Badger Basket SILENT I User manual

BADGER
Owner's
Manual
for
Silent
I
and
Silent
II
Compressors
SILENT
II

INTRODUCTION
Congratulations!
When
you
purchased
your
Badger
compressor,
you
guaranteed
yourself
a
well
built
and
highly
efficient
machine
which,
used
properly,
will
perform
every
task
you
assign
it,
however
demanding.
This
compressor
meets
the
high
quality
and
performance
standards
of
all
Badger
equipment.
It
is
designed
to
be
used
with
any
air-brush.
The
air
outlet
is
1/4"
pipe
and
will
conveniently
adapt
to
almost
any
air-hose.
This
compressor
has
met
or
exceeded
our
highest
testing
procedures.
We
suggest
that
for
easy
and
correct
operational
assembly,
mainte¬
nance,
and
spare
parts,
you
follow
the
instructions
given
in
this
pamphlet.
READ
THE
ENTIRE
MANUAL
BEFORE
YOU
OPERATE
THE
COMPRESSOR.
FAILURE
TO
FOLLOW
DIRECTIONS
MAY
DAMAGE
UNIT
AND
VOID
THE
WARRANTY.
BE
SURE
TO
FILL
OUT
THE
WARRANTY
CARD
AND
RETURN
TO
THE
MANUFACTURER
WITHIN
30
DAYS
OF
THE
DATE
OF
THE
ORIGINAL
RETAIL
PURCHASE!
DO
NOT
ATTEMPT
TO
OPERATE
THIS
COMPRESSOR
WITHOUT
FIRST
FILLING
WITH
OIL!
FILL
THE
OIL
TO
THE
CENTER
BETWEEN
MAX.
AND
MIN.
ON
OIL
LEVEL
SIGHT
GAUGE.
DO
NOT
OVERFILL!
TECHNICAL
FEATURES
The
most
notable
features
of
your
Badger
unit
are
its
silent
running,
reliability,
small
size,
reasonable
weight,
and
ease
of
use.
SILENT
I
The
compressor
used
on
the
unit
is
the
product
of
advanced
design
applied
to
modern
technology.
It
is,
in
fact,
a
compressor
with
oil
bath
lubrication,
enclosed
in
a
metal
casing
to
reduce
noise
to
a
minimum.
The
Silent
I
electric
motor
develops
1/3
HP
The
Silent
II
motor
develops
1/2
HP
Both
compressor’s
electrical
power
input
is
115V
at
60
Hz
single
phase.
Though
compact
in
size
and
weight,
the
Silent
I
&
II
have
all
the
features
of
much
larger
compressors...
pressure
gauge,
filter,
pressure
regulator,
automatic
cut-off
and
safety
valve.
The
Silent
I
I
gallon
tank
allows
you
to
maintain
a
reserve
air
supply
at
a
maximum
of
85
PSI.
The
Silent
II
has
a
1.3
gallon
tank
and
allows
you
to
maintain
a
reserve
air
supply
at
a
maximum
of
100
PSI.
The
tank
also
prevents
pulsating
sprays
during
operation
and
allows
the
com¬
pressor
to
rest
for
long
periods
even
under
normal
working
conditions.
Your
compressor
is
equipped
with
a
standard
filter
regulator
which
removes
all
dust
particles
over
5/1000
mm
in
size
from
the
com¬
pressed
air
stream.
MACHINE
SET
UP
Once
you
have
unpacked
your
compressor,
check
it
for
visible
signs
of
shipping
damage.
NOTE:
your
unit
is
shipped
without
oil.
This
is
to
prevent
oil
from
getting
into
the
compression
chamber
and
thus
reducing
future
operating
efficiency.
It
is
not
uncommon
to
have
units
turned
upside
down
during
shipping.
SILENT
II

OIL
FILLING
PROCEDURE
A
container
of
oil
is
packed
with
your
unit.
Remove
plug
from
inside
the
mouth
of
the
oil
container
and
attach
the
filler
spout
to
the
oil
container.
Cut
end
of
filler
spout.
Open
drain
plug
and
remove
air-
intake
filter
cap.
Insert
the
filler
spout
into
the
tube
marked
oil
(fig.
I).
Fill
to
the
middle
level
(between
MAX.
and
MIN.
on
oil
level
sight
glass,
fig
2)
on
the
side
of
your
Silent
I.
DO
NOT
FILL
ABOVE
THE
MIDDLE
LEVEL.
THIS
WILL
DAMAGE
YOUR
UNIT
You
will
need
about
12
fl.
oz.
(.35
Itr.)
to
fill.
Keep
the
remaining
oil
to
top
off
the
tank
later
Close
the
drain
plug
(fig.
3)
and
replace
air
intake
filter
cap.
Do
not
operate
the
Silent
I
without
the
air
intake
filter
in
place.
USE
ONLY
THE
OIL
SUPPLIED
AND
SOLD
BY
THE
MANUFAC¬
TURER.
FAILURE
TO
DO
SO
WILL
VOID
YOUR
WARRANTY
(fig.
3)
Drain
plug
OIL
FILLING
PROCEDURE
Inside
the
shipping
carton
you
will
find
2
oil
containers
Remove
plug
from
inside
the
mouth
of
the
larger
oil
container
and
attach
the
filler
spout
to
the
oil
container.
Cut
end
of
filler
spout.
Remove
both
caps
(shipping
oil
cap
and
breather
cap).
Insert
the
filler
spout
into
the
tube
marked
oil
(fig.
1).
Fill
to
the
middle
level
(between
MAX.
and
MIN
on
oil
level
sight
glass)
on
the
side
of
the
motor.
DO
NOT
FILL
ABOVE
THE
MIDDLE
LEVEL.
THIS
WILL
DAMAGE
YOUR
UNIT
Keep
the
remaining
oil
to
top
off
the
oil
level
later
Replace
the
oil
breather
cap.
At
the
tube
where
you
inserted
the
oil,
replace
the
shipping
cap
with
the
air
intake
filter
cap
found
in
the
plastic
bag.
This
filter
will
prevent
foreign
matter
from
entering
the
compression
chamber
Do
not
operate
the
compressor
without
the
air
intake
filter
in
place
Save
the
shipping
oil
cap
for
use
when
transporting
for
short
distances
when
filled
with
oil.
NEVER
TURN
COMPRESSOR
ON
ITS
SIDE
WHEN
IT
CONTAINS
OIL.
USE
ONLY
THE
OIL
SUPPLIED
AND
SOLD
BY
THE
MANUFAC¬
TURER.
FAILURE
TO
DO
SO
WILL
VOID
YOUR
WARRANTY!
To
prevent
oil
from
spilling
out,
never
turn
your
unit
upside
down
or
position
it
on
a
sharp
incline.
Always
drain
the
oil
before
transporting
the
unit.
If
you
transport
the
unit
with
oil
in
it,
oil
may
enter
the
com¬
pression
chamber
and
cause
dam¬
age.
If
the
unit
is
accidentally
tipped
over,
use
the
following
pro¬
cedure
to
remove
oil
and
prevent
damage.
Let
the
unit
set
for
5
to
10
minutes
before
attempting
to
oper¬
ate.
Remove
the
hose
assembly
where
it
attaches
to
the
motor
(see
illustration
of
parts
No.
26
&
27
on
Silent
I
or
parts
No.
36
&
37
on
Silent
II)
and
run
the
unit
in
15
minute
cycles
until
no
more
oil
comes
out.
Let
the
unit
cool
between
cycles.
(fig.
1)
Filler
tube

SILENT
I
Start
Up
Procedure
Once
you
have
completed
these
operations,
the
compressor
is
ready
for
operation.
When
you
activate
the
on/off
switch:
(fig.
4)
1
T
h
e
compressor
will
turn
on
and
begin
to
pump
air
into
the
tank.
(If
this
does
not
occur,
check
that
you
do
not
have
a
faulty
outlet,
blown
fuse
or
tripped
circuit
breaker.)
(fig.
4)
On/off
switch
2
The
Silent
I
will
operate
for
about
60
seconds,
until
the
air
pressure
in
the
tank
reaches
about
85
P.S.I.
When
this
pressure
is
achieved,
the
compressor
will
automatically
stop.
3
After
the
initial
start-up,
check
the
oil
level
sight
gauge.
Motor
operation
may
have
driven
trapped
air
out
of
the
unit,
and
slight
topping
off
may
be
necessary
to
bring
oil
back
to
proper
level
(between
Max.
and
Min.).
SILENT
II
Start
Up
Procedure
Once
you
have
completed
the
oil
filling
procedures,
the
compressor
is
ready
for
operation.
When
you
turn
on
the
on/off
switch
located
on
the
upper
front
section
of
the
compressor
(fig.
2)
the
following
should
take
place.
1
T
h
e
motor
will
go
on.
The
compressor
will
begin
to
pump
air
into
the
tank.
(If
the
motor
does
not
work,
check
that
you
do
not
have
a
faulty
outlet,
blown
fuse
or
tripped
circuit
breaker)
(fig.
2)
On/off
switch
2
The
Silent
II
will
operate
for
about
2
minutes,
until
the
air
pressure
in
the
tank
reaches
about
120
P.S.I.
When
this
pressure
is
achieved,
the
compressor
will
automatically
stop.
3
After
the
initial
start-up,
check
the
oil
level
sight
gauge.
Motor
operation
may
have
driven
trapped
air
out
of
the
unit,
and
slight
topping
off
may
be
necessary
to
bring
oil
to
proper
level.
The
compressor
operates
on
a
115V-60
Hz
three
pronged
plug
electrical
power
supply.
Make
sure
that
you
use
a
grounded
electrical
outlet
for
the
unit.
If
the
ground
is
missing,
short
circuit
could
cause
electrical
discharge
in
the
compressor
itself.

The
automatic
on-off
pressure
switch
on
your
Silent
I
has
been
calibrated
to
stop
when
the
pressure
of
the
air
in
the
tank
reaches
approximately
85
P.S.I.
It
will
automatically
turn
on
again
when
the
pressure
falls
below
approximately
60
RS.I.
Should
the
pressure
valve
fail
to
operate,
your
Silent
I
is
equipped
with
a
safety
valve
which
opens
automatically
should
the
pressure
on
the
tank
exceed
115
RS.I.
DO
NOT
REMOVE
OR
REPAIR
THIS
VALVE!
NEVER
USE
YOUR
COMPRESSOR
ON
AN
UNEVEN
SURFACEI
I
The
automatic
on-off
pressure
switch
on
your
Silent
II
has
been
calibrated
to
stop
when
the
pressure
of
the
air
in
the
tank
reaches
approximately
120
P.S.I.
It
will
automatically
turn
on
again
when
the
pressure
falls
below
approximately
80
RS.I.
Should
the
pressure
valve
fail
to
operate,
your
Silent
II
is
equipped
with
a
safety
valve
which
opens
automatically
should
the
pressure
on
the
tank
exceed
145
PS.I.
DO
NOT
REMOVE
OR
REPAIR
THIS
VALVE!
NEVER
USE
YOUR
COMPRESSOR
ON
AN
UNEVEN
SURFACE!
REGULATOR
THIS
PROCEDURE
REFERS
TO
BOTH
THE
SILENT
I
AND
SILENT
II.
Once
the
compressor
has
completed
an
operational
cycle,
the
tank
is
under
pressure.
Install
the
1/4"
male
pipe
thread
fitting
to
the
in-line
oil
filter
opening.
You
may
want
to
put
some
sealing
material,
i.e.
teflon
tape,
on
the
threads
to
prevent
any
air
leakage.
After
installing
the
fitting,
attach
your
air
hose
and
air-brush
to
this
fitting,
again
sealing
the
threads.
The
filter
regulator
has
been
set
to
0
PSI
value
by
the
manufacturer.
The
filter
regulator
can
now
be
set
to
the
pressure
required.
To
do
this
just
turn
the
ring
on
the
filter-regulator
clockwise
until
you
can
read
the
pressure
you
want
on
the
gauge.
You
are
now
ready
to
use
your
compressor.
SILENT
I
&
II
IN-LINE
OIL
FILTER
\
1/4
to
1/4
1/4
PIPE
THREAD
FITTING
MANUAL
DRAIN
VALVE
Your
Silent
I
or
II
is
furnished
with
a
99.9%
effective
in-line
oil
filter
to
assure
that
no
oil
enters
the
air-stream.
Every
time
the
oil
level
is
checked,
inspect
the
oil
filter
for
oil
build-up.
Remove
accumulated
oil
by
pushing
up
on
the
manual
drain
valve,
and
letting
the
oil
drain.
Do
not
reuse
this
oil
since
it
has
been
contaminated.

PROCEDURES
FOR
ATTACHING
SILENT
I
IN-LINE
OIL
FILTER
Silent
I
Compressor
tour
Silent
I.
is
furnished
with
an
in-line
oil
filter
to
assure
that
no
oil
enters
the
air-stream.
After
the
compressor
is
filled
with
oil
and
before
it
is
pressurized,
attach
the
oil
filter.
To
insure
a
tight
fit.
put
teflon
tape
on
the
threads
of
all
the
finings,
regulator
and
oil
removal
filter.
,
*
Eveiy
time
the
oil
level
is
checked,
inspect
the
oil
filter
for
oil
build-up.
Remove
;
accumulated
oil
by
pushing
up
on
the
'
,
manual
drain
valve,
and
letting
the
oil
drain.
Do
not
re-use
this
oil
since
it
has
been
contaminated.
NOW
STANDARD
EQUIPMENT
CN
380-1
:
%
.
t
%
*
-

MAINTENANCE
FOR
THE
SILENT
I
&
II
CONDENSATION
Remove
the
condensate
that
has
collected
in
the
tank.
Under
normal
operating
conditions,
once
a
week
is
sufficient.
If
the
compressor
is
used
constantly,
in
areas
of
high
humidity,
more
frequent
removal
may
be
required.
To
empty
the
tank,
put
it
under
pressure,
remove
the
electrical
plug
from
the
outlet,
take
the
compressor
to
an
area
where
water
will
not
damage
the
floor
covering.
Tip
the
compressor
slightly
forward,
and
open
the
drain
plug
on
the
bottom
of
the
air
storage
tank.
After
the
tank
is
completely
drained,
replace
the
drain
plug,
reconnect
the
electrical
supply,
and
repressurize
the
tank.
Air-hoses
and
other
accessories
should
be
drained
on
a
regular
basis.
OIL
CHANGE
Change
the
oil
after
every
100
hours
of
running
operation
to
guarantee
adequate
lubrication
and
perfect
operating
efficiency.
To
change
the
oil,
remove
the
air
intake
filter
and
tip
the
unit
so
that
the
air
intake
tube
is
facing
down.
Keep
the
compressor
in
this
position
until
all
the
oil
has
drained
out.
Refer
to
the
procedure
for
filling
your
unit
with
oil.
Add
new
oil
to
the
required
level
(fill
to
middle
level
between
MAX.
and
MIN.).
Begin
operation.
USE
BADGER
REPLACEMENT
OIL
ONLY!
OIL
LEVEL
CHECK
During
the
first
weeks
of
operation,
check
the
oil
level
daily.
After
a
break-in
period,
check
the
oil
level
weekly.
Visually
check
the
oil
level
with
the
sight
glass.
Add
oil
when
the
level
falls
below
minimum.
Only
use
Badger
Silent
Ones
replacement
oil
#50-052.
FILTER-REGULATOR
Clean
any
residue
in
the
filter
cup
after
each
working
day.
Push
upward
on
the
manual
drain
located
on
the
bottom
of
the
filter
bowl
It
may
be
easier
to
complete
this
operation
when
the
tank
is
pressurized.
ELECTRICAL
POWER
CABLE
Periodically
check
the
condition
of
the
electrical
power
cable.
If
you
have
to
replace
the
electrical
cord,
make
sure
that
you
use
a
grounded
three
prong
plug
and
three
wire
cord.
The
cord
should
be
identified
with
the
following
colors:
Black-Live
White-Neutral
Green-Ground
If
an
extension
cord
is
necessary,
it
should
be
kept
as
short
as
possible.
An
undersized
extension
cord
will
reduce
operating
voltage
and
cause
power
loss
to
your
compressor.
The
following
wire
gauge
chart
has
been
specified
for
different
lengths
when
an
extension
cord
is
needed.
Cord
length
Min.
wire
size
Note.-
the
smaller
the
less
than
25
ft.
16
gauge
number,
the
heavier
25
to
50
ft.
14
the
cord
50
to
100
ft.
12
NEVER
USE
A
TWO
PRONG
PLUG
OR
TWO
WIRE
REPLACEMENT
CORD.
CASING
SCREWS
Periodically
check
the
casing
screws.
Tighten
if
necessary.
AIR
INTAKE
FILTER
Every
month,
remove
the
air
intake
filter
and
check
that
the
screening
is
not
blocked.
If
it
is,
place
the
screen
in
a
pan
of
warm
soapy
water
and
clean.
Flush
with
clean
water,
dry
completely
and
replace.
If
you
do
an
excessive
amount
of
air-brushing,
clean
the
filter
every
week.
UNDER
NO
CIRCUMSTANCES
ATTEMPT
TO
FIX
THE
INTERNAL
PARTS
OF
YOUR
COMPRESSOR
BY
REMOVING
THE
DOME
SHELL
REMOVING
THE
DOME
SHELL
WILL
VOID
YOUR
WARRANTY
AND
RESULT
IN
ADDITIONAL
CHARGES
FOR
NECESSARY
REPAIRS

HELPFUL
HINTS
1
Your
Silent
I
&
II
is
equipped
with
a
motor
thermal
overload
pro¬
tective
device
which
automatically
shuts
the
unit
off
in
the
event
of
power
overload
or
if
the
temperature
of
the
compressor
reaches
212°F
(JOO°C).
If
this
should
happen
during
normal
operations,
turn
the
on/off
switch
to
the
off
position
and
wait
until
the
unit
has
cooled
down
(about
30
minutes).
The
motor
thermal
overload
device
will
automatically
reset
when
the
temperature
reaches
between
130-
150°F
(60-70°C).
Switch
the
compressor
on
and
check
that
every¬
thing
is
functioning
correctly.
2
Always
use
the
compressor
on
a
flat
surface.
3
Never
check
or
repair
the
compressor
when
it
is
plugged
into
a
power
source.
4
Keep
the
unit
free
from
dust
and
dirt.
5
Use
only
those
replacement
parts
recommended
by
the
manufacturer.
6
Use
only
Badger
Silent
Ones
replacement
oil,
#50-052
Do
not
substitute
or
mix
the
oil
in
the
compressor
with
oil
other
than
that
recommended
by
the
manufacturer.
TO
DO
SO
WILL
VOID
THE
WARRANTYI
7
Do
not
expose
the
compressor
to
water
or
excessive
humidity
For
any
shipment,
oil
must
be
drained
and
filter
spout
replaced
with
oil
cap.
If
unit
is
sent
to
manufacturer
while
it
contains
oil,
the
warranty
may
be
voided,
and
a
clean-up
charge
will
be
assessed.
SERVICE
CHECK
LIST
PROBLEM
POSSIBLE
CAUSE
SOLUTION
1
.
Compressor
will
not
run.
No
Power.
Thermal
overload
has
tipped.
Check
outlet
voltage,
fuse
and
circuit
breakers.
Wait
10
minutes
and
try
starting
again.
See
the
"Electrical"
section
of
your
manual.
Bad
cord
connection.
Check
cord
connection
for
any
visual
damage.
2.
Compressor
runs
but
will
not
supply
air.
Air
filter
cap
is
closed.
Air
filter
is
dirty
and
clogged.
Remove
protective
cap
on
filter
Remove
and
clean
air
filter
in
mild
soap
solution.
3.
Air
leak.
Leak
in
safety
relief
valve.
Safety
relief
valve
is
sticking—must
replace
Loose
fittings
and
hose
connections.
Tighten
fittings
and
check
hose
connections.
4.
Rattling
noise
during
operation.
Compressor
motor
is
touching
the
compressor
shell.
Lack
of
oil
Operate
on
a
flat
or
level
surface.
Periodic
checks
of
the
oil
level
sight
glass.
Keep
oil
level
no
lower
than
the
“Minimum"
marking
in
compressor.
5.
Milky
oil
in
compressor.
Oil
has
been
contaminated
with
moisture
or
other
foreign
materials.
Complete
oil
change.
6.
Air
tank
does
not
hold
pressure
Faulty
check
valve.
See
“Air
Leaks"
Disassemble
check
valve
assembly
and
clean
or
replace
when
compressor
is
not
running.
7

8
SILENT
I
REPLACEMENT
PARTS
LIST
C.
1
Capacitor
C.
2
CapacitorBracket
C.
3
Washer
C.
4
Cover
C.
5
Retaining
Clamp
C.
6
6'
Power
Cord
C.
7
Storage
Tank
C.
8
Oil
Sight
Glass
C.
9
1/4"
Nut
C.
10
l"O.D.
Washer
C.
11
Sleeve
C.
12
Grommet
C.
13
1/4"
x
1/4"
Threaded
Rod
C.
14
Rubber
Feet
C.
15
DrainPlug
C.
16
Inline
Oil
Filter
#50-053
C.
17
1/4"
Nipple
C.
18
Air
Regulator
C.
19
Air
Gauge
C.
20
Pressure
Relief
Valve
C.
21
1/4"
Male
to
Female
90°
Elbow
C.
22
Pressure
Switch
C.
24
1/4"
Nipple
C.
25
Check
Valve
C.
26
Hose
Assembly
C.
27
90°
Elbow
1/4*
to
1/4"
Male
C.
28
Oil
Cap
C.
29
Motor
Cover
Gasket
C.
30
Motor
Cover
C.
31
Air
Intake
Filter
C.
32
Thermal
Overload
C.
33
Retaining
Clamp
Overload
C.
34
Starter
Relay
C.
35
CapacitorBracketScrew
C.
36
Cover
Clamping
Band
C.
37
Band
Screw
and
Nut
C.
38
Compressor
Cover
C.
39
Compressor
Cover
Screws
C.
40
Handle
C.
41
Handle
Screw

8
9
10
11
12
13
14
15
17
18
9

to
SILENT
II
REPLACEMENT
PARTS
LIST
4
B.
1
Air
Intake
Filter
\
B.
2
Starting
Relay
/
B.
3
Starting
Relay
Cover
B.
4
Retaining
Clamp
Relay
\
B.
5
Retaining
Clamp
Overload
)
B.
6
Thermal
Overload
B.
7
Capacitor
B.
8
Capacitor
Screws
B.
9
Capacitor
Mounting
Bracket
5
B.
10
Oil
Sight
Glass
B.
11
Grommet
6
B.
12
Sleeve
B.
13
I"
Washer
B.
14
1/4"
Bolt
B.
15
Motor
&
Cover
B.
16
Motor
Cover
Gasket
B.
17.Oil
Cap
B.
18
Cover
Clamping
Band
7
B.
19
Band
Screw
&
Nut
B.
20
1/4"
Nipple
8
B.
2
1
1/4"
FPT
x
1/4"
MPT
Elbow
B.
22
Pressure
Relief
Valve
(
9
)
B.
23
Air
Regulator
B.
24
Air
Gauge
B.
25
Air
Regulator
Mounting
Bar
B.
26
Tank
Pressure
Gauge

B.
27
Drain
Plug
B.
28
1/4"
Bolt
B.
29
1"
Washer
B.
30
Storage
Tank
B.
31
Tank
Ring
B.
32
1/8"
Nipple
B.
33
Check
Valve
B.
34
Pressure
Switch
Mounting
Bar
B.
35
Pressure
Switch
B.
36
Hose
Assembly
B.
37
1/8"MPTx
l/8rPT
90°
Elbow
B.
38
6'
Power
Cord
B.
39
Handle
Grip
B.
40
Check
Valve
Adaptor
B.
41
Tank
Base
B.
42
In-Line
Oil
Filter
#50-053

Keep
this
manual
with
compressor
for
Information
on
the
ordering
of
replacement
parts
Always
use
caution
and
good
sense
when
air-brushing
with
any
material
You
should
have
an
exhaust
ventilation
system
to
dilute
all
vapors
when
brushing
indoors.
An
open
window
or
a
poorly
maintained
or
improperly
fitted
respirator
may
not
provide
adequate
protection.
For
additional
information
on
safety
considerations,
contact
NIOSH,
the
foundation
for
the
Community
of
Artists,
and
the
Consumer
Product
Safety
Commission.
Ask
your
retailer
for
a
booklet
on
other
Badger
air-brush
accessories
and
supplies,
including
a
complete
line
of
air-brushes,
compressors,
hoses,
regulators
and
Foto/Frisket
film.
Badger
also
has
the
most
comprehensive
how-to
books.
For
more
information
send
504
for
a
full
color
catalog
BA-300
BADGER
AIR-BRUSH
CO.
9128W
BELMONT
AVE
FRANKUN
PARK
IL
60131
.in
Canada
by:
HOBBY
INDUSTRIES
•
24
Ronson
Drive
•
Rexdale.
Ontario
M9W1B4
This manual suits for next models
1
Table of contents
Popular Air Compressor manuals by other brands
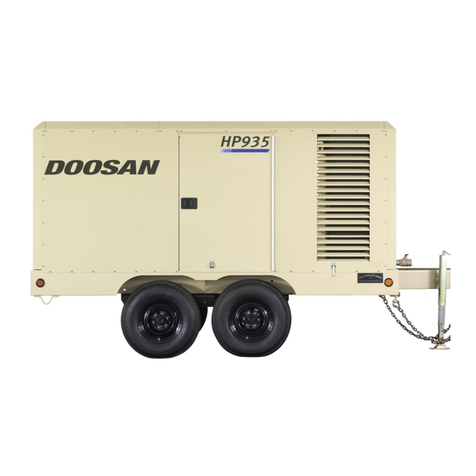
Doosan
Doosan HP935WCU Operation and maintenance manual
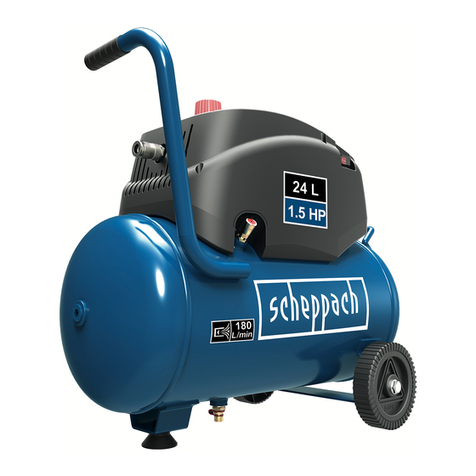
Scheppach
Scheppach GK240ofx Translation of original instruction manual
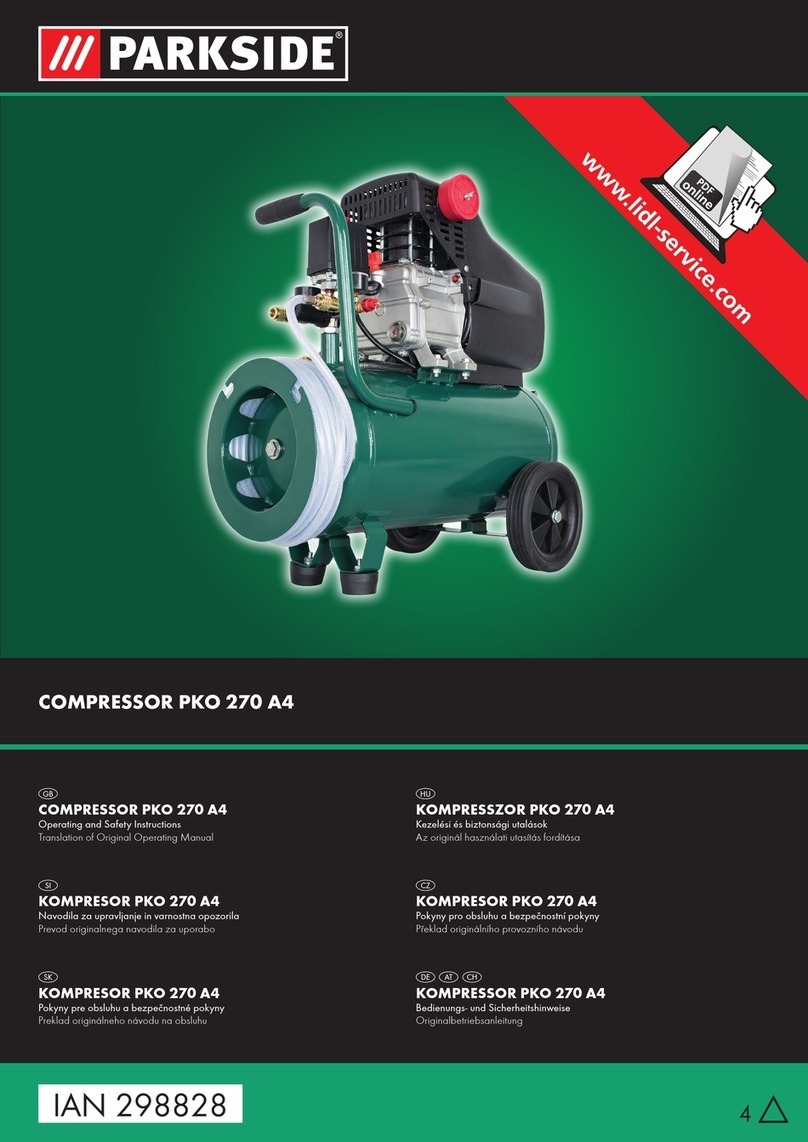
Parkside
Parkside PKO 270 A4 Operating and safety instructions
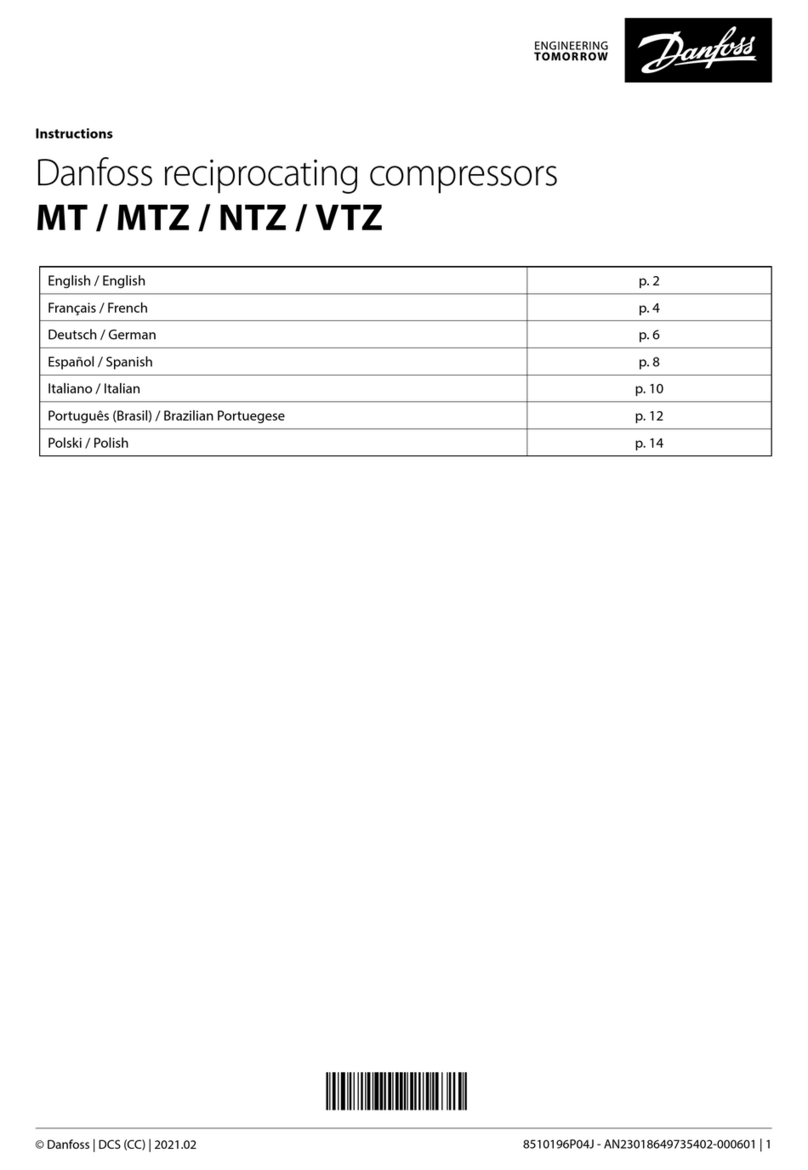
Danfoss
Danfoss VTZ Series instructions
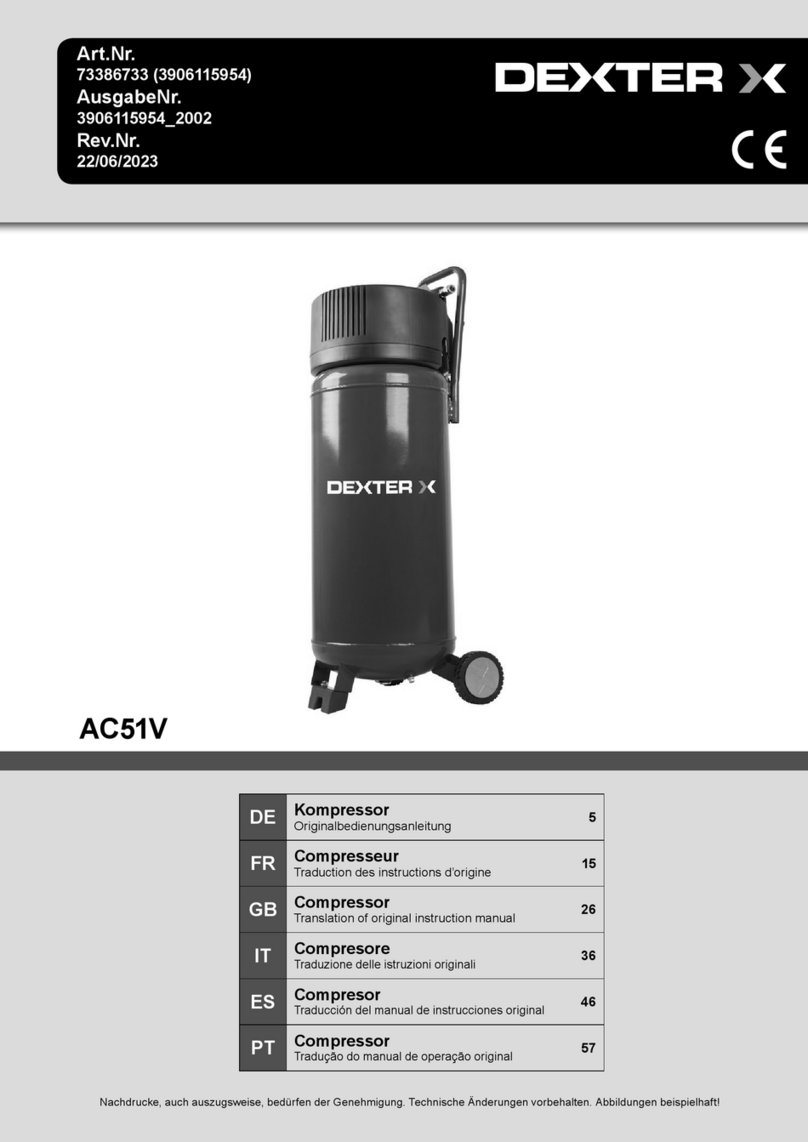
Dexter Laundry
Dexter Laundry AC51V Translation of original instruction manual
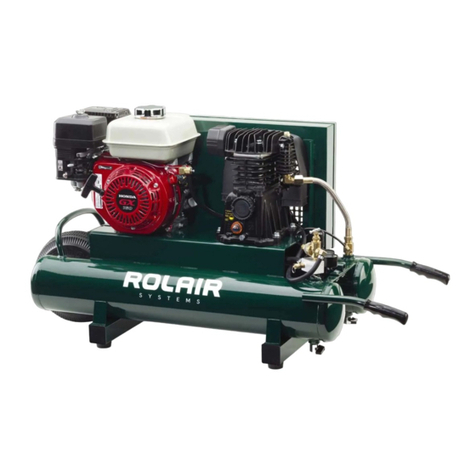
Rolair
Rolair 5520MK103 owner's manual
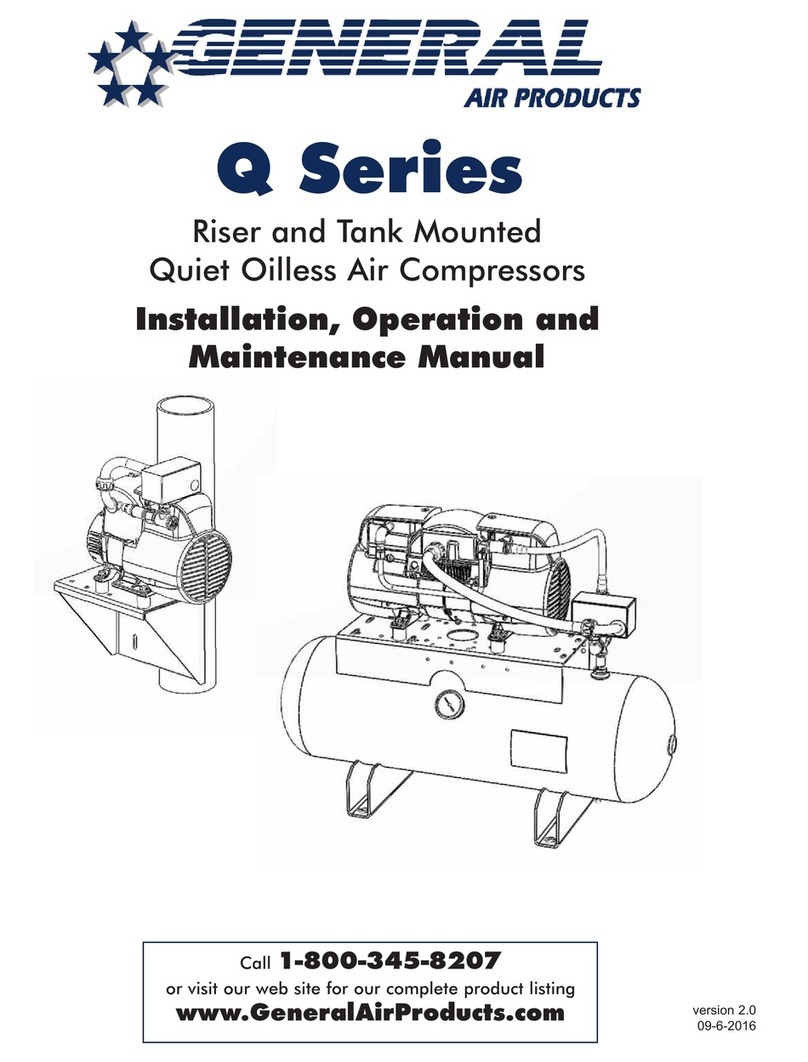
General Air Products
General Air Products Q Series Installation, operation and maintenance manual
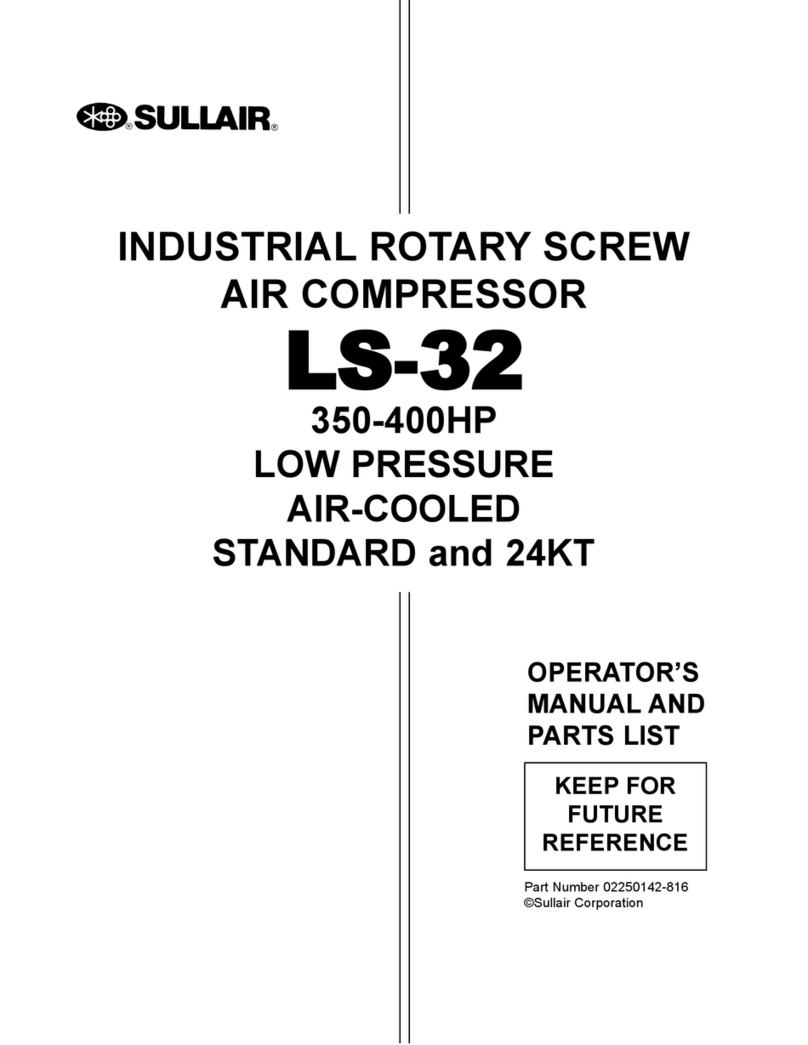
Sullair
Sullair LS-32 Operator's manual and parts list
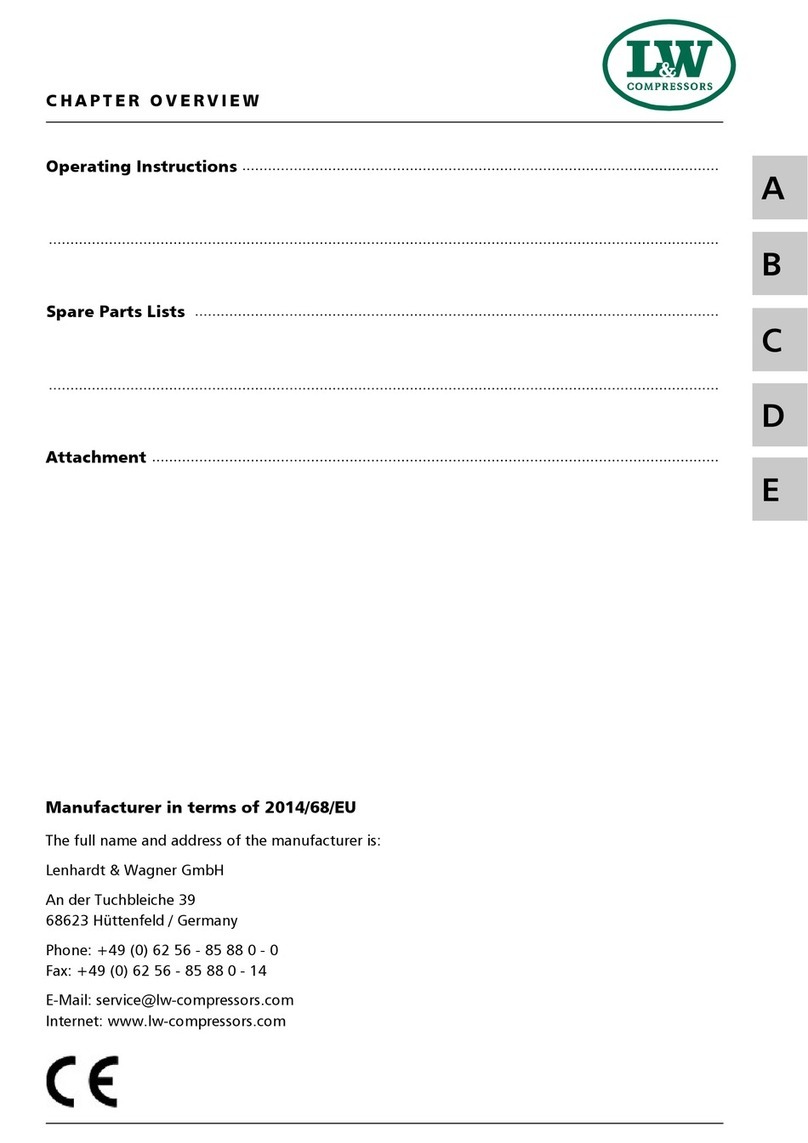
L&W
L&W SC-600 ES operating instructions

Gardner Denver
Gardner Denver L160 110A V2 user manual

Cartrend
Cartrend 10737 Original instruction manual
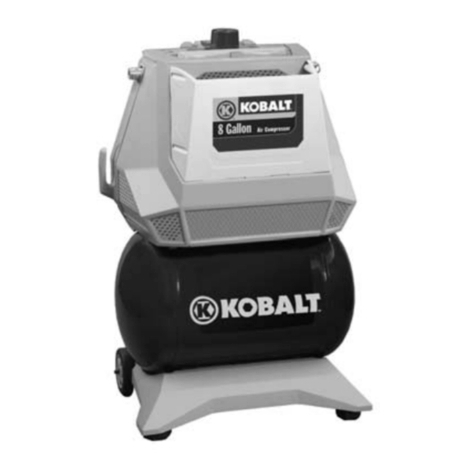
Kobalt
Kobalt 162700 Operator's & parts manual