
Injector
10000415
G
-
Push button for automatic clean rinse,
completely assembled incl. Connectors
10000414
H
-
Fresh dilution jet
10000419
I
-
T- Connector
10000845
J
-
Cross connector
10000893
K-1
-
Timer, 6 min
10000444
K-2
-
Bracket
10000327
K-3
-
Switch-plate
10000328
K-4
-
Scale for timer
10000445
K-5
-
Timer button
10000443
L
-
Air connection NW 7.2
10000908
M
-
Middle jet
10000420
N
-
Cup holder
10000418
O
-
Lid holder
10000439
P
-
Injector
10000429
Q
-
Chromed hand grip
10000461
R
-
Two ball snapper
10000467
S
-
Corrugated hose 25 x 28, black
10000658
T-1
-
Filter, stainless steel
10000473
T-2
-
Strainer connecting clamp
10000663
U-1
-
Corrugated hose 13 x 10, transparent
10000656
U-2
-
Corrugated hose 13 x 10, grey
10000655
V
-
Brush with hose
10000417
W
-
Corrugated hose 15 x 12, black
10000657
X
-
Grounding cable
10000391
Y
-
Jet gun with short tube
10000446

Cleaning Device d-800 Page 16
equipment and facility engineering
6. Requirements for the Installation Site
This device is classified as machine category 2, group II, machine type explosion group II B and can be
used in zone 1.
See also device type sign: II 2 G c II B T6
Safety regulations for the installation site of B-TEC devices
The risk zoning around the cleaning machine and the possible creation of an explosion protection
document is, in accordance with legal requirements, the operator´s obligation, because this division
is inter alia depending on the solvents used and various conditions such as the ventilation. However,
at this point the operator should be supported with general advice to comply with the obligation.
Helpful advice can also be read at DGUV rule 113‐001, DGUV rule 109‐010 and also DIN EN 12921‐1
and ‐3.
For example, in many cases the classification of the zones looks like this:
Zone 1 => The interior of the machine
Zone 2 => In periphery of 1,0 –1,5 m
Identify the different zones with appropriate warning and prohibition signs. Marks at the floor can be
helpful. In the area surrounding the unit, open flames and other ignition sources (e.g. welding or
grinding equipment places) are not allowed. Similarly, smoking is prohibited. Temporary work with
ignition must be approved in writing and appropriate additional safety precautions must be adhered
to (remove all combustible materials, classification of a fire station,...).
Foundation, building
Dry and protected from frost.
Very well ventilated and means of ducting the exhaust fumes to an approved area.
Follow the safety instructions about the site.
Maintain the ambient temperatures (5° - 35°C / 41°F - 95°F) and do not expose the machine
to direct sunlight, as this carries a risk of overheating.
Space requirement for operation and maintenance
The device can be placed or be mounted on a wall. In front of the device, there should be space of
1,5m.
Horizontal and industrial floor
Conductive industrial floor (max. conductive resistance 108Ohm).
Follow the safety instructions according to the zone designations (chapter 6.).

Cleaning Device d-800 Page 17
equipment and facility engineering
7. Transport and Installation
The machine is delivered in carton.
Take the machine out of the carton and bring it to the installation site.
7.1 Connecting Exhaust
The waste air hose must lead outside. Place the waste
air hose minimum one meter lengthwise for optimal
work of the exhaust system. Stretch the hose as far as
possible in order to avoid a reduced flow cross-
section. This is necessary in order to ensure that the
exhaust system works well. One has to ensure that
the fumes are not led into areas where people are
likely to be. The waste air has to be exhausted safely.
This means that it has not to be fed into chimneys
serving furnaces or fireplaces and not into exhaust
channels of spraying and drying cabinets.
You can adjust the exhaust air flow at the throttles as needed for the length of the waste air hose.
Waste air hose
Attention! Only use original B-TEC
waste air hoses. Risk of fire if
other hoses are used.
Table of contents
Popular Other manuals by other brands

SAFERA
SAFERA Airis Stove Guard user manual
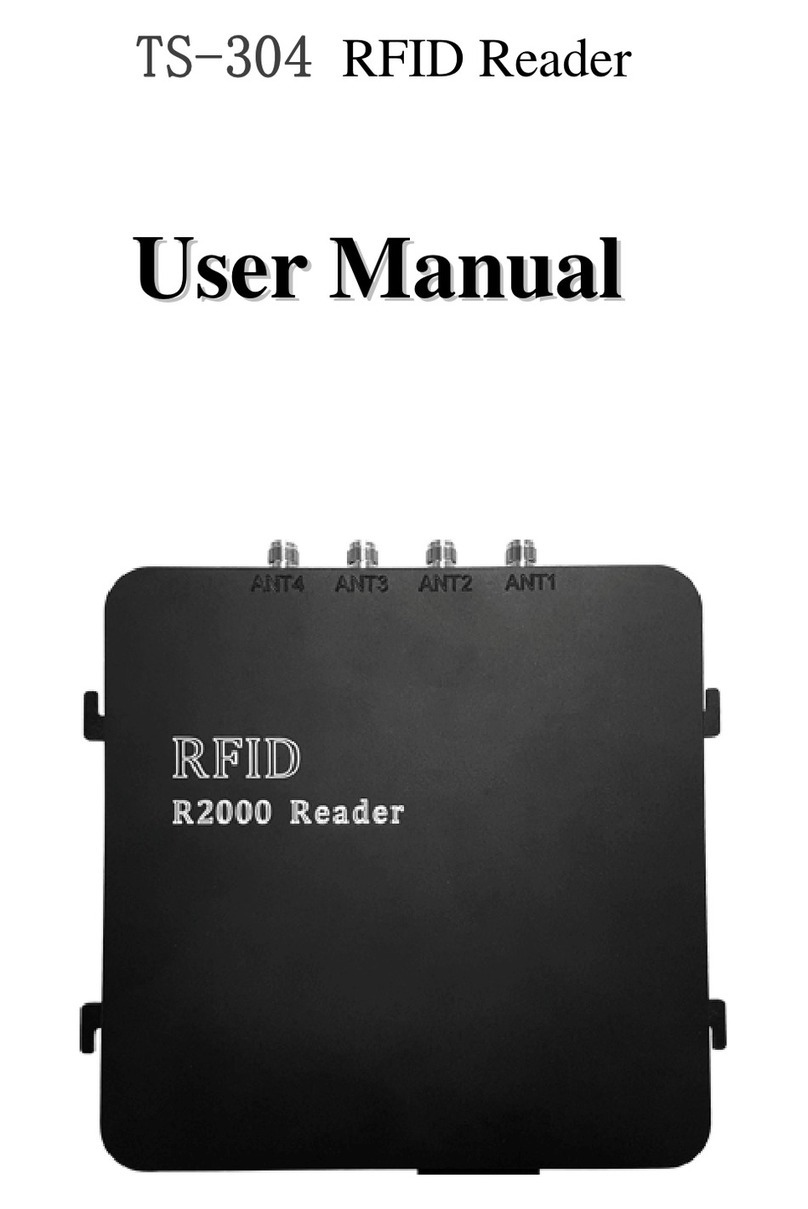
TASEI
TASEI TS-304 user manual
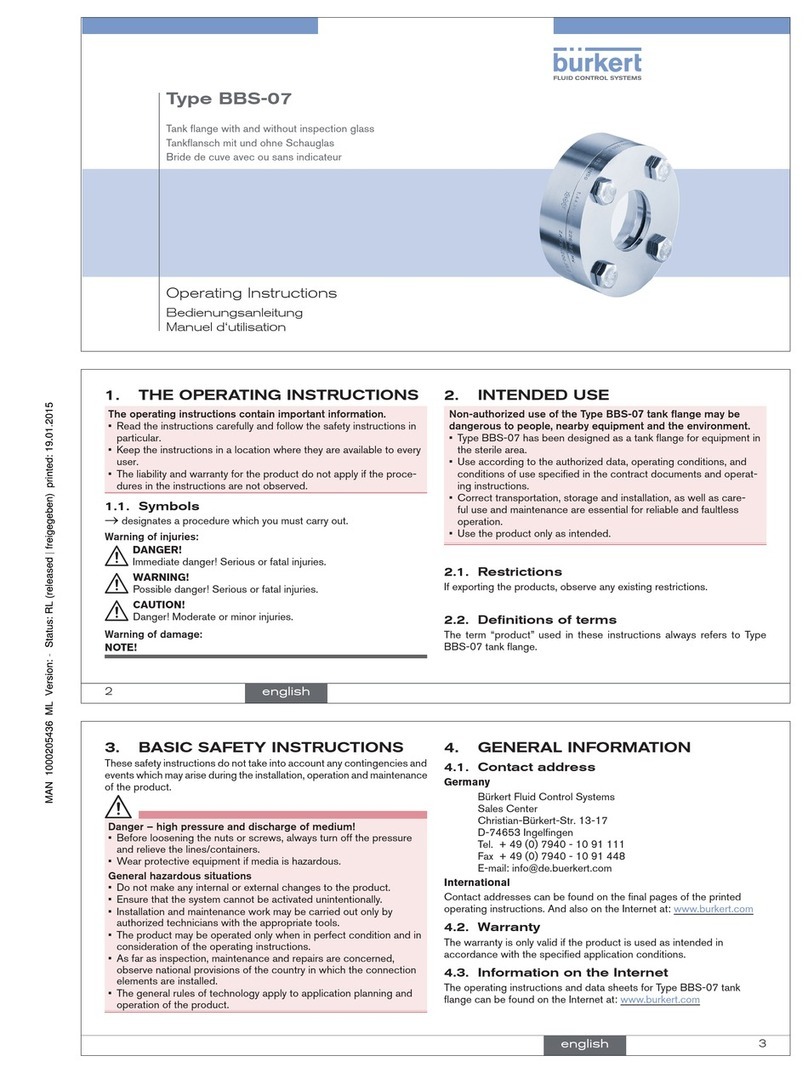
Burkert
Burkert BBS-07 operating instructions
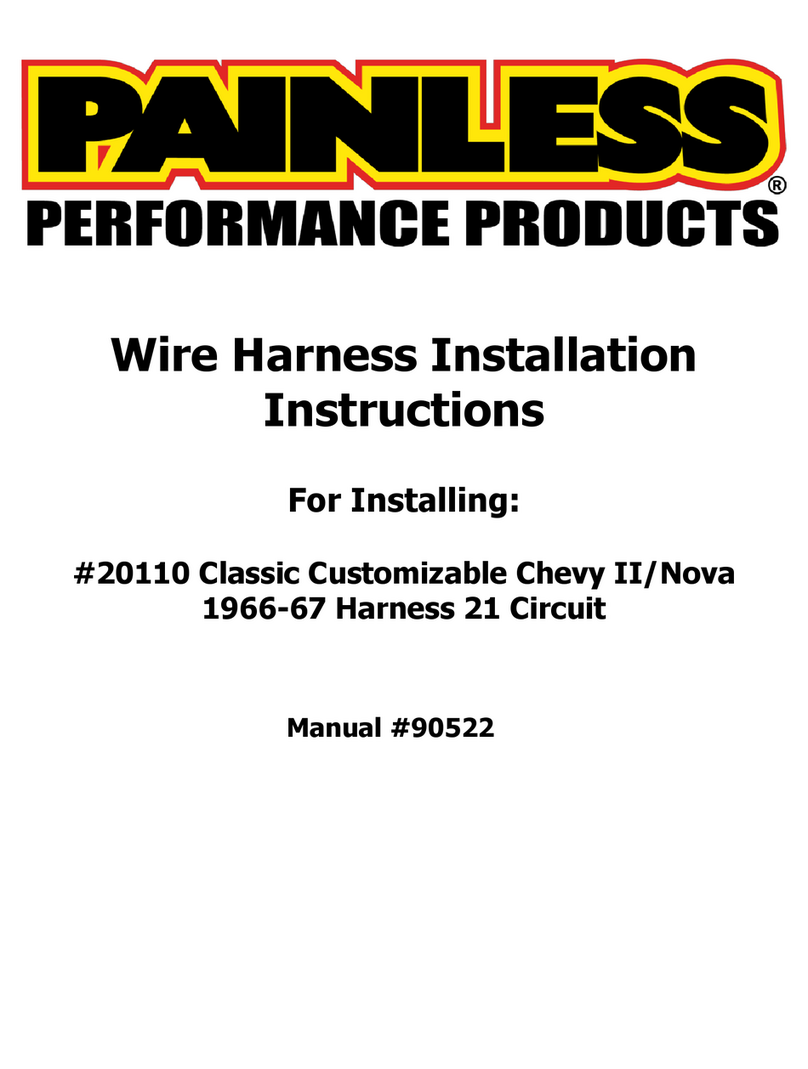
Painless Performance Products
Painless Performance Products 20110 installation instructions
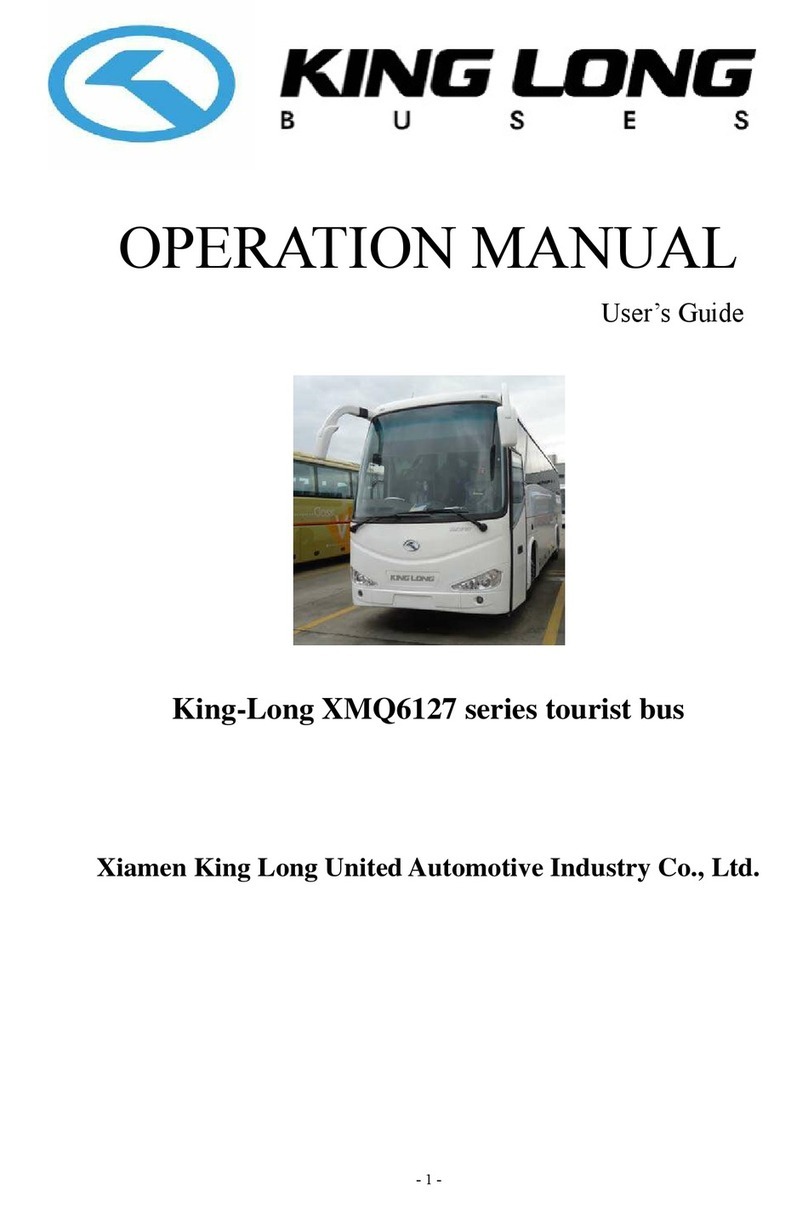
King Long
King Long XMQ6127 series operating manual
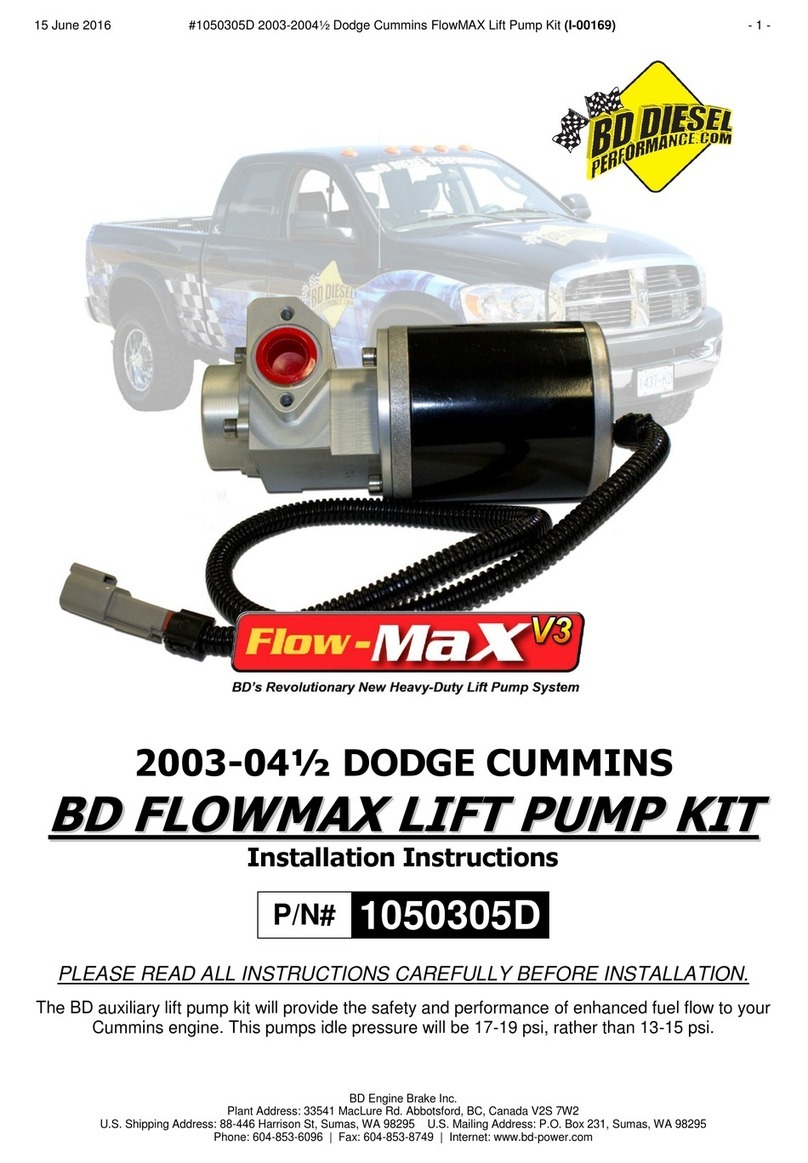
BD Diesel Performance
BD Diesel Performance FlowMAX Lift Pump V3 installation instructions